Технология производства газобетонных блоков | Полезная информация о газобетоне завода ДСК Грас
В 60-х годах прошлого века, когда развивалось производство автоклавных бетонов, существовали разные способы их изготовления. Одни из них подразумевали использование цементных, другие — известковых, третьи — смешанных вяжущих составов. В те годы был распространён термин «газосиликатный бетон», который применяется и в наши дни — но уже ошибочно: силикатные ячеистые бетоны ушли в прошлое как класс. Промышленность XXI века не выпускает чистых газосиликатов — сегодня распространены более долговечные бетоны на цементном и смешанном вяжущем составе. Поэтому те, кто в наши дни говорят «газосиликат», в большинстве случаев имеют в виду автоклавный ячеистый газобетон.
За последние 15 лет среднегодовой ввод жилья в России вырос в 2,5 раза. Выпуск автоклавного газобетона за этот же период увеличилось в 12 раз. Он стал самым массовым материалом для возведения стен, применяемым в строительстве.
В последние годы растёт популярность газобетонных блоков — в частности, марок низких плотностей, например, D350. Стоит отметить, что сегодня в России ежегодно выпускается более 1,5 млн м3 блоков низких плотностей. Всё чаще звучит вопрос: как производится этот материал? Развёрнутый ответ на него — в этой статье.
Подготовка сырья
Для изготовления блоков из ячеистого бетона используется смесь цемента, гипса, песка, извести и воды. В неё в небольших объёмах добавляется алюминиевая паста. За точное дозирование всех компонентов отвечает автоматизированная установка.
Формование
Из миксера сырьё поступает в формы большого объёма. Здесь смесь находится несколько часов при температуре, составляющей приблизительно 50º С. Идёт реакция, и массив поднимается, напоминая дрожжевое тесто. Возникает огромное количество ячеек (пор), которые и дают стройматериалу его название. После того, как массив приобрёл требуемый объём, нужно еще некоторое время, чтобы он предварительно отвердел.
По окончании процесса смесь подаётся на участок резки.
Резка на блоки
На очередной стадии массив, сохраняя вертикальное положение, движется по участку резки. Здесь с применением ножей и струн он режется по заранее заданным размерам.
Интересный факт
Отходы материала, образующиеся при резке, вновь поступают в производство. Технологический процесс выпуска ячеистого бетона, таким образом, становится безотходным.
Обработка в автоклаве
Нарезанные блоки помещаются в автоклав — камеру с температурой 180-190ºС, давлением около 12 бар и насыщенным паром. Здесь будущий стройматериал выдерживается в течение 12 часов. За это время в блоках формируется кристаллическая структура, выгодно отличающая автоклавный газобетон от других материалов и придающая ему достойные практические свойства.
После обработки в автоклаве готовый стройматериал с применением крана-делителя выкладывается для остывания.
Упаковывание
На последнем этапе блоки из ячеистого бетона — например, марки D300 — аккуратно запаковываются в перфорированную термоусадочную пленку с помощью автоматического оборудования.
Упакованные газобетонные блоки транспортируются на склад с помощью вилочных погрузчиков. С этого момента они готовы к реализации.
Отличительные особенности применяемого оборудования
Для производства автоклавного ячеистого газобетона на нашем заводе применяется оборудование марки HESS AAC Systems B.V., отвечающее самым строгим международным стандартам.
Система подачи сыпучих материалов. В ней используется запатентованная технология Lahti Precision, реализованная только в линиях HESS, в основе которой — псевдоожижение (флюидизация) материалов. Система разгружает силоса и дозирует подачу сыпучих материалов в псевдоожиженном состоянии, создаваемом с помощью воздуха.
Устройство кантования массива. Массив перед резкой кантуется в форме в вертикальное положение, после чего корпус формы удаляется. Массив не подвергается механическому захвату манипулятором, что положительно влияет на качество конечного продукта. Предотвращается появление трещин, исключается деформация массива, сохраняются прочностные и геометрические характеристики блоков.
Устройство вертикальной, предварительной и окончательной боковой резки. Обрезает материал по трём измерениям, позволяет регулировать толщину снимаемого слоя или выравнивать поверхность массива после предварительной резки. Линия оснащена системой, следящей за обрывом струн. Обрезки массива отбрасываются в шлам-канал, промываемый водой. Отсюда они поступают в ёмкость с размалывающим устройством и мешалкой, расположенную под линией резки. Из ёмкости шлам транспортируется в шламбассейн для дальнейшего использования. Такое решение даёт экономию сырья и служит частью концепции «Безотходное производство».
Система разделения массива. В ней реализована уникальная технология разделения «зелёного» массива, позволяющая расслаивать его непосредственно после резки — до автоклавирования. Массив подается в автоклав разделённым на слои. Благодаря этому пропаривание выполняется максимально равномерно и качественно, и газобетон приобретает предельно возможную прочность. В отличие от традиционных технологий, подразумевающих резку вертикально стоящего массива и разделение «белого» продукта, слипания слоёв при пропаривании не происходит. Поэтому не требуется и дополнительного разделения блоков после автоклавирования. Благодаря этому сохраняется привлекательный вид блоков, исключается появление сколов, отверстий и трещин, обеспечивается идеальная геометрия конечного продукта.
ООО «Газобетон» — Ивановский завод автоклавного газобетона
ivgb. ru|ivgazbeton.do.am|ivgb.ru
ООО «Газобетон» единственный производитель автоклавного газобетона в Иванове и Ивановской области. Направление деятельности предприятия – производство стенового материала, который используется в процессе многоэтажного и малоэтажного строительства, а также в коттеджном домостроении.
Завод выпускает газобетонные блоки на современном немецком оборудовании фирмы WKB, являющейся международным производителем инновационного высокотехнологичного оборудования для промышленности строительных материалов. Таким образом, у покупателей есть возможность купить газобетонные блоки, выбрав наиболее подходящий вариант из широкого ассортимента, который предлагает предприятие.
Производство стеновых материалов, соответствует нормам ГОСТа.
Газобетонные блоки в Иванове и Ивановской области, благодаря взаимовыгодным договоренностям с поставщиками сырья, приобрели особые ценовые условия, которые дают возможность осуществлять продажу строительного стенового материала потребителю по выгодной цене, которая является ниже средней рыночной.
В Иванове купить газобетонные блоки выгодно исходя из следующих причин:
- Большой ассортимент выпускаемой продукции, который предлагает завод
- Возможность купить газобетонные блоки от производителя по демократичным ценам
- Быстро получить свой заказ с помощью наших услуг по доставке. Доставка газобетонных блоков с завода осуществляется длинномерным автотранспортом и манипуляторами в предварительно оговоренное с покупателем место и время. Пакет всех необходимых документов на покупку товара предоставляется покупателю в процессе получения заказа
- Бесплатные консультации по расчету количества стенового и перегородочного материала, который необходим для вашего объема строительства
- Работу с безналичным и наличным расчетом на условиях предоплаты
Производство автоклавного газобетона в России — статьи завода «ЭКО», в Москве
к.т.н. Вишневский А.А., Гринфельд Г.И.
Национальная Ассоциация производителей автоклавного газобетона
Массовое производство АГБ в СССР началось в конце 50-х годов прошлого столетия, когда были построены 10 заводов на польском оборудовании с совокупной мощностью более 1,5 млн м3/год [1]. Предприятия преимущественно выпускали крупноразмерные армированные изделия с плотностью 800-1000 кг/м3.Позже к этим предприятиям добавились заводы с отечественным оборудованием («Универсал 60» и «Силбетблок» и др.), позволяющие выпускать мелкие блоки по резательной технологии. К 1984 году в СССР насчитывается уже 99 предприятий по выпуску ячеистого бетона с суммарной годовой производительностью около 5,9 млн. м3 изделий, выпускающие армированные изделия и мелкие блоки с плотностью 600-700 кг/м3[2, 3].
С распадом Советского Союза, в России, как и в других странах бывшего СССР, отмечается общий спад в производстве газобетона. В связи с резким сокращением объемов строительства в начале 90-х годов наблюдается значительное падение спроса на строительные материалы.
Новый этап в развитии газобетона связан с появлением в России в 1994-1997 гг. импортных технологических линий, позволяющих выпускать АГБ «нового поколения», отличающийся от прежнего точными геометрическими размерами и лучшими физико-механическими свойствами. Заводы на импортном оборудовании, обеспечили появление на российском рынке более 0,5 млн.м³ газобетонных блоков плотностью 500-600 кг/м3. Газобетонные изделия «нового поколения» быстро нашли свое место на рынке стеновых материалов, постепенно вытесняя неавтоклавные ячеистые бетоны, керамзитобетон, создавая конкуренцию керамическому и силикатному кирпичу.
На этом фоне начиная с 2004 г. вводятся в эксплуатацию новые заводы с импортными технологическими комплексами (рис. 1). В итоге, к концу 2014 г. число производителей АГБ увеличилось до 74, а их общая производственная мощность составила 15,9 млн м В большей степени (79,2 %) эти мощности представлены именно импортными технологическими комплексами (табл. 1).
Таблица 1
Данные об установленных мощностях по выпуску АГБ
Технологические линии |
Количество заводов |
Количество технологических линий* |
Установленные мощности |
|
м3/год |
% |
|||
Импортные |
50 |
51 |
12 628 000 |
79,2 |
Отечественные |
24 |
31 |
3 320 300 |
20,8 |
Все |
74 |
82 |
15 948 300 |
100 |
* Число линий и заводов не совпадает, так как некоторые заводы имеют несколько линий.
В прошедшем году всеми предприятиями отрасли было выпущено 12 899 318,94 м3 изделий из АГБ. В сравнении с прошлым годом выпуск АГБ увеличился на 14,2 %. Повышение выпуска обусловлено как вводом новых мощностей, так и увеличением выпуска на действующих заводах. Как показал проведенный анализ, в 2014 г. большая часть предприятий (46) увеличила выпуск АГБ в сравнении с 2013 г.
Больше всего газобетона, как в абсолютных, так и в относительных единицах выпустили заводы Центрального федерального округа. Выпуск на долю населения (табл. 2) в ЦФО составил 0,14 м3/чел, что более чем в 1,5 раза больше, чем в среднем по России (0,09 м3/чел). Косвенно это свидетельствует о большем объеме потребления газобетона в данном регионе. Меньше всего АГБ производится и применяется в Дальневосточном и Северо-Кавказском округах, что связано с небольшим числом производителей газобетона в этих регионах, низкой популярностью данного материала, а также невысокими объемами строительства.
Таблица 2
Выпуск АГБ по федеральным округам
Федеральный округ |
Число заводов |
Общий выпуск, м3 |
Выпуск на душу населения, м3/чел |
Центральный |
24 |
5 579 914,96 |
0,14 |
Приволжский |
16 |
2 489 934,25 |
0,08 |
Южный |
5 |
1 163 287,50 |
0,08 |
Северо-Западный |
9 |
1 247 628,56 |
0,09 |
Уральский |
7 |
1 147 255,92 |
0,09 |
Сибирский |
7 |
1 047 697,75 |
0,05 |
По общему объему произведенного АГБ можно оценить объем внутрироссийского потребления данного материала, приняв во внимание тот факт, что российский газобетон практически не поставляется на экспорт. Но в тоже время импорт изделий из АГБ, главным образом, из Белоруссии остается достаточно высоким. По данным Секретариата межправительственного совета по сотрудничеству в строительной деятельности стран СНГ, экспорт газобетона из Республики Беларусь в Россию в 2014 г. составил 1,3 млн м3, в том числе в Центральный и Северо-Западный регионы по 500 тыс. м3. Кроме этого, по данным торговых организаций, реализующих АГБ в Калининградской области, объем импорта газобетона из Польши в этот регион составил 200 тыс. м3. В этой связи, общее потребление изделий из АГБ в России в 2014 г. можно оценить на уровне 14,4 млн м3.
В настоящее время практически весь АГБ в России производится в виде мелких стеновых блоков. На долю армированных изделий (перемычки, плиты, панели) по результатам 2014 г. приходится лишь 0,46 % от общего выпуска АГБ. Объем армированных изделий, произведенных в 2014 г., составил 58306,91 м3.
Стеновые блоки чаще всего производят с плотностью от 300 до 800 кг/м3(рис. 2), при этом основной объем газобетона (90 %) представлен марками D500 и D600. Усредненный показатель плотности всего газобетона, выпущенного в 2014 г., составляет 516,7 кг/м3. В сравнении с 2013 годом (518,4 кг/м3) он незначительно снизился. Таким образом, направленность рынка в сторону снижения плотности производимого АГБ сохраняется в течение последних лет [4, 5].
На импортных линиях, как правило, выпускают более легкие изделия, на отечественных — чуть тяжелее (рис. 3). Это связано с особенностями оборудования: импортные комплексы предоставляют большую возможность для выпуска изделий пониженной плотности (за счет точной дозировки компонентов,интенсивного смешивания, наличия закрытых зон твердения, автоклавирования при повышенном давлении и др.).
Исследования рынка, проводимые НААГ, в последние годы позволили выявить некоторые региональные особенности выпуска АГБ. Наиболее легкую продукцию выпускают заводы Северо-Западного региона: усредненная плотность выпускаемого газобетона там самая низкая по России — 465 кг/м3. Наиболее тяжелый газобетон выпускается в Сибири: средняя плотность 569 кг/м3(рис. 4). Подобный результат объясняется главным образом сложившимися традициями, которые в свою очередь зависят от возможностей производителей и их усилий по продвижению продукции. В Северо-Западном регионе одними из первых освоили массовый выпуск АГБ с плотностью 400 кг/м3и ниже, а также провели активную компанию по его продвижению. В Сибирском округе сложилась обратная ситуация. Там основные производители сориентировались на выпуск продукции с плотностью 500 кг/м3 и выше и до настоящего времени активного производства продукции пониженной плотности не производят. В ряде случаев на плотность выпускаемых изделий влияет сейсмичность региона. В частности, в Южном округе выпуск изделий пониженной плотности затруднен в связи с высокой сейсмичностью.
Подводя итог вышесказанному можно отметить, что производство автоклавного газобетона продолжает активно развиваться. Ежегодно запускаются новые линии по выпуску АГБ, действующие заводы наращивают свои объеме. Все это обеспечивает ежегодный рост мощностей по производству АГБ в средним на 3-5 % в год. Как следствие, растет выпуск данного материала и в 2014 совокупный объем впущенного АГБ составил 12,9 млн м3. При этом качественно меняется выпускаемая продукция. На смену армированным панелям плотностью 700-800 кг/м3 пришли мелкие стеновые блоки плотностью 400-600 кг/м3 с точными геометрическими размерами и улучшенными физико-механическими характеристиками. Другими словами, тенденции, сопровождающие рынок на протяжении всей его истории сохраняются и в настоящее время.
Весомый вклад в результаты отрасли вносят предприятия-члены НААГ. На сегодняшний день Ассоциация объединяет около половины всех мощностей по выпуску АГБ – совокупная мощность членов НААГ 7,3 млн м3/год. В 2014 г. 23 завода, входящие в НААГ, произвели 6,4 млн м3 АГБ (49,6 % от общего выпуска).
НААГ это не просто объединение лидеров отрасли, эта организация занимающаяся поддержкой производителей АГБ (нормативной базой, научно-техническими исследованиями), а также осуществляющая популяризацию и продвижение автоклавного газобетона. В рамках этой работы НААГ ежегодно реализует исследование рынка, по результатам которого и была подготовлена данная статья.
Литература
- Вылегжанин В.П. Газобетон в жилищном строительстве, перспективы его производства и применения в Российской Федерации / В.П. Вылегжанин, В.А. Пинскер. Строительные материалы, 01. 2009. С.4-8.
- Домбровский А.В. Производство ячеистых бетонов. Обзорная информация. ВНИИЭСМ. Выпуск 2. 1983. с.76.
- Коровкевич В.В., Пинскер В.А и др. Малоэтажные дома из ячеистых бетонов. Рекомендации по проектированию, строительству и эксплуатации. Ленинград: ЛенЗНИИЭП., 1989. 284 с.
- Вишневский А.А., Гринфельд Г.И., Куликова Н.О. Анализ рынка автоклавного газобетона России // Строительные материалы. 2013. №7. С.40-44.
- Вишневский А.А., Гринфельд Г.И., Смирнова А.С. Итоги работы предприятий по производству автоклавного ячеистого бетона в 2013 г // Технологии бетонов. 2014. №4. С. 44-47.
состав, сырьё, свойства, сферы применения
Введение:
Газобетон, (именуемый также ячеистый бетон), наряду с силикатным кирпичом относится к строительным материалам, твердеющим в результате пропаривания. Речь идет о легком, высокопористом, минеральном строительном материале.
Газобетон состоит приблизительно на 20% объема из твердых материалов и приблизительно на 80% объема — из воздуха. — из воздуха. Это означает особенно эффективное и экономное использование сырьевых материалов в процессе его производства (из 1 м3 твердых материалов изготавливается от 4 до 5 м3 газобетона).
Производство:
Газобетон производится из следующего сырья: негашеная известь, цемент, алюминиевая паста и кварцевый песок. Сначала сырьевые материалы в определенных пропорциях и в определенной последовательности (очередность смешивания) перемешиваются с добавлением воды до состояния гомогенной массы. В данную смесь добавляется небольшое количество алюминиевой паста. Состав смеси зависит от желаемых физических показателей газобетона. Полученная смесь заливается в предварительно смазанные формы, где далее протекает реакция алюминия со щелочной средой из извести и цемента с выделением газообразного водорода. Возникает большое количество маленьких воздушных пузырьков (пор), которые вспучивают (поднимают) постепенно твердеющую массу. После 10 — 15 минут достигается конечный объем. Еще через 1,5 — 2 часа выдержки газобетонный массив можно резать на отдельные элементы желаемых размеров при помощи пневматически натянутых струн. Запаривание порезанных блоков происходит в автоклавах при давлении насыщенного пара 10-12 бар и температуре 180-195 °С. По истечении 8 — 11 часов материал приобретает свои окончательные характеристики и прочность. Процесс производства позволяет изготавливать как неармированные изделия, так и строительные элементы со стальным армированием. При замкнутом цикле производства не выделяется никаких веществ, которые бы загрязняли воздух, воду или почву. Благодаря твердению под действием водяного пара энергопотребление при производстве газобетона, по сравнению с обжигаемыми строительными материалами, сравнительно невысоко.
Свойства:
Наряду со строительно-физическими свойствами, как то прочность на сжатие и на изгиб, теплоизоляция и звукоизоляция, для потребителей газобетона важны также прочие факторы, влияющие, например, на комфортность и на здоровье. Сюда относятся загрязнение воздуха, вредные выбросы и доза облучения. Газобетон в составе строительной конструкции не дает ни твердых, ни газообразных выбросов. Газобетон как строительный материал был проанализирован в ходе многочисленных групповых исследовании и каждый раз все проверяемые параметры оказывались ниже установленного предельного значения. На свойства газобетона можно оказывать влияние с помощью различного состава рецептур для смеси. За счет добавления различного количества алюминия можно изменять объемную плотность газобетона в пределах большого диапазона. Общепринято производство продукции плотностью от 300 кг / м3 до 700 кг/м3 Газобетон, в сравнении с традиционным бетоном обладает, вследствие своей меньшей плотности, также и меньшей теплопроводностью, что определяет его очень высокие теплоизоляционные качества. Благодаря равномерной структуре материала теплоизоляционные качества являются изотропными, т.е. одинаковыми во всех направлениях.
Объемная масса: от 400 до 600 кг/ м3
Прочность на сжатие: от 2,0 до 7,5 Н/мм2
Размеры изделий: длина 625 или 600 мм
высота 200 или 250 мм
ширина от 100 до 500 мм
Система паз-гребень начиная с ширины изделий 150 мм.
Коэффициент теплопроводности: от 0,096Вт/ мК до 0,16Вт/мК
Класс пожаростойкости: Al – огнестойкий
Применение:
Из газобетона производят строительные материалы для кладки (блоки, крупноформатные элементы) и армированные детали конструкции (стеновые и кровельные панели, плиты перекрытия). Газобетон используется для возведения внешних и внутренних стен. Прежде всего, в качестве наружной обшивки при монолитном строительстве в полной мере проявляются его преимущества (теплоизоляция и однородность материала). Благодаря тому, что газобетон легко и разнопланово поддается обработке, он также популярен в качестве материала для индивидуальной внутренней отделки. При использовании газобетона в частном домостроении этот строительный материал берет на себя, помимо несущей способности и придания жесткости зданию, также строительно-физические свойства: теплоизоляцию, противопожарную защиту и звукоизоляцию. Коробка здания данного типа постройки полностью собирается из газобетона.
В высотном строительстве используются только строительно-физические свойства газобетона. Несущая способность и придание жесткости высотному зданию -задачи каркасной конструкции из железобетона или стальных балок.
Производство газобетона
Ячеистый бетон – современный строительный материал, позволяющий экономить средства, за счет высокой экономичности, повышенного удобства и функциональности. Газобетон – это высококачественный, многообразный строительный материал, который производится в форме блоков, элементов или армированных плит. Благодаря своим многочисленным достоинствам, газобетон превратился в незаменимым строительным материалом настоящего и будущего. Ячеистый бетон известен под различными названиями: ячеистый бетон, газобетон, газоблок.
Газобетон является представителем семейства ячеистых бетонов, и обладает характерной чертой представителей данной группы — ячеистой структурой. Пузырьки газа (ячейки) занимают больше половины объема материала, поэтому автоклавный газобетон имеет небольшой вес.
Производство газобетона
Ячеистый бетон изготавливается из воды, извести, цемента и кварцевого песка. В течение 4 – 5 минут в газобетоносмесителе готовится «масса» — тщательно смешанная смесь исходных компонентов. Далее в эту смесь в небольшом количестве добавляют суспензию алюминиевой пудры на водной основе, которая вступает в реакцию с известью. Водород возникший в результате реакции образует в сырьевой массе пену из пор от 0,5 до 2 мм, равномерно распределенных внутри материала. Все составляющие материала дозируются компьютером.
После добавления готовой алюминиевой пасты смесь загружают в специальные металлические емкости, в которых и проходит основной этап производства газобетона вспучивание. Чтобы ускорить процесс химической реакции, схватывания и твердения массу подвергают виброусадке. Когда газобетон достигает стадии предварительного твердения, с застывшей смеси материала срезают неровную верхушку, и далее массу уже нарезают на готовые газоблоки определённых размеров. На следующем этапе производства газобетона полученные блоки подвергают тепловой обработке в автоклаве. Затем производится калибровка блоков специальной фрезерной машиной. И на конечном этапе производства выполняется отделка фасадных поверхностей.
Применение современных технологий, позволяющее управлять процессом производства газобетона, обеспечивает абсолютную однородность готового материала, поэтому свойства газобетонных блоков одинаковы в горизонтальном и вертикальном направлении.
производство, свойства и разновидности – Новости Владивостока и Приморья (16+)
Удивительный газобетон для знатоков качества.
Газобетон — один из типов бетона в виде ячеек, появившийся несколько десятилетий назад. Применяется практически во всех видах строительства, в качестве основного материала и при теплоизоляции.
Газобетон и его изготовление
Производятся блоки из газобетона с использованием безопасных и экологичных комплектующих от цемента до пудры из алюминия. Пудра нужна для образования газов в процессе производства. После изготовления материал режут на части, обрабатываемые позже в автоклаве. В итоге получается материал, который годен для решения различных строительных заданий.
В зависимости от свойств, необходимых в материале на выходе, может производиться с разным количеством составляющих. Это даёт возможность изготавливать блоки с непохожими свойствами.
Основные качества газобетона
Материал стал прорывом в строительстве, он показывает отличные пользовательские свойства, похожие одновременно на свойства камня, бетона, кирпича и дерева.
Низкоэтажная стройка частных домов почти не проводится без использования газобетона, показывающего следующие качества:
• невысокий удельный вес, всего 20% от веса обычного бетона;
• убедительная прочность, не глядя на малый вес;
• звукоизолирующие и теплосберегающие свойства на отличном уровне;
• огнеупорность, экологичность и отсутствие токсичности;
• низкая чувствительность к биоактивным влияниям, морозостойкость;
• чёткость геометрии, лёгкость монтажа;
• невысокая стоимость;
• расчётная долговечность (поскольку материал относительно новый, статистики ещё нет).
Достоинства газобетона
Отличные тех. характеристики и различные пользовательские свойства дают в итоге множество достоинств применимого в разных условиях материала. Поэтому его избирают в линии остальных видов блоков или иных стройматериалов. На сайте компании «Партнер» https://gazoblok-spb.ru/ Вы можете узнать цену на газобетонные блоки.
Некоторые, требующие упоминания достоинства:
1. Газобетон имеет похожие свойства с камнем, он не портится и не меняет прочность со временем.
2. Используемое при производстве натуральное сырьё даёт экологическую чистоту.
3. Лёгкий состав с порами — стена из газобетона «дышащая», однако тёплая.
4. Хорошие теплоизоляционные свойства помогают экономить энергоресурсы.
5. Несложная механическая обработка даёт возможность изменения конструкции в нужную сторону.
6. Простая сборка без использования спецоборудования делает проще строительство и уменьшает затраты.
Разновидности газобетонных блоков
Технологии изготовления дают возможность сделать блоки из газобетона разных размеров и типов. Имеет смысл пользоваться той или иной разновидностью блоков из газобетона согласно требованиям проектов и условий стройки.
Стандартные блоки с плоскими стенками
Привычная форма, прямоугольная или квадратная, с плоскими прямыми стенками. Этот вид материала содержит более плотный бетон, порядка 500 кг/м3. Это обеспечивает прочность и действенную звукоизоляцию. Стандартные блоки соответствуют требованиям любого вида кладки.
Система «паза-гребня»
Это вид блоков с гребне-пазовыми соединениями торцевых поверхностей. Немного меньшая плотность (400 кг/м3). Монтаж более удобен, — поверхности типа «гребень-паз» соединяются в замки. Соответственно, обработка вертикальных швов раствором не требуется. Система не только снижает затраты на раствор и повышает скорость монтажа, но и облегчает ручную переноску.
Перегородочные блоки
При возведении внутренних стен и перегородок, не являющихся несущими, используются неширокие блоки (до 150 мм). Их высота и длина достаточно велика, что позволяет быстро и с небольшим расходом материала построить перегородку в помещении. Блоки лёгкие, но достойной надёжности и прочности.
U-блоки
Нестандартное предназначение у U-блоков — они применяются при оборудовании монолитных армопоясов. Блоки длиной в 500 мм и U-образной в сечении формы предназначены для того, чтобы внутреннюю полость заполняли бетоном.
Не глядя на то, что стройка из блоков несложна и доступна, необходимо соблюдать важные технологические процессы и детали. Тогда скорость и стоимость возведения дома будет оптимальной, и постройка будет обладать гарантированными качествами и безопасностью.
Области применения
Газобетон используется при возведении несущих стен, наружных и внутренних, конструкции дополнительного слоя теплоизоляции. Применяется для быстрого строительства тонких и лёгких ненесущих перегородок. Этот материал используется в любых погодных условиях.
«Партнер» — Ваш надежный поставщик газобетонных блоков и кирпича по выгодным ценам.
«Группа ЛСР» запустила новую линию производства газобетона на заводе в Ленинградской области
«Группа ЛСР» запустила новую линию производства газобетона на заводе в Ленинградской области
Накануне Дня строителя «Группа ЛСР» запустила новую линию производства газобетона на собственном заводе в Сертолово Ленинградской области. Мощность завода теперь увеличится с 180 тыс. до 560 тыс. куб. м изделий в год, что позволит компании стать крупнейшим производителем газобетона на Северо-Западе.
В торжественной церемонии запуска линии приняли участие губернатор Ленинградской области Александр Дрозденко, генеральный директор «Группы ЛСР», почетный гражданин 47 региона Андрей Молчанов и председатель Законодательного собрания Ленинградской области Сергей Бебенин.
– Радостно, что в наших краях продолжают открываться новые востребованные предприятия, – заявил Александр Юрьевич в своей приветственной речи перед сотрудниками «Группы ЛСР» и другими официальными лицами. – Объём выпускаемой здесь продукции должен закрыть все потребности Санкт-Петербурга и Ленинградской области в материалах для индивидуального и малоэтажного строительства. Надеюсь, что Сертоловский газобетон будет таким же качественным, как и все остальное, выпускаемое «Группой ЛСР». Эта компания – наш давний и надежный партнер. Совместно на территории области мы реализовали не один проект. Думаю, в будущем нам предстоит еще много таких.
– «Группа ЛСР» завершила перевод своих газобетонных мощностей из Петербурга в Ленинградскую область, – добавил Андрей Молчанов. – Сейчас на Сертоловском газобетонном заводе уже работают 230 человек. Большинство – жители области. А это значит, что «Группа ЛСР» остается не только одним из крупнейших налогоплательщиков Ленинградской области, но и одним из главных работодателей домашнего региона. Мы и впредь продолжим работать на благо области и ее жителей.
Сертоловский газобетонный завод является частью компании «ЛСР. Стеновые» – производителя керамической и газобетонной продукции в составе «Группы ЛСР». Ранее производство газобетонных изделий компании располагалось на Октябрьской набережной в Санкт-Петербурге. В 2017-2018 годах состоялся постепенный переезд и модернизация площадки в Сертолово. Благодаря четкости планирования и решения организационных вопросов, эта работа была выполнена в сжатые сроки. Новая линия Сертоловского газобетонного завода – это современное полностью автоматизированное производство. Ее мощность позволяет выпускать до 380 тыс. куб. м газобетона в год. На территории завода действует также еще одна линия, ранее принадлежавшая предприятию «211 КЖБИ», которое «Группа ЛСР» приобрела на открытом аукционе в 2016 году. Объем выпуска продукции на этой линии – 180 тыс. куб. м. Таким образом, совокупная мощность предприятия на данный момент 560 тыс. куб. м в год.
Производство автоклавного газобетона | Группа Маса
Газобетон изготавливается из сырья: кварцевого песка, извести, цемента, гипса (ангидрита), алюминиевого порошка или пасты и воды.
В шаровой мельнице с мокрым покрытием (01) сырой песок перерабатывается в песчаную суспензию, которая хранится в резервуарах для песчаной суспензии. Затем песчаная суспензия вместе с другим сырьем транспортируется на дозирующую и смесительную установку Masa (02).
Когда процесс смешивания завершен, смесь подается в литейную форму.Литейную форму перемещают в зону предварительного затвердевания, чтобы пройти процесс ферментации (03), в ходе которого пирог из пенобетона, наконец, достигает заданной прочности на резку. В этот момент лепешка из газобетона извлекается из формы (04) в два этапа, сначала удаляются боковые стороны. Затем пустая литейная форма собирается, смазывается маслом (05) и возвращается в производственный цикл.
Пирог из пенобетона проходит через различные станции линии резки (06) и после этого помещается на решетку для твердения с помощью транспортной установки / поворотного стола (07).
Три кека на решетках для закалки укладываются друг на друга на тележку для закалки и транспортируются в зону ожидания (08) с помощью транспортной платформы. Отсюда кексы загружаются в автоклавы (09). Внутри автоклавов лепешки из пенобетона затвердевают под давлением пара и создают свою окончательную прочность.
Кекки затвердевшего газобетона затем транспортируются к наклоняющемуся столу (10) и, при необходимости, к разделительной машине (11).
После этого газобетонные блоки транспортируются к устройству передачи блоков (12) и укладываются на деревянные поддоны.Отсюда готовая продукция фасуется (13).
Использованные закалочные решетки и закалочные машины возвращаются в производственный цикл через устройство транспортировки закалочной решетки и устройство возврата закалочной тележки (10).
Завод может быть расширен оборудованием для производства изделий со стальной арматурой (14).
Попытка удешевить материалы производства автоклавного газобетона
Для снижения стоимости материалов для производства газобетона в автоклаве (AAC) эти два типа твердых отходов теоретически могут использоваться в качестве аэрирующего агента и источника кремнезема соответственно.
Зольный остаток от сжигания твердых бытовых отходов (зольный остаток MSWI) содержит заметное количество металлического алюминия, а зольный остаток от сжигания в циркулирующем псевдоожиженном слое (CFBC) богат активным SiO2. Таким образом, два типа твердых отходов теоретически могут использоваться в качестве аэрирующего агента и источника кремнезема для производства автоклавного газобетона (AAC) соответственно.
Эта работа направлена на оценку возможности производства AAC, сочетающего зольный остаток ТБО с золой уноса CFBC. Было обнаружено, что AAC с удовлетворительными свойствами может быть успешно получен только из зольного остатка MSWI, летучей золы CFBC, цемента и извести в соответствующих пропорциях, даже без дигидрата гипса и алюминиевого порошка.
Предлагаемый метод значительно снизит стоимость производства AAC.
Анализ выветривания золы сжигания твердых отходов, оцененный по индексам для природных горных пород
Дополнительная информация: Чжицзюань Ван и др.
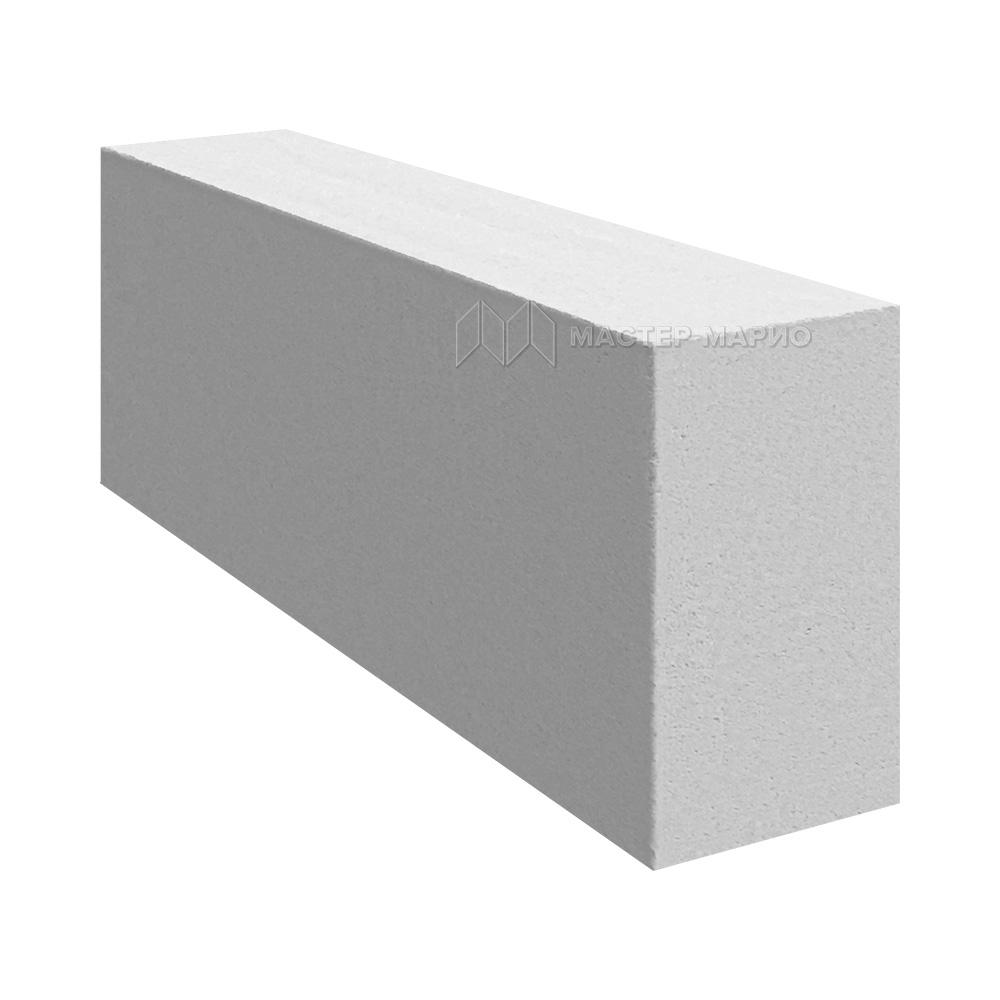
Предоставлено Издательство Bentham Science
Ссылка : Попытка снизить себестоимость материалов для производства автоклавного газобетона (20 июня 2016 г.) получено 19 августа 2021 г. с https: // физ.org / news / 2016-06-materials-autoclaved-aerated -crete-production.html
Этот документ защищен авторским правом. За исключением честных сделок с целью частного изучения или исследования, никакие
часть может быть воспроизведена без письменного разрешения. Контент предоставляется только в информационных целях.
(PDF) ПРОИЗВОДСТВО БЛОКА AAC
8 | Стр.
Цемент — Обычный портландцемент (OPC) марки 53 от производителя требуется для изготовления
блоков AAC.Цемент, поставляемый заводами, не рекомендуется из-за различий по качеству в разных партиях цемента
.
Летучая зола или песок — Летучая зола смешивается с водой с образованием суспензии летучей золы. Образовавшаяся таким образом суспензия смешивается с
другими ингредиентами, такими как порошок извести, цемент, гипс и алюминиевый порошок, в пропорциональном количестве с образованием
блоков.
Порошок известняка — Порошок известняка, необходимый для производства AAC, получают путем измельчения известняка до мелкого порошка
на заводе AAC или путем непосредственной закупки его в виде порошка на различных заводах.
Гипс — Гипс легко доступен на рынке.
Шаг 2 — Дозирование и смешивание-
После подготовки сырья следующим шагом процесса производства блоков AAC является дозирование и смешивание. Процесс
дозирования и смешивания означает качество конечных продуктов. Сохранение соотношения всех ингредиентов как —
ЛЕТУЧАЯ ЗОЛА ИЛИ ПЕСК: ИЗВЕСТЬ: ЦЕМЕНТ: ГИПС = 69: 20: 8: 3
Алюминий составляет около 0,08% от общего количества сухих материалов в смеси
Водное соотношение = 0 .60-0,65
Цикл смешивания и заливки составляет 5,5 минут. Блок дозирования и смешивания используется для формирования правильной смеси для
блоков ААС. Летучая зола перекачивается в контейнер. После того, как желаемый вес добавлен, откачка
прекращается. Аналогичным образом известковый порошок, цемент и гипс разливаются в отдельные емкости с помощью конвейеров.
После того, как необходимое количество каждого ингредиента залито в их индивидуальные контейнеры, система управления выпускает все
ингредиентов в смесительный барабан. . Меньшая конструкция чаши, используемая для подачи алюминиевого порошка, также
присоединена как часть смесительного устройства. После взбивания смеси в течение установленного времени ее можно разлить в формы
с использованием дозатора. Дозатор выпускает эту смесь в заданных количествах в формы. Дозирование и смешивание
процесс выполняется непрерывно, потому что, если есть промежуток между загрузкой и выгрузкой ингредиентов, остаточная смесь
может начать затвердевать и забить всю установку.При производстве блоков AAC вся операция дозирования и смешивания
полностью автоматизирована и требует минимального вмешательства человека.
Этап 3 — Литье, подъем и отверждение-
Когда смесь сырья готова, ее разливают в формы. Формы могут быть разных размеров в зависимости от установленной емкости
, например, размером 4,2 м x 1,2 м x 0,65 м. Перед отливкой формы покрываются тонким слоем масла
, чтобы гарантировать, что зеленый пирог не прилипает к формам. Пока суспензия смешивается и разливается в смазанные формы,
Алюминий реагирует с гидроксидом кальция и водой с выделением газообразного водорода. Это приводит к образованию крошечных
ячеек, вызывающих расширение суспензии. Такое расширение может быть в три раза больше первоначального объема. Размер пузыря составляет около 2-
5 мм, что является причиной небольшого веса и изоляционных свойств блока AAC. По окончании процесса подъема
зеленому пирогу дают осесть и затвердеть.
(PDF) Материалы, производство, свойства и применение легкого пористого бетона: Обзор
становится возможным с заменой
объема гидроцементовснижает выбросы углекислого газа.
(Awang and Noordin, 2002) [22] провели исследование для
по изучению влияния щелочно-стойкого стекловолокна на прочность
на сжатие легкого пенобетона.
Щелочестойкое стекловолокно было добавлено к пенобетонной смеси
с использованием трех различных процентных соотношений (0,2%, 0,4%, 0,6%).
Экспериментальные данные показывают, что увеличение содержания волокна на
может дать более прочный пенобетон.Результаты испытаний
на сжатие, расщепление и изгиб
прочности пенобетона, армированного стекловолокном, показывают, что
значительно увеличивается при увеличении процентного содержания стекловолокна
. (Na Ayudhya, 2011) [23] исследовали прочность на сжатие и растяжение
автоклавного газобетона
(AAC), содержащего перлитный заполнитель и полипропиленовое волокно
, подвергнутых воздействию высоких температур.К смеси добавляли
полипропиленовых (ПП) волокон с содержанием 0, 0,5, 1, 1,5 и 2%
по объему. Результаты показали
, что прочность на сжатие и расщепление без нагрева
волокна ПП, содержащего ААС, не была значительно выше на
, чем волокна без ПП. Кроме того,
наличие волокна PP не было более эффективным для остаточной прочности на сжатие
, чем прочность на разрыв
при расщеплении. (Салман и Хассан, 2010) [9] говорят, что плотность
и прочность на сжатие газобетона уменьшается с
увеличением процентного содержания алюминиевого порошка (Al). Добавление
Al также увеличивает объем газобетона.
Это было между (13,3-50,8)% и (18,7-61,3)% для отверждения на воздухе
и паром соответственно, когда Al был в пределах (0,1-
0,4)%. Результаты испытаний показали, что наилучшее процентное содержание
Al составляет 0,2% от веса цемента, что дает плотность
1389 кг / м3 и прочность на сжатие 0.26 МПа для отверждения на воздухе
и 1431 кг / м3 и 0,55 МПа для отверждения паром.
IV. ПРЕИМУЩЕСТВА И ПРИМЕНЕНИЕ ЛЕГКОГО БЕТОНА
Ячеистый бетон считается более прочным
по сравнению с традиционными изоляционными материалами, особенно
, с учетом потенциального химического / пожарного воздействия, такого как
, как на производственных объектах [24]. Легкий бетон
имеет очевидные преимущества более высокого отношения прочности к весу,
лучшей способности к деформации при растяжении, более низкого коэффициента теплового расширения
и улучшенных тепло- и звукоизоляционных характеристик
из-за наличия воздушных пустот в бетоне [25], [26].
Уменьшение собственного веса конструкции
материалов с использованием легкого бетона может привести к уменьшению на
поперечного сечения бетонных конструктивных элементов
(колонны, балки, плиты и фундамент). Также уменьшение статической нагрузки на
может снизить передаваемую нагрузку до
ифундаментов и несущей способности грунта [4], [27].
Впоследствии стальная арматура может быть минимизирована за счет
легкости.Блоки AAC могут быть уместны в
разных частях здания; его можно использовать как в ненесущих несущих стенах
, так и в несущих стенах [17]. Автоклавные газобетонные блоки
могут быть применены в строительстве
инженерных (компенсация фундамента, засыпка трубопровода
, изоляция кровли и т. Д.), Но также могут быть получены результаты применения
на объектах инфраструктуры (таких как мост
и т. Д.) засыпка водопропускных труб, уширение дороги, устранение неровностей
неровностей моста на насыпи мягкого основания [28].
V. ВЫВОДЫ
Легкий пористый бетон отличается от обычного бетона
некоторыми материалами и свойствами смеси. Газобетон
легкий бетон не содержит крупного заполнителя,
и обладает многими преимуществами, такими как низкая плотность с более высокой прочностью на
по сравнению с обычным бетоном,
с улучшенной тепло- и звукоизоляцией, уменьшенной мертвой нагрузкой
в емкости приводят к ряду преимуществ в уменьшении
элементов конструкции и уменьшении передаваемой нагрузки на фундаменты
и несущей способности.Пенобетон
отличается по агенту образования воздушных пустот по сравнению с автоклавным газобетоном
. Воздушные пустоты во вспененном бетоне
, образованные пенообразователем, эта операция является физической обработкой
. Против воздушных пустот в автоклавном газобетоне
, образованных добавлением алюминиевого порошка к другим материалам
и взаимодействием между ними, и эта операция
является химической обработкой. Воздушные пустоты — это
однородного распределения внутри легкого пенобетона
. Прочность на сжатие пенобетона
может быть увеличена до структурной прочности по сравнению с
пенобетоном из автоклавного пенобетона. Легкий пенобетон
учитывает экономию материалов и потребление побочных продуктов и отходов
, таких как зола-унос
.
ССЫЛКИ
[1] A.М. Невилл и Дж. Дж. Брукс, Concrete Technology, второе издание
, Prentice Hall, Pearson Education, 2010, стр. 351-352.
[2] Л. Б. Йен, «Исследование проникновения воды в пенобетон», M.S.
диссертация, Национальный университет Сингапура, 2006 г.
[3] З. Ли, Advanced Concrete Technology, Хобокен, Нью-Джерси:
John Wiley & Sons, 2011, стр. 219-220.
[4] Сулейман С.Х. Водопроницаемость и карбонизация вспененного бетона
, М.S. thesis, University Tun Hussein Onn Malaysia,
2011.
[5] KC Brady, GRA Watts и MR Jones, Спецификация для пенобетона
, Великобритания: Highway Agency, 2001.
[6] F. Зулкарнайн и М. Рамли, «Характеристики смеси пенобетона
с дымом кремнезема для общего жилищного строительства»,
European Journal of Technology and Advanced Engineering
Research, vol. 1, вып. 2. С. 18-28, 2011.
[7] KJ Byun, HW Song и SS Park, «Разработка конструкционного легкого пенобетона
с использованием вспененного полимера
», ICPIC-98, 1998.
[8] КАМ Гелим, «Механические и физические свойства летучей золы
пенобетон», МС диссертация, факультет гражданского строительства и инженерии окружающей среды
, Университет Тун Хусейн Онн
Малайзия (UTHM), 2011.
[9] М. М. Салман и С.А. Хассан, «Эмпирические формулы для
оценки некоторых физических свойств газобетона, полученного
путем добавления алюминиевого порошка», Journal of Engineering and
Development, vol. 14, вып. 4, 2010.
[10] Р. Боггелен. Безопасное дозирование алюминия на заводах AAC. Aircrete
Europe B. V., Oldenzaal, Нидерланды [Интернет]. В наличии:
http: // aircrete-
europe.ru/images/download/D.R.van_Boggelen_Safe_aluminium
_dosing_in_AAC_plants.pdf
[11] Э. К. Намбиар и К. Рамамурти, «Характеристики пенобетона с воздушными пустотами
», Цемент и бетон
Research, vol. 37, нет. 2, pp. 221-230, 2007.
[12] Дж. Ньюман, Б.С. Чу и П. Оуэнс, Advanced Concrete
Technology Processes, Elsevier Ltd, 2003 г., часть 2, стр. 2 / 7-2 / 9.
[13] С. Соми, «Влияние влаги на свойства автоклавного газобетона
», М.С. диссертация, Университет Восточного Средиземноморья,
Северный Кипр, 2011.
[14] Э. Р. Доминго, «Введение в автоклавный газобетон
, включая проектные требования с использованием расчета прочности», M.S. диссертация,
Государственный университет Канзаса, Манхэттен, Канзас, 2008.
156
Журнал материаловедения и инженерии Vol. 2, № 2 декабрь 2014 г.
© 2014 Инжиниринг и Технологии
Процесс производства блоков из автоклавного газобетона
Технологическая схема производства автоклавного газобетона aac…
Технологическая схема производства автоклавного газобетона ААС блочного оборудования. 1. Хранение и поставка сырья для автоклавного газобетона aac block equipment process. Сырьевая зола или песок доставляется на завод на автомобиле. Летучая зола (или песок, каменный порошок) концентрируется на складе сырья и транспортируется в бункер модным способом. Цемент в мешках или навалом …
Узнать ценуПроизводство автоклавного газобетона Masa Group
Производство изделий из газобетона в автоклаве требует высоких стандартов смешивания и дозирования заполнителей, контроля процесса ферментации и контроля каждого этапа производства.Заводы Masa по производству газобетона в автоклаве технически развиты и спроектированы в соответствии с индивидуальными требованиями наших клиентов для производства блоков из автоклавного газобетона и / или …
Узнать цену(PDF) ПРОЦЕСС ИЗГОТОВЛЕНИЯ БЛОКА AAC
В данном исследовании рассматривается процесс производства блоков из автоклавного газобетона. показывает Фигуры блоков AAC, загруженные Анурагом Ваханом. Авторский контент. Все рисунки в этом …
Узнать ценуПроцесс производства бетонных блоков / панелей — TEEYER
Схема нашего оборудования для производства блоков / панелей из автоклавного газобетона представлена на рисунке.Вы можете проверить подробную информацию о производственном процессе и задействованных машинах для производства бетонных блоков ниже. 1. Взвешивание и дозирование сырья. 2. Загрузите сырье в разливочную машину, чтобы приготовить суспензию. 3. После тщательного перемешивания суспензия выливается в форму. 4 …
Узнать ценуТехнологическая схема производства автоклавного газобетона aac …
Технологическая схема производства автоклавного газобетона ААС блочного оборудования. 1. Хранение и поставка сырья для автоклавного газобетона aac block equipment process. Сырьевая зола или песок доставляется на завод на автомобиле.Летучая зола (или песок, каменный порошок) концентрируется на складе сырья и транспортируется в бункер модным способом. Цемент в мешках или навалом …
Узнать ценуЗавод по производству автоклавного газобетона и автоклавного газобетона …
Каков процесс производства блоков AAC? Admin 07 августа, 2019; Автоклавный газобетон — это легкий, несущий, отличный изоляционный, долговечный строительный продукт, который производится в широком диапазоне размеров и прочности. Блоки AAC (автоклавные газобетонные блоки) также известны как автоклавный легкий бетон (ALC).AAC — это экологически чистый и сертифицированный продукт
Get PriceОценка жизненного цикла автоклавированной аэрированной летучей золы и …
Являясь своего рода экологически чистым строительным материалом и продуктом для комплексного использования ресурсов, автоклавная аэрированная летучая зола и бетонный блок обладают лучшими характеристиками с точки зрения сохранения тепла. Оценка жизненного цикла автоклавной аэрированной летучей золы и производства бетонных блоков: тематическое исследование, проведенное в China Environ Sci. Pollut Res Int. 2019 Сен; 26 (25): 25432-25444. DOI: 10.1007 / s11356-019-05708-8.Epub
Получить ценуАвтоклавные изделия из газобетона и производство APEX
Производство автоклавного газобетона; Блочная гидравлическая формовочная машина; Другие; ПРОДУКТЫ AAC. Автоклавный газобетон (сокращенно AAC) — это экологически чистый, энергосберегающий и сборный строительный материал, который присутствует на мировом рынке более 70 лет. Он изготовлен из природного сырья, такого как вода, хвосты кварцевого песка, известь, цемент и небольшое количество алюминия.
Узнать цену(PDF) БЛОКИ ИЗ АВТОКЛАВИРОВАННОГО БЕТОНА (AAC):
ПРОЦЕСС ПРОИЗВОДСТВА Автоклавный газобетон сильно отличается от плотного бетона (то есть «нормального бетона») как по способу производства, так и по составу конечного продукта.Автоклавный газобетон выдерживают в автоклаве — большом сосуде под давлением. При производстве газобетона автоклав обычно представляет собой стальную трубу диаметром около 3 метров и длиной 45 метров. Steam подается в …
Получить ценуБлоки из автоклавного пенобетона (блоки AAC …
Блоки из автоклавного газобетонаявляются новинкой в гражданской промышленности. Он заменяет нынешнее использование красного кирпича. Поскольку он имеет много особенностей по сравнению с традиционным красным кирпичом. Некоторые из них вы можете узнать ниже.Преимущества блоков AAC. 1- Номинальный размер блока AAC составляет 9 ″ X 8 ″ X 4 ″ -12 ″ 2- По сравнению с объемом обычного красного кирпича с кирпичами AAC. Объем 1 …
Узнать цену Характеристики блоковAAC — (Газобетон автоклавный …
Процесс изготовления блока AAC. Сначала автоклавный газобетон получают путем смешивания кремнезема, песка или летучей золы с цементом, известью, водой и расширительными добавками, такими как алюминиевый порошок. После смешивания этот бетон заливается в форму стандартного размера.(Для структурно армированных изделий из AAC стальная арматура или сетка также помещаются в форму.) Когда мы смешиваем алюминиевый порошок с …
Узнать цену(PDF) БЛОКИ ИЗ АВТОКЛАВИРОВАННОГО БЕТОНА (AAC):
Целью проекта BIO-CEM является испытание инновационной запатентованной системы аэрации бетона при масштабном доиндустриальном производстве пенобетонных блоков из автоклавного бетона. Система аэрации относится к …
Узнать ценуЗАВОД АВТОКЛАВНЫХ БЕТОННЫХ БЛОКОВ (AAC)
AAC (Автоклавный газобетон) был изобретен в середине 1920-х годов шведским архитектором и изобретателем Йоханом Акселем Эрикссоном.Автоклавы — одно из важнейших достижений 20 века в строительстве. Это легкий сборный строительный материал, который одновременно обеспечивает структуру, изоляцию, а также огнестойкость и устойчивость к плесени. Блоки AAC — это уникальный и отличный тип строительства …
Узнать ценуАвтоклавный газобетон: применение, преимущества и недостатки
Автоклавный газобетон (AAC) — это легкий сборный пенобетонный строительный материал, подходящий для производства блоков бетонной кладки (CMU), состоящих из кварцевого песка, кальцинированного гипса, извести, цемента, воды и алюминиевого порошка. полимеризуется под действием тепла и давления в автоклаве.. Ячеистый бетон увлажняют паром при атмосферных температурах, хотя и высоких …
Узнать ценуОценка жизненного цикла автоклавированной аэрированной летучей золы и …
Являясь своего рода экологически чистым строительным материалом и продуктом для комплексного использования ресурсов, автоклавная аэрированная летучая зола и бетонный блок обладают лучшими характеристиками с точки зрения сохранения тепла. Оценка жизненного цикла автоклавной аэрированной летучей золы и производства бетонных блоков: тематическое исследование, проведенное в China Environ Sci. Pollut Res Int.2019 Сен; 26 (25): 25432-25444. DOI: 10.1007 / s11356-019-05708-8. Epub
Получить ценуАвтоклавная технология газобетона APEX
13.04.2020 Процесс изготовления газобетонного автоклавного блока. 1. Хранение сырья и поставка газобетонных блоков. Сырье доставляется на завод автомобилем, а летучая зола (или песок, каменный порошок) концентрируется на складе сырья и загружается в бункер при использовании. Цемент в мешках или насыпной цемент хранится на складе цемента.При использовании он отправляется в
Get Price.Автоклавные изделия из газобетона и производство APEX
Производство автоклавного газобетона; Блочная гидравлическая формовочная машина; Другие; ПРОДУКТЫ AAC. Автоклавный газобетон (сокращенно AAC) — это экологически чистый, энергосберегающий и сборный строительный материал, который присутствует на мировом рынке более 70 лет. Он изготовлен из природного сырья, такого как вода, хвосты кварцевого песка, известь, цемент и небольшое количество алюминия.
Узнать цену(PDF) БЛОКИ ИЗ АВТОКЛАВИРОВАННОГО БЕТОНА (AAC):
ПРОЦЕСС ПРОИЗВОДСТВА Автоклавный газобетон сильно отличается от плотного бетона (то есть «нормального бетона») как по способу производства, так и по составу конечного продукта.Автоклавный газобетон выдерживают в автоклаве — большом сосуде под давлением. При производстве газобетона автоклав обычно представляет собой стальную трубу диаметром около 3 метров и длиной 45 метров. Steam подается в …
Получить цену Характеристики блоковAAC — (Газобетон автоклавный …
Процесс изготовления блока AAC. Сначала автоклавный газобетон получают путем смешивания кремнезема, песка или летучей золы с цементом, известью, водой и расширительными добавками, такими как алюминиевый порошок.После смешивания этот бетон заливается в форму стандартного размера. (Для структурно армированных изделий из AAC стальная арматура или сетка также помещаются в форму.) Когда мы смешиваем алюминиевый порошок с …
Узнать ценуАВТОКЛАВИРОВАННЫЙ ПЕЗОБЕТОН или блок AAC легкий …
производственный процесс был усовершенствован за счет добавления системы парового давления или паровой отверждения. Это отправная точка для внедрения нового строительного материала, а именно; легкий газобетон (автоклавный газобетон / AAC) легкий газобетон (автоклавный газобетон / AAC), является легким высокопрочным строительным материалом и имеет хорошие характеристики…
Узнать цену(PDF) БЛОКИ ИЗ АВТОКЛАВИРОВАННОГО БЕТОНА (AAC):
Целью проекта BIO-CEM является испытание инновационной запатентованной системы аэрации бетона при масштабном доиндустриальном производстве пенобетонных блоков из автоклавного бетона. Система аэрации относится к …
Узнать ценуБлоки из автоклавного пенобетона (блоки AAC …
Блоки из автоклавного газобетонаявляются новинкой в гражданской промышленности. Он заменяет нынешнее использование красного кирпича. Поскольку он имеет много особенностей по сравнению с традиционным красным кирпичом.Некоторые из них вы можете узнать ниже. Преимущества блоков AAC. 1- Номинальный размер блока AAC составляет 9 ″ X 8 ″ X 4 ″ -12 ″ 2- По сравнению с объемом обычного красного кирпича с кирпичами AAC. Объем 1 …
Узнать ценуРЫНКИ И История автоклавного газобетона
Газобетон Автоклавный газобетон (AAC) … Kalkbruk Skovde начал с производства блоков AAC, и продукт приобрел торговую марку Durox. В 1934 г. возник важный конкурент, который начал производство блоков AAC под торговой маркой Siporit и с 1937 г. переименован в Siporex.Siporex также была первой, кто представил в 1935 году элементы, армированные AAC, а именно крышу, пол
Узнать ценуИсследование производства газобетонных блоков в Бангладеш
Ключевые слова- Автоклавный газобетон, Алюминиевый порошок. I … агенты, используемые в производстве газобетона, методы, зависящие от химической реакции вспенивающего агента, лучше всего подходят для производства пенобетона / ячеистого бетона на производственных предприятиях и установках для предварительного литья (10). Сборный газобетон методом алюминиевой пудры (11) используется в виде блоков армированных
Узнать ценуАВТОМАТИЧЕСКАЯ ЛИНИЯ ПО ПРОИЗВОДСТВУ ПЕРИОДИЧЕСКИХ БЕТОННЫХ БЛОКОВ С ЗАПОЛНИТЕЛЬНОЙ ЗОЛОЙ.Производительность 50 м3 / смену
Технические характеристики линии
Емкость | 50 м 3 / смену (100 м 3 / сутки) |
Потребляемая мощность | 54 кВт / ч (без водяного отопления) |
Использование воды | ~ 13 тн / смену |
Утилизация цемента | ~ 12,5 тн / смену |
Утилизация летучей золы | ~ 10,5 тн / смену |
Производство | мелкие стеновые блоки по ГОСТ 21520-89 |
Требуемая площадь производственного помещения | 500-1000 м 2 |
Высота потолка в зоне смешивания | не менее 6 м * |
Высота потолка в производственной зоне | не менее 3 м * |
Температура окружающей среды | не менее +15 o С |
Требуемый персонал | 6 рабочих, 1 начальник производства / прораб |
ПРЕИМУЩЕСТВА
Автоматизация управления процессами
На производственных линиях используются электронные системы для управления загрузкой и дозированием сырья в зоне смешивания.В системах управления предусмотрены функции регистрации и контроля сырья. Зона смешивания контролируется одним оператором. В зоне раскроя есть отрезной станок, которым также управляет один оператор. Процесс демонтажа формы и укладки блоков автоматизирован.
Точность дозирования
Сырье подается на весы с тензодатчиками и весовым контроллером, который обеспечивает точное дозирование.
Высокая емкость
Высокая производительность обеспечивается автоматизированной системой загрузки и дозирования сырья, а также высокой скоростью заполнения смесителя водой и сырьем.Высокопроизводительный отрезной станок обеспечивает высокую скорость резки монолита на блоки заданного размера.
Высокое качество
Система автоматизации процессов обеспечивает высокое качество продукции и гарантирует точность дозирования, а также стабильный и однородный состав, что позволяет нам выпускать качественную и конкурентоспособную продукцию.
СЫРЬЕ ДЛЯ ПРОИЗВОДСТВА ПЕТРОБЕТОНА
- Папка. Портландцемент ПЦ-500 Д0, ПЦ-400 Д20 ГОСТ 30515 и ГОСТ 10178 применяется в качестве вяжущего для газобетонных изделий.
- Кремнеземный компонент. Зола уноса применяется для ТЭЦ с содержанием SiO2 не менее 45%, CaO не более 10%, R2O не более 3%, SO3 не более 3%.
- Вода для замешивания. Вода соответствует требованиям ГОСТ 23732.
- Смазка для форм. Смазки для форм SDF или другие антиадгезионные агенты используются для обеспечения эффективного удаления плесени.
- Армирующие вещества. В качестве армирующего агента используются полипропиленовые волокна диаметром 12 мм.
- Модификаторы. ГОСТ 24211
- Газообразующие вещества. Алюминиевый порошок или пыль на его основе используются в качестве газообразующего агента.
ОБЗОР ПРОЦЕССА
1. Производство газобетонной смеси
Смеситель для наполнения водой
Для дозирования воды используется электронный водомер.Оператор зоны смешивания вводит необходимое количество воды и запускает цикл загрузки миксера.
Загрузка сырья в смеситель
Контроллер веса используется для загрузки сырья (цемент, летучая зола) на весы и реагентов на весы химических добавок. Цемент, летучая зола и примеси транспортируются шнековыми конвейерами. Цемент и летучая зола выгружаются из весов в смеситель. Раствор перемешивают 2–3 минуты до однородности.Когда раствор будет готов, в смеситель выгружают добавки и снова перемешивают газобетонную смесь в течение 1–2 минут.
Оператор контролирует все процессы в зоне смешивания в режиме реального времени. Оператор может использовать панель управления для корректировки или изменения рецепта, времени смешивания и других параметров процесса.
Оборудование поддерживает как ручной, так и автоматический режимы.
2. Монолитный багет
По готовности газобетонную смесь выгружают до 0.85 м 3 форма через смесительный клапан. Форма заполняется за один раз. Состоит из основы и съемных сменных бортов. Перед заполнением форма смазывается и транспортируется в зону смешивания для заполнения.
3. Отверждение монолита из пенобетона
Заполненная форма транспортируется по перилам в зону отверждения (в камеру термообработки), где монолит достигает своей прочности на отрыв. Заказчику рекомендуется устраивать герметичные туннельные камеры с полной теплоизоляцией по всем поверхностям.Температура в камере должна быть +30 … +40 о С. Достижение прочности снятия изоляции может занять от 3 до 5 часов и зависит от плотности газобетона, активности, типа кремнезема, температуры и т. Д.
4. Демонтаж форм и вырезание массивов
После того, как массив наберет необходимую прочность, форма, содержащая массив, по железным дорогам переносится на демонтажную машину, основание формы фиксируется на пути. Затем четыре стенки формы снимаются и поднимаются захватом.После демонтажа формы основание формы и массив переносятся в секцию резки. Затем свободные стены накладываются на свободное основание, которое находится на прилегающей железной дороге. Форма в кожухе отправляется на участок разливки. Массив разрезают на блоки заданных размеров режущим агрегатом АРК-004. На участке резки находятся два отдельных последовательных модуля для вертикальной и горизонтальной резки массива.
Основание пресс-формы фиксируется захватом на вертикальном модуле, в то время как оператор запускает вертикальный модуль.Двигаясь по направляющим, модуль разрезает массив в вертикальной плоскости и обрезает его с обоих концов. После вертикальной резки опалубка с массивом переносится в зону горизонтального модуля, фиксируется захватом, после чего разрезается в горизонтальной плоскости на блоки заданных размеров, а также нижний слой и верх срезан. Пока горизонтальный модуль работает, следующий массив подается в зону вертикального модуля. Таким образом, одновременно производится резка двух массивов, что обеспечивает высокую пропускную способность линии.
5. Укладка блоков на поддоны, упаковка и хранение
Опалубка с вырезанным массивом переносится в блок штабелирования блоков. Основание пресс-формы закреплено на рельсе. Затем половину среза массива с помощью захвата укладывают на поддон. Для комплектации поддона вручную устанавливаются восемь блоков. Затем укладывается вторая половина массива, а также восемь блоков вручную (в зависимости от их размеров).Поддон с блоками обматывают стрейч-пленкой.
6. Блок термовлагообработки
В зависимости от климатической зоны и типа производимого материала блоки, штабелированные на поддоны, могут набирать марочную прочность на складе готовой продукции или при термовлагообработке. Для ускорения набора прочности блоков необходима термовлажная обработка блоков. При термовлагообработке блоки выдерживаются в камере от 8 до 12 часов при температуре от +40 до 60оС.Режим термовлагообработки также зависит от плотности материала, активности цемента и определяется заказчиком для каждого конкретного вида выпускаемой продукции.
7. Переработка отходов резки
Режущие модули вырезают монолит с обоих концов, вверху и внизу. Инновационным решением является использование измельчителя отходов ДГ-1 для переработки отходов резки. Позволяет измельчать отходы газобетона до частиц размером до 0–30 мм.Грунт может быть использован как сыпучий утеплитель для крыш, чердаков, пола и т. Д. Измельчитель делает производство бетона практически безотходным.
ТЕХНИЧЕСКИЕ ХАРАКТЕРИСТИКИ ЛИНИЙ
N | Имя | Количество |
Участок хранения, подготовки и отгрузки сырья | ||
1 | Шнековый транспортер цемента (L = 6 м *, мотор-редуктор (Италия), N = 4 кВт) | 1 |
2 | Шнековый транспортер летучей золы (L = 6 м *, мотор-редуктор (Италия), N = 4 кВт) | 1 |
Зона смешивания | ||
1 | Электронная система управления (со встроенным водосчетчиком + подкачивающим насосом) | 1 |
2 | Весовой дозатор (тензодатчики, пневмоклапан, макс.600 кг) | 1 |
3 | Дозатор химических добавок ДХД-1 (N = 0,5 кВт) | 1 |
4 | Смеситель для газобетона ГБ-0.85 (N = 11 кВт, V = 0,85 м3 3 ) | 1 |
5 | Компрессор C200LB40 (500 л / мин, 8–10 атм.) | 1 |
Участок резки монолита | ||
1 | Автомат раскройный АРК-004 (Н-19.5 кВт) | 1 |
2 | ФМ-0,91 м 3 опалубка для монолита из газобетона (V = 0,91 м 3 ). | 55 |
3 | Транспортная тележка | 4 |
4 | Комплекс для демонтажа форм (N = 2,0 кВт) | 1 |
5 | Комплекс для укладки блоков на поддоны (N = 2.5 кВт) | 1 |
Режущие отходы участка измельчения | ||
1 | Измельчитель ДГ-1 (N = 4,5 кВт) | 1 |
РАСХОД МАТЕРИАЛА * НА 1 м
3 ИЗ НЕАУТОКЛАВИРОВАННОГО ПЕРИОДИЧЕСКОГО БЕТОНА D-600Материал | Количество |
Цемент (ПЦ500 Д0), кг | 250 |
Летучая зола, кг | 210 |
Вода, л | 250 |
Газообразующий агент, кг | 0,5-1,5 |
Клетчатка, кг | 0,6 |
Химические добавки, кг | ** |
* Рецепты корректируются с учетом свойств сырья, выбранного заказчиком.
** Тип и количество добавок определяется на этапе проектирования бетона.
ОБЩАЯ ИНФОРМАЦИЯ
Для снижения затрат заказчика линия поставляется без силоса для цемента, бункера для песка и перил для транспортировки форм. Заказчику предоставляются чертежи раздельного изготовления этих узлов.
Кроме того, заказчик несет ответственность за подогрев воды до +35 … + 40 ° C и устройство камер пропаривания.Для работы линии в 2 смены требуются дополнительные опалубки.
Гарантийный срок на поставляемое оборудование — 12 месяцев. Компоненты каждой единицы оборудования указаны в контракте, паспорте оборудования и акте приема-передачи.
Специалисты ООО «Сибирские строительные технологии» (СКТ) разрабатывают компоновку оборудования на производственном объекте заказчика. Установка оборудования согласно схеме осуществляется заказчиком и за его счет.Заказчику предоставляется схема (чертежи) оборудования соответствующих помещений и подробная иллюстрированная инструкция по установке.
После того, как заказчик завершит установку и подключение оборудования, SCT выполняет следующие работы:
• пуско-наладка оборудования;• конструкция из газобетона;
• оптимизация технологии производства;
• обучение персонала заказчика.
Заказчик несет ответственность за соблюдение всех правил техники безопасности, требований по охране труда и окружающей среды, а также других местных нормативных актов.
Все расходы по транспортировке и размещению персонала SCT на период проведения работ берет на себя заказчик. Оптимизация технологии включает оптимизацию состава бетона на основе сырья, предоставленного заказчиком. SCT предоставляет услуги поддержки.
После ввода оборудования в эксплуатацию заказчику предоставляется техническая документация, в том числе:
• технический регламент на производства;• Диаграмма процесса;
• описание вакансии;
• правила техники безопасности;
• ГОСТы.
УСЛОВИЯ ПОСТАВКИ
Стоимость указана для EXW-Новосибирск (Россия) и не включает стоимость растаможки и отгрузки. Срок изготовления оборудования: от 30 рабочих дней с момента получения предоплаты.УСЛОВИЯ ОПЛАТЫ
Оплата 1—70% от стоимости контракта в течение 5 дней с момента подписания контракта.
Оплата 2–30% от стоимости контракта в течение 5 дней с момента получения подтверждения о готовности оборудования к отгрузке.
Анализ выбросов CO2 в течение жизненного цикла производства газобетона в Китае
[1] J.A. Се, Д.С. Хао, В. Се. Идеи и меры противодействия развитию низкоуглеродной экономики [J]. Современная экономика и менеджмент. 30 (2008) 1-8.
[2] Б.Ву. О промышленных выбросах углерода и потреблении энергии [J]. Журнал Нанкинского технологического университета (издание по общественным наукам). 9 (2010) 25-30.
[3] Z.X. Luo. Исследование метода расчета выбросов CO2 и стратегий сокращения выбросов CO2 в строительных материалах [J]. Строительная наука. 27 (2011) 1-8.
[4] ИКС.Л. Гуан, Х. Л. Ху. Автоклавный бетон на основе летучей золы и предотвращение образования обычных [J]. Журнал Цзилиньского института архитектуры и гражданского строительства (2009 г.).
[5] Ю.Ф. Лян, X.R. Чен, Х.З. Он. История развития нашей отрасли по производству газобетона и ее перспективы [J]. Угольная зола. 20 (2008) 41-44.
[6] Z.Г. Ци, Ю. Цзян. Ситуация в отрасли и тенденции развития газобетона в Китае [J]. Инновации в стеновых материалах и энергосбережение в зданиях (2008 г.).
[7] ЧАС.М. Чжоу. Оценка жизненного цикла процессов производства чугуна и стали [D]. Кандидат наук. Диссертация Пекинского технологического университета (2001 г.).
[8] Л.L. Ma. Жизненный цикл гипсокартона [D]. Магистерская диссертация Пекинского технологического университета (2012 г.).
[9] X.H. Ди, З.Р. Ни, Б. Юань и др. Инвентаризация жизненного цикла производства электроэнергии в Китае [J]. Int J LCA. 12 (2007) 217-224.
DOI: 10.1007 / s11367-007-0331-7
[10] Л.П. Ма, З.Х. Ван, X.Z. Гонг и др. Инвентаризационный анализ жизненного цикла двух типов грузового транспорта на городских дорогах [J]. Прогресс в области материаловедения и инженерии (2006).
[11] NRC (2010).Развитие науки об изменении климата. Национальный исследовательский совет. The National Academies Press [J], Вашингтон, округ Колумбия, США.
[12] Дж.Дж. Тан, Дж. У. Ян, Л. Чен. Керамзитобетонный пустотелый блок и кирпичный дом [M]. Издательство Центрального Южного Университета (2007 г.).
[13] Л.Лю. Исследование и применение модели анализа воздействия на окружающую среду для землепользования в материальном производстве [D], канд. Диссертация Пекинского технологического университета (2012).
.