Полистиролбетон своими руками в домашних условиях: состав и пропорции
Полистиролбетон – это разновидность легкого бетона. В его состав входят цемент, вода, ПАД и полистирол. К преимуществам относят хорошие теплоизоляционные характеристики, малый вес, который создает минимальную нагрузку на основание дома. Его можно сделать самостоятельно в домашних условиях, и он легко обрабатывается.
Оглавление:
- Из чего состоит полистиролбетон?
- Инструкция по изготовлению
- Советы и рекомендации
Такой бетон заметно отличается прочностными характеристиками от других подобных материалов. Все благодаря высокой степени адгезии цемента с полистирольными гранулами. Для производства не требуется тяжелый щебень, поэтому блоки легко перевозить и класть даже одному человеку.
Состав и соотношение
Коэффициент теплопроводности зависит от плотности полистиролбетона, но находится он всегда в диапазоне 0,055-0,145 Вт/м·К.
Различается полистиролбетон по структуре – она может быть плотной, с мелкими и крупными порами. В домашних условиях в основном изготавливают первый тип материала, так как для его производства не требуется специальное оборудование.
Циклов морозостойкости у полистиролбетона меньше, чем у других бетонных изделий. Если сделать блоки самому, то максимально возможный показатель морозостойкости не будет превышать F25, а у заводских – F25-100. Но этот недостаток перекрывается низким коэффициент теплопроводности, устойчивостью к солнечному излучению, плесени и хорошей степенью адгезии.
Бывает следующих видов:
- теплоизоляционный – D150-200;
- теплоизоляционно-конструкционный – D250-350;
- конструкционно-теплоизоляционный – D400-600.
Для строительства стен потребуется марка не ниже D500, для менее нагружаемых конструкций, например, перегородок, достаточно D300-D400. Если блоки полистиролбетона будут применяться только в качестве теплоизоляционного слоя, то D200-D300. Также раствор отлично подходит для заливки пола на втором этаже дома. Тогда нагрузка на перекрытия будет меньше, чем при заливке стандартной бетонной стяжки. Каждый третий ряд кладки необходимо армировать, чтобы конструкция получилась максимально прочной.
Руководство приготовления по шагам
Перед тем как начать делать полистиролбетон своими руками, нужно точно рассчитать марку бетона. Так как именно от нее зависит максимальная нагрузка, которую он сможет выдержать. Блоки с минимальной прочностью используются только в теплоизоляционных целях, а с повышенной для строительства несущих конструкций.
Для их производства понадобится цементный порошок, полистирольные гранулы, поверхностно-активные добавки и вода. Пропорции компонентов напрямую зависят от назначения материала. Если нужна марка D200, то потребуется смешать все в следующем соотношении: 16 кг цементного порошка М400, 0,1 кг поверхностно-активных добавок и 9 л воды.
Чтобы получить D500, перемешиваются компоненты в другой пропорции: 4,1 кг цемента, 0,08 кг поверхностно-активных добавок и 15 л воды. Чем больше пропорция цемента в составе, тем выше его прочностные характеристики, но тем меньше теплоизоляционные свойства.
Наличие поверхностно-активных добавок обязательно, так как они способствуют равномерному распределению гранул по всему объему смеси и обволакиванию их цементом. Чтобы уменьшить расходы цемента и уплотнить раствор, в него можно всыпать песок, но не более 15% от всего объема цементного порошка. Если вместо ПАД применяется обычное моющее средство, то на 10 л воды достаточно 0,05 л.
В качестве поверхностно-активных добавок используется древесная обмыленная смола, моющее средство (для посуды, шампунь) или пластификаторы. Применяются в соотношении 2% от всего объема цементного порошка. Чем меньше цемента, тем больше их требуется вводить. Перед добавлением пластификаторов, следует изучить их инструкцию, так как некоторые из них необходимо заранее развести с водой, а другие сразу же засыпаются в раствор при замешивании. ПАД не только способствуют равномерному распределению цемента по смеси, но и снижает риск растрескивания материала.
Чтобы полистиролбетон получился наилучшего качества, необходимо соблюдать соотношения компонентов и последовательность их ввода. Если планируется изготавливать блоки, то сначала сооружаются формы. Сделать их можно из фанеры или досок. Если основание, на котором будут стоять формы, ровное, то необязательно обустраивать в них дно.
Пошаговая инструкция:
- В емкость или бетономешалку засыпается цемент и вода, после чего все перемешивается до однородной консистенции.
- В смесь всыпается просеянный песок.
- Добавляются гранулы полистирола, но не весь объем сразу, а лишь часть. Как только раствор перемешивается до однородного состояния, высыпают следующую часть гранул.
- Вливается поверхностно-активная добавка или моющее средство.
Если изготавливаются блоки в формах, то их оставляют застывать на 1-3 дня. Время схватывания зависит от температуры в помещении и влажности. После вытаскивания из форм оставляют набирать прочность на 2 недели, потом можно приступать к их кладке. Если полистиролбетон производится в зимнее время, то после заливки раствора в опалубку его нужно оставить минимум на неделю.
Полезные рекомендации
1. Чтобы конструкция прослужила как можно дольше, советуется закрыть ее отделочными материалами для защиты от внешних воздействий (атмосферных осадков, пыли), например, штукатуркой.
2. Добавляя воду при замешивании, следует учитывать, что смесь должна получиться не слишком жидкой и не сухой. Соотношение можно подобрать методом проб и ошибок на небольшом объеме. Если будет избыточное количество воды, то показатель прочности блоков ухудшится, а если недостаточное, то после высыхания в них появятся трещины.
3. Для замешивания рекомендуется приобретать только качественный полистирол и наполнители. Если использовать пластификатор неизвестной марки, то могут значительно ухудшиться показатели морозостойкости и устойчивости к влаге.
4. Для кладки используется специальный клеевой состав, но не цементно-песчаный раствор. Разводить его нужно только по указанному на нем руководству. Тогда швы получатся тонкими и вероятность появления мостиков холода снизится.
5. Чтобы проверить качество и правильность подобранного соотношения, советуется заранее изготовить несколько блоков и дождаться полного набора ими прочности. Качественный материал при распиливании не будет крошиться и разрушаться под тяжестью, а также выдержит постоянный нагрев в течение полутора часов.
6.
Стоимость гранул зависит от их размера. Чем меньше фракция, тем выше цена, но тем прочнее и надежнее получится полистиролбетон. Песок можно не покупать, а использовать речной, главное – тщательно просеять от мусора.
расчет пропорций и состав раствора на 1 м3 пенополистиролбетона и полистиролбетона на песке, рецепт в домашних условиях
Бетон – одно из лучших изобретений человечества в сфере строительства за всю историю цивилизации, но у его классической разновидности есть один принципиальный недостаток: бетонные блоки весят слишком много. Неудивительно, что инженеры много работали над тем, чтобы сделать материал менее плотным, но при этом очень прочным. В результате было создано несколько модифицированных вариантов бетона, а одним из наиболее популярных среди них является полистиролбетон.
Источник фото: https://beton57.ru/proizvodstvo-polistirolbetona/
Необходимые материалы
Как и положено любой другой бетонной смеси, полистиролбетон предполагает использование в первую очередь цемента, просеянного песка и пластификаторов. Вода также необходима, причем ее количество важно просчитать идеально точно. В принципе, если влаги будет много, вы это сразу заметите: слишком жидкая масса спровоцирует всплытие всей взвеси. Если же состав получился слишком густым, последствия обнаружатся позже – неуместно сгущенный полистиролбетон имеет повышенную склонность к растрескиванию. Кроме того, необходимо добавить и полистирол.
Этой комбинации ингредиентов уже достаточно, чтобы масса получилась универсальной и могла быть использована в различных условиях. Добавление каких-либо дополнительных компонентов не требуется – стандартного набора составляющих хватит для того, чтобы полистиролбетон мог быть использован для всех основных сфер, а именно: строительства зданий, установки перемычек и заливки пола.
При этом материал не содержит токсичных или любых других опасных для человека компонентов, является экологически чистым и безвредным для окружающей среды.
Инструменты и оборудование
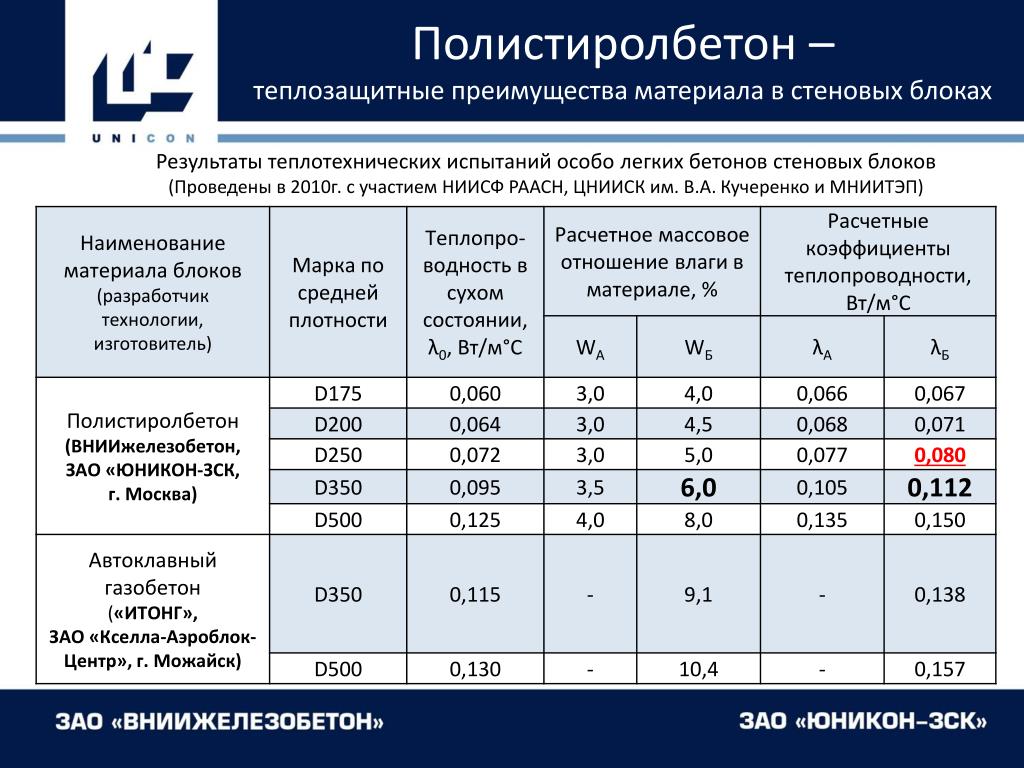
В условиях большого частного строительства, если полистиролбетона надо хотя бы 20 кубов, актуально использование отдельного электрогенератора. Он позволит подавать производимую массу на место укладки без перебоев, а ведь в сельской местности, где обычно занимаются любительским строительством, перебои с напряжением вполне вероятны.
Более того, согласно ГОСТу 33929-2016 качественная заливка материала возможна только с полноценным применением генератора.
Заливка возможна и с определенной дистанции, но для удобства выполнения масштабных работ гораздо удобнее обзавестись мобильной установкой для замешивания полистиролбетона. Другое дело, что ее покупка очень сильно бьет по карману владельца, а в процессе возведения одного объекта, пусть даже довольно крупного, окупиться она не успеет. Таким образом, подобное оборудование актуально для профессиональных строительных бригад, но вряд ли должно рассматриваться в качестве решения для индивидуального строительства.
Можно также уточнить, что на больших предприятиях, конечно, автоматизация процесса организована на порядок выше. Самые лучшие образцы современной техники – полностью автоматизированные конвейерные линии – позволяют выдавать свыше 100 м3 готового материала ежедневно, причем уже сформированного в блоки нужного размера и формы. Такое оборудование не могут позволить себе даже предприятия среднего размера, которые вместо этого обходятся сравнительно компактными и недорогими стационарными линиями.
Рецептура
В интернете можно встретить различные рекомендации относительно пропорций всех входящих в рецепт компонентов, но в каждом отдельном случае правильный состав будет разным. Удивляться этому не стоит: как и обычный бетон, полистирольная версия бывает разных марок, каждая из которых подходит для определенных задач. Именно с этим стоит разобраться в первую очередь.
Марки полистиролбетона по плотности обозначаются буквой D и трехзначным числом, которое указывает, сколько примерно килограммов веса приходится на 1 м3 застывшей массы. Менее плотные растворы, марка которых ниже D300, не годятся ни для стяжки пола, ни для возведения стен: они очень пористые и из-за этого хрупкие, неспособные выдерживать значительную нагрузку. Такие блоки, как правило, используют в качестве теплоизоляции.
Полистиролбетон в пределах D300–D400 называют теплоизоляционно-конструкционным: он и теплоизоляцию обеспечивает, и может быть использован для малоэтажного строительства, но только при условии, что не станет несущей опорой для тяжелых конструкций. Наконец, составы плотностью от 400 до 550 кг на 1 м3 называются конструкционно-теплоизоляционными. Они уже не годятся для полноценной теплоизоляции, но выдерживают более высокую нагрузку.
Тем не менее даже их нельзя использовать для многоэтажного строительства.
Теперь можно переходить непосредственно к пропорциям. В каждом случае за неизменную основу будем брать 1 кубометр гранулированного полистирола. Если брать для замешивания цемент марки М-400, то на куб полистирола для производства бетона D200 надо взять 160 кг цемента, для D300 – 240 кг, D400 – 330 кг, D500 – 410 кг.
Количество воды по мере роста потенциальной плотности тоже возрастает: брать надо, соответственно, 100, 120, 150 и 170 л. А также нередко добавляют смолу древесную омыленную (СДО), но ее надо совсем немного и тем меньше, чем выше плотность: соответственно, 0. 8, 0.65, 0.6 и 0.45 л.
Использование цемента более низкой марки, чем М-400 крайне нежелательно. Если марка более высокая, можно немного сэкономить цемент, сделав массу частично на песке.
Профессионалы указывают, что использование высококачественных марок цемента позволяет треть его массы заменять песком.
Отдельного внимания заслуживает использование СДО, которая считается необязательной. Это вещество добавляют по той причине, что оно создает в толще бетона маленькие воздушные пузырьки, способствующие повышению теплоизоляционных свойств. При этом небольшая доля СДО в общей массе на плотность радикально не влияет, но если теплоизоляция вам совершенно ни к чему, можно сэкономить на производстве полистиролбетона, не добавляя в него этот компонент.
Необходимыми компонентами являются пластификаторы, но в пропорциях выше они рассмотрены не были. Так произошло потому, что каждый производитель предлагает продукцию с совершенно разными свойствами, поэтому разумно вчитываться в инструкции на таре, а не руководствоваться некой общей логикой. При этом в домашних условиях очень часто не применяют специальные пластификаторы, используя вместо них жидкое мыло либо средство для мытья посуды.
Хотя они тоже бывают разными, некая общая рекомендация существует: такой «пластификатор» добавляется в воду в количестве примерно 20 мл на ведро.
Как сделать?
Изготовление полистиролбетона своими руками не является особо сложной задачей, но важно выдержать процедуру приготовления, иначе материал окажется ненадежным, не сможет соответствовать лучшим ожиданиям или попросту будет приготовлен в недостаточном или чрезмерном количестве. Разберемся, как получить хороший пенополистиролбетон без очевидных ошибок.
Расчет объема
Хотя пропорции выше даны правильно, в домашних условиях ими пользуются мало: в них учтены слишком большие объемы, которые не только не используются в частном строительстве, но и сложно измерять. Для большего удобства мастера-любители используют перерасчет на ведра – это своеобразный общий знаменатель для килограммов цемента, литров воды и кубометров полистирола. Даже если нам нужен раствор на базе кубометра гранул, все равно такой объем в бытовую бетономешалку не поместится, а значит, лучше измерять ведрами.
Сначала нужно понять, сколько ведер цемента надо для замешивания массы. Как правило, стандартное 10-литровое ведро цемента весит примерно 12 кг. Согласно приведенным выше пропорциям, для приготовления полистиролбетона марки D300 надо 240 кг цемента или 20 ведер. Раз общую массу можно поделить на 20 «порций», определяем, сколько других материалов понадобится для одной такой «порции», деля рекомендованное в пропорциях количество на 20.
Кубометр полистирола – это объем, равняющийся 1000 л. Поделим его на 20 – получится, что на каждое ведро цемента надо 50 л гранул или 5 10-литровых ведер. По такой же логике вычисляем количество воды: суммарно ее надо было 120 л, при делении на 20 частей получается по 6 литров на порцию, отмерять их можно даже обыкновенными бутылками из-под различных напитков.
Сложнее всего с СДО: ее суммарно надо было всего 650 мл, а значит, для каждой порции – всего 32,5 мл. Конечно, небольшие отклонения допустимы, но помните, что снижение дозировки отрицательно сказывается на теплоизоляционных свойствах, а превышение делает материал менее прочным.
Эта же формула используется и для расчетов пропорций составляющих для изготовления полистиролбетона любых других марок: определяйте, сколько ведер цемента надо на 1 м3 гранул, а потом делите соответствующий объем других компонентов на число ведер.
Замешивание
Замешивать полистиролбетон надо, соблюдая определенный порядок действий, иначе получившаяся масса не будет однородной, а значит, блоки из нее не будут прочными и долговечными. Последовательность шагов предполагается следующая:
- в бетономешалку высыпают все полистирольные хлопья и сразу же включают вращение барабана;
- пластификатор или моющее средство, которое его заменяет, растворяют в воде, однако выливают в барабан не всю жидкость, а только ее треть;
- в сравнительно небольшом количестве влаги и пластификатора гранулы полистирола должны отмокать на протяжении некоторого времени – к следующему шагу переходим только после того, как каждая гранула наверняка промокла;
- после этого можно засыпать в бетономешалку весь объем цемента, а сразу за ним влить всю оставшуюся воду;
- если СДО входит в состав вашего рецепта, она вливается самой последней, но ее надо предварительно растворить в небольшом объеме воды;
- после добавления СДО остается вымешивать всю массу на протяжении 2 или 3 минут.
На самом деле процесс домашнего разведения полистиролбетона может оказаться и более простым, если вы купите его в сухом виде и просто добавите воды. На упаковке будет написано, какая марка стройматериала должна получиться на выходе, а также должно быть указано, сколько именно жидкости надо для получения ожидаемого результата.
В составе такой сухой массы уже есть все необходимое, включая СДО и пластификаторы, поэтому ничего, кроме воды, добавлять не нужно.
Инструкцию по изготовлению полистиролбетона своими руками смотрите в видео ниже.
видео инструкция, состав и пропорции
Полистиролбетон представляет собой разновидность легких (композитных) бетонов, руководством по техническим условиям эксплуатации является ГОСТ 51263-99. К преимуществам этого материала относят хорошие теплоизоляционные свойства, малую нагрузку на стены и фундамент, возрастание прочностных характеристик в процессе эксплуатации и возможность производства непосредственно на строительной площадке. Последнее позволяет самостоятельно создавать конструкции с любыми требуемыми габаритами.
Оглавление:
- Отличия от обычного бетона
- Пропорции компонентов
- Как сделать своими руками?
- Мнение специалистов
Единственным недостатком является высокая стоимость, для снижения затрат рекомендуется сделать полистиролбетон своими руками, тем более, что приготовленный в домашних условиях раствор не уступает в качестве заводскому. Важно лишь отслеживать свойства используемого полистирола и вяжущего, и соблюдать пропорции, в зависимости от необходимой прочности.
Описание материала
Полистиролбетон выделяется из остальной группы легких бетонов. Как и у них, его плотность не превышает 1800 кг/м3, но он прочнее из-за значительной адгезии цемента и поверхности гранул полистирола. Тяжелые и крупные фракции щебня в таком бетоне отсутствуют, изготавливаемые из него блоки легко поднять самому, что очень актуально при строительстве частного дома. В зависимости от плотности, теплопроводность полистиролбетона в сухом состоянии варьируется в пределах 0,055–0,145 Вт/(м∙°C), паропроницаемость — от 0,135 до 0,068 мг/(м∙ч∙Па). Различают плотную, поризованную и крупнопоризованную структуру такого бетона, своими руками проще сделать первую разновидность (не требуются специальные бетоносмесители).
Морозостойкость уступает у тяжелых сортов (от 20 до 100 циклов), по этой причине блоки с добавлениями полистирола при равной прочности менее долговечны. У автоклавных марок этот показатель больше, приготовленный полистиролбетон в домашних условиях редко бывает выше F25. Но материал выигрывает в легкости и теплоизоляционных свойствах, он не подвержен влиянию УФ-лучей, биологическим воздействиям, обладает существенной адгезией и сохраняет свою малую теплопроводность при намокании. Устойчивость теплофизических параметров объясняется низкой сорбционной влажностью (4–8 %). Но в целом, полистиролбетон нуждается в защите от влаги, как из-за морозостойкости, так из-за угрозы вымывания частиц под атмосферными осадками.
Состав и соотношения компонентов
Для приготовления бетона используется цемент, вспененный полистирол, поверхностно активные добавки и вода. В зависимости от ожидаемой плотности, рекомендуемые пропорции на 1 м3 теплоизоляционного наполнителя составляют:
Марка | Цемент (не ниже М400), кг | ПАД, кг (или л) | Вода, л |
D200 | 160 | 1-1,1 | 90–100 |
D300 | 240 | 0,9–1 | 110–120 |
D400 | 330 | 0,8–0,9 | 130–150 |
D500 | 410 | 0,7–0,8 | 150–170 |
Нетрудно заметить, что соотношение В/Ц не превышает 0,5, чем больше требуемая плотность, тем существеннее доля вяжущего. Пропорции цемента регулируют марку прочности и теплоизоляционные свойства. Основная проблема заключается в необходимости его равномерного распределения и взаимодействия со всеми гранулами полистирола, поэтому ввод ПАД является обязательным, в отличие от других видов бетона. В целях экономии и уплотнения допускается добавление песка, но не более 15 % от общей массы цемента.
В роли легкого теплоизоляционного заполнителя выступает вспененный полистирол (гранулированный или полученный путем домашнего дробления). Размер фракций ограничен, согласно руководству 51263-99 он не должен превышать 20 мм (желательно придерживаться 2–4 мм). Оптимальными по форме считаются кубические гранулы, полистиролбетон на их основе будет самым прочным. В некоторых случаях в качестве заполнителя используются кусочки экструдированного пенополистирола, но такой бетон не соответствует строительным стандартам, его свойства еще не исследованы.
Обязательным условием технологии является введение в состав ПАД, именно они отвечают за обволакивание гранул цементным раствором. В промышленных масштабах часто применяются СДО (смола древесная обмыленная), в частном строительстве — моющие средства или пластификаторы. Ориентировочные пропорции ПАД — 2 % от массы цемента, чем меньше доля вяжущего, тем больше требуется добавок. Перед вводом их в бетон следует ознакомиться с инструкцией, некоторые пластификаторы разбавляются заранее, другие достаточно просто залить в бетономешалку одновременно с водой.
Руководство по приготовлению
Важно соблюдать правильную последовательность подготовки компонентов, засыпки и перемешивания. Основные этапы пошаговой инструкции для приготовления полистиролбетона своими силами включают:
- Подготовку компонентов и оборудования: емкости для ручного замеса или бетономешалки.
- Разбавление в воде добавок (жидкого мыла, пластификаторов).
- Засыпку вспененного полистирольного наполнителя, частичное смачивание, потом — заливку всей жидкости и перемешивание.
- Добавление цемента, согласно выбранным пропорциям.
- Перемешивание всех компонентов.
- Заливку полистиролбетона в смазанную автомобильным маслом опалубку или в качестве стяжки.
Весь процесс приготовления бетона в бетономешалке занимает не более 5 минут, при ручном замесе полистирол, вода и цемент вводятся одновременно и перемешиваются лопатой (важно оставить пространство для всплывающего легкого наполнителя). Раствор отгребается с краев и закидывается в центр емкости. Если полистиролбетон используется для изготовления блоков для дома или построек, то его 2–3 дня держат в опалубке и только через 2 недели после заливки приступают к кладке. Размер изделий не ограничен, но существует риск повреждения крупных заготовок при вынимании из формы. Для соединения полистирольных блоков покупается специальный клей, цементный раствор подходит хуже из-за образования мостиков холода, толщину швов лучше сделать минимальной.
Советы и рекомендации
Положительный эффект при замесе в домашних условиях достигается лишь при максимальной однородности смеси и качественном полистироле. Поэтому в раствор желательно вводить сертифицированный наполнитель, только так полистиролбетон будет многофункциональным. В противном случае возможно снижение полезных свойств: влаго- и морозостойкости, прочности. При использовании материала для наружных теплоизоляционных работ обязательно предусматривается защита (покрытие толстым пластом штукатурки, термокраской). Для улучшения характеристик конструкций из этого бетона, рекомендуется:
1. Применять свежее вяжущее, при сомнении в качестве следует увеличить его расход.
2. Выбирать состав и соотношения компонентов в зависимости от назначения полистиролбетона. Рекомендуемая плотность раствора: для несущих стен дома — не ниже D500, для перегородок и легких конструкций — D300–D400, для теплоизоляции перекрытий и чердачных помещений — в пределах D200–D300.
3. Армировать кладку (каждый третий ряд).
4. Сделать 1–2 пробных изделия перед началом основных работ и проверить их прочность. Качественный полистиролбетон не крошится (даже при распиле или обработке), выдерживает до 90 минут нагрева до высоких температур и весовые нагрузки, в зависимости от марки (не деформируется).
5. При ведении работ в зимнее время оставлять блок в опалубке как минимум на неделю. При этом используемое соотношение В/Ц должно быть минимальным.
Полистиролбетон своими руками — пропорции и состав
Полистиролбетон изготовление своими руками
Полистиролбетон является одним из видов легких бетонов. Данный материал быстро стал востребованным в строительстве, благодаря характеристикам. Ячеистая структура позволяет значительно повысить теплоизоляционные свойства, сохраняя вместе с этим прочность. Технология производства не сложна, поэтому можно сделать полистиролбетон своими руками, тем самым экономя средства на покупке готовых блоков или смесей.
Пропорции для видов полистиролбетона
Для возведения различных строительных конструкций потребуются разные по прочности и теплопроводности блоки.
Пропорции для их изготовления:
D200
- цемент – 160 кг;
- полистирол – 1 м³;
- СДО – от 1 кг до 1,1 кг;
- вода – от 90 л до 100 л.
D300
- цемент – 240 кг;
- полистирол – 1 м³;
- СДО – от 0,9 кг до 1 кг;
- вода – от 110 л до 120 л.
D400
- цемент – 330 кг;
- полистирол – 1 м³;
- СДО – от 0,8 кг до 0,9 кг;
- вода – от 130 л до 150 л.
D500
- цемент – 410 кг;
- полистирол – 1 м³;
- СДО – от 0,7 кг до 0,8 кг;
- вода – от 150 л до 170 л.
Во время приготовления видов смесей используется цемент марки М400 и пенополистирол с фракцией от 2,5 до 10 мм. Количество песка рассчитывается из количества взятого цемента.
По поводу необходимости добавления песка и его пропорций много разных мнений, советуем посмотреть вариант приготовления с песком на видео.
Для экономии средств рекомендуется, вместо приобретения фасованных гранул высокого качества приобретать обычный дробленый полистирол, который остается после переработки вторсырья. Качество смеси от вида используемого пенополистирола не меняется.
Добавка СДО присутствует в составе для уменьшения расхода всех прочих материалов. Благодаря ней смесь немного вспенивается и заполняется пузырьками. Вследствие этого не только экономятся средства, но и повышается уровень теплоизоляции.
Процесс изготовления
В домашних условиях данный материал изготавливается либо полностью вручную, либо при помощи бетономешалки. Ручной и механический вариант смешения будут немного отличаться друг от друга.
Ручное смешивание
В глубокой емкости с высокими бортами (к примеру, старая ванна) замешивается сначала смесь из цемента, песка, воды и омыленной древесной смолы. После полного смешения всех материалов добавляют пенополистирол.
Необходимо учесть, что он добавляется постепенно и небольшими порциями, каждая следующая порция добавляется только, после полного растворения предыдущей. Делается это для более качественного смешения и для облегчения самого процесса замеса.
Движения инструментом, которым размешивается смесь (чаще всего лопата), должны осуществляться по кругу. Смесь необходимо поднимать слегка вверх и набрасывать на пенополистирол.
Механическое смешивание
В бетономешалку загружают весь пенополистирол и добавляют к нему около трети необходимого количества воды. Перемешивают в течение минуты (можно менее) и добавляют цемент.
Замес длится около минуты, после чего добавляется оставшаяся часть воды и омыленная смола. Собранные все вместе части перемешиваются еще минуту. Необходимо учесть, что общая продолжительность процесса замеса не должна быть менее 5 минут, иначе качество смеси может от этого пострадать.
Информация на заметку: Керамзитобетонные блоки своими руками, Производство пеноблоков в домашних условиях
Полистиролбетон своими руками: пропорции и порядок изготовления
Наступил такой период, когда строители стали отдавать большее предпочтение современным материалам, которые имеют ряд преимуществ над устаревшими строительными элементами. Многие изделия, используемые при строительстве домов, имеют лучшие показатели теплопроводности и точки росы.
К таким современным элементам, при помощи которых происходит возведение домов, стоит отнести и полистиролбетон, своими руками который изготавливают много специалистов.
Полистиролбетон, его преимущество и недостатки
Полистиролбетон — это легкая бетонная смесь, основными элементами которой являются сам цемент и различного размера гранулы полистирола.
Этот материал имеет отличные показатели надежности и долговечности. Он быстро устанавливается и имеет приемлемую стоимость, иногда меньшую от цены традиционных элементов для возведения домов.
Использованию пенополистиролбетона и полистиролбетона отдают множество профессионалов в области строительства и возведения домов. Материал привлекает специалистов не только выдающимися свойствами, но и тем, что полистиролбетон своими руками можно создать в домашних условиях.
Организация самостоятельного производства данного материала позволит не только сэкономить денежные средства, но и создать качественное изделие, которое прослужит долгие годы.
Преимущество и недостатки полистиролбетона
Материал обладает хорошими теплоизолирующими качествамиБольшинство строителей образно узнают преимущества полистирола от знакомых, но с этим материалом стоит познакомиться подробнее, узнав все его достоинства:
- изделия из полистиролбетона имеют хорошие теплоизоляционные свойства;
- материал не выделяет вредных и токсичных веществ и является абсолютно безопасным для окружения;
- многие компании, которые производят блоки из полистиролбетона, озвучивают эксплуатационный период материала до 100 лет;
- данный строительный материал может выдерживать температурное воздействие в течение длительного периода, он считается не горючим веществом;
- низкие значения теплопроводности материала позволяют для стен домов использовать изделия толщиной от 10 см, что соответствует 25 см кирпичной кладке и 40 см шлакоблока;
- строительные элементы из полистиролбетона, практически, не проводят звук, используя блоки из данного материала для межкомнатных перегородок, помещения получаются абсолютно изолированными друг от друга;
- материал обладает хорошими гидрофобными свойствами и не подвержен воздействию грибков и плесени.
Полистиролбетон стоит отнести к хорошо обрабатываемым материалам, он легко крепится, в нем можно сверлить монтажные отверстия, изделия хорошо устанавливаются как на клеевую, так и на цементную основу. Изделия делятся на части и возможно изменять их форму методом распиловки.
Полистиролбетон, как и любой строительный материал, имеет некоторые недостатки. По сути, недостаток один, это подверженность влиянию резким перепадам температуры. После 20-30 циклов заморозки на изделиях появляются характерные трещины, что приводит к разрушению отдельных элементов и всей конструкции в целом.
Следует знать, что все разработчики материала и фирмы, которые производят из него различные изделия, для удаления этого недостатка добавляют специальные волокна, которые создаются из различных пластичных материалов, связывающих пенополистиролбетон в отдельных элементах (блоках и плитах).
Состав, пропорции и самостоятельное производство полистиролбетона
Составы полистиролбетона могут иметь различные пропорции добавляемых веществ, что разделяет материал по определенным сферам применения.
Для каждой строительной цели используется определенный пенополистиролбетон своей марки. В зависимости от сферы применения и окружающей среды эксплуатации здания из данного материала подбирается соответствующая марка полистиролбетона и выбирается определенное соотношение для создания требуемого изделия.
Также для соблюдения производственной технологии изделия из полистиролбетона должны выполняться все условия изготовления, при этом, появляется необходимость в применении качественного оборудования особенно для масштабного производства.
Варианты пропорциональных соотношений материалов для получения определенного состава полистиролбетона, требуемого для нужной цели, можно увидеть из таблицы.
Плотность (кг/м3) | Вода (л) | Цемент М400 (кг) | СДО (кг) | Полистирол (м3) |
---|---|---|---|---|
D200 | 100 | 160 | 0,8 | 1 |
D300 | 120 | 240 | 0,65 | 1 |
D400 | 150 | 330 | 0,6 | 1 |
D500 | 170 | 410 | 0,45 | 1 |
Самостоятельное изготовление пенополистиролбетона
Для экономного производства можно раскрошить уже имеющийся старый пенопластЧтобы изготовить самостоятельно пенополистиролбетон, следует приобрести основной материал. Он есть в наличии в свободной продаже во многих строительных магазинах.
Если же вы решили сэкономить, то можно раскрошить устаревшие плиты пенопласта (если они у вас есть).
Для создания хороших теплозащитных свойств в изделие необходимо добавлять древесно-омыленную смолу (СДО). Чтобы блок или плита имели надежный и защищенный верхний слой, специалисты советуют добавлять пластификаторы, но при их отсутствии можно прибегнуть к применению обычных моющих средств в пропорциях 20 мл на 1 л воды.
Бетоно-полистирольную смесь заливают в специальные формы, которые также можно сделать своими рукамиВ качестве изделий из полистиролбетона для домашнего строительства применяют блоки (созданные при помощи форм) и заливные стены (раствор заливается в готовую опалубку).
Специалисты советуют для перегородок и заливных стяжек использовать материал плотностью 350 кг/м3, а для возведения стен создавать блоки плотностью 1000 – 1200 кг/м3, так как на стены ложится большая нагрузка.
При создании изделия не стоит забывать, что вы делаете для себя. Выполненный по технологии блок прослужит вам долгие годы. Подробнее о технологии самостоятельного производства данного вида материала смотрите в этом видео:
Следует помнить, что при производстве изделий из полистиролбетона необходимо в состав добавлять поверхностные активные добавки (ПАД), которые применяются для связки раствора в комплексе с пластификаторами. Количество ПАД на 1 кг цемента должно не превышать 25 гр.
Подводя итог статье, стоит сказать, что готовые изделия из полистиролбетона являются не дешевым строительным материалом, поэтому не стоит платить лишние деньги. Организовать собственное производство изделий из данного материала под силу каждому хозяину.
Полистиролбетон своими руками: состав и пропорции
Технология производства полистиролбетона известна в России уже лет 30. Но вот предприятий по изготовлению функционирует не более трех-четырех. Хотя композитный состав из бетона и шариков пенопласта представляет собой лучший теплоизоляционный материал для строительства домов, малая востребованность остается загадкой. Кустарное производство тоже четкой тенденции в увеличении не имеет. Но если самостройщик решил ваять из ПолистиролБетона, результаты будут великолепными.
Низкое поглощение воды, негорючесть и принципиальное отличие затвора бетона – это то, за что цепляется экономный строитель. А дальновидный хозяин собственного дома еще и на отделке экономит. В этой статье мы расскажем о преимуществах полистиролбетона. На примере собственного опыта дадим несколько рекомендаций, и поделимся находками. Полистиролбетон — для тех, кто умеет правильно экспериментировать, добиваясь нужных результатов. Полученные знания обязательно пригодятся.
Все дело в цементе
Мы предполагаем, что статью сейчас читает человек, у которого во дворе залежи пенопласта, а на днях грузовик оставил поддон мешков с цементом. Может быть много вариантов дальнейших действий. Ведь к шарикам полистирола или дробленке пенопласта (не рваной) больших вопросов нет. Остается цемент и добавки. А так как с цементом трудно работать уже на этапе транспортировки, то нужно подстраховаться и лишний раз не торопиться.
Во-первых, не покупайте старый цемент. Это касается обычных заливок и бетонирования. Свежий материал в работе проявляет себя сразу. Бетон предназначен для чего-то основательного. А может ли быть даже пара бетонных блоков под подсобное помещение из старого цемента? Решать вам. Но в любом случае для полистиролбетона следует применять исключительно свежак.
Во-вторых, какую марку покупать? Для полистиролбетона нужен цемент марки 500 бездобавочный. Главное, отсутствие добавок. Есть еще несколько обозначений:
- Тип вещественного состава. Маркировка СЕМ и римские цифры от одного до пяти. Вот вам-то и нужна цифра один. То есть СЕМ I – бездобавочный.
- Подтип массовой доли добавок.
Здесь маркировка буквами А, В, С. Нас добавки уже не интересуют. Ток что пропускаем эти характеристики.
- Класс прочности. Всего их три: 32,5; 42,5 и 52,5. Эти цифры означают гарантию прочности по минимуму в мПа.
- Подкласс скорости твердения. Обозначается буквами Н, Б и М. Соответственно норма, быстро и медленно. Этот показатель лично мы не учитывали, так как применяли ускоритель твердения дополнительно. Дальше расскажем, почему.
Еще есть буковки обозначающие добавки типа шлака или золы. Из всего перечисленного ориентиром является обозначение на мешке ДО-500 СЕМ I 42,5.
Основные качества полистиробетона
Несмотря на прорыв в строительной сфере, многие до сих пор в качестве опалубки применяют доски, которые после и сжечь нельзя, и распилить. Хотя все поголовно обшивают фундамент утеплителем и наружной отделкой из сайдинга или цсп. Спрашивается, а сразу можно лить бетон в опалубку из пенопласта и отделки? Конечно, можно. Вот только предварительных расчетов и аккуратности в изготовлении будет гораздо больше.
Кто может позволить себе бетон из пенопласта, тот делает. Из полистиролбетона даже стены возводят, которые не нуждаются в дополнительной отделке, кроме окрашивания. Если применять материал для стяжки на пол, можно исключить дорогостоящее утепление. Отсюда очевидны основные характеристики и области применения полистиролбетона:
- Изготовление несущих конструкций. Речь о фундаменте и стенах. Причем если для фундамента нужен более плотный ПБ, то в стенах особенно внутренних плотность можно снизить. Составы будут отличаться не только пропорциями, но и компонентами. В более плотный материал добавляют песок. Но это уже другая история, поскольку классически состав ПБ обходится без песка.
- В качестве утеплителя ПБ показывает положительные результаты. Главное, с ним удобно работать. Он легкий по массе относительно объема.
- Точность дозировки – это еще один положительный фактор.
Вода, цемент и добавки меряются весами, а не ведрами или лопатами. Только гранулы полистирола измеряются объемом. У вас никогда не получится лишнего или нехватки.
- С правильными добавками бетон практически не впитывает влагу. Простые добавки можно купить практически в каждом строительном магазине или на рынке.
- Сохранение тепла выше, чем у газобетона и пенобетона.
- Материал не горит, независимо от вида применяемых гранул.
Полистиролбетон позволяет сэкономить на материалах. Не нужен песок, цемента требуется меньше. А за экономией гоняются все самостройщики. И если кто-то делает свой дом капитально и основательно, тратя большие деньги, то услышав про экономию на отоплении сооружения с применением ПБ, сразу же задумывается о возможном применении.
Из чего состоит полистиролбетон
Еще раз замечу, что состав подробно рассмотрен в ГОСТе. Перечислим компоненты, которые использовали сами. Критика со стороны профи будет обоснована. Но только критика, а не критиканство. Для полистиролбетона мы использовали:
СДО еще образует мелкие пузырьки. То есть вспенивает цемент. Поэтому ПБ хорошо противостоит влаге при эксплуатации. Но так как СДО мы не смогли достать, сделали эту добавку сам. Для этого нужно растворить каустическую соду в небольшом объеме воды. Сода продается в магазине бытовой химии как универсальное чистящее средство. Это и есть едкий натр, в котором нужно растворить древесную смолу. Нужно собрать немного сосновой смолы и оставить в растворе соды на два дня.
Еще мы использовали хлористый кальций и строительный ПВА. Первый для удержания воды в рабочей смеси, поскольку погода стояла жаркая. Испарение воды препятствует схватыванию цемента должным образом. Однако хлористый кальций является ускорителем твердения. Это также плюс. ПВА придавал густоту и вязкость жидкому цементу. Бетон с ПВА тянется за мастерком.
Пропорции для изготовления полистиролбетона
Перед нами стояла задача – утеплить фундамент со стороны улицы. Поэтому мы ориентировались на бетон D250. На куб требуется 1,1 куба гранул полистирола. Сократив числа в десять раз, получили значение в 11 литров. И так далее. Для изготовления 1 одного замеса нам потребовалось:
- 2 кг цемента для прочности D250.
- 1 кг воды, что означает водоцементное соотношение 0,5.
- 11 литров шариков пенопласта.
- 20 г хлористого кальция. Это 1% от массы цемента. Вообще допускается не более 2%.
- 2 г СДО. Мы использовали минимум – 0,1%.
- 2% ПВА. Его можно добавлять и больше. Но не более 10%.
- Щепотки фибры было предостаточно.
Эти все материалы не сложно было найти в нашем городе. Все, чего не хватало – было куплено в ближайшем скромненьком строительном магазине в нескольких кварталов от дома.
Пошаговое изготовление полистиролбетона своими руками
Пропорции определялись объемом емкости, в которой производили замес. Мы использовали строительную бадью в 44 литра, а гранулы отмеряли ведром из-под краски в 10 литров. Плюс сверху горочка. Пошаговое изготовление одного замеса полистиролбетона:
ШАГ 1. В бадью отмеряем 1 кг воды. Он же 1 литр.
ШАГ 2. Добавляем 20 г хлористого кальция, предварительно разведенного в пластиковом стаканчике.
Внимание! Это вещество при растворении выделяет много тепла. Можно и сразу в бадью его кинуть. Но только размешать. Иначе пластик в месте, где будет горочка этих гранул, деформируется.
ШАГ 3. Следом добавляем щепотку фибры. Достаточно несколько раз наклонить бадью из стороны в сторону. Кальций растворится, а фибра распределится по дну.
ШАГ 4. Отмеряем на весах цемент.
- Цемент D250 для полистиролбетона
- Отмеряем необходимое количество
ШАГ 5. Добавляем цемент в бадью и размешиваем миксером. Мы использовали шуруповерт со специальной насадкой.
- Добавляем цемент в смесь
- Размешиваем все миксером
ШАГ 6. После этого добавляем клей ПВА и размешиваем.
- Строительный ПВА клей
- Добавляем в смесь полистиролбетона
ШАГ 7. Далее насыпаем 11 литров гранул полистирола. Сейчас нужно хорошо поработать миксером.
- Насыпаем шарики пенопласта в ведро
- Готовим 11 литров шариков из пенопласта
- Добавляем пенопласт
- Размешиваем полистиролбетон миксером
ШАГ 8. Когда все шарики покрываются цементом, полистиролбетонная смесь готова.
Объемы укладки ПБ у нас были маленькие, поэтому работали шуруповертом. Хотя медлить с замесом не стоит.
Смесь схватывается быстрее обычного. В течение четырех дней я добавлял немного воды на уже застывший ПБ. Это было нужно из-за высокой температуры воздуха.
Для нас полистиролбетон стал открытием, поскольку бетон оказался намного легче, чем обычно. Всем известно, что самостройщики применяют другие технологии приготовления. В ход идут бетономешалки и даже ванны с лопатами. Мы же считаем, что однородность цементной смеси определяет итоговый результат. В дальнейшем можно рассматривать полистиролбетон в качестве основного при бетонировании или утеплении. Нужно только подумать об увеличении объема при производстве.
Полистиролбетон своими руками: пропорции и состав
При выборе строительных материалов застройщику приходится учитывать целый ряд требований: надежность, долговечность, простота в использовании, экологичность, экономичность. Такими свойствами обладает полистиролбетон. А чтобы сэкономить и быть уверенным в качестве материала, можно приготовить полистиролбетон своими руками, ведь технология его производства довольно проста.
Достоинства материала
Полистиролбетон многофункционален. Его применяют для возведения несущих стен в малоэтажном строительстве, для заливки перекрытий и создания перегородок, в качестве теплоизоляции. У него масса достоинств:
Применение полистиролбетона в строительстве
- Минимум оборудования. Изготовление полистиролбетона не требует сложных технологических процессов, поэтому легко наладить массовое производство.
- Огнеупорность. Этот материал способен выдерживать воздействие высоких температур.
- Низкая теплопроводность. Позволяет использовать в качестве утеплителя.
- Прочность. Полистиролбетон показывает хорошие результаты на изгиб и сжатие, морозоустойчив, выдерживает много циклов колебания температур (заморозка-разморозка), не гигроскопичен.
- Простота в обработке. Блоки из этой смеси цемента и пенопласта легко пилить, сверлить – даже вбивать в них гвозди.
- Возможность производства «на коленке». Подобрав правильные пропорции цемента и остальных составляющих, несложно справиться с самостоятельным изготовлением полистиролбетонных блоков и растворов для заливки в опалубку.
Полистиролбетон для устройства легких и утепленных полов
Недостатки
Но идеальных материалов не бывает, поэтому стоит перечислить недостатки:
- Точность пропорций. При нарушении технологии есть риск получить низкокачественный и недолговечный результат.
- Длительный период застывания и усадки. После изготовления полистиролбетона блоки нельзя использовать сразу, нужно время для полного застывания цементной основы – до нескольких недель.
- Особый крепеж. Обычным цементным раствором постройку из полистиролбетона не скрепить, нужны специальные клеевые составы. Но это скорее плюс – соединительные швы получаются гораздо тоньше, уменьшая возможность теплопотери.
- Обязательность отделки. В процессе изготовления полистиролбетонных блоков получается ровная поверхность. Но у материала низкие адгезивные свойства, поэтому прежде чем нанести краску, следует покрыть поверхность грунтовкой.
Материалы для производства
Чтобы изготовить полистиролбетон своими руками, требуется такой набор материалов:
- Гранулы вспененного полистирола. Это обычный пенопласт, но не спрессованный, а разделенный на гранулы. Чем мельче частицы, тем выше прочность итогового продукта.
- Цемент. Экономить на нем нельзя – для получения качественного материала нужен качественный цемент. Оптимальным выбором станут марки М400 и М500.
- Песок. Желательно, чтобы песок был кварцевым, но не возбраняется применение намывного песка.
- ПАД. Поверхностно-активные добавки могут быть разными, чаще всего при изготовлении полистиролбетона используется омыленная древесная стружка или моющие средства. Специальные пластификаторы тоже применяются.
- Вода. Обычная пресная вода.
- Инструменты: в зависимости от объемов, бетономешалка (в ней удобно непрерывно мешать смесь, не допуская застывания состава) или корыто и дрель с насадкой.
Пропорции для приготовления полистиролбетона
У процесса изготовления полистиролбетона есть свои маленькие хитрости, позволяющие получить более качественный результат:
- Если добавить в цементный раствор пенопластовые гранулы квадратной формы, блоки выйдут более крепкими.
- При подготовке омыленной древесной стружки ее заливают кипятком. А нужна она, чтобы раствор не расслаивался.
- Речной песок перед использованием обязательно тщательно просеивается, чтобы в цементную смесь не попали мусор и крупные камни.
Что понадобится для изготовления полистиролбетона
Пропорции цемента
Самое сложное – подобрать правильные пропорции цемента, воды и гранул. Для строительных блоков нужна одна плотность, для заливки стяжки другая, для создания теплоизоляционного слоя третья. И тут важно не запутаться, потому что основные проблемы с качеством полистиролбетонных блоков возникают именно из-за неправильного подбора плотности раствора.
Условия, используемая техника и качество исходных материалов – цемента, пенопластовых гранул и остального – сильно влияют на результат. Поэтому, собравшись изготавливать полистиролбетон своими руками, стоит вначале отработать технологию и отлить пару блоков на пробу. Если получилось не совсем то, что требовалось, необходимо внести изменения в состав и попробовать еще раз.
Примерные пропорции для производства 1 кубометра смеси разных марок различаются. Если исходить из того, что полистироловых гранул берется 0,84 кубометра, то для D200 понадобятся 100 л воды и 200 кг цемента, для D250 – 120 л и 250 кг, для D300 – 150 л и 300 кг. При изготовлении полистиролбетонных блоков можно добавить в раствор песок вместо части цемента – но не более 15% от объема.
Технология в подробностях
Чтобы не ошибиться с технологией производства полистиролбетона, необходимо следовать инструкции:
Полистиролбетон технология изготовления
- Смешать в бетономешалке (или вручную, если нужен маленький объем) воду и цемент. Должна получиться однородная масса.
- Всыпать песок и снова перемешать.
- Небольшими порциями всыпать полистироловые гранулы, каждый раз тщательно перемешивая смесь.
- Не переставая мешать, добавить выбранный ПАД.
- Залить раствор в деревянную опалубку или специальные формы.
- Подождать не менее 2–3 дней – время застывания может меняться в зависимости от температуры воздуха, влажности и других факторов.
- Достав готовые блоки из форм, их надо оставить «вылежаться» минимум на две недели – чтобы они успели набрать прочность.
При использовании опалубки легко создать сплошное перекрытие в здании. Тем же способом получаются блоки большого размера, которые потом распиливаются на небольшие – очень удобно при постройке нестандартных конструкций. Заливка в формы позволяет делать стандартизированные блоки для возведения стен и перегородок. Благодаря малому весу их может перемещать один человек.
Видео по теме: Полистиролбетон своими руками
(PDF) Дозирование легкого бетона включениями пенополистирола (EPS) и пенопласта
Dawood and Hamad / Tikrit Journal of Engineering Sciences 23 (2) (2016) 65-73
Выводы
В этой статье показано дозирование легкого бетона
, имеющего приемлемую обрабатываемость, плотность, прочность на сжатие
и модуль разрыва
, с использованием шариков EPS или пенообразователя
. Некоторые выводы
можно сделать следующим образом:
1- Плотность легкого бетона на
уменьшается с увеличением пустот
, образовавшихся за счет валиков пенополистирола или объема пены.
Таким образом, плотность легкого бетона
составила 1498 кг / м3 при включении 43,16%
EPS. Плотность пенобетона
составила 1690,84 кг / м3 за счет включения пенообразователя
1 кг / м3.
2- Для легкого бетона с валиками EPS
использование 31,5% EPS демонстрирует лучшие характеристики
с точки зрения плотности, прочности на сжатие
и модуля упругости
на разрыв.Значения для них следующие: 1726
кг / м3, 18,29 МПа и 3,2 МПа,
соответственно.
3- Для легкого бетона с использованием пенообразователя,
обнаружено использование 1 кг / м3 пенообразователя, чтобы
создавало около 15,21% пустот в легкой бетонной смеси
и, таким образом, лучшие характеристики
по плотности , прочность на сжатие
и модуль разрыва составляют:
1830 кг / м3, 34,02 МПа и 5. 36 МПа,
соответственно.
Ссылки
1- Оуэнс, П., Ньюман, Дж. И Чу Б.С.,
«Передовая технология бетона
Процессы», Elsevier Ltd, 2003.
2- Альшихри, М.М., Азми, А.М. и Эль- Бизи,
MS, «Нейронные сети для прогнозирования
Прочность на сжатие конструкционного легкого
Вес бетона», Construct Building
Material, Vol. 23, No. 6, pp. 2214-2219,
2009.
3- Бабу Д. С., Бабу К. Г. и Ви Т. Х.,
«Влияние размера заполнителя полистирола на
прочность и миграцию влаги
Характеристики легкого бетона»,
Цемент и бетонный композит, Vol. 28,
No. 6, pp. 520–527, 2006.
4- Чен Б. и Лю Дж. «Вклад
гибридных волоконв свойства легкого бетона с высокой прочностью
с хорошей
Технологичность «, Исследование цемента и бетона,
Vol.35, No. 5, pp. 913–917, 2005.
5- Chia, KS, Zhang M .H., «Water
Проницаемость и проницаемость для хлоридов
High Strength Light Aggregate
Concrete», Cement and Concrete Research,
Vol. 32, No. 4, pp. 639–645, 2002.
6- Невилл, AM и Брукс, JJ, «Concrete
Technology», второе издание, Prentice Hall,
Pearson Education, pp. 339-340, 2010.
7- Го, Ю.С., Кимура, К., Ли, М.В., Дин, Дж.
Т. и Хуанг, М.Дж., «Свойства легкого заполнителя с высокими эксплуатационными характеристиками
», Международный симпозиум по легкому конструкционному бетону
,
No. 2, pp. 548-561, 2000.
8- Mehta, PK, and Monteiro, PJM,
«Бетон: микроструктура, свойства и материалы
», третье издание, Нью-Йорк: McGraw-
Хилл, 2006.
9- Невилл А.М., «Свойства бетона»,
Четвертое и последнее издание, Прентис Холл,
, стр. 711-713, 2000.
10- ACI 213R-87, «Руководство по конструкционным
Легкие. Агрегатный бетон », Детройт,
Мичиган, 1999.
11- Вальравен, Дж.,« Самоуплотняющийся бетон
в Нидерландах », Труды Первой
Североамериканской конференции по проектированию
и использованию Самоуплотняющийся бетон,
Эванстон, США, стр. 355-360, 2002.
12- Майлд, К., Рой Р.Л., Саб, К. и Буле,
C., «Поведение идеализированного легкого бетона
EPS на сжатие: размерные эффекты и режим отказа
» . Механика материалов.
36, № 11, стр. 1031–1046, 2004.
13 — Фуад Х.Ф., Ламонд, Дж. Ф. и Пилерт, Дж.
Х. «Значение испытаний и свойств
Бетон и бетонное производство. Материалы, stp
169d, ASTM International, 2006.
14- Рамамурти К., Кунханандан Намбьяр,
Э. К. и Ранджани Г. И. С., «Классификация
исследований свойств пенобетона»,
Цемент и бетонные композиты, Vol. 31,
pp. 388-396, 2009.
15- BYUN, KJ, SONG, HW and PARK, S.
S., «Разработка конструкционного легкого бетона
с использованием вспененного полимера
, агента. ICPIC -98, 1998.
16- Шорт, А.and Kinniburgh, W.,
«Легкий бетон», 3-е изд., Applied
Science Publishers Ltd., Лондон, стр. 1-14,
1978.
17- Зулкарнайн, Ф. и Рамли, М. ,
«Характеристики конструкции пенобетонной смеси
с дымом кремнезема для жилищно-коммунального хозяйства
Легкий заполнитель бетона | Enstyro Shred
Enstyro Shred
Бетонный заполнитель
Пенополистиролсуществует уже более пятидесяти лет, почему сейчас его не используют в бетоне?
EPS (пенополистирол) был использован в бетоне.Новые шарики из пенополистирола в настоящее время продаются как заполнитель для бетона, и несколько университетов изучали измельченный переработанный пенопласт в качестве заполнителя для бетона. Оба метода малоэффективны по разным причинам.
Новые валики круглые и гладкие, что является худшей формой и поверхностью для заполнителя бетона. Когда в смесь добавляется слишком много воды, шарики в форме пузырей всплывают вверх и портят работу. Подрядчики, которым приходится срывать новую работу из-за того, что это происходит, отказываются снова попробовать EPS.Новые бусинки и молва сделали EPS плохой репутацией в бетоне.
Измельченный EPS не прижился по совершенно другой причине. Он не всплывает наверх, потому что имеет большую шероховатость поверхности. Однако он действительно содержит очень мелкие частицы, которые, будучи разорванной пеной, имеют огромную площадь поверхности. Такое огромное количество поверхности из мельчайших частиц требует слишком много воды, чтобы бетон хорошо растекался и быстро застывал. Слишком много воды снижает прочность бетона на сжатие.
Оборудование Enstyro решает проблемы путем измельчения до точного диапазона размеров с последующим удалением мельчайших частиц за один простой шаг. Этот метод дает шероховатость поверхности и изменение формы, чтобы она не всплыла даже при сильной вибрации. Удаление мельчайших частиц упрощает процесс смешивания. Влажный цемент, который легко течет и имеет высокую прочность, теперь используется вместе с переработанным пенополистиролом.
Enstyro Shred действительно лучший из всех миров, когда дело касается заполнителя EPS. Если вы уже пробовали EPS в прошлом, дайте ему еще один шанс. Enstyro потратила много времени, чтобы сделать это правильно, и теперь каждый может пожинать плоды изоляционного бетона, устойчивого к трещинам.
• Аэрокосмическая техника | • Антропология | • Агротехника |
• Агротехника | • Астрофизика | • Автоматизация и робототехника |
• Архитектура и региональное планирование | • Биология | • Биоинженерия |
• Автомобильная инженерия | • Ботаника | • Биоинформатика |
• Химическая инженерия | • Химия | • Биотехнологии |
• Гражданское строительство | • Компьютерные науки | • Строительная техника |
• Коммуникационная техника | • Вычислительная математика | • Пищевая наука и технологии |
• Компьютерная инженерия | • Науки о Земле | • Генная инженерия |
• Электротехника и электроника | • Науки об окружающей среде | • Геномика и протеомика |
• Электроника и связь | • Геология | • Обработка изображений |
• Геотехническая инженерия | • Генетика | • Иммунология |
• Промышленное проектирование | • Медицинские науки | • Информационные технологии |
• Технологии материалов и производства | • Науки о жизни | • Приборостроение |
• Машиностроение | • Математика | • Металлургические технологии |
• Оптическая инженерия | • Физика | • Молекулярная биология |
• Технологический инжиниринг | • Физиология | • Микробиология |
• Строительное проектирование | • Космические науки | • Нанотехнологии |
• Теплотехника | • Зоология | • Фармацевтические технологии |
Прочность на сжатие | EPS Industry Alliance
EPS — это легкий и прочный пенопласт с закрытыми ячейками, состоящий из атомов водорода и углерода. Механическая прочность пенополистирола зависит от его плотности. Самым важным механическим свойством изоляционных материалов и строительных материалов из пенополистирола является их устойчивость к сжимающим напряжениям, которые возрастают с увеличением плотности. EPS имеет сопротивление сжатию от 10 до 60 фунтов на квадратный дюйм для большинства строительных приложений. В этом диапазоне можно производить пенополистирол, отвечающий определенным требованиям к прочности.
ASTM C578, Стандартные спецификации для жесткой теплоизоляции из ячеистого полистирола — это согласованный стандарт производительности, разработанный производителями пенополистирола, сторонними испытательными лабораториями, регулирующими органами и специалистами в области строительства в Североамериканском регионе.Он охватывает типы, физические свойства и размеры пенополистирола, используемого в качестве теплоизоляции для температур от -65 до 165 ° F. ASTM C578 охватывает типы теплоизоляции из пенополистирола, доступные в настоящее время, и минимальные требования к свойствам, которые считаются наиболее важными. Включены значения прочности на изгиб и сопротивления сжатию. Эти значения были определены на основе ASTM C203, Метод испытаний на разрывную нагрузку и свойства изгиба блочной теплоизоляции и C165, Метод испытаний для измерения характеристик сжатия теплоизоляции и / или D1621 для метода испытания свойств жестких ячеистых пластиков на сжатие.
Для соответствия требованиям сопротивления сжатию, установленным в стандарте ASTM C578, теплоизоляционная плита из полистирола должна обеспечивать следующие значения прочности на сжатие при 10% деформации при испытании в соответствии с ASTM D 1621.
Типичные прочностные характеристики — теплоизоляционная плита EPS
Недвижимость | шт. | Тест ASTM | ASTM C 578 Тип | |||
---|---|---|---|---|---|---|
Я | VIII | II | IX | |||
Диапазон плотности | шт. | C303 | 0.90 | 1,15 | 1,35 | 1,80 |
Прочность на изгиб | фунтов на кв. Дюйм | C203 | 25 | 30 | 35 | 50 |
Сопротивление сжатию — | фунтов на кв. Дюйм | C165 или D1621 | 10 | 13 | 15 | 25 |
Для фундаментов и стен, в которых изоляция из пенопласта выдерживает минимальную нагрузку, ASTM C 578 тип I (номинальная плотность 0. 9 фунтов на кубический фут) материала вполне достаточно. Картон EPS, произведенный в соответствии с требованиями EPS типа I, был протестирован и обнаружил, что его давление составляет от 10 до 14 фунтов на квадратный дюйм. Эластичность изоляционной плиты EPS обеспечивает разумное поглощение движений здания без передачи нагрузки на внутреннюю или внешнюю отделку в местах стыков.
В кровельных покрытиях материал EPS типа I обеспечивает стабильность размеров и прочность на сжатие, необходимые для того, чтобы выдерживать легкое движение по крыше и вес оборудования при достаточно высоких температурах поверхности.Изоляция из пенополистирола может претерпевать изменения размеров и свойств при воздействии температур выше 167 ° F. Тем не менее, пенополистирол с низкой плотностью, не подвергнутый нагрузке, не покажет заметной потери стабильности размеров при температурах до 184 ° F. Продолжительность температуры, условия внешней нагрузки и плотность являются переменными, влияющими на изоляцию пеной при повышенных температурах. EPS должен быть надлежащим образом защищен от температур выше 165 ° F во время установки и может потребовать использования защитных панелей, отражающего балласта или светлой мембраны в зависимости от задействованной системы кровельного покрытия.
Оптимальные характеристики несущей изоляции часто связаны как с прочностными характеристиками, так и с упругостью. Под эластичностью понимается способность материала восстанавливать свою прочность после деформации, вызванной напряжением. Если требуется большая прочность и жесткость, можно получить сопротивление сжатию до 60 фунтов на квадратный дюйм за счет увеличения плотности изоляции EPS, чтобы удовлетворить практически любые требования к прочности на сжатие.
Изоляция из пенополистирола благодаря своим высоким характеристикам упругости и прочности предлагает:
- Поглощение движений основы и облицовки, вызванных изменениями температуры и деформациями конструкции.
- Поглощение неровностей основания.
- Восстановление толщины после чрезмерных строительных нагрузок.
- Подходящая реакция на грунте для эффективного распределения нагрузки.
Рекомендации по проектированию
Значения прочности на сжатие и изгиб для пенополистирола основаны на условиях кратковременной нагрузки в соответствии с типичными стандартами испытаний ASTM. Как и большинство несущих строительных материалов, изоляционные материалы из пенополистирола ползучесть в условиях длительной постоянной нагрузки, и в критических случаях эту характеристику необходимо учитывать при расчетах конструкции.Специалисты по дизайну должны помнить, что пенополистирол обеспечивает более высокие прочностные характеристики за счет увеличения плотности. Доступны данные, отражающие прогиб в результате непрерывного воздействия сжимающей нагрузки для изоляции из пенополистирола.
Воздействие на пенополистирол влаги в результате таких факторов, как периодическая внутренняя конденсация или влажные грунтовые условия при укладке фундамента, не влияет на характеристики механической прочности теплоизоляционной плиты из пенополистирола.
Патент США на тонкий изоляционный бетон с высокой прочностью и низким водопотреблением Патент (Патент № 4293341, выданный 6 октября 1981 г.)
ПРЕДПОСЫЛКИ ИЗОБРЕТЕНИЯДанное изобретение относится к улучшенным легким бетонам, содержащим цементирующее гидратируемое связующее и вспученный вермикулит или перлитный заполнитель с низкой плотностью, наносимый в виде влажных слоев на кровельные покрытия и т.д.
Смеси гидратируемых цементирующих вяжущих, таких как портландцемент и вспученный вермикулитовый заполнитель, широко используются для образования легких бетонов с низкой плотностью, обладающих теплоизоляционными и огнестойкими свойствами. Такие бетоны идеально подходят для использования в строительстве теплоизоляционной кровельной системы на строительной площадке. При смешивании с водой влажные вермикулит-цементные бетонные смеси можно смешивать на уровне земли и перекачивать на относительно большие расстояния под относительно высоким давлением к крышам зданий и т. п. без нежелательного разрушения пористой структуры вспученного вермикулитового заполнителя или расслоения. компоненты влажной смеси при перемешивании и перекачивании.Включение в смеси воздухововлекающих поверхностно-активных веществ для улучшения прокачиваемости и снижения плотности затвердевшего продукта давно практикуется в данной области. Изоляционные бетоны этого типа из вспененного вермикулит-портландцемента уже некоторое время успешно используются в сочетании с легкими теплоизоляционными плитами из пенопласта, например, пенополистирольными плитами, для строительства исключительно легких, теплоизоляционных, «сборных» кровель. системы. Примеры таких кровельных систем, в которых бетон заливается слоями, прилегающими к таким пластиковым изоляционным плитам, показаны на U.С. Пат. №3,619,961, Sterrett et al. и Патент США. № 3884009, Frohlich et al.
Изоляционные бетоны, содержащие пористый вспученный легкий заполнитель с высокой водопоглощающей способностью, должны быть смешаны с относительно большим количеством воды, чтобы обеспечить влажную смесь с достаточной текучестью для перекачивания. В то время как типичное соотношение воды и цемента для конструкционных портландцементных бетонов (содержащих тяжелый непористый камень и песчаный заполнитель) составляет от 0,4 до 0,7, типичное соотношение воды и цемента для легких бетонов, содержащих вспученный вермикулитовый заполнитель (содержащих обычные от 1 до 6 , соотношение цемента к вермикулиту по объему) превышает 2.Вода в таких легких бетонных смесях значительно превышает воду, необходимую для гидратации цементного компонента, и ее присутствие после укладки и отделки бетона нежелательно. Это привело в прошлом к ограниченному использованию таких изоляционных бетонов в сборных кровельных системах вышеупомянутого типа над настилом крыши или основанием крыши, которые имели ограниченные средства отвода избыточной влаги.
Из уровня техники известны легкие теплоизоляционные бетоны, требующие относительно низкого расхода воды.Известны бетоны на основе смесей цемента и вспученного перлита (объемное соотношение от 1: 3 до 1: 4) и шариков из цемента и пенополистирола (объемное соотношение от 1: 3 до 1: 5). Однако такие перлитные бетоны могут быть абразивными и их трудно перекачивать. Бетоны из пенополистирола с шариками имеют тенденцию забивать шланги во время перекачивания, особенно если шланг каким-либо образом ограничен, а также расширенные шарики имеют тенденцию всплывать на поверхность бетона. Известны также бетоны с «предварительно сформированной пеной», имеющие относительно низкую водопотребность, которые получают путем смешивания цемента с подготовленными «взбитыми» пенами, имеющими вид крема для бритья.Однако такие бетонные конструкции из «предварительно сформированного пенопласта» страдают тем недостатком, что их плотность очень трудно контролировать.
Изобретение представляет собой улучшенную изоляционную бетонную композицию из легкого цемента / вспененного заполнителя, которую можно укладывать в слои с относительно тонкими сечениями и которая имеет желаемые свойства, такие как гибкость, прочность на изгиб и растяжение, способность удерживать гвозди, контроль плотности, хороший выход, прокачиваемость. и т. д. Возможность нанесения композиции слоями тонкого сечения с хорошей прочностью и т. д.приводит к уменьшению общего количества воды, попадающей на крышу или другой субстрат. Кроме того, количество «свободной» воды, то есть воды, превышающей количество, необходимое для гидратации цементного компонента, также уменьшается при использовании бетонной композиции по настоящему изобретению. Бетоны по изобретению, таким образом, идеальны для использования в кровельных системах поверх оснований, которые в кровельном искусстве характеризуются как «не вентилируемые».
Бетонный состав согласно изобретению дополнительно демонстрирует, в частности, (а) более высокую скорость развития прочности, позволяющую раньше размещать покрытия поверх бетонного слоя; (б) более высокая плотность, прочность на сжатие и предел прочности на разрыв; (c) удерживающая способность гвоздя, равная более толстым слоям предыдущего состава, используемым в вышеописанных кровельных системах; (d) повышенная однородность, в результате чего улучшается перекачивание, выравнивание и затирка; (e) высокая степень воспроизводимости плотности и прочности в полевых условиях; и (f) меньший вес на квадратный фут площади размещения за счет возможности заливки более тонкой секции. Бетоны по настоящему изобретению, имеющие такие желательные характеристики, получают в настоящем документе путем объединения определенных выбранных компонентов в указанных пропорциях, как более конкретно определено ниже.
Усовершенствованные легкие изоляционные бетоны по изобретению получают из смесей, содержащих:
(а) одна объемная часть вяжущего;
(b) от примерно 2 до примерно 5 объемных частей вспученного вермикулита или перлита на объемную часть вяжущего вяжущего;
(c) Около 0.03 до примерно 0,08 процентов по массе цементирующего связующего из воздухововлекающих поверхностно-активных веществ;
(d) от примерно 0,005 до примерно 0,20 мас.% Цементирующего связующего вещества для диспергирования полиэлектролитического сульфоната; и
(e) Примерно до 20 процентов по массе вяжущего вяжущего инертного уплотняющего ингредиента в форме частиц.
Вышеуказанные ингредиенты можно смешивать любым удобным способом, следуя любой желаемой последовательности добавления отдельных ингредиентов. Предпочтительно сначала объединить ингредиенты меньшего размера (c) и (d) с расширенным заполнителем и, необязательно, с уплотняющим компонентом (e), а затем смешать полученную комбинацию с цементирующим веществом (e), а затем смешать полученную комбинацию с цементное связующее (а).
К сухой смеси, указанной выше (а) — (d) или (а) — (е), добавляется достаточное количество воды для гидратации цементирующего вяжущего и для того, чтобы влажная смесь была перекачиваемой, а также работоспособной после укладки.Следует избегать количества воды, превышающего то, что достаточно для гидратации цемента и придания перекачиваемости и удобоукладываемости, поскольку это нежелательно на поверхности крыши. Избыточное количество воды в смеси также может вызвать сегрегацию компонентов в смеси, что приводит к негомогенному продукту после укладки, имеющему участки, отличающиеся по прочности. Предпочтительно количество воды, добавляемой к указанной выше смеси, составляет от примерно 90 до примерно 110, особенно примерно от 95 до 105 мас. % В расчете на общую массу сухой композиции.
Вяжущий связующий компонент связывает ингредиенты композиции вместе. Здесь можно использовать любое цементирующее связующее, которое затвердевает или схватывается после смешивания с водой (далее «цементирующее гидратируемое связующее»). Портландцемент является предпочтительным таким связующим для использования здесь из-за его доступности, долговечности и устойчивости к атмосферным воздействиям. В качестве связующего компонента можно использовать другие неорганические гидратируемые связующие, известные в данной области, а также смеси двух или более различных гидратируемых связующих.Особенно предпочтительными для использования здесь в качестве связующего компонента являются портландцементы, обозначенные ASTM (Американское общество испытаний и материалов) C150 как типы I или III.
Вспученный вермикулит или легкий перлитный заполнитель, используемый здесь, имеет плотность менее 10 фунтов на кубический фут, предпочтительно в диапазоне от примерно 5,5 до 8 фунтов на кубический фут. Вспученный вермикулит или перлитный заполнитель используется в композиции для придания затвердевшему бетону легкости и низкой плотности.Вспученный вермикулит и перлит имеют ряд преимуществ перед другими легкими заполнителями, такими как частицы вспененного полистирола в изоляционных бетонах низкой плотности. Частицы вспененного полистирола имеют тенденцию всплывать на поверхность слоев литого бетона, содержащих такие частицы. Для сравнения, вспученный вермикулит и перлит не так плавают, и слои, содержащие такие, можно обработать, например «крикнул» менее проблемно. Вермикулит и перлит неорганического минерального происхождения обладают большей огнестойкостью, чем пенопласты из органических материалов.Более того, вспененный вермикулит и заполнитель перлита имеют преимущества по стоимости по сравнению с заполнителем пенополистирола. Вспученный вермикулит является предпочтительным для использования в композициях по настоящему изобретению. Агрегат вермикулита не забивает насосное оборудование и является самосмазывающимся (неабразивным для оборудования).
Хороший «выход» получается после размещения композиции по изобретению, содержащей вермикулит, и размещенные композиции имеют хорошие характеристики «скольжения», то есть легко обрабатываются.грамм. стяжкой. Легкий заполнитель из вспученного перлита дает менее желательные композиции с точки зрения «текучести» и характеристик перекачивания. Компонент вспученного легкого заполнителя композиции предпочтительно присутствует в количестве от примерно 3 до примерно 4 частей по объему на часть по объему вяжущего гидратируемого связующего компонента.
Любой из обычно используемых воздухововлекающих поверхностно-активных агентов (поверхностно-активных веществ), используемых в легких ячеистых бетонах, может быть использован в композициях по настоящему изобретению.Эти агенты захватывают воздух в композицию, когда она смешивается с водой и / или перекачивается. Увлеченный воздух не только снижает плотность затвердевшего уложенного бетона, но также способствует перекачиваемости влажной смеси. В частности, для этой цели специалистами используются поверхностно-активные сульфонаты. Натриевые соли сульфонатов альфа-олефинов, как описано в патентах США No. В качестве воздухововлекающих поверхностно-активных веществ в композициях по настоящему изобретению предпочтительны № 3926650, выданные Lange et al. Эти поверхностно-активные вещества особенно эффективны и эффективны как при высоких, так и при низких температурах.Также для этой цели в настоящем изобретении подходят омыленные или нейтрализованные продукты смолы Vinsol. Смола Vinsol — это экстракт сосновой древесины, широко известный в торговле. Считается, что это сложная смесь, содержащая высокомолекулярные фенольные соединения, смоляные кислоты, нейтральный материал и несколько второстепенных компонентов. Омыленные продукты из смолы коммерчески доступны под торговым наименованием «Vinsol NVX». Последний продукт описан в патенте США No. № 3 257 338 на имя Sefton.Другие подходящие воздухововлекающие поверхностно-активные вещества включают «Тритон Х-100», неионный конденсат октилфенола и этиленоксида, производимый Rohm & Haas Co.
, и лаурилсульфат или сульфонат натрия. Используется, по меньшей мере, количество поверхностно-активного вещества, достаточное для захвата воздуха и снижения плотности композиции на месте. Слишком большое количество поверхностно-активных веществ может привести к обрушению уложенного влажного бетона, что приведет к увеличению плотности и снижению выхода. Предпочтительная доля поверхностно-активных веществ в композициях по изобретению составляет примерно от 0.05 примерно до 0,07 процентов по массе вяжущего.
Полиэлектролитический сульфонатный диспергатор используется в композициях по настоящему изобретению для придания однородности бетонной смеси. Диспергатор образует влажную смесь кремообразной природы со стабильными суспензионными свойствами, что приводит к улучшенным характеристикам перекачивания и лучшему выравниванию и затирке по сравнению с композициями, не содержащими их. Кроме того, диспергатор, по-видимому, увеличивает плотность продукта, позволяя уменьшить количество компонента, уплотняющего частицы, в композиции по настоящему изобретению. Полиэлектролитические сульфонатные диспергаторы представляют собой соли, содержащие множество сульфогрупп. Особенно предпочтительными являются диспергирующие агенты, которые представляют собой соли полимеризованных алкилнафталинсульфоновых кислот, особенно их высокополимеризованные (высокомолекулярные) варианты. Добавление таких солей полимеризованных алкилнафталинсульфоновых кислот к композициям портландцемента в качестве диспергаторов, водовосстанавливающих агентов, «пластификаторов» и т.д. хорошо известно в данной области. Получение таких солей конденсацией альдегида, такого как формальдегид, с нафталинсульфоновой кислотой с последующей нейтрализацией описано, например, в U.С. Пат. № 2141569 на имя Такера. Приготовление и использование в бетонных композициях портландцемента высокомолекулярных версий таких конденсатных солей описано в патентах США No. № 3686133, Hattori et al.
Другие применяемые здесь полиэлектролитические сульфонатные диспергирующие агенты включают меламин-формальдегидные конденсаты, содержащие группы сульфоновой кислоты, и соли лигносульфоната. Продукты конденсации меламина и формальдегида, содержащие группы сульфоновой кислоты, продаются на рынке под торговым наименованием «Melment».Эти диспергаторы и их использование в легких бетонах описаны в патентах США No. № 3795653, Aignesberger et al. Соли лигносульфоновой кислоты, такие как лигносульфонат кальция, давно используются в качестве водовосстанавливающих агентов, «пластификаторов» и агентов, замедляющих схватывание, в композициях портландцемента. Эти материалы полностью описаны, например, в патентах США No. № 4 169 747, De Rooy et al. В композиции по настоящему изобретению включают достаточное количество полиэлектролитических сульфонатных диспергаторов для обеспечения желаемой гомогенности, насосных свойств и т. Д.Верхний предел добавляемого количества, по-видимому, определяется практичностью, поскольку продолжающееся добавление диспергатора сверх определенной пропорции не приводит к существенному улучшению полученных результатов. Диспергирующий агент на основе сульфонатного полиэлектролита или его смесь предпочтительно включают в композиции по настоящему изобретению в количестве от примерно 0,025 до примерно 1 процента от веса вяжущего связующего.
Инертные уплотняющие частицы предпочтительно используются в композиции по настоящему изобретению для увеличения плотности затвердевшей композиции и, таким образом, улучшения ее прочности на сжатие.Неожиданным результатом использования уплотняющего наполнителя является явное и измеримое улучшение смеси для воспроизводимости смеси. Бетонные партии, изготовленные с помощью уплотнителя, обеспечивали наименьшее расчетное стандартное отклонение по выходу, плотности и экономичности. Частицы инертны по отношению к другим компонентам композиции и имеют плотность выше, чем у легкого компонента, предпочтительно более примерно 50 фунтов на кубический фут. Частицы меньше примерно 0,185 дюйма (4,7 миллиметра), то есть будут проходить через 4 ячейки (U.С. экран). Предпочтительно частицы меньше примерно 0,093 дюйма (2,36 мм) и будут проходить через сито 8 меш (США). Предпочтительными уплотняющими частицами являются натуральный кладочный песок. Также подходит концентрат вермикулитовой руды или промышленный заполнитель, например щебень, гравий или чугунный шлак с воздушным охлаждением. Частицы предпочтительно имеют объемную плотность от около 50 до около 100, обычно от около 75 до 95 фунтов на кубический фут, и следующее распределение размера частиц:
______________________________________ U.S. Совокупный% экран, оставшийся от веса ______________________________________ 4 0 8 0 16 Макс. 30 30 25-60 50 65-90 100 85-98 ______________________________________
Инертные уплотняющие частицы предпочтительно используются в количестве от примерно 1 до примерно 20 процентов по массе вяжущего вяжущего.
Изобретение далее иллюстрируется следующими примерами.
ПРИМЕР I На каждые 4 кубических фута вспученного вермикулита (руда, добываемая в Южной Каролине) добавляют 15 фунтов уплотняющих частиц, 10 граммов натриевой соли высокополимеризованной алкилнафталинсульфоновой кислоты («Daxad 19», продукт W.R. Grace & Co.) и 25 граммов альфа-олефинсульфоната натрия в хлопьях из (от 90 до 91% активности) (Lakeway «301-10F», продукт Lakeway Chemical, Inc. ). Вспученная вермикулитовая руда, добываемая в штате Монтана, может быть заменена вермикулитовым компонентом, указанным выше, и в этом случае количество добавленных уплотняющих частиц увеличивается до 17 фунтов, а количество добавленной соли альфа-олефинсульфоната увеличивается до 30 граммов. Используя промышленный смеситель, такой как Strong «Deck-Mate», модель D, 95 галлонов воды смешивают с (а) 24 кубическими футами вермикулита, обработанного вышеупомянутыми добавками, и (b) 644.4 фунта портландцемента типа I (ASTM C-150) в течение 1,5-минутного периода, доводя водой до консистенции от 43 до 47 по Вика, используя конический вика, взвешенный на 50 граммов. Перекачивание полученной влажной смеси предпочтительно осуществляется с помощью объемного насоса с прогрессивной полостью и производительностью от 1 до 2 кубических футов в минуту.
Композиция по настоящему изобретению сравнивается ниже в таблице I с составом обычного легкого бетона из вспененного вермикулита того типа, который используется в сочетании с изоляционными плитами из полистирола в изолированной кровельной системе, как показано на U. С. Пат. № 3884009, Frohlich et al. Обычная бетонная смесь содержала портландцемент и вспученный вермикулит в соотношении 1: 6 по объему.
ТАБЛИЦА I ______________________________________ Затвердевший бетон на сухой основе Обычная смесь Смесь по изобретению ______________________________________ Портландцемент типа I 376 фунтов. 644,4 фунта. Exp. вермикулит 144 фунта. 144 фунта. «Lakeway 301-10F» 0,4 фунта. 0,33 фунта. «Даксад 19» нет 0,132 фунта. Уплотнение твердых частиц нет 90 фунтов. Увлажняющая вода 88.36 фунтов. 151,43 фунта. Всего партии 608,76 фунтов. 1030,39 фунтов. Средняя плотность в сухом состоянии (фунт / фут 3) 25 38 Cu. фут / партия 24,35 27,11% Выход 101,46 112,96 фунтов негидратированный цемент / фут 3 15,441 23,770 фунтов Совокупный / фут 3 5,914 5,312 фунта Свободная вода / фут 3 33,35 26,15 фунта Свободная вода / на месте 6,94 3,27 толщины (при толщине (при толщине 2,5 дюйма) 1,5 дюйма) ______________________________________
Каждая из смесей, показанных в Таблице I, представляет собой типичную полевую партию, смешанную с одним и тем же «Вика» (с одинаковой текучестью) для того, чтобы партии перекачивались примерно одинаково. Смесь согласно изобретению является «более богатой», то есть имеет объемное соотношение цемента к вермикулиту от 1 до 3,5 и имеет более высокую плотность в сухом состоянии. Общее количество воды (гидратная вода плюс «свободная» вода), требуемая для смеси согласно настоящему изобретению, больше, но более богатая цементом смесь согласно настоящему изобретению требует повышенного количества воды для гидратации и оставляет меньше «свободной» воды после размещения. Процентный выход (полученный путем деления общей массы партии на плотность перекачиваемой смеси и последующего деления результата на объем заполнителя, включенного в смесь) был выше в случае смеси по изобретению.
По сравнению с легкими бетонами типа «от 1 до 6» на основе вермикулита, обычно используемых в комбинации с пенопластовыми изоляционными плитами в изолированных кровельных системах, смеси по настоящему изобретению демонстрируют более высокую плотность, более высокую прочность на сжатие и более высокую прочность на разрыв. Таким образом, смеси по настоящему изобретению можно отливать слоями с более тонкими сечениями, чем обычные смеси, без образования трещин, особенно в местах стыков между пенопластовыми плитами, покрытыми такими слоями. Возможность заливки более тонких слоев приводит к тому, что на крышу попадает меньше воды, и слой имеет меньший вес на квадратный фут площади крыши.Композиции по изобретению также демонстрируют более быстрое развитие прочности, что позволяет раньше наносить поверх них гидроизоляционные мембраны. Способность удерживать гвоздь (сопротивление вырыванию из них механических крепежных элементов) смесей по настоящему изобретению равняется более толстым слоям обычной смеси. Более того, смеси по настоящему изобретению, по-видимому, обладают повышенной однородностью, что приводит к улучшениям при перекачивании, выравнивании и затирке.
В лабораторных экспериментах был приготовлен ряд легких изоляционных бетонных композиций, смешанных с водой, прокачанных через шланг и отлитых в виде влажных слоев. Шланг был снабжен «пережимным клапаном» для ограничения проходящего через него потока (для создания противодавления) в попытке имитировать «полевые» условия перекачки, когда смеси перекачиваются на крыши зданий. Шланг также был снабжен манометром для измерения противодавления. Были измерены некоторые свойства влажной смеси. Используемое оборудование для смешивания и откачки было типа, описанного в Примере I. Композиции перечислены в Таблице II. Свойства влажной смеси композиций перечислены в таблице III.Все композиции содержали 107,4 фунта портландцемента типа I (марка «Marquette»). За исключением бетонов с 1 по 4, все смеси имели конструкцию «от 1 до 3,5», то есть отношение объема цемента к легкому заполнителю составляло от 1 до 3,5. Объемное отношение цемента к легкому заполнителю в смесях 1-4 составляло 1: 3,41. Воздухововлекающий агент, обозначенный «А» в таблице II, представляет собой альфа-олефинсульфонат, как в примере I. Воздухововлекающий агент, обозначенный «В», представляет собой «Vinsol NVX», как описано ранее.
Диспергирующим агентом, обозначенным «X» в таблице II, был «Melment F10», коммерческий продукт Suddeutsche kalkstickstoff-Werke AG, сульфонат натрия смолы меламиноформальдегидного типа, описанный ранее. Диспергатор «Y» в Таблице II представляет собой солюбилизированный, обессахариваемый путем ферментации лигносульфонат кальция (50% водный раствор), не содержащий пеногасителя и полученный из древесины мягких пород, такой как ель и болиголов. Диспергатор «Z» представляет собой «Daxad I9», как описано ранее.
В Таблице III измерения, проведенные для мокрых смешанных и перекачиваемых композиций Таблицы II, были следующими; «Фунты.Wat / FBM «- количество воды в каждой из пронумерованных композиций на дощатый фут смеси, то есть количество воды в слое размером один фут на фут на один дюйм залитой композиции;»% выхода «- это рассчитанное как описано ранее; «Расчетная плотность в сухом состоянии» получается путем измерения плотности образца мокрой перекачиваемой и размещенной смеси и на основе этого расчета ожидаемой плотности смеси после высыхания и затвердевания, то есть после потери избыточной воды воды, прореагировавшей с цементом, как «гидратная вода», «обратное давление в шланге» считывается с манометра, установленного на шланге, а «перекачиваемая жидкость по Вика» — это мера текучести перекачиваемой смеси, полученная путем падения 50-граммового конического груза. в образец влажной смеси с заданной высоты и измеряя расстояние в миллиметрах, на которое он опускается в образец.Чем больше расстояние, тем более «текучей» считается влажная смесь.
ТАБЛИЦА II __________________________________________________________________________ Легкий уплотняющий СОСТАВ Расширенный воздухововлекающий диспергатор № Тип заполнителя Граммы Тип Граммы (фунты) __________________________________________________________________________ 1 Вермикулит A 25 X 9,3 15 2 Вермикулит A 25 Y 20,5 15 3 Вермикулит A 30 X 10 17 4 Вермикулит A 30 Y 20,5 17 5 Вермикулит B 50 Z 10 15 6 Вермикулит B 75 Z 10 15 7 Вермикулит B 100 Z 10 15 8 Перлит A 25 Z 10 15 9 Перлит A 25 Z 10 15 10 Вермикулит A 25 Z 488 15 11 Вермикулит A 25 Z 244 15 12 Вермикулит A 25 Z 10 Нет 13 Вермикулит B 50 Z 10 15 14 Вермикулит B 75 Z 10 15 15 Вермикулит B 100 Z 10 15 16 Перлит A 25 Z 10 15 17 Вермикулит A 25 Z 10 15 18 Вермикулит A 25 Z 10 15 19 Вермикулит A 25 Z 488 15 20 Вермикулит A 25 Z 10 Нет 21 Вермикулит A 25 X 10 15 22 Вермикулит A 25 Y 20. 5 15 23 Полистирол A 25 Z 10 15 гранул 24 Вермикулит A 25 Z 10 15 __________________________________________________________________________
ТАБЛИЦА III __________________________________________________________________________ СОСТАВ, фунты. Вода% Расчет. Сухой шланг с обратной перекачкой NO. на FBM Плотность выхода Давление Vicat __________________________________________________________________________ 1 2,75 124,69 36,07 50 PSIG 44 мм 2 2,77 126,09 35,23 50 PSIG 43 мм 3 2,64 130,06 34,99 50 PSIG 42 мм 4 2.74 127,28 35,77 50 PSIG 44 мм 5 2,53 124,50 35,60 50 PSIG 37 мм 6 2,53 125,34 35,27 50 PSIG 39 мм 7 2,48 131,24 33,72 50 PSIG 40 мм 8 1,91 132,35 30,51 15 PSIG 43 мм 9 2,25 118,32 34,49 53 PSIG 42 мм 10 2,38 126,00 35,47 50 PSIG 40 мм 11 2,40 129,68 34,36 50 PSIG 41 мм 12 2,50 123,82 32,73 50 PSIG 39 мм 13 2,58 122,00 36,43 80 PSIG 36 мм 14 2,49 125,62 35,44 70 PSIG 36 мм 15 2,43 129,00 34,35 80 PSIG 34 мм 16 2,34 105,00 40,19 35 PSIG 45 мм 17 2,49 126,41 34,85 80 PSIG 35 мм 18 2,47 127,75 34,72 90 PSIG 32 мм 19 2. 32 126,00 35,43 85 PSIG 36 мм 20 2,38 126,00 32,09 80 PSIG 34 мм 21 2,71 122,54 36,00 80 PSIG 40 мм 22 2,79 118,40 37,15 80 PSIG 41 мм 23 1,14 133,95 28,37 42 PSIG 42 мм 24 2,37 133,71 32,75 85 PSIG 39 мм __________________________________________________________________________
Следующие комментарии могут быть сделаны относительно лабораторных экспериментов, описанных в Примере III (Таблицы II и III). Противодавления в шланге, которые пытались создать путем ограничения шланга с помощью «пережимного клапана», считаются «низкими» в случае Композиций 1-12 (Таблица III) в том смысле, что эти противодавления ниже, чем можно было бы ожидать, если Композиции закачивались в реальных полевых условиях на крыши зданий и т.п.Композиции 20 и 21 можно рассматривать как «контрольные» смеси в том смысле, что они предпочтительны согласно настоящему изобретению. Данные о смесях, содержащих «Melment F10», лигносульфонат кальция и «Vinsol NVX», показывают, что эти материалы являются приемлемыми заменителями. По сравнению с двумя «контрольными» смесями, смеси, содержащие «Melment F10», по-видимому, снижали «выход» и увеличивали плотность. Диспергатор на основе лигносульфоната кальция в виде 42% общего количества твердых веществ, добавленных к «Даксаду 19», по-видимому, оказывал более выраженное влияние на снижение «выхода» с соответствующим увеличением плотности.«Vinsol NVX», кажется, действует как воздухововлекающее средство «классическим» способом, увеличивая «урожайность» по мере увеличения его количества. Замена вспученного перлита в качестве легкого заполнителя, по-видимому, приводит к смеси, которая требует меньше воды (около 22%) по сравнению с двумя «контрольными». Смеси, содержащие перлит, имели низкие характеристики выхода и откачки (по сравнению с контролями). Усадка после формования всех трех перлитовых смесей была значительной, что было подтверждено измерениями толщины литых образцов прочности на растяжение и изгиб.Количество воды, требуемое для композиции, содержащей гранулы пенополистирола (№ 23), было снижено на 51 процент по сравнению с двумя «контрольными».
Шарики имели удельный вес 1,075 фунта / куб. футов. Выход полистиролсодержащей композиции был очень высоким, и тщательный осмотр этой композиции после накачивания не выявил истирания гранул или разрушения. Перекачивающие свойства смеси, содержащей полистирол, были крайне плохими. Даже при «низком» противодавлении 42 фунта на квадратный дюйм периодическое засорение «пережимного клапана» полистироловыми шариками было правилом.Смесь, содержащая полистирол, не будет перекачиваться при более высоком давлении в условиях эксперимента, но, конечно, эксперимент не обязательно указывает на то, что смесь будет работать так же в реальных «полевых» условиях, когда не используется «пережимной клапан» для моделирования «полевые» условия. Оказалось, что высокий уровень «Даксад 19» снизил потребность в воде. Композиции, не содержащие уплотняющих частиц (песка), требовали на 5% меньше воды и имели на 7-8% более низкую плотность бетона, чем контрольные смеси.
Для проверки характеристик композиций по изобретению в реальных «полевых» условиях в 1978 календарном году композиции были смешаны, закачаны и отлиты в виде слоев, выступающих в качестве компонентов изоляционных кровельных систем, которые были нанесены на крыши нескольких зданий, расположенных в США и Канада. В таких изолированных кровельных системах бетонные композиции наносили слоями, смежными со слоем, образованным множеством пенополистирольных плит, как показано в вышеупомянутом U.Патент S. Frohlich et al. Полистирольные плиты имели ряд сквозных отверстий, как показано в патенте Frohlich et al. Сначала на кровельную основу был нанесен тонкий слой бетонной композиции, который скрепил слой пенопласта с основанием. Дополнительный более толстый слой бетонной композиции был нанесен поверх слоя вспененных плит и, наконец, поверх этого дополнительного более толстого слоя бетона была нанесена обычная гидроизоляционная мембрана. Бетонные композиции были приготовлены в соответствии с примером I, то есть все компоненты, за исключением цемента и воды, сначала были объединены, а затем упакованы.Упакованные композиции смешивались с водой и цементом на стройплощадке и закачивались на крыши крыш зданий. К индивидуальным установщикам систем, в которых применяются композиции по изобретению, входили несколько коммерческих специалистов по нанесению кровельных систем, которые согласились заменить новыми композициями согласно настоящему изобретению ранее приобретенную изоляционную бетонную композицию обычного типа, описанного выше.
Каждое приложение и информация, относящаяся к каждому, например, тип здания, местоположение и т. Д., приведена в таблице IV.
ТАБЛИЦА VI __________________________________________________________________________ 1978 г. Применения в полевых условиях № № задания Тип кровли Бетонные мешки для крыши № выхода. Дата Расположение здания Площадь основания (кв. Фут) Партии Цемент Остаток% __________________________________________________________________________ 1 марта 29 Офис в Пенсильвании Существующая крыша 1980 Неизвестно Неизвестно Неизвестно Неизмеримо 1978 2 8 июня Склад в Канаде Стальная вентилируемая 22661 176 1238 1056 113.8 1978 3 марта 30 Лаборатория С. Каролина Существующая крыша 1000 7 48 42 123,7 1978 Укрытие 4 мая 1 Выставочный зал Флорида Бетонные тройники 9600 68 470 408 109,1 1978 5 июня Школа Флорида Существующая крыша 4455 Не залита Не залита Не залита Не залита 1978 6 июля 19 Школа в Нью-Йорке Существующая крыша 4687 39 273234 111,2 1978 7 сентября 25 Больница Миссури Монолитная 6828 56 392 336 107,8 1978 бетон 8 ноября 9 Больница Пенсильвания Монолитная 6172 49 335 294 111,7 1978 бетон 9 21 ноября Школа Пенсильвания Бетонные тройники 10080 65 446 390 110. 4 1978 г. __________________________________________________________________________
Работы, пронумерованные 1,3 и 6 в Таблице IV, относятся к типу, который в кровельном искусстве называется «повторное кровельное покрытие», то есть строительство новой кровельной системы поверх существующей крыши. В этих работах существующие покрытые крыши состояли из слоев обычной «застроенной» кровли (один или несколько слоев асфальтовых листов, склеенных между собой асфальтом) с верхним покрытием из гравия и, таким образом, были «не вентилируемыми». В работе № 2 покрытая основа крыши была сделана из стали с просверленными в ней отверстиями для выхода влаги.В работах 4 и 9 покрытый субстрат крыши состоял из ряда сборных бетонных секций, имеющих Т-образную форму в поперечном сечении. В работах 7 и 8 покрытые основания крыши представляли собой бетонные настилы, сформированные путем заливки монолитных бетонных плит на рабочих площадках.
Как видно из Таблицы IV, в общей сложности было покрыто 63 000 квадратных футов крыш и было представлено четыре типа оснований. Смешивание, перекачивание и укладка бетонных композиций по настоящему изобретению осуществляли лица, которые включали 5 различных коммерческих фирм.Были отмечены некоторые недостатки оборудования, в частности, некалиброванные водомеры, но не было выявлено проблем, которые не были бы обычными для обычных ранее используемых легких изоляционных бетонных композиций. Семь работ, показанных в Таблице IV, были проверены и опробованы в 1979 году для определения содержания влаги и, если возможно, прочности на сжатие и плотности бетона. Работа № 9 была пропущена, потому что в ней использовалась гидроизоляционная мембрана, которую было бы трудно отремонтировать, если бы ее разрезать для отбора проб.В таблице V указано содержание влаги в отобранных и испытанных бетонах по изобретению и в пенополистирольной плите непосредственно под ним. Также указан возраст бетона при отборе проб, плотность, прочность на сжатие, толщина сердцевины и «открытое время» бетона, то есть временной интервал между заливкой бетонного слоя и нанесением на него последнего гидроизоляционного слоя.
В Таблице IV сразу было отмечено, что бетон, использованный в Работе № 3, значительно суше, чем остальные.Считается, что это связано со сравнительно длительным «открытым временем» этой работы и преобладающими условиями высокой температуры окружающей среды и ветра. Также на палубе, покрытой этой работой, были боковые отверстия для отвода влаги.
ТАБЛИЦА V __________________________________________________________________________ Open Wt. % Влажности Начальное время работы в возрасте отбора проб Образцы с бетонным наполнителем,% свободного (количество в сухом состоянии (дни) Возраст бетонной плиты (Мо) Толщина PCF PSI на водной основе) __________________________________________________________________________ 1 6 52.0 * 3,0 1,28 дюйма 31,0 213 * 1 6 36,5 92,0 17,0 1,3 дюйма * * * 2 12 30,3 * 0,25 * * * 64,6 2 12 24,4 28,6 6,0 * * * * 64,6 3 13 21,7 27,6 0,6 1,87 дюйма 38,0 * 77,0 3 13 10,2 25,6 1,6 1,25 дюйма 37,4 * 77,0 3 13 19,3 55,9 2,5 1,75 дюйма 36,2 * 77,0 3 13 9,2 73,8 4,6 1,63 дюйма 40,7 * 77,0 3 13 12,4 64,8 5,8 1,5 дюйма 38,2 * 77,0 3 13 9,3 20,9 8,5 1,62 дюйма 37,3 * 77,0 3 13 7,0 19,6 11,3 1,63 дюйма 40,0 * 77,0 3 13 10,6 32,8 11,3 1,0 дюйма * * 77,0 4 Неизвестно 60,4 38,3 11,5 2,75 дюйма 34,1 349 68,0 6 4 33,1 39,3 11,0 1,89 дюйма 39,8 402 59,8 7 3 37,3 12,1 9. 0 2,3 «37,4 381 61,2 8 3 51,2 32,4 9,0 2,01» 34,5 416 67,1 __________________________________________________________________________ * Недоступно
Международный журнал инженерного менеджмента и прикладных наук
Международный журнал новейших технологий в машиностроении, менеджменте и прикладных науках — IJLTEMAS
Международный журнал новейших технологий в инженерии, менеджменте и прикладных науках (IJLTEMAS) — это ежемесячный рецензируемый международный журнал по инженерным наукам, менеджменту и прикладным наукам с минимальной платой за обработку.Мы обеспечиваем отличную платформу для обмена мнениями между исследователями, широко заинтересованными в области инженерии, менеджмента и прикладных наук.
Научно-исследовательское и инновационное общество
Общество исследований и научных инноваций (RSIS International) — ведущее международное профессиональное некоммерческое общество, которое способствует прогрессу исследований и инноваций посредством международных конференций, дискуссий, семинаров и публикации профессиональных международных онлайн-журналов, информационных бюллетеней и проведения исследований и инноваций. на международном уровне.
Прием статей Февраль 2021 г.
Международный журнал новейших технологий в инженерии, менеджменте и прикладных науках — IJLTEMAS приглашает авторов / исследователей предложить свои исследовательские работы в области инженерии, менеджмента и прикладных наук. Все заявки должны быть оригинальными и содержать соответствующие результаты исследований в области инженерии, менеджмента и прикладных наук. Мы нацелены на качественную исследовательскую публикацию и предоставляем читателю достоверные исследования.
Правила подачи заявок
Срок подачи | 26.01.2021 — 25.02.2021 |
Новое представление | Подача онлайн |
Окончательная подача принятой статьи | Подача онлайн |
Месяц / Год / Объем / Выпуск | Февраль 2021 г.![]() |
Сборы за публикацию (индийские авторы) | 900 INR |
Сборы за публикацию (международные авторы) | 20 $ |
Почему открытый доступ?
Журналы открытого доступа доступны бесплатно в Интернете для немедленного открытого доступа во всем мире к полному содержанию статей, отвечающих интересам основных исследователей.Каждый заинтересованный читатель может бесплатно читать, скачивать или потенциально распечатывать статьи в открытом доступе! Мы приглашаем подавать документы превосходного качества только в электронном (только .doc) формате.
Оптимальное использование полистирола при производстве бетона
Ecoratio помогает вам реализовать детали в ваших бетонных элементах с оптимальным использованием полистирольных форм. В дополнение к разделительным агентам для ваших форм Ecoratio предлагает раствор для клеевого полистирола, который остается на бетоне.В этом блоге мы обсуждаем использование полистирола и преимущества полистирола Ecoratio для вашей компании!
Использование полистирола при производстве бетона
Полистирол используется при производстве бетона для придания формы бетонным элементам. Полистирол легко обрабатывать, а формы можно создавать по индивидуальному заказу, что позволяет создавать бетонные элементы различной формы и геометрии. Это контрастирует с деревом, которому труднее придавать форму и к которому бетон легко прилипает.
Полистирол не оказывает прямого влияния на качество бетонной поверхности. Однако при низком качестве полистирола он может сломаться, в результате чего весь бетонный элемент будет покрыт гранулами полистирола. Это отрицательно сказывается на производственном процессе в виде дополнительного времени на очистку.
Как использовать полистирол? Используйте высококачественные полистирольные продукты в сочетании с высококачественными разделительными добавками, чтобы предотвратить разрушение полистирольных форм и образование гранул на бетонном элементе. Полистирол не только сэкономит вам время на чистку, но и его можно использовать повторно, что дешевле и долговечнее.
Как Ecoratio может помочь при использовании полистирола
Хороший и эффективный разделительный состав важен для удаления полистирольной формы с бетонного элемента. Ecoratio конкурирует здесь с различными продуктами, но по сравнению с конкурентами отличается в нескольких отношениях.
Конкурентоспособная продукция имеет то преимущество, что стоимость покупки ниже.Это связано с продуктовой базой нефти. Однако дополнительными недостатками являются воспламеняемость продуктов на нефтяной основе и наличие предупреждающих надписей.
Удобство использования
Благодаря составу продукта Ecoratio для полистирола, агент тоньше других агентов и поэтому его легче наносить. Кроме того, в отличие от продуктов конкурентов, полистирол Ecoratio легко наносится благодаря яркому зеленому цвету. Это делает нанесение оптимальным, так что в процессе высвобождения полистирола не происходит повреждений.
Лучшие результаты
Благодаря многолетним исследованиям Ecoratio является экспертом в области разделительных смазок и сопутствующих продуктов.
Таким образом, производство полистирольных форм из бетонных элементов также является успешным.
Полистирол остается неповрежденным и не оставляет остаточных частиц.
Сейф для людей и планеты
Весь ассортимент продукции Ecoratio состоит из экологически чистых продуктов, которые не представляют опасности для людей и окружающей среды.Разделительный продукт, который вы используете для форм из полистирола, также сделан из натуральных материалов растительного происхождения без вредных растворителей, влияющих на окружающую среду или рабочую среду.
С продуктами Ecoratio вы ощутите большое удобство, сэкономите время и дополнительные расходы. Хотите сами убедиться, какие преимущества Ecoratio может предложить вам? Загрузите наши продукты и услуги для электронных книг, чтобы получить обзор возможностей.