ШПАЛЫ ЖЕЛЕЗОБЕТОННЫЕ. Описание, технические характеристики – ГК РОСАТОМСНАБ
Задать вопрос
Железобетонные шпалы – главное составляющие железнодорожных путей.
В настоящие время, они получили широкое применение в отличии от деревянных шпал. В железнодорожном пути опору укладывают на верхнее строение балластного слоя, что создаёт устойчивость в взаимном расположении рельсовых нитей. Давление воспринимаемое от промежуточных скреплений или от рельсов, передается на балластный слой (пошпальное основание). Основным преимуществом является создание наилучшей равно упругости рельсовых опор. Наряду с этим шпалы более устойчивы к гниению, а так же имеют большую прочность при смятии. Срок эксплуатации железобетонных шпал при ежедневной нагрузке достигает в среднем до 50 лет.
Практика показывает, что движения поезда по железобетонным шпалам, более плавное, при этом отмечается создание наилучших условий для работы бесстыкового пути вследствие большой поперечной устойчивости.
Изготовление шпал осуществляется непосредственно с требованиями указанными в ГОСТ.
Существует ряд основных технических характеристик производства железобетонных шпал.
• Длина — 2700 мм.
• Ширина — 300 мм.
• Высота — 230 мм.
• Устойчивость к морозу – не ниже F200
• Категория бетона – не менее B40 (М500)
Железобетонные шпалы представляют собой достаточно сложную конструкцию, которая подвержена различным погодным условиям, а так же эксплуатируется с ежедневными чрезвычайными нагрузками.
Железобетонные шпалы современного типа – цельнобрусковые из напряженного железобетона, армированные высокопрочной проволокой, полностью удовлетворяющие ТУ 5864 – 019 — 11337151-95 и ГОСТу 10629-88.
Классификация ЖБ шпал:
• ЖБ шпалы Ш 1-1 (угол наклона упорных кромок подрельсовых площадок в шпалах 55 град.o) применяются для раздельного клеммно — болтового скрепления КБ с болтовым прикреплением подкладки к шпале. Производятся они из тяжелого бетона класса по прочности на сжатие В40 (М500).Марка бетона по морозостойкости должна быть не ниже F200 (Мрз200). Для бетона шпал применяется щебень (из природного камня или гравия) фракция 5-20 мм. ГОСТ 10629-88.
• ЖБ шпалы Ш 1-2 (угол наклона упорных кромок подрельсовых площадок в шпалах 72 град.o) используются для раздельного клеммно — болтового скрепления КБ с болтовым прикреплением подкладки к шпале. ГОСТ 10629-88.
• ЖБ шпалы Ш 2-1 применяются для нераздельного клеммно-болтового рельсового скрепления БПУ с болтовым прикреплением подкладки или рельса к шпале. ГОСТ 10629.
• ЖБ шпалы Ш 3 используются для нераздельного клеммно-болтового скрепления ЖБР65 с болтовым прикреплением рельса к шпале.
• ЖБ шпалы ШС-АРС применяются для анкерного рельсового скрепления.
• ЖБ шпалы Ш 1-16*5 — шпалы с высокопрочной проволочной арматурой периодического профиля диаметром от 3 до 5 мм.
• ЖБ шпалы Ш 1-4*10 представляют собой шпалы с высокопрочной стержневой арматурой периодического профиля диаметром стержней от 7 до 12 мм.
Для шпал широко используется в качестве арматуры стальная проволока периодического профиля. При этом к ее диаметр должен составлять 3 мм, а сама проволока иметь вид класса Вр. Число проволок в номинале шкалы составляет 44, при чем каждая натянута с особым усилием 8,1 кН. В отличии от трещино — стойкости, геометрические параметры и качество бетонных поверхностей разделяют на две категории: первая и вторая. Осуществление укладки на подъездных путях, а также на стационарных и малодеятельных производиться шпалами второго сорта. Причем поставка происходит только при согласии потребителя.
На рельсах Р65 имея скрепление КБ, наработка тоннажа составляет минимум 2000 млн т брутто. Объем дефекта железобетонных шпал при общем выходе и ремонта всех видов не превышает 5-6 % после пропуска 1,0 млрд т брутто.
Наиболее значительную экономию играет перекладка старых железобетонных шпал снятых с путей 1-ой и 2-ой категории при капитальном ремонте, на пути 3-4-го классов и подъездные пути промышленных предприятий.
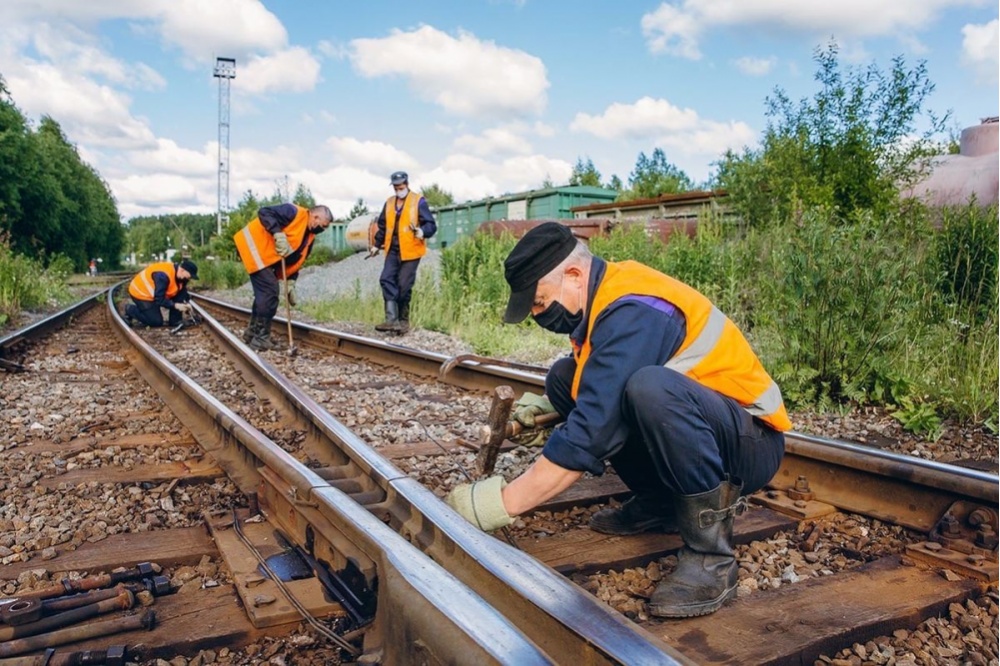
При транспортировке железобетонных шпал необходимо руководствоваться требованиями ГОСТ 13015-2003, так же это требование напрямую относиться и к методам хранения. Хранить шпалы необходимо в штабелях при этом ряды должны быть строго горизонтальные и подошвой вниз т.е в рабочем положении. Штабель должен быть высотой в 16 рядов, но не больше! Так же под шпалы и между ними необходимо уложить деревянные подкладки. Между шпалами их располагают в углублениях. Минимальная толщина подкладок составляет 50 мм. Допустимо отклонение применения деревянных прокладок с сечением минимально 40х40 мм, но лишь с согласованием потребителя.
Изготовитель железобетонных шпал осуществляет гарантийный срок эксплуатации 3 года с момента укладки их на железнодорожные пути.
|
||
|
||
|
||
|
||
|
Задать вопрос
Деревянные или железобетонные шпалы — преимущества и недостатки
Когда прокладываются новые железнодорожные пути, встаёт вопрос о том, каким именно шпалам отдать предпочтение — деревянным или железобетонным. Чаще всего вопрос упирается в цену. Тут выигрывают деревянные шпалы. В то же время, железобетонные шпалы выигрывают в плане долговечности. Железобетонные изделия могут прослужить очень долго, а потому их устанавливают на путях, которые могут принести большой доход быстро. В противоположность этому, деревянные шпалы чаще используют там, где нет большой нагрузки и нужно сэкономить деньги.
Железобетонные шпалы: преимущества и недостатки
У железобетонных и древесных изделий есть и много других значительных отличий. При монтаже и дальнейшей эксплуатации у железобетонных шпал выявляется ряд преимуществ:
- Хорошая морозоустойчивость;
- Можно использовать от 40 до 50 лет;
- Им не страшна ржавчина и разложение;
- Придают рельсам особую устойчивость:
- Создают однородный ж/д путь.
Тем не менее, выявляется и ряд недостатков. К проблемам железобетонных изделий относится:
- • Высокая проводимость тока;
- • Плохая устойчивость к механическим ударам;
- • Путь становится жёстким — рельсы изнашиваются;
- • Каждая шпала весит около 270 кг, что немало;
- • Шпалы ж/б сложно устанавливать;
- • Они стоят больших денег.
Деревянные шпалы: преимущества и недостатки
Несмотря на то, что железобетонные шпалы для путей приобретают всё чаще, деревянные тоже пользуются достаточно большим спросом. Несмотря на расхожие суждения деревянные шпалы не хуже, а во многом и лучше. Они имеют свои плюсы и минусы. К безусловным преимуществам относится:
- Приятная цена — деревянные шпалы очень недороги и быстро окупаются;
- Деревянная шпала весит всего 80 кг — в 3 раза меньше, чем ж/б;
- С деревянными шпалами колею можно и уменьшить, и увеличить;
- Древесина совсем не проводит электричество;
- Материал устойчив к перепаду температур;
- Шпалы из дерева дают отличное сцепление с гравием;
- Они упруги, что тоже важно для железных дорог.
В то же время у деревянных шпал есть один недостаток, который считается критическим:
- В необработанном виде срок использования составляет всего 3 года!
Но всё не так плохо, потому что при хорошей обработке шпалы могут использоваться до 40 лет — срок эксплуатации не сильно уступающий тому, который называют изготовители железобетонных шпал. Мы занимаемся производством деревянных шпал. При изготовлении они пропитываются маслами и антисептиками, препятствующими гниению и разложению. В результате наши изделия имеют срок службы около 40 лет.
В чем преимущества и недостатки железобетонных шпал?
15 октября’18
Материал изготовления
Шпалы — опорная конструкция под железнодорожные рельсы. Они укладываются на подготовленный слой баласта. Для железной дороги используется сыпучий песок, городское метро же возводится на бетонном основании. Главная задача — закрепить рельсы в идеальном параллельном состоянии и снять с них часть нагрузки от проезжающих составов.
- Каменные шпалы, которые использовались в самом начале тяжелы в изготовлении. Потому цена на такой продукт слишком высока для больших проектов. Помимо этого, камень не самый стойкий к износу материал. От постоянных вибраций он легко трескается и приходит в негодность
- Деревянные долго считались идеальным вариантом. Они легки как в производстве, так и в установке. Цена значительно ниже. Не копят статический ток. Вот только страдают от влажного и холодного климата, поедаются термитами, высыхают на солнечном свете. Для защиты от этого, дерево покрывается специальными составами. Но это повышает расходы на обслуживание путей и снижает общую надежность конструкции

Преимущества железобетонной шпалы
Применение железобетонных конструкций в ЖД — отрасли обусловлено положительными характеристиками этого изделия:- Высокая износостойкость. Сделанное по ГОСТу изделие без проблем справляется как с климатическими, так и с рабочими условиями эксплуатации. Армирование стальной проволокой усиливает конструкцию, а создаваемое растягивающее усилие закаляет материал перед нагрузками
- Длительный срок службы. В среднем, ЖБ прослужит в 10 раз дольше, чем дерево. Армированный бетон не подвержен коррозии, не гниет и не усыхает. Поэтому, в тяжелом климате этот срок увеличивается еще больше
-
Устойчивость к механическим нагрузкам.
Технология изготовления, включающая в себя заливку бетона в форму, на подготовленные арматурные балки под напряжением, отлично справляется с весом проходящих составов. А также крепко удерживает возложенные рельсы. Это важный параметр в современных требованиях к безопасности путей
- Низкая стоимость. Налаженный поток производства позволяет снижать цену на одно изделие. Особенно это важно при крупных поставках, для больших и важных проектов. Это та ситуация, когда можно сэкономить бюджет строительства без потери его качества
- В отличие от того же дерева, вам не требуется регулярно проверять пути и обрабатывать шпалы специальными антисептическими средствами, дабы замедлить их гниение. Бетон и сам прекрасно справляется с этой задачей. Затраты на обслуживание меньше, что в долгосрочной перспективе отличный плюс к бюджету строительства
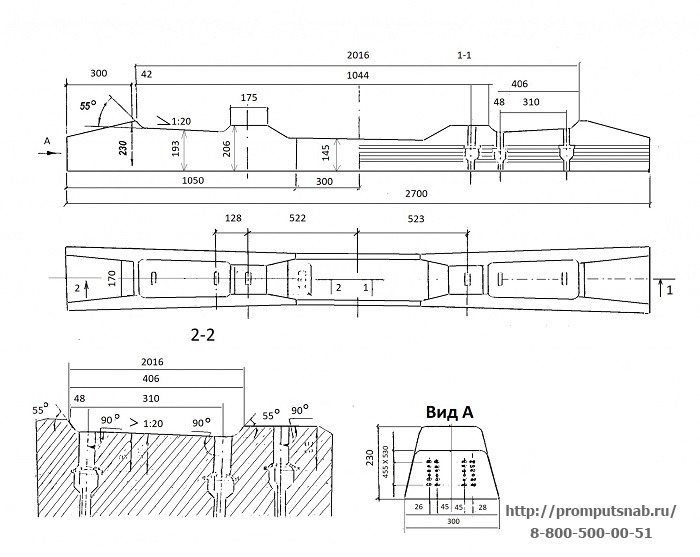
Недостатки
Недостатком считается вес получившегося изделия. Но современные технологии укладки позволяют нивелировать этот минус. Масса готового изделия составляет 0.27 тонны. Поэтому применяются специальные устройства — шпалоукладчики. Да, деревянные шпалы можно водружать ручной рабочей силой. Но итоговые положительные стороны железобетона все-таки выглядят более сильными, нежели один минус. Также сложностью считают, что для ЖБ-шпалы требуется изоляция. Это действительно так, они должны быть изолированы, чтобы снимать электропроводность.Типы шпал
Согласно ГОСТ, все заводы, производящие это изделие, должны придерживаться и классификации. Первая из них — размеры:- Длина шпалы составляет 2 700 миллиметров
- Ширина — 300 миллиметров
- Толщина в центральной части — 145 мм
- Высота в местах, где производится крепление рельсы — 206 мм
- Виды подразделяются и по типу рельсового крепления:
-
Ш-1.
Раздельное клемно-болтовое крепление. Стык к опоре закрепляется при помощи прокладки и болта
- Ш-2. Нераздельное соединение
- Ш-3. Аналог к Ш-2, но применяются разные типы установки рельсы

Подробно о размерах весе железобетонныйх шпал читайте в следующем материале.
Производство шпал на ОАО «Спецжелезобетон»;
Описанная выше технология производства, в полном соответствии с государственными актами и ГОСТ, применяется на предприятии ОАО «Спецжелезобетон» под торговой маркой «Микабет». Текущие мощности позволяют создавать 300 000 изделий за год. Объемы производства не ставят в ущерб качество и надежность итогового продукта. Продукция без проблем выдерживает сравнение с лучшими европейскими аналогами, а в таких компонентах, как несущая способность и материалоемкость и вовсе превосходят их.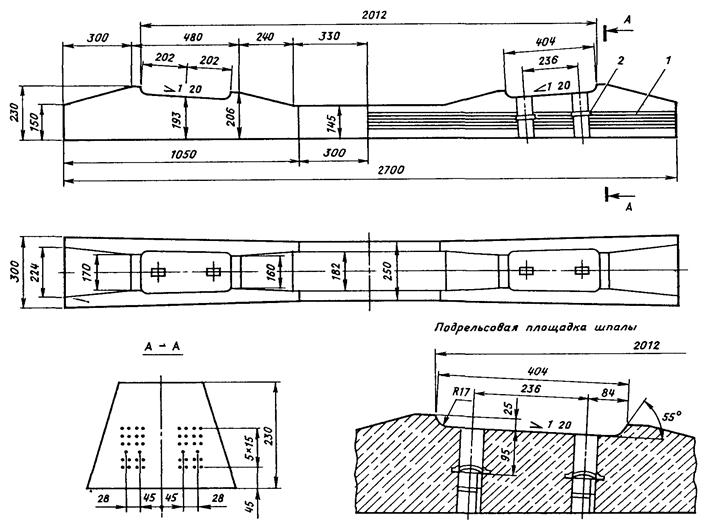
Время перемен – железобетонные шпалы вместо деревянных
Время перемен – железобетонные шпалы вместо деревянных
06 сентября 2014 г.
В ходе эксплуатации железобетонных шпал были в полной мере оценены все их достоинства, главное из которых долговечность. Если средний срок службы деревянных шпал на железных дорогах СССР не превышал 16 лет, то расчетный срок службы их железобетонных «собратьев» составлял 40–50 лет, то есть втрое больше.
Железобетонные шпалы имеют еще ряд существенных плюсов, например обеспечивают повышенную устойчивость колеи в отношении боковых сдвигов и выброса вверх, что особенно важно при использовании длинных рельсовых плетей, чувствительных к изменениям температуры. Именно это свойство железобетона способствовало внедрению на отечественных магистралях бесстыкового («бархатного») пути, придающего движению поездов замечательную плавность. Кроме того, шпалы из железобетона сохраняют однородность физического состояния на протяжении всего срока службы, что позволяет обеспечивать одинаковую упругость подрельсового основания.
Наконец, наращивание производства таких шпал позволяет значительно сократить расход древесины, снизив тем самым остроту экологических проблем. Ведь для изготовления шпал только на один километр пути вырубается до двух гектаров высококачественного леса из 80–100-летних деревьев. В свое время из-за истощения ресурсов места заготовки древесины в СССР были перемещены на северо-восток, где восстановление лесов длится намного дольше, а иногда вообще невозможно. Кроме того, массовые вырубки меняют климат целых регионов, уложенные в путь деревянные шпалы, пропитанные креозотом, отравляют почву, а те, что отслужили свой век, очень сложно поддаются утилизации.
Однако и у железобетонных шпал есть свои противники. В числе недостатков этой технологии называют ее относительную дороговизну. Поэтому, с одной стороны, всегда стояла задача удешевить производство верхнего строения пути, а с другой – использовать железобетон на самых грузонапряженных участках пути, чтобы ускорить его окупаемость. Другой недостаток – высокая жесткость пути приводит к повреждению рельсов в зоне стыков. Эту проблему старались нивелировать укладкой железобетонных шпал под бесстыковой путь. Сочетание железобетонной шпалы с бесстыковым путем в значительной мере компенсировало изъяны обоих элементов рельсошпальной решетки и было признано оптимальным.
В целом же плюсы всегда намного перевешивали минусы. А потому полигон использования железобетонных шпал рос буквально каждый год. Вот лишь несколько цифр. К 1967 году в СССР железобетонные шпалы были уложены более чем на 8 тыс. км путей (развернутая длина всех главных путей была тогда 171,2 тыс. км). А в 1977 году они эксплуатировались более чем на 45 тыс. км пути.
К 1970-м годам ежегодные объемы укладки были доведены до 4,4–4,5 тыс. км, а в середине 1980-х они превысили 4,7 тыс. км. Для того чтобы
обеспечивать растущий спрос, по всей стране строились новые заводы. Впрочем, далеко не все они носили узкоспециализированный характер. Многиепредприятия производили не только шпалы, но и иную железобетонную продукцию, к примеру строительные плиты, трубы.
Однако конец XX века для многих предприятий отрасли стал настоящей проверкой на прочность. Проблемы в экономике страны нарастали как снежный ком. Строительные проекты какое-то время еще велись по инерции, но на рубеже 1980-х и 1990-х годов почти все остановились. Из-за резкого сокращения спроса производства, ориентировавшиеся на выпуск строительных конструкций, были поставлены на грань выживания.
Подобная участь постигла, к примеру, Лискинский завод «Спецжелезобетон». Обиднее всего, что это было почти новое предприятие: его пустили в строй лишь летом 1980 года. А уже в 1988-м Министерство промышленности строительных материалов СССР, в состав которого входил тогда завод, решило закрыть предприятие, посчитав его неэффективным. На базе производственных активов вполне в духе того времени был создан кооператив «Струна», который тоже просуществовал недолго. Таких историй было очень много, а производственные линии останавливались почти повсеместно. Для предприятий, выживших в те тяжелые годы, это оборачивалось прежде всего потерей квалифицированных кадров – предприятия были вынуждены сокращать штат.
Но даже если спрос на продукцию сохранялся, возникал вопрос: сможет ли покупатель рассчитаться? Популярным инструментом в 1990-е стал бартер: за железобетонные конструкции различной сложности платили консервами, сапогами, бытовой техникой, одеждой и даже сигаретами, то есть всем, что служило средством натурального обмена.
Впрочем, сложности были не только с покупателями, но и с поставщиками сырья и комплектующих. К примеру, на Челябинском заводе, который когда-то был пионером в деле выпуска железобетонных шпал, чтобы снизить зависимость от поставщиков, начали осваивать вспомогательные производства. Так, был построен цех, где изготавливались закладные шайбы и пилорама, на которой выпускались деревянные прокладки.
Одним из немногих надежных партнеров в те времена являлось Министерство путей сообщения, продолжавшее закупки железобетонных конструкций (в первую очередь шпал). Поэтому неудивительно, что заводы стремились расширять взаимодействие с железной дорогой. «1990-е – это были тяжелейшие времена. Задача была выстоять, ведь Министерство промышленности строительных материалов СССР, куда входил наш завод, ликвидировали. У нас было два пути – приватизация, как это сделал Муромский завод, после чего и закрылся, или вхождение в состав МПС, нашего основного заказчика. Это был правильный выбор. Мы выстояли», – вспоминает заместитель генерального директора Вяземского завода Олег Свиридов.
Стремясь к сотрудничеству с железной дорогой, некоторые предприятия спешно меняли вид деятельности. Например, расположенный в Энгельсе (Саратовская область) ЖБИ № 6 до распада СССР был крупным производителем сборного железобетона для мелиоративного строительства. В начале 1990-х государство прекратило финансировать это направление, выпускаемая заводом продукция оказалась никому не нужна. Зато на находящейся рядомПриволжской железной дороге ощущался острый дефицит шпал: привозить их издалека было невыгодно, а вблизи ни одного производителя не было. Энгельсский ЖБИ № 6 в сжатые сроки наладил выпуск шпал, а в дальнейшем вошел в состав данной железной дороги.
Коллектив Энгельсского завода неоднократно отмечался за производственные достижения. Так, например, в марте 1981 года предприятие было награждено орденом Трудового Красного Знамени. «Эта государственная награда не только стала венцом десятилетнего юбилея завода, но и подчеркнула его заслуженный статус лучшего железобетонного предприятия Советского Союза», – говорит председатель профкома Энгельсского филиала Александр Имкин. Он вспоминает, что уже в первые годы работы предприятие не только освоило выпуск простейших конструкций из железобетона, но и запустило в производство такие уникальные изделия, как крупногабаритные преднапряжные плиты облицовки каналов, напорные трубы с металлическим сердечником. «Талантливые, думающие специалисты, выросшие на предприятии, они брались за реализацию наиболее важных проектов для мелиорации и строительства», – говорит Александр Имкин
Надо сказать, что по такому пути в те годы пошли многие предприятия. Магистраль, в состав которой включалось предприятие, гарантированно получала материалы верхнего строения пути, а завод обеспечивался твердым заказом. Для многих такая схема оказалась единственным спасением. Например, после ликвидации производственного кооператива «Струна» все производственные мощности Лискинского завода вошли в состав Юго-Восточной железной дороги. Сначала ситуация была крайне тяжелой, но со временем картина выправилась. «В первый год зимой д ля обогрева в цехах разводили костры – центральное отопление попросту не работало. Но постепенно началось возрождение завода. Пошли заказы на шпалы, началось восстановление предприятия», – вспоминает тот период нынешний директор Лискинского филиала Александр Кадуков. Уже в 1990-х предприятие удалось модернизировать. А вскоре Лискинский завод расширил ассортимент своей продукции, приступив к производству бруса для стрелочных переводов.
Присоединение к Министерству путей сообщения сыграло важную роль также в истории Горновского завода – предприятия, являющегося теперь крупнейшим производителем за Уралом. Первую партию шпал и железобетонных труб, на тот период крайне важной и необходимой для развития народного хозяйства на востоке страны продукции, завод выпустил в 1974 году. Для своего времени это было очень прогрессивное по уровню оснащения предприятие. Важно и то, что оно «привязано» к весьма богатой местной сырьевой базе: расположенные рядом Буготакские сопки содержат запасы качественных диабазовых порфиритов и базальтов. Однако в 1990-х перед этим заводом, как и перед многими другими, встал вопрос выживания. Решением оказалась полная переориентация производства на выпуск железнодорожной продукции.
Вспоминает Иван Маложон, начальник Дирекции по ремонту пути Западно-Сибирской железной дороги:
– Из-за резкого уменьшения спроса на профильную продукцию – железобетонные трубы – Горновский завод оказался в 1990-х на грани остановки. Его руководство во главе с директором Валерием Александровичем Отмаховым наметило программу освоения видов продукции, пользующейся спросом у платежеспособных партнеров.
Так в круг интересов завода попала наша магистраль. Главной продукцией, изготовленной для железнодорожников, естественно, стали шпалы. Затем – склейка изолирующих стыков. Следующим этапом, который смело можно назвать революционным, было освоение технологии изготовления рельсовых скреплений, в которых дорога испытывала острую нужду. Их выпуск позволил избежать срыва планов ремонта пути.
К списку новостей
Шпалы железобетонные
Шпалы железобетонные — это специальные балочные конструкции, которые применяются при строительстве железнодорожной колеи в качестве опор для рельсов, по которым перемещается типовой подвижной состав с нагрузками и скоростями, установленными для общей сети железных дорог, без ограничения по грузонапряженности. Шпалы обеспечивают неизменность взаимного расположения рельсовых нитей, воспринимают давление, которое исходит от рельсов и проезжающего по ним транспорта, от промежуточных креплений, и передают его на подшпальное основание (в железнодорожном строительстве это, как правило, балластный слой, в метрополитене — бетонное основание).
Первые упоминания о колейных дорогах из рельсов и шпал относятся к середине XVI века. Рельсы представляли собой деревянные брусья и применялись в рудниках и угольных шахтах, по которым перемещались вагонетки. Деревянные брусья быстро изнашивались, что приводило к тому, что повозки, проходящие по рельсам, сходили с пути. Для того чтобы уменьшить износ, деревянные рельсы стали укреплять полосами, которые укладывались поперек колеи. Срок службы деревянных рельсов и шпал, в зависимости от типа древесины, внешних условий и интенсивности эксплуатации, составлял от семи до сорока лет. Несмотря на такие достоинства, как упругость, хорошее сцепление с щебеночным балластом, легкость обработки, существовал главный недостаток — дерево в местах крепления рельсов и шпал просто гнило из-за накапливающейся влаги. Первая железнодорожная колея, выполненная полностью из чугуна, появилась в XVIII веке, в Петрозаводске.
Тем не менее, учитывая развитие железнодорожного транспорта (появление быстроходных составов, увеличивающаяся скорость передвижения), инженеры столкнулись с быстрым износом чугунной колеи. С открытием новых сплавов на основе металла было установлено, что рельсы из стали меньше и равномернее подвергаются износу по сравнению с другими металлами. С тех пор и по настоящее время во всех мире применяются только стальные рельсы. В годы Великой Отечественной войны (1941-1945 гг.) развитие железных дорог было приостановлено. Однако после нее, в ходе выполнения работ по восстановлению железнодорожного транспорта, были предложены нововведения, призванные усилить железнодорожные пути — бесстыковой путь колеи, снижающий удельное сопротивление движению поездов, расходы электроэнергии и топлива, и железобетонные шпалы, срок службы которых достигает порядка 60 — 70 лет. Сегодня, в строительстве железных дорог применяются исключительно железобетонные шпалы.
Какие же есть преимущества у железобетона в качестве материала для изготовления шпал? Во-первых, долговечность железобетона, позволяющая подвергать шпалы длительной эксплуатации. Во-вторых, высокая степень механической прочности, благодаря которой железобетонные шпалы имеют повышенную несущую способность и могут сопротивляться многочисленным и длительным нагрузкам без потерь первоначальных физических свойств. Помимо этого, железобетонные шпалы устойчивы к агрессивным факторам окружающей среды, в том числе — к влаге, гниению. Простота конструкций высокотехнологична — их можно использовать повторно. По сравнению с другими материалами (дерево, металл) шпалы легко справляются с высокой степенью грузонапряженности. Это основные и очевидные причины высокой актуальности железобетона в сфере строительства.
Железнодорожные железобетонные шпалы представляют собой цельнобрусковые балки специального профиля, имеющие переменное сечение. В конструкции шпал предусмотрены специальные площадки, которые позволяют производить монтаж рельсов, а также отверстия для установки крепежных болтов для рельсошпального крепления, что позволяет также использовать промежуточные скрепления железобетонных шпал. В последнее время для скрепления рельсов и шпал все чаще используется анкерное соединение.
Шпалы в зависимости от типа рельсового скрепления подразделяют на:
- тип I — для раздельного клеммно-болтового рельсового скрепления с резьбовым прикреплением рельса и подкладки к шпале;
- тип II — для нераздельного анкерного рельсового скрепления с безрезьбовым прикреплением рельса к шпале;
- тип III — для нераздельного клеммно-болтового рельсового скрепления с резьбовым прикреплением рельса к шпале.
Шпалы железобетонные подразделяются на классы по наличию или отсутствию электроизолирующих характеристик и виду используемой арматуры напрягаемого типа. По электроизолирующим параметрам шпалы железобетонные выпускаются следующих типов:
- изолированными. Предполагается установка специальных вкладышей изолирующего типа, которые называются пустообразователями;
- неизолированными. Наличие вкладышей не предусмотрено.
По применимости в кривых участках железнодорожного пути разного радиуса шпалы всех типов относят к двум видам:
- для прямых и кривых участков железнодорожного пути радиусом 350 м и более;
- для кривых малого радиуса (менее 350 м) и переходных кривых.
Также основными признаками, по которым выполняется классификация изделий, являются степень трещиностойкости, качество, а также точность геометрических параметров данного типа железобетонных изделий. Принято выделять шпалы 1го и 2го сорта. Шпалы из железобетона второго сорта имеют более низкую степень трещиностойкости, меньшие требования к геометрическим параметрам изделия, пониженное качество изготовления, что обуславливает возможность использования только при обустройстве подъездных и внутризаводских железнодорожных путей пятого класса, которые отличаются невысокой степенью нагрузки и интенсивности эксплуатации.
Железобетонные шпалы изготавливаются в соответствии с номами и требованиями, установленными ГОСТ 10629-88 и ГОСТ Р 54747-2011, из тяжелого бетона класса прочности на сжатие не ниже В40 (по ГОСТ 26633). Фактическая прочность бетона (в проектном возрасте, передаточная и отпускная) должна соответствовать требованиям ГОСТ 13015.0. Нормируемую передаточную прочность бетона следует принимать равной 32 МПа (326 кгс/см2). Отпускную прочность бетона принимают равной передаточной прочности бетона. Марка бетона по морозостойкости должна быть не ниже F200. Для бетона шпал следует применять щебень из природного камня или щебень из гравия фракции 5 — 20 мм по ГОСТ 10268. Допускается по согласованию изготовителя с потребителем применять: щебень фракции 20 — 40 мм в количестве не более 10 % от массы щебня фракции 5 — 20 мм по ГОСТ 10268; щебень из природного камня фракции 5 — 25 мм по ГОСТ 7392 при соответствии его всем другим требованиям ГОСТ 10268.
Железобетонные шпалы армируются предварительно напряженной арматурой, для придания дополнительной прочности, необходимой для железнодорожных путей с большими динамическими нагрузками.
Согласно ГОСТ 10629-88 в качестве арматуры шпал применяется стальная проволока периодического профиля класса Вр диаметром 3 мм по ГОСТ 7348 и ТУ 14-4-1471-87. Номинальное число арматурных проволок в шпале — 44. Расположение проволок, контролируемое на торцах шпалы, должно соответствовать проекту. Расстояние по вертикали в свету между парами или отдельными проволоками, в случае их отклонения от проектного положения, не должно быть менее 8 мм. Допускается разворот пар проволок на 90° при сохранении указанного выше расстояния. Для обеспечения проектного расположения проволок могут применяться разделительные проставки, остающиеся в теле бетона шпалы. Допускается по согласованию изготовителя с потребителем применять проставки, отличающиеся от проектных.
Согласно ГОСТ Р 54747-2011 для армирования шпал следует применять: стальную холоднодеформированную проволоку гладкую и периодического профиля диаметром от 3 до 8 мм, не ниже класса прочности В1200; холоднодеформированную арматуру гладкую и периодического профиля диаметром от 8 до 10 мм, не ниже класса прочности 1400К; горячекатаную и термомеханически упрочненную гладкую арматуру и периодического профиля диаметром от 8 до 10 мм, не ниже класса прочности А1200К; арматурные канаты диаметром от 6 до 14 мм, не ниже класса прочности К1500К. Гладкая арматура может применяться только с концевыми анкерами. Диаметр и класс прочности арматуры, число и расположение арматурных элементов, отклонения от номинального числа арматурных элементов и величина начального натяжения всей арматуры должны быть указаны в технической документации на изделие. Допускается по согласованию с заказчиком применять другие виды арматуры.
Шпалы обозначают марками в соответствии с требованиями ГОСТ 23009. Марка шпалы состоит из двух буквенно-цифровых групп, разделенных тире. Первая группа содержит обозначение типа шпалы. Во второй группе указывают вариант исполнения подрельсовой площадки.
ЦПТ 17 Технические указания по ведению шпального хозяйства с железобетонными шпалами
МИНИСТЕРСТВО ПУТЕЙ СООБЩЕНИЯ СССР
ГЛАВНОЕ УПРАВЛЕНИЕ ПУТИ
№ ЦПТ-17 |
Утверждаю: Начальник Глав ного |
ТЕХНИЧЕСКИЕ УКАЗАНИЯ
ПО ВЕДЕНИЮ ШПАЛЬНОГО ХОЗЯЙСТВА
С ЖЕЛЕЗОБЕТОННЫМИ ШПАЛАМИ
МОСКВА «ТРАНСПОРТ» 1990
СОДЕРЖАНИЕ
1. Указания по применению железобетонных шпал 2, Конструкции железобетонных шпал к основные технические требования к ним 3. Правила приемки, транспортирования, погрузки, выгрузки и складирования железобетонных шпал 4. Особенности сборки и укладки звеньев, а также текущего содержания пути с железобетонными шпалами 5. Дефекты и повреждения железобетонных шпал 6. Повторное применение железобетонных шпал 7. ПРИЛОЖЕНИЕ ДОПУСКАЕМЫЕ К ПРИМЕНЕНИЮ ЖЕЛЕЗОБЕТОННЫЕ ШПАЛЫ, ИЗГОТОВЛЕННЫЕ ПО РАНЕЕ ДЕЙСТВОВАВШИМ СТАНДАРТАМ ИЛИ ТЕХНИЧЕСКИМ УСЛОВИЯМ |
1.1. Железобетонные шпалы предназначены для применения на всех железнодорожных линиях и путях с рельсовой колеей шириной 1520 мм, по которым обращается типовой подвижной состав с нагрузками и скоростями, установленными для общей сети железных дорог, без ограничения по грузонапряженности.
1.2. Железобетонные шпалы следует применять в бесстыковом пути. Применение железобетонных шпал в звеньевом пути может допускаться на станционных и подъездных путях, а также кратковременно на главных путях в период до замены инвентарных рельсов бесстыковыми рельсовыми, плетями.
1.3. Типовые железобетонные
шпалы предназначены для применения с рельсами типов Р75, Р65 и Р50 на прямых
участках пути и в кривых радиусом не менее 350
м.
1.4. На железобетонных шпалах должны применяться рельсовые скрепления, конструкция, детали и сферы применения которых утверждены Главным управлением пути МПС.
Рельсовые скрепления могут быть с металлическими подкладками (КБ, К2), без подкладок (ЖБ), а также комбинированными (БПУ), т.е. с подкладками или без них в зависимости от эксплуатационных условий на участке.
Конструкция рельсового скрепления должна включать упругие прижимные элементы (пружинные клеммы, шайбы), амортизирующие и виброизолирующие подрельсовые и (или) нашпальные прокладки, электроизолирующие детали, обеспечивающие работу рельсовых цепей автоблокировки.
1.5. Железнодорожные шпалы следует укладывать на щебеночном или асбестовом балласте.
Щебень должен быть из природного камня фракций 25-60 мм и иметь марку по истираемости И20 и по сопротивлению удару — У75.
Допускается применение щебня марки по
истираемости И40. и по сопротивлению удару — У50. Применение щебня с более
низкими показателями по истираемости и прочности может допускаться только как
исключение с разрешения Главного управления пути МПС.
На участках пути, подвергающихся интенсивному засорению перевозимыми сыпучими грузами (уголь, руда, торф и; др.), — железобетонные шпалы рекомендуется укладывать на асбестовом балласте.
1.5.1. На главных путях линий грузонапряженностью до 10 млн. т-брутто в год, не подвергающихся засорению сыпучими грузами, разрешается укладывать железобетонные шпалы на щебеночном балласте фракций 5-25 мм.
1.5.2. На станционных путях (кроме
главных в пределах станций и приемоотправочных с безостановочным пропуском
поездов) железобетонные шпалы следует укладывать на щебеночном балласте фракции
5-25 мм.
На погрузочно-выгрузочных, вытяжных, деповских и прочих станционных путях, а
также на подъездных путях допускается укладывать железобетонные шпалы также на
гравийном и гравийно-песчаном балластах.
1.5.3. Все балластные материалы должны удовлетворять требованиям соответствующих стандартов на них.
1.5.4. Конструкция балластной призмы и толщина балластного слоя под железобетонными шпалами должны соответствовать утвержденным поперечным профилям железнодорожного пути.
1.6. Железобетонные шпалы не должны применяться на участках с нестабилизировавшимся или больным земляным полотном. Перед укладкой железобетонных шпал земляное полотно должно быть обследовано и обнаруженные больные места (пучины, просадки и др.) оздоровлены.
1.7. Система ведения хозяйства с железобетонными шпалами должна предусматривать наиболее полное использование повышенной долговечности железобетонных шпал многократным повторным применением их в главных и станционных путях.
1.8. Поступающие от
промышленности новые железобетонные шпалы — должны использоваться только для
сплошной смены шпал при капитальном ремонте пути линий грузонапряженностью
свыше 15 млн. т брутто в год и участков скоростного движения поездов. Для линий
с меньшей грузонапряженностью, а также для выборочной или одиночной замены
негодных железобетонных шпал три среднем и подъемочных ремонтах и текущем
содержанки всех путей следует применять старогодные железобетонные шпалы.
2.1. Железобетонные шпалы, выпускаемые промышленностью, должны отвечать требованиям государственных стандратов или технических условий утвержденных в установленном порядке.
2.2. Конструкция и размеры железобетонных шпал марок Ш1-1, Ш1-2 к Ш2-1 по ГОСТ 10629-88 «Шпалы железобетонные предварительно напряженные для железных дорог колеи 1520 мм. Технические условия» представлены на рис. 1- 4 и в табл. 1,
Рис. 1. Железобетонные шпалы марок ШЫ, I1 I1-2,
Ш2-1:
1 — проволочная арматура; 2 — закладная шайба’
Рис. 2. Подрельсовая часть шпалы Ш1-1
Рисунок 3
Рисунок 4
2. 2.1. Марка шпалы состоит из
двух буквенно-цифровых групп, разделенных дефисом.
Первая группа содержит обозначение типа шпалы в зависимости от конструкции рельсового скрепления:
Ш1-для раздельного клеммно-болтового скрепления КБ с болтовым прикреплением подкладки к шпале;
Ш2-для нераздельного клеммно-болтового скрепления БПУ с болтовым прикреплением подкладки или рельса к шпале.
Вторая группа указывает вариант исполнения подрельсовой площадки шпалы в соответствии с табл. 1.
2.2.2. Форма и размеры шпал должны соответствовать указанным в табл. 1 и на рис. 1- 4.
Таблица 1
Марка шпалы |
Расстояние между упорными кромками разных кондов шпалы (а), мм |
Расстояние между упорными кромками одного конца шпалы (а1), мм |
Расстояние между осями отверстий для болтов (а2), мм |
Расстояние между осью отверстия и упорной кромкой (а3), мм |
Угол
наклона упорных кромок, град. |
Направление большей стороны отверстия для болта относительно продольной оси шпалы |
Ш1-1 |
2012 |
404 |
310 |
47 |
55 |
Поперечное |
Ш1-2 |
2000 |
392 |
310 |
41 |
72 |
То же |
Ш2-1 |
2012 |
404 |
236 |
84 |
55 |
Продольное |
На кромках, примыкающих к подошве и торцам шпалы, допускаются фаски шириной не более 15. мм.
По согласованию изготовителя с потребителем допускается изготовлять шпалы, у которых расположение и размеры углублений на подошве отличаются от указанных на рис. 1, а форма и размеры вертикальных каналов для закладных болтов отличаются от указанных на рис. 2- 4.
2.2.3. Конструкции и размеры допускаемых к применению железобетонных шпал, изготовленных по ранее действовавшим стандартам и техническим условиям, даны в приложении.
2.3. Железобетонные шпалы в зависимости от трещиностойкости, точности геометрических размеров и качества бетонных поверхностей подразделяют на два сорта: первый и второй.
2.4. Шпалы второго сорта предназначены для укладки на малодеятельных линиях, станционных и подъездных путях. Поставка шпал второго сорта производится только с согласия потребителя.
Шпалы должны изготовляться из тяжелого бетона класса по прочности на сжатие В40 в соответствии с ГОСТ 26633-85.
2.5. В качестве арматуры шпал (рис. 5) применяется высокопрочная стальная проволока периодического профиля класса Вр диаметром 3 мм. Номинальное число проволок — 44. Предельные отклонения по числу проволок — 2 шт.
Для обеспечения проектного расположения проволок применяются разделительные проставки, которые могут оставаться в бетоне на торцах шпал.
2.6. Отклонения размеров шпал не должны превышать предельных значений, указанных в табл. 2.
2.7. Отклонение от прямолинейности профиля подрельсовых площадок на всей длине или ширине не должно быть более 1 мм.
2.8. Уклон подрельсовых площадок к продольной оси шпалы в вертикальной плоскости, проходящей через ось (подуклонка), должен быть в пределах от 1:18 до 1:22 для шпал первого сорта и от 1:16 до 1:24 для шпал второго сорта.
2.9. Разница уклонов подрельсовых площадок разных концов шпалы в поперечном к оси шпалы направлении (пропеллерность) не должна превышать 1:80.
2.10. Отклонения толщины защитного слоя бетона до верхнего ряда арматуры не должны превышать: для шпал первого сорта +7, — 5 мм, для шпал второго сорта + 10, — 5 мм.
Рис. 5. Размещение арматуры на торце (а) и в среднем сечении (б) шпалы
2.11. Размеры раковин на бетонных поверхностях и околов ребер у шпал не должны превышать значений, указанных в табл. 3.
2.12. В новых шпалах не допускаются:
наплывы бетона в каналах для закладных болтов, препятствующие свободной установке и повороту этих болтов в рабочее положение;
местные наплывы бетона на подрельсовых площадках;
провертывание закладных болтов рельсового скрепления в каналах шпалы при завинчивании гаек;
трещины в бетоне.
Таблица 2
Наименование размера |
Предельное отклонение, мм, для шпал |
|
первого сорта |
второго сорта |
|
Расстояние а |
± 2 |
+ 3, -2 |
Расстояние а 1 |
+ 2, -1 |
+ 3, — 1 |
Расстояния а2 и а 3 |
± 1 |
± 1 |
Глубина заделки в бетон закладной шайбы |
+ 6, -2 |
+ 6, — 2 |
Длина шпалы |
± 10 |
± 20 |
Ширина шпалы Высота шпалы |
+ 10, — 5 + 8, -3 |
+ 20, — 5 + 15, -5 |
Таблица 3
Участки поверхности шпалы |
Предельные размеры, мм |
|||
раковин |
околов ребер |
|||
Глубина |
Диаметр (наибольший размер) |
Глубина |
Длина по ребру |
|
Подрельсовые площадки Упорные кромки подрельсовых площадок |
10/15 10/15 |
10*/15* Щ**/15** |
15/30 10/10 |
30/60 20/40 |
Верхняя поверхность средней части шпалы |
10/15* |
30/45 |
15/30 |
30/60 |
Прочие участки верхней поверхности |
15/25 |
60/90 |
15/30 |
Не регламентируются |
Боковые и торцовые поверхности |
15/25 |
60/90 |
30/60 |
Не регламентируются |
* Не более трех раковин на одной площадке.
** Не более одной раковины.
Примечание. В числителе — данные для шпал первого сорта, в знаменателе — для второго.
Рис. 6. Маркировка шпалы:
1 — номер партии; 2 — товарный знак или краткое наименование предприятия-изготовителя; 3 — год изготовления; 4 — знак шпалы второго сорта
2.13. На верхней поверхности шпал штампованием при формовании должны быть нанесены товарный знак или краткое наименование предприятия-изготовителя (на каждой шпале) и год изготовления двумя последними цифрами (не менее чем у 20 % шпал партии).
В концевой части шпал краской наносят штамп ОТК и номер партии. Места нанесения маркировочных надписей указаны на рис. 6.
На обоих концах шпалы второго сорта наносится краской поперечная полоса шириной 15-20 мм (см. рис. 6).
3.1. Сдачу готовых железобетонных шпал железным дорогам производит отдел технического контроля предприятия-изготовителя, а техническую приемку шпал осуществляет инспектор-приемщик МПС.
3.2. Каждая отгружаемая партия шпал должна сопровождаться документом (паспортом) установленной формы о качестве шпал и соответствии их требованиям стандарта или технических условий. В документе указывается:
номер документа и дата;
наименование и адрес предприятия-изготовителя; марка и сорт шпал;
количество отгруженных шпал в партии; обозначение стандарта или технических условий.
Документ (паспорт) подписывают ответственный представитель предприятия-изготовителя и инспектор-приемщик МПС.
3.3. Предприятие-изготовитель должно гарантировать соответствие отгруженных шпал требованиям стандарта при соблюдении потребителем правил их эксплуатации, транспортирования и хранения. Гарантийный срок эксплуатации шпал, в течение которого изготовитель обязан устранить обнаруженные потребителем скрытые дефекты или заменить негодные шпалы, составляет 3 года со дня укладки их в путь. Исчисление гарантийного срока начинается не позже 9 мес. со дня поступления шпал потребителю.
3.4. Шпалы транспортируют в открытых полувагонах или автомобилях. Транспортирование шпал разных марок и сортов в одном полувагоне или автомобиле не допускается.
3.5. Шпалы при транспортировании и хранении должны укладываться горизонтальными рядами в рабочем положении (подошвой вниз). Между рядами шпал должны укладываться деревянные прокладки сечением не менее 50×50 мм, располагаемые по середине углублений в подрельсовых площадках шпал. По соглашению изготовителя с потребителем допускается применять деревянные прокладки сечением не менее 40×40 мм при расположении их на расстоянии 30-40 мм от упорных кромок углублений подрельсовых площадках шпал.
3.6. Погрузку шпал в полувагоны и их выгрузку следует производить пакетами по 16-32 штуки в зависимости от грузоподъемности крана. Шпалы в пакетах должны размещаться в соответствии с указаниями п. 3.5. Торцы шпал должны лежать в одной вертикальной плоскости. Во избежание нарушения пакетного расположения шпал в пути следования между пакетами устанавливают вертикальные стойки диаметром 10-15 см.
3.7. При погрузке и выгрузке шпал следует принимать меры предосторожности против их повреждений: не ударять по ним металлическими предметами, не допускать удары шпал друг о друга, не сбрасывать шпалы с полувагона, не выгружать шпалы рядами с помощью троса, так как при этом происходит повреждение кромок шпал.
3.8. Шпалы должны храниться в штабелях расположенными по маркам и сортам с соблюдением требований п. 3.5. Высота штабеля не должна быть более 16 рядов шпал. Между штабелями должны быть проходы шириной не менее 1 м.
4.1. Сборка рельсовых звеньев с железобетонными шпалами производится на производственных базах МПС на механизированной звеносборочной линии или на пути-шаблоне.
4.2. При сборке рельсовых скреплений должно соблюдаться точное взаимное расположение всех деталей. Нашпальные прокладки и металлические подкладки должны укладываться на подрельсовых площадках шпал без перекосов и смещений с точным совпадением отверстий для закладных болтов в подкладках, прокладках и шпалах. Все детали скреплений должны соответствовать утвержденным чертежам.
4.2.1. На железобетонных шпалах марки Ш1-1 с углом наклона упорных кромок подрельсовых площадок 55° следует применять нашпальные прокладки с уширенным буртиком (рис. 7, а). При отсутствии таких прокладок допускается применение нашпальных прокладок с узким буртиком (рис. 7, 6). На шпалах марки Ш1-2 и ранее выпускавшихся видах железобетонных шпал с углом наклона упорных кромок 72° применяют нашпальные прокладки с узким буртиком.
4.3. Гайки болтов промежуточных рельсовых скреплений к а железобетонных шпалах следует затягивать крутящим моментом 120-150 Н·м (12-15 кгс·м). Допускается для рельсовых скреплений типа КБ с жесткими клеммами усиленная затяжка закладных болтов крутящим моментом до 180-220 Н·м (18-22 кгс·м), а клеммных болтов — до 220-240 Н·м (22-24 кгс·м).
Рис. 7. Нашпальные прокладки:
а — с широким буртиком для шпал Ш1-1; б — с узким буртиком для шпал Ш1-2 10
Таблица 4
Температура воздуха, °С |
Минимальное электрическое сопротивление звена, Ом |
||||
длиной 25 м |
длиной 12.5 м |
||||
при погоде |
|||||
сухой |
сырой |
сухой |
сырой |
||
От 0 до + 5 |
400 |
200 |
800 |
400 |
|
От + 6 до + 10 |
300 |
150 |
600 |
300 |
|
От + 11 до + 15 |
250 |
125 |
500 |
250 |
|
От + 16 и выше |
200 |
100 |
400 |
200 |
|
4.4. Состояние инвентарных рельсов должно обеспечивать возможность содержания пути в пределах допусков, в том числе и после замены этих рельсов на рельсовые плети.
В главных путях не допускается применять инвентарные рельсы, имеющие боковой износ или уширение головки более 2 мм, кривизну в плане, искривление и смятие концов рельсов в вертикальной плоскости в сумме более 2 мм. Разница в высоте стыкуемых инвентарных рельсов не должна быть более I мм. Для этого инвентарные рельсы следует рассортировать на группы по средней величине вертикального износа головки с допуском ±0,5 мм и замаркировать.
Замена инвентарных рельсов сварными рельсовыми плетями должна выполняться в возможно короткий срок после укладки звеньев, чтобы исключить появление потайных толчков в местах стыков инвентарных рельсов. При этом должно выполняться сплошное подтягивание клеммных и закладных болтов до значений, указанных в п. 4.3.
4.5. Необходимое электрическое сопротивление между двумя рельсовыми нитями на железобетонных шпалах обеспечивается электроизолирующими деталями рельсового скрепления (втулки, прокладки) при условии их должного качества, правильной сборки и исправного состояния в пути.
В целях контроля правильности сборки и качества деталей следует периодически проводить выборочную (у 5 % звеньев) проверку электрического сопротивления собранных звеньев на базе ПМС прибором, прошедшим государственную проверку. Электрическое сопротивление между двумя рельсами одного звена не должно быть менее значений, указанных в табл. 4.
Электрическое сопротивление каждого звена измеряют дважды. Второе измерение производят сразу после первого. При втором измерении проводник, подключавшийся при первом измерении к левому рельсу, подключают к правому, а проводник, подключавшийся ранее к правому рельсу, подключают к левому. Результаты первого и второго измерений складывают и делят пополам.
Если у собранного звена сопротивление меньше значения, указанного в табл. 4 для данных погодных условий, то следует на этом звене снять один из рельсов и измерить электрическое сопротивление между двумя подкладками на каждой шпале. На тех шпалах, у которых электрическое сопротивление меньше нормативного для одной шпалы, необходимо тщательно обследовать состояние всех электроизолирующих деталей (втулок, прокладок), проверить правильность сборки скреплений и устранить причины пониженного сопротивления.
Нормативное сопротивление одной шпалы определяют как произведение бального электрического сопротивления звена при данных погодных условиях на число шпал в звене.
Пример . При температуре воздуха более 16°С и сухой погоде по табл. 4 минимальное электрическое сопротивление звена длиной 25 м при эпюре укладки шпал 1840 шт./км должно быть 200 Ом. Следовательно, нормативное сопротивление одной шпалы при их числе на звено 46 шт. должно быть 200×46=9200 Ом.
4.6. На главных путях железобетонные шпалы следует укладывать, как правило, на протяжении целого перегона. Укладка деревянных шпал на таком перегоне допускается только в кривых радиусом менее 350 м, на участках подхода к стрелочным переводам с деревянными брусьями, мостам с деревянными мостовыми брусьями, а также в стыках рельсов на уравнительных пролетах бесстыкового пути (по три шпалы с каждой стороны от стыка).
4.6.1. На мостах, имеющих балластную призму, следует применять специальные мостовые железобетонные шпалы, имеющие закладные детали для крепления контруголков или контррельсов, а при их отсутствии — деревянные шпалы.
4.6.2. Переход от железобетонных шпал к деревянным осуществляют комбинированным звеном, собранным из железобетонных и деревянных шпал. Место перехода от одного вида шпал к другому должно располагаться на расстоянии 6-6,5 м от стыка рельсов.
4.7. Звенья с железобетонными шпалами следует укладывать на выровненную поверхность балластного слоя. Допускается между подошвой шпалы в средней ее части (на длине не более чем по 25-30 см в обе стороны от оси колен) и поверхностью балласта оставлять зазор высотой до 4-5 см, предупреждающий образование поперечных трещин. Такую же поверхность балласта целесообразно делать и при проходе щебнеочистительной машины путем устройства на ней специальных планирующих устройств.
При выправке пути с применением машин ВПО-3000, ВПР-1200 и др.» а также электрошпалоподбоек, железобетонные шпалы подбивают только на протяжении по 1 м от их концов.
После выправки пути шпальные ящики должны быть заполнены балластом до уровня верха средней части железобетонных шпал.
4.8. Выправка пути с железобетонными шпалами по высоте производится с подбивкой шпал или укладкой регулировочных прокладок между рельсом и подкладкой (при бесподкладочном скреплении — между рельсом и шпалой).
4.8.1. Сплошную подбивку шпал на всем протяжении пути с одновременным удалением регулировочных прокладок производят при планово-предупредительных работах по выправке пути. Периодичность такой выправки при текущем содержании зависит от грузонапряженности линии, нагрузок от колесных пар подвижного состава на рельсы, состояния рельсов, загрязненности балластного слоя и других факторов, но не реже одного раза в 3 года.
4.8.2. В периоды между планово-предупредительными работами производят выправку пути с укладкой регулировочных прокладок. Выправку прокладками следует выполнять таким образом, чтобы общая толщина регулировочных прокладок под рельсом (кроме резиновой амортизирующей прокладки) не была более 10 мм. При достижении предельной высоты регулировочные прокладки удаляют, а путь выправляют с подбивкой шпал балластом.
4.9. Для устранения угона рельсовых плетей и уменьшения износа закладных шайб в железобетонных шпалах следует не реже двух раз в год — весной и осенью — проводить сплошное подтягивание гаек закладных и клеммных болтов. В уравнительных пролетах и на концевых участках рельсовых плетей (по 40-50 м) в периоды между сплошными подтягиваниями гаек следует дополнительно проводить подтягивание ослабших гаек закладных и клеммных болтов. Подтягивание гаек болтов до нормативного значения следует проводить также перед сплошной выправкой пути с подбивкой шпал.
Работы это сплошному подтягиванию и смазке клеммных и закладных болтов следует выполнять в плановом порядке клеммно-болтовыми машинами, путевыми моторными гайковертами или электрогаечными ключами, а подтягивание одиночных ослабших болтов при неотложных работах - торцовыми гаечными ключами.
5.1. Все новые железобетонные шпалы, поступающие на звеносборочную базу, должны быть осмотрены. При обнаружении в полученных шпалах отклонений от требований стандарта, такие шпалы должны быть забракованы. Руководство ПМС или дистанции пути должно поставить об этом в известность службу пути дороги и предъявить претензию изготовителю шпал.
5.2. В табл. 5 даны перечень и классификация дефектов и повреждений железобетонных шпал, встречающихся при их эксплуатации в пути. В таблице каждому дефекту присвоен определенный номер, дано схематическое изображение дефекта и его краткое описание при двух степенях развития, указаны основные причины возникновения дефекта и мероприятия по эксплуатации пути со шпалами, имеющими этот дефект.
Цифровое обозначение номера дефекта включает: номер группы дефектов (1-поперечные трещины и изломы, 2-продольные трещины, 3 — околы бетона, 4 — разрушение и износ бетона, 5 — повреждения закладных деталей), порядковый номер дефекта в группе и, после точки, степень развития дефекта.
5.3. Причинами возникновения дефектов шпал в эксплуатации могут быть проявление скрытых дефектов изготовления шпал, не обнаруженных при приемке шпал, а также изменение рабочих свойств шпал под действием поездных нагрузок, эксплуатационных и климатических факторов.
5.3.1. Дефекты № 22 и 41 всегда являются прямым следствием недостатков изготовления шпал. При обнаружении таких дефектов в период действия гарантийного срока на шпалы руководству дистанции пути или службы пути дороги следует предъявить претензию изготовителю шпал.
5.3.2. Дефекты № 11, 12, 21, 31, 32, 42, 51, 52, 53, если они не были обнаружены до сборки звеньев и шпалы с ними не были своевременно забракованы, следует относить к эксплуатационным дефектам, включая в эксплуатационный период также транспортирование шпал, сборку и укладку звеньев, хотя на появление этих дефектов могут влиять также недостатки изготовления шпал.
5.4. Оценку состояния шпал следует производить визуально и лишь в необходимых случаях измерять дефекты шпал методами, указанными ниже, после удаления с поверхности шпал загрязнителей или слоя балласта.
5.4.1. При оценке состояния шпал по трещинам во внимание принимают только такие трещины, которые видны в бетоне невооруженным глазом (обычно их раскрытие более 0,2 мм) и направлены либо поперек, либо вдоль шпалы. Беспорядочно расположенные тонкие усадочные трещины в бетоне во внимание не принимают. При необходимости ширину раскрытия трещин определяют с помощью измерительной лупы, щупа пли пластинки, имеющей толщину, равную предельной ширине раскрытия трещины.
5.4.2. Длину окола бетона измеряют линейкой по ребру шпалы, поврежденному околом. За глубину окола принимают наибольшее расстояние от ребра линейки, приложенной к ребру шпалы, до края окола на примыкающих поверхностях шпалы.
5.4.3. Глубину выработки бетона на подрельсовой площадке шпалы определяют после снятия сломанной подкладки и изношенной нашпальной прокладки измерением наибольшего зазора между поверхностью площадки и ребром приложенной к ней линейки.
Таблица 5
Номер дефекта |
Степень развития |
Краткое описание дефекта |
Схематическое изображение дефекта |
Основные причины появления и развития дефекта |
Указания по дальнейшей эксплуатации пути со шпалами, имеющими дефект. Ремонтопригодность шпал. |
11.1. |
Первая |
Поперечные трещины с раскрытием до 1 мм в подрельсовой части шпалы. |
|
Плохое содержание рельсовых стыков: просадки, увеличенные зазоры, сбитые концы или разная высота рельсов. Недонапряжение или смещение арматуры при производстве шпал. |
Выправить путь в стыках и подбить шпалы. Заменить негодные уравнительные рельсы или рельсы звеньевого пути. Провести шлифовку головки рельсов шлифовальным поездом. |
11.2. |
Вторая |
Излом шпалы в подрельсовой части с разрушением бетона, раскрытием поперечной трещины или разрывом арматуры. |
|||
12.1. |
Первая |
Поперечные трещины с раскрытием до 1 мм в средней части шпалы |
Неправильное опирание шпал на балласт после укладки звеньев, очистки щебеночной призмы или в результате длительного отсутствия выправки пути в эксплуатации: опирание шпал серединой или, наоборот, только концами при провисшей вниз на большой длине середине шпалы (трещины снизу) |
Провести сплошную выправку и подъемку пути с подбивкой шпал по всей длине подрельсовых частей. Устранить провисание середины шпал. Засыпать шпальные ящики балластом. Проверить планирующие устройства у путевых машин для исключения подпора шпал в середине. |
|
12.2. |
Вторая |
Излом шпалы в средней части с разрушением бетона, раскрытием поперечной трещины или разрывом арматуры. |
|||
21.1. |
Первая |
Продольная трещина с раскрытием до 3 мм, проходящая через отверстия для закладных болтов или через дюбели. |
|
Передача сил угона рельсов на прикрепителе при слабой их затяжке. При шурупном скреплении — удары по шурупу (забивка), недостаточный диаметр отверстия в дюбеле для шурупа, разбухание древесины дюбеля при некачественной его пропитке. |
Провести сплошное подтягивание закладных болтов. При повторном применении шпал с деревянными дюбелями соблюдать правила завинчивания шурупов в дюбели |
21.2. |
Вторая |
Раскол шпалы по сквозной продольной трещине с раскрытием более 3 мм, проходящей через отверстия для закладных болтов или через дюбели. |
|||
22.1. |
Первая |
Продольная трещина с раскрытием до 3 мм, проходящая через арматурные проволоки на торцах и в середине шпалы. |
Развитие микротрещин в бетоне, возникших из-за недостаточной прочности бетона, применения исходных материалов, непригодных для шпального бетона, неправильного режима термообработки бетона. Коррозия арматуры из-за недостаточной толщины и плотности защитного слоя бетона. |
При обнаружении дефекта в период действия гарантийного срока на шпалы — предъявить претензию изготовителю. При осмотрах пути установить особое наблюдение за такими шпалами. |
|
22.2 |
Вторая |
Раскол шпалы по сквозной продольной трещине проходящей через арматурные проволоки |
|||
31.1 |
Первая |
Окол бетона на упорной кромке углубления в подрельсовой площадке длиной (l) от 40 до 100 мм и глубиной (h) от 10 до 20 мм |
Отсутствие, недостаточная толщина или неправильное расположение деревянных прокладок между рядами шпал при их складировании или транспортировании. Удары по шпалам. Плохая рихтовка пути. Ослабление затяжки закладных болтов. Износ, буртиков нашпальных прокладок |
Соблюдать правила складирования и транспортирования новых и старогодных шпал. Отрихтовать путь и выправить кривые по стрелам. Провести сплошное подтягивание гаек закладных болтов. Заменить изношенные нашпальные прокладки |
|
31.2 |
Вторая |
Окол бетона по всей длине (l) высоте (h) упорной кромки углубления в подрельсовой площадке |
|||
32.1 |
Первая |
Околы бетона на ребрах и плоскостях шпалы (кроме упорных кромок) глубиной (h) не более 60 мм с обнажением арматуры на длине (l) не более 100 мм |
Удары по шпалам при их транспортировании, погрузке, выгрузке, сборке и укладке звеньев, выполнении путевых работ, падении на путь тяжелых предметов. Местные перенапряжения бетонных кромок шпал при опирании их на опоры с очень малой поверхностью контакта |
При наличии шпалоремонтных мастерских околы бетона могут быть заделаны полимерцементными растворами и отремонтированные шпалы использованы в малодеятельных главных или станционных путях |
|
32.2 |
Вторая |
Крупные околы бетона на ребрах и плоскостях шпалы глубиной (h) более 100 мм, обнажающие арматуру на длине (l) более 300 мм |
|||
41.1 |
Первая |
Множество раковин на поверхности бетона. Начальное разрушение бетона (шелушение) в пределах толщины защитного слоя бетона над арматурой |
Недостаточные морозостойкость и долговечность бетона вследствие использования непригодных для шпального бетона исходных материалов, неправильного подбора состава бетонной смеси и плохого уплотнения ее при изготовлении шпал |
При обнаружении дефекта в период действия гарантийного срока предъявить претензию изготовителю шпал. Установить особое наблюдение за дефектными шпалами при осмотрах пути |
|
41.2 |
Вторая |
Полное разрушение структуры бетона на отдельные составляющие (щебень, раствор) с обнажением арматуры |
|||
42.1 |
Первая |
Местная выработка (износ) бетона на глубину (f)до 2 мм на подрельсовых площадках в местах опирания подкладок или рельсов |
Истирание бетона сломанными подкладками после износа нашпальных прокладок и ослабления затяжки закладных болтов |
Заменить сломанные подкладки и изношенные капитальные прокладки, затянуть закладные болты. При наличии шпалоремонтных мастерских возможен ремонт подрельсовых площадок шпал нанесением на них полимерцементных растворов для последующего использования отремонтированных шпал в малодеятельных главных или станционных путях |
|
42.2 |
Вторая |
Неравномерная выработка (износ) бетона глубиной (f) более 5 мм на под рельсовых площадках в местах опирания сломанных подкладок |
|||
51.1 |
Первая |
Смятие материала (древесины) дюбеля с образованием вокруг шурупного отверстия зазора более 5 мм |
Смятие материала дюбеля при действии на шуруп горизонтальных, поперечных и продольных сил. Износ нарезки в дюбеле при частых перешивках колеи. Старение материала дюбеля. Растрескивание и загнивание древесины дюбеле при плохой пропитке. Усталость шурупа при передаче на него продольных и боковых сил |
Усиленный контроль за шириной рельсовой колеи. Замена изношенных и изогнутых шурупов. При наличии шпалоремонтных мастерских — ремонт деревянных дюбелей с извлечением сломанных шурупов и заливкой шурупных отверстий полимерным составом для использования отремонтированных шпал в малодеятельных и станционных путях |
|
51.2 |
Вторая |
Разрушение материала дюбеля, при котором шуруп при завинчивании его в дюбель провертывается. Излом шурупа в дюбеле |
|||
52.1 |
Первая |
Провертывание закладного болта при завинчивании гайки (завинчивание выполнимо при подтягивании болта вверх) |
Окол бетонных выступов ниже закладной шайбы, удерживающих болт от провертывания в начале завинчивания гайки |
Приподнять закладной болт вверх, чтобы его квадратный подголовок вошел в отверстие в закладной шайбе, и удерживая его специальной вилкой, в этом положении завинтить гайку |
|
52.2 |
Вторая |
Невозможность завинчивания гайки закладного болта из-за провертывания этого болта в отверстии шпалы даже при подтягивании болта вверх |
Износ продольных кромок отверстия в закладной шайбе до размера, превышающего диагональ подголовка закладного болта (30 мм) |
При наличии шпалоремонтных мастерских — заливка болтов в отверстиях полимерным составом для использования таких шпал в малодеятельных станционных путях |
|
53.1 |
Первая |
Загрязнение каналов в шпалах засорителями, затрудняющими извлечение и установку закладных болтов |
Заполнение каналов для закладных болтов засорителями, особенно в местах выплесков при очень загрязненном балласте, а также сыпучими грузами |
Устранить выплески. Провести чистку щебеночной баластной призмы. Применять изолирующие втулки скреплений, плотно закрывающие отверстия в подкладках сверху. При наличии шпалоремонтных мастерстких возможна прочистка каналов в шпалах |
|
53.2 |
Вторая |
Невозможность извлечения из шпалы поврежденных закладных болтов вследствие затвердения засорителей в каналах шпалы |
5.4.4. При оценке разрушения бетона шпалы (дефект № - 41) следует отличать его от окола бетона (дефект № 32). При околе бетон плотный, края окола резко очерчены. При разрушении бетона в начальной стадии его повер хность покрыта сеткой мелких беспорядочных трещин или множеством ракови н. В дальнейшем бетон рассыпается на отдельные его составляющие — щебень, куски цементного камня и раствора. Края зоны разрушения бетона резко не очерчены.
5.4.5. Смятие материала (древесины) дюбеля определяют после снятия подк ладки, нашпальной прокладки и вывинчивания шурупа. При необход имости величину смятия определяют как разность между наибольшим ( d 1 ) ч наименьшим ( d 2 ) размерами шурупного отверстия, измеренными по диаметру у самого верха дюбеля. О разрушении материала дюбеля судят по провертыванию шурупа при завинчивании его в дюбель. Наличие обломка нижней части шурупа в дюбеле определяют погружением щупа в отверстие дюбеля.
5.4.6. Провертывание закладного болта в шпале может быть следствием окола кромок бетонных выступов ниже закладной шайбы или износа отверстия в закладной шайбе. В первом случае можно завинтить гайку болта, если приподнять его вверх так, чтобы квадратный подголовок болта вошел в отверстие в шайбе, и поддержать его в этом положении. Во втором, случае, при износе отверстия в шайбе до размера в поперечном направлении более 30 мм. что превышает размер по диагонали квадратного подголовка, подтягивание болта вверх не дает результата и затянуть гайку болта нельзя.
5.5. В главных путях шпалы с дефектами первой степени допускается оставлять до очередного капитального ремонта пути, при котором такие шпалы следует заменить. В станционных и подъездных путях шпалы с дефектами первой степени замене не подлежат.
5.5.1. Шпалы с дефектами, превышающими первую степень, но меньшими второй степени, в главных и станционных путях следует заменять при очередном подъемочном или среднем ремонтах пути в зависимости от состояния шпал.
5.5.2. Шпалы с дефектами второй степени, лежащие во всех видах путей по две и более подряд, должны заменяться при текущем содержании пути в возможно короткие сроки. Допускается одиночно лежащие шпалы с дефектами второй степени оставлять в пути до очередного подъемочного или среднего ремонта пути, при котором такие шпалы должны быть заменены.
6.1. При капитальном ремонте пути все железобетонные шпалы должны обследованы и в зависимости от их состояния отнесены либо к одной из двух групп годности, либо к негодным шпалам с соответствующей дополнительной маркировкой.
1-й группе годности относят шпалы, не имеющие дефектов.
Ко 2-й группе годности относят шпалы с дефектами первой степени развития (см. табл. 5).
К негодным относят шпалы с дефектами второй степени развития (см. табл.5).
Шпалы 1-й группы годности дополнительной маркировке не подлежат. Шпалы 2-й группы годности обозначают поперечной полосой, наносимой средней части шпалы. Негодные шпалы обозначают двумя поперечными полоcaми, наносимыми краской в средней части шпалы.
6.2. Старогодные шпалы 1-й группы годности могут повторно применяться во всех главных, станционных и подъездных путях в соответствии с указаниями пп. 1.1 и 1.8.
6.2.1. Старогодные шпалы 2-й группы годности могут повторно применяться только в станционных (кроме главных в пределах станции) и подъездных путях.
6.2.2. Негодные шпалы повторной укладке в действующие пути не подлежат.
6.3. При выполнении капитального ремонта пути с полной разборкой на базе снятой путевой решетки с железобетонными шпалами обследование и сортировка шпал по группам годности производятся до сборки новой решетки со старогодными шпалами.
6.3.1. Если снятую при капитальном ремонте пути рельсошпальную решетку с железобетонными шпалами укладывают повторно без разборки в главный путь, то в ней до укладки должны быть заменены все обнаруженные шпалы 2-й группы годности и негодные шпалы. Если эту решетку укладывают повторно без разборки в станционный или подъездной путь, то в ней до укладки должны быть заменены только негодные шпалы.
6.3.2. При выполнении капитального ремонта главного пути без снятия рельсошпальной решетки в ней должны быть заменены все обнаруженные шпалы 2-й группы годности и негодные шпалы.
6.4. Негодные железобетонные шпалы могут использоваться для железнодорожных обустройств, а излишние — реализовываться по ценам, установленным на дороге, для нужд дистанций пути, ПМС и других организаций железнодорожного транспорта, а также нетранспортных организаций.
6.5. При организации на производственных базах ПМС специализированных мастерских по ремонту железобетонных шпал, имеющих дефекты, поддающиеся ремонту (см. табл. 5), часть негодных шпал может быть восстановлена и использована для укладки на станционных и подъездных путях. Ремонт шпал выполняют в соответствии с Техническими указаниями по ремонту железобетонных шпал,
6.6. Шпалы с дефектами, превышающими первую степень развития, но меньшими второй степени развития, могут быть выборочно использованы в малодеятельных станционных путях.
7.1. Состояние железобетонных шпал в пути проверяют сплошь ежегодно осенью на 1 ноября при комиссионном осмотре пути. Данные проверки вносят в отчетную форму ПО-6. По результатам проверки дистанция пути разрабатывает план замены шпал по километрам и станционным путям с указанием видов ремонта, при которых эта замена будет производиться.
7.2. Назначение железобетонных шпал к замене производит лично дорожный мастер, руководствуясь указаниями раздела 5.
Подлежащие замене шпалы отмечают на шейке рельсов с внутренней стороны правой нити по счету километров известью круглым пятном диаметром около 50 мм. После замены шпал отметки с шейки рельсов должны быть смыты.
7.3. При капитальном ремонте пути со снятием рельсошпальной решетки учет старогодных шпал выполняется следующим порядком.
7.3.1. Перед началом ремонта на основании натурного осмотра составляется акт по форме ПУ-81 о количестве материалов верхнего строения пути на данном участке, в том числе железобетонных шпал с выделением числа негодных шпал, подлежащих замене.
7.3.2. Начальник ПМС при производстве работ обязан обеспечить вывоз полностью всех снимаемых с пути материалов, в том числе железобетонных шпал в звеньях и одиночных, оставшихся на перегоне после снятия рельсошпальной решетки.
7.3.3. На базе ПМС после сортировки и штабелирования старогодных железобетонных шпал составляется акт о числе и состоянии шпал.
7.3.4. Сортировку шпал, их хранение и учет на звеносборочных базах осуществляют под контролем специального работника, назначаемого начальником ПМС, который отвечает за правильную сортировку и хранение шпал. Учет старогодных шпал на звеносборочных базах (с указанием данных о результатах сортировки шпал) ведут в специальном журнале.
7.4. Указанный выше порядок сортировки старогодных железобетонных шпал должен осуществляться и при выполнении работ силами дистанций пути.
7.5. Все изъятые из пути железобетонные шпалы приходуются по актам рассортировки, составляемым при окончании работ по капитальному, среднему и подъемочному ремонтам пути, а при текущем содержании пути — ежемесячно.
7.6. Железобетонные шпалы, лежащие в пути, учитываются в книге учета по форме ПУ-5. Кроме этого, дефектные железобетонные шпалы, лежащие в пути, учитываются по форме ПУ-1.
7.7. Учету подлежат железобетонные шпалы на всех путях, включаемых в развернутую длину главных и станционных путей, а также на путях специального назначения и подъездных. Учет ведут раздельно: на главных путях — по каждому километру, на станционных путях — по протяжению станционных путей и отдельно по подъездным путям.
7.8. При учете лежащие в пути железобетонные шпалы группируют по типу и сроку службы: 1-го срока (т.е. новые) и 2-го срока (т.е. переложенные). Если на отдельных километрах главных путей или на станционных путях имеются шпалы разных типов или сроков службы, то для каждых из них в шпальной книге отводят самостоятельные строки. В этих случаях повторяют в первой графе номера километров и станционных путей.
7.9. Данные о числе уложенных и изъятых за отчетный год железобетонных шпал должны соответствовать данным сдачи километров для производства работ и приемки выполненных работ (форма ПУ-48), а также графикам по текущему содержанию и оценке состояния пути и путевых устройств (форма ПУ-74).
7.10. На основании актов осмотра железобетонных шпал по состоянию на 1 ноября дорожный мастер представляет начальнику дистанции пути не позднее 5 ноября данные по отчетной форме ПО-6. Начальник дистанции пути не позднее 10 ноября направляет сводный отчет по дистанции в отдел статистического учета и отчетности, управления дороги, а последний в сводном по дороге виде не позднее 20 ноября представляет его в Управление статистического учета и отчетности МПС.
Тип (марка) шпалы |
Тип скрепления |
Номер стандарта или ТУ |
Характерные отличительные особенности конструкции данной шпалы |
Сведения о времени выпуска и заводах — изготовителях данных шпал |
Сферы повторного применения шпал данного типа |
ШС-1, ШС-1у |
КБ |
ГОСТ 10629-78 |
По форме и основным размерам идентична шпале Ш1-2 по ГОСТ 10629-88 (см. рис. 1 и 3). Угол наклона упорных кромок 72°. Размеры: a = 2000 mm , a1 = 392 мм, а2 = 310 мм, а3 — 41 мм |
Основной вид шпал, выпускавшихся всеми заводами ЖБШ в период с. 1978 по 1986 г. |
В соответствии с указаниями разделов 1 и 6 |
ШС-1у |
КБ |
ТУ 21-33-38-86 |
По форме и основным размерам идентична шпале Ш1-1 по ГОСТ 10629-88 (см. рис. 1 и 2). Угол наклона упорных кромок 55°, Размеры: а = 2012 мм, а1 =404 мм, a 2 = 330 мм, а3 = 47 мм |
Выпускались большинством заводом ЖБШ в период с 1986 по 1989 г. |
В соответствии с указаниями разделов 1 и 6 |
ШС-2, ШС-2у |
БП и ЖБР |
ГОСТ 10629-78 |
По форме и основным размерам идентична шпале ШС-1 (ШС-1 у), отличается расположением болтовых отверстий. Размеры: а = 2,000 мм, а1 = 392 мм; а2 = 244 мм, а3 = 74 мм |
Выпускались Киевским экспериментальным заводом ЖБШ в 1970-х годах крупными партиями для опытных участков большого протяжения |
При наличии рельсовых скреплений типов БП и ЖБР в соответствии с указаниями раздела 6 |
С-56-2 |
КБ |
ГОСТ 10629-73. ГОСТ 10629-63, ВСН 60-61 |
По форме и основным размерам соответствует шпале Ш1-2 по ГОСТ 10629-88 (см. рис. 1 и 3), но отличается меньшей глубиной выемки в подрельсовьгх площадках (15 мм). Угол наклона упорных кромок 72°. Размеры: а = 1993 мм, а1 = 384 мм, а 2 =310 мм, а3 = 37 мм |
Основной вид шпал. выпускавшихся всеми заводами ЖБШ в период с 1963 по по 1980 г, Кременчугским заводом ЖБШ в 1966-1973 гг. выпускались такие же шпалы, длиной. 260. см.. |
В соответствии с указаниями раздела 6 |
С-56-3 |
ЖБ |
ГОСТ 10629-71, ГОСТ 10629-63, ВСН 60-61 |
По форме и основным размерам соответствует шпале С-56-2, но отличается конфигурацией подрелъсовой площадки с углублениями для пружинных клемм и размещением болтовых отверстий. Размеры: а = 1934 мм, a1 — 332 мм, а2 — 210 мм, а3 = 61 мм |
Выпускались Бесланским щебеночношпальным заводом МПС в период с 1961 по 1984 г |
При наличии скреплений ЖБ — линии грузонапряженностью до 10 млн. т км брутто/км в год, станционные и подъездные пути. Кривые радиусом более 600 м |
С-56, С-56-у |
К2 |
ВСН 60-61 |
По форме и основным размерам соответствует шпале С-56-2, но отличается отсутствием углублений в подрельсовых площадках и наличием деревянных дюбелей для шурупного прикрепления подкладок (по 2 дюбеля на каждой подрельсовой площадке) |
Изготовлялись в 1956 — 1966 гг. Киевским, Коростенским, Челябинским, Сергелийским, Алмазнянским, Староконстантиновским заводами ЖБШ |
При наличии скреплений К2 — линии с грузонапряженностью до 10 млн. т км брутто/км в год, станционные и подъездные пути |
Шпала деревянная пропитанная тип 1, 2: срок службы, сколько весит, размер по ГОСТу
Ключевая часть ж/д пути – это опорные элементы: их укладка должна проходить по всем нормам, жизненно важно правильно их выбрать, а для этого нужно знать их особенности. Поэтому сегодня расскажем о шпале деревянной пропитанной, тип 1, 2: ее размеры, ГОСТ, срок службы и другие технические характеристики будут рассмотрены подробнейшим образом. Зачем? Чтобы вы понимали, чем один вид отличается от другого, как эксплуатировать, чтобы они служили максимально долго, не требуя замены.
Содержание
- Классификация деревянных шпал по типам
- Применение и размеры шпалы деревянной пропитанной типа 1
- Размеры и применение шпалы деревянной пропитанной типа 2
- Технические условия
- Ремонт
- Методики обработки
- Фактор влажности
- Отклонения, которые допускаются
- Стандартизованные размеры
- Габариты брусьев для стрелочных переводов и критерии параметров их соответствия
- Мостовые брусья: специфика стандартизации
Сразу отметим, что такие конструкции до сих пор традиционно используются на дорогах, оставаясь актуальными даже несмотря на наличие более прочных железобетонных. Все дело в материале их исполнения: хвойные породы (сосна, кедр, лиственница, пихта, ель) и даже береза значительно легче бетонных аналогов, в результате чего различные элементы ВСП не расползаются под воздействием динамических нагрузок, а при необходимости их проще поменять. Колея сохраняет структуру, необходимую для безопасного движения транспорта. Кроме того, их цена ниже. А для предохранения от влияния осадков и разрушения насекомыми-короедами их покрывают специальными составами.
Они подразделяются на следующие группы, в зависимости от назначения:
Для рельсовых ж/д линий первого-второго класса; допустим и третий, если его годовая грузонапряженность больше 5 миллионов т/км и/или локомотивы едут по ним со скоростью выше 100 км/ч.
Для подъездных, приемоотправочных (станционных), сортировочных линий, а также для магистралей четвертого класса.
Для малодеятельных, маневрово-вывозных и прочих колей пятого класса.
Рассматриваемые нами опорные элементы используются в первом и во втором случае соответственно, а значит их геометрия и эксплуатационные характеристики должны быть строго стандартизированы.
Используется для укладки самых ответственных участков – главных Ж/Д-путей, испытывающих максимальные нагрузки, – и поэтому должна быть повышенной прочности, что отражается как на ее габаритах, так и на ее цене – она стоит дороже других вариантов, так как материала на ее изготовление уходит больше.
а) обрезная;
б) полуобрезная;
в) необрезная.
Плотность шпалы деревянной пропитанной (типа 1), размеры, вес
Ее масса составляет 85 кг, она на 5 кг тяжелее той, что 2 вида (которую мы подробно рассмотрим ниже). Эту разницу как раз и обеспечивает увеличенная на 2 см ширина. В результате повышенная нагрузка на грунтовую подушку не становится критичной, а вот избежать деформаций помогает.
Именно такая геометрия была проверена на практике и поэтому до сих пор указывается в качестве актуальной в межгосударственных стандартах.
Отдельного внимания заслуживают те параметры, которые не подпадают под стандартные ДхШхВ, но все равно являются достаточно важными. Это:
Параметр | Показатель, мм | ||
Длина | 2750 ± 20 | ||
Ширина по пласти | |||
Нижняя | Верхняя | 250-255 | 180 и 210 |
Подъем | 180 |
Благодаря такому соотношению геометрии они и способны выдерживать серьезные воздействия в течение длительного времени, не испытывая деформаций.
Шпалы деревянные, пропитанные по ГОСТ 78-2004 и 78-89, являются настоящей классикой для Ж/Д-проектирования. Древесина для их производства – это преимущественно хвойные породы: уже упомянутая сосна, как самый распространенный и доступный по цене вариант, а также ель, пихта, реже лиственница, – но возможно исполнение из березового массива.
Могут быть как обрезными (полуобрезными), так и нет, но все три варианта укладываются на широких путях, преимущественно главных, на которых требования к качеству опорных конструкций самые высокие.
При должной прочности отличаются легкостью (по сравнению с ЖБ-элементами ВСП). Еще одно их практическое преимущество – универсальность: рассчитаны на все классы железных дорог, поэтому они актуальны вот уже 100 лет и не собираются сдавать своих позиций.
Так как шпалы, пропитанные креозотом, весом в 85 кг достаточно технологичны в эксплуатации, их удобно менять, а переделывание полотна не вызывает проблем, они продолжают быть задействованы на ответственных ж/д линиях. Свою роль здесь играет и упругость материала: сосна, ель или другая порода, из которой может быть выполнен брус, хорошо переносит динамические воздействия и не просаживается в областях стыка.
При ремонте для скрепления с рельсом требуется минимум элементов: пара подкладок и десяток костылей (в общем случае). Поэтому чинить поврежденные участки можно по шаблону – быстро и при этом качественно.
В числе минусов – сравнительно небольшой ресурс (в среднем 15 лет) и склонность к растрескиванию. Чтобы предотвратить появление дефектов, можно набивать по бокам специальные пластины.
Похожие новости
Размеры и применение шпалы деревянной пропитанной типа 2Используется для укладки на подъездных и станционных линиях, то есть на не самых ответственных объектах. Поэтому тоньше, если сравнивать ее с первым видом, следовательно, и стоит дешевле. Материал исполнения не влияет на конечную цену, так как в любом случае представляет собой одну из вышеназванных пород – ель, сосна, береза, пихта или лиственница – точно так же предварительно просушенную и покрытую тем же защитным составом от влаги и микроорганизмов.
а) обрезная;
б) полуобрезная;
в) необрезная.
Размеры и масса шпалы деревянной пропитанной типа 2
Ее вес равняется 80 кг, она на 5 кг легче той, что 1 вида – именно за счет уменьшенной на 2 см ширины, которая никак не снижает надежность или долговечность использования, а также не нагружает грунтовую подушку. Так как укладывается на линиях с не самой большой грузонапряженностью, не испытывает настолько серьезных нагрузок, чтобы возникали деформации. Проще говоря, таких габаритов хватает, что уже было доказано в течение десятилетий практики.
По аналогии с предыдущим вариантом отдельно приводим параметры, не подпадающие под соотношение ДхШхВ, но в значительной степени определяющие эксплуатационные свойства. Это, опять же:
Параметр | Показатель, мм | ||
Длина | 2750 ± 20 | ||
Ширина по пласти | |||
Нижняя | Верхняя | 230-235 | 150 и 195 |
Подъем | 160 |
Геометрия опорных брусьев регламентирована межгосударственным стандартом 78-89.
Внимание, вес шпалы деревянной пропитанной Б/У будет несколько отличаться от новой – из-за износа, от степени которого и зависит разница (обычно она не превышает нескольких десятков грамм, поэтому не может считаться существенной).
Выпускается согласно требованиям межгосударственного стандарта 78-89 (78-2004) в одном из трех вариантов исполнения: бывает обрезной, полуобрезной, необрезной. Материал для изготовления – хвойные породы (массивы уже упомянутых сосны, ели, пихты или лиственницы), либо береза.
Находит самое активное применение в создании главных Ж/Д-колей третьего-четвертого класса.
Кроме того, шпалы железнодорожные деревянные пропитанные длиной 2750 мм и 230 мм шириной, становятся надежной основой при строительстве путей сортировки и приема-отправки на подъездных участках и станциях, если эти места отличаются достаточно интенсивным характером эксплуатации.
Согласно межгосударственному стандарту 78-2004:
Расположение нижней и верхней пластей – взаимно параллельное, с допусками строго в рамках заданных норм по ДхШ.
Пропилы торцов – только перпендикулярно продольной оси, со скосом, не превышающим 20 мм по толщине.
При производстве необходимо очистить обзольные места от луба и/или коры.
Закомелистость и сучки нужно срезать, не допуская зарубов и запилов по верхней стороне или делая их не шире 40 мм и не глубже 20 мм в других случаях.
Шпалы, пропитанные ултаном или другим средством по ГОСТам 20022.0 и 20022.5, должны быть предварительно защищены от растрескивания – способом, принятым у производителя и соответствующим общей инструкции по содержанию элементов ВСП.
Маркировка обязана быть явной и четкой и представлять собой клеймление или обозначение краской на торце.
Может осуществляться без снятия опорных конструкций с пути, в этом случае:
Изношенные части удаляются, заусенцы зачищаются, после чего места обработки покрываются каменноугольным маслом (или другим подходящим составом).
На время перешивок устанавливаются втулки при шурупном стыке или пластины-закрепители – при костыльном.
Трещины и отверстия от элементов крепежа также защищаются от влаги и вредителей.
На торцах нижняя пласть армируется П-образными скобами (их нужно 6 штук или больше).
Шпалы железнодорожные деревянные пропитанные антисептическими средствами отработанные снимаются с колеи и заменяются. Непригодными к дальнейшей эксплуатации они считаются тогда, когда их повреждения превышают допуски и/или когда они лежат подряд в количестве от 3 штук. До их замены необходимо ограничить скорость движения по участку до минимально возможной.
Представляют собой несколько схем воздействия на конструкцию давлением (Д) и вакуумом (В). Актуальный сегодня вариант – Д-Д-В:
Для достижения нужной глубины проникновения порода предварительно накалывается.
Заготовки помещаются в камеру, из которой откачивают воздух.
Затем туда заливается маслянистый состав.
Средство пропитывает поры древесины.
Завершающим этапом становится просушка.
Чтобы предохранить массив от гнили, применяют следующие жидкие составы:
Креозотный – дистиллят каменного или древесного угля дегтярной смесью. Пропитка дешевая, однако крайне ядовитая. Дерево после нее чернеет.
Элемсепт – включает в себя оксидные соединения, содержащие в составе медные, хромовые и мышьяковые выключения. Менее ядовит, дает брусу светлый оттенок зеленого.
ЖТК – расшифровывается как жидкость термоконденсационная. Хотя и результат перегонки нефти, токсичных паров практически не выделяет. Точного состава в открытом доступе нет. Древесину практически не окрашивает.
Ултан – средство на водной основе. Хорошо проникает внутрь массива, придавая ему зеленый цвет. Губителен для вредителей, питающихся древесиной. Для человека и животных в целом безопасен.
По умолчанию шпала деревянная пропитанная типа I, II изготавливается из массива, содержащего до 22% влаги. Если же данный показатель выше, в габариты конструкции должны быть заложены припуски на усушку. Поэтому фактическая ДхШхВ готового изделия может несколько отличаться от указанной в нормативных документах.
Межгосударственные стандарты подразумевают возможность некоторых погрешностей при производстве – по следующим параметрам:
длина – ± 20 мм,
толщина – 5 мм,
подъем боковых сторон,
ширина пластей,
отступы между болтами,
отклонения от оси.
Геометрические характеристики опорных конструкций 1 и 2 типа мы привели в таблицах выше (а также рассмотрели, сколько весит шпала железнодорожная деревянная пропитанная – напоминаем, 85 и 80 кг). Поэтому сейчас давайте взглянем на третью категорию.
а) обрезная;
б) полуобрезная;
в) необрезная.
Параметр | Показатель, мм | ||
Длина | 2750 ± 20 | ||
Ширина по пласти | |||
Нижняя | Верхняя | 230 ± 5 | 140-190 |
Подъем | 160 |
В конструкции ВСП есть еще один важный элемент, который также должен отвечать ряду нормативов – предлагаем обратить на него внимание.
Отметим, что как и обычные опоры, они могут использоваться:
На главных (магистральных) линиях первой и второй категории, а также третьей, если скорость движения по таким колеям превышает 100 км/ч, а грузонапряженность больше 50 млн т/год.
На основных путях II-IV класса, на интенсивно эксплуатируемых подъездных, на точках сортировки и приемоотправки.
На малодеятельных, станционных, маневрово-вывозных колеях.
Показатель влажности идентичный: нормой признаны 22%, если же он выше, следует предусматривать допуск на усушку. Цифровые значения выпуска регламентированы межгосударственными стандартами 6782.1-75 и 6782.2-75.
Для наглядности сведем их в таблицу:
Параметр | Показатель, мм | ||
для I | для II | для III | |
Ширина | |||
По верхней пласти | 200 или 220 | 175 и 220 | 175 и 200 |
По нижней | 260 | 250 | 230 |
По частям без пропилов | 300 | 280 | 260 |
Толщина | 180 ± 5 | 160 ± 5 | |
Высота боковой стороны | 150 | 130 |
Если тот же вес одной шпалы железнодорожной деревянной пропитанной типа 1, 2, по ГОСТ 78-2004, отличался в зависимости от вида опорной конструкции, но был строго определен – либо 85, либо 80 кг, – то в данном случае есть не конкретная цифра, а их диапазон, причем достаточно широкий.
Варианты исполнения могут быть от 3 до 5,5 м, с шагом в 0,25 м и допуском в ± 0,02 м.
Изготавливаются из тех же пород, что и уже рассмотренные элементы, но должны быть прямоугольной формы, одного из следующих видов сечения:
или 220 х 240 мм;
или 220 х 260 мм.
Длина обоих одинакова и составляет 3250 мм, хотя критические отклонения уже могут различаться. По отдельной договоренности с клиентом производитель может выпустить опорные брусья 220 х 280 или 240 х 300 мм. Но допустимый уровень влажности у каждого по умолчанию 20%, а не 22%.
Альтернатива деревянным: эти конструкции предварительно напряженные и укладываются на магистральных линиях – для рельсов Р-50, Р-65, Р-75. Разделяются по нескольким показателям, в числе которых:
способ крепления;
вид арматуры;
уровень исполнения;
качество электроизоляции.
Итак, как же наша такая опора соединяется с направляющими? Возможны 3 варианта:
Ш1 – раздельно, с фиксацией подкладки болтами;
Ш2 – уже нераздельно;
Ш3 – без использования прокладки.
Чтобы было проще сравнивать, представлены в формате таблицы:
Значение | Показатель, мм | ||||||
Ш1 | Ш2 | Ш3 | |||||
Крайние точки между кромками | |||||||
Упорными | Концевыми | 2016 | 406 | 2016 | 406 | 1966 | 359 |
Подъем в сечении | |||||||
Подрельсовое | Среднее | 193 | 145 | 193 | 145 | 193 | 145 |
ДхШ при этом фиксированные – 2700 на 300 мм. Подобная геометрия обеспечивает приемлемую безопасность при прохождении транспорта даже на высокой скорости.
Совпадения, а также различия с железобетоннымиДля шпалы деревянной пропитанной, средний срок службы которой составляет 15 лет, при хорошем уходе и не особенно интенсивном использовании его можно продлить до 20 лет. У ЖБ-конструкций ресурс значительно выше и достигает 45-50 лет, при том, что за их состоянием не нужно столь пристально следить.
Выполненные из массива сосны, пихты, ели (и других пород) опорные элементы верхнего строения пути значительно легче – 80-85 кг против, как минимум, 270 кг. Они создают меньшую нагрузку на подушку и поэтому используются на слабых грунтах. Кроме того, они обходятся дешевле при производстве, а значит и стоят меньше. Плюс, их не так сложно утилизировать. Еще одно различие кроется во внешнем виде: вы можете посмотреть, как выглядят шпалы деревянные пропитанные новые (фото мы представляем ниже) и сравнить их с железобетонными.
В остальном же два этих вида опорных конструкций похожи. В частности, близки они по сферам применения: на некоторых линиях и участках они даже продолжают, заменяют, взаимно дополняют друг друга. И оба варианта остаются актуальными в условиях Ж/Д-проектирования и строительства, как у нас, в России, так и в Европе или Америке.
Мы постарались как можно более подробно рассмотреть данные элементы ВСП и дать вам представление об их особенностях. А если потребуется еще и купить их, обращайтесь в «ПромПутьСнабжение»: мы продаем их по доступным ценам, предъявляем сертификат на шпалы деревянные пропитанные, паспорт качества и другие необходимые документы, заботимся о быстроте доставки – у нас удобно заказывать.
Также смотрите видео.
___________________
материалов | Бесплатный полнотекстовый | Численное исследование структурных характеристик железнодорожных шпал с использованием сверхвысокопрочного бетона (UHPC)
Вклад авторов
Концептуализация, M.S., Y.B. и С.П .; методология, М.С., Ю.Б. и С.П .; программное обеспечение, M.S .; валидация, М. и Y.B .; формальный анализ, М. и Y.B .; следствие, М.С., Ю.Б. и С.П .; ресурсы, М.С., Ю.Б. и С.П .; курирование данных, M.S. и Y.B .; письменность — подготовка оригинального черновика, М.С .; написание — просмотр и редактирование, М.С., Ю.Б. и С.П .; визуализация, М. и Y.B .; надзор, С.П .; администрация проекта, Ю. и С.П .; привлечение финансирования, Ю. и С.П. Все авторы прочитали и согласились с опубликованной версией рукописи.
Рисунок 1. Полученные экспериментально усредненные зависимости напряжения от деформации при прямом испытании на растяжение на UHPC с различным объемным содержанием волокон и соответствующие численные модели.
Рисунок 1. Полученные экспериментально усредненные зависимости напряжения от деформации при прямом испытании на растяжение на UHPC с различным объемным содержанием волокон и соответствующие численные модели.
Рисунок 2. Геометрический размер шпалы серии Л-150 (единица измерения: мм): ( a ) вид сверху; ( б ) вид спереди; ( c ) рельсовая секция; ( d ) центральная секция.
Рисунок 2. Геометрический размер шпалы серии Л-150 (единица измерения: мм): ( a ) вид сверху; ( б ) вид спереди; ( c ) рельсовая секция; ( d ) центральная секция.
Рисунок 3. Двухмерная численная модель шпалы ( a ), ее сетка ( b ) и граничные условия ( c ).
Рисунок 3. Двухмерная численная модель шпалы ( a ), ее сетка ( b ) и граничные условия ( c ).
Рисунок 4. Установка для испытания на статический изгиб на участке рельса-опора.
Рисунок 4. Установка для испытания на статический изгиб на участке рельса-опора.
Рисунок 5. Кривые напряжения и деформации после применения понижающего коэффициента 0,785 для растяжения.
Рисунок 5. Кривые напряжения и деформации после применения понижающего коэффициента 0,785 для растяжения.
Рисунок 6. Сравнение кривых усилия и ширины трещины с 0,5% стальной фибры UHPC на участке седла рельса.
Рисунок 6. Сравнение кривых усилия и ширины трещины с 0,5% стальной фибры UHPC на участке седла рельса.
Рисунок 7. Сравнение кривых усилия и ширины трещины с 1,0% стальной фибры UHPC на участке седла рельса.
Рисунок 7. Сравнение кривых усилия и ширины трещины с 1,0% стальной фибры UHPC на участке седла рельса.
Рисунок 8. Сравнение кривых усилия и ширины трещины для 1,5% стальной фибры UHPC на участке рельса-седла.
Рисунок 8. Сравнение кривых усилия и ширины трещины для 1,5% стальной фибры UHPC на участке рельса-седла.
Рисунок 9. Схемы спальных секций UHPC.
Рисунок 9. Схемы спальных секций UHPC.
Рисунок 10. Диаграмма «сила-ширина» шпал типа L, M и L диаметром 9,2 мм, 1% стальной фибры и fy 1275 МПа.
Рисунок 10. Диаграмма «сила-ширина» шпал типа L, M и L диаметром 9,2 мм, 1% стальной фибры и fy 1275 МПа.
Рисунок 11. Диаграммы силы и ширины трещины в зависимости от диаметра и предела текучести арматуры из полистирола (содержание стальной фибры сохранялось на уровне 1.0% константа).
Рисунок 11. Диаграммы силы и ширины трещины в зависимости от диаметра и предела текучести арматуры PS (содержание стальной фибры сохранялось на постоянном уровне 1,0%).
Рисунок 12. Соотношение силы и ширины трещины шпал L- и H-типа по отношению к трем различным содержаниям стальной фибры.
Рисунок 12. Соотношение силы и ширины трещины шпал L- и H-типа по отношению к трем различным содержаниям стальной фибры.
Рисунок 13. Результаты моделирования кривых усилия и ширины трещины с 0,5% стальной фибры UHPC на участке седла рельса.
Рисунок 13. Результаты моделирования кривых усилия и ширины трещины с 0,5% стальной фибры UHPC на участке седла рельса.
Рисунок 14. Результаты моделирования кривых усилия и ширины трещины с 1,0% стальной фибры UHPC на участке седла рельса.
Рисунок 14. Результаты моделирования кривых усилия и ширины трещины с 1.0% стальной фибры UHPC в секции рельсового седла.
Рисунок 15. Результаты моделирования кривых усилия и ширины трещины с 1,5% стальной фибры UHPC на участке седла рельса.
Рисунок 15. Результаты моделирования кривых усилия и ширины трещины с 1,5% стальной фибры UHPC на участке седла рельса.
Таблица 1. Краткое описание свойств материала.
Таблица 1. Краткое описание свойств материала.
Бетон | Модуль Юнга | 51,0 ГПа | ||
Прочность на сжатие | 150 МПа | |||
Коэффициент Пуассона | 0,2 | Коэффициент Пуассона | 0,2 | Прочность стального волокна MPa |
Прочность на разрыв (стальная фибра 1,0%) | 15,6 МПа | |||
Прочность на растяжение (стальная фибра 1,5%) | 18,4 МПа | |||
Начало растрескивания при прямом напряжении (стальная фибра 0.5%) | 3,17 МПа | |||
Начало растрескивания при прямом напряжении (стальная фибра 0,5%) | 6,52 МПа | |||
Начало растрескивания под прямым напряжением (стальная фибра 0,5%) | 5,58 МПа | |||
9 Стальная арматура | Модуль Юнга | 200 ГПа | ||
Предел текучести | 1275 МПа | |||
Коэффициент Пуассона | 0,3 |
Таблица 2. Сводка входных параметров.
Таблица 2. Сводка входных параметров.
Содержание стальной фибры (%) | 0,5 | 1,0 | 1,5 | ||||||||
Предел текучести предварительно напряженной арматуры (f y ) (МПа) | 1 080 | ||||||||||
Диаметр натяжного стержня (φ) (мм) | 9,2 | 11,0 | |||||||||
Параметры поперечного сечения | Тип L | Тип M | Тип H | ||||||||
Высота рельса -седельная секция, h r (мм) (h r1 , мм) | 140 (125) | 165 (150) | 195 (180) | ||||||||
Высота средней части , h c (мм) | 125 | 150 | 180 | ||||||||
Расположение натяжного стержня, P 1 (мм) | 32.5 | 35 | 50 | ||||||||
Расположение натяжного стержня, P 2 (мм) | 60 | 75 | 80 |
Таблица 3. Краткое изложение числовых моделей бетонных шпал и их номенклатур.
Таблица 3. Краткое изложение числовых моделей бетонных шпал и их номенклатур.
Sp. № | Стальная фибра 0,5% | Sp.№ | Стальное волокно 1,0% | Sp. № | Стальная фибра 1,5% |
---|---|---|---|---|---|
№ 1 | L-φ9.2-f y 1275 | No. 8 | L-φ9.2-f y 1275 | № 15 | L-φ9.2-f y 1275 |
№2 | L-φ11.0-f y 1275 | №9 | L-φ11.0 -f y 1275 | № 16 | L-φ11.0-f y 1275 |
No.3 | L-φ11.0-f y 1 080 | No. 10 | L-φ11.0-f y 1080 | No. 17 | L-φ11.0-f y 1080 |
№ 4 | M-φ09.2-f y 1275 | № 11 | M-φ9.2-f y 1275 | № 18 | M-φ9.2-f y 1275 |
No. 5 | M-φ09.2-f y 1080 | No. 12 | M-φ9.2-f y 1 080 | №19 | M-φ9.2-f y 1 080 |
No. 6 | H-φ09.2-f y 1275 | No. 13 | H-φ9.2-f y 1275 | No. 20 | H-φ9.2-f y 1275 |
No. 7 | H-φ09.2-f y 1080 | No. 14 | H-φ9.2-f y 1080 | No. 21 | H-φ9.2-f y 1080 |
Таблица 4. Сводка шпал типа L, M и H со следующими параметрами: 9.Диаметр 2 мм, fy 12 175 МПа и 1% стальной фибры.
Таблица 4. Краткое описание шпал типа L, M и H со следующими параметрами: диаметр 9,2 мм, fy 12 175 МПа и 1% стальной фибры.
Simulation Case | Седло рельса Сечение Площадь (мм 2 ) | Усилие (кН) | Трещина Ширина (мм) | 100Fr B / Площадь | ΔF 1 кН) = (Fr 0,05 — Fr r ) | ΔF 2 (кН) = (Fr B — Fr 0.05 ) | Fr B /2.5Fr 0 | |||||||||||
---|---|---|---|---|---|---|---|---|---|---|---|---|---|---|---|---|---|---|
L / 9,2 / 1 275 / 1,0% | 47200 | Fr r | 230,4 | 1,0 | 158,4 | 91,2 | 1,51 | |||||||||||
Fr 0,05 | 388,8 | 0,056 4 | ||||||||||||||||
Fr B | 1,0 B | 1,0 | 48022 1 % | 56075 | Fr r | 300.0 | 0,009 | 1,12 | 206,2 | 118,8 | 1,97 | |||||||
Fr 0,05 | 506,2 | 0,051 | ||||||||||||||||
9,2 / 1275 / 1,0% | 66 725 | Fr r | 400,8 | 0,009 4 | 1,25 | 276,5 | 158,7 | 2,63 | ||||||||||
005 | 676,3 | 0,052 8 | ||||||||||||||||
Fr B | 835,0 | 1,988 |
Таблица 5. Сводка результатов моделирования в отношении диаметра и предела текучести арматуры PS (содержание стальной фибры сохранялось на постоянном уровне 1,0%).
Таблица 5. Сводка результатов моделирования в отношении диаметра и предела текучести арматуры PS (содержание стальной фибры сохранялось на уровне 1.0% константа).
Чемодан для анализа | Седло рельса Сечение Площадь (мм 2 ) | Усилие (кН) | Трещина Ширина (мм) | 100Fr B / Площадь | ΔF 1 кН) = (Fr 0,05 — Fr r ) | ΔF 2 (кН) = (Fr B — Fr 0,05 ) | Fr B / 2.5Fr | ||||||||||||||||||||||||||||||||||||||||||||||||||||||||||||||||||||||||||||||||||||||||||||||||||||||||||||||||||||||||||||||||||||||||||||||||||||||||||||||||||||||||||||||||||||||||||||||||||||||||||
---|---|---|---|---|---|---|---|---|---|---|---|---|---|---|---|---|---|---|---|---|---|---|---|---|---|---|---|---|---|---|---|---|---|---|---|---|---|---|---|---|---|---|---|---|---|---|---|---|---|---|---|---|---|---|---|---|---|---|---|---|---|---|---|---|---|---|---|---|---|---|---|---|---|---|---|---|---|---|---|---|---|---|---|---|---|---|---|---|---|---|---|---|---|---|---|---|---|---|---|---|---|---|---|---|---|---|---|---|---|---|---|---|---|---|---|---|---|---|---|---|---|---|---|---|---|---|---|---|---|---|---|---|---|---|---|---|---|---|---|---|---|---|---|---|---|---|---|---|---|---|---|---|---|---|---|---|---|---|---|---|---|---|---|---|---|---|---|---|---|---|---|---|---|---|---|---|---|---|---|---|---|---|---|---|---|---|---|---|---|---|---|---|---|---|---|---|---|---|---|---|---|---|---|---|---|---|---|---|---|
L / 9,2 / 1 275 / 1,0% | 47 200 | Fr r | 230.4 | 0,0086 | 1,02 | 158,4 | 91,2 | 1,51 | |||||||||||||||||||||||||||||||||||||||||||||||||||||||||||||||||||||||||||||||||||||||||||||||||||||||||||||||||||||||||||||||||||||||||||||||||||||||||||||||||||||||||||||||||||||||||||||||||||||||||
Fr 0,05 | 388,8 | 0,0564 | |||||||||||||||||||||||||||||||||||||||||||||||||||||||||||||||||||||||||||||||||||||||||||||||||||||||||||||||||||||||||||||||||||||||||||||||||||||||||||||||||||||||||||||||||||||||||||||||||||||||||||||||
Fr 11,0 / 1 275 / 1,0% | 47200 | Fr r | 276,0 | 0,0098 | 1,22 | 155,3 | 142,7 | 1,81 | |||||||||||||||||||||||||||||||||||||||||||||||||||||||||||||||||||||||||||||||||||||||||||||||||||||||||||||||||||||||||||||||||||||||||||||||||||||||||||||||||||||||||||||||||||||||||||||||||||||||||
0169 Fr05 | 431,3 | 0,0452 | |||||||||||||||||||||||||||||||||||||||||||||||||||||||||||||||||||||||||||||||||||||||||||||||||||||||||||||||||||||||||||||||||||||||||||||||||||||||||||||||||||||||||||||||||||||||||||||||||||||||||||||||
Fr B | 575,0 | 7,292 | |||||||||||||||||||||||||||||||||||||||||||||||||||||||||||||||||||||||||||||||||||||||||||||||||||||||||||||||||||||||||||||||||||||||||||||||||||||||||||||||||||||||||||||||||||||||||||||||||||||||||||||||
L / 11,0 / 1 080 / 1,0% | 47 20016 | 902 | 0,01151,10 | 171,6 | 98,8 | 1,64 | |||||||||||||||||||||||||||||||||||||||||||||||||||||||||||||||||||||||||||||||||||||||||||||||||||||||||||||||||||||||||||||||||||||||||||||||||||||||||||||||||||||||||||||||||||||||||||||||||||||||||||
Fr 0,05 | 421,2 | 0,0532 | |||||||||||||||||||||||||||||||||||||||||||||||||||||||||||||||||||||||||||||||||||||||||||||||||||||||||||||||||||||||||||||||||||||||||||||||||||||||||||||||||||||||||||||||||||||||||||||||||||||||||||||||
104 | |||||||||||||||||||||||||||||||||||||||||||||||||||||||||||||||||||||||||||||||||||||||||||||||||||||||||||||||||||||||||||||||||||||||||||||||||||||||||||||||||||||||||||||||||||||||||||||||||||||||||||||||||
H / 9,2 / 1 275 / 1,0% | 66 725 | Fr r | 400,8 | 0,0094 | 1,25 | 276,5 | 158,7 | 3 9026 902676,3 | 0,0528 | ||||||||||||||||||||||||||||||||||||||||||||||||||||||||||||||||||||||||||||||||||||||||||||||||||||||||||||||||||||||||||||||||||||||||||||||||||||||||||||||||||||||||||||||||||||||||||||||||||||||||
Fr B | 835,0 | 1,988 | |||||||||||||||||||||||||||||||||||||||||||||||||||||||||||||||||||||||||||||||||||||||||||||||||||||||||||||||||||||||||||||||||||||||||||||||||||||||||||||||||||||||||||||||||||||||||||||||||||||||||||||||
H / 9,2 / 1 080 / 1,0% | 66 725 | 168 908 909 Fr00841,12 | 264,0 | 152,0 | 2,52 | ||||||||||||||||||||||||||||||||||||||||||||||||||||||||||||||||||||||||||||||||||||||||||||||||||||||||||||||||||||||||||||||||||||||||||||||||||||||||||||||||||||||||||||||||||||||||||||||||||||||||||||
Fr 0,05 | 648,0 | 0,0539 | |||||||||||||||||||||||||||||||||||||||||||||||||||||||||||||||||||||||||||||||||||||||||||||||||||||||||||||||||||||||||||||||||||||||||||||||||||||||||||||||||||||||||||||||||||||||||||||||||||||||||||||||
Fr16 | |||||||||||||||||||||||||||||||||||||||||||||||||||||||||||||||||||||||||||||||||||||||||||||||||||||||||||||||||||||||||||||||||||||||||||||||||||||||||||||||||||||||||||||||||||||||||||||||||||||||||||||||||
9024 | 9024 Таблица 6. Сводка результатов моделирования в отношении содержания стальной фибры 0,5%, 1,0% и 1,5%. Таблица 6. Сводка результатов моделирования по отношению к 0.5%, 1,0% и 1,5% стальной фибры.
|