Приготовление асфальтобетонной смеси, расчет
Для того чтобы обеспечить получение доброкачественного асфальтобетона, необходимо установить правильное количественное соотношение составляющих его материалов. Одним из условий, обеспечивающих механическую прочность асфальтобетона, является плотность его каменного остова.
Существует несколько методов подбора или проектирования состава асфальтобетона. В настоящее время чаще всего пользуются методом подбора по кривым плотных смесей.
На основании теоретических расчетов установлено, что плотные минеральные смеси получаются при определенном весовом соотношении частиц, диаметры которых относятся как 2 : 1 (например, фракции 16—8 мм, 8—4 мм, 4—2 мм и т. д.).
На рис. 1. Кривые оптимальных смесей.
При подборе состава определяется прежде всего гранулометрический (зерновой) состав всех составляющих: щебня (или гравия), песка и минерального порошка.
Так как особенно важное значение имеет содержание в смеси наиболее мелкой фракции (размером 0,074 мм), то прежде всего устанавливается соотношение исходных материалов, обеспечивающее нужное количество этой фракции.
Предположим, что требуется подобрать мелкозернистый асфальтобетон из материалов, имеющих следующий гранулометрический состав:
Таблица 1.
№№ | Наименование материалов | Частные остатки на ситах, % | |||||||
5 | 2 | 1 | 0,5 | 0,25 | 0,15 | 0,074 | меньше 0,074 мм | ||
1 | Щебень | 60 | 20 | 10 | 5 | 3 | 2 | — | — |
2 | Песок | — | 1,5 | 50 | 30 | 15 | 3,5 | — | — |
3 | Минеральный порошок | — | — | — | — | — | — | 40 | 60 |
Расчет состава каменных материалов для асфальтобетона состоит в нахождении такого весового соотношения имеющихся каменных материалов, при котором одноразмерные фракции в сумме дают требуемое количество данной фракции в смеси, согласно кривым наиболее плотных составов (график 3, рис. 1).
Назначение необходимого количества материалов производится из следующих соображений.
1) Фракция мельче 0,074 мм содержится только в минеральном порошке. Поэтому мы должны взять такое количество минерального порошка, чтобы данной фракции было около 15%:
15X100/ 60 = 25%.
2) Так же рассчитаем количество щебня. Фракция 5 мм содержится в щебне в количестве 60%. В смеси ее должно быть около 25%. Следовательно, для этого потребуется щебня:
25 х 100/ 60 = 42%.
Далее подсчитывается содержание каждой фракции щебня в этой доле, т. е. в 42%.
Содержание этих фракций определяется делением 42% пропорционально частным остаткам:
42/100 Х 60=25,2%; 42/100 X 20 = 8,4%;
42/100 Х 10 ==4,2%; 42/100 Х 5=2,1 % и т, д.
3) Следовательно, песка потребуется:
100—25 — 42 = 33%.
Для проверки правильности произведенного подбора суммируем одноразмерные фракции и наносим на график 3 рис. 1.
Если кривая при этом получается плавная и не выходит за пределы кривых плотных смесей, то при полученном соотношении будем иметь наилучшую смесь. Если кривая получается ломаная и отдельные точки ее выходят за пределы кривых, это указывает на недостаток или избыток соответствующей фракции. Изменив соотношение исходных материалов (но так, чтобы количество фракций 0,074 мм не выходило за пределы плотных смесей), можно улучшить состав. Если же отклонение слишком большое, следует добавить другого материала.
При подборе необходимо учитывать, что при применении гравийного материала и щебня мягких пород следует придерживаться верхнего предела кривых. При твердом и хорошо уплотняющемся дробленом каменном материале можно брать меньшее количество фракций размером 0,074 мм. Оптимальное количество битума определяется по величине временного сопротивления сжатию с проверкой процента объемного водонасыщения.
Для этого изготовляют несколько пробных смесей с различным содержанием битума и определяют временное сопротивление сжатию. При недостаточном количестве битума асфальтобетон получается малосвязный, с низким сопротивлением сжатию вследствие слабого сцепления частиц.
С увеличением количества битума сопротивление сжатию возрастает до известного предела. При избытке битума асфальтобетон становится излишне пластичным и сопротивление сжатию снова уменьшается. За оптимальное количество битума принимается то, при котором получается наибольшее сопротивление сжатию.
Расчет асфальтобетонной смеси
Правильное дозирование материалов имеет большое значение для получения доброкачественного асфальтобетона. Дозирование может производиться по весу (у смесителей типа Д-152 и Д-225) и по объему (у смесителя типа Г-1).
Во втором случае должны быть определены объемные веса всех материалов, входящих в состав асфальтобетона. Зная объемный вес материалов, легко перейти к нужным соотношениям, отвечающим запроектированным в процентах по весу Приведем пример: запроектирован следующий состав асфальтобетонной смеси для приготовления в смесителе Г-1: 50% щебня, 30% песка, 20% минерального порошка, 7% битума.
Полная загрузка смесителя 3 т.
При подборе состава количество каменных материалов принимается за 100%, а битум берется сверх 100%.
3000 X7 / 100 +7 = 196,2 кг.
Общее количество каменных материалов 3000 — 196 = 2804 кг.
Запроектированное количество щебня
50 X 2804/ 100 = 1402 кг.
Объем щебня будет равняться 1402/ объемный вес
Так же производится расчет и остальных материалов.
При весовой дозировке необходимо учитывать влажность материала.
Расчет производится следующим образом: предположим, что влажность песка 5%.
Весовое количество сухого песка подсчитывается так же, как и в приведенном выше примере, т. е.
25 X 2804 /100 = 701 кг.
Так как во влажном песке содержится 95% сухого песка и 5% воды, т. е 701 х 5/ 95 = 37,9, или, округляя, 38 кг.
Следовательно, влажного песка нужно взять 701 кг+38 кг=739 кг.
При объемном способе получается менее точная дозировка, поэтому предпочтение следует отдавать весовому способу.
Асфальтовое вяжущее вещество и мастика
Асфальтовая мастика представляет собой твердое вещество темно-бурого или черного цвета
Асфальтовый порошок
Асфальтовый порошок получается в результате тонкого помола асфальтовых известняков или доломитов, содержащих обычно от 4 до 8% твердого тугоплавкого битума. Из-за низкого содержания битума порошок без добавки битума в строительствe не применяется; его смешивают с битумом на заводе или на стройке и получают асфальтовое вяжущее вещество.
Асфальтовая мастика
Асфальтовая мастика представляет собой (при нормальной температуре) твердое вещество темно-бурого или черного цвета. Она выпускается заводами в виде квадратных плит толщиной 10-12 см и весом 32 кг. Изготовляют ее, смешивая в определенном соотношении молотую асфальтовую породу с расплавленным нефтяным битумом. Однородную расплавленную смесь разливают в формы, где она и застывает.
- быть однородной;
- содержать битума не менее 13% от общего веса;
- обладать водонепроницаемостью: при слое толщиной 2 см не пропускать воду под давлением в 3 ати в течении час;
- предел прочности при растяжении трамбования образцов — восьмерок — должен быть не менее 30 кг/см2.
Альтовая мастика называется также асфальтовым вяжущим веществом и применяется для изготовления литых асфальтовых растворов.
Асфальтобетон ➤ состав, свойства, требования к асфальтобетонной смеси
Дата публикации: 08.04.2020
На самом деле асфальт и асфальтобетон – разные вещи, которые часто путают. Асфальтобетон – это скорее модифицированный вариант асфальта, несмотря на то, что у них много схожих характеристик, сфер применения и свойств.
Разница в том, что асфальт – более природный материал, который получается смешением битумов, песка и гравия. А асфальтобетонная смесь – это микс из битумов, дополнительных компонентов (которые мы знаем, как обычный асфальт) и различных веществ, в том числе химических, для получения совершенно других, улучшенных, свойств.
Состав асфальтобетона позволяет получить более высокую прочность, твердость, увеличенные показатели по износостойкости, термостойкости и нагрузке. Физико механические свойства асфальтобетона позволяют применять его для покрытия дорог с повышенным трафиком, аэродромов, полов хозяйственных и производственных помещений.
Классификация асфальтобетона
Тип асфальтобетона полностью зависит от его характеристик и компонентов, которые применяются в его составе. В первую очередь от размера наполнителя.
Так, асфальтобетон бывает:
- Крупнозернистым составом, с размерами фракций элементов наполнителя до 40 мм
- Мелкозернистым асфальтобетоном, если размер фракции не превышает 20 мм
- Песчаный асфальтобетон – с фракциями до 5 мм.
Кроме того, разновидности асфальтобетона делятся по проценту минерального наполнителя (щебня/гравия) в нем:
- Высокоплотный асфальтобетон с % наполнителя от 60%
- Асфальтобетон А-категории с 50-60% минерального наполнителя
- Асфальтобетон Б-категории – когда процент наполнителя составляет 40-50%
- Асфальтобетон В-категории, если процент наполнителя не больше 40%
Различают так же асфальтобетоны по типу основного каменного составляющего элемента (минерального заполнителя):
- Гравийные
- Щебеночные
- Песчаные
И еще одна классификация асфальтобетонных смесей зависит от остаточной его пористости:
- Высокоплотные, когда остаточная пористость не превышает 2%
- Плотные, с пористостью от 2 до 7%
- Пористые, если пористость превышает 7% и до 12%
- Высокопористые смеси – с пористостью 12-18%
Кроме того, бывает холодный, теплый и горячий асфальтобетон, который различают по типу вяжущего битумного компонента и температуре, которая требуется для укладки смеси.
- Горячий асфальтобетон укладывается при 120 °С (важно – не ниже этой температуры), сразу же после приготовления
- Теплый асфальтобетон изготавливают и сразу укладывают при температуре от 70 °С
- Холодный асфальтобетон может использоваться для укладки при температуре от -5 °С
Из чего состоит асфальтобетон
Состав асфальтобетонной смеси чаще всего самый стандартный, когда для основы берется битум (его используют в качестве вяжущего вещества) и минеральный заполнитель. В качестве заполнителя используется песок, минеральные порошки и гравий или щебень.
Задача гравия служить наикрупнейшим заполнителем, создать остов будущего покрытия, а минеральные порошки заполняют получившиеся пустоты, созданные щебнем и песком. Помимо чистых фракций щебня в производстве асфальтобетона часто используются смеси различных фракций – можно встретить комплекс и асфальтобетона категории В, и категории Б, и асфальтобетона высокоплотного. Так обычно получается самый распространенный асфальтобетон. Состав обязательно дополняется минеральными порошками, которые получают при дроблении горной породы, например, доломита или известняка.
Так же асфальтобетон состоит из смеси битума и различных компонентов, которые улучают свойства битума и улучшают общие физические и механические свойства асфальтобетона. Это могут быть как специально изготовленные добавки, так и различное сырье, например, резина в гранулах.
Чаще всего состав смеси определяется индивидуально для каждой задачи, так как для изготовления смеси асфальтобетона требуется понимать условия его будущей эксплуатации и различные погодные и нагрузочные характеристики места укладки покрытия.
Требования к асфальтобетону
Основные требования, которые выдвигают к асфальтобетону, зависят от его прочности. Так, предел прочности асфальтобетонной смеси к усилию его сжатия должен составлять не меньше 10 при температуре +50°.
Коэффициент теплоустойчивости асфальтобетона должен не превышать 3,0. Водостойкость (или отношение предела прочности смеси к усилию сжатия водонасыщенного и сухого образца конкретной смеси асфальтобетона) – не меньше 0,9. А водонасыщение по объему – 1-3% и не больше.
Все эти свойства асфальтобетона напрямую зависят от качества вяжущего составляющего и различных заполнителей, которые влияют на прочность, плотность, водо- и термостойкость асфальтобетона.
Механические свойства асфальтобетона
Основные механические и физические свойства асфальтобетона зависят от условий, в которых он будет эксплуатироваться. Кроме механического воздействия от проезжающих автомобилей, асфальтобетон подвергается воздействию атмосферных осадков, талых вод, солевых смесей от наледи, смене температуры окружающей среды.
Основное свойство асфальтобетона, на которое обращают внимание при проектировании смеси – это его прочность. Это прочность при сжатии при температуре +50°С, прочность при сжатии при температуре +20°С, прочность при сжатии при температуре в 0 градусов. Для каждого из этих температурных режимов асфальтобетон должен показывать определенную прочность.
Кроме того, для асфальтобетона важны:
- Сдвигоустойчивость, которая влияет на долговечность уложенного покрытия. Должна составлять от 0,66 до 0,91 при оценке по коэффициенту трения
- Сцепление при сдвиге, которое указывает на плотность, с которой будет сцепляться колесо и дорожное покрытие (показатели должны варьироваться в пределах 0,6 – 0,95)
- Водостойкость – это соотношение между прочностями сухого образца и такого же, но напитавшегося водой.
- Износостойкость – она же долговечность. Для асфальтобетонных смесей стандарт износа не должен превышать 0,3-1,0 мм в год.
Средняя плотность асфальтобетона
Для выполнения укладочных работ нужно понимать, какой расход потребует асфальтобетон. Вес смеси в килограммах необходимо разделить на асфальтобетон удельный вес. Так мы сможем узнать цифру расхода асфальтобетонной смеси. Показатели смеси для расчета можно узнать у производителя или из технических таблиц.
Эти расчеты позволят составить смету расходов.
Плотность асфальтобетонной смеси рассчитывается из его остаточной пористости. Типы пористости мы уже описывали ранее. Средняя плотность смеси зависит от фракции, которая используется в его составе: крупнозернистый асфальтобетон 2100 кг/м³, асфальтобетон на шлаковом и кварцевом песке 2350 кг/м³ и 2200 кг/м³ соответственно.
«Асфальтобетонные смеси и асфальтобетон. Проектирование асфальтобетона»
Тема дорог всегда являлась проблемой нашего государства. Поэтому правильный подбор материалов для строительства дороги обеспечит долговечность и надежность дорожной конструкции. А хорошие дороги — это показатель экономической стабильности государства и качества жизни его граждан.
Асфальтобетон является наиболее распространенным материалом для устройства дорожных покрытий. Поэтому знание этого материала, умение правильно ориентироваться в его свойствах и особенностях, разбираться в его разновидностях, умение правильно подобрать состав – это тот необходимый минимум, которым должен обладать техник — дорожник.
Определение предмета исследования: Асфальтобетон, его классификация и особенности применения.
Цель данного исследовательского проекта: запроектировать состав асфальтобетона, обеспечивающий качество и долговечность дорожного покрытия для поставленной ситуационной задачи «Амурский предприниматель открывает в Благовещенском районе близ села Белогорье с/х предприятие (свиноферму). Необходимо усовершенствовать грунтовую дорогу, положив 2х-слойное асфальтобетонное покрытие. Рельеф местности — равнинный, отдельные участки на невысоких холмах. Подобрать вид, тип и марку асфальтобетона для каждого слоя дорожной одежды, сделав упор на местные дорожно-строительные материалы. Категорию дороги принять самостоятельно. Обосновать сделанный выбор и доказать выгоду данного асфальтобетона».
Задачи исследования:
- Изучить асфальтобетон, его свойства и классификацию;
- Изучить и проанализировать условия строительства дороги;
- Запроектироватьвид, тип и марку асфальтобетона в зависимости от климатических и геологических условий местности и категории дороги;
- Рассчитать состав асфальтобетона;
- Доказать целесообразность и выгоду применения данного асфальтобетона.
Гипотеза: Для данной дороги целесообразней применять горячий асфальтобетон.
Асфальтовый бетон — строительный материал в виде уплотнённой смеси щебня, песка, минерального порошка и битума. Перед смешиванием составляющие высушивают и нагревают до температуры 100-160°C. Различают асфальтобетон горячий, содержащий вязкий битум, укладываемый и уплотняемый при температуре смеси не ниже 120°C; холодный — с жидким битумом, уплотняемый при температуре окружающего воздуха не ниже 10°C, а температуре смеси не ниже 50С. Асфальтобетонприменяют для покрытий дорог, аэродромов, эксплуатируемых плоских кровель, в гидротехническом строительстве. В зависимости от нагрузок и климатических условий к асфальтобетону предъявляются соответствующие требования по плотности, прочности, сдвигоустойчивости, водостойкости. Для приготовления асфальтобетона используют фракционированные минеральные материалы и битумы, качество которых регламентируются государственными стандартами.
Требования к материалам:
Щебень и гравий. Для приготовления асфальтобетонных смесей следует применять щебень игравий для строительных работ по ГОСТ 8267-93, щебень из металлургических шлаков по ГОСТ 3344-83.Щебень с размером зерен мельче 20 мм предназначен для приготовления мелкозернистых асфальтобетонных смесей, мельче 40 мм — для крупнозернистых.
Для смесей типа Б III марки, предназначенных для верхнего слоя искусственных покрытий, не рекомендуемся использовать недробленый гравий.
Средневзвешенное содержание зерен пластинчатой (лещадной) и игловатой формы в смеси фракций щебня и гравия должно быть, % по массе, не более:15 — для смесей типа А и высокоплотных; 25 — для смесей типов Б и высокопористых; 35 — для смесей типов В и пористых.
Песок. Природный песок и песок из отсевов дробления горных пород должен соответствовать требованиям ГОСТ 8736.
Для приготовления асфальтобетонных смесей следует использовать природные и дробленые пески, а также отсевы продуктов дробления.
Песок может быть использован в качестве компонента щебенистых смесей, а также как самостоятельный наполнитель в песчаных асфальтобетонах.
В зависимости от крупности природного песка содержание пылеватых и глинистых частиц не должно превышать 3% по массе, в дробленом — 5 %.
Минеральный порошок. Для приготовления асфальтобетонных смесей следует применять активированные и неактивированные минеральные порошки (ГОСТ 16557-78), изготавливаемые путей измельчения карбонатных горных пород.Применение минеральных порошков обязательно в асфальтобетонах I- II марок, предназначенных для использования в I- III климатических зонах. В этих же условиях предпочтение следует отдавать активированным минеральным порошкам, обеспечивающим повышенную плотность, водо- и морозостойкость асфальтобетонных покрытий.
В горячих смесях для плотного асфальтобетона II — III марок допускается использование в качестве минерального порошка тонкоизмельченных основных металлургических шлаков, а также самораспадающихся металлургических шлаков, к которым может быть отнесенаферропыль — отход производства заводов по выплавке феррохромов. Другие порошковые отходы промышленности, например, пыль уноса цементных заводов, золы уноса ТЭЦ и пр. допускается использовать в горячих смесях для плотного асфальтобетона III марки и I- II марок для пористых и высокопористых асфальтобетонов.
Использование всех порошковых отходов промышленности в качестве минерального порошка следуем допускать только при условии полного соответствия всего комплекса физико-механических свойств асфальтобетона требованиям ГОСТ 9128-2009.
Битум. Битумы — это органические вяжущие вещества, состоящие из высокомолекулярных углеводородов: нафтенового, метанового и ароматического, а так же кислородных, сернистых и азотистых производных.
Для приготовления асфальтобетонных смесей применяют нефтяные дорожные вязкие и нефтяные дорожные жидкие битумы. Для горячих асфальтобетонных смесей I и II марок следует применять только битумы марок БНД, а для горячих асфальтобетонных смесей III и IV марок, а также для асфальтобетонных смесей, предназначенных для устройства оснований и нижних слоев покрытий, наряду с битумами марок БНД допускается также применение марок БН соответствующей вязкости.
Выбор оптимального состава асфальтобетона принято производить в зависимости от свойств исходных материалов, характера автомобильного движения и климатических условий местности, что всегда являлось определяющим условием строительства долговечных асфальтобетонных покрытий.
На стадии разработки проекта автомобильной дороги выбирают асфальтобетон определенной разновидности, конкретно для каждого конструктивного слоя дорожной одежды.
В верхних слоях покрытий на дорогах всех категорий используют только плотный асфальтобетон.
Нижние слои покрытий на дорогах I — II категорий устраивают из пористого асфальтобетона, а на дорогах III — IV категорий — из высокопористого асфальтобетона.
Для создания хорошего асфальтового покрытия необходимо обеспечить ему надежное основание с помощью щебня и песка. При этом щебень укладывается более крупными фракциями вниз, а мелкими – в верхние слои покрытия, что не только улучшает качество дороги, но и снижает затраты на ее строительство.
Вид и тип плотного асфальтобетона для верхних слоев покрытий назначают в зависимости от категории дороги и климатических условий района строительства.
Двухслойное асфальтобетонное покрытие, исходя из условия задачи, будем укладывать на дорогу Благовещенск – Белогорье, проходящую через Моховую Падь. Так как дорога предназначена не только для обеспечения нужд фермы, но и обеспечивает транспортное сообщение населенных пунктов и нескольких баз отдыха, расположенных по данной трассе, то интенсивность движения и нагрузка на дорогу будут высокими, по ней будут проходить как легковые, так и грузовые автомобили, обеспечивающие будущую ферму, турбазы и населенные пункты сырьем и вывозящие продукцию.Данная дорога по принадлежности относится к дорогам общего пользования областной собственности. Предполагаемая интенсивность движения составит до 6000 автомобилей в сутки, что соответствует III технической категории дороги.
Анализ климатических условий:
Климат Амурской областирезко континентальный с муссонными чертами. Климат, прежде всего, характеризуют показатели температуры самого холодного и самого тёплого месяцев. Одинаковые показатели разных мест объединяются изотермами. Зима в области суровая. На широте Благовещенска январские температуры варьируют от −24 °C до −27 °С. Бывают морозы до −44 °С.Лето на юге области тёплое. Здесь проходят изотермы от 18 °C до 21 °С. Средние абсолютные максимумы температуры могут достигать до 42 °С.Годовое количество осадков в Благовещенске — до 550 мм.
Для всей области характерен летний максимум осадков, что обусловлено муссонностью климата. За июнь, июль и август может выпадать до 70 % годовой нормы осадков. Возможны колебания в выпадении осадков. Так, летом с возрастанием испарения увеличивается абсолютная и относительная влажность, а весной из-за сухости воздуха снежный покров большей частью испаряется, и следствием этого становится незначительный весенний подъём уровня воды в реках.
Такие климатические условия характерны для III дорожно-климатической зоны. Строительство планируется на весенний период (апрель), то есть будет осуществляться в благоприятный (теплый, сухой) период, поэтому целесообразно использовать горячую асфальтобетонную смесь.Для горячих смесей в средних условиях России (II и III климатические зоны) в основном применяют битумы с вязкостью 60/90, 90/130, 130/200.Главное при выборе марки битума — климатические условия и нагруженность слоев дорожной одежды, то есть категория дороги.Рекомендуемая с учетом климатических условий область применения асфальтобетонов и битумов при устройстве верхних слоев покрытий автомобильных дорог приведена в приложении АГОСТа9128-2009.
Качество битумов БНД выше, чем БН, так как они характеризуются более широким температурным интервалом пластичности и более высокой теплостойкостью, обладают низкой температурой хрупкости, лучшим сцеплением с поверхностью зерен минерального материала, но менее устойчивы к старению.
На основании указанных свойств битумов, учитывая время строительства, условия климата и категорию дороги, выбираем битум марки БНД 90/130.
В районах III дорожно-климатический зоны, характеризующейся достаточно холодным и влажным климатом при строительстве верхнего слоя покрытий на дорогах третьей категории можно использовать горячие смеси типов А, Б, В, Г и Д II марки. Для устройства верхнего слоя покрытия,исходя из технической категории данной дороги,целесообразно использовать мелкозернистую смесь типа Б с содержанием щебня 40 — 50 % II марки, в которой формируется структура переходного типа в большей степени сзамкнутыми порами, препятствующими прониканию воды в покрытие. В тоже время, так как наша дорога проходит по холмам и имеет уклон, данный тип асфальтобетона обладает достаточно шероховатой текстурой, обеспечивающей хорошее сцепление колеса автомобиля с покрытием и гарантирующей безопасное движение.К тому же для повышения шероховатостив верхнийслойпри укатывании асфальтобетона на уклонах будем втапливатьчерный щебень фракции 5–20мм.
Для нижнего слоя нами был выбран высокопористый асфальтобетон, характеризующийся низким содержанием битума. Снижение расхода битума в асфальтобетонных смесях уменьшит стоимость покрытия с обеспечением необходимого качества оснований дорожной одежды. Высокопористый асфальтобетон рекомендован для устройства оснований под асфальтобетонные полотна на дорогах II и III категорий. Применяем высокопористый щебеночный крупнозернистый асфальтобетон марки I, с использованием щебня фракции 20 — 40мм.
В качестве каменных материалов, проанализировав доступность и экономическую выгоду, будем применять: щебень и отсев ООО «Гравелон»,эта компания зарегистрирована по адресу г. Благовещенск, ул. Игнатьевское шоссе, 24 — 303 офис; 3 этаж.На сегодняшний день «Гравелон» – единственная компания, занимающаяся производством щебня в непосредственной близости к Благовещенску: месторождение располагается всего в 15 километрах от областного центра.Продукция ООО «Гравелон» по всем параметрам соответствует требованиям в строительной и дорожной отраслях — это подтверждено лабораторными исследованиями. Песок речной — производства ООО «Фараон», эта компания зарегистрирована по адресу675520, Амурская область, Благовещенский район, с. Чигири, ул. Новая, д. 4.В проекте мы делаем упор на местные, а значит наиболее экономически выгодные, но при этом высококачественные материалы.
Существует два подхода к проектированию составов асфальтобетонных смесей. Первый — подбор смеси с непрерывной гранулометрией каменного материала (так называемый Макадам). Этот вариант гарантирует высокие механические свойства покрытия благодаря расклиниванию мелкими фракциями щебня более крупных фракций. Покрытие, выполненное из смеси с непрерывной гранолуметрией минеральной части, обладает высокой шероховатостью, устойчивостью к сдвигу. Свойства смеси не изменяются в результате отклонения в дозировке минерального порошка и битума, она легко распределяется, формируется и уплотняется в процессе устройства покрытия. При втором способе подбора смеси — по принципу плотного бетона — разрешается применять каменные материалы с окатанной формой зерен и прерывистой гранулометрией. В процессе уплотнения этих смесей образуется асфальтобетон с замкнутой пористостью, покрытие приобретает более высокую водостойкость и морозостойкость. Однако подобные смеси в большей степени склонны к неравномерному распределению в объеме зерен минеральной составляющей и битума. На их физико-механические свойства большое влияние имеют отклонения в дозировке минерального порошка и битума. Для покрытий из смесей, подобранных по принципу плотного бетона, характерна низкая шероховатость.
Мы применяем метод Макадам.
Для приготовления горячей асфальтобетонной смеси (типа Б, марки II) для верхнего слоя покрытия принимаем следующие материалы: щебень гранитный фракционированный (фракции 20 — 10 и 15 -5) с истинной плотностью ρ=2620кг/м3;отсев гранитный с плотностью ρ=2760кг/м3;песок речной кварцевый с плотностью ρ=2700кг/м3;известняковый порошок с плотностью ρ=2910кг/м3.Зерновые составы материалов приведены в частных остатках в %:
Материал | Содержание зерен в %, крупнее данного размера в мм | ||||||||||
20 | 15 | 10 | 5 | 2,5 | 1,25 | 0,63 | 0,315 | 0,16 | 0,071 | <0,071 | |
Щебень 20-10 | 3 | 41 | 54 | 2 | — | — | — | — | — | — | — |
Щебень 15-5 | — | 5 | 38 | 54 | 3 | — | — | — | — | — | — |
Отсев | — | — | — | 13 | 27 | 30 | 10 | 7 | 6 | 4 | 3 |
Песок | — | — | — | — | 12 | 18 | 47 | 5 | 8 | 8 | 2 |
Мин. | — | — | — | — | — | — | 2 | 3 | 5 | 15 | 75 |
Рассчитаем состав минеральных компонентов. Расчёт ведем в табличной форме, рассчитав сначала полные остатки на ситах, а затем полные остатки с учетом долевого содержания каждого материала в минеральной смеси. Долевое содержание каждого материала рассчитываем исходя из рекомендованных ГОСТом.
Расчет минеральной части асфальтобетона в полных остатках приведен в таблице:
Материал | Содержание зерен в %, крупнее данного размера в мм | Д.С. | ||||||||||
20 | 15 | 10 | 5 | 2,5 | 1,25 | 0,63 | 0,315 | 0,16 | 0,071 | <0,071 | ||
Рек. | 0 — 10 | 0 — 20 | 0 — 30 | 40 — 50 | 52 — 62 | 63 — 72 | 72 — 80 | 78 — 86 | 84 — 90 | 88 — 94 | 100 |
|
Щебень 20-10 | 3 | 44 | 98 | 100 | 100 | 100 | 100 | 100 | 100 | 100 | 100 |
|
Щебень 15-5 | — | 5 | 43 | 97 | 100 | 100 | 100 | 100 | 100 | 100 | 100 |
|
Отсев | — | — | — | 13 | 40 | 70 | 80 | 87 | 93 | 97 | 100 |
|
Песок | — | — | — | — | 12 | 30 | 77 | 82 | 90 | 98 | 100 |
|
Мин. | — | — | — | — | — | — | 2 | 5 | 10 | 25 | 100 |
|
Щебень 20-10 | 0,45 | 6,6 | 14,7 | 15 | 15 | 15 | 15 | 15 | 15 | 15 | 15 | 0,15 |
Щебень 15-5 | — | 1,55 | 13,33 | 30,07 | 31 | 31 | 31 | 31 | 31 | 31 | 31 | 0,31 |
Отсев | — | — | — | 2,86 | 8,8 | 15,4 | 17,6 | 19,14 | 20,46 | 21,31 | 22 | 0,22 |
Песок | — | — | — | — | 2,64 | 6,6 | 16,04 | 18,04 | 19,8 | 21,56 | 22 | 0,22 |
Мин. | — | — | — | — | — | — | 0,2 | 0,5 | 1 | 2,5 | 10 | 0,1 |
Сумма | 0,45 | 8,15 | 28,03 | 47,93 | 57,44 | 68 | 79,84 | 83,68 | 87,26 | 91,4 | 100 |
|
Долевое содержание щебня 20-10 определяем по ситу № 10. Рекомендуется 0÷30%, принимаем 15%. Д.С. = =0,15. Для щебня 15 — 5, рекомендуется 40÷50%, а крупного щебня на сите № 5 у нас уже есть 15%, поэтому рекомендуем 25÷35%, Д.С.= =0,31. Для минерального порошка должно быть 100-(88÷94)= 12÷6%, Д.С.= =0,12. Принимаем Д.С. = 0,1. На песок и отсев приходится Д.С.=1-(0,31+0,15+0,1)=0,44. Отсев повышает шероховатость и сдвигоустойчивость покрытия, но удорожает асфальтобетон, поэтому чтобы не повышать стоимость асфальтобетона, принимаем соотношение отсева и речного песка 50/50. Д.С. песка = 0,22, Д.С. отсева = 0,22
Поправ.коэффициент = плотность материала/плотность основного материала
Уточненное содержания минеральных материалов приведено в таблице:
Материал | Истинная плотность | Поправочный коэффициент | Содержание материалов | ||
Доли объёма | Доли массы | % по массе | |||
Щебень 20-10 | 2620 | 1 | 0,15 | 0,15 | 14,6 |
Щебень15-5 | 2620 | 1 | 0,31 | 0,31 | 30,1 |
Отсев | 2760 | 1,05 | 0,22 | 0,23 | 22,3 |
Песок речной | 2700 | 1,04 | 0,22 | 0,229 | 22,2 |
Мин. | 2910 | 1,11 | 0,10 | 0,111 | 10,8 |
Итого |
|
| 1 | 1,03 | 100 |
Содержание битума в смеси выбирают предварительно в соответствии с рекомендациями приложения Г ГОСТа 9128-2009и с учетом требований стандарта к величине остаточной пористости асфальтобетона для конкретного климатического региона. Битума для горячего плотного асфальтобетона типа Б рекомендуется 5 – 6,5%.
Оптимальное количество битума рассчитываем по битумоемкости материалов, входящих в состав асфальтобетонной смеси. Для этого вначале рассчитываем зерновой состав материалов, рассматривая породы из которых произведены каменные материала:
Материал | Остатки на ситах | Размер сит, мм | ||||||||||
20 | 15 | 10 | 5 | 2,5 | 1,25 | 0,63 | 0,315 | 0,16 | 0,071 | < 0,071 | ||
Гранит | П. | 0,45 | 8,15 | 28,03 | 47,93 | 54,8 | 61,4 | 63,6 | 65,14 | 66,46 | 67,34 | 68 |
Ч.О | 0,45 | 7,7 | 19,88 | 19,9 | 6,87 | 6,6 | 2,2 | 1,54 | 1,32 | 0,88 | 0,66 | |
Известняк | П.О | — | — | — | — | — | — | 0,2 | 0,5 | 1 | 2,5 | 10 |
Ч.О | — | — | — | — | — | — | 0,2 | 0,3 | 0,5 | 1,5 | 7,5 | |
Песок | П. | — | — | — | — | 2,64 | 6,6 | 16,94 | 18,04 | 19,8 | 21,56 | 22 |
Ч.О | — | — | — | — | 2,64 | 3,96 | 10,34 | 1,1 | 1,76 | 1,76 | 0,46 |
Количество битума:
Размер фракций
| Частный остаток от целого числа | Битумоёмкость, % | Количество битума,% | ||||
Гранит | Известняк | Песок | Гранит | Известняк | Песок |
| |
20-25 | 0,0045 | — | — | 4,5 | — | — | 0,0202 |
15-20 | 0,077 | — | — | 4,5 | — | — | 0,3465 |
10-15 | 0,198 | — | — | 4,7 | — | — | 0,9306 |
5-10 | 0,199 | — | — | 5,2 | — | — | 1,0348 |
2,5-5 | 0,0951 | — | 0,0264 | 5,5 | — | 3,3 | 1,0348+0,0871=1,1219 |
1,25-2,5 | 0,1056 | — | 0,0396 | 5,7 | — | 3,8 | 0,6019+0,1504=0,7523 |
0,63-1,25 | 0,1254 | 0,002 | 0,1034 | 5,9 | 6,0 | 4,6 | 0,73986+0,012+0,47564=1,2275 |
0,315-0,63 | 0,029 | 0,003 | 0,011 | 6,4 | 7,0 | 4,8 | 0,1856+0,021+0,0528=0,2594 |
0,16-0,315 | 0,0276 | 0,005 | 0,0176 | 7,4 | 7,3 | 6,1 | 0,20424+0,0365+0,10736=0,34801 |
0,071-0,16 | 0,027 | 0,015 | 0,0176 | 8,4 | 9,4 | 7,0 | 0,2268+0,141+0,16544=0,3678 |
<0,071 | 0,0066 | 0,075 | 0,0046 | 18 | 16 | 14 | 0,00891+1,2+0,064=1,27331 |
Итого |
|
|
|
|
|
| 5,80821 |
В лаборатории готовят три образца из асфальтобетонной смеси с рассчитанным количеством битума и определяют: среднюю плотность асфальтобетона, среднюю и истинную плотность минеральной части, пористость минеральной части и остаточную пористость асфальтобетона по ГОСТ 12801-98. Если остаточная пористость не соответствует выбранной, то из полученных характеристик рассчитывают требуемое содержание битума Б (%) по формуле
где V°пop — пористость минеральной части, % объема; Vмпор — выбранная остаточная пористость, % объема, принимается в соответствии с ГОСТ 9128-2009 для данной дорожно-климатической зоны; rб — истинная плотность битума, г/см3;rб = 1 г/см3; rмm — средняя плотность минеральной части, г/см3. Рассчитав требуемое количество битума, вновь готовят смесь, формуют из нее три образца и определяют остаточную пористость асфальтобетона. Если остаточная пористость совпадает с выбранной, то рассчитанное количество битума принимается. Так как мы не имеем возможности отформовать образцы из-за нехватки оборудования, считаем на этом наше исследование законченным.
Проведя нашу исследовательскую работу с нормативной литературой и интернет-источниками,мы получили следующие результаты для решенияконкретной ситуационной задачи:
- Техническая категория дороги – III;
- Дорожно-климатическая зона участка строительства – III;
- Минеральные материалы доставляются: из ООО «Гравилон» — щебень и отсев; из ООО «Фараон» — песок речной кварцевый;
- В зависимости от климатических условий, категории дороги, геологического строения местности, выбран горячий асфальтобетон, приготавливаемый на битуме марки БНД 90/130;
- Для нижнего слоя покрытия – горячий высокопористый щебёночный асфальтобетон I марки, крупнозернистый с использованием щебня фракции 20 – 40 мм;
- Для верхнего слоя покрытия –горячий плотный асфальтобетон II марки, типа Б мелкозернистый с использование щебня фракции 10 – 20мм.
Исходя из используемых материалов, рассчитали состав асфальтобетона для верхнего слоя покрытия:
Щебень гранитный фракции 20 – 10 мм — 14.6%;
Щебень гранитный фракции 15 – 5 мм — 30.1%;
Отсев гранитный — 22,3%;
Песок речной кварцевый — 22,2%;
Минеральный порошок известняковый — 10.8%;
Вязкий битум марки БНД 90/130 — 5,8 % от массы минеральной смеси.
Мы доказали в процессе исследования, что именно горячая асфальтобетонная смесь более целесообразна для устройства покрытия данной дороги, так как она пригодна как для верхнего, так и для нижнего слоя. Рекомендуется для III дорожно-климатической зоны, применима в весенний период строительства. Позволяет в более короткие сроки по сравнению с холодным асфальтом запустить движение автотранспорта по дороге – структура горячего асфальтобетона формируется сразу после уплотнения и остывания асфальта до температуры окружающей среды. Горячий асфальтобетон более устойчив к воздействию автомобилей и атмосферных факторов. То есть, гипотеза подтверждена.
Для нашей страны асфальтобетон – основной материал дорожного строительства и теперь мы знаем «почему», знаем его основные преимущества. По сравнению с цементобетоном, это менее жесткий и более пластичный материал, а большая часть России находится на территории, характеризующейся большим перепадом среднегодовых, а кое-где и среднесуточных температур. Деформативность асфальтобетона обеспечивает его долговечность. Кроме того после затвердевания он становится более ровным, а значит, менее шумным и обладает необходимой шероховатостью. Во-вторых, по уложенному асфальтобетону можно сразу открывать движение и не ждать, пока он затвердеет, в отличие от цементобетона, который набирает необходимую прочность только на 28-й день. В-третьих, покрытие из асфальтобетона легко ремонтируется, моется, убирается, на нём хорошо держится любая разметка.
Литература и интернет источники
- Справочник дорожного мастера.
Строительство, эксплуатация и ремонт автомобильных дорог.М.: «Инфра-Инженерия», 2005
- ГОСТ 9128-2009 Смеси асфальтобетонные дорожные, аэродромные и асфальтобетон. Технические условия.
- СП 78.13330.2012 «Автомобильные дороги»
- ФГУП «Информационный центр по автомобильным дорогам». Автомобильные дороги и мосты. Проектирование состава асфальтобетона и методы его испытаний. Обзорная информация. Выпуск 6. М. 2005.
- Википедия, свободная энциклопедия [Электронный ресурс]. – Асфальтобетон. – Режим доступа: https://ru.wikipedia.org/, свободный
- «Гравилон». Добыча строительного камня, производство щебня. Стабильность, Качество, Надежность. [Электронный ресурс]. – режим доступа: http://gravelon.ru/, свободный
- Доркомтех. [Электронный ресурс]. — Марки и состав асфальта. – Режим доступа: http://dorkomteh.ru/, свободный
Отличия асфальта и асфальтобетона, их состав
Анастасия
Специалист примет заявку и ответит на ваши вопросы!
8 (800) 700-97-90
Содержание страницы
В дорожном строительстве используются многочисленные виды асфальтобетонных смесей. На их выбор оказывают влияние различные факторы. Основные из них – характеристика режима движения автотранспорта и климатические условия в регионе строительства. Кроме этого, выбор материала (асфальт или асфальтобетон) зависит от способа его укладки и применяемого для дорожных работ оборудования.
Асфальт – его особенности
По происхождению асфальт бывает природный и созданный искусственно путем смешивания гравия, песка с битумом, минеральным порошком. Природный материал получается из тяжелых нефтяных фракций при испарении из них наиболее легких компонентов. Добыча асфальта осуществляется из пластовых жильных залежей, а также там, где нефть имеет естественный выход нефти на поверхность.
В природном асфальте количество смолисто-асфальтеновых веществ может достигать до 75 процентов, масел – до 40 процентов. Масла придают битуму подвижность и текучесть. Сравнивая между собой асфальт и асфальтобетон в чем разница между ними, следует обратить внимание, что внешне природный асфальт трудно отличить от обычной смолы. Поэтому его называют горной смолой. Асфальтобетонная смесь часто содержит в своем составе крупные фракции щебня, гравий.
Выбирая асфальтобетон или асфальт, сравнивая их характеристики, отмечены положительные качества искусственного материала. Он выдерживает большие нагрузки, обладает лучшей демпфирующей способностью. В зависимости от процентного содержания битума, щебня, минерального порошка, песка производится асфальт следующих марок: 1, 2, 3.
Асфальтобетон – его разновидности и свойства
Получаемый в результате уплотнения асфальтобетонной смеси и включения в ее состав других добавок материал называется асфальтобетоном. Для его изготовления применяется смесь следующего состава:
- Минеральный заполнитель (щебень и гравий из высокопрочных горных пород, природный или дробленый песок). В качестве структурообразующего компонента также используется минеральный порошок, который производится путем измельчения доломита, битуминозного известняка, доменных шлаков.
Он необходим для заполнения пор между гравием (щебнем), а также для увеличения прочности битума.
- Битумное вяжущее. В эту категорию входят битумы, а также их модифицированные разновидности. Класс и марка битума выбирается с учетом особенностей климата в местах использования асфальтобетона, категории дорожного покрытия. Требования к дорожным нефтяным битумам содержатся в ГОСТ 22245-90.
Перемешиваются компоненты в нагретом состоянии и при определенной температуре. Вид используемых добавок оказывает влияние на свойства асфальта или асфальтобетона, который подразделяется на следующие виды:
- Щебеночный.
- Гравийный.
- Песчаный.
По типу вяжущего вещества и способу укладки асфальтобетонные смеси бывают:
- Холодные. Для них применяются жидкие нефтяные дорожные битумы. Укладывается смесь при температуре не менее 5°C. Асфальтобетон, одним из компонентов которого является полимермодифицированное битумное вяжущее, и приготовленный без нагревания, может использоваться при температуре от +5 до -5 °C.
Одно из главных свойств, чем асфальт отличается от асфальтобетона, это способность последнего после приготовления долго находиться в рыхлом состоянии. Составы холодных асфальтобетонных смесей отличаются от горячих тем, что в холодных составах содержится большее количество минерального порошка (до 20%), а щебня – не более 50%.
- Теплые. Производятся на вязких и жидких нефтяных битумах. Укладываются при температуре смеси не менее 70°C.
- Горячие. Готовятся на дорожных нефтяных битумах (вязких и жидких). Применяются сразу после изготовления смеси, температура которой должна быть равной или выше 120°C.
К основным характеристикам, определяющим свойства и отличие асфальта от асфальтобетона, относятся:
- прочность;
- водостойкость;
- плотность.
Их значения указаны в ГОСТ 9128-2013 и других нормативных документах.
Выбор сферы применения
Асфальт или асфальтобетонная смесь – что выбрать? Это зависит от областей применения, главной из которых является дорожное строительство. Асфальтобетон находит широкое применение при создании монолитных слоев дорожного покрытия, где ценится высокая механическая прочность, технологичность, более низкая стоимость по сравнению с природным асфальтом. Асфальтобетонные смеси незаменимы при строительстве:
- автомобильных дорог различных категорий;
- взлетных полос на аэродромах;
- автостоянок;
- торговых площадок;
- улиц, тротуаров в населенных пунктах, пр.
В чем разница между асфальтом и асфальтобетоном, из-за которой асфальтобетонная смесь может использоваться для ремонта дорог даже в холодное время года? Различие заключается в том, что смесь не замерзает при температуре до -5°C. Благодаря этому можно увеличить промежуток времени, необходимого для проведения ремонтных работ. Работы с асфальтом можно осуществлять при плюсовых температурах. Зная, чем асфальт отличается от
Подбор состава асфальтобетона и характеристика компонентов смеси
Асфальтобетон – материал для дорожного строительства, набирающий заданную прочность после своего остывания и уплотнения. Купить асфальтобетон можно у компании «ИСО Альтаир» по следующей ссылке — iso-altair.ru.
Состав асфальтобетона
Состав этого материала может различаться для разных марок, но в общем случае в его состав входит вяжущее вещество, каменный наполнитель, песок и различные дополнительные ингредиенты. Рассмотрим эти элементы подробнее.
Вяжущее вещество
Вяжущим элементом для изготовления асфальта служит битум. Вязкость его должна обеспечивать покрытие твердого компонента, но он не должен с него стекать. Битум также должен противодействовать деформированию, при этом сохранять пластичность и не трескаться. Иногда применяется разжиженный битум – праймер, разведенный на растворителе, или эмульсия – смесь с добавлением воды и эмульгатора. Повышение текучести битума ценно при использовании в морозную погоду. При охлаждении смеси вода и растворитель испаряются, а битум сохраняют свои качества. В зависимости от марки асфальта и тепловых показателей смеси (горячая или холодная) подбирается соответствующая марка битума.
Встречаются и целенаправленно разработанные вяжущие составы, например, полимерно-битумные, придающие упругость асфальтовому покрытию, модифицированные и другие.
Каменный наполнитель
В этих целях используется гравий или щебень. Играют важную роль форма и размеры камней и даже их происхождение. Учитывается содержание пыли и глинистых веществ. Наличие плоских и игольчатых камешков снижает качество материала, поэтому их содержание регламентируется ГОСТом, который определяет также размеры зерен.
Что касается происхождения, то щебень может быть получен из горных пород – диабаза, базальта, габбро, серпентина. Осадочные породы также допустимы – известняки и доломиты. Использование металлургического шлака допустимо, если прочность покрытия и его плотность не важны. Гравийный щебень также не используют для получения асфальта высокой плотности.
Песок
Песок входит в состав всех асфальтобетонов, а в песчаных их сортах является единственным минеральным компонентом. Песок может быть добытым в карьере или полученным в качестве отсева при дроблении камней. Для плотных сортов асфальта используют песок, имеющий прочность класса 800 и 1000. Пористые асфальты содержат песок класса 400. Ограничивается также количество глинистых частиц, которое не должно составлять более 0,5 – 1%.
Минеральный порошок
Этот пылевидный компонент заполняет промежутки между частицами гравия и уменьшает внутреннее трение. Зерна порошка размером около 0,074 мм получаются из пылеуловителей. По сути, это – отходы металлургии и цементных производств
Дополнительные компоненты
Эти составляющие служат для придания асфальту заданных свойств. Они могут быть:
§ специально разрабатываемыми и изготавливаемыми – это стабилизаторы, пластификаторы и прочие;
§ отходы или вторсырье – гранулированная резина, сера и другие, более дешевые материалы.
Особенности структуры асфальтобетона
Для разных практических целей (шоссе, улица, велодорожка) необходим разный асфальт. Структура асфальта бывает каркасной и бескаркасной. В первом случае зерна каменной составляющей друг друга касаются и формируют четкую структуру. Во втором случае соприкосновения между ними нет. Оптимальным является использование щебня кубовидной формы, гарантирующего максимальную прочность покрытия и минимальный износ.
Если щебень использован из горных пород, которые трудно полируются, это положительно влияет на свойство сдвигоустойчивости асфальта. Дробленый песок также положительно влияет на этот параметр. Минеральный порошок не должен быть слишком мелким, чтобы не повышалась пористость материала. Если асфальт укладывают в засушливых районах, его пористость должна быть минимальной.
Автор статьи: «ИСО Альтаир»
www.proektstroy.ru — Строительный Интернет портал
Асфальтобетонные смеси Суперпейв → АБЗ «Бетас»
На многие участки отечественных шоссейных и городских дорог приходится повышенная нагрузка – в силу популярности этих трасс, а также из-за особенностей их расположения и эксплуатации.
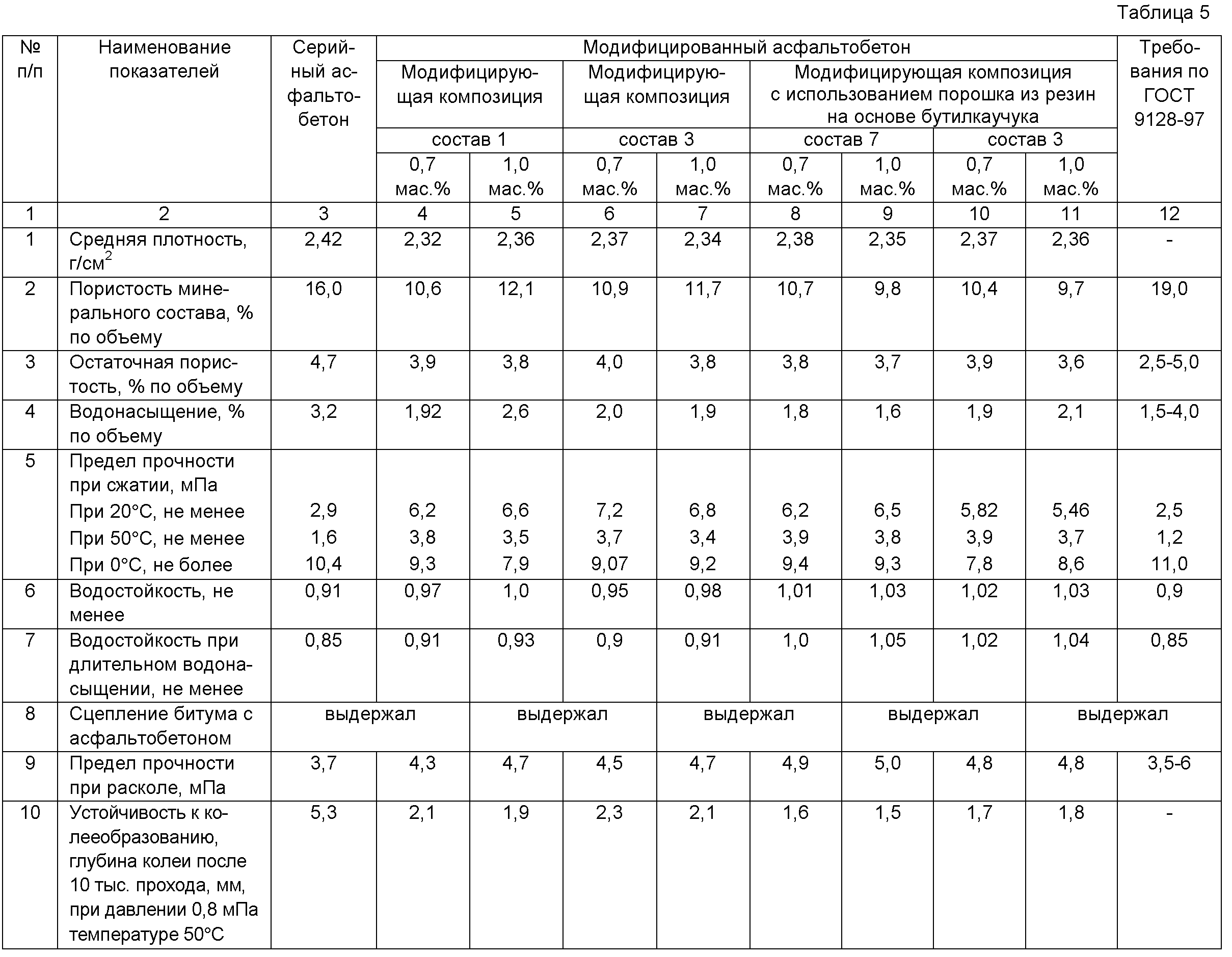
Выходом из сложившейся ситуации становится применение для укладки асфальтобетонных смесей, эксплуатационные характеристики которых выше стандартных. Технологию изготовления таких материалов называют Суперпейв, что дословно переводится как “асфальт в супер исполнении”.
Разработки данных составов асфальтобетона велись долгие годы. Полученные исследователями данные активно применяются проектировщиками. При подборе смеси для укладки на конкретном участке учитывается множество факторов, включая местные климатические условия, уровень и характер деформационных сил, воздействующих на дорожное полотно. Когда необходимый состав асфальтобетона подобран, его тестируют с помощью специального оборудования, и лишь затем применяют на практике.
Критерии подбора и испытания вяжущегоСуществует особая шкала (ее называют PG Grade), с помощью которой рассчитывается взаимосвязь между деформационными свойствами битумного вяжущего материала и температурными условиями его эксплуатации.
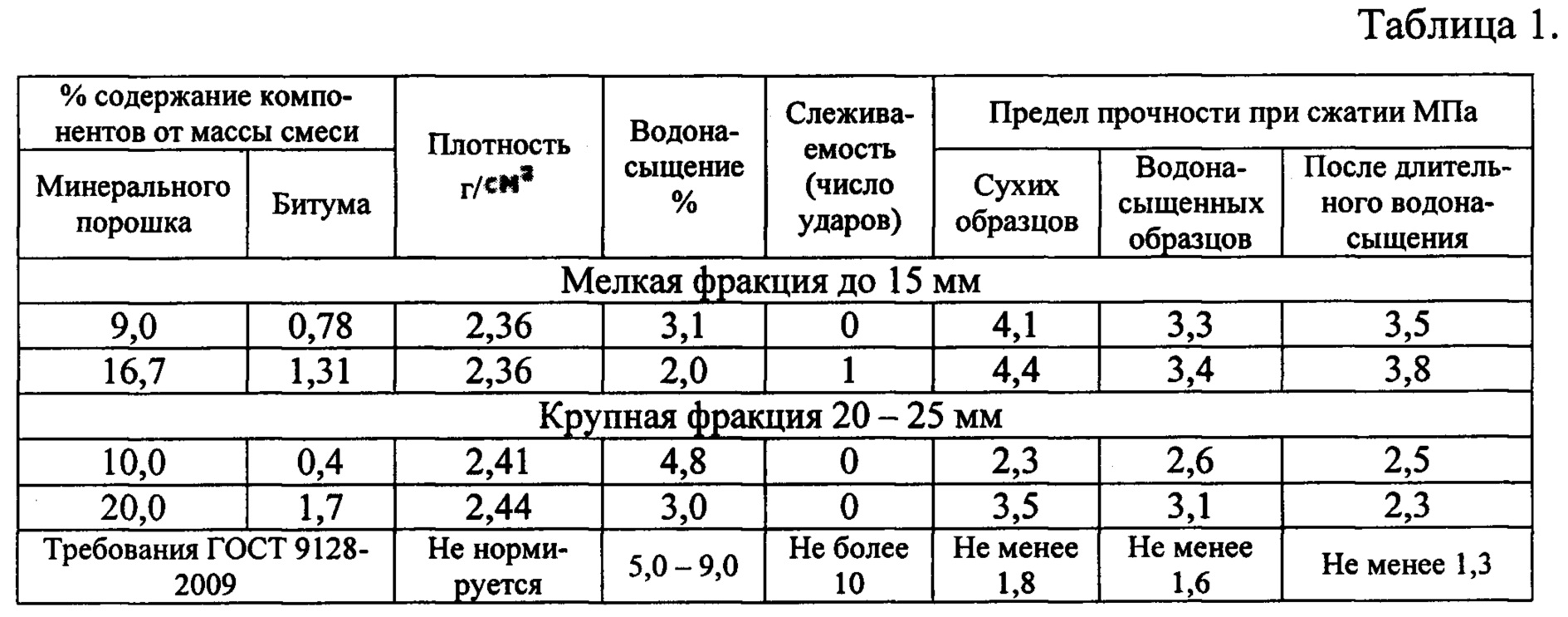
В результате такого подбора сроки эксплуатации дорожного покрытия существенно возрастают. При определении необходимой PG-марки исследователи учитывают полный диапазон температур, в которых будет эксплуатироваться дорожное покрытие.Критерии подбора и испытания каменного материала
Используемая методика позволяет безошибочно определить все важные характеристики щебня. А именно: стойкость к механическому износу и к низким температурам, содержание частиц пыли и глины, средние размеры дробленых, игловатых и лещадных зерен и их процентное соотношение в общей массе материала.
Лабораторные испытания позволяют получить информацию о том, каким способом лучше просеивать каменный материал, чтобы получить его оптимальную плотность в составе смеси асфальтобетона. Кроме того, готовый состав будет обладать наилучшей сопротивляемостью к пластической деформации и к разрушению в результате накопления усталости.
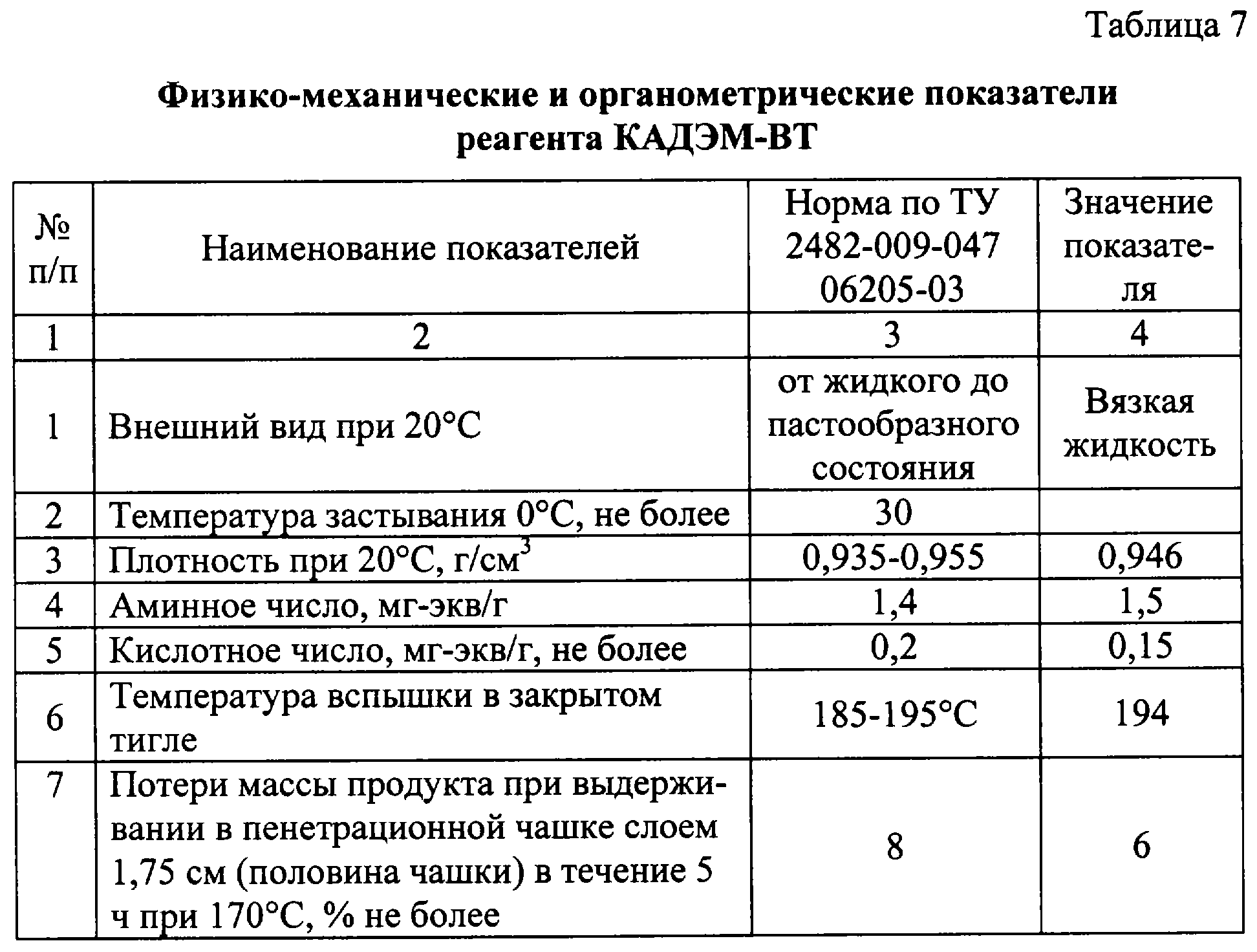
Метод Суперпейв позволяет проектировщикам определить наилучшее сочетание массовых долей щебня и битума в составе готовой смеси. При этом выясняется, какая пористость будет у такого материала после его укладки и уплотнения с помощью дорожного катка. Для получения необходимых данных используется специальный вращательный пресс (гиратор-компактор).
Значение сведений о количестве пор в асфальтобетонном покрытии очень велико. Плохо уплотняющийся материал может быть пригоден лишь для пешеходных тротуаров, но выдержать тяжелые грузовики сможет лишь поверхностный слой с высоким показателем уплотнения.Лучшее основание для укладки асфальтобетона по методу Суперпейв
Метод обустройства оснований сверхпрочных асфальтобетонных покрытий называют холодным ресайклингом. На нижнем слое дороги вероятность возникновения трещин из-за усталости материала окажется минимальной. Дополнительную прочность дорожному полотну придают, в частности, ровно лежащие слои покрытия.
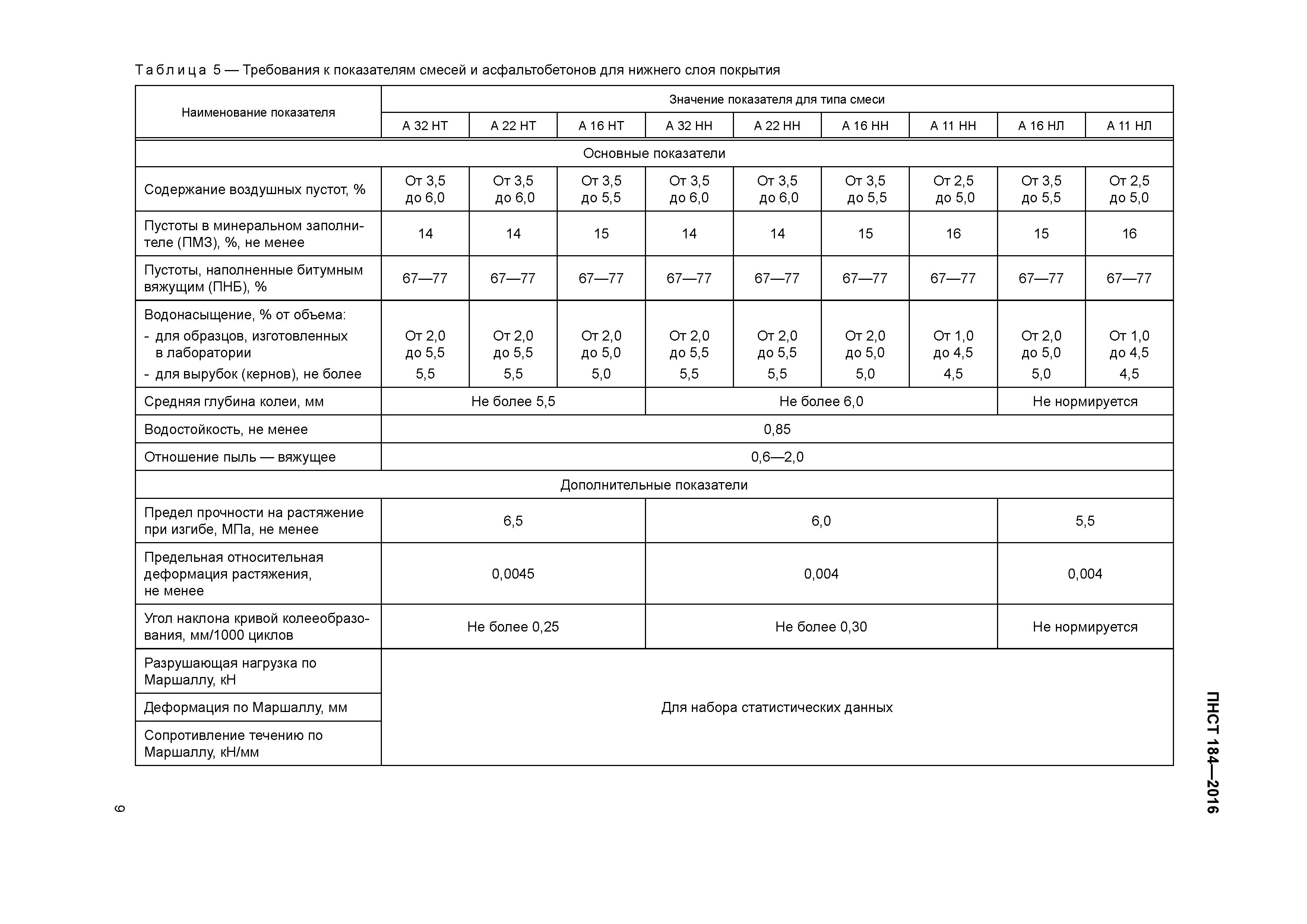
Данная методика предусматривает использование рециклеров – особых машин с фрезерными барабанами, которые перерабатывают старое дорожное полотно и вносят в состав модифицирующие добавки. Полученный новый состав обладает повышенной прочностью и стойкостью к перепадам температур. Выгоды от применения холодного ресайклинга очевидны – исчезают затраты на транспортировку к месту ремонта значительных объемов материалов. Кроме того, уложенная повторно смесь покроет дорогу ровной и прочной плитой, готовой для нанесения сверху финишного слоя асфальтобетона.Практическое применение метода Суперпейв
Расчеты, которыми по методу Суперпейв определяются составы асфальтобетонных смесей, не противоречат действующим в России ГОСТам – они их дополняют. Методика позволяет определить необходимое процентное содержание в смеси вяжущей компоненты, а также параметры гранул щебня в ней.
Готовый асфальтобетон окажется идеально пригодным к эксплуатации на конкретной трассе, в существующих на этой территории климатических условиях.
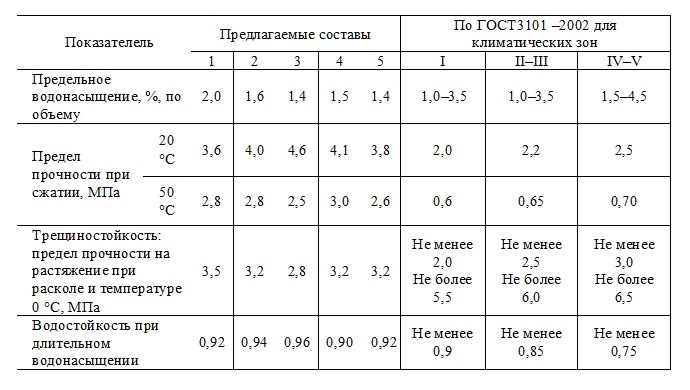
Номер один на дороге: асфальтобетон
Автор: Прогресс Технологий 11.10.2016 3749 Просмотров
Состав и свойства
Представляя собой смесь природных материалов и дорожного битума, асфальтобетон имеет общую для многих регионов мира технологию укладки — при этом характеристики покрытия из него отличаются в зависимости от характера присутствующих (или отсутству- ющих) в его составе полимерных добавок. Благодаря натуральным инертным материалам достигается прочность покрытия, а битум сообщает этому материалу равномерную, единообразную консистенцию.
В качестве инертных материалов для производства асфальтобетона используются измельченные в крошку щебень из природного камня или переработанных бетонных конструкций либо гравий, а также специально подготовленный песок. Битум, как любое вяжущее, в разогретом состоянии имеет скрепляющие свойства. Именно поэтому асфальтобетон чаще кладут горячим. При этом есть и технология холодной укладки этого материала, реализация которой возможна благодаря использованию особого битума, сохраняющего вязкую консистенцию при температурах до пяти градусов по Цельсию. Есть и разновидность этого материала, известная как жидкий битум, не застывающий до –30° С.
Содержание инертных материалов в составе различных асфальтобетонов также различно: 30—40% в группе В, 40—50% в группе Б и, наконец, 50—60% щебня или гравия в группе А. При этом величина щебня в асфальтобетонах, используемых для укладки верхнего слоя дорожных покрытий, составляет 10—20 миллиметров. С учетом тех или иных условий эксплуатации в смесь при ее приготовлении также добавляют полимеры и ПАВ.
Литой асфальтобетон
Разновидность интересующего нас материала улучшенного качества, позволяющего укладывать его без последующего уплотнения поверхности, называется литым асфальтобетоном. Он применяется как в дорожном строительстве, так и при ремонте дороги. Благодаря большему количеству битума и полимерным добавкам, входящим в его состав для улучшения его физических свойств, этот асфальтобетон имеет высокую эластичность. Объем инертных материалов при этом, наоборот, снижен: содержание щебня фракций до 5 миллиметров в смеси может составлять от половины массы до нуля. За счет своей минимальной зернистости такой асфальтобетон и приобретает тягучую консистенцию и не требует уплотнения после укладки. Однако приготовление литого асфальтобетона требует абсолютного соблюдения технологии, включая пропорции всех входящих в его состав материалов. А укладка ос ществляется при температуре от 190 гра- дусов Цельсия. Приготовленный в соответствии с рецептурой и уложенный согласно нормам работы с этим материалом, литой асфальтобетон придает верхнему слою дорожных покрытий особую прочность и износостойкость и служит долго.
Декоративное использование
Асфальтобетон широко применяется для обустройства пешеходных дорожек, площадок, дворов. Для декорирования их площадей выполняются тиснение, рифление, в смесь при приготовлении добавляются окрашивающие пигменты — сурик, крон, окись хрома, цинковые белила, а также цветной щебень фракции до 5 миллиметров и песок из гранита, известняка, мрамора, клинкера. На проезжей части из цветного асфальтобетона могут быть выполнены разделительные полосы, пешеходные переходы — «зебры», другие элементы дорожной разметки.
Чтобы получить литой асфальтобетон нужной яркости, используют осветленные и синтетические битумы. Иногда цветную крошку не добавляют на стадии приготовления смеси, а втирают в верхний слой покрытия в ходе строительства дороги, где она и остается, обеспечивая нужную степень окрашивания.
Расчет расхода смеси
Говоря о физико-механических характеристиках асфальтобетона, нужно отметить, что его плотность может быть разной. Состав со шлаковым песком имеет лучшее уплотнение, его нормативная плотность — 2300 кг/м3. Состав с кварцевым песком имеет плотность 2100 кг/м3. Эти цифры учитываются при расчете объемного веса асфальтобетона и его количества, необходимого для укладки дорожного покрытия. Нормы расхода асфальтобетонной смеси зависят от толщины слоя смеси той или иной марки. Также учитывается удельный вес асфальтобетона, который составляет 2000—2700 кг/м3. Принимаются во внимание и погрешности в зависимости от климатических зон и марки асфальта. Средний же расход дорожного покрытия определяют с учетом толщины слоя и площади поверхности, так как физико-механические показатели практически не отличаются.
К примеру, на сто квадратных метров площади пешеходных дорожек при толщине слоя 15 сантиметров понадобится 37,5 тонны асфальтобетона. Причем, если использовать его литую разновидность, расход будет меньше, так как можно сделать покрытие более тонким без ущерба его качеству. И совсем простой алгоритм расчета расхода асфальтобетона: на каждый квадратный метр дороги при толщине слоя 1 сантиметр необходимо 25 килограммов смеси. Подставляя в эту формулу нужные цифры, независимо от зернистости щебня, можно получить искомый результат. Этой формулой вполне можно обойтись при небольших объемах работ, где погрешности, возникающие при столь упрощенном расчете, будут небольшими.
Применительно к асфальтобетону и его разновидностям, в конечном счете главный вопрос сводится к одному: как получить качественный, долговечный в эксплуатации материал при минимальных затратах на его изготовление, транспортировку и укладку. При этом слово «качественный», помимо всего прочего, подразумевает и параметр качества сцепления колес с дорогой. Чтобы его улучшить, в смеси увеличивают содержание измельченного щебня (вплоть до 80%), а также добавляют в нее измельченные автомобильные покрышки. Кроме того, в состав смеси с той же целью включается до 7,5% мастики. В результате дорожное полотно, выполненное из такого асфальтобетона, который называют щебеночно-мастичным, имеет долгий срок эксплуатации, прочность и хороший коэффициент сцепления колес с дорогой. Чтобы минимизировать появление трещин, выбоин, ям, в щебеночно-мастичный асфальтобетон на стадии приготовления смеси также добавляют мельчайшие гранулы целлюлозы. При такой технологии приготовления расходы на будущий ремонт дорожного полотна сокращаются на 40%. Укладка щебеночно-мастичного асфальтобетона производится в горячем виде. Нужно отметить, что приготовление щебеночно-мастичного асфальтобетона не требует сложного оборудования — главное, чтобы точно соблюдались нормы дозирования всех компонентов смеси.
Асфальт и асфальтобетон
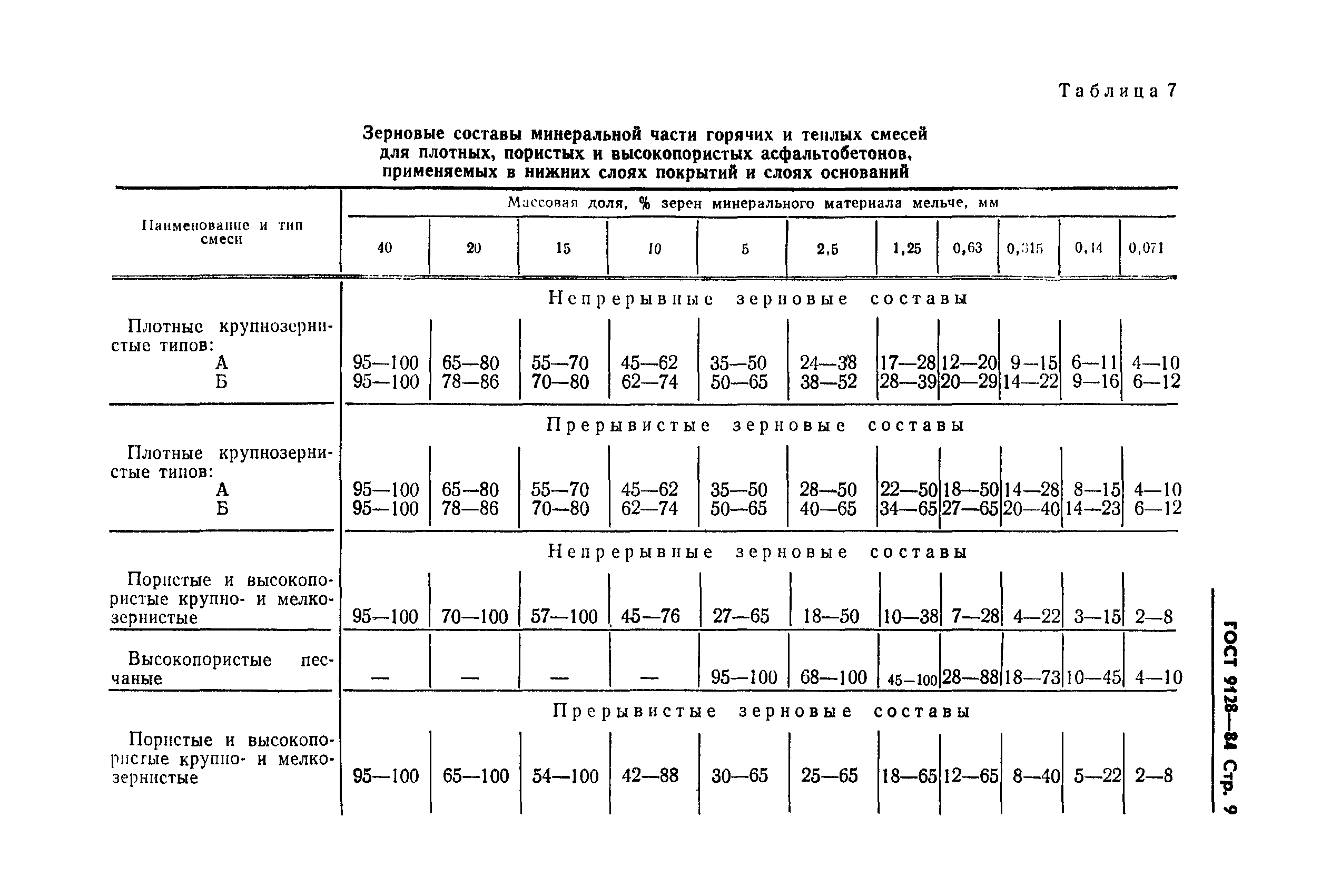
Асфальтобетон, в свою очередь, является в большей степени искусственным материалом, имеющим и более широкую сферу применения. Получают его, как уже было сказано, в результате смешивания битумов и вспомогательных веществ (проще говоря, обычного асфальта) с инертными веществами — обработанным песком, гравием, щебнем из природного камня или вторичного бетона, — которые придают смеси более высокие показатели по нагрузке, твердости, прочности и так далее. Кроме того, асфальтобетонную смесь тщательно уплотняют. Таким образом, асфальтобетон — это, если можно так выразиться, укрепленный асфальт. Кроме того, технология укладки двух этих материалов и применяемое при этом дорожное оборудование также различаются.
Асфальтобетонный завод
Приготовление асфальтобетонных смесей для дорожного строительства и ремонта происходит на основных предприятиях дорожного хозяйства — асфальтобетонных заводах (АБЗ).
На этих предприятиях осуществляются прием и хранение компонентов будущей смеси, при необходимости — дробление и сортировка инертных материалов, а для минеральных — нагрев и сушка, дозировка и подача в бункер материалов, приготовление смеси, складирование и отгрузка готового асфальтобетона.
Основной частью технологического оборудования любого АБЗ является асфальтосмесительная установка. По принципу действия асфальтобетонные установки подразделяются на циклические (периодического действия) и непрерывные (непрерывного действия). К основному технологическому оборудованию также относятся приемные устройства для щебня, гравия, песка, минерального порошка, ПАВ, приемные устройства для каменных материалов, площадки для хранения каменных материалов и емкости для битума с нагревательным оборудованием и битумными насосами, емкости для ПАВ с нагревателями и насосами, емкости для минерального порошка и системы для его подачи; машины для подачи каменных материалов в бункеры смесительных установок; устройство для загрузки готовой продукции, накопители готовой продукции; дробильно-сортировочное оборудование для каменных материалов.
Кроме того, в состав асфальтобетонного завода могут входить оборудование для приготовления и хранения битумных эмульсий, хранилища топлива — газа, дизтоплива, мазута, объекты энергообеспечения и сети электро-, тепло- и водоснабжения, котельные, компрессорные станции, лаборатории, ремонтные мастерские, склады и постройки административно-бытового назначения.
Стационарные асфальтобетонные заводы рассчитаны на эксплуатацию в течение десяти лет и более. По типу размещения бывают прирельсовыми или притрассовыми, в зависимости от того, каким транспортом на них поступает большая часть материалов для приготовления смеси. Передвижные или самоходные АБЗ располагаются на базе прицепов или полуприцепов, реже — на шасси крупнотоннажного грузовика. Существует также промежуточная между двумя этими категориями разновидность — инвентарные АБЗ, которые могут быть разобраны и собраны вновь после перемещения с места на место; как правило, они рассчитаны на эксплуатацию в течение двух-четырех лет. Существует разделение АБЗ на категории в зависимости от количества и суммарной производительности и асфальтосмесительных установок.
Классическая технология приготовления асфальтобетонных смесей включает в себя такие этапы, как предварительное дозирование влажных щебня и песка, нагрев и сушка минеральных материалов в бункерах-дозаторах, их сортировка по фракциям и складирование в «горячих» бункерах, дозирование нагретых материалов по фракциям на весовой площадке и подача в смеситель, нагрев минерального порошка в теплообменнике, его дозирование на весовой площадке или в дозаторе и подача в смеситель. Затем происходит «сухое», без вяжущего, перемешивание минеральных материалов в смесителе, нагрев вяжущего в рабочей емкости, последущее его дозирование и подача в смеситель для «мокрого» перемешивания всех компонентов. После приготовления таким образом готовая асфальтобетонная смесь либо сразу же выгружается в кузов транспортного средства — либо же подается с помощью подъемного устройства («горячий» элеватор или скиповый подъемник) в бункер-накопитель готовой смеси и уже оттуда попадает в кузов машины.
Количество смесительных установок, непосредственно занятых приготовлением асфальтобетонной смеси, может варьироваться в пределах от 2 до 6 на стационарных АБЗ и 1—2 на мобильных. Современные асфальтобетонные заводы, в особенности мобильные (самоходные) и инвентарные (быстромонтируемые), отличаются большим разнообразием моделей и воплощенных в них конструктивных решений. Эта тема, несомненно, заслуживает отдельного обстоятельного разговора, поэтому мы обязательно вернемся к ней в одном из будущих номеров нашего журнала.
Если вы нашли ошибку, пожалуйста, выделите фрагмент текста и нажмите Ctrl+Enter.
Как делают асфальт? | Санленд Асфальт
Как производится асфальт?
10 января, 18 / Ремонт асфальта
Люди ездят и ходят по асфальту каждый день, даже не задумываясь об этом. Асфальтовое покрытие покрывает дороги, взлетно-посадочные полосы и автостоянки, чтобы люди во всем мире могли добраться туда, куда им нужно. Это один из наиболее часто используемых материалов для дорожного покрытия, потому что он прочный, его можно быстро отремонтировать и повторно использовать для строительства других дорожных покрытий.
Какие ингредиенты входят в состав асфальтового покрытия?
Два основных ингредиента, смешанных вместе, чтобы сделать асфальтовое покрытие, — это асфальтовый цемент и заполнитель. Асфальтовый цемент — это высоковязкая жидкая форма нефти. Он действует как клей, который связывает совокупность (небольшие камни) вместе, чтобы создать жесткий и гибкий материал. Асфальтовое покрытие обычно состоит из 5% асфальтобетона и 95% заполнителя. Как правило, на нижних уровнях слоя дорожного покрытия частицы заполнителя более крупные и немного менее угловатые; на поверхностных уровнях частицы более мелкие и более угловатые.Для продления срока службы покрытия могут быть добавлены очень мелкие частицы заполнителя, называемые «мелкими частицами». Помимо асфальтового цемента и заполнителя, компании-производители могут добавлять в смесь определенные химические вещества, такие как гашеная известь для более плотного сцепления или полимеры для повышения гибкости. Состав может несколько отличаться в зависимости от климата места, где будет укладываться асфальтовое покрытие. Асфальт для участков с более теплым климатом становится более твердым, чтобы выдерживать более высокие температуры, а асфальт для участков с более холодным климатом — более мягким.
Как производится смесь для асфальтового покрытия?
Смеси для асфальтовых покрытий обычно производятся на заводе. Все ингредиенты должны быть точно отмерены, чтобы соответствовать типу проекта и климату объекта. Затем толстый битумный цемент нужно сделать более жидким, чтобы его можно было смешать с заполнителем и другими компонентами. Методы разбавления асфальта включают разбавление путем применения растворителя, эмульгирование в воде или нагревание. Отопление — самый распространенный метод.Заполнитель необходимо очистить, просушить и прогреть. Когда и заполнитель, и асфальт нагреваются до нужной температуры, они смешиваются вместе в барабане или толкательной мельнице, которые представляют собой разные типы смесительных машин, которые производят гомогенную смесь. Выбор правильной температуры для процесса имеет решающее значение — производители должны регулировать температуру в зависимости от времени, которое потребуется для транспортировки смеси для дорожного покрытия с завода на строительную площадку, от толщины асфальтового цемента в начале и того, сколько времени потребуется для уплотните смесь после нанесения.
В чем разница между горячим асфальтом и теплым асфальтом?
Горячий асфальт в настоящее время является наиболее часто используемой формой асфальтового покрытия, но теплый асфальт все чаще используется в строительных проектах. HMA требует, чтобы заполнитель был высушен и нагрет, а асфальтовый цемент был нагрет до очень высокой температуры перед их смешиванием. Кроме того, HMA необходимо поддерживать при высоких температурах во время его нанесения и уплотнения.Для изготовления WMA определенные эмульсии, цеолиты, воски или вода добавляются в асфальтовый цемент перед его смешиванием с заполнителем. Этот метод позволяет производить продукцию при гораздо более низких температурах, что снижает потребление энергии, использование нефти и выбросы вредных газов.
Производство асфальта — это разнообразный, но точный процесс. При использовании обученными профессионалами и надлежащем уходе он может прослужить десятилетия.
Что такое асфальт?
Мы едем на нем, ходим по нему, играем и ездим на велосипеде. На него садятся даже наши самолеты, но мы редко останавливаемся и думаем о том, что такое асфальт и как за ним ухаживать. Во-первых, давайте взглянем на ингредиенты асфальта.
Состав асфальта
Так что же такое асфальт и его ингредиенты? На самом деле асфальт состоит из двух основных ингредиентов. Первые агрегаты ; это смесь щебня, гравия и песка. Заполнители составляют около 95% горячего асфальта.
Остальные 5% — это битум .Битум — это черный или темный вязкий материал, который скрепляет агрегаты и состоит из полициклических углеводородов (побочный продукт нефти).
Для более глубокого понимания ингредиентов асфальта, элементарные компоненты асфальта включают углерод, водород, серу, кислород, азот и следовые количества железа, никеля и ванадия.
На самом деле существует несколько различных типов асфальта, и они классифицируются в зависимости от процесса, используемого для связывания заполнителя с битумом.
Типы асфальта
- Горячий асфальтобетон образуется при высоких температурах и является самым прочным из видов асфальта. Обычно он используется в приложениях с интенсивным движением, таких как шоссе и взлетно-посадочные полосы аэропортов.
- Теплый асфальтобетон не требует высоких температур для производства из-за добавления эмульсий, парафинов и цеолитов. Хотя он более безопасен для окружающей среды и рабочих и использует меньше ископаемого топлива при производстве, он не обеспечивает такой же уровень долговечности, как горячий асфальтобетон.Таким образом, он в основном используется для районов с низким трафиком или для исправления ошибок.
- Мастичный асфальт имеет меньшее содержание битума, чем горячий асфальтобетон, и обычно используется для изготовления дорог, пешеходных дорожек, игровых площадок и кровли.
Независимо от типа, любой асфальт требует определенного ухода для обеспечения дополнительной защиты и долговечности.
Прочность асфальта
Если вы когда-нибудь сталкивались с трещиной на асфальтовой дороге, вы знаете, что материал не вечен.Характеристики асфальта могут широко варьироваться в зависимости от ряда переменных, включая наличие влаги, колебания температуры, интенсивность движения и воздействие определенных химикатов. Даже различные ингредиенты асфальта могут определить его долговечность.
Поскольку асфальт может выдерживать вес транспортных средств, он является предпочтительным материалом для дорог, парковок и проездов. Его можно быстро нанести и легко залатать, вдавив его прямо в трещины и выбоины.
Со временем компоненты асфальта могут начать разрушаться и разрушаться в результате интенсивного движения, воздействия элементов, расширения и сжатия. По этой причине использование герметика абсолютно необходимо для надлежащего ухода за любой асфальтированной поверхностью. Несмотря на то, что на рынке имеется ряд герметиков, мы рекомендуем использовать только битумный герметик из каменноугольной смолы из-за его способности создавать эффективный буфер против дорожного движения, воды, масляной соли и других окрашивающих веществ.
Когда компоненты асфальта не защищены слоем герметика, они неизбежно треснут.Если оставить открытыми и не ремонтировать даже небольшие трещины и трещины, это определенно приведет к более серьезным повреждениям, таким как выбоины, крошащийся асфальт и повреждение фундамента. В конечном итоге это приводит к необходимости дорогостоящей замены асфальта.
Какова наиболее эффективная стратегия обслуживания асфальта?
Для домовладельцев важно понимать состав асфальта, потому что его нужно регулярно обслуживать. Асфальтированная подъездная дорога может оставаться в хорошем состоянии десятилетиями, если за ней правильно ухаживать.
Также важно знать, что может негативно повлиять на состав асфальта. Поскольку масло, смазка, газ, соль и трансмиссионная жидкость могут ухудшить качество асфальта и, в конечном итоге, привести к растрескиванию и крошению, эти вещества следует быстро удалить, если они пролились на асфальт.
Заполнение трещин
В рамках профилактического обслуживания следует проверить асфальт на наличие трещин. Даже небольшие, незатронутые или незаполненные микротрещины могут привести к порче компонентов асфальта.Со всеми типами асфальта неизбежно образование трещин. Секрет в том, чтобы заполнить трещины до того, как они разовьются и превратятся в выбоины или более крупные участки осыпающегося покрытия. Есть два типа заполнителей трещин, которые можно использовать на любой асфальтовой или бетонной поверхности. Заливка трещин асфальта холодной жидкостью является высокоэффективной при заделке трещин шириной до ½ дюйма. Продукт прост в использовании и сохраняет трещины на всех типах асфальта заделанными в течение нескольких лет.
Горячий заполнитель для трещин — это прорезиненный асфальтный герметик промышленного качества, предназначенный для заделки трещин шириной до 1 дюйма.Его можно безопасно нагреть в чайнике или расплавителе для заливки трещин и залить в трещины, чтобы защитить от воды, льда и мусора. Он будет держать трещины закрытыми до четырех лет.
Уплотнительное покрытие
Все типы асфальта требуют надлежащего ухода и профилактического ремонта для сохранения их внешнего вида и общего состояния. Из-за характера ингредиентов асфальта подъездные пути следует герметизировать каждые два-три года, чтобы предотвратить окисление, потерю гибкости, растрескивание и рассыпание.В Asphalt Kingdom мы рекомендуем использовать герметик из каменноугольной смолы, который защищает битум от окисления, хрупкости и растрескивания. Его легко наносить с помощью распылителя или ракеля, и он быстро сохнет за три-четыре часа.
Независимо от того, есть ли у вас подъездная дорога или парковка для вашего бизнеса, асфальтовое покрытие должно быть приоритетом.
Бесплатное асфальтовое покрытие
Чтобы узнать, как ухаживать за асфальтом, пройдите бесплатный 4-дневный электронный курс по уходу за асфальтом от Asphalt Kingdom AKPRO.С курсом вы можете узнать все, что вам нужно знать, чтобы защитить свои вложения в асфальт.
ЧТО ЭТО МАТЕРИАЛ? 22 ноября 1999 г. ![]() Том 77, номер 47 CENEAR 77 47 с.81 ISSN 0009-2347 Асфальт Майкл Фримантл
«Около 70 миллиардов фунтов асфальта используется ежегодно только в США, и использование асфальта в Азии резко вырастет в течение следующих 10 лет», — отмечает Артур М. Усмани, главный научный сотрудник Usmani Development Co., Индианаполис, предисловие к его книге «Асфальтовая наука и технология» (Нью-Йорк: Марсель Деккер, 1997). Он добавляет, что асфальтосодержащие материалы находят применение не только в мощении и строительстве дорог, но также в кровле, покрытиях, клеях и аккумуляторах. Широкое распространение асфальта обусловлено его замечательными гидроизоляционными и связывающими свойствами. Например, твердое покрытие дорог зависит от способности асфальта связывать агрегаты из камня и песка. Большинство асфальтов также отлично поглощают свет. Вот почему они черные. Американское общество испытаний и материалов определяет асфальт как цементный материал от темно-коричневого до черного цвета, в котором преобладающими компонентами являются битумы, встречающиеся в природе или получаемые при переработке нефти.Битум — это общий термин для природных или промышленных твердых, полутвердых или вязких вяжущих материалов черного или темного цвета, которые состоят в основном из высокомолекулярных углеводородов. Этот термин включает смолы и пекы, полученные из угля. «Практически весь используемый сегодня асфальт получают из нижней части бочки — то есть последней фракции нефтеперерабатывающего завода после удаления нафты, бензина, керосина и других фракций из сырой нефти», — сказал Усмани C&EN. Асфальты — это очень сложные и плохо охарактеризованные материалы, содержащие насыщенные и ненасыщенные алифатические и ароматические соединения, содержащие до 150 атомов углерода. Их состав варьируется в зависимости от источника сырой нефти. Многие из соединений содержат кислород, азот, серу и другие гетероатомы. Асфальт обычно содержит около 80 мас.% Углерода; около 10% водорода; до 6% серы; небольшое количество кислорода и азота; и следовые количества металлов, таких как железо, никель и ванадий.Молекулярные массы составляющих соединений колеблются от нескольких сотен до многих тысяч. Соединения классифицируются как асфальтены или мальтены в зависимости от их растворимости в гексане или гептане. Асфальтены представляют собой высокомолекулярные соединения, которые нерастворимы в этих растворителях, тогда как мальтены имеют более низкие молекулярные массы и растворимы. Асфальты обычно содержат от 5 до 25 мас.% Асфальтенов и могут рассматриваться как коллоиды мицелл асфальтенов, диспергированных в мальтенах. Многие соединения в асфальте полярны, поскольку они содержат спиртовые, карбоксильные, фенольные, аминные, тиоловые и другие функциональные группы. В результате этой полярности молекулы самоорганизуются в многомолекулярные кластеры с молекулярной массой до 100000. Считается, что адгезия асфальта к заполнителю также зависит от полярного притяжения между молекулами в асфальте и полярными поверхностями заполнителей. «Асфальт имеет уникальную сеть полимерного типа, — говорит Усмани.Хотя это не полимер в строгом смысле этого слова, это термопластичный материал — он размягчается при нагревании и затвердевает при охлаждении. В определенном диапазоне температур асфальт также является вязкоупругим, что означает, что он проявляет механические характеристики вязкого течения и упругой деформации. Хотя асфальт используется в сырой нефти миллионы лет, он не вечен при использовании для мощения дорог. Мало кто из нас мог пропустить тряску по трещинам и выбоинам на дорогах с интенсивным движением. На характеристики асфальта влияет ряд факторов. К ним относятся ее состав и источник сырой нефти, тип и количество используемого заполнителя, наличие влаги, способ строительства дороги, температура и, конечно же, объем движения. В идеале, асфальт, используемый для мощения дорог, должен оставаться вязкоупругим при любых погодных условиях. Однако многие асфальтовые дороги летом размягчаются и страдают от колейности или постоянной деформации, как ее еще называют.При низких температурах нейтральные молекулы асфальта образуют более организованные структурные формы. В результате материал затвердевает, становится хрупким и трескается под воздействием тяжелых транспортных нагрузок. Это называется термическим и усталостным растрескиванием. Асфальты также теряют свою пластичность и, следовательно, твердеют, трескаются или крошатся, когда они теряют свои более летучие компоненты с более низкой молекулярной массой или когда эти компоненты окисляются. Этот процесс известен как старение. Характеристики асфальта можно улучшить с помощью различных методов модификации. Например, продувка воздуха через горячий жидкий асфальт удаляет больше летучих соединений и приводит к получению продукта с более высокой вязкостью. Добавление модификаторов, таких как полибутадиен в виде резиновой крошки из использованных шин и других полимеров, также увеличивает жесткость асфальта. По словам Усмани, не совсем понятно, как полимерные модификаторы устраняют недостатки асфальта. «Чтобы поддерживать текущее использование асфальта и разрабатывать новые приложения, существует острая необходимость в активизации исследований, разработок и инженерии в области асфальтовых материалов», — отмечает он. Новости химии и машиностроения |
ПРОИСХОЖДЕНИЕ Восстановленное асфальтовое покрытие (RAP) — термин, используемый для удаленных и / или повторно обработанных материалов дорожного покрытия, содержащих асфальт и заполнители. Асфальтовое покрытие обычно удаляется фрезерованием или удалением на всю глубину. Фрезерование подразумевает удаление поверхности покрытия с помощью фрезерного станка, который может удалить толщину до 50 мм (2 дюйма) за один проход. Удаление на всю глубину включает рыхление и разрушение тротуара с помощью рожка носорога на бульдозере и / или пневматических отбойных молотков.В большинстве случаев сломанный материал забирается и загружается в самосвалы с помощью фронтального погрузчика и транспортируется на центральный объект для обработки. На этом предприятии RAP обрабатывается с помощью ряда операций, включая дробление, просеивание, транспортировку и штабелирование. Хотя большинство старых асфальтовых покрытий перерабатывается на центральных перерабатывающих предприятиях, асфальтовые покрытия можно измельчать на месте и включать в гранулированные или стабилизированные слои основания с помощью самоходной измельчающей машины. Надежные данные о генерации RAP недоступны для всех государственных дорожных агентств или местных юрисдикций.Основываясь на неполных данных, предполагается, что ежегодно в Соединенных Штатах может производиться до 41 миллиона метрических тонн (45 миллионов тонн) РАП. (1) Дополнительную информацию по переработке асфальтового покрытия можно получить в следующих организациях: Национальная ассоциация асфальтобетонных покрытий 5100 бульвар Форбс Лэнхэм, Мэриленд 20706-4413 Институт асфальта Research Park Drive Лексингтон, Кентукки 40512 Ассоциация по переработке и регенерации асфальта # 3 Церковный круг, офис 250 Аннаполис, Мэриленд 21401 ОПЦИИ ТЕКУЩЕГО УПРАВЛЕНИЯПереработка Большая часть производимого ПДП перерабатывается и используется, хотя и не всегда в том же году, в котором он был произведен. Было подсчитано, что примерно 33 миллиона метрических тонн (36 миллионов тонн), или от 80 до 85 процентов производимого в настоящее время избыточного асфальтобетона, по сообщениям, используется либо как часть переработанного горячего асфальта в холодных смесях. , или как заполнитель в гранулированных или стабилизированных основных материалах. (2) Часть RAP, которая не перерабатывается или не используется в течение того же строительного сезона, когда она была произведена, складывается и в конечном итоге используется повторно. Утилизация Избыток асфальтобетона вывозится на свалки или иногда в полосе отчуждения. В большинстве случаев это происходит, когда речь идет о небольших количествах, или когда материал смешивается с другими материалами, или когда нет средств для сбора и обработки ПДП. ИСТОЧНИКИ РЫНКА В большинстве случаев переработанный горячий асфальт можно получить на центральных предприятиях по переработке асфальта, где асфальтобетонные покрытия измельчают, просеивают и складывают для использования в производстве асфальтобетона, холодной смеси или в качестве гранулированного или стабилизированного основного материала. Большинство этих перерабатывающих предприятий расположены на площадках заводов по производству горячего асфальта, где RAP либо продается, либо используется в качестве сырья для производства переработанного горячего асфальта для дорожного покрытия или переработанного холодного асфальта. Свойства RAP во многом зависят от свойств составляющих материалов и типа асфальтобетона, используемого в старом покрытии. Поскольку RAP можно получить из любого количества старых источников дорожного покрытия, качество может варьироваться. ТРЕБОВАНИЯ К ЭКСПЛУАТАЦИИ И ОБРАБОТКЕ НА ДОРОГАХ Измельченный или измельченный РАП может использоваться во многих приложениях для строительства дорог. К ним относятся его использование в качестве заменителя заполнителя и добавки к асфальтному цементу в переработанном асфальтовом покрытии (горячая или холодная смесь), в качестве гранулированного основания или подстилающего слоя, стабилизированного основного заполнителя или в качестве материала насыпи или насыпи. Асфальтобетонный заполнитель и добавка к асфальтобетону Переработанное асфальтовое покрытие можно использовать в качестве материала-заменителя заполнителя, но в этом случае оно также обеспечивает дополнительное вяжущее асфальтобетонное покрытие, тем самым снижая потребность в асфальтовом вяжущем в новых или переработанных асфальтобетонных смесях, содержащих РАП. При использовании в асфальтобетонных покрытиях (горячая или холодная) RAP может обрабатываться либо на центральном технологическом предприятии, либо на строительной площадке (обработка на месте).Введение РАП в асфальтобетонные смеси осуществляется путем горячего или холодного ресайклинга. Горячий асфальт (центральная технологическая установка) Переработанная горячая смесь обычно производится на центральном предприятии по переработке RAP, которое обычно содержит дробилки, грохоты, конвейеры и штабелеукладчики, предназначенные для производства и складирования готового гранулированного продукта RAP, обработанного до желаемой степени. Горячий асфальт (вторичная переработка на месте) Горячая переработка на месте — это процесс повторной укладки, который выполняется в один или несколько проходов с использованием специального оборудования для нагрева, скарификации, омоложения, укладки и уплотнения. Перед фактической переработкой не требуется никакой обработки. Холодная асфальтовая смесь (центральная технологическая установка) Требования к переработке RAP для рециркуляции холодной смеси аналогичны требованиям для переработанной горячей смеси, за исключением того, что классифицированный продукт RAP включается в смеси для холодного асфальта для дорожного покрытия в качестве заменителя заполнителя. Холодная асфальтовая смесь (рециклинг на месте) Процесс холодной рециркуляции на месте включает в себя специализированные заводы или технологические линии, при которых существующее покрытие фрезеруется на глубину до 150 мм (6 дюймов), обрабатывается, смешивается с асфальтовой эмульсией (или вспененным асфальтом), укладывается и уплотняется за один проход. Гранулированный основной агрегат Для производства гранулированного заполнителя или субстрата, RAP необходимо измельчить, просеять и смешать с обычным гранулированным заполнителем или иногда регенерированным бетонным материалом.Смешивание гранулированного RAP с подходящими материалами необходимо для достижения несущей способности, необходимой для большинства несущих несвязанных гранулированных материалов. Сам по себе RAP может иметь несколько более низкую несущую способность, чем обычные основы из гранулированного заполнителя. Стабилизированный базовый агрегат Для получения стабилизированной основы или заполнителя подосновы, RAP также должен быть измельчен и просеян, а затем смешан с одним или несколькими стабилизирующими реагентами, чтобы смешанный материал при уплотнении приобрел прочность. набережная или насыпь Складчатый RAP-материал может также использоваться в качестве гранулированного наполнителя или основы для строительства насыпи или обратной засыпки, хотя такое применение широко не используется и не представляет собой наилучшего или наиболее подходящего использования для RAP. СВОЙСТВА МАТЕРИАЛА Физические свойства Свойства РАП в значительной степени зависят от свойств составляющих материалов и типа асфальтобетонной смеси (изнашиваемая поверхность, слой связующего и т. Д.). Между асфальтобетонными смесями могут быть существенные различия по качеству заполнителя, размеру и консистенции. Поскольку заполнители в поверхностном слое (слой износа) асфальтобетона должны обладать высокой устойчивостью к износу / истиранию (полировке), чтобы способствовать приемлемым характеристикам сопротивления трению, эти заполнители могут быть более высокого качества, чем заполнители в слоях связующего, где сопротивление полировке составляет не беспокоит. Как измельчение, так и дробление могут вызвать некоторое разрушение заполнителя. Градация измельченного РАП обычно более тонкая и более плотная, чем у первичных заполнителей. Измельчение не приводит к такому разрушению, как размол; Следовательно, градация измельченного RAP обычно не такая мелкая, как измельченный RAP, но более мелкая, чем чистые агрегаты, измельченные с помощью того же типа оборудования. Гранулометрический состав измельченного или измельченного RAP может до некоторой степени варьироваться в зависимости от типа оборудования, используемого для производства RAP, типа заполнителя в дорожном покрытии и от того, был ли какой-либо нижележащий заполнитель или заполнитель нижнего основания был смешан с вторичный асфальтный материал дорожного покрытия при снятии покрытия. Во время обработки практически весь произведенный РАП измельчается или измельчается до размера 38 мм (1,5 дюйма) или меньше, с максимально допустимым верхним размером 51 мм (2 дюйма) или 63 мм (2,5 дюйма). Удельный вес измельченного или переработанного RAP зависит от типа заполнителя в утилизированном покрытии и влажности складированного материала. Информация о влагосодержании RAP скудна, но есть признаки того, что влажность RAP будет увеличиваться во время хранения. Измельченный или измельченный РАП может собирать значительное количество воды под дождем.Измеренное содержание влаги в хранящемся измельченном RAP составляет до 5 процентов или выше. (4) Как отмечалось ранее, в периоды обильных осадков влажность некоторых запасов РПД может достигать 7-8 процентов. (5) Таким образом, следует свести к минимуму длительные складирования измельченного или измельченного РАП. Содержание асфальтового цемента в РАП обычно составляет от 3 до 7 процентов по массе. Асфальтовый цемент, прилипающий к заполнителю, несколько тверже, чем новый асфальтовый цемент. Таблица 13-1. Типичный диапазон гранулометрического состава восстановленного асфальтового покрытия (RAP) (в процентах по массе).
RAP, полученный из большинства смесей изнашиваемых поверхностей, обычно имеет содержание асфальта в диапазоне от 4,5 до 6 процентов. Восстановленный асфальт из RAP обычно показывает низкую пенетрацию и относительно высокие значения вязкости, в зависимости от количества времени, в течение которого исходное покрытие находилось в эксплуатации.Значения пенетрации при 25 ° C (77 ° F) могут находиться в диапазоне от 10 до 80, тогда как абсолютные значения вязкости при 60 ° C (140 ° F) могут варьироваться от 2000 пуаз (эквивалент AC-20) до до 50 000 пуазов или больше, в зависимости от степени старения. Таблица 13-2. Физико-механические свойства восстановленного асфальтового покрытия (РАП).
Химические свойства Минеральные агрегаты составляют подавляющее большинство (от 93 до 97 процентов по весу) RAP. Асфальтовый цемент состоит в основном из высокомолекулярных алифатических углеводородных соединений, но также из небольших концентраций других материалов, таких как сера, азот и полициклические углеводороды (ароматические и / или нафтеновые) с очень низкой химической активностью.Асфальтовый цемент — это комбинация асфальтенов и мальтенов (смол и масел). Асфальтены более вязкие, чем смолы или масла, и играют важную роль в определении вязкости асфальта. Окисление состаренного асфальта вызывает превращение масел в смолы, а смолы — в асфальтены, что приводит к старению и более высокой вязкости связующего. (7) Механические свойства Механические свойства RAP зависят от исходного типа асфальтового покрытия, методов, используемых для извлечения материала, и степени обработки, необходимой для подготовки RAP для конкретного применения. Удельный вес уплотненного RAP будет уменьшаться с увеличением веса единицы, при этом максимальные значения плотности в сухом состоянии, по сообщениям, находятся в диапазоне от 1600 кг / м 3 (100 фунтов / фут 3 ) до 2000 кг / м 3 (125 фунтов / фут 3 ). (8) Калифорния Значения коэффициента несущей способности (CBR) для RAP-материала, содержащего заполнитель ловушечной породы, находятся в диапазоне от 20 до 25 процентов.Однако, когда RAP смешивают с натуральными заполнителями для использования в гранулированной основе, асфальтовый цемент в RAP со временем оказывает значительное упрочняющее действие, так что образцы, содержащие 40 процентов RAP, дают значения CBR, превышающие 150 через 1 неделю. (9) В Таблице 13-2 приводится сводка механических свойств RAP, описанных в предыдущих параграфах. ССЫЛКИ
Предыдущая | Содержание | Следующий |
Асфальтобетон — главное в правильном перемешивании
Асфальтобетон — это композитный материал, обычно используемый для покрытия дорог, автостоянок, аэропортов, а также в качестве сердцевины плотин насыпей.Он состоит из минерального заполнителя, связанного с асфальтом, уложенного слоями и уплотненного. Асфальтобетон является предпочтительным для наземных дорог, поскольку он создает меньше шума от проезжей части, чем бетонное покрытие из портландцемента, и, как правило, менее шумно, чем поверхности с зазором.
Обычно считается, что асфальтобетон на 100% пригоден для вторичной переработки, так как очень мало асфальтобетона фактически выбрасывается на свалки.
Следует отметить, что методы проектирования смесей и требования к проектированию являются неотъемлемой частью всех асфальтобетонных смесей. Асфальтобетонная смесь должна быть спроектирована, произведена и должным образом размещена, чтобы обеспечить максимальную стабильность, долговечность, гибкость, сопротивление усталости и скольжению, а также непроницаемость.
Смесь должна обеспечивать оптимальную устойчивость, чтобы противостоять толчкам и колейности под нагрузкой. В то же время следует отметить, что очень высокая устойчивость сделает дорожное покрытие слишком жестким и, следовательно, менее прочным, чем хотелось бы. Максимальное содержание связующего увеличивает долговечность, поскольку толстые пленки связующего не стареют и не затвердевают так быстро, как тонкие.В некоторой степени непроницаемость важна для долговечности уплотненных смесей для дорожного покрытия, поскольку она препятствует прохождению воздуха и воды в асфальтовое покрытие или через него.
Произведенная асфальтовая смесь должна быть такой, чтобы ее можно было легко укладывать и уплотнять. Смеси, содержащие высокий процент крупнозернистого заполнителя, имеют тенденцию к расслоению во время работы, а также их трудно уплотнять. Смесевую смесь также сложно уплотнить. Идеальная смесь должна обеспечивать постепенное оседание и перемещение основания без образования трещин.Смесь открытой фракции с высоким содержанием связующего обычно более гибкая, чем смесь плотной фракции с низким содержанием связующего.
Большинство проблем с асфальтобетоном возникает из-за неправильного смешивания и из-за тех, кто не имеет базовых знаний о бетоне. Всегда следует помнить, что соотношение ингредиентов также играет такую же важную роль, как и качество ингредиентов в асфальтобетоне (в этом отношении в любом бетоне).
Что такое горячее асфальтовое покрытие?
Асфальтовое покрытие — это дорога с твердым покрытием, покрытая асфальтом.Горячий асфальт (HMA) представляет собой смесь примерно 95% камня, песка или гравия, связанных вместе асфальтовым цементом, продуктом сырой нефти. Асфальтовый цемент нагревается, комбинируется и смешивается с заполнителем на установке HMA. Полученный горячий асфальт загружается в грузовики для транспортировки к месту мощения. Самосвалы выгружают горячую асфальтовую смесь в бункеры, расположенные в передней части асфальтоукладчиков. Асфальт укладывается, а затем уплотняется тяжелым катком, который перемещается по асфальту.Как правило, движение по тротуару разрешается, как только оно остынет.
HMA Ultra-Thin предлагает простой и экономичный способ ухода за дорогами и улицами, поскольку он защищает ваши вложения в них. HMA Ultra-Thin — это горячая асфальтобетонная смесь, разработанная специально для укладки тонких слоев (3/4 дюйма) для структурно прочных дорожных покрытий с признаками старения, окисления или незначительного разрушения поверхности.В результате вы получаете более прочное и красивое покрытие, которое улучшает качество езды для водителей и снижает уровень шума дорожного движения для населения. Сочетание хорошо задокументированных преимуществ асфальта в гладкости и безопасности с продвинутым процессом проектирования многослойного покрытия .
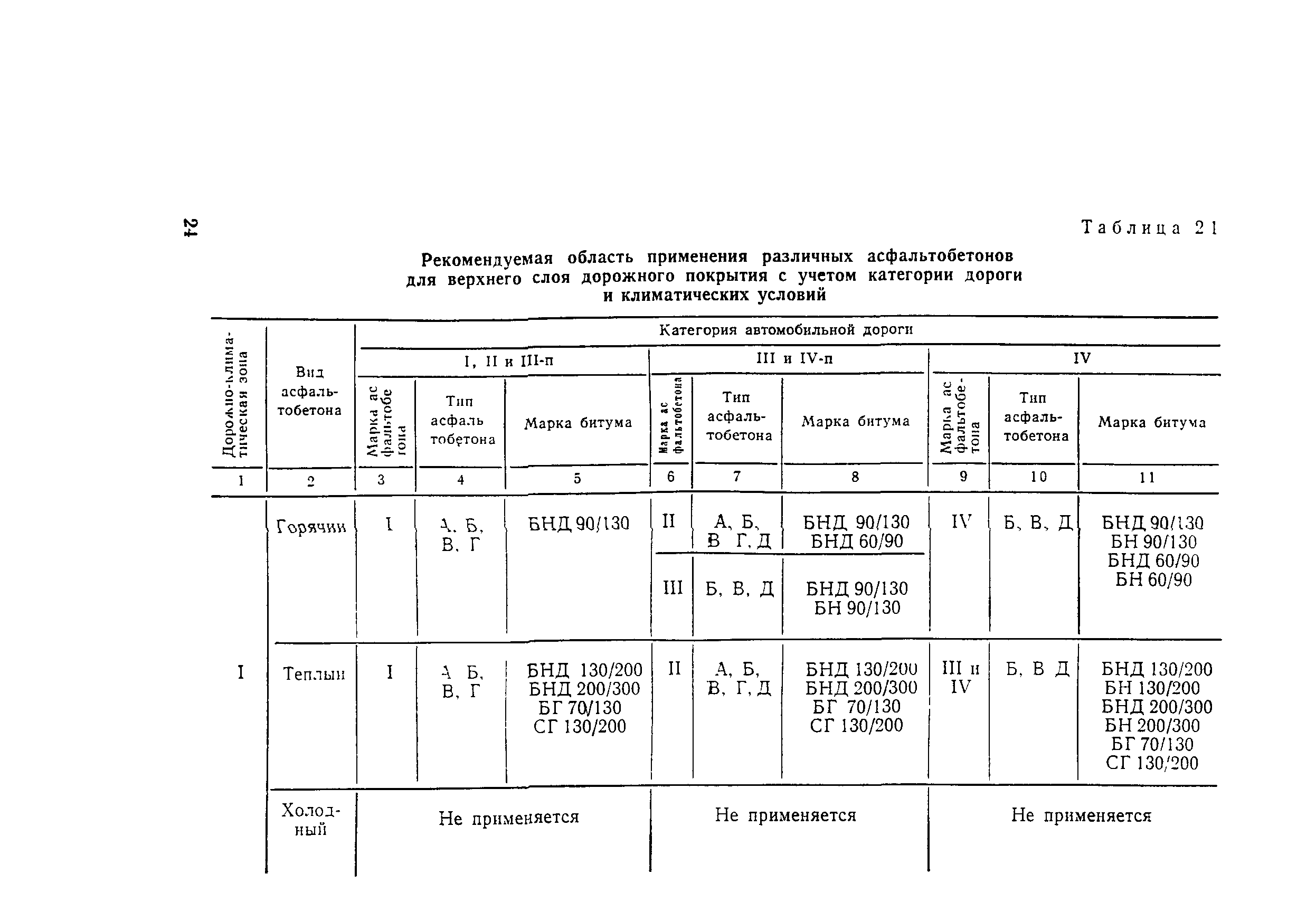
Руббилизация
Руббилирование — это проверенный метод строительства, который превращает разрушенную бетонную дорогу в основание для создания гладкого, безопасного, тихого и прочного покрытия из горячего асфальта (HMA). Это сводит к минимуму задержки для автомобилистов и позволяет строить в «непиковые» часы. Обработка асфальтом — очень экономичный метод восстановления.
Стоимость жизненного цикла
Асфальтовое покрытие на начальном этапе строительства и в долгосрочной перспективе экономит деньги на строительстве и обслуживании. К такому выводу пришли дорожные инженеры и отделы транспорта всей страны. «Затраты на жизненный цикл» — деньги, потраченные на строительство и обслуживание дороги в течение ее срока службы — значительно ниже при использовании горячего асфальта (HMA), чем при использовании бетона.
Ваше экономичное решение
Тонкие покрытия HMA, 1 ½ дюйма или меньше, являются экономически эффективным решением для сохранения дорожного покрытия, прежде всего благодаря их способности:
Гладкости
Забота автомобилистов про ровные тротуары.Асфальт будет обеспечивать водителям плавную и тихую езду, на которую они привыкли. Гладкие дороги позволяют экономить топливо. Гладкое покрытие снижает эксплуатационные расходы транспортного средства. Гладкие тротуары служат дольше. Асфальтовое покрытие более гладкое, и его легче поддерживать, чем бетонное.
Управляемость автомобиля
Национальное исследование показало, что водители предпочитают ухоженные, безопасные и ровные дороги; более того, они понимают, что эти качества требуют периодического обслуживания и финансовых вложений.
Оценка свойств битумного бетона, приготовленного из каменно-кирпичной смеси заполнителя
В статье описываются исследования механических свойств каменно-кирпичной битумно-бетонной смеси. Было оценено влияние кирпично-каменной смеси на различные механические свойства битумного бетона, такие как стабильность Маршалла, текучесть, коэффициент Маршалла (отношение стабильности к текучести), прочность на непрямое растяжение, зачистка, колейность и усталостная долговечность битумного бетонного покрытия.В этом исследовании перегоревший кирпичный заполнитель (OBBA) и каменный заполнитель (SA) были смешаны в различных соотношениях (по весу), таких как 20: 80, 40: 60, 60: 40 и 80: 20, соответственно. Лабораторные результаты показывают, что битумный бетон, приготовленный из 20% заполнителя кирпича и 80% заполнителя камня, дает наивысшую стабильность по Маршаллу. Эта битумно-бетонная смесь демонстрирует значительное улучшение различных механических свойств смеси по сравнению с другими смесями.
1. Введение
В последнее время в Индии резко активизировались работы по строительству дорог с внедрением схемы Прадхан Мантри Грам Садак Йоджона (PMGSY) и Золотого четырехугольника, а также схем Бхарат Нирман по всей стране.Одной из основных проблем, с которыми сталкиваются многие штаты Индии, является отсутствие каменных агрегатов для строительства дорог. В северо-восточной части Индии, особенно в Трипуре, Мизорам и Манипуре, камни местного производства недоступны. Требуемый натуральный каменный заполнитель постоянно привозится из других штатов Индии, чтобы удовлетворить потребности этих штатов. Таким образом, чтобы свести к минимуму зависимость от других регионов для постоянных поставок каменного заполнителя, стало необходимым изучить возможные применения альтернативных материалов для строительства дорог в качестве полной или частичной замены каменного заполнителя.Один из перспективных и эффективных способов — использование в дорожном строительстве заполнителей из переобожженного кирпича (ОББА).
Кирпичи, полученные путем обжига формованного грунта, содержат достаточное количество глины. Примерно 13% кирпичей, получаемых в процессе обжига, перегорают из-за неконтролируемого распределения температуры в печи во время производства. Эти перегоревшие кирпичи не используются при приготовлении цементобетона и, следовательно, считаются отходами. Кроме того, производители кирпича часто сталкиваются с проблемой утилизации этих огромных отходов перегоревшего кирпича.Обожженный кирпич имеет на 7–10% меньше потерь на истирание и на 6–9% меньше водопоглощения, чем кирпич первого класса. Обожженные кирпичи имеют максимальное значение абразивного износа в Лос-Анджелесе 30%, что находится в установленных пределах и может использоваться в качестве заполнителя [1]. Чрезмерная нехватка натуральных камней и непомерно высокая стоимость импортируемых природных камней усилили необходимость поиска местных доступных материалов для использования в качестве грубого заполнителя в некоторых отдаленных местах северо-восточного региона Индии. Наблюдается устойчивость по Маршаллу 14,0 кН, 12,5 кН и 12,3 кН, соответственно, для свежего камня, свежего кирпича и пустого кирпича. Они выше по стабильности, чем минимальное значение в отношении точки устойчивости по Маршаллу согласно стандартам [2]. Кирпич — это высокопористый керамический материал, обладающий высокой водопоглощающей способностью. Усилие уплотнения влияет на характеристики сопротивления остаточной деформации материалов, приготовленных из кирпичного заполнителя. В зависимости от степени замещения как у крупнозернистого, так и у мелкозернистого кирпича наблюдается снижение прочности от 20% до 30% [3, 4].Плотные битумные смеси на щебеночном заполнителе с более высоким процентным содержанием битума также хороши по сравнению с битумными смесями из щебеночного заполнителя для использования в качестве основы асфальтобетонного покрытия [5].
Только OBBA нельзя использовать в битумно-бетонных смесях, так как они непрочные. Но кирпич — это легко доступный местный материал. С другой стороны, по механическим свойствам битумный бетон с камнем намного превосходит OBBA. Но во многих местах каменные крошки не доступны.В этой ситуации лучшим решением будет смесь кирпича и камня.
В настоящем исследовании заполнители кирпич-камень были смешаны в различных соотношениях (по весу), таких как 20: 80, 40: 60, 60: 40 и 80: 20, соответственно. В лаборатории были проведены стандартные испытания, такие как удельный вес, водопоглощение, абразивный износ Лос-Анджелеса, удар, прочность по Маршаллу, прочность на непрямое растяжение, зачистка, образование колейности и усталостные испытания. Цель исследования — охарактеризовать механические свойства кирпично-битумного бетона.
2. Материал для данного исследования
Составляющими битумного бетона являются крупный заполнитель, мелкий заполнитель, наполнитель и битум. В качестве материала для исследования использовались перегоревшие кирпичи и щебень в качестве крупного заполнителя и битум марки ВГ 30 в качестве связующего материала. Каменная пыль используется в качестве наполнителя. Перегоревшие деформированные кирпичи были собраны в местных печах для производства кирпича. Кирпичи дробятся на куски, а затем куски измельчаются до желаемых размеров с помощью лабораторной дробилки.Приблизительно 2 тонны обожженных заполнителей кирпича и такое же количество заполнителей камня были использованы в этой работе для изучения физико-механических свойств.
3. Свойства материала
Материалы, используемые для этого исследования, включают крупный заполнитель, мелкий заполнитель, наполнитель и связующее. В качестве крупнозернистого заполнителя также используют щебень и кирпич. Все вышеперечисленные ингредиенты используются при приготовлении битумно-бетонной смеси. Свойства ингредиентов, а также смеси проверяются в лаборатории.
3.1. Заполнитель
Крупнозернистые заполнители, используемые для битумного бетона, обязательно будут чистыми, твердыми, прочными, долговечными и однородными по качеству. Перегоревшие кирпичные заполнители (OBBA) и каменные заполнители испытываются в соответствии с рекомендациями ASTM [6–9]. Грубый заполнитель получают путем смешивания ОББА и щебня в различных соотношениях (по весу). Физические свойства обычного OBBA и смеси представлены в Таблице 1.
|
Министерство автомобильного транспорта и автомобильных дорог (MoRT & H), 2013, определяет предельное значение различных результатов испытаний для свойств грубого заполнителя, используемого для приготовления битумного бетона. Согласно MoRT & H (2013), величина удара, абразивность Лос-Анджелеса и водопоглощение заполнителя не должны превышать 30%, 40% и 2% соответственно [10]. Также удельный вес должен быть в пределах 2.5–3.0. Предельные значения ударов, истирания, водопоглощения и удельного веса являются удовлетворительными при соотношении смеси кирпича и камня 20: 80.
3.2. Наполнитель
Минеральные наполнители содержат мелкодисперсные минеральные вещества, такие как каменная пыль, шлаковая пыль, гашеная известь, гидравлический цемент, летучая зола, лесс и другие подходящие минеральные материалы. Минеральные наполнители должны содержать 100 процентов частиц, проходящих через 0,60 мм, от 95 до 100 процентов, проходящих через 0,30 мм, и 70 процентов, проходящих через 0,075 мм. Во время подготовки образца минеральный наполнитель будет достаточно высушен, чтобы течь свободно.В этом исследовании каменная пыль использовалась в качестве минерального наполнителя. Свойства каменной пыли, использованной в данном исследовании, перечислены в таблице 2.
|
3.3. Битум
Битум марки ВГ-30 использован в качестве вяжущего для приготовления битумного бетона. Свойства битума, использованного в этом исследовании, представлены в таблице 3 и сравниваются с приемлемыми значениями, указанными в индийских стандартных кодексах [11–14].
| 4 | Пластичность (см) | 93 | 75 (минимум) | ||||||||||||||||||||||||
4.

Тест Маршалла, испытание на стабильность, применим к дизайну горячей смеси битумов и заполнителей.В Индии битумно-бетонную смесь обычно разрабатывают по методу Маршалла. Этим методом измеряется сопротивление пластической деформации цилиндрического образца битумной смеси [15, 16]. Процедура испытаний используется при проектировании и оценке битумных смесей для дорожного покрытия. В данном исследовании тест Маршалла проводится с использованием смеси перегоревшего кирпича и каменного заполнителя. В данном исследовании соблюдается стандартная градация агрегатов при подготовке образца для испытаний в соответствии с MoRT & H, представленным в таблице 4.
| 9014 9013100 | Крупный заполнитель 38% | ||||||||
13,2 | 90–100 | 89,5 | ||||||||
9,5 | 70–88 | 79,0 | ||||||||
4.![]() | 53–71 | 62,0 | ||||||||
2,36 | 42–58 | 50,0 | Мелкий заполнитель 55% | |||||||
1,18 | 349 0,60 | 26–38 | 32,0 | |||||||
0,30 | 18–28 | 23,0 | ||||||||
0,15 | 12–20 | 16,0 | 0 | |||||||
Одна из целей дизайна смеси — найти подходящее содержание битума. Метод Маршалла используется для определения оптимального содержания битума (OBC). Стандартные значения результатов теста Маршалла и коэффициента прочности на разрыв (TSR), как указано MoRT & H, представлены в таблице 5.
|
Образцы для испытаний были подготовлены и протестированы в лаборатории в соответствии с рекомендациями MoRT & H. По результатам испытаний была изучена взаимосвязь между стабильностью по Маршаллу, значением текучести, объемной плотностью, воздушными пустотами (VA) и пустотами, заполненными битумом (VFB) с различным процентным содержанием связующего для заполнителя из кирпича и камня. В настоящем исследовании образцы Маршалла приготовлены из заполнителя, содержащего кирпич и каменный заполнитель в соотношении 20: 80, 40: 60, 60: 40 и 80: 20, соответственно. Результаты теста Маршалла, полученные в лаборатории, перечислены в Таблице 6.
13,75 | 13,23 | 12,50 | 10,78 | Расход (мм) | 3,35 | 3,44 | 3,56 | 3,70 |
5.![]() В данном исследовании испытание проводится для различных смесей заполнителя из кирпича и камня.Результаты представлены в Таблице 8. Отмечено, что величина снятия изоляции является наименьшей в случае соотношения кирпича и камня 20: 80. Удовлетворяет допустимому значению (согласно таблице 5). Следовательно, соотношение 20: 80 для битумного бетона показывает лучшую прочность связывания с битумом, даже когда он подвергается наихудшему содержанию влаги.
5.2.3. Результаты исследований колейностиВ настоящем исследовании напряжение, которое колесо прикладывает к образцу, составляет 0,70 МПа. Два LVDT (линейно-регулируемых дифференциальных преобразователя) прикреплены к оси резинового колеса для контроля глубины колеи. Выход LVDT подключен к компьютеру. Специальное программное обеспечение контролирует глубину колеи и строит график зависимости количества проходов от глубины колеи.Результаты отслеживания колеса показаны на рисунке 2. Колейность ниже в случае битумно-бетонной смеси, содержащей соотношение 20: 80 (5,3 мм) по сравнению с соотношением 80: 20 (7,1 мм). 5.2.4. Результаты испытания на усталостную долговечностьРезультат испытания показывает, что усталостная долговечность битумного бетона с соотношением 20: 80 намного выше, чем у битумного бетона с заполнителем из кирпича и камня 80: 20 при равной деформации растяжения. Это связано с твердостью смеси заполнителя, так как процент камня больше в соотношении 20: 80.На рисунке 3 показано, что для данной деформации растяжения 200 × 10 -6 соответствующая усталостная долговечность битумного бетона из каменного заполнителя 20: 80 и 80: 20 составляет 534 и 370 соответственно. Таким образом, можно сделать вывод, что усталостная долговечность битумно-бетонной смеси при соотношении 20: 80 увеличивается в 1,44 раза. Это ясно указывает на то, что смесь BC с соотношением 20: 80 может выдерживать высокие нагрузки и требует большего количества повторений до отказа. Настоящее исследование убедительно доказывает, что можно ожидать, что битумно-бетонные смеси с соотношением 20: 80 будут иметь гораздо более длительную усталостную долговечность, чем битумно-бетонные смеси с заполнителем из кирпича и камня 80: 20. 5.2.5. Результаты испытания модуля упругостиИспытание проводится при различных температурах, таких как 5 ° C, 25 ° C, 35 ° C и 45 ° C. Результаты испытания модуля упругости, полученные в ходе исследования, показаны на рисунке 4. Видно, что значение RM уменьшается с увеличением температуры от 5 ° C до 45 ° C. При 5 ° C значение RM для смеси 20: 80 в 0,63 раза выше, тогда как при 45 ° C оно примерно в 1,32 раза выше, чем для смеси из кирпича и камня 80: 20.Это показывает, что смесь в соотношении 20: 80 больше подходит для жаркого климата. Более того, значения MR, содержащие 20% кирпича и 80% камня при всех указанных температурах, выше по сравнению со смесью кирпича и камня 80: 20. 6. ЗаключениеНа основании анализа результатов, полученных в настоящих исследованиях, сделаны следующие выводы: (1) Увеличение каменного заполнителя в смеси кирпично-каменного заполнителя значительно снижает величину Impact, Los -Angeles истирание и водопоглощение, но увеличивает удельный вес.Предельное значение удара, истирания, водопоглощения и удельного веса является удовлетворительным при соотношении смеси кирпича и камня 20: 80. (2) Максимальное значение устойчивости по Маршаллу получается в случае отношения смеси кирпича и камня 20: 80. . Стабильность увеличивается на 28% при соотношении 20: 80 по сравнению с соотношением 80: 20 щебеночной смеси. Величина потока по Маршаллу также находится в пределах (3–5 мм) для этой смеси. Более того, коэффициент Маршалла также находится в пределах допуска, поскольку он показывает, что соотношение кирпича и камня с соотношением 20: 80, приготовленное для битумно-бетонной смеси, лучше и больше подходит для строительства гибких дорожных покрытий.(3) Выбор OBC — это тонкое уравновешивание, в котором есть ряд переменных. Баланс должен поддерживаться таким образом, чтобы одновременно соблюдались указанные пределы, рекомендованные в своде правил. В этом исследовании содержание битума 5,45% при соотношении смеси кирпича и камня 20: 80 выбрано в качестве оптимального содержания битума, и оно также удовлетворяет всем допустимым диапазонам. (4) Значение ITS увеличивается с увеличением использования камня в смеси, поскольку он достигает пикового значения при соотношении 20:80.Значение ITS для соотношения 20: 80 увеличивается на 80% и 118% по сравнению со смесью 80:20 для некондиционированных и кондиционированных образцов, соответственно. Коэффициент прочности на разрыв также находится в пределах, установленных для смеси 20: 80. Таким образом, битумно-бетонная смесь с соотношением 20: 80 безопасна от усталости. (5) Величина снятия изоляции снижается с увеличением процентного содержания камня в смеси заполнителя. Величина полосы в случае смеси 20: 80 составляет 2%, что имеет более высокую стойкость к полосам. (6) Результаты испытаний показывают, что битумно-бетонная смесь с соотношением 20: 80 менее подвержена деформации колеи по сравнению с битумно-бетонной смесью с соотношением 80:20. щебеночно-каменная смесь.Замечено, что общая глубина депрессии со смесью 20:80 уменьшилась на 24% по сравнению с смесью кирпича и камня 80:20. (7) Замечено, что значения RM уменьшаются с увеличением температуры от 5 ° C до 45 ° С. Результаты для RM, полученные при низких и высоких температурах, показывают, что смесь с соотношением 20: 80 имеет высокое значение RM по сравнению со смесью 80:20. (8) Отмечено, что усталостная долговечность битумно-бетонной смеси с кирпичом-камнем в соотношении 20: 80 смесь заполнителя увеличивается в 1,44 раза при температуре от 35 ° C до 37 ° C при уровне деформации растяжения по сравнению с смесью заполнителя кирпича и камня в соотношении 80: 20. |