Газобетон или пенобетон в чем разница
Прежде чем строить дом, надо решить, из чего же его строить. Именно выбранный материал определяет, насколько крепким и комфортабельным получится жилище. Хорошие стены и тепло не отдадут на улицу, и постороннему шуму не позволят в комнаты проникнуть. А еще они должны быть экологичными и пожаробезопасными. Сейчас на пике популярности легкие и прочные ячеистые материалы для стен. Нередко застройщик долго раздумывает, что купить: газобетон или пенобетон — в чем разница между ними. На первый взгляд, ее и нет вовсе. А давайте-ка приглядимся повнимательнее.
Разбираемся в терминологии
Ячеистыми бетонами называют материалы на цементной основе облегченного типа. Их особенностью является наличие многочисленных ячеек, благодаря чему материал приобретает множество полезных свойств – как физических, так и механических. Ячеистый бетон имеет несколько разновидностей. Кроме уже упомянутых выше пенобетона и газобетона, существует, например, и газозолобетон. Пористый бетон может быть автоклавным и неавтоклавным.
По способу образования этих ячеек выделяют такие материалы как:
- Газобетон;
- Пенобетон;
- Газопенобетон.
По способу затвердевания пористые бетоны делятся на:
- Автоклавный метод подразумевает твердение материала при повышенном давлении в герметичном резервуаре, в который добавлены насыщенные водяные пары.
- Неавтоклавный метод предполагает, что материал твердеет в естественной среде. При этом он прогревается с помощью электричества. Возможна также обработка бетона насыщенным водяным паром. Но, в отличие от предыдущего метода, давление не повышается.
Пенобетон и газобетон достаточно существенно отличаются друг от друга. У них и состав различный, и характеристики. И в эксплуатации оба материала проявляют себя совершенно по-разному.
Особенности производства пеноблоков и газоблоков
1. Чтобы сделать пенобетон, перемешивают цементную основу со специальными добавками. Они необходимы для вспенивания массы. Данные пенообразователи бывают как на основе синтетических веществ, так и органическими. Вспененная масса попадает в специальные формы, где и твердеет в естественной среде. В итоге получаются пенобетонные блоки. Материал, называемый монолитным, заливают не в формы, а в опалубку. После застывания съемную опалубку разбирают. Несъемная опалубка остается на месте.
Структура пенобетона.
2. Имеется существенная разница между пенобетоном и газобетоном, изготовленным автоклавным методом. Последний, в отличие от пенобетона, можно изготовить лишь в производственных условиях. Для того чтобы он вспенился, не нужны особые химические добавки. Газобетон состоит из натуральных веществ — воды, цемента, извести и гипса. Также в него добавляется некоторое количество алюминия – в виде пудры или пасты. Именно это вещество способствует газообразованию.
Изготавливают газобетон в особой емкости – автоклаве. Для придания материалу прочности его подвергают воздействию высокого давления и температуры, а также водяного пара. В процессе производства происходит химическая реакция между компонентами, и образуется вещество с новыми свойствами. А его кристаллическая решетка похожа на решетки некоторых органических веществ. Это, например, силикаты кальция, в частности, тоберморит. Химическая реакция сопровождается выделением водорода – именно этот газ делает материал пористым и заполняет эти самые поры.
Структура газобетона.
Когда газобетон окончательно затвердевает, приходит время разрезать его на аккуратные одинаковые блоки. Для этого используются струны, которые обеспечивают практически идеальный ровный разрез. Благодаря этому при укладке блоков из газобетона швы получаются очень тоненькими. Так что мостиков холода, через которые может уходить на улицу много тепла, удается избежать.
Сравним характеристики пенобетона и газобетона
ГОСТы для изготовления и того, и другого материала одни и те же. Не допускается отклонения от них. Казалось бы, и характеристики обоих пористых бетонов должны совпадать. На самом деле отличия существуют.
Впитывание влаги и морозостойкость
Отличие технологий изготовления влияет на эти два параметра. Так, газобетон вбирает в себя воду, как губка. Из-за этого во время морозов он себя проявляет не лучшим образом. У пенобетона водопоглощение гораздо ниже. Но следует помнить, что обычно стены из ячеистых материалов не оставляют «как есть» — их покрывают защитным слоем. Это может быть штукатурка, сайдинг или плиточная облицовка. Так что на практике можно не учитывать разницу в водопоглощении. Но можете знать, что газобетон здесь проигрывает.
Что прочнее
Плотность обеих пористых бетонов может варьироваться от 300 до 1200 килограммов на кубический метр. Если провести сравнение газобетона и пенобетона одинаковой плотности, то окажется, что последний менее надежен и крепок. Кроме того, прочность этого материала напрямую зависит от качества пенообразующих веществ. Так как хороший пенообразователь имеет высокую цену, некоторые изготовители хитрят и заменяют его на более дешевый. Прочность пенобетона нестабильна и по всей поверхности блока. А вот газобетонный блок однороден и одинаково себя проявляет во всех точках.
Экологическая безопасность
В процессе производства автоклавного газобетона происходит реакция между известью и алюминием. Выделяемый в результате водород далеко не весь выходит во время отвердевания материала. Часть этого газа (впрочем, совсем немного) может выходить и во время строительства, и потом, когда стены дома уже сложены.
Но водород не относится к ядовитым газам, поэтому отравляющего воздействия на организм человека он не производит. Образующие пенобетон вспениватели, как белковые, так и искусственные, тоже вредных веществ не содержат. Кроме того, поры у пенобетона замкнуты и герметичны. Получается оба данных материала не имеют существенных недостатков в экологическом плане и этот параметр не может быть определяющим в выборе того или иного материала.
Какой материал более подвержен усадке
В стене, выложенной из пенобетонных блоков, могут возникнуть трещины. Ведь показатель усадки у этого материала составляет от 1 до 3 мм/м. Газобетонные блоки практически не трескаются, так как аналогичный параметр у них – не более 0,5 мм/м.
Способность удерживать тепло
Чем более плотной является структура ячеистого бетона, тем хуже его теплоизоляционная способность. Поэтому пенобетон, обладающий небольшой плотностью – лучшим теплоизолятором чем газобетон. Но несущие стены из него не выложить – недостаточно прочен. Поэтому приходится использовать более плотный материал, но стены делать толще, потому как теплопроводность его выше. К примеру, для Новосибирска стены дома из пенобетонных блоков D600 должны быть не тоньше 65 сантиметров. Тогда в доме будет достаточно тепло.
Если же при таких же условиях класть стены из газобетона, то они получатся не толще, чем 45 или 50 сантиметров. Да и плотность при этом будет достаточна D 400 или D 500. Как видите, газобетон гораздо лучше способен удерживать тепло, а стена из него получается легче и прочнее. Впрочем, газобетон или пенобетон использовать для своего дома, решать вам.
Огнестойкость
Оба материала хорошо себя проявляют в этом отношении. А еще данные ячеистые бетоны неплохо пропускают воздух, а также имеют в своем составе только вещества естественного происхождения. Они легкие и удобные в эксплуатации. Что касается устойчивости к морозу, то газобетон в этом плане надежнее вдвое, а порой и втрое.
Сравниваем стоимость
Пенобетон существенно дешевле – примерно процентов на 20. Ведь компоненты для его изготовления не очень дорогие, а оборудование не является сложным. Но при строительстве его может понадобиться больше, чем газобетона. Поэтому не стоит смотреть только на цену кубометра материала – сначала весь проект будущего дома просчитайте.
Важно и то, что газобетон укладывают на клеевую смесь, а для пеноблоков и недорогой цементный раствор вполне подходит. Правда, с клеем укладка проходит быстрее, и понадобится его намного меньше, чем цементной смеси. В итоге получается, что стоимость укладки пеноблоков (включая все материалы) превышает затраты на укладку газоблоков. Кроме того, тонкий слой клея, в отличие от цемента, не дает мостиков холода. В итоге дом получается более энергосберегающим.
Сравниваем размеры
Так как блоки из газобетона изготавливаются в заводских условиях, то их размеры более стабильны, чем у пеноблоков. Ведь пенобетон делать можно прямо на стройплощадке – при помощи специальных установок. В результате и расход материалов для укладки, и удобство самой кладки у обоих ячеистых бетонов отличаются. Но это отнюдь не говорит о том, что газобетон – победитель по всем пунктам.
Надеемся, что это сравнение преимуществ и недостатков пенобетона или газобетона было своевременным и оказало вам помощи. Удачи в строительстве!
Если вы заметили ошибку, не рабочее видео или ссылку, пожалуйста, выделите фрагмент текста и нажмите Ctrl+Enter.
газоблоки и пеноблоки разница и сходство
При строительстве дома важно правильно подобрать материал, который будет достаточно прочным, легким и при этом сможет сохранять тепло в доме. Среди строительных материалов для частного строительства наиболее популярными являются газоблоки и пеноблоки. Разница между ними, на первый взгляд незначительна, но их технические показатели существенно отличаются.
Сравнительные характеристики пеноблоков и газоблоков
Пенобетон и газобетон относятся к ячеистым бетонам, и они имеют схожую структуру. Но благодаря различному сырьевому составу и технологии производства ячеистые блоки имеют различные свойства и технические характеристики. Взвесит отличие газоблока от пеноблока важно для правильного выбора строительного материала. Разница между ними должна быть тщательно изучена.
Основные показатели, по которым отличаются данные строительные материалы, для удобства анализа, сведены в таблицу.
Технические показатели | Газоблок | |
---|---|---|
Цвет | Серый | Белый |
Структура поверхности | Гладкая | Шероховатая |
Марка по плотности | 700, 800, 900 | 350, 400, 500, 600, 700 |
Прочность | Класс В2,0 при D800 | Класс В2,0 при D500 |
Долговечность | 70 лет | 50 лет. Поскольку это современный материал не было возможности проверить опытным путем |
Паропроницаемость | Ниже | Выше |
Теплопроводность | Выше, но в случае с этим показателем, это является недостатком для стен дома | Ниже |
Кладка | Выполняется кладка на цементно-песчаный раствор с толщиной шва 10 мм. Это способствует образованию мостиков холода | Кладка газоблоками выполняется на специальный клей. Толщина шва составляет 1 мм, что исключает формирования мостиков холода |
Геометрические параметры | Производство выполняется в формах и отклонения могут достигать 5 мм. | Автоклавный газоблок нарезается на современном оборудовании и отклонение размеров от нормы составляет ± 1 мм |
Усадка | 3 мм/м | Процесс усадки проходит в автоклаве, поэтому он не превышает 0,1 мм/м |
Нагрузка на фундамент | Из-за большего удельного веса нагрузка на фундамент выше | Ниже |
Удобство выполнения работ | Сложнее, за счет большего веса | Проще, т.к. удобнее работать с легким материалом |
Звукоизоляция | Ниже | Выше |
Удобство обработки | Сложнее | За счет меньшей плотности материала, его легко пилить |
Коэффициент экологичности | 4 | 2 |
Влагостойкость | Выше | Ниже |
Морозостойкость | Ниже | Выше |
Огнестойкость | Высокая | Высокая |
Стоимость | Ниже | Значительно выше |
Вернуться к содержанию
Всё о пеноблоках
Пеноблоки изготавливаются из пенобетона, который образуется путем механического перемешивания бетонной смеси с пеной. Таким образом, значительно облегчается вес материала. Поры пеноблоков закрыты, что способствует повешенной влагостойкости.
Составные компоненты пеноблоков:
- песок;
- цемент;
- вода;
- пена.
Технические характеристики:
- размеры пеноблоков и газоблоков выбраны одинаковые – 200х300х600 мм;
- вес одного блока соответствующего размера – 22 кг;
- плотность материала – (300 – 1200) кг/м3;
- водопоглощение – 14%;
- теплопроводность – (0,1 – 0,4) Вт/м*К;
- морозостойкость – 35 циклов;
- предел прочности на сжатие – (0,25 – 12,5) Мпа;
- расход материала – (21 — 27) шт/м3.
Достоинства пеноблоков:
- Низкий уровень теплопроводности. Это позволяет не пропускать холод и долго сохранять тепло в помещении. Теплопроводность пеноблоков ниже, чем у большинства строительных материалов.
- Небольшой вес. Масса блока из пенобетона значительно меньше, чем у других строительных материалов соответствующего объема, хотя газоблок легче. Такое свойство позволяет уменьшить расходы на фундамент, т.к. есть возможность уменьшить его прочность и объем. Также легкий штучный материал проще транспортировать и монтировать.
- Высокая прочность. При использовании блоков марки D900 возможно возводить несущие стены из пеноблока для трехэтажного дома. Для здания повышенной этажности используют несущие конструкции из других материалов.
- Микроклимат
- Хорошо выдерживают низкую температуру, даже сильные морозы ему не страшны.
- Огнестойкость. Несущая конструкция из пенобетона способна выдерживать высокую температуру и находится под влиянием открытого огня более 4 часов. При этом она не теряет своей несущей способности.
- Экологичность. Материал выполнен из экологичных компонентов, а пена образуется при помощи белковых или синтетических вспенивателей, которые не выделяют вредных веществ. К тому же структура пенобетона подобна структуре пенопласта и все поры изолированы.
- Биостойкость. Материал не подвергается гниению.
- Влагостойкость. Благодаря изолированным ячейкам газобетон имеет хорошую влагостойкость.
- Легкость обработки. Пеноблок легко пилить и сверлить без применения специального оборудования и больших физических затрат.
Их недостатки:
- Усадка конструкции из пеноблоков может составлять до 3 мм на каждый метр высоты стены. Особенно проявляется такое свойство, если была нарушена технология изготовления штучного материала.
- Способность впитывать влагу пеноблоками и необходимость их дополнительной защиты. Небольшая вероятность такой неприятности существует, возможно Вам понадобится выполнить дополнительную отделку.
- При повреждении образуются сколы в углах блоков. Именно поэтому, его необходимо транспортировать на поддонах в упаковке и бережно переносить на место выполнения работ.
- Если в стену из пеноблока нужно будет вбить гвоздь или дюбель он не будет держаться. Для этих целей необходимо использовать специальные дюбеля из АВС-пластика.
- Благодаря простоте изготовления, широко развито кустарное производство пеноблоков. В случае приобретения такого штучного материала, его технические характеристики могут не соответствовать заводским показателям. На первый взгляд трудно определить, какая партия пеноблоков является фабричной.
Вернуться к содержанию
Всё о газоблоках
Газоблоки изготавливаются в автоклавах из газобетона. Он образуется благодаря химической реакции, в результате которой выделяется газ. В структуре газобетона создается множество мелких трещин под действие выходящего газа, поэтому такой материал пропускает воздух и влагу.
Составные компоненты газобетона:
- цемент;
- кварцевый песок;
- известь;
- вода;
- алюминиевая пудра;
- химические добавки.
Технические характеристики:
- габариты блоков из газобетона – 200х300х600 мм;
- вес одного блока соответствующего размера – 18 кг;
- плотность материала – (300 – 1200) кг/м3;
- водопоглощение – 20%;
- теплопроводность – (0,1 – 0,4) Вт/м*К;
- морозостойкость – 35 циклов;
- предел прочности на сжатие – (0,5 – 25) Мпа;
- расход материала – (21 — 27) шт/м3.
Плюсы газоблоков:
- Прочность. Хотя газобетон и не самый прочный материал, но для его веса этого более чем достаточно.
- Легкость. Можно без особых усилий доставлять штучный материал на место выполнения работ.
- Простота обработки. Газобетон легко пилить и сверлить даже при помощи ручного инструмента.
- Теплоизоляция. Коэффициент теплопроводности достаточно низкий, что позволяет сохранять тепло в помещении в зимнее время года и не пропускать его в жаркие летние дни.
- Огнеустойчивость
- Звукоизоляционные свойства, как правила достаточно высокие, однако они зависят от марки материала и толщины конструкции.
- Экологичность. Токсичность материала значительно ниже существующих норм.
- Биостойкость. На газоблоках не образуется грибок, гниль или плесень.
Минусы:
- Высокий процент водопоглощения. По этой причине фасадная штукатурка плохо держится на поверхности стены. Чтобы обеспечить достаточную адгезию, поверхность стены необходимо обрабатывать грунтовкой глубокого проникновения.
- Плохо работает на изгиб. Важно чтобы фундамент был надежным и не давал усадки. В противном случае стены могут дать трещины.
- Большая проблема закрепить что-либо на стене из газоблока. Для этого понадобятся специальные крепежи.
- Металлические элементы, вмонтированные в стену из газобетона, поддаются окислению.
- Учитывая, что газобетон недавно стал использоваться в строительстве, нельзя опытным путем проверить долговечность материала.
Вернуться к содержанию
Технологии изготовления этих материалов
Процесс создания пенобетонных блоков:
- В промышленный бетоносмеситель засыпается цемент и песок в необходимой пропорции. Предварительно взвешиваются все компоненты, необходимые для изготовления продукта. В зависимости от пропорциональных соотношений песка и цемента определяется марка прочности от D400 до D1000. Чем выше марка пенобетона, тем прочнее и массивнее материал.
- В сухую смесь добавляется необходимое количество воды, чтобы получить раствор нужной консистенции.
- Вымешивается состав до формирования однородной консистенции.
- Когда раствор будет готова, в промышленный миксер добавляется пена.
- Выполняется перемешивание цементно-песчаной смеси с пеной.
- После того как раствор будет готов, его выливают в формы.
- После заливки формы должны выстояться до 4 часов, за это время происходит первичное схватывание.
- По истечении 4-х часов формы загружаются и вывозятся в место, где пенобетон будет сохнуть в естественных атмосферных условиях. За три недели материал достигает достаточной прочности для возведения несущих конструкций здания.
- Оставшаяся прочность набирается на протяжении последующего полугода. В дальнейшем, прочность материала только увеличивается. Этот процесс длится на протяжении 50 лет эксплуатации.
Технология изготовления газобетонных блоков:
- Цемент, кварцевый песок и известь дозируется в необходимой пропорции. Все компоненты погружаются в специальный смеситель и тщательно перемешиваются.
- К сухой смеси добавляется алюминиевая пудра и вода в необходимом количестве.
- После тщательного перемешивания состав погружается в формы.
- В течение нескольких часов он отстаивается и в этот период происходит химическая реакция, в результате которой выделяется углекислый газ. Реакция происходит в результате взаимодействия воды с алюминиевой пудрой. Вследствие химического процесса образуются поры, и материал увеличивается в объеме. За время отстаивания происходит первичное схватывания материала.
- После первичного схватывания формируется полусырой массив. Из него специальной резательной установкой нарезаются блоки по размерам. Такая технология позволяет выполнить очень точную нарезку. Обрезки материала собираются, повторно замешиваются и снова идут на порезку.
- Нарезанный материал отправляется в автоклав, где в течение нескольких часов под давлением 11,5 атмосфер блоки пропариваются при температуре 180 градусов. При пропаривании под давлением в автоклаве штучный материал набирает свою прочность в полном объеме.
- На выходе из автоклава газоблоки укладываются на поддоны и накрываются для предотвращения попадания влаги. В таком состоянии материал отправляется на реализацию.
Отдельно отметим, что оборудование для изготовления блоков из газобетона достаточно сложное и дорогостоящее.
Изучив, из чего состоят газоблоки и пеноблоки, их технические характеристики, технологию производства и отличия, легче определиться, из чего строить дом или дачу. Какой материал выбрать для возведения здания пеноблок или газоблок зависит от технических требований и финансовых возможностей будущего хозяина дома.
Не нашли ответов в статье? Больше информации по теме:
Чем отличается газобетон от пенобетона
Ячеистые бетоны считаются востребованными строительными материалами, из которых получаются теплые, долговечные, экологически чистые и надежные строения. Они считаются доступными по стоимости, поэтому на строительство не приходится тратить много денежных средств. Однако многие люди в процессе выбора такого материала сталкиваются со сложностью определения оптимального вида.
Обычно выбирать приходится из газобетона и пенобетона. Данные материалы обладают многими одинаковыми параметрами, однако имеют и некоторые отличия, которые должны быть изучены перед непосредственной покупкой конкретного вида ячеистого бетона. Давайте рассмотрим, чем отличается газобетон от пенобетона.
СОДЕРЖАНИЕ
- Определение пенобетона и газобетона
- Теплоизоляционные свойства газобетона и пенобетона
- Прочность
- Экологичность
- Огнестойкость
- Паропроницаемость
- Стоимость и усадка
- Область применения газобетона и пенобетона
- Итог
Определение пенобетона и газобетона
От качества купленных строительных материалов зависит качество, долговечность и надежность самого возведенного объекта.
Важно! Безответственное отношение к выбору материала обычно приводит к строительству дома, не обладающего нужными параметрами для постоянного проживания или других целей.
Газобетон создается в специальных автоклавах, что обеспечивает следующие его особенности:
- все компоненты газобетона правильно и четко измеряются, поэтому отсутствует возможность, что будет добавлено слишком много одного материала;
- гарантируется контроль над технологией обработки и этапами производственного процесса;
- обеспечивается высокое качество конечного сырья.
Процесс производства газобетона делится на несколько последовательных этапов:
- Замес смеси, состоящей из песка и цемента, а также извести и оптимального количества воды. Полученная масса должна обладать белой расцветкой. В нее добавляется специальная пудра из алюминия, необходимая для того, чтобы при совершении химической реакции выделялся водород. Это гарантирует наличие вспенивания и образования в структуре газобетона закрытых воздушных пузырьков, за счет которых получается материал с высокими теплоизоляционными параметрами.
- Формовка. Сделанная смесь заливается в заранее подготовленные формы, предназначенные для застывания. Она там оставляется на определенный промежуток времени, после чего полученные блоки газобетона разрезаются на отдельные элементы, обладающие оптимальными размерами и параметрами. Данный процесс реализуется на специальных линиях, поэтому является полностью автоматизированным. Это гарантирует точность разрезания блоков газобетона.
- Запекание. Полученные блоки направляются в автоклав, представленный специальной камерой. В ней подается на блоки газобетона горячий пар под высоким давлением. Это гарантирует оперативное застывание, в результате чего они приобретают высокую прочность.
К плюсам применения газобетона относится:
- автоматизация производства, поэтому минимизируется возможность ошибки, совершенной человеком;
- в технических условиях контролируется качество результата;
- полученные качественные и прочные блоки газобетона могут использоваться для создания несущих стен;
- получаются изделия, обладающие прекрасной геометрией, поэтому швы в стенах отличаются небольшими размерами;
- газобетон за счет застывания в автоклаве обладает хорошим показателем прочности по сравнению с пенобетоном;
- так как используется автоматизированное оборудование, то производство не занимает много времени.

Структура газобетона
К минусам газобетона относится высокий показатель водопроницаемости, поэтому не желательно работать с этим материалом в условиях высокой влажности.
Пенобетон формируется с применением песчано-цементного раствора. Его вспенивание производится с помощью специального пенообразователя. Полученная смесь заливается в специальные формы, где в течение нужного количества времени происходит застывание материала. После этого блоки вынимаются из форм и разрезаются при необходимости.
Пенобетон по сравнению с газобетоном имеет не слишком точные размеры, а также для его застывания требуется довольно много времени, поэтому обычно тратится на это около 28 дней. К плюсам его применения относится невысокая стоимость, возможность сделать самостоятельно непосредственно на строительной площадке и отсутствие необходимости пользоваться дорогостоящим оборудованием. Однако минусов у такого способа производства ячеистого бетона имеется намного больше:
- не слишком высокое качество пенобетона, если застывает сырье меньше 28 дней;
- сушка должна выполняться в оптимальном и отапливаемом помещении, поэтому повышаются затраты на содержание и аренду такого места;
- блоки пенобетона не обладают идеальной геометрией.

Структура пенобетона
Таким образом, хотя структура газобетона и пенобетона схожа, они обладают существенными отличиями в технологиях производства, поэтому их характеристики различны.
Теплоизоляционные свойства газобетона и пенобетона
Данный параметр важен для каждого жилого строения. Газобетонные блоки имеют более низкую морозостойкость по сравнению с пеноблоками, однако за счет того, что они обладают идеальными размерами и ровными краями, швы в стенах отличаются небольшими размерами, что положительно сказывается на защите строения от холода и ветра.
Коэффициент теплопроводности у газобетона и пенобетона значительно отличается:
- у газобетона, с плотностью D 500 он равен 0,12;
- у пенобетона с плотностью D 700 данный показатель равен 0,24.
Поэтому пеноблоки обладают лучшими теплоизоляционными параметрами, а также отличаются прекрасным термическим сопротивлением.
Важно! Пенобетонные блоки обладают уникальной способностью накапливать тепло, что важно для каждого жилого строения, поэтому существенно снижаются затраты на обогрев зданий, однако для достижения такого эффекта стены должны быть толще газобетонных в два раза.
Прочность газобетона и пенобетона
Данный параметр так же важен для каждого владельца дома. Он зависит от плотности конкретного материала, причем она равна:
- у пенобетона – от 600 до 100 кг/м3;
- у газобетона – 459 кг/м3.
В соответствии с этими значениями пеноблоки должны быть более прочными, однако за счет использования современного оборудования в процессе создания газобетонных блоков, они выдерживают при меньшей плотности более высокие нагрузки.
Таким образом, газобетон считается более прочным и качественным материалом, поэтому если возводится строение, на которое будут воздействовать разные существенные нагрузки, то желательно выбирать именно этот материал.
Экологичность газобетона и пенобетона
Жилые строения должны возводиться исключительно из безопасных и экологически чистых материалов, так как иначе будет создаваться опасность для жизни людей. Оба материала производятся без использования опасных или вредных компонентов, что обусловлено особенностями процесса их производства:
- для вспенивания газобетона используется водород, который остается в порах готовых блоков, однако он считается абсолютно безопасным для людей и природы;
- в процессе производства пенобетона используются разные искусственные или белковые вспениватели, а они так же считаются безопасными, поэтому не выделяют вредных веществ.
Таким образом, оба материала являются экологически чистыми. Поэтому можно без опасений выбирать их для возведения жилого строения.
Огнестойкость газобетона и пенобетона
Оба материала обладают хорошей стойкостью перед возгоранием. Они выдерживают прямое воздействие огня, поэтому жилые строения считаются безопасными для постоянного проживания.
Важно! Перед продажей любого материала производители осуществляют их испытания, что гарантирует наличие высоких параметров.
Паропроницаемость газобетона и пенобетона
По данной характеристике ячеистые бетоны приближены к натуральной древесине. Поэтому строения из них считаются комфортными для жизни. В помещениях устанавливается приятный и безопасный микроклимат.
В строениях регулярно обновляется воздух, поэтому газобетон и пенобетон эффективно применяются для возведения не только обычных частных домов, но даже для строительства бани.
Стоимость и усадка газобетона и пенобетона
Цена строительных материалов регулярно меняется, причем обычно она увеличивается.
Пенобетон по стоимости считается дешевле, чем газобетон, однако возведение дома из него обходится дороже, чем при использовании газобетонных блоков. Такой необычный факт обусловлен тем, что для получения качественных стен из пеноблоков требуется намного больше материала, чем при использовании газоблоков.
Клей, используемый во время строительства, обладает высокой стоимостью, причем его требуется больше при использовании пенобетона.
Область применения газобетона и пенобетона
Оба данных материала могут использоваться для разных целей. Из них делаются конструкции:
- несущие стены;
- разнообразные межкомнатные перегородки;
- ограждения.
Важно! За счет высокой прочности газобетонных блоков, они могут применяться для строительства домов, являющихся двухэтажными или даже трехэтажными.
Итог
Таким образом, пенобетонные и газобетонные блоки считаются эффективными и востребованными строительными материалами. Они используются для разных целей, являются долговечными, экологически чистыми и обладающими хорошей паропроницаемостью.
Они имеют схожую прочность, хотя качество газобетона считается выше, чем у пенобетонных блоков. Газоблоки производятся по особой технологии, поэтому обладают идеальными гранями и геометрическими формами. Однако производством пенобетона можно заниматься непосредственно на строительной площадке, и они имеют более высокие теплоизоляционные параметры.
Таким образом, для возведения жилого строения подходят оба данных материала, причем получаются теплые, качественные и долговечные здания. Выбор зависит от финансовых возможностей и предпочтений владельцев дома. Если на строения будут воздействовать разные серьезные нагрузки, то выбирается газобетон, а если дом будет находиться в регионе с суровым климатом, то лучше всего приобрести для строительства пенобетон. Также может быть полезна статья — «чем штукатурить газобетон снаружи и внутри дома».
Также может заинтересовать:
Отличие газобетона и пеноблока — в чем разница?
Газобетон отличается от пенобетона составом, способом производства и характеристиками. Оба материала являются ячеистыми бетонами, в которых поры занимают до 85% общего объема.
Особенности пеноблока
Достоинство пенобетона – это возможность производства непосредственно на стройплощадке. Для создания пузырей в цемент добавляют органические и синтетические элементы. Затем смесь поступает в формы, где застывает при атмосферных условиях.
Чтобы изготовить монолитный пенобетон, вместо формы используют разборную или неразборную опалубку. Вторая остается на месте после схватывания смеси.
Характеристики пеноблока
- возьмем за основу размер пеноблока – 200х300х625 мм;
- масса одного блока – 22,6 кг;
- плотность – от 300 до 1200 кг/м3;
- влагопоглощение – 14%;
- коэффициент теплопроводности – от 0,1 до 0,4 Вт/м*К;
- степень морозостойкости – до 35 циклов;
- прочность на сжатие – от 0,25 до 12,5 МПа;
- расход – примерно 22-26 шт/м3.
Особенности газоблока
Автоклавный газобетон изготавливается исключительно на заводе из природного сырья: воды, цемента, кварцевого песка, негашеной извести (оксида кальция), гипса. Газообразователем служит алюминиевая паста, без применения химических добавок. Песок предварительно измельчается до состояния порошка.
Дозировка и перемешивание компонентов происходит в специальном сосуде – автоклаве. В результате взаимодействия алюминиевой пасты, извести и воды, происходит активное выделение водорода, который формирует поры. При этом объем смеси увеличивается в 2 раза.
Характеристики газоблока
- размер блока – 200х300х625 мм;
- масса одного блока – 19,26 кг;
- плотность – от 300 до 1200 кг/м3;
- показатель поглощения влаги – 20%;
- коэффициент теплопроводности – от 0,1 до 0,4 Вт/м*К;
- степень морозостойкости – до 35 циклов;
- прочность на сжатие – от 0,5 до 25 МПа;
- расход – примерно 22-26 шт/м3.
Предварительно затвердевший массив поступает в зону кантовки и резки. Резка осуществляется пневматическими струнами толщиной до 1 миллиметра. Это позволяет добиться идеально ровной поверхности по заданным типоразмерам. Одновременно с резкой происходит изготовление захватных карманов при помощи фрезера.
Далее газобетонные блоки поступают в автоклавную камеру на 12 часов – для полного высыхания. Под действием давления, температуры и водяного пара, материал приобретает требуемые свойства. Минимальная шероховатость поверхности упрощает кладку, а также сокращает попадание холодного воздуха в дом.
Сравнение пенобетона и газобетона
Изготовление данных материалов регламентируется одними ГОСТами (ГОСТ 31359 «Бетоны ячеистые автоклавного твердения. ТУ» и ГОСТ 31360 «Изделия стеновые не армированные из ячеистого бетона автоклавного твердения. ТУ»). Несмотря на единый стандарт, их технические параметры отличаются.
Влагопоглощение и устойчивость к морозу
Процент поглощения влаги у пенобетона несколько меньше. Однако кладку из пористых бетонов, как правило, покрывают защитным слоем в виде штукатурки, сайдинга, облицовки или декоративного камня. Поэтому в реальной жизни разница не играет большой роли.
Прочность ячеистого бетона
Плотность обоих материалов составляет 300 – 1200 кг/м3. Газобетон более крепкий по сравнению с пенобетоном. Прочность последнего во многом зависит от качества компонентов. Газоблок однородный по всей плоскости и лучше выдерживает сверление, штробление, забивание гвоздей.
Экологичность
При изготовлении газоблоков, известь вступает в химическую реакцию с алюминиевой пастой. Процесс сопровождается выделением водорода. Часть данного газа сохраняется в затвердевшем составе и выходит уже после возведения стен.
Водород не является токсичным веществом и не представляет угрозы здоровью человека. Также безопасны синтетические и белковые присадки, которые содержатся в пенобетоне. Герметичные поры надежно удерживают газ. Оба материала обладают одинаковыми экологическими свойствами.
Подверженность усадке
Усадка пеноблоков варьируется от 1 до 3 мм/м, тем временем у газобетона – менее 0,5 мм/м. Вероятность появления трещин в конструкции из газоблоков, значительно ниже, чем у постройки из пенобетона.
Теплопроводность
Теплоизоляционная способность пористого бетона обратно пропорциональна плотности структуры. Пеноблок с малой плотностью обладает лучшей теплоизоляцией по сравнению с газоблоком. Однако возводить опорные стены из него нельзя по причине недостаточной прочности. В такой ситуации используют более плотный бетон, одновременно увеличивая толщину кладки. Например, в Сибири толщина стен здания должна быть минимум 65 сантиметров (при использовании пеноблоков марки D600). Иначе в помещении будет холодно.
Толщина кладки из газоблоков при тех же условиях получится менее 50 сантиметров, без потери плотности. Как видим, газобетон эффективнее держит тепло. Кроме этого, конструкция обладает меньшим весом.
Пожаробезопасность
Оба материала устойчивы к воздействию огня, хорошо пропускают кислород и выполнены из природных элементов. Легкость позволяет ускорить монтажные работы. По морозостойкости газоблок превосходит пеноблок в несколько раз.
Стоимость блоков
Газобетон дороже пенобетона на 15-20% по причине высокой себестоимости изготовления. Однако на этапе строительства его может потребоваться меньше. Кроме того, вес пеноблоков больше, что увеличит транспортные расходы. Не стоит забывать про армирование и утепление фасада. Поэтому перед закупкой материала, необходимо выполнить оценку проекта.
На итоговую стоимость также влияет связующий раствор. Газоблоки укладывают на клей, в то время как для пеноблока подойдет недорогой цемент. Но во втором случае потребуется больше времени и сырья на его приготовление. Получается, что строительство из газобетона (вместе со всеми материалами) выгоднее. Помимо этого, тонкий клеевой слой сокращает риск проникновения холодного воздуха в жилое помещение.
Разница в габаритах блоков
Газоблоки обладают более точной геометрией благодаря заводскому оборудованию. Пеноблоки делают прямо на стройплощадке в специальных установках (баросмесителях, пеногенераторах, компрессорах). Все это влияет на расход материала, скорость и удобство работы.
Думаем, что детальное знакомство с пенобетоном и газобетоном было для вас полезным. Окончательный выбор зависит от назначения объекта и финансовых возможностей. Желаем успехов в строительстве!
Строительство каменных домов в настоящее время набирает все возрастающую популярность. Во многом это связано с появлением таких современных материалов, как блоки из ячеистого бетона.
Изначально бетонные блоки применялись в качестве земены более дорогому кирпичу, однако они нуждались в последующем покрытии штукатуркой. В наши дни их используют практически повсеместно, от возведения фундаментов до обустройства стен и внутренних перегородок. При этом современные блоки обладают даже лучшими теплоизоляционными и акустическими свойствами, нежели глиняные кирпичи.
Ниже приведена сравнительная характеристика свойств керамического кирпича и блока из газобетона.
Параметры | Керамический кирпич | Газобетон |
Предел прочности на сжатие (кг/см2) | 110-220 | 25-50 |
Масса стены 1м3 (кг) | 1200-2000 | 70-900 |
Теплопроводность (Вт/мК) | 0,32-0,46 | 0,09-0,12 |
Морозостойкость (цикл) | 50-100 | 50 |
Водопоглощение (% по массе) | 8-12 | 20 |
Огнестойкость (класс) | 1 | 1 |
Наибольшее применение легкобетонных блоков из поризованного бетона (пенобетона, ячеистого бетона или газобетона) обусловлено, в частности, легкостью их монтажа и простотой в обработке (блоки легко поддаются сверлению, резанию или штроблению).
Таким образом, сейчас все реже стали использоваться блоки из так называемого «обычного» тяжелого бетона, хотя и стоят они дешевле тех же пенобетонных. Но так ли хороши столь широко разрекламированные газо- и пеноблоки? Удовлетворяют ли они критериям прочности, тепло- и шумоизоляции, пожаробезопасности и экологичности? Существует ли принципиальное отличие между пеноблоками и газоблоками, или между ними значительной разницы нет и по сути это одно и то же?
Газобетон, газозолобетон, пенобетон, газопенобетон и др. являются одними из многочисленных разновидностей пористого (ячеистого) бетона. Все они отличаются по способу получения ячеистой структуры, связанному с особенностями производства. По громогласным заявлениям производителей такие материалы благодаря своей пористости имеют ряд неоспоримых преимуществ. Так ли это на самом деле, нам и предстоит разобраться.
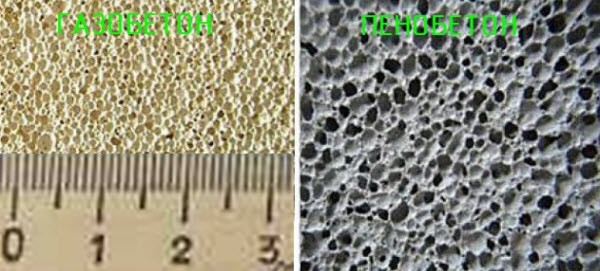
Структура газобетона (слева) и пенобетона
Начнем с особенностей изготовления строительных блоков.
Все ячеистые бетоны в зависимости от способа твердения производятся:
- автоклавным методом, при котором затвердевание материала происходит в герметичном резервуаре при высоком давлении в присутствии насыщенных паров воды.
- неавтоклавным методом, когда затвердевание осуществляется в естественной среде. В этом случае бетон прогревается с использованием электричества. При этом также возможна обработка насыщенными водяными парами, только уже при нормальном атмосферном давлении.
Особенности производства пенобетона
Пенобетон изготавливают перемешиванием цементной основы с добавлением специальных добавок — пенообразователей. В специальных формах, куда поступает вспененная масса, происходит затвердевание бетона в естественной среде, в результате чего получаются блоки. Возможно также заливание бетона не в формы, а в опалубку с последующим разрезанием на пеноблоки.
Особенности производства газобетона
Газобетон изготавливается только в специальной емкости — автоклаве — из цемента, воды, гипса и извести. Для обеспечения газообразования добавляют алюминиевую пасту или пудру. Чтобы материал получился прочным, на него воздействуют парами воды при высоких температурах и давлении. Происходящая при этом химическая реакция притекает с выделением водорода, благодаря чему обеспечивается пористость получаемого материала.
Окончательно застывший газобетон разрезается струнами на идеально ровные блоки, поэтому швы при кладке получаются весьма тонкими, благодаря чему удается избежать появления мостиков холода.
Таким образом, оставляющие компоненты данных материалов почти идентичны. Отличие заключается лишь в методе затвердевания и применяемых вспенивающих добавок. Газобетону в этом плане можно отдать предпочтение только потому, что автоклавный способ изготовления позволяет добиться нужных характеристик материала и равномерных качественных свойств. Производство пенобетона, как правило, не требует таких дорогостоящих вложений и изготавливать его могут в «гаражных» условиях, без каких-либо исследований и сертификации. зачастую даже не соответствует тем характеристикам, которые заявляют производители. Но и газобетон бывает низкого качества. Например, и в наши дни все еще производится устаревший неавтоклавный газобетон в той же Перми. Поэтому здесь нужно очень внимательно подходить и к выбору производителя.
Пенобетон и газобетон: в чем отличие?
Для производства обоих материалов пользуются одними и теми же ГОСТами. Тем не менее характеристики этих ячеистых бетонов сильно отличаются.
Морозо- и влагостойкость
Высокая морозостойкость газобетона — не более чем реклама. Более-менее высокими показателями морозостойкости могут обладать только достаточно плотные газобетонные блоки, о чем производители предпочитают не распространяться. Ввиду особенности технологии производства газобетон подобно губке «впитывает» воду, что не лучшим образом сказывается зимой в период холодов. Влажность по массе может достигать более 30%, а это значительно снижает теплосопротивление материала, в результате чего теряются заявленные изготовителем свойства и жилье становится холодным. Как правило, газобетонные стены изнутри покрываются грунтовкой для снижения паропропускаемости. Стоит иметь ввиду, что нельзя наносить штукатурку без грунтовки, а также наклеивать бумажные обои, чтобы снизить вероятность отсыревания блоков. Поверхность фасада стены нужно гидрофобизировать, при этом желательно эту процедуру проводить не реже, чем раз в 2-3 года. Благодаря гидрофобизации влага из внешней среды не будет впитываться так быстро в газоблоки, а ввиду ее паропроницаемости пары воды смогут выходить из стен в атмосферу. Нередко строения из газоблоков снаружи обкладывают кирпичем, однако тут стоит учитывать высокую паронепроницаемость кирпича и связанную с этим вероятность насыщения конструкции влагой, а значит, нужно предусмотреть зазор между стеной и облицовочной кладкой для возможности вентиляции. Чтобы облицовка не рухнула в один прекрасный момент, ее нужно обязательно прикрепить к несущей стене специальными анкерами из пластика или нержавейки. На крепеже сэкономить тут не удастся — не позволит низкая плотность газобетона.
У пенобетона такой недостаток, как способность вбирать в себя влагу, проявляется в гораздо меньшей степени.
Однако, как правило, стены из ячеистого бетона либо облицовываются тем же сайдингом или плиточной облицовкой, либо покрываются штукатуркой. В таком случае способность материалов к водопоглощению можно в расчет и не брать, тогда газобетон можно считать вдвое, а то и в три раза лучше по показателю морозостойкости.
Прочность
Если сравнивать пенобетон и газобетон, то первый при равной плотности обоих материалов однозначно проигрывает. А поскольку недобросовестные производители стараются экономить на пенообразующих, напрямую влияющих на прочность пенобетона, а также из-за неоднородности прочностных свойств по поверхности пенобетонных блоков, в этом плане, пожалуй, опять же логично сделать выбор в пользу газобетона.
Невысокая прочность обоих материалов не всегда дает возможность применять стандартный крепеж. Нередко приходится покупать более дорогие элементы, предназначенные специально для пористых бетонов.
Экологичность
Частично выделяемый в результате протекающей в процессе изготовления газобетона автоклавным способом реакции водород, большая часть которого остается в порах газоблока и может выделяться в процессе дальнейшей эксплуатации, не представляет никакой опасности для окружающей среды и жизнедеятельности человека.
Различные искусственные либо белковые вспениватели, применяемые в производстве пенобетона, также не таят в себе никакой опасности.
Соответственно, оба материала в этом плане никаких явных недостатков не имеют.
Склонность к усадке
Возникновению трещин и усадке наиболее подвержен пенобетон, превосходящий по этому показателю газосиликатные блоки в 2-6 раз.
Теплоизоляционные свойства
Теплоизоляционная способность пористого бетона возрастает с уменьшением плотности структуры материала. Тут пенобетон однозначно выигрывает. Но для кладки несущих стен он не годится из-за низкой прочности. Приходится делать стены из материала большей плотности и имеющего более высокую теплопроводность. Для комфортного проживания требуемая толщина стен из блоков пенобетона может достигать БОЛЕЕ ОДНОГО МЕТРА!
Газобетон может удерживать тепло намного лучше при равных климатических условиях и необходимая расчетная толщина стен получается меньше – в условиях Новосибирска в диапазоне 45-50 см. Плотность в данном случае будет также в пределах норм — D400 – D500.
Таким образом можно сделать вывод, что способность газобетона удерживать тепло гораздо выше, а стены прочнее и легче. Однако, не стоит забывать и про то, что газобетон является сильнейшим абсорбентом, а пропитавшись влагой он резко теряет по всем теплотехническим параметрам. Возникновение в связи с этим деформации строения способно испортить всю отделку. Для того, чтобы предотвратить такие последствия, нужно заранее побеспокоиться об организации защиты газобетонных конструкций от возможного сильного переувлажнения, а это дополнительные затраты по отделке фасада. Получается так, что газобетон для возведения наружных стен зданий без отделки применять крайне нежелательно.
Огнестойкость
В плане огнестойкости нет необходимости долго размышлять на тему, что выбрать — газобетон или пенобетон — хороши оба.
Что дешевле?
Если вопрос стоит в цене, то купить пенобетон оказывается выгоднее газобетона процентов на 20. Однако стоит иметь ввиду, что его может потребоваться больше, так что не торопитесь, а для начала все просчитайте.
Также стоит учесть, что пеноблок можно класть на обычный цементный раствор, а газобетон — на дорогую клеевую смесь, что не каждому по карману. Однако тоненький слой клея при кладке газобетона не создает таких мостиков холода, как цемент, что очень важно в плане энергосбережения. При этом клея также понадобится не так много, как цемента, и прежде чем говорить, дешевле кладка из газоблоков или пеноблоков, нужно учесть все параметры и выполнить необходимые расчеты.
Поскольку газобетонные блоки производятся лишь на заводах, то и размеры их стабильнее, нежели у пенобетонных. Поэтому при кладке газобетона и расход компонентов меньше, и скорость выше.
Прежде чем решить, что все-таки лучше выбрать — пеноблок или газоблок — нужно тщательно проанализировать все «за» и «против», определиться с необходимыми характеристиками материала и предварительно прикинуть все возможные затраты.
Видео: Газобетон или пенобетон: что лучше?
В сегменте ячеистых бетонов конкурируют два популярных материала – пенобетон и газобетон. Планируя строительство дома, дачи, гаража или бани, каждый хозяин старается учесть все нюансы, предугадать различные ситуации, прикинуть стоимость, в общем, создать максимально реальный план, прежде чем приступить к работе.
Первая и важная задача – выбор материала для несущих стен. Из чего лучше строить дом, из пеноблока или газоблока? О каждом из них есть свои как положительные, так и отрицательные отзывы.
Пенобетон или газобетон – что лучше для строительства дома
Ячеистые бетоны – это группа строительных материалов, изготовленных из бетона и различных добавок, придающих ему пористую структуру. Наиболее известные представители этого вида – газобетон и пенобетон.
На первый взгляд это идентичные материалы. Однако есть и различия, формирующие отличительные свойства, которые и являются камнем преткновения между сторонниками и противниками этих материалов.
Чтобы сделать объективный вывод и правильный выбор предлагаем ознакомиться, чем отличается газоблок от пеноблока – сравнение по характеристикам, свойствам и цене. Для этого изучим все этапы жизненного цикла этих стеновых материалов, начиная с технологического процесса производства, заканчивая декоративной отделкой, т.е. проведем полный сравнительный анализ.
Рекомендуем материал по теме:
Плюсы и минусы домов из газобетона + отзывы владельцев
Плюсы и минусы домов из пенобетона + отзывы владельцев
а также
Преимущества и недостатки пенобетонных блоков + какой выбрать
Сравнение, что лучше: пеноблоки или газоблоки
1. Производство пенобетона и газобетона
Сравнение в рамках технологии изготовления (производства)
Состав
Оба материала производятся путем смешивания бетона с материалами, которые сообщают ему пористую структуру.
Но, при производстве пенобетона таким материалом (пенообразователь, пластификатор) выступает смола древесная омыленная (СДО), а газобетона – пылевидный алюминий.
Технология изготовления
Пенобетон производится в виде отдельных блоков. В связи с этим разновидность его типоразмеров и видов ограничена.
Газобетон изготавливается в массе, которая после застывания нарезается на блоки заданной величины и конфигурации. Таким образом, достигается большее геометрическое разнообразие элементов по габаритам.
Производство
Газоблок производится только в заводских условиях на специализированном оборудовании.
Пенобетон может изготавливаться и на небольших предприятиях (мини-заводы, установки, кустарное, частное производство).
Поры (ячейки)
Ввиду особенностей производства поры на внешней поверхности газобетонного блока остаются открытыми, что делает его похожим на губку. За сутки пребывания в воде газобетон набирает до 47% влаги. Т.е. становится тяжелее почти вдвое. материал незащищенным перед воздействием влаги или осадков. Если к этому прибавить мороз, то незащищенная стена из газобетона довольно быстро покроется сеткой мелких трещин, устранить которые можно разными способами.
Поры пенобетонного блока закрыты по всей массе. Это придает ему гидрофобные свойства. Пенобетон подобен поплавку – будет держаться на воде длительной время.
Как показывают тесты пользователей – выстоянный (набравший прочности) в течение месяца пенобетон (рекомендованное время) способен держаться на поверхности воды более месяца.
2. Характеристики пенобетона и газобетона
Параллельное сравнение в пределах свойств и характеристик материала
Размеры пор
Алюминиевая пудра или паста, распределяясь по газобетонной смеси позволяет получить одинаковые по своему размеру пузырьки – поры.
В пенобетоне поры разные по виду (объему). Материал подготовлен для сайта www.moydomik.net
Плотность
Одинаковая у пенобетона и газобетона, колеблется в пределах от 300 до 1200 кг/м.куб и зависит от марки. Например, марка D 500 обладает плотностью в 500 кг/м.куб при естественной влажности материала;
Вес (что тяжелее)
Вес ячеистых бетонов также зависит от марки. Например, 1 м.куб. материала марки D 500 будет весить 500 кг.
Прочность (что прочнее, крепче)
У газобетона одинаковая по всему объему блока, у пенобетона неоднородная, что обусловлено спецификой распределения пенообразующей добавки.
Кроме того, пенобетон и газобетон отличаются низкой прочностью на изгиб. Это выдвигает дополнительные требования к устройству фундамента и его способность обеспечить формостабильность дома (предотвратить неравномерную усадку).
Набор прочности
Газобетон имеет максимальную плотность (соответствует марке) на ранних стадиях изготовления. В процессе хранения газоблоков или эксплуатации строения она снижается.
Пенобетону же, нужно не менее 28 дней с момента производства, для того, чтобы выйти на заявленный показатель плотности. Это выдвигает особые условия к началу строительных работ.
Чтобы убедиться в том, что блок набрал прочность, его лучше приобрести заранее и хранить на месте строительства месяц. В противном случае, конструкция, построенная из свежеизготовленного пенобетона, даст существенную усадку. Стоит отметить, что пенобетон набирает прочность по мере эксплуатации. Т.е., чем старше блок или дом из пенобетона, тем он прочнее.
Размер (геометрия)
Благодаря тому, что газобетон режется, а не заливается в опалубку, его размеры гораздо точнее. Это способствует достижению меньшей толщины кладочного шва (2-3 мм) и сокращение площади, через которую тепло уходит наружу (мостики холода).
Толщина шва пеноблока колеблется в больших пределах и составляет 2-5 мм. В значительной мере толщина шва определяется мастерством кладочника.
Влагопоглощение
Способность впитывать воду больше у газобетона, что обусловлено наличием открытых пор.
Теплопроводность (что теплее)
При одинаковой плотности (марке блока) пенобетон и газобетон по-разному удерживают тепло.
Газобетон выступает лучшим теплоизолятором, нежели пенобетон. Например, достаточной толщиной стены для Москвы и Подмосковья при использовании пеноблока марки D 500 будет 600 мм, при использовании газобетона, всего лишь 450 мм.
3. Укладка пенобетона и газобетона
Сравнение отличий в рамках строительного процесса (монтаж, укладка, обработка)
Требования к фундаменту
Идентичны, поскольку оба вида ячеистых бетонов относится к легким. Однако, незащищенный газобетонный блок, после намокания становится тяжелее почти на половину, что создает дополнительное давление на фундамент. Пенобетон же такой чертой не обладает.
Резка, выпиливание, сверление блоков и доборных элементов
Идентичны, благодаря структуре и составу придать ячеистобетонным блокам нужную форму можно с помощью обычной ручной пилы. Просверлить, проштробить отверстие или канавку (паз), тоже легко.
Скорость строительства (укладки, монтажа)
Малый вес обоих сравниваемых материалов делает процесс строительства быстрым и простым, по сравнению, например, со штучным кирпичом.
Требования к раствору, клею для укладки
Для газобетона нужно использовать специальную клеящую смесь, это позволяет снизить расход и обеспечить тонкий шов.
Пенобетон можно класть на клей или песчано-цементную смесь.
Защита (консервация)
Если возникла потребность приостановить или прекратить строительные работы, например, на зимнее время, материалы нуждаются в консервации. При этом стены из пеноблока простоят определенный период без проблем, а вот из газоблока нужно укутывать в пленку, чтобы он не потянул влагу. Причем в защите газобетон нуждается в любое время года. Конечно, летом это не столь критично, стена из газобетона высохнет за неделю-другую (стоит ли прерывать работу так надолго?), то зимой – это намокание с последующим замерзанием-оттаиванием может привести к разрушению;
Усадка
Пенобетон может дать усадку в пределах 1-3 мм/м.п, усадка газобетона не превышает 0,5 мм/м.п.
Способность удерживать крепежи
Для обоих материалов нужно использовать специальные крепежные элементы (метизы, саморезы, химические анкера). Они разработаны специально для того, чтобы закрепляться в стенах из блоков с пористой структурой.
4. Отделка пенобетона и газобетона
Сравнительный анализ в пределах отделочных материалов и работ
Материал для отделки
Для облицовки газобетонных и пенобетонных стен (фасада) можно использовать: сайдинг, вагонку, штукатурку, вентилируемый фасад.
Материал для утепления
Благодаря тому, что в порах пеноблока и газоблока содержится воздух они являются хорошими теплоизоляторами. Поэтому дом из газобетона или пенобетона не нуждается в утеплении (при достаточной толщине стен). Если же такая необходимость возникла или, например, построена баня из этих материалов следует применять только гибкий утеплитель.
Штукатурная смесь
Для пенобетона и газобетона нужно использовать специальные смеси. Главное достоинство штукатурки для ячеистых бетонов в том, что она сохраняет способность дышать. При этом требования к штукатурке для пенобетона состоят еще и в том, что состав должен обладать хорошей адгезией к поверхности.
Технология оштукатуривания
Более пористая структура газобетона сообщает ему большую адгезию к любой штукатурке.
Пенобетон требует применения армировочной сетки, для того, чтобы штукатурка держалась надежно. В качестве альтернативы, мастера советуют обрабатывать поверхность пеноблока теркой или наждачной бумагой.
5. Стоимость пенобетона и газобетона (что дешевле)
Пенобетон дешевле на 20% газобетона той же марки. Он является более дешевым, т.к. в его производстве используются более дешевые материалы и оборудование. Это же приводит к появлению большого числа фальсифицированного материала.
Однако, при расчете стоимости строительства не стоит брать во внимание только цену покупки блоков. Нужно еще учитывать цену и расход клеевой смеси, отделочных материалов, потребности в дополнительных материалах (арматура, армирующая сетка, дополнительная изоляция, гидрофобизаторы и т.п.). Только после этого можно с уверенностью сказать, что дешевле, газобетон или пенобетон.
Что лучше, пеноблок или газоблок (сравнение) – видео
Сравнение пенобетона и газобетона – что лучше (таблица)
В таблице сопоставлены главные параметры, которые определяют свойства газоблоков и пеноблоков. В результате можно определить, какой материал выбрать для строительства при заданных условиях и требованиях.
Параметр | Пенобетон | Газобетон |
---|---|---|
Порообразующая добавка | смола древесно омыленная (относится к умеренно опасным веществам) | пылевидный алюминий |
Технология изготовления | Отливка блоков | Нарезание блоков |
Разнообразие элементов | Меньше | Больше |
Изготовление | Возможно кустарное производство | В заводских условиях |
Поры | Закрытые | Внешние – открытые, внутренние, в большинстве своем, закрытие |
Размеры пор | разноразмерные | одинакового размера |
Размеры блоков | ||
высота (толщина) | 200, 300, 400 | 200 |
длина | 600 | 500, 600 |
ширина | 100-300 | 75-500 |
Плотность, кг/м.куб. | 300-1200 | |
Вес, кг/м.куб. | 300-1200 | |
Прочность на сжатие, для марки D500 | В 1 | В 2,5 |
Набор прочности | Не соответствует расчетному, с дальнейшим набором | Моментальный с дальнейшей потерей |
Точность размера | Объективно существующие погрешности | Минимальная погрешность |
Влагопоглощение | Меньшее | Большее |
Морозостойкость, циклов | F-30 | F-25 |
Теплопроводность, Вт/М*к | 0,08 (теплоизоляционный) – 0,36 (конструкционный) | 0,1 (теплоизоляционный) — 0,14 (конструкционный |
Внешний вид | Хуже | Лучше |
Требования к фундаменту | идентичны | |
Простота монтажа, резки, сверления | идентичны | |
Требования к клеевой смеси | Любая | Только специальная смесь |
Защита стен | Не нужна | Нужна |
Усадка, мм/м.п. | 2-3 | 0,5 |
Способность удерживать метизы | идентична | |
Материал для отделки | Любой | Позволяющий сохранить способность блока «дышать» |
Материал для утепления | Предпочтительно мягкий утеплитель (при необходимости) | |
Оштукатуривание | Сложнее, ввиду гладкой структуры блока | Простое |
Цена, руб/м.куб. | 2200-2800 | 3200-3500 |
Итог
Как видим, однозначного ответа на вопрос, что лучше, газобетон или пенобетон, нет и быть не может. Исходя из этой таблицы, можно сделать вывод, что пенобетон и газобетон имеют существенные отличия, не позволяющие ставить их в один ряд. Несмотря на это, общим выводом станет: газобетон имеет лучшие показатели по прочности, пенобетон по всем остальным. Какой критерий важнее, зависит от конкретной ситуации, региона и бюджета на строительство. Соответственно, каждый сам решает строить ли дом из пеноблоков или газоблоков.
Для возведения жилого дома, дачи, бани, гаража и хозяйственной постройки успешно используются современные бетонные материалы с пористой структурой. Они обладают высокими теплоизоляционными свойствами, небольшим весом и простотой обработки. На этапе планирования будущей постройки каждый хозяин, анализируя эксплуатационные характеристики материалов, пытается выбрать выгодный для себя вариант.
Так что же лучше использовать для строительства – газобетон или пенобетон? Для этого достаточно сравнить материалы, чтобы определить основные сходства и различия между ними.
Содержание статьи
Сферы применения
Пеноблоки и газоблоки – одни из самых востребованных строительных материалов, имеющих облегченную ячеистую структуру и отличные теплоизоляционные характеристики.
Пенобетон обладает большей массой, длительным сроком службы и высокой прочностью. Это позволяет успешно использовать его для строительства малоэтажных зданий жилого и коммерческого назначения, сооружений для домашнего скота и хозяйственных построек, высота которых не превышает 3 полноценных этажей. Из него строят:
- Несущие стеновые конструкции.
- Внутренние перегородки.
- Технические ограждения и заборы.
- Армированные перекрытия.
Газобетон обладает постоянной и равномерной структурой, стойкой к усадке и растрескиванию. Эти характеристики позволяют использовать его в массовом строительстве промышленных, коммерческих и бытовых объектов различного типа. Зачастую он применяется для возведения:
- Перегородок.
- Несущих стен.
- Пролетов каркасных зданий.
- Многоэтажных комплексов.
Особенности производства ячеистых блоков
Основное отличие между газобетоном и пенобетоном заключается в технологии производства, которая позволяет формировать внутреннее пористое основание блочных материалов.
Облегченные пористые бетоны производятся из экологически безопасных компонентов. Именно в процессе производства материалов формируются их уникальные эксплуатационные характеристики.
Производство пеноблоков
Для изготовления пеноблоков применяется более упрощенная технология, позволяющая получить практичный и безопасный материал высокого качества.
Этапы технологического процесса:
- Компоненты в сухом виде смешиваются в подготовленной емкости и разводятся небольшим количеством воды.
- В полученную смесь добавляется пенообразователь. Все компоненты подвергаются механическому смешиванию для получения однородного раствора. В процессе замеса происходят необходимые химические реакции с выделением свободных газов. Газовый наполнитель обеспечивает необходимую пористость материала.
- Готовый раствор выливается в специальные формы и оставляется до полного затвердения в течение 5-10 часов. Изделия извлекаются из форм и складируются для естественной просушки в хорошо вентилируемом месте, защищенном от дождя.
- Технологическая прочность готовых блоков достигается через 2–3 недели после производства.
Отличительной особенностью изделий являются неровности поверхности, существенные отклонения в геометрии форм и размеров.
Важно! В качестве основы для заливки бетонной смеси может использоваться монолитная опалубка. После просушки основание нарезается на отдельные блоки.
Производство газоблоков
В отличие от пенобетона газобетонные блоки производятся в промышленных условиях, что гарантирует отменное качество и прочность материала.
Этапы технологического процесса:
- Сухие компоненты в нужных пропорциях разводятся водой и замешиваются до получения однородного раствора. Продолжительность замеса устанавливается технологической картой (ТК).
- Готовый раствор выливается в формы. В этом случае в качестве пенообразователя используется алюминиевая пудра или паста, вступающая в химическую реакцию с жидким цементным раствором. Выделение водородных газов способствует увеличению общего объема раствора.
- После полного застывания цементное основание извлекается из формы и нарезается на отдельные заготовки в виде блоков, плит и панелей.
- На завершающем этапе готовые изделия подвергаются термической обработке при помощи автоклавов или электрических печей. В автоклавах блоки проходят обработку горячим паром под давлением в 12 атмосфер, в электрических печах – сушку под воздействием высоких температур.
Подобная технология производства обеспечивает практически идеальную геометрию и высокую прочность газосиликата.
В этом плане газоблок более предпочтителен, чем его прямой аналог, поскольку технология производства в автоклаве обеспечивает отменное качество и хорошие эксплуатационные характеристики материала. Изготовление пенобетона не предусматривает применение дорогостоящего оборудования, поэтому весь технологический процесс можно организовать в домашних условиях.
Сравнительные характеристики газобетона и пенобетона
Несмотря на то, что производство ячеистых бетонных блоков строго регламентируется едиными государственными стандартами, технические параметры этих материалов имеют существенные различия.
Составляющие компоненты
Бетонные материалы производятся по технологии смешивания цемента с наполнителями, обеспечивающими ему ячеистую структуру.
Пенобетон производится на основе следующих компонентов:
- Портландцемент – связующее вещество.
- Известь или песок средней фракции – минеральный наполнитель.
- Пенообразователь – химическая добавка для создания пористой структуры.
- Вода.
В состав газоблока входят такие компоненты:
- Портландцемент – связующее вещество.
- Кварцевый песок, гипс, известь, древесная зола, шлаковые отходы – минеральные наполнители.
- Алюминиевая паста или порошок – компонент для образования пор.
- Вода.
Алюминиевый пенообразователь является вредным компонентом в чистом виде, при производстве газобетонного раствора он полностью растворяется в воде.
Структура
Разница между газобетонными и пенобетонными блоками заключается в их структуре и внешнем виде:
- Пеноблоки: крупные закрытые ячейки с низким уровнем влагопоглощения, отличными звукоизоляционными и теплоизоляционными свойствами. Имеют гладкую поверхность серого оттенка.
- Газоблоки: мелкие ячейки с микротрещинами, образованными в результате газообразования. Отличаются хорошей воздухо- и влагопропускной способностью, недостаточной теплоизоляцией и требуют обязательной внешней отделки. Материал имеет рельефную шероховатую поверхность белого цвета.
Прочность
Какой материал более прочный – газобетон или пенобетон? Данный параметр напрямую зависит от плотности блоков.
Плотность газобетонных блоков составляет от 200 до 600 кг/куб. м, плотность пенобетонных блоков – от 300 до 1600 кг/куб. м.
Современные технологии позволяют создавать газосиликатный бетон плотностью до 400 кг/куб. м, способный выдерживать предельную нагрузку, как и пеноблок плотностью свыше 600 кг/куб. м.
Несмотря на высокую плотность, пенобетон однозначно уступает своему конкуренту. Это связано с неоднородностью структуры по всей площади материала.
Морозостойкость
Данный параметр определяет способность ячеистого материала сохранять свои эксплуатационные характеристики при многократных циклах заморозки и разморозки.
По сравнению с другими пористыми материалами автоклавные газобетонные блоки обладают повышенной морозостойкостью, низкой теплопроводностью и отличной паропроницаемостью.
Например, благодаря особой структуре крепкий конструкционный газоблок «Сибит» способен выдержать 75 полных циклов заморозки и разморозки, в то время как у пеноблока этот показатель составляет лишь 35 циклов.
Важно! При добавлении в исходное сырье гидрофобных компонентов показатель морозостойкости газобетона может быть увеличен до 75 циклов.
Особенности использования
Обладая массой преимуществ, пористый пенобетон широко используется для малоэтажного строительства. Также он пригоден для возведения монолитных зданий и сооружений. В этом случае он применяется в качестве утепляющего или дополнительного материала.
Газобетонные блоки применяются как основной конструкционный и теплоизоляционный материал для возведения объектов различной сложности. Блоки подходят для обустройства жаростойких и прочих перегородок, заполнения каркасных конструкций из металла и бетона, реставраций ветхих зданий и возведения фахверковых конструкций жилых домов. При этом они могут эксплуатироваться в любых климатических условиях.
Стоимость
В чем заключается основная разница между пенобетоном и газобетоном? В их рыночной стоимости. При равных технических параметрах и размерах газосиликат обойдется дороже пенобетонных блоков. Это обусловлено сложностью технологического процесса, высокой стоимостью оборудования и расходного сырья, а также существенными расходами на его транспортировку.
Пеноблоки производятся на более дешевых и простых агрегатах, которые можно расположить на строительной площадке.
Рыночная стоимость газобетонных блоков выше, но производственные расходы компенсируются качеством строительства. При этом строить тёплый дом из газобетона экономически выгодно благодаря меньшему расходу строительного материала. К тому же на облицовку газобетона уйдет меньше цементного раствора, чем потребуется для выравнивания пенобетонных блоков.
Таблица технических параметров пенобетона и газобетона
В итоговой сравнительной таблице указаны основные технические параметры, определяющие эксплуатационные свойства газобетона и пенобетона. Подобное сравнение позволит определить, какой из материалов следует выбрать для возведения жилых домов и других объектов.
Технические параметры | Пеноблоки | Газоблоки |
---|---|---|
Наполнитель для создания пористой структуры | Омыленная древесная смола | Алюминий мелкой дисперсии |
Технологический процесс | Методом нарезки блоков или кассетной отливки | Методом отливки одиночных блоков |
Составляющие компоненты |
|
|
Оборудование для производства | Заводское оборудование или самодельные установки | Промышленное оборудование – автоклавы и электрические печи |
Тип пор (ячеек) | Неоднородная структура с закрытыми порами | Однородная пористая структура с внешними открытыми и внутренними закрытыми порами |
Размеры пор | Разного размера | Единого размера |
Типоразмеры блоков, см | ||
По высоте | 20, 30, 40 | 20 |
По длине | 60 | 50, 60 |
По ширине | 10-30 | 7,5-50 |
Плотность, кг/куб. м | 300-1600 | 200-600 |
Вес, кг/куб. м | 300-1600 | 300-600 |
Показатель прочности на механическое сжатие материала | 1,2 | 2,5 |
Время для приобретения прочности | Постепенно с последующим повышением прочности в течение 2-3 недель | Моментально при схватывании бетона в течение нескольких часов |
Точность геометрии формы | При нарезке цельной основы – незначительные погрешности. При производстве кассетным методом – существенные расхождения. Это является основным минусом материала. До 25 мм | Допускаются незначительные расхождения. Это основной плюс материала. До 2 мм |
Уровень влагопоглощения, % (при непосредственном контакте с водой) | 10 | 45 |
Морозостойкость (количество циклов заморозки и разморозки) | Средняя морозостойкость – до 35 циклов | Высокая морозостойкость в зависимости от плотности материала – от 35 до 75 циклов. Снижение уровня влажности приводит к существенному увеличению морозостойкости |
Звукоизоляция | Высокая | Низкая |
Показатель экологичности | 4 | 2 |
Теплопроводность, Вт/М*к | Для термоизоляции – 0,2 Для возведения конструкций – 0,35 | Для термоизоляции – 0,1 Для возведения конструкций – 0,18 |
Внешняя составляющая | Гладкая поверхность серого цвета | Шероховатая поверхность белого цвета |
Показатель паропроницаемости, мг/м×ч×Па | От 0,8 до 0,12 | От 0,15 до 0,23 |
Срок службы | Не более 35 лет | Свыше 60 лет |
Особенности проведения монтажных работ | Поскольку пористые бетоны легче, чем полнотелые материалы, их проще резать, сверлить, штробить и укладывать | |
Требования к клеевому составу | Для кладочных работ могут использоваться традиционные бетонные составы или специальные клеевые смеси. Толщина шва – 22 мм | Для монтажа предназначены специальные кладочные составы. Толщина шва – 3 мм |
Дополнительная защита стеновых конструкций | Не требуется | |
Степень усадки, мм/кв. м | 2-4 | 0,6 |
Способность удерживать крепежные элементы | Одинаковая. Необходимость использования специальных креплений, предназначенных для пористых материалов | |
Материал для облицовки | Все доступные материалы | Материалы с воздухопропускной способностью |
Материал для теплоизоляции | При необходимости используется надежный теплоизоляционный материал – минеральная или базальтовая вата | |
Нанесение штукатурного состава | Для оштукатуривания пористых оснований подходят специальные штукатурные составы с высоким уровнем воздухопроницаемости. Для повышения адгезии состава с обрабатываемой поверхностью дополнительно используется армированная сетка | |
Цена, дол./куб. м | 35-50 | 55-60 |
Сложно дать однозначный ответ на вопрос, какой же материал является лучшим – пенобетон или газобетон. Каждый из материалов обладает своими отличительными преимуществами и недостатками. Исходя из представленной таблицы, можно сделать краткий вывод: газоблоки имеют более высокие показатели морозостойкости и прочности, а пеноблоки – теплопроводности и экологичности. Какой технический параметр является более важным, зависит от сферы и особенностей применения строительного материала.
90000 WHAT IS AERATED CONCRETE (OR FOAMED OR CELLULAR OR GAS CONCRETE)? 90001 90002 90003 Aerated Concrete 90004 90005 90006 Aerated concrete may be defined as concrete made very light and cellular by the addition of prepared foam or by generation of gas within the unhardened mixture. It is also termed as cellular concrete and foamed concrete. 90007 90006 90007 90002 90003 By Generation of Gas 90004 90005 90006 The addition of powered aluminium or zinc to the cement causes evolution of hydrogen gas on addition of water.The powered metal is added to the cement in dry state in the ratio of 1: 1000. After thorough mixing in the dry state, water is mixed. This cause the evolution of gases and the process goes on for an hour or so. This cement paste is filled in the moulds up to about 1/3 90015 rd 90016 depth and soon afterwards, the paste fills the mould up to top and overflows. The excess paste is then struck off and the paste allowed to set. The paste hardens to a mass having the innumerable small bubbles surrounded by cement.This concrete is quite impervious to water but has a high drying shrinkage. So each block or unit should be fully cured and dried, before being used to eliminate any subsequent shrinkage. The density of this concrete is about 650 to 950 kg / m 90015 3 90016 and its strength is about 15 to 30 kg / cm 90015 2 90016. 90007 90002 90003 By Use of Foaming Agents 90004 90005 90006 Sometimes ordinary concrete can be made light by adding foaming agents like resin soaps. These agents develop bubbles inside the concrete and its density is reduced.The ordinary heavy aggregates are also sometimes replaced by wooden fibres, chips and saw dust etc. this also helps to reduce the weight of concrete. 90007 90002 90003 Where to Use Aerated Concrete? 90004 90005 90006 Aerated concrete is used for the following purpose 90007 90034 90035 Partitions for heat insulation because of its low thermal conductivity and weight 90036 90035 In fir proofing because of its better fire resistivity 90036 90035 Floor construction and light insulation 90036 90041 .90000 Aerated concrete vs. thin-shell concrete 90001 90002 Aerated concrete is conventional concrete infused with air bubbles or styrofoam beads to make the concrete less dense and lighter — like pumice compared to granite. It’s often used to replace heavier concrete blocks in small to medium-sized buildings. 90003 90002 Could this lightweight material replace shotcrete in constructing a Monolithic Dome? No, because the dome is already «aerated» using an entirely different method. 90003 90006 Whipped concrete 90007 90002 Aerated concrete is also known as Aircrete, cellular concrete, foam concrete, foamcrete, lightweight concrete, porous concrete.Some products use a foaming agent to add air bubbles in the concrete while it sets. Other products mix in polystyrene or cork. The goal of all aerated concrete is to displace the concrete with air. 90003 90002 Think of it as whipped yogurt. A container of whipped yogurt may be the same volume as regular yogurt, but it actually contains less yogurt. Less yogurt is fewer calories by volume. That’s why it’s sold as a diet product. Unfortunately, the consumer is only buying air for the same money.90003 90002 A cheaper alternative is to buy regular yogurt and eat less. Yes, that’s assuming the person has the willpower to eat less. If they do, they save money. 90003 90002 If aeration reduces concrete by adding air — like whipped yogurt — is there a method to minimize regular concrete — like putting a concrete wall on a diet? Yes, make thinner walls. 90003 90006 Thin concrete 90007 90002 The Monolithic Dome is a thin-shell concrete structure — emphasis on 90019 thin 90020. The critical advantage of thin-shell construction is how it uses the least material to enclose a given volume.The Monolithic Dome shell is so thin that it’s proportionally 90019 thinner 90020 than an egg shell. 90003 90002 The Monolithic Dome displaces concrete by using less concrete rather than adding lightweight fillers. It’s like eating less regular yogurt instead of more whipped yogurt. 90003 90006 Not both 90007 90002 An inevitable question arises, why not use both? Is not aerated concrete still a viable replacement for standard shotcrete for the dome shell? It is not. The problem is 90019 strength 90020.Aerated concrete lowers concrete density and 90019 compressive strength 90020. The dome shell is so thin; it requires concrete with a minimum amount of compressive strength to maintain the structure. For a typical dome, the design is for 4,000 psi concrete after 28-days. In practice, shotcrete often reaches 8,000 psi in 28-days. 90003 90002 If we replace high-density shotcrete with aerated concrete, we drop compressive strength — typically down to about 1,000 psi. In turn, we need much more aerated concrete to make up for the loss of compressive strength.Adding more aerated concrete thickens the shell. Now we have a problem. The thicker shell alters the engineering enough to require more aerated concrete to support the greater thickness of the shell. Then the newly thicker shell requires even more support and added depth. 90003 90002 The aerated concrete might reach an equilibrium where the thicker shell supports the dome. Of course, it ends up using about the same amount of actual concrete, plus paying for the lightweight mix additives. 90003 90002 And construction becomes more dangerous.90003 90002 It takes longer to build the dome because it requires more passes of lower density concrete. The structure is more vulnerable to failure during construction because each layer is less supportive than high-density concrete. 90003 90002 Plus there is the challenge of evenly distributing the lower density material in the concrete mix. It must be entirely consistent in mix and application. If too much filler is added to a batch and sprayed on the wall, that section will be weaker and prone to failure.It is visually identical to sections applied with the proper mix design. This is a huge problem that can not be fixed without rigorous tests and oversight. 90003 90006 No thermal benefit 90007 90002 The other main benefit of aerated concrete is thermal insulation. It does resist heat and cold better than regular concrete. However, it’s practically an energy conductor compared to polyurethane foam. 90003 90002 The Monolithic Dome has a full layer of polyurethane foam that not only protects the concrete shell from the exterior day-night cycle, it also helps keep water out of the building.90003 90002 Then there is the thermal flywheel effect. 90003 90002 The mass of the concrete shell — protected from exterior temperature swings by foam — absorbs the day-night changes of the interior. This thermal flywheel is maximized by the 90019 mass 90020 of the shell. So if we successfully build an aerated concrete shell and 90019 if 90020 it happens to lessen the density — and mass — of this shell, it will lower the mass of the thermal flywheel. In the end, it will require more energy to heat and cool the structure than a standard, high-density, shotcrete shell.90003 90006 The right material 90007 90002 Aerated concrete is an interesting material. There are many applications where it would be appropriate. However, the Monolithic Dome is not one of those applications. The Monolithic Dome already uses the least material possible while delivering the maximum benefits of strength, energy savings, and cost. 90003 90062 .90000 Weighing in on the Differences 90001 90002 Lightweight concrete presents a number of benefits to the building industry-lighter weight on a building’s structural load, greater sound absorption, better shock absorption and flexibility, improved insulation values-when compared to standard concrete blends. However, it has also been suspected in increasing cases of moisture-related flooring failures. Knowing the advantages and disadvantages of lightweight concrete can be the foundation for making better choices at the design and installation stages.90003 90002 90005 90006 90003 90008 Concrete Mix Differences 90009 90002 The prime difference between standard concrete mixes and lightweight concrete mixes lies in the aggregate that is used in the concrete mixture. 90003 90002 Standard concrete mixes typically use crushed natural stone as the coarse aggregate in the mix (along with Portland cement, water, and sand). The actual weight may vary slightly depending upon the local stone that is available, but generally, natural stone is relatively dense for its size, adding to the weight of the concrete mix.(This also adds to increased transportation and equipment costs.) 90003 90002 90015 Lightweight concrete instead uses a variety of alternate aggregate materials that may include more porous rock like pumice, manufacturing byproducts like fly ash or slag, or clay, shale or slate that has been treated with a heat process that expands the material and creates a series of internal pores in the aggregate. In effect, these materials provide lower mass per volume in the aggregate. Lightweight concrete may also be «foamed» by mixing a cement slurry into a pre-formed foam or AAC (autoclaved aerated concrete) in a process which introduces entrained air into the mix to reduce the final concrete weight.90003 90002 While the change in the aggregate for lightweight concrete does not seem to significantly impact the final concrete’s compressive strength, any type of lightweight concrete has a significant trade-off in two areas: the advantage of reduced structural weight once it’s dry, and the disadvantage of moisture retention that makes that drying process significantly longer. 90003 90008 Concrete Moisture Testing Differences 90009 90002 The weight advantage of lightweight concrete may provide the best benefit, but the same feature that reduces the weight-the pores in the aggregate or foam, or in the air introduced during mixing-also become additional spaces within the concrete that can trap and retain moisture.90003 90002 Unless a self-desiccant or another chemical material that locks moisture into the slab is also introduced, the water from the initial mix and hydration process must eventually find its way to the surface to evaporate away. Certain admixtures like fly ash retain moisture for longer periods, and the sheer volume of the many additional pores of the aggregate will also increase the amount of water retained, as well as the weight that additional moisture would cause until it is released.90003 90002 90026 90027 Because lightweight concrete has this increased capacity for moisture absorption, it can take two to three times longer than regular aggregate concrete to dry. This can present real challenges for the builder or contractor tasked with keeping the building schedule on track and under budget if this characteristic of lightweight concrete was not accounted for during the design and planning stage. The delays can be significant setbacks to the schedule or additional costs for dehumidification processes and equipment.90003 90002 It also means that surface-based concrete moisture test methods are at an extreme disadvantage in trying to gauge the level of moisture in a lightweight concrete slab. In fact, this became evident as moisture-related flooring failures became more common as the use of lightweight concrete expanded, and based on the findings, the ASTM has specifically disallowed calcium chloride (CaCl) testing for lightweight concrete. 90003 90002 So how can you mitigate the disadvantages of lightweight concrete’s propensity for retaining moisture when applying a flooring or finish to the slab? 90003 90033 90034 90035 Allow time.90036 90027 As has already been pointed out, lightweight concrete takes significantly longer to dry. By understanding this at the planning stage, the schedule can be adjusted to maximize the drying time. 90038 90034 90035 Optimize ambient conditions. 90036 90027 There are a number of environmental factors that influence concrete drying time. Having the slab at service condition, or adjusting airflow, relative humidity (RH) levels and temperature to maximize the drying process can optimize the movement of the moisture from the slab to the surface and away.90038 90034 90035 Test with RH testing. 90036 90027 Only RH testing, like the Rapid RH 90048 ® 90049, can accurately gauge the moisture condition of a lightweight concrete slab. Because the Rapid RH® places sensors within the slab at the optimal depth, test results will provide an accurate picture of the RH within the slab and allow for informed decisions about installation schedules, adhesive or finish choices and remedial steps if necessary. The Rapid RH 90048 ® 90049 provides fast, easy-to-use technology for immediate updates on the slab conditions.It also complies with ASTM F2170 to allow documented warranty information when necessary. 90038 90053 90002 Lightweight concrete has distinct advantages and disadvantages in the building industry. Knowing what they are allows building and flooring professionals to make informed decisions, and includes the necessity of accurate RH testing to confirm and document the readiness of the slab. The Rapid RH 90048 ® 90049 helps you be sure that the slab is ready for the next step towards a long-lasting and beautiful floor.90003 90058 90002 Jason has 20+ years ‘experience in sales and sales management in a spectrum of industries and has successfully launched a variety of products to the market, including the original Rapid RH® concrete moisture tests. He currently works with Wagner Meters as our Rapid RH® product sales manager. 90003 .90000 Compressive Strength of Lightweight Concrete 90001 90002 1. Introduction 90003 90004 Concrete is a mixture made of aggregates, water, cement, and different additives. The «lightweight» term can be added to different types of concrete which are all common in one specification, and that is «lower density» than normal weight concrete (NWC). This reduction in density is achievable by different methods such as using lightweight aggregate (LWA) in concrete, foamed concrete (FC), and autoclaved aerated concrete (AAC) or by any other techniques that reduce the final specific weight of the product, and thus the achieved weight is less than what we have in NWC mixtures.Whereas NWC weighs from 2240 to 2450 kg / m 90005 3 90006, lightweight concrete weighs ~300-2000 kg / m 90005 3 90006, but the practical range of density for lightweight concrete is 500-1850 kg / m 90005 3 90006. Before talking about the background of LWC, we prefer to explain a little more about the different types of LWC and their mechanical properties. 90011 90012 1.1 Lightweight aggregate concrete (LWAC) 90013 90004 There are a variety of lightweight aggregates that can be used in the production of LWAC, such as natural materials, like volcanic pumice, and the thermal-treated natural raw materials like expanded glass, clay , shale, etc.LECA is an example of expanded clay and Poraver is an example of expanded glass aggregates. There are also other types, which are aggregates made of industrial by-products such as fly ash, like Lytag. The final properties of the LWC will depend on the type and mechanical properties of LWA used in the concrete mixture. 90011 90012 1.2 Foamed concrete (FC) 90013 90004 With incorporation of considerable amount of entrained air (20% to 50%) in concrete, foamed concrete is produced which is a workable, low-density, pumpable, self-levelling, and self- compacting LWC.Foamed concrete is used more as a nonstructural concrete for filling voids in infrastructures, a good thermal insulation, and filler for space in buildings with less increase in the dead load. 90011 90012 1.3 Autoclaved aerated concrete (AAC) 90013 90004 AAC, or also named as autoclaved gas concrete, to which a foaming agent is added, was first produced in 1923 in Sweden and is one of the oldest types of LWC. AAC construction systems were then popular all around the world because of its ease of use.90011 90012 1.4 Structural and nonstructural lightweight concrete 90013 90004 Lightweight aggregate concretes (LWAC) can be used for structural applications, according to the American Concrete Institute (ACI). To be considered as structural lightweight concrete (SLWC), the minimum 28-day compressive strength and maximum density are 17 MPa and 1840 kg / m 90005 3 90006, respectively. The practical range for the density of SLWC is between 1400 and 1840 kg / m 90005 3 90006. LWC made of a material with lower densities and higher air voids in the cement paste are considered as nonstructural lightweight concrete (NSLWC) and will most likely be used for its insulation and lower weight properties.LWC with compressive strength less than 17 MPa is also considered as NSLWC. There are several benefits with using LWAC such as improved thermal specifications, better fire resistance, and dead load reduction which results in lower cost of labor, transportation, formworks, etc., especially in precast concrete construction industry. With the reduction of the concrete density, the properties of the concrete change fundamentally. For two specimens of concrete with the same compressive strength, but one made of LWC and the other one made of NWC, the tensile strength, ultimate strains, and shear strengths are all lower in LWC than NWC, while the amount of creep and shrinkage is higher for LWC.LWC are also less stiff than the equivalent NWC. However, there are benefits in using LWC such as reduction in dead load that results in slight reduction in the depth of a beam or slab. It is also observed that the elastic modulus of LWC is lower than the equivalent strength of NWC, but when considering the deflection of a slab or beam, this is counteracted by the reduction in dead load. 90011 90004 In the present chapter after the discussion about the lightweight concrete and its properties, we will study about the compressive strength of LWC and the methods for evaluation and prediction of compressive strength of LWC.Further a case study of LWC made of LWA will be conducted and presented for a better understanding of the properties of LWC. In the end the conclusion of the chapter will be drawn. 90011 90002 2. Background of lightweight concrete 90003 90004 Concrete is a relatively heavy building material; therefore many experiments have been conducted throughout the twentieth century to decrease its weight without impairing other properties. During the 1920s and 1930s, many different types of lightweight concrete were developed, e.g., Durisol, Siporex, Argex, and Ytong. Probably the most famous and first type of autoclaved gas concrete was Ytong. It was invented by the Swedish architect, Johan Axel Eriksson, assistant professor at the Royal Institute of Technology in Stockholm. In the early 1920s, Eriksson experimented with different samples of gas concrete and put the mixtures in an autoclave to speed up the curing process. In November 1929 року, the industrial production of Ytong blocks began. The name combines the y of Yxhult, the town where the first Swedish factory was located, and the end of betong, the Swedish word for concrete.The material was very popular in Sweden from 1935 onward, with a true breakthrough immediately after World War II, when it became one of the most important building materials in the country. Also, the manufacturing process was exported to other countries such as Norway, Germany, the UK, Spain, Poland, Israel, Canada, Belgium, and even Japan. The autoclaved gas concrete Siporex was developed in Sweden in 1935. The LWAC, Argex, was first produced in Denmark in 1939 under the international brand name Leca.Starting with an annual production in Copenhagen of 20,000 m 90005 3 90006, the total production throughout Europe had increased by тисячі дев’ятсот сімдесят дві to nearly 6 million m 90005 3 90006 per year (adopted from postwar building materials «postwarbuildingmaterials.be»). 90011 90004 The later type of LWC which is called LWAC is one of the most popular one among them and from that time until today has been the subject of many research works around the word. Even today there are many ongoing extensive research programs on SLWC and NSLWC made of LWA.In the present chapter, we focus on LWAC, and for the case study, we will discuss a part of the ongoing research of the author on LWAC [1]. Categorized examples of the research works conducted recently have been discussed below: 90011 90012 2.1 LWC including recycled lightweight aggregate 90013 90004 In 2013, a research was conducted on producing concrete containing recycled aggregates obtained from crushed structural and nonstructural lightweight concrete [2]. The mechanical properties of this concrete were investigated.Concrete compositions made of recycled lightweight concrete aggregates (RLCA) were measured for their compressive strength, modulus of elasticity, tensile strength, and abrasion resistance. The influence of the properties of the aggregates on concrete properties were discussed including concrete density, compressive strength, structural efficiency, splitting tensile strength, modulus of elasticity, and abrasion resistance. This research proved that it is possible to produce structural recycled lightweight concrete from crushed, structural, and nonstructural LWC with densities below 2000 kg / m 90005 3 90006.Improvements in mechanical properties can be seen when the LWA is replaced with RLCA. The study concluded that recycled lightweight aggregate is a potential alternative to conventional LWC. 90011 90012 2.2 LWC including expanded clay aggregates 90013 90004 In 2015 року, other researchers studied the properties of LWC consisting of cinder and light expanded clay aggregates (LECA) [3]. By replacing coarse aggregate with blended lightweight aggregates such as cinder and LECA, there was a reduction in weight and, respectively, a decrease in compressive strength, but they were able to use cinder and LECA as a replacement for normal coarse aggregate to reduce the cost , while the compressive strengths were close to the strengths of NWC.The average compressive strength for samples that included the abovementioned LWA was 39.2 N / mm 90005 2 90006, while the average compressive strength for NWC was 43.4 N / mm 90005 2 90006. The density of the LWC varied from 1800 to 1950 kg / mm 90005 3 90006 and the density for the NWC was 2637 kg / m 90005 3 90006. The slump from the fresh concrete mix and the average compressive and tensile strength of the hardened concrete were analyzed in the research. 90011 90012 2.3 LWC including foam glass aggregates 90013 90004 Similar research presented on waste materials showcased that waste materials can be reused as construction materials, in 2016 [4].Foam glass and high-impact polystyrene (HIPS) are materials they collected through the processing of waste materials. The glass foam is found from a glass cutlet, and the polystyrene is collected from butadiene modified rubber. They investigated the compressive and flexural strength, water absorption, and bulk density of the proposed concrete mixtures. LWC with foamed glass aggregates was affected by the amount of aggregate. Larger amounts of aggregate cause a decrease in compressive and bending strength and an increase in absorption.The addition of HIPS improved the compressive strength; however, it did not have a significant influence on water absorption. In 2017, Kurpinska and Ferenc studied on the physical properties of lightweight cement composites consisting of granulated ash aggregate (GAA) and granulated expanded glass aggregate (GEGA) [5]. This study showcased the significant impact of grain type and size on the physical properties of lightweight concrete. After the mechanical properties of 15 different mixtures were calculated and measured, they utilized a finite element modeling program to study the possibility of applying this type of LWC in structural elements, extenders, and insulation material.90011 90012 2.4 LWC including expanded glass aggregates 90013 90004 In 2017, the material properties and effects of crushed and expanded waste glass aggregates on LWC properties were evaluated [6]. In this study, an image-based approach is used to extract the characterization of the materials. Pore measurement and pore structures of each material type were evaluated using a microscope, 3D, and X-ray micro-computed tomography. Thermal conductivity for the material was measured. There results showed that crushed and expanded waste glass aggregates are supported as alternatives for lightweight aggregates.LWC with a density less than 2000 kg / m 90005 3 90006, including crushed waste aggregate, have shown to have a compressive strength over 38 MPa. This was considered as effective lightweight concrete, and it satisfied the desired mechanical properties. 90011 90012 2.5 LWC including expanded glass aggregates and expanded clay aggregates 90013 90004 An experimental investigation on the compressive strength and durability of LWC with fine expanded glass (FEG) and expanded clay aggregates (ECA) using different micro-fillers including ground quartz sand and silica fume was conducted in 2018 [7].Based on their research, ECA is one of the most popular aggregates for SLWC, and using this aggregate is important for sustainable development in the construction industry. The relationships between compressive strength and density of concrete mixtures with different proportions of LWA were explored. The effects of fine LWA on density and compressive strength of LWAC were also analyzed. They could reach to compressive strengths of 39.5-101 MPa for the mixtures containing EGA and 43.8-109 MPa for mixtures containing ECA.The density of the mixtures containing EGA and ECA are 1458-2278 and 1588-2302 kg / m 90005 3 90006, respectively. Different compressive strength-density relationships were obtained for LWC containing EGA and LWC containing ECA even though the compositions had the same amount of cement, water to cement ratio, micro filler, and total volume of LWA. While understanding the basic mechanical properties (density and compressive strength) of concrete containing LWA such as ECA and EGA was the main goal of this study, it was concluded that the application of expanded glass aggregate (EGA) in concrete is still in its early stages .90011 90004 As in the present book, compressive strength of concrete is the main subject of discussion; later in this chapter, we will discuss a case study on compressive strength of a specific type of LWC containing EGA implementing a NDT method in addition to the conventional compression test. Therefore in the next section, we will briefly talk about the usage of NDT in the evaluation of compressive strength and properties of concrete. 90011 90002 3. Nondestructive testing methods 90003 90004 Nondestructive testing (NDT) methods are widely used in the investigation of the mechanical properties and integrity of concrete structures.As seen in Table 1, provided by AASHTO [8], the following techniques are used for detecting defects in concrete structures for field use. In the present study, ultrasonic pulse velocity (UPV) method is used to evaluate the properties of LWC. Ultrasonic techniques measure the velocity of a pulse, generated from a piezoelectric transducer in concrete, and this measurement assesses the mechanical properties of a concrete. Based on research and correlations, the pulse velocity relates items such as compressive strength or corrosion [1].As seen in Table 1, UPV detects corrosion in reinforcement; however, it is not studied in this report. 90011 90012 3.1 Ultrasonic pulse velocity (UPV) 90013 90004 AASHTO states that the accurate measurement of the concrete’s strength depends on several factors and is best determined experimentally [8]. In the present work in addition to the conventional compression test, UPV is utilized to explore the properties of concrete. In general UPV tests are used to distinguish the material and integrity of concrete sample being tested.This technique enhances quality control and detection of defects. In the field, UPV verifies concrete uniformity, detects internal imperfections and finds the imperfections ‘depth, estimates the deformation moduli and compressive strength, and monitors characteristic variations in concrete throughout time [9]. From observations, certain factors influence UPV. The theory for elasticity for homogeneous and isotropic materials states that the pulse velocity of compressional waves (P-waves) is indirectly proportional to the square root of the dynamic modulus of elasticity, Ed, and inversely proportional to the square root of its density, 90087 ρ 90088 [10].The aggregate type used in a mixture has a significant influence on the elastic modulus; therefore for our current LWA, a significant change in the pulse velocity is expected. To differentiate results, correlations need to be analytically determined. As an example an expression for the modulus of elasticity of concrete and its relation between the compressive strength (fc), the oven-dried density, and the Ec itself is suggested by EN 1992-1-1, Eurocode 2 [11]. This relationship suggests that UPV and fc are not unique and are affected by factors such as the type and size of aggregate, physical properties of the cement paste, curing conditions, mixture composition, concrete age, voids / cracks and moisture content [12].Factors influencing the UPV method are presented in Table 2 [13]. Constituents of the concrete and its moisture content, age, and voids / cracks impact UPV significantly. Previous works have shown that a correlation between the compressive strength in concrete and the ultrasonic pulse velocity must be determined for each particular concrete mix [13, 14]. Finding a general correlation between fc and UPV will be an enhancement for inspection and assessment of structures made of LWC. 90011 90090 90091 90091 90091 90091 90091 90091 90091 90098 90099 90100 The capability of defect detection 90101 90102 90099 90104 Method based on 90101 90104 Cracking 90101 90104 Scaling 90101 90104 Corrosion 90101 90104 Wear and abrasion 90101 90104 Chemical attack 90101 90104 Voids in grout 90101 90102 90119 90120 90099 90122 Strength 90123 90122 N 90123 90122 N 90123 90122 P 90123 90122 N 90123 90122 P 90123 90122 N 90123 90102 90099 90122 Sonic 90123 90122 F 90123 90122 N 90123 90122 Gb 90123 90122 N 90123 90122 N 90123 90122 N 90123 90102 90099 90122 Ultrasonic 90123 90122 G 90123 90122 N 90123 90122 F 90123 90122 N 90123 90122 P 90123 90122 N 90123 90102 90099 90122 Magnetic 90123 90122 N 90123 90122 N 90123 90122 F 90123 90122 N 90123 90122 N 90123 90122 N 90123 90102 90099 90122 Electrical 90123 90122 N 90123 90122 N 90123 90122 G 90123 90122 N 90123 90122 N 90123 90122 N 90123 90102 90099 90122 Nuclear 9012 3 90122 N 90123 90122 N 90123 90122 F 90123 90122 N 90123 90122 N 90123 90122 N 90123 90102 90099 90122 Thermography 90123 90122 N 90123 90122 Gb 90123 90122 Gc 90123 90122 N 90123 90122 N 90123 90122 N 90123 90102 90099 90122 Radar 90123 90122 N 90123 90122 Gb 90123 90122 Gc 90123 90122 N 90123 90122 N 90123 90122 N 90123 90102 90099 90122 Radiography 90123 90122 F 90123 90122 N 90123 90122 F 90123 90122 N 90123 90122 N 90123 90122 F 90123 90102 90265 90266 90012 Table 1.90013 90004 Capability of investigating techniques for detecting defects in concrete structures in field use [8]. 90011 90004 G = good; F = fair; P = poor; N = not suitable; Gb = beneath bituminous surfacing; Gc = detects delamination. 90011 90090 90091 90091 90091 90091 90120 90099 90280 Constituents of concrete 90123 90282 Aggregate 90123 90122 Size 90123 90122 Average influence 90123 90102 90099 90122 Type 90123 90122 High influence 90123 90102 90099 90282 Cement 90123 90122 Percentage 90123 90122 Moderate influence 90123 90102 90099 90122 Type of cement 90123 90122 Moderate influence 90123 90102 90099 90282 Other constituents 90123 90122 Fly ash content 90123 90122 Average influence 90123 90102 90099 90122 Water / cement ratio 90123 90122 High influence 90123 90102 90099 90324 Humidity degree / moisture content 90123 90122 Average influence 90123 90102 90099 90330 Other factors 90123 90122 Reinforcements 90123 90122 Moderate influence 90123 90102 90099 90122 Age of concrete 90123 90122 Moderate influence 90123 90102 90099 90122 Voids, crack 90123 90122 High influence 90123 90102 90265 90266 90012 Table 2.90013 90004 Influencing factors for UPV method. 90011 90004 Therefore based on the previous studies, it is recommended that for each type of LWA used in LWC, the researchers conduct an experimental program to drive a brand new relation between UPV and compressive strength of concrete, which is not the focus of the present chapter. Hence in the present chapter, we have presented some of the most recent proposed equations, relating UPV to compressive strength of LWC, and presented some of the available equations relating UPV to compressive strength of LWC and NWC for those interested to compare the configurations of the equations and to initial their research for the specific types of LWA of interest.90011 90012 3.2 Utilizing UPV to find the compressive strength 90013 90004 During the last decades, many researchers presented different methods for the evaluation of compressive strength for LWA concrete versus UPV. The LWA in those studies consists of different types of natural or man-made LWA such as recycled lightweight concrete aggregates (RLCA), light expanded clay aggregate (LECA), high-impact polystyrene (HIPs), granulated ash aggregate (GAA), granulated expanded glass aggregate (GEGA), foam expanded glass aggregate (FEG), expanded clay aggregate (ECA), and expanded glass aggregate (EGA).In the literature several factors that influence the relation between compressive strength and UPV were examined. Most important analyzed factors included the cement type and content, amount of water, type of admixtures, initial wetting conditions, type and volume of aggregate, and the partial replacement of normal weight coarse and fine aggregates by LWA. As a result, simplified expression was proposed to estimate the compressive strength of different types of LWAC and its composition. The dependence of UPV and the modulus of elasticity were also explored in many of works [13].They presented the expression below for a wide range of SLWC with compressive strength varying from 20 to 80 MPa. UPV and density are measured in meters per second and kg / m 90005 3 90006. From the regression analysis, Kupvcan be a constant equal to 54.6, 54.3, 0.86, etc. and is a correlation coefficient. Values of UPV and strength measurements were performed on cubed concrete specimen in their study: 90011 90004 fc = UPVKupv * p0.523E1 90011 90004 where fc is the compressive strength of concrete (MPa), UPV is the ultrasonic pulse velocity (m / s) , KUPV is a constant representing the correlation coefficient, and ρ is the dry density of specimen (kg / m 90005 3 90006).In the research presented elsewhere [9], equations for LWC containing fibers were proposed to estimate the concrete compressive strength from respective UPV values. The equations presented below are the compressive strength of concrete at days 7 and 28, respectively: 90011 90004 fc = 1.269exp.0.841v7daysE2 90011 90004 fc = 0.888exp.0.88v28daysE3 90011 90004 where f 90374 c 90375 is the compressive strength of concrete ( MPa) and v is the pulse velocity (m / s). Other types of equations were presented in 2015 [10], which contributed the coarse aggregate content as a ruling factor in the relationships presented.In the developed equations, the fc was represented for a compressive cube strength measured in MPa. The variable, v, is UPV and it was measured in kilometers per second. The expressions are presented below for different coarse aggregate (CA) contents: 90011 90004 For CA (coarse aggregate content) = 1000 kg / m 90005 3 90006 90011 90004 fc = 8.88exp.0.42vE4 90011 90004 For CA = 1200 kg / m 90005 3 90006 90011 90004 fc = 0.06exp.1.6vE5 90011 90004 For CA = 1300 kg / m 90005 3 90006 90011 90004 fc = 1.03exp.0.87vE6 90011 90004 For CA = 1400 kg / m 90005 3 90006 90011 90004 fc = 1.39exp.0.78vE7 90011 90004 Table 3 showcases some of the different equations generated by researchers in the last decades to predict compressive strength of concrete, fc , in terms of UPV [15]. 90011 90090 90091 90091 90091 90098 90099 90409 No. 90101 90409 Proposed equations 90101 90409 Author, year 90101 90102 90119 90120 90099 90419 1 90123 90419 fc = 1.2 × 10-5 × UPV1.7447 90123 90419 Kheder, 1999 90123 90102 90099 90419 2 90123 90419 fc = 36.75 × UPV-129.077 90123 90419 Qasrawri, 2000 90123 90102 90099 90419 3 90123 90419 fc = 21.5 × UPV62 90123 90419 AIJ, 1983 90123 90102 90099 90419 4 90123 90419 fc = 0.6401 × UPV2.5654 90123 90419 Ali-benyahia 2017 90123 90102 90099 90419 5 90123 90419 fc = 0.0316exp1.3 * UPV 90123 90419 Atici, 2011 90123 90102 90099 90419 6 90123 90419 fc = 0.5208 × UVP5 90123 90419 Khan, 2012 90123 90102 90099 90419 7 90123 90419 fc = 50.163 × UPV-178.2 90123 90419 Kim, 2012 90123 90102 90099 90419 8 90123 90419 fc = 0.0136 × UPV-21.34 90123 90419 Najim, 2017 90123 90102 90099 90419 9 90123 90419 fc = 38.05 × UPV2-316.76 × UPV + 681.62 90123 90419 Rashid, 2017 90123 90102 90099 90419 10 90123 90419 fc = 0.854exp1.28882 × UPV 90123 90419 Trtniket et al., 2009 90123 90102 90265 90266 90012 Table 3. 90013 90004 Proposed equations for finding the compressive strength of concrete using UPV [15]. 90011 90002 4. Experimental program 90003 90004 In this section an experimental program was developed and conducted by the author and his graduate student to investigate the compressive strength of LWAC containing a specific type of expanded glass aggregate (EGA), to better showcase the properties of LWAC [1].90011 90012 4.1 Lightweight and normal weight aggregates 90013 90510 4.1.1 NWA 90511 90004 Tables 4 and 5 consist of the sieve analyses for the normal weight gravel and coarse sand, respectively, which were measured according to ASTM C136-01 [16]. The NWA’s absorption capacity, specific gravity, and moisture content are evaluated according to ASTM C 127-01 [17] and ASTM C 566 [18]. Table 6 includes aggregate properties such as specific gravity, absorption capacity, moisture content, and fineness modulus (FM).In Figures 1 and 2, the individual aggregates are shown. The maximum normal weight aggregate size was 9.53 mm (3/8 «). 90011 90090 90091 90091 90091 90091 90091 90098 90099 90104 Sieve analysis 90101 90524 Sample size (SS): 2.27 kg 90101 90102 90099 90104 Sieve size 90101 90409 Weight retained (kg.) 90101 90409% retained 90101 90409% coarser 90101 90409% finer 90101 90102 90119 90120 90099 90122 19 mm 90123 90419 0 90123 90419 0 90123 90419 0 90123 90419 0 90123 90102 90099 90122 13 mm 90123 90419 0 90123 90419 0 90123 90419 0 90123 90419 0 90123 90102 90099 90122 9 mm 90123 90419 0.047 90123 90419 2.073 90123 90419 2.073 90123 90419 97.93 90123 90102 90099 90122 No. 4 90123 90419 1.6 90123 90419 70.49 90123 90419 72.56 90123 90419 27.4 90123 90102 90099 90122 No. 8 90123 90419 0.5 90123 90419 21.622 90123 90419 94.18 90123 90419 5.82 90123 90102 90099 90122 No. 10 90123 90419 0.021 90123 90419 0.92 90123 90419 95.1 90123 90419 4.9 90123 90102 90099 90122 Passing 90123 90419 0.112 90123 90419 4.9023 90123 90419 99.99 90123 90419 0.001 90123 90102 90099 90122 Sum of SS 90123 90419 2.27 90123 90630 90630 90630 90102 90265 90266 90012 Table 4. 90013 90004 Sieve analysis for normal weight gravel mix. 90011 90090 90091 90091 90091 90091 90098 90099 90104 Sieve analysis 90101 90649 Sample size (SS) 1000 g 90101 90102 90099 90104 Sieve no. 90101 90409 Weight retained (g) 90101 90409% retained 90101 90409% finer 90101 90102 90119 90120 90099 90122 8 90123 90419 5 90123 90419 0.5 90123 90419 99.5 90123 90102 90099 90122 10 90123 90419 49.5 90123 90419 5.45 90123 90419 94.55 90123 90102 90099 90122 16 90123 90419 283 90123 90419 33.75 90123 90419 66.25 90123 90102 90099 90122 20 90123 90419 286.5 90123 90419 62.4 90123 90419 37.6 90123 90102 90099 90122 30 90123 90419 364.5 90123 90419 98.85 90123 90419 1.15 90123 90102 90099 90122 40 90123 90419 11 90123 90419 99.95 90123 90419 0.05 90123 90102 90099 90122 pan 90123 90419 0.5 90123 90419 100 90123 90419 0 90123 90102 90099 90122 Sum of SS 90123 90419 1000 90123 90630 90630 90102 90265 90266 90012 Table 5.90013 90004 Sieve analysis for normal weight coarse sand. 90011 90090 90091 90091 90091 90091 90091 90091 90098 90099 90104 Property 90101 90759 Normal weight aggregates 90101 90759 Lightweight aggregates 90101 90763 90102 90099 90763 90409 Gravel mix (GM) 90101 90409 Coarse sand (CS) 90101 90409 Poraver (0.25-0.5 mm) 90101 90409 Poraver (1-2 mm) 90101 90409 Poraver (2-4 mm) 90101 90102 90119 90120 90099 90122 Specific gravity 90782 (ton / m 90005 3 90006) 90123 90419 2.4 90123 90419 2.75 90123 90419 0.55 90123 90419 0.36 90123 90419 0.32 90123 90102 90099 90122 Absorption capacity (%) 90123 90419 2.3 90123 90419 1.87 90123 90419 19 90123 90419 9 90123 90419 9 90123 90102 90099 90122 Moisture content (%) 90123 90419 4.5 90123 90419 6.4 90123 90419 0.5 90123 90419 0.5 90123 90419 0.5 90123 90102 90099 90122 Fineness modulus 90123 90419 3.64 90123 90419 2.9 90123 90419 1.92 90123 90419 3.81 90123 90419 4.7 90123 90102 90265 90266 90510 Figure 1.90511 90004 NWA, from left to right, normal weight gravel mix, and coarse sand. 90011 90510 Figure 2. 90511 90004 LWA, from left to right, Poraver 0.25-0.5, 1-2, and 2-4 mm. 90011 90510 4.1.2 LWA 90511 90004 The LWA used in this study is Poraver, [19] which is an expanded glass granule. The material is pressure resistant, durable and dimensionally stable, 100% mineral, spherical in shape, ecological, and not hazardous to health. According to the Poraver technical data sheet, the aggregate is lightweight according to ASTM C330, C331, and C332 and DIN EN 13055-1.Mineral casting and polymer concrete, plaster and dry mortar, lightweight panels, automotive, 3D printing, and other additional practices are practical applications of this material. The aggregate sizes and properties of the LWA are presented in Table 6. The Poraver technical data sheet provided the absorption capacity and moisture content on delivery and specific gravity for the LWA [19]. 90011 90012 4.2 Mix proportion 90013 90004 The experimental work includes various concrete mixes consisting of lightweight EGA, and these concrete mixes were created with partial or total replacement of NWA with LWA.The ACI 211.2-98 guide for LWC was followed for mix designing [20]. In this study, the control of the cement content is intended to properly understand the compressive strength for different concrete mixes without being influenced by the cementitious material effects. Many combinations of aggregates were tested and the optimum aggregate sizes to increase the compressive strength were selected. The mix proportions of the LWAC mixes are found in Table 7. The cement type used was Ordinary Portland cement CEM I 42.5 N. In the presented tables, Poraver size 0.25-0.5 is referred to as LWA (fine), while the LWA sizes, 1-2 and 2-4 mm, are considered as LWA (coarse). 90011 90090 90091 90091 90091 90091 90091 90091 90091 90091 90091 90098 90099 90869 Mix label 90101 90869 w / c 90101 90869 Cement (g) 90101 90869 Water (g) 90101 90869 GM (g) 90101 90869 CS (g) 90101 90104 LWA 90101 90409 LWA 90101 90409 LWA 90101 90102 90099 90409 (0.25-0.5 mm) (g) 90101 90409 (1-2 mm) (g) 90101 90409 (2-4 mm) (g) 90101 90102 90119 90120 90099 90122 1 90123 90419 0.29 90123 90419 685 90123 90419 199 90123 90419 304 90123 90419 2545 90123 90419 — 90123 90419 — 90123 90419 154 90123 90102 90099 90122 2 90123 90419 1.88 90123 90419 576 90123 90419 1084 90123 90419 658 90123 90419 1275 90123 90419 — 90123 90419 — 90123 90419 2631 90123 90102 90099 90122 3 90123 90419 0.31 90123 90419 576 90123 90419 177 90123 90419 3284 90123 90419 508 90123 90419 — 90123 90419 — 90123 90419 767 90123 90102 90099 90122 4 90123 90419 0.47 90123 90419 576 90123 90419 272 90123 90419 2631 90123 90419 1021 90123 90419 — 90123 90419 658 90123 90419 254 90123 90102 90099 90122 5 90123 90419 0.47 90123 90419 576 90123 90419 272 90123 90419 658 90123 90419 1021 90123 90419 254 90123 90419 658 90123 90419 — 90123 90102 90099 90122 6 90123 90419 0.7 90123 90419 576 90123 90419 404 90123 90419 1973 90123 90419 767 90123 90419 508 90123 90419 329 90123 90419 — 90123 90102 90099 90122 7 90123 90419 0.7 90123 90419 576 90123 90419 404 90123 90419 658 90123 90419 1021 90123 90419 254 90123 90419 658 90123 90419 — 90123 90102 90099 90122 8 90123 90419 0.47 90123 90419 576 90123 90419 272 90123 90419 3284 90123 90419 1021 90123 90419 181 90123 90419 — 90123 90419 — 90123 90102 90099 90122 9 90123 90419 0.47 90123 90419 576 90123 90419 272 90123 90419 3284 90123 90419 767 90123 90419 167 90123 90419 — 90123 90419 — 90123 90102 90099 90122 10 90123 90419 0.47 90123 90419 576 90123 90419 272 90123 90419 3284 90123 90419 508 90123 90419 253 90123 90419 — 90123 90419 — 90123 90102 90099 90122 11 90123 90419 0.47 90123 90419 576 90123 90419 272 90123 90419 3284 90123 90419 254 90123 90419 340 90123 90419 — 90123 90419 — 90123 90102 90099 90122 12 90123 90419 0.47 90123 90419 576 90123 90419 272 90123 90419 3284 90123 90419 340 90123 90419 421 90123 90419 — 90123 90419 — 90123 90102 90265 90266 90012 4.3 Test methods 90013 90004 ASTM C 192 was used as the guide for making and curing concrete test specimens in the laboratory [21]. The specimens were demolded after 24 hours and submerged underwater until a day before testing. UPV (Figure 3) and the axial compression machine (ACM) in Figure 4 were used to determine the compressive strength of concrete at days 7 and 28. 90011 90510 Figure 3. 90511 90004 Ultrasonic pulse velocity instrument. 90011 90510 Figure 4. 90511 90004 Compression test machine.90011 90012 4.4 Results and discussion 90013 90004 In general it was observed that with increase in the amount of LWA in the concrete mixture, the compressive strength and UPV of LWC decrease, which was expected. In Figure 5, the relationship between UPV and fc (measured with ACM), at the age of 7 and 28 days for the LWC is presented. It can be observed that the results are scattered and more tests and specimens and concrete mixtures will be required to be able to establish a solid relationship between UPV and compressive strength for this type of LWAC.The best empirical relation obtained from curve fitting analyses for this study can be written as below: 90011 90510 Figure 5. 90511 90004 UPV versus fc for LWC tested at days 7 and 28. 90011 90004 fc = 0.8exp0.335vE8 90011 90004 where f 90374 c 90375 is the compressive strength of concrete (MPa) and v is the pulse velocity (km / s). 90011 90004 To be able to investigate the effect of the LWA content in the mix proportions, we have selected the mixes with constant w / c ratio of 0.47 and gradually replaced the NWA with LWA (Table 8).Figure 6 depicts the relation between fc and replacement ratio (RR) or LWA content for these individual mix proportions. From this figure, it can be observed that for the LWC in this study, as the LWA content increases, fc decreases. Figure 7 shows the relation between UPV and RR or LWA content for these individual mix proportions. From this figure, it can be observed that for the LWC in this study, as the LWA content increases, UPV decreases as expected. 90011 90090 90091 90091 90091 90091 90091 90091 90091 90091 90091 90098 90099 90104 Mixes 90101 90409 RR 90101 90409 w / c 90101 90409 Cement (g) 90101 90409 Water (g) 90101 90409 GM (g) 90101 90409 CS (g) 90101 90409 LWA , coarse (g) 90101 90409 LWA, fine (g) 90101 90102 90119 90120 90099 90122 12a 90123 90419 0 90123 90419 0.47 90123 90419 576 90123 90419 272 90123 90419 3284 90123 90419 1275 90123 90419 — 90123 90419 0 90123 90102 90099 90122 12b 90123 90419 20 90123 90419 0.47 90123 90419 576 90123 90419 272 90123 90419 3284 90123 90419 1021 90123 90419 — 90123 90419 254 90123 90102 90099 90122 12c 90123 90419 40 90123 90419 0.47 90123 90419 576 90123 90419 272 90123 90419 3284 90123 90419 767 90123 90419 — 90123 90419 508 90123 90102 90099 90122 12d 90123 90419 60 90123 90419 0.47 90123 90419 576 90123 90419 272 90123 90419 3284 90123 90419 508 90123 90419 — 90123 90419 767 90123 90102 90099 90122 12e 90123 90419 80 90123 90419 0.47 90123 90419 576 90123 90419 272 90123 90419 3284 90123 90419 254 90123 90419 — 90123 90419 1021 90123 90102 90099 90122 12f 90123 90419 100 90123 90419 0.47 90123 90419 576 90123 90419 272 90123 90419 3284 90123 90419 0 90123 90419 — 90123 90419 1275 90123 90102 90265 90266 90012 Table 8. 90013 90004 Comparison between different LWA contents. 90011 90510 Figure 6. 90511 90004 fc versus RR for LWC. 90011 90510 Figure 7. 90511 90004 UPV versus RR for LWC. 90011 90004 The relationship between UPV, fc (compressive strength), and dry density for the mix proportions in Table 8 is presented in Figures 8 and 9.It can be observed that for the LWC in this study, as the dry density increases, UPV and fc also increase, but the results are scattered when working with LWC. To be able to compare these results from those of NWC, mixes of NWC with similar compositions but without any LWA were produced, and results were presented in Figures 10 and 11. It is observed that the result for the relationship between UPV, fc and, dry density for LWC is more scattered than similar test result for NWC. 90011 90510 Figure 8.90511 90004 fc versus dry density for LWC. 90011 90510 Figure 9. 90511 90004 UPV versus dry density for LWC. 90011 90510 Figure 10. 90511 90004 fc versus dry density for NWCUPV versus dry densit 90011.