Сколько весит газоблок
Сколько весят газобетонные блоки: масса и плотность
Вес газоблоков зависит от размеров, плотности и количества влаги в нем. К примеру, блок D400 (600x300x250) весит в сухом состоянии около 21 кг, а во влажном состоянии вес может доходить и до 23 кг.
Стоит отметить, что блоки большей высоты более целесообразны, так как стена возводится быстрее, количество кладочного клея уходит меньше, мостиков холода также становится меньше. Но блок высотой 30 см на 50% тяжелее, чем блок 20 см.
Частые размеры газоблоков
Газобетонные блоки чаще всего делают длиной по 60 см, а по высоте от 20 до 30 см. Но разнообразие размеров блоков очень большое. Чаще всего встречаются следующие размеры: 600х200х300 мм, 600×250х250. Такие блоки имеют удобные габариты и допустимый вес, который подходит для кладки усилиями одного человека.
Если газоблок весом 20 кг поднять и поставить можно без проблем, то блок в 40 кг, без хорошей физической подготовки уже проблематично. Так что, если вы планируете свое строительство дома в одиночку, учитывайте вес блоков, иначе сорвете спину и ваш дом будет достраивать другой мужик.
Подметим еще один факт – чем плотность газобетона ниже, тем больше влаги он может впитать.
Далее мы рассмотрим четыре таблицы, в которых показаны примерные веса газоблоков различной плотности (D300, D400, D500, D600). Также стоит отметить, что эти значения подходят именно для сухого состояния газоблоков, намокшие блоки весят на несколько килограмм больше.
Сколько весят газоблоки D300
Сколько весят газоблоки D400
Сколько весят газоблоки D500
Сколько весят газоблоки D600
Водопоглощение газобетона
В добавок к теме веса газоблоков, хотелось бы рассказать про водопоглощении блоков. Газобетон быстро впитывает влагу, но это впитывание очень ограничено. Причиной тому является величина капилярного подсоса газобетона, которая составляет около 30 мм, что довольно хорошо. Другими словами, газобетон под проливным дождем сможет набрать влаги всего 30 мм от края.
Эта информация нужна для того, чтобы правильно оценить теплопроводность газобетона в намокшем состоянии. Плоскость мокрого газобетона плохо сохраняет тепло, но намокает всего 30 мм, что для блока толщиной 300 мм составляет всего 10%. То есть, мокрый блок толщиной 30 см будет хуже сохранять тепло примерно на 10%. А потом он просохнет и будет работать в штатном режиме.
Для тестирования, часто берут газоблоки и погружают их в ведро с водой, где они перебывают несколько суток, + ко всему еще и придавливают чем-то, дабы полностью погрузить блок со всех сторон. Естественно, что маленькие блоки наберут очень много воды и промокнут почти насквозь. Но тут дело в том, что небольшие блоки не отражают реальное поглощение больших блоков. Ведь маленький блок быстрее наберет воду. На наш взгляд, это абсолютно неразумные тестирования, которые в реальных условиях эксплуатации дома не будут применены.
stroy-gazobeton. ru
Сколько весит газоблок: информация для строителей
Газобетон — отличный материал для малоэтажного строительства! Прочный дом возводится быстро и очень просто. Во многом благодаря тому, что средний газоблок значительно превосходит по габаритам стандартный кирпич!
Проектировщику необходимо знать, сколько весит газобетонный блок. Это позволит:
правильно рассчитать нагрузку на фундамент;
предусмотреть использование опорной арматуры;
выяснить общее количество газобетона, необходимого для постройки дома.
Важно! Вес конкретного блока зависит от его габаритов и плотности материала. Здесь «работает» очень простая формула. Если маркировка газобетона Д600, значит, его плотность 600 кг/ м³, то есть один кубический метр весит 600 кг.
Сколько весит газобетонный блок заданного размера
Чтобы высчитать вес одного блока, необходимо знать его марку и линейные размеры. Самый распространенный вариант для возведения зданий: газоблок 600×300×200, весит он при плотности 500 кг/м³ 18 кг. При плотности 700 кг/м³, вес увеличивается до 25 кг.
Обратите внимание! Чтобы узнать вес отдельного газоблока, необходимо перемножить его размеры (высоту, длину, ширину) и умножить на плотность. Но эта формула справедлива только для блоков прямоугольной формы.
Иногда в строительстве применяют более крупные блоки. 1 газоблок 600×400×300 весит при плотности 500 кг/м³ 36 кг. Работать с такими «кирпичиками» без привлечения специальной техники сложнее. Вес газоблока 600×300×300 той же марки — 27 кг. В таблице приведены самые распространенные виды газобетонных блоков и их основные характеристики:
Размеры газобетонного блока (ДШВ), мм | Плотность, кг/м³ | Вес одного блока, кг | Количество блоков в поддоне, шт. |
600×300×100 | 600 | 10.7 | 64 |
600×300×200 | 600 | 21,4 | 32 |
600×300×300 | 600 | 32,1 | 24 |
600×300×400 | 600 | 42. | 16 |
Это интересно! Иногда строителям удобно знать, сколько блоков умещается на поддоне. Эта цифра также плавающая, зависит от габаритов отдельного «кирпича». Поддон с газоблоками может вмещать от 16 до 64 блоков в зависимости от их размеров. Чтобы узнать эту цифру, нужно разделить 1 на объем одного блока, выраженный в кубических метрах.
Сколько весит куб газоблока
Строителей интересует и вопрос, сколько кубических метров вмещает поддон и каков вес кубометра заданной марки. 1 куб стандартных блоков 600×300×200 Д600 весит 600 кг, при этом в поддон вмещается 1,15 кубометра (то есть общий вес паллеты 685 кг). В целом, чем больше габариты одного газоблока и выше его плотность, тем больше вес одного блока и общий вес «упаковки».
Важно! Чтобы узнать вес одного газоблока, не обязательно прибегать к сложным формулам. Все параметры подсчитаны и занесены в специальные таблицы. В них есть информация по:
количеству блоков в поддоне,
габаритам одного блока,
весу,
морозостойкости,
теплопроводности,
индексу шумоизоляции и т.
д.
Получить полную информацию о выбранной марке не составит труда! Сегодня таким материалом, как газобетон, заинтересовались в различных странах. У нас делают заказы подрядчики и частные лица из Казахстана, Узбекистана, Киргизии, различных регионов России. Если Вы захотите изготавливать газоблок самостоятельно, Вам может пригодиться линия по производству газобетонных блоков, которые поставляет «под ключ» завод «АлтайСтройМаш». Ознакомиться с полным спектром выпускаемой продукции можно на нашем сайте!
asm.ru
Вес газосиликатного (газобетонного) блока: как рассчитать сколько весит 1 штука и 1 м3 материала
Газоблоки относят к легким каменным материалам, по сравнению с монолитным бетоном и кирпичом, при помощи которых возводят стены дома. Основные компоненты — цемент, песок и известь. Один из важных параметров такого материала – его масса. Прежде всего вес газобетонного блока нужно знать для расчета фундамента дома.
От чего зависит масса
На вес газоблока влияют два параметра:
Плотность
Значение плотности отображено на маркировке материала и указано в единицах измерения кг/м3.
Марка газобетона | Плотность (кг/м3) | Вес 1 м3 газобетона (кг) |
D300 | 300 | 300 |
D400 | 400 | 400 |
D500 | 500 | 500 |
D600 | 600 | 600 |
Из таблицы следует, что 1 куб газобетона марки D400 весит 400 кг, 1 куб марки D500 весит 500 кг.
Влажность
Что касается влажности, то этот показатель влияет на массу аналогичным образом. Чем больше процент влаги, тем большей будет масса материала.
По технологии производства автоклавные газобетоны подвергаются длительной выдержке в среде насыщенного пара под высоким давлением. Изделия, выходящие с конвейера, содержат 25-30% влаги. Отпускная влажность газобетона составляет 25-30%, что увеличивает вес блоков в 1,25-1,3 раза по сравнению с высохшим материалом.Однако, в течение 3-х лет, если строительство произведено с учетом требований по защите ограждающих конструкций от переувлажнения, материал высыхает и приобретает эксплуатационную равновесную влажность меньше 5%. Причем бóльшая часть влаги уходит в первый год эксплуатации. [adinserter block=»3″]
Расчет массы
Сколько весит блок
Чтобы провести расчеты, необходимо изначально знать габариты материала и плотность.
Расчеты проводят по формуле m=V*p. Обозначения следующие: m – вес блока (кг), V – объем(м3), р – плотность (кг/м3). Для того чтобы узнать объем, нужно перемножить все значения.В качестве примера посчитаем вес газосиликатного блока 600х300х200 мм и плотностью D500.
- Размер: 200х300х600 мм
- Плотность: 500 кг/м3.
Решение:
- Зная размеры, можно высчитать объем. Для указанного изделия он будет составлять: V = 200 мм * 300 мм * 600 мм = 36000000 мм3 = 0,036 м3
- Далее, отталкиваясь от марки, на которой указана плотность, определяется вес блока: m = 0,036 м3 * 500 кг/м3 = 18 кг
Ответ: Вес газобетонного блока 200х300х600 без учета влажности составляет 18 кг.
Закрепим знания и произведем расчет для популярного стенового блока 250х400х600 мм и плотностью D400.
- Размер: 250х400х600 мм
- Плотность: 400 кг/м3.
Решение:
- V = 250 мм * 400 мм * 600 мм = 60000000 мм3 = 0,06 м3
- m = 0,06 м3 * 400 кг/м3 = 24 кг
Ответ: Масса 250х400х600 без учета влажности составляет 24 кг.
Если расчет производится с целью определения нагрузки стен дома на фундамент, то влажность не играет большое значение в определении массы в данном случае. Так как параметр влажности в эксплуатируемых стенах не поднимается выше 5% при любых погодных условиях.
На начальном этапе строительства фундамент будет нагружаться стенами, нагрузка от которых больше расчетной за счет отпускной влажности. Но к моменту установки окон, возведения крыши, внутренней и внешней отделки, установки оборудования и мебели стеновой материал отдаст в окружающую среду значительную часть влаги и примет расчетную массу. Именно поэтому не стоит учитывать влажность при расчете нагрузок.
Некоторые самозастройщики возводят стены из газобетона в одиночку. И не по наслышке проверяют на себе массу блока лишь при кладке первого ряда. В этом случае им стоит понимать, что свежие заводские блоки за счет содержащейся в них влажности будут тяжелее рассчитанных выше значений примерно на 25%. Если толщина стен по проекту составляет 500 мм, то один человек будет не в состоянии поднимать такие тяжелые изделия. Ему придется либо взять помощника, либо купить более легкий материал толщиной 200 мм и 300 мм (и выложить из него двойную стену вразбежку).
Строителю на заметку
Помимо стандартных блоков с прямолинейными гранями некоторые современные заводы выпускают блоки с захватами для рук с обеих сторон.
Такой материал удобно поднимать и переносить.
При этом расход клея не увеличивается, так как по технологии монтажа пустоты заполнять не нужно.
Так, в нашем первом примере свежий заводской блок, только сошедший с конвейера, будет тяжелее расчетных значений на 30%. Его вес для нашего первого примера составит:m = 18 кг * 1,30 = 23,4 кгДля второго примера предлагаю произвести этот несложный расчет самостоятельно и прикинуть свои возможности по подъему таких блоков на стены в одиночку. [adinserter block=»4″]
Вес поддона с блоками
Эта характеристика пригодится при планировании доставки материала на объект. У каждого грузового автомобиля есть предельные значения грузоподъёмности и объема перевозимых грузов.
Допустим, визуально вам покажется, что в грузовой автомобиль войдет 10 поддонов. Но водитель, узнав массу поддона, скажет, что сможет взять только 8 поддонов. И он будет прав, так как грузоподъемность транспортного средства не должна превышаться.
Определить массу паллеты с газобетоном просто. Зная количество единиц материала в паллете и вес одного газоблока, перемножьте эти значения.
Кстати, многие продавцы отпускают материал со склада целыми поддонами. И в прайс-листе указывают плотность и объём поддона. Мы уже знаем, что плотность блоков соответствует массе одного кубометра. Соответственно, перемножив плотность на объём получим искомый вес паллеты.
Например, как видно из предложенного прайс-листа, объём поддона с блоками 600х200х300 мм составляет 1,8 м3. Рассчитаем массу поддона для плотности D400.m = V*p = 1,8 м3 * 400 кг/м3 = 720 кгЕсли мы везем газобетон с завода, то сделаем поправку на влажность: 720 кг * 1,25 = 900 кг.
Сколько весит куб газобетона и определение реальной плотности
В начале статьи самой первой таблице приведены эти значения без всякого расчета. Вес кубометра газосиликатного материала соответствует плотности, указанной в маркировке (D400, D500 и т.д.).
Однако, ситуации бывают разные. Возможно, вы захотите проверить соответствие заводского газосиликата заявленным характеристикам. Или вам не хватило поддона блоков, а у соседа остались излишки. При этом ваш сосед не помнит характеристики своего газобетона.
Узнав реальную массу мы можем посчитать реальную плотность.В этом случае нам понадобится взвесить 1 блок и произвести расчет по обратной формуле p=m/V. Где:
- m – вес (кг) — нужно найти весы и взвесить 1 блок;
- V – объем(м3) — его мы считали выше;
- р – плотность (кг/м3).
Не забывайте брать поправки на влажность.
Расчет количества материала в 1м3
Расчет проводят в два действия:
- Изначально у продавца узнают геометрические размеры конкретного стенового материала и вычисляется его объем. Такой параметр для блока 200х300х600 мы уже считали, исходя из предыдущего примера он равен 0,036 м3.
- Далее нужно разделить общий объем (в нашем случае 1 м3) на объем данного блока. В итоге получается 27,778 штук.
Эту характеристику обычно указывают в прайс-листе.
В проектной документации на строительство дома в калькуляции указывается объём необходимого материала, который получают перемножением площади стен с учетом проемов под окна и двери на толщину стен.
Произведя расчет количества материала в кубическом метре, и умножив его на общий объём, мы можем узнать необходимое количество блоков для постройки нашего дома. Кстати, следует помнить при расчете, что над окнами выполняются перемычки. И эти участки в расчет не брать. Но позаботиться о выборе и покупке материала для перемычек.
Размеры и вес
Подводя итоги и учитывая зависимость массы от плотности материала, можно привести следующие параметры веса для каждой марки. Данные представлены одним из производителей.
В заключении напомню, что при выборе марки и размера, нужно учитывать длину, ширину и высоту стен, а также их функциональное назначение.
Полезное видео
Как поднять тяжелый газосиликатный блок на второй этаж, проявив смекалку.
izbloka.com
ДСК ГРАС
В большом многообразии современных строительных материалов особого внимания заслуживают блоки из газобетона. В последние годы они пользуются большой популярностью при возведении жилых и нежилых зданий, и тому есть причины.
Газобетонные блоки имеют сравнительно большие размеры. При взгляде на них может показаться, что и весят они тоже немало, но это не так: масса этих блоков сравнительно невелика. Это, в свою очередь, упрощает и ускоряет строительство.
Заслуживает внимания точность геометрии блочных изделий из газобетона. Их поверхности почти идеально ровные, что также облегчает использование этого стройматериала при возведении зданий разного назначения.
Газобетонные блоки — экологически чистый материал. При их изготовлении на заводе ДСК ГРАС используются только компоненты натурального происхождения. Блочные изделия не выделяют в воздух вредных веществ — а значит, безопасны как для владельцев возведённого из них жилья, так и для окружающей среды.
Ознакомиться с характеристиками газобетона и сравнить его с другими стройматериалами можно с помощью таблицы, приведённой ниже.
Наименование | Газобетон автоклавный | Кирпич полнотелый | Пенобетон |
Плотность, кг/куб. м | 300-700 | 1550-1700 | 500-1200 |
Вес 1 кв. | 300-700 | 1800 | 300-900 |
Водопоглощение, в % к общей массе | 20 | 12 | 18 |
Морозостойкость, циклы | 15-100 | 20-25 | 15-50 |
Паропроницаемость, мг/(кв. м*ч*Па) | 0,14 | 0,11 | 0,11 |
Прочность на сжатие, МПа | 1,5-10 | 2,5-25 | 1,5-17 |
Теплопроводность, Вт/кв. м. | 0,07-0,14 | 0,6-0,95 | 0,12-0,38 |
Акустические характеристики для стены толщиной 30 см, Дб | 30-47 | 55-64 | 45-58 |
Достоинства газобетона автоклавного твердения
Стеновые блоки из газобетона, выпускаемые на заводе ДСК ГРАС, имеют следующие достоинства, в числе которых:
- идеальная геометрия;
- высокие шумоизоляционные свойства;
- малый удельный вес;
- лёгкость обработки — пиления, нарезки, сверления, штробления, выполнения других операций;
- простота монтажа;
- экологичность;
- морозостойкость;
- возможность использования клеевых смесей для соединения блоков — а значит, минимальная ширина образующихся швов;
- высокая огнестойкость.
Газобетон — это стройматериал категории НГ (несгораемый), его теплопроводность в соответствии с ГОСТ 30244 и ГОСТ 31359 минимальна. При нагревании от пламени газобетон теряет свою прочность очень медленно;
- наконец, ценовая доступность.
Связь между размерами и массой: Блоки и перегородки
Номенклатура и количество блоков на стандартном поддоне (размер 1,0*1,5 м, высота 1,35 объём блоков 1,8м3). | |||||||||||||
Размеры, мм | Вес 1 блока, кг | Кол-во блоков на поддоне | Вес 1 поддона, кг | ||||||||||
длина | высота | ширина | D300 | D350 | D400 | D500 | D600 | шт | D300 | D350 | D400 | D500 | D600 |
600 | 200 | 100 | 4,97 | 6,00 | 6,57 | 8,20 | 9,80 | 150 | 745 | 900 | 985 | 1230 | 1470 |
250 | 12,42 | 15,00 | 16,4 | 20,50 | 24,50 | 60 | |||||||
300 | 14,90 | 18,00 | 19,7 | 24,60 | 29,40 | 50 | |||||||
375 | 18,63 | 22,50 | 24,6 | 30,75 | 36,75 | 40 | |||||||
250 | 75 | 4,66 | 5,63 | 6,16 | 7,69 | 9,19 | 160 | ||||||
100 | 6,21 | 7,50 | 8,21 | 10,25 | 12,25 | 120 | |||||||
150 | 9,31 | 11,25 | 12,31 | 15,38 | 18,38 | 80 | |||||||
250 | 15,52 | 18,75 | 20,52 | 25,63 | 30,63 | 48 | |||||||
300 | 18,63 | 22,50 | 24,63 | 30,75 | 36,75 | 40 | |||||||
375 | 23,28 | 28,13 | 30,78 | 38,44 | 45,94 | 32 | |||||||
Номенклатура и количество блоков на увеличенном поддоне (размер 1,2*1,5 м, объём блоков 2,16 м3). | |||||||||||||
Размеры, мм | Вес 1 блока, кг | Кол-во блоков на поддоне | Вес 1 поддона, кг | ||||||||||
длина | высота | ширина | D300 | D350 | D400 | D500 | D600 | шт | D300 | D350 | D400 | D500 | D600 |
600 | 300 | 100 | 7,42 | 8,63 | 9,83 | 12,25 | 14,67 | 120 | 890 | 1035 | 1180 | 1470 | 1760 |
200 | 300 | 14,90 | 18,00 | 19,70 | 24,60 | 29,40 | 60 | ||||||
300 | 250 | 18,63 | 22,50 | 24,63 | 30,75 | 36,75 | 48 | ||||||
250 | 400 | 24,72 | 28,75 | 32,78 | 40,83 | 48,89 | 36 |
Связь между размерами и массой: Армированные изделия
Номенклатура и количество перемычек | |||||
Размер перемычек | Размер поддона | Количество перемычек | Объём | Вес упаковки (факт) | Вес 1 шт |
1500. | 1500.750 | 20 | 1,125 | 800 | 40 |
2000.150.250 | 2000.750 | 20 | 1,5 | 1100 | 55 |
2500.150.250 | 2500.750 | 20 | 1,875 | 1400 | 70 |
1500.100.250 | 1500.700 | 28 | 1,05 | 750 | 27 |
2000.100.250 | 2000.700 | 28 | 1,47 | 1100 | 39 |
2500.100.250 | 2500.700 | 28 | 1,75 | 1300 | 46 |
1500.200.250 | 1500.800 | 16 | 1,2 | 900 | 56 |
2000. | 2000.800 | 16 | 1,6 | 1200 | 75 |
2500.100.250 | 2500.800 | 16 | 2 | 1500 | 94 |
Связь между размерами и массой: П-образные блоки
Номенклатура и количество П-образных перемычек | |||||
Размер перемычек | Размер поддона | Количество перемычек | Объём упаковки | Вес упаковки (факт) | Вес 1 шт |
500.300.250 | 1500.1000 | 40 | 1,5 | 400 | 10 |
500.375.250 | 1500.1000 | 32 | 1,5 | 420 | 13 |
500.400.250 | 1500. | 36 | 1,8 | 550 | 15 |
Ключевые характеристики
Прочность блоков из газобетона, выпускаемых ДСК ГРАС, зависит от плотности этого материала. Сравнительно небольшую плотность имеют разновидности с маркировкой D300, которая указывает на то, что плотность составляет 300 кг на 1 м3.
Обладает самой малой прочностью среди ячеистых бетонов (В2.0). Такой материал чаще всего применяется для возведения несущих конструкций до полутора этажей, закладки проемов внутри здания, а также, теплоизоляции помещений. Газобетонные блочные изделия D500 прочнее, поэтому их можно использовать для сооружения несущих конструкций до пяти этажей.
Наибольшую прочность имеют блоки марки D600 В5.0. Их можно использовать для возведения высоких строений.
Ещё одна важная характеристика предлагаемого стройматериала — его устойчивость к морозу. На заводе ДСК ГРАС выпускаются разновидности с морозостойкостью от F75 до F100. Чем холоднее климат региона, в котором ведётся строительство, тем более морозостойкий материал понадобится.
Покупать стройматериалы у нас легко и удобно
В нашей компании вы сможете купить качественные строительные материалы на основе газобетона с минимальными затратами времени и сил. Обратитесь к нашим консультантам и расскажите им о ваших потребностях. Специалисты порекомендуют оптимальные марки материала, выполнят расчёт необходимого объёма, ответят на возникающие вопросы и помогут оформить оптовый или розничный заказ.
Copyright © 2019 Холдинг ГРАС. Все права защищены.Продажа газобетона, строительных блоков и смесей в Москве, Ставрополе, Ставропольском крае и Саратове.
ООО «ДСК ГРАС-Саратов» ОГРН: 1076432002624Юридический адрес: 410511, Саратовская область, Саратовский район, с. Александровка, ул. Заводская № 1
Войти
Впервые на нашем сайте?Зарегистрируйтесь – это недолго!www.dskgras.ru
Удельный и объемный вес газобетона в 1м3.
Газобетон – строительный материал, изготовленный из цемента с добавлением песка и извести. При изготовлении используются только чистые экологические материалы, которые не содержат вредных веществ. Из-за особых технологий производства обладает отличительными характеристиками, такими как устойчивость к огню, ржавчине, гнили, морозу и воде.
Марка газобетона | Вес 1 м3 газобетона (кг) | Популярные размеры блоков |
D300 | 300 | 200х200х600 250х200х600 280х200х600 300х200х600 360х200х600 400х200х600 500х200х600 75х200х600 100х200х600 120х200х600 150х200х600 |
D400 | 400 | |
D500 | 500 | |
D600 | 600 | |
D700 | 700 | |
D800 | 800 | |
D1000 | 1000 | |
D1100 | 1100 | |
D1200 | 1200 |
При строительстве в первую очередь рассчитывается сколько весит газобетон (вес куба газобетона) так как на основании данной характеристики определяется спецификой его использования и применения. Существуют два понятия для расчета веса – объёмный вес газобетона и удельный вес газобетона. Объёмный – полный вес материала, удельный – вес без учета газовых вкраплений и воздуха.
Смотри так же статьи : удельный вес керамзита и удельный вес газосиликатных блоков
Для вычисления необходимо узнать сколько блоков находятся в кубе газобетона. Делается это очень легко исходя из математической формулы кубического метра. Кубический метр – это перемноженные высота, ширина и длина между собой. Давайте рассмотрим на примере газоблока с такими параметрами: высота – 250 мм, ширина – 400 мм, длина – 625 мм. Переведем эти параметры в метры, соответственно получаем 0,25; 0,4 и 0,625 м. Теперь для вычисления кубического метра одного блока перемножим параметры и получим 0,0625 м3. Зная этот параметр мы легко можем вычислить количество блоков, для этого разделим единицу на кубический метр одного блока. Сделав это получаем 16 – то есть в одном кубе именно такое количество блоков.
Определяем удельный вес газобетона по марке, плотности и размеру газоблока.
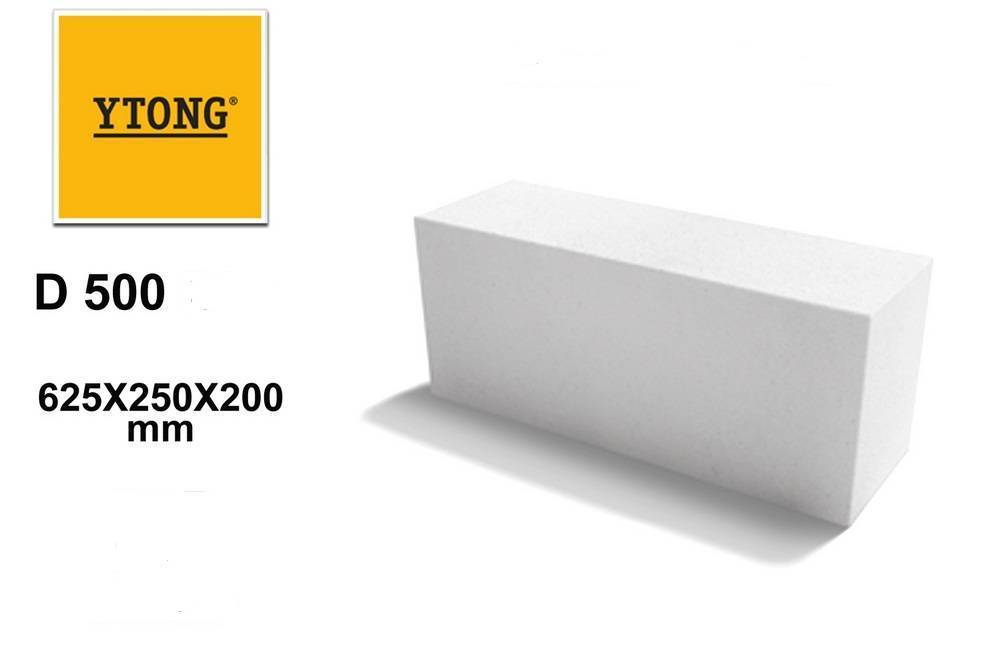
Итак, для вычисления веса куба газобетона необходимо перемножить объём блока (который вычислялся выше), плотность блока на количество блоков. Плотность указывается маркой материала. Так, блок с маркой D500 имеет плотность в 500 кг/м3, а D900 соответственно 900 кг/м3.
Возвращаясь к нашему примеру, вычислим вес одного блока, для примера возьмём плотность с маркой D500 – умножаем 500х0.0625 и получаем вес блока газобетона, который равен 31,25 кг. Теперь умножаем на количество блоков 31,25х16, получаем вес 1м3 газобетона 500 кг.
naruservice.com
Сколько весит один газоблок?
Сегодня многие строительные организации в качестве основного материала для возведения стен используют элементы из ячеистого бетона. Прочность и легкость, простота обработки и низкая стоимость обуславливают популярность газоблоков как у крупных застройщиков, так и среди начинающих строителей.
Оглавление:
- Особенности изготовления
- Основные преимущества
- Маркировка и классификация
Производство газобетонных изделий
Смешанные в определенных пропорциях цемент, кварцевый песок и вода вспениваются химической реакцией извести и алюминия (пылеобразного или в виде пасты, суспензии). Выделившийся водород образует во всей массе замкнутые сферические поры, увеличивающие в 5 раз объем исходного сырья. После предварительного схватывания монолитное цементное тесто нарезается струнами на необходимые размеры. Прочность деталей получают двумя способами:
- В автоклаве: при температуре 190°C прессуются под давлением в несколько атмосфер.
- В сушильных камерах с электроподогревом.
Чтобы правильно рассчитать прочность фундамента, важно знать массу постройки. Производители указывают вес 1 изделия в сухом состоянии или при определенном % влажности (максимально допустимый показатель 40 %). Например, перегородки D600 (600х300х100) в зависимости от сухости весят 9-13 кг, а стеновые элементы с размерами 600х400х250 или 600х300х250 – 17-30 кг. D500 с габаритами 600х300х200 при максимальной влажности имеет массу 25 кг, а D400 – 21,5 кг. Вес газоблока любого размера определяется путем умножения его объема на плотность.
Чтобы быстро и дешево построить теплый дом, необходимо купить хорошие материалы. Следует внимательно изучить все предложения рынка, ознакомиться с заявленными качествами, определиться с необходимыми параметрами и сопоставить цену аналогичных элементов у разных изготовителей.
Преимущества газоблоков
К основным достоинствам относят:
1. прочность: допускается строительство зданий до 5 этажей;
2. эксплуатационный срок около 100 лет: при условии соблюдения норм;
3. морозоустойчивость: вода при замерзании расширяется в порах материала, не повреждая его структуру;
4. малый вес: образование пор уменьшает массу в 3-5 раз;
5. геометрически точные размеры: нарезание слегка затвердевшего цементного раствора позволяет изготавливать детали с погрешностью не более 1 мм;
6. простота обработки: из газоблоков выкладываются идеально ровные стены и перегородки; их пористая структура легко фрезеруется, пилится, штробится, сверлится;
7. шумоизоляция: мягкая поверхность пористой поверхности отлично поглощает и рассеивает звуковые волны;
8. не горит: выдерживает температуру до +400°C;
9. паропроницаемость: «дышащие» пористые стены не гниют и не плесневеют;
10. теплоизоляция и энергоэффективность: низкая теплопроводность газобетона обуславливает сбережение энергии на обогрев или охлаждение помещений;
11. экономичность: низкая стоимость, легкие стеновые конструкции не требуют установки дорогостоящего капитального фундамента, экономятся средства на транспортировке, погрузо-разгрузочных, монтажных и ремонтных работах, а также на материалах для тепло- и звукоизоляции.
Недостатком является низкая прочность на изгиб и растяжение. При строительстве многоэтажных зданий рекомендуется армирование.
Маркировка и назначение блоков из ячеистого бетона
Марка, обозначаемая D300-1200, указывает на плотность материала, то есть какое количество бетонной смеси вспенивается при получении 1 м3 пористой структуры. Например, сырье для производства D400 весит 400 кг, а для D900 – 900. В D400 воздушных пузырей больше, чем в марках 500 и выше. Следовательно, вес такого блока меньше, плотность, прочность и теплопроводность – ниже.
По назначению делятся на 3 типа:
- Конструкционные. D1000-1200, объем пор – 40-55 %. Применяются для монтажа несущих стен, так как самые прочные и плотные.
- Конструкционно-теплоизоляционные. D500-900, пористость – 55-75 %. Рекомендуются для возведения несущих стен одноэтажных зданий, перегородок и утепления.
- Теплоизоляционные. D300-400, содержание воздушных капсул – выше 75 %. Хрупкие, менее прочные, но более теплые применяются для утепления, закладки проемов, строительства гаражей, бань, сараев для домашнего скота и птицы.
Для частного дома оптимально покупать стройматериалы марки D500-D600. Стоимость одинаковых по размеру деталей с разной плотностью несущественна.
stroitel-lab.ru
Сколько весят газобетонные блоки?
На сегодняшний день газосиликатный блок используется для строительства домов гораздо чаще, чем другие кладочные материалы. Он обладает высокой прочностью, при этом подходит для возведения одноэтажного дома или многоэтажного сооружения за счет малого веса и простоты в обработке.
Оглавление:
- Масса газобетона
- Пример расчета
- Стоимость
Вес блоков разных размеров
Основными факторами, влияющими на массу, являются габариты и плотность. Газосиликат относится к легким ячеистым бетонам, поэтому его плотность намного меньше, чем полнотелого кирпича или шлакоблока. Вес газосиликата варьируется от 500 до 1800 кг на 1 м3. Газообразователь в составе смеси обеспечивает ей пористость: чем интенсивнее его воздействие, тем больше получится воздушных пустот в готовой продукции.
Чтобы провести расчеты по необходимому количеству стройматериала и узнать, сколько весит один газоблок, нужно знать маркировку. Плотность обозначается буквой «D» и измеряется в кг/м3. Марки указаны в ГОСТе, если производитель точно следует технологии, то результаты расчетов будут наиболее достоверными.
В D300-D1200 цифра указывает на количество смеси, которая используется для производства и вспенивания для получения 1 м3 ячеистой структуры. К примеру, D500 будет весить 500 кг, а D800 – 800 кг. Чем выше показатель, тем меньше воздушных образований в теле газобетона. Таким образом, характеристики прочности, теплоизоляции и массы будут больше.
По назначению газосиликатные блоки делятся на:
- Теплоизоляционные – D300-D400. Содержание воздуха составляет около 75% от всего объема. Они наиболее легкие, но при этом достаточно хрупкие. Используются для возведения перегородок, стен небольших построек, а также теплоизоляционного контура. Обрабатывать ударными инструментами крайне нежелательно.
- Конструкционно-теплоизоляционные – D500-D900. Пористость равняется 55-70 %. Для строительства несущих и самонесущих стен одноэтажного дома, перегородок.
- Конструкционные – D1000-D1200. Количество пор – до 50 %. Наиболее прочные и надежные, поэтому подходят для несущих стен двух- или трехэтажного здания.
При обработке способны выдержать сверление (о том, чем сделать отверстия в бетоне, читайте тут), штробление перфоратором, распил.
Практичным вариантом для жилого дома в 1 этаж будет марка D500-D600. Габариты также влияют на массу, поэтому блоки размером 600х300х200 мм будут весить больше, чем 300х100х100 при условии одинаковой плотности.
Типовой расчет массы газобетона
Определение веса проводится на примере блока 600х250х400 мм. Формула для вычисления имеет следующий вид: плотность (кг/м3) х объем (м3) = масса (кг).
- Определяется объем. Для этого размеры переводятся в метры и перемножаются между собой: 400х250х600 = 0,4х0,25х0,6 = 0,06 м.
- Далее смотрится плотность. В качестве примера используется марка D600. В этом случае 1 м3 будет весить 600 кг.
- Проводится расчет по формуле: 0,06х600=36 кг – столько будет весить один элемент.
Такой метод можно применять для любых размеров газоблоков разной плотности. Однако важно учитывать нагрузку, которая будет воздействовать на фундамент.
Стоимость газосиликата в Москве
Производитель | Марка | Размеры, мм | Цена за 1 м3, рубли |
Bonolit | D500 | 200x400x600 | 2800 |
D600 | 500x250x625 | 2750 | |
ЭКО | D600 | 350x250x600 | 2700 |
D600 | 150x250x600 | 2600 | |
E3CM | D400 | 100x250x625 | 2650 |
D500 | 50x250x625 | 2680 | |
D600 | 500x250x625 | 2700 |
cemgid.ru
Вес блока газосиликатного 625х400х250 — Строй журнал lesa-sevastopol.ru
Сколько весят газобетонные блоки: масса и плотность
Вес газоблоков зависит от размеров, плотности и количества влаги в нем. К примеру, блок D400 (600x300x250) весит в сухом состоянии около 21 кг, а во влажном состоянии вес может доходить и до 23 кг.
Стоит отметить, что блоки большей высоты более целесообразны, так как стена возводится быстрее, количество кладочного клея уходит меньше, мостиков холода также становится меньше. Но блок высотой 30 см на 50% тяжелее, чем блок 20 см.
Частые размеры газоблоков
Газобетонные блоки чаще всего делают длиной по 60 см, а по высоте от 20 до 30 см. Но разнообразие размеров блоков очень большое. Чаще всего встречаются следующие размеры: 600х200х300 мм, 600×250х250. Такие блоки имеют удобные габариты и допустимый вес, который подходит для кладки усилиями одного человека.
Если газоблок весом 20 кг поднять и поставить можно без проблем, то блок в 40 кг, без хорошей физической подготовки уже проблематично. Так что, если вы планируете свое строительство дома в одиночку, учитывайте вес блоков, иначе сорвете спину и ваш дом будет достраивать другой мужик.
Подметим еще один факт – чем плотность газобетона ниже, тем больше влаги он может впитать.
Далее мы рассмотрим четыре таблицы, в которых показаны примерные веса газоблоков различной плотности (D300, D400, D500, D600). Также стоит отметить, что эти значения подходят именно для сухого состояния газоблоков, намокшие блоки весят на несколько килограмм больше.
Сколько весят газоблоки D300
Сколько весят газоблоки D400
Сколько весят газоблоки D500
Сколько весят газоблоки D600
Водопоглощение газобетона
В добавок к теме веса газоблоков, хотелось бы рассказать про водопоглощении блоков. Газобетон быстро впитывает влагу, но это впитывание очень ограничено. Причиной тому является величина капилярного подсоса газобетона, которая составляет около 30 мм, что довольно хорошо. Другими словами, газобетон под проливным дождем сможет набрать влаги всего 30 мм от края.
Эта информация нужна для того, чтобы правильно оценить теплопроводность газобетона в намокшем состоянии. Плоскость мокрого газобетона плохо сохраняет тепло, но намокает всего 30 мм, что для блока толщиной 300 мм составляет всего 10%. То есть, мокрый блок толщиной 30 см будет хуже сохранять тепло примерно на 10%. А потом он просохнет и будет работать в штатном режиме.
Для тестирования, часто берут газоблоки и погружают их в ведро с водой, где они перебывают несколько суток, + ко всему еще и придавливают чем-то, дабы полностью погрузить блок со всех сторон. Естественно, что маленькие блоки наберут очень много воды и промокнут почти насквозь. Но тут дело в том, что небольшие блоки не отражают реальное поглощение больших блоков. Ведь маленький блок быстрее наберет воду. На наш взгляд, это абсолютно неразумные тестирования, которые в реальных условиях эксплуатации дома не будут применены.
ПОХОЖИЕ СТАТЬИ:
Изготовление армопояса для газобетона
Чем отличается газобетон от пенобетона
Сравнение кирпича и газобетона
Гидроизоляция фундамента под газоблоки
Какой марки выбрать газобетон?
Какие инструменты нужны для работы с газобетоном?
Разновидности крепежей для газобетона
Сколько стоит построить газобетонный дом?
Выбираем и сравниваем клей для кладки блоков
Блок газосиликатный Д600 625х250х400 Бонолит-Калуга
В ноябре 2009 года заработал первый завод ООО «Грас» в Калужской области, в городе Малоярославец, производственная мощность которого составит до 500 000 кубометров продукции в год.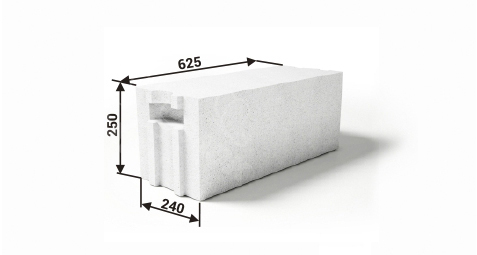
Предприятие успешно работает на российском строительном рынке, обеспечивая производство и поставку высококачественных строительных материалов, пользующихся повышенным спросом при современном строительстве: стеновые блоки из ячеистого бетона (газосиликатные блоки), перемычки, плиты перекрытия, плиты покрытия.
Технические данные по отгрузкам с завода ГРАС-Калуга г. Малоярославец
Объем
блока м 3
Вес блока
кг.
Кол-во блоков на
под. D400, D500
Высота
поддона ( м)
Кол-во блоков на
поддоне D600
Высота
поддона ( м)
Самовывоз со склада в Москве
Если необходима небольшая партия товара (от 1 штуки), и товар есть на складе, вы можете в кратчайшие сроки приобрести товар в одной из розничных точек:
Доставка на объект и разгрузка
Мы доставим любое необходимое количество товара в удобное для вас время непосредственно на объект строительства. Стоимость доставки зависит от объема заказа и удаленности объекта от завода-производителя или склада. Норма разгрузки малотоннажного транспорта составляет 30 минут, средне- и крупнотоннажного – до 1 часа.
Компания Кирпич.ру располагает собственным автотранспортом и может предложить клиентам самые выгодные и удобные условия по доставке товара на машинах различной грузоподъемности (от 9 до 20 т), в том числе оборудованных краном-манипулятором. Для расчета стоимости и сроков доставки обращайтесь к менеджерам по телефону +7 495 369-33-88 с 9 до 21.
Подробнее с условиями доставки вы можете ознакомиться на странице Доставка.
Вы можете оплатить заказ любым удобным для Вас способом:
Оплатить товар наличными вы можете в офисах, шоу-румах и на складских комплексах компании Кирпич.РУ, а также курьеру или водителю при получении товара на объекте.
Оплата по безналичному расчету
Договор-счет действителен в течение 2 (двух) банковских дней.
Для оплаты по безналичному расчету достаточно согласовать с менеджером сроки поставки товара и получить договор-счет.
Оплата банковской картой возможна в офисах компании, а также курьеру при получении.
Подробнее с условиями оплаты и гарантии вы можете ознакомиться на странице Оплата и гарантии.
Как рассчитать вес газосиликатного блока в зависимости от размера и плотности материала
Газоблоки относят к легким каменным материалам, по сравнению с монолитным бетоном и кирпичом, при помощи которых возводят стены дома. Основные компоненты — цемент, песок и известь. Один из важных параметров такого материала – его масса. Прежде всего вес газобетонного блока нужно знать для расчета фундамента дома.
От чего зависит масса
На вес газоблока влияют два параметра:
- плотность;
- влажность.
Плотность
Значение плотности отображено на маркировке материала и указано в единицах измерения кг/м 3 .
Из таблицы следует, что 1 куб газобетона марки D400 весит 400 кг, 1 куб марки D500 весит 500 кг.
Влажность
Что касается влажности, то этот показатель влияет на массу аналогичным образом. Чем больше процент влаги, тем большей будет масса материала.
По технологии производства автоклавные газобетоны подвергаются длительной выдержке в среде насыщенного пара под высоким давлением. Изделия, выходящие с конвейера, содержат 25-30% влаги.
Расчет массы
Сколько весит блок
Чтобы провести расчеты, необходимо изначально знать габариты материала и плотность.
Расчеты проводят по формуле m=V*p. Обозначения следующие: m – вес блока (кг), V – объем(м 3 ), р – плотность (кг/м 3 ).
- Размер: 200х300х600 мм
- Плотность: 500 кг/м 3 .
- Зная размеры, можно высчитать объем. Для указанного изделия он будет составлять:
V = 200 мм * 300 мм * 600 мм = 36000000 мм 3 = 0,036 м 3 - Далее, отталкиваясь от марки, на которой указана плотность, определяется вес блока:
m = 0,036 м 3 * 500 кг/м 3 = 18 кг
Ответ: Вес газобетонного блока 200х300х600 без учета влажности составляет 18 кг.
- Размер: 250х400х600 мм
- Плотность: 400 кг/м 3 .
- V = 250 мм * 400 мм * 600 мм = 60000000 мм 3 = 0,06 м 3
- m = 0,06 м 3 * 400 кг/м 3 = 24 кг
Ответ: Масса 250х400х600 без учета влажности составляет 24 кг.
Если расчет производится с целью определения нагрузки стен дома на фундамент, то влажность не играет большое значение в определении массы в данном случае. Так как параметр влажности в эксплуатируемых стенах не поднимается выше 5% при любых погодных условиях.
На начальном этапе строительства фундамент будет нагружаться стенами, нагрузка от которых больше расчетной за счет отпускной влажности. Но к моменту установки окон, возведения крыши, внутренней и внешней отделки, установки оборудования и мебели стеновой материал отдаст в окружающую среду значительную часть влаги и примет расчетную массу. Именно поэтому не стоит учитывать влажность при расчете нагрузок.
Некоторые самозастройщики возводят стены из газобетона в одиночку. И не по наслышке проверяют на себе массу блока лишь при кладке первого ряда. В этом случае им стоит понимать, что свежие заводские блоки за счет содержащейся в них влажности будут тяжелее рассчитанных выше значений примерно на 25%. Если толщина стен по проекту составляет 500 мм, то один человек будет не в состоянии поднимать такие тяжелые изделия. Ему придется либо взять помощника, либо купить более легкий материал толщиной 200 мм и 300 мм (и выложить из него двойную стену вразбежку).
Помимо стандартных блоков с прямолинейными гранями некоторые современные заводы выпускают блоки с захватами для рук с обеих сторон.
Такой материал удобно поднимать и переносить.
При этом расход клея не увеличивается, так как по технологии монтажа пустоты заполнять не нужно.
Так, в нашем первом примере свежий заводской блок, только сошедший с конвейера, будет тяжелее расчетных значений на 30%. Его вес для нашего первого примера составит:
Вес поддона с блоками
Эта характеристика пригодится при планировании доставки материала на объект. У каждого грузового автомобиля есть предельные значения грузоподъёмности и объема перевозимых грузов.
Допустим, визуально вам покажется, что в грузовой автомобиль войдет 10 поддонов. Но водитель, узнав массу поддона, скажет, что сможет взять только 8 поддонов. И он будет прав, так как грузоподъемность транспортного средства не должна превышаться.
Определить массу паллеты с газобетоном просто. Зная количество единиц материала в паллете и вес одного газоблока, перемножьте эти значения.
Кстати, многие продавцы отпускают материал со склада целыми поддонами. И в прайс-листе указывают плотность и объём поддона.
Мы уже знаем, что плотность блоков соответствует массе одного кубометра. Соответственно, перемножив плотность на объём получим искомый вес паллеты.
Например, как видно из предложенного прайс-листа, объём поддона с блоками 600х200х300 мм составляет 1,8 м 3 . Рассчитаем массу поддона для плотности D400.
Сколько весит куб газобетона и определение реальной плотности
В начале статьи самой первой таблице приведены эти значения без всякого расчета. Вес кубометра газосиликатного материала соответствует плотности, указанной в маркировке (D400, D500 и т.д.).
Однако, ситуации бывают разные. Возможно, вы захотите проверить соответствие заводского газосиликата заявленным характеристикам. Или вам не хватило поддона блоков, а у соседа остались излишки. При этом ваш сосед не помнит характеристики своего газобетона.
В этом случае нам понадобится взвесить 1 блок и произвести расчет по обратной формуле p=m/V. Где:
- m – вес (кг) — нужно найти весы и взвесить 1 блок;
- V – объем(м 3 ) — его мы считали выше;
- р – плотность (кг/м 3 ).
Не забывайте брать поправки на влажность.
Расчет количества материала в 1м 3
Расчет проводят в два действия:
- Изначально у продавца узнают геометрические размеры конкретного стенового материала и вычисляется его объем. Такой параметр для блока 200х300х600 мы уже считали, исходя из предыдущего примера он равен 0,036 м3.
- Далее нужно разделить общий объем (в нашем случае 1 м3) на объем данного блока.
В итоге получается 27,778 штук.
Эту характеристику обычно указывают в прайс-листе.
В проектной документации на строительство дома в калькуляции указывается объём необходимого материала, который получают перемножением площади стен с учетом проемов под окна и двери на толщину стен.
Произведя расчет количества материала в кубическом метре, и умножив его на общий объём, мы можем узнать необходимое количество блоков для постройки нашего дома. Кстати, следует помнить при расчете, что над окнами выполняются перемычки. И эти участки в расчет не брать. Но позаботиться о выборе и покупке материала для перемычек.
Размеры и вес
Подводя итоги и учитывая зависимость массы от плотности материала, можно привести следующие параметры веса для каждой марки. Данные представлены одним из производителей.
В заключении напомню, что при выборе марки и размера, нужно учитывать длину, ширину и высоту стен, а также их функциональное назначение.
Полезное видео
Как поднять тяжелый газосиликатный блок на второй этаж, проявив смекалку.
Вся информация о параметрах газосиликатных блоков
Блоки, выполненные из ячеистого бетона, являются разновидностью стенового материала. Они отличаются минимальной массой, упрощают возведение стен, обеспечивают хорошую теплоизоляцию помещений. Газосиликатные блоки размеры которых установлены нормами ГОСТа, используются для возведения подсобных объектов и жилых домов.
Достоинства и недостатки
Основными преимуществами материала являются:
- Незначительный вес снижает трудоёмкость при укладке.
- Высокая прочность позволяет возводить несущие стены.
- Отличные теплоизоляционные характеристики.
- Звукоизоляция почти в 10 раз выше, чем у кирпича.
- Возможность теплового аккумулирования помогает снизить расходы на отопление.
- Паропроницаемость помогает создать внутри объекта комфортный микроклимат.
- Не опасен для здоровья человека.
- Высокая сопротивляемость огню.
Любой строительный материал имеет недостатки. У газосиликатных блоков выделяют следующие отрицательные моменты:
- чрезмерное влагопоглощение;
- невысокая прочность и морозостойкость;
- усадка, приводящая к образованию трещин и расколов;
- образование грибка в условиях намокания.
Разновидность газосиликата
По назначению блоки условно разделяют на несколько видов:
- Стеновые. Камень используется для выкладывания наружных стен.
- Перегородочные. Кирпич применяется для монтирования стен внутри объекта.
Газосиликатные блоки условных групп различаются габаритами. С технической позиции для монтирования перегородок в помещении выгодно использовать изделия меньших размеров. Ведь это ещё и экономия финансовых вложений.
По форме газосиликатные блоки производят следующих видов:
- прямоугольные, используются для выкладывания несущих стен;
- пазогребневые – с двух сторон выполнены два выступа, при соединении между блоками не образовывается мостик холода;
- U-образные, применяются для выполнения армирующего пояса в верхней части стен и возведения перемычки.
К тому же производители выпускают блоки произвольной формы, со специальными ручками для захвата.
Размеры блоков
Размеры газосиликатных блоков установлены согласно, стандартам. Для строительства дома и других объектов производят изделия следующих габаритов:
- Ширина стенового камня: 200, 250, 300, 350, 375, 400, 500 миллиметров, перегородочного – 100-150 миллиметров.
- Длина – 600, 625 миллиметров.
- Высота газосиликата: 200, 250, 300 мм.
Согласно ГОСТ допускаются отклонения размеров готовых изделий. Они различаются по 1 и 2 категории. При выборе продукции стоит обращать внимание на габариты, вес и плотность. От этих показателей зависит сложность кладки, прочность и теплосохраняющие свойства. Благодаря разным размерам каждый покупатель может выбрать подходящий вариант.
Плотность
Готовые изделия различают по составу, который влияет на эксплуатационные характеристики. Плотность влияет на теплопроводность и прочность газосиликатных блоков.
Чем ниже плотность материала, тем выше морозостойкость и теплопроводность. Оптимальной показателем плотности газосиликата является 500 килограмм на кубический метр. Марка D500 хорошо подойдёт для возведения наружных и внутренних стен.
Следует учитывать: низкая плотность – низкая прочность на сжатие. В таблице приведены технические показатели в зависимости от плотности материала.
Газосиликатные блоки: Таблицы размеров и технических характеристик, плюсы и минусы газосиликата
Данный материал обладает существенными конкурентными преимуществами и пользуется заслуженной популярностью на строительном рынке нашей страны. Отличается минимальным весом, что упрощает возведение стен, а также обеспечивает надёжную теплоизоляцию внутренних помещений, благодаря пористой структуре. Помимо этого, газосиликатные блоки привлекают покупателей доступной ценой, чем выгодно отличаются от кирпича или дерева.
Вполне естественно, что данный строительный материал имеет свои особенности, а также специфику применения. Поэтому, не смотря на низкую стоимость, использование блоков из газоселекатного бетона не всегда целесообразно. Чтобы лучше разобраться в этих тонкостях, имеет смысл детально рассмотреть основные технические характеристики материала.
Cостав газосиликатных блоков
Материал изготавливается по уникальной технологии. В частности, блоки производятся путём вспенивания, что придаёт им ячеистую структуру. Для этого в формы с исходной смесью добавляют газообразователь, в роли которого обычно выступает алюминиевая пудра. В результате, сырьё значительно увеличивается в объёме, образуются пустоты.
Для приготовления исходной смеси, обычно применяют такой состав:
-
Цемент высокого качества, где содержания силиката калия превышает 50%.
-
Песок, с 85% содержанием кварца.
-
Известь, с содержанием оксидов магния и кальция более 70%, и скоростью гашения до 15 минут.
-
Сульфанол C.
-
Вода.
Стоит отметить, что включение в состав смеси цемента не является обязательным условием, а если используется, то в минимальных количествах.
Твердение блоков завершается в автоклавных печах, где создаются высокое давление и температурный режим.
Технические характеристики
Для газосиликатных блоков характерны такие технические параметры:
-
Объёмная масса от 200 до 700 единиц. Это показатель сухой плотности ячеистого бетона, на основании которого происходит маркировка блоков.
-
Прочность на сжатие. Это значение варьируется в пределах B0.03-B20, в зависимости от целевого использования.
-
Показатели теплопроводности. Эти значения находятся в диапазоне 0.048-0.
24 Вт/м, и напрямую зависят от плотности изделия.
-
Паронепроницаемость
-
Усадка. Здесь оптимальные значения изменяются в пределах 0.5-0-7, в зависимости от исходного сырья и технологии изготовления.
-
Циклы замораживания. Это морозоустойчивость, которая обеспечивает блокам замораживание и оттаивание без повреждения структуры и показателей прочности. По этим критериям, газосиликатным блокам присваивается классификация от F15 до F100.
Необходимо уточнить, что здесь приведены не эталонные показания, а средние значения, которые могут изменяться в зависимости от технологии производства.
Параметры |
Перегородочные |
Стеновые |
Прочность на сжатие |
25 кгс |
25-40 кгс |
Влажность |
20-25% |
20-25% |
Морозостойкость |
25F |
25-35F |
Усадка при высыхании |
0,23 мм/м |
0,23 мм/м |
Теплопроводность |
0,139 Вт/м ОС |
0,139 Вт/м Ос |
Паропроницаемость |
0,163 мг/м чПа |
01,163 мг/м чПа |
Размеры по нормам ГОСТ
Разумеется, что производители выпускают газосиликатные блоки разного типоразмера.
-
250*250*600.
-
250*400*600.
-
500*200*300.
-
600*100*300.
-
600*200*300.
Важно понимать, что согласно ГОСТ допускаются отклонения величин длины и диагонали, которые относят готовые изделия к 1-ой или 2-ой категории.
Размеры стеновых блоков
ТД «Лиски-газосиликат» | ||||
Наименование блока | Длина,мм | Ширина,мм | Высота,мм | Объем одного блока, м3 |
Рядовые блоки | 600 | 200 | 250 | 0,03 |
600 | 250 | 250 | 0,038 | |
Пазогребневые блоки | 600 | 200 | 250 | 0,03 |
600 | 300 | 250 | 0,045 | |
600 | 400 | 250 | 0,06 | |
600 | 500 | 250 | 0,075 | |
Газосиликатные блоки «YTONG» | ||||
Рядовые блоки | 625 | 200 | 250 | 0,031 |
625 | 250 | 250 | 0,039 | |
625 | 300 | 250 | 0,047 | |
625 | 375 | 250 | 0,058 | |
625 | 500 | 250 | 0,078 | |
Пазогребневые блоки | 625 | 175 | 250 | 0,027 |
625 | 200 | 250 | 0,031 | |
625 | 250 | 250 | 0,039 | |
625 | 300 | 250 | 0,047 | |
625 | 375 | 250 | 0,058 | |
U-образные блоки | 500 | 200 | 250 | * |
500 | 250 | 250 | * | |
500 | 300 | 250 | * | |
500 | 375 | 250 | * |
Количество блоков на 1м3 кладки
Зная стандартные размеры, можно рассчитать, сколько газосиликатных блоков уходит на 1м3 кладки. Такие расчёты являются обязательными и помогают определить точное количество необходимого для строительства материала.
Для этого, необходимо перевести стороны блока в искомую единицу измерения и определить, сколько кубических метров занимает один блок.
Наиболее часто встречающиеся на рынке изделия имеют такой типоразмер: 600*200*300. Переводим миллиметры в метры, и получаем 0.6*0.2*0.3. Чтобы выяснить объём одного блока, перемножаем числа и получаем 0.036 м3. Затем делим кубический метр на полученную цифру.
В результате получается число 27.7, что после округления даёт 28 газосиликатных блоков в кубическом метре кладки.
Размеры перегородочных блоков
ТД «Лиски-газосиликат» | ||||
Наименование блока | Длина,мм | Ширина,мм | Высота,мм | Объем одного блока, м3 |
Рядовые блоки | 600 | 100 | 250 | 0,015 |
600 | 150 | 250 | 0,0225 | |
Газосиликатные блоки «YTONG» | ||||
Рядовые блоки | 625 | 50 | 250 | 0,008 |
625 | 75 | 250 | 0,012 | |
625 | 100 | 250 | 0,016 | |
625 | 125 | 250 | 0,02 | |
625 | 150 | 250 | 0,024 |
Вес материала
Конструкционная масса блока изменяется в зависимости от плотности готового изделия.
-
D400. Масса 5-21 кг.
-
D500/D600. Вес – 9-30 кг.
-
D700. Вес – 10-40 кг.
Помимо плотности, основополагающим фактором изменения веса считается габаритный размер готового блока.
Размер (мм) |
Плотность |
Вес (кг) |
600 х 200 х 300 |
D700 |
20-40 |
D500-D600 |
17-30 |
|
D400 |
14-21 |
|
600 х 100 х 300 |
D700 |
10-16 |
D500-D600 |
9-13 |
|
D400 |
5-10 |
Плюсы и минусы газосиликатного бетона
Как и любой строительный материал, газосиликатные блоки имеют сильные и слабые стороны. К положительным характеристикам можно отнести такие моменты:
-
Газосиликатный бетон относится к категории негорючих материалов и способен выдерживать воздействие открытого пламени до 5 часов, без изменения формы и свойств.
-
Большие габаритные размеры обеспечивают быстрое возведение стеновых конструкций.
-
Блоки обладают удельно низким весом, что существенно упрощает рабочий процесс.
-
При производстве используются только природные материалы, поэтому газосиликатные блоки являются экологически безопасными.
-
Пористая структура обеспечивает высокие значения теплоизоляции помещений.
-
Материал легко поддаётся обработке, что помогает возводить стены со сложной геометрией.
К недостаткам можно отнести следующее:
-
Хорошо впитывают влагу, что снижает эксплуатационный срок.
-
Применение для сцепления специальных клеевых составов.
-
Обязательная внешняя отделка.
Стоит отметить, что для газосиликатных блоков требуется прочный фундамент. В большинстве случаев обязателен армирующий пояс.
Газосиликат или газобетон?
Оба материала относятся к категории ячеистых бетонов, поэтому имеют практически идентичную структуру и свойства. Многие строители считают, что газосиликат и газобетон – это два названия одного материала. Однако это заблуждение. При внешнем сходстве, ячеистые бетоны имеют ряд отличительных признаков, что определяет их дальнейшее применение и технические характеристики.
В частности, при изготовлении газобетона допускается естественное твердение блока на открытом воздухе, для газосиликата – автоклавные печи являются обязательным условием. Кроме этого, для газобетонных блоков основным связующим компонентом является цемент, у силикатных аналогов – известь. Применение разных компонентов влияет цвет готовых блоков.
Если говорить о конкретных характеристиках, можно заметить такие отличия:
-
Газосиликатные блоки имеют равномерное распределение пустотных ячеек, что обеспечивает высокую прочность.
-
Вес газобетонных блоков гораздо больше, что требует усиленного фундамента при строительстве.
-
В плане теплоизоляции, газосиликатные блоки выигрывают у газобетонных.
-
Газобетон лучше поглощает влагу, что обеспечивает большее количество циклов замораживания.
-
Газосиликатные блоки обладают более выдержанной геометрией, в результате можно упрощается финишная отделка стеновых конструкций.
В плане долговечности материалы идентичны и могут прослужить более 50 лет.
Если отвечать на вопрос: «Что лучшее?», у газосиликатных блоков намного больше технических преимуществ. Однако технология изготовления вынуждает повышать стоимость готовых изделий, поэтому газобетонные блоки обходятся дешевле. Поэтому, те, кто желает возвести дом из качественного и современного материала выбирают газосиликат, желающие сэкономить на строительстве – отдают предпочтение газобетону.
При этом нужно учитывать регион применения: в областях с повышенной влажностью воздуха, эксплуатационный срок газосиликатных блоков заметно снижается.
Штукатурка стен из газосиликатных блоков
Оштукатуривание стен подразумевает соблюдение определённых норм и правил. В частности, внешняя отделка производится только после завершения внутренних работ. В противном случае, на границе газосиликата и слоя штукатурки будет образовываться слой конденсата, что вызовет появление трещин.
Кроме этого, не рекомендуется использование обычного цементно-песчаного раствора. Блок впитает влагу, оставив только сухой слой. Поэтому для оштукатуривания необходимо использовать только специальные смеси.
Если говорить о технологии проведения работ, можно выделить три основных этапа:
-
Нанесение грунтовочного слоя для повышения адгезии.
-
Монтаж армирующей сетки из стекловолокна.
-
Оштукатуривание.
Для отделочных работ лучше использовать силикатные смеси и силиконовые штукатурки, которые обладают отличной эластичностью. Наносят штукатурку шпателем, уминая смесь поверх армирующей сетки. Минимальная толщина слоя 3 см, максимальная – 10. Во втором случае, штукатурка наносится несколькими слоями.
Клей для газосиликатных блоков
Структура материала подразумевает использования специальных клеевых составов при возведении стеновых конструкций. Стоит отметить, что специалисты рекомендуют приобретать клей и блоки в комплекте, чтобы исключить конфликт материалов и обеспечить максимальную сцепляемость. При выборе клея, нужно учитывать время застывания состава. Некоторые смеси схватываются за 15-20 минут, но это не является показателем качества клея. Оптимальное время застывания – 3-4 часа.
Если говорить о конкретных названиях, можно обратить внимание на такие марки клея:
-
Победит-160.
-
Юнис Униблок.
-
Престиж.
-
Бонолит.
-
AEROC.
Стоит отметить, что для летнего и зимнего строительства используются разные клеевые составы. Во втором случае, в смесь добавляют специальные добавки, на упаковке имеется соответствующая пометка.
Расход клея на 1м3
Эта информация обычно указывается производителем и варьируется в пределах 1.5-1.7 кг. Нужно уточнить, что приведенные значения актуальны только для горизонтальных поверхностей: для кубатуры расход клея будет заметно выше. Средние значения расхода клеевого состава на 1м3 кладки составят около 30 кг.
Отметим, что это расчёты производителей, которые могут отличаться от реальных значений. Например, профессиональные строители утверждают, что на 1м3 кладки из газосиликатных блоков уходит не менее 40 кг. Это вызвано тем, что пластичный состав заполняет все пустоты и изъяны готового блока.
Независимый рейтинг производителей
Перед началом строительства, важно выбрать производителя материалов, который поставляет на рынок качественную продукцию. В российском регионе доверие потребителя заслужили такие компании:
-
ЗАО «Кселла-Аэроблок Центр». Это немецкая компания, часть производственных мощностей которой находится в России. Продукция предприятия известна во всём мире, присущим всему немецкому качеством. Любопытно, что компания XELLA ведёт свою деятельность в нескольких направлениях, три из которых нацелены на добычу и последующую переработку сырья.
-
ЗАО «ЕвроАэроБетон».
Предприятие специализируется на производстве газосиликатных блоков с 2008 года. Компания имеет собственные производственные линии, где используется автоматизированный процесс, используется оборудование ведущих мировых брендов. Завод расположен в Ленинградской области, город Сланцы.
-
ООО «ЛСР. Строительство-Урал». Головной офис компании находится в Екатеринбурге, завод занимает лидирующие позиции на Урале. Предприятие имеет полувековую историю, использует автоматизированный производственный процесс, контролирует качество на всех этапах.
-
ЗАО «Липецкий силикатный завод». История предприятия началась в 1938 году, это один из основных поставщиков центрального региона России. В 2012 году, компания получила сертификат международного образца по классу ISO 9001.2008, что говорит о высоком качестве продукции.
-
ОАО «Костромской силикатный завод».
Это одно из старейших предприятий страны, основанное в 1930 году. За годы существования, был выработан специальный устав, позволяющий вывести качество выпускаемой продукции на принципиально новый уровень. Компания дорожит своей репутацией и может похвастаться отсутствием негативных отзывов со стороны потребителей.
Отметим, что это далеко не полный перечень заслуживающих доверия производителей газосиликатных блоков российского региона. Однако продукция этих брендов является оптимальным соотношением стоимости и качества.
Блок из автоклавного газобетона (AAC) Falcon
АВТОКЛАВНЫЙ ПЕРИОДНЫЙ БЕТОН СТАНДАРТНЫЙ (60 x 20 x ТОЛЩИНА)
ТОЛЩИНА (см) | ||||||
---|---|---|---|---|---|---|
ВЕС на поддон (1 x 1,2 x 1,5 м) | ||||||
кг / м 2 | кг / шт. | кг / поддон | шт. | M 2 | M 3 | |
7,5 | 45 | 5,4 | 1 080 | 200 | 24 | 1,8 |
10 | 60 | 7,2 | 1 080 | 150 | 18 | 1,8 |
12,5 | 75 | 8,78 | 1 080 | 120 | 14,4 | 1,8 |
15 | 90 | 10,53 | 1 080 | 100 | 12 | 1,8 |
17,5 | 105 | 12,6 | 1,134 | 90 | 10,8 | 1,89 |
20 | 120 | 14,4 | 1,152 | 80 | 9,6 | 1,92 |
JUMBO АВТОКЛАВИРОВАННЫЙ ПЕРИОДНЫЙ БЕТОН (ТОЛЩИНА 60X40X)
ТОЛЩИНА (см) | ||||||
---|---|---|---|---|---|---|
ВЕС на поддон (1 x 1,2 x 1,5 м) | ||||||
кг / м2 | кг / шт.![]() | кг / поддон | шт. | M 2 | M 3 | |
7,5 | 45 | 10,8 | 1 080 | 100 | 24 | 1,8 |
10 | 60 | 14,4 | 1 080 | 75 | 18 | 1,8 |
12,5 | 75 | 18,0 | 1 080 | 60 | 14,4 | 1,8 |
15 | 90 | 21,6 | 1 080 | 50 | 12 | 1,8 |
17,5 | 105 | 25,2 | 1,134 | 45 | 10,8 | 1,89 |
20 | 120 | 28,8 | 1,152 | 40 | 9,6 | 1,92 |
(PDF) Оценка технической пригодности автоклавного газобетонного блока в качестве альтернативного строительного материала для стен; Случай Непала
Deepak Khanal et al. , Saudi J Civ Eng, июль 2020 г .; 4 (5): 55-67
© 2020 | Опубликовано Scholars Middle East Publishers, Дубай, Объединенные Арабские Эмираты 56
рост населения в Бхаратпуре увеличился. Для удовлетворения жилищных потребностей увеличивающегося населения
строится многоэтажный дом
в формах коллективного и многоквартирного
жилых домов. Строительство здания
около десяти лет назад было полностью личным делом.
Есть традиция строить дома своими силами
с использованием обычных строительных материалов и средств
.Принимая во внимание эти аспекты, правительство
сформулировало национальную политику в области жилья на 2012 год с видением
обеспечения безопасного, адекватного и соответствующего уровню жизни
жилья для всех [2].
Согласно отчетам Всемирного банка, группы людей
с дневным доходом менее 1,25 долларов США
считаются группами с низким доходом или группами бедных
. Темпы урбанизации оставались более высокими
и, вероятно, останутся таковыми в будущем.Примерно 17,1%
участков по переписи 2011 года. Однако с добавлением
131 муниципалитета в 2014 г., 38,26% от
выделенные городские районы.
Были колебания в темпах роста городских
между переписями. Хотя темпы роста за период переписи
составляли 3,43%, среднегодовой прирост
в период с 1981 по 2011 год оставался высоким —
5.3%. Дифференциал роста городских и сельских районов в 2011 году составил 2,4%.
Уровень урбанизации самый высокий в горном районе
21,7% по сравнению с тераем 15,1% и горным районом
2,8% [3]. По данным CBS 2001 года,
составляли 4 174 374 дома / здания или жилые постройки
в целом, из которых около 1,3 миллиона домов в
сельской местности и около ста тысяч в городской
области были временными. природы, что означает, что около
33% от общего числа жилых домов
были построены временно.Согласно обследованию уровня жизни
Непала, 2003/04 г.,
населения, проживавшего в принадлежащих им домах, составляло
около 91,6%, а тех, кто живет на арендную плату, составляло 8,4%,
, тогда как это число оказалось равным. 92,8% и 2,2%
соответственно в 1995/96 году. По результатам
финансового года 2009/10 эти цифры составляют 90%,
,и 8% соответственно. Таким образом, количество людей, живущих в арендованном доме
, увеличилось с 2% до 8% по сравнению с
в первом исследовании уровня жизни, т.е.е. в течение
периодов 15 лет [3].
Сравнительные преимущества блока AAC
Блоки AAC производятся с использованием природного сырья
, такого как глина, сланец, сланец, летучая зола и
Загрязнение окружающей среды. Они известны своими улучшенными тепловыми свойствами
, а также не горючими и огнестойкими (до 1600 ° C) свойствами, отличными от
.
Наличие блоков AAC различных размеров
делает их экономичными для стен разных размеров. В
в дополнение к этому, легкость резки, сверления, забивания гвоздей, фрезерования
и канавки делают блок
индивидуальным требованием конструкции. Из-за
это, снижение эксплуатационных расходов примерно на 30% до
40% наблюдается в AAC.
Блоки AAC в 3-4 раза легче традиционных кирпичей
, что ускоряет и упрощает строительные работы
и, в свою очередь, требует меньше опалубки
и подпорок в строительстве.Кроме того, использование этих блоков
снижает общую статическую нагрузку здания
, тем самым обеспечивая меньшее поперечное сечение конструктивных элементов
. Конструктивно в этой конструкции каждая стена
и плита ведут себя как стена сдвига. Эти строительные конструкции
доказали свою высокую долговечность, низкие затраты на обслуживание
и лучший цвет [4].
Жесткость блока AAC
Жесткость k тела является мерой сопротивления
, оказываемого упругим телом деформации.
Для упругого тела с одной степенью свободы
(DOF) каркас RC, заполненный блоком AAC, показал постепенное снижение боковой жесткости
с 215 кН / мм до
1,5 кН / мм [19].
Прочность на сжатие блока AAC
Прочность на сжатие можно определить как
, измеренное максимальное сопротивление образца бетона
осевой нагрузке. Средняя прочность на сжатие
2.86 МПа было выполнено на
кубиках AAC с плотностью 650 кг / куб.м после 28 дней отверждения в обычной воде —
. Энергия сжатия более 20 МПа составляет
, которую можно получить с добавлением паров кремнезема, полипропиленовых волокон
и армирующих стальных сеток для специальных программ
, в которых требуется дополнительная энергия сжатия
. Поскольку блоки, изготовленные из AAC, составляют от 1/3 до ½
веса обычных бетонных блоков.В качестве причины подшипника
, самонагрузки стенового блока AAC, используются блоки с нулевой мощностью сжатия
, 210,31 МПа, в
по сравнению с традиционными блоками 0,42-0. Пятьдесят шесть
МПа [5].
Размер и форма образца, приближение порообразования
, путь нагружения, возраст, влажность материала
, характеристики используемых веществ и метод отверждения
влияют на прочность пенобетона
.Пористая структура воздушных пор и механическое состояние
оболочки пор оказывают заметное влияние на общую прочность
. Значения прочности на сжатие
для различных плотностей приведены в таблице 2.1
[6].
Таблица-0.1: Свойство блока AAC в отношении плотности
Прочность на сжатие (МПа)
Статический модуль упругости (кН / мм2)
Теплопроводность (Вт / м0С)
Твердые бетонные блоки по сравнению с блоками AAC
Махадев Десаи — основатель и генеральный директор gharpedia. com и SDCPL — ведущая консалтинговая фирма по дизайну, имеющая сильное национальное присутствие. Он имеет степень в области гражданского строительства (BE) и права (LLB) и имеет богатый 45-летний опыт работы. Помимо того, что он является главным редактором, он также является наставником команды GharPedia. Он связан со многими профессиональными организациями. Он также является соучредителем 1mnt.in первого в отрасли программного обеспечения для выставления счетов подрядчикам. Он заядлый читатель, отредактировал 4 книги и пионер движения за чтение книг в Гуджарате, Индия.
Этот пост также доступен на: हिन्दी (хинди)
Из всех строительных материалов в мире бетон является одним из наиболее широко используемых.Два основных компонента бетонных блоков — это цементная паста и инертные материалы. Цементная паста состоит из портландцемента, воды и небольшого количества воздуха. Инертные материалы обычно состоят из мелких заполнителей, таких как песок, и крупных заполнителей, таких как гравий, щебень или шлак.
Блок из автоклавного газобетона — одно из важнейших достижений 20 века в области строительства. Это революционный строительный материал, предлагающий уникальное сочетание высокой прочности и прочности, малого веса, а также превосходных экологических характеристик.
Полнобетонные блоки и блоки AAC являются важными строительными материалами для возведения стен. Твердые бетонные блоки и блоки AAC используются в стенах в соответствии с их свойствами, доступностью и стоимостью. Поэтому здесь мы даем вам краткое сравнение бетонного блока и блока AAC, чтобы помочь вам сделать правильный выбор.
- Полнобетонные блоки — это один из нескольких сборных железобетонных изделий, используемых в строительстве. Термин сборный железобетон относится к тому факту, что блоки формуются и затвердевают перед тем, как их доставят на строительную площадку.
Блок из газобетона в автоклаве
- Блоки AAC — это легкий строительный материал, разрезанный на блоки из каменной кладки или сформированный из больших досок и панелей.
- Блок AAC относительно однороден по сравнению с другими материалами стеновых блоков и не содержит фазы крупного заполнителя.
- Полнобетонные блоки изготавливаются из смеси портландцемента, воды, песка и гравия.
Блок из автоклавного газобетона
- Изготовлен из смеси летучей золы, цемента, извести, гипса и аэрирующего агента.
- Летучая зола, используемая в производстве блоков AAC, является экологически чистой, а цемент используется в очень небольшом количестве.
- Проблема удаления летучей золы решается за счет использования летучей золы в блоке AAC, что до сих пор было основной проблемой.
- Полнобетонные блоки используются как для несущих, так и для ненесущих стен.
- Также используется для строительства подпорных стен, садовых стен, дымоходов и каминов.
- Также используется как перемычка.
Блок из газобетона в автоклаве
- Блоки AAC можно использовать для строительства как внутренних, так и внешних стен.
- Может также использоваться как для несущих, так и для ненесущих стен.
- Монолитные бетонные блоки отличаются гибкостью и простотой изготовления.
- Полнобетонные блоки идеально подходят для фундамента и стены подвала.
- Полнобетонные блоки не подвержены воздействию термитов.
- Полнобетонные блоки обеспечивают изоляцию от холодной и жаркой погоды.
- Стена из массивных бетонных блоков долговечна, долговечна и требует меньшего ухода.
- Полнобетонные блоки обладают высокой устойчивостью к экстремальным погодным условиям, таким как штормы, наводнения и сильные ветры.
- Полнобетонные блоки обладают высокой устойчивостью к растрескиванию и крошению при экстремальных температурах, в отличие от заливного бетона.
- Монолитные бетонные блоки практически звуконепроницаемы.
Блок из автоклавного газобетона
- Силы землетрясения пропорциональны весу здания и, следовательно, в конечном итоге сокращают статическую нагрузку на здания и, следовательно, меньше стали в случае конструкций RCC.
- Экономия стали и бетона за счет уменьшения собственного веса.
- Увеличение площади пола за счет уменьшения размеров колонн и толщины стены.
- Блоки AAC очень просты в обращении, и для их резки используются обычные инструменты.
- Блоки AAC доступны в больших размерах и, следовательно, с меньшим количеством стыков. В конечном итоге это приводит к более быстрому строительству на месте и меньшему расходу цемента.
- Блоки AAC изготовлены из неорганического материала, который помогает избежать термитов, повреждений или потерь
- Легко транспортировать на верхние этажи
- Экономия времени при строительстве
- Блоки AAC имеют очень низкую теплопроводность, что сохраняет внутреннюю прохладу в помещении. лето и тепло зимой
- Блоки AAC уменьшают колебания внутренней температуры, поддерживая приятную и здоровую температуру для жителей
- Блоки AAC значительно снижают затраты на кондиционирование воздуха благодаря своим тепловым свойствам
- Блоки AAC подходят для огнестойкости приложение для желаемой безопасности.
- В случае блоков AAC потери минимальны.
- Они не наносят вреда окружающей среде, а также позволяют экономить воду. Следовательно, он широко используется в качестве экологически чистого продукта.
- Хотя стоимость производства блоков AAC высока, но в целом стоимость проекта снижается.
- Стоимость строительства из монолитных бетонных блоков может быть выше, чем у традиционного каркасного строительства.
- Вес монолитного бетонного блока больше, чем AAC Block
- Из-за большого веса бетона стоимость конструкции высока.
- Трудно организовать скрытые работы с электропроводкой, водопроводом и кабелепроводами.
Блок из газобетона в автоклаве
- Стоимость производства единицы блока AAC выше.
- Штукатурка иногда плохо держится из-за ее гладкой поверхности.
- Требует ухода во время самого производства, чтобы поверхность не была очень гладкой
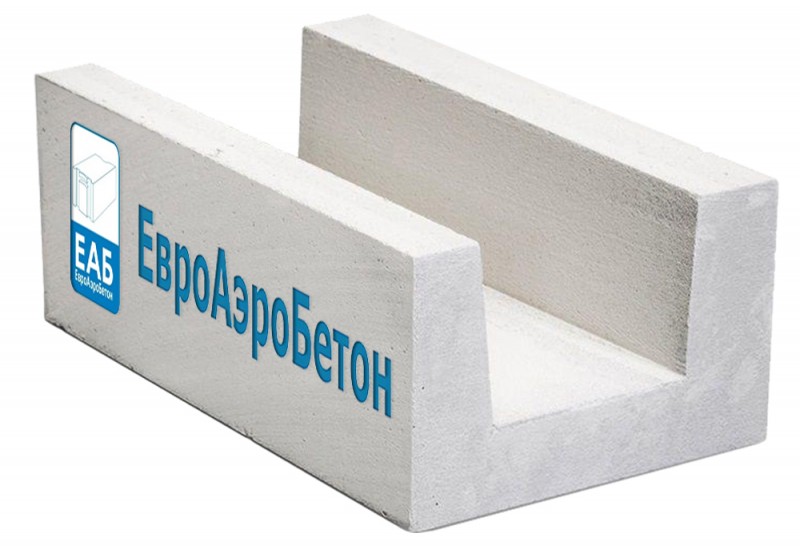
- Цвет твердого бетонного блока светло-серый
Автоклавный пенобетонный блок
- Цвет блока AAC — серый
Блок из пенобетона в автоклаве
- 400-600 × 100-200 × 100-300 мм Однако
- он передает от производителя к производителю.
- Изменение длины блоков не должно превышать 5 (+/-) мм, а изменение высоты и ширины блоков не должно превышать 3 (+/-) мм.
Блок из газобетона в автоклаве
- 1,5 мм (+/-)
- Блоки AAC имеют точные размеры, потому что они производятся по технологии проволочной резки и являются заводским продуктом.
Блок из автоклавного пенобетона
- 451-550
- 551-650
- 651-750
- 751-850
- 851-1000 кг / м3
- В зависимости от аэрации -50 Н / мм2
- Прочность определяется как способность противостоять силе или давлению.
Блок из автоклавного газобетона
- 30-35 кг / см2
- Но для того, чтобы выполнить стену в конструкции RCC, вам не нужно больше прочности.
- Водопоглощение блоков не должно превышать 10% от его веса.
Блок из автоклавного газобетона
- Водопоглощение этого блока не должно составлять 10% от его объема.
- Стена из массивных бетонных блоков толщиной 100 мм может выдерживать огонь до 4 часов.
Блок из автоклавного пенобетона
- Стена толщиной 100 мм может противостоять огню до 4 часов.
- 0,7–1,28 Вт / мк
- Степень теплопередачи от определенного материала, которая называется теплопроводностью.
- Теплопроводность блока высокая, следовательно, теплоотдача от блока больше, чем от блока AAC.
Блок из автоклавного пенобетона
- 0,21 — 0,42 Вт / мк
- Теплопроводность блока ниже и, следовательно, меньше теплоотдача от блока.
- Звукоизоляция определяется как способность снижать передачу звука элементами здания.
- Звукоизоляция также зависит от толщины стены.
- Звуки 51 дБ уменьшаются за счет стены 150 мм.
Блок из автоклавного пенобетона
- Блок AAC имеет хорошие свойства звукопередачи из-за наличия воздушных пустот.
- Уровень шума 40-45 дБ уменьшается для толщины 200 мм
- Цельный бетонный блок не допускает распространения термитов и вредителей, следовательно, увеличивает срок службы стены.
Блок из автоклавного пенобетона
- Блоки AAC — устойчивый к насекомым, неорганический и прочный строительный материал для стен.
- Блок AAC также не допускает распространения термитов и вредителей, следовательно, увеличивает продолжительность жизни. стены.
- Полнобетонные блоки имеют большие размеры и форму.
Это обеспечивает быстрое строительство, следовательно, в человеко-час кладется больше стен по сравнению с кирпичом, но не по сравнению с блоком AAC.
Блок из газобетона в автоклаве
- Быстрое строительство будет выполнено из-за большего размера и меньшего веса блоков AAC.
- Доступна большая площадь ковра за счет меньшей толщины блока.
Блок из газобетона в автоклаве
- Доступна большая площадь ковра за счет меньшей толщины блока.
- Полнобетонные блоки используются как для несущих, так и для ненесущих стен.
Блок из газобетона в автоклаве
- Блоки AAC рекомендуются для высотных зданий, поскольку они значительно снижают общую статическую нагрузку здания
- Требуется меньше стыков и, следовательно, значительная экономия раствора по сравнению с обычными каменными конструкциями .
Блок из автоклавного пенобетона
- Требуется меньше раствора из-за плоской и ровной поверхности и меньшего количества стыков.
- Быстрое возведение стены за счет большего размера блока и меньшего количества стыков.
Блок из автоклавного пенобетона
- Быстрое возведение стены за счет большего размера блока, легкого веса и меньшего количества стыков.
- Требуется больше воды для отверждения и, следовательно, более высокие счета за электроэнергию и трудозатраты.
Блок из газобетона в автоклаве
- Блок в основном отверждается паром, и кладка блоков также требует меньшего затвердевания, следовательно, меньшее использование воды и экономия на счетах за электроэнергию.
- Незначительная поломка происходит из-за ее твердой поверхности.
Блок из автоклавного пенобетона
- Незначительный поломка возможна почти 100% утилизация.
- Полнобетонные блоки следует хранить таким образом, чтобы исключить любой контакт с влагой на объекте. Их следует складывать на доски или другие опоры, не соприкасаясь с землей, и накрывать их для защиты от намокания.
Блок из газобетона в автоклаве
- Доступен в любое время и в любое время года в короткие сроки, поэтому хранение не требуется.
- Выцветание происходит из-за наличия соли в воде и песке.
Блок из автоклавного пенобетона
- Выцветание происходит через раствор и воду.
- Такая экономия невозможна
Автоклавный газобетонный блок
- Экономия стали до 15% и экономия бетона до 7%. расход стали. Следовательно, снижает структурные затраты.
- Это не зеленый продукт.
Блок из газобетона в автоклаве
- Он в основном решает проблему удаления летучей золы с электростанции и, следовательно, не наносит вреда окружающей среде.
- Блоки AAC изготовлены из нетоксичного материала, не наносящего вреда окружающей среде. Его использование снижает количество промышленных отходов, а также снижает выбросы парниковых газов.
- В процессе производства отходы блока AAC перерабатываются и используются снова. Эти отходы образуются в процессе резки.
- Следовательно, блоки AAC являются экологически чистым продуктом.
- Твердые бетонные блоки выдерживают средние силы землетрясения, поскольку плотность бетонных блоков выше, чем у блоков AAC.
Блок из автоклавного газобетона
- Силы землетрясения пропорциональны весу здания. Блоки AAC уменьшают вес здания, поэтому повышают безопасность от землетрясений.
Полнобетонные блоки используются в качестве альтернативы глиняным кирпичам, но бетонные блоки имеют большой вес, поэтому здания становятся тяжелыми. Стоимость кладки из бетонных блоков также высока, поэтому при строительстве стены используются блоки AAC. Использование блока AAC очень выгодно, потому что оно сохраняет окружающую среду, экономит энергию и обеспечивает безопасность жизни.
Также читайте:
Глиняный кирпич против блока AAC Как сделать правильный выбор
10 качеств хорошего глиняного кирпича
Махадев Десаи — основатель и генеральный директор gharpedia.com и SDCPL — ведущая консалтинговая фирма по дизайну, имеющая сильное национальное присутствие. Он имеет степень в области гражданского строительства (BE) и права (LLB) и имеет богатый 45-летний опыт работы. Помимо того, что он является главным редактором, он также является наставником команды GharPedia. Он связан со многими профессиональными организациями. Он также является соучредителем 1mnt.in первого в отрасли программного обеспечения для выставления счетов подрядчикам. Он заядлый читатель, отредактировал 4 книги и пионер движения за чтение книг в Гуджарате, Индия.
Starken-CoolPro3-Autoclaved-Aerated-Light-Concrete-AAC-Block-100MM-Tx-600MM-Lx-200MM-H-S3
Описание
Стандартные блоки Starken предлагают быстрый, удобный и универсальный решение для большинства требований к стенам. Каждый блок эквивалентен 7 частям обычного кирпича. С блоками Starken AAC легко работать, и их можно разрезать до нужного размера с помощью ручной пилы с твердосплавным напылением. Это обеспечивает максимальную гибкость и минимизирует потери.
Приложение:
- Общие внутренние и внешние стены.
- Сторона, отсек и перегородки.
- Акустические и огнестойкие стены. Только
- Блоки толщиной 125 мм и выше подходят для использования в качестве несущих стен.
Технические характеристики
Свойство | Значение |
Длина (Д) x Высота (В) | 600 мм (Д) x 200 мм (В) |
Толщина (T) | 100 — 200 мм |
Номинальная плотность в сухом состоянии | 500 ± 50 кг / м³ |
Рабочая плотность | 700 ± 50 кг / м³ |
Прочность на сжатие | 3 .![]() |
Теплопроводность, К | 0,172 Вт / мк |
Модуль упругости | 1500 — 2500 МПа |
Предел прочности при растяжении | 0,44 — 0,55 МПа |
Модуль разрыва | 0,44 — 0,55 МПа |
Стандартная номинальная длина и высота (мм) | Стандартная номинальная толщина (мм) | м² на поддон | No.штук на поддоне |
600 x 200 | 100 | 21,60 | 180 |
125 | 17,30 | 144 | |
150 | 14,40 | 120 | |
200 | 10,10 | 84 |
Преимущества AAC
1. Плотность блоков Starken AAC составляет примерно одну пятую плотности бетона. с ним легко обращаться.Фундамент (сваи и заглушки) = 12% экономии Армирование балки и колонны = 17% экономии ** Анализ основан на 18-этажной квартире с обслуживанием, состоящей из 5 уровней автостоянки и 13 уровней посуточная квартира. | |
2. Огнестойкий Превосходство традиционной кирпичной кладки для изделий с огнестойкостью до 4 часов при номинальной толщине блока 100 мм.Утеплитель более чем в 3 раза превосходит кирпичную стену. | |
3. Ударопрочный Стены, возведенные из материалов AAC толщиной 100 мм, классифицируются как «тяжелые» и способны выдерживать ударные нагрузки, потенциально возникающие в результате грубого использования. | |
4. Скорость и простота монтажа приводят к снижению затрат по сравнению с традиционным строительством из кирпича. | |
5. Durable История использования, насчитывающая более 50 лет, защищает ограждающие конструкции зданий и сохраняет долговечность даже в экстремальных погодных условиях. | |
6. Экологичный Starken AAC помогает сократить не менее 30% экологических отходов, снизить на 50% парниковое излучение и более 60% интегрированной энергии на поверхности кирпич. | |
7. Тепловой комфорт и энергосбережение Отличные теплоизоляционные свойства Starken AAC приводят к повышению уровня комфорта и сокращению затрат на отопление и охлаждение. | |
8. Звукоизоляция Научно доказано, что обеспечивает лучшую изоляцию от звука, передаваемого по воздуху, по сравнению с другими твердыми строительными материалами. | |
9. Water Resistant Starken AAC содержит миллионы закрытых микроскопических ячеек, которые сильно препятствуют проникновению влаги. | |
10. Точность размеров Блоки и панели производятся в заводских условиях с использованием самого современного оборудования, что приводит к продукции с более жесткими допусками по размерам. | |
11. Хорошая обрабатываемость Starken AAC можно легко распиливать, резать, резать, прибивать или сверлить с помощью обычных ручных инструментов. |
Сравнение AAC и Brick
Отказ от ответственности
Все изображения продуктов показаны только для иллюстрации. Реальные продукты могут отличаться по размеру, типу, бренду, версии, цвету и другим соответствующим характеристикам.
Легкие кирпичи AAC, блоки Aerocon, блоки из пенобетона для автоклавов, блоки AAC, блоки Fusion Rectangle, в Khade Bazar, Belgaum, SUNSHINE BUILDING SOLUTIONS
Легкие кирпичи AAC, блоки Aerocon, газобетон для автоклавов Блоки, Прямоугольные блоки Fusion, ब्लॉक в Хаде Базар, Белгаум, СОЛНЕЧНЫЕ СТРОИТЕЛЬНЫЕ РЕШЕНИЯ | ID: 13814753388Описание продукта
Автоклавный газобетон — это универсальный легкий строительный материал, который обычно используется в виде блоков.По сравнению с обычным (т.е. «плотным» бетоном) газобетон имеет низкую плотность и отличные изоляционные свойства.
Низкая плотность достигается за счет образования воздушных пустот для создания ячеистой структуры. Эти пустоты обычно имеют диаметр 1-5 мм и придают материалу характерный внешний вид. Блоки обычно имеют прочность в диапазоне 3-9 Нмм-2 (при испытании в соответствии с BS EN 771-1: 2000). Плотность колеблется от 460 до 750 кг м-3; для сравнения, бетонные блоки средней плотности имеют типичный диапазон плотности 1350-1500 кг м-3, а плотные бетонные блоки — 2300-2500 кг м-3.
Автоклавные газобетонные блоки являются отличными теплоизоляторами и обычно используются для формирования внутреннего листа полой стены. Они также используются во внешнем листе, когда они обычно визуализируются, и в фундаменте. Из автоклавного газобетона можно построить практически целый дом, включая стены, полы — с использованием железобетонных балок, перекрытия и крышу. Автоклавный газобетон легко режется до любой необходимой формы.
Заинтересовал этот товар? Получите актуальную цену у продавца
Связаться с продавцом
Изображение продукта
О компании
Юридический статус фирмы Физическое лицо — Собственник
Характер бизнеса Оптовик
Участник IndiaMART с декабря 2015 г.
GST29ASQPA2142M1ZI
За это время промоутеры «SUNSHINE BUILDING SOLUTIONS» заработали заслуженную репутацию для всей торговли строительными материалами в Карнатаке и Гоа с доступными ценами и качеством продукции.
Компания Sunshine Building Solutions была основана Шри Четаном М. Ангади в Белагави и постепенно расширила бизнес в направлении Северной Карнатаки в 2010-11 финансовом году, работая в различных сегментах, например, цемент, блоки AAC (легкие кирпичи), окна и двери из ПВХ и т. поддерживается его братом и сестрой, г-ном Нагендра С. Ангади и мисс Чайтра М. Ангади, которые также являются директорами компании, ведущей бизнес в Северной Карнатаке. Sunshine Building Solutions имеет собственный дочерний концерн в логистике и компаниях Infra Projects, а именно «ANGADI ЛОГИСТИКА »и« CN INFRASTRUCTURES », расположенные в Белагави и ведущие бизнес на всей территории Карнатаки и Гоа.Компания в основном ориентирована на поставку целых строительных материалов под одной крышей.
Есть потребность?
Получите лучшую цену
Есть потребность?
Получите лучшую цену
Автоклавный газобетон (AAC) — история легкого материала
- Детали
- Опубликовано: 13.02.2014 10:44
- Автор UDK Gazbeton
ТЕКУЩЕЕ ПОЛОЖЕНИЕ
AAC является привлекательным на мировом рынке. Производство растет примерно на 5 млн. 3 в год, в то время как общий спрос достигнет 100 млн. 3 в 2010 году, согласно Х. Багери (2006). Это высококачественный строительный материал, состоящий из простых или даже ненужных ингредиентов (песок и / или летучая зола) с ограниченным количеством минеральных вяжущих (известь, цемент). Вспенивание обычно активируется алюминиевым порошком. Подъем на более высокий уровень является примером нынешней тенденции к экономии материалов, которая активизируется благодаря хорошо адаптированному низкотемпературному производственному процессу.Автоклавирование под давлением (180-200 ° C, примерно 1 МПа в течение примерно 10 ч) превращает минералы химически в прочную кристаллическую структуру торберморита. А уровень воплощенной энергии относительно низок. Резка проволокой очень точна, что позволяет получить точную геометрию блока и кладку тонким слоем (1-3 мм) раствором.
На практике теперь AAC имеет плотность в сухом состоянии от 275-400 кг / м 3 (изоляционная плотность) до 450-750 кг / м 3 (структурные качества). Он используется для простой кирпичной кладки или изоляционных целей, а также для армированных компонентов, таких как перемычки, кровельные / напольные и стеновые панели. Коэффициент ползучести увеличивается с уменьшением плотности материала. Это может иметь важное влияние на несущие стены с низким содержанием арматуры. На практике плотность 500 кг / м 3 в таких случаях является хорошим компромиссом. Горизонтальные элементы также имеют усиление на сжатой стороне, что снижает их чувствительность к долгосрочным воздействиям. Об этом свидетельствуют исследования горизонтальных элементов возрастом до 70 лет.Более низкая плотность компенсируется большим количеством стали, которая имеет четыре цели: противостоять растяжению, сжатию, сдвигу и подаче анкеровки.
Предел пролета горизонтального элемента традиционно составлял 6 м. Количество стали тогда было еще умеренным. Увеличение пролета привело к быстрому увеличению стали. Шведский производитель Siporex расширил форму до 8,0 м, но на практике предел был 7,2 м при плотности 500 или 600 кг / м 3 (Lättbetonghandboken, 1993). Одним из важнейших факторов был прогиб под действием собственного веса — испытательный элемент с пролетом 8 м сильно завис.
до н.э.
Совершенно иное решение проблемы пролета дает технология BCE, первоначально предложенная одним из авторов в начале 1990-х годов (Hellers B.G. & Lundvall O., 1992). Это гибридная комбинация AAC (PFA или песок) и HPC (High Performance Concrete), которая особенно привлекает производителей блоков, которые хотят расширить свое производство до полной строительной системы. Основная идея BCE заключалась в том, чтобы увеличить емкость AAC до 9 м для панелей пола и 12 м для панелей крыши.Установки состоят из блоков, уложенных друг на друга в вертикальном или горизонтальном направлении на втором этапе производства. Совместимость обеспечивается предварительным напряжением, выполняемым HPC-компонентом, в то время как AAC является «заполняющим» компонентом, составляющим основу конструкции. Предварительное напряжение предназначено для устранения прогиба собственного веса. Эта продукция хорошо адаптирована к условиям CAD / CAM применительно к конкретному проекту. Комбинация позволяет экономить материал, поскольку бетон используется для сжатия, а также для сдвига и закрепления арматуры.Три из четырех требований к стали в настоящей AAC-панели устранены. Как правило, со стороны AAC экономится 75% стали, в то время как 75% бетона и половина воплощенной энергии сохраняется (Aroni, 1993), если исходить со стороны чистого бетона (HDelements, полые плиты перекрытия ). Это указывает на то, что при переходе от бетона к BCE сохраняется половина выбросов углекислого газа. Сложность возникает при обращении с двумя разными видами бетона. Проект BCE все еще находится в стадии разработки.
КОРОТКАЯ НЕДВИЖИМОСТЬ
— воплощенная энергия AAC сравнительно низкая, 1.0 ГДж / м 3 (треть бетона).
— Плотность AAC варьируется от 275 (изоляционное качество) до 750 кг / м. 3 (структурное качество).
— Электропроводность (Вт / мК) изоляционных материалов на практике составляет 0,08 (275), 0,09 (350), 0,10 (400).
— Характеристическая прочность на сжатие (Н / мм 2 ) AAC составляет 2,3 (450), 3,0 (500), 5,0 (600), 10,0 (750) (рецепт песка).
— Характеристическая прочность на сжатие (Н / мм 2 ) AAC составляет 2,9 (460), 3.6 (600), 7,3 / 8,7 (750) (рецепт PFA).
— Коэффициент ползучести составляет 0,5 (750), 0,7 (600), 1,0 (500), 1,5 (450) (рецепт песка).
— Армированные панели на практике изготавливаются из подлинного AAC с пролетом до 6,0 / 7,2 м (песочная рецептура). Армированные элементы не могут быть изготовлены по подлинному рецепту PFA.
— Армированные панели производятся по гибридной технологии (HPConcrete / AAC: рецепт PFA или рецепт песка) с пролетом до 9,0 м (кровельные панели до 12,0 м).
— Модуль упругости (Н / мм 2 ) составляет 1200 (450), 1700 (500), 2500 (600), 4000 (750).
НАЧАЛО AAC
Все началось в 1923 году, когда шведский архитектор Дж. Аксель Эрикссон почти случайно обнаружил возможность использования процесса автоклавирования для стабилизации смеси сланца и негашеной извести, вспененной алюминиевым порошком. У него была очень ограниченная усадка в зависимости от влажности (в более ранней литературе (Ytong, 1942) утверждается, что его усадка равна нулю!). Патент был выдан в 1924 году, но потребовалось целых пять лет, до 1929 года, прежде чем изобретение было использовано в коммерческих целях, компания Yxhults stenhuggeri AB, производитель натурального камня, превратилась в производителя искусственных каменных блоков.Это был смелый шаг промышленника Карла Августа Карлена, который вскоре окупился, так как рынок с нетерпением ждал изоляционных материалов для каменной кладки. Швеция испытала серьезный дефицит энергии после Первой мировой войны. Ytong, как материал был назван в честь 1940 года, получил широкое признание благодаря сочетанию желаемых свойств, несущей способности, тепло- и звукоизоляции, огнестойкости и прочности, устойчивости к гниению влаги и насекомым. Усиленные компоненты производились после 1933/34 года (Ytong, 1954). Арматура в перемычках была залита обычным бетоном, который был покрыт с обеих сторон AAC (Ytong, 1942).
Насколько нам известно, это первый случай гибридной комбинации двух бетонов, идея, которая сейчас повторяется в ранее представленной системе BCE. И все же Ytong остался, прежде всего, производителем блоков.
Немедленный успех продукции Eriksson вскоре привлек конкуренцию внутри страны. В случае с Carlsro kalkbruk в Скёвде соревнования носили дружеский характер и основывались на обмене опытом. Конкурент имел репутацию производителя плоских пенобетонных блоков с 1924 года (Rönnow, 1948), а позже он инвестировал в автоклавы, следуя примеру Yxhult, чтобы стабилизировать продукт.Модернизированное производство AAC началось в 1932 году. Название компании было изменено на Skövde Gasbetong AB в 1943 году и снова на AB Durox в 1964/65 году, взяв название компании из продукта AAC. Имя Durox теперь связано с голландской группой, которая до сих пор производит AAC на более чем десяти заводах по всему миру, девять из которых находятся в Европе.
Гораздо более серьезная ситуация возникла, когда Siporit (с 1937 года Siporex) появился на шведском рынке в 1934 году (Rosenborg, 1998). Этот материал был изготовлен по рецепту, полностью основанному на цементе, который был разработан как альтернатива более старому составу из сланца и извести, используемому Эрикссоном и другими.Первоначальной целью Siporex было создание полной строительной системы, включая простые блоки и армированные изделия. Перемычки были доступны с самого начала, а через год (1935) — элементы крыши. Обычно доля армированных продуктов от Siporex превышала 60% (1964 г.), тогда как доля Ytong всегда была намного меньше. В европейском масштабе это соотношение оставалось низким, 16% в 1991 г. (Dubral, 1992), что указывает на то, что к AAC как материалу в целом подходили на довольно низком уровне. Считается, что текущая тенденция в значительной степени в пользу армированного материала, составляющего компоненты законченных строительных систем, более высокого уровня подхода.Кроме того, нынешняя архитектура способствует свободе выбора компонентов, которые предназначены для проектирования, помимо любых стандартных размеров.
Датская группа H + HA / S (Henriksen og Henriksen Aktieselskab) была образована в 1937 году. Позже она объединилась с британской компанией Celcon Ltd. и в настоящее время расширяется в Восточной Европе за счет выкупа производственных мощностей. где рецепты PFA были созданы после Второй мировой войны. Компания Celcon начала использовать PFA для замены кремнистого песка в своих продуктах уже после 1955 года.
Распространение технологии AAC по всему миру указывает на то, что рынок созрел для этого вида продукции и что сохранение патентных прав действительно было трудным. Ytong AB долго пыталась это сделать, выступая против Siporex AB, что привело к соглашению, основанному на modus vivendi. Тем временем другие производители, такие как H + H A / S, попробовали свои удачи на рынке и добились многолетнего успеха.
ИНИЦИАТИВА ЕВБЕЛИ
Другой рецепт изготовления AAC, третий из появившихся и, вероятно, вдохновленный, как и Siporex (Rosenborg, 1998), немецким материалом Mikroporit, был разработан в технических университетах Аахена и Штутгарта после 1942 года (Schramm, 2005). Более чем вероятно, что источником вдохновения послужил патент Siporex 1937 года. Были ли права на самом деле нарушены в условиях войны, все еще остается открытым вопросом. Но исследователи, безусловно, знали о чувствительности традиционных деревянных полов в результате военных действий — в 1942 году бомбардировки немецких городов начали вызывать разрушительные огненные ураганы, вызванные широким использованием древесных материалов в зданиях, особенно в конструкциях полов, начиная со средневековья. вплоть до 1935 г. (Берг, 2006).(Некоторые конструкции крыш все еще сделаны из дерева, например, в Скандинавии.) Стены и дымоходы обычно были кирпичными, которые остались стоять после того, как исчезло все, что могло гореть (Friedrich, 2002). В условиях войны был сделан вывод, что новый строительный материал должен быть огнестойким и изготавливаться из простых материалов с минимальной нагрузкой на ресурсы. Это полностью современный аспект, важный в наше время, когда по причинам климата мы должны отдавать предпочтение эффективным решениям в области поставок строительных материалов, измеряемым каким-либо резким индексом ресурсов или энергии.
AAC имеет низкую внутреннюю энергию по сравнению с большинством других продуктов.
Йозеф Хебель, баварский подрядчик, пользующийся высокой репутацией с 1926 года, был проинформирован о новом материале, AAC, от мюнхенского генерала Германа Гислера, который организовал встречу с важными подрядчиками Южной Германии по запросу из Reichsregierung (L Hebel , 2008)! Некоторое время в 1941-42 годах J Hebel был приглашен для посещения новых заводов AAC (Siporex) в Прибалтике (Таллинн и Рига), чтобы узнать о производстве армированных панелей (Rosenborg, 1998).Это удивительная информация: не о том, что способный инженер был назначен на промышленный шпионаж, хотя и с согласия Швеции (Jönsson, 2009), а о том, что это произошло во время войны, когда немецкая промышленность, по мнению Фюрербефеля, была полностью ориентирована на воюющее производство. Фактически, это было явным преступлением — заниматься чем-либо, кроме самой цели войны. Очевидно, что внутренняя и государственная политика не совпадали! Какое-то общепринятое неповиновение, должно быть, характеризовало Wirtschaftsministerium, где такой человек, как Отто Олендорф, был открыт для долгосрочного планирования в отношении Германии, несмотря на запрет (Herbst, 1982). Неизвестно, была ли связь между Олендорфом и Гислером на самом деле, но это признак здравого смысла, что во времена Третьего рейха были хорошие люди, которые готовились к другим условиям, чем нынешние. Или они были так уверены, что война будет выиграна, так или иначе? Только 9 -го сентября 1943 г. опасная ситуация была изменена Führererlass, разрешившим строительство аварийного жилья для многих несчастных людей, пострадавших от бомбежек.Весьма вероятно, что производство ААС Хебелем в Меммингене, начавшееся в марте 1943 года, было частью этой программы. Йозеф Хебель расширил свой бизнес, приобретя в конце того же года заброшенный завод силикатного кирпича в Эммеринге, на котором были действующие автоклавы, готовые к эксплуатации. Его офис в Меммингене (с 1921 года) был разбомблен в 1945 году, незадолго до окончания войны. Затем он разработал свою продукцию в усиленных панелях, вырезанных из мягкого материала тонкой проволокой. Резка проволоки была старой технологией, использовавшейся е.
грамм. на сыр, но теперь подлежит патентной заявке Ytong (1942), (Byttner, 1968). Весьма вероятно, что Хебель знал об этом приложении.
Йозеф Хебель был способным инженером, но сам не изобретателем. Технология, которую он применил в производстве, начиная с 1948 года в Эммеринге, представляла собой мудрый выбор доступных процедур. Рецепт AAC был немецким, но технология армирования и резки пришла из Швеции. Первоначальные деньги поступили от помощи Маршалла Германии.Hebel специализировалась на армированных панелях и элементах, профиль которых близок к профилю Siporex. В 1961 году первый дом был построен компанией Hebel, а в следующем году было сформировано еще одно подразделение, Hebel House, которое сосредоточилось на жилых проектах по всей Германии. С тех пор Hebel поглотила заводы Siporex на нескольких рынках. Еще в 1980-х годах (Wittmann, 1992 / Pytlik & Saxena) количество производственных площадок у двух компаний было примерно равным, или 35. В 1994 году насчитывалось 45 заводов под названием Hebel. В 2002 году (Charleston RBJ, 2002) количество растений Hebel составляло 115, прирост в среднем на 4 новых растения в год. Фирма «Сипорекс» со временем была потеряна для Hebel. Успех марки AAC компании Hebel во всем мире является доказательством его высокого инженерного статуса в сочетании с превосходным менеджментом. Общее количество заводов в мире в 2004 г. превышало 300 (Budwell, 2004), из которых Hebel принадлежала 40%. Его имя само по себе стало брендом.
ДАЛЬНЕЙШИЕ ЭТАПЫ РАЗВИТИЯ
Материал AAC в сочетании со стальной арматурой образует строительную систему, которую можно использовать исключительно или в сочетании со сталью, бетоном, а иногда и деревом.В состав AAC были включены отходы (уже в 1950-х годах, на основе патентов 1930-х годов!), Такие как PFA (пылевидная топливная зола), класс F, заменяющая часть песка в коммерческих целях или являющаяся единственным источником кремнеземистого вещества, исключая процесс измельчения. Это экологически чистый шаг, который хорошо работает с более низкой плотностью. В настоящее время такие композиции пытаются использовать с армированными изделиями. Согласно имеющемуся опыту (Siporex), было невозможно заменить более 70% песка, чтобы избежать продольного растрескивания, но этот вывод ставится под сомнение другими производителями, такими как H + H Celcon.Один из способов избежать такого растрескивания — включить в рецепт кальцинированный оксид магния. Насколько нам известно, Hebel больше не использует PFA после серьезных проблем с испытательной лабораторией в 1986 году.
Производство цельных панелей до 30 м. 2 возможно с односторонним предварительным напряжением в вертикальном направлении. Такая технология вдохновлена разработкой Дж. Даля интегральных стен (Rosenborg, 1998). Система BCE представляет собой полутяжелую строительную технику — характерно, что она несет динамическую нагрузку, вдвое превышающую собственный вес, в то время как массивный бетон несет только половину.
Считается, что технология BCE помогает преодолеть некоторые недостатки традиционной AAC-технологии. Это довольно расточительно со сталью, как технология HD (не говоря уже о массивных бетонных конструкциях на месте) расточительна с бетоном. Этот материал не следует рассматривать как бесплатный товар в нашем современном мире из-за большого количества энергии, связанной с цементом, и жестких ограничений на использование природного гравия. Подобные ограничения, возможно, будут распространены на щебень, который теперь заменяет природный гравий на скандинавских рынках.И зачем разрушать природу, если это не абсолютно необходимо? В долгосрочной перспективе мы считаем, что промышленность сборных железобетонных изделий также должна будет приблизиться к технологии BCE. При любом подходе новая технология более эффективна, чем исходная.
Бо Г. Хеллерс, Бо Р. Шмидт, Автоклавный газобетон (AAC) — история легкого материала, — Материалы 5-й Международной конференции по автоклавному газобетону «Обеспечение устойчивого будущего», Быдгощ, Польша, 2011 г., — п.63-68.
Бетонный блокAac | Автоклавный газобетон
Что такое блок AAC? Блок из автоклавного газобетона (AAC) — это сборный, легкий и теплоизоляционный материал для зеленых зданий, который используется в качестве материала для стен и в качестве замены кирпичей, блоков CLC и т. Д. Благодаря сильной теплоизоляции блоки AAC также находят применение в специальных приложениях, таких как противопожарные стены, звуковые стены, черепица и т. д.Magicrete AAC Blocks производит эти продукты на своем современном заводе с использованием последних инноваций с использованием передовых технологий в Сурате под торговой маркой Magicrete AAC Blocks.
AAC используются более 90 лет по всему миру. Сооружения, построенные более 85 лет назад, все еще стоят.Однако для Индии это развивающийся продукт.
Когда был впервые разработан AAC? AAC был разработан в 1924 году в Швеции преподавателем архитектурных наук, который искал альтернативный строительный материал с такими же свойствами, как у дерева, такими как хорошая теплоизоляция, прочная структура, простота в эксплуатации и т. Д.и имеющий сопротивление огню и термитам.
Цемент, летучая зола и известь являются ключевыми ингредиентами для изготовления блоков Magicrete AAC Blocks. Они отверждаются паром, известным как автоклав. Благодаря оболочке из экологически чистого материала, эти продукты сертифицированы по системе зеленого рейтинга и помогают строителю получать кредитные баллы.
Является ли Magicrete AAC Blocks экологически безопасным и сертифицированным экологически чистым продуктом? Да. Magicrete AAC Blocks — это экологически чистый строительный материал. Продукты Magicrete AAC Blocks сохраняют и защищают драгоценные природные ресурсы земли, в отличие от кирпичей, которые поглощают верхний слой почвы.Блоки Magicrete AAC Blocks производятся из летучей золы — промышленных отходов тепловых электростанций. Во время производства энергия, потребляемая в производственном процессе, составляет лишь небольшую часть по сравнению с производством других материалов. Производственный процесс не выделяет загрязняющих веществ и не создает побочных продуктов или токсичных отходов. При установке стены практически не образуются отходы, и этот продукт потребляет очень мало воды. Во время утилизации блоки Magicrete AAC Blocks, являясь нетоксичным продуктом, не загрязняют воздух, землю или воду.Благодаря его ресурсоэффективности и материальному охвату, можно заработать большое количество кредитов в процессе зеленой сертификации, такой как LEED, GRIHA и т. Д.
помогают лучше обрабатывать и размещать блоки, что приводит к сокращению потерь и более быстрому завершению работы. Tongue & Groove обеспечивает автоматическое выравнивание стены, избавляя от необходимости проверять отвес. Это также снижает расход раствора и обеспечивает аккуратную стену с экономией времени и денег.
1. Ассортимент продукции • Первая компания AAC, которая предоставила комплексные решения для ограждающих конструкций. • Материал 1-го класса, прочность на 33% выше • Маркировка ISI
Целесообразно ли использовать блоки Magicrete AAC Blocks в высотных зданиях? • Да. Будучи легкими (1/3 веса глиняного кирпича), блоки Magicrete AAC Blocks настоятельно рекомендуются для высотных зданий и помогают снизить общую статическую нагрузку на конструкцию, что напрямую помогает в структурной экономии до 20%.
Прочность блоков Magicrete AAC Blocks соответствует стандарту IS: 2185-Part III, который является абсолютно безопасным и достаточно прочным для использования в любых ненесущих стеновых конструкциях. Иногда наблюдается появление трещин в стене блока AAC.В чем может быть причина?
Прогиб балки, оседание грунта в сторону, неравномерное размещение блоков при строительстве — некоторые причины растрескивания стен. Структурные сдвиги из-за теплового расширения или изменения содержания влаги или движения влаги. Чтобы преодолеть это, необходимо использовать блоки AAC с задержкой до достижения равновесного содержания влаги. Для этого блоки AAC необходимо хранить 10-15 дней до нанесения.Прогиб балки, оседание грунта в одну сторону, неравномерное размещение блоков при строительстве — другие причины. Трещины появляются во всех типах бетона, в том числе и в глиняном кирпиче. Используя некоторые строительные методы и надлежащее качество изготовления, мы можем минимизировать эти трещины. Выравнивание блоков должно быть точным и должно проверяться с помощью спиртового уровня, желательно длиной 2 метра. Первому курсу блоков нужно дать достаточно времени для схватывания, и на это нужно дать не менее 24 часов. Каркасной конструкции необходимо дать достаточно времени, чтобы она затвердела и осела, чтобы можно было заметить любые изменения в структуре из-за ее движения.Контрольный шов толщиной 10 мм необходимо наносить через каждые 3 метра от низа до верха стены. Управляющий шарнир должен быть заполнен упругим материалом или стержнем-подкладкой, который легче сжимается.
И запечатать конопаткой. Расширительные швы должны быть выполнены после каждого 3-го курса и помещены между промежутками контрольного шва. Связующая балка должна быть сделана через каждые 1200 мм по высоте с использованием армирования двумя стержнями MS по 8 мм, связанными сталью 6-8 мм с зазором 6–9 дюймов. Минимальная толщина соединительной балки должна быть 3 дюйма с бетонным покрытием 15-20 мм по сторонам.Связующий луч должен быть прерывистым в контрольном соединении. Стальные стержни необходимо заделать в колонну в 5-6 раз больше ее диаметра и зафиксировать с помощью безусадочного высокопрочного раствора. Растворную смесь для заливки связующего бруса можно взять цемент: песок в соотношении 1: 4. Назначение соединительной балки — придать стене устойчивость и прочность. После каждого 3-го ряда необходимо использовать стяжки между блоком и бетонной колонной.
Вы можете использовать блоки AAC для строительства всех типов стен между двумя колоннами в каркасной конструкции, такой как перегородка, навесная стена, балконная стена, ограждающая стена.
Испытание на водопоглощение при 24-часовом погружении в воду не указано в стандарте блоков AAC IS-2185, часть 3. Рекомендуется испытать теплоизоляционные элементы стен, такие как AAC, на капиллярное водопоглощение.AAC должен превосходить капиллярное водопоглощение по сравнению с обычным кирпичом. Подобно кирпичу из красной глины, AAC не рекомендуется использовать в фундаментах и во влажной среде, поэтому испытание на водопоглощение не применимо для AAC.
А как насчет норм поломки и выкрашивания блоков AAC? По разным причинам блоки могут быть повреждены во время транспортировки или погрузочно-разгрузочных работ на объекте. Его можно использовать как полуобрезанные блоки после обрезки по размеру. Пункт 8.1.1 индийского стандарта IS-2185, часть 3 допускает небольшие трещины и небольшие сколы размером не более 25 мм и не может считаться основанием для отклонения.
Блоки AAC бывают разных размеров.Длина 650, 600 мм. Высотой 250,240,200 мм и толщиной 75,100,125,150,200,225 мм.
Можем ли мы использовать блоки AAC в Foundation.Нет, блоки AAC не рекомендуется использовать в фундаменте и в местах с повышенной влажностью.
В чем ее недостаток? Его водопоглощение выше, чем у кирпича из красной глины при погружении в воду на 24 часа. Поэтому в некоторых случаях, например, в фундаменте, в основной яме и в бетонных резервуарах для воды, его не рекомендуется использовать.
Да, у AAC есть теплоизоляционные свойства, его теплопроводность составляет 1/5 глиняного кирпича.Таким образом, AAC сохраняет тепло в течение более длительного периода и снижает затраты на электроэнергию за счет кондиционирования воздуха или обогревателя помещения.
Есть ли какой-либо стандартный индийский кодекс? Да. IS-2185 Часть-3 — это стандартная спецификация Индии для блоков AAC.
Нет, AAC не загорается, а его огнестойкость составляет 4 часа для 8-дюймовой стены.
Что требуется, если мы хотим проверить прочность на сжатие блоков AAC на месте?Вам понадобится машина для испытаний на сжатие малой мощности на 250 кН и отрезной станок. Машины большой мощности 2000-3000 кН использовать не рекомендуется. Следуйте инструкциям по тестированию, указанным в IS-6441 Part-5.
Когда мы проверяем плотность, она составляет 700-750, но вы утверждаете, что она находится в пределах 551-650 кг / м3.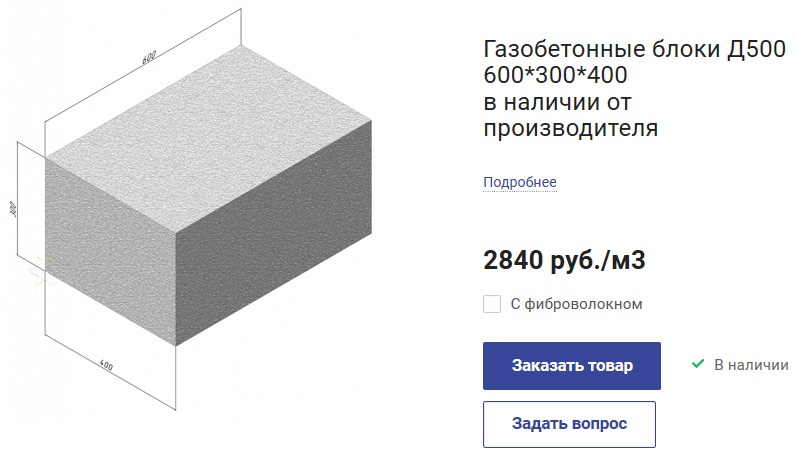
Есть разница между плотностью при сушке и плотностью в сушильном шкафу. В нормальных условиях блоки AAC имеют определенное содержание влаги, поэтому их плотность выше, но для целей тестирования мы сушим образец при 105 ° C в течение 4-5 дней до достижения постоянного веса, а затем мы получаем плотность без содержания влаги или плотность в сухом состоянии.См. IS-6441 Часть-1 для проверки плотности сухой печи
Насколько прочен AAC в различных климатических условиях? Автоклавный газобетон чрезвычайно прочен. Он не гниет и не гниет, как дерево или другие органические материалы. Он не ржавеет, как металл. Термиты и другие вредители его не едят.AAC не сгорит. Миллионы крошечных ячеек в AAC амортизируют здания от большой силы, предотвращая прогрессирующее обрушение. AAC выдержала землетрясения в Японии, низкие температуры северной Европы, суровый соленый воздух французской Риверии и пожары на склоне холмов Сан-Франциско.
№Конструкция AAC обеспечивает прочную монолитную стеновую систему с закрытой несвязанной ячеистой структурой. Внешняя отделка дополняет эту структуру, обеспечивая здоровый баланс между влагостойкостью и диффузией пара. Положительное давление системы кондиционирования выталкивает водяной пар через стены, предотвращая проникновение влаги извне.
Целесообразно ли использовать блоки Magicrete AAC Blocks в высотных зданиях? Да. Будучи легкими (1/3 веса глиняного кирпича), блоки Magicrete AAC Blocks настоятельно рекомендуются для высотных зданий и помогают снизить общую статическую нагрузку на конструкцию, что напрямую помогает в структурной экономии до 20%.
Нет. Несмотря на то, что они кажутся похожими, это совершенно разные продукты. Прочностные параметры ХЖК — 25 кг на кв. См. В то время как прочность блока AAC составляет от 35 до 40 кг на кв. См. CLC нельзя разрезать проволокой, а края не точны и легко повреждаются.CLC отверждают обычными методами, и AAC готов к использованию с достаточной прочностью на стадии постпроизводства благодаря усовершенствованному процессу отверждения в автоклаве.
Можно ли использовать его для несущих конструкций? Да. Вы можете использовать блоки Magicrete AAC Blocks для несущих конструкций до 3 этажей
№Замачивание и смачивание AAC не требуется. Достаточно небольшого увлажнения.
Сколько в кубометре AAC?42 блока Magicrete размерами 600 X 200 X 200 мм составляют Кончить.
Поставляете ли вы или рекомендуете какие-либо специальные добавки для лучшего склеивания блоков AAC? Да, делаем. Мы производим и поставляем клей Magicbond для блоков AAC.
Машина для испытаний на сжатие (CTM) должна быть предпочтительно (250-500 кН), должна быть гидравлической и позволять считывать предельную нагрузку с максимальной погрешностью \ m (+/-) 2.0%. Норма нагрузки должна составлять от 0,5 до 2 кгс / кв. См таким образом, чтобы выход из строя происходил за 30 секунд. Сушильная печь
Какова процедура проверки прочности на сжатие блоков AAC? • Образец должен быть пересушен при 105 +/- 5 градусов Цельсия в течение 4 часов или может быть повторен несколько раз для достижения влажности образца от 8% до 12%. • Поверхности образцов должны быть равны прижимной поверхности СТМ.• Направление нагрузки должно быть перпендикулярно направлению подъема массы во время производства.
• Норма нагрузки должна составлять от 0,5 до 2 кгс / кв. См таким образом, чтобы отказ произошел в течение 30 секунд.
• Блоки Magicrete AAC: Размеры: Блоки Magicrete AAC доступны в следующих размерах / толщине / длине и высоте: Стандартные размеры блоков: Толщина: 75/100/125/150/200/225 мм Длина: 625/600 мм Высота: 240/200 мм
Сколько блоков потребуется на 100 кв.фут кладка? • Для 100 Sft. (9,29 кв.м) кладка / площадь стены = 63,15, т.е. 63 шт. (Для блоков высотой 240 мм)
• Для 100 Sft. (9,29 кв.м) кладка / площадь стены = 72,52, т. Е. 73 номера (для блоков высотой 200 мм)
• Требуются блоки стандартных размеров с учетом толщины швов цементного раствора 10 мм.
• Легкий вес • Экономически эффективным • Высокая теплоизоляция. • Огнестойкость • Звукоизоляция • Устойчивость к влаге, вредителям и плесени • Устойчивость к землетрясениям • Экологичность
.