Технология приготовления асфальтобетонной смеси и контроль. ГОСТ 9128-97
— Для приготовления а/б смеси необходимо предварительно разработать в лабораторных условиях его состав (количества щебня, песка, минерального порошка и битума).
— Для обеспечения точного состава а/б смеси необходимо предварительная сортировка этих материалов (сортировочные устройства устанавливаются до холодного вертикального элеватора).
— Количество материалов, отпускаемых со складов завода в смеситель, должно соответствовать составу смеси, предложенного лабораторией.
— Для восстановления кровель применяется а/б смесь, используемая для всех типов дорог:
Тип А
Марки I,
где содержание щебня должно составлять 50-60% (гос. стандарт 9128-97)
— Для приготовления смеси в смеситель в первую очередь подается щебень, песок, минеральный порошок; после получения смеси подается соответствующее количество битума для последующего смешения.
— Температура щебня и песка в процессе смешивания должна составлять 165-185 С°
— Минеральный порошок подается в холодном виде.
— Температура битума должна составлять 140-160 С°
— После выпуска из смесителя температура смеси должна составлять 140-160 гр. С.
— Состав щебня должен быть таким, чтобы его зерна проходили:
через 20-мм сито – 90-100%,
через 15-мм сито – 75-100%.
— Допустимое отклонение в количестве материалов в процессе приготовления а/б смесей должно быть не более:
щебня – 3%,
песка – 3%,
битума – 1,5%,
мин. порошка – 1,5%.
— температура битума проверяется каждые 2 часа.
— Контроль за остальными компонентами смеси ведется непрерывно.
— Температура готовой смеси проверятся при каждой погрузке в самосвал.
— Качество а/б смеси проверяется в каждую смену в лабораторных условиях.
— Время доставки а/б смеси не должно превышать 1, 5 часа при температуре воздуха свыше 10 С°.
— Работа механизмов предварительной сортировки и устройств по взвешиванию компонентов проверяются каждые 2 недели, а при возникновении подозрений в неточности – немедленно.
— При визуальном осмотре а/б смесь должна выглядеть однородной, рыхлой, не должна прилипать к кузову автомобиля.
В случае возникновения сомнений она должна быть проверена в лабораторных условиях.
— Состав зерен а/б смеси проверяется раз в 3 смены, а содержание щебня – каждую смену, ускоренным методом.
— Прочность используемых в а/б смесях (тип А) щебня не должна быть ниже 1000.
— В щебне (тип А) допустимо наличие не более 15% плоских и игольчатых зерен.
— Содержание глинистых или пылевых частиц в щебне и песке не должно превышать 1%.
— Пористость минерального остова не должна превышать 23%.
— А/б смесь должна соответствовать следующим требованиям:
Наименование показателей | Климатические зоны | ||
l | ll, lll | lV, V | |
Водонасыщенность в % по объему Тип А Б и Г В и Д Остаточная пористость по % объема | 2. 1.5-3.0 1.0-2.5 2.0-3.5 |
2.0-5.0 1.5-4.0 1.0-4.5 2.0-5.0 |
3.0-7.0 2.5-6.0 2.5-6.0 3.0-7.0 |
Состав зерен а/б смесей типа А марки I должен составлять:
Тип смеси | Состав зерен в % меньше мм | |||||||||
20 | 15 | 10 | 5 | 2.5 | 1.25 | 0.63 | 0.315 | 0.14 | 0.071 | |
А | 90-100 | 75-100 | 62-100 | 40-50 | 28-38 | 20-28 | 14-20 | 10-15 | 6-12 | 4-10 |
— Нагретый до рабочего состояния битум необходимо использовать в течение 5 часов.
— После готовности а/б смеси его необходимо загрузить в автомашины или в складское хранилище
— В зависимости от консистенции битума, используемые материалы в процессе приготовления а/б смеси должны иметь следующую температуру:
Вид смеси | Марка битума | Температура в С° | ||
Битум | Щебень и песок | А/б смесь | ||
горячий | БНД: 40/60 60/90 90/130 БН: 60/90, 90/130 | 130-150 | 165-185 | 140-160 |
Холодный | БНД: 130/200, 200/300, 130/200 БН: 200/300 | 110-130 | 145-165 | 120-140 |
АГ: 130/200 МГ: 130/200 | 80-100 | 115-135 | 90-110 |
— Для приготовления а/б смеси необходимо иметь необходимое количество щебня, песка, минерального порошка и битума.
— В ходе приготовления смеси необходимо произвести предварительное дозирование по объемам – в соответствии с зерновым составом, разработанным в лаборатории.
Влажный щебень и песок определенного зернового состава в установленных объемах поступает в сушильно-нагревочную печь. После печи поступает на сита двойной сортировки, а оттуда – в соответствующие бункеры.
Из этих бункеров щебень, песок и минеральный порошок в определенных дозах подаются в смеситель (битум подается отдельно).
— Цикл приготовления смеси считается завершенным, когда она поступает в машину по перевозке смеси или в заводское складское хранилище.
Асфальт
Асфальтобетонные смеси
Тип и марка асфальтобетонной смеси (асфальтобетона) |
---|
Для верхнего слоя покрытия |
Щебеночно-мастичная смесь ЩМА — 15, ЩМА — 20 (Габбро, ПБВ 60) |
Щебеночно-мастичная смесь ЩМА — 15, ЩМА — 20 (Габбро) |
Мелкозернистая смесь тип А М 1 (Габбро) |
Мелкозернистая смесь тип Б М 1, Б М 2(Габбро) |
Мелкозернистая смесь тип Б М 2 |
Мелкозернистая смесь тип В М 2 |
Песчаная смесь тип Г М 1, 2 |
Песчаная смесь тип Д М 2 с добавлением щебня фракции 5-20 мм до 10% |
Песчаная смесь тип Д М 2 |
Для нижнего слоя покрытия |
Мелкозернистая смесь пористая М 1, М 2 |
Крупнозернистая смесь плотная Б М 1 / Б М 2 |
Крупнозернистая смесь пористая М 1,2 (щебень фр.![]() |
ГОСТ 9128-97 Смеси асфальтобетонные дорожные, аэродромные и асфальтобетон.
Виды выпускаемых смесей:
1. КРУПНОЗЕРНИСТЫЕ – для нижних слоёв двухслойных асфальтобетонных покрытий.
2. МЕЛКОЗЕРНИСТЫЕ – для строительства магистральных федеральных дорог и улиц с высокой интенсивностью движения.
3. ПЕСЧАНЫЕ – для пешеходных дорожек и тротуаров, стоянок легковых автомобилей, торговых площадей.
4. СМЕСИ НА ПОЛИМЕРНО-БИТУМНОМ ВЯЖУЩЕМ – для увеличения долговечности покрытий.
5. СМЕСИ НА РЕЗИНО-БИТУМНОМ ВЯЖУЩЕМ(БИТРЭК).
6. СМЕСИ С МОДИФИКАТОРОМ УНИРЕМ.
7. РЕЗИНОАСФАЛЬТОБЕТОННЫЕ СМЕСИ – покрытия пониженной жёсткости, например для покрытия стадионов, беговых дорожек
8. ЦВЕТНЫЕ – мощение покрытий площадей у важных государственных, административных, культурно-просветительных учреждений, площадей парков и т.д.
9. ХОЛОДНЫЕ СКЛАДИРУЕМЫЕ СМЕСИ – для ямочного ремонта, транспортируются на любые расстояния в полиэтиленовых мешках.
10. ЛИТЫЕ – могут использоваться для работ в зимнее время и ямочного ремонта, разогреваются до высокой температуры, перевозятся в специальных машинах – кохерах.
11. ЩЕБЁНОЧНО-МАСТИЧНЫЕ – долговечные и трещиностойкие с повышенным содержанием щебня мелких фракций, особо прочные.
12. ЧЁРНЫЙ ЩЕБЕНЬ – для устройства оснований.
13. ТЁПЛЫЕ АСФАЛЬТОБЕТОННЫЕ СМЕСИ — для работы при пониженных температурах.
Характеристики асфальтобетонной смеси:
Тип I применяется для нового строительства и капитального ремонта.
— наибольший размер зерен до 15 мм, содержание щебня св. 45 до 55%;
— температура смеси при отгрузке 220-240˚С.
Тип II применяется для нового строительства и капитального ремонта.
— наибольший размер зерен до 20 мм, содержание щебня св. 35 до 50%;
Тип III применяется для нового строительства и капитального ремонта.
— наибольший размер зерен до 40 мм, содержание щебня св.
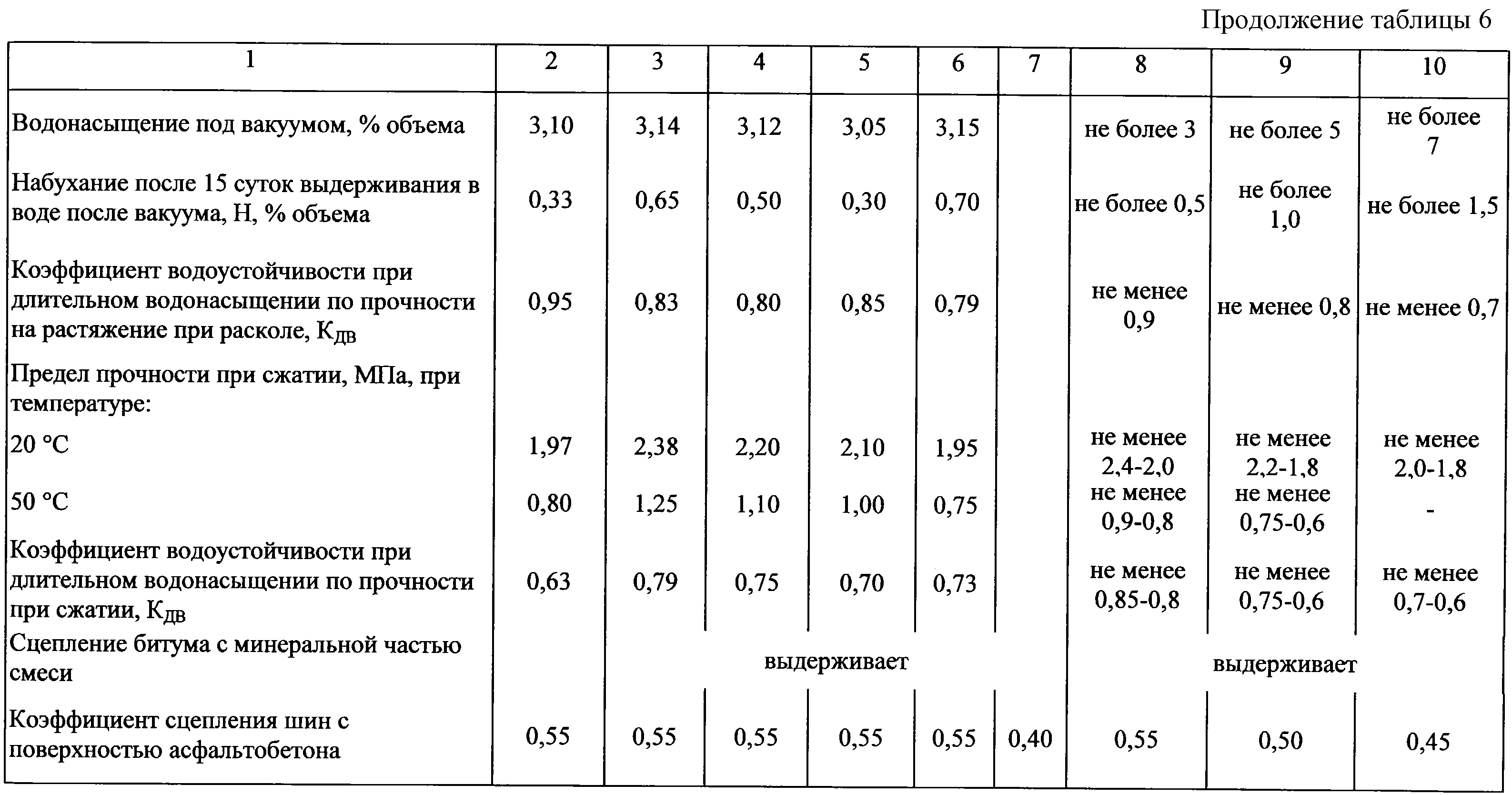
— температура смеси при отгрузке 200-230˚С.
Тип IV применяется для устройства тротуаров.
— наибольший размер зерен до 5 мм;
— температура смеси при отгрузке 165-210˚С.
Тип V применяется для текущего ремонта
— наибольший размер зерен до 20 мм и содержанием щебня св. 35 до 50%;
— температура смеси при отгрузке 180-220˚С.
Холодные асфальтобетонные смеси
Холодный асфальт в мешках Холодная смесь – это готовый материал для осуществления ямочного ремонта асфальтобетонных покрытий дорог, улиц, тротуаров, спортивных и стояночных площадок, дворовых территорий, а также заделки лунок после взятия кернов.
Горячий асфальт
Асфальтобетонная смесь тип А, марки I плотного асфальтобетона по ГОСТ 9128-2009
Применяется для устройства верхних слоев покрытий при новом строительстве и капитальном ремонте дорог I и II категорий, улиц с высокой интенсивностью движения автотранспорта.
Характеристики асфальтобетонной смеси и асфальтобетона:
- мелкозернистая асфальтобетонная смесь, с размером минеральных зёрен до 20мм;
- содержание щебня св.
50 до 60%;
- асфальтобетон плотный, с остаточной пористостью св. 2,5 — 5,0%;
- температура асфальтобетонной смеси при отгрузке от 145 до 155 ˚С.
Показатели физико-механических свойств асфальтобетона соответствуют требованиям ГОСТ 9128-2009.
Асфальтобетонная смесь тип Б, марки I плотного асфальтобетона по ГОСТ 9128-2009
Применяется для устройства верхних слоев покрытий при новом строительстве и капитальном ремонте дорог I и II категорий, улиц с высокой интенсивностью движения автотранспорта.
- мелкозернистая асфальтобетонная смесь, с размером минеральных зёрен до 20мм;
- содержание щебня св. 40 до 50%;
- асфальтобетон плотный, с остаточной пористостью св. 2,5 — 5,0%;
- температура асфальтобетонной смеси при отгрузке от 145 до 155 ˚С.
Показатели физико-механических свойств асфальтобетона соответствуют требованиям ГОСТ 9128-2009.
Асфальтобетонная смесь тип Г, марки I, плотного асфальтобетона по ГОСТ 9128-2009
Применяется для устройства верхних слоев покрытий при новом строительстве и капитальном ремонте дорог I и II категорий, улиц, проездов, площадок.
Характеристики асфальтобетонной смеси и асфальтобетона:
- песчаная асфальтобетонная смесь на дробленном песке (отсевах дробления), с размером минеральных зёрен до 5мм;
- асфальтобетон плотный, с остаточной пористостью св. 2,5 — 5,0%;
- температура асфальтобетонной смеси при отгрузке от 145 до 155 ˚С.
Показатели физико-механических свойств асфальтобетона соответствуют требованиям ГОСТ 9128-2009.
Асфальтобетонная смесь тип Д, марки II, плотного асфальтобетона по ГОСТ 9128-2009
Применяется для устройства верхних слоев покрытий при новом строительстве и капитальном ремонте дорог III категорий, пешеходных зон и тротуаров.
Характеристики смеси:
- песчаная асфальтобетонная смесь на природном песке, с размером минеральных зёрен до 5мм;
- асфальтобетон плотный, с остаточной пористостью св. 2,5 — 5,0%;
- температура асфальтобетонной смеси при отгрузке от 145 до 155 ˚С.
Показатели физико-механических свойств асфальтобетона соответствуют требованиям ГОСТ 9128-2009.
Асфальтобетонная смесь тип В, марки II плотного асфальтобетона по ГОСТ 9128-2009
Применяется для устройства верхних слоев покрытий при новом строительстве и капитальном ремонте дорог III категорий, улиц, проездов, площадок, пешеходных зон.
Характеристики асфальтобетонной смеси и асфальтобетона:
- мелкозернистая асфальтобетонная смесь, с размером минеральных зёрен до 20мм;
- содержание щебня св. 30 до 40%;
- асфальтобетон плотный, с остаточной пористостью св. 2,5 — 5,0%;
- температура смеси при отгрузке от 145 до 155˚С.
Показатели физико-механических свойств асфальтобетона соответствуют требованиям ГОСТ 9128-2009.
Асфальтобетонная смесь, марки I, пористого асфальтобетона по ГОСТ 9128-2009
Применяется для устройства нижних слоев покрытий и оснований при новом строительстве и капитальном ремонте дорог I и II категорий, улиц, проездов, площадок.
Характеристики асфальтобетонной смеси и асфальтобетона:
- крупнозернистая асфальтобетонная смесь, с размером минеральных зёрен до 40мм;
- содержание щебня св.
40 до 60%;
- асфальтобетон пористый, с остаточной пористостью св. 5,0 — 10,0%;
- температура асфальтобетонной смеси при отгрузке от 145 до 155 ˚С.
Показатели физико-механических свойств асфальтобетона соответствуют требованиям ГОСТ 9128-2009.
Щебеночно-мастичные асфальтобетонные смеси (ЩМА) по ГОСТ 31015-2002
Применяется для устройства верхних слоев покрытий при новом строительстве и капитальном ремонте дорог I и II категорий, улиц с высокой интенсивностью движения автотранспорта.
Характеристики асфальтобетонной смеси и асфальтобетона:
- ЩМА-15 с наибольшим размером зерен до 15 мм и содержанием щебня св. 65 до 75%;
- ЩМА-20 с наибольшим размером зерен до 20 мм и содержанием щебня св. 70 до 80%;
- асфальтобетон с остаточной пористостью св. 1,5 — 4,5%;
- температура смеси при отгрузке 155-170˚С.
Показатели физико-механических свойств асфальтобетона соответствуют требованиям ГОСТ 31015-2002.
Щебеночно-мастичные асфальтобетонные смеси по ГОСТ 31015-2002: ЩМА-15, ЩМА-20 с применением модификатора «УНИРЕМ» по ТУ 5718-001-78364424-05
Дробимость минеральной и асфальтобетонной смеси при лабораторном уплотнении секторным прессом Текст научной статьи по специальности «Технологии материалов»
УДК 691. 16:625.089.11
ДРОБИМОСТЬ МИНЕРАЛЬНОЙ И АСФАЛЬТОБЕТОННОЙ СМЕСИ ПРИ ЛАБОРАТОРНОМ УПЛОТНЕНИИ СЕКТОРНЫМ ПРЕССОМ В.П. Корюк, аспирант, ХНАДУ
Аннотация. Рассмотрено влияние методов лабораторного уплотнения на дробление щебня в асфальтобетонных смесях. Показано преимущество их уплотнения укаткой.
Ключевые слова: прессование, укатка, уплотнение, асфальтобетон, щебень, дробимость.
ПОДРІБНЮВАНІСТЬ МІНЕРАЛЬНОЇ Й АСФАЛЬТОБЕТОННОЇ СУМІШІ ПРИ ЛАБОРАТОРНОМУ УЩІЛЬНЕННІ СЕКТОРНИМ ПРЕСОМ В.П. Корюк, аспірант, ХНАДУАнотація. Розглянуто вплив методів лабораторного ущільнення на роздрібнення щебеню в асфальтобетонних сумішах. Показано перевагу їх ущільнення укоченням.
Ключові слова: пресування, укочення, ущільнення, асфальтобетон, щебінь, подрібнюваність.
BREAKABILITY OF MINERAL AND ASPHALT MIXES DURING LABORATORY COMPACTION BY SECTOR PRESS V. Koruk, postgraduate, KhNAHU
Abstract. The influence of laboratory compaction methods on the breakability of asphalt mixes is considered. The advantage of compaction by rolling is shown.
Введение
Процесс укатки асфальтобетона — завершающий и очень важный этап в формировании структуры искусственного монолитного материала, получаемого в результате уплотнения асфальтобетоновой смеси, приготовленной путем тщательного перемешивания при определенных технологических режимах, отдозированных в соответствии с расчетом минеральных составляющих и битума [1]. В результате вытеснения свободного битума в межзерновое пространство происходит сближение частиц и образуется плотная и прочная структура асфальтобетона [2, 3]. Недо-уплотненный асфальтобетон, как утверждается в [4, 5], начинает жизнь со множества дефектов, снижающих работоспособность покрытия из-за слабого сцепления частиц материала и большого объема пор. Под дей-
ствием природно-климатических факторов и эксплуатационных нагрузок частицы такого покрытия выкрашиваются, приводя со временем к образованию других дефектов [4, 5].
Анализ публикаций
В процессе укладки и уплотнения асфальтобетонных смесей существует возможность влиять на долговечность, регулируя их технологические параметры и режимы. Для обеспечения хорошего уплотнения рекомендуется начинать катку непосредственно за асфальтоукладчиком, при максимально высокой температуре смеси и низкой скорости [2]. При высокой температуре смесь имеет низкое сопротивление перемещению зерен в момент уплотнения, что снижает дробимость в покрытии [6]. Это соответствует главной цели уплотнения — предупреждению измене-
ния состава смеси и достижению проектной плотности смеси и асфальтобетона.
В работах [7, 8] показана существенная разница между показателями остаточной пористости объемного водонасыщения, плотности и прочности образцов, заформованных в лаборатории, и вырубок. Это вызывает необходимость разработки эффективного, адаптированного к производству лабораторного метода уплотнения асфальтобетонной смеси. С этой целью в мире используется несколько методов. В некоторых штатах США применяют уплотнение по Маршаллу, которое представляет собой трамбование асфальтобетонной смеси в цилиндрической обойме грузом с массой, зависящей от типа смеси, вида работ и количества ударов [9]. Недостаток такого уплотнения состоит в том, что процесс трамбования не соответствует работе дорожных катков, а устойчивость по Маршаллу не позволяет оценить прочность асфальтобетона на сдвиг и изгиб. В США и Европе применяют вращательный уплотнитель асфальтобетона, в большей степени моделирующий физику и механику деформирования смеси за счет вращения цилиндрической формы под углом 1° и одновременного приложения вертикального давления, равного
0,6 МПа [10].
В странах бывшего СНГ лабораторные образцы уплотняют статической нагрузкой 40 МПа или совмещением вибрирования и давления (20 МПа) в течение 3 минут в случае многощебенистых смесей [11, 12]. При постепенном нагружении, после некоторой начальной осадки смеси в металлической лабораторной форме, крупные частицы, не огибая друг друга, прекращают движение, в результате чего уплотнение ухудшается [13], а опасность дробимости щебня растет.
В работе Стефановича А.Е. сказано, «что особенностью статического разрушения от разрушения ударом является факт концентрации энергии в точках контакта щебенок между собой и рабочими органами (форма, пресс, валец)» [14]. Этот факт описан в работе [6]. При осмотре образцов, уплотненных давлением 30 МПа, обнаружено разрушение зерен щебня, в основном в зоне его контакта с формой. Приведенные в табл. 1 данные [13] свидетельствуют о том, что самым эффективным лабораторным методом при проектировании состава асфальтобетонной смеси
является вращательный пресс. В этом случае относительно большое дробление зерен щебня (10,6 %) отвечает смеси с 65 % щебня.
Таблица 1 Влияние лабораторного метода уплотнения на дробимость щебня в асфальтобетоне [131
Метод уплотнения лабораторного образца Дробление щебня (%) при его содержании в асфальтобетоне:
20 % 35 % 50 % 65 %
Давление при сжатии: 30 МПа 40 МПа 50 МПа 2,1 4,0 4,9 10,6 10,8 15,5 16,8 25
Комбинированный: вибрация 3 мин и сжатие под давлением 20 МПа — 3,7 8,5 10,0
Трамбование по Маршаллу с обеих сторон образца по 50 ударов 1,1 1,7 5,8 8,1
Вращательное уплотнение на гира-тором 20 оборотов 1,8 3,0 4,3 10,6
Цель и постановка задачи
Стремление к изучению механизма уплотнения и формирования плотности многокомпонентного материала на основе органических вяжущих привело к разработке и появлению новых методов уплотнения асфальтобетона, приближенных к производственным условиям. Кроме рассмотренных выше методов, в США, Франции и Германии используют укатку смесей колесом, возвратно-поступательно воздействующим на смесь, засыпанную в прямоугольную форму 300×350 мм, которая устанавливается на подвижной тележке. Радиус рабочего катка обеспечивает возможность перемещения сектора от края до края формы, одновременно на смесь передают вертикальное давление, что хорошо воспроизводит работу дорожного катка при уплотнении черных слоев дорожных одежд
[15, 16].
Подобными прессами в Украине оснащены лаборатории НТУ, ФПГ «Альтком» и ХНАДУ. На кафедре ТДСМ ХНАДУ выполняются исследовательские работы с использованием секторного пресса, разработанного предприятием НТЦ «Доряюсть». Принцип действия пресса заключается в укатке асфальтобетонных плит размерами сторон 230×160 мм высотой не более 90 мм. Методика уплотнения смесей предусматривает следующие операции: в смазанную, нагретую до технологической температуры форму засыпают предварительно взвешенную смесь и устанавливают ее на подвижную тележку, после чего при помощи винтовой передачи опускают уплотняющий металлический сектор, нагруженный металлическими плитами, массой 20 кг каждая. По завершению заданного числа проходов уплотняющий сектор поднимают, образец оставляют для остывания до температуры окружающей среды. В результате такой укатки образуется асфальтобетонная плита, которую распиливают на 9 образцов кубовидной формы со стороной ребра, равной 50 мм. Образцы испытывают в соответствии с целями эксперимента.
Стабильность зернового состава минерального остова является одним из главных условий выбора лабораторного метода уплотнения асфальтобетонных смесей. Как следует из табл. 1, при статическом давлении имеет место максимальное дробление зерен щебня. В то же время оно практически отсутствует при уплотнении по Маршаллу и вращательным прессом.
Результаты экспериментальных данных
Дробимость зерен щебня при лабораторной укатке секторным прессом практически не изучена. В связи с этим в данной работе изучена дробимость при укатке секторным прессом щебня марки типа А, состоящей из: 5 % щебня марки М 1000 фракции 10-20 мм; 45 % щебня 5-10 мм; 40 % отсева и 10 % минерального порошка.
Минеральные составляющие перемешивали в течение 3 мин, затем с высоты 5-6 см засыпали до половины в форму секторного пресса, штыковали 10-12 раз по всей площади формы, затем форму заполняли до верха смесью и разглаживали её шпателем.
Смесь каменных материалов уплотняли заданным количеством проходов и линейных
давлений секторного пресса. Линейное давление определяли как отношение массы, действующей на секторный каток, к его длине. Содержимое формы рассеивали на контрольных ситах 5 и 10 мм. Остатки на ситах взвешивали и сравнивали с исходной массой. Дробимость определяли по формуле, приведенной в [17]. Результаты испытаний приведены на рис. 1.
Др =
m — m
•100;
m
где m — исходная масса щебня, г; ml — масса остатка на контрольном сите с размером отверстий 5 мм, г. — 8,4 кг/см;
▲ — 11,3 кг/см; ■ — 14,0 кг/см
Приведенные на рис. 1 зависимости свидетельствуют прежде всего о том, что дроби-мость минеральных зерен в диапазоне принятых давлений и количестве проходов очень низка. При самом неблагоприятном сочетании (14,0 кг/см и 70 проходов) дробимость равна 3,7 %. Увеличение давления при 70 проходах от 5,6 кг/см до 14,0 кг/см приводит к росту дробимости в 3,4 раза, а увеличение количества проходов от 10 до 70 при давлении 14,0 кг/см увеличивает дробление в 2,7 раза. Таким образом, более опасным в отношении дробимости минеральных зерен является линейное давление.
Для комбинаций — 5,60 кг/см и 60 проходов,
8,4 кг/см и 40 проходов, 11,3 кг/см и 20 проходов — наблюдается одинаковый уровень дробления. Уровень дробления 1,75 % достигается для комбинации: 8,4 кг/см и 60 проходов; 11,3 кг/см и 37 проходов; 14 кг/см и 17 проходов (рис. 1). В то же время ступенчатое
уплотнение по 50 проходов с серией давлений: 5,6; 8,4; 11,3 и 14 кг/см повысило дро-бимость до 5 %.
Из работы [6] следует, что дробимость щебня в результате лабораторного давления прессованием выше, чем при уплотнении катками в покрытии. Сопоставление результатов уплотнения исходной смеси секторным прессом и прессованием (рис. 1 и табл. 2) в режиме 30 МПа за 3 мин показывает, что дробление при прессовании почти в 8 раз выше (29/3,7), чем при укатке сектором с линейным давлением 14,0 кг/см при 70 проходах сектора.
Переход от сухой смеси к смеси каменных материалов с битумом изменяет уровень дробимости зерен щебня. Для оценки влияния содержания битума на дробимость щебня был проведен эксперимент, в котором смеси с 50 % щебня без битума и с битумом марки БНД 60/90 уплотняли в стандартной цилиндрической форме в течение 3 мин под давлением 30 МПа, после чего проверяли ее гранулометрический состав экстрагированием (табл. 2). Из приведенных данных следу-
ет, что увеличение вяжущего от 4,5 до 6,0 % способствует снижению дробимости щебня на 9 %.
Таблица 2 Влияние содержания вяжущего на дробимость каменного материала при уплотнении давлением 30 МПа
Содержание вяжущего, % 0 4,5 5,0 5,5 6,0
Дробимость, % 29 26 25 23 20
Для установления уровня дробимости в асфальтобетонной смеси с малым содержанием щебня был проведен эксперимент со смесью типа «В». Асфальтобетонную смесь уплотняли на секторном прессе нагрузкой
8,4 кг/см и 50 проходами и стандартным давлением 40 МПа в течение 3 мин.
Результаты, приведенные в табл. 3, показывают, что при понижении содержания щебня в смеси до 30 % практически исключается дробимость как при прессовании давлением 40 МПа, так и при укатке секторным прессом.
Таблица 3 Зерновой состав минеральной части асфальтобетонной смеси типа «В» до и после уплотнения
Вид уплотнения Полные остатки в % на ситах с размерами отверстий сит в мм Битум, %
10 5 2,5 1,25 0,63 0,31 0,14 0,071 <0,071
Исходный состав 9,6 21,0 10,0 12,3 10,0 10,2 8,9 9,6 8,4 7,6
Секторный пресс 10,1 22,7 11,5 12,6 9,8 8,7 6,5 8,7 9,4 7,6
Прессование 40 МПа 10,4 20,5 12,4 12,3 9,4 8,8 7,6 8,3 10,3 7,6
Выводы
Литературный анализ и лабораторные экспериментальные данные показали, что наибольшая дробимость щебня соответствует стандартному уплотнению асфальтобетона прессованием. Особенно это проявляется на многощебенистых смесях.
Дробимость при укатке многощебенистой минеральной смеси линейным давлением 14 кг/см и 70 проходами секторного пресса составила 3,7 %. Уплотнение прессованием под давлением 30 МПа показало, что дроби-мость зерен щебня при введении в смесь 6 % битума снижается на 9 %. В малощебенистой асфальтобетонной смеси типа «В» дробление щебня не обнаруживается ни при уплотнении прессованием, ни укаткой.
Результаты выполненной работы свидетельствуют о необходимости отказа от лабораторного метода уплотнения давлением и замены его методом, в большей степени отвечающим условиям производства.
Литература
1. Рыбьев И.А. Асфальтовые бетоны: учеб-
ное пособие строительных ВУЗов / И.А. Рыбьев. — М.: Высшая школа, 1969.
— 399 с.
2. Шестаков В.Н. Оценка теплофизической
надежности технологии строительства асфальтобетонных покрытий. Ч. 1. / В.Н. Шестаков. — Омск: Изд-во СибА-ДИ, 1998. — 184 с.
3. Волков М.И. Дорожно-строительные ма-
териалы / М.И. Волков, И.М. Борщ,
И.В. Королев. — М.: Транспорт, 1965. -518 с.
4. Лобзова К.Я. Уплотнение асфальтобетона и
битумо-минеральных смесей / К.Я. Лоб-зова // Сборник трудов Союздорнии, 1962. — С.267-289.
5. Королев И.В. Исследование асфальтового
бетона, применяемого в теплом состоянии / И. В. Королев // Сборник трудов Союздорнии, 1962. — С. 300-311.
6. Лобзова К.Я. Дробимость щебня при
уплотнении асфальтобетонных покрытий / К.Я. Лобзова, Н.В. Горелышев // Автомобильные дороги. — 1969.- Вып. 2.
— С. 18-19.
7. Кузмичев В.Т. Гидрофобизация местных
минеральных порошков для асфальтобетона. / В.Т. Кузмичев // Сборник трудов Союздорнии, 1962. — С. 317-324.
8. Раковский Э.И. Опыт устройства асфаль-
тобетонного покрытия с шероховатой поверхностью / Э.И. Раковский // Сборник трудов Союздорнии, 1962. — С. 329335.
9. Радовский Б.С. Методы проектирования
состава асфальтобетонных смесей в США / Б. С. Радовский // Дорожная техника, 2006. — С. 62-71.
10. Moutier F. Utilisation et possibilites de la
presse a cisaillement giratoire. Bitumes et enrobes bitumineux / F. Moutier // LCPC.
— 1977. — Numero spesial V. — P. 173-180.
11. Смеси асфальтобетонные дорожные и аэродромные, дегтебетонные дорожные, асфальтобетон и дегтебетон. Методы испытаний: ГОСТ 12801-84. Действителен от 1985-01-01. — М. Государственный комитет СССР, 1985. — 33 с. -(Государственный стандарт ССР).
12. Суміші асфальтобетонні і асфальтобетон
дорожній та аеродромний. Технічні умови: ДСТУ Б В.2.7-119-2011. Чинний від 2003-07-01. — К.: Харківський національний автомобільно-дорожній універ-
ситет (ХНАДУ), Національний транспортний університет (НТУ) і Державний дорожній науково-дослідний інститут ім. М.П. Шульгіна (ДерждорНДІ), 2003.
— 44 с. (Державний стандарт України).
13. Костельов М.П. Зачем уплотнять асфаль-
тобетон выше минимальной нормы? / М.П. Костельов. — К.: Дорожная техника, 2005.- С. 133-138.
14. Стефанович А.Е. Показатели долговечно-
сти щебня в несущих слоях нежестких дорожных одежд: автореф. дисс. на соиск. учен. степени канд. техн. наук 05.23.11 «Проектирование и строительство дорог, метрополитенов, аэродромов, мостов и транспортных тоннелей» / А.Е. Стефанович. — К., 1967. — 23 с.
15. Sviertz D. Ashpalt Mixture Compaction and
Aggrigate Analysis Techniqres / D. Sviertz, M. Enad, H. Bahia. — Madison: University of Wisconsin, 2010. — 97 р.
16. Bituminous Mixtures — Test Methods for Hot Mix Asphalt. — Part 33: Specimen Prepared by Roller Compactor: EN 12697-33. Current 01.01.2011. — European Committee for Standartization, 2007. — 15 p.
17. Щебень и гравий из плотных горных по-
род и отходов промышленного производства для строительных работ. Методы физико-механических испытаний: ДСТУ Б В.2.7-71-98. Чинний від 1999-01-01. — К.: Государственный комитет строительства, архитектуры и жилищной политики Украины, 1999. — 84 с.
— (Національний стандарт України).
Рецензент: В.А. Золотарев, профессор, д.т.н., ХНАДУ.
Статья поступила в редакцию 20 ноября 2013 г.
Асфальт и асфальтобетон
Асфальтобетонные смеси (далее — смеси) и асфальтобетоны в зависимости от вида минеральной составляющей подразделяют на щебеночные, гравийные и песчаные.
Смеси в зависимости от вязкости используемого битума и температуры при укладке подразделяют на:
- Горячие, приготавливаемые с использованием вязких и жидких нефтяных дорожных битумов и укладываемые с температурой не менее 120 °С;
- Холодные, приготавливаемые с использованием жидких нефтяных дорожных битумов и укладываемые с температурой не менее 5 °С.
Горячие смеси и асфальтобетоны в зависимости от наибольшего размера минеральных зерен подразделяют на:
- крупнозернистые с размером зерен до 40 мм;
- мелкозернистые — до 20 мм;
- песчаные — до 5 мм.;
Холодные смеси подразделяют на мелкозернистые и песчаные.
Асфальтобетоны из горячих смесей в зависимости от величины остаточной пористости подразделяют на виды:
- высокоплотные с остаточной пористостью от 1,0 до 2,5 %;
- плотные — от 2,5 до 5,0 %;
- пористые — от 5,0 до 10,0 %;
- высокопористые — от 10,0 до 18,0 %.
Асфальтобетоны из холодных смесей должны иметь остаточную пористость свыше 6,0 до 10,0 %. Щебеночные и гравийные горячие смеси и плотные асфальтобетоны в зависимости от содержания в них щебня (гравия) подразделяют на типы:
- «А» — с содержанием щебня от 50 до 60 %;
- «Б» — от 40 до 50 %;
- «В» — от 30 до 40 %.
Щебеночные и гравийные холодные смеси и соответствующие им асфальтобетоны в зависимости от содержания в них щебня (гравия) подразделяют на типы Бх и Вх.
Горячие и холодные песчаные смеси и соответствующие им асфальтобетоны в зависимости от вида песка подразделяют на типы:
- «Г и Гх» — на песках из отсевов дробления, а также на их смесях с природным песком при содержании последнего не более 30 % по массе;
- «Д и Дх» — на природных песках или смесях природных песков с отсевами дробления при содержании последних менее 70 % по массе.
Марка смеси и асфальтобетона определяет показатели физико-механических свойств, водонасыщение, зерновые составы и пористость минеральной части.
Щебень из плотных горных пород и гравий, щебень из шлаков, входящие в состав смесей, по зерновому составу, прочности, содержанию пылевидных и глинистых частиц, содержанию глины в комках должны соответствовать требованиям ГОСТ 8267-93. «Щебень и гравий из плотных горных пород для строительных работ.»
Содержание зерен пластинчатой (лещадной) формы в щебне и гравии должно быть по массе не более:
- 15% — для смесей типа А и высокоплотных;
- 25% — для смесей типов Б, Бх;
- 35% — для смесей типов В, Вх.
Гравийно-песчаные смеси по зерновому составу должны отвечать требованиям ГОСТ 23735, а гравий и песок, входящие в состав этих смесей, — ГОСТ 8267-93. «Щебень и гравий из плотных горных пород для строительных работ.» и ГОСТ 8736-93. «Песок для строительных работ.» соответственно.
Для приготовления смесей и асфальтобетонов применяют щебень и гравий фракций от 5 до 10 мм, от 10 до 20 (15) мм, от 20 (15) до 40 мм, а также смеси указанных фракций.
Минеральный порошок, входящий в состав смесей и асфальтобетонов, должен отвечать требованиям ГОСТ 16557. Допускается применять в качестве минеральных порошков для пористого и высокопористого асфальтобетона, а также для плотного асфальтобетона II и III марок техногенные отходы промышленного производства (измельченные основные металлургические шлаки, золыуноса, золошлаковые смеси, пыль-уноса цементных заводов и пр.).
Для приготовления смесей применяют битумы нефтяные дорожные вязкие по ГОСТ 22245 и жидкие по ГОСТ 11955, а также полимерно-битумные вяжущие и модифицированные битумы по технической документации, согласованной в установленном порядке.
Асфальтобетонная смесь | Выпускается в соответствии ГОСТ 31015-2002.Используется полимерно-битумное вяжущее (ПБВ). | Цена: 6 000 ₽ |
Асфальтобетонная смесь | Выпускается в соответствии ПНСТ 183-2019.Используется полимерно-битумное вяжущее (ПБВ). | Цена: 8 800 ₽ |
Асфальтобетонная смесь | Выпускается в соответствии ГОСТ 31015-2002.C наибольшим размером зерен щебня до 15мм. | Цена: 5 400 ₽ |
Асфальтобетонная смесь | Выпускается в соответствии ПНСТ 183-2019.Используется полимерно-битумное вяжущее (ПБВ). | Цена: 7 800 ₽ |
Высокоплотная мелкозернистая | Выпускается в соответствии ГОСТ 9128-2013.Содержание щебня от 50-70%. | Цена: 5 000 ₽ |
Плотная асфальтобетонная смесь | Выпускается в соответствии ГОСТ 9128-2013.Содержание щебня от 50-60%. | Цена: 4 700 ₽ |
Плотная асфальтобетонная смесь | Выпускается в соответствии ПНСТ 184-2019.![]() Содержание щебня от 50-60%. | Цена: 6 900 ₽ |
Плотная асфальтобетонная смесь | Выпускается в соответствии ГОСТ 9128-2013.Содержание щебня от 40-50%. | Цена: 4 600 ₽ |
Плотная асфальтобетонная смесь | Выпускается в соответствии ГОСТ 9128-2013.Содержание щебня от 40-50%. | Цена: 4 300 ₽ |
Плотная асфальтобетонная смесь | Выпускается в соответствии ГОСТ 9128-2013.Содержание щебня от 30-40%. | Цена: 4 600 ₽ |
Плотная асфальтобетонная смесь | Выпускается в соответствии ГОСТ 9128-2013.Содержание щебня от 30-40%. | Цена: 4 300 ₽ |
Плотная асфальтобетонная смесь | Выпускается в соответствии ГОСТ 9128-2013.Объемный вес — 2,38 т./м3 | Цена: 4 600 ₽ |
Плотная асфальтобетонная смесь | Выпускается в соответствии ГОСТ 9128-2013.Объемный вес — 2,38 т./м3 | Цена: 4 300 ₽ |
Крупнозернистая пористая | Выпускается в соответствии ГОСТ 9128-2013.![]() Объемный вес — 2,32 т./м3 | Цена: 4 200 ₽ |
Крупнозернистая пористая | Выпускается в соответствии ГОСТ 9128-2013.Объемный вес — 2,32 т./м3 | Цена: 4 400 ₽ |
Черный щебень фракции 5-20мм | Выпускается в соответствии ГОСТ 30491-2012.Объемный вес — 2,34 т./м3 | Цена: 4 000 ₽ |
Черный щебень фракции 5-40мм | Выпускается в соответствии ГОСТ 30491-2012.Объемный вес — 2,34 т./м3 | Цена: 3 800 ₽ |
Тесты Основы геодезии ВВ | Тест:
Вариант 1
1. Гидравлические вяжущие вещества могут твердеть и повышать прочность:
1) только в воздушной среде;
2) только в водной среде;
3) в воздушной и в водной средах;
4) в кислоте.
2. Основной горной породой для получения портландцемента является:
1) известняк;
2) песок;
3) гранит;
4) глина.
3. К каким материалам по своему строению относятся битумы:
1) к кристаллическим;
2) к неорганическим;
3) к полимерным;
4) к коллоидным;
4. Какой маркой обозначаются битумы дорожные:
1) БН;
2) БНД;
3) БНК;
4) СГ.
5. Асфальтобетон — это:
1) битумоминеральная смесь, получаемая при нагревании;
2) смесь щебня и песка, обработанная горячим битумом;
3) битумоминеральная смесь с добавкой щебня и песка;
4) материал, получаемый в результате уплотнения специально приготовленной смеси, состоящей из щебня, песка, минерального порошка и битума.
6. Асфальтобетон состоит:
1) из щебня (гравия), песка, минерального порошка и битума;
2) щебня (гравия), песка, минерального порошка и дегтя;
3) щебня (гравия), песка, битума и воды;
4) щебня (гравия), песка, цемента и воды.
7. Асфальтовяжущее вещество в асфальтобетоне — это:
1) смесь песка, минерального порошка и битума;
2) минеральный порошок;
3) битум;
4) смесь битума и минерального порошка.
8. Расчет составов асфальтобетонных смесей производится по принципу:
1) абсолютных объемов;
2) максимальной прочности минеральной части;
3) минимальной пустотности минеральной части;
4) постепенного приближения.
9. Асфальтобетонную смесь для горячего асфальтобетона готовят при температуре:
1) порядка 120 °С;
2) 180 — 200 °С;
3) 140 — 160 °С;
4) 80 — 110 °С.
10. Классификация асфальтобетонов по вязкости битума и температуре уплотнения асфальтобетонной смеси:
1) горячие и холодные;
2) плотные и пористые;
3) щебеночные и песчаные;
4) асфальтобетоны, полимербетоны, дегтебетоны.
11. Основное назначение минерального порошка в асфальтобетоне:
1) повышает удобоукладываемость асфальтобетонной смеси;
2) снижает температуру приготовления асфальтобетонной смеси;
3) переводит битум в пленочное состояние, повышает вязкость и прочность битума;
4) понижает вязкость битума и повышает уплотняемость асфальтобетонной смеси.
12. Горячий асфальтобетон при содержании щебня 46 % по массе относится к структурному типу:
1) А;
2) Б;
3) В;
4) Г.
13. Горячий асфальтобетон при остаточной пористости 3 % относится:
1) к плотному;
2) высокоплотному;
3) пористому;
4) высокопористому.
14. Мелкозернистые асфальтобетонные смеси содержат зерна размером:
1) до 5 мм;
2) до 20 мм;
3) до 10 мм;
4) до 40 мм.
15. В зависимости от крупности щебня горячие асфальтовые бетоны делят:
1) на мелкозернистые и среднезернистые;
2) среднезернистые и крупнозернистые;
3) мелкозернистые и крупнозернистые;
4) среднезернистые и песчаные.
Вариант 2
1. Удобоукладываемость бетонов и растворов будет лучше при использовании:
1) гидрофобных добавок;
2) пластифицирующих добавок;
3) шлакопортландцемента;
4) битума.
2. Какой из факторов НЕ влияет на прочность цементов:
1) тонкость помола;
2) минералогический состав;
3) способ производства;
4) вода.
3. Какой маркой обозначаются битумы нефтяные:
1) БН;
2) БНД;
3) БНК;
4) СГ.
4. Какие эмульсии используются для строительства дорог:
1) нефтяные;
2) полимерные;
3) резиновые;
4) битумные.
5. Основное назначение минерального порошка в асфальтобетоне:
1) повышает удобоукладываемость асфальтобетонной смеси;
2) снижает температуру приготовления асфальтобетонной смеси;
3) переводит битум в пленочное состояние, повышает вязкость и прочность битума;
4) понижает вязкость битума и повышает уплотняемость асфальтобетонной смеси.
6. Горячий асфальтобетон при содержании щебня 46 % по массе относится к структурному типу:
1) А;
2) Б;
3) В;
4) Г.
7. Горячий асфальтобетон при остаточной пористости 3 % относится:
1) к плотному;
2) высокоплотному;
3) пористому;
4) высокопористому.
8. Мелкозернистые асфальтобетонные смеси содержат зерна размером:
1) до 5 мм;
2) до 20 мм;
3) до 10 мм;
4) до 40 мм.
9. В зависимости от крупности щебня горячие асфальтовые бетоны делят:
1) на мелкозернистые и среднезернистые;
2) среднезернистые и крупнозернистые;
3) мелкозернистые и крупнозернистые;
4) среднезернистые и песчаные.
10. Асфальтобетон — это:
1) битумоминеральная смесь, получаемая при нагревании;
2) смесь щебня и песка, обработанная горячим битумом;
3) битумоминеральная смесь с добавкой щебня и песка;
4) материал, получаемый в результате уплотнения специально приготовленной смеси, состоящей из щебня, песка, минерального порошка и битума.
11. Асфальтобетон состоит:
1) из щебня (гравия), песка, минерального порошка и битума;
2) щебня (гравия), песка, минерального порошка и дегтя;
3) щебня (гравия), песка, битума и воды;
4) щебня (гравия), песка, цемента и воды.
12. Асфальтовяжущее вещество в асфальтобетоне — это:
1) смесь песка, минерального порошка и битума;
2) минеральный порошок;
3) битум;
4) смесь битума и минерального порошка.
13. Расчет составов асфальтобетонных смесей производится по принципу:
1) абсолютных объемов;
2) максимальной прочности минеральной части;
3) минимальной пустотности минеральной части;
4) постепенного приближения.
14. Асфальтобетонную смесь для горячего асфальтобетона готовят при температуре:
1) порядка 120 °С;
2) 180 — 200 °С;
3) 140 — 160 °С;
4) 80 — 110 °С.
15. Классификация асфальтобетонов по вязкости битума и температуре уплотнения асфальтобетонной смеси:
1) горячие и холодные;
2) плотные и пористые;
3) щебеночные и песчаные;
4) асфальтобетоны, полимербетоны, дегтебетоны.
Вариант 3
1. Какой строительный материал НЕ является минеральным вяжущим:
1) воздушная строительная известь;
2) щебень;
3) шлакопортландцемент;
4) мел.
2. Основная формула гипсового камня:
1) CaSO4*Н2O
2) CaCO3*h3O
3) 3CaO*SiO2
4) h3O
3. Какой маркой обозначаются битумы кровельные:
1) БН;
2) БНД;
3) БНК;
4) СГ.
4. При какой температуре (оС) укладывают горячий асфальтобетон:
1) 140…170;
2) 60…70;
3) 100…200;
4) 200…250:
5. Асфальтобетонную смесь для горячего асфальтобетона готовят при температуре:
1) порядка 120 °С;
2) 180 — 200 °С;
3) 140 — 160 °С;
4) 80 — 110 °С.
6. Классификация асфальтобетонов по вязкости битума и температуре уплотнения асфальтобетонной смеси:
1) горячие и холодные;
2) плотные и пористые;
3) щебеночные и песчаные;
4) асфальтобетоны, полимербетоны, дегтебетоны.
7. Основное назначение минерального порошка в асфальтобетоне:
1) повышает удобоукладываемость асфальтобетонной смеси;
2) снижает температуру приготовления асфальтобетонной смеси;
3) переводит битум в пленочное состояние, повышает вязкость и прочность битума;
4) понижает вязкость битума и повышает уплотняемость асфальтобетонной смеси.
8. Горячий асфальтобетон при содержании щебня 46 % по массе относится к структурному типу:
1) А;
2) Б;
3) В;
4) Г.
9. Горячий асфальтобетон при остаточной пористости 3 % относится:
1) к плотному;
2) высокоплотному;
3) пористому;
4) высокопористому.
10. Мелкозернистые асфальтобетонные смеси содержат зерна размером:
1) до 5 мм;
2) до 20 мм;
3) до 10 мм;
4) до 40 мм.
11. В зависимости от крупности щебня горячие асфальтовые бетоны делят:
1) на мелкозернистые и среднезернистые;
2) среднезернистые и крупнозернистые;
3) мелкозернистые и крупнозернистые;
4) среднезернистые и песчаные.
12. Асфальтобетон — это:
1) битумоминеральная смесь, получаемая при нагревании;
2) смесь щебня и песка, обработанная горячим битумом;
3) битумоминеральная смесь с добавкой щебня и песка;
4) материал, получаемый в результате уплотнения специально приготовленной смеси, состоящей из щебня, песка, минерального порошка и битума.
13. Асфальтобетон состоит:
1) из щебня (гравия), песка, минерального порошка и битума;
2) щебня (гравия), песка, минерального порошка и дегтя;
3) щебня (гравия), песка, битума и воды;
4) щебня (гравия), песка, цемента и воды.
14. Асфальтовяжущее вещество в асфальтобетоне — это:
1) смесь песка, минерального порошка и битума;
2) минеральный порошок;
3) битум;
4) смесь битума и минерального порошка.
15. Расчет составов асфальтобетонных смесей производится по принципу:
1) абсолютных объемов;
2) максимальной прочности минеральной части;
3) минимальной пустотности минеральной части;
4) постепенного приближения.
Вариант 4
1. Какой маркой обозначаются битумы кровельные:
1) БН;
2) БНД;
3) БНК;
4) СГ;
2. При какой температуре (оС) укладывают горячий асфальтобетон:
1) 140…170;
2) 60…70;
3) 100…200;
4) 200…250.
3. В каких видах работ наиболее распространено применение гипса:
1) при возведении фундаментов;
2) при возведении стен;
3) при производстве отделочных работ;
4) при земляных работ.
4. Строительную известь применяют для приготовления:
1) строительных растворов;
2) асфальтобетона;
3) кровельных материалов;
4) битума.
5. Горячий асфальтобетон при остаточной пористости 3 % относится:
1) к плотному;
2) высокоплотному;
3) пористому;
4) высокопористому.
6. Мелкозернистые асфальтобетонные смеси содержат зерна размером:
1) до 5 мм;
2) до 20 мм;
3) до 10 мм;
4) до 40 мм.
7. В зависимости от крупности щебня горячие асфальтовые бетоны делят:
1) на мелкозернистые и среднезернистые;
2) среднезернистые и крупнозернистые;
3) мелкозернистые и крупнозернистые;
4) среднезернистые и песчаные.
8. Асфальтобетон — это:
1) битумоминеральная смесь, получаемая при нагревании;
2) смесь щебня и песка, обработанная горячим битумом;
3) битумоминеральная смесь с добавкой щебня и песка;
4) материал, получаемый в результате уплотнения специально приготовленной смеси, состоящей из щебня, песка, минерального порошка и битума.
9. Асфальтобетон состоит:
1) из щебня (гравия), песка, минерального порошка и битума;
2) щебня (гравия), песка, минерального порошка и дегтя;
3) щебня (гравия), песка, битума и воды;
4) щебня (гравия), песка, цемента и воды.
10. Асфальтовяжущее вещество в асфальтобетоне — это:
1) смесь песка, минерального порошка и битума;
2) минеральный порошок;
3) битум;
4) смесь битума и минерального порошка.
11. Расчет составов асфальтобетонных смесей производится по принципу:
1) абсолютных объемов;
2) максимальной прочности минеральной части;
3) минимальной пустотности минеральной части;
4) постепенного приближения.
12. Асфальтобетонную смесь для горячего асфальтобетона готовят при температуре:
1) порядка 120 °С;
2) 180 — 200 °С;
3) 140 — 160 °С;
4) 80 — 110 °С.
13. Классификация асфальтобетонов по вязкости битума и температуре уплотнения асфальтобетонной смеси:
1) горячие и холодные;
2) плотные и пористые;
3) щебеночные и песчаные;
4) асфальтобетоны, полимербетоны, дегтебетоны.
14. Основное назначение минерального порошка в асфальтобетоне:
1) повышает удобоукладываемость асфальтобетонной смеси;
2) снижает температуру приготовления асфальтобетонной смеси;
3) переводит битум в пленочное состояние, повышает вязкость и прочность битума;
4) понижает вязкость битума и повышает уплотняемость асфальтобетонной смеси.
15. Горячий асфальтобетон при содержании щебня 46 % по массе относится к структурному типу:
1) А;
2) Б;
3) В;
4) Г.
Вариант 5
1. Какой маркой обозначаются битумы нефтяные:
1) БН;
2) БНД;
3) БНК;
4) СГ;
2. Какие эмульсии используются для строительства дорог:
1) нефтяные;
2) полимерные;
3) резиновые;
4) битумные;
3. Количество воды необходимое для затворения извести зависит от:
1) активности и состава извести;
2) тонкости помола;
3) всех вышеперечисленных факторов;
4) объема.
4. Воздушные вяжушие вещества могут твердеть:
1) только в воздушной среде;
2) только в водной среде;
3) в воздушной и водных средах;
4) в кислоте.
5. Классификация асфальтобетонов по вязкости битума и температуре уплотнения асфальтобетонной смеси:
1) горячие и холодные;
2) плотные и пористые;
3) щебеночные и песчаные;
4) асфальтобетоны, полимербетоны, дегтебетоны.
6. Основное назначение минерального порошка в асфальтобетоне:
1) повышает удобоукладываемость асфальтобетонной смеси;
2) снижает температуру приготовления асфальтобетонной смеси;
3) переводит битум в пленочное состояние, повышает вязкость и прочность битума;
4) понижает вязкость битума и повышает уплотняемость асфальтобетонной смеси.
7. Горячий асфальтобетон при содержании щебня 46 % по массе относится к структурному типу:
1) А;
2) Б;
3) В;
4) Г.
8. Горячий асфальтобетон при остаточной пористости 3 % относится:
1) к плотному;
2) высокоплотному;
3) пористому;
4) высокопористому.
9. Мелкозернистые асфальтобетонные смеси содержат зерна размером:
1) до 5 мм;
2) до 20 мм;
3) до 10 мм;
4) до 40 мм.
10. В зависимости от крупности щебня горячие асфальтовые бетоны делят:
1) на мелкозернистые и среднезернистые;
2) среднезернистые и крупнозернистые;
3) мелкозернистые и крупнозернистые;
4) среднезернистые и песчаные.
11. Асфальтобетон — это:
1) битумоминеральная смесь, получаемая при нагревании;
2) смесь щебня и песка, обработанная горячим битумом;
3) битумоминеральная смесь с добавкой щебня и песка;
4) материал, получаемый в результате уплотнения специально приготовленной смеси, состоящей из щебня, песка, минерального порошка и битума.
12. Асфальтобетон состоит:
1) из щебня (гравия), песка, минерального порошка и битума;
2) щебня (гравия), песка, минерального порошка и дегтя;
3) щебня (гравия), песка, битума и воды;
4) щебня (гравия), песка, цемента и воды.
13. Асфальтовяжущее вещество в асфальтобетоне — это:
1) смесь песка, минерального порошка и битума;
2) минеральный порошок;
3) битум;
4) смесь битума и минерального порошка.
14. Расчет составов асфальтобетонных смесей производится по принципу:
1) абсолютных объемов;
2) максимальной прочности минеральной части;
3) минимальной пустотности минеральной части;
4) постепенного приближения.
15. Асфальтобетонную смесь для горячего асфальтобетона готовят при температуре:
1) порядка 120 °С;
2) 180 — 200 °С;
3) 140 — 160 °С;
4) 80 — 110 °С.
Вариант 6
1. К каким материалам по своему строению относятся битумы:
1) к кристаллическим;
2) к неорганическим;
3) к полимерным;
4) к коллоидным;
2. Какой маркой обозначаются битумы дорожные:
1) БН;
2) БНД;
3) БНК;
4) СГ;
3. При твердении гипса происходит:
1) увеличение объёма;
2) уменьшение объёма;
3) остаётся без изменений;
4) потеря массы.
4. При затворении гипса водой происходит химический процесс:
1) гидратации;
2) окисления;
3) восстановления;
4) коррозия.
5. Асфальтовяжущее вещество в асфальтобетоне — это:
1) смесь песка, минерального порошка и битума;
2) минеральный порошок;
3) битум;
4) смесь битума и минерального порошка.
6. Расчет составов асфальтобетонных смесей производится по принципу:
1) абсолютных объемов;
2) максимальной прочности минеральной части;
3) минимальной пустотности минеральной части;
4) постепенного приближения.
7. Асфальтобетонную смесь для горячего асфальтобетона готовят при температуре:
1) порядка 120 °С;
2) 180 — 200 °С;
3) 140 — 160 °С;
4) 80 — 110 °С.
8. Классификация асфальтобетонов по вязкости битума и температуре уплотнения асфальтобетонной смеси:
1) горячие и холодные;
2) плотные и пористые;
3) щебеночные и песчаные;
4) асфальтобетоны, полимербетоны, дегтебетоны.
9. Основное назначение минерального порошка в асфальтобетоне:
1) повышает удобоукладываемость асфальтобетонной смеси;
2) снижает температуру приготовления асфальтобетонной смеси;
3) переводит битум в пленочное состояние, повышает вязкость и прочность битума;
4) понижает вязкость битума и повышает уплотняемость асфальтобетонной смеси.
10. Асфальтобетон — это:
1) битумоминеральная смесь, получаемая при нагревании;
2) смесь щебня и песка, обработанная горячим битумом;
3) битумоминеральная смесь с добавкой щебня и песка;
4) материал, получаемый в результате уплотнения специально приготовленной смеси, состоящей из щебня, песка, минерального порошка и битума.
11. Асфальтобетон состоит:
1) из щебня (гравия), песка, минерального порошка и битума;
2) щебня (гравия), песка, минерального порошка и дегтя;
3) щебня (гравия), песка, битума и воды;
4) щебня (гравия), песка, цемента и воды.
12. Горячий асфальтобетон при содержании щебня 46 % по массе относится к структурному типу:
1) А;
2) Б;
3) В;
4) Г.
13. Горячий асфальтобетон при остаточной пористости 3 % относится:
1) к плотному;
2) высокоплотному;
3) пористому;
4) высокопористому.
14. Мелкозернистые асфальтобетонные смеси содержат зерна размером:
1) до 5 мм;
2) до 20 мм;
3) до 10 мм;
4) до 40 мм.
15. В зависимости от крупности щебня горячие асфальтовые бетоны делят:
1) на мелкозернистые и среднезернистые;
2) среднезернистые и крупнозернистые;
3) мелкозернистые и крупнозернистые;
4) среднезернистые и песчаные.
КЛЮЧ
Вариант 1 | Вариант 2 | Вариант 3 | Вариант 4 | Вариант 5 | Вариант 6 | |
1 | 3 | 3 | 2 | 3 | 1 | 4 |
2 | 1 | 3 | 1 | 1 | 4 | 2 |
3 | 4 | 1 | 3 | 3 | 3 | 1 |
4 | 2 | 4 | 1 | 4 | 1 | 1 |
5 | 3 | 3 | 3 | 1 | 1 | 4 |
6 | 1 | 2 | 1 | 2 | 3 | 3 |
7 | 4 | 1 | 3 | 3 | 2 | 3 |
8 | 3 | 2 | 2 | 3 | 1 | 1 |
9 | 3 | 3 | 1 | 1 | 2 | 3 |
10 | 1 | 3 | 2 | 4 | 3 | 3 |
11 | 3 | 1 | 3 | 3 | 3 | 1 |
12 | 2 | 4 | 3 | 3 | 1 | 2 |
13 | 1 | 3 | 1 | 1 | 4 | 1 |
14 | 2 | 3 | 4 | 3 | 3 | 2 |
15 | 3 | 1 | 3 | 2 | 3 | 3 |
(PDF) Эффект частичной замены щебеночно-пылевого наполнителя на стеклянный порошок при производстве горячего асфальтобетона
IV. ВЫВОДЫ
Лабораторные испытания порошка отработанного стекла, проведенные на градацию и индекс пластичности, следовательно, удовлетворяют Стандарту
Технические условия для использования в качестве наполнителя при производстве горячего асфальтобетона. Аналогичным образом, оптимальное содержание наполнителя в пыли щебня
(CSD) было определено на основе теста максимальной стабильности по Маршаллу.Было обнаружено, что 6,5% -ное содержание наполнителя CSD
указывает на максимальную стабильность по Маршаллу при 5,10% -ном содержании битума. Кроме того, лабораторный эксперимент, основанный на каждом результате испытания
для стабильности по Маршаллу, насыпной плотности и VFA, показал повышенное значение по мере увеличения количества стеклянного порошка. Значения потока, пустоты Air
и пустоты в минеральных заполнителях уменьшались по мере увеличения содержания стеклянного порошка. При 75% замене щебеночной пыли
стеклянным порошком смесь показывала максимальную стабильность, максимальную насыпную плотность и Va в пределах допустимого диапазона Стандартных технических условий
. Следовательно, процентное содержание стеклянного порошка при 75% по весу наполнителя из щебня (CSD) или
, содержащем 4,875% по весу заполнителя, может обеспечить оптимальную производительность при интенсивном движении.
БЛАГОДАРНОСТЬ
Авторы выражают свою глубокую благодарность Технологическому институту Джиммы, Университету Джиммы и Университету Дебретабор
за всю поддержку, оказанную во время проведения исследовательской деятельности.
ССЫЛКИ
[1] Ghasemi, M.И Маранди, С. М. Улучшение характеристик битума, модифицированного резиновой крошкой, с использованием переработанного стеклянного порошка. Журнал Чжэцзян
University-Science A (Прикладная физика и инженерия), 14 (11), стр. 805-814, 2013.
[2] Джусто, К. и Веерарагаван, А., Утилизация пластиковых пакетов для отходов в Битумная смесь для улучшения характеристик дорог. Центр транспорта
Engineering, 2002.
[3] Мохаммед Атта Эль-Сайкали, проф. Д-р Шафик Джендия. Исследование возможности повторного использования пластиковых пакетов для отходов в качестве модификатора свойств асфальтобетонных смесей
(слой связующего материала), M.Sc. Тезис. Факультет гражданского строительства / инфраструктуры Исламского университета Газы, деканат, 2013.
[4] Алуко, О.Г., Оке, О.Л., Аволуси, Т.Ф. Исследование кратковременной прочности на сжатие сжатого стабилизированного земляного блока с порошком отработанного стекла
в качестве замены части цемента, Международный журнал научных и технологических исследований, том 4, выпуск 12, стр. 62-66, 2015
[5] Блюетт, Дж. И Вудворд, П. К., Некоторые геотехнические свойства стеклянных отходов. Департамент гражданского и морского строительства, Университет Хериот-Ватт,
Эдинбург, 2000.
[6] Ясанти, Р. Г., Ренгарасу, Т. М., Бандара, В. Р., Исследование характеристик отработанных материалов в горячем асфальтобетоне. American Scientific
Research Journal for Engineering, Technology и Science, 23 (1), pp. 252-267, 2016.
[7] Collins, R.Дж. И Чесельски, С. К., Переработка и использование отходов и побочных продуктов при строительстве автомобильных дорог. 1 (2), 1993.
[8] Йилдирим Ю., Модифицированные полимером асфальтовые вяжущие. Строительные и строительные материалы, 21 (1), с. 66–72, 2007.
[9] Риллагода Г. Н. Ясанти, Терренс М. Ренгарасу, W.M.K.R.T.W. Бандара. Исследование характеристик отходов в горячем асфальтобетоне;
Американский научно-исследовательский журнал инженерии, технологий и наук; Том 23, No 1, стр 252-267, 2016.
[10] Роксана А. и М. Камал Х. Влияние золы и шлака рисовой шелухи как наполнителей в асфальтобетонных смесях. Американский журнал инженерных исследований
(AJER), 6 (1), стр. 303-311, 2017.
[11] Зулкати, А., Дью, В.Й. и Делай, Д.С., Влияние наполнителей на свойства асфальта. Бетонная смесь. Journal of Transportation Engineering, 138 (7), стр.
902-910, 2011.
[12] Тапкин С. Механическая оценка смесей асфальт-заполнителей, приготовленных с использованием золы-уноса в качестве замены наполнителя. Canadian Journal of Civil Engineering,
35 (1), p.27-40, 2008.
[13] Сингх В. и Сакале Р. Влияние использования пластиковых отходов и стеклянных отходов на свойства асфальтового покрытия. Международный журнал исследований в области
Engineering and Technology, 07 (02) февраля, стр. 2321-7308, 2018.
[14] Моханти, М., Исследование использования отходов полиэтилена в битумных смесях для дорожных покрытий. M.Sc. Диссертация, Национальный технологический институт Руркела, ODISHA-
769008, 2014.
[15] Илан Ишай, Джозеф Краус и Арье Сайдс, «Модель связи свойств наполнителя с оптимальным поведением битумных смесей», AAPt ‘, Vol. 49, 1980.
[16] Д-р Хассан Х. Джони, Мейс Ф. Аль-Рубайе и Исраа Й. Джахад. Влияние применения стеклянной порошковой шпатлевки на свойства горячих асфальтобетонных смесей; Англ. &
Тех. Журнал, Vol. 29, №1, 2011 г .; Стр. 44–57, 2011.
[17] Фиссеха Вагав, Эмер Тукай Кесон, Антене Геремью. Оценка эффективности кирпичной пыли в качестве наполнителя для конструкции смеси горячего асфальта:
Пример из района Джимма; Международный журнал инженерии и науки; Vol. 7, выпуск 3 вер. II, Pp 64-72, 2018.
[18] Моника Моханти. Исследование использования отходов полиэтилена в битумных дорожных смесях. M.Sc. Тезис. Департамент гражданского строительства, Национальный институт технологий
Rourkela, 2013.
[19] ERA, Руководство по проектированию дорожных покрытий, (2002). «Эфиопское руководство дорожного управления по проектированию тротуаров для гибких покрытий». Эфиопия.
[20] Институт асфальта, (2003). «Метод расчета смесей для асфальтобетона и других типов горячих смесей», Руководство Серии No.02. Six Edition Ed. Кентукки, США
Журнал Сидянского университета
ТОМ 14, ВЫПУСК 9, 2020
Номер ISSN: 1001-2400
http://xadzkjdx.cn/
https://doi.org/10.37896/jxu14. 9/060
587
Агрегат — тротуар интерактивный
Заполнитель »- это собирательный термин для минеральных материалов, таких как песок, гравий и щебень, которые используются со связующей средой (например, вода, битум, портландцемент, известь и т. Д.) Для образования сложных материалов (таких как асфальтобетон. и портландцементный бетон).По объему на заполнитель обычно приходится от 92 до 96 процентов HMA и от 70 до 80 процентов портландцементного бетона. Заполнитель также используется для слоев основания и основания как для гибких, так и для жестких покрытий.
Заполнители могут быть натуральными или промышленными. Природные агрегаты обычно добываются из более крупных горных пород путем открытых выработок (карьеров). Извлеченная порода обычно измельчается до пригодных для использования размеров путем механического дробления. Промышленный агрегат часто является побочным продуктом других отраслей обрабатывающей промышленности.
В этом разделе кратко обсуждаются источники заполнителя и операции разработки карьеров, затем описываются основные минеральные, химические и физические свойства заполнителя, наиболее важные для дорожных покрытий, и типовые тесты, используемые для определения этих свойств. Следующий источник содержит более подробную информацию об агрегате:
Агрегированные источники
Заполнители могут происходить как из природных, так и из искусственных источников. Природные агрегаты происходят из горных пород, которые можно разделить на три широкие геологические классификации (Roberts, et al., 1996):
- Магматическая порода
- Эти породы в основном кристаллические и образуются в результате охлаждения расплавленного горного материала под земной корой (магмой).
- Осадочные породы
- Эти породы образованы из отложений нерастворимого материала (например, остатков существующей породы, отложенных на дне океана или озера). Этот материал превращается в скалу под действием тепла и давления. Осадочные породы имеют слоистый вид и далее классифицируются в зависимости от преобладающего минерала как известняковые (известняк, мел и т. Д.).), кремнистые (кремни, песчаники и др.) или глинистые (сланцы и др.).
- Метаморфическая порода
- Это магматические или осадочные породы, которые подверглись воздействию тепла и / или давления, достаточно сильного, чтобы изменить свою минеральную структуру и стать отличной от исходной породы.
Произведенная порода обычно состоит из промышленных побочных продуктов, таких как шлак (побочный продукт металлургической обработки — обычно получаемый при обработке стали, олова и меди) или особая порода, получаемая с особыми физическими характеристиками, которых нет в природной породе (например, низкая плотность легкого заполнителя).
Совокупное производство
Заполнители производятся в карьере или руднике (рис. 1), основная функция которых заключается в преобразовании in situ горной породы в заполнитель с заданными характеристиками. Обычно порода взрывается или выкапывается из стен карьера, а затем уменьшается в размере с помощью серии грохотов и дробилок. Некоторые карьеры также способны промывать готовый заполнитель.
Рисунок 1. Агрегатный рудник.Минеральные свойства
Минеральный состав заполнителя во многом определяет его физические характеристики и то, как он ведет себя как материал дорожного покрытия.Следовательно, при выборе источника заполнителя знание минеральных свойств карьерной породы может дать отличную подсказку относительно пригодности полученного заполнителя. Кордон (1979) дает некоторые общие рекомендации для агрегатов, используемых в HMA.
Таблица 1. Желаемые свойства горных пород для HMA
(из Cordon, 1979, как указано в Roberts et al., 1996)
Скальный тип | Твердость, вязкость | Устойчивость к зачистке 1,2 | Текстура поверхности | Форма дробленая |
---|---|---|---|---|
Магматические | ||||
Гранит | Ярмарка | Ярмарка | Ярмарка | Ярмарка |
Сиенит | Хорошо | Ярмарка | Ярмарка | Ярмарка |
Диорит | Хорошо | Ярмарка | Ярмарка | Хорошо |
Базальт (ловушка) | Хорошо | Хорошо | Хорошо | Хорошо |
Диабаз (ловушка) | Хорошо | Хорошо | Хорошо | Хорошо |
Габбро (ловушка) | Хорошо | Хорошо | Хорошо | Хорошо |
Осадочные | ||||
Известняк | Плохо | Хорошо | Хорошо | Ярмарка |
Песчаник | Ярмарка | Хорошо | Хорошо | Хорошо |
Черт | Хорошо | Ярмарка | Плохо | Хорошо |
Сланец | Плохо | Плохо | Ярмарка | Ярмарка |
Метаморфические | ||||
Гнейс | Ярмарка | Ярмарка | Хорошо | Хорошо |
Сланец | Ярмарка | Ярмарка | Хорошо | Ярмарка |
шифер | Хорошо | Ярмарка | Ярмарка | Ярмарка |
Кварцит | Хорошо | Ярмарка | Хорошо | Хорошо |
Мрамор | Плохо | Хорошо | Ярмарка | Ярмарка |
Змеевик | Хорошо | Ярмарка | Ярмарка | Ярмарка |
Примечания:
|
В целом взаимосвязь между минеральными и физическими свойствами довольно сложна, что затрудняет точное прогнозирование поведения конкретного источника агрегатов на основе одних только свойств минерала.
Химические свойства
Несмотря на то, что он относительно не важен для рыхлого заполнителя, его химические свойства важны для материала дорожного покрытия.В HMA химический состав поверхности заполнителя может определить, насколько хорошо асфальтобетонное вяжущее будет сцепляться с поверхностью заполнителя. Плохое прилегание, обычно называемое зачисткой, может привести к преждевременному разрушению конструкции. В PCC заполнители, содержащие реакционноспособные формы диоксида кремния, могут активно реагировать со щелочами, содержащимися в цементном тесте. Это расширение может вызвать растрескивание, выскакивание поверхности и растрескивание. Обратите внимание, что некоторые химические свойства заполнителя могут изменяться со временем, особенно после его измельчения.Вновь измельченный агрегат может проявлять сродство к воде, отличное от того же агрегата, который был измельчен и оставлен на складе в течение года.
Ниже приведены типичные химические свойства, измеренные для заполнителей:
Физические свойства
Агрегатные физические свойства являются наиболее очевидными агрегатными свойствами, и они также имеют самое прямое влияние на то, как заполнитель работает либо как компонент материала дорожного покрытия, либо как сам по себе как материал основы или подосновы.Обычно измеряемые физические агрегатные свойства (Roberts et al., 1996):
Это не единственные физические свойства агрегатов, а, скорее, наиболее часто измеряемые. Тесты, используемые для количественной оценки этих свойств, в основном являются эмпирическими. Физические свойства агрегата могут изменяться со временем. Например, недавно измельченный заполнитель может содержать больше пыли и, следовательно, быть менее восприимчивым к связыванию с асфальтовым вяжущим
.
Заполнитель в качестве основного материала
Aggregate часто используется сам по себе как несвязанный базовый или вспомогательный курс.При использовании как таковой заполнитель обычно характеризуется предшествующими физическими свойствами, а также общей жесткостью слоя. Жесткость слоя характеризуется теми же испытаниями, которые используются для определения жесткости земляного полотна.
Щебень — обзор
1.2 Влияние температурно-влажностных условий созревания на деформативные свойства и прочность бетонных элементов
Прочностные и деформационные свойства бетона очень чувствительны к температурным и влажностным условиям созревания.
Известно, что при созревании в благоприятных условиях процесс повышения прочности бетона за счет химической гидратации цемента может длиться долго. Это подтверждается результатами исследований, приведенных ниже.
Микашвили [76] исследовал изменения прочности и деформируемости элементов из гидротехнического бетона, хранящихся от 5 до 40 лет во влажной (водной) среде. В результате измерений он обнаружил непрерывное увеличение прочности элементов в течение заданных интервалов времени, которое в случае сжатия пропорционально логарифму времени.В случае осевого растяжения увеличение прочности оказалось незначительным по сравнению с увеличением прочности на сжатие. Данные, приведенные в [76], свидетельствуют о том, что высокое значение модуля упругости является характерной чертой многолетнего бетона, хранящегося в водной среде.
Гнутов и Осипов [77] провели исследование прочности бетона, хранящегося в благоприятных условиях для роста прочности в течение 32 лет. В качестве опытных образцов использовались керны диаметром 11,0 см, взятые из водопровода канальной насосной станции.Образцы керна были пробурены из горизонтально направленных скважин в стенках акведуков. Часть скважин, из которых были пробурены керны, находились под водой на протяжении всей эксплуатации конструкции.
В результате испытаний, проведенных авторами [77], было установлено, что прочность бетона, находящегося> 30 лет во влажных условиях, в 3,5 раза превышает его прочность, зафиксированную в возрасте 28 дней.
Результаты исследований прочностных и деформационных свойств бетонных элементов, выдержанных в различных влажных условиях, отражены в рассмотренных ниже статьях.
В 1956 году Гудавердян опубликовал статью, посвященную исследованию влияния влажной среды на прочность на сжатие трех составов бетона [78]. Использовались тяжелый бетон из кварцевого речного песка и базальтового камня, бетон из заполнителей из литоидной пемзы и туфобетон из туфа Ереванского месторождения. Марка цемента 32,5 МПа. Некоторые образцы для испытаний в виде усеченных конусов с размерами d = 15 см, D = 20 см и H = 15 см и кубов с размером кромки 10 см после извлечения из формы хранились в лаборатории в нормальных условиях твердения, а другие образцы за пределами лаборатории хранились под навесом.Исследования проводились летом.
Согласно данным, приведенным в [78], тяжелый бетон, выдержанный в течение месяца в среде с низкой влажностью, набирает лишь около 50% прочности, которую он мог бы получить при нормальных условиях твердения. Указанная разница для литоидно-пемзового бетона и для туфобетона составила 30% и 10% соответственно.
Худавердян объяснил выявленную низкую чувствительность созревания литоидно-пемзового бетона и особенно туфобетона к условиям низкой влажности способностью пористых заполнителей накапливать значительное количество воды при производстве бетона, что сохраняет бетон во влажном состоянии в течение длительного времени определенный период времени, тем самым способствуя интенсификации процесса гидратации цемента.
Подобные исследования были проведены в 1970 г. Ботвиной [79].
На этот раз объектами исследования явились газосиликат из природного суглинка и негашеной извести, из негидратированного лёсса и негашеной извести, из кварцевого песка и извести, а также виброформованный силикатный бетон из известково-лёссового вяжущего как на обезвоженном, так и на природном лёссе. Часть образцов в виде кубов размером 10х10х10 см и балок размером 4х4х16 см в течение 5 лет подвергалась воздействию среды с условиями сухого жаркого климата. Другая часть исследуемых образцов (контрольные образцы для испытаний) хранилась в обычных лабораторных условиях в течение указанного периода времени. В ходе исследований температура воздуха в летний период достигала 50–65 ° C, а относительная влажность — 5–8%.
В результате проведенных измерений было установлено, что прочность на сжатие и изгиб испытуемых образцов силикатного бетона, оставленных после извлечения из формы в течение 5 лет вне лаборатории, примерно на 23–30% меньше прочности контрольного образца. тестовые образцы [79].
Качественно подобное явление для прочности и модуля упругости бетона было обнаружено в идентичных исследованиях, проведенных Плауманом [80], а также Ашрабовым и др. [81]. В первом случае в качестве образцов использовались цилиндры с соотношением диаметров и высот 1: 3 из цементно-песчаного материала, а во втором — призмы размером 10 × 10 × 40 см из тяжелого бетона.
Исследования, проведенные Хасэгава Тосио, Сугияма Масаси и др. [82], также похожи на рассмотренные выше.
В этих исследованиях сушка бетона в конструкциях с разными значениями удельной открытой поверхности и времени извлечения из формы моделировалась в течение 2 лет на испытательных образцах-призмах размерами 10 × 10 × 20 см и 20 × 40 × 40 см. Влажность среды также варьировалась.
В результате измерений, проведенных авторами [82], было установлено, что в ряде случаев увеличение прочности бетона сменяется ее снижением через несколько месяцев. Также было установлено, что при снижении относительной влажности среды с 85% до 60% наблюдаемое снижение прочности бетона достигает 11.2 МПа, а модуль упругости достигает 50%.
Ниже рассмотрены результаты исследований изменения прочностных и деформационных свойств образцов из цементно-песчаных растворов и бетонов, созревших после отливки сначала в условиях влажности, а затем в среде с низкой влажностью.
Хак и Кук исследовали влияние снижения начальной высокой степени влажности среды на динамический модуль упругости образцов, изготовленных из тяжелого бетона, цементно-песчаного раствора и портландцементной пасты [83]. В этих исследованиях состав исследуемых материалов варьировался: водоцементное соотношение — от 0,3 до 0,5, конусный осадок смесей — от 10 до 60 мм. Экспериментальные призматические образцы имели размеры 10,2 × 10,2 × 50,8 см.
В результате проведенных исследований было установлено, что независимо от вышеперечисленных факторов для всех рассмотренных случаев потеря влаги приводит к значительному снижению динамического модуля упругости этих материалов, созревших до начала этот процесс во влажных условиях.При этом наибольшее снижение данного показателя зафиксировано в образцах из цементно-песчаного раствора и портландцементного теста.
Явление, обнаруженное авторами [83], объясняется тем, что усадка, возникающая в результате высыхания, приводит к необратимым изменениям в структуре указанных материалов, что является причиной снижения их динамических характеристик. модуль упругости.
В работе Карапетяна приведены экспериментально установленные закономерности изменения прочностных и деформационных свойств образцов из разных типов бетона, сначала выдержанных во влажных условиях, а затем в среде с пониженной влажностью в течение 10–20 лет [84] .
Исследования проводились на двух составах легкого бетона — из песка и из литоидно-пемзового щебня, на одном составе смесового бетона на основе песка из литоидной пемзы и базальтового щебня и на одном составе тяжелого бетона на основе кварцевого песка. и базальтовый щебень. В качестве вяжущего использовался портландцемент марки 40 МПа. Экспериментальные образцы-кубы с краями 20 см и цилиндры диаметром 14 см и высотой 60 см были извлечены из форм на третьи сутки после изготовления.Далее их хранили при следующих двух режимах влажности:
- I.
Первые 3 года во влажной камере при температуре T = 17 ± 9 ° C и относительной влажности W = 92 ± 4%, затем 18 лет в лабораторной комнате при T = 20 ± 8 ° C и W = 55 ± 11%;
- II.
28 дней в камере влажности, а затем до 10 лет в лабораторных условиях при T = 21 ± 7 ° C и W = 50 ± 10%.
На основании проведенных исследований Карапетян установил, что закономерности изменения во времени прочности как кубических, так и цилиндрических образцов из легкого бетона на основе литоидной пемзы, созревающих по I режиму, качественно имеют одинаковый характер. А именно, при трехлетнем влажном хранении прочность образца увеличивается с уменьшением скорости. После этого при их дальнейшем хранении в течение 18 лет в обычных лабораторных условиях наблюдается длительный процесс снижения прочности этих образцов, но в результате значения прочности как кубических, так и цилиндрических образцов несколько превышают определенные значения. в возрасте 1 мес.
Все сказанное практически применимо к образцам из оставшихся двух составов бетона, выдержанных 21 год по режиму I.Единственное отличие состоит в том, что в последнем случае снижение прочности образцов бетона в результате их хранения в течение 18 лет в среде с низкой влажностью наблюдается в более зрелом возрасте.
Исследование изменения во времени механических свойств образцов литоидно-пемзового бетона, выдержанных в течение 10 лет в условиях влажной среды по указанному выше режиму II, показало, что снижение влажности среды после хранения влаги в течение месяца сначала приводит к замедлению интенсивности роста прочности образца, а затем к длительному процессу его деградации. В результате в возрасте 10 лет конечное значение прочности было ниже, чем его значение к возрасту 1 месяц.
Карапетян также заявил, что изменения тангенциального модуля деформаций образцов бетона, выдержанных как по режиму I, так и по режиму II, имеют те же качественные характеристики, что и в случае прочности.
Итак, согласно экспериментально подтвержденным данным, конечная прочность бетонных элементов, выдержанных длительное время при нормальных условиях твердения, а затем в среде с низкой влажностью, в некоторых случаях может быть ниже их прочности, зафиксированной в возрасте 28 дн.
Это явление требует внимания, поскольку возводимый или уже возведенный бетон, предназначенный для эксплуатации в регионах с низкой влажностью (w↕75%, [1]), не может набрать прочность, предусмотренную проектом, но также со временем может быть потеряна значительная часть уже набранных сил. Этот факт становится очень важным для прогнозирования долговечности и срока службы проектируемых и уже построенных бетонных и железобетонных конструкций, работающих в регионах с указанными выше климатическими условиями.
Ниже обсуждаются результаты экспериментальных исследований, проведенных автором монографии [85], посвященной изучению изменения прочности легкого бетона, выдержанного в течение десятков лет в среде с низкой влажностью.
Эксперименты проводились на образцах кубической формы из трех легких бетонов на основе природных пористых заполнителей. Составы этих бетонов:
- 1.
Литоидно-пемзовый бетон — весовой состав 1: 1.54: 2,40, В / Ц = 0,95.
- 2.
Шлакобетон — состав по массе 1: 2,51: 2,65, W / C = 1,18.
- 3.
Туфобетон — состав по массе 1: 1,80: 2,74, В / Ц = 1,43.
После извлечения образцы хранили в лаборатории при средней температуре 22 ° C и относительной влажности 65% в течение 10–23 лет.
Кратковременные испытания кубиков проводились периодически в определенном возрасте. Для каждого случая было протестировано 3–5 двойных образцов.При этом максимальный разброс значений прочности отдельных образцов по сравнению с их средними арифметическими значениями не превышал + 6% и — 5%.
Отметим, что в опытах с кубиками бетонного состава № 1 с ребрами 20 см они испытывались до 15-месячного возраста, а во всех остальных случаях кубики имели ребра 10 см. Результаты опытов с составами бетонов № 1, 2 и 3 до 10 лет опубликованы в [38, 61, 86].
Проведенные исследования показали, что характер изменения прочности бетона исследуемых составов во времени одинаков: сначала до определенного возраста наблюдается рост показателя прочности бетона, а в дальнейшем — увеличение. возраста бетона приводит к снижению значения прочности (рис.1.4). В результате в возрасте 10 лет прочность бетона состава № 1 (кривая 1, рис. 1.4) оказалась примерно на 20% меньше его прочности в возрасте 28 суток. Падение прочности бетона составов № 2 (кривая 2, рис. 1.4) и № 3 (кривая 3, рис. 1.4) в возрасте 22 и 23 лет соответственно по сравнению с их значениями в возрасте 28 дней то же самое и составляет около 17%.
Рис. 1.4. Прочность легких бетонных кубических образцов изменяется с течением времени.
Отметим, что качественно аналогичное изменение значения прочности бетонных элементов (кубов, призм) во времени в случае тяжелого бетона исследовалось в [87, 88].
На основании результатов прямых измерений вышеупомянутого явления можно высказать некоторые соображения, касающиеся проектирования бетонных и железобетонных конструкций, предназначенных для работы в средах с низкой влажностью.
В практике проектирования бетонных и железобетонных конструкций существует тенденция к экономии цемента с учетом увеличения запаса прочности бетона во времени.В частности, это отражено в упомянутых выше стандартах строительных проектов [1], действующих в странах СНГ, в том числе в Республике Армения. Такой подход, по всей видимости, оправдан тем, что бетон в конструкции набирает заданную проектом прочность, как правило, раньше, чем конструкция воспринимает расчетные нагрузки [87, 89–92] и т. Д.
Такой подход не всегда может быть оправдан, так как в указанных исследованиях за 1 год зафиксировано существенное увеличение прочности бетона по сравнению с его прочностью в возрасте 28 суток (класс прочности на сжатие R 28 , [1]).
Из данных, представленных на рис. 1.4, следует, что на самом деле наблюдается значительное увеличение прочности бетона на указанном выше интервале времени. Однако, согласно той же цифре, прочность бетона, созревшего в условиях с низкой влажностью за 10–23 года, намного ниже, чем R 28 .
В строительных нормах [93], действующих в бывшем СССР, указывалось, что при проведении расчетов конструкций расчетное сопротивление бетона для предельных состояний первой группы в соответствующих случаях следует умножать на коэффициенты конкретные условия труда.Среди последних также был отмечен коэффициент условий работы бетона (м δ1 ), учитывающий продолжительность и характеристики действия эксплуатационных и атмосферных воздействий на строительные конструкции. В частности, в этих стандартах было оговорено, что при расчете постоянных, длительных и кратковременных нагрузок, кроме нагрузок с малой общей продолжительностью действия, а также при расчете специальных нагрузок, вызванных деформациями просадки, набухания, вечная мерзлота и другие подобные грунты:
- •
Для тяжелого бетона и бетона на пористых заполнителях естественного твердения или подвергнутых термической обработке, если конструкция эксплуатируется в условиях, благоприятных для повышения прочности бетона (затвердевание под водой, во влажной почве или при влажности окружающей среды выше 75%) значение m δ1 следует принять равным 1.
00.
- •
Во всех остальных случаях значение указанного коэффициента следует принимать равным 0,85.
Для стандартов стран СНГ [1] как для легкого, так и для тяжелого бетона во втором рабочем случае, упомянутом выше, значение коэффициента условий труда (в этих стандартах этот коэффициент присваивается γ δ2 ) составляет установить равным 0,90 вместо 0,85, как это было принято стандартами [93]. По всей видимости, такая поправка к строительным нормам была сделана на основании вышеупомянутых исследований [87, 89–92].
Однако, как следует из результатов исследований, приведенных в [84, 87, 88] и на рис. 1.4, в условиях низкой влажности окружающей среды значение прочности бетона через некоторое время может быть значительно ниже. чем его ценность приобрела к 28-дневному возрасту. В частности, через 10–23 года прочность легкого бетона на естественных пористых заполнителях снижается до 0,8 R 28 (рис. 1.4).
Данное обстоятельство может служить рекомендательным аргументом для снижения значения коэффициента условий труда γ δ2 не менее чем до 0. 85 при переработке строительных норм [1], как было предусмотрено указанными выше строительными стандартами [93].
Эффект частичной замены щебеночного наполнителя на стеклянный порошок при производстве горячего асфальтобетона Дестав Кифиле, Эмер Тукай Кесон, Абель Тесфайе :: SSRN
Xi’an Dianzi Keji Daxue Xuebao / Journal of Xidian University, Volume 14, Issue 9, 2020, https: // doi.org / 10.37896 / jxu14.9 / 060
10 стр. Добавлено: 17 ноя 2020 Последняя редакция: 28 нояб.2020 г.
См. Все статьи Дестоу КифилеDebretabor University
IIC University of Technology; Университет Амбо; Гражданское и строительное проектирование и управление потоками
принадлежность не указана в SSRN
Дата написания: 12 сентября 2020 г.
Абстрактные
Использование переработанных материалов в дорожном строительстве в настоящее время считается положительным средством обеспечения улучшенных характеристик дорожного покрытия.Это исследование было сфокусировано на оценке влияния порошка отработанного стекла на частичную замену наполнителя из щебня в горячей асфальтовой смеси. Были изготовлены три образца горячей асфальтовой смеси с использованием 5%, 6,5% и 8% щебня в качестве минерального наполнителя с пятью различными содержаниями битума 4%, 4,5%, 5%, 5,5% и 6% соответственно. Из предварительных серийных испытаний на содержание асфальта был выбран наполнитель из щебня 6,5%, обеспечивающий наивысшую стабильность стеклянных порошков. Содержание наполнителя из щебеночной пыли было заменено на 0%, 25%, 50%, 75% и 100% для проверки стабильности Маршала для получения оптимального содержания битума и оптимального содержания наполнителя.Результаты показали 75% замену щебеночной пыли порошком отработанного стекла при содержании битума 5,10%, значении устойчивости по Маршаллу 12,0 кН, значении потока 2,84 мм, пустотах 4,0%, VFB 72,3% и насыпной плотности 2,360 г / см3. Таким образом, смесь 75% порошка отработанного стекла с наполнителем из щебня соответствует минимальным требованиям Эфиопского дорожного управления и Института асфальта.
Ключевые слова: Пыль из щебня, горячий асфальт, стабильность маршала, оптимальное содержание наполнителя, стеклянный порошок для отработанного стекла
Рекомендуемое цитирование: Предлагаемая ссылка
Кифиле, Десто и Кесон, Эмер Тукай и Тесфайе, Абель, Эффект частичной замены щебеночного наполнителя пыли стеклянным порошком при производстве горячего асфальтобетона (12 сентября 2020 г.).Сиань Дяньцзи Кеджи Даксуэ Сюэбао / Журнал Сидянского университета, том 14, выпуск 9, 2020 г., https://doi.org/10.37896/jxu14.9/060, доступно на SSRN: https://ssrn.com/abstract = 3701753A | |
Абсолютная вязкость | Мера вязкости жидкости, равная силе на единицу площади, необходимой для поддержания разности скоростей в одну единицу расстояния в единицу времени между двумя параллельными плоскостями в жидкости, которые лежат в направлении потока и разделены одной. Единица расстояния: обычно выражается в пуазах или сантипуазах. |
Разбрасыватели заполнителей | Часть оборудования, используемая для размещения заполнителя на желаемую глубину на проезжей части или на стоянке. |
Агрегат | Материал или структура, образованные из свободно уплотненной массы осколков или частиц. |
Воздушные пустоты | — это небольшие воздушные пространства или воздушные карманы, которые возникают между частицами заполнителя с покрытием в окончательно уплотненной смеси. |
Асфальт | Смесь темной битумной смолы с песком или гравием, используемая для покрытия дорог, полов, крыш и т. Д. |
Трещины аллигатора | Также называемое усталостным растрескиванием или растрескиванием аллигатора, является распространенным типом повреждений асфальтового покрытия. Обычно это изучается в транспортном разделе гражданского строительства. |
Асфальтобетон | (обычно называемый асфальтом, асфальтом или тротуаром в Северной Америке и асфальтом или битумным щебнем в Великобритании и Ирландии) представляет собой композитный материал, обычно используемый для покрытия дорог, парковок и аэропортов. |
Асфальтовая эмульсия | В коллоидной мельнице асфальт находится в тесном контакте с химическим раствором. Это химическая стабилизация. После слива эмульсия состоит из воды с диспергированными в ней мелкими частицами асфальта, все, что находится между частицами и друг другом, — это вода и химикаты. |
Уплотнение для битумно-эмульсионной суспензии | Смесь медленно схватывающегося эмульгированного асфальта, мелкого заполнителя и минерального наполнителя с консистенцией суспензии. |
Асфальтовое покрытие | Тротуары, состоящие из слоя асфальтобетона поверх несущих слоев, таких как асфальтобетонные основания, щебень, шлак, гравий, портландцементный бетон (PCC), кирпич или блочное покрытие. |
Асфальтовое грунтовочное покрытие | Грунтовка — это нанесение асфальта с низкой вязкостью на гранулированную основу при подготовке к нанесению начального слоя (или поверхностного слоя) асфальта. |
Асфальтовая грунтовка | Жидкий асфальт с низкой вязкостью, который наносят на небитуминозную поверхность, например бетон, для подготовки поверхности к укладке асфальта. |
Асфальт-каучук — Асфальтобетон (AR-AC) | — это материал для дорожного покрытия, полученный путем смешивания измельченных переработанных шин с асфальтом для получения связующего, которое затем смешивается с обычными заполнителями. Затем эта смесь укладывается и уплотняется на дорожном покрытии. |
Асфальтовое связующее покрытие | Липкое покрытие представляет собой тонкий битумный жидкий асфальт, эмульсию или слой разреза, наносимый между подъемниками дорожного покрытия HMA для улучшения сцепления. |
Асфальтены | Асфальтены — это молекулярные вещества, которые содержатся в сырой нефти вместе со смолами, ароматическими углеводородами и насыщенными углеводородами (т.е. насыщенные углеводороды, такие как алканы). Слово «асфальтены» было придумано Буссинго в 1837 году, когда он заметил, что остатки дистилляции некоторых битумов имеют свойства, подобные асфальту. |
Автоматический контроль цикла | Система управления, в которой открытие и закрытие разгрузочной заслонки весового бункера , разгрузочного клапана битумной дробилки и разгрузочной заслонки толкателя приводится в действие с помощью самодействующих механических или электрических механизмов без какого-либо промежуточного ручного управления.Система включает в себя предварительно настроенные устройства синхронизации для управления желаемыми периодами циклов сухого и влажного смешивания. |
B | |
Обратный расчет | Аналитический метод, используемый для определения эквивалентных модулей упругости слоев дорожного покрытия, соответствующих измеренной нагрузке и прогибам. В итеративном методе модули слоев выбираются и регулируются до тех пор, пока разница между расчетным и измеренным прогибами не окажется в пределах выбранных допусков или пока не будет достигнуто максимальное количество итераций. |
Серийный завод | Бетонный завод, также известный как бетонный завод или бетонный завод, представляет собой устройство, которое объединяет различные ингредиенты для образования бетона. Некоторые из этих материалов включают песок, воду, заполнители (камни, гравий и т. Д.), Летучую золу, поташ и цемент. |
Битум | Черная вязкая смесь углеводородов, полученная естественным путем или в виде остатка от перегонки нефти. Применяется для покрытия дорог и кровли. |
Доменный шлак | Является побочным неметаллическим продуктом. Он состоит в основном из силикатов, алюмосиликатов и алюмосиликатов кальция. Расплавленный шлак, который поглощает большую часть серы из шихты, составляет около 20 процентов по массе производства железа. |
С | |
Cape Seal | Обработка поверхности, при которой за герметизацией от стружки следует нанесение суспензионного уплотнения или микроповерхности. |
Клинкер | Каменные остатки сгоревшего угля или печи; кирпич с керамической поверхностью. |
Каменноугольная смола | Густая жидкость черного цвета, полученная в результате разрушительной перегонки битуминозного угля. Он содержит бензол, нафталин, фенолы, анилин и многие другие органические химические вещества. |
Уплотнение | Действие сжатия заданного объема материала в меньший объем. |
Свойства консенсуса | Совокупные характеристики, которые должны соответствовать определенным критериям для соответствия конструкции смеси Superpave.Указанные тестовые значения для этих свойств не зависят от источника, но широко согласованы. К ним относятся грубая совокупная угловатость, мелкая совокупная угловатость, плоские или удлиненные частицы и содержание глины. |
Трещина и седло | Технология трещиноватых плит, используемая при восстановлении покрытий PCC, которая сводит к минимуму воздействие плиты в соединенном бетонном покрытии (JCP) за счет разрушения слоя PCC на более мелкие сегменты. Такое уменьшение длины плиты сводит к минимуму отражающее растрескивание в новых покрытиях HMA. |
Отверждение | Разработка механических свойств битумного вяжущего. Это происходит после того, как эмульсия разрушится, и частицы эмульсии слипнутся и сцепятся с заполнителем. |
D | |
Глубокое прочное асфальтовое покрытие | Тротуары, содержащие не менее четырех дюймов HMA над нестабилизированными базовыми рядами. |
Прогиб | Перемещение участка дорожного покрытия вниз под действием нагрузки. |
Уплотнение | Действие увеличения плотности смеси в процессе уплотнения. |
Дизайн ESAL | Общее количество эквивалентных нагрузок на одну ось 80 кН (18 000 фунтов), ожидаемых в течение расчетного периода. |
Распад | Разрушение дорожного покрытия на мелкие рыхлые фрагменты, вызванное движением транспорта или погодными условиями (например, дрейфом). |
Пластичность | Способность вещества вытягиваться или растягиваться до тонкости. В то время как пластичность считается важной характеристикой асфальтовых цементов во многих областях применения, наличие или отсутствие пластичности обычно считается более значительным, чем фактическая степень пластичности. |
E | |
Трещины краевого шва | Разделение стыка между дорожным покрытием и обочиной, обычно вызванное чередованием смачивания и высыхания под поверхностью обочины.Другими причинами являются оседание уступа, усадка смеси и переезд грузовиков в стык. |
Эмульгатор или эмульгатор | Химикат, добавляемый в воду и асфальт, который удерживает асфальт в стабильной суспензии в воде. Эмульгатор определяет заряд эмульсии и контролирует скорость разрушения. |
Ф | |
Сопротивление усталости | Наивысшее напряжение, которое материал может выдержать в течение заданного количества циклов без разрушения — также называемое пределом прочности — сравните предел выносливости. |
Гибкость | Способность конструкции асфальтового покрытия соответствовать осадке фундамента. Как правило, эластичность асфальтовой смеси повышается за счет высокого содержания асфальта. |
Противотуманное уплотнение | Легкое нанесение разбавленной медленно схватывающейся асфальтовой эмульсии на поверхность состаренной (окисленной) поверхности дорожного покрытия. Противотуманные уплотнения дешевы и используются для восстановления гибкости существующей поверхности дорожного покрытия HMA. |
G | |
Уровень депрессии | Локализованные низкие области ограниченного размера. |
H | |
Горячий асфальт (HMA) | представляет собой смесь примерно 95% камня, песка или гравия, связанных вместе асфальтовым цементом, продуктом сырой нефти. Асфальтовый цемент нагревается, комбинируется и смешивается с заполнителем на установке HMA. |
Я | |
Герметичность | Сопротивление асфальтовому покрытию прохождению воздуха и воды внутрь или через покрытие. |
Дж | |
К | |
Кинематическая вязкость | Показатель вязкости асфальта, измеренный в сантистоксах, проведенный при температуре 135 ° C (275 ° F). |
л | |
Трещины перемычки | Продольные зазоры по шву между двумя полосами мощения. |
Земляное покрытие, обработанное известью | Метод подготовки земляного полотна, при котором грунт земляного полотна и добавленная известь механически смешиваются и уплотняются для получения основного материала с более высоким модулем упругости, чем у материала на месте. |
M | |
Смесь для технического обслуживания | Смесь асфальтовой эмульсии и минерального заполнителя для использования на относительно небольших площадях для заделки ям, углублений и поврежденных участков в существующих покрытиях. Соответствующие ручные или механические методы используются для размещения и уплотнения смеси. |
Асфальт средней твердости (MC) | Битум жидкий, состоящий из асфальтобетона и разбавителя (разбавителя) керосинового типа средней летучести. |
Микроповерхность | Смесь модифицированной полимером битумной эмульсии, дробленого плотного заполнителя, минерального наполнителя, добавок и воды. Он обеспечивает тонкое покрытие от 10 до 20 мм (от 3/8 до 3/4 дюйма) до покрытия. |
Минеральный наполнитель | Мелкодисперсный минеральный продукт, не менее 70 процентов которого проходит через сито 0,075 мм (№ 200). Измельченный известняк является наиболее часто производимым наполнителем, хотя также используются другие виды каменной пыли, гашеная известь, портландцемент и некоторые природные месторождения мелкодисперсных минеральных веществ. |
Модифицированный асфальтобетон — асфальтобетон (MAR-AC) | Высококачественная, тщательно контролируемая горячая смесь модифицированного битумно-каучукового связующего (AR) и хорошо отсортированного высококачественного заполнителя, который может быть тщательно уплотнен до однородной плотной массы. |
№ | |
Натуральный (родной) асфальт | Асфальт, встречающийся в природе, который был получен из нефти в результате естественных процессов испарения летучих фракций, оставляя фракции асфальта.Самый важный природный асфальт находится в отложениях озера Тринидад и Бермудес. Асфальт из этих источников часто называют озерным асфальтом. |
O | |
Заполнитель открытого типа | Один, содержащий менее мелкий заполнитель, в котором пустоты в уплотненном заполнителе относительно большие и взаимосвязаны, обычно на 10% больше. |
п. | |
Класс проникновения | Система классификации асфальтовых цементов на основе пенетрации 0.1 мм при 25 ° C (77 ° F). Существует пять стандартных степеней проникновения для мощения: 40-50, 60-70, 85-100, 120-150 и 200-300. |
Проникновение | Консистенция битумного материала, выраженная как расстояние (в десятых долях миллиметра), на которое стандартная игла проникает в образец вертикально при определенных условиях нагрузки, времени и температуре. |
Растительная смесь (холодная) | Асфальтобетон, изготовленный из медленно затвердевающего асфальта и используемый в основном как временный ямочный материал при закрытии заводов по производству горячих смесей.Холодная смесь используется для ремонта выбоин, но она менее долговечна, чем горячая. |
Агрегат полированный | Частицы агрегата на поверхности тротуара, которые были разглажены дорожным движением. |
Насосная плита | Прогиб под действием проходящих нагрузок, иногда приводящий к оттоку воды и грунта земляного полотна по стыкам, трещинам и краям дорожного покрытия. |
Q | |
R | |
Раствор | Постепенное отделение частиц заполнителя в дорожном покрытии от поверхности вниз или от краев внутрь. |
Дорожное масло | Асфальтовый цемент и масла с низкой летучестью, как правило, аналогичные одной из марок медленно отверждаемых (SC). |
Притирка | — это строительный и инженерный метод, который включает экономию времени и транспортных расходов за счет превращения существующего бетона в щебень на его текущем месте, а не его транспортировку в другое место. |
S | |
Песок-асфальт | Смесь неклассифицированного песка и жидкого асфальта, используемая в качестве экономичной основы или изнашиваемой поверхности для тротуаров. |
Уплотнительное покрытие | Тонкая обработка поверхности, используемая для улучшения текстуры поверхности и защиты асфальтового покрытия. Основными типами герметизирующих покрытий являются противотуманные, песочные, жидкие, микроповерхности, накидные уплотнения, многослойные уплотнения и уплотнения для стружки. |
Листовой асфальт | Горячая смесь асфальтового вяжущего с чистым гранулированным песком и минеральным наполнителем. Его использование обычно ограничивается вкладышами резервуаров и крышками полигонов; обычно укладывается на промежуточный или выравнивающий курс. |
Земляное полотно | Грунт, подготовленный для поддержки конструкции или системы дорожного покрытия. Это основа конструкции дорожного покрытия. |
Т | |
U | |
В | |
Вт | |
Хорошо сортированный заполнитель | Заполнитель с относительно однородными пропорциями, от максимального размера до наполнителя. |
X | |
Y | |
Z |
ВВЕДЕНИЕ Пылеуловитель из пылеулавливающих устройств на асфальтосмесительных установках обычно утилизируется как вся или часть минерального наполнителя в горячих асфальтобетонных смесях.Поскольку эти мелкие частицы получены из природных заполнителей (щебня или песка и гравия), их свойства обычно очень похожи на свойства обычно используемых минеральных наполнителей, таких как каменная пыль или гашеная известь. Пыль на рукавных фильтрах с определенного завода и типа заполнителя следует использовать только на этом предприятии и с типом заполнителя, из которого он был получен, поскольку пыль в рукавном фильтре от разных заполнителей различается по градации, химическому составу и сродству к асфальту. РЕГИСТРАЦИЯ ДЕЯТЕЛЬНОСТИ Существует ограниченное количество задокументированных данных о эксплуатационных характеристиках, связанных с использованием рукавной пыли в качестве минерального наполнителя.Между 1975 и 1980 годами Департамент транспорта Пенсильвании (PennDOT) контролировал работу 12 участков дорожного покрытия в западной Пенсильвании, которые содержали различные источники штрафов за рукавные фильтры. Изучение образцов керна с этих покрытий показало, что необычно большое или непостоянное включение пыли рукавного фильтра привело к получению жестких, хрупких и трудных для уплотнения смесей. (1) Кроме того, в ряде исследуемых смесей наблюдалось высокое содержание воздушных пустот, что ускоряло твердение асфальта и способствовало преждевременному повреждению в виде расслоения, потери мелких частиц и снижения прочности покрытия.Эти проблемы, по-видимому, были более распространены, когда использовалась пыль из рукавных фильтров от заполнителей шлака, по сравнению с пылью из рукавных фильтров из заполнителей щебня. Сердцевины дорожного покрытия для проектов с использованием шлаковой мелочи показали чрезмерное количество мелочи и высокое содержание воздушных пустот (от 9 до 14 процентов), что привело к плохому уплотнению смеси и ускоренному старению асфальта. (1) Ряд государственных транспортных агентств и / или торговых ассоциаций также исследовали использование рукавной пыли или рукавной пыли в качестве минерального наполнителя в асфальтовых смесях.Многие из этих исследований были лабораторными исследованиями, в которых основное внимание уделялось изменчивости пылеуловителя и влиянию такой изменчивости на поведение смеси. В 1976 году Департамент транспорта Калифорнии изучил влияние шести различных источников пылеуловителя на расчетные параметры смеси Hveem. В отчете сделан вывод о том, что максимальное содержание мелочи в рукавных фильтрах 2,0 процента мало влияет на стабильность асфальтовых смесей и, как было обнаружено, благоприятно сказывается на сцеплении смеси. (2) В 1978 году Институт асфальта оценил свойства асфальтовых смесей, содержащих пыль из рукавных фильтров из ряда источников. Свойства смесей с пылью рукавного фильтра сравнивали с известными свойствами коммерческих минеральных наполнителей и смесей наполнитель-асфальт. Хотя в образцах пыли, отобранных с разных заводов, были обнаружены значительные различия в градации, был сделан вывод, что качество рукавной пыли является удовлетворительным для использования в асфальтовых смесях, если качество исходного заполнителя является удовлетворительным. (3) Департамент автомобильных дорог Западной Вирджинии изучил 16 различных источников пыли, содержащейся в рукавных фильтрах, с широким диапазоном размеров частиц и физическими и химическими свойствами. Исследование показало, что мелкие частицы пыли (0,020 мм и меньше) соединяются с асфальтовым вяжущим и действуют как наполнитель. В отчете сделан вывод, что пыль из рукавных фильтров не вредна для смеси для дорожного покрытия и может быть успешно повторно введена в асфальтобетонную смесь. (4) Департамент транспорта штата Вашингтон исследовал гранулометрический состав 12 различных источников пыли из рукавных фильтров и добавил 3 из них в асфальтовые смеси.Градация штрафов за рукавный фильтр значительно варьировалась от завода к предприятию. Вязкость смесей пыли и асфальта значительно варьировалась, а температурная восприимчивость и твердение были разными для разных видов пыли и двух асфальтовых вяжущих. Была обнаружена небольшая корреляция между размером частиц и консистенцией асфальтобетонных смесей. (5) ТРЕБОВАНИЯ К ОБРАБОТКЕ МАТЕРИАЛА Пыль из рукавного фильтра из первичной системы сбора (циклона), если она есть, обычно возвращается в горячий элеватор.Пыль из рукавного бункера может быть возвращена в горячий элеватор, горячий бункер № 1 или весовую камеру. В любом случае пыль высохла и дальнейшая обработка не требуется. ИНЖЕНЕРНЫЕ СВОЙСТВА Некоторые свойства рукавной пыли, которые представляют особый интерес, когда рукавная пыль используется в качестве минерального наполнителя в асфальтовом покрытии, включают градацию, органические примеси и индекс пластичности. Требования к минеральным наполнителям, которые учитывают эти свойства, указаны в Американской ассоциации государственных служащих автомобильных дорог и транспорта (AASHTO) M17 (6) и показаны в таблице 2-2. Градация : Соответствует ли пыль из рукавного фильтра спецификациям градации AASHTO, во многом зависит от того, оборудован ли асфальтовый завод первичным пылеуловителем (циклоном). Первичный коллектор улавливает более крупные частицы, таким образом гарантируя, что остальная часть пыли будет достаточно хорошо сортированной и достаточно мелкой, чтобы постоянно соответствовать требованиям градации AASHTO M17. (7) Таблица 2-2. Технические условия ААШТО М17-83 на минеральный наполнитель для использования в битумных смесях для дорожных покрытий.
Органические примеси : В исследовании, проведенном Национальной совместной программой исследований автомобильных дорог (NCHRP) на пыли из рукавных фильтров, в 26 различных образцах пыли из рукавных фильтров было обнаружено небольшое количество глины или ее отсутствие. Органические примеси редко обнаруживаются в пыли рукавных фильтров, за исключением, возможно, асфальтовых заводов, сжигающих нефть. (8) Индекс пластичности : В том же упомянутом исследовании NCHRP все показатели пластичности 23 образцов были меньше 4. (8) Свойства асфальтобетона, на которые может повлиять пыль из рукавного фильтра, включают проникновение цемента и вязкость, стабильность, модуль упругости и чувствительность к влаге. Пенетрация и вязкость : Предыдущие исследования показали, что увеличение соотношения мелкие фракции / асфальт (с 0,2 до 0,5 по объему) может привести к почти линейному снижению проницаемости полученного вяжущего материала на основе асфальта. (7) Можно ожидать, что вязкость смесей мелкие фракции / асфальт увеличится или станет жестче по мере увеличения соотношения мелкие частицы / асфальт. Стабильность : Общий объем мелочи в смеси будет иметь прямое влияние на стабильность по Маршаллу. По мере увеличения соотношения мелкие частицы / асфальт можно также ожидать увеличения стабильности по Маршаллу, пока не будет достигнута пиковая стабильность при или около 55 процентов насыпного объема мелких частиц в связующем. (1) Модуль упругости : Лабораторные испытания показывают, что можно ожидать увеличения модуля упругости с увеличением содержания пыли. (9) Чувствительность к влаге : Чувствительность к влаге является возможной проблемой в асфальтовых смесях, в которых пыль рукавного фильтра используется в качестве всего или части минерального наполнителя.Рекомендуется, чтобы объем мелкой фракции составлял менее 50 процентов, чтобы свести к минимуму возможность повреждения от влаги или отслоения плотных смесей асфальтового покрытия. (1) ПРОЕКТИРОВАНИЕ Смешанный дизайн Асфальтовые смеси, содержащие мелкие частицы рукавного фильтра, могут быть разработаны с использованием стандартных лабораторных процедур. Чувствительность конструкционных смесей к влаге, определенная в лаборатории, должна определяться с помощью испытания методом погружения-сжатия по Маршаллу (ASTM D1075) с минимальной остаточной прочностью 75%. (10) При проектировании смеси следует внимательно следить за соотношением мелких частиц и асфальта, чтобы ограничить объемный объем мелких частиц менее 50%. Гранулометрический состав пыли рукавного фильтра должен быть хорошо оценен, при этом часть пыли должна быть мельче 0,010–0,020 мм. Процент свободного асфальта следует поддерживать примерно на уровне 40 процентов, поскольку чрезмерное количество пыли рукавного фильтра в качестве наполнителя может привести к образованию асфальтовой смеси, которую будет трудно уплотнять. Отношение мелких фракций к асфальту является лучшим критерием контроля, чем поиск верхнего предела или процентного содержания мелких фракций в смеси. (16) При проектировании асфальтовой смеси необходимо также учитывать место (или места), где пыль собирается и добавляется в дорожную смесь на асфальтовом заводе. Если пыль добавляется из устройства первичного сбора (такого как циклон) и / или рукавного фильтра, необходимо заранее знать относительные пропорции пыли, собираемой из каждого источника, и тщательно контролировать их во время производства асфальта, чтобы гарантировать их постоянство. Было обнаружено, что тип и градация пыли оказывают значительное влияние на механические свойства асфальтовой смеси.Хорошо сортированная пыль ведет себя наиболее предсказуемым образом. Аномального поведения можно ожидать, когда пыль очень однородна (один размер) и мельче 0,010–0,015 мм, или когда пыль крупная и в ней отсутствует материал размером менее 0,010–0,020 мм. (9) Источник заполнителя, из которого образуется пыль из рукавного фильтра, также может влиять на свойства асфальтового вяжущего. Сообщалось, что мелкие фракции из гнейса, ловушки, песка и гравия, а также шлаковые агрегаты приводят к большему увеличению вязкости (и соответствующему снижению пластичности) при введении с высоким соотношением мелкие частицы / асфальт (0.От 3 до 0,5), чем мелочь из карбонатных агрегатов. (7) Объемная объемная концентрация мелких частиц в системе мелкие частицы / асфальт, однако, является основным фактором, вызывающим повышение жесткости битумного вяжущего. (1) Структурное проектирование Обычные методы проектирования конструкции покрытия AASHTO подходят для асфальтовых покрытий, содержащих мелкие частицы рукавного фильтра. ПРОЦЕДУРЫ СТРОИТЕЛЬСТВА Погрузочно-разгрузочные работы и хранение Пыль из рукавного фильтра может подаваться непосредственно из рукавного фильтра в растительную смесь или храниться в бункере перед использованием.Место, где мелкие фракции рукавного фильтра должны быть добавлены в заводскую смесь, зависит от того, является ли завод заводом периодического действия или заводом барабанного смешивания. Во многих случаях пыль из рукавного фильтра может быть только частью минерального наполнителя смеси. В смесительной установке периодического действия мелкие фракции рукавных фильтров могут быть возвращены в смесь для дорожного покрытия в трех разных местах: (1) горячий элеватор, (2) горячий бункер № 1 или (3) ящик для взвешивания. Предпочтительный метод — это прямой возврат пыли в горячий элеватор или в элеватор No.1 горячий бункер, если можно обеспечить надлежащий контроль однородности. Для улучшения равномерности дозирования могут быть добавлены расширительный бункер и система принудительной подачи. Если эти системы не обеспечивают однородность количества мелких частиц, может возникнуть необходимость дозировать пыль в весовой бункер. (11) В барабанной смесительной установке пыль из рукавного фильтра может быть возвращена в одно из четырех возможных мест: (1) конвейер холодной подачи, (2) вход в барабан, (3) разгрузка барабана или (4) в точке, где вводится асфальтовый цемент.Это последнее место наиболее широко рекомендовано государственными транспортными агентствами и производителями барабанных смесительных установок. (7) Введение пыли одновременно с асфальтовым цементом исключает повторное унос пыли в системный газ и обеспечивает хорошее распределение пыли по зоне покрытия. Если пыль попадает в холодную подачу или на входе в барабан, она может быть рециркулирована через системный газ. Наименее желательный метод — вдувание пыли в смесь на выходе из барабана.Внесение пыли вместе с асфальтовым цементом является рекомендуемым методом, а также наиболее широко применяемым государственными дорожными агентствами и производителями барабанных смесительных установок. (7) Смешивание, укладка и уплотнение Те же методы и оборудование, которые используются для смешивания, укладки и уплотнения обычных асфальтобетонных смесей, применимы и для мелочи на рукавных фильтрах. Однако, если соотношение наполнитель / асфальт с мелкими фракциями рукавного фильтра слишком велико, может получиться более густая смесь, и может быть трудно получить заданный уровень уплотнения.Неадекватное уплотнение, по-видимому, является большей проблемой, когда в качестве наполнителя используется очень мелкая пыль рукавного фильтра. Контроль качества Те же процедуры полевых испытаний, которые используются для обычных горячих асфальтобетонных смесей, следует использовать для смесей, содержащих мелкие частицы рукавного фильтра. Смеси должны быть отобраны в соответствии с AASHTO T168, (12) и испытаны на удельный вес в соответствии с ASTM D2726 (13) и плотность на месте в соответствии с ASTM D2950. (14) НЕРЕШЕННЫЕ ВОПРОСЫ Существуют большие различия в эффектах жесткости пыли из рукавного фильтра, которые не полностью объясняются ни тонкостью, ни градацией конкретного источника пыли. Необходимо более полно понять влияние пыли от различных типов заполнителей на уплотняемость асфальтобетонных смесей. Влияние упрочняющего эффекта пылеуловителя на усталостные и механические свойства асфальтобетонных смесей также требует дальнейшего изучения. Диапазон свойств пыли, которые увеличивают расширение асфальта, и влияние расширения асфальта на характеристики жесткости, усталости и старения асфальтоцементного вяжущего также заслуживают исследования. (7) Существует некоторая обеспокоенность тем, что внесение мелких фракций в рукавные фильтры без надлежащей проверки конструктивных свойств смеси может быть причиной тендерных смесей. (15) Нежные смеси характеризуются одним из двух способов.Во-первых, асфальтовую смесь трудно уплотнить при использовании обычных строительных технологий, что обычно проявляется в проталкивании материала под стальной колесный каток. Другой тип нежности связан с медленным схватыванием асфальтовой смеси после укладки, что делает ее чувствительной к повороту колес или сосредоточенной нагрузке, особенно в периоды жаркой погоды. (16) Может потребоваться дальнейшее расследование этой проблемы. ССЫЛКИ
Предыдущая | Содержание | Следующий |
Оценка воздействия мелких частиц на асфальтобетон
% PDF-1.7 % 1 0 obj > / Metadata 2 0 R / Outlines 6 0 R / Pages 3 0 R / StructTreeRoot 7 0 R / Type / Catalog / Viewer Preferences >>> эндобдж 5 0 obj > / Шрифт >>> / Поля [12 0 R 13 0 R 14 0 R 15 0 R] >> эндобдж 2 0 obj > поток application / pdf