Свойства, виды и марки керамзитобетона
Керамзитобетон – строительный материал, основными составляющими которого являются пористый керамзит и цемент, производится путем смешивания следующих ингредиентов: цемент, песок и пористый керамзит в соотношении 1-2-3 соответственно.
Для приготовления используются гранулы керамзита диаметром в пять миллиметров. Бетон керамзитовый производится с соблюдением ГОСТ, имеет преимущество над легкими типами бетона по тепло- и звукоизоляции, а также по стойкости к влаге и химическим реактивам. Использование в строительстве этого материала позволяет возводить стены домов в четыре, пять раз по времени быстрее.
Свойства керамзитобетона
К основным характеристикам и свойствам бетона из керамзита относятся:
- Прочность.Материал обладает свойством сопротивления к различным внешним силам, не разрушаясь. Предел его прочности при сжимании составляет 20 МПа, этот показатель проверятся путем давления грузом в 80 тонн на эталон, изготовленный в виде куба с длиной ребра в 20 см.
- Плотность. Она характеризуется отношением величин массы к объему материала. Плотность керамзитобетона находится в пределах от 500 до 1800 кг/м³. Качество керамзитобетона характеризуется его плотностью, чем она выше, тем он прочней. Поры в изделии появляются в процессе его изготовления путем испарения лишней воды, при твердении цемента, при недостатке цемента.
- Пористость керамзитобетона определяется отношением величин объема пор к объему всего материала. Какой бы плотностью не обладал керамзитобетон, он всегда имеет поры, которые условно дополняют его плотность до 100%-го уровня.
- Водостойкость. Керамзитобетон обладает свойством противостояния воде, не подвергаясь разрушению. Водостойкость определяется опытным путем, для этого берутся два эталона из керамзитобетона, которые подвергаются исследованию: первый экземпляр подвергается давлению прессом в сухом виде для установления уровня его прочности, второй эталон вначале помещают в воду до его полного насыщения, после чего подвергают его разрушению с помощью пресса.
В воде составляющие бетона утрачивают прочность взаимодействия между собой, что приводит к уменьшению уровня прочности эталона изделия. Для бетонного изделия из керамзита коэффициент, характеризующий размягчающуюся способность материала, составляет свыше 0,8, он равен отношению прочности эталона, напитанного водой, к уровню прочности эталона сухого вида.
- Теплопроводность. Эта свойство показывает способность передавать тепло от прогретых участков к холодным. Теплопроводность изделия выше, чем у кирпича строительного и меньше почти в двести пятьдесят раз, чем у стальных конструкций. Использование керамзитобетона в строительстве может сократить потери тепла до 70%.
- Огнестойкость. Керамзитобетон обладает высоким уровнем огнестойкости, он может выдерживать температуру, превышающую тысячу градусов достаточно длительное время. При высоких температурах изделие не подвергается трещинам и разрушению.
- Морозостойкость. Вода, попадая в поры изделия, плотно заполняет их и замерзает, а также подвергается расширению. При этом бетон из керамзита может выдержать не однократное замерзание и оттаивание воды, не подвергаясь разрушению и сохраняя уровень своей прочности.
Виды керамзитобетона
По форме выпуска:
- Блок
- Панель
- Плита
По плотности:
- Поризованный керамзитобетон:
- Теплоизоляционный – 600-800 кг/м³
- Конструкционно-теплоизоляционный – 800-1200 кг/м³
- Конструкционный – 1500-1800 кг/м³
По сфере применения:
- Блок стены
- Блок фундамента
- Блок перегородки
- Блок вентиляции
Марки керамзитобетона
Керамзитобетон представлен марками от М50 (используется для строительства перегородок и несущих конструкций) до М300 (используется при строительстве инженерных сооружений).
Керамзитобетон: характеристики, сфера использования — Производство и доставка бетона Логойск
При строительстве сооружений как жилого, так и нежилого помещения, вопрос, вопрос материала для строительства стен вызывает вопросы. Чему отдать предпочтение: проверенным десятилетиями материалам или новым полимерным многослойным? Или выбрать промежуточный материал, как керамзитобетон, сочетающий прочность бетона и современными добавками.
Сегодня керамзитобетон снова возвращается на российский строительный рынок, вместо некачественных составов предлагая прочный и недорогой материал, изготовленный по немецким технологиям.
- Портландцемент – имеет хорошие вяжущие свойства. Затвердевает при добавлении воды, на открытом воздухе скорость затвердевания увеличивается.
- Кварцевый песок – этот материал придает керамзитобетону прочность, влагостойкость, устойчивость к химическим веществам.
- Керамзит – за счет использования мелкогранулированного керамзита, блоки получаются легкими, удобными в транспортировке и установке. Керамзит обеспечивает пористую структуру керамзитобетона, что способствует регуляции влаги и сохранению тепла.
Следует отметить, что свойства керамзитобетона меняются в зависимости от пропорций компонентов, что влияет и на использование блоков в строительстве:
- Теплоизоляционный
- Конструктивный
- Теплоизоляционно-конструктивный
- Плотный (с наибольшим содержанием цемента).
- Прочность – керамзитобетон используется при строительстве в сейсмоопасных районах.
- Плотность – придает материалу теплосберегающие свойства, усиливает звукоизоляцию.
- Небольшой вес при крупном формате, удобство при транспортировке, укладке, меньшие затраты труда.
- Блоки используются и как несущая конструкция, и как теплоизоляция.
- Не токсичен, экологичен.
- Долговечность и морозоустойчивость. Керамзитобетон имеет несколько разновидностей – от 25 до 50 циклов размораживания.
- Высокий уровень пожаробезопасности – при горении керамзитобетон не разрушается в течение первых 7 часов, кроме того, не выделяет ядовитые продукты горения.
Однако керамзитобетон характеризует не только полезные свойства, есть и ряд недостатков:
- Небольшая ударная прочность, пористая структура делает блоки более хрупкими, по сравнению с цементно-песчатными блоками.
- Блоки очень тяжело подвергаются резке – изменить форму можно только инструментом с алмазными дисками.
- Поверхность керамзитобетона нуждается в выравнивании и обработке перед финишной облицовкой.
Свойства и характеристики керамзитобетонных блоков
Один из наиболее перспективных стройматериалов сегодня – это керамзитобетонные блоки (ещё их называют керамзитные блоки), которым удалось полностью преобразовать стандартные понятия о строительстве и материаловедении. Этот лёгкий и пористый материал обладает высочайшими прочностными характеристиками, при этом совмещая в себе достоинства древесины и натурального камня. Характеристики керамзитобетонных блоков в плане экономичности использования и скорости возведения стройобъектов из них превосходят большинство современных стройматериалов. Удобные для проведения монтажа форма и крупные размеры керамзитных блоков заметно сокращают сроки постройки сооружений различных категорий, ощутимо минимизируют бюджет перепланировки или нового строительства.
Действительно, с появлением керамзитобетонных блоков был решён большой диапазон строительных задач, как сокращение бюджета, рост производительности, безопасная эксплуатация, надежность и максимальная продолжительность службы зданий. Производимые исключительно из природных компонентов керамзитобетонные блоки не создают в помещении опасного для проживания людей или выполнения ими служебных обязанностей фона, не выделяют никаких токсичных компонентов в окружающую среду. В строениях, для возведения которых использовались керамзитобетонные блоки, в любой сезон года царят комфортные условия. Керамзитобетонные блоки пригодны для постройки жилых и прочих строений в любой из климатических зон.
История керамзитобетонных блоков берёт начало во времена существования Советского Союза (в 60-тые годы). В тот период активно возводились панельные дома, и в строительстве довольно широко применялся пористый керамзит в роли материала-наполнителя.
Керамзитобетонные блоки включают в себя воду, цемент, а кроме того, вспененную и затем обожженную глину. Рецептурное изменение пропорций составляющих его веществ влечет за собой и некоторое изменение свойств керамзитобетононных блоков, а точнее их прочности и плотности. Например, чем больше в керамзитной смеси цемента, тем крепче и прочнее получится керамзитобетонный блок. Правда, есть одно «но»: пропорционально его прочности увеличится и теплопроводность. Это значит, что стены станут более холодными.
Керамзитобетонные блоки стали достойной заменой использовавшихся ранее шлакоблоков. Процесс изготовления и их состав практически идентичны керамзитобетонному, однако в качестве заполнителя в них использовался так называемый доменный шлак, в результате чего строительные блоки имели низкий прочностный коэффициент и слабую морозостойкость. Стены из такого рода материала служили весьма недолго. Столь серьёзный недостаток доменного шлака исправил заменивший его керамзит. Кроме того, этот наполнитель является ещё и более экологичным. В Европе блоки из керамзитобетона даже называют «эко-блоками».
Спустя некоторое время возникла некоторая проблема с дефицитом керамзита, разрешившаяся путем разработки и последующего внедрения в производственный процесс аналоговых материалов — вспененных бетонов. Пено- и газобетон заняли свою нишу среди подобных им строительных материалов.
Минусом же использования бетонов является невозможность возведения из них надёжных несущих стен. Керамзитобетон на их фоне — конструкционный материал, обладающий высоким уровнем плотности на сжатие. Кроме того, керамзитобетонные блоки используются в качестве утеплителя, так как имеют крайне низкий коэффициент теплопроводности.
Уникальность свойств керамзитобетонных блоков основывается на специфике их производства. Основным ингредиентом для изготовления керамзитобетонных блоков является экологически чистый керамзит. Вспененная, прошедшая через процедуру обжига глина, из которой делается керамзит, по структуре похож на застывшую пену. Внешняя оболочка, что покрывает каждую глиняную гранулу, дает ей весьма высокую прочность, тем самым преобразуя керамзит в главный вид пористого заполнителя не только в керамзитобетонных блоках. По своему назначению и физико-техническим характеристикам керамзитобетонные блоки делятся на конструкционно-теплоизоляционные, конструкционные и теплоизоляционные. Для производства теплоизоляционных керамзитобетонных блоков, имеющих малую плотность, используется керамзит самых крупных и легковесных фракций (2-4см и более). Он обжигается по специальному режиму, обеспечивающему повышенное вспучивание гранул и формирование крупных пор. Подобные гранулы обладают плотностью 150—200 килограмм/м3.
Применение керамзитобетонных блоков, что имеют показатели прочности, близкие к натуральному камню, не ограничивается какими бы то ни было технологическими рамками. Причём цена керамзитобетонных блоков является более чем доступной. С их помощью возводятся сегодня несущие конструкции, а также лёгкие перегородки между комнатами (вес керамзитного блока при его объёмности небольшой, начинается с 11 кг.), их широко применяют и в монолитном домостроении в роли стройматериала для заполнения каркаса. Пожалуй, единственным на сегодня ограничением для использования керамзитобетонных блоков становится возведение фундамента, который требует повышенной плотности и прочности стройматериала. А вот стены из керамзитобетонных блоков отличаются превосходнейшей прочностью. При этом керамзитобетонные блоки без особого труда можно штробить и в отличие от того же бетона или кирпича в керамзитобетонные стены без усилий забиваются гвозди, в них идеально прокладывается скрытая электропроводка.
В последние годы большинство строителей охотно переходят на применение прогрессивных керамзитобетонных блоков, поскольку на практике убедились в их технологичности, практичности, прочности и долговечной износостойкости. Отличающиеся легким весом керамзитобетонные блоки дают возможности выстраивать презентабельные и вместе с тем прочные здания даже на ленточных малозаглубленных, либо столбчатых фундаментах.
Керамзитобетонные блоки преимуществаК основным преимущественным качествам керамзитных блоков можно отнести:
керамзитобетонные блоки размеры :размер керамзитобетонных блоков идеальны для скоростного монтажа. Каждый керамзитобетонный блок намного крупнее стандартного кирпича, что значительно облегчает и ускоряет процесс строительных работ, позволяет экономично использовать раствор при выполнении кладки. При возведении стен из керамзитобетонных блоков раствора нужно примерно в 2,2 раза меньше, а скорость монтажа бывает раз в 5 выше, масса же метра кладки бывает меньше в 1,5 раза;
керамзитобетонные блокои вес :вес керамзитобетонного блока полнотелого стандартного размера 390 х 190 х 188 мм. примерно 26 кг., вес щелевого керамзитобетонного блока размером 390 х 190 х 188 мм. от 17 кг., вес перегородочного (толщина 90 мм.) полнотелого керамзитобетонного блока равен примерно 14,5 кг., а вес щелевой перегородки керамзитобетонного блока составляет 8-9 кг.. Столь малый вес керамзитобетонных блоков создаёт удобство во время транспортировки и при монтаже, что исключает необходимость в обустройстве дорогостоящего массивного фундамента;
керамзитные блоки паропроницаемость :благодаря ей не образуется конденсационная влага и не наступает преждевременное старение как самих керамзитобетонных блоков, так и материалов отделки,
керамзитобетонные блоки огнеустойчивость:характеристики керамзитобетонных блоков придают им хорошую сопротивляемость горению, которая обуславливает применение керамзитобетонных блоков как в частном, так и в индустриальном строительстве сооружений любой категории;
керамзитобетонные блоки морозостойкость :морозостойкость керамзитобетонных блоков составляет 50 циклов последовательной шоковой проморозки и оттаивания, кроме того, стоит отметить сопротивляемость разного рода негативным атмосферным, а вместе с тем химическим воздействиям;
керамзитобетонные блоки теплоизоляционные свойства :керамзитобетон, постепенно накапливая энергию солнца, тепло отдаёт медленно и равномерно, что защищает от перегрева летом и отлично сохраняет тепло в зимнее время, сделанные из него стены «дышат», поддерживая внутри помещения оптимальную влажность;
экологическая безопасность керамзитобетонного блока:обоснована использованием исключительно чистого в экологическом плане натурального сырья;
блоки из керамзитобетона замечательная шумоизоляция :показатели изоляции керамзитобетона дают возможность обойтись без монтажа дополнительных систем утепления и защиты от извне поступающих звуков;
Керамзитобетонные блоки цена :благодаря по-настоящему низкой стоимости керамзитных блоков, этот материал год от года становится всё востребованнее. Посмотреть цены на керамзитобетонные блоки с доставкой на объект.
При постройке стен из керамзитных блоков вам потребуется раза в два меньше раствора, нежели при строительстве кирпичных стен. Скорость же монтажа стен из керамзитобетонных блоков, наоборот, значительно больше — более чем в 4-ыре раза!
Как уже было замечено, керамзитобетонные блоки обладают замечательными теплоизоляционными свойствами. При применении керамзитобетона тепловые потери можно сократить более чем на семьдесят пять процентов. Доказательством этого служат множественные испытания в научно-исследовательских институтах, которые производились над блочным заполнителем — керамзитовым гранитом. В итоге, характеристики керамзитобетонных блоков в плане теплоизоляции обеспечивают им большую популярность в сравнении с иными строительными материалами, как при строительстве в теплых, так и в холодных условиях климата.
Одной из самых важных характеристик керамзитобетонных блоков стала его воздухопроницаемость, то есть керамзитобетонные блоки могут «дышать», тем самым регулируют в здании влажность воздуха.
Стройобъекты, возведённые из блоков керамзитобетонных, отличаются повышенной долговечностью и не нуждаются в специальном уходе. Керамзитобетонные блоки не склонны к появлению ржавчины, не горят и не гниют.
Качества керамзитобетонных блоков дают им ряд преимуществ и на фоне других видов стройматериалов, к примеру, кирпича:
Удельный вес керамзитных блоков ниже, чем вес кирпичей в два с половиной раза.
Всего за одну смену опытный каменщик может выложить из керамзитных блоков стену, которая в три раза превышает по объему кирпичную кладку.
Обычных размеров керамзитный блок может заменить семь стандартных кирпичей.
Стоимость керамзитобетонных блоков и себестоимость проведения строительных работ в сравнении с использованием стандартного кирпича ниже процентов на 30-40.
Также стоит отметить, что возможно размещать в теле стены скрытый каркас за счет наличия особых сквозных пустот в материале, тем самым во много раз увеличивая ее несущую способность.
Керамзитобетонные блоки выполнение кладкиКладка стен из керамзитных блоков не требует каких-либо особых конструктивных решений и практически не отличается от процедуры кладки стен из обычного керамического кирпича, поскольку так же выполняются тычковые и ложковые ряды с соблюдением перевязки. Керамзитобетонный блок неплохо сочетается с другими, а кроме того, с металлическими и железобетонными изделиями. За счёт малого веса, керамзитобетонные блоки обладают возможностью снижения тяжести железобетонных конструкций большого размера, что значительно удешевляет обустройство фундамента.
Кладку стен из керамзитных блоков начинают с углов дома и ведут рядами по периметру. До того, как установить 1-вый ряд, следует позаботиться о гидроизоляции, для этого на фундамент в 2 слоя укладывается рубероид. Затем основание тщательно выравнивается. На гидроизоляцию укладывается выравнивающий песчано-цементный раствор, чья толщина не должна превышать 30-ти миллиметров, сверху же кладутся керамзитобетоные блоки.
При выполнении кладки этого вида молоток каменщика не понадобится, вместо него следует запастись увесистым резиновым молотком. Остальной набор будет стандартным. Только вот армировать стены из блоков надо не кладочной сеткой, а особой арматурой с диаметром около 10 мм. Арматуру попросту укладывается на законченный кладочный ряд во всю стеновую длину по периметру и кладку начинают со следующего ряда непосредственно по арматуре, которую желательно укладывать примерно через каждые три ряда керамзитобетонных блоков, соответственно с чем следует делать перевязку тычковыми ложковых рядов. При этом стена, имеющая толщину в один керамзитобетонный блок – 39см, соответствует стены в полтора кирпича толщиной, высота же керамзитного блока соответствует высоте 2-ух полуторных кирпичей, тем самым процесс возведения стены из керамзитобетонных блоков значительно облегчается и убыстряется.
При выполнении кладки стен надо учитывать то, что керамзитобетонным блокам свойственна небольшая конусность, потому, укладку буквально каждого из них желательно проверять с помощью строительного уровня.
Есть еще одна важная особенность. Кладку стен внутри нужно производить совместно с наружными, точно также пропуская по всему ряду арматуру. Во избежание мостиков холода блочный торец, который заходить будет в наружную стену, следует изолировать пенопластовым прямоугольником толщиной в 40-50 миллиметров.
Кладку стен из керамзитобетонного блока ведут согласно схеме, осуществляя цепную перевязку вертикальных швов. При выполнении кладки в два керамзитобетонных блока, вертикальные и наружные швы перевязывают не меньше, чем на сотню миллиметров. Выполняя работу необходимо следить за точным соблюдением высоты рядов. Это делается с помощью лазерного уровня или же натянутого шнура.
Армопояс
Когда кладка стен из блоков керамзитобетона окончена, по верху стены следует залить армопояс – особую железобетонную конструкцию, призванную принимать на себя нагрузку всей стропильной системы и не давать стенам разрушаться.
Керамзитобетонные блоки отделкаБлагодаря своим уникальным качествам керамзитобетонные блоки совместимы с любой облицовкой, применяемой в настоящее время. За счёт этого возможно выполнение абсолютно любой композиции экстерьера. Респектабельность зданию из керамзитобетонных блоков может придать облицовка с помощью искусственного камня или декоративного кирпича, оштукатуривание, обшивка блок-хаусом, различными фасадными панелями и т.д.
На сегодняшний день российский стройрынок способен предложить вам огромное разнообразие керамзитобетонных блоков, в числе которых и те, что имеют основу в виде керамзитного гравия мельчайших фракций, дающего возможность использовать такие блоки не для одного лишь малоэтажного строительства, но и в иных стройсферах.
Однако из-за «кустарей-умельцев», коих по мере возрастания спроса на этот материал появляется всё больше, керамзитоблоки порой обзаводятся «дурной» славой. Они изготавливают стройматериал едва ли не на дому, нарушая рецепт и саму технологию производства керамзитобетона, что влечёт за собой потерю качества и прочности получаемых изделий.
Лишь произведенный в соответствии с ГОСТовскими нормами керамзитобетонный блок, становится по-настоящему прочным материалом, который в этом плане превосходит пенобетонные блоки по конструкционным и теплоизоляционным характеристикам, не говоря уже о цене керамзитных блоков и конечной стоимости возводимого сооружения, где керамзитобетонным блокам нет равных.
Доказательством замечательной прочности керамзитобетонных блоков служат многоэтажки (3-ёх, 5-ти, 12-ти этажные), которые построены во многих городах государств бывшего СССР. В них керамзитоблок использовался не исключительно в роли заполнителя, но и как материал для постройки несущих стен.
Почему при подборе оптимальных блоков из керамзитобетона предпочтение следует отдать компании Атрибут-С? Наша компания предлагает своим покупателям керамзитобетонные блоки высокого качества, производимые из лучших экологически чистых материалов. В результате характеристики керамзитобетонных блоков (звуко- и теплоизолирующие качества, вес керамзитных блоков, прочность и т.д.) соответствуют высокому качественному уровню, гарантируя долговечность и беспроблемность эксплуатации строений, при возведении которых будет использован данный материал. Кроме того, мы осуществляем не только продажу, но и доставку керамзитобетонных блоков любыми партиями по Москве и всей Московской области. А самое главное: выгодная цена на керамзитобетонные блоки в нашей компании не может не устроить даже самого бережливого хозяина.
Чтобы заказать керамзитобетонные блоки, свяжитесь с нами по телефону 8-499-340-35-47, либо отправьте заявку на наш электронный адрес
Этот e-mail адрес защищен от спам-ботов, для его просмотра у Вас должен быть включен Javascript
, и вам оперативно ответят. Вы сможете задать все интересующие вас вопросы, получить консультацию по стоимости необходимого вам объёма керамзитобетонных блоков и их доставке, уточнить срок поставки блоков на объект, что, как правило, составляет не более 1 — 2 дней с момента принятия заказа. Мы работаем для вас без праздников и выходных, каждый клиент для нас дорог и может рассчитывать на индивидуальный подход.
КЕРАМЗИТОБЕТОННЫЕ БЛОКИ ПОДРОБНО…
ГОСТ 6133-99 на керамзитобетонные блоки
Цена на керамзитобетонные блоки, купить керамзитобетонные блоки здесь
Керамзитобетонные блоки: характеристики и особенности материала
01.11.2016Керамзитобетон – строительный материал, занимающий нишу между кирпичом и различными легкими блоками: газо-, пенобетон и др. Он разделяет некоторые преимущества кирпича – прочность и длительную службу. От пористых бетонов у него: габаритность, низкая теплопроводность, малый вес.
Керамзитные блоки появляются в результате смешения между собой цементного раствора, керамзитового гравия и песка (из керамзита). Различные фракции гравия (5-10 мм) гарантируют различную прочность стройматериала и его теплопроводность. Но приходится выбирать между прочностью и возможностью сбережения энергии. Если гравий крупный, то это гарантия теплых и недостаточно прочных стен, и наоборот.
Технические характеристики
- Замеры. Стандартный керамзитобетонный блок – 18,8х19х39 см и 18,8х9х39 см. Допустимо, чтобы габариты были больше/меньше на 1-2 см. Блок с шириной в 19 см предназначен для возведения стен, с 9 см – для перегородок.
- Вес: 10-23 кг.
- Разновидности по качеству. Также блоки делятся на рядовые и лицевые. Р. имеют более низкое качество, поэтому используются только с последующей внешней отделкой. Л. же не нуждаются в дополнительной обработке фасада плиткой или штукатуркой.
- Наличие пустот. Полнотелые блоки прочные и более тяжелые, тогда как пустотелые – легкие и имеют повышенные энергосберегающие качества, но при этом менее прочные. Пустоты могут быть сквозными или несквозными.
- Прочность – надежность всей строительной конструкции. Материал считается достаточно прочным, но все зависит от фракции гравия, которая входит в состав того или иного блока.
- Плотность. От этой характеристики зависят энергосберегающие и акустические свойства. Фракция наполнителя дает понять, какой плотности будет материал. ρ имеет широкий диапазон – 500-1800 кг/м3 и характеризуется классами – от В 3,5 до В 22,5.
Соответствие марки и класса
Марка |
Класс |
Характеристики |
М 50 |
В 3,5 |
F 50 / D 800 |
М 75 |
В 5 |
F 50 / D 1000 |
М 100 |
В 7,5 |
F 50 / D 1200 |
М 150 |
В 12,5 |
F 50 / D 1400 |
М 200 |
В 15 |
F 50 / D 1600 |
М 300 |
В 22,5 |
F 50 / D 2000 |
Блоки способны выдержать различные виды статичной нагрузки, но динамические нагрузки приводят к деформациям из-за пористой структуры материала. Также последний можно назвать достаточно хрупким, ронять его не рекомендуется, поскольку удар, скорее всего, приведет к расколу блока.
Разные показатели влажности воздуха и плотности материала по-разному влияют на коэффициент теплопроводности.
Плотность |
Коэффициент теплопроводности |
|
период сухости |
период эксплуатации |
|
500 кг/м3 |
0,146 Вт/( м·°С) |
0,17-0,24 Вт/( м·°С) |
600 |
0,163 |
0,2-0,26 |
800 |
0,211 |
0,24-0,32 |
1000 |
0,272 |
0,33-0,40 |
1200 |
0,361 |
0,44-0,51 |
1400 |
0,475 |
0,56-0,64 |
1600 |
0,583 |
0,67-0,78 |
1800 |
0,669 |
0,8-0,91 |
Блоки с объемным весом 600-1100 кг/куб. м. – конструкционно-теплоизоляционный материал, 1200-1800 кг/куб. м. – конструкционный.
- Паропроницаемость. Эта характеристика указывает, дышащий ли это материал. Керамзитобетонные блоки обладают хорошей паропроницаемостью с показателями в 0,3-0,09 мг/(м·ч·Па). Данные зависят от плотности материала.
Плотность |
Паропроницаемость |
600 |
0,09 |
800 |
0,1 |
1000 |
0,14 |
1200 |
0,2 |
1400 |
0,26 |
Показатели говорят о том, что паропроницаемость керамзитобетона в 2 раза лучше, чем у кирпича, практически приравнивается к древесине. Также материал поглощает избыточную влагу из помещения, и при сухом воздухе возвращает ее обратно. Поэтому в доме из керамзитобетона всегда комфортный микроклимат.
- Морозостойкость. По ГОСТу керамзитобетонные блоки имеют марки морозостойкости: 25, 35, 50, 75. Обозначаются буквой F. Цифры указывают на кол-во циклов заморозки и оттаивания, которые может выдержать блок, не потеряв свою прочность. В последующий цикл от указанного, прочность снизится на 10%. Наиболее распространено производство блоков с пометкой F50.
- Огнестойкость. Материал относится к категории пожарной безопасности – А1 – кладка, находящаяся под воздействием огня до 10 часов не разрушится.
Маркировка
Все характеристики блоков можно узнать самому, не обращаясь к продавцу-консультанту магазина. С помощью маркировки. Согласно ГОСТу 6133-99 различают обозначения:
- С – для укладки стен;
- П – для кладки перегородок;
- Л – лицевой блок;
- Р – рядовой.
Это варианты второй и третьей буквы в маркировке, первая для керамзитобетона – К (искусственный камень). Далее идут параметры, указывающие на способ укладки блоков:
- ПР – порядовый;
- УГ – угловой;
- ПЗ – перевязочный.
Следующие показатели – наличие/отсутствие пустот: ПЛ – полнотелый и ПС – пустотелый. Далее указывается длина, марка (М), морозостойкость (F) и плотность. Последнее – указание ГОСТа. Например: КПР-ПР-ПС-39-100- F50-1400 ГОСТ 6133-99.
Применение
- Укладка наружных стен в малоэтажных домах.
- Возведение перегородок со звукоизоляционными свойствами.
- Облицовка строений.
- Сооружение вентиляции с помощью укладки блоков, которые имею естественные сквозные отверстия.
- Закладка фундамента малогабаритных домов.
- Постройка заборов.
- Строительство столбов для ограждений.
- Использование как опорных тумб для скамеек.
- Качественная замена бордюрного камня.
Почему выбирают керамзитобетон
Достоинства материала, в особенности состав, делают бетонные блоки такими популярными:
- Экологичность. В составе только цемент, керамзит (может быть в различном виде), вода, песок.
- Длительный срок службы, который приравнивается к кирпичу. Материал теряет прочность (на 10%) по истечению 50 циклов замерзания и оттаивания.
- Небольшой вес в соотношении с размером. Позволяет производить кладку самостоятельно, без дополнительной техники или рабочей силы.
- Низкая теплопроводность – практически не отдает тепло, сохраняя его порядка 75 часов.
- Регулирует влажность воздуха в помещении – впитывает избыток и возвращает его во времена повышенной сухости.
- Не подвластны горению. Из-за огня блоки могут треснуть или рассыпаться, но при этом не выделят вредных продуктов горения.
- Относится к дышащим материалам, поскольку имеет хорошую паропроницаемость.
Недостатков не так много и среди них:
- Плохая переносимость динамических нагрузок, приводящих к деформации.
- Их сложно порезать, зачастую крошатся, образуются трещины, края получаются неровными и осыпающимися.
Сравнение легких блоков и кирпича
К легким блокам относятся: пеноблоки, газосиликатные, опилкобетонные, шлакоблоки и керамзитобетонные.
- Объемный вес. Наибольший у кирпича – 1000-2000 кг/м3, далее идет керамзитобетон – 700-1500, третье место между собой разделили: опилкобетонные (500-900), шлакоблоки (500-1000), пеноблоки (450-900). С наименьшим объемным весом – газосиликатные блоки – 200-600 кг/м3.
- Прочность. Самым прочным из легких блоков является керамзитобетон, который не уступает показателями кирпичу – 50-150 кг/см2. Второе место со значительным отрывом – шлакоблоки – 25-75 кг/см2. Менее прочными являются пеноблоки (10-50) и газосиликатные блоки (5-20).
- Теплопроводность. Наибольше количество тепла будет уходить через кирпич (0,3-0,8 вт/(м·град)) и шлакоблоки (0,3-0,5). Далее по показателям идут опилкобетонные (0,2-0,3) и пеноблоки (0,2-0,4). И третье место с наихудшей теплопроводностью – керамзитобетонные и газосиликатные блоки – 0,15-0,45 и 0,15-0,3 соответственно.
- Морозостойкость (средние показатели). Больший срок службы у кирпича и керамзитобетона – по 50 циклов, далее – пеноблоки и опилкобетонные блоки – 25, третьи – шлакоблоки (20 циклов). Наименьший показатель долговечности у газосиликатных блоков – 10 циклов.
- Время остывания. Дольше всего остывает кирпич и керамзитобетон – 75-90 часов, вторые по показателям – опилкобетонные и шлакоблоки – 65 часов, третьи – пеноблоки (60).
И быстрее всего остывают газосиликатные блоки – за 50 часов.
- Усадка. После строительства толщина кирпича, керамзитобетона и шлакоблоков не меняется – усадка составляет 0% мм/м. На 0,5-1% мм/м уменьшается опилкобетон. Пеноблок – 0,6-1,2 и больше всего газосиликатные блоки – 1,5 % мм/м.
- Водопоглощение. Газосиликатные блоки способны поглотить 100% влаги, пеноблоки – 95%, опилкобетонные – 60-80, шлакоблоки – 75, и меньше всего поглощают: керамзитобетон (50%) и кирпич (40%).
По данным сравнения можно сделать вывод, что керамзитобетон по характеристикам является одним из наиболее подходящих материалов по всем показателям для строительства домов, бань и укладки фундамента. Такие же хорошие показатели у кирпича. Остальные легкие блоки уступают, либо всеми показателями (газосиликатные), либо некоторыми из них (пеноблоки, опилкобетонные, шлакоблоки).
Керамзитобетонные блоки технические характеристики
Керамзитобетонные блоки характеристики.
Керамзитобетонные блоки характеристики.Керамзитобетонные блоки – это популярный в современном строительстве стеновой материал, активно используемый при возведении малоэтажных зданий.
Основные характеристики керамзитобетонных блоков — морозостойкость, теплопроводность и прочность. Одним из достоинств характеристик керамзитобетонных блоков является низкая теплопроводность, которая позволяет использовать блоки в холодном климате. Также керамзитобетонные блоки «дышат», регулируя влажность воздуха в помещении.
Одной из основных характеристик керамзитобетонных блоков является прочность – способность сохранять свою целостность под действием внешних разрушителей. Чтобы определить эту основную характеристиу керамзитобетонного блока, изготавливается небольшой кубик из керамзитобетона с длиной ребра 200 миллиметров, если он развалится на части под действием нагрузки в восемьдесят тонн, то лимит прочности при сжатии составит 20 МПа. В зависимости от значения прочности, керамзитобетон делится на марки. Маркировка производится по лимиту прочности эталонного кубика с ребром 200 миллиметров. Например, различают керамзитобетонные блоки с прочностью «100», «150», «200».
Теплопроводность керамзитобетонных блоков, вес, размеры.
Плотность керамзитобетонных блоков, марка, прочность.
Теплопроводность керамзитобетонных блоков, вес, размеры.
Теплопроводность керамзитобетонных блоков обеспечивает выполнение современных требований по теплосбережению. С середины прошлого века такие показатели считались вполне приемлемыми. Морозостойкость керамзитобетона, подразумевающая теплопроводность керамзитобетонных блоков в этом случае в соответствии со стандартом должна быть не ниже 25 циклов для стен и 35 циклов для цокольных этажей.
Самый главный критерий доступный для проверки любому строителю это вес керамзитобетонных блоков т.к. керамзит в 3-ри раза легче песка то качественные керамзитобетонные блоки весят гораздо легче, вес пустотелого керамзитобетонного блока колеблется от 14кг. сухого до 16кг. влажного, псевдо керамзитобетонного блока от 18 до 20 кг. соответственно.
Керамзитобетонные блоки — размеры этого материала могут быть самыми разными, в зависимости от потребностей заказчика. Самые распространенные размеры керамзитобетонных блоков– 190/390/90мм и 190/390/188мм. Такие блоки чаще всего используются при строительстве жилых, производственных и гражданских объектов. Керамзитобетонные блоки и их размерыконтролируются технологическим регламентом и не должны отклоняться от нормы больше следующих значений:
- тклонение по длине +(-)4 мм
- тклонение по ширине +(-)3 мм
- тклонение по высоте +(-)4 мм
- тклонение от плоскости граней и прямолинейности ребер до 6 мм
В одной партии допускается не более 10% изделий с трещинами, которые пересекают хотя бы одно ребро. При производстве керамзитобетонных блоков, их размеры тщательрно контролируются, поэтому размеры керамзитобетонных блоков никогда не отклоняются от допустимых значений и соответствуют всем стандартам качества.
Керамзитобетонные блоки относятся к группе легких бетонов, хотя обладает более значительным объемным весом, в 1,5-2 раза превышающим объемный вес пенобетона, газобетона и полистиролбетона. Изготавливается из керамзита, песка, цемента и воздухововлекающих добавок. Керамзитобетонные блоки – продукт обжига легкоплавких глинистых пород, представляющий собой пустотелые шарики из обожженной глины. В процессе изготовления керамзитобетона эти шарики склеиваются между собой, образуя прочный, экологически чистый и сравнительно легкий материал. Плотность керамзитобетонных блоков, применяемых в малоэтажном строительстве – 700-1200 кг/м?, причем плотность керамзитобетонных блоков монолитных превышает 1000 кг/м?. Морозостойкость материала – 50 циклов. Эксплуатационная влажность – 5-7%. Коэффициент паропроницаемости – 0,08 мг/м·ч·Па. Класс прочности на сжатие – В 3,5. Расчетная теплопроводность кладки – от 0,21 до 0,5 Вт/м-°С. Необходимая толщина однослойной стены в условиях центрального региона – от 0,9 до 1,5 м, в зависимости от вида блоков. При производстве керамзитобетона используют различные фракции гравия и щебня: 5-10, 10-20 и 20-40 мм — это как раз и влияет на плотность керамзитобетонных блоков и их применяемость для тех или иных задач. Готовые блоки могут быть монолитными или пустотелыми. Все это обуславливает значительный разброс эксплуатационных характеристик. Пустотелые блоки обычно используют для возведения стен, а монолитные – для кладки печей, каминов и дымоходов.
Керамзитобетонные блоки марка морозостойкости показывает сколько полных циклов замораживания и размораживания должно пройти, чтобы прочность блока уменьшилась на 10%. Марка морозостойкости керамзитобетонных блоков определяет долговечнось и надежность блока. Чем выше марка керамзитобетонного блока прочности и морозостойкости, тем более долговечны и надежны Ваши стены. Для несущих стен загородного дома целесообразно использовать керамзитобетонные блоки марки морозостойкости не менее F50. Существуют и другие марки морозостокости керамзитобетонных блоков: F100, F200 для бордюрных камней и тротуарной плитки. Марки меньше F50 использовать на стены жилого дома нежелательно.
Еще одно свойство керамзитобетонные блоков – водостойкость – способность не разрушаться под напором воды. Для определения водостойкости используют два эталона – один в сухом виде раздавливают на прессе и вычисляют его прочность при нормальных условиях, а другой сперва погружают в воду, а затем только помещают под пресс. Из-за ослабления связей между частицами прочность керамзитобетона уменьшается. Отношение прочности намоченного материала к сухому называется коэффициентом размягчения. Для керамзитобетона он равен 0.8.
Керамзитобетонные блоки: технические характеристики
При выборе керамзитобетонных блоков вы столкнётесь с несколькими их разновидностями. Существуют полнотелые и пустотелые блоки. Характеризовать полнотелые блоки нет смысла, так как по форме это параллелепипед с ровными сторонами без выемок и отверстий, если, конечно, не учитывать пористость самого керамзитобетона. Несколько более разнообразные формы имеют пустотелые блоки, они могут иметь разное количество и размер пустот, которые могут быть сквозными или же несквозными.
Также существуют стеновые и перегородочные блоки, они могут быть разных размеров, которые частично определяются форм-фактором.
Стеновой блок представляет собой параллелепипед с соотношением сторон, близким к таким же у кирпича. Перегородочный же блок менее широкий по сравнению с рядовым, например, размеры первого могут быть 490*90*185, а у второго – 490*300*185. Соответственно, в зависимости от вида керамзитобетонных блоков, в 1 кубе их разное количество.
Выделяют лицевые и рядовые блоки, отличаются они характеристиками поверхности. Первые уже облицованы разнообразными листами, плитами, штукатурками, окрашиванием, контурированием или другими элементами, которые наиболее часто применяются не по отдельности, а в комплексе. Второй вариант нуждается в дополнительной облицовке.
Любые из представленных типов материала могут иметь формованные торцы, служащие в качестве замков для удобства кладки.
Перегородочный блок
Стеновой блок
Характеристика плотности и прочности
Плотность и прочность – это основные технические характеристики описываемого материала, которые напрямую зависят друг от друга, а также влияют на ряд других характеристик.
Плотность керамзитобетонного блока зависит от фракции керамзита, используемого для его изготовления. Чем крупнее фракция – тем ниже плотность, а чем ниже плотность – тем ниже прочность. На прочность также влияет марка используемого бетона.
Если говорить о цифрах, то материал может иметь плотность в диапазоне от 500 до 1800 килограмм на метр в кубе. В соответствии с плотностью, материал может противостоять статическим нагрузкам в диапазоне от 35 до 250 килограмм на сантиметр квадратный.
Конечно же, плотность материала влияет и на вес, который также варьируется, и в зависимости от размера изделия. В основном он близок к показателям в районе от десяти до двадцати килограмм.
Совет прораба: если у Вас есть возможность «пощупать» товар перед покупкой, то обратите внимание, насколько легко отделить керамзитные шарики от блока. Если Вы без труда смогли отломать несколько шариков керамзита, то это свидетельствует о применении низких марок бетона и, соответственно, низком качестве продукции. Все составляющие блока должны быть крепко связаны между собой, в противном случае снижается их несущая нагрузка, срок эксплуатации и устойчивость перед динамическими нагрузками.
Теплопроводность и паропроницаемость керамзитобетона
Теплопроводность и паропроницаемость имеют прямую зависимость от плотности, и чем она выше – тем сильнее падает паропроницаемость и возрастает теплопроводность. В зависимости от плотности блока, он может иметь паропроницаемость равную от 0,094 до 0,260 мг/м*ч*Па и теплопроводность от 0.18 до 0.90 Вт/м*.
Совет прораба: как видно, разбежности в показателях могут быть довольно большими, именно по этой причине стоит тщательно подбирать материал по плотности. Рассчитывайте на достижение лишь необходимой несущей способности стен. Помните, что чересчур высокая плотность способствует снижению последующей экономической выгоды на расходе энергоносителей, используемых для отопления. Другим вариантом является увеличение расходов на утепление стен.
Исходя из изложенного о теплопроводности, различают блоки конструкционно-теплоизоляционного и конструкционного типа. Чертой, разделяющей эти два типа, является плотность блока в 1100 килограмм на кубический метр, соответственно, плотность ниже – первый тип, выше – второй.
Стойкость к пониженным температурам и огню
Керамзитобетон сохраняет свои прочностные свойства при замораживании и оттаивании от 25 (F25) до 75 (F75) циклов.
Материал может противостоять открытому огню до десяти часов, то есть имеет класс пожарной безопасности A1.
Керамзитобетон – благодатный материал для строительства, который по многим техническим характеристикам превосходит кирпич, но требует обязательного утепления и облицовки (если вы используете необлицованный блок). Помните, что утепления и должной гидроизоляции требуют не только жилые помещения, но также требует утепления баня из керамзитобетонных блоков или другие помещения с повышенной влажностью.
Видео
Керамзитобетон – характеристики, состав, изготовление
Современное строительство предполагает использование современных строительных материалов. Одним из таких материалов является керамзитобетон. Керамзитобетоном называют стройматериал, который в своем составе содержит не только цемент, но и керамзит. По сравнению с аналогичными материалами – эта разновидность легкого бетона является весьма демократичной по цене, что делает его достаточно востребованным материалом на строительном рынке.
Что входит в
состав керамзитобетона Структура керамзитобетона зависит от того, насколько он пористый. Таким образом, различают: плотный, поризованный и крупнопористый керамзитобетон.В целом же, в состав керамзитобетона входят такие компоненты: песок, цемент, керамзит, добавки, сопутствующие вовлечению воздуха (например, омыленная древесная смола). Его главным отличием от бетона обыкновенного, строительного, является меньший, по сравнению с последним, вес, за счет более легкого керамзита.
Керамзит же, в свою очередь, является ничем иным, как вспененной и обожженной глиной, с соответствующей структурой. Такая структура приближает его по своим свойствам к арболиту, но по цене керамзит значительно дешевле. Самым распространенным изделием из этого материала можно считать керамзитоблок.
Производство, или
изготовление керамзитобетонаСам по себе, керамзит, поскольку это пористый материал – может впитывать и задерживать какое-то количество воды, и с этим его свойством связаны особенности производства керамзитобетона в целом.
При изготовлении этого строительного материала, расчет воды, которую требуется добавить к материалу, делается на основании 1 части воды к 1 части цемента. Впрочем, здесь все сильно зависит от степени влажности самого наполнителя. Если последний хранился не в помещении, а под открытым небом, попадая под дождь – его масса будет отличаться от хранившегося в помещении, порой даже значительно.
При изготовлении керамзитобетона, особая важность уделяется последовательности загрузки каждого компонента.
Затем добавляется одна часть воды, и снова запустить процесс перемешивания. Только теперь, на данном этапе добавляют три части керамзита, не забывая снова перемешать. Стоит следить, чтобы в результате масса была влажной, поскольку, если керамзит был очень сухим, то он может впитать больше влаги, из-за чего смесь получится суховатой. Во избежание этого, следует добавить еще немного воды, ровно до тех пор, пока все гранулы наполнителя (керамзита) не покроются цементом целиком. Только нужно тщательно отслеживать, чтобы воды не было слишком много.
После очередного тщательного перемешивания – полученную массу раскладывают по кирпичным формам. Если же, назначение керамзитобетона не для изготовления блоков, а, скажем, для наливных полов – воду добавляют еще чуть-чуть, до консистенции густой сметаны, с включениями керамзита. Единственный нюанс состоит в том, что до застывания следует оградить контакт обычного бетона и керамзитобетона.
Все эти моменты прописаны в инструкции, и следует тщательно изучить ее, чтобы избежать негативных последствий. После того, как пройдет несколько дней – образуется монолит из керамзитобетона, которому больше прочности можно придать с помощью регулярных обрызгиваний водой в течение месяца, либо же, чтобы избежать недоразумений, просто закрыть его полиэтиленом, таким образом обеспечив влажный микроклимат на месяц.
Когда речь идет о таком материале, как керамзитобетон характеристики его во многом определяются качеством его компонентов.
Давайте рассмотрим основные из них:
- 1. Прочность – этот показатель зависит от прочности наполнителя, а также от качества цемента, который используется в процессе изготовления. Прочность готового материала (керамзитобетона) со временем только возрастает.
- 2. Плотность керамзитобетона. Это отношение массы материала к объему, причем плотность данного строительного материала никогда не бывает 100%, она всегда меньше. В данном случае, чем выше плотность – тем прочнее материал.
- 3. Водостойкость. Это свойство не поддаваться воздействию воды, для керамзитобетона он больше 0,8.
- 4. Теплопроводность и огнестойкость. Теплопроводность керамзитобетона более высокая, чем у кирпича, но ее нельзя назвать действительно высокой. А следовательно, огнестойкость – вполне достойного уровня. Этот материал может выдерживать воздействие высокой температуры (выше 1000 градусов по Цельсию).
- 5. Морозостойкость керамзитобетона также подтверждена многочисленными примерами. Так, этот материал способен выдерживать неоднократное замерзание и оттаивание.
Улучшение термических и механических свойств бетона на легком заполнителе с использованием неорганического материала с изменяющейся фазой, керамзитового заполнителя, алккофина 1203 и технологического песка
Абсорбционные характеристики PCM-ECA
Наибольшая абсорбционная способность была определена при различных температурах и приведена в таблице 3. Утечка композиционного материала с покрытием из цементного раствора и без него определялась методом диффузионного просачивания, определенным по [21]. Количество включения PCM в ECA при различных температурах и времени показано в таблице 3.Из таблицы 3 видно, что ECA при 50 ° C через 18 ч имеет максимальное поглощение 27%. Различные абсорбционные характеристики композита показаны в Таблице 3 и на Фиг.3. Из Фиг.3 видно, что без покрытия из ЭХА утечка превышала круг просачивания при всех температурах и даже при комнатной температуре. Когда покрытие из цементного раствора было нанесено на ECA, утечка снизилась на 40% при всех температурах. Даже при комнатной температуре с покрытием утечка была уменьшена на 50%, что было резким снижением, и по мере повышения температуры утечка увеличивалась, но находилась в пределах круга просачивания.
Испытание круга диффузионного просачивания для ЭХА без покрытия (WC) и с покрытием (C) a , e при комнатной температуре (RT), b , f при 40 ° C, c , г при 50 ° C, d , h при 60 ° C
Водопоглощение образцов бетона с PCM-ECA и без него
Испытания на водопоглощение проводились для всей смеси после завершения 28 дней лечения. Смесь-2 с PCM имеет 22,3% водопоглощения, что является самым высоким поглощением по сравнению с эталонной смесью; потому что смесь-2 содержит самый высокий процент ЭКА.Точно так же смесь-2 без РСМ также показала самое высокое водопоглощение на 17,05%, за ней следовали смесь-4 и смесь-6 с 2,35% и 1,76%, соответственно, по сравнению с эталонной смесью. Смесь-1 и смесь-3 показали меньшее водопоглощение, чем контрольная смесь, на 4,11% и 3,23% соответственно.
Когда PCM-ECA вводили в бетон, водопоглощение увеличивалось почти во всех смесях, кроме смеси-5. Наибольшее водопоглощение наблюдалось у смеси-2 с 22,35%, за которой следовали смесь-6, смесь-2, смесь-4 и смесь-3 с 17%.05%, 15,88%, 9,41% и 6,76% соответственно по сравнению с эталонной смесью. Микс-5 показал снижение водопоглощения на 3,82%. Когда алккофин1203 и ЭХА без ПКМ добавляли в бетон с м-песком, было замечено, что из-за увеличения содержания алккофина1203 на 10% водопоглощение снижалось на 17,33%, но для тех же 10% алккофина1203, когда ЭХА составляла 20%; водопоглощение увеличилось на 5,45% по сравнению между смесью-3 и смесью-4. Шаблон был другим для mix-5 и mix-6 по сравнению с mix-3 и mix-4 соответственно; водопоглощение увеличилось на 3.51% и 6,53 для смеси-5 и смеси-6 соответственно (рис. 4).
Рис. 4Водопоглощение бетонных кубиков ECA после 28 дней отверждения с PCM и без него
По мере увеличения процентного содержания alccofine1203 с 10 до 20% водопоглощение снижается на 12,09% по сравнению с смесью-4 и смесью- 5 а; когда 20% алккофина 1203 было включено с 20% в смесь 6 ECA с PCM, процент водопоглощения увеличился на 6,53% по сравнению между смесью-4 и смесью-6, это связано с тем, что смесь-6 даже содержит 20% ECA, что дает больше вода. В смеси-2 и смеси-3 10% алккофина 1203 было частично заменено цементом, что привело к снижению водопоглощения на 12,74%, но все же водопоглощение было больше, чем у эталонной смеси.
Термические свойства композитов PCM
На рис. 5 и в таблице 4 показан анализ DSC чистого PCM (HS24), композитного PCM-ECA и температуры плавления / замерзания со скрытой теплотой, рассчитанной по измерениям теплового потока. Точки плавления и замерзания значительно изменились по сравнению с чистым ПКМ.Это может быть связано с физическим взаимодействием пористых материалов между ПКМ и внутренней поверхностью и удержанием ПКМ (HS24) в очень маленьких порах, как утверждали предыдущие исследователи [21]. Значения скрытого тепла, полученные из оценки DSC, затем коррелировали с потенциальными значениями скрытого тепла, рассчитанными по формуле. (1). Теоретические значения скрытой теплоты из таблицы 4 были очень похожи на результаты, полученные при исследовании DSC, что свидетельствует об однородном распределении PCM в порах ECA.
$$ H _ {{\ text {T}}} = H _ {{{\ text {PCM}}}} \ times W _ {{{\ text {PCM}}}} $$
(1)
, где H T = теоретическая скрытая теплота; H PCM = скрытая теплоемкость чистого PCM; W PCM = весовой процент PCM в композите.
Рис.5Анализ DSC чистого PCM (HS24) и композита (LECA с PCM)
Таблица 4 Температура фазового изменения и энтальпия PCM (HS24) и композита Когда ECA и alccofine1203 были смешаны с бетоном без ПКМ, относительно эталонной смеси, теплопроводность улучшена в 5 раз.02% и 12,78% для смеси-2 и смеси-6 соответственно. Наибольшее снижение теплопроводности было зарегистрировано для смеси-5 на 36,0%, за которой следовали 32,8%, 12,7% и 0,4%, соответственно, для смеси-3, смеси-4 и смеси-1. По сравнению с PCM-ECA и без него в бетоне смеси-1 и смесь-6 показали улучшение теплопроводности на 3,63% и 20,94% для смеси-1 и смеси-6. Когда 10% PCM-ECA вводится в бетон, количество alccofine1203 увеличивается с 0 до 10%, а теплопроводность увеличивается на 24.39% и 26,17% соответственно от 10 до 20%.
Точно так же было падение теплопроводности на 15,7% для 20% PCM-ECA, но теплопроводность 20% alccofine1203 была улучшена на 8,17%. Поскольку ЭКА был введен в бетон с ПКМ, теплопроводность снизилась на 28,31%, 13,2% и 7,76%, соответственно, для смеси-2, смеси-3 и смеси-4. По сравнению с эталонной смесью наблюдалось улучшение теплопроводности смеси-1, смеси-5 и смеси-6 на 4,11%, 18,26% и 5,47% соответственно.
Когда алккофин1203 был добавлен в смесь на 10% с 10% -ным ECAPCM, теплопроводность снизилась на 16,66% по сравнению со смесью-1 с последующим введением 20% ECAPCM для того же процентного содержания алкофина1203; теплопроводность увеличена на 22,22% по сравнению с смесью-2. Аналогично, когда 20% алккофина 1203 было добавлено к смеси с 10% ECAPCM, теплопроводность увеличилась на 11,96% по сравнению со смесью-1, а для той же смеси, когда ECAPCM составляла 20%, теплопроводность увеличилась на 32.03% по сравнению с смесью-2. Наибольший процент снижения теплопроводности зафиксирован для смеси-2 на 28,31% (рис. 6).
Рис. 6Теплопроводность легкого бетона с PCM и без него
Прочность на сжатие
Совершенно очевидно, что из-за увеличения процента ECA интенсивность уменьшается. Наибольшее снижение прочности наблюдалось для смеси-5 с 30,7% на 7-й день с ПКМ и 57,6% для смеси-4 без ПКМ. Между смесью-1 и смесью-2 не наблюдалось большого снижения прочности, но смесь-6 дала значительно меньшее снижение прочности с 14.8% с PCM, а прочность смеси-3 увеличилась на 4,5% без PCM. Интересно, что с PCM прочность увеличилась для смесей-1, mix-3 и mix-6 на 36,3%, 75% и 6,6% соответственно на 7-й день по сравнению с без PCM (рис. 7).
Рис. 7Прочность на сжатие различных смесей на a 7-й день и b 28-й день с PCM и без него
Картина изменилась на 28-й день силы сжатия; только Mix-4 продемонстрировал снижение силы на 11. 6% по отношению к ПКМ, а все остальные смеси показали рост прочности. Наибольшее снижение интенсивности было обнаружено в смеси-5 с 33,6% и смеси-1 с 56,2% с ПКМ и без него по сравнению с эталонной смесью. Для Mix-3 наблюдалось гораздо меньшее снижение интенсивности — 11,9% для PCM и 20,1% для без PCM.
Mix-4 показал наилучшие результаты с 31,77 кН / м 2 и 37,61 кН / м 2 на 7-й и 28-й день с PCM, соответственно. Микс-5 показал резкое увеличение прочности с 26,08 кН / м 2 до 48.69КН / м 2 на 7-е и 28-е сутки соответственно с ПКМ. Наименьшая прочность на 28-й день без ПКМ составила 18,68 кН / м 2 для смеси-3, и 34,11 кН / м 2 для смеси-6 была отмечена как самая высокая прочность на сжатие без ПКМ.
Прочность на изгиб
На основании достигнутых механических свойств пропорции ЭКА с ПКМ и алккофином 1203 были частично заменены, а М-песок с полной заменой ТВС был отлит с размером балки 500 мм × 100 мм × 100 мм и испытан на 28-е сутки приведено в таблице 5 и на рис.8.
Таблица 5 Прочность на сжатие в разном возрасте с разным процентным содержанием ЭХА и алккофина 1203 Рис. 8Прочность бетона на изгиб с PCM и без него
Тенденция прочности на изгиб отличается от прочности на сжатие; весь микс с PCM дал снижение прочности, в то время как микс без PCM дал другой образец значений. Наибольшее снижение прочности было обнаружено в смеси-3 на 15,2% при частичной замене ЭКА на ПКМ.Смесь-2 имела примерно такую же крепость, что и эталонная смесь, за ней следовали смеси-5 и смесь-1 с 4,3% и 5,3% снижением ЭХА с РСМ. В смеси 1 и смеси 5 прочность на изгиб улучшилась на 4,1% и 10,7% по сравнению с ПКМ и без него, но оставшаяся комбинация привела к существенному снижению прочности на изгиб. Mix-3 дает резкое снижение примерно на 24,8% для с включением PCM и без него.
Шаблон для PCM-free полностью отличался от PCM. Крепость смеси-1, смеси-3 и смеси-4 увеличилась на 12,7%, 1,4% и 12,7%, после чего последовало снижение прочности на 9,1%, 8,4% и 13,5%, соответственно, для смеси-2, смеси. -5 и микс-6. Mix-2 продемонстрировал одинаковую силу как с PCM, так и без него. Было обнаружено, что хотя процентное содержание алккофина 1230 увеличилось с 10 до 20% в смеси-4 и смеси-5, прочность также увеличилась с 5,11 кН / м 2 до 5,42 кН / м 2 , соответственно. Из Таблицы 5 и Рис. 8 мы можем утверждать, что смесь-3 является наиболее подходящим материалом с точки зрения прочностных свойств для интеграции PCM с alccofine1203 и без нее.
Испытание на долговечность
Быстрое испытание на проницаемость для хлоридов (RCPT) было проведено для всей смеси, чтобы определить, насколько бетон может противостоять проникновению хлорид-ионов. В соответствии с ASTM C1202-2012 испытание проводится на образце бетона, и количество кулонов, прошедших через образец бетона, регистрируется и приводится на рис. 9. Степень проницаемости для хлоридов, соответствующая> 4000, считается высокой; От 2000 до 4000 кулонов, от 1000 до 2000 кулонов и <1000 считаются умеренными, низкими и очень низкими соответственно.Коррозия, проницаемость и растрескивание, которые взаимосвязаны друг с другом, и их результаты будут влиять на бетон. Низкая и умеренная проницаемость для хлоридов является ключом к хорошей проницаемости для бетона. Стойкость к проникновению хлорид-иона в пересчете на общее количество пройденных зарядов (кулоны) для различных смесей через 28 дней.
Рис. 9Испытание RCPT для легкого бетона с PCM и без него
Скромное значение проникновения хлорид-ионов с 2407,2 кулонами было показано эталонной смесью.Самая низкая скорость проникновения хлорид-иона наблюдалась в Mix-1 с 1212,6 кулонами, а самая высокая — в Mix-4 с 2537,5 кулонами. Оставшаяся смесь отображала смесь низких и высоких значений. Поскольку процентное содержание ECA с PCM увеличивалось, проникновение хлорид-ионов также увеличивалось на 33,12% по сравнению с Mix-2 по сравнению с Mix-1.
Alccofine1203 — более сильное вещество, чем цемент, которое уплотняет бетон, что, в свою очередь, увеличивает процентную концентрацию хлорид-ионов.Проникновение хлорид-ионов улучшилось на 42,75 процента по сравнению со смесью-1, когда в смесь был добавлен алккофин 1203 на 10 процентов с 10-процентным ECA-PCM. Точно так же с 20% ECAPCM был добавлен такой же объем алккофина 1203; процентное содержание хлорид-иона было увеличено на 23,96% и 10,21% по сравнению со смесью-1 и эталонной смесью, соответственно.
Из-за увеличения доли алккофина 1203 в смеси-5 и смеси-6 с 10 до 20 процентов произошло резкое падение концентрации хлорид-иона на 36.03 процента и 39,14 процента по сравнению с эталонной смесью и 11,45 процента и 28,14 процента по сравнению с смесью-1 и смесью-2. Проникновение хлорид-ионов улучшилось в смеси-1 и смеси-2 из-за увеличения дозы в ECAPCM, но оно было ниже, чем у контрольной смеси. Такая же закономерность была обнаружена для смесей-5 и смесей-6, но для смесей-3 и смесей-4 тенденция была иной.
Испытание на герметичность на образцах бетона
Для всей смеси было проведено испытание на герметичность на образцах бетона. Образцы сушат при температуре окружающей среды в течение 2 часов после 28 дней отверждения, поэтому все образцы оборачиваются фильтровальной бумагой и взвешиваются по весу фильтровальной бумаги перед постукиванием.Эти образцы теперь хранятся в печи при повышенных температурах, т. Е. Следующие 2 ч при 50 ° C. Оба образца извлекаются во время процесса сушки в печи, взвешивается вес фильтровальной бумаги и обнаруживаются пятна на фильтровальной бумаге.
Процентное различие фильтровальной бумаги было обнаружено в смеси-2 с 4%, когда не было добавлено покрытие из цементного раствора, но оно уменьшилось до 1,5%, когда было нанесено покрытие из цементного раствора. Наблюдалось небольшое количество следов пятен на фильтровальной бумаге для смесей-5 и смесей-6, но без изменения веса фильтровальной бумаги.
Долговечность легкого пенобетонного заполнителя Научно-исследовательский доклад по «Гражданскому строительству»
Доступно на сайте www. sciencedirect.com
ScienceDirect
Инженерные процедуры
ELSEVIER
Инженерная процедура 65 (2013) 2-6
www.elsevier.com/locate/procedia
Бетон и бетонные конструкции 2013 Конференция
Прочность легкого керамзитобетона
аЛиас Винтифов, легкий строительный материал к.s., 357 44 Винтифов, Чешская Республика b Технологический университет Брно, Технологический институт строительных материалов и компонентов, Вевери 331/95, 612 00 Брно, Чехия
Республика
В статье описывается разработка и использование легкого бетона и легкого самоуплотняющегося бетона с использованием искусственного легкого заполнителя на основе керамзита для товарного бетона и сборных элементов. Целью данного исследования была оценка легкого бетона на долговечность бетонов, помещенных в химически агрессивные жидкие и газообразные среды (высокие концентрации сульфата, хлорид-ионов, автомобильный газ, нефтяные и газообразные среды CO2 и SO2).
© 2013TheAuthors. Опубликовано Elsevier Ltd.
Отбор и экспертная оценка под ответственность Жилинского университета, факультета гражданского строительства, отдела сооружений и мостов
Ключевые слова: керамзитовый заполнитель, легкий бетон, прочность;
1. Введение
Легкие бетоны с высокими эксплуатационными характеристиками, то есть самоуплотняющийся бетон и легкий бетон, армированный фиброй, — это типы бетона, которые не включены ни в какие стандарты или директивы.Высокая водопоглощающая способность, малый объемный вес и низкая прочность легкого заполнителя — основные проблемы проектирования, производства и укладки легкого бетона. Отсюда, в частности, тип и свойства легкого
* Тел .: +420777740014 Электронный адрес: michala. [email protected].
Michala Hubertováa * 9 Rudolf Helab
Аннотация
1877-7058 © 2013 Авторы. Опубликовано Elsevier Ltd.
Отбор и экспертная оценка под ответственностью Жилинского университета, факультет строительства, кафедра конструкций и мостов doi: 10. 1016 / j .proeng .2013.09.002
, которые в наибольшей степени влияют на поведение этих типов бетона. Единственным пористым агрегатом, использованным для экспериментов, был легкий агрегат Liapor, произведенный в Чехии.
В рамках исследования легкого бетона на первом этапе было проверено влияние добавки метакаолина на реологические свойства свежего бетона и физико-механические свойства затвердевшего бетона [2].После оценки результатов испытаний 40 составов смесей, которые с учетом вышеупомянутых свойств и экономичности, партия, содержащая 5% по объему метакаолина, может считаться очень эффективной. В настоящее время в рамках исследовательских работ проводятся испытания на устойчивость легкого бетона и легкого самоуплотняющегося бетона к агрессивным средам. В данной статье описывается оценка части разработанных конструкций смесей после 1 года воздействия агрессивных сред, а также влияние выбранных добавок на стойкость легкого бетона.
2. Экспериментальный
Разработан набор из 5 смесей-дизайнов, отличающихся только используемым типом используемых добавок. Количество портландцемента (370 кг / м3), добавок (40% по объему цемента) и добавок (суперпластификаторы на основе поликарбоксилатов) было одинаковым для всех смесей. Состав заполнителей был для всех микс-дизайнов одинаковым. Использовалась комбинация легкого заполнителя на основе керамзита и природного плотного камня.Количество эффективной воды для поддержания постоянной консистенции составляло от 160 до 170 кг / м3 в зависимости от используемой добавки.
Базовая эталонная смесь (MIX I-A) была смешана с летучей золой каменного угля в пропорции 40% по объему цемента. Эта смесь была модифицирована метакаолином в пропорции 5% по объему цемента (MIX I-B) и порошком микрокремнезема в пропорции 5% по объему цемента (MIX I-C). Состав смеси (MIX I-D) содержал микронизированный известняк в количестве 40% по объему цемента.Химический анализ использованного метакаолина и микрокремнезема приведен в таблице 1. Через 28 дней основные физико-механические свойства были проверены на контрольных образцах. Образцы для испытаний, изготовленные из указанных смесей, подвергались воздействию различных агрессивных сред. Остальные образцы были помещены в агрессивные среды сроком на 12 месяцев.
Таблица 1. Химические характеристики метакаолина и микрокремнезема
Ti02 P205 Si02 Fe203 A1203 CaO MgO K20 Na20 SO42- S03 MgO
мета-каолин 0.49 0,15 49,2 1,01 42,2 0,9 1,83 0,79 0,11 0,48 ……
микрокремнезем 0,02 0,09 89,25 0,67 0,21 1,55 1,83 1,45 0,49 — 0,33 2,85
Таблица 2. Спецификация сред
Вещество Концентрация Относительная влажность
Газообразная среда — C02 98% 75%
Газообразная среда — S02 98% 75%
Жидкая среда — NaCl 1000 мг ДИ на 1 литр раствора —
Жидкая среда — Дизельное топливо 100% —
Референтное размещение — 100%
3.Оценка микс-дизайнов. Наблюдение и комментарии
В следующих таблицах с 3 по 8 указана оценка смешанных дизайнов в соответствии с методологией [1].
Михала Хубертова и Рудольф Хела / Процедура Инжиниринг 65 (2013) 2 Таблица 3. Изменение физико-механических свойств образцов в газовых средах
Прочность на сжатие Разница в прочности на сжатие Разница в объемном весе через 180 дней [МПа] по сравнению с исх.образец [%] комп. до значений перед экспонированием [%]
СО2 СО2 СО2 СО2 СО2 СО2
И-А 49,8 51,6 2,47 6,07 1,37 1,21
И-Б 49,8 49,8 6,98 6,87 1,25 1,37
И-К 49,0 49,6 0,62 1,95 0,67 1,40
И-Д 47,2 48,8 0,21 3,61 1,22 0,91
Таблица 4. Изменение физико-механических свойств образцов в жидких средах — постоянные условия
Прочность на сжатие Разница в сжатии Разница в объемном весе
через 180 дней [МПа] прочность по сравнению с исх.образец [%] комп. до значений перед экспонированием [%]
хлориды хлориды дизельного топлива хлориды дизельного топлива дизельное топливо
И-А 49,7 48,2 2,16 -0,93 0,85 0,68
И-Б 50,0 45,3 7,3 -2,69 0,62 1,3
I- c 49,5 48,1 1,64 -1,23 1,26 0,96
И- Д 47,5 47,2 0,85 0,32 1,19 1,01
Таблица 5. Изменение физико-механических свойств образцов в жидких средах — циклические условия
Прочность на сжатие после разницы в сжатии Разница объемного веса
Прочность на 180 дней [МПа] по сравнению с исх.образец [%] комп. до значений перед экспонированием [%]
хлориды хлориды дизельного топлива хлориды дизельного топлива дизельное топливо
И -А 48,7 48,8 0,21 0,31 0,8 0,86
И -Б 46,8 46,4 0,43 -0,32 0,75 1,63
I -C 48,9 40,2 0,41 -1,03 0,92 0,5
I -D 48,7 47,0 3,4 -0,21 0,56 0,95
Таблица 6. Классификация образцов, подвергшихся воздействию СО2 на стадии карбонизации
MIX Степень карбонизации ° K [%] Степень изменения модификации ° MP [-] pH [-] Стадия карбонизации I-A (P) 52.1 0,85 11,51 I. I-B (P) 34,1 0,95 11,84 I. I-C (P) 64,2 0,45 10,51 II. И — Д (П) _65.3_0.41_10.78_II.
Таблица 7. Классификация образцов, подвергшихся воздействию SO2 на стадии сульфатирования
MIX Степень сульфатирования ° S ‘%] pH [-] Степень сульфатирования
И-А (П) 7,778 11,51 И.
И-Б (П) 8,660 11,84 И.
I-C (P) 13,695 10,51 I.
I-D (P) 12,935 10,78 I.
И-Б (Н) 12.802 11,13 I.
Примечание: (П) — отбор проб с поверхности образца
.(H) — отбор проб с глубины 20-30 мм от поверхности испытуемого образца
Таблица 8. Химический анализ проб, помещенных в хлориды
Хлориды — постоянные [%] Хлориды — циклические [%]
l-A (P) 1 -B (P) 1- C (P) l-D (P) 1 -B (H)
<0,010 <0,010 0,040 0,070 <0.010
<0,010 <0,010 0,040 0,050 <0,010
3.1. Эффект C02
Образцы, подвергшиеся воздействию CO2 в определенных поверхностных слоях (глубиной 0-20 мм от поверхности), находятся на второй стадии карбонизации, за исключением MIX I-A с летучей золой и MIX I-B с метакаолином. Степень карбонизации подтверждается также наличием продуктов карбонизации (кальцит, арагонит, ватерит) в микроструктуре бетонной матрицы этих смесевых конструкций.На второй стадии карбонизации другие продукты гидратации цемента изменяются, например, вновь образовавшаяся модификация СаСО3 вместе с аморфным гелем кремниевой кислоты образуют кристаллические новообразования СаСО3 с очень мелким зерном. Свойства бетона не сильно меняются, что объясняет лишь небольшие различия в прочности на сжатие и объемном весе смесей. MIX I-A (с летучей золой) и I-B (с метакаолином) находятся на первой стадии карбонизации после 360 дней воздействия 98% CO2 и 75% относительной влажности воздуха.что является таким же состоянием, что и образцы, помещенные во внешнюю среду, в отношении уровня карбонизации. На первом этапе карбонизации. Гидроксид кальция в микроструктуре цементной матрицы (как кристаллический — портландит, так и из пространства между зернами) подвергается воздействию углекислого газа. Продуктом этих химических реакций является карбонат кальция, кристаллизующийся в виде кальцита. На второй стадии карбонизации. углекислый газ реагирует с гидросиликатами кальция, образуя мелкозернистый карбонат кальция в микроструктуре бетона, в частности, в форме арагонита и фатерита.
3.2. Эффект S02
Все конструкции смесей были отнесены к стадии 1 сульфатирования после 360 дней воздействия 98% SO2 при относительной влажности воздуха 75%. После сравнения содержания SO2 в образцах, находящихся в агрессивном газе и внешней среде, мы должны констатировать значительное увеличение содержания SO2. Повышенная деградация поверхностных слоев подтверждалась также заметным окрашиванием образцов. Однако результаты рентгеноструктурного анализа не подтвердили наличие продуктов сульфатирования (гипс, моносульфат.трисульфат), что указывает на повышенную деградацию цементной матрицы. На первом этапе. Ca (OH) 2 (или его раствор) в промежутках между зернами превращается в полугидрат сульфата кальция, который частично заполняет поры. Прочность бетона повышается, но значение pH снижается.
3.3. Эффект CI ‘
Сравнение результатов минералогического состава смеси-конструкции, помещенной в хлориды и во внешнюю среду, показало, что действие хлоридов на смеси-конструкции, модифицированные летучей золой, в течение 360 суток не вызывает образования новых фаз в их микроструктуре.что означало бы деградацию бетонной матрицы из-за хлоридов. Мы должны подчеркнуть, что ни один из протестированных смесей не показал через 360 дней появления хлоридов соли Фриделя или других минералов, которые могут вызвать давление расширения в микроструктуре материала и разрушить матрицу до степени снижения прочности тестируемого бетона. Модифицированный MIX I-B показал прирост прочности, что свидетельствует о положительном эффекте метакаолина. Хотя мы
предполагал более высокий уровень разложения из-за циклического действия хлоридов, мы не обнаружили каких-либо серьезных изменений по сравнению с постоянной экспозицией тестовых образцов.
3.4. Эффект дизель
Образцы, подвергшиеся воздействию дизельного топлива в течение 360 дней, не показали каких-либо серьезных изменений микроструктуры цементной матрицы. Наиболее очевидным доказательством загрязнения нефтепродуктами (дизельным топливом) является потеря воспламенения. Результаты этого анализа показывают незначительное загрязнение поверхностных слоев тестируемых смесевых конструкций. Сравнение образцов с глубины 200 мм образца, помещенного в дизельное топливо, и во внешней среде показывает, что загрязнена была только поверхность испытываемого бетона.Загрязнение поверхности образцов с циклической экспозицией дизельным топливом ниже, чем у образцов в постоянной экспозиции. Разница в прочности по сравнению с контрольными значениями незначительна, всего в пределах 3%. Сравнение загрязнения различных смесей-конструкций показывает, что смеси I-A (с летучей золой) и I-B (с метакаолином) однозначно противостоят проникновению нефтепродуктов (дизельное топливо).
4. Заключение
Смеси имеют классы прочности от LC 30/33 до LC 35/38 и классы объема D 1.6 по D 2.0 согласно европейскому стандарту EN 206-1. На основании полученных результатов можно утверждать, что использование угольной летучей золы однозначно положительно с точки зрения устойчивости и долговечности легкого бетона в агрессивных средах, в частности, CO2 и SO2. Анализы показывают, что смесь I-A (с летучей золой) и, в частности, смесь с летучей золой, модифицированной метакаолином (I-B), намного более устойчивы к коррозионным агентам, чем другие смеси. Использование пористых заполнителей для высокопрочных бетонов может быть неожиданным, учитывая важность прочности заполнителя для прочности высокопрочного бетона.Легкий заполнитель пористый и имеет довольно низкую прочность. Тем не менее, падение объемного веса бетона прочностью 50-60 МПа ниже 1800 кг / м3 может означать определенную экономию средств за счет снижения общего веса конструкции. Легкий самоуплотняющийся бетон на легком заполнителе Лиапор (максимальная прочность 10 МПа) с прочностью на сжатие от 50 до 60 МПа в настоящее время можно отнести к легким высокопрочным бетонам.
Благодарности
Этот результат был достигнут при финансовой поддержке Министерства промышленности и торговли Чешской Республики, проект MPO TIP FR — TI4 / 412.
Список литературы
[1] М. Матушек. Р. Дрочитка. 1998 «Атмосферная коррозия бетона». IKAS Прага. Республика Чехия. 1998. ISBN 80
809..[2] М. Губертова. Р. Хела. 2007 «Разработка и экспериментальное исследование свойств легкого самоуплотняющегося бетона». На 5-м симпозиуме RILEM по самоуплотняющемуся бетону. 1. Гент. Бельгия. 2007.
[3] М.Н. Хак. Х. Аль-Хайят. О. Каяли. 2004 «Прочность и долговечность легкого бетона».Цемент и бетонные композиты 26 (2004) 307-314.
[4] http://www.liapor.com.
Прочность конструкционного легкого бетона, содержащего вспученный перлитовый заполнитель | Международный журнал бетонных конструкций и материалов
Удельный вес и прочность на сжатие
Ключевым фактором, влияющим на удельный вес бетона, является удельный вес заполнителя, используемого при производстве бетона, поскольку он составляет основную долю во всей бетонной смеси.Удельный вес бетона постепенно уменьшался по мере увеличения количества EPA в бетонной смеси, как показано на рис. 5. Он находился в диапазоне от 2497 до 1729 кг / м. 3 , самый низкий показатель в смеси, приготовленной с 20%. EPA и самый высокий в смеси, приготовленной без него. Удельный вес бетона, приготовленного с EPA, снизился примерно на 20-30% по сравнению с обычным бетоном. Согласно классификации ACI 318 (ACI 318–10 2010), бетон, произведенный с 15% и 20% EPA, вполне может быть классифицирован как легкий бетон.
Рис.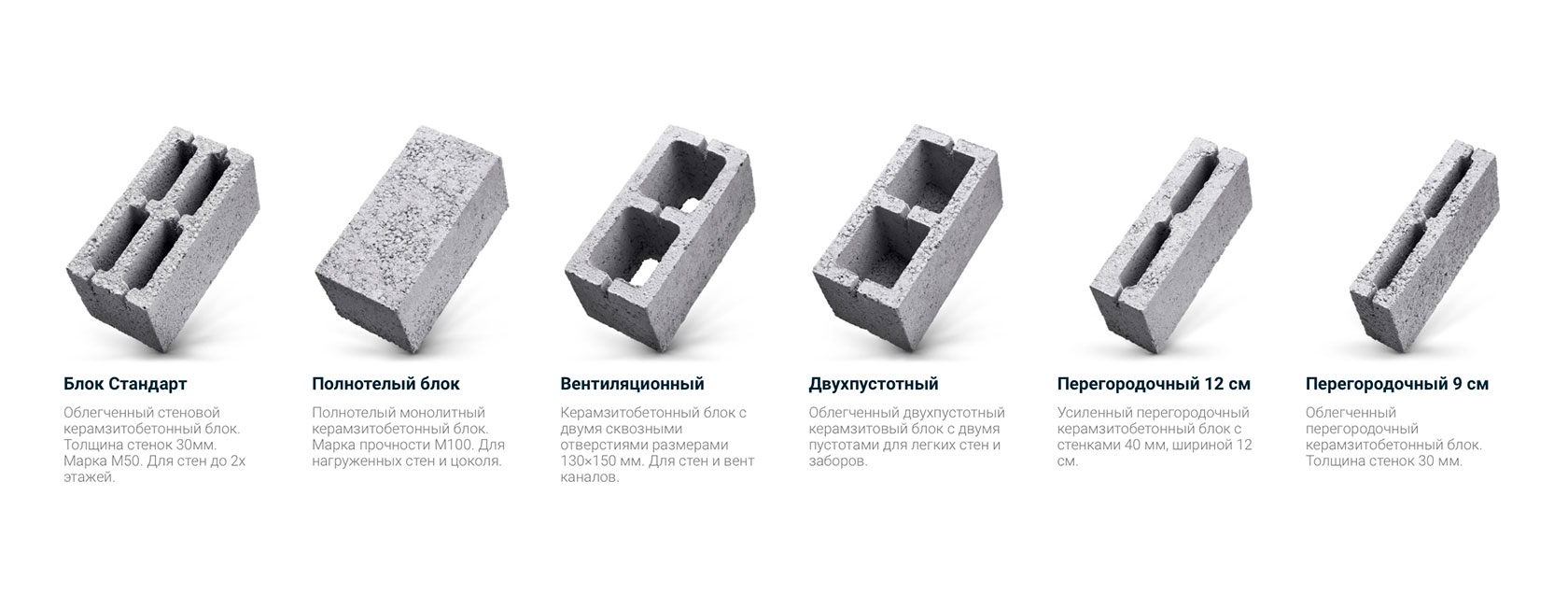
Удельный вес бетона, содержащего разное количество EPA.
На рисунке 6 показано изменение прочности бетона на сжатие. Как и ожидалось, прочность на сжатие была высокой в бетоне, приготовленном без EPA. После 1 дня отверждения прочность на сжатие составила 44,22, 16,97, 13,56 и 10,84 МПа в бетоне, содержащем 0, 10, 15 и 20% EPA, соответственно. Однако по мере продолжения отверждения прирост прочности бетона, содержащего ЭПК, был хорошим и через 28 дней составил 41.58, 31,13 и 23,69 МПа в бетонных смесях, содержащих 10, 15 и 20% ЭПК соответственно. Согласно стандартной классификации конструкционного легкого бетона ASTM C330 (2010), представленной на рис.7, бетон, имеющий равновесную плотность 1760 кг / м 3 , должен иметь минимальную 28-дневную прочность на сжатие 21 МПа, тогда как минимальная прочность 28 МПа требуется для плотности 1840 кг / м 3 . Следовательно, бетон, приготовленный в этом исследовании с 15 и 20% EPA, вполне может быть классифицирован как конструкционный легкий бетон.Прочность EPA-бетона была незначительно выше, чем стандартная спецификация, определяющая конструкционный легкий бетон.
Рис. 6Прочность на сжатие бетона, приготовленного с различным количеством EPA.
Рис. 7Минимальная прочность по ASTM 28 дней конструкционного легкого бетона.
В аналогичном исследовании, проведенном Кан и Демирбога (Кан и Демирбога, 2009), для производства бетона использовались модифицированные отходы заполнителя пенополистирола. Плотность разработанного LWC находилась в диапазоне 900–1700 кг / м 3 , тогда как соответствующая прочность на сжатие составляла от 13 до 23.5 МПа. В нескольких других исследованиях вулканическая пемза использовалась в качестве частичной замены грубого заполнителя, что позволило производить конструкционный легкий бетон с разумной прочностью и плотностью (Hossain 2004; Kılıç et al. 2003). Более низкая прочность на сжатие бетона, полученного из заполнителей, таких как пенополистирольные шарики, вулканическая пемза, а также EPA, вполне может быть отнесена на счет более низкой прочности и большого объема этих заполнителей, что приводит к недостаточному количеству цементного теста для их связывания.Кроме того, пористая природа заполнителя, а также повышенное количество воздуха, захваченного бетонной смесью, приводят к ослаблению цементирующей матрицы, что в конечном итоге снижает прочность бетона.
Прочность на изгиб
На рис. 8 показана прочность на изгиб бетона, полученного с различным содержанием EPA после трехточечной нагрузки на призматические образцы. Было отмечено, что разрушение бетона, модифицированного EPA, было до некоторой степени пластичным по сравнению с обычным бетоном.Результаты прочности на изгиб следовали той же тенденции, что и прочность на сжатие. Максимальная прочность на изгиб 4,70 и 5,29 МПа была получена после 28 и 90 дней отверждения соответственно в контрольной смеси, тогда как она была самой низкой в бетоне, приготовленном с 20% EPA. Произошло постепенное снижение прочности на изгиб по мере увеличения содержания EPA в бетонной смеси, которое составляло около 10,6, 26,3 и 38,6% в бетоне, приготовленном с 10, 15 и 20% EPA, соответственно, по сравнению с контрольной смесью через 28 дней. лечения.Снижение прочности на изгиб бетона, полученного с использованием EPA, может быть объяснено более слабой связью между соседними заполнителями, что приводит к более слабым плоскостям.
Рис. 8Прочность на изгиб бетона, приготовленного с различным содержанием EPA.
Водопоглощение
Водопоглощение — одна из основных характеристик бетона, определяющих его долговечность. Обычный бетон нормального веса обычно дает около 5% водопоглощения, что считается хорошим (Али и др.2018). Водопоглощение бетона, отвержденного в течение 28 дней, полученного в этом исследовании, составляло от 1,58 до 7,22%, в то время как оно составляло от 1,51 до 6,67% в образцах, отвержденных в течение 90 дней, как показано на рис. 9. Оно было самым низким для обычного бетона и самый высокий в бетоне, модифицированном 20% EPA. Более высокое водопоглощение бетона, модифицированного EPA, было связано с чрезмерными воздушными пустотами в бетоне и заполнителе, что делает его разрушительным по своей природе. Тем не менее, менее 6% водопоглощения, как в случае бетона, модифицированного EPA 10 и 15%, также считается очень хорошим.Как правило, водопоглощение легкого бетона составляет от 6 до 12% (Али и др., 2018; Анди Прасетио Вибово, 2017; Баджаре и др., 2013).
Водопоглощение бетона, приготовленного с различным содержанием EPA.
Водопоглощение в диапазоне от 4,10 до 7,22% после 28 дней отверждения в бетоне, модифицированном EPA, можно рассматривать как умеренное по сравнению с результатами предыдущих исследований. Такой тип характеристик разработанного бетона стал возможен благодаря тому, что он был произведен с более низким отношением воды к цементу в дополнение к частичной замене OPC на GGBFS, а также SF.Водопоглощение контрольной смеси по той же причине было менее 2%.
Усадка при высыхании
Деформация усадки при высыхании была измерена с использованием призматических образцов бетона. Частота измерения усадки была больше на начальных этапах воздействия по сравнению с последними. Как и ожидалось, усадка была быстрой во время первой стадии воздействия, впоследствии она была уменьшена, как показано на рис. 10. Деформация усадки при высыхании была максимальной в 20% модифицированном EPA бетоне с микродеформацией порядка 712, в то время как она была самый низкий в контрольной смеси около 548 мкД.Основным фактором, влияющим на характеристики усадки бетона, является скорость испарения воды с поверхности бетона, она была выше в случае бетона, приготовленного с 20% EPA. Впитывающая природа заполнителя также приводит к более высокой усадке бетона, и по мере увеличения количества такого типа заполнителя увеличивается и усадка (2010 г. ).
Деформация усадки при высыхании в бетоне, модифицированном EPA.
В ранее проведенном исследовании влияние сухой среды на усадочные свойства высокопрочного легкого бетона (HSLWC) было исследовано Zhang et al.(2010). LWC был приготовлен с использованием обычного песка в качестве мелких заполнителей и керамзита в качестве крупных заполнителей. Для сравнения, NWC был подготовлен с использованием обычного песка и гранита в качестве крупного заполнителя. Усадка LWC уменьшалась с уменьшением плотности агрегатов и увеличивалась с увеличением пористости агрегатов и водопоглощения. Добавление до 1,5% по объему волокна и 5% микрокремнезема в качестве замены связующего привело к получению LWC, который был менее подвержен усадке (2010 г.).В другом исследовании, где LWC был разработан с использованием волокна опунции, усадка увеличилась примерно на 18% из-за включения такого волокна в количестве 15 кг / м 3 по сравнению с контрольной смесью (Kammoun and Trabelsi, 2019).
Проницаемость и миграция хлоридов
На рисунках 11 и 12 показаны быстрая проницаемость и коэффициент миграции хлоридов в бетоне, приготовленном с EPA и без него, соответственно. Быстрая проницаемость для хлоридов справедливо указывает на долговечность бетона в хлоридной среде.Кроме того, коэффициент миграции, определенный на основе нестационарного состояния с помощью Nordtest NT BUILT 492, можно использовать для прогнозирования начала коррозии арматурной стали, залитой в бетон. Проницаемость для хлоридов в бетонных смесях, приготовленных с 0, 10, 15 и 20% EPA, составила 216, 354, 407 и 844 кулонов соответственно после 28 дней отверждения. Когда отверждение продлилось до 90 дней, эти значения значительно снизились и находились в диапазоне от 130 до 265 кулонов. На основании стандарта ASTM C1202 бетон, полученный в этом исследовании, можно классифицировать как очень низкопроницаемый.Коэффициент миграции хлоридов различных бетонных смесей следовал той же тенденции, что и проницаемость хлоридов. Он был максимальным в бетоне, приготовленном с 20% EPA, и самым низким в контрольной смеси. Величина коэффициента миграции хлоридов находилась в диапазоне от 8,80 до 17,07 (x10 −12 ) м 2 / с при 28 днях отверждения. Однако оно незначительно уменьшилось по мере того, как отверждение продлилось до 90 дней.
Хлоридопроницаемость бетона, модифицированного EPA.
Рис. 12Коэффициент миграции хлоридов в бетоне, приготовленном с различным содержанием EPA.
Обзор литературы показал, что было проведено меньше исследований для изучения аспекта долговечности LWC, особенно характеристик такого бетона в среде, содержащей хлориды. Среди немногих из них Чиа и Чжан (Chia and Zhang 2002) провели исследование свойств долговечности LWC, измерив проницаемость HSLWC для хлоридов и воды. Результаты сравнивались с результатами для высокопрочного NWC и обычного бетона, имеющего прочность на сжатие от 30 до 40 МПа.Результаты показали, что водопроницаемость LWC была ниже, чем у NWC. Высокопрочные LWC и NWC показали аналогичные результаты по водопроницаемости. Аналогичные результаты были также сообщены о способности LWC и высокопрочного NWC противостоять проникновению хлорид-ионов. Также сообщалось об отсутствии корреляции между глубиной проникновения воды и проникновением хлорид-ионов в бетон. По-видимому, существует корреляция между проницаемостью хлоридов и проникновением хлорид-ионов из-за того, что значения проницаемости увеличивались с глубиной проникновения хлоридов (Chia and Zhang 2002).
Коррозия арматурной стали
Потенциалы коррозии полуэлементов и плотность тока коррозии на стали, залитой в бетон, приготовленный с различным содержанием EPA, показаны на рис. 13 и 14 соответственно. Цилиндрические образцы бетона, приготовленные с использованием и без EPA, с центрально размещенной арматурой диаметром 12 мм, подвергались воздействию 5% раствора NaCl в течение более 600 дней. Измерения скорости коррозии проводились в течение всего периода эксплуатации. В начале воздействия потенциалы коррозии стали находились в диапазоне от -100 до -300, более отрицательные в образцах бетона, приготовленных с EPA.Эти значения постепенно становились все более отрицательными по мере продолжения воздействия. Величина потенциала коррозии стали, залитой в бетон, приготовленный с 0, 10, 15 и 20% EPA, составила -338, -327, -437-420 мВ, соответственно, примерно через 600 дней воздействия. Эти значения указывают на то, что вероятность того, что арматурный стержень находится в состоянии активной коррозии, составляет> 90%. Однако значения, измеренные для бетона, модифицированного 0 и 10% EPA, были менее отрицательными, чем значения для 15% и 20% EPA.
Потенциалы коррозии полуэлементов на стали, залитой в бетон, модифицированный EPA.
Рис. 14Плотность тока коррозии на стали, залитой в бетон, модифицированный EPA.
Состояние коррозии стали, основанное на величине плотности тока коррозии по классификации Милларда С. (Millard 2003), приведено в таблице 4. Плотность тока коррозии на стали во всех смесях, приготовленных в этом исследовании, была очень низкой. в начале воздействия. Она начала значительно увеличиваться для бетонной смеси, приготовленной с 20% EPA, и по прошествии примерно 150 дней скорость коррозии в этой конкретной смеси можно было классифицировать как высокую.Однако в других смесях, а именно с 0, 10 и 15% EPA, плотность тока коррозии была от очень низкой до умеренной на протяжении всего воздействия. После примерно 600 дней непрерывного воздействия 5% раствора NaCl плотность тока коррозии на стали в бетоне, приготовленном с использованием 0, 10, 15 и 20% EPA, составила 0,44, 0,41, 0,39 и 0,56 мкм / см 2 соответственно.
Таблица 4 Состояние коррозии стального стержня на основе плотности тока коррозии (Millard 2003).
Как упоминалось ранее, аспект долговечности LWC не исследовался подробно в предыдущих исследованиях.В частности, данные по коррозии арматурной стали, залитой в LWC, были ограничены. Ввиду потенциального воздействия на такой бетон среды, содержащей хлориды, аспект коррозии арматурной стали является существенным. Было изучено проведенное ранее исследование, в ходе которого LWC был разработан с использованием полиэтиленовых шариков и шлакового агрегата, вызывающего коррозию арматурной стали (Али и др., 2018). Однако в этом исследовании потенциалы коррозии стали были более отрицательными, чем -600 мВ, а плотность тока коррозии достигала 0.7 мкм / см 2 в некоторых предлагаемых бетонных смесях. Это было связано с пористой природой заполнителя, используемого при производстве такого бетона, в частности, из-за шлаков. В текущем исследовании эффективность LWC, разработанного с использованием EPA, была лучше по сравнению с предыдущим исследованием. Улучшенные характеристики бетона были связаны с низким водоцементным соотношением и добавлением дополнительных вяжущих материалов.
Тепловые характеристики
Результаты испытаний теплопроводности для всех четырех типов образцов бетона, приготовленных без и с различным процентным содержанием вспученного перлитового заполнителя (EPA), варьирующимся от 0 до 20%, представлены в числовом виде в таблице 5.Данные показывают, что было снижение теплопроводности для образцов бетона, модифицированного EPA, по сравнению с обычным бетоном (без EPA). Коэффициент теплопроводности для нормального бетона (без EPA) составил 1,138 Вт / мК, что является самым высоким значением по сравнению с другими образцами бетона (с EPA). Теплопроводность образцов бетона с 10, 15 и 20% EPA была намного ниже, чем у нормального образца бетона, примерно на 49,3, 58,7 и 65,6% соответственно. Уменьшение теплопроводности образцов бетона EPA объясняется изоляционной природой заполнителя, и по мере увеличения количества такого типа заполнителя в работе теплопроводность снижалась. Данные, полученные в этом исследовании, были сопоставимы с результатами более ранних исследований, проведенных с использованием различных типов заполнителей для производства легкого бетона (Али и др., 2018).
Обычно теплопроводность LWC колеблется от 0,1 до 0,7 Вт / мК для диапазона 600-1600 кг / м 3 плотности бетона (Jones and McCarthy 2005). Это значение уменьшается по мере уменьшения плотности. Теплоизоляционные свойства бетона обычно обратно пропорциональны плотности (Шривастава, 1977).В целом было замечено, что уменьшение удельного веса бетона на 100 кг / м 3 приводит к снижению теплопроводности на 0,04 Вт / м · К (Weigler and Karl 1980; Van Deijk 1991). Кроме того, в другом месте сообщалось, что использование пены в бетоне может привести к снижению удельного веса от 1000 до 1200 кг / м 3 с соответствующей теплопроводностью в диапазоне от 0,2 до 0,4 Вт / мК (Jones and McCarthy 2006 ). Результаты, полученные в текущем исследовании, показали аналогичные результаты.Основная причина снижения теплопроводности бетона, модифицированного EPA, в этом исследовании была связана с увеличением пути теплового потока из-за ячеистой природы агрегата перлита.
Структурное моделирование и поведение
Модель конечных элементов (МКЭ) была разработана в ABAQUS для изучения поведения предлагаемого бетонного материала при сейсмической нагрузке. Чтобы убедиться в достоверности модели, многоэтажная рамочная модель FEM была извлечена из исследования, проведенного Владом Инкулетом (Inculet, 2016).Первоначально модель была подготовлена и воспроизводила результаты, полученные в ходе первоначального исследования, а позже она была модифицирована для предполагаемого материала, используемого в этом исследовании. Подготовленная модель и дискретизация показаны на рис. 15а, б соответственно. Как показано на рис. 15b, была выбрана очень мелкая сетка, чтобы получить лучшее поведение конструкции при напряжении и деформации. Сейсмическая нагрузка прикладывалась к конструкции по оси z, анализ проводился для реальной землетрясения. Спектр нагрузки был извлечен из данных Влада Инкулета (Inculet, 2016), который представляет собой землетрясение, произошедшее в Румынии в 1977 году.Спектр нагрузок показан на рис. 16. Модель была проанализирована для бетонного материала, и свойства материала были определены на основе экспериментальных данных для бетонных смесей, модифицированных EPA M0, M10, M15 и M20.
МКЭ для сейсмического анализа. a FEM, b дискретизация.
Рис. 16Спектр нагрузок во время землетрясения во Вранче 1977 года в Румынии.
Сравнение распределения напряжений в основании колонны и пластического сноса на каждом уровне этажа было рассчитано на основе результатов ABAQUS.Дрейф сюжета по оси z был рассчитан с использованием уравнения, приведенного в формуле. 3, где \ (u_ {top} \) и \ (u_ {bottom} \) представляют боковое смещение (в данном случае по оси z) этажа на верхнем и нижнем уровне соответственно, и \ (H \) это высота рассматриваемого рассказа.
$$ d_ {s} = \ frac {{u_ {top} — u_ {bottom}}} {H} $$
(3)
Рисунок 17: Изменение времени в зависимости от дрейфа сюжета: (a) M0 (b) M10 (c) M15 (d) M20.17 (a) — 17 (d) представляет собой изменение дрейфа сюжета на каждом временном отрезке Спектр нагрузок для бетона, модифицированного EPA M0, M10, M15 и M20, соответственно.Во всех случаях максимальный дрейф наблюдался на уровне первого этажа, соответствующие значения: \ (6.30, 6.78, 5.18, 4.78 \) для \ ({\ text {M}} 0, {\ text {M}} 10, {\ text {M}} 15 \) и \ ({\ text {M}} 20 \), соответственно, как показано на рис. 17: Изменение времени с течением истории: (a) M0 (b) M10 (c) M15 (d) M20.17 (a) — 17 (d). Это показывает, что меньший дрейф сюжета наблюдался при использовании \ (20 \% \) EPA (M20). Это лучшее наблюдение с точки зрения требований к удобству обслуживания конструкции по сравнению с другими смесями.
Изменение времени с дрейфом сюжета: ( a ) M0 ( b ) M10 ( c ) M15 ( d ) M20.
Аналогичным образом, изменение напряжения колонны на уровне первого этажа было исследовано с использованием результатов МКЭ, как показано на рис. 18a – d для M0, M10, M15 и M20, соответственно. Это показывает, что в случае нормального бетона (M0) конструкция достигает пластической области, а максимальные напряжения составляют \ (5.57 \, {\ text {MPa}} \) при сжатии и \ (4.74 \, {\ text {MPa}} \) при растяжении (см. Рис. 18а). Эти значения лучше согласуются с экспериментальными данными, поскольку прочность на сжатие и изгиб бетона M0 составляет \ (62.49 \, {\ text {MPa}} \) и \ (4.70 \, {\ text {MPa}}, \) соответственно (см. рис. 6, 8). Таким образом, в колоннах можно наблюдать трещину при изгибе, следовательно, структура демонстрирует неупругое поведение в последовательных циклах нагрузки.
Рис.18Изменение деформации в зависимости от напряжений на уровне первого этажа колонны: ( a ) M0 ( b ) M10 ( c ) M15 ( d ) M20.
С другой стороны, когда используется бетон \ (M10, M15 \) и \ (M20 \), конструкция все еще находится в упругой области, как показано на рис. 18b – d соответственно. Как показано на рис. 18b, максимальные напряжения составляют \ (4.34 \, {\ text {MPa}} \) при сжатии и \ (3.34 \, {\ text {MPa}} \) при растяжении в случае \ ( M10 \) бетон, однако эти значения равны \ (2.17 \, {\ text {MPa}} \) & \ (1.67 \, {\ text {MPa}} \), \ (1.54 \, {\ text {MPa }} \) & \ (0.93 \, {\ text {MPa}} \), соответственно, когда используется бетон \ (M15 \) и \ (M20 \).Эти значения меньше характерной прочности на изгиб при сжатии этого бетона. Таким образом, бетон M20 показывает лучшее поведение при сейсмической нагрузке из-за его гибкости и пониженной плотности.
Легкий конструкционный бетон | Журнал Concrete Construction
Осознание стоимости и желание использовать новые конструкции стимулировали интерес строителей к легкому конструкционному бетону. Тридцать процентов производства керамзита, сланца и сланца и около 5 процентов заполнителей вспученного шлака использовались в конструкционном бетонном бетоне.В настоящее время для производства вспученных шлаковых заполнителей используется несколько процессов. В процессе Кинни-Осборна шлак сначала проходит через диафрагму, а затем обрабатывается воздухом, паром или водой. В машине Колдвелла вода смешивается со шлаком в цилиндрическом корпусе, и радиальные лопасти выбрасывают расширенный продукт через отверстие в корпусе к стальной мишени на расстоянии нескольких футов. Немеханическое средство производства вспученного шлака называется струйной или шахтной системой. Здесь расплавленный шлак падает потоком перед соплом, из которого выделяется пар, воздух или вода.Расширение происходит по мере падения шлака. Свойства легкого бетона сильно различаются по соотношению содержания цемента, прочности и веса. Например, различные легкие заполнители, даже те, которые производятся аналогичными способами, требуют значительного диапазона содержания цемента для производства бетона с эквивалентной прочностью. Таким образом, есть логика обратиться к производителю конкретного материала за рекомендациями относительно пропорций пробной смеси. Другие характеристики: модуль упругости находится в диапазоне от полутора до двух третей значений для бетонов, содержащих гравий, камень или с воздухововлекающими добавками, они обладают отличными теплоизоляционными свойствами, но усадка при высыхании имеет тенденцию к несколько более высокой.Удовлетворительные результаты с легкими заполнителями из глины, сланца, сланца и шлака требуют адекватного времени перемешивания и более длительного цикла, чем с обычным бетоном. Полная рекомендуемая процедура: (1) загрузите в смеситель от 65 до 75 процентов от общего количества воды и всего предварительно увлажненного заполнителя. (2) Перемешивайте около 1 минуты. (3) Добавьте цемент, любую добавку и оставшуюся воду для затворения. (4) Смешайте всю партию в течение 60 секунд для миксеров на 1 кубический ярд плюс 15 секунд для каждого кубического ярда.
ГЛИНА ОБЛЕГЧЕННАЯ И СЛАНЦЕВЫЕ ЗАПОЛНИТЕЛИ
LES GRANULATS LEGERS D’ARGILE ET DE SCHISTE РАСШИРЯЕТСЯ
Приведены подробные сведения об использовании и производстве легкого керамзита и сланцевых заполнителей.Образование небольших полостей внутри агрегатов происходит между 1100 и 1200 градусами. Это явление обусловлено присутствием в глине минеральных ингредиентов, которые вызывают газообразные выбросы при температуре, превышающей температуру плавления глины или равной ей, и возникновением фазы плавления с достаточной вязкостью для улавливания выделяемых газов. Приведены данные о сырье, используемом в производстве (в основном, глине и сланце), и о наиболее удовлетворительных характеристиках. Описаны технологические аспекты производства: подготовка материалов, сушка, обжиг, а также основные характеристики: насыпная плотность (от 250 до 900 кг / м3), коэффициент водопоглощения (менее 15%), химический состав (спецификация: составляется и будет ограничивать содержание серы).Проводятся исследования по изучению методов измерения механической прочности. Рассмотрены основные способы использования. / TRRL /
- Наличие:
- Корпоративных авторов:
Editeur Dunod
26 Boulevard de l’Hopital
Paris 5e, Франция - Авторов:
- Дата публикации: 1972-6
Язык
Информация для СМИ
Предмет / указатель терминов
Информация для подачи
- Регистрационный номер: 00099620
- Тип записи: Публикация
- Агентство-источник: Центральная лаборатория мостов и домов (LCPC)
- Файлы: ITRD, TRIS
- Дата создания: 18 ноября 1975 г., 00:00
ПРОИЗВОДСТВО ОБЛЕГЧЕННЫХ НАПОЛНИТЕЛЕЙ ГЛИНЫ
Была сделана попытка исследовать возможности производства легких керамзитовых заполнителей из некоторых иракских почв.Исследования почвы проводились в некоторых регионах в средней и южной частях страны с целью найти подходящие природные экспансивные глины. Результаты испытаний показали, что исследованные почвы не подходят для прямого расширения из-за высокого содержания в них флюса и, в частности, кальцита. На таких почвах гранулы быстро, в коротком диапазоне температур, превращаются в липкую стекловидную массу. Затем исследования были направлены на изучение возможностей уменьшения флюса за счет надлежащей обработки почвы, а также за счет модификации техники обжига.Помимо организации дальнейших исследований почв в других частях страны с целью обнаружения обширных глин. В отдельных разделах представлены данные для проверки основных характеристик грунтов, используемых методов обработки, свойств полученных заполнителей, а также свойств некоторых низкодисперсных бетонов, изготовленных с некоторыми из спеченных заполнителей. (Автор / TRRL)
- Корпоративных авторов:
Центр Строительных Исследований
с.О. Box 127, Джадрия
Багдад, Ирак - Авторов:
- Аль-Касс, R M
- Аль-Халисси, F Q
- Дата публикации: 1979-12
Информация для СМИ
Предмет / указатель терминов
Информация для подачи
- Регистрационный номер: 00341430
- Тип записи: Публикация
- Агентство-источник: Транспортная исследовательская лаборатория
- Номер отчета / статьи: Res Paper 61/79 Monograph
- Файлы: ITRD, TRIS
- Дата создания: 22 декабря 1981 г., 00:00
Прочность легкого самоплотного бетона
Башанди А.A. 1 , Etman Z. A. 1, 2 , Azier H. Y. 3
1 Доцент, Civil Eng. Кафедра инженерного факультета Университета Менуфия, Египет
2 Доцент, инженер гражданского строительства. Деп., Высший инженерно-технологический институт, Менуфия, Египет
3 Инженер-строитель и магистр наук. Кандидат 1
Адрес для корреспонденции: Азье Х.Ю., инженер-строитель и магистр наук. Кандидат 1.
Эл. Почта: |
Copyright © 2019 Автор (ы). Опубликовано Scientific & Academic Publishing.
Эта работа находится под лицензией Creative Commons Attribution International License (CC BY).
http://creativecommons.org/licenses/by/4.0/
Аннотация
Легкий бетон является отличной альтернативой с точки зрения снижения собственной нагрузки на конструкцию, в то время как самоуплотняющийся бетон облегчает заливку и уплотнение во время строительства.Сочетание преимуществ обоих типов — новая область исследований. Учитывая его легкую структуру и простоту укладки, легкий самоуплотняющийся бетон может быть ответом на возрастающие требования к конструкции сильно армированных структурных элементов. Основными переменными в этом исследовании являются коэффициент замены легкого керамзита LECA при использовании суперпластификаторов. Предлагаемый подход основан на модифицированной конструкции смеси и включает возможности реализации LW-SCC в зависимости от двух основных параметров: класса плотности и класса прочности на сжатие.Для этого было использовано 12 бетонных смесей. Были проведены испытания бетонных образцов для определения прочности на сжатие, модуля упругости и прочности на разрыв. Также измеряли удельный вес. Эти испытания позволили понять поведение легких самоуплотняющихся бетонов при воздействии хлоридов или сульфатов. Результаты показали, что лучшая прочность достигается при использовании коэффициента замены 50% с более низким весом примерно на 30% по сравнению с самоплотным бетоном с нормальным весом.Также было показано, что можно производить конструкционный легкий самоуплотняющийся бетон с достаточной прочностью. Следовательно, его можно использовать в строительных целях и в сборных железобетонных элементах с умеренной стоимостью и удовлетворительной прочностью.
Ключевые слова: Легкий самоуплотняющийся, Бетон, Прочность, LECA
Цитируйте эту статью: Bashandy A.А., Этман З. А., Азье Х. Й., Долговечность легкого самоплотного бетона, Международный журнал строительной инженерии и управления , Vol. 8 No. 5, 2019, pp. 127-135. DOI: 10.5923 / j.ijcem.201
|
|
|
|
|
|
3.2. Бетонные образцы
- Были проведены испытания бетонных образцов для определения прочности на сжатие, модуля упругости и прочности на разрыв.Также измеряли удельный вес. Эти тесты позволили понять поведение этих легких бетонов. Стандартные бетонные кубы с длиной стороны 100x100x100 мм и длиной стороны 150x150x150 мм со встроенным стержнем диаметром 12 мм были использованы для определения прочности на сжатие (FCU) и прочности сцепления (Fb) соответственно. Стандартные бетонные цилиндры 100×200 мм, испытание на непрямое растяжение (метод раскалывания) и 150×300 мм были проведены для определения прочности на разрыв и модуля упругости, соответственно, бетонных смесей.Призмы размером 100x100x500 мм были отлиты и использовались в качестве образца для испытаний на изгиб (fcr). Усиленные балки LW-SCC размером 100x150x1000 мм были отлиты для изучения поведения железобетонных балок, отлитых с использованием этого типа бетона, как показано на рис. (1).
Рис ure 1 . Образцы бетона |
3.3. Отверждение бетона
- Отверждение проводят обычным образом (отверждение водой) для обычных образцов бетона, образцы выдерживали в формах в течение 24 часов, затем их вынимали и погружали в чистую воду для отверждения при комнатной температуре в диапазоне 25-32 ° C до испытательного возраста.
3.4. Моделирование сульфатной атаки
- Для моделирования сульфатной атаки образцы погружали в раствор MgSO4 с концентрацией 20% на периоды до 4 месяцев непрерывного погружения и циклического погружения. Все образцы погружают, а затем тестируют через 2 и 4 месяца соответственно. Результаты сравнивают с контрольными образцами LW-SCC A5 в качестве контрольной смеси. Испытываемые образцы представляют собой стандартные кубы, цилиндры и призмы для получения значений прочности на сжатие, растяжение при расщеплении и изгиб.Эффекты сульфатной атаки достигаются с точки зрения прочности на сжатие, растяжение при расщеплении и изгиб.
3.5. Моделирование атаки хлоридов
- В этих экспериментах моделирование атаки хлоридов было выполнено путем непрерывного погружения и циклического погружения образцов в 5% раствор HCL в течение 4 месяцев. Все образцы погружают, а затем тестируют через 2 и 4 месяца соответственно. Результаты сравнивают с контрольными образцами LW-SCC A5 в качестве контрольной смеси.Испытываемые образцы представляют собой стандартные кубы, цилиндры и призмы для получения значений прочности на сжатие, растяжение при расщеплении и изгиб. Эффекты сульфатной атаки достигаются с точки зрения прочности на сжатие, растяжение при расщеплении и изгиб.
3,6. Процедуры испытаний
- Экспериментальная программа проводилась в два этапа. Первый этап был выполнен для получения конструкционного LW-SCC. Это было проведено двумя методами; один, смесь A LW-SCC, путем замены обычного грубого и мелкого заполнителя на легкий заполнитель (расширенный легкий заполнитель LECA) в качестве частичной замены (как 10%, 20%, 30%, 40%, 50%, 60% использованного доломита), а другой — смеси B LW-SCC, с использованием примесей с воздухововлекающими добавками.. Вторая часть была проведена для оценки стойкости LW-SCC к воздействию сульфатов или хлоридов. Были проведены испытания свойств свежего и затвердевшего бетона. Испытание на оседание было проведено для оценки пластической консистенции свежих смесей в соответствии с египетскими практическими правилами (E.C.P. 203/2018) [10], как показано на рис. (2), а в таблице (8) указаны результаты оседания. Затвердевшие свойства бетона были получены с точки зрения прочности на сжатие, растяжение при раскалывании и изгиб.
Рис ure 2 . J-образное кольцо и испытание на поток LW-SCC |
4. Результат и обсуждение
4.1. Основные свойства образцов LW-SCC
- Были получены свойства свежего и затвердевшего бетона контрольных смесей LW-SCC. Разработка с использованием LECA в качестве крупнозернистого заполнителя с 12 следами смесей для улучшения легкого самоуплотняющегося концерта, как показано на рис.(1). Была получена прочность на сжатие 70 МПа. Сравнение смесей LW-SCC для получения конструкции смеси с удельным весом менее 1900 кг / м 3 и прочностью на сжатие более 28 МПа.
4.1.1. Прочность на сжатие
- Прочность на сжатие кубов LW-SCC в возрасте 3, 7 и 28 дней была получена, как показано на рис. (3). значения прочности на сжатие были взяты как среднее значение для 3 одинаковых кубов. Полученные результаты испытаний показали, что прочность на сжатие для смеси A5 такая, как показано на рис.(7) и (8). Результат показал, что LW-SCC всегда меньше, чем у обычных, в зависимости от процента замены заполнителей на LECA, начиная с 10%, 20%, 30%, 40%, 50% и 60%, прочность на сжатие снижается на 19,39%, 28,33%, 35,1%, 39,1%, 42,22% и 45,14% соответственно, а из-за аэрированной добавки прочность на сжатие снизилась на 22,1%, 32,02%, 39,81%, 45,7%, 52,02% и 61,04% соответственно. Значения прочности были записаны, как показано в таблице (8).
Стол (8) . Пропорции используемых смесей NW-SCC и LW-SCC |
4.1.2. Прочность на разрыв при расщеплении
- Предел прочности при расщеплении цилиндров LW-SCC в возрасте 28 дней был получен, как показано на рис. (5). значения прочности на разрыв при расщеплении были взяты как среднее значение для 3 идентичных цилиндров. Результат показал, что LW-SCC всегда меньше обычных, связанных с процентом замены агрегатов на LECA, начиная с 10%, 20%, 30%.40%, 50% и 60% прочность на разрыв при раскалывании снизилась на 10%, 27,3%, 27,3%, 31,8%, 45,5% и 50% соответственно, а из-за аэрированной добавки прочность на разрыв при раскалывании снизилась на 22,1%, 32,02%. , 39,81%, 45,7%, 52,02% и 61,04% соответственно. Значения прочности были записаны, как показано на рис. (9).
Рис ure 3 . Испытание на прочность при сжатии |
Рис. ure 4 . Испытание модуля упругости |
Рис. ure 5 . Испытание на прочность при раскалывании |
4.1.3. Прочность на изгиб
- Прочность на изгиб призм LW-SCC в возрасте 28 дней была получена, как показано на рис. (6). значения прочности на изгиб были взяты как среднее значение 3 идентичных призм.
Рис ure 6 . Испытание бетонных призм на изгиб 100 * 100 * 500 мм |
Рис. ure 7 . Прочность на сжатие группы «А» образцов LW-SCC разного возраста |
Рис. ure 8 . Прочность на сжатие группы «В» образцов LW-SCC разного возраста |
Рис ure 9 . Значения прочности на разрыв для контрольных смесей, смесей «А» и смесей «В» через 28 дней |
Рис. ure 10 . Значения прочности на изгиб для контрольной смеси, смесей «А» и смесей «В» через 28 дней |
4.1.4. Модули упругости
- Модули упругости цилиндров LW-SCC в возрасте 28 дней были получены, как показано на рис. (4). модули значений упругости были приняты как средние для 3-х идентичных цилиндров. Результат показал, что LW-SCC всегда меньше обычных, связанных с процентом замены агрегатов на LECA, начиная с 10%, 20%, 30%.40%, 50% и 60% модули упругости уменьшились на 12,78%, 28,1%, 38,12%, 38,8%, 40,2% и 45,1% соответственно, а из-за аэрированной примеси модули упругости уменьшились на 28,27%, 31,12 %, 37,50%, 41,8%, 48,9% и 51,06% соответственно. Значения прочности были записаны, как показано на рис. (12).
4.1.5. Относительная прочность сцепления
- Относительная прочность сцепления кубиков LW-SCC диаметром 12 мм в возрасте 28 дней была получена таким образом, что LW-SCC всегда меньше, чем обычные, связанные с процентом замены заполнителей на LECA, начиная с 10 %, 20%, 30%.40%, 50% и 60%, напряжение уменьшилось на 21%, 32%, 41%, 47%, 52% и 57% соответственно, а за счет аэрированной добавки напряжение уменьшилось на 35%, 41%, 57%. , 60%, 63% и 71% соответственно. Значения относительной прочности связи были записаны, как показано на рис. (11).
Рис ure 11 . Значения относительного напряжения сцепления для контрольной смеси, смесей «А» и смесей «В» через 28 дней |
Рис. ure 12 . Значения модуля упругости и прочности контрольной смеси, смесей «А» и смесей «В» через 28 дней |
4.2. Долговечность образцов LW-SCC
- Это исследование было выполнено в основном для изучения долговечности LW-SCC из-за проникновения хлорида 5% и сульфата 20% концентрации, были изучены характеристики потенциала коррозии.
4.2.1. LW-SCC под воздействием хлоридов
- Смесь LW-SCC «A5» была выбрана как лучшая смесь для изучения ее стойкости к воздействию хлоридов. Прочность на сжатие образцов LW-SCC снизилась после воздействия хлорида в течение 2 месяцев при непрерывном погружении и циклическом погружении в раствор хлорида примерно на 12,6% и 7,94% соответственно по сравнению с контрольными образцами A5, как показано на рис. 13). Через 4 месяца прочность на сжатие образцов LW-SCC снизилась для погруженных и циклических погружений в раствор хлорида примерно на 33,3% и 26,98%, соответственно, по сравнению с контрольными образцами A5, как показано на рис. (13).
Рис ure 13 . Прочность на сжатие LW-SCC, смесь «A5», под воздействием хлоридов 5% концентрации через 2 и 4 месяца |
Рис ure 14 . Прочность на растяжение при раскалывании смеси LW-SCC, смесь «A5», под воздействием хлоридов с концентрацией 5% через 2 и 4 месяца |
Рис ure 15 . Прочность на изгиб LW-SCC смеси «А5» при воздействии хлоридов 5% концентрации через 2 и 4 месяца |
4.2.2. LW-SCC при сульфатной атаке
- Смесь LW-SCC «A5» была выбрана как лучшая смесь для изучения ее стойкости при сульфатной атаке. Прочность на сжатие образцов LW-SCC снизилась после сульфатной атаки в течение 2 месяцев при непрерывном погружении и циклическом погружении в раствор сульфата примерно на 30,1% и 20,6% соответственно по сравнению с контрольными образцами A5, как показано на рис. 16). Через 4 месяца прочность на сжатие образцов LW-SCC снизилась для погруженных и циклических погружений в раствор сульфата примерно на 49,2% и 39,7%, соответственно, по сравнению с контрольными образцами A5, как показано на рис. (16).
Рис ure 16 . Прочность на сжатие LW-SCC, смесь «A5», под воздействием сульфатов с концентрацией 20% через 2 и 4 месяца |
Рис ure 17 . Предел прочности на разрыв смеси LW-SCC, смесь «A5», под воздействием сульфатов с концентрацией 20% через 2 и 4 месяца |
Рис ure 18 . Прочность на изгиб LW-SCC, смесь «A5», под воздействием сульфатов 20% концентрации через 2 и 4 месяца |
5. Выводы
- В этом исследовании была проведена серия экспериментов для исследовать поведение LW-SCC. Результаты, полученные в результате этого исследования, можно резюмировать следующим образом: 1. Конструкционный бетон LW-SCC может быть получен с использованием керамзитового заполнителя (LECA). 2. Плотность полученного LW-SCC варьировалась от 1870 до 1950 кг / м 3 , что меньше веса обычного бетона с плотностью 2450 кг / м 3 . 3. Прочность на сжатие LW-SCC снизилась на 33,45% по сравнению с контрольной бетонной смесью. Прочность на разрыв при расщеплении и модуль упругости имели аналогичный характер. 4. Армированные балки LW-SCC ведут себя так же, как обычные бетонные балки. 5.На долговечность смесей LW-SCC влияет общая доля LWA. 6. Под воздействием хлоридов прочность на сжатие снизилась до 33,3%, разрывное растяжение снизилось до 29%, прочность на изгиб снизилась до 37,5% по сравнению с контрольными образцами. 7. Под действием сульфата прочность на сжатие снизилась до 49,2%, растяжение при расщеплении снизилось до 37,5%, прочность на изгиб снизилась до 37,5% по сравнению с контрольными образцами. 8.Прочность легкого самоуплотняющегося бетона «LW-SCC» достаточна по сравнению с прочностью самоуплотняющегося бетона нормального веса «NW-SCC» с уменьшением LW-SCC при воздействии хлоридов и сульфатов примерно на 33,3%. и 49,2% соответственно. Как правило, лабораторные исследования подтверждают возможность получения структурных LW-SCC. Его использование эффективно там, где требуется легкий бетон с характеристиками самосуплотнения, например, в облицовках и декоративных бетонах.По результатам испытаний на долговечность; LW-SCC рекомендуется использовать в условиях низкой и средней агрессивности. В случае агрессивных условий необходима защита / изоляция бетона.
Каталожные номера
[1] | Б.Вахшоури, С.Неджади, Смешанное проектирование легкого самоуплотняющегося бетона Примеры использования строительных материалов 4 (2016) 1–14. |
[2] | П. Л. Домоун, самоуплотняющийся бетон: анализ практических примеров за 11 лет, Cement Concr. Комп. 28 (2006) 197–208. |
[3] | Э. П. Келер, Д. У. Фаулер, ICAR Project 108: Заполнители в самоконсолидирующемся бетоне, Фонд агрегатов для технологий, исследований и образования (AFTRE) (2015). |
[4] | P. Y. Lin, Y. Y. Chang, C. J. Chen, S. B. Wen. Приготовление легкого заполнителя из смеси низководного пластового ила и сухих порошков.В: Конференция и выставка технологий бетона TCI 2007, Бумага; 2007 [N-5]. |
[5] | С. Жардин, Г. Балоевич, А. Харапин, Экспериментальные испытания влияния мелких частиц на свойства самоуплотняющегося легкого бетона, Adv. Матер. Sci. Англ. 2012 (2012) 8 Идентификационный номер статьи 398567. |
[6] | М. Каффетзакис, К. Папаниколау, Метод дозирования смеси для легкого заполнителя SCC (LWSCC) на основе концепции оптимальной точки упаковки, Innovative Mater. |