состав и пропорции, плотность материала и изготовление своими руками, рекомендации по выбору
На протяжении многих лет бетон являлся одним из наиболее востребованных строительных материалов, с помощью которого возводились всевозможные конструкции и постройки. В настоящее время у стройматериала есть масса разновидностей, имеющих ряд преимуществ и свойств. В их числе — высококачественный шлакобетон, который показывает отличные прочностные показатели и стоит сравнительно недорого.
Особенности и состав
Шлакобетон представляет собой очень популярный стройматериал, который продается по доступной цене и при этом соответствует всем нормам современного строительства. Из-за многих плюсов материал широко задействуется в разных строительных направлениях в том числе и в частном возведении домов. Застройщики массово покупают шлакоблоки и создают на их основе качественные постройки разного назначения. Многие начинающие мастера часто интересуются, можно ли изготовить своими руками шлакобетон?
Состав данного материала не содержит в себе труднодоступных или дорогих компонентов, поэтому решить такую задачу вполне возможно. Из названия становится понятно, что одним из ключевых элементов шлакобетона является промышленный шлак, т. е. всевозможные отходы. В их числе может быть обычная древесная зола. Роль вяжущей добавки исполняет цементная смесь повышенной марки. Еще к составу добавляют известь, воду, песок и ряд химических компонентов.
Перед тем как начать изготовление шлакобетона своими руками, нужно внимательно рассмотреть пропорции и состав. В настоящее время он сводится к следующему:
- Цементная смесь будет использоваться в качестве вяжущего элемента и повышать прочностные характеристики будущей конструкции. Кроме этого, строители добавляют к шлакобетону и известь.
- Что касается размеров зерен шлака, то они зависят от марки шлакобетона.
- Зачастую в составе материала имеются такие добавки как кирпичная, бетонная или цементная крошка, перлит и отсев щебня.
- Для повышения плотности можно задействовать наполнитель с небольшой фракцией. Если используются крупные фракции, это приведет к появлению противоположного эффекта: показатели теплоизоляции существенно вырастут, а прочность — упадет.
- Промышленные производители шлакобетона добавляют в свое сырье всевозможные химические добавки. Их вариативность бывает чрезмерно высокой и зависит от индивидуальной рецептуры, которая используется торговой маркой. Основное предназначение таких элементов заключается в повышении пластичности, сокращении времени схватывания и твердения, улучшения качеств готовых блоков и т. д.
- Если применять щелочной раствор, то это позволит получить высококачественный шлакощелочной бетон. В таком случае состав материала будет содержать в себе шлак, а также крупный или мелкий заполнитель. Среди ключевых свойств подобного стройматериала выделяют превосходную устойчивость к морозам и проникновению влаги. Его задействуют для возведения построек в экстремальных условиях эксплуатации в том числе и в северных регионах.
Исходя из вышесказанного, можно сделать вывод, что состав и пропорции компонентов шлакобетона напрямую влияют на конечное качество и характеристики материала.
Поэтому при самостоятельном изготовлении нужно тщательно подобрать состав и не отклоняться от рецептуры.
Свойства и технические характеристики
Готовый строительный материал может обладать разными свойствами. Чтобы найти оптимальный вариант для будущего проекта, нужно тщательно разобраться с его техническими характеристиками. Итак, шлакобетон может отличаться такими показателями:
- Морозостойкость. Шлакобетонные блоки обладают разной маркой устойчивости к морозам. Зачастую она увеличивается вместе с плотностью и прочностью, а максимальное количество циклов, которое выдержит будущее изделие, варьируется от 15 до 50. Особую роль отыгрывает и индивидуальная рецептура производителя, ведь некоторые модели способны демонстрировать около 150 циклов.
- Гигроскопичность. Еще одним рабочим свойством шлакоблоков является высокое водопоглощение. Материал способен впитывать влагу до семидесяти пяти процентов.
- Проводимость тепла.
Варьируется в зависимости от показателей удельного веса.
- Значения плотности и коэффициент теплопроводности.
- Эксплуатационный срок. Если возводить стеновые конструкции из шлакоблоков, срок их службы может превысить 100 лет.
- Пропускание звука. Показатели звукопоглощения достигают 43 дБ.
- Огнестойкость. Качественный материал без особых сложностей выдерживает контакт с огнем вплоть до 800 градусов Цельсия.
Согласно официальным стандартам, на основе шлакобетонного стройматериала можно возводить всевозможные помещения с максимальной этажностью до 3 этажей. Правда, это касается только несущих конструкций.
Габариты полнотелого изделия составляют 390х190х188 миллиметров. В свою очередь, пустотелые модели обладают шириной 120 или 90 мм.
Преимущества и недостатки
Нередко начинающие строители не могут определиться с выбором стройматериала для своего проекта. Это не странно, ведь вся продаваемая в гипермаркетах продукция может обладать и плюсами, и недостатками. Шлакобетон не исключение.
Если говорить о его плюсах, то они следующие:
- Изделия из шлакобетона способны сохранять тепло, что обусловлено соответствующей плотностью.
- Материал демонстрирует неплохие прочностные показатели. В связи с этим его внедряют для самых различных строительных работ.
- Из-за высокой устойчивости к морозам шлакоблоки можно использовать в специфических климатических условиях, например, на Крайнем Севере.
- На рынке предоставлены различные виды блоков и других изделий из шлакобетонного состава.
- Сроки службы материала превышают сотню лет.
- Монтаж и работа со шлакоблоками не требуют особых усилий или навыков. Из-за крупных габаритов процесс строительства существенно упрощается.
- Немаловажным достоинством шлакобетонных блоков является устойчивость к огню и биологическая стойкость.
- Если сравнивать стройматериал с другими, то он стоит гораздо дешевле, что снижает расходы на возведение постройки.
- У шлакоблоков хорошее шумопоглощение и паропроницание.
- Изготовить материал своими руками совсем несложно, т. к. технология производства предоставляется в свободном доступе и не имеет каких-либо секретов. Достаточно подготовить пропорции и найти пошаговое руководство по замешиванию.
Однако, как и у любой другой продукции, у шлакобетона есть и недостатки. К ним относятся следующие пункты:
- Наличие усадки, что заставляет строителей начинать отделочные работы только по истечении определенного срока времени.
- Для достижения марочной прочности нужно ждать несколько дней.
- Если заниматься самостоятельным производством материала, то за процессом нужно постоянно следить, периодически смачивая изделия для предотвращения появления трещин.
- Декоративные свойства шлакоблоков невысокие.
- При высокой плотности шлакобетона его вес становится очень большим.
Также повышается коэффициент теплопроводности, что заставляет строителя выполнять ряд работ по утеплению постройки.
- Гигроскопичность — весомый недостаток материала.
Основные разновидности
После тщательного изучения состава шлакобетона, пропорций и характеристик, нужно разобраться с существующими разновидностями материала, который доступен на рынке. Шлакоблоки бывают пустотелыми и полнотелыми.
Первый тип обладает небольшим весом, т. к. в его составе присутствуют пустоты. Его отличает повышенная теплоэффективность, но небольшая плотность. Такие блоки незаменимы при сооружении частных домов, пристроек, гаражей и прочих промышленных конструкций.
Изделия полнотелого типа демонстрируют повышенную плотность. Однако это сказывается на весе и конструкционных свойствах. Из недостатков полнотелых блоков — низкая теплоэффективность. В большинстве случаев из такого сырья создают несущие конструкции разного назначения.
В зависимости от назначения шлакобетон может быть лицевым и рядовым.
Первая разновидность имеет одну или 2 облицовочные поверхности, а рядовые применяются для основных кладочных работ.
Как уже говорилось раньше, при выборе состава можно использовать различные вяжущие добавки. Тип этих компонентов определяет торговую марку и свойства материала:
- СКЦ — содержит в своем составе цементную смесь.
- СКШ — изготовляется из шлака.
- СКГ — создан на основе гипса.
- СКИ — содержит известь.
Конструкции также могут быть стеновыми или перегородочными. Последний тип характеризуется небольшим диаметром и является незаменимым элементом для обустройства перегородок. С его помощью нередко создают основания зданий.
В строительной сфере широко распространены шлакоблоки из тяжелых и легких составляющих. Кстати, легкий бетон нередко называется «теплым». Он способен сохранять тепло внутри помещения, весит сравнительно немного, но не может похвастаться внушительность плотностью. Тяжелые конструкции обладают отличными прочностными показателями и большим весом. Их устойчивость к различным воздействиям и нагрузкам находится на высоком уровне.
Кроме традиционного исполнения, шлакобетон может предлагаться в виде плит. Такие конструкции заслуживают особого внимания, т. к. они характеризуются многими эксплуатационными свойствами и достоинствами. Их создают на основе шлакобетона с маркой не ниже М50. В качестве армирующего элемента задействуется стальная сетка с ячейками 10 на 10 сантиметров. Роль вяжущего компонента исполняет цементная смесь марки не меньше М25.
Технология изготовления
Создать шлакобетонный блок своими руками относительно несложно. Зная об основных тонкостях состава и пропорциях, а также найдя пошаговое руководство, можно решить такую задачу за короткий промежуток времени.
Для начала нужно подготовить специальное оборудование и материалы. К ним относятся:
- Вибропресс.
- Бетономешалка.
- Заготовочная форма.
Также в строительных гипермаркетах доступны небольшие установки для массового производства блоков, которые повышают объемы производства в несколько раз. Что касается стационарного оборудования, то оно обладает колоссальной мощностью и работает в автоматическом режиме. Но для частных целей покупка таких систем нецелесообразна, т. к. стоимость установки очень высокая. В свою очередь, небольшой вибропресс или станок для создания бетона можно создать самостоятельно.
Рекомендации по выбору
При покупке материалов нужно руководствоваться некоторыми правилами и рекомендациями:
- Лучше отказаться от просроченного сырья и материалов с недостаточно качественной консистенцией. В первую очередь нужно обращать внимание на состояние цементной смеси — она не должна иметь в своем составе комков.
- Рекомендуется покупать компоненты у проверенных поставщиков.
Такой подход позволит снизить затраты на доставку и получить экономию.
Пошаговое руководство
Доставив все нужные инструменты и материалы на объект, можно начинать производство шлакоблоков. Для начала нужно провести замес раствора, предварительно подготовив шлак и просеяв его через мелкое сито. Также на этом этапе нужно разделить его на две фракции — крупную и мелкую. Последней фракции должно быть в два раза больше, что положительно повлияет на прочностные свойства.
- Для повышения плотности шлак можно покрыть водой и щелочным составом. Это снизит уровень гигроскопичности.
- Дальше нужно смешать две фракции шлака и добавить оставшиеся компоненты. После появления однородной массы можно начинать заливать ее в формы.
- Следующий этап заключается в уплотнении бетона с помощью вибропресса.
- Как только бетон начнет частично застывать, его можно достать из формы.
В завершение остается просушить материал и дождаться окончательного затвердения.
Вот и все — при небольших усилиях и минимальных затратах времени и финансов можно самостоятельно изготовить столь востребованный строительный материал.
цемент, шлак, песок и вода, технология изготовления
При возведении небольших зданий, хозяйственных пристроек, гаражей используются недорогие стройматериалы. Для стен оптимальным вариантом является шлакоблок. Это настолько дешевый и простой в производстве искусственный камень, что его вполне можно изготовить своими руками. Главное – соблюсти верные пропорции раствора.
Особенности и область применения
Шлакоблок представляет собой искусственный камень, который состоит из смеси воды, цемента и наполнителя. В качестве последнего используется шлак – измельченные отходы, образовавшиеся в результате:
- производства металла в доменных, мартеновских печах;
- некоторых химических процессов;
- сжигания разных видов твердого топлива (каменный уголь, торф, горючие сланцы и другие).
Шлакобетон относится к легким видам бетонов плотностью до 1800 кг/м
В заводских условиях пропорции раствора соблюдаются очень точно, ведь от этого зависит качество шлакоблока. Готовая смесь заливается в формы и отправляется на вибропрессование, реже – автоклавирование (пропаривание и прессовка). Благодаря данной технологии срок производства сокращается до нескольких дней. Стандартные габариты: 39х19х18,8 см.
Если шлакоблок изготавливается своими руками, то акцент делается на правильную рецептуру и естественные условия вызревания так называемых цементных минералов:
- Срок сушки – не менее 28 дней.
- Влажность – минимум 60 %.
- Температура – от +15 до +25 °С.
Нередко для шлакоблока, изготовленного самостоятельно, используются дешевые и доступные для конкретного региона заменители шлака: гранитный щебень, отсев, кирпичный бой, бетонный скол и многое другое.
Несмотря на разную рецептуру, полученные изделия условно называют одним и тем же термином – «шлакобетонные блоки».
Сферы применения: при возведении складских зданий, времянок, гаражей, помещений хозяйственного назначения (сарай, котельная), подвалов, беседок и тому подобное. Материал отличается высоким уровнем гигроскопичности, поэтому строение нуждается в полноценной гидроизоляции.
Пропорции компонентов
Раствор для производства шлакоблока готовится из следующих составляющих:
1. цемент марки не ниже М350. Иначе изделие получится недостаточно прочным и быстро начнет разрушаться;
2. шлак средне- или мелкофракционный;
3. песок либо отсев – применяется для увеличения плотности шлакоблока;
4. пластификаторы (УПД) или модифицирующие добавки – улучшают некоторые свойства бетона либо ускоряют процессы цементации. Смешиваются с водой в пропорции, указанной в инструкции;
5. вода техническая.
Рецептура шлакобетона различается в зависимости от состава и размера зерен шлака и силиката.
Раствор в усредненном варианте «цемент-шлак-вода» имеет соотношение 1:7:0,7. Более точные пропорции приведены в таблице ниже.
Компоненты | Количество | Плотность шлакобетона, кг/м3 | Марка полнотелого шлакоблока, кг/см2 | Марка пустотелого шлакоблока, кг/см2 |
Цемент, шлак гранулированный, вода | 200, 720 кг, 130 л | 950 | 75 | 45 |
Цемент, шлак гранулированный, песок силикатный, вода | 200, 500, 540 кг, 130 л | 1250 | 100 | 60 |
Цемент, шлак зольный (твердотопливный), вода | 200, 1080, 130 л | 1300 | 75 | 45 |
Цемент, шлак зольный, песок кварцевый, вода | 200, 720, 540 кг, 130 л | 1450 | 100 | 60 |
Производство шлакоблоков
Процесс изготовления включает три этапа:
1. Замес раствора в бетоносмесителе.
2. Загрузка в форму, вибропрессование.
3. Выгрузка готовых, но еще сырых изделий, штабелирование на 1-3 недели для просушки.
Как делать шлакоблок в домашних условиях? Практически так же, с той разницей, что вместо бетоносмесителя можно воспользоваться обычной лопатой, а уплотнение производится ручным способом.
состав, марки, виды и способы изготовления
Шлакобетонная продукция в виде блоков широко используется в строительстве зданий различной этажности. Дом полностью можно выстроить из шлакоблоков, в том числе и собрать фундамент. Развитые технологии производства позволяют реализовать в шлакоблоках заданные характеристики, эксплуатационные и технологические свойства. Таким образом, отходы металлургического и теплоэнергетического производств получают вторую жизнь, входя в состав шлакоблоков. Вместе с тем изделия имеют как большие плюсы, так и значительные, в том числе и технологические минусы.
Где используются?
Шлакобетонные изделия завоевали популярность у промышленных и частных застройщиков. Место укладки и решаемые задачи определяют набор придаваемых свойств. Характеристики шлакоблоков формируют пропорции и состав компонентов. Дом может получить фундамент и все стены из шлакоблоков. Модификации продукции позволяют формировать наружные несущие и ненесущие стены, перегородки, перемычки проемов, дымо- и газоходы и пр. Также изделия могут формировать пояса жесткости. Плиты перекрытий при использовании внутреннего армирования могут быть целиком изготовлены из шлакобетона.
Состав
Шлакобетонные блоки включают в состав вылежавшиеся шлаки определенных фракций. Размер зерна шлакового песка — формирующий свойства параметр шлакобетонной продукции. Вяжущим компонентом выступают в основном цемент, известь. Для раствора используется чистая вода либо специально закисленная. Известные рецептуры материала предполагают дополнительно к шлаку использовать цементную, кирпичную и бетонную крошку, отсев щебня, золу, вулканический перлит, песок, керамзит и пр.
Пониженную теплопроводность продукции придают хвоя, древесные опилки. Сокращение размеров камневидных наполнителей придает блокам высокую прочность, дополнительный вес. Однако, низкие теплопроводность и масса достигаются использованием более крупных их фракций. Таким образом, характеристики граншлака являются определяющими.
Особый состав имеет шлакощелочной бетон. Смесь включает молотый песчаный шлак, подобранный щелочной раствор, крупные и мелкие заполнители. Легкий шлакощелочной бетон создается на основе доменного граншлака или керамзита. Вместе с тем в смеси находится место для аглопорита, пемзы, известняка (ракушечника), отходов деревообработки.
Марки
Конкретная пропорция компонентов материала формирует его характеристики — марки блока. Параметр прочности изделий — один из основных. Несущая способность шлакобетонных блоков установлена от М10 до М125 (кг/см2). В фундамент укладываются шлакоблоки с М100 и М125, они выдержат и дом.
В ненесущих стенах используются М25, М35. Несущие стены возводят блоками с М50 и больше. Дом целесообразно утеплять изделиями с прочностью М10. Теплопроводность увязана с марками прочности изделий.
Так, для плотности материала 1050-1200 кг/м3 показатели теплопроводности оказываются в пределах 0,35 – 0,48 Вт/(м °С). Шлакощелочной бетон имеет другие установленные марки прочности (от В10 до В110), влагостойкости, морозостойкости и пр., получаемые благодаря существенным отличиям в технологии производства. Теплопроводность подобного материала может быть очень низкой — лежать в допусках 0,059 – 0,13 Вт/(м °С), дом эффективнее утеплять именно такими блоками.
Способы изготовления
Используются формы (в том числе без дна), в которых материал набирает первичную прочность камня. Начальные механические свойства ему придают вибропрессование, прессование и формовка. Основная цель — равномерно и быстро уплотнить формируемую массу. На крупных предприятиях данные операции автоматизированы и технологически объединены соответствующим оборудованием.
Вернуться к оглавлениюПрессование
Масса материала, загруженная в прочные матрицы, подвергается уплотнению путем механического прижима. Прессовое оборудование развивает усилие порядка нескольких тонн. Операция единообразна при изготовлении как монолитных, так и пустотелых изделий.
Вернуться к оглавлениюВибропрессование
Подвижная смесь в формах уплотняется на участке вибропрессования. Операция создает условия для поддержания массой приобретенной пространственной формы перед высвобождением из матриц. Длительность процесса составляет 20 – 30 сек. и может быть увеличена до полутора минут (для оборудования без усиленного прессования). Частота встряхивания составляет около 50 Гц. На менее оснащенных производствах используются вибрационные столики и ручные поверхностные электровибраторы.
Формовка
Может быть ручной и автоматизированной, предусматривающей использование для заливки смесью деревянных, полиуретановых и стальных матриц, которые могут иметь различные конструкции, в том числе многоячейковые. Поверхности форм покрываются смазкой. Для декоративных изделий (например, для создания лицевой фактуры «колотый кирпич») на дне разравнивается штукатурная масса.
Затем в матрицу до половины глубины выливают шлакобетонную смесь, которую уплотняют. Далее в форму вводят пустотообразователи, заливаемые до края формы остатками смеси. Форма подвергается вибропрессованию и прессованию Наружная поверхность изделий создается последней. Качественные камни, освобожденные из форм, имеют плотное сплошное тело, правильную устойчивую форму по граням и ребрам.
Разновидности
В строительной индустрии принято подразделять шлакоблоки в зависимости от степени пустоты внутреннего объема на полнотелые и пустотелые. Воздух может занимать до 40% размера камня.
Вернуться к оглавлениюПолнотелый
Марка прочности определяет, каким быть изделию — пустотелым или полнотелым. Фундамент, опорные конструкции формируются только из полнотелых камней. Однако, стеновые, перегородочные камни могут быть как первыми, так и вторыми.
Вернуться к оглавлениюПустотелый
Продукция различается количеством и размерами внутренних пустот. Форма полостей играет существенную роль. Отверстия в теле камня создаются сквозными и глухими. Последние позволяют экономить кладочный раствор. Изделия с прямоугольными пустотами возможно легко ровно поломать.
Вместе с тем круглые и овальные воздушные полости создают дополнительную прочность. Изделия, объем которых на 40% заполняет воздух, имеют приемлемую теплопроводность. Однако, уменьшение объема полостей до 30% при небольшом ухудшении теплоизоляционных свойств значительно повышает прочность камня.
По назначению
Типовые размеры и предназначение камня увязаны. Полные стеновые блоки и полублоки — стандартный размерный ряд типоразмеров. Их функциональное предназначение: рядовой (в кладке) и лицевой. Последние прочнее и долговечнее.
Вернуться к оглавлениюПолный стеновой блок
Изделие изготавливается как полнотелым, так и пустотелым. Стандартные размеры одной единицы — 390×190×188 мм.
Вернуться к оглавлениюСтеновой полублок — пустотелый
Изделие имеет меньшие размеры по сравнению с полным стеновым блоком. Выпускается только в пустотелой модификации. Единица продукции представлена в двух размерах: 390×120×188 мм и 390×90×188 мм.
Вернуться к оглавлениюПерегородочные
Целевым образом используется только один типоразмер стенового полублока — 390Х120Х188. Реализуемая толщина кладки — 120 мм, что аналогично ширине стен при их выведении с применением стандартного кирпича.
Декоративные стеновые полублоки и блоки
Изделия отливаются в специальных формах, дно которых формирует фактурный рисунок («битый кирпич», «дикий камень» и пр.) лицевой стороны изделий. Могут иметь конструкционные пазы, повышающие удобство кладки. Изделия оригинально смотрятся в кладке ограждений. Их состав включает красители, имеющие высокую влагостойкость.
Вернуться к оглавлениюДостоинства и недостатки
Одним из преимуществ есть простота укладки.Плюсы камня:
- Практически самая низкая стоимость по сравнению с материалами аналогичного назначения.
- Возможность отливки камня с любыми заданными свойствами.
- Шлакоблоки зарекомендовали себя при установке в фундамент сооружений.
- Стеновые модификации сокращают нагрузку на основание и конструкцию в целом, имеют хорошие звукоизоляционные свойства.
- Увеличенный размер единиц камня сокращает сроки и затраты на строительство.
- Простота укладки.
- Длительность эксплуатации — десятки лет.
Минусы продукции:
- Теплоизоляционные свойства изделий не являются анизотропными.
- Отстоявшийся камень сохраняет эксплуатационные качества даже при интенсивном воздействии влаги. Однако, набор полный прочности происходит через 1 год, что требует после укладки надлежащего ухода за ним.
- Теплопроводность шлакоблоков, используемых в наружных стенах, слишком высокая.
Вывод
Шлакобетонный камень широко используется в строительстве. Возможность маневра ингредиентами рецептур позволяет создавать блоки относительно низкой стоимости с заданными выраженными свойствами. Поэтому подобная продукция находит применение в зданиях от котлована до возведения любых стен и перекрытий.
характеристики, плюсы и минусы метериала
Конструкционный материал – шлакобетон – отлично подходит как для высотного строительства, так и для небольших коттеджей различного типа. Из него можно выводить монолитные стены как внутри помещения, так и снаружи, а для его производства не требуется сложных конструкций, замысловатого технологического процесса и какого-либо особенного вида сырья, что, безусловно, говорит в пользу его экономичности и растущей популярности среди строительных компаний. Несмотря на относительно небольшое время, прошедшее с момента изобретения шлакобетона и активного введения его в сферу строительства, этот материал ничем не уступает своим предшественникам, а в чем-то даже превосходит последних.
Характеристики из изготовление шлакобетона
В основе шлакобетона лежат такие вяжущие составляющие, как гипс, цемент, известь или глина, а прослойками служат различные виды шлака – каменноугольный или антрацитовый. Необходимо учитывать качество шлака, ибо, чем больше в нем содержится несгоревших частиц угля (что можно определить по его темному цвету), тем огнеопаснее становится он в качестве наполнителя, и тем больше требуется использовать разнообразных вяжущих материалов.
Для удаления вредоносных примесей используют несколько способов. Одним из самых распространенных является преднамеренное сохранение приобретенного шлака на стройплощадке на весь зимний период, предварительно разложив его по кучам высотой около двух метров. За зиму шлак размокает, внутри него происходит гашение извести, а примеси, представлявшие угрозу, вымываются и уходят в землю. Чтобы ускорить процесс очистки, шлак можно просеять или дополнительно полить водой, пока он не достигнет требуемого предела чистоты.
Прочность и долговечность шлакобетону обеспечивает специальный гранулометрический состав. Чтобы его добиться, массу просеивают несколько раз, используя разные сита: на первом этапе ячейки имеют диаметр 40 мм, затем 5 мм и, наконец, 1 мм. Шлак с гранулами боле пяти миллиметров считается крупным, а прошедший сито в один миллиметр – мелким.
От состава гранул зависит не только прочность, но и теплопроводность шлакобетона. Чем крупнее частицы, тем теплее получается конечный продукт, но такой материал будет менее прочным, нежели с мелкими гранулами.
Использование шлакоблоков в строительстве
Для малого коттеджного строительства используют несколько составов шлакобетона, существенно различающихся между собой. Марка 40 — состав с плотностью 1200 кг на один кубический метр. Его используют для возведения наружных стен и дымоходов.
Плотность шлакобетона уступает параметрам стандартного бетона, и его тщательное перемешивание влияет на основные характеристики прочности и сроки эксплуатации. Для максимального проникновения вяжущих веществ в гранулы шлакобетона, его следует тщательно увлажнить и оставить на несколько часов перед непосредственным приготовлением. Перемешивать до смачивания не рекомендуется, так как это может не лучшим образом сказаться на качестве материала, оттого что влага будет вытекать из полученной массы. Увлажненный состав перемешивают с известью, после чего добавляют необходимое количество воды для получения однородной массы.
При строительстве следует учитывать, что время затвердения шлакобетона значительно выше, чем обычного бетона. Кроме того, такие характеристики, как прочность к воздействию окружающей среды и механическим повреждениям, у шлакобетона ниже, чем у его старшего брата – бетона. Во избежание проблем следует использовать блоки небольших размеров и применять дополнительные отделочные материалы.
Если соблюдать все правила кладки и использовать качественные материалы и пропитки, загородный дом из шлакобетона простоит долгое время, а его возведение обойдется вам гораздо дешевле, чем аналога из кирпича. Кроме того, шлакобетонные сооружения по теплоизоляционным характеристикам значительно лучше, чем дома из кирпичной кладки.
Шлакобетон пропорции для стяжки — Строительный журнал
Шлакобетон — особенности и характеристики материала
Материал для формирования конструкций здания должен быть не только прочным, а и экономичным. Желательно использование для нужд строительства вторсырья других отраслей производства. Для наших широт с суровыми зимами крайне важны утепляющие свойства материала.
Его характеристики позволяют использовать изделия, как для несущих, так и для ограждающих элементов. Все зависит от соотношения пропорций входящих в него веществ.
Шлакобетон — состав и пропорции
Определяет название материала присутствие в его составе топливных шлаков или отходов металлургической промышленности. Крупность зерен шлака составляет от 2,5 мм до 8мм. Так же для лучшего сцепления материалов применяется шлаковая пыль. Зерна отсеиваются при помощи сита. Точно так же просеиваются пылевые массы.
Благодаря легкости и пористости заполнителя конструкция получается легкой и имеет повышенные теплоизоляционные свойства.
Перед добавлением в раствор шлак необходимо смочить водой. Это обусловлено высокой пористостью материала. При сухом шлаке он будет хуже схватываться с бетоном, оставляя поры, заполненные воздухом. Такие изъяны конструкции снизят ее прочность. На смачивание 1м3 шлакового продукта уходит почти 80 л воды. Если шлак увлажнен под дождем дополнительное смачивание не нужно.
Так же в состав шлакобетона входит известь. Она может быт гашеной или не гашеной. Гашеную известь необходимо перед добавлением в раствор разбавить водой до консистенции молока. Масса извести это 1/3 от объема шлаковых продуктов. Для большей прочности в раствор добавляется 2/3 глины. Такой состав дольше набирает прочность, зато его прочностные характеристики увеличиваются.
Вода, применяемая для разбавления смеси, должна быть без органических примесей. Химический состав воды, при недопустимых примесях, может войти в реакцию с другими составляющими, приведя к нежелательным последствиям. Расход воды на 1м3 шлакобетона составляет примерно 200 литров. В это количество входит жидкость, которой разбавляют известь и вода, добавленная в шлак.
Марка цемента определяется работой конструкции и требованиями к ней. Доза цемента в составе раствор составляет 2/3 от объемного веса шлака.
Шлакобетон — технические характеристики
Основным отличием шлакобетона от обычного бетона на песчано-гравийном заполнителе является его легкость.
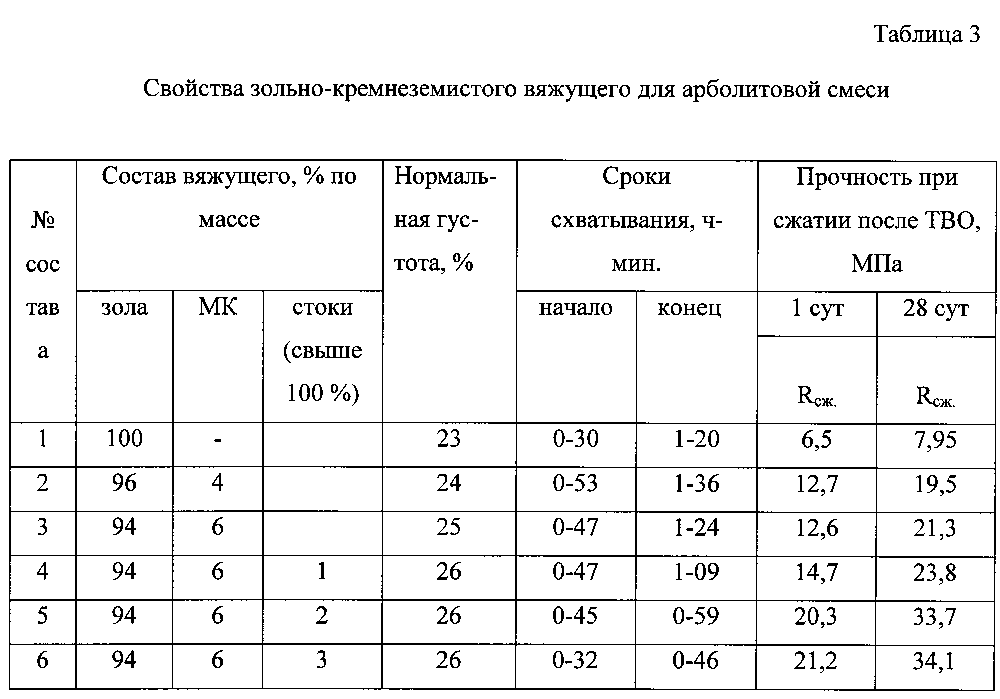
Шлакобетонные блоки легко монтируются и имеют разнообразие размеров и форм. Так как, в основном, шлакобетон готовят на строительной площадке, опалубку под него делают там же.
Пористый заполнитель позволяет увеличить шумопоглащение конструкции. К тому же производятся пустотелые блоки для стен и перегородок. Они обеспечивают большее задержание тепла и не пропускают шумы. Срок эксплуатации шлакобетонных конструкций 100 лет, это больше чем многие строительные материалы.
В зависимости о марки цемента и добавление пластификаторов определяется морозостойкость конструкции. Для наружных стен используется количество циклов разморожения не менее 35, для севера не менее 50.
Шлакобетонные конструкции имеют высокую гигроскопичность. Необходимо обратить пристальное внимание на гидроизоляцию данного изделия. Зато стены из этого материала «дышат», не создавая препятствие парам. Шлакобетон, изготовленный в заводских условиях, имеет сертификат качества и отвечает всем характеристикам. Блоки, вылитые на стройплощадке обходятся дешевле, но определить их показатели и срок годности достаточно тяжело.
Пропорции бетона для стяжки пола
В качестве напольного покрытия в загородных домах и квартирах применяется бетон для стяжки. Строительный материал удовлетворяет высоким требованиям к надежности, длительности эксплуатации и простоте укладки. Любые неровности и дефекты основы с легкостью устраняются бетонным раствором. Однако прочностные показатели и длительность срока службы покрытия определяется многими параметрами, такими как соблюдение технологии приготовления бетонного раствора, правильность выбора соотношений главных ингредиентов и выполнения заливки.
Почему важно соблюдать требуемое соотношение?
Сегодня в качестве напольных покрытий применяются различные материалы: плитка, шпаклевка, штукатурка и т. п. Для их прочного и надежного обустройства требуется соблюдать строгие пропорции главных составляющих смеси на бетоне. Визуально определить правильность соотношений компонентов можно по густоте раствора. Консистенция должна быть подобна жирной сметане с немного рассыпчатой структурой без комков. Такой состав легче наносится и разглаживается. Если основа ровная, смесь будет слегка растрескиваться.
Если переборщить с водой, соотношение компонентов окажется неправильным, следовательно, смесь хуже ляжет, а пол со временем станет трескаться.
Чтобы правильно смешать все ингредиенты в необходимых количествах, нужно четко следовать рекомендациям производителя. Это касается готовых сухих смесей. Если использовать растворы собственного приготовления, рекомендуется подобрать соотношения, согласно марке цемента и выбранного заполнителя. Соотношение ингредиентов в песко-цементной смеси определяет не только конечное качество покрытия, но и звуко-, тепло- и влагостойкие параметры, возможность прокладки коммуникаций.
Отношение цемента и песчаного наполнителя
Марка цемента определяет отношение основных ингредиентов в смеси, таких как цемент, песчаный наполнитель, вода.
Таблица соотношений ингредиентов.
Рекомендуется стяжку месить из марки раствора более М150 с прочностью на сжатие 10 МПа. Оптимальный сорт — М200. Песок для выбора соотношения нужно брать с минимальным содержанием глины. Примеси снижают адгезионные свойства смеси, следовательно, уменьшаются прочностные характеристики пола. Если глины не удалось избежать, следует увеличить долю цемента в общей массе на 20%.
Как рассчитать раствор для заливки пола?
В качестве примера приведем расчет на бетонной стяжке для помещения в 35 м2. Требуемая толщина слоя заливки 5 см:
- Общий объем смеси равен результату перемножения толщины пласта и площади комнаты: 0,05*35=1,75 м3.
- Объем песчаного заполнителя, вяжущего и полезных добавок. В этом случае — песок, цемент, щебень. Округленное соотношение имеет вид 1 : 3 : 5. Из приведенного относительного количества находим объем песка: 1,75*(3/9)=0,57 м3. Рассчитанный объем щебня составит 1,75*(5/9)=0,95 м3. Объем цемента равен 1,75-0,57-0,95=0,23 м3.
- Преобразование единиц измерения — от объемных к массовым. Для этого расчет ведется на 10 литров каждого ингредиента смеси. Указанный объем песка, цемента и щебня имеют соответствующе массы: 14—16 кг (1 м3=1400—1600 кг), 15—17 кг (1 м3=1500—1700 кг) и 13—14 кг (1 м3=1300к—1400 кг).
Следовательно, перевод единиц выглядит так:
- массовая доля цемента — 0,23*1300 (1400)=299 (322)кг;
- песка — 0,57*1400 (1600)=798 (912) кг;
- щебня — 0,95*1500(1700)=1425 (1615) кг.
Пример является приблизительным, но полезным. Специалисты рекомендуют при приготовлении раствора для полов учитывать, что готовая стяжка может уменьшиться в объеме: примерный выход из 1 м3 сухого продукта составляет 0,59—0,71 м3 готовой массы. Следовательно, должен быть определенный запас всех необходимых компонентов.
В помощь начинающим строителям существует большое количество полезных графиков, таблиц, онлайн-калькуляторов, которые позволят подобрать соотношение и рассчитать количество ингредиентов. Затем можно самостоятельно приготовить качественный раствор для стяжки на полу.
Что лучше — бетон или цпс?
Для приготовления цпс или цементно-песчаной стяжки требуется одна часть цемента и три части песка кварцевой породы. Количество воды составляет 45—55% массы сухой смеси. Это соотношение позволяет получить марку 150—200. Расход полученного раствора зависит от толщины укладываемого слоя и типа напольного покрытия. Для выравнивания поверхности достаточно 2 см. Если дополнительно использовать пластификатор, слой может достигать 3 см. Как правило, цпс используется для выравнивания небольших неровностей с укладкой заливки до 6 см или для ровной поверхности. В противном случае рекомендуется более прочная и надежная бетонная масса. Уже при слое более 4 см бетон не растрескивается. При использовании смеси с керамзитом покрытие может стать хорошим теплоизолированным полом, а раствор со щебнем даст лучшее сцепление, следовательно, повышенную стойкость к любой степени нагрузок.
Ответом, какая лучше смесь для пола, могут послужить условия для укладки стяжки бетоном, соответствующие необходимости:
- создания уклона или подъема;
- заливки непосредственно на подготовленную почву;
- выравнивания поверхности под декоративную отделку;
- сооружения монолитного пола.
Вне зависимости от того, какая пропорция или тип смеси выбраны, заливка пола должна осуществляться в один этап.
Вывод
Технология приготовления бетонной или песко-цементной стяжки трудоемкая и кропотливая работа, требующая четкого следования соотношениям компонентов и инструкциям. При верном расчете ингредиентов с последующим получением однородной массы в заданной пропорции и при правильной заливке пола, можно собственноручно создать прочное, надежное покрытие. Прослужит такой пол, несомненно, долгое время без потери исходных свойств и внешнего вида.
Шлакобетон и шлакощелочной бетон: сырьё и способы их производства
При строительстве малоэтажных сооружений невысокие нагрузки на стены позволяют существенно расширить ассортимент материалов, из которых можно возводить стеновые и другие строительные конструкции. Это относится и к шлакобетону, который хоть и принадлежит к категории тяжёлых бетонов, но имеет гораздо меньший вес, чем аналоги на традиционных заполнителях – гравии и щебне природного происхождения. Из молотого шлака может быть изготовлен и полноценный вяжущий компонент – шлакощелочной цемент, способный качественно заменить традиционный портландцемент.
Требования к шлаку
Шлак – это сопутствующий продукт, представляющий собой сплав различного рода оксидов, образующийся при высокотемпературной обработке сырья. В зависимости от состава сырьевых материалов шлак может быть основным или кислым.Для производства шлакобетона подходит не любое сырьё. Основным требованием к шлаку является отсутствие в сплаве оксидов химических соединений, отрицательно воздействующих на характеристики получаемого строительного материала. Особые требования предъявляются и к чистоте шлака. Он должен быть свободен от земли, глины, золы и иного мусора.
Для производства шлакобетона применяют шлаки металлургической и топливной промышленности.
Применение металлургического шлака даёт возможность получать более прочный бетон. Из шлаков топливной промышленности наиболее подходящим сырьём являются продукты горения антрацитных пород. Непригодны для производства бетона продукты сгорания бурых углей, так как они содержат примеси, присоединенные к шлаку на основе неустойчивых связей.
Желательно, чтобы при хранении шлак около трёх раз перемещали с места на место. Такая мера позволяет достигнуть высокой степени очистки материала от примесей извести и серы.
Предназначенный для производства бетона шлак не менее полугода должен храниться на открытом воздухе. За этот период материал приобретает необходимые свойства, а под воздействием атмосферных осадков он освобождается от вредных компонентов.
Опилкобетон — стройматериал, обладающий высокими санитарно-гигиеническими характеристиками. Здесь Вы можете ознакомиться с рецептом и технологией производства опилкобетона.
Высокую надежность и низкую стоимость плит перекрытия Вам предлагает компания Навигатор.
Шлаки остаются пригодными для производства шлакобетона до тех пор, пока сохраняется их кристаллическая структура и не проявляются признаки распада, которые возникают при переходе одних соединений материала в другие под влиянием влаги и газов, находящихся в воздухе. Новые соединения имеют больший объём, чем первоначальные, поэтому такой переход сопровождается растрескиванием и разрушением кусков шлака.
Особенности изготовления шлакобетона
В зависимости от размеров зерен шлак для шлакобетона разделяют на щебень, имеющий фракцию 5-40 мм, и песок с гранулами до 5 мм. Применение шлакового песка повышает такие показатели бетона, как прочность и плотность. Благодаря использованию шлакового щебня получают более лёгкий бетон с высокими теплоизоляционными свойствами, но более низкими прочностными характеристиками.
Для приготовления шлакобетона используют два вида сит: с крупными (40 х 40 мм) и мелкими (5 х 5 мм) ячейками.
- Для изготовления наружных стен для бетона берут 7 частей крупного и 3 части мелкого шлака.
- Для внутренних стен пропорция фракций будет несколько иной: 6 частей крупных зёрен и 4 части мелких.
Увеличить прочность шлакобетона можно заменой пятой части самой мелкой фракции на обычный песок и исключением из состава смеси наиболее крупных зёрен шлака.
Для снижения стоимости сооружения из шлакобетона возможно использование в его составе сочетания двух вяжущих компонентов: цемента и глины, цемента и извести. Оптимальные пропорции компонентов вяжущего в шлакобетоне: цемент – не менее 2/3 от объёма вяжущего, известь – не более 1/3.
Добавки глины и извести не только удешевляют строительство, но и делают стены более сухими и тёплыми. Известковый шлакобетон, вяжущее которого состоит из 1/3 извести и 2/3 глины, твердеет гораздо дольше цементного, но в дальнейшем он имеет более высокие прочностные характеристики.
Перед установкой перекрытий со времени сооружения стен из известкового шлакобетона должно пройти не менее трёх месяцев. Такие стены необходимо начинать возводить в начале тёплого периода года, чтобы успеть закончить работы до наступления морозов.
Известь можно не добавлять, но в этом случае смесь не будет обладать достаточной пластичностью и её невозможно будет перемешать до образования однородного цвета массы.
Качество перемешивания оказывает существенное влияние на несущую способность строительных конструкций из шлакобетона.
Последовательность приготовления шлакобетона своими руками аналогична производству традиционного строительного материала:
- в сухом состоянии смешивают песок, цемент и шлак, который предварительно увлажняют;
- добавляют глиняное или известковое тесто, этот компонент способствует повышению пластичности смеси;
- заливают воду.
Использование шлакобетона при возведении различных строительных конструкций
Шлакобетон на сегодняшний день является одним из наиболее дешевых строительных материалов. Из шлакобетона изготавливают не только стены, но и армированные плиты перекрытия. Если весь дом сооружается из облегченных материалов, то для устройства фундамента и пола также возможно использование шлакобетона.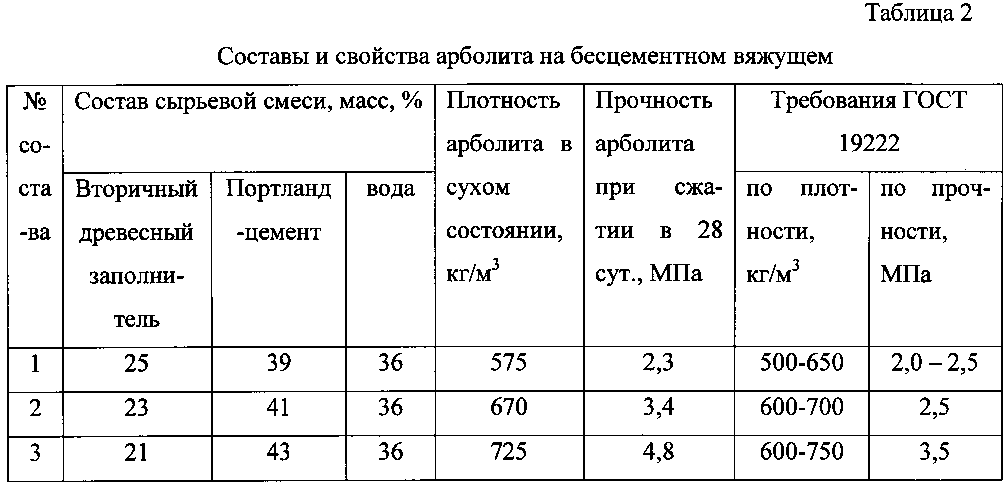
Для возведения стен может быть применена монолитная технология с переставной опалубкой. Но всё большую популярность приобретают готовые стеновые и фундаментные блоки из шлакобетона.
Шлакобетон классифицируется по маркам. Марка 10 применяется в основном для теплоизоляции. Из шлакобетона марок 25 и 35 возводят не несущие конструкции, марка 50 применяется для изготовления армированных перемычек, внутренних и наружных несущих стен.
Главным преимуществом шлакобетона является его меньший удельный вес по сравнению с керамическим или силикатным кирпичом. Это свойство позволяет снизить нагрузку на фундамент и прочие несущие конструкции строения. Большие размерные параметры блоков способствуют сокращению временных и материальных затрат на их укладку. Шлакобетонные блоки удобны для транспортировки.
К недостаткам блоков из шлакобетона можно отнести их медленное твердение. Через месяц после изготовления этот материал приобретает всего половину своей марочной прочности.
Полное соответствие всем заложенным в данной марке характеристикам у шлакобетонных блоков наступает примерно через год после их изготовления.
Стены из шлакобетона гигроскопичны, легко впитывают воду, поэтому у такого сооружения крыша должна иметь свесы не менее 500 мм. Предохранять шлакобетонные элементы от воздействия влаги необходимо уже через 2-3 дня после их производства.
Наиболее высокой теплопроводностью обладает шлакобетон марки 10. Если вы хотите сами приготовить материал с повышенной теплоизоляцией, добавьте в вяжущее вещество известь или гипс.
Особенности шлакощелочного бетона
Высокие цены на портландцемент привели к поискам более дешевых типов вяжущего компонента. Одной из наиболее интересных находок можно назвать шлакощелочной цемент. История его использования началась в Германии ещё в начале девятнадцатого века, а в современных условиях он применяется на строительных площадках во всём мире. Создание таких цементов стало возможным благодаря установлению вяжущих способностей у соединений щелочных металлов, к которым относятся литий, натрий, калий, рубидий, цезий.
Шлакощелочной цемент – вяжущее высокой прочности, состоящее из молотого шлака и любой щёлочи – жидкого стекла, соды и других.
На базе шлакощелочного цемента получают железобетонные элементы с повышенной устойчивостью к химически агрессивным веществам. При их изготовлении могут быть использованы загрязненные глинистыми включениями наполнители.
Шлакощелочной бетон является незаменимым при возведении массивных объектов. Это связано с тем, что при изготовлении крупных элементов из бетона на портландцементе происходит выделение значительного количества тепла, при этом температура конструкции может достигать 80°С. Если охлаждение бетонного объекта произойдет слишком быстро, то могут образоваться деформационные трещины. Применение шлакощелочного бетона даёт возможность избежать возникновения этой проблемы.
Наиболее широкое применение получил шлакощелочной цемент на базе молотого металлургического шлака и соединений щелочных металлов, у которых преобладающими являются гидросиликаты кальция, а вспомогательными – гидроалюмосиликаты.
Достоинства бетона на основе шлакощелочного цемента
- Применение бетона на шлакощелочном цементе позволяет получать конструкции с меньшим количеством капиллярных пор, чем при использовании обычного бетона на портландцементе.
Это свойство существенно снижает водопоглощение и повышает морозоустойчивость бетона, что способствует росту эксплуатационных качеств строительной конструкции.
- Коррозия арматуры в шлакощелочном бетоне протекает значительно медленнее, чем в традиционном материале.
- Прочность бетона на шлакощелочном вяжущем достигает 130 МПа.
- Бетонная смесь прекрасно укладывается, а изготовленные элементы хорошо обрабатываются.
- В первые сутки материал набирает около 30% прочности.
- Такие бетоны устойчивы к воздействию морской воды и некоторых других агрессивных сред – кислот, хлоридов, сульфатов.
Благодаря возможности управлять свойствами шлакощелочного цемента на разных стадиях структурообразования стало возможным получение вяжущих со специальными свойствами: жаро- и морозостойких, с повышенной коррозионной устойчивостью, безусадочных, с высокой скоростью твердения, тампонажных.
Если Вы не знаете, чем заделать трещины в бетоне, здесь подробно описаны рецепты.
Предлагаем Вам раствор бетона по низким ценам с доставкой любыми видами спецтехники.
Цемент со шлаком — применение смеси
Очень часто в строительстве используется цемент со шлаком, что это за материал, не нужно объяснять опытным мастерам. А вот новичкам в строительном деле будет полезно узнать, что шлакоцемент — это гидравлическая вяжущая субстанция, образованная посредством измельчения клинкера, гипса, а также доменного шлака — вторичного металлургического продукта. Химический состав шлаков играет важнейшую роль в определении класса прочности шлакоцемента. В цемент могут идти гранулированные и негранулированные, кислые, основные шлаки.
Технология производства
Такой материал производят с использованием доменного шлака, который представляет собой вторичный продукт металлургического производства. Класс данного материала определяется качеством исходных материалов клинкера и доменных шлаков. Клинкер исполняет роль активизатора шлаков в составе шлакоцемента.
В основе технологии производства лежит принцип высушивания шлака в сушилках до получения показателей влажности не более 1%. Затем клинкер, шлак и гипс загружается в бункер цементной мельницы, и измельчается до гомогенного тонкодисперсного порошка.
Класс шлакоцемента зависит и от используемого вида шлака: это могут быть основные, кислые, гранулированные и негранулированные шлаки. Особое значение в определении прочности имеет не физическая структура, а химический состав. На данной закономерности основывается правило выбора сырья. С экономической стороны предпочтение стоит отдать гранулированным видам, в связи с тем, что использование негранулированных масс усложняет производственный процесс. Цемент со шлаком, который получается в результате, затвердевает медленнее обычного, потому что содержание шлака в нем варьируется в пределах 20-80% общей массы.
При изготовлении портландцемента используют сито с крупными (40х40 мм) и мелкими (5х5 мм) ячейками.
Шлаковый портландцемент изготавливают, используя два вида сит: с мелкими (5х5 мм) и крупными (40х40 мм) ячейками.
- При использовании материала для наружных стен соединяют крупный и мелкий шлак в соотношении 7:3.
- Для внутренних стен в пропорции 4 части мелких зерен и 6 частей крупных.
- Для увеличения прочности материала заменяют пятую части самой мелкой фракции обычным песком и исключают из состава наиболее крупные зерна шлака.
- Благодаря использованию сочетаний 2-х вяжущих компонентов (цемента и извести, цемента и глины) удается существенно снизить стоимость материала. Наиболее оптимальной являются пропорция: известь – не более 1/3 и цемент – не менее 2/3 общего объема.
Глина и известь способны не только снизить стоимость, но и делают стены более теплыми и сухими. Известковый портландцемент на основе шлака, в состав вяжущего которого входит 2/3 глины и 1/3 извести, твердеет дольше цементного, однако в дальнейшем показывает более высокие показатели прочности.
Состав возможных смесей шлакобетона
Технические характеристики
По ГОСТ 1017-85 шлакопортландцемент включает в себя такие компоненты и технические условия:
- Клинкер должен содержать магний не больше 5-6 %, так как этот элемент способен снизить качественные характеристики бетона.
- Шлаки в гранулах, полученные доменным или электротермометаморфическим путем – примерно, 20-80 % (в зависимости от того какие характеристики нужны).
- Минералы гипсового происхождения – чистый гипс, добытый природным путем с добавление фосфора и фтора, но не больше 5 процентов от всего объема клинкера.
ШПЦ делят на два вида – нормальнотвердеющий и быстротвердеющий. Во второй материал добавляют специальные присадки, которые являются ускорителями минерального и вулканического происхождения – пепел, пемза. Бетон из шлака имеет такие пропорции: 4-5 частей шлака, 2 части цемента, 2 части песка. Прочность таких изделий достигается уже через 1-2 недели.
Бетоны на основе металлургических шлаков отрицательно переносят перепады температуры, поэтому материал будет затвердевать долгое время в прохладных условиях. Для ускорения процесса используют специальные присадки или обрабатывают конструкцию теплом при помощи тепловых подушек либо опалубок с электроподогревом. При воздействии высоких температур бетон наберет прочность через 28 дней. Вяжущее вещество обладает такими качествами:
- если в состав входит большое количество шлаков, тем будет дольше твердеть бетонная смесь и меньше тепла будет выделено при гидратации;
- шлаковые цементы дают такую же усадку, как и портландцемент;
- жаростойкость ШПЦ составляет от 600 до 800 градусов С;
- цемент на шлаке при отсутствии активных веществ и плотной молекулярной консистенции после застывания не будет вступать в реакции с водой. Такой материал является незаменимым для возведения сооружений во влажных условиях.
Сроки годности шлакопортландцемента намного ниже, чем у обычного сухого цементного раствора. Материал пригодный к использованию около 45 дней с момента отгрузки с производства. Категорически не рекомендуется применять просроченный стройматериал, так как он теряет свои качества на прочность и водонепроницаемость.
Портландцемент и шлакопортландцемент имеют такие отличия:
- Стоимость портландцемента гораздо выше, чем обычная смесь ШПЦ.
- Портландцемент быстрее становится прочным, а бетон, со шлаком спустя 21 день.
- В портландцементном составе нет шлака, туда входят клинкер и определенный минеральный состав со специальными присадками-ускорителями.
- ШПЦ имеет менее выраженную экзотермическую реакцию в процессе затвердения, бетонная смесь почти не нагревается, это в свою очередь приносит трудности при показателях температуры ниже +4 градусов С.
- Шлакопортландцемент имеет меньшую плотность и вес готовых конструкций.
Как приготовить шлакобетон
До начала приготовления смеси (примерно за несколько часов) необходимо увлажнить шлак водой, чтобы улучшить долговечность будущего бетона. Далее необходимо смешать компоненты в одной из указанных выше пропорций, хорошо перемешать. После добавления воды раствор следует вымесить до однородного состояния. Для получения средней марки бетона, можно использовать 4-5 частей шлака (фракционной смеси), 2 части цемента и 2 части песка.
Готовую массу желательно использовать в течение часа, максимальное время обработки – 1,5 часа. Более дешевым раствор можно сделать, смешав цемент с известью в соотношении 3:1. Стены дома могут быть возведены набивным методом (монолитная конструкция) или из приготовленных шлакобетонных блоков.
Сфера использования
Цемент со шлаком для чего он нужен? Портландцемент со шлаком пользуется популярностью при возведениях подводных бетонных и железобетонных конструкций, которые будут подвержены воздействиям водной среды. Материал имеет высокие показатели прочности, используется при изготовлении бетонного раствора, панелей для стен и сухих смесей. Данный вид цемента ничем не уступает марке М500, который является классическим цементом.
Цемент с добавлением шлака наиболее экономичный и популярный стройматериал для постройки стен и плит перекрытия с арматурой. Когда при постройке конструкций из облегченного мастерила для фундамента используют шлакобетон, который распределяется по классам:
- 10 – применяется при теплоизоляционных работах;
- 25-35 – незаменимы при постройках несущих элементов;
- 50 класс — лучший вариант при сооружении армированных перемычек, наружных несущих стен и внутренних перегородок.
Шлакобетон применяется на масштабных объектах, и ценится за маленький удельный вес, если сравнивать его с силикатными или керамическими изделиями. Благодаря таким положительным качествам нагрузка на фундаментные и конструктивные части получается сниженная. Также имеется возможность создавать плиты больших габаритов, такая методика экономит время и финансы в процессе монтажа. При надобности панели можно без затруднений транспортировать.
Сферы применения портландцемента со шлаком:
- возведение сборных и монолитных элементов в частных и промышленных стройках;
- изготовление конструкции, в технологии которой требуется ускоренное твердение;
- работы по укладке дороги, где требуется быстрое схватывание смеси;
- при производстве коммуникационных труб из бетона;
- постройка моста, эстакады;
- применение шлакопортландцемента для замеров растворов для штукатурки и кладки.
Хотя ШПЦ обладает хорошими характеристиками в эксплуатационный период, спустя три, четыре десятка лет качество каменных конструкций резко снижается. По этой причине имеет значение вовремя принять меры, которые предупредят разрушение построек.
Выбор сырья и особенности хранения
Портландцемент на основе шлака следует на протяжении длительного времени выдерживать во влажной среде, поскольку преждевременное высыхание плохо влияет на его твердение. При достаточных показателях влажности и повышенных температурах ускоряется твердение, поэтому обработка портландцемент в автоклавах и камерах весьма эффективна.
Прочность строительного материала достигается выполнением мельчайшего помола. Благодаря таким действиям цемент быстрее твердеет и становится более прочным. Тонкость помола отвечает за такой показатель, как активность. С целью получения вяжущего высокого качества специалисты рекомендуют применять двухступенчатый или сепараторный помол.
В производстве шлакобетона может использоваться не любое сырье. Главным требованием в отношении шлака выступает отсутствие оксидов химических соединений, которые способны отрицательно влиять на характеристики получаемого строительного материала. С особым вниманием относятся и к чистоте шлака, он должен быть лишен глины, земли, золы и иного мусора. В производстве шлакобетона используют шлаки топливной и металлургической промышленности.
Прочность портландцемента достигается мельчайшим помолом (двухступенчатым или сепараторным).
Благодаря металлургическому шлаку получают максимально прочный бетон. Из всего разнообразия шлаков топливной промышленности наиболее подходящий класс – антрацитные породы. Непригодными для данных целей считаются продукты сгорания бурых углей, поскольку они содержат примеси, которые присоединены к шлаку на основе неустойчивых связей.
Не последние место в достижении чистоты, а как результат и прочности принадлежит правильному хранению, в процессе которого шлак перемещают не менее 3-х раз с места на место, тем самым позволяя избавиться от примесей извести и серы.
Шлаки пригодны для производства до тех пор, пока сохраняют кристаллическую структуру и не проявляют признаков распада, возникающих при переходе одних соединений в другие под действием влаги и газов, которые находятся в воздухе. Образующиеся соединения обладают большим объемом, поэтому переход сопровождается разрушением кусков шлака и растрескиванием.
Класс шлакобетона зависит от размеров зерен шлака, которые могут варьироваться в пределах 5-40 мм. Песок для получения смеси используют с размером гранул не более 5 мм. Благодаря наличию шлакового песка повышается ряд показателей бетона, среди которых плотность и прочность. Шлаковый щебень позволяет получить более легкий бетон, обладающий высокими теплоизоляционными свойствами, однако его прочностные характеристики будут иметь более низкий уровень.
плюсы и минусы шлакобетонного дома, характеристики
Шлакобетон широко используется в частной застройке из-за целого ряда достоинств и простоте работы с материалом. Благодаря тому, что материал намного легче обычного бетона, его использование позволяет снизить нагрузку на конструкции дома при том, что теплоизолирующие свойства сохраняются на достаточно высоком уровне. Рассмотрим основные виды данной группы изделий, их преимущества и особенности использования.
Шлакобетонные блоки обладают высокими эксплуатационными свойствами
Обзор основных особенностей материала
Чтобы принять решение о целесообразности использования подобных изделий, необходимо знать всю информацию о них, чтобы сравнить с другими вариантами и сделать правильные выводы (читайте также статью «Бетонирование дорожек на даче – особенности проведения работ»).
Виды изделий
В зависимости от используемого наполнителя и особенностей приготовления состава можно выделить несколько основных групп:
- Шлакобетон изготавливается на основе шлаков металлургического производства. Лучше всего подходит шлак антрацита, но и другие варианты также обладают достаточно высокими характеристиками. Главное условие, о котором не стоит забывать: материал должен быть чистым, без примесей чернозема, остатков растений и других загрязнений.
- Шлакопемзобетон изготавливается на основе шлаковой пемзы, представляющей собой вспученный доменный шлак в виде щебня диаметром 2-3 сантиметра.
Еще одно название материала – термозит, из-за чего готовый материал имеет еще одно название – термозитобетон, но это то же самое.
- Еще один интересный вариант – шлакощелочной пенобетон. Добавление щелочи в шлаки придает материалу высокие свойства морозостойкости, а также устойчивости изделий к влаге и перепадам температур. Такие конструкции отлично подходят даже для сложных условий эксплуатации, в качестве щелочной добавки может использоваться известь, кальцинированная или каустическая сода, а также жидкое стекло.
Добавление щелочи добавляет изделиям прочность и стойкость к неблагоприятным воздействиям
Достоинства и недостатки данной группы изделий
Чтобы понять все плюсы и минусы шлакобетонного дома, нужно знать все особенности материала (см.также статью «Методы склеивания таких материалов, как пенополистирол и бетон, с целью создания качественного утепления»).
В первую очередь рассмотрим преимущества:
- Технические характеристики шлакобетона достаточно высоки, благодаря чему его можно использовать для малоэтажной застройки любого назначения.
Универсальность использования позволяет применять его практически для любых целей.
- Отличные теплосберегающие свойства позволяют сэкономить значительные средства на обогрев в дальнейшем. Это очень полезно как в регионах с холодными зимами, так и в теплых поясах: в таких строениях постоянно будет поддерживаться микроклимат, приближенный к оптимальному.
- Все знают, что резка железобетона алмазными кругами – процесс трудоемкий и сложный, но резать изделия на основе шлаков в разы легче, это упрощает самостоятельную работу и позволяет провести работы за меньшее время. Это касается и прокладки коммуникаций: если алмазное бурение отверстий в бетоне требует наличия специального оборудования, то рассматриваемый нами материал можно просверлить и самостоятельно.
- В зависимости от особенностей применения можно выбрать как полнотелые блоки, так и варианты с пустотами, которые гораздо легче. При этом и конфигурация пустот может очень сильно различаться, но согласно строительным нормам пустотность не должна превышать 40%.
Пустоты облегчают изделия, но снижаются и показатели прочности
- Еще одно очень важное свойство, которым обладает шлакобетон – стойкость к огню. Материал не поддерживает горение, что значительно повышает уровень безопасности возводимых объектов.
- Изделия устойчивы к поражению плесенью и грибком, что также немаловажно в случаях, когда на конструкции постоянно воздействует избыточная влажность, губительная для большинства аналогов.
- Хорошая паропроницаемость конструкций делает помещение комфортным для проживания. Свойства рассматриваемого материала приближены к характеристикам древесины – идеального варианта для использования в жилых комнатах.
- Еще одно несомненное достоинство – низкая цена бетонных изделий на основе шлака, благодаря чему данный вариант относится к одним из самых доступных.
- Возможность возведения строений, как с применением шлакоблоков, так и методом монолитных конструкций. Это позволяет добиться высокой прочности и долговечности там, где это особенно необходимо.
На фото: при возведении стен монолитным способом важно провести качественное армирование
- Еще одно большое преимущество – возможность изготовления изделий своими руками. При этом характеристики шлакобетонных блоков зависят от пропорций компонентов. Специальные формы позволяют создать идеально ровные блоки и упрощают рабочий процесс.
Специальные формы позволяют сделать блоки прямо на стройплощадке
Конечно, нельзя не затронуть и недостатки, их немного:
- Одна из главных проблем, это очень длительный период набора прочностных характеристик. Через 4 недели блок набирает только 50% прочности, а полное затвердевание происходит примерно в течение года.
- При самостоятельном изготовлении очень важно периодически увлажнять материал, иначе он потрескается.
- Из-за большой усадки отделку помещений желательно начинать не ранее, чем через год после возведения сооружения.
Совет! Если вы приобретаете готовые изделия, то следует уделить особое внимание качеству материала.
Маленькие полукустарные производства не имеют надежной системы контроля качества, поэтому велика вероятность брака. Лучше выбирать проверенных изготовителей.
Особенности самостоятельного приготовления раствора
Как отмечалось выше, состав шлакобетона достаточно прост, и его можно приготовить своими руками.
Инструкция по приготовлению раствора несложная, но все же имеет целый ряд особенностей:
- Вначале нужно подготовить шлак, для этого его необходимо просеять для получения двух фракций: вначале через сетку 40*40 мм, а затем через сетку 5*5 мм. Оптимальное соотношение крупной и мелкой фракций при изготовлении изделий для стен 3:7.
Слишком большие гранулы шлака снижают прочность конструкций, поэтому и нужно просеивание
Совет! Чтобы добиться наивысшей прочности готовых изделий, шлак желательно замочить в воде за несколько часов до применения, это позволит снизить забивание пор цементом и увеличить свойства вяжущего компонента.
- Далее следует смешать две фракции шлака так, как указано выше, должна получиться равномерная масса.
- Для снижения стоимости и повышения влагостойкости требуется добавление щелочи. Самый популярный вариант раствора следующий: цемент марки М500 1 часть, известь пушонка гашеная 0,8 части, песок 3 части и смешанный шлак 12 частей. Такие пропорции шлакобетона позволяют добиться оптимального соотношения высоких теплоизоляционных свойств и прочности изделий.
Важно! Применение извести позволяет не только повысить прочность, но сделать раствор гораздо пластичнее, что повышает удобство работы с ним.
Известь стоит немного, но благодаря ей значительно улучшаются свойства раствора
- Все компоненты тщательнейшим образом перемешиваются. Чем лучше это сделано, тем выше будет прочность конструкций. Если вы не используете бетономешалку, то лучше всего использовать обыкновенные металлические грабли.
- В последнюю очередь добавляется вода, и состав опять же размешивается до однородной массы.
- Использовать готовый раствор желательно в течение 60-80 минут.
Как отмечалось выше, при высыхании важно проводить периодическое увлажнение поверхности, чтобы избежать появления трещин на поверхности.
Многие выбирают данный вариант в качестве основного материала для возведения дома
Вывод
Как видите, можно сделать шлакобетон своими руками, а можно приобрести и готовые изделия. Стоит помнить, что при всех достоинствах прочность данного варианта все-таки ниже, чем у обычного бетона, поэтому обращаться с ним стоит бережнее (см.также статью «Железнение бетона: способы, материалы, последующая обработка»).
Видео в этой статье подробнее расскажет некоторые факты касательно рассматриваемой в данном обзоре темы.
Бетон из шлака: как приготовить своими руками
Шлакобетонные смеси пользуются заслуженной популярностью не только в промышленном, но и в частном малоэтажном строительстве. Это обусловлено характеристиками данного материала. Шлаки, добавляемые в состав бетона, получают в качестве вторичного материала в металлургической промышленности.
Длительное время гранулированный материал считался просто отходами, но мировая практика доказала его целесообразность для применения в строительстве. Шлаковый бетон более легкий, нежели песчано-гравийный, отличается своей долговечностью, устойчивостью к колебаниям температуры, звукоизолирующими свойствами.
Наибольшей прочностью обладает именно металлургический материал в смеси с цементом. Также в качестве вяжущего агента могут выступать известь, гипс или даже глина. Активно используются две разновидности гранулированного шлака:
- с мелкими зернами (0,5-1,5 мм) – получается довольно тяжелый бетон высокой прочности с хорошей теплопроводностью;
- с крупными зернами (20-30 мм) – бетон более легкий, обеспечивает хорошую теплоизоляцию, но чуть менее долговечен.
Использовать разновидности крупнее 6 мм не рекомендуется, поскольку долговечность такого бетона будет неудовлетворительной. Более мелкие фракции предпочтительно заменить песком. Шлак для строительства должен быть максимально чистым, без примесей глины, почвы, органических элементов.
Учитывая свойства бетона с разной фракцией, для создания наружных стен часто смешивают крупные и мелкие зерна в пропорции 7:3 соответственно. Для внутренних перегородок можно взять на единицу больше мелкого шлака. Если вы хотите получить максимально прочную после застывания смесь, желательно полностью убрать фракцию 12 мм, а 20% самого мелкого шлака заменить песком.
Как приготовить шлакобетон
До начала приготовления смеси (примерно за несколько часов) необходимо увлажнить шлак водой, чтобы улучшить долговечность будущего бетона. Далее необходимо смешать компоненты в одной из указанных выше пропорций, хорошо перемешать. После добавления воды раствор следует вымесить до однородного состояния. Для получения средней марки бетона, можно использовать 4-5 частей шлака (фракционной смеси), 2 части цемента и 2 части песка.
Готовую массу желательно использовать в течение часа, максимальное время обработки – 1,5 часа. Более дешевым раствор можно сделать, смешав цемент с известью в соотношении 3:1. Стены дома могут быть возведены набивным методом (монолитная конструкция) или из приготовленных шлакобетонных блоков.
Прочность шлакового цемента
Почему важны улучшенные сильные стороны?
Бетон из шлакобетона обеспечивает более высокую прочность на сжатие и изгиб по сравнению с прямым портландцементным бетоном. Повышенная прочность облегчает достижение заданных коэффициентов безопасности бетонной смеси и может предоставить инженерам инструмент для оптимизации конструкции бетонных элементов. Он обеспечивает улучшенные свойства материала, позволяя производителям оптимизировать конструкции бетонной смеси. Владельцы могут осознавать снижение затрат в течение жизненного цикла.
Как шлаковый цемент улучшает прочность?
Шлаковый цемент увеличивает прочность на сжатие и изгиб обычного бетона (рис. 1 и 2) и часто является жизненно важным компонентом при производстве высокопрочного бетона. 28-дневная прочность обычно увеличивается по мере увеличения процентного содержания шлакового цемента до примерно 50 процентов шлакового цемента в процентах от вяжущего материала. Когда портландцемент реагирует с водой, он образует гидрат силиката кальция (CSH) и гидроксид кальция (Ca (OH) 2 ).CSH — это клей, который обеспечивает прочность и скрепляет бетон, Ca (OH) 2 — это побочный продукт гидратации портландцемента, который не способствует прочности. Когда шлаковый цемент
используется в составе вяжущего материала в бетонной смеси, вступает в реакцию с водой и
Са (ОН) 2 для формирования дополнительных CSH. Дополнительный CSH уплотняет бетонную матрицу, повышая прочность.
Как шлаковый цемент влияет на развитие прочности?
Когда в бетонных смесях используется шлаковый цемент, раннее развитие прочности может быть медленнее, в то время как предел прочности будет выше, чем у простых смесей портландцемента. Если требуется более быстрое развитие прочности, бетонную смесь можно модифицировать с помощью обычной технологии, например, с использованием ускоряющих добавок или использования нагретых материалов или условий отверждения. Бетон, сделанный из шлакобетона, будет иметь более высокий рост прочности в течение срока службы бетонного элемента по сравнению с прямыми портландцементными бетонными смесями. Несколько факторов влияют на развитие прочности смеси. Они включают:
- Химический состав шлака.
- Пропорции шлаковой составляющей.
- Температура среды отверждения.
- Химический состав цементного компонента.
- Температура бетона.
- Крупность шлаковой составляющей.
- Наличие растворимой щелочи.
Шлаковый цемент особенно сильно влияет на прочность бетона на изгиб. Прочность на изгиб (или модуль разрыва) является одним из основных факторов при проектировании бетонного покрытия.Повышенная прочность на изгиб очевидна на Рисунке 2, где при использовании 50-процентного шлакового цемента достигается 20-процентное улучшение прочности, даже несмотря на то, что общее содержание вяжущего снизилось на 52 фунта / куб. Ярд. Повышенная прочность на изгиб объясняется повышенной плотностью пасты и улучшенной связью паста-заполнитель.
Каковы преимущества повышенной прочности
Функция | Предел прочности на сжатие | Преимущества прочности на изгиб |
---|---|---|
Повышенный коэффициент безопасности | Повышенная надежность | Повышенная надежность |
Оптимизированная конструкция элементов | Более тонкие элементы Более легкие элементы Меньшее количество элементов Меньшая статическая нагрузка Больше полезной площади пола | Более тонкая секция |
Оптимизированный дизайн смеси | Более низкие цементирующие факторы Меньшая усадка Меньшее тепло | Более низкий коэффициент цементирования Меньшая усадка Меньше скручивания |
Стоимость жизненного цикла | Увеличенный срок службы | Увеличенный срок службы Снижение затрат на техническое обслуживание Повышение способности справляться с неожиданным увеличением объемов трафика |
«Как и любой бетон. смеси, следует провести пробные партии для проверки бетона
характеристики.Результаты могут отличаться в зависимости от различных обстоятельств, в том числе
температура и компоненты смеси, среди прочего. Вам следует
обратитесь за помощью к своему специалисту по шлаковому цементу. Ничего не содержало
в данном документе следует рассматривать или толковать как гарантию или гарантию, либо
явные или подразумеваемые, включая любую гарантию пригодности для конкретного
цель.»
Что такое шлаковый цемент
Шлаковый цемент — это гидравлический цемент, образующийся при измельчении гранулированного доменного шлака (GGBFS) до необходимой степени измельчения и использования для замены части портландцемента. Это рекуперированный побочный продукт производства чугунной доменной печи. Расплавленный шлак, отводимый из доменной печи, быстро охлаждается, образуя стекловидные гранулы, которые при измельчении до крупности цемента дают желаемые реактивные вяжущие характеристики.
После охлаждения и измельчения до пригодной для использования крупности шлак хранится и отправляется поставщикам по всей территории Соединенных Штатов. Шлаковый цемент обычно содержится в товарном бетоне, сборном железобетоне, каменной кладке, грунтовом цементе и строительных изделиях, устойчивых к высоким температурам. Хотя существует множество применений и преимуществ шлакового цемента, некоторые из них выделены ниже, а подробные информационные листы: , расположенные здесь .
- Цемент шлаковый — SCIC № 1
- Шлаковый цемент или измельченный гранулированный доменный шлак (GGBFS) уже более века используется в бетонных проектах в США для повышения долговечности и снижения затрат на жизненный цикл. Среди ощутимых преимуществ для бетона — лучшая обрабатываемость и обрабатываемость, более высокая прочность на сжатие и изгиб, а также улучшенная стойкость к агрессивным химическим веществам.
SCIC # 1, Slag Cement, дает представление о преимуществах материала, производственном процессе и соответствующей терминологии, а также является отличной грунтовкой для новичков в цементной и бетонной промышленности.
- Просмотр Скачать
- Шлаковый цемент и летучая зола -SCIC № 11
- Шлаковый цемент и летучая зола являются дополнительными вяжущими материалами, часто включаемыми в современные бетонные смеси. SCIC # 11, Шлаковый цемент и летучая зола, сравнивает эти два материала, объясняя, что, хотя между ними существует химическое сходство, они оказывают различное влияние в конкретных применениях. Шлаковый цемент — это гидравлический цемент, а летучая зола — пуццолан. В этом информационном листе перечислены свойства, которые цементный шлак может придать бетону как в пластичной, так и в затвердевшей форме. Например, добавление шлакового цемента обычно приводит к снижению потребности в воде, более быстрому схватыванию, улучшенной перекачиваемости и отделимости, более высокой 28-дневной прочности, более низкой проницаемости, устойчивости к сульфатному воздействию и щелочно-кремнеземной реактивности (ASR), а также к более легкой цвет.
- Просмотр Скачать
- Смешанные цементы — SCIC № 21
- ASTM C595, Стандартные технические условия на смешанные гидравлические цементы, требует, чтобы смешанные цементы состояли из однородной и однородной смеси определенных составляющих материалов.Смешанный цемент производится путем взаимного измельчения портландцементного клинкера с другими указанными материалами или путем смешивания портландцемента с другими материалами, или путем сочетания измельчения и смешивания. Цементы с бинарными смесями содержат два составляющих материала, а трехкомпонентные цементы содержат три составных материала. Смешанный цемент может позволить некоторым производителям бетона воспользоваться преимуществами шлакового цемента, несмотря на ограничения по хранению.
- Просмотр Скачать
Терминология по шлаковому цементу
Терминология
- Цемент шлаковый (шлак доменный гранулированный):
- Гидравлический цемент, образующийся при измельчении гранулированного доменного шлака до подходящей крупности.
- Шлак доменный гранулированный:
- Стекловидный гранулированный материал, образующийся при быстром охлаждении расплавленного доменного шлака, как при погружении в воду. Также называется гранулами.
- Доменный шлак:
- Неметаллический продукт, состоящий в основном из силикатов и алюмосиликатов кальция и других оснований, который вырабатывается в расплавленном состоянии одновременно с железом в доменной печи.
- Доменная печь:
- Печь, используемая для восстановления сырья в расплавленный чугун.Горение происходит под давлением сжатого воздуха.
- Доменный шлак с воздушным охлаждением:
- Материал, полученный в результате отверждения расплавленного доменного шлака в атмосферных условиях. Последующее охлаждение можно ускорить, нанеся воду на затвердевшую поверхность. (Этот материал можно добывать и измельчать для использования в качестве заполнителя для бетона или заполнителя, но он не является цементным.
)
- Расширенный доменный шлак:
- Легкий ячеистый материал, получаемый путем контролируемой обработки расплавленного доменного шлака водой или водой и другими агентами, такими как пар или сжатый воздух, или и тем, и другим.(Обычно используется как легкий заполнитель и не вяжущий.)
- Портландцемент:
- Гидравлический цемент, получаемый путем измельчения портландцементного клинкера и обычно содержащий сульфат кальция.
- Смешанный цемент:
- Гидравлический цемент, полученный путем взаимного помола портландцементного клинкера с другими материалами, или путем смешивания портландцемента с другими материалами, или путем сочетания перемола и смешивания.
- Портланд доменный шлаковый цемент:
- Комбинированный цемент, состоящий из тщательно перемолотой смеси портландцементного клинкера и гранулированного доменного шлака или однородной смеси портландцемента и мелкозернистого гранулированного доменного шлака, в котором количество составляющего шлака находится в пределах указанные пределы.
- Гидравлический цемент:
- Цемент, который схватывается и затвердевает при химическом взаимодействии с водой и способен делать это под водой.
- Пуццолан:
- Кремнистый или кремнийсодержащий и глиноземистый материал, который сам по себе обладает незначительной цементирующей способностью или не имеет ее, но в мелкодисперсной форме и в присутствии влаги будет химически реагировать с гидроксидом кальция при обычных температурах с образованием соединений, обладающих вяжущими свойствами. .
- Стекло:
- Неорганический продукт плавления, остывший до твердого состояния без кристаллизации.
Технические характеристики
Стандартные технические условия на измельченный гранулированный доменный шлак для использования в Бетон и строительные растворы — ASTM C 989
1 Настоящая спецификация охватывает три сорта мелко измельченного гранулированного доменного шлака для использования в качестве вяжущего материала в бетоне и растворе. Материал, описанный в этой спецификации, может быть использован 1) для смешивания с портландцементом с целью получения цемента, соответствующего требованиям Спецификации C 595 или 2) в качестве отдельного ингредиента в бетонных и строительных смесях. Материал также может быть использован в различных растворах и растворах.
Стандартная спецификация для смешанных гидравлических цементов — ASTM C 595
2Настоящая спецификация относится к пяти классам смешанного гидравлического цемента для общего и специальные применения, с использованием шлакового цемента, или пуццолана, или того и другого, с портландцементом или портландцементом цементный клинкер или шлак с известью.Эта спецификация предписывает ингредиенты и пропорции. В Двумя наиболее распространенными типами цемента с добавлением шлакового цемента являются:
- Тип IS — портландцемент доменного шлака (в котором содержание шлака составляет от 25% до 70 процентов по массе)
- Тип I (SM) — портландцемент с модифицированным шлаком (в котором содержание шлака менее 25 процентов) Стандартные технические условия для гидравлического цемента — ASTM C 1157 3
В данной спецификации рассматриваются гидравлические цементы как общего, так и специального назначения. Это спецификация, которая определяет требования к характеристикам цемента и не ограничивает состав цемента или его составляющих. В спецификации цементы классифицируются по типу, исходя из конкретных требований для общего использования, высокой начальной прочности, устойчивости к воздействию сульфатов и теплоты гидратации. Дополнительные требования предусмотрены для свойства низкой реакционной способности с агрегатами, реагирующими с щелочами.
Измельченный гранулированный доменный шлак как цементирующий компонент в бетоне
4 (По данным Комитета 233 ACI) В этом отчете в первую очередь рассматривается использование шлакового цемента в качестве отдельного вяжущего материала, добавляемого вместе с портландцементом при производстве бетона.Другие шлаки, полученные при плавке материалов, отличных от железной руды, в этом отчете не рассматриваются. Читатель должен знать, что характеристики материала, описанные в этом отчете, и рекомендации по использованию относятся исключительно к шлаковому цементу, а не к другим формам или типам шлака.
Спецификации конструкционного бетона
5 (Сообщено Комитетом 301 ACI)Эта спецификация является справочным стандартом, который инженер или архитектор может применить к любому строительному проекту, указав его в спецификациях проекта.Пользователь при необходимости дополняет его, обозначая индивидуальные требования к проекту. Документ охватывает материалы и пропорции бетона; арматурные и преднапряженные стали; производство, укладка и выдержка бетона; и проектирование и строительство опалубки. Уточнены методы обработки стыков и закладных деталей, ремонта дефектов поверхности и отделки формованных поверхностей. Отдельные главы посвящены строительству и отделке перекрытий, архитектурному бетону, массивному бетону, а также материалам и методам изготовления бетона, подвергающегося последующему напряжению.Включены положения, регулирующие испытания, оценку и приемку бетона, а также приемку конструкции.
Строительные нормы и правила для конструкционного бетона
6 (Сообщено Комитетом 318 ACI) Кодовая часть этого документа охватывает надлежащее проектирование и строительство конструкционного и простого бетона для зданий. Код был написан в такой форме, что его можно использовать в качестве ссылки в общих строительных нормах и правилах. Среди охваченных тем: чертежи и спецификации;
осмотр; материалы; требования к долговечности; качество бетона, перемешивание и укладка; опалубка;
закладные трубы и строительные швы; анализ и дизайн; прочность и удобство эксплуатации; изгиб
и осевые нагрузки; сдвиг и кручение; плитные системы; стены; опоры; сборный бетон; композитные элементы на изгиб; и предварительно напряженный бетон.
Ссылки
- ASTM C989-99, Стандартные спецификации для измельченного гранулированного доменного шлака для использования в бетоне и строительных растворах, Американское общество испытаний и материалов, Вест Коншохокен, Пенсильвания, 2003 г.
- ASTM C595-03, Стандартные спецификации для смешанных гидравлических цементов, Американское общество испытаний и материалов, Вест Коншохокен, Пенсильвания, 2003.
- ASTM C1157-02, Стандартные технические условия для гидравлического цемента, Американское общество испытаний и материалов, Вест Коншохокен, Пенсильвания, 2003.
- ACI 233R-95, Гранулированный доменный шлак в качестве цементирующего элемента в бетоне, Американский институт бетона, Фармингтон-Хиллз, Мичиган, 1995.
- ACI 301-99, Технические условия на конструкционный бетон, Американский институт бетона, Фармингтон-Хиллз, Мичиган, 1999.
- ACI 318-02, Требования строительных норм для конструкционного бетона, Американский институт бетона, Фармингтон-Хиллз, Мичиган, 2002.
«Как и любой бетон. смеси, следует провести пробные партии для проверки бетона характеристики.Результаты могут отличаться в зависимости от различных обстоятельств, в том числе температура и компоненты смеси, среди прочего. Вам следует обратитесь за помощью к своему специалисту по шлаковому цементу. Ничего не содержало в данном документе следует рассматривать или толковать как гарантию или гарантию, либо явные или подразумеваемые, включая любую гарантию пригодности для конкретного цель.»
Свойства шлакового цемента и его влияние на структуру затвердевшей цементной пасты
Реферат
Измельченный доменный гранулированный шлак, используемый при производстве строительных материалов и изделий, отличается своим химическим составом, дисперсностью, количеством аморфная фаза и т. д., что приводит к изменению свойств цементной смеси, состоящей из ЦЕМ I и дополненной разным количеством шлака.Химический и минералогический состав портландцемента, условия его созревания, активаторы и др. Также влияют на свойства цементной смеси. Кислый шлак не является связывающим в отличие от основного, но из-за пуццолановых свойств он взаимодействует с гидроксидом кальция с образованием дополнительного количества гидратированного силиката кальция с низким содержанием основного основания в структуре затвердевшего цементного теста. Прочность смешанного цемента с увеличением дозировки шлака изменяется по-разному — небольшое количество шлака в цементе даже немного увеличивает прочность на сжатие и изгиб по сравнению с смешанным цементом без дополнительного CEM I.При увеличении дозировки шлака в смешанном цементе его прочность на сжатие несколько снижается, особенно на ранней стадии, а прочность на изгиб остается на том же уровне при увеличении дозировки до 70-80% от массы смешанного цементного шлака.
Помимо эффекта разбавления CEM I, увеличение водопотребности смеси с увеличением дозировки шлака влияет на прочность образцов раствора из равномерных и легко обрабатываемых смесей. Истинное соотношение воды и связующего значительно увеличивается, если содержание шлака превышает 70%.
Проведенные исследования показали, что замещение ЦЕМ I 70% шлака оптимально как с точки зрения влияния на технические характеристики получаемой породы, так и с экономической точки зрения.
Структура горных пород, полученная из цементной смеси, отличается высокой концентрацией аморфизированных низкоосновных продуктов гидратации и снижением содержания в них Са (ОН) 2 . Последняя пропорциональна количеству шлаковой добавки и существенно влияет на фазовый состав породы и ее свойства.
Ключевые слова
доменный гранулированный шлак
портландцемент
водопотребность
время схватывания
прочность на сжатие
портландит
Рекомендуемые статьиЦитирующие статьи (0)
© 2016 Автор (ы). Издано Elsevier Ltd.
Рекомендуемые статьи
Цитирующие статьи
цемент | Определение, состав, производство, история и факты
Цемент , в общем, клейкие вещества всех видов, но, в более узком смысле, связующие материалы, используемые в строительстве и гражданском строительстве.Цементы этого типа представляют собой мелкоизмельченные порошки, которые при смешивании с водой становятся твердой массой. Отверждение и затвердевание являются результатом гидратации, которая представляет собой химическое сочетание цементных смесей с водой, которое дает субмикроскопические кристаллы или гелеобразный материал с большой площадью поверхности. Из-за их гидратирующих свойств строительные цементы, которые схватываются и затвердевают даже под водой, часто называют гидравлическими цементами. Самый важный из них — портландцемент.
процесс производства цемента Процесс производства цемента, от дробления и измельчения сырья, обжига измельченных и смешанных ингредиентов до окончательного охлаждения и хранения готового продукта.
В этой статье рассматривается историческое развитие цемента, его производство из сырья, его состав и свойства, а также проверка этих свойств. Основное внимание уделяется портландцементу, но также уделяется внимание другим типам, например, шлакосодержащему цементу и высокоглиноземистому цементу. Строительный цемент имеет общие химические составляющие и технологии обработки с керамическими изделиями, такими как кирпич и плитка, абразивные материалы и огнеупоры.Подробное описание одного из основных применений цемента см. В статье «Строительство зданий».
Применение цемента
Цемент может использоваться отдельно (т.е. «в чистом виде» в качестве затирочного материала), но обычно используется в растворе и бетоне, в которых цемент смешан с инертным материалом, известным как заполнитель. Строительный раствор представляет собой цемент, смешанный с песком или щебнем, размер которого должен быть менее примерно 5 мм (0,2 дюйма). Бетон представляет собой смесь цемента, песка или другого мелкого заполнителя и крупного заполнителя, который для большинства целей составляет от 19 до 25 мм (0.От 75 до 1 дюйма), но крупный заполнитель также может достигать 150 мм (6 дюймов), когда бетон помещается в большие массы, такие как дамбы. Растворы используются для связывания кирпичей, блоков и камня в стенах или для визуализации поверхностей. Бетон используется для самых разных строительных целей. Смеси грунта и портландцемента используются в качестве основы для дорог. Портландцемент также используется при производстве кирпича, черепицы, черепицы, труб, балок, шпал и различных экструдированных изделий.Продукция собирается на заводах и поставляется готовой к установке.
Заливка бетона в фундамент дома.
Karlien du Plessis / Shutterstock.com Производство цемента чрезвычайно широко распространено, так как бетон сегодня является наиболее широко используемым строительным материалом в мире.
% PDF-1.3
%
949 0 объект
>
endobj
xref
949 89
0000000016 00000 н.
0000003667 00000 н.
0000003773 00000 н.
0000004808 00000 п.
0000005185 00000 п.
0000005533 00000 н.
0000005893 00000 н.
0000006269 00000 н.
0000006408 00000 п.
0000006769 00000 н.
0000006902 00000 н.
0000007443 00000 н.
0000007580 00000 н.
0000007714 00000 н.
0000008293 00000 н.
0000008790 00000 н.
0000009473 00000 н.
0000011038 00000 п.
0000011843 00000 п.
0000013004 00000 п.
0000014172 00000 п.
0000015497 00000 п.
0000016751 00000 п.
0000018575 00000 п.
0000019401 00000 п.
0000020567 00000 п.
0000021170 00000 п.
0000022268 00000 п.
0000023647 00000 п.
0000024992 00000 н.
0000025985 00000 п.
0000026625 00000 п.
0000027604 00000 п.
0000028575 00000 п.
0000029795 00000 п.
0000030614 00000 п.
0000031882 00000 п.
0000032776 00000 п.
0000033214 00000 п.
0000034384 00000 п. 0000035086 00000 п.
0000035848 00000 п.
0000036661 00000 п.
0000037441 00000 п.
0000038275 00000 п.
0000039139 00000 п.
0000040387 00000 п.
0000040585 00000 п.
0000040655 00000 п.
0000040855 00000 п.
0000040882 00000 п.
0000041227 00000 п.
0000072940 00000 п.
0000073144 00000 п.
0000073215 00000 п.
0000073568 00000 п.
0000073597 00000 п.
0000074088 00000 п.
0000094398 00000 п.
0000094595 00000 п.
0000094666 00000 п.
0000094860 00000 п.
0000094889 00000 н.
0000095231 00000 п.
0000118770 00000 н.
0000118968 00000 н.
0000119039 00000 н.
0000119245 00000 н.
0000119274 00000 н.
0000119622 00000 н.
0000119737 00000 н.
0000119852 00000 н.
0000119930 00000 н.
0000120397 00000 н.
0000120955 00000 н.
0000125682 00000 н.
0000128992 00000 н.
0000132382 00000 н.
0000135173 00000 н.
0000136308 00000 н.
0000149449 00000 н.
0000166751 00000 н.
00001 00000 н.
0000212501 00000 н.
0000234789 00000 н.
0000239359 00000 н.
0000243294 00000 н.
0000003468 00000 н.
0000002119 00000 п.
трейлер
] >>
startxref
0
%% EOF
1037 0 объект
> поток
xV} L [U? ~ AA (18͚uRC ‘= h) (lF`0Ae (S [PYL! / D
~ Q
# S0x {-Q ޤ sOoN
SCM в бетоне: шлаковый цемент
Автор: Кайла Хэнсон, П.E.
Примечание редактора. Это вторая статья из серии, в которой подробно рассматриваются типы доступных дополнительных вяжущих материалов (SCM) и их роль в прочности бетона. Чтобы прочитать первую статью из серии о летучей золе, щелкните здесь.
Сегодня и производители, и потребители находятся в бесконечной охоте за быстрыми, доступными, высококачественными и экологичными решениями. Будь то новые концепции, такие как Amazon Dash для мгновенного заказа; программы обмена автомобилями в перегруженных городах; или просто растущая популярность существующих идей, таких как сокращение, повторное использование и переработка, люди повсюду и в каждой отрасли играют определенную роль.Промышленность сборного железобетона ничем не отличается. Такой подход и активное поведение привели к новым решениям производственных проблем, даже если решения исходят из существующих материалов, таких как шлаковый цемент.
По данным Ассоциации шлакового цемента, некоторые количественные преимущества использования шлакового цемента или измельченного гранулированного доменного шлака в бетоне включают улучшенную обрабатываемость и обрабатываемость, более высокую прочность на сжатие и изгиб, повышенную стойкость к агрессивным химическим веществам, повышенную долговечность и сокращение срока службы. расходы.
По этой причине Фил Лапп, менеджер завода Faddis Concrete Products в Даунингтауне, штат Пенсильвания, сказал, что в 2016 году его компания начала использовать шлаковый цемент вместо летучей золы для производства 90% своей продукции. Он сказал, что многие отделы транспорта предъявляют требования к шлаковому цементу для снижения реакционной способности щелочи и кремнезема, формы разрушения бетона, которая возникает, когда определенные заполнители вступают в реакцию со щелочами в портландцементе. После перехода не было замечено никаких сложностей, и он хочет оставить продюсерам одно важное сообщение.
«Не бойтесь этого, — сказал он.
Производство шлакового цемента начинается в доменной печи. (Фото любезно предоставлено Шлакоцементной ассоциацией и St.Marys Cement)
Производственный шлакШлак — это побочный продукт плавки железной руды в процессе производства стали. Железо и многие другие типы металлических руд, обнаруженные в органическом виде, являются нечистыми и содержат следы других материалов или металлов. При нагревании железной руды до температуры свыше 2700 градусов по Фаренгейту металл плавится и отделяется чистое железо от примесей в руде.Вместе примеси и другие материалы в печи создают шлак. Расплавленный шлак плавает над более плотным расплавленным чугуном. Жидкий шлак отделяется и закаливается в воде, чтобы быстро охладить его, в результате получается твердое, каменное вещество с поверхностью, напоминающей стекло.
Охлажденный и высушенный шлак измельчается в мелкий порошок, в результате чего образуются мелкие грубые неровные частицы. Затем портландцемент может быть непосредственно смешан с ним для создания шлакового цемента. Шлак можно использовать в порошкообразном виде и добавлять в смеситель во время дозирования как отдельный вяжущий компонент.
Шлаковый цемент будет подвергаться пуццолановым реакциям в сочетании с водой и активатором, таким как гидроксид кальция (CH) или гидроксид натрия. Пуццолановые реакции начинаются, как только в результате реакций гидратации цемента образуется достаточное количество СН или гидроксида натрия. Когда шлаковый цемент, вода и CH вступают в реакцию, CH расходуется и образуется гидрат силиката кальция, добавляя прочность и долговечность матрице растущей пасты.
Как и другие дополнительные вяжущие материалы, которые производятся как промышленные побочные продукты или побочные продукты, химический состав шлакового цемента варьируется в зависимости от исходных материалов, которые используются для производства чугуна и других веществ в печи, из которой образовался шлак. Поведение шлака в бетоне определяется прежде всего его химическим составом.
Частицы измельченного шлака примерно такого же размера или немного меньше, чем частицы портландцемента. Большинство зерен шлака имеют длину или диаметр менее 45 микрометров, что дает частицам большую площадь поверхности на единицу объема по сравнению с портландцементом. Несмотря на угловатость и грубую текстуру материала, добавление шлакового цемента в бетонную смесь может снизить потребность в воде из-за меньшего размера частиц.Подобно тому, как оптимальная упаковка частиц среди хорошо отсортированных заполнителей может помочь повысить прочность и долговечность бетона за счет уменьшения количества и размера пустот, то же самое можно сказать и о компонентах, составляющих бетонную пасту. Использование более мелких вяжущих частиц, например, при использовании частичной замены шлакового цемента, позволяет цементу и зернам SCM уплотняться ближе друг к другу. В некоторой степени это может помочь снизить потребность в воде. В случаях, когда частицы SCM намного мельче цемента (например, микрокремнезем), общая площадь поверхности материала значительно больше, чем у цемента, что приводит к увеличению потребности в воде.
Шлаковый цемент обычно используется в количестве от 30% до 50% по массе вяжущего материала. Однако в некоторых уникальных сценариях шлаковый цемент может составлять до 80% от общего вяжущего материала.
Преимуществом шлакового цемента является его консистенция и однородность при изготовлении. Это может привести к повышению предсказуемости и повторяемости.
Бетон, изготовленный из шлакового цемента, обычно имеет пониженную водопотребность, но повышенную удобоукладываемость.По данным Portland Cement Association, «влияние шлакового цемента на просачивание и сегрегацию обычно зависит от его крупности. Бетоны, содержащие измельченные шлаки, сравнимые по крупности с портландцементом, имеют тенденцию проявлять повышенную скорость и степень просачивания, чем простые бетоны, но это, по-видимому, не оказывает неблагоприятного воздействия на сегрегацию. Шлаковые цементы с более мелким помолом, чем портландцемент, как правило, уменьшают просачивание ».
Шлаковый цемент обычно не влияет на содержание воздуха в бетоне.Содержание углерода в цементирующем материале может вызвать изменение содержания воздуха в свежем бетоне, но шлак не содержит углерода. Недостаток углерода помогает снизить колебания и непредсказуемую изменчивость увлеченного воздуха.
Установка, развитие прочности и износостойкость Поскольку пуццоланы продлевают процесс гидратации, бетон, изготовленный из шлакобетона, может иметь более низкую теплоту гидратации, более медленное время схватывания и более низкую прочность в раннем возрасте. Однако через 28 дней показатели прочности шлакобетона могут превосходить показатели прочности обычного портландцементного бетона.Бетон, изготовленный из пуццолановых SCM, может продолжать набирать прочность и после 28 дней, хотя скорость набора прочности со временем неуклонно замедляется. Шлакобетон не только отличается повышенной прочностью на сжатие, но и повышенной прочностью на изгиб. Это во многом объясняется повышенной плотностью пасты и улучшенным сцеплением паста-заполнитель.
Низкая теплота гидратации цементного шлакобетона полезна при применении в массовом бетоне и в случаях, когда необходимо избегать чрезмерных температур бетона или холодных швов.
Бетон, изготовленный с частичной заменой шлакового цемента, также обычно демонстрирует пониженную проницаемость, абсорбцию и щелочно-кремнеземную реактивность. Использование шлакового цемента в бетоне также способствует повышению коррозионной стойкости и устойчивости к сульфатам.
Используйте с осторожностью При добавлении шлакового цемента в конструкцию смеси необходимо учитывать не только положительные результаты, которые даст новый материал, но также то, как этот материал может повлиять на поведение других компонентов штапельной смеси и как другие ингредиенты могут повлиять на шлаковый цемент.Как и в случае любого SCM, также важно учитывать тип продукта, в котором будет использоваться шлаковый цемент, окружающая среда, в которой продукт будет находиться, а также условия, в которых будет находиться бетон во время укладки, отделки и отверждения.