Опилкобетон своими руками — свойства, характеристики и применение
Опилкобетон является лёгким бетоном, в составе которого обязательно наличие цемента, опилок, минерализаторов и песка. Этот материал отличается экологичностью, малый весом, а также повышенным уровнем устойчивости к огню, низкой теплопроводностью и высокой проницаемостью для пара. Его применяют для строительства монолитных зданий или для создания строительных блоков. Также из него можно возводить несущие конструкции. В регионах, где имеются деревообрабатывающие предприятия, заполнителем выступают древесные опилки. Такой композитный материал по своим санитарно-гигиеническим характеристикам можно назвать самым комфортным из всех легких бетонов для возведения жилых зданий.
Состав опилкобетона
Наиболее оптимальным вариантом для формирования блоков опилкобетона можно назвать использование свежих опилок из древесины хвойных сортов. В том случае, если вы намерены создавать блоки из старых опилок, то их обязательно нужно защитить от гниения специализированными препаратами.
Коэффициент плотности опилкобетона находится в непосредственной зависимости от соотношения опилок, вяжущего материала и песка. При увеличении процентного количества органических ингредиентов, повышаются теплотехнические показатели, но падает уровень прочности. В то время, как повышение количества вяжущего компонента и песка приводит к повышению прочностных качеств, водонепроницаемости, морозостойкости и снижению коррозии арматурных элементов.
Готовим опилкобетон своими руками
Марка опилкобетона |
Цемента М400 на 1м3 (кг) |
Известь гашеная на 1м3 |
Песок | Опилки | Удельная плотность (кг/м3) |
Коэф.![]() водности |
М10 (одноэтажный дом) |
90 | 165 | 530 | 210 | 950 | 0.21 |
М15 (двухэтажный дом) |
135 | 105 | 610 | 200 | 1050 | 0.24 |
М25 (технологические постройки) |
300 | 100 | 670 | 190 | 1250 | 0.37 |
Где применяется опилкобетон?
Исходя из количественного соотношения ингредиентов, данный композитный материал бывает таких марок:
- 15 и М 20 является прекрасным материалом для создания внутренних и наружных стен домов, коттеджей, дач, хозяйственных построек – сараев, гаражей, бань. Кроме этого они применяются для реконструкции зданий
- М 5 и М 10, вследствие высоких теплоизоляционных свойств, подходят для утепления уже построенных стен, подвалов.
Из опилкобетона создают даже заборы и столбы.
В том случае, если вы используете опилкобетон для реконструкции здания, то нет необходимости усиливать фундамент.
Главной отличительной особенностью опилкобетона можно назвать его небольшую массу. Строение, имеющее площадь 250 м2 будет весить лишь 50 тонн, что дает возможность обойтись без создания сложного фундамента. Опилкобетон может применять в любом строительном проекте, который рассчитан на другие материалы. С применением опилкобетона, вы существенно снизите расходы на возведение объекта.
Плюсы и минусы опилкобетона
Среди положительных качеств стоит выделить:
- он отлично поддается механической обработке. Опилкобетонный блок можно пилить, сверлить, крепить гвоздями, вследствие чего повышается качество монтажных работ и экономится стеновой материал. В случае необходимости подгонки блока, от него куски не откалывают, а рубят. Если нужно получить точные размеры опилкобетонный блок режут ножовкой.
По удобству этот материал можно сравнить с газосиликатными и пеноблоками
- цемент, который лежит в основе опилкобетона, представляет собой отличную основу для всех покрытий защитного и декоративного назначения. Клей, применяемый в ходе облицовки блоков, гарантирует прочное сцепление отделки с основой
- водопоглощение опилкобетона находится на уровне обычных строительных материалов. Посредством облицовки опилкобетонных поверхностей защитно-декоративными покрытиями или применения гидрофобизирующих средств дает возможность уменьшить водопоглощающую способность до 2-4 %
- опилкобетон, который создан с соблюдением специальной технологии, не имеет горючих свойств. Высокий уровень огнестойкости материала гарантируется тем, органические ингредиенты полностью покрыты цементно-песчаной стенкой. Блок, имеющий до 50% опилок, отличается огнестойкостью на протяжении 2,5 часов при температуре до 12000С. Стоит отметить, что по уровню огнестойкости опилкобетон превосходит пенополистиролбетон, по этой причине он подходит для реализации всего объема строительных работ
- теплотехнические показатели опилкобетоны вплотную приближают его к очень популярным поризованным бетонам
- отличные звукоизоляционные показатели
- легкость монтажа
- длительный период эксплуатации
- доступная цена.
К сожалению, идеальных материалов не существует и у опилкобетона есть свои минусы. К главным минусам относят:
- медленный набор прочности в процессе изготовления элементов, толщина которых превышает 200 мм. Свои марочные прочностные характеристики опилкобетон приобретает лишь через 90 дней после изготовления
- необходимость качественной влагозащиты, как внутри, так и снаружи, а также монтажа пароизоляции – пергамина между блоками и облицовкой
- опилкобетон на протяжении длительного времени находится в легкодеформируемом состоянии, то есть блоки пружинят во время монтажа.
Опилкобетон своими руками
Все составляющие опилкобетона, хороши тем, что их нет необходимости заготавливать заранее. Все, их чего состоит данный материал можно приобрести в магазинах, занимающихся торговлей стройматериалами, а также на рынках или складах. По этой причине заготовкой можно начать заниматься практически за день до начала производства.
Поскольку приготовление опилкобетона своими руками представляет собой довольно трудоемкий процесс, стоит для смешивания компонентов приобрести бетономешалку или растворосмеситель. Первым делом высушенные опилки нужно просеять через сито, с ячейками 10*10 мм. После этого опилки смешивают с песком и цементом. Далее в приготовленную смесь добавляется глиняное или известняковое тесто и все хорошо вымешивается. Полученную смесь нужно развести водой, порционно добавляя ее. После каждого долива воды смесь нужно перемешать.
О правильном приготовлении смеси говорит пластичный комок при сжатии в кулаке. На этом комке должны быть видны следы от пальцев и не должно быть выступающих капель воды. Это главные признаки готовности смеси. Далее из смеси можно формировать блоки. Помните, что нельзя медлить! Через 1,5-2 часа смесь станет твердой. При укладке смеси в форму нужно удостовериться, что весь воздух вышел во время утрамбовывания.
Для того, чтобы сделать определенную марку, нужно соблюсти пропорции:
- М5.
На 200 кг опилок нужно взять 50 кг цемента, 50 кг песка, 200 кг извести или глины. Получаемая плотность составит 500 кг/м3
- М10. На 200 кг опилок нужно взять 100 кг цемента, 200 кг песка, 150 кг извести или глины. Плотность конечного продукта будет составлять 650 кг/м3
- М15. На 200 кг опилок нужно взять 150 кг цемента, 350 кг песка, 100 кг извести или глины. Плотность конечного продукта будет составлять 800 кг/м3
- М20. На 200 кг опилок нужно взять 200 кг цемента, 500 кг песка, 50 кг извести или глины. Плотность конечного продукта будет составлять 950 кг/м3.
Чтобы из сделанных блоков было удобно строить здание, нужно заранее высчитать длину блока. Длина или ширина простенка должна быть кратна блочным размерам. Чаще всего блоки делают толщиной в два красных кирпича, учитывая и уложенный между ними раствор. Это примерно 140 мм. Принимая во внимание тот факт, что при кладке зачастую применяется и красный обожженный кирпич, то данный подход является очень практичным.
Большие опилкобетонные блоки высыхают продолжительное время. Чтобы его уменьшить, в блоке нужно сделать 2-3 отверстия, это не только уменьшит время высыхания, но и повысит теплозащитные свойства этого стройматериала.
Монолитный опилкобетон – это возможный вариант, но не оптимальный. Лучше возводить строение из заранее подготовленных блоков. Их нужно просушить примерно три месяца. Поле этого блоки приобретут марочную прочность. Форму с опилкобетонного блока нельзя снимать сразу, а только через 3-5 дней. Чтобы ускорить процесс изготовления нужно иметь 10-20 форм.
Формы бывают:
- для габаритных блоков. В таких формах получаются крупные блоки. Форма должна быть разборная одинарная или двойная. Такие формы делают в виде сбитых из досок ящиков. Доски нужно брать толщиной примерно 20 мм. Части разъемной конструкции можно скрепить с помощью металлических стержней Г-образной формы, имеющих резьбу М8, на которую накручивается барашковая гайка
- для небольших блоков.
Чтобы создать такие блоки нужно сделать сотовую форму. Чаще всего такая форма рассчитана на изготовление 9 блоков из опилкобетона одновременно. Однако количество блоком можно изменить, по вашему желанию.
Чтобы доски, из которых созданная форма для отливки, не поглощали влагу их необходимо выстелить внутри кровельной сталью, пластиком или полиэтиленовой пленкой. Из таких форм вынуть блок очень легко, он не пристает к деревянным стенкам.
Во время высыхания наблюдается усушка блоков. Поэтому формы должны быть чуть больших размеров, чем конечный продукт. Сделайте формы примерно на 10% больше нужного рвам размера блока.
Строительство из опилкобетона
Дом из опилкобетона можно построить из соответствующих блоков или создав опалубку, отлить стены дома, при этом сэкономив и время и средства. Вариант с созданием блоков – довольно длительный, потому что блокам нужно время для набирания прочности. Если вы хотите построить дом более быстро, тогда вас придется соорудить надежную опалубку и заполнить ее приготовленным раствором. Еще один момент — опалубку нужно переставлять не один раз, и с увеличением высоты заполнять ее опилкобетоном будет гораздо труднее. Именно поэтому наиболее привлекательным вариантом является строительство из опилочных блоков.
Как мы уже говорили, возведение дома из опилкобетона связано с большим количеством нюансов, соблюдение которых является крайне важным. Ведь именно всякие, на первый взгляд, незначительные нюансы, оказывают влияние на эксплуатационные характеристики готового строения, а также на долговечность постройки.
Несколько советов:
- фундамент нельзя создавать из опилкобетона, тут понадобится кирпич или настоящий бетон. Фундамент должен быть выше уровня грунта минимум на полметра. Его необходимо качественно гидроизолировать со всех сторон – с боку и сверху. Подобная капитальная гидроизоляция гарантирует полное предотвращение попадания влаги из грунта через бетон в стены здания
- армирование углов здания. Идеальным вариантом для двухэтажного здания можно назвать создание бетонных опор по углам здания с заложенной в них арматурой.
Для невысокой монолитной постройки углы можно армировать связанным из арматуры угловым горизонтальным каркасом по всей высоте стены
- также стоит обратить большое внимание на процедуру армирования оконных и дверных проемов. Стандартным решением является установка армирующего пояса вокруг проема
- свес крыши для предотвращения попадания талой и дождевой воды на стены должен иметь ширину не менее 600мм.
Краска для опилкобетона. Какой краской покрасить опилкобетон?
При строительстве дома для возведения стен в последнее время стали широко использовать опилкобетон, который состоит из цемента, деревянных опилок, песка и воды. Очень хорошо держит тепло, экологически безопасен и имеет невысокую цену.
После возведения стен дома из опилкобетона возникает вопрос: отштукатурить стены, положить кирпичную кладку снаружи или отделать сайдингом, заделать гипсокартонном внутри помещения. Или есть ещё более дешёвые способы отделки?
Для значительной экономии денежных средств мы рекомендуем покрасить опилкобетон специальной краской, которая будет защищать материал от влаги и мороза.
Конечно, если Вы хотите получить абсолютно гладкие стены внутри или снаружи помещения, тогда нужно будет перед покраской выровнять поверхности блоков путем шпаклевания или отделкой гипсокартона.
стена из опилкобетона покрашена резиновой краской супер декорСуществует множество видов лакокрасочных покрытий, которые используются для нанесения на штукатурку, гипсокартон, сайдинг, кирпич и т.д.
Но для прямого нанесения на опилкобетон мы рекомендуем специализированную краску — это резиновая краска Super Decor, которая на протяжении двадцати лет получила положительные отзывы от частных лиц до крупных строительных компаний.
В своём составе имеет уникальный финский полимерный латекс, который надёжно заполняет мелкие трещины и неровности создавая латексную пленку, которая способна сдерживать трещины при значительных колебании температуры окружающей среды от -70 до +130 градусов.
Покрашенную поверхность резиновой краской можно мыть любыми химическими средствами.
Обладает высокой паропроницаемостью, т.е. способностью краски «дышать«, пропускать воздух через мембранный состав краски.
Не содержит опасных растворителей, поэтому не возгорается и не имеет запаха, имеет все необходимые сертификаты для применения в внутри, так и снаружи помещения. Экологически безопасная для здоровья человека.
Не выгорает в течение многих лет под постоянным воздействием прямых солнечных лучей.
Выбор цвета:
Подбор нужного оттенка нужно осуществлять только по пробным выкрасам на небольших участках, потому что реальный цвет значительно отличается от оттенков на компьютере, который искажает цветопередачу.
Можно самостоятельно добавить нужное количество колера в белую краску и получить желаемый оттенок, но для этого нужен профессиональный опыт, иначе можно всё испортить.
Мы рекомендуем использовать мировые палитры: NCS, Ral, Dulux и другие. В этих классических линейках можно найти более 10000 цветов.
Алгоритм нанесения:
Удаляем грязь при помощи мыльного раствора и ветоши или используем аппарат высокого давления, который ускоряет и облегчает процесс.
Шелушащейся слой краски нужно удалить используя наждачную бумагу или шлифовочную машину. Также существуют смывки для снятия краски.
Если предыдущий слой держится хорошо и не трескается, то снимать его не нужно.
Используем грунт глубокого проникновения для улучшения адгезию » прилипания» краски к опилкобетона и снижение расхода материала. На один квадратный метр потребуется 100 грамм грунтовки в один слой. Грунт высохнет через час и сразу можно красить.
Для достижения абсолютно гладкой поверхности нужно отшпаклевать стены, трещины и дефекты. Также можно просто покрасить, но тогда поверхность не будет ровной.
Начальный слой краски наносим при помощи велюрового валика и кисти. Советуем использовать краскопульт, который ускоряет и облегчает процесс покраски стен.
Окрашивать начинаем сверху и далее спускаемся вниз, избегая подтёков. Первый слой высыхает через два часа.
По технологии второй слой наносим на следующий день, чтобы покрытие максимально прилипла к стене. На один метр квадратный нужно 150 грамм лакокрасочного материала.
Промываем водой валики, кисти и краскопульт сразу после проведенных работы, с целью дальнейшего применения этих инструментов.
Вывод:
Покупайте резиновую краску у проверенных производителей, которые дают гарантию на их продукция проверена временем и отзывами клиентов.
Правильная подготовка материала к окрашиванию очень важный шаг к длительной эксплуатации.
На каждой банке есть информация по применению, поэтому сначала прочитайте её внимательно, чтобы не допустить ошибок.
Погодные условия для окрашивания должны быть не менее +5 градусов и относительная влажность воздуха не более 85 %.
Опилкобетон своими руками
Опилкобетон представляет собой одну из разновидностей бетонов, отличающуюся крайней дешевизной, при вполне приемлемых качественных характеристиках. Основная сфера его применения – изготовление блоков. Полученные блоки могут использоваться для возведения ограждающих несущих конструкций, а так же для утепления стен, фундаментов и иных элементов.
Рассмотрим основные свойства опилкобетона с точки зрения различных факторов:
- Экология. Материал является полностью экологически чистым, и не вступает в противоречие с существующими нормами СанПиН.
- Водопоглощение и морозостойкость. Исходя из того, что плотность опилкобетона и влажность его сырья может колебаться в весьма значительных пределах, то же самое можно сказать и про эти показатели. Если делать относительно плотный раствор, и принимать меры по защите компонентов от влаги, то водопоглощение опилкобетона может быть снижено до 2-4 %, что позволит поднять показатель морозостойкости до 100 циклов, а это хороший показатель.
- Огнестойкость. Несмотря на то что материал на 50 % состоит из опилок, он обладает достаточно высоким показателем огнестойкости.
- Прочность. Здесь все зависит от конкурентного состава материала, а так же от марки цемента, используемого в процессе его приготовления. Для получения максимальной прочности, рекомендуется использовать цемент М 500.
Отметим, что в опилкобетоне может вовсе не использоваться цемент, который заменяется известью.
Чтобы приготовить опилкобетон своими руками, необходимо, для начала рассмотреть его состав.
Основой материала являются древесные опилки. Кроме того, он содержит песок, цемент или известь и воду. Опилкобетон делится на марки, исходя из используемых компонентов и их пропорций. Рассмотрим их по соотношению цемент — известь — песок — опилки.
- М10: 1 — 2 — 1 — 8
- М15: 1 — 1,2 — 1,2 — 4
- М15 (вариант без извести): 1 — 0 — 2,3 — 6
- М25: 1 — 1 — 1,2 — 4
- М25 (вариант без извести): 1 — 0 — 1,7 — 3,8
Плотность материала находится в прямой зависимости от доли песка, и в обратной от доли опилок. Чем плотнее опилкобетон, тем выше его прочность и ниже теплозащитные свойства.
Если из блоков опилкобетона планируется возведение зданий, то материал необходимо армировать.
Теперь, готовим опилкобетон своими руками:
1. Подготовленные опилки необходимо просеять (рекомендуемая ячейка сита 10-20 мм), чтобы устранить примеси коры. В качестве сита можно использовать обычную сетку-рабицу с соответствующей ячейкой.
2. Если опилки долго хранились или вы предполагаете использовать блоки в условиях высокой влажности, опилки необходимо обработать минерализатором. Это снизит водопоглощение материала, улучшив его свойства. Выполняется данная процедура путем вымачивания опилок в известковом молоке с последующей просушкой и вымачиванием уже в составе из воды и жидкого стекла.
3. Песок, цемент, известь и опилки заготавливаются исходя из указанных пропорций для выбранного вами типа бетона.
4. Сначала, смешивается песок, цемент и известь.
5. К полученной сухой смеси добавляются опилки.
6. Только после этого, состав постепенно заливается водой с постоянным перемешиванием. Оптимальным вариантом добавления воды является разбрызгиватель.
7. Оптимальное количество воды можно определить следующим образом: смесь сжимается в руке, и оценивается результат этого действия. Если смесь после сжатия сохранила форму, а ладонь осталась слегка влажной, то пора прекращать увлажнение.
8. Набор полной прочности опилкобетоном занимает примерно 90 суток.
Использование опилкобетона в дачном строительстве
Возле любого деревообрабатывающего предприятия можно найти горы опилок и стружек. Несмотря на дешевизну, эти древесные отходы — ценный строительный материал. Его можно использовать в дачном и индивидуальном строительстве как наполнитель для бетона.
Дома, построенные из опилкобетона, обладают отличными потребительскими качествами, их микроклимат близок к домам с деревянными срубами. Стены в них отлично держат тепло, в 15-20 раз лучше кирпичных. Кроме того, в отличие от обычного бетона, бетон из опилок, содержащий до 90% древесины, можно резать ножовкой и забивать в него гвозди.
Подготовка опилок
Частички древесины в опилкобетоне находятся в капсулах из вяжущего раствора, что защищает их от вредного воздействия окружающей среды и определяет долговечность конструкций в целом. Лучший результат дает использование свежих опилок хвойных пород.
Если опилки старые, то их надо предварительно обработать, чтобы дополнительно защитить от гниения. В качестве консерванта используют 10%-й раствор хлорида кальция или известковое молочко. После высыхания опилки обрабатывают повторно раствором жидкого стекла или битумной эмульсией. Еще один способ подготовки опилок — «запаривание» негашеной известью. Смесь опилок и извести слегка смачивают водой и оставляют на 3-4 дня под полиэтиленовой пленкой.
Внешние стены жилых домов, возведенных из опилкобетона, дополнительно защищают от атмосферных осадков с помощью кирпичной кладки или другой облицовки. Внутренние стены штукатурят. Вместе с тем, в интернете можно найти множество примеров, когда различные постройки из опилкобетона стоят десятилетиями без всякой дополнительной защиты.
Для опилкобетона не годится мелкая древесная пыль. Поэтому перед началом обработки опилки просеивают последовательно через сетки с ячейками 20, 10 и 5 мм. Отсеиваются самые крупные и наиболее мелкие фракции. Рабочий наполнитель — остаток на сетке 5 мм, в него добавляют до 30% стружек и фракций размером 10 мм. Перед закладкой необработанных древесных составляющих их тщательно просушивают.
Приготовление опилкобетона
Рецептов опилкобетона множество. В зависимости от назначения можно готовить смеси плотностью от 500 до 1250 кг/м3. В качестве вяжущего вещества применяют цемент, известь, гипс, глину, получая бетоны марки от М5 до М25. Общее требование: весовое соотношение вяжущих веществ и наполнителей должно быть не менее чем 1:1. Иными словами, на 100 кг опилок в смеси должно суммарно приходиться не менее 100 кг вяжущей составляющей. В таблице в качестве примера приведены несколько вариантов.
Марка бетона | Цемент М300 (кг) | Гашеная известь (кг) | Песок (кг) | Опилки (кг) | Плотность бетона (кг/м3) |
---|---|---|---|---|---|
М10 | 105 | 150 | 530 | 210 | 950-1050 |
М15 | 210 | — | 630 | 210 | 1050-1150 |
М25 | 300 | — | 670 | 190 | 1150-1250 |
Главная технологическая операция, обеспечивающая долговечность и прочность бетона — тщательное перемешивание сухих компонентов. Даже если требуется относительно небольшое количество бетона, вручную достичь необходимого результата трудно, значительно проще и надежнее использовать бетономешалку.
Сначала перемешивают вяжущие составляющие и песок до образования однородной смеси. Затем засыпают опилки, после чего постепенно, малыми порциями вводят воду.
Для приготовления опилкобетона требуется 250-350 литров воды на 1м3 раствора. Достаточное количество влаги определяют опытным путем — сжатием раствора в кулаке. При оптимальном соотношении смесь удерживает форму, и из нее не выжимается вода.
Использование опилкобетона
Легкие бетоны М5 используют для теплоизоляции. Бетоны M10, М15 годятся для возведения стен одноэтажных строений, М25 — двухэтажных и неотапливаемых помещений.
Опилкобетон можно заливать непосредственно в опалубку. Но ввиду того, что он сравнительно долго затвердевает и пружинит при трамбовании, предпочтительно выкладывать стены из заранее приготовленных блоков.
Для изготовления блоков потребуются деревянные или стальные формы. Размеры форм могут быть любыми, но на практике редко превышают 20×20×40 см. Блоки больших размеров плохо сохнут, тяжелы и неудобны в работе. Для уменьшения веса их делают пустотелыми, устанавливая в форму на время заливки и трамбовки различные пустотозаполнители из стали или дерева.
Качество блоков и их долговечность зависит от степени уплотнения смеси в форме. На практике применяют ручную и вибротрамбовку. В первом случае смесь уплотняется штыкованием при помощи куска арматуры. Операция трудоемкая, поэтому ее проводят в несколько этапов, заливая блок слоями.
Для вибротрамбовки используют вибростолы, вибрирующие поверхности, на которых размещают форму с раствором. Можно ограничиться и обычным перфоратором. Бур в режиме удара упирают в стальную плоскость (рамку из уголка, широкую полоску), размещенную на поверхности уплотняемого раствора.
Особенность блоков из опилкобетона заключается в том, что из формы их достают уже после схватывания, а не сразу после вибротрамбовки. Поэтому, чтобы ускорить строительные работы в целом, потребуется заранее изготовить несколько заливочных форм.
Успехов!
Опилкобетон своими руками для изготовления стеновых блоков — каталог статей на сайте
Теплые стеновые блоки из опилкобетона изготовить самостоятельно вполне реально.
Безусловно, повозиться придется, зато в результате получим экономию немалую на материале для постройки дома, либо другого строения. К тому же, стеновые блоки из опилкобетона относятся к категории теплых, поэтому, если нужен не конструкционный материал, а утеплитель, опилкобетон и в этом плане выгоден – теплоизолятор он мощный.
Формы для опилкобетонных блоков
Формы для блоков нужны разборные. Можно использовать для их изготовления тонкие строганные доски, а изнутри прикрепить пластик или кровельную сталь, чтобы изделия легко вынимались. А можно просто прикрепить толстую полиэтиленовую пленку. Хотя сегодня не обязательно мастерить формы для блоков своими руками: в продаже есть специальные пресс формы из прочного пластика для изготовления блоков распространенных размеров. Что хорошо в таких покупных формах – выверенная геометрия, а также наличие пуансонов – верхних элементов наподобие крышек, с помощью которых смесь в формах трамбуется.
Конечно, чем больше строение, которое вы хотите возвести, тем больше форм для блоков понадобится. Можно обойтись и минимальным их количеством, но тогда изготовление блоков растянется во времени до невозможности. Дело в том, что форму с крупных блоков снимают приблизительно через 5 дней, а с более мелких изделий – через 3 дня. Исходя их этого, лучше все-таки обзавестись большим количеством форм (хотя бы, 10-15 шт.).
Размеры стеновых блоков из опилкобетона различны. Имейте в виду, что при высыхании изделия дают усушку, поэтому формы нужны чуть больше по размерам (примерно на 10%).
Опилкобетон своими руками: рецепты
1. Опилок – 12 ведер, цемента – 3 ведра, глины – 5 ведер, вода – 10-15% от объема замеса.
+ Изделия из опилкобетона, приготовленного по этому рецепту, обладают большим запасом прочности, а также высокими теплоизоляционными свойствами.
2. Опилки – 10 ведер, цемент – 3 ведра, известь – 10 ведер, вода – 10-15% от объема замеса.
* Теплоизоляционные свойства стеновых блоков их опилкобетона по данному рецепту невысоки, их изготавливают, в основном, для строительства подсобных помещений (например, гаражей).
- Соединяют цемент с песком.
- К массе добавляют известь (по второму рецепту).
- Всыпают опилки.
- Вливают воду.
На каждом этапе все ингредиенты хорошо перемешивают – вручную или в бетономешалке. Массу укладывают в формы, утрамбовывают как можно тщательнее, чтобы в теле стеновых блоков не осталось пустот.
Стеновые блоки из опилкобетона к началу возведения стен должны быть готовы, то есть, хорошо высушены. Времени на сушку понадобится немало: в зависимости от размеров блоков – от 1,5 до 3-х месяцев.
ЕЩЕ СТЕНОВЫЕ БЛОКИ
Теплостен или полиблок
Стеновые блоки арболит
Как рассчитать нужное количество блоков
Поризованные блоки
Стеновые блоки керамзитобетонные
Бетонные блоки своими руками
Хочу больше статей:
Оставьте Ваш отзыв
Average rating: 0 reviewsTags:
газобетон панели штукатуркаИспользование обработанных опилок в бетоне в качестве частичной замены природного песка
https://doi.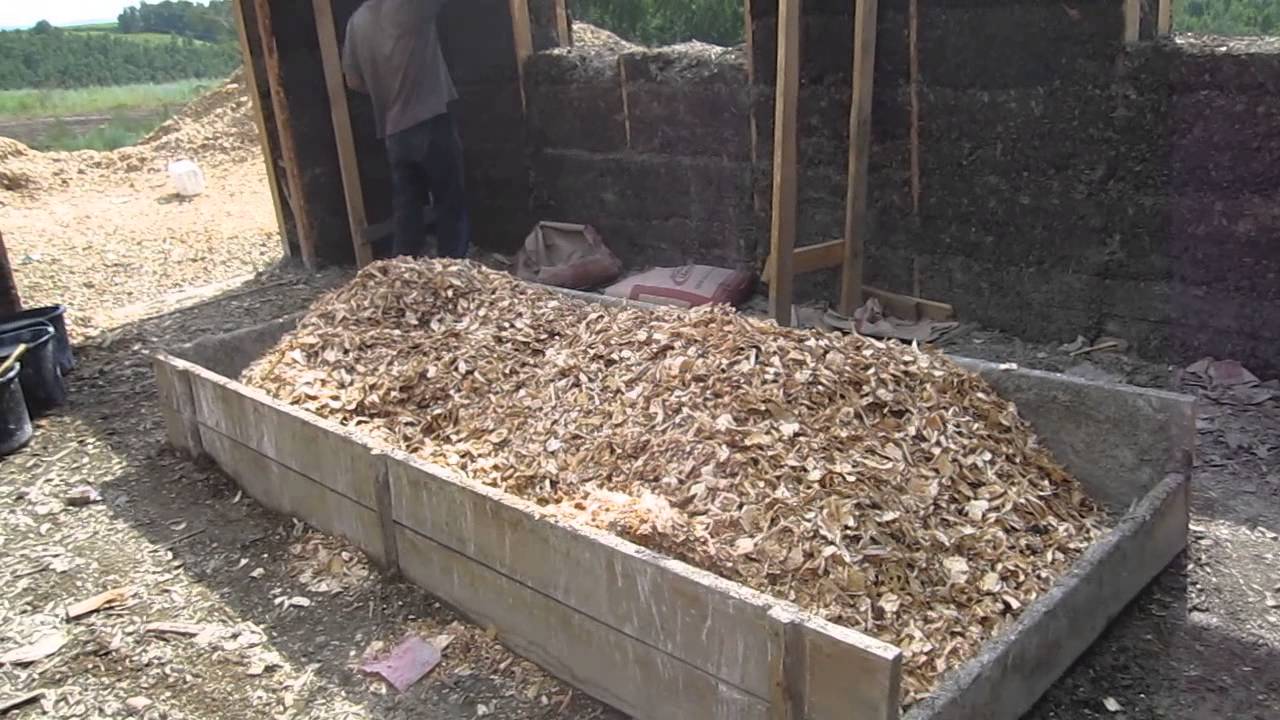
Основные моменты
- •
Песок в бетоне заменен на 5 , 10, 15 и 20% опилки, обработанные водой.
- •
Оптимальное количество опилок, обработанных водой или силикатом натрия, составляет 5%.
- •
Плотность бетона снизилась при использовании опилок.
- •
Прочностные характеристики бетона, модифицированного 5% опилками, сопоставимы.
- •
Улучшена проницаемость для хлорид-ионов по дыму кремнезема в бетоне, модифицированном опилками.
Реферат
Добыча природных материалов, таких как песок, в крупных масштабах для использования в строительстве инфраструктуры в развивающихся странах, таких как Индия, представляет угрозу для окружающей среды. Поэтому для сохранения окружающей среды исследователь становится обязательным исследовать возможность использования побочных продуктов промышленности вместо природного материала. В этом исследовании было изучено использование опилок, образующихся в деревообрабатывающей промышленности, в бетоне. В этой статье представлены свойства бетона, использующего различное процентное содержание опилок, обработанных водой и силикатом натрия, в качестве замены песка. Перед использованием в бетоне опилочную пыль, прошедшую через сито 4,75, обрабатывали водой и силикатом натрия в течение 24 ч. Природный песок был заменен на 5, 10, 15 и 20% водоочищенные опилки в бетонной смеси. Влияние микрокремнезема на свойства бетона, содержащего 5% опилок, обработанных водой, также было изучено путем замены 4, 8 и 12% цемента на микрокремнезем в бетоне.Было отмечено, что бетон, изготовленный из опилок, обработанных 5% водой или силикатом натрия, показал прочность на сжатие, сравнимую с прочностью контрольного бетона. Однако для уровня замены 10% прочность на сжатие и разрывная прочность на разрыв снизились на 30,30% и 32,19% соответственно через 28 дней. Общая пропускная способность, водопроницаемость и капиллярное водопоглощение увеличились на 224%, 153% и 117,4%, соответственно, при использовании 10% обработанных опилок.
Бетонная смесь, модифицированная опилками, обработанными силикатом натрия, показала значительное улучшение устойчивости к проникновению хлорид-ионов.Как и ожидалось, результаты показали значительное снижение плотности бетона с использованием опилок вместо песка. Добавление опилок, обработанных силикатом натрия, привело к образованию большого количества эттрингита в бетоне.
Ключевые слова
Опилки
Бетон
Прочность на сжатие
Сорбционная способность
Хлоридопроницаемость
Рекомендуемые статьиЦитирующие статьи (0)
Полный текст© 2020 Elsevier Ltd. Все права защищены.
Рекомендуемые статьи
Ссылки на статьи
Пригодность опилок бетона для жестких покрытий на основе долговечности
В этой статье бетонные опилки с номинальными смесями 1: 1: 2, 1: 1½: 3, 1: 2: 4, 1: 3: 6 и 1: 4: 8 были подвергнуты испытанию на прочность. Водопоглощение смесей за 28 дней составляет 5,69, 8,97, 8,29, 7,83 и 11,11%, линейная усадка за 28 дней составляет 0,67, 0,50, 1,83, 1,83 и 1,95% соответственно. 28-дневная теплопроводность составляет 0,229, 0,232, 0,229, 0,223 и 0,176 Вт / мК соответственно. Прочность на сжатие в течение 28 дней смесей 1: 1: 2 и 1: 1½: 3 составляет 18,33 и 8,78 Н / мм2, соответственно, а их прочность на изгиб в течение 28 дней составляет 1,71 и 1,33 Н / мм2, соответственно. Эти значения указывают на то, что они являются хорошим и прочным бетоном и могут использоваться для строительства жесткого покрытия.
Информация:
Проф. Акии Оконигбон Акахомен Ибхадоде, А.И. Игбафе и Б.У. Анята
На эту статью нет ссылок.
IRJET — Запрошенная вами страница не найдена на нашем сайте
IRJET приглашает доклады по различным инженерным и технологическим дисциплинам, научным дисциплинам для Тома 8, выпуск 10 (октябрь 2021 г. )
Отправить сейчас
IRJET Vol-8, выпуск 10, Октябрь 2021 г. Публикация продолжается…
Обзор статей
IRJET получил «Импакт-фактор научного журнала: 7,529» за 2020 год.
Проверить здесь
IRJET получил сертификат регистрации ISO 9001: 2008 для своей системы менеджмента качества.
IRJET приглашает специалистов по различным инженерным и технологическим дисциплинам, научным дисциплинам для Тома 8, выпуск 10 (октябрь 2021 г.)
Отправить сейчас
IRJET том-8, выпуск 10, октябрь 2021 г. Публикация продолжается…
Обзор статей
IRJET получил «Импакт-фактор научного журнала: 7,529» за 2020 год.
Проверить здесь
IRJET получил сертификат регистрации ISO 9001: 2008 для своей системы менеджмента качества.
IRJET приглашает специалистов по различным инженерным и технологическим дисциплинам, научным дисциплинам для Тома 8, выпуск 10 (октябрь 2021 г. )
Отправить сейчас
IRJET том-8, выпуск 10, октябрь 2021 г. Публикация продолжается…
Обзор статей
IRJET получил «Импакт-фактор научного журнала: 7,529» за 2020 год.
Проверить здесь
IRJET получил сертификат регистрации ISO 9001: 2008 для своей системы менеджмента качества.
IRJET приглашает специалистов по различным инженерным и технологическим дисциплинам, научным дисциплинам для Тома 8, выпуск 10 (октябрь 2021 г.)
Отправить сейчас
IRJET том-8, выпуск 10, октябрь 2021 г. Публикация продолжается…
Обзор статей
IRJET получил «Импакт-фактор научного журнала: 7,529» за 2020 год.
Проверить здесь
IRJET получил сертификат регистрации ISO 9001: 2008 для своей системы менеджмента качества.
IRJET приглашает специалистов по различным инженерным и технологическим дисциплинам, научным дисциплинам для Тома 8, выпуск 10 (октябрь 2021 г. )
Отправить сейчас
IRJET том-8, выпуск 10, октябрь 2021 г. Публикация продолжается…
Обзор статей
IRJET получил «Импакт-фактор научного журнала: 7,529» за 2020 год.
Проверить здесь
IRJET получил сертификат регистрации ISO 9001: 2008 для своей системы менеджмента качества.
IRJET приглашает специалистов по различным инженерным и технологическим дисциплинам, научным дисциплинам для Тома 8, выпуск 10 (октябрь 2021 г.)
Отправить сейчас
IRJET том-8, выпуск 10, октябрь 2021 г. Публикация продолжается…
Обзор статей
IRJET получил «Импакт-фактор научного журнала: 7,529» за 2020 год.
Проверить здесь
IRJET получил сертификат регистрации ISO 9001: 2008 для своей системы менеджмента качества.
IRJET приглашает специалистов по различным инженерным и технологическим дисциплинам, научным дисциплинам для Тома 8, выпуск 10 (октябрь 2021 г. )
Отправить сейчас
IRJET том-8, выпуск 10, октябрь 2021 г. Публикация продолжается…
Обзор статей
IRJET получил «Импакт-фактор научного журнала: 7,529» за 2020 год.
Проверить здесь
IRJET получил сертификат регистрации ISO 9001: 2008 для своей системы менеджмента качества.
IRJET приглашает специалистов по различным инженерным и технологическим дисциплинам, научным дисциплинам для Тома 8, выпуск 10 (октябрь 2021 г.)
Отправить сейчас
IRJET том-8, выпуск 10, октябрь 2021 г. Публикация продолжается…
Обзор статей
IRJET получил «Импакт-фактор научного журнала: 7,529» за 2020 год.
Проверить здесь
IRJET получил сертификат регистрации ISO 9001: 2008 для своей системы менеджмента качества.
Зола опилок в качестве порошкового материала для самоуплотняющегося бетона, содержащего нафталинсульфонат
Испытания проводятся для определения текучести портландцементной пасты Ashaka и ее совместимости с золой опилок в качестве порошкового материала для самоуплотняющегося цемента (SCC). ) смеси.Результаты исследования показали, что насыщение достигается при соотношении в / ц 0,4 и 0,42, при дозировках суперпластификаторов нафталинсульфоната 3,5% и 2% соответственно. Оптимальный уровень замены для смеси SCC составлял 10 мас.% Цемента на SDA и 2% от дозировки суперпластификатора. Достигнутое время распространения и истечения составило 26 см и 8 секунд и находится в указанном диапазоне от 24 см до 26 см и от 7 до 11 секунд, соответственно. Статистический вывод показал, что смесь, w / c, и взаимодействие между смесью и соотношением w / c являются значительными.
1. Введение
Суперпластификаторы часто добавляют на стадии смешивания бетона в небольших количествах, связанных с массой цемента, для увеличения текучести свежего бетона, увеличения прочности и продления срока службы затвердевшего бетона. Исследования показали, что на совместимость цемента и суперпластификаторов влияют такие факторы, как содержание фазы C 3 A и C 4 AF в клинкере ПК, общее количество щелочи, крупность цемента, а также тип и количество сульфата кальция [ 1].
Сообщалось о проблемах совместимости суперпластификаторов и цемента, которые могут характеризоваться текучестью цементного теста и его потерей со временем [2, 3]. Добавление суперпластификатора снижает предел текучести пасты почти до нуля, но пластичность существенно не снижается [4]. Суперпластификатор нафталинсульфонат часто используется для улучшения реологии свежего бетона [5]. Termkhajornkit и Nawa [4] сообщили в своей работе, что поверхностный потенциал летучей золы отличается от обычного портландцемента (OPC) как по знаку, так и по величине, и, таким образом, это является причиной флокуляции летучей золы и цементного теста.Когда суперпластификатор нафталинсульфонат был введен в зольную цементную пасту, признаки были такими же и, следовательно, хорошо диспергировались из-за более высокого потенциального барьера. Адсорбция суперпластификаторов нафталинсульфоната на поверхность частиц цемента изменяет дзета-потенциал поверхности частиц на отрицательный и, таким образом, увеличивает его абсолютное значение [6, 7].
Текучесть опилочно-золоцементного теста не сообщается. В этом исследовании было сочтено необходимым определить, во-первых, реологические свойства цементного раствора с использованием суперпластификатора нафталинсульфонат и, во-вторых, влияние SDA и его совместимость на свойства текучести.Зола опилок (ЗДД) была получена в результате сжигания древесных отходов мукомольной промышленности, и зола содержит в основном силикаты (67%). Методы получения, сжигания и характеристики SDA были полностью обсуждены в предыдущей статье, где он использовался с бетоном [8]. SDA обладает пуццолановыми свойствами и, таким образом, является многообещающим дополнительным материалом для производства бетона.
2. Эксперимент
Фиг. 1 представляет собой блок-схему, использованную при разработке смеси для самоуплотняющегося бетона; Использовался портландцемент «Ашака» стандарта BS 12 [9].Использовали АСД, полученный из термически активированных древесных отходов при температурах от 400 ° С до 600 ° С [8]. Физические и химические свойства портландцемента Ashaka и SDA приведены в таблице 1. Мелкодисперсный заполнитель представляет собой речной песок с удельным весом 2,57, влажностью 14,4% и насыпной плотностью 1472 кг / м 3 и зона 2 в таблице классификации в соответствии с BS 882 [10]. Суперпластификатор представлял собой коммерческий суперпластификатор нафталинсульфоната, производимый W.R. Grace and Co., США, названный Daracem 19. Он имеет удельный вес 1,18 и pH 9,5, а сухой экстракт по массе составляет 40%.
|
2.
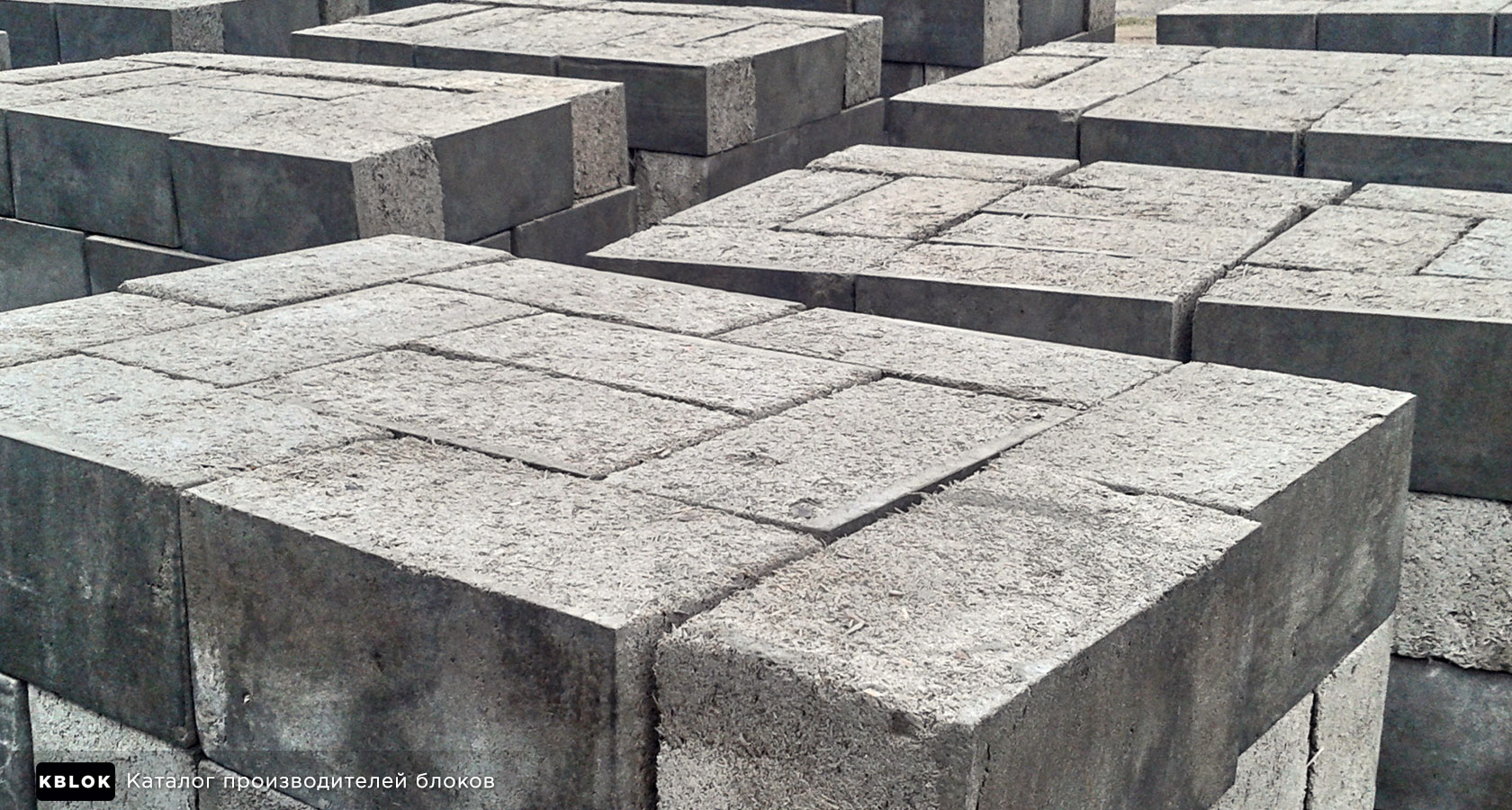
В таблице 2 показаны пропорции смеси для теста на совместимость (тест на текучесть). Соотношение воды и связующего в пасте составляло от 0,3 до 0,42. Дозировка суперпластификатора варьировалась от 0 до 4 мас.% Цемента. Чтобы оценить совместимость портландцемента с суперпластификатором нафталинсульфонат, для измерения расхода использовался стандартный усеченный конус (рис. 2). Он имеет верхний внутренний диаметр 70 мм, нижний внутренний диаметр 100 мм и высоту 60 мм.Конус помещался на стеклянную пластину размером 750 мм × 750 мм и заполнялся навеской раствора. Верхняя поверхность раствора обрабатывалась шпателем, конус поднимался вертикально. Диаметр распространения раствора после подъема конуса измеряли в двух перпендикулярных направлениях (и) с помощью линейки, и записывали среднее значение. Результаты представлены в Таблице 3.
|
|
2.2. Тест на содержание порошка
Тест на содержание порошка проводился сразу после достижения насыщения в результате испытания на совместимость (текучесть).Это было сделано с помощью тестов потока и V-воронки (рисунок 3). Пропорции смеси для испытания показаны в Таблице 4. Оптимальная дозировка 2% суперпластификатора нафталинсульфоната и содержание цемента 479 кг / м. 3 были использованы при водном / цементном соотношении 0,42. Это были значения в точке насыщения из теста совместимости (текучести). Коэффициенты замещения SDA в тесте на содержание порошка варьировались от 0 до 20 мас.% Цемента. Всего было использовано 5 смесей (от PC-01N до PC-05N). PC-01N представлял собой контрольную смесь, содержащую NS без SDA (порошкового материала), в то время как PC-05N содержал SDA в количестве 20 мас. % цемента в качестве замены. Буква P обозначает порошковый материал. Для каждого уровня замены проводились два теста, и фиксировалось среднее значение. Результаты представлены в Таблице 5.
|
|
3. Результаты и поздние обсуждения. силикатов.Ему требуется больше воды для консистенции, и при добавлении в цемент он запускает пуццолановую реакцию с избытком Ca (OH)
2 , образующимся во время гидратации цемента. Таким образом, SDA задерживает гидратацию пасты и увеличивает время схватывания [9]. Было установлено, что несгоревший углерод (<5%) влияет на адсорбцию суперпластификаторов [4]; поэтому потери при прокаливании SDA не превышали 4,6%, и, таким образом, влияние несгоревшего углерода в этой работе не учитывалось.Результаты испытаний на текучесть показаны на рисунках 4 (a) –4 (c).Отношения между реологией строительного раствора при различных дозировках суперпластификатора довольно параллельны. Совместимость (текучесть) при водном соотношении 0,3 (рис. 4 (а)) увеличивалась с увеличением дозировки NS без какой-либо точки насыщения. Однако при соотношении 0,4 в / ц (рис. 4 (б)) текучесть также увеличивалась, но насыщение было достигнуто при дозировке примерно 3,5%. При соотношении w / c 0,42 (рис. 4 (c)) текучесть раствора не увеличилась значительно при дозировке 2%.Диаметр потока при этой дозировке составляет 28 см. Это точка насыщения, а 2% — пороговая дозировка. Можно сказать, что эти значения удовлетворяют требованиям кодов для материалов SCC [11].
Период удобоукладываемости определяется взаимодействием порошковых материалов и добавки [12]. На рисунке 5 показан график уровней замещения в зависимости от потока и времени для смесей SDA (от PC-01N до PC-05N). Расход уменьшался по мере увеличения процента замены. Время достижения такого потока также увеличилось.Объяснение такому поведению может быть получено из работ Termkhajornkit и Nawa [4] по летучей золе. В таблице 6 показаны значения дзета-потенциалов и потока в системе по данным Термхаджорнкита и Нава [4]. Видно, что когда система не содержала суперпластификатора, дзета-потенциал OPC имел заряд, противоположный заряду летучей золы. Это стимулировало флокуляцию. Это означает, что общая потенциальная энергия частиц цемента и летучей золы стала ниже, чем между частицами OPC.Обратное было при применении суперпластификатора. Заряды были такими же, и, следовательно, происходило отталкивание и улучшение потока. SDA можно классифицировать как летучую золу класса C, и, таким образом, можно привести те же причины для поведения смесей SDA без и с нафталинсульфонатом. В коде [11] указано, что смесь, прошедшая испытание на SCC, должна быть смесью с диаметром распределения от 24 см до 26 см, а также временем истечения от 7 до 11 секунд. Из таблицы результатов испытаний на содержание порошка смесью, которая удовлетворяла обоим условиям, была смесь PC-03N, которая содержала 10% замену цемента суперпластификатором нафталинсульфоната.
4. Статистический анализ4.1. Тест на совместимость (тест текучести)В таблице 7 перечислены коэффициенты независимых переменных с их соответствующим стандартным отклонением (SD), значением скорости и вероятности, а значение указывает на значимость переменной в модели, соответствующей вероятность.Если значение меньше или равно 5% (≤ 0,05), переменная принимается как значимая на уровне 5%. Анализ таблицы 7 показывает, что только независимые переменные водоцементного отношения (в / ц) и дозировка нафталинсульфоната представляют значения ниже 5%; следовательно, оставшаяся переменная (репликация) не является статистически значимой. Стандартное отклонение () составляет 1,25, коэффициент корреляции% и adj = 92,8%. Уравнение регрессии выглядит следующим образом: расход = 8,11 + 3,38 w / c + 1.13 дозировок.
В таблице 8 представлен анализ дисперсии, степени свободы (DF), суммы квадратов (SS), средних квадратов (MD), () и вероятности (). Статистически подтверждается наличие регрессии на уровне значимости 5%. Степени свободы регрессии и остаточной ошибки равны 3 и 128 соответственно.На рисунке 6 представлен график остатков в зависимости от скорректированных значений. Этот график показывает, что дисперсия постоянна; то есть точки равномерно разбросаны около нуля.
|