Среди огромного количества композитно-отделочных материалов стеклофибробетон входит в число наиболее востребованных. Среди его главных преимуществ можно отметить высокие прочностные характеристики, эксплуатационные свойства. Такой материал отлично подходит для зон с любым климатом и температурой, при этом изделия способны сохранять внешнюю привлекательность в течение длительного времени. | |
Среди огромного разнообразия строительных материалов особого внимания заслуживаетстеклофибробетон. Активно используют его в различных отраслях, а именно при отделке зданий, изготовлении малых архитектурных форм, элементов декора, ландшафтного дизайна. В сравнении с обычным бетоном, производство стеклофибробетона является куда более трудоемким процессом, который требует грамотного подхода. | |
Стеклофибробетон представлен современным композиционным материалом.![]() Этот материал отличается возможностью увеличить прочность изделий на разрыв, растяжение, изгиб. Отмечаются идеальные показатели устойчивости к образованию трещин. | |
С каждым годом популярность стеклофибробетона постепенно увеличивается, и это не удивительно. Этот материал обладает уникальными эксплуатационными свойствами, благодаря чему применение ему нашли в различных отраслях строительства. Используют его и в качестве несъемной опалубки. | |
Стеклофибробетон – материал с уникальными характеристиками. Он легкий и твердый, прочный, как армированный бетон, и пластичный. Выбрать его для отделки фасадов, интерьера банка, отеля или коттеджа – грамотное решение. При этом часто возникает вопрос о том, как формируется цена стеклофибробетона на изделия. Эта схема не у всех организаций одинакова. | |
Изящные карнизы, русты, колонны, балясины и другие архитектурные элементы повышают эстетическую привлекательность здания. | |
Облицовка фасада — ответственный процесс, ведь именно от этого будет зависеть внешний вид здания. Для этого в наше время используется огромное количество различных материалов. Среди них особое место занимает стеклофибробетон. Широко использовать его начали сравнительно недавно, лишь в начала 2000-ых годов. | |
С каждым годом всё больше людей задумываются над изменением внешнего облика фасада своего дома. Процесс это достаточно трудоемкий и требует особых навыков, поэтому самостоятельно справиться с ним по силам лишь настоящим профессионалам в данной сфере. ![]() |
Производство стеклофибробетона в Москве, изготовление изделий из СФБ.
Производство стеклофибробетона — сложный процесс, благодаря которому можно получить прочные декоративные изделия любой формы и размера. Если вас интересует производитель стеклофибробетона в Москве и Московской области, обратите внимание на нашу компанию.
Производство стеклофибробетона (СФБ).
Наша фирма занимается производством стеклофибробетона в Москве, изготавливая лепнину высокого качества из композитных бетонов. Задачей компании является создание продукции, удовлетворяющей спрос покупателя с любыми запросами и возможностями. Цены на стеклофибробетон производители обычно формируют на основе сложности изготавливаемых изделий, поэтому в нашей компании каждый заказчик сможет подобрать декор, подходящий по стоимости. Качественное и квалифицированное изготовление изделий из стеклофибробетона делает нашу компанию надежным поставщиком для требовательных к качеству клиентов.
Проектирование и изготовление изделий из стеклофибробетона.
Этап проектирования.
При изготовлении стеклофибробетона производство делится на этапы, каждый из которых важен для качества и внешнего вида изделия. Первый этап — проектирование стеклофибробетона и моделирование. Для этого ведутся работы с чертежами и эскизами будущей лепнины, на базе которых создаются модели. Материал модели подбирается в зависимости от сложности изготавливаемого изделия. Для скульптурных композиций — барельефов, панно, капителей — делают лепные модели в соответствии с рисунком или эскизом. При производстве стеклофибробетона (СФБ) в виде карнизов, колонн, пилястр, карнизов, создают компьютерные модели. Далее подготовленные файлы поступают с цех ЧПУ, где производится изготовление моделей в материале. Создание моделей для производства СФБ на этом этапе осуществляют специалисты, опыт работы которых гарантирует отличный результат.
Подготовка формы для заливки.
Второй этап изготовления СФБ: производство формы, в которой будет производиться отливка будущего декора или изделия. Форма создается на базе изготовленной модели. Материал формы для производства стеклофибробетона выбирается в соответствии со сложностью элементов, их количества и назначения. При простых формах и небольшом количестве нередко в качестве материала для формы выбирают фанеру. Если декор имеет более сложную форму, а необходимое количество — несколько десятков единиц, то форма может быть изготовлена из стеклопластика. Оригинальный объемный рисунок изделий может потребовать использования резиновой (силиконовой) формы. При создании изделий из стеклофибробетона изготовление формы — наиболее важная составляющая, которая будет влиять на внешний вид и качество. На этом этапе получения конечного изделия, производство формы и выбор материала для нее во многом будут определять его конечную стоимость.
Отливка в форму.
Следующим этапом производства стеклофибробетона становится отливка будущей лепнины в готовую форму. При этом подготовленную смесь бетона и стеклофиброволокон — стеклофибру — напыляют в полученную форму. На обратной стороне изделия нередко создаются монтажные утолщения, с помощью которых деталь будет крепиться к фасаду. В соответствии с заказом на стеклофибробетон производители оставляют его белым для дальнейшего окрашивания, либо в смесь при отливке добавляют пигмент, получая цвет в массе. Также в смесь на данном этапе могут быть добавлены наполнители — это может быть, например, песок, кусочки доломита, мрамора.
Сушка изготовленных из СФБ изделий.
Окончательный этап наступает, когда после суточной выдержки в форме элемент вынимают и устанавливают в камеру для вызревания и сушки. Этот этап в процессе изготовления стеклофибробетона очень важен для улучшения прочностных свойств изделий. Камера сокращает время сушки изделий, помогает избежать микротрещин в элементах. После камеры просушенный декор шлифуют и подготавливают к отправке, так как он готов для отделки дома.
О стеклофибробетоне | Эстет-Бетон Стеклофибробетон
ИСТОРИЯ СТЕКЛОФИБРОБЕТОНА
Производство стеклофибробетона
Стеклофибробетон(СФБ) является конгломератным строительным материалом, в котором стекловолокна заменяют крупный заполнитель и стальную арматуру.

При сочетании цементно-песчаной матрицы и стекловолокон получаются гомогенно армированные конструкции, они имеют меньшую толщину нежели,когда армируются стальной арматурой. В этом стеклофибробетон является крайне коммерчески привлекательным.
Изделия СФБ в основном весят только 10% от веса изделий, которые выполнены из сборного железобетона.
Начали использовать стекловолокно для армирования бетона в 1941 году. Но в начале своего пути, стеклофибробетон был провальным, потому что щелочная среда — агрессивная среда для стекловолокна,приводящая к коррозии. Позднее, уже в 1967 году в Великобритании, Строительному научно-исследовательскому институту удалось получить стекловолокно, стойкое к щелочи.
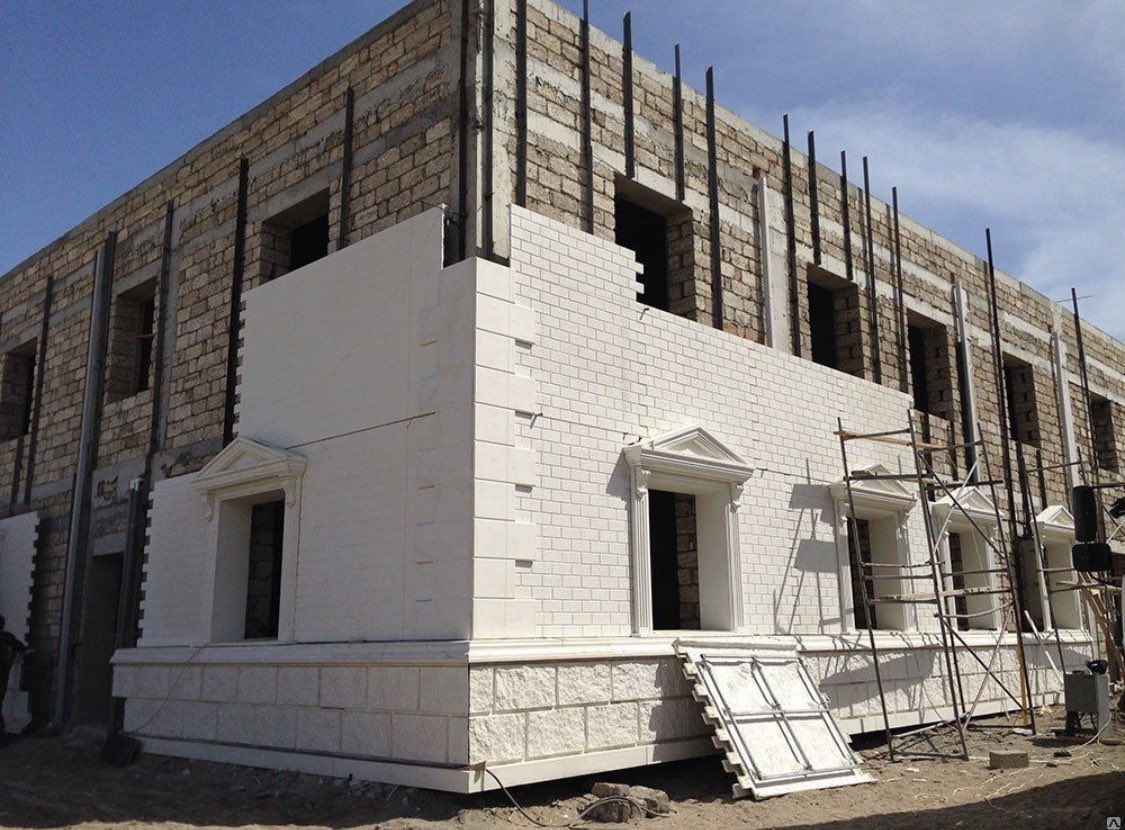
И с 1967 года начали уже активно использовать стеклофибробетон в Западной Европе, а с 1974 года в США. Ежегодный прирост применения СФБ в США и Европе — 31%. Стеклофибробетон имеет ряд активных преимуществ перед сборным железобетоном. В основном в США и Европе СФБ используется для производства сборных облицовочных панелей для высотных зданий.
В СССР начали исследовать стеклофибробетона в 60х гг, но свойства и преимущества не были оценены и про него забыли. Наконец стеклофибробетон в России был признан на основе опыта работы с ним за рубежом. Современные архитекторы и проектировщики все чаще и чаще используют СФБ в своих проектах. А такие компании по производству, как Эстет-Бетон с удовольствием воплощаем их в жизнь.
СПОСОБЫ ПРОИЗВОДСТВА СТЕКЛОФИБРОБЕТОНА
Способ напыления стеклофибробетона — пневмонабрызг
Стеклофибробетон возможно изготовить различными способами. Первым способом является пневмораспыление в формы, вторым — ручное смешивание всех составляющих в бетономешалке.
Пневмобрызг имеет ряд преимуществ:
— отдельное приготовление смеси;
— точную дозировку;
— быстрое нанесение;
— высокое качество раствора.
напыление стеклофибробетона пистолетом
Самым основным достоинством является автоматическое измельчение стеклонити на выходе из пистолета.
Минусами данного способа являются:
— наличие специального оборудования, пистолета, в частности его стоимость.
В бетономешалке стеклофибробетон изготавливается также как и товарный бетон. Сначала замешиваются все компоненты, а потом в течении нескольких минут мешаются с фиброй.
Необходимо нанести смесь как можно быстрее, чтобы избежать преждевременного затвердевания, потому что когда смесь затвердеет,сложно что либо поправить. Поэтому чтобы этого не произошло необходимо наносить небольшими порциями.

Для того, чтобы придать цвет цвет изделиям из СФБ добавляют пигменты. Изделиям возможно придать его любой, а также возможно произвести в любой фактуре.
Из-за стекловолокон в бетонной смеси, необходимо работать в защитных масках.
ЭТАПЫ ПРОИЗВОДСТВА
Стеклофибробетон является универсальным строительным материалом. Изделия из него имеют тонкие стенки, но не смотря на это очень прочные.
Из стеклофибробетона производят:
— архитектурные элементы декора фасада;
— облицовочные панели;
— сборные здания;
— солнцезащитные экраны;
— имитация натурального камня;
— шумозащитные барьеры;
— водоотводные лотки и водотоки;
— элементы внутренней отделки канализационных систем;
— элементы несъемной опалубки;
— малые архитектурные формы (лавочки, вазоны, урны, фонтаны, шезлонги и др)
производство изделий сфб для фасада
Для производства изделий из стеклофибробетона не малую роль играют формы, в которые заливают бетонную смесь с фиброй. Они могут быть:
— стальные;
— деревянные;
— стеклопластиковые;
— резиновые.
При производстве изделий из стеклофибробетона используются следующие расходные материалы:
— цемент;
— песок;
— вода;
— стекловолокно;
— хим. добавки;
— полимеры;
— пигменты.
Для того,чтобы приступить к производству необходимо приготовить нужное количество форм, для того чтобы рабочий процесс не прерывался. Далее необходимо очистить формы и нанести опалубочную смазку кистью или тряпкой. Потом производится набрызг или формование. Выбор способа зависит от размера изделия. После этого происходит процесс затвердевания. Достают изделия из форм только тогда, когда изделие наберет прочности. Далее изделия выдерживаются и складируются на поддонах.
ОТДЕЛКА ПОД КАМЕНЬ
Стеклофибробетон очень пластичный в области проектирования. Он дает возможность разнообразить архитектурные формы и текстуры. С помощью него можно изготовить все архитектурные элементы в различных стилях. СФБ способен воссоздать почти любые поверхности и повторить фактуру таких материалов как камень, шифер, мрамор, гранит, терракота и даже тонкую фактуру дерева. Работа с натуральным камнем очень дорогостоящая и долгая. Каменные изделия очень тяжелые. Из стеклофибробетона же можно интерпретировать цвет и поверхность природного материала. Эти изделия гораздо легче, их проще перемещать, складировать и монтировать.
производство изделий из стеклофибробетона
Руководитель Эстет-Бетон имеет опыт работы с стеклофибробетоном более 9 лет. Наш генеральный директор принимает активное участие в жизни компании. Он до сих пор, совместно с опытным отделом, изучает свойства стеклофибробетона, проводит испытания, разрабатывает новые текстуры и фактуры, открывает новые возможности СФБ. Все это проводится для того,чтобы повысить качество и внешний вид производимых изделий, чтобы снизить себестоимость и соответственно конечную стоимость производства СФБ. Для нашей компании стеклофибробетон является очень важным направлением, которое можно изучать и узучать.

Производство стеклофибробетона в Москве | Завод-изготовитель
Мы гарантируем красоту и качество
Компания ООО «Геомонтаж» – проектно-строительное предприятие, успешно работающее на российском строительном рынке с 2002 года. За годы работы компания успешно зарекомендовала себя в качестве опытного и надежного партнера, который способен легко справиться с целым комплексом архитектурных, проектных, строительных, реставрационных и дизайнерских задач, независимо от их сложности.
Сегодня ООО «Геомонтаж» – это профессиональный коллектив опытных специалистов, предоставляющих клиентам широкий спектр качественных услуг, среди которых:
— архитектурное проектирование;
— изготовление любых архитектурных изделий из стеклофибробетона и его аналогов, а также из искусственного камня;
— реставрация исторических зданий, памятников архитектуры и зодчества;
— украшение фасадов зданий и оформление интерьеров с использованием сфб и иных современных материалов;
— работы по ландшафтному дизайну.
— стеклофибробетон
Наши преимущества
Несмотря на высокую конкуренцию в строительном сегменте рынка ООО «Геомонтаж» продолжает стабильно развиваться. Этому способствует масса конкурентных преимуществ, выгодно отличающих нас от многочисленных строительных компаний.
Среди прочих достоинств фирмы назовем основные:
1. Работа с любыми инновационными материалами – такими, как стеклопластик, стеклофибробетон, полимербетон и искусственный камень. Наши клиенты имеют возможность недорого купить изделия из стеклофибробетона или иного современного композитного материала для украшения фасада дома, изготовления ландшафтных композиций или создания уникального дизайна в интерьере.
2. Комплексный подход и внимание к каждому клиенту. Нашим заказчикам удобно работать с нами: они получают возможность в одном месте заказать проект, купить стеклофибробетон или уже готовое изделие с доставкой, что сокращает и время, и расходы.
3. Гарантия самой низкой цены. Только в ООО «Геомонтаж» можно купить изделия из стеклофибробетона по максимально низким ценам в московском регионе — от 4500р/кв.м.
4. Разнообразная продукция из сфб, изготовленная нашим предприятием, – это проверенное временем качество, огромный выбор изделий и масса положительных отзывов, оставленных довольными клиентами.
5. Производство полного цикла: от создания чертежей и макетов, до готовых изделий
Изделия из стеклофибробетона: оборудование для производства
В отделке зданий, фасадов успешно используются изделия из стеклофибробетона, имитирующие тяжелый природный материал. Однако, они имеют значительно меньший вес, соответственно, меньшую нагрузку на стеновые конструкции и фундамент. Обеспечивается это особой структурой и технологией изготовления материала.
Состав и характеристики
Основу материала составляет цементный раствор. Наполнителем выступает щелочестойкая стеклянная фибра, дающая особые показатели прочности на растяжение и сжатие, стойкости к перепадам температуры, что выделяет стеклофибробетон из ряда подобных композитных материалов. Стекловолокна располагаются хаотично, имеют малое сечение, но большую длину, это обеспечивает особые свойства композита. Другими компонентами, добавляемыми в раствор в процессе производства, являются кварцевый песок и присадки. Они улучшают формовочные свойства, придающие конечным изделиям вид гранита, песчаника. Добавки следующие:
- Пластификаторы. Повышают пластичность смеси.
- Воздухововлекающие вещества. Увеличивают морозостойкость, долговечность, щелочестойкость и подвижность материала.
- Ускоритель схватывания. Сокращает время затвердения.
- Противоморозные компоненты. Сохраняют жидкую фазу в смеси, необходимую по технологии производства для качественного твердения.
- Гидрофобизатор. Придает гидрофобные свойства.
- Замедлитель схватывания. Необходим при производстве в жаркую сухую погоду.
Приготовление раствора предполагает четкое соблюдение пропорций смешиваемых песка и цемента.Глиноземистый или высокоалюминатный цемент более всего подходит для изготовления стеклофибробетона. Он хорошо кристаллизуется, сохраняет прочность, обеспечивает высокую водонепроницаемость продукции.
Важно строго придерживаться пропорций компонентов раствора для фибробетона. Чтобы получить максимально прочный композит, кварцевый песок и цемент берутся в соотношении 2:1. В зависимости от области использования материала пропорции могут меняться в сторону увеличения кварца и составлять 7:3, при этом прочность продукции снижается. Стекловолокно добавляется из расчета 3—5% общей смеси, добавки — 1—2%.
Плюсы и минусы
Недостатками можно назвать быструю схватываемость, что вынуждает проводить работы максимально быстро, восприимчивость к щелочи, содержащейся в цементе, это компенсируется использованием щелочестойкого стекловолокна. В пользу использования продукции из стеклофибробетона говорят следующие факты:
- имеет повышенную прочность и небольшую массу;
- огне- и морозостойкость;
- сейсмоустойчивость;
- экологичность стройматериала;
- повышенная пластичность, что позволяет использовать стеклофибробетон в специальных проектах, нетиповых постройках;
- легкость обработки, транспортировки, монтажа.
Оборудование для производства
В зависимости от назначения изделий определяются соотношения компонентов при производстве.Процесс изготовления более технологичен и трудоемок по сравнению с обычным бетоном. Пропорции веществ определяются в зависимости от назначения изделий и влияют на качество и свойства конечной продукции. Производство стеклофибробетона может выполняться методом пневмонабрызга или виброформирования, что определяет конечную стоимость изделий. Способ пневмобрызга позволяет изготавливать более сложные элементы и формы с помощью специального комплекса, например, СЦ-45.
Оборудование для стеклофибробетона включает:
- пневмопистолет, осуществляющий набрызгивание премикса;
- меситель;
- станция насосная;
- компрессор;
- гибкие или твердые формы;
- пружинные валики.
Методика производства
Пневмонабрызг выполняется пневмопистолетом, что делает возможным тщательное смешение компонентов, образование однородной массы и их равномерное распределение при заливке в специальные формы. В технологии изготовления этого композита важен размер стекловолокна. Производство стеклофибробетона таким методом имеет плюс, заключающийся в возможности измельчать волокно до нужного размера перед смешиванием компонентов непосредственно в пневмопистолете. Минус — высокая стоимость установок для изготовления стеклофибробетона и конечной продукции.
При виброформировании берется предварительно подготовленный раствор песка и цемента, добавляется стекловолокно, смесь перемешивается и проводится виброформирование. Этот метод не требует дорогостоящего оборудования, достаточно иметь в наличии стенд для стеклофибробетона, с помощью вибрации которого формируется смесь и распределяется стекловолокно в ней. Имеет низкую себестоимость, пригоден только для формирования простых изделий и форм.
Стеклофибробетон
Стеклофибробетон – востребованный композитный материал, который получается из смеси портландцемента, кварцевого песка и воды. В качестве армирующей составляющей в нем используется стекловолоконная фибра. Подобный метод армирования придает материалу свойства, выгодно выделяющие от бетона со стальным армированием. К примеру, материал в отличие от железобетонных конструкций не подвержен внутренней коррозии; обладает большой прочностью на разрыв и сжатие. Панели из сфб широко используются в архитектурном оформлении жилых и административных зданий.
Из других выгодных свойств материала выделим следующие:
- небольшой вес, по этому показателю сфб превосходит бетон в разы;
- по показателю прочности фибробетон превосходит железобетон в 7 раз;
- широкий выбор фактур, в том числе древесины и натурального камня;
- технология производства позволяет создавать изделия любой формы, в том числе и криволинейной, также нет ограничений по размерам. Благодаря этому преимуществу обеспечивается легкий и быстрый монтаж готовых панелей.
Где используются панели?
Панели часто используются для декорирования фасадов зданий. При помощи стеклофибробетонных конструкций отделываются фасады монолитных перекрытий многоэтажных зданий. Также они применяются в местах, где существуют киски вандализма со стороны людей. Это подземные пешеходные переходы, пункты остановки общественного транспорта и прочие места.
СФБ находит применение в тонкостенных элементах и конструкциях зданий, сооружений, которым нужно уменьшить собственный вес, увеличить стойкость к образованию трещин. Также материал используется, когда нужно обеспечить водонепроницаемость бетона и увеличить срок его службы. Используется и для увеличения ударной вязкости и сопротивления истиранию.
Производство стеклофибробетона для декора фасада
Компания СК «ПК АрхБетон» занимается производством и поставкой данной продукции по стране. Наши производственные мощности позволяют изготавливать панели любых форм и размеров. Стеклофибробетон производство возможно любого цвета, это позволяет выбрать подходящее по цвету фасада решение.
На выбор покупателям предлагаем элементы из фибробетона в широком разнообразии вариантов. Это позволяет подобрать решения для декоративного украшения любого фасада. Благодаря нашей продукции вы сможете оформить дом в любом стиле.
На стеклофибробетон цена у нас рассчитывается индивидуально для каждого покупателя с учетом ряда факторов. В частности, это сложность создания элемента декора и формы; объем заказываемой партии; назначение панелей. При заказе большой партии действуют дополнительные скидки.
Если хотите стеклофибробетон купить на выгодных условиях, позвоните нам по номеру +7 (495)776-98-77. Вас проконсультируют наши сотрудники, расскажут об условиях заказа товара. Качество товара гарантируем!
Дополнительная информация:
Карнизы и карнизные блоки из стеклофибробетона – по цене производителя
Производство панелей, плит и других изделий из стеклофибробетона
Крепления, узлы крепления, системы и подсистемы крепежа стеклофибробетона
Монтаж деталей из стеклофибробетона
Декор из стеклофибробетона для оформления фасадов домов
Технологии производства стеклофибробетона, стеклофибробетон технология
При получении бетона, упрочняемого стекловолокнами, важное значение имеет не только правильный подбор и рациональное сочетание исходных материалов, но и технология его изготовления. Свойства конечного композита находятся в большой зависимости от обеспечения равномерности распределения фибр в бетоне, их ориентации, анкеровки, определяющих в значительной мере способность материала оказывать сопротивление внешним воздействиям.
Большинство изделий и конструкций из стеклофибробетона изготавливаются, как правило, по одной из двух основных технологических схем – пневмонабрызг смеси и виброформование премикса (или премиксинг), т.е. предварительное смешивание нарубленного стекловолокна с цементно-песчаным раствором.
В первом случае речь идет о набрызге цементно-песчаного раствора под давлением (подобно торкретированию) с одновременной подачей волокна на большой скорости. Порядок выполнения операций таков: приготовление смеси цемента, песка, воды и химдобавок производится в высокоскоростном широкозахватном смесителе с высоким срезывающим усилием. Затем смесь выгружается в нагнетательную растворонасосную станцию, откуда она поступает в специальный пистолет-напылитель. В рубящее устройство пистолета также подается нить стекловолокна (стеклоровинг), где она нарубается на короткие отрезки (фибру) и далее смешивается в воздушной струе с цементно-песчаной смесью. Затем такая стеклофибробетонная смесь набрызгом наносится на форму или на формообразующую рельефную матрицу.
Пневмонабрызг СФБ смеси
Метод формования премикса подразумевает предварительное введение уже нарубленной стеклофибры в цементное тесто с последующим виброформованием. Получаемый в результате этого процесса материал обычно называют СФБ-премиксом. Его приготовление включает две стадии: сначала в высокоскоростном смесителе готовится смесь цемента, песка, воды и химдобавок, а затем в эту смесь уже на малой скорости работы смесителя добавляется стеклофибра. Далее премиксом заполняются формы и производится его виброуплотнение.
С появлением технологии самоуплотняющегося бетона благодаря применению суперпластификаторов нового поколения эта методика распространилась и на СФБ, что позволило получать изделия из СФБ премикса без традиционного уплотенения с помощью вибрации (см. видеоролик «Формование самоуплотняющегося премикса» на главной странице).
Пневмонабрызг |
Формование премикса |
Свежеотформованные изделия, полученные в результате обоих технологических процессов, должны выдерживаться в течение 7-ми дней во влажной среде.
Прочность пневмонанесенного СФБ обычно выше, чем у СФБ премикса. В первую очередь, это объясняется тем, что при пневмонабрызге содержание волокна может достигать 5-6%, в то время как у премикса этот показатель ограничивается 3-3.5%. Во-вторых, у стеклофибробетона, полученного в результате пневмонабрызга, более низкое водоцементное отношение, чем у премикса. В-третьих, пневмонанесение позволяет получать более длинные отрезки стекловолокон и придавать им плоскостную (в отличие от трехмерной у премикса) ориентацию.
Выбор производственного метода определяют такие факторы, как заданные требования в отношении прочности, размер формы, архитектурно-проектные условия. Как правило, изделия больших размеров, такие как стеновые панели, напыляются, в то время как малые изделия формуются из премикса.
Типовые составы стеклофибробетонных смесей:
Третий сравнительно новый производственный метод называется пневмонабрызг премикса. Этот технологический прием, вобравший в себя все самое лучшее из двух традиционных методов производства СФБ, приобретает все большую популярность у производителей стеклофибробетона при изготовлении изделий малых и средних размеров общей площадью не более 2-х кв.м. Разработанная в 80-х годах прошлого столетия эта технология сделала недавно значительный прорыв благодаря последним разработкам как в области СФБ материалов, так и в сфере технологического оборудования.
Этот метод применяется также и для нанесения штукатурных покрытий. Для последних степень стеклоармирования не превышает 1-2% и, в то же время, гарантирует высокую прочность и стойкость к растрескиванию и отслаиванию.
Пневмонабрызг СФБ-премикса |
Пневмонанесение СФБ штукатурки |
Изделиям и конструкциям из стеклофибробетона можно придавать различные характеристики, меняя методы изготовления, составы смеси, типы используемого волокна, длину и ориентацию фибры в смеси, применяемые химдобавки и т.д. При этом, производитель по своему усмотрению может задавать материалу нужные параметры широкого диапазона, с тем чтобы получаемые изделия в зависимости от их назначения отвечали необходимым требованиям. Типовые значения свойств пневмонанесенного СФБ и СФБ-премикса на 28-е сутки приведены в нижеследующей таблице.
Что такое бетон, армированный стекловолокном?
Состав бетона, армированного стекловолокном (GFRC)
Композиты из бетона, армированного стекловолокном, содержат высокопрочные стекловолокна, окруженные вяжущей средой. В этой форме волокна и окружающая среда сохраняют свои естественные индивидуальные химические характеристики. Однако полученный бетон имеет улучшенные результирующие свойства, которые не могут быть достигнуты, если любой из компонентов используется по отдельности.Стекловолокно являются основными элементами, несущими нагрузку, в то время как заключенная в него матрица удерживает волокна в предпочтительном положении и направлении. Среда облегчает передачу нагрузки на волокна и защищает их от повреждений окружающей средой. Стекловолокно может быть встроено в матрицу постоянной или нестандартной длины. Наиболее распространенная форма, в которой композиты, армированные стекловолокном, используются в конструкционных приложениях, известна как ламинат. Эта форма достигается за счет объединения слоев тонких волокон и матрицы до желаемого размера.Ориентацию волокна в каждом слое и последовательность укладки слоев можно использовать для получения ряда механических свойств композитных материалов.
Все эти свойства сочетаются с тем фактом, что GFRC выглядит как твердый бетон, хотя его вес составляет лишь одну треть от первоначального веса твердого бетона. Это делает его идеальным для наружных и внутренних работ, где требуется легкий и прочный бетон. К таким приложениям могут относиться декоративные конструкции, фонтаны, купола, цветочные горшки и т. Д.
A Декоративное приложение GFRC
Стекловолокно
Стекловолокно состоит из 200-400 отдельных нитей, слегка связанных друг с другом для образования подставки. Затем эти стойки можно нарезать на кусочки различной длины и использовать для различных целей. Основное промышленное применение стекловолокна — армирование цементных или растворных матриц, используемых для производства тонколистовых изделий. Обычные методы смешивания бетона позволяют использовать только около 2% (по объему) волокон длиной 25 мм.Наиболее распространенным типом стеклянных волокон, используемых для общего применения, является электронное стекло. В смеси из стекловолокна также могут быть добавлены полимеры для улучшения физических свойств, таких как движение влаги _._
Преимущества бетона, армированного стекловолокном
GFRC — это специально разработанный материал. Его свойства могут меняться в зависимости от состава смеси, содержания волокна и технологий, используемых для производства. Использование GFRC стало популярным благодаря его многочисленным благоприятным свойствам:
- GFRC был испытан в лаборатории, а также на реальных установках, и можно ожидать, что он прослужит столько же, сколько и сборный бетон.В различных условиях окружающей среды, например, при воздействии солей или влаги, GFRC, вероятно, будет лучше функционировать из-за отсутствия стальной арматуры, которая может подвергнуться коррозии.
- Относительно легкий по сравнению с традиционными камнями. Его установка выполняется быстро и сравнительно просто.
- GFRC имеет характеристики, позволяющие придать практически любую форму.
- GFRC состоит из материалов, которые вряд ли горят. Бетон играет роль терморегулятора при воздействии огня и защищает материалы от тепла пламени.
- GFRC тонкий и прочный, его вес на 75–90% меньше по сравнению с твердым бетоном. Меньший вес способствует легкой и быстрой установке, а также снижает нагрузку на конструкцию. Легкий и прочный материал также сводит к минимуму расходы на транспортировку, обеспечивает гибкость конструкции и снижает воздействие на окружающую среду.
- Превосходная прочность увеличивает способность выдерживать сейсмические нагрузки.
- GFRC менее уязвим к погодным условиям и более устойчив к замерзанию и оттаиванию, чем обычный бетон.
Сравнение GFRC и сборного железобетона
Эластичность и плотность GFRC выше, чем у сборного железобетона. Соотношение цемента и песка для GFRC составляет примерно 1: 1, а для сборного железобетона — 1: 6. Стекловолокно, используемое для армирования бетона, обеспечивает значительно большую ударную вязкость и меньшую проницаемость для воды и воздуха, чем сборный бетон. GFRC выглядит как натуральный камень и дает дизайнеру большую гибкость в выборе формы, цвета и текстуры.
Проверьте также: Бетон, армированный стальным волокном
Кредиты на изображения:
GFRC Полубревенчатая скамья
Стекловолокно для армирования бетона
(PDF) ИССЛЕДОВАНИЕ СТЕКЛЯННОГО ВОЛОКНА В КАЧЕСТВЕ ДОБАВКИ В БЕТОНЕ ДЛЯ ПОВЫШЕНИЯ ПРОЧНОСТИ БЕТОНА
000 GRA — GLOBAL RESEARCH ANALYSIS X 86
Объем: 2 | Выпуск: 2 | Февраль 2013 г. • ISSN № 2277 — 8160
ВОЛОКНА В ЖЕСТКОМ Дорожном покрытии
Дорожное покрытие — это композитный материал, который выдерживает вес пешеходов
и транспортных средств.Толщина, ширина и тип покрытия должны варьироваться
в зависимости от предполагаемой функции вымощенной территории.
Толщина покрытия: определяется четырьмя факторами: окружающей средой,
трафиком, характеристиками основания и используемым материалом покрытия.
Ширина дорожного покрытия: Как и толщина, ширина дорожного покрытия должна варьироваться
в зависимости от предполагаемого использования. Очевидно, что межгосударственные автомагистрали
идолжны быть намного шире, чем местные жилые дороги. Точно так же парковка
, обслуживающая региональный торговый центр, будет намного больше, чем место для круглосуточного магазина
.
Жесткое покрытие имеет достаточную изгибную прочность, чтобы передать нагрузку колеса
на более широкую область под ним. По сравнению с гибким покрытием, жесткое покрытие
укладывается либо непосредственно на подготовленный грунтовый слой
, либо на один слой гранулированного или стабилизированного материала. Поскольку между бетоном и основанием находится только один слой материала
, этот слой
можно назвать слоем основания или основания.
Типы жестких дорожных покрытий
Жесткие покрытия можно разделить на четыре типа:
• «Размытое» однотонное »бетонное покрытие (JPCP)
•« Узловое »железобетонное покрытие» ( JRCP)
• Непрерывноеармированноебетонное покрытие (CRCP)
• Преднапряженноебетонноеодельное покрытие (PCP)
Критерии разрушения жестких покрытий
Усталостное растрескивание долгое время считалось основным или единственным критерием —
для проектирования жестких покрытий.Допустимое количество повторений нагрузки
, вызывающее усталостное растрескивание, зависит от соотношения напряжений между изгибным напряжением
при растяжении и модулем разрушения бетона. В последнее время перекачка
считается важным критерием отказа. Перекачивание — это выброс
суспензии грунта через стыки и трещины цементобетонного покрытия
, возникающий при движении плиты вниз под действием больших колесных нагрузок
. К другим основным типам повреждений жесткого покрытия относятся разломы
, отслаивание и износ.Поэтому для уменьшения трещин
в бетоне используются волокна для приклеивания бетонных поверхностей.
не разделяет частицы материалов, используемых в бетоне.
ПРЕИМУЩЕСТВА АРМИРОВАННОГО БЕТОНА из стекловолокна
(GFRC)
Есть много веских причин для использования GFRC для тонких секций бетона:
• Легче отлитые по более тонким профилям
и, следовательно, на 75% легче, чем аналогичные детали, отлитые из
из традиционного бетона.Согласно сообщению в блоге Джея Жирара,
, Преимущества использования смеси GFRC для столешниц, бетонная столешница
может иметь толщину 1 дюйм с GFRC, а не 2 дюйма
. при использовании обычной стальной арматуры.
• Высокая прочность: GFRC может иметьизносительную прочностьвысокую 4000 фунтов на квадратный дюйм
и имеет очень высокое отношение прочности к массе.
• Армирование: Так как GFRC армирован изнутри, нет
необходимости в других видах армирования, которые могут быть затруднены
для придания им сложных форм.
• Уплотнение: Для напыляемого GFRC вибрации не требуется. Для
заливки GFRC, вибрация или ролики легко использовать для достижения затвердевания
.
• Оборудование: «Дорогостоящее» оборудование не требуетсядля наливанияиливи-
крашеный стеклопластик с лицевым покрытием; для распыленного GFRC, оборудование, как правило,
союзника стоит около рупий. 50 000.
• Прочность: «GFRC» не взламывает легко — его можно «разрезать» без чипа —
ping.
• Поверхность Покрытие: Поскольку поверхность распыляется, поверхность не имеет ошибок
отверстий или пустот.
• Возможность адаптации: «Распыление» или «заливка» в форму, «GFRC» может адаптироваться к
практически любой сложной формы, от камней до мелких декоративных деталей.
• Долговечность: Согласно ACI544.1R-96, Отчету о состоянии техники по бетону, армированному волокном
, «прочность полностью состаренного бетона GFRC com-
снизится примерно до 40 процентов. начальной прочности при-
или старению ». Майкл Драйвер, руководитель подразделения Nippon Electric
Glass, главный производитель AR-стекла, не согласен. «Есть…
, никогда не- долговечная» проблема. «Вода» не может попасть внутрь — нет… трещин нет —
и «это прочный» материал. outlastprecastconcrete,
литой камень, даже немного натурального камня ». Прочность
была увеличена за счет использования слабощелочных цементов и пуццоланов.
• Устойчивый: «Поскольку в нем используется не цемент, а не эквивалентный бетон»
, а также часто используются значительные количества переработанных материалов (например,
пуццолан), GFRC квалифицируется как устойчивый.
ТАБЛИЦА: 3
ПРИМЕНЕНИЕ СТЕКЛЯННОГО ВОЛОКНА
Архитектура Строительство
Сборные
архитектурные
облицовки, архитектурные
молдингов и
и ландшафтный дизайн.
Промышленное и
сельскохозяйственное
Крыша, стены и
Окна, Ремонт,
Модульные здания.
Постоянный
Опалубка, инженерные сети,
Акустика, мосты
и туннели, вода
и дренаж.
ПРИМЕР
«Эффект стекловолокна на обычном портландцементном бетоне» Desh-
mukhSH, BhusariJ.P, ZendeA.M
Бетон — это строительный материал, слабый на растяжение. которые часто являются трещинами —
ден, связанными с пластическим и затвердевшим состояниями, усадкой при высыхании и
и т.п. Кроме того, бетон страдает низкой прочностью на разрыв, ограниченной пластичностью
и низким сопротивлением растрескиванию. Чтобы улучшить эти свойства
, была предпринята попытка изучить эффект добавления
стекловолокна в обычный портландцементный бетон.В настоящем эксперименте
периодических исследований стекловолокна в разном процентном соотношении от 0 до 0,1%
было изучено на предмет влияния на механические свойства бетона с помощью
, проводящего испытание на прочность при сжатии, испытание на изгибную прочность и испытание на прочность на разрыв
. Результаты показали улучшение механических свойств
и прочности за счет добавления стекловолокна.
В этом исследовании контрольная смесь A была разработана в соответствии с IS 10262: 1982–
, достигая целевой прочности на сжатие 20 Н / мм2.Были использованы стекловолокно
0%, 0,03%, 0,06% и 0,1% по объему бетона.
ТАБЛИЦА: 4
ПРОЧНОСТЬ НА СЖАТИЕ, ГИБКАЯ ПРОЧНОСТЬ, РАЗДЕЛЕНИЕ-
РЕЗУЛЬТАТЫ ИСПЫТАНИЙ НА ПРОЧНОСТЬ НА РАСТЯЖЕНИЕ ЗА 28 ДНЕЙ
Тип бетона
Средняя
Прочность на сжатие
000
Средняя0004
Прочность Н /
мм2
Расщепление
Растяжение
Прочность Н /
M-20 с 0.0% стекло
волокно
23,93 3,344
M-20 со стеклом 0,03%
волокно
26,07 3,587
волокно M-20 с содержанием стекла 0,06%
26,6 3.654
M-20 с содержанием стекла 0,1%
волокно
29,54 3,99
ВЫВОДЫ
Поскольку мы знаем, что бетон плохо воспринимает растяжение, поэтому для повышения его прочности на десять-
мы можем добавить стекловолокно, из-за которого волокна стекла
не будут отделять частицы из бетона.Добавление стеклянных волокон
в бетонную смесь незначительно улучшает прочность на сжатие
через 28 дней. Из экспериментальных результатов видно, что
прочность бетона на сжатие, изгибная прочность бетона,
прочность на растяжение при раскалывании бетона увеличивается с добавлением процентного возраста стекловолокна
. Добавление 0,1% стекловолокна в бетон
показывает лучшие механические свойства и долговечность.
БЛАГОДАРНОСТИ
Авторы выражают свою благодарность доктору CLPatel, Председателю, Charu-
tarVidyaMandal, Er.VMPatel, Hon.Jt.Secretary, CharutarVidyaMandal, CharutarVidya0005
Мистер Ятинбхай, Десай, Джей Махарадж, строительство, доктор Ф. С. Умригар, Главный,
BVM Инженерный колледж, доктор А.К. Верма, руководитель и профессор, структурный
Инженерный факультет, доктор Б.К. Шах, доцент, структурный
Инженерный отдел, B.V.M. Engineering College, Vallabh Vidyana-
gar, Гуджарат, Индия за их мотивационную и инфраструктурную поддержку
для проведения этого исследования.
(PDF) Бетон, армированный стекловолокном (GFRC)
Искендер, М., Карасу, Б.
159
[115] Криадо, М., Гарсия-Диас, И., Бастидас, Дж. М., Альгуасиль, ФК , Лопес, Ф.А., Монтичелли, К.,
«Влияние переработанного стекловолокна на коррозионное поведение армированного раствора»,
Construction and Building Materials 64, 2014, 261–269.
[116] Бхуопати Р., Рамеш М., Дипа К., «Производство и оценка свойств банана —
композитов, армированных коноплей и стекловолокном», Procedure Engineering 97, 2014, 2032–2041.
[117] Ван, Л., Чжан, Дж., Ян, X., Чжан, К., Гонг, В., Ю, Дж., «Свойства эпоксидной смолы на изгиб
Синтаксические пены, армированные стекловолоконной сеткой и / или короткое стекловолокно », Материалы и
Design 55, 2014, 929–936.
[118] Нигро, Э., Чефарелли, Г., Билотта, А., Манфреди, Г., Козенца, Э., «Рекомендации по сопротивлению изгибу
армированных бетонных плит и балок из стеклопластика при пожаре», Композиты, часть B 58,
2014, 103–112.
[119] Гарсия, Д., Вегас, И., Качо, И., «Механическая переработка отходов стеклопластика в виде коротких волокон
Армирование в микробетоне», Строительство и строительные материалы 64, 2014, 293–300.
[120] Хенриксен, Т., Ло, С., Кнаак, У., «Инновационный подход к производству тонкостенного бетона
, армированного стекловолокном, для ограждающих конструкций завтрашних архитектурных зданий со сложной геометрией
», Журнал строительства Инженерное дело 4, 2015, 189–199.
[121] Маранан, Б. Б., Манало, А. С., Бенмокран, Б., Карунасена, В., Мендис, П., «Оценка
флюсовой прочности и эксплуатационной пригодности геополимерных бетонных балок, армированных стекловолокном
– Армированные полимерные стержни (GFRP) », Engineering Structures 101, 2015, 529–
541.
[122] Пехливанлы, З.О., Узун, И., Демир, И.,« Механические и микроструктурные особенности автоклавного бетона с бортиком
Армированный автоклавированным полипропиленом, углеродом, базальтом
и стекловолокном », Строительные и строительные материалы 96, 2015, 428–433.
[123] Ге, З., Ван, Х., Чжан, К., Сюн, К., «Армированная стекловолокном асфальтовая мембрана для межслойного соединения
между асфальтовым покрытием и бетонным покрытием», Строительство и
Строительные материалы 101, 2015, 918–925.
[124] Ярек, Б., Кубик, А., «Исследование армированных стекловолокном полимерных композитных стержней
с точки зрения применения для армирования бетона», Procedure Engineering 108, 2015,
394–401.
[125] Шмитт, А., Карвелли, В., Пан, М., «Термомеханическое нагружение армированных стеклопластиком тонких бетонных панелей
», Композиты, часть B 81, 2015, 35–43.
[126] Миотто, Дж. Л., Диас, А. А., «Конструктивная эффективность полномасштабного композитного дерева и бетона
балок, усиленных полимером, армированным стекловолокном», Composite Structures 128, 2015,
145–154.
[127] Кушартомоа, В., Бали, И., Сулайман, Б., «Механическое поведение реактивного порошка
Бетон с заменителем стеклянного порошка», Технологии процедур 125, 2015, 617–622.
[128] Гарсия-Эспинель, Дж. Д., Кастро-Фресно, Д., Гайо, П. П., Баллестер-Муньос, Ф., «Воздействие моря
Водная среда на армированные стекловолокном пластмассовые материалы, используемые для морского гражданского строительства.
Инженерное дело Конструкции », Материалы и дизайн 66, 2015, 46–50.
[129] Феррейра, Д., Оллер, Э., Баррис, К., Торрес, Л., «Влияние деформации сдвига в ответной работе службы
армированных бетонных балок из FRP», Composite Structures 121, 2015, 142– 153.
[130] Паглиолико, С.И., Ло Версо, VRM, Торта, А., Жиро, М., Канонико, Ф., Лиджи, Л., «A
Предварительное исследование светопропускающих свойств полупрозрачных бетонных панелей с
Крупнозернистые включения из отработанного стекла », Энергетические процедуры 78, 2015, 1811–1816.
[131] Neagoe, CA, Gil, L., Pérez, MA, «Экспериментальное исследование гибридных балок из стеклопластика и бетона
с низкой степенью сопротивления сдвигу», Construction and Building Materials 101, 2015,
141–151 .
[132] Дас, С., Хендрикс, А., Стоун, Д., Нейтхалат, Н., «Реакция на излом нового железа
Карбонатная матрица — композит из стекловолокна и его сравнение с портландцементом
.Композиты », Строительные материалы 93, 2015, 360–370.
Синергетическое влияние полипропилена и стекловолокна на механические свойства и долговечность бетона из переработанного заполнителя | Международный журнал бетонных конструкций и материалов
Внешний вид Повреждения
На рисунке 5 показана морфология кубических образцов RAC и RAC с волокнами после разрушения при испытании на прочность на сжатие.На рисунке 5а наглядно показано хрупкое разрушение обычного КИП. После того, как образцы потрескались, большие куски мусора отвалились, и бетон был серьезно поврежден, что привело к очевидному локальному отслаиванию. После добавления полипропиленовых волокон на рис. 5b или стекловолокон на рис. 5с явного отслаивания не наблюдается, и видны только несколько вертикальных трещин и небольшие отслаивающиеся кусочки по краям, что указывает на то, что добавление волокон может замедлить развитие трещин и изменить хрупкое разрушение в пластическое разрушение. На рис. 5d показана вертикальная трещина, но без трещин или отслоений по краям и углам в RAC с гибридными волокнами.Эффект от добавления гибридного волокна для улучшения характеристик деформации RAC лучше, чем от использования любого типа волокна по отдельности. На рисунке 6 показан внешний вид RAC после 50 циклов замораживания-оттаивания. На рис. 6а видно, что куски цементного раствора отслаивались по краям и углам, а образцы имели плохую целостность. Рисунок 6b показывает, что смешивание полипропилена и стекловолокна с RAC ингибировало осыпание цементного раствора или песчинок, и образцы сохранили свою целостность.
Рис. 5Характер отказов RAC при сжатии: a RAC без волокон и b RAC с волокнами.
Рис. 6Видимое повреждение образцов RAC после 50 циклов замораживания-оттаивания солевого раствора: a RAC без волокон и b RAC с волокнами.
На рис. 7 показан внешний вид RAC после сочетанного действия механической нагрузки и циклов замораживания-оттаивания солевого раствора. На рис. 7а показано, что эталонный ППЦ имел отслоение цементного раствора по краям и углам на большой площади, и даже небольшое количество ПКА было обнажено. Совместное воздействие более серьезно повредило целостность, чем цикл замораживания-оттаивания.Рисунок 7b показывает, что смешивание полипропилена и стекловолокна с RAC сохраняло целостность образцов. По краям и углам практически не было отслаивания или отслаивания. Это указывает на то, что пластичность волокон задерживает денудацию цементного раствора из-за механической нагрузки и цикла замораживания-оттаивания и улучшает сопротивление отслаиванию.
Рис. 7Видимое повреждение RAC после механической нагрузки и циклов замораживания-оттаивания солевого раствора: a RAC без волокон и b RAC с волокнами.
Прочность на сжатие
В таблице 4 представлены результаты прочности на сжатие. RAC с волокнами показал более низкую 28-дневную прочность на сжатие, чем RAC без волокон. Это означает, что добавление волокон может отрицательно сказаться на прочности на сжатие. Добавление 1,0 кг / м 3 полипропиленовых волокон с соотношением масс коротких и длинных волокон 0: 1 (только длинные волокна), 3: 7, 5: 5, 7: 3 и 1: 0 (только короткие волокна) уменьшало прочность бетона на сжатие на 15,0%, 9,6%, 13,0%, 1,2% и 12,8% соответственно.Прочность на сжатие RCP73 была очень близка к прочности на сжатие RAC без волокон. Это указывает на то, что смешивание волокон разных размеров обеспечивает лучшую производительность, чем использование волокон одного размера. Добавление 1,0 кг / м стекловолокна 3 с массовыми отношениями короткие: длинные 0: 1, 3: 7, 5: 5, 7: 3 и 1: 0 снизило прочность на сжатие RAC на 15,0%, 14,0%, 12,1%, 6,2% и 9,4% соответственно. Прочность на сжатие RCG73 (соотношение 7: 3) была близка к прочности на сжатие RAC без волокон. Смешивание волокон двух разных размеров снизило отрицательное влияние на механические характеристики.Добавление 1,0 кг / м 3 гибридных волокон с соотношением масс ПП: стекло 0: 1, 3: 7, 5: 5, 7: 3 и 1: 0 снизило прочность на сжатие RAC на 15,0%, 11,1%. , 8,6%, 3,9% и 15,0% соответственно. Смешивание двух типов волокон вместо использования только одного типа снижает отрицательное влияние на механические характеристики. Прочность на сжатие RAC с соотношением 7: 3 была очень близка к прочности RAC без волокон.
Во многих исследованиях изучалось влияние добавления волокна на прочность на сжатие RAC, но однозначного вывода не было сделано.Некоторые результаты (Mohseni et al. 2017; Chen et al. 2016; Katkhuda and Shatarat 2017) показали, что добавление волокна может улучшить прочность на сжатие, но другие результаты (Kim et al. 2010; Dong et al. 2017) показали, что негативное воздействие. Результаты этого эксперимента показали, что включение полипропилена, стекла или гибридных волокон оказывает негативное влияние на прочность на сжатие RAC. Бетон обычно разрушается, потому что, будучи многофазным материалом, он содержит большое количество микротрещин, отверстий и других слабых звеньев.Когда бетон нагружается снаружи, в этих слабых звеньях возникают концентрации напряжений, и дальнейшее расширение трещин приводит к разрушению бетона. Уменьшение прочности на сжатие может быть связано с тем, что разница между модулями упругости и шероховатостью волокон и RAC формирует новый слабый интерфейс внутри RAC и вносит новый разрушающий фактор. Волокна также влияют на текучесть и удобоукладываемость и уменьшают компактность, что увеличивает внутренние дефекты RAC. В этом испытании прочность на сжатие демонстрирует немонотонное снижение по мере увеличения содержания длинных волокон в смешиваемых волокнах разного размера.Это указывает на то, что влияние различных комбинаций коротких и длинных волокон на механические свойства RAC очень сложно и не может быть точно предсказано с помощью упрощенного правила смесей. Основная причина заключается в том, что существует множество факторов, влияющих на прочность на сжатие RAC, не только длину волокна, но также его дисперсию и ориентацию волокна (Kasagani and Rao 2018). Дальнейшие исследования будут проводиться для количественной оценки влияния каждого из этих факторов на прочность на сжатие RAC, армированного волокном.
Воздействие замораживания-оттаивания солевого раствора
В соответствии с GBT50082-2009 (Стандарт для методов испытаний на длительные эксплуатационные характеристики и долговечность обычного бетона) потеря прочности на сжатие RAC определяется как
$$ Q = \ гидроразрыв {{f_ {0} — f_ {1}}} {{f_ {0}}} \ times 100 $$
(1)
, где Q — потеря прочности бетона на сжатие, \ (f_ {0} \) — 28-дневная прочность на сжатие RAC, а \ (f_ {1} \) — прочность на сжатие RAC после 50 циклы замораживания-оттаивания солевого раствора или совместное действие механической нагрузки и циклов замораживания-оттаивания солевого раствора.На рисунке 8 показана потеря прочности на сжатие RAC после 50 циклов замораживания-оттаивания и совместного действия циклов нагружения и замораживания-оттаивания.
Рис. 8Потеря прочности на сжатие RAC с волокном a PP, стекловолокном b и гибридным волокном c после 50 циклов замораживания-оттаивания солевого раствора и сочетанного действия механической нагрузки и замораживания солевого раствора –Тепловые циклы.
После 50 циклов замораживания-оттаивания солевого раствора и сочетанного действия механической нагрузки и циклов замораживания-оттаивания солевого раствора потеря прочности на сжатие с волокнами была намного ниже, чем без волокон.Это указывает на то, что волокна могут значительно улучшить морозостойкость и долговечность RAC. Потеря прочности на сжатие эталонного RAC и волоконного RAC была больше при совместном действии, чем только при циклах замораживания-оттаивания, особенно для эталонного RAC. Сочетание механической нагрузки и воздействия окружающей среды ускорило процесс ухудшения состояния окружающей среды.
Рисунок 8a показывает, что RCP37 имеет самые низкие потери прочности на сжатие — 5,2% и 11,9% с циклами замораживания-оттаивания солевого раствора и сопряженным действием, соответственно.RAC с большим содержанием длинных волокон (RCP01 и RCP37) имел более низкие потери на сжатие, чем RAC с большим содержанием коротких волокон (RCP73 и RCP10), что указывает на то, что длинные волокна из полипропилена более эффективны, чем короткие волокна, в улучшении долговечности RAC против совместное действие механической нагрузки и циклов замораживания – оттаивания солевого раствора. Рисунок 8b показывает, что RCG55 имеет наименьшие потери прочности на сжатие в циклах замораживания-оттаивания и сопряженного действия — 7,8% и 10,6%, соответственно. Потери при сжатии RAC были ниже при большем содержании длинных волокон (RCG01 и RCG37), чем при большем содержании коротких волокон (RCG73 и RCG10), что указывает на то, что длинные стеклянные волокна улучшают долговечность RAC в большей степени, чем короткие волокна.Более ранние исследования (Kasagani and Rao 2018) показывают, что волокна короткой длины помогают противостоять открытию микротрещин и повышают прочность перед трещинами, но могут вытягиваться после того, как микротрещины трансформируются в макротрещины, в то время как волокна большой длины могут перекрывать растрескивание и повышение устойчивости к растрескиванию. Следовательно, волокна большой длины обеспечивают большую армирующую способность, чем волокна короткой длины, что увеличивает предельную прочность на сжатие RAC за счет объединения волокон разных размеров после циклов замораживания-оттаивания солевого раствора и совместного действия.Рисунок 8c показывает, что RCH55 (соотношение массы ПП: стекла 5: 5) имел самую низкую потерю прочности на сжатие до 50 циклов замораживания-оттаивания при 4,3%. Потеря прочности на сжатие РЧ47 имеет наименьшую потерю прочности на сжатие из-за сопряженного действия — 8,0%. Морозостойкость RAC также улучшилась более значительно при смешивании двух типов волокон, чем при использовании только одного типа.
На поведение после растрескивания влияет разная длина волокна; Образцы с короткими волокнами показали способность к размягчению, тогда как образцы с более длинными волокнами показали пластичность или упрочнение, а также увеличение максимальной нагрузки (Olivito and Zuccarello 2010).Смешивание волокон разного размера в RAC позволяет более мелким волокнам перекрывать микротрещины и препятствовать их расширению в макротрещины. Между тем, волокна большего размера сдерживают макротрещины, когда RAC подвергаются внешним нагрузкам. При дальнейшем расширении трещин волокна потребляют большое количество энергии, что увеличивает ударную вязкость RAC. Влияние волокон разного размера на сдерживание распространения трещин RAC не изолировано. Волокно одного размера улучшает характеристики бетона, что может усилить функцию волокна другого размера и вызвать синергетический эффект (Teng et al.2018).
Сочетание двух типов волокон также дает синергетический эффект. Благодаря своей гибкости, волокна PP могут препятствовать образованию микротрещин RAC. Когда RAC подвергается совместному действию, добавление волокна PP может снизить концентрацию напряжений в слабых частях RAC. Когда микротрещины в RAC начинают расширяться и проникать в некоторые области, образуя большие трещины, стеклянные волокна имеют высокий модуль упругости и могут препятствовать дальнейшему расширению трещин. Когда два типа волокон с разными модулями упругости смешиваются в RAC, жесткие волокна (т.е.например, полипропиленовые волокна) препятствуют образованию внутренних трещин и предотвращают расширение трещин при малых нагрузках. Когда внешняя нагрузка велика, волокна ПП достигают предела прочности на разрыв и текучести. Затем волокна с высоким модулем упругости (то есть стекловолокна) в основном несут внутреннее растягивающее напряжение, чтобы предотвратить образование и дальнейшее расширение более крупных трещин.
Синергия комбинированных волокон
Чтобы понять эффективность комбинированных волокон в улучшении механических свойств и долговечности RAC, синергетический коэффициент был рассчитан для различных комбинаций волокон.Синергетический коэффициент комбинированных волокон для 28-дневной прочности на сжатие RAC определяется как
$$ \ alpha _ {\ text {c, ab}} = \ frac {{\ beta _ {{c, {\ text {a}) } b}}}} {{\ delta_ {a} \ beta_ {c, a} + \ delta_ {b} \ beta_ {c, b}}} — 1 $$
(2)
где \ (\ alpha _ {\ text {c, ab}} \) — синергетический коэффициент волокон a и b , \ (\ beta _ {\ text {c, ab}} \) — усиление коэффициент прочности на сжатие RAC с комбинированными волокнами a и b по сравнению с обычным RAC, \ (\ beta _ {\ text {c, a}} \) и \ (\ beta _ {\ text {c , b}} \) — коэффициенты увеличения прочности волокон a и b соответственно, а также \ (\ delta _ {\ text {a}} \) и \ (\ delta _ {\ text {b}} \ ) — массовые доли волокон a и b соответственно.Коэффициент улучшения прочности на сжатие определяется как
$$ \ beta _ {\ text {c}} = {\ raise0.7ex \ hbox {$ f $} \! \ Mathord {\ left / {\ vphantom {f { f_ {m}}}} \ right. \ kern-0pt} \! \ lower0.7ex \ hbox {$ {f_ {m}} $}} $$
(3)
где \ (f \) — прочность на сжатие армированного волокном RAC в течение 28 дней; \ (f_ {m} \) — это 28-дневная прочность на сжатие обычного RAC. Когда \ (\ beta _ {\ text {c}} \) больше 1, волокно увеличивает прочность на сжатие RAC; и наоборот, когда \ (\ beta _ {\ text {c}} \) меньше 1, волокно отрицательно влияет на прочность бетона на сжатие.
Синергетический коэффициент комбинированных волокон при воздействии циклов замораживания-оттаивания солевого раствора или совместного действия механической нагрузки и циклов замораживания-оттаивания определяется как
$$ \ alpha _ {\ text {d, ab}} = 1 — \ frac {{\ beta_ {d, ab}}} {{\ delta_ {a} \ beta_ {d, a} + \ delta_ {b} \ beta_ {d, b}}} $$
(4)
где \ (\ alpha _ {\ text {d, ab}} \) — синергетический коэффициент волокон a и b , \ (\ beta _ {\ text {d, ab}} \) — затухание коэффициент RAC с волокнами a и b относительно потери прочности на сжатие простого RAC, \ (\ beta _ {\ text {d, a}} \) и \ (\ beta _ {\ text {d, b}} \) равны коэффициенты затухания волокон a, и b, соответственно, а \ (\ delta_ {a} \) и \ (\ delta_ {b} \) являются массовыми долями волокон a и b, соответственно.Коэффициент затухания волокон в RAC определяется как
$$ \ beta _ {\ text {d}} = {\ raise0.7ex \ hbox {$ Q $} \! \ Mathord {\ left / {\ vphantom {Q { Q_ {m}}}} \ right. \ Kern-0pt} \! \ Lower0.7ex \ hbox {$ {Q_ {m}} $}} $$
(5)
, где Q — потеря прочности на сжатие армированного волокном RAC, а \ (Q_ {m} \) — потеря прочности на сжатие простого RAC.
Идея этого подхода заключается в том, что положительное значение (\ (\ alpha _ {\ text {c}} \), \ (\ alpha _ {\ text {d}} \)> 0) указывает, что гибридная комбинация волокон дает синергетический эффект с лучшими свойствами, чем сумма свойств, обеспечиваемых отдельными типами волокон.Нулевое значение синергетического коэффициента указывает на отсутствие синергизма, а отрицательное значение означает, что гибрид работает хуже, чем отдельные типы волокон. На рисунке 9 показаны рассчитанные синергетические коэффициенты. На рис. 9а показано, что коэффициенты синергизма и усиления 28-дневной прочности на сжатие RAC для различных массовых долей комбинаций волокон имели постоянную тенденцию и достигли пика при одной и той же доле. На рис. 9b, c показано, что синергетический коэффициент и потеря прочности на сжатие RAC из-за циклов замораживания-оттаивания и сопряженного действия для различных массовых долей комбинаций волокон имели постоянную тенденцию и достигли пика при одной и той же доле.Это означает, что синергетический коэффициент, представленный в этой статье, в основном правильный.
Рис. 9Синергетические коэффициенты для прочности на сжатие и долговечности RAC: a синергетические коэффициенты и коэффициенты улучшения 28-дневной прочности на сжатие, b синергетический коэффициент и потеря прочности на сжатие при замораживании-оттаивании 50 солевых растворов циклов, и c синергетический коэффициент и потеря прочности на сжатие при совместном действии механической нагрузки и циклов замораживания-оттаивания солевого раствора.
Синергетический коэффициент для 28-дневной прочности на сжатие RAC не всегда был больше нуля. Однако синергетический коэффициент RAC, подвергнутого циклам замораживания-оттаивания солевого раствора и сочетанному действию механической нагрузки и циклов замораживания-оттаивания, был намного больше нуля во всех случаях, за исключением RCP37, что указывает на то, что объединенные волокна имели значительный синергетический эффект. влияние на долговечность РАК. Это также означает, что смешивание коротких и длинных волокон улучшило долговечность RAC в большей степени, чем использование волокон одного размера, а сочетание полипропилена и стекловолокна имело больший эффект, чем использование любого типа волокна по отдельности.
Рисунок 9 показывает, что тенденции синергетических коэффициентов прочности на сжатие и долговечности при циклах замораживания-оттаивания солевого раствора и долговечности при совместном действии механического нагружения и циклов замораживания-оттаивания изменяются для различных массовых долей волокна. комбинации. Это указывает на то, что синергетический эффект различных комбинаций волокон на механические свойства и долговечность RAC очень сложен и не может быть точно предсказан с помощью упрощенного правила смесей, потому что механизмы предотвращения разрушения каждого волокна и взаимодействие между каждым волокном в матрице не являются согласно унифицированным моделям (Banthia et al.2014). Поскольку процессы повреждения при загрузке и циклах замораживания-оттаивания различны, прочность на сжатие и долговечность можно улучшить, правильно комбинируя волокна разных размеров и свойств для заданной объемной доли. Поэтому обратите внимание, что не все характеристики могут быть оптимизированы при одинаковой пропорции объединенных волокон.
Анализ микроструктуры
Для изучения механизма синергетического эффекта на RAC, SEM использовался для изучения поперечных сечений образцов до и после совместного действия в эксперименте.Продукты гидратации RAC до и после совместного действия и границы раздела между волокнами и матричными материалами были проанализированы на микромасштабе. На рисунке 10 показан анализ микроструктуры. На рис. 10а показано, что перед совместным действием механической нагрузки и циклов замораживания-оттаивания солевого раствора продукты гидратации заполняли поры и повышали стабильность структуры, придавая ей хорошую компактность. На рис. 10б видно, что после совместного воздействия микроморфология стала шероховатой и неупорядоченной, а плотность уменьшилась.Таким образом, прочность на сжатие каждой группы образцов значительно снизилась после совместного воздействия.
Рис. 10Микроструктура RAC до и после совместных воздействий механической нагрузки и циклов замораживания – оттаивания солевого раствора: микроструктура RAC a до, b после совместных воздействий; интерфейс c до и d после совместных действий; и следы вытягивания волокна e до и f после совместных воздействий.
На рисунках 10c, d показано, что поверхность волокна полностью контактировала с гелем, а общая микроструктура матрицы была компактной до сопряженного воздействия. После совместного воздействия в межфазной зоне присутствовало большое количество микропор, и трещины, распространяющиеся от тела цемента, распространялись на поверхность волокна. Таким образом, прочность переходной зоны границы раздела уменьшилась, и ударная вязкость каждой группы образцов значительно снизилась после совместного воздействия.
На рис. 10e, f показано, что след отрыва волокон до и после совместного действия был плавным.Это указывает на то, что вытягивание волокон было слабее. Общеизвестно, что нет химической связи между гидрофобным полипропиленовым волокном и матрицей и слабой связи между стекловолокном и матрицей. Кроме того, прочность границы раздела между волокном и бетонной матрицей уменьшается после совместного действия. Таким образом, прочность связи между волокном и бетонной матрицей была относительно низкой.
На рис. 10d, f показано, что трещина выходила из объема на границе раздела после совместного воздействия. Это объясняет, как волокна из полипропилена достигли предела прочности на разрыв и деформировались в микромасштабе при большой внешней нагрузке.В течение этого времени волокна с высоким модулем упругости (т.е. стекловолокна) в основном выдерживали внутреннее растягивающее напряжение и предотвращали образование и развитие более крупных трещин. Два типа волокон взаимодействовали, создавая синергетический эффект.
Цемент и гипс, армированный стекловолокном, на JSTOR
АбстрактныйЦемент, армированный стекловолокном, и гипсовая штукатурка представляют собой примеры композиционных материалов, в которых оба компонента являются хрупкими, а матричная фаза разрушается при гораздо более низкой деформации, чем волокно.В этих матрицах обычно присутствует пористость порядка 30% или более. Межфазное соединение, которое образуется между волокном и матрицей, очень прерывистое и неравномерное. Диспергировать стекловолокно в матрице непросто. Когда измельченные многоволоконные нити распределяются в матрице путем распыления, прочность на растяжение и изгиб композитного материала, полученного из гипсовой штукатурки, достигает максимальных значений около 10% от объема добавленного волокна. За пределами упругости композитный материал проявляет квазипластичность, пока не выходит из строя из-за вытягивания волокна.Огнестойкость и ударная вязкость штукатурки значительно улучшаются за счет включения волокон. Стекловолокно, имеющееся в настоящее время в продаже, не устойчиво к щелочной среде, присутствующей в гидратирующих портландцементах. Экспериментальные волокна, изготовленные из более стойких к щелочам стекол, изучаются на предмет их пригодности для армирования цемента и бетона. Можно предвидеть, что при использовании прочного стекла композитный материал будет иметь явные преимущества по сравнению с существующими листовыми материалами в отношении ударной прочности и устойчивости к растрескиванию, прочности на растяжение и изгиб и огнестойкости.
Информация об издателеКоролевское общество — это самоуправляемое товарищество многих самых выдающихся ученых мира, представляющих все области науки, техники и медицины, и старейшая научная академия, которая постоянно существует. Основная цель Общества, отраженная в его учредительных документах 1660-х годов, заключается в признании, продвижении и поддержке передового опыта в науке, а также в поощрении развития и использования науки на благо человечества.Общество сыграло роль в некоторых из самых фундаментальных, значительных и изменяющих жизнь открытий в истории науки, и ученые Королевского общества продолжают вносить выдающийся вклад в науку во многих областях исследований.
Разработка материалов FRC с использованием переработанного стекловолокна, извлеченного из промышленных стеклопластиковых акриловых отходов
Бетон, армированный волокном (FRC) и инженерные цементные композитные материалы, продемонстрировали многообещающую потребность в строительной отрасли благодаря своим превосходным механическим свойствам и долговечности.В этом исследовании был выбран устойчивый подход, то есть использование промышленных отходов в качестве арматуры с улучшенным межфазным сцеплением, что привело к улучшенным механическим характеристикам FRC. Эффективный процесс переработки на месте позволил авторам извлекать стекловолокно из полимерных акриловых отходов, армированных стекловолокном. Были приготовлены бетонные смеси с низкой дозировкой волокна, включая 0,1%, 0,2% и 0,3% (по объему) переработанного, а также первичного стекловолокна. Осадка бетона поддерживалась ∼150 мм с использованием высокой водоредуцирующей добавки (HWRA).Примечательно, что для сырого стекловолокна требовалось меньшее количество HWRA по сравнению с переработанным из-за его гидрофобной природы. В целом, FRC, содержащий 0,3% переработанного стекловолокна, продемонстрировал> 20% повышение прочности на сжатие, растяжение и изгиб по сравнению с контролем (после 28 дней отверждения), что также подтверждается морфологическим анализом.
1. Введение
Композиционные материалы на основе цемента демонстрируют лучшие характеристики при сжатии, чем при растяжении.Обычно древние конструкции, такие как арки и кладка, не армируются стальными прутьями. Единственная цель стальных стержней в бетоне — действовать в качестве основного материала, который может выдерживать огромные растягивающие напряжения, тем самым увеличивая общую пластичность конструктивного элемента. С развитием технологий исследователи начали искать другие альтернативы для усиления конструкции. Поскольку коррозия стальных стержней значительно повлияла на свойства материала, что в конечном итоге привело к разрушению конструкции, одним из возможных решений было использование натуральных или синтетических волокон.Случайно распределенное армирование волокном в таких матрицах, как полимер / бетон, получило огромное признание и признание в коммерческих приложениях уже более двух десятилетий, в основном в строительном, автомобильном, морском и авиационном секторах [1–8].
Полимерный материал, армированный стекловолокном (GFRP), обладает такими свойствами, как высокое отношение прочности к весу, высокая коррозионная стойкость и низкие эксплуатационные расходы, а также простота изготовления. В результате материалы на основе стеклопластика могут выдерживать высокие структурные нагрузки, увеличивать долговечность, служить отличным рентабельным ремонтным материалом и, таким образом, являются отличной альтернативой обычным материалам [3–5, 8–12].Коммерчески жизнеспособные продукты, производимые с использованием GFRP, включают в основном автомобильные детали, ванны, печатные платы, лодки и аэрокосмические компоненты. Исследователи также пытались интегрировать армирование фиброй в бетонный материал, называемый фибробетоном (FRC) [1, 13–20]. Листы, изготовленные из FRC или GFRP, устанавливаются на балки, колонны и плиты для предотвращения коррозии конструкции, а также для увеличения ее долговечности [21]. Волокна, которые успешно используются для повышения прочности и долговечности бетонных инфраструктур, включают стекло [1, 7, 10, 11, 18, 22, 23], сталь [1, 10, 11, 14, 15, 17, 24], углеродные волокна [24–28] и полипропиленовые волокна [13, 15, 17, 29].В частности, свойства изгиба и усадки значительно улучшились при добавлении волокон в цемент [16, 18, 22, 30]. В частности, работа, проведенная группой Banthia [16, 22, 30], продемонстрировала, что улучшенные свойства FRC зависят от таких параметров, как ориентация волокна, соотношение вода / цемент, объемная доля волокна и внутренние характеристики самого волокна. Именно из-за этих факторов и анизотропного поведения моноволокон (в частности, стекловолокон) исследователи сообщили о различных результатах.В результате произошел значительный рост синтеза стекловолокна с последующим его использованием в качестве армирующего материала для различных применений по всему миру.
Например, в начале 1900-х годов сантехническая промышленность производила ванны из керамического материала, но с развитием технологий его заменили композитами из стеклопластика. Композиты GFRP изготавливаются либо с использованием термореактивного полимера (например, эпоксидной смолы), либо термопластичного полимера (например, акрила) вместе со стекловолокном, и после отверждения получается легкий, высокопрочный и долговечный композитный материал.Трехмерная сшитая структура материала улучшает его характеристики и долговечность по сравнению с керамической. В настоящее время большая часть отходов FRP на основе термореактивных материалов либо сжигается, либо вывозится на свалки, что приводит к негативным воздействиям на окружающую среду и дополнительным расходам для производителей и поставщиков FRP [9, 31–36]. Кроме того, исследователи отметили, что переработка отходов стеклопластика на основе термореактивных материалов является сложной задачей [9, 23, 31, 37–39], а также добавляет неценную стоимость для владельца их использования в производственном процессе.Следовательно, более широкое использование GFRP в коммерческих целях также приводит к увеличению производства отходов GFRP.
Санитарная промышленность воспользовалась этой концепцией создания композитов, таких как стеклопластик. Отходы, образующиеся в сфере санитарии (поступающие от выброшенных продуктов и обрезанных обрезков), представляют собой серьезную проблему [40, 41]. Кроме того, эти отходы по сравнению с традиционным стеклопластиком еще сложнее переработать, поскольку они представляют собой не только смолу, армированную стекловолокном, но также тонкое покрытие из акрила, полиметилметакрилата (ПММА) и термопластической смолы в качестве отделочной поверхности, с экологической и экономической точки зрения [41–43].В данной статье авторы определяют эти отходы как отходы полимера акрила, армированного стекловолокном (GFRPA). Усовершенствованные термохимические методы, такие как пиролиз и методы псевдоожиженного слоя, показали положительные результаты с точки зрения переработки отходов GFRPA и регенерации стекловолокна, а также смолы [31, 41]. В частности, Эсмизаде и др. [41] описали преимущества, а также недостатки различных механизмов рециркуляции ПММА, таких как термический крекинг, каталитический крекинг, применение высокой температуры и пиролиз.Автор предпринял попытку разработать нанокомпозиты путем повторного использования переработанных отходов ПММА. Но, напротив, процесс рециклинга привел к отрицательному эффекту с точки зрения прочности на разрыв переработанного стекловолокна, где прочность волокна была снижена до 50–90% по сравнению с первичными волокнами [23]. Кроме того, во время этого процесса выделяются вредные газы, такие как CO и CO 2 , что приводит к загрязнению окружающей среды [35, 44]. Таким образом, возможность вторичной переработки как производственных отходов, так и продуктов с истекшим сроком службы (EOL) стала важной и жизненно важной проблемой во всем мире.Исследования по переработке отходов GFRPA и повторному использованию последующих рециклатов ограничены [40, 45]. Казинс и др. [45] использовали процесс растворения для извлечения составляющих материалов из термопластичных композитных отходов, а также использовали регенерированные стеклянные волокна для изготовления нового материала. Интересно отметить, что новый материал с переработанными стеклянными волокнами показал более высокую жесткость и механическую прочность по сравнению с первичными волокнами, что предполагает возможность повторного использования переработанных стеклянных волокон и возможность продажи волокон и смолы по более низкой цене в различных отраслях промышленности.Однако Correia et al. [23] сообщили об ухудшении характеристик бетона (связанных с механическими свойствами и долговечностью) из-за использования отходов стеклопластика на основе термореактивных материалов в бетонной смеси и предложили использовать низкую дозировку отходов стеклопластика в неструктурных приложениях в качестве средства поддержки управления отходами материалов из стеклопластика. Однако, с повышением осведомленности об окружающей среде, исследователи в прошлом определили и внедрили несколько методов извлечения стекловолокна из акриловых отходов [41, 45], но все же результаты не были столь многообещающими.Кроме того, описанные до сих пор работы по использованию отходов GFRPA очень ограничены с точки зрения экологически безопасных методов извлечения и использования в качестве арматуры в бетоне.
Таким образом, в этой статье авторы представляют экономичный и экологичный метод извлечения стекловолокна, а также акрилового порошка из промышленных отходов. На сегодняшний день в литературе описаны различные химические и механические процессы; однако все они, по-видимому, оказывают воздействие на окружающую среду, а также связаны с более высокой стоимостью процесса [40, 41, 45].
Кроме того, в настоящем исследовании изучается влияние использования переработанного стекловолокна из акриловых отходов на различные механические свойства, такие как прочность на сжатие и изгиб, а также прочность на разрыв при разделении при использовании в качестве арматуры в бетоне. Наконец, рентабельность более точно оценивается путем сравнения результатов механических испытаний, полученных для аналогичных бетонных смесей, армированных первичным стекловолокном, и путем наблюдения морфологии первичного и вторичного стекловолокна под электронным микроскопом.
2. Материалы и методы
Одной из интересных методологий, описанных в этом исследовании, является отделение стекловолокна и полимерной смолы от отходов GFRPA в лабораторных условиях. Авторы разработали процесс механической переработки in situ , который позволяет собирать количественное количество переработанного стекловолокна из отходов GFRPA, обеспечивая тем самым экологически безопасное решение для промышленности. Кроме того, это переработанное стекловолокно также имеет большой потенциал для разработки экологически чистого ремонтного материала для бетона.В результате переработанные стеклянные волокна анализировали на их морфологическую структуру с помощью сканирующего электронного микроскопа (SEM) и на химический состав с помощью EDX, а затем сравнивали с первичными (необработанными) волокнами.
Бетонные цилиндры диаметром 100 мм (4 дюйма) и высотой 200 мм (8 дюймов) были отлиты для исследования прочности бетона как на сжатие, так и на разрыв. Напротив, образцы призм размером 100 мм × 100 мм × 350 мм были отлиты для оценки прочности бетонной смеси на изгиб.Для каждого из упомянутых выше испытаний отливали по три образца с армированием волокном и / или без него. Параметры исследования включают контроль (без волокна) и 2 типа волокна (переработанное и сырое стекловолокно), каждый с дозировкой волокон 0,1%, 0,2% и 0,3%. В результате получено в общей сложности 105 испытательных образцов (84 цилиндрической формы и 21 призматической формы). Подробности о том, как подготовить эти образцы, обсуждались в разделе 2.2.
2.1. Материалы
В настоящем исследовании использовался обычный портландцемент (OPC) общего назначения, тип 10, так как он соответствует требованиям к цементу типа I и типа II согласно стандартам ASTM C150 [46].Естественно, что доступные агрегаты, обнаруженные в карьере Sechelt в Британской Колумбии (Канада), были использованы в исследовании в качестве крупных агрегатов. Эти агрегаты имели максимальный размер 25 мм и характеристики поглощения 0,69%.
Кроме того, в этой экспериментальной работе в качестве мелкого заполнителя использовался природный песок, имеющийся в том же карьере. Собранный из ямы песок подвергали встряхиванию сит для определения различного размера частиц. Результаты суммированы в таблице 1. Примечательно, что мелкие заполнители имели модуль крупности 2.61 и абсорбция 0,79%.
|
Кроме того, авторы использовали высокодисперсный водовосстанавливающий агент (HWRA) или суперпластификатор MasterGlenium® 3030.Этот суперпластификатор содержит поликарбоксилатный эфир, который действует как катализатор, повышая удобоукладываемость или величину осадки бетонной смеси. Исследование Asokan et al. [47] заявили, что добавление 2 об.% Суперпластификатора увеличивает прочность на сжатие бетона, приготовленного из отходов стеклопластика, на 11%. Кроме того, автор сообщил о положительном эффекте включения отходов стеклопластика на усадку при высыхании, а также на компактность бетона для потенциального использования в конструкционных и неструктурных применениях.
Как указывалось ранее, в настоящем исследовании были выбраны два типа стекловолокна, а именно: сырое стекловолокно (первичное) и переработанное стекловолокно. Свойства сырых и переработанных волокон указаны в Таблице 2. Можно видеть, что переработанные стеклянные волокна примерно такого же диаметра, как и исходные, но имеют меньшую длину. Этого следовало ожидать, поскольку процесс изготовления ванн не меняет диаметр волокна. Кроме того, диаметры первичного и переработанного стекловолокна были подтверждены анализом SEM (более подробную информацию см. В разделе 3.1). Как правило, первичные волокна из Е-стекла обладают пределом прочности на разрыв от 3,1 до 3,8 ГПа. В этой статье инновационное и экономичное извлечение и подготовка вторичного волокна в качестве арматуры в бетоне подробно обсуждались в разделе 2.4.
|
2.2. Дизайн смеси
В настоящем исследовании руководствовались рекомендациями ACI 211.1-91 [48] для определения дизайна смеси обычного бетона. Пропорции смеси для изготовления образцов бетона обсуждаются ниже.
Для поддержания осадки 150 мм был использован заполнитель с максимальным размером 25 мм и безвоздушный цемент.Кроме того, соотношение вода: цемент 0,45 было выбрано из таблицы A 1.5.3.4 (a) ACI 211.1, чтобы подготовить образцы бетона с разумной прочностью на сжатие. Кроме того, согласно стандарту ACI, на 1 м 3 бетона требовалось 0,67 м сухого стержневого грубого заполнителя. С учетом этого было рассчитано необходимое количество мелких заполнителей. В Таблице 3 кратко описан дизайн смеси, использованный в настоящем исследовании для разработки FRC-бетона с отходами GFRPA.
|
Кроме того, согласно ACI 211.1-91, рекомендуется добавить 10% дополнительной воды для лабораторных испытаний для достижения требуемой осадки. Однако в этом исследовании авторы рассматривали добавление 0,3% HWRA вместо добавления дополнительной воды для поддержания значения осадки около 150 мм, прочности на сжатие около 50 МПа для контрольного бетона и для облегчения диспергирования волокон в бетонной смеси.
В настоящем исследовании несколько рассмотренных параметров привели к получению 7 различных бетонных смесей, 6 из которых были основаны на вторичном и необработанном стекловолокне (Таблица 3).Стекловолокно использовалось в качестве частичного заменителя мелких заполнителей при различных объемных концентрациях цемента для отливки образцов FRC. Как указано в Таблице 3, аббревиатуры CV1, CV2 и CV3 относятся к бетонным смесям, которые содержат 0,1, 0,2 и 0,3 об.% Первичных (сырых или первичных) стекловолокон, соответственно. Точно так же бетон CR1, CR2 и CR3 был приготовлен с использованием 0,1, 0,2 и 0,3 об.% Переработанного стекловолокна, соответственно. Смесь CCON, указанная в таблице 3, была приготовлена для проведения сравнительного анализа контрольной смеси по отношению к образцам FRC.Пропорции смеси вместе с массой на кубический метр (в кг / м 3 ) цемента, песка, заполнителей, воды, суперпластификатора и волокон также указаны в таблице 3.
2.3. Процедура смешивания и отверждения
Все ингредиенты бетона, такие как цемент, крупные и мелкие заполнители, вода, стекловолокно и HWRA, были взвешены с помощью цифровых весов. Во время дозирования сначала все грубые и мелкие заполнители вместе со стекловолокном были смешаны на умеренной скорости с помощью барабанного смесителя в течение 1 минуты для получения однородной сухой смеси.После этого цемент был добавлен в сухую смесь посредством непрерывного процесса смешивания, постепенно вливая 70% воды, необходимой для превращения в пасту. Оставшееся количество воды было добавлено в цементную пасту для получения бетона с приемлемой удобоукладываемостью, подтвержденной перекрестной проверкой путем записи значения осадки и затем, наконец, помещения пасты в формы. Примечательно, что синтетический химикат был распылен на боковые стороны внутренней поверхности форм, чтобы предотвратить прилипание бетона к форме для облегчения изготовления.После заполнения форм бетоном их подвергали уплотнению на вибростоле в течение 1 минуты, чтобы избежать образования сот.
Наконец, свежую смесь оставили для отверждения при комнатной температуре (15 ± 3 ° C) на 24 часа. Через 24 часа образцы вынимали из формы и помещали в водяную баню при 23 ± 2 ° C на 7 и 28 дней отверждения.
В следующем разделе рассказывается о творческом подходе авторов к извлечению стекловолокна из промышленных отходов.
2.4. Экстракция стеклянных волокон из акриловых отходов
Производственный процесс включает приготовление ванны с использованием смеси смолы Aropol с отвердителем, поскольку она смачивает случайные пряди стекловолокна внутри формы до тех пор, пока она не затвердеет.
Этот процесс включал измельчение жгута стекловолокна с помощью измельчителя и включение нагретой жидкой смолы. Следует также отметить, что это делается вручную с помощью пистолета-распылителя, и материал, поступающий на приемную форму, подлежит оценке человеком.После затвердевания тонкий лист акрила, ПММА, термоформовывается на верхнюю поверхность ванны для обеспечения высокой стойкости к царапинам и ударам готового продукта. ПММА считается экономичной альтернативой поликарбонату (ПК) из-за его умеренных свойств, простоты обращения и обработки, низкой стоимости и характеристик прозрачности. Отходы, полученные от промышленности, показывают, что целевой объем волокна в полимерной матрице составляет около 10–15%, что дает объем волокна 6–9%, если в качестве матрицы рассматривать все акрил и смолу.С этого момента авторы будут использовать слово «матрица» как термин для обозначения комбинации смолы и ПММА для разъяснения читателям. В целом, во время производственного процесса остатки (края и небольшие кусочки) акрила собираются в основном во время процессов резки и сборки вакуумного формования, что называется отходами GFRPA.
Авторам удалось собрать количественные отходы GFRPA в основном с двух участков промышленной площадки: производственной линии и контроля качества.Рабочие отрезали лишние края, свисающие после изготовления ванны, с помощью резака, в результате чего был получен образец, как показано на Рисунке 1. Авторы определили, что в настоящее время эти акриловые отходы (из промышленности) вывозятся промышленными предприятиями на свалки. Однако с инженерной точки зрения они твердо верили, что переработка этих отходов может иметь двойную выгоду, то есть экологическую и экономическую.
2.4.1. Состав и свойства отходов GFRPA
Во-первых, авторы определили следующие физические и химические свойства отходов: (i) Размер: варьируется от 150 мм до 200 мм (ii) Толщина отходов: 4.От 70 мм до 5,00 мм (iii) Смола для армирования стекловолокна: смола Aropol TM K 1866–18 C (45% стирола) (iv) Доля отходов GFRPA (по объему): стекловолокно 6–9%, смола 65–70 % и PMMA ~ 25%
Aropol классифицируется как ненасыщенная полиэфирная смола, которая обладает свойством, заключающимся в том, что после отверждения, т.е. сшивки со стиролом, жидкость превращается в твердое вещество и сохраняет форму формы. Эта смола демонстрирует исключительно высокие характеристики прочности и долговечности. Комбинация смолы с полимером ПММА и отвердителем приводит к получению материала, который является легким, имеет высокую прочность, демонстрирует стойкость к химическим веществам, обеспечивает отличную отделку поверхности и водоотталкивающие свойства и, следовательно, является отличным источником для изготовления ванн.
Как обсуждалось ранее в Разделе 1, переработка отходов GFRPA является сложной задачей и представляет собой проблему для более здорового сообщества. Существующая практика имеет тенденцию выделять во время процесса вредные газы, такие как CO и CO 2 , что в конечном итоге приводит к загрязнению окружающей среды. Учитывая вышеизложенные факты и для разработки недорогого процесса рециклинга (на месте), авторы предпочли механический (экологичный) метод извлечения стекловолокна из акриловых отходов.Короче говоря, механическая переработка и процесс измельчения имеют такие преимущества, как (i) отсутствие загрязнения атмосферы выбросами газа, (ii) требуется гораздо более простое оборудование по сравнению с печами, необходимыми для термического процесса, и (iii) отсутствие необходимости в химических растворителях с последующие воздействия на окружающую среду [9, 23, 49, 50]. Хедлунд-Остром [50] рассмотрел оценку жизненного цикла (LCA) и окончания срока службы (EOL) полимерных композиционных материалов и предложил модель переработки, которую можно было бы использовать для существующих больших объемов отходов GFRP, которая является рентабельной и экологически чистой. .Аналогичным образом Ribeiro et al. [49] и Мейра Кастро и др. [9] производили полиэфирные полимерные растворы, содержащие отходы стеклопластика, полученные в процессе измельчения и измельчения, и сообщили об улучшенных механических свойствах с использованием вторичного армирования в качестве наполнителя.
Принимая во внимание выводы из литературы, авторы представляют в этой статье трехэтапный экологически чистый процесс механической переработки, осуществляемый на коммерческой «Дробильно-измельчающей системе», как показано на Рисунке 2, с мощностью 45 кВт. закуплено у Zhangjiagang City Yili Machinery Co.Ltd., Китай, для получения переработанных отходов GFRPA. Краткое описание процесса приведено ниже:
2.4.2. Механическое измельчение
Оборудованием управлял обученный техник, который подавал большие прямоугольные куски оставшихся акриловых композитных отходов (размером 150 × 150 мм или 200 × 200 мм) для измельчения. Измельчитель разбил эти большие листы GFRPA на мелкие гранулы (10–50 мм), как показано на Рисунке 3, примерно за 3-5 минут (в зависимости от объема).Система одновременного водяного охлаждения в шлифовальном станке позволит ему работать непрерывно и эффективно, пока весь требуемый объем не будет измельчен. В конце этого процесса небольшие отходы GFRPA были собраны в поддон в нижней части измельчителя, который представлял собой смесь стеклянных волокон с покрытием PMMA наверху. Следующим шагом было отделение арматуры GFRP от слоя PMMA.
2.4.3. Рекультивация стекловолокна
На этапе 2 измельченные отходы GFRPA из этапа 1 служили исходным материалом, который помог отделить лист PMMA и некоторое количество смолы от арматуры GFRP с помощью высокоскоростного, имеющегося в продаже вентилятора.Поскольку измельченные отходы свободно падали перед вентилятором, из-за эффекта веяния вентилятора волокна с меньшей плотностью опускались дальше, что приводило к отделению основного слоя ПММА (и некоторого количества смолы) от образцов GFRP. Как показано на Рисунке 4, регенерированные стекловолокна могут содержать некоторое количество связанной смолы. Точно так же отдельные акриловые куски включают смолу и некоторую фракцию волокон, которые внедрены в куски ПММА.
Авторы заметили, что этот процесс воспроизводится, имея эффективность 80–90% для регенерации стекловолокна.После этого использовали сито 600 мкм мкм для отделения мелкой пыли от полученных стекловолокон.
2.4.4. Измельчение полимерных отходов
Наконец, на этапе 3, цель состояла в том, чтобы приготовить мелкий порошок полимерных отходов с использованием шлифовального станка. В результате авторы пропустили большие куски акриловых отходов и небольшие гранулы акрила, собранные на предыдущих двух этапах, через промышленную дробилку. В итоге авторы получили очень мелкий порошок, как показано на рисунке 5.Этот мелкодисперсный порошок потенциально может быть использован в качестве армирующего наполнителя при разработке полимерных композиционных материалов и цементных композиционных материалов. Интеграция порошка в качестве частичной замены цемента в бетоне была сохранена как будущая область этого исследования. Напротив, собранные переработанные волокна продемонстрировали сильную связь друг с другом, вероятно, из-за смолы, прикрепленной к их поверхности. Исходя из этих наблюдений, авторы предполагают, что это соединение может повлиять на дисперсию волокон в цементе.
2.5. Характеристика
2.5.1. Технологичность
Технологичность образцов GFRC и нормального бетона измерялась с использованием ASTM C143.
2.5.2. Прочность на сжатие бетона
Прочность на сжатие образцов GFRC и нормального бетона была получена с использованием ASTM C39 [51]. Все испытания на сжатие проводились с использованием пилота-испытателя Forney грузоподъемностью 650 тысяч фунтов. Образцы цилиндрической формы диаметром 100 мм (4 дюйма) и длиной 200 мм (8 дюймов) с контрольным бетоном и FRC были испытаны через 7 и 28 дней отверждения для определения прочности на сжатие.Подготовка образца включала шлифовку бетонных цилиндров для удаления шероховатой поверхности. Позже к цилиндрам постепенно прикладывалась сжимающая осевая нагрузка, пока не произошло разрушение, а затем была отмечена пиковая нагрузка. Впоследствии эта информация была использована для расчета прочности материала на сжатие. Для каждой смеси были протестированы 3 образца, и в этом документе указано среднее значение.
2.5.3. Прочность на растяжение при разделении
ASTM C496 использовался для измерения прочности бетона на разрыв при разделении [52].Испытания на растяжение при разделении были проведены на всех бетонных смесях и трех образцах каждой смеси, и среднее значение было указано в этой статье. Цилиндрические образцы бетона диаметром 100 мм (2 дюйма) и длиной 200 мм (4 дюйма) были испытаны летчиком-испытателем Форни грузоподъемностью 65000 фунтов. Диаметральное сжимающее усилие по длине цилиндра прикладывалось до тех пор, пока не произошло разрушение, и была записана пиковая нагрузка. В результате предел прочности при раскалывании рассчитывали по следующей формуле: где P = пиковая нагрузка в Ньютонах, l = длина цилиндра в мм и d = диаметр цилиндра в мм.
2.5.4. Свойства изгиба бетонных образцов с использованием замкнутой системы
Для оценки изгибных характеристик GFRC, в настоящем исследовании использовался ASTM C1609 [53]. Четырехточечный изгиб с использованием замкнутой и сервоуправляемой испытательной системы MTS 250 K, имеющей нагрузку 250 кН, был использован для получения кривой нагрузки-прогиба. Затем рассчитывались характеристики изгиба образцов призмы / балки (имеющих размеры: 100 мм (4 дюйма) × 100 мм (4 дюйма) × 350 мм (14 дюймов)) с использованием параметров, полученных из кривых нагрузки-прогиба.
Для загрузки использовалась замкнутая система; отклонение в центре призмы измерялось и использовалось для контроля скорости отклонения. Размах призмы оставался постоянным и составлял 300 мм (12 дюймов), а расстояние между загрузочными роликами составляло 100 мм (4 дюйма). Чтобы достичь режима замкнутого контура, авторы убедились, что сборка зажимного приспособления оставалась прикрепленной к балке, чтобы правильно удерживать LVDT (линейный регулируемый дифференциальный трансформатор). Два LVDT, как показано на рисунке 6, эффективно поддерживали отклонение со скоростью 0.025 мм / мин до отклонения L / 900 и 0,05 мм / мин сверх L / 900. Характеристики изгиба GFRC до стадии растрескивания определяли по первой пиковой прочности. Однако для определенного прогиба остаточная прочность характеризует остаточную емкость после растрескивания. Первый пик прочности рассчитывали по следующей формуле. Ту же формулу можно использовать для расчета модуля разрыва при конкретном прогибе: где P = нагрузка в Ньютонах, L = длина пролета в мм, b = ширина образца в мм и d = глубина образца в мм.
2.5.5. Морфологический и химический анализ
Растровый электронный микроскоп HITACHI S-4800 использовался для анализа морфологии поверхности образцов бетона, в то время как EDX позволил определить химический состав переработанного стекловолокна и сырого стекловолокна. Кроме того, образцы были покрыты слоем углерода толщиной 10 нм, чтобы сделать поверхность образца проводящей и повысить скорость образования вторичных электронов.
3. Результаты и обсуждение
3.1.Свойства стекловолокна
3.1.1. Необработанные стеклянные волокна
Рубленые первичные стекловолокна из промышленности по производству ванн были собраны для этого исследования, как показано на Рисунке 7 (а). С помощью рубильного пистолета их длина была сокращена до 15 мм от ровницы. Кроме того, для регистрации физических и химических свойств этих необработанных стекловолокон были проведены SEM и EDX характеристики. Морфологический анализ показал, что волокна имели диаметр 14 мкм м (рис. 7 (b)), тогда как EDX-анализ на рис. 7 (c) показал отсутствие циркония (Zr).Замечено, что стекловолокно чувствительно к щелочам в пасте портландцемента, но волокна с Zr продемонстрировали устойчивость к разрушению щелочью [54, 55].
3.1.2. Переработанное стеклянное волокно
Кроме того, для сравнения регенерированного стекловолокна с необработанным, авторы провели морфологический и химический анализ образцов, собранных после завершения процесса экстракции (раздел 2.4). Во время анализа SEM авторы заметили, что диаметр отдельного переработанного стекловолокна был аналогичен диаметру исходного стекловолокна, т.е.е., ∼14 мкм м (рис.8, а). Кроме того, под микроскопом наблюдались более толстые пучки переработанных волокон из-за того, что полимерная смола скрепляла несколько прядей волокон вместе (рис. 8 (b)). Наконец, химический состав (рис. 8 (c)) переработанного стекловолокна, легированного смолой, демонстрирует максимальную концентрацию таких ионов, как Ca, S и O, что подчеркивает обильное присутствие сульфата кальция. Дополнительный сульфат кальция подвергнется реакции гидратации и будет действовать как катализатор в повышении прочности бетона на сжатие.
3.2. Технологичность бетона
При приготовлении образцов фибробетона важно поддерживать удобоукладываемость, что обычно достигается путем регистрации величины осадки. Было замечено, что добавление волокон в бетон имеет тенденцию влиять на его удобоукладываемость. В результате исследователи решили эту проблему, добавив в цемент восстановитель с высоким содержанием воды (HWRA), также известный как суперпластификатор. Исследователи рекомендовали максимальную концентрацию 2% (от содержания цемента) для образцов FRC для поддержания значения осадки бетона выше 150 мм.Принимая во внимание это явление, авторы провели серию экспериментов, и каждый раз осадку бетона измеряли с помощью конуса, как описано ранее. Значения осадки, полученные для различных бетонных смесей, указаны в таблице 4.
|
Значения в таблице 4 показывают, что концентрация HWRA варьировалась в зависимости от типа волокна, а также от количества волокна в цементе. Образцы первичного стекловолокна (CV) требовали более высокой концентрации по сравнению с образцами переработанного стекловолокна (CR). Интересно, что смесь CV3, содержащая 0,3% сырых стекловолокон, имела минимальную осадку, то есть 130 мм, но самое высокое содержание HWRA, равное 1%. Использование 1% суперпластификатора в FRC считается более высокой дозировкой согласно Aruntas et al.[56]. Кроме того, экспериментальные результаты показывают, что по мере увеличения процентного содержания стекловолокна требуется более высокая дозировка HWRA для поддержания осадки около 150 мм и борьбы с эффектом жесткости армирующих волокон. Кроме того, более высокое количество HWRA в бетоне действовало как катализатор для преодоления гидрофильного поведения стекловолокна. Примечательно, что для бетона, приготовленного из переработанного стекловолокна, требовалось меньшее количество HWRA по сравнению с необработанным стекловолокном. Возможно, это связано с тем, что переработанное стекловолокно существовало в виде пучка, и на его поверхности также было покрытие из смолы.Покрытие, возможно, уменьшило адсорбцию воды волокнами, и, таким образом, для этой бетонной смеси требовалось меньшее количество HWRA. Таким образом, можно утверждать, что добавление волокон влияет на удобоукладываемость бетона и, кроме того, зависит от типа и количества волокон. В частности, переработанное стекловолокно показало лучшие характеристики в бетоне, чем сырое. Интересно наблюдать за последствиями обрабатываемости на различных механических свойствах, которые обсуждались в следующих разделах статьи.
3.3. Прочность на сжатие
На рис. 9 показаны абсолютные значения средней прочности на сжатие после 7 и 28 дней режима отверждения как для вторичного, так и для необработанного стекловолокна с различными концентрациями волокна по сравнению с контрольным.
FRC, приготовленный с использованием 0,3% переработанного стекловолокна, показал максимальное увеличение, 21,46% (с 43,02 до 52,25 МПа), по сравнению с контрольными образцами. Примечательно, что тенденция к увеличению прочности наблюдалась при увеличении дозировки переработанного стекловолокна.Возможная причина для объяснения этого явного поведения может быть связана с увеличением содержания сульфата кальция в матрице, вызванным переработанными стеклянными волокнами, присутствующими в образце. Напротив, никаких значительных изменений не наблюдалось, когда образцы бетона были армированы первичным стекловолокном. Даже при увеличении дозировки волокна до 0,2% прочность увеличилась всего на 1,47%. Прочность значительно упала (до 40,11 МПа), когда дозировка волокна была увеличена до 0,3%, как показано на Рисунке 9.Возможное объяснение низкой прочности смеси CV3 по сравнению с контрольной смесью связано с ее низкой удобоукладываемостью, что привело к менее плотной микроструктуре по сравнению с другими смесями.
Кроме того, отверждение образцов в течение 28 дней и последующие испытания продемонстрировали аналогичное поведение, как показано на Рисунке 9. Авторы сделали важное наблюдение, что прочность на сжатие образцов FRC, приготовленных из переработанного стекловолокна, увеличилась примерно на 20%. специально для дозировки волокна 0,1 и 0,2% по сравнению с аналогичными образцами при отверждении в течение 7 дней.Это показывает, что бетон набрал 90% своей прочности в течение первых 7 дней, что демонстрирует надежность экспериментального исследования. Кроме того, средняя прочность на сжатие, зарегистрированная для 0,3% переработанного образца стекловолокна, все еще была максимальной, 59 МПа, по сравнению с 48 МПа для контроля. Напротив, образцы бетона, приготовленные с использованием первичного стекловолокна, продолжали демонстрировать ухудшение со временем отверждения, а также с увеличением дозировки волокна при испытании через 28 дней.
Следовательно, из этого испытания можно сделать вывод, что переработанное стекловолокно превзошло показатели прочности на сжатие по сравнению как с контрольными образцами, так и с образцами из первичного стекловолокна.
3.4. Прочность на разрыв при разделении
Прочность на растяжение считается одним из основных и важных свойств бетона. Как правило, бетон очень слаб при растяжении из-за его хрупкости, и поэтому не ожидается, что он будет противостоять действующим на него силам растяжения, что приведет к образованию трещин. Именно по этим причинам авторы были заинтересованы в определении пиковой нагрузки, при которой элементы из фибробетона могут растрескаться, а также были ли какие-либо изменения в механизме разрушения, такие как от хрупкого до пластичного.
На рисунке 10 показана прочность на разрыв при разделении, полученная для двух типов волокна вместе с 3 различными дозировками по сравнению с контрольным образцом после 7-дневного режима отверждения. Из рисунка 10 можно увидеть, что контрольный образец имел прочность на разрыв при разделении 2,45 МПа, и с введением волокон в качестве армирующего материала наблюдается увеличение прочности при различных дозировках волокон.
Интересно, что FRC, приготовленный с дозировкой переработанного стекловолокна 0,3%, показал максимальное увеличение на 22%, 2.От 45 до 2,99 МПа относительно контрольного образца. Более прочное соединение между поверхностью волокна и цементной матрицей, возможно, противодействует внешним силам, прикладываемым во время испытания, и, таким образом, приводит к увеличению прочности на сжатие и растяжение. Напротив, прочность на разрыв FRC, полученного из сырых стеклянных волокон (CV1, CV2 и CV3), также показала улучшение по сравнению с контрольной смесью. Однако в этом случае прочность 2,86 МПа была зафиксирована для дозировки сырого волокна 0,2%, тогда как она немного снизилась до 2.83 МПа при дозировке 0,3%. Это еще раз показывает, что увеличение дозировки волокна, возможно, привело к плохой обрабатываемости и агломерации волокон в матрице, что имеет тенденцию влиять на свойства бетонной смеси.
Дальнейшее отверждение образцов в течение 28 дней показало улучшение прочности на разрыв при раздельном растяжении, как показано на Рисунке 11, и, как наблюдалось ранее для результатов прочности на сжатие (Рисунок 9). По сравнению с образцами с 7-дневным режимом отверждения, аналогичная картина прочности на разрыв визуализируется для образцов FRC, т.е.е. максимальное значение 3,46 МПа зафиксировано для образца бетона из переработанного стекловолокна 0,3%. Прочность на разрыв образца CR3 увеличилась на 24% и 11% по сравнению с контролем и CV3, соответственно. Кроме того, по мере увеличения процента переработанного стекловолокна увеличивается прочность на разрыв при разделении. Краткий обзор рисунка 11 показывает, что увеличение прочности на разрыв через 28 дней для смеси CV1 и CV2 выше по сравнению со смесью CR1 и CR2. Следовательно, из этого теста можно утверждать, что армирование сырых стекловолокон с 0.Содержание 1% также оказывает значительное положительное влияние на разделительную прочность бетона на растяжение. Об аналогичном улучшении прочности на разрыв также сообщили Гупта и Бантия [16] при армировании бетона различными типами первичного волокна.
Таким образом, можно констатировать, что переработанное стекловолокно показало лучшие характеристики, чем сырое стекловолокно и контрольный бетон, с точки зрения как прочности на сжатие, так и прочности на разрыв, в частности, при дозировке волокна 0,3%. Авторы полагают, что лучшая производительность при более высокой дозировке переработанного стекловолокна в FRC способствует управлению отходами материалов FRP.
3.5. Прочность на изгиб
После исследования поведения FRC как в условиях сжимающей, так и при растягивающей нагрузке, стало интересно наблюдать за эффектом волокон в условиях изгибной нагрузки. С этой целью авторы провели испытание на четырехточечный изгиб с использованием замкнутой системы, как описано ранее в документе для всех смесей. Абсолютные значения средней прочности на изгиб, полученные в результате экспериментального исследования после 28 дней отверждения, представлены на рисунке 12.
Контрольный образец бетона имел среднюю прочность на изгиб 4,70 МПа. Анализируя фиг. 12, становится очевидным, что увеличение дозировки волокна приводит к повышению прочности материала. Интересно, что при дозировке 0,1% как сырые, так и переработанные образцы стекловолокна демонстрируют аналогичное увеличение прочности, примерно на 7%. Напротив, прочность на изгиб смесей CV2 и CV3 была сравнительно выше, чем у смесей CR2 и CR3, соответственно. Кроме того, чистый прогиб при растрескивании также оказался выше для смеси CV3 по сравнению со смесью CV1.Возможной причиной такого поведения является более высокая прочность на сжатие, полученная для смеси CV1 по сравнению со смесью CV3. Подобное поведение авторы также наблюдали для CR1, чем для смеси CR3. Анализ этого испытания показывает, что добавление 0,3% сырых стеклянных волокон увеличивает прочность на изгиб на 28,93%, в то время как добавление переработанных стеклянных волокон с той же концентрацией увеличивает прочность на 22,16%. Ранее сообщалось о подобном улучшении прочности на изгиб за счет включения отходов стеклопластика [33] и правильной ориентации волокон в цементирующей матрице [22].
Следовательно, можно констатировать, что необработанные стеклянные волокна показали лучшие характеристики в отношении прочности на изгиб, но в целом переработанные стеклянные волокна показали лучшее улучшение других механических свойств. Таким образом, положительные экспериментальные результаты, полученные с использованием переработанного стекловолокна, по-прежнему подтверждают мнение авторов о переработанном стекловолокне, поскольку оно может обеспечить более устойчивое, экологичное и экономичное решение для будущих структурных разработок строительной отрасли в целом. .
До сих пор авторы сообщали о механическом воздействии, но также важно проанализировать влияние волокон и различных концентраций волокон на границу раздела волокно-матрица, что было выполнено путем анализа морфологии сломанных образцов.
3.6. Морфологический анализ
Изломанные поверхности двух образцов, т. Е. Бетона, армированного необработанным и переработанным стекловолокном с дозировкой 0,3%, были проанализированы для изучения границы раздела волокно-матрица и химического состава.В связи с этим образцы были обезвожены путем помещения в вакуумную камеру на пару часов перед анализом на сканирующем электронном микроскопе. После этого на образцы наносился слой углерода толщиной 15 нм. Морфология образцов CV3 (сырые волокна) и CR3 (переработанные волокна) различалась, как показано на рисунках 13 (a) –13 (c) и 14 (a) –14 (c), соответственно.
На рис. 13 (a) показано изображение, полученное с помощью SEM, при увеличении 300x, наглядно демонстрирующее, что необработанные стеклянные волокна были беспорядочно ориентированы в бетоне в виде агломератов, в то время как выдергивание волокон также было видно.Наличие выдергивания волокон подчеркивает плохое межфазное сцепление волокон с бетонной смесью, что, в свою очередь, оправдывает более низкую прочность на сжатие и прочность на разрыв, о которых сообщалось ранее в этой статье. Кроме того, при большем увеличении (Рисунок 13 (b)) был исследован химический состав конкретного участка на поверхности образца, и результаты были сведены в таблицу, как показано на Рисунке 13 (c). Из таблицы (представленной на Рисунке 13 (c)) можно понять, что в 3 разных местах, в частности, PA 60, который относится к необработанному стекловолокну, основная концентрация — это кремний, который является основным компонентом стекловолокна. .Однако PA 58 и 59 сообщают о присутствии ионов кремния, алюминия и кальция, что, возможно, связано с некоторой ковалентной связью между стеклянными волокнами и C-S-H, а также гелем C-A-H внутри границы раздела.
Напротив, микроскопический анализ рециклированного стекловолоконного бетона (как показано на Рисунке 14) сильно отличается от анализа, полученного с использованием сырых стекловолокон. На рисунке 14 (а) стеклянные волокна кажутся ориентированными в продольном направлении, окруженными толстым матричным слоем и присутствующими небольшими пучками.Это подчеркивает тот факт, что между цементными материалами и стекловолокном была лучшая межфазная связь, благодаря чему образцы продемонстрировали значительно лучшие характеристики во время различных механических испытаний. Внимательно проанализировав Рисунки 14 (c) и 13 (c), можно отметить, что в переработанном стекловолокне более высокая комбинированная концентрация кальция, кремния, серы и алюминия по сравнению с необработанным стекловолокном. Несколько более высокая концентрация гидрата силиката кальция на границе раздела объясняет положительное влияние, наблюдавшееся ранее на прочность бетона на сжатие.Следовательно, механические характеристики FRC кажутся оправданными после анализа изломанных поверхностей.
Авторы считают, что это исследование можно расширить, увеличив дозировку переработанного стекловолокна в цемент, чтобы изучить влияние на усадочные свойства. Кроме того, остаточный мелкодисперсный порошок, собранный путем просеивания стекловолокна, может действовать как один из наполнителей при приготовлении бетонного материала, что может привести к созданию экологически чистой и экономичной альтернативы портландцементу.После этого можно исследовать механические свойства бетона.
4. Выводы
На основании результатов этого экспериментального исследования были сделаны следующие выводы: (1) Механический метод рециклинга in situ продемонстрировал количественную регенерацию стекловолокна и порошка ПММА из отходов GFRPA. Техника веялки была эффективной в отделении стеклопластиков от измельченных отходов. После этого мелкое сито помогло удалить мелкодисперсный полимерный порошок из переработанных стеклянных волокон.(2) Переработанные стеклянные волокна, по-видимому, имели покрытие из смолы, которое способствовало их существованию в пучках, как это видно на сканирующем электронном микроскопе. Ионы силиката кальция (гипса) были идентифицированы на границе раздела волокно-матрица с использованием EDX-анализа, который помог улучшить механические характеристики бетона. Острые изломанные края стекловолокна подтвердили хрупкое разрушение бетонного материала во время механических испытаний. (3) Прочность бетонной смеси на сжатие увеличивалась по мере увеличения процентного содержания переработанного стекловолокна как в течение 7, так и 28 дней по графику отверждения.В случае смесей FRC, армированных первичными волокнами, прочность на сжатие снижалась для 0,2% (28 дней отверждения) и 0,3% (7 и 28 дней отверждения) дозировок волокна по сравнению с контрольной смесью. Напротив, максимальное улучшение в 22% было достигнуто для 0,3% объемной доли переработанного стекловолокна по сравнению с контрольным образцом бетона как в течение 7, так и 28 дней режима отверждения. (4) Включение обоих типов стекловолокна продемонстрировало положительный эффект. влияние на разрывную прочность бетона.Кроме того, увеличение дозировки волокон в смеси показало увеличение прочности как на 7, так и на 28 дней цикла отверждения. Интересно, что снова 0,3% переработанного стекловолокна имело максимальный предел прочности на разрыв 3,46 МПа против 2,48 МПа (контроль). Кроме того, образцы необработанного стекловолокна с более низкой концентрацией показали немного лучшую прочность, чем другие волокна. Авторы считают, что на результаты прочности на разрыв частично повлияла прочность бетона на сжатие для этой смеси.(5) Наконец, армирование первичным и переработанным стекловолокном (с увеличивающейся концентрацией) также повысило прочность бетона на изгиб. По сравнению с контрольным образцом средняя прочность на изгиб была увеличена на 29% и 22% для первичных и переработанных образцов стекловолокна, соответственно, после 28 дней отверждения при объемной доле смеси 0,3%. Однако все бетонные смеси имели хрупкое разрушение, и прогиба после трещин не наблюдалось.
Доступность данных
Экспериментальные данные, использованные для подтверждения выводов этого исследования, будут предоставлены по запросу.
Конфликт интересов
Авторы заявляют об отсутствии конфликта интересов в отношении публикации этой статьи.
Выражение признательности
Эта исследовательская работа была поддержана Канадским советом по естественным и инженерным исследованиям (NSERC) (Engage Grant No. 501581-16). Авторы хотели бы поблагодарить г-на Рама Бансала и г-жу Рави Бич из Valley Acrylic Inc. за их поддержку в предоставлении акриловых отходов GFRP, что является важным вкладом в проведение этого исследования.
Цемент, армированный стекловолокном | Журнал Concrete Construction
Стекловолокно в качестве армирования портландцементной пасты рассматривалось как интересная, но экзотическая возможность. В сочетании с цементом он обеспечивает высокую ударопрочность, повышенную прочность на растяжение и изгиб, а также общее снижение веса. Однако до недавнего времени не существовало стекловолокна, достаточно стойкого к щелочному воздействию гидратированного портландцемента, чтобы сделать его практичным строительным материалом.Такое стойкое к щелочам стекло было разработано в Англии Building Research Establishment и Pikington Brothers Limited. После пяти лет совместной разработки двух организаций цемент, армированный стекловолокном (GRC), теперь становится новым и универсальным материалом для строительной отрасли. Стекловолокно, устойчивое к щелочам, может поставляться в виде непрерывной нити, рубленой нити, шерстяного каната или тканого материала. Обычно он поставляется в виде непрерывной или рубленой пряжи, а композиты из стеклопластика производятся одним из трех стандартных методов производства с последующим периодом отверждения.Процесс предварительного смешивания требует смешивания почти так же, как перлит, вермикулит или пенополистиролбетон; рубленое волокно вводится в цементный раствор в кастрюле или лопастной мешалке. Смесь заливается вибрацией. В присутствии небольшого количества подходящей смазочной добавки, такой как полиэтиленоксид или метилцеллюлоза, можно было ввести в цементную смесь от пяти до шести процентов по объему волокон длиной 25 миллиметров. Этот предварительно смешанный материал можно отливать, распылять, лить под давлением или экструдировать.В технике прямого распыления измельченные волокна длиной 38 миллиметров и цементный раствор одновременно наносятся из ручного пистолета в форму. Этот метод особенно подходит для таких применений, как архитектурные облицовочные панели. Автоматический метод распыления аналогичен, за исключением того, что пистолет для фиброцементного раствора автоматически проходит через форму, когда форма проходит под ним. Используется водоцементное соотношение 0,5, а избыточная вода удаляется всасыванием с нижней стороны листа после изготовления.Пока цемент еще не затвердел, материал можно легко формовать в двухмерной форме.
.