Укрепляющие пропитки для ремонта бетонного пола
Новый уровень качества
Бетонный пол может представлять собой самостоятельное покрытие или же служить основой для каких-либо декоративных напольных материалов. Залитая вручную, особенно из замешенной прямо на объекте цементной смеси, такая стяжка обычно требует доработки.
Базовыми требованиями, предъявляемыми к бетонному покрытию, являются его механическая прочность, ровность поверхности и отсутствие пыления. Немаловажным фактором, определяющим выбор именно бетонного пола, является его сравнительно невысокая себестоимость (как самих материалов, так и строительных работ) при обеспечении достаточно длительного срока эксплуатации.
Бетонные полы в чистом виде, то есть без устройства дополнительного декоративного и защитного слоя, находят своё применение, когда дело касается больших помещений и находящихся под открытым небом площадок. В основном это складские и производственные площади плюс то, что касается автомобильного и иного транспорта (ангары, гаражи, парковки), а также открытые склады, летние кафе и т.п.
Причём открытые площадки находятся в наиболее уязвимом положении, поскольку помимо стандартного набора нагрузок подвергаются разрушительному воздействию ультрафиолета и перепадов температуры и влажности. При этом происходит разрушение бетонного пола, появляется сетка мелких трещин, сколы и раковины. Через открывающиеся поры в тело бетона проникают агрессивные компоненты, которые только увеличивают интенсивность разрушения.
Если бетонная поверхность предусматривает движение автотранспорта, на первый план выходит стойкость к повреждениям. Когда при устройстве стяжки применяются бетоны высоких марок (М300 или М400), это создаёт определённый запас прочности покрытия на некоторое время. Но применение низкомарочного бетона очень быстро приводит к возникновению проблем.
Степень повреждений пола зависит от многих параметров, однако царапаться и истираться будет любое покрытие.
Вне зависимости от марки на поверхности бетона также происходит постоянное и весьма значительное пылеобразование. Причина кроется в составе цемента, точнее, результате его взаимодействия с атмосферой. Именно образующиеся в больших количествах солевые соединения и «пылят». Причём процесс этот может продолжаться бесконечно. Прекратить пылеобразование можно только путём устройства дополнительного полимерного покрытия или пропитки бетона особыми обеспыливающими и укрепляющими составами.
Как правило, для большинства бетонных полов декоративное оформление поверхности не требуется, поэтому и применение дорогих полимерных покрытий не совсем оправдано. Однако сохраняются требования к прочности, долговечности, влагостойкости и отсутствию пылеобразования. Поэтому в дело вступают особые составы – укрепляющие и обеспыливающие пропитки для бетона. Они могут применяться как при устройстве новых бетонных полов, так и ремонте старых. При этом стоимость подобных материалов значительно ниже полимерных покрытий, а срок эксплуатации больше.
Выбор типа пропитки для бетона
Выбор типа пропитки зависит от нескольких факторов. Необходимо принимать во внимание качество поверхности, марку бетона, условия нанесения (влажность обрабатываемой основы, температуру нанесения и полимеризации состава) и условия эксплуатации пола.
Силикатная пропитка
Одной из самых популярных является силикатная обеспыливающая пропитка Антидаст. Её особенность в том, что состав не создаёт на поверхности бетонного пола собственной плёнки. Упрочнение происходит за счёт глубокого проникновения материала непосредственно в саму структуру бетона и связывания присутствующих там солей, шлаков и иных частиц. Происходит скрепление компонентов бетона примерно такими же связями, какие имеются в его собственной кристаллической решётке.
Сама силикатная пропитка имеет водную основу, поэтому избыточная влажность стяжки ей не помеха. Однако это накладывает и определённые ограничения на температурный диапазон во время использования и в период набора прочности бетона. Температура нанесения силикатного состава должна быть не ниже +5°С (наиболее активна пропитка при температуре не ниже +10°С). Набор бетоном прочности (14 дней) также должен происходить при положительных температурах.
Необходимым условием также является наличие в теле бетона необходимой концентрации цементного связующего, соответствующей марке бетона не ниже М200 (класс B15). Дело в том, что пропитка использует их для создания сплошной кристаллической решётки и в случае недостатка компонентов эффективность обработки резко снижается. Наиболее эффективен Антидаст при работе со свежеуложенными бетонными полами.
Полиуретановая пропитка
Полиуретановый состав (например, пропитка VL-Floor) создаёт на поверхности бетона особый слой, кардинально отличающийся от той структуры, которую создаёт пропитка силикатным материалом. Марка бетона здесь уже не имеет такого значения.
Полиуретановая пропитка представляет собой однокомпонентный высокодисперсный материал и предназначена для обработки и упрочнения пористых и слабых бетонных оснований, предотвращения пылеобразования, грунтования стяжек перед укладкой декоративных напольных покрытий и рулонной гидроизоляции. Состав прост в применении, обладает отличной адгезией к любым бетонным поверхностям, быстро полимеризуется.
Проникая вглубь структуры бетона, пропитка взаимодействует с атмосферной влагой и полимеризуется, образуя прочный полимербетонный слой. Такое покрытие эластично и выдерживает небольшие подвижки основания, морозостойко и невосприимчиво к длительному воздействию воды. Глубина проникновения полиуретана зависит от открытости пор бетона и текучести состава. В слабых пористых бетонных основаниях материал способен проникнуть на достаточно большую глубину.
Чем выше температура, тем выше текучесть пропитки и её проникающая способность. Но даже и низкие отрицательные температуры не мешают материалу проникать вглубь бетона на необходимую для обеспечения требуемых качеств глубину. Поскольку основным связующим веществом является однокомпонентный полиуретан (при его взаимодействии с водой образуется непрочная полиуретановая пена), главным ограничением по применению такой пропитки является влажность бетона (не более 5%).
Эпоксидная пропитка
Связующим в двухкомпонентной эпоксидной пропитке на водной основе WB-Floor является эпоксидная смола. При взаимодействии состава с бетоном образуется механически прочное и химически стойкое полимербетонное соединение. Раз пропитка на водной основе, то и влажность бетона большого значения не имеет. Это простой в использовании водорастворимый материал, который имеет исключительно высокую адгезию ко всем видам оснований.
В верхней части покрытия создается обладающий уникальными характеристиками слой. Он способен в десятки раз увеличить прочность слабых бетонов, поверхность пола становится химически стойкой и абсолютно невосприимчивой к влаге, держит даже отрицательное гидростатическое давление. Основные ограничения накладывает температура. Нанесение материала и его полная полимеризация должны происходить при положительных температурах.
Окончание: Технология нанесения пропиток на бетонную поверхность
Пропитка для бетона: водоотталкивающая, полиуретановая и другие
Для улучшения качеств бетона в определенных условиях используют различные вещества, которые воздействуют на внутреннюю структуру стройматериала, придавая новые свойства. Одно из них – полиуретановая пропитка для бетона. Особенность этого средства и отличие от других добавок заключается в том, что оно наносится на готовую цементированную поверхность и модифицирует только внешний слой толщиной до 5 мм.
Основные функции пропитки
Из названия становится понятен принцип действия средства: жидкость пропитывает бетонный слой. Главные задачи:
- Увеличивает прочность. Поверхность бетона становится менее уязвимой к механическим воздействиям (ударам, трениям и др.), что повышает износостойкость и увеличивает срок службы строительной конструкции. Это свойство полезно на складах, парковках, в гаражах и других местах, где часто транспортируются грузы и перемещается техника.
- Делает бетон устойчивым к атмосферным условиям. Актуальна такая обработка для внешних поверхностей, на которые воздействуют солнце, влага, ветер, перепады температур.
- Защищает бетон от влияния агрессивных химических составов.
На основе полиуретана
Полиуретановая смесь – это универсальная формула, выполняющая сразу несколько функций. Средство действует как обеспыливающая и упрочняющая пропитка для бетона. Полимерный состав проникает на толщину 4 мм, закрывает поры и хорошо связывает между собой частицы строительного материала. Покрытие применяют в основном для пола в тех местах, где бетон испытывает постоянные нагрузки: в гаражах, на торговых площадках, парковках, в сельскохозяйственных загонах и др.
Полиуретановая пропитка нетоксична после высыхания, несмотря на выделение запахов. Применять состав можно как на промышленных объектах, так и в бытовых условиях. Данное вещество также защищает бетон от химических реагентов и применяется на производстве, в ремонтно-сборочных мастерских и в других местах, где осуществляется работа с ГСМ и химикатами.
Эстетичность – неоспоримое достоинство полимерной пропитки. Состав придает обрабатываемой поверхности глянцевый эффект (не такой сильный, как в журналах или на полиуретановых полах, но привлекательный). При этом бетон не становится скользким и легко подвергается уборке.
Особенности нанесения покрытия:
- Пропитка устойчива к низким температурам, поэтому обработку цементного слоя проводят даже в мороз.
- Состав высыхает быстро, уже через день по полу можно ходить, а через 3 суток – подвергать максимальной механической нагрузке.
- Обрабатываемой поверхности легко придать окраску, для этого в средство добавляют краситель. Цветная пропитка для бетона продается уже в готовом виде. Однако если необходимо окрасить бесцветный состав, следует обращать внимание на совместимость красителя и исходного вещества.
При таком количестве полезных и необходимых функций полиуретановая смесь стоит недорого и при этом отличается небольшим расходом.
Доказано практикой: экономия на укрепляющей пропитке нерациональна. Одноразовое вложение в покрытие всей поверхности позволяет надолго защитить бетонный слой. В противном случае уже через 3-4 года подверженные усиленной нагрузке участки требуют ремонта и обновления материала.
Защита от влаги
Акриловая смесь – это легкая водоотталкивающая пропитка для бетона, доступная по цене. Состав обладает стойкостью сохранения цвета и не разрушается от ультрафиолета. Эти качества позволяют использовать пропитку на улице, на открытых поверхностях и в местах воздействия излучающей техники.
Акриловая смесь дополнительно обеспыливает бетон при условии отсутствия высоких силовых нагрузок. При использовании состава для наружных работ покрытие наносят раз в 2-3 года.
Водоотталкивающие свойства акриловой пропитки не так сильно выражены, как у эпоксидной. Последняя – наиболее эффективная защита от влаги. На рынке представлены как красящие, так и бесцветные смеси. Кроме водоотталкивающей функции, важная задача эпоксидного наполнителя – сопротивление износу. Бетонный слой становится неуязвимым к абразивному воздействию и механическому стиранию поверхности.
youtube.com/embed/OGciIrfcsEw?feature=oembed&wmode=opaque» frameborder=»0″ allow=»autoplay; encrypted-media» allowfullscreen=»»/>Обработка эпоксидной пропиткой – ответственный процесс. Сорок минут – и смесь загустевает, становясь непригодной к нанесению. Готовят гидрофобный состав порциями, размер которых определяется скоростью работ, чтобы пропитка не успевала застыть. Диапазон температур нанесения – от + 5 до + 20 градусов по Цельсию.
Эпоксидные смеси применяются в медицинских и пищевых учреждениях, а также в бассейнах и подвальных помещениях с повышенной влажностью, в том числе находящихся под влиянием грунтовых источников.
Испытание на прочность
«Крепкий орешек» в ряду покрытий – пропитка для бетона Монолит-20М, обеспечивающая надежность цементной поверхности. Основные выполняемые функции – это повышение плотности слоя путем образования кристаллов и увеличение прочности за счет использования водостойкого геля.
Основой состава служит вода – универсальный растворитель, поэтому Монолит-20М – это экологически нейтральное соединение, не приносящее вреда окружающей среде и здоровью человека. Не имеет запаха, обладает стойкостью к высоким температурам.
Частично, за счет тех же кристаллов, образующихся в структуре пропитки под действием воды, средство ограничивает проникновение влаги в нижние слои бетона. Несмотря на высокую стоимость, укрепляющая смесь служит долго и не требует регулярного обновления.
А вот пропитка для бетона Аквастоун (дословно – вода и камень) обладает меньшим укрепляющим действием, но более глубоким проникновением (до 10 мм), что несвойственно другим покрытиям. Формула средства построена на неорганических составляющих и целевых добавках, растворенных в воде.
Результат от использования пропитки Аквастоун получается такой же, как и от Монолит-20М, а иногда – даже лучше. Это связано с тем, что состав хотя и укрепляет слой всего в 2-3 раза (а не в 5-6), но проникает на двойную глубину, и малое действие компенсируется большим объемом обрабатываемого бетонного слоя.
Укрепляющая пропитка для бетона | Plastall™ Украина
Полы в мастерских, на предприятиях, в складских и хозяйственных помещениях подвержены интенсивному износу. Пористая поверхность традиционных бетонных покрытий способствует быстрому поглощению влаги и всевозможных химикатов, которые разрушают структуру материала, снижают технические и эксплуатационные характеристики пола. В итоге полы становятся эстетически непривлекательными и даже непригодными к эксплуатации.
Решить эту проблему помогают укрепляющие пропитки по бетону, являющиеся жидкими составами на эпоксидной, полиуретановой или акриловой основе. Их применение не требует значительных затрат, а результат превосходит все ожидания.
Укрепляющие пропитки делают поверхность прочней, предотвращают образование мелкой цементной пыли, препятствуют впитыванию воды, масел и химических жидкостей. Они содержат полимеры, присадки, минеральные вещества и специальные компоненты, способные закупоривать капилляры бетона и создавать водостойкую, прочную пленку.
Использовать пропитки для бетона рекомендуется еще до начала эксплуатации помещения.
Также есть возможность упрочнения старых бетонных полов, имеющих множество трещин, выбоин и других дефектов. Это позволяет продлить срок службы покрытий, улучшить их внешний вид и решить проблему пылеобразования в техническом помещении.
Преимущество пропитывающих средств заключается в том, что они подходят практически для любых помещений. Они имеют доступную стоимость, легко наносятся и быстро схватываются. Перед их нанесением не нужно тщательно обрабатывать поверхность или наносить поверх старого пола новую стяжку.
Существует несколько разновидностей пропиток, отличающихся составом, способом нанесения, свойствами.
Грунтовки
Код | Назначение | Цена |
---|---|---|
1015 | Грунтовка бетонных и цементных оснований с повышенной влажностью для внутренних и наружных работ. На эпоксидной основе. | 294 |
8001П | Грунтовка для внутренних работ предприятий пищевой промышленности, организаций общественного питания. На эпоксидной основе. | 344 |
3201 | Грунтовка бетонных и цементных оснований для внутренних и наружных работ. На полиуретановой основе. Может использоваться в качестве связующего при приготовлении эластичных смесей. | 364 |
D301 | Полиуретановый грунт для упрочнение бетонных и цементных оснований, перед нанесением защитных покрытий на различных промышленных объектах, для внутренних и наружных работ. | 353 |
D801 | Грунтовка с высоким сухим остатком для внутренних и наружных работ на предприятиях пищевой, нефтехимической и фармацевтической промышленностях. Грунтование в системах покрытия для бетонных и металлических оснований. | 339 |
Пропитки
Код | Назначение | Цена |
---|---|---|
1007 | Пропитка основания под наливные полы, под защитное покрытие. На эпоксидной основе для наружных работ | 332 |
1005 | Пропитка бетонных и цементных оснований с повышенной влажностью под напыление и окрашивание, для наружных и внутренних работ. На эпоксидной основе.![]() | 348 |
D103 | Водорастворимая пропиточная композиция на базе эпоксидных смол, не содержащая растворитель. Для внутренних и наружных работ. Наносится на различные виды цементосодержащих оснований. | 294 |
3205 | Пропитка основания под наливные полы, под защитное покрытие. На полиуретановой основе для внутренних и наружных работ. | 388 |
Цены указаны в гривнах на 01.10.2018
Силикатные пропитки
Чтобы предотвратить образование мелкодисперсной цементной пыли в помещении, бетонную поверхность обрабатывают силикатными составами.
Действующие компоненты впитываются по капиллярам в глубокие слои бетонной структуры, вступают в химическое взаимодействие с материалом и преобразуются в нейтральные соединения, устойчивые к воздействию воды и обладающие хорошими прочностными характеристиками. Пропитка на силикатной основе обеспечивает бетону надежную гидроизоляционную защиту и улучшает его внешний вид, придавая блеск.
Полиуретановые составы
Однокомпонентные полиуретановые составы способны создавать прочный слой на поверхности бетона и проникать в капилляры, заполнять микропустоты.
Обработка полиуретаном позволяет увеличить износостойкость промышленных полов, выполненных из низкомарочного бетона.
Благодаря их нанесению прекращается процесс пылеобразования, повышается химическая стойкость бетонного покрытия. Также нужно отметить, что полиуретановый слой придает обработанной поверхности дополнительную защиту от повреждения в результате колебаний температуры.
Эпоксидные пропитки
Преимущество эпоксидных составов заключается в их высокой адгезии. Это позволяет обрабатывать поверхности с любой степенью износа, с большим количеством загрязнений, масляных пятен. Обработанные полы становятся более прочными и устойчивыми к воздействию химически активных веществ. Поскольку в эпоксидной пропитке есть некоторое количество воды, появляется возможность наносить эмульсию на влажные конструкции, не дожидаясь их полного высыхания.
Эпоксидные пропитки по бетону можно наносить при положительной температуре, тогда как полиуретановые можно применять в любых условиях, в том числе в неотапливаемых помещениях. Обработанные эпоксидным составом поверхности приобретают твердую пленку, обладающую крайне низкой эластичностью.
Обработка бетонных полов укрепляющими пропитками является экономически целесообразным решением в большинстве случаев. Достаточно вложить немного средств на реализацию этой технологии, чтобы в дальнейшем не отвлекаться на регулярные ремонты полов. Качественно нанесенные пропитки продлят срок эксплуатации бетонных конструкций и позволят собственнику помещения сэкономить внушительные ресурсы.
Упрочнение бетона. Укрепление бетона — Тюмень. Упрочнить бетонный пол, упрочнить бетон, укрепить стяжку. Упрочняющие пропитки, укрепляющие пропитки
В настоящее время в промышленном и жилищно-гражданском строительстве для укрепления бетона, упрочнения бетона, укрепления стяжек широко применяют различные укрепляющие пропитки, упрочняющие пропитки. Наиболее эффективны для укрепления бетона полимерные пропитки, принцип действия которых заключается в следующем: поры бетона в верхнем слое заполняются полимером, модифицируя данный слой в бетонополимер с улучшенными прочностными характеристиками.
Очевидно, что эффективность данной технологии по упрочнению пола напрямую зависит
от глубины проникновения укрепляющей пропитки, то есть от проникающей способности полимерного материала.
Вне конкуренции по этому параметру полиуретановые упрочняющие пропитки.
Предлагаем для решения задач по упрочнению полов из бетона следующие технологии с применением полиуретановых материалов «Элакор-ПУ»:
1. Полиуретановая пропитка (Элакор-ПУ Грунт)Наиболее часто применяемая технология. Рекомендуется для укрепления бетона, упрочнения пола, укрепления стяжек марочной прочности М150-М350. Обеспечивает глубину пропитки около 3мм. Позволяет упрочнить бетон в верхнем слое до М600 и более, независимо от начальной марочной прочности.
Не только упрочняет бетон, но и комплексно решает большинство эксплуатационных проблем: обеспыливает и герметизирует основание, повышает химическую стойкость и износостойкость, бетонные полы с укрепляющей пропиткой легко убираются с применением любых моющих средств. Может выполняться при низких температурах от минус 30 °С.
2. Пропитка глубокого проникновения (Элакор-ПУ Грунт-2К/50)Характеризуется максимальной проникающей способностью.
Глубина пропитки для бетона М300 – около 5мм.
Решает тот же круг задач, что и предыдущая технология.
Наносится при температурах от 5 °С.
Применяется с целью укрепления бетона на слабых (до М150) основаниях, либо для максимального упрочнения бетона «стандартных» оснований. Для увеличения глубины проникновения рекомендуется накрывать в момент нанесения полиэтиленовой пленкой (глубина 5мм при М150 обеспечивается без укрывания).
Также применяется как защитное покрытие для оснований с малой пористостью – укрепляющая пропитка способна проникать в высокопрочные бетоны и влажные (но не мокрые) основания.
В ряде случаев задачу упрочнения бетона может решить не относящаяся к полимерным:
3. Флюат пропитка (Элакор-МБ1 + МБ2)Самый экономичный вариант упрочняющей пропитки.
Увеличивает прочность бетона до 50%.
Увеличивает износостойкость в десять раз.
Не меняет внешнего вида бетонного пола, не образует пленки на поверхности основания.
Выше описано, как упрочнить бетон на готовых полах,
прочностные характеристики которого по тем или иным причинам не соответствуют планируемым нагрузкам. Отметим, что все указанные выше пропитки полностью обеспыливают бетонный пол,
то есть одновременно являются обеспыливающими пропитками.
Обеспыливание бетонных полов
Чтобы избежать затрат на укрепление стяжки пола целесообразно достигать необходимых прочностных параметров при выполнении бетонного основания. Для устройства высокопрочных оснований предлагаем комплексные добавки-модификаторы для бетона «Элакор Эластобетон», которые позволяют достигать марочной прочности М700 и выше только за счет введения данного материала в товарный бетон, никак не изменяя технологии устройства бетонного пола.
Производство — www.teohim.ru упрочнение бетона
Укрепляющая пропитка для бетона подробная технология работ материалы составы
НАЗНАЧЕНИЕУкрепляющая пропитка для бетона раствором флюата Resmix Fluat для упрочнения и защиты бетонной и железобетонной поверхности согласно методам и принципам ГОСТ 32016-2012.
При пропитке бетонной поверхности, флюат реагирует с растворимыми известковыми соединениями бетона и образует прочные нерастворимые соединения, не снижая паропроницаемость основания.
Укрепляющая пропитка бетона и железобетона раствором флюата:- повышает поверхностную прочность;
- увеличивает стойкость к агрессивным средам;
- снижает истираемость;
- увеличивает морозостойкость.
Эффективность действия флюата зависит от впитывающей способности основания.
Наилучший результат при укрепляющей пропитке бетона Resmix Fluat получается при нанесении раствора флюата на сухую, хорошо впитывающую поверхность.
Основание должно быть очищено от загрязнений, цементного молочка, разделяющих веществ (масла, жира, краски) и отслаивающихся элементов.
Для очистки от загрязнений применяется Resmix RM.
Приготовление флюатаResmix Fluat разбавляется с водой из питьевого водоснабжения в соотношении от 1:2 до 1:4.
Готовый флюатирующий раствор равномерно наносится на основание кистью средней жесткости до полного насыщения поверхности. Для полной нейтрализации солей и укрепления поверхности, раствор Resmix Fluat наносится за два рабочих прохода.
Первая обработка флюатом выполняется при соотношении Resmix Fluat:Вода = 1:4. Вторая обработка укрепляющей пропиткой производится через 1 сутки при соотношении Resmix Fluat:Вода = 1:2.
При воздействие прямых солнечных лучей, обрабатываемую поверхность необходимо защищать пленкой перед повторным нанесением флюата и после него в течение 1 суток.
МАТЕРИАЛЫ ДЛЯ УКРЕПЛЯЮЩЕЙ ПРОПИТКИ БЕТОНА:Монолит-20М пропитка для бетона укрепляющая в Тюмени -Пропитки для бетона, стяжки пола, камня и кирпича в Тюмени
Монолит-20М — экологически безвредный продукт на водной основе, негорюч, без запаха, лимонного цвета. Пропитка Монолит-20М применяется для упрочнения и обеспыливания старого и свежеуложенного бетона (от 14 дней).
В отличие от представленных на строительном рынке продуктов этого класса, обладает пониженным содержанием щелочи, останавливает силикатно-щелочные реакции в бетоне. Бетон, обработанный пропиткой для бетона Монолит-20М, приобретает три уровня защиты:
Поверхность бетона отталкивает воду.
В порах бетона образуются кристаллы, уплотняющие бетон.
Вся структура бетона цементируется прочным, водостойким гелем.
В микротрещинах бетона образуются кристаллы, расширяющиеся в присутствии влаги. Таким образом, эти кристаллы ограничивают проникновение влаги в бетон. Кристаллы не создают напряжение в бетоне, поскольку расширение ограничивается объемом пор. Монолит-20М повышает твердость, износостойкость бетона, обеспыливание и упрочнение бетонного пола, способствует зарастанию микротрещин. Отличается от ранее разработанных материалов большей глубиной проникновения, и эффективным уплотнением бетона. Применим для бетонных полов промышленного и коммунально-бытового назначения, а также бетонных плиток. Влажность бетона, обработанного Монолит-20М, за несколько месяцев снижается до 4-7%. Это останавливает коррозию арматуры, и стабилизирует состояние бетона. Монолит-20М — является ингибитором коррозии арматуры. Монолит-20М рекомендован к применению для погрузочных терминалов, мостов, бетонного пола жилых зданий, промышленных складов, текстильных фабрик, разливочных производств, авторемонтных предприятий, гаражей, паркингов, бассейнов, магазинов, супермаркетов и многих других объектов.
Пропитка для бетона Монолит-20М значительно снижает образование усадочных трещин и коробление бетона (подъем краев бетона). Водонепроницаемость бетона увеличивается на 3 марки. Морозостойкость: потеря массы после 360 циклов — 2,8%. Износостойкость повышается на 30%. Твердость поверхности повышается на 30%. Проникает на глубину до 50 мм. Бетон не пылит, сохраняет способность «дышать». Отличная стойкость к воздействию органических кислот, жиров, нефтепродуктов. Кратковременная стойкость к неорганическим кислотам. Снижает миграцию паров влаги, но бетон «дышит». Защищает арматуру и стальную фибру от коррозии. Повышает прочность на сжатие и растяжение в поверхностном слое 50 мм до 20%. Повышает адгезию эпоксидных и полиуретановых покрытий и красок. Повышает в три раза долговечность фасадных красок, нанесенных после пропитки.
Срок службы
Наносится 1 раз на весь срок службы бетона.
Расход
В среднем расход пропитки Монолит-20м составляет 0,3 л/ м² , расход зависит от пористости и состояния бетона.
Сертификаты
Свидетельство о государственной регистрации на Монолит-20М
Инструкция
Технические характеристики и инструкция по применению Монолит-20М
Компания Полимер Технолоджи предлагает вам купить по низкой цене Монолит-20М для профессионального строительства в городах Тюмень, Екатеринбург, Челябинск, Ишим, Курган, Ялуторовск, Тобольск, Ханты-Мансийск, Сургут, Ноябрьск, Новый Уренгой, Нижневартовск, Омск, Пермь, Новосибирск, Красноярск.
11.04.2011, 36947 просмотров.
Укрепляющая пропитка для бетона | «БетонПрофи» в Томске
Повышение стойкости бетонного покрытия по отношению к самым разным воздействиям, оказываемым человеком или окружающей средой – ключевое свойство пропиток для бетона. Это жидкие вещества, очень простые и удобные в использовании, помогают придать бетону превосходные эксплуатационные качества, среди которых можно выделить износостойкость, влагостойкость и морозоустойчивость. Пропитки глубоко проникают в воздушные поры, по пути заполняя все микротрещины и пустоты, тем самым создавая дополнительный защитный слой. Срок службы любой бетонной конструкции после обработки пропиткой может увеличиться в два или даже три раза. Полы в цехах перестают стираться, стены, пораженные влажностью, становятся сухими и прочными.
Химическая промышленность разработала органические и неорганические пропитки. Акриловый, полиуретановый, а также эпоксидный состав из смолы отличает органические жидкости. Цепочки молекул, заполняющие поры, действуют довольно быстро, обеспыливая поверхность и защищая ее как от биологических, так и от химических воздействий.
Неорганические защитные жидкости работают через преобразование растворимых соединений в нерастворимые, тем самым увеличивая их прочность и стойкость к любой влажности и даже кислоте. Но очень важно понимать, что пропитки и добавки для бетона – разные вещи, используемые в различное время и на других этапах технологического процесса. Добавки попадают в раствор еще на фабрике, когда рабочий процесс по замешиванию бетона подходит к концу. А пропитки наносятся сразу на готовую стену, пол или потолок – они предназначены для застывшего бетонного покрытия. Однако их свойства внешне довольно похожи. Тем не менее, есть ряд отличий.
Ключевая особенность, которая во многом обуславливает их превосходные эксплуатационные свойства – полная впитываемость, пропитки не оставляют никаких следов или слоев. Поэтому износостойкость конструкции и устранение пыли с ее поверхности происходит без каких-либо побочных эффектов в виде отслаивающихся со временем следов жидкости. Холод, влага или щелочь – все эти вещи больше не причинят бетонному сооружению каких-либо проблем. Причем не только бетонному – пропитки отлично подходят и для каменного, кирпичного или гипсового строения, они придают ему те же свойства и защиту. Таким же образом их можно использовать в качестве подготовительного материала перед нанесением лакокрасочного покрытия или оштукатуриванием.
Обеспыливание – одно из важнейших свойств пропиток для бетона, оно особенно полезно в производственных и складских помещениях. Любые отрасли промышленности, как и жилые и торговые здания могут использовать эти жидкости – они безвредны для человека.
Существует одна особенность, с помощью которой покрытие может стать еще более устойчивым по отношению к истираемости: если пол или другую поверхность загрубить кварцевым песком (подойдет мелкая фракция), то можно легко придать ей антискользящие свойства.
Гидрофобизирующие пропитки
В отдельную разновидность можно выделить специальные средства для защиты от влажности – гидрофобизаторы. Эти жидкости действуют намного эффективнее, чем другие известные гидроизоляционные материалы. Те же гидростеклоизолы или битумные мастики не способные защитить конструкцию из железобетона изнутри, а гидрофобизаторы вполне могут это сделать. Поэтому их часто применяют для реконструкции фундамента и стен из монолита.
Есть еще так называемые кольматирующие вещества, отличительной особенностью которых является простота использования. Но самыми эффективными веществами можно назвать двухкомпонентные защитные составы – они способны выдержать огромную нагрузку от больших объемов воды. Минусом является их достаточно высокая стоимость.
Напоминаем вам, что вы можете купить бетон с добавлением пропиток под любые цели в компании «БетонПрофи» в Томске!
Влияние водоотталкивающей пропитки поверхности на долговечность цементных материалов
Во многих случаях срок службы железобетонных конструкций сильно ограничивается проникновением хлоридов до стальной арматуры или карбонизацией облицовочного бетона. Водоотталкивающая обработка поверхностей материалов на основе цемента часто считается защитой бетона от этих повреждений. В этой статье на поверхность бетонных образцов были нанесены три типа водоотталкивающих агентов.Профили проникновения силиконовой смолы в обработанный бетон были определены с помощью ИК-Фурье спектроскопии. Были измерены капиллярное всасывание воды, проникновение хлоридов, карбонизация и коррозия арматуры как в образцах с пропиткой, так и в необработанных образцах. Результаты показывают, что поверхностная пропитка существенно снизила коэффициент капиллярного всасывания бетона. Эффективный барьер для хлоридов можно создать путем глубокой пропитки. Пропитка водоотталкивающей поверхности силанами также может замедлить процесс карбонизации.Кроме того, был сделан вывод, что пропитка поверхности может обеспечить эффективную защиту от коррозии арматурной стали в бетоне с мигрирующим хлоридом. Следовательно, улучшения прочности и увеличения срока службы железобетонных конструкций можно ожидать за счет применения соответствующей водоотталкивающей пропитки поверхности.
1. Введение
Разработка цемента и бетона началась в середине 1800-х годов, и это оказалось революционным нововведением в строительных материалах.Сегодня железобетон является единственным наиболее широко используемым строительным материалом в мире как для целых зданий, так и для ключевых структурных элементов, которые должны выдерживать различные существенные нагрузки. Железобетон используется в таких больших количествах, потому что он обладает такими характеристиками, как относительно хорошая долговечность, низкие затраты на обслуживание и удобство. Однако в настоящее время принято считать, что срок службы многих железобетонных конструкций зачастую недостаточен. Стоимость мероприятий по раннему ремонту часто значительно превышает стоимость нового строительства.Основная причина этих проблем, связанных с затратами на техническое обслуживание и ремонт, а также плохой эксплуатационной пригодностью, заключается в недостаточной прочности железобетонных конструкций [1–3].
Перенос влаги в материалах на основе цемента является критическим физическим процессом для их долговечности, поскольку многие эффекты, влияющие на долговечность конструкции здания, вызваны самой водой, а также переносимыми ею вредными веществами. Если материалы на основе цемента, такие как раствор и бетон, подвергаются воздействию воды, может иметь место ряд процессов ухудшения.Один доминирующий процесс или комбинация различных процессов может в конечном итоге ограничить ожидаемый срок службы железобетонных конструкций. Коррозионное воздействие воды на бетон можно разделить, по крайней мере, на три различных типа. Во-первых, чистая вода при постоянном контакте с материалами на основе цемента действует как растворитель. Связывающая матрица, состоящая из Ca (OH) 2 и геля C-S-H, постепенно растворяется путем гидролиза. Во-вторых, газы окружающей среды могут растворяться в пористом водном растворе бетона.Таким образом, кислоты образуются, например, при растворении CO 2 и SO 2 , которые могут быстро реагировать с продуктами гидратации цемента. При третьем типе коррозионного воздействия вода действует по существу как носитель и переносит растворенные соединения, такие как ионы хлора, в пористую систему цементирующей матрицы. Помимо коррозионного воздействия, вода также играет важную роль в некоторых других физических и химических повреждениях бетона, таких как замораживание-оттаивание, реакция щелочного заполнителя, коррозия стали и усадка при высыхании.
Очевидно, что все эти три типа агрессивных атак действуют с поверхности бетона. На протяжении всей истории на открытые поверхности структурных бетонных элементов наносился ряд защитных материалов для предотвращения проникновения воды, включая масла, воски или краски. В настоящее время большой прогресс достигнут в производстве водоотталкивающих средств и разработке водоотталкивающих средств. Доказано, что пропитка поверхности водоотталкивающими добавками должна быть эффективным методом профилактики бетонных конструкций [4–9]. Более подробную информацию об исследованиях водоотталкивающих средств можно найти в материалах серии конференций HYDROPHOBE (Hydrophobes I – VIII) из [10–17].
В этой статье кратко описан основной механизм водоотталкивающей обработки материалов на основе цемента. На поверхность двух типов материалов на основе цемента были нанесены три типа водоотталкивающих агентов в форме жидкости, крема и геля. Последующие эффекты пропитки поверхности на уменьшение капиллярного всасывания воды, проникновения хлоридов, карбонизации и коррозии арматуры в бетоне будут измерены и обсуждены.
2. Основной механизм водоотталкивающей обработки
В целом, водоотталкивающие средства обработки поверхности в основном подразделяются на три группы в зависимости от механизма, с помощью которого достигается защита. На рисунке 1 показаны типы обработки поверхности в соответствии с этой классификацией [18]. Обработка поверхности силанами относится к «пропитке», основные механизмы которой описаны в следующих двух абзацах.
Наиболее важными водоотталкивающими агентами на основе кремния являются те, которые изготовлены из силанов и силоксанов, которые представляют собой полимеры, содержащие три алкоксигруппы, обозначенные OR ‘, связанные с атомом кремния, причем каждый атом кремния несет органическую алкильную группу, обозначенную R.Функциональная алкоксигруппа кремния реагирует с водой и дает реакционноспособную силанольную группу (стадия гидролиза). Дальнейшая конденсация путем сшивания с гидроксильными группами приводит к образованию полисилоксана (кремнийорганической смолы) в качестве активного водоотталкивающего продукта, который связан с неорганическим субстратом посредством ковалентных силоксановых связей, как показано на рисунке 2. Органические функциональные алкильные группы уменьшают критическое поверхностное натяжение. поверхности материала и, таким образом, обеспечивают гидрофобность, в то время как функциональные группы кремния обеспечивают реакционную способность с подложкой и регулируют глубину проникновения.
Действие гидрофобизаторов в основном основано на их низком поверхностном натяжении. Поведение воды при контакте с поверхностью материала определяется поверхностным натяжением, которое можно измерить с помощью угла контакта, как феноменологически показано на рисунке 3. Интенсивность водоотталкивающих свойств связана с углом контакта между водой и поверхностью. обработанная поверхность. Углы смачивания капли воды более 90 ° представляют собой гидрофобные свойства с гидрофильностью менее 90 °.Чем больше угол смачивания, тем более водоотталкивающей становится поверхность. Фактически гидрофобность гидрофобизаторов реализуется в два этапа. Во-первых, эффект бусинок заставляет капли воды быстро стекать и покидать поверхность. Во-вторых, когда вода имеет тенденцию растекаться и образовывать водную пленку на поверхности, водопоглощение уменьшается за счет исключения через обработанные капилляры.
3. Материалы и методы
3.1. Материалы и подготовка образцов
Два типа раствора и образцы бетона были подготовлены для серии испытаний.Использовали обычный портландцемент типа 42,5, щебень с максимальным диаметром 20 мм и плотностью 2620 кг / м 3 и речной песок с максимальным размером зерна 5 мм и плотностью 2610 кг / м 3 . Точные составы бетона, используемого в этом проекте, приведены в Таблице 1. Смесь с W / C = 0,5 была названа бетоном C. Также был приготовлен раствор с более высоким водоцементным соотношением (W / C = 0,6) и назван раствором. M. Некоторые образцы, приготовленные как из бетона C, так и из раствора M, позже были пропитаны поверхностью с различным количеством водоотталкивающих агентов.Бетонные образцы использовались для испытания на водопоглощение, проникновения хлоридов, испытания на карбонизацию и испытания на коррозию стали. Образцы минометов были подготовлены только для испытаний с помощью нейтронной радиографии, чтобы избежать влияния конечно-совокупности во время анализа изображения.
|
Из всех полученных смесей в Таблице 1 были изготовлены кубы с длиной стороны 100 мм. Другой тип призматических образцов с размерами 280 × 150 × 115 мм с двумя стальными стержнями также был подготовлен для испытания на коррозию стали. Все образцы были уплотнены в стальных формах и отверждены в течение одного дня перед извлечением из формы.После этого образцы были перемещены в камеру для отверждения (° C, относительная влажность> 95%). В возрасте 28 дней их вывели из камеры полимеризации для водоотталкивающей обработки поверхности.
3.2. Водоотталкивающая пропитка поверхности
После 28 дней влажного отверждения образцы хранили при относительной влажности 60% в течение 7 дней для сушки. Затем одна из формованных поверхностей кубических образцов и верхняя поверхность (280 × 115 мм) прямоугольных параллелепипедов пропитывались водоотталкивающими добавками трех различных типов.Типы агентов, количество использования и соответствующие коды образцов перечислены в таблице 2. После этого образцы снова хранили при относительной влажности 60% в течение еще 7 дней, чтобы обеспечить достаточную полимеризацию силана. Затем образцы с пропиткой поверхности были готовы к дальнейшим испытаниям.
|
Одна серия пропитана жидким силаном. В этом случае бетонная поверхность контактировала с жидким силаном на один час. В этот период жидкий силан может абсорбироваться образцом из-за капиллярного всасывания. Во второй серии одна из формованных поверхностей была покрыта силановым кремом. Расход на поверхности составил 400 г / м 2 . Для серий с третьей по пятую наносили 100, 400 и 600 г / м 2 силанового геля. Крем с силаном и гель наносили на бетонные поверхности небольшой кистью.
На образцах, обработанных водоотталкивающими добавками, слои обработанной поверхности толщиной 1 мм каждый были последовательно фрезерованы с помощью специально построенной фрезы.Порошок, полученный в результате этого процесса, собирали. Затем содержание кремния в этих порошках определяли с помощью ИК-Фурье спектроскопии. Этот метод был разработан и усовершенствован для этого конкретного приложения Гердесом и Виттманном [19].
3.3. Водопоглощение и проникновение хлоридов
Водопоглощение образцов с обработанной и необработанной поверхностью измеряли стандартным методом [20]. Перед испытанием кубические образцы разрезали на две половины и сушили в вентилируемой печи при температуре 50 ° C в течение 7 дней до достижения равновесия масс.Когда образцы охлаждались до комнатной температуры, обработанные и необработанные образцы контактировали с водой на определенные периоды времени, как показано на рисунке 4. Затем количество поглощенной воды капиллярным отсасыванием измеряли путем взвешивания образцов через 1 час. 2, 4, 8, 24, 48 и 72 часа.
Аналогично тому, как описано в последнем абзаце, испытание на проникновение хлоридов (3% раствор NaCl) для образцов, обработанных и необработанных водоотталкивающим средством, проводилось в течение 28 дней.После испытания порошок измельчали последовательно, начиная с поверхности образцов, подвергшейся воздействию солевого раствора. Затем содержание хлоридов в порошке определяли методом ионоселективного электрода. Таким образом были определены профили хлоридов в образцах с пропиткой и необработанной водоотталкивающей поверхностью.
3.4. Нейтронная радиография
Образцы водоотталкивающих растворов и необработанные сопутствующие образцы были также испытаны методом нейтронной радиографии в Институте Пауля Шеррера (PSI) в Швейцарии.Нейтронная радиография была определена как идеальный и уникальный неразрушающий метод для изучения движения воды и распределения влаги в материалах на основе цемента из-за их сильного ослабления водородом и их нечувствительности к доминирующим ингредиентам, таким как кремнезем и кальций, в материалах на основе цемента. Подробнее об этой технике можно прочитать в [21–26].
Сначала были получены нейтронные изображения на образцах, которые находились в гигральном равновесии с атмосферой помещения (RH ≈ 60%; T ≈ 20 ° C).Затем снова были сделаны нейтронные изображения на обработанных водоотталкивающих и необработанных образцах строительных растворов после контакта с водой в течение 0,5 и 2 часов. Таким образом было визуализировано движение воды в образцах. Кроме того, некоторые образцы с пропиткой и необработанной поверхностью помещали в воду на три дня. Этого времени было достаточно для полного насыщения образцов. Затем на этих водонасыщенных образцах были получены нейтронные изображения. Были исследованы как необработанные образцы строительных растворов, так и образцы растворов с пропиткой в водонасыщенном состоянии.По нейтронным изображениям можно количественно проанализировать распределение влажности.
3.5. Ускоренная карбонизация
После сушки в лаборатории в течение 7 дней образцы как с обработанной поверхностью, так и необработанные были подвергнуты ускоренной карбонизации на 7 и 28 дней. Согласно китайскому стандарту [27], концентрация газа CO 2 поддерживалась постоянной в%; относительная влажность в камере для карбонизации около 70%; температура была ° C. Четыре поверхности, за исключением обработанной поверхности и ее противоположной поверхности, были запечатаны воском перед помещением в режим карбонизации. Таким образом, в бетон была наложена карбонизация по нормали к двум противоположным поверхностям. Через 7 и 28 дней измеряли глубину карбонизации в поверхностных пропитанных и необработанных образцах путем распыления 1% раствора фенолфталеина в этаноле.
3.6. Коррозия арматуры
Этот тест проводился в соответствии с ASTM G 109-07 [28]; Размеры образцов 280 × 150 × 115 мм с резервуаром с раствором NaCl на исследуемой поверхности. Резервуар размером 150 × 75 × 75 мм располагался по центру верхней поверхности.Верхняя армированная сталь располагалась на расстоянии 20 мм от поверхности бассейна, а нижняя сталь — на расстоянии 25 мм от нижней поверхности. Концы стали были защищены гальванической лентой, а 200-миллиметровая часть посередине оголена. Во время испытания потенциал полуячейки и плотность тока коррозии стальной арматуры в образцах бетона с пропиткой и необработанной поверхностью измерялись непрерывно каждую неделю.
4. Результаты и обсуждение
4.1. Влияние водоотталкивающей пропитки поверхности на водопоглощение
Водопоглощение как необработанных, так и обработанных образцов бетона было измерено при 72-часовом контакте с водой.Результаты, полученные в разное время, показаны на рисунке 5. Точки, указанные на рисунке 5, представляют собой средние значения трех независимых измерений. Также показаны вариации отдельных измерений. Из результатов видно, что вся пропитанная поверхность бетона впитывает гораздо меньше воды по сравнению с необработанным бетоном. В этом случае это не жидкая вода, а водяной пар, улавливаемый капиллярной конденсацией, когда он пересекает пропитанный силаном слой. Кроме того, в нанопорах бетона может происходить капиллярная конденсация, поскольку молекулы силана не могут проникать в эти узкие пространства по геометрическим причинам.Следовательно, небольшое количество капиллярно-конденсированной воды все еще может мигрировать в поры путем диффузии. Но, по сравнению с необработанным бетоном, количество поглощенной воды значительно снижается за счет пропитки поверхности каждым типом силана.
Для однородного пористого материала из теории капиллярности можно вывести простое выражение, описывающее капиллярное всасывание как функцию времени; см. (1) [29, 30]. Это уравнение является только первым приближением, потому что скин-эффект бетона всегда будет причиной отклонения результатов измерений от теоретического прогноза.где — количество поглощенной воды капиллярным отсосом на единицу площади и т, — продолжительность контакта. A — коэффициент капиллярного всасывания. Можно рассчитать коэффициент капиллярного всасывания, полученный на Рисунке 5 для обработанного и необработанного бетона. Результаты показывают, что коэффициент капиллярного всасывания для необработанного образца составляет 248,7 г / (м 2 ч 0,5 ), а для образца L1 (пропитанного жидким силаном) он составляет 40,9 г / (м 2 ч 0). .5 ), примерно одна шестая от необработанного образца; для образцов С400 (силановый крем) и G400 (силановый гель) коэффициенты составляют 34,5 и 24,5 г / (м 2 h 0,5 ) соответственно. Они составляют менее одной седьмой и одной десятой от необработанного образца. Это, очевидно, указывает на то, что пропитка поверхности водоотталкивающими силанами может значительно снизить проникновение воды в бетон.
На рис. 6 показано визуальное наблюдение проникновения воды в необработанные и обработанные водоотталкивающим средством образцы раствора после 0.5 и 2 часа с помощью нейтронной радиографии. Хорошо видно, что через полчаса контакта с водой в необработанном бетоне становится виден фронт проникновения. Этот нерегулярный фронт постепенно перемещается в пористый материал с увеличением времени. Но для образца, пропитанного поверхностью, невооруженным глазом нельзя было наблюдать поглощение воды даже через два часа из-за полисилоксановой пленки, образованной из силана, которая делала приповерхностную область гидрофобной.
(а) Нейтронное изображение после 0.
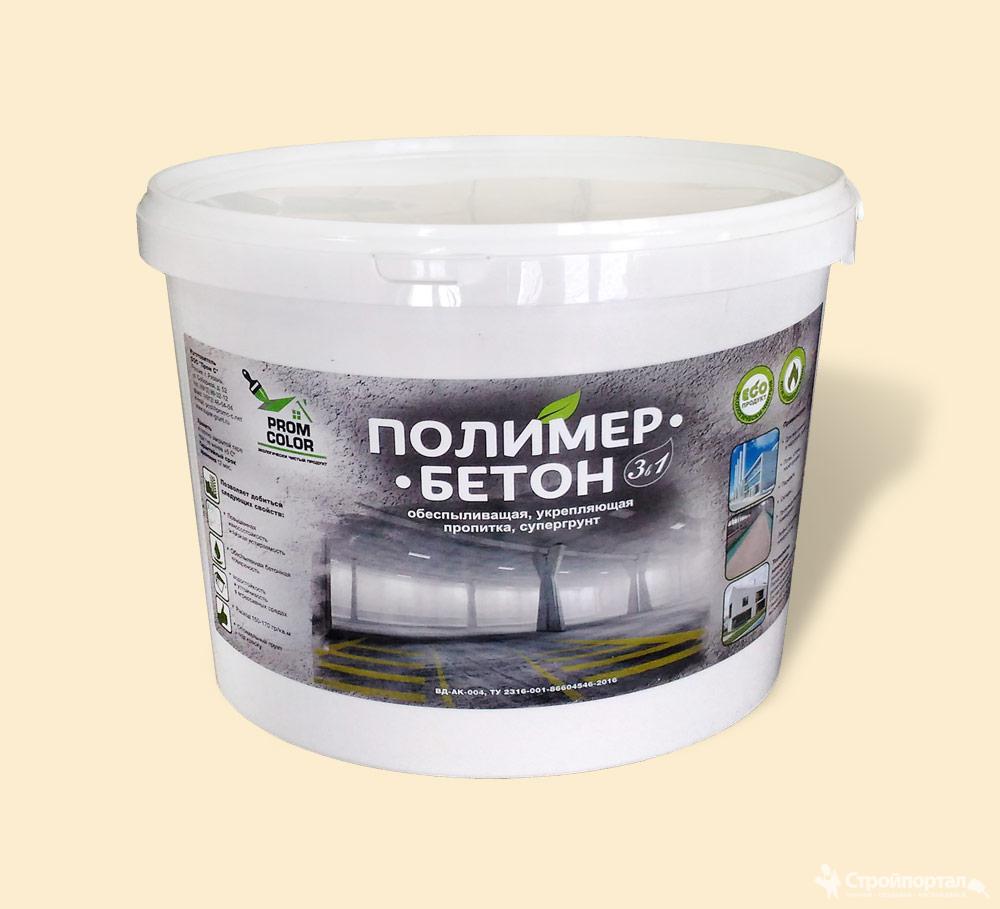
(b) Изображение через 2 часа
(a) Нейтронное изображение через 0,5 часа
(b) Изображение через 2 часа
После нанесения на поверхности бетона силан проник и образовал полисилоксан (кремний смола) в приповерхностной зоне. Концентрация полисилоксана в образцах с пропиткой поверхности была измерена с помощью ИК-Фурье спектроскопии. Результаты показаны на рисунке 7. Можно видеть, что в каждом случае была достигнута глубина проникновения около девяти миллиметров.Эту обработку можно назвать глубокой пропиткой в отличие от простой пропитки поверхности. В некоторых случаях достаточно простой пропитки поверхности. Однако для создания надежного и прочного хлоридного барьера часто требуется минимальная глубина проникновения 7 мм [5]. Это необходимо подтвердить в контексте обеспечения качества после обработки поверхности на практике. Если глубина проникновения слишком мала, проникновение агрессивных ионов с водой замедляется, но не предотвращается в течение длительного времени.
Кроме того, на рисунке 8 показаны нейтронные изображения трех типов пропитанных и водонасыщенных образцов строительных растворов.Верхняя пропитанная поверхность представляет интерес исключительно в этом контексте. Невооруженным глазом хорошо видно, что пропускание нейтронов во внешнем пропитанном слое значительно выше. Толщину пропитанного слоя можно оценить по результатам, показанным на Рисунке 8. Средние значения, определенные визуальным осмотром, составляют 2,0, 4,1 и 6,3 мм для образцов G100, G400 и G600 соответственно.
Далее было измерено распределение влажности в приповерхностной зоне, как показано прямоугольной рамкой, показанной на Рисунке 8 (M-G600), на основе нейтронных изображений, полученных от водонасыщенных образцов.Результаты показаны на рисунке 9. Как и ожидалось, содержание влаги в необработанном образце по существу равномерно распределено по всему объему. Наблюдаемое небольшое уменьшение содержания воды вблизи поверхности может быть связано с небольшой потерей воды во время обработки до получения первого нейтронного изображения.
Однако на образцах с пропиткой на поверхности отчетливо прослеживается влияние водоотталкивающей приповерхностной зоны. Как и ожидалось, содержание воды в водоотталкивающей зоне значительно снижено.Также четко прослеживается ширина водоотталкивающей зоны. В образцах M-G100 установлен водоотталкивающий слой толщиной примерно 2 мм. В образцах M-G400 и M-G600 толщина водоотталкивающей зоны может быть оценена примерно в 4 и 6 мм соответственно. Однако наиболее важным является тот факт, что в образце M-G100 содержание воды в водоотталкивающей зоне, безусловно, существенно снижено, но все же в этой области можно наблюдать определенное количество воды.В отличие от образца M-G600, можно обнаружить только минимальное количество воды. Из этих результатов снова можно сделать вывод, что для эффективного барьера от хлоридов необходима глубокая пропитка.
4.2. Влияние водоотталкивающей пропитки поверхности на проникновение хлоридов
Поверхности обработанных и необработанных образцов бетона контактировали с водным раствором NaCl с концентрацией 3% в течение 28 дней. Были определены профили хлоридов. Результаты показаны на рисунке 10.Видно, что даже на глубину до 30 мм в необработанный бетон проникло много хлорид-ионов. Уже было показано, что капиллярное всасывание является наиболее мощным механизмом переноса хлоридов в бетон. При отсутствии капиллярного действия солевой раствор не может поглощаться пористым материалом, а если микропоры не заполнены водой, хлорид также не может диффундировать в пористую структуру. Таким образом, посредством пропитки поверхности силанами он препятствует проникновению воды в бетон и, следовательно, предотвращает миграцию хлоридов.За время выдержки обработанного бетона хлорид не проник в глубокую часть материала. Небольшое количество хлорид-ионов, которое может быть обнаружено в первых 3 мм, связано с шероховатостью поверхности и открытыми большими порами в приповерхностной зоне. Следовательно, пропитка поверхности силаном является эффективным барьером для хлоридов для пористых материалов на основе цемента.
4.3. Влияние водоотталкивающей пропитки поверхности на карбонизацию
После 7 и 28 дней карбонизации была измерена глубина карбонизации обработанного водоотталкивающим и необработанного бетона.Результаты показаны на рисунке 11. Очевидно, что образцы с пропитанной поверхностью имеют меньшую глубину карбонизации, чем необработанный бетон. При обработке поверхности нанесение силанового крема 400 г / м 2 2 и силанового геля снижает примерно наполовину глубину карбонизации по сравнению с эталонным бетоном, эффективность которого намного выше, чем при использовании покрытия 100 г / м 2 .
Благодаря пропитке поверхности силанами гидрофобная пленка защищает бетон от проникновения воды, что обычно делает гидрофобный слой почти сухим.В этой области происходит очень слабое действие карбонизации, потому что для нейтрализации между газом CO 2 и гидратом кальция или гелем CSH требуется вода, в то время как этот слой также снижает диффузию влаги в бетоне и, следовательно, делает область за гидрофобным слоем влажной, при этом условии не может происходить и карбонизация. Однако следует отметить, что заключение о том, что пропитка поверхности снижает глубину карбонизации примерно наполовину, было получено при относительной влажности 70% в камере для карбонизации.Если окружающая среда очень сухая, необработанный бетон очень скоро потеряет воду; но в обработанном бетоне скорость высыхания замедляется, и, следовательно, жидкая вода в порах может ускорить процесс карбонизации [31].
4.4. Влияние водоотталкивающей пропитки поверхности на коррозию арматуры
Были измерены потенциал полуячейки (Cu-CuSO 4 ) и плотность тока коррозии стальной арматуры в железобетоне. Результаты показаны на Рисунке 12.Это ясно указывает на то, что образцы бетона без поверхностной пропитки демонстрируют высокий уровень отрицательного потенциала коррозии и плотности тока коррозии, особенно после приблизительно 33 недель периода воздействия. На этом этапе потенциал коррозии составлял около -460 мВ. Согласно стандарту ASTM это означает, что риск коррозии превышает 90% [32]. Плотность тока коррозии составляла около 0,4 ~ 0,5 мк А / см 2 , что означает, что стальная арматура начала корродировать, в то время как для бетона с водоотталкивающей обработкой поверхности и электрический потенциал, и плотность тока коррозии поддерживались намного ниже на протяжении всего периода период измеряется.Риск коррозии поддерживался на уровне ниже 10% от результатов потенциальной коррозии. Судя по плотности тока коррозии, коррозией можно пренебречь. Это показывает, что на образцах, обработанных водоотталкивающим средством, коррозии не происходило. Следовательно, коррозионная активность может быть значительно снижена путем пропитки поверхности.
(а) Потенциал полуячейки Cu-CuSO4
(б) Плотность тока коррозии
(а) Потенциал полуячейки Cu-CuSO4
(б) Плотность тока коррозии
5.Выводы
На основании представленных результатов можно сделать следующие выводы.
(1) Когда поверхность бетона с водоотталкивающей пропиткой находится в контакте с водой, проникновение воды в воду отсутствует; но небольшое количество водяного пара все еще абсорбируется и конденсируется в необработанных порах материала. Таким образом, гидрофобный слой толщиной в несколько миллиметров может значительно снизить водопоглощение бетона.
(2) Однако водяной пар не участвует в переносе ионов.Если поры бетона не заполнены водой, диффузия ионов эффективно замедляется. Следовательно, пропитка поверхности силаном обеспечивает эффективный барьер для хлоридов. Как следствие, срок службы бетонной конструкции, подверженной воздействию морской воды или противообледенительной соли, может быть увеличен.
(3) Глубина карбонизации бетона с поверхностной пропиткой может быть уменьшена наполовину при относительной влажности окружающей среды 70% по сравнению с необработанным бетоном.
(4) Пропитка поверхности силанами также обеспечивает эффективную защиту от коррозии арматурной стали в бетоне, контактирующей с раствором хлорида.Чтобы продлить срок службы железобетонных конструкций, можно принять во внимание водоотталкивающую обработку, чтобы снизить риск коррозии стали, при условии надлежащей обработки поверхности, что может быть достигнуто за счет соответствующего нанесения и глубокой пропитки (> 6 мм) [ 33]. Кроме того, необходимо изучить долговечность самой пропитки силаном и ее долговременную остаточную защиту. В этом смысле эффективность защитных мер следует контролировать через регулярные промежутки времени.Если первоначальные требования больше не выполняются, лечение следует повторить.
Конфликт интересов
Авторы заявляют об отсутствии конфликта интересов.
Благодарности
Финансовая поддержка текущих проектов Национальным фондом естественных наук Китая (51420105015, 51278260), Программой фундаментальных исследований Китая (2015CB655100) и 111 Project выражается с благодарностью.
Водоотталкивающая пропитка поверхности для продления срока службы железобетонных конструкций в морской среде: роль трещин
Повышение долговечности морских конструкций представляет интерес для многих исследователей.Исследование, представленное в этой статье, исследует эффективность водоредуктора и пропитки хлоридной барьерной поверхности бетонного покрытия железобетонных (ЖБИ) конструкций, подверженных воздействию морской среды. Особое внимание уделяется тому, как поверхностные трещины, образовавшиеся (1) до пропитки и (2) после пропитки, влияют на эффективность обработки поверхности. Эксперименты проводятся в среде, максимально приближенной к реальной влажной субтропической морской среде.
Ряд железобетонных (RC) призм и бетонных цилиндров, каждый из которых был обработан различными коммерческими агентами для пропитки поверхности, подвергался циклическому воздействию морской воды на открытом воздухе для ускорения циклов сухой / влажной среды в течение 1 года. Были применены шесть типов агентов для пропитки поверхности, в том числе четыре типа водоотталкивающих агентов на основе силана и два типа блокаторов пор на основе силиката натрия (жидкое стекло). Были подготовлены три типа призм RC для моделирования различных возможностей растрескивания, которые могут возникать в бетонных конструкциях с пропиткой на поверхности в течение срока их службы. В первой группе призм трещины не возникли, в то время как трещины возникли до и после пропитки поверхности во второй и третьей группах соответственно.Зависимое от времени водопоглощение всех образцов контролировали во время циклов «сухой / влажный». Наконец, образцы были разрезаны, чтобы измерить глубину проникновения агентов для пропитки поверхности и профили проникновения хлоридов. Также были измерены участки с коррозией, заметной в стальной арматуре в призмах RC.
Было обнаружено, что блокаторы пор на основе силиката натрия неэффективны для предотвращения проникновения хлоридов в бетон при моделировании воздействия на море.Было обнаружено, что долговременная эффективность водоотталкивающих агентов, используемых для пропитки поверхности, сильно зависит от типа агента и от того, проводилась ли пропитка до или после образования трещин.
% PDF-1.4
%
1 0 obj
>
эндобдж
2 0 obj
> поток конечный поток
эндобдж
3 0 obj
>
эндобдж
6 0 obj
> / ProcSet [/ PDF / Text] / Font >>>
эндобдж
5 0 obj
> поток
HW˒WH: Z \ o3p’Á! ; lRKRm>; cc [HV2? * ~ M «> DGGU! Oo O G_? QVYMeTdl2 ع WeIQtOa1y ^ e, _. ̢ « X. = aAd} Gi ~ ՛ 0 F» »
U? 2a ݎ M | h4k 螲 olap_} s | G (@ [ڷ & o5V ߵ IL%
X [S / aI ٶ dw- o ~ I) u) 6_l [K؟ FUDa / A5 د a «* WfKc) lSe {CUXCsHl + Ӹ / {R :% 0g. @ | W 颺 넴, N. (O (Y (rC-e V-OjĶ8v5P: V) ӊUi8qUU [b [| (+ ŻY ~) Zv4 — ## — SS [= XW ص4͟ n $ 3T ܺ2 X_voCYx0 # W
(PDF) Водоотталкивающая пропитка поверхности для продления срока службы железобетонных конструкций в морских условиях: роль трещин
Соотношение цемента бетонное основание, исходная влажность
и подготовка поверхности бетонного основания [5–12].В последнем случае
продукт реакции может блокировать поры, что приводит к умеренному упрочнению
, но глубина проникновения обычно минимальна —
мала, за исключением случаев, когда бетон чрезвычайно пористый [2].
До сих пор результаты испытаний на эффективность пропитанного силикатом натрия
бетона ограничены, и поэтому мало что известно о его влиянии на проникновение углекислого газа или хлорида
. Напротив, с 1980-х годов было проведено много исследований по долговечности бетона, пропитанного водоотталкивающими агентами на основе силана
.Ранний обзор методов оценки
и сообщенных характеристик такой гидрофобной импрег-
нации и соответствующих механизмов можно найти в Refs.
[13,14]. Обширные лабораторные испытания [15–18] подтвердили, что гидрофобная пропитка
может создать эффективный барьер для бетона
, отсрочить начало коррозии и снизить скорость коррозии
внутренней стальной арматуры. Некоторые обнадеживающие результаты испытаний длительного воздействия на поле
были также недавно опубликованы
[19–21].Хотя некоторые из недавних исследований
показали, что гидрофобная пропитка может иметь лишь незначительное влияние
на механизмы диффузии хлорид-ионов в бетоне [22,23],
ее эффективность в снижении внутренней влажности и значительном подавлении
капиллярное водопоглощение хорошо изучено [23–25]. Вышеупомянутые свойства, безусловно, могут рассматриваться как улучшающие долговечность морских железобетонных конструкций, поскольку подача воды и хлоридов
является ключевым фактором, влияющим на коррозию внутренней стальной арматуры.
При проектировании конструкции обычно допускаются трещины
в наружных железобетонных элементах. Эти трещины, однако, могут служить легкими путями
для проникновения воды и ионов хлора, растворенных в воде
. Крайне важно точно знать, когда пропитка поверхности
наиболее эффективна: то есть эффективны ли водоотталкивающие агенты или герметики
в бетоне с трещинами
, которые существуют во время пропитки, или
образуется после пропитки.
Однако, несмотря на вышеупомянутую обширную исследовательскую работу,
на сегодняшний день мало что известно о том, в какой степени наличие трещин
в бетонных конструктивных элементах, возникающих на поверхностях (1) до
нанесения герметиков или других материалов. обработка поверхности (2) после нанесения
катионов герметиков или другой обработки поверхности влияет на долгосрочную эффективность этих мер и последующую долговечность
конструкций в морской среде.Недавно Tittarelli и Mor-
iconi [26] применили один тип гидрофобной добавки на основе силана
к бетону и изучили ее влияние на коррозию арматурной стали
. Они обнаружили, что добавление силана существенно снижает скорость коррозии стальной арматуры в образцах
без трещин. Однако было также обнаружено, что коррозия стальной арматуры
в гидрофобных образцах из бетона с трещинами оказалась неожиданно более серьезной.Предполагаемая причина заключалась в том, что кислород
быстрее диффундировал через открытую пористость бетона в гидрофобном бетоне
по сравнению с медленной диффузией через заполненные водой поры
насыщенного бетона. Относительно данной ситуации следует отметить, что ширина трещины в их исследовании составила
1 мм, что нереально для железобетонных конструкций в условиях эксплуатации. Также важно отметить, что Титтарелли и Морикони добавили
водную силановую эмульсию алкилтриэтоксисилана к свежей бетонной смеси
; Это означает, что они приготовили цельный водоотталкивающий материал
.Следовательно, их результаты нельзя напрямую сравнивать с наблюдениями, полученными на пропитанном водой бетоне, пропитанном водой
, в реальном случае.
Чтобы избежать неправильного применения, необходимы дальнейшие исследования в реальных условиях эксплуатации
, чтобы понять, как проникновение хлорида
в пропитанный поверхность бетона и последующая
коррозия внутренней стальной арматуры и долговечность конструкции-
туров в морской среде подвержены влиянию
трещин.Таким образом, этот проект направлен на изучение долгосрочной эффективности различных материалов для пропитки поверхности после обработки образцов бетона с трещинами и без трещин в ходе хорошо контролируемой программы воздействия на открытом воздухе
и определение
какой материал для обработки поверхности обеспечивает наиболее значительное улучшение долговечности морских железобетонных конструкций с трещинами и
без трещин.
2. Эксперимент
2.1. Материалы
Для эксперимента бетон был изготовлен с содержанием цемента
248 кг / м
3
, водоцементным отношением (W / C) 0,68 и отношением мелкости к
коэффициент крупного заполнителя 0,49. Прочность на сжатие con-
crete при 28-дневном отверждении составила 34,0 МПа. Относительно высокое соотношение W / C
было выбрано по нескольким причинам. Во-первых, глубина проникновения водоотталкивающих агентов на основе si-
увеличивается с соотношением W / C
[7,10].Относительно высокое соотношение W / C приводит к более глубокому проникновению
и, следовательно, обеспечивает лучшее сравнение с характеристиками
различных материалов для пропитки поверхности. Во-вторых, на практике бетон
, который требует защиты или ремонта, обычно имеет низкое качество
из-за, например, ошибки в системе водоснабжения на строительной площадке. В-третьих, высокое соотношение W / C
лучше подходит для демонстрации того, как различные пропиточные материалы поверхности
влияют на коррозию внутренней арматуры из стали
в течение относительно короткого периода воздействия (1 год
в этом исследовании), поскольку ионы хлора может легко проникать.Всего в этом исследовании
было применено
шести типов материалов для пропитки поверхности (см. Таблицу 1). Они перечислены как A, B, C, D, E и F и образуют
два набора для обработки поверхности, а именно водоотталкивающие агенты на основе силана
(A, B, C и D) и блокаторы пор на основе силиката натрия. (E
и F). Их свойства и дозировка дополнительно описаны в Таблице
1. Влагосодержание боковых поверхностей RC призм составляло около
4.0% при нанесении поверхностных пропиток.
2.2. Детали образцов
Были подготовлены образцы двух типов, включая сорок призм RC
(150 100 100) мм и 14 бетонных цилиндров (/
100 65 мм), как показано на рис. 1. Бетонные цилиндры были предварительно изготовлены. —
, в основном для исследования профилей проникновения хлоридов в
бетоне без трещин при применении различных материалов для пропитки поверхности. Призмы RC были подготовлены для проведения исследования того, как пропитка поверхности влияет на проникновение хлорида
в бетон с трещинами и последующую коррозию внутренней стальной арматуры
.Призмы RC имели два слоя стальных стержней
(/ 10) на глубине 17,5 мм и 45 мм соответственно (см.
рис. 1), чтобы контролировать состояние стальных стержней на разной глубине покрытия,
после воздействие. Две боковые поверхности каждой призмы RC
были обработаны пропиточными агентами, а остальные четыре стороны
были заделаны эпоксидной смолой (см. Рис. 1). Как видно из таблицы 2, в которой
собраны все образцы, было три типа призм
RC.Первый тип призмы не имел трещин, поверхность второго типа
была пропитана после появления трещин,
и поверхность третьего типа была пропитана до появления трещин
. Испытательные образцы, соответствующие трем типам
, упомянутым выше, обозначены символами
«NC», «AC» и «BC» соответственно (см. Таблицу 2). Наличие
стальных стержнейв призмах способствовало легкости, с которой трещины
были введены в бетон в результате испытаний на раскалывание.
Во время испытаний на расщепление ширина трещин контролировалась
с использованием двух датчиков смещения для перекрытия трещин (см.
Рис. 2a). После испытаний на расщепление под микроскопом была измерена ширина трещин на двух боковых поверхностях каждой призмы RC (см.
рис. 2b). Ширину трещины измеряли в пяти точках на каждой боковой поверхности
, и их среднее значение затем принимали за трещину
102 J.-G. Dai et al. / Цементно-бетонные композиты 32 (2010) 101–109
% PDF-1.7
%
559 0 объект
>
эндобдж
xref
559 144
0000000016 00000 н.
0000004070 00000 н.
0000004306 00000 н.
0000004333 00000 п.
0000004382 00000 п.
0000004418 00000 н.
0000005020 00000 н.
0000005133 00000 п.
0000005333 00000 п.
0000005445 00000 н.
0000005556 00000 н.
0000005665 00000 н.
0000005776 00000 н.
0000005887 00000 н.
0000005998 00000 н.
0000006109 00000 п.
0000006220 00000 н.
0000006333 00000 п.
0000006446 00000 н.
0000006558 00000 н.
0000006673 00000 н.
0000006785 00000 н.
0000006898 00000 н.
0000007007 00000 н.
0000007120 00000 н.
0000007231 00000 п.
0000007347 00000 н.
0000007461 00000 п.
0000007577 00000 н.
0000007692 00000 п.
0000007801 00000 н.
0000007917 00000 п.
0000008028 00000 н.
0000008139 00000 н.
0000008254 00000 н.
0000008363 00000 н.
0000008472 00000 н.
0000008636 00000 н.
0000008789 00000 н.
0000008956 00000 н.
0000009125 00000 н.
0000009282 00000 п.
0000009362 00000 п.
0000009442 00000 н.
0000009523 00000 н.
0000009603 00000 п.
0000009683 00000 н.
0000009762 00000 н.
0000009842 00000 н.
0000009923 00000 н.
0000010002 00000 п.
0000010082 00000 п. 0000010163 00000 п.
0000010243 00000 п.
0000010322 00000 п.
0000010400 00000 п.
0000010480 00000 п.
0000010559 00000 п.
0000010638 00000 п.
0000010716 00000 п.
0000010793 00000 п.
0000010873 00000 п.
0000010953 00000 п.
0000011033 00000 п.
0000011114 00000 п.
0000011194 00000 п.
0000011274 00000 п.
0000011354 00000 п.
0000011435 00000 п.
0000011516 00000 п.
0000011800 00000 п.
0000012409 00000 п.
0000018399 00000 п.
0000018502 00000 п.
0000019015 00000 п.
0000019406 00000 п.
0000019796 00000 п.
0000020831 00000 п.
0000021663 00000 п.
0000021831 00000 п.
0000022299 00000 н.
0000022533 00000 п.
0000023189 00000 п.
0000023289 00000 п.
0000028419 00000 п.
0000028814 00000 п.
0000029209 00000 н.
0000029486 00000 п.
0000030218 00000 п.
0000030462 00000 п.
0000030769 00000 п.
0000031729 00000 п.
0000031950 00000 п.
0000032320 00000 н.
0000032470 00000 п.
0000032531 00000 п.
0000033667 00000 п.
0000037050 00000 п.
0000037371 00000 п.
0000037749 00000 п.
0000037952 00000 п.
0000038346 00000 п.
0000039609 00000 п.
0000040732 00000 п.
0000041085 00000 п.
0000042265 00000 п.
0000043277 00000 п.
0000047921 00000 п.
0000095177 00000 п.
0000128282 00000 н.
0000128747 00000 н.
0000128944 00000 н.
0000129228 00000 н.
0000129290 00000 н.
0000130633 00000 п.
0000130872 00000 н.
0000131202 00000 н.
0000131298 00000 н.
0000132895 00000 н.
0000133171 00000 н.
0000133709 00000 н.
0000133831 00000 н.
0000157163 00000 н.
0000157202 00000 н.
0000157727 00000 н.
0000157834 00000 н.
0000207979 00000 н.
0000208018 00000 н.
0000208076 00000 н.
0000208281 00000 н.
0000208386 00000 н.
0000208487 00000 н.
0000208607 00000 н.
0000208725 00000 н.
0000208842 00000 н.
0000208996 00000 н.
0000209119 00000 н.
0000209237 00000 н.
0000209388 00000 н.
0000209498 00000 н.
0000209600 00000 н.
0000209718 00000 н.
0000003885 00000 н.
0000003242 00000 н.
трейлер
] >>
startxref
0
%% EOF
702 0 объект
> поток
х ڔ RMhQfw6 ՚ Ve5EOk7Y
ECbnS
AzKML!
EP
# gy3 {XPyWtn> ^ Xo9 = C3 ܞ | h ‘{M tM lxdt, LJǏ; dXXtqN & Qhpv «‘R’] ӧl% ) (~ ۹ceHo ۻ / av, VW6 [SVjJB = XFD ^ ̲LA- + ̣hPZp
Водоотталкивающая пропитка поверхности для продления срока службы железобетонных конструкций в морских условиях: роль трещин
Повышение долговечности морских конструкций представляет интерес для многих исследователей. Исследование, представленное в этой статье, исследует эффективность водоредуктора и пропитки хлоридной барьерной поверхности бетонного покрытия железобетонных (ЖБИ) конструкций, подверженных воздействию морской среды. Особое внимание уделяется тому, как поверхностные трещины, образовавшиеся (1) до пропитки и (2) после пропитки, влияют на эффективность обработки поверхности. Эксперименты проводятся в среде, максимально приближенной к реальной влажной субтропической морской среде. Ряд железобетонных (RC) призм и бетонных цилиндров, каждый из которых был обработан различными коммерческими агентами для пропитки поверхности, подвергался циклическому воздействию морской воды на открытом воздухе для ускорения циклов сухой / влажной среды в течение 1 года.Были применены шесть типов агентов для пропитки поверхности, в том числе четыре типа водоотталкивающих агентов на основе силана и два типа блокаторов пор на основе силиката натрия (жидкое стекло). Были подготовлены три типа призм RC для моделирования различных возможностей растрескивания, которые могут возникать в бетонных конструкциях с пропиткой на поверхности в течение срока их службы. В первой группе призм трещины не возникли, в то время как трещины возникли до и после пропитки поверхности во второй и третьей группах соответственно.Зависимое от времени водопоглощение всех образцов контролировали во время циклов «сухой / влажный». Наконец, образцы были разрезаны, чтобы измерить глубину проникновения агентов для пропитки поверхности и профили проникновения хлоридов. Также были измерены участки с коррозией, заметной в стальной арматуре в призмах RC. Было обнаружено, что блокаторы пор на основе силиката натрия неэффективны для предотвращения проникновения хлоридов в бетон при моделировании воздействия на море. Было обнаружено, что долговременная эффективность водоотталкивающих агентов, используемых для пропитки поверхности, сильно зависит от типа агента и от того, проводилась ли пропитка до или после образования трещин.(A) Перепечатано с разрешения Elsevier.
- Наличие:
- Авторов:
- DAI, J G
- АКИРА, У
- WITTMANN, F H
- ЙОКОТА, H
- ZHANG, P
- Дата публикации: 2010-2
Язык
Информация для СМИ
Предмет / указатель терминов
Информация для заполнения
- Регистрационный номер: 01158289
- Тип записи: Публикация
- Агентство-источник: Транспортная исследовательская лаборатория
- Файлы: ITRD
- Дата создания: 3 июня 2010 г., 7:45
Ремонт трещин в бетонных конструкциях
В этой статье мы обсудим: — 1.Ремонт бетона полимерной пропиткой 2. Ремонт бетона на основе смол 3. Общее применение эпоксидных смол в бетонных конструкциях 4. Ремонт трещин в массивных конструкциях 5. Распространенные виды ремонта.
Ремонт бетона полимерной пропиткой:В этой системе ремонта поврежденная бетонная поверхность тщательно очищается и просушивается. После очистки и высыхания поверхность бетона с трещинами заливается мономером, который затем полимеризуется на месте, заполняя и структурно ремонтируя трещину.
Мономерная система — это жидкость, состоящая из небольших органических молекул, способных соединяться с образованием твердого пластика. Мономерная система, используемая для пропитки или впрыскивания в бетон, содержит катализатор или инициатор и основной мономер. Они также содержат сшивающий агент. При нагревании мономеры соединяются. Процесс соединения известен как полимеризация. После полимеризации продукт при охлаждении становится жестким, прочным и долговечным, пластичным, что значительно улучшает ряд свойств бетона.
Мономеры не смешиваются с водой. Они обладают разной степенью токсичности, воспламеняемости и летучести. Это жидкости с низкой вязкостью, которые впитываются в сухой бетон, заполняя трещины так же, как вода. Однако, если трещины содержат влагу, мономер не пропитается бетоном на каждой поверхности трещины, что приведет к неудовлетворительному ремонту. Кроме того, если летучий мономер испаряется до полимеризации, ремонт будет неэффективным.
Ремонт сломанных элементов:
Для ремонта сломанных элементов можно использовать метод пропитки полимером.В этом случае трещину сначала сушат, а затем временно закрывают водонепроницаемым листовым металлом. Теперь трещина пропитывается мономером и полимеризуется. При полимеризации мономера разрушенный элемент становится твердой массой с повышенной прочностью и свойствами. Большие пустоты в зонах сжатия могут быть заполнены мелкими и крупными заполнителями перед их заполнением мономерами, что обеспечит ремонт полимербетона.
Обработка бетонных поверхностей с большим количеством трещин:
В этом случае можно использовать вакуумную пропитку.
Процесс:
Ремонтируемая часть конструкции закрывается воздухонепроницаемой пластиковой крышкой, после чего воздух из всех трещин в крышке засасывается с помощью вакуума. После выпуска воздуха из всех трещин мономерный или полимерный раствор нагнетается под давлением в одно атмосферное в трещины и поры бетонной поверхности. По окончании пропитки крышку снимают до того, как пропитка затвердеет.
Выбор подходящей пропитки и степени вакуума зависит от опыта.Этот процесс широко используется для снижения проницаемости слабого бетона или кирпичной кладки. Этот процесс также может быть использован для улучшения абразивной стойкости промышленных бетонных плит перекрытия. Однако полимерная пропитка не оказалась успешной для ремонта мелких трещин.
Ремонт бетона на основе смолы: В трещинах в железобетоне шириной более 0,3 мм требуется герметизация для предотвращения проникновения влаги, кислорода, других вредных газов и т. Д.Выбор метода и материалов будет зависеть от причины растрескивания и от того, есть ли необходимость в постоянном структурном заполнении трещин для выполнения любого другого необходимого усиления.
Было обнаружено, что для восстановления первоначальной прочности конструкции очень эффективно использование эпоксидной смолы с низкой вязкостью. Система эпоксидной смолы позволяет полностью заполнить трещины размером менее 5 мм, используя метод впрыска под давлением. Однако работу следует проводить с умом, чтобы избежать сдувания поверхностных уплотнений из-за противодавления, которое может возникнуть в случае очень мелких трещин.Для заполнения мелких трещин может потребоваться постоянное давление в течение нескольких минут.
Обычно смола и отвердитель находятся в жидкой форме, и каждый сам по себе стабилен в течение неопределенного периода времени. При смешивании этих веществ происходит химическая реакция, и их жидкая система превращается в твердое пластичное твердое вещество при температуре окружающей среды. Они обладают отличными прочностными и адгезионными свойствами. Они устойчивы ко многим химическим веществам. Было обнаружено, что они обладают хорошей химической и физической стабильностью.Они быстро затвердевают и сопротивляются проникновению воды. Таким образом они обеспечивают долговечность и устойчивость к растрескиванию. Растворы на основе смолы можно получить, добавив в качестве наполнителя крупный песок.
Компаунды на основе эпоксидной смолы неизменно включают пластификаторы, наполнители, разбавители и наполнители для производства большого количества продуктов, обладающих широким диапазоном свойств. Отличные адгезионные характеристики, быстрое схватывание, высокая прочность и химическая стабильность привели к их широкому использованию в бетонных конструкциях.
Общее использование эпоксидных смол в бетонных конструкциях:В бетонном строительстве эпоксидные смолы используются для следующих целей:
(a) Для создания противоскользящих накладок и изнашиваемых поверхностей на бетонных полах.
(b) В качестве водонепроницаемой мембраны.
(c) Наиболее широко используется при ремонте выбоин.
(d) Для заделки трещин в элементах конструкции.
Чистая и сухая поверхность перед укладкой ремонтных материалов окрашивается эпоксидным составом.Трещины можно заделать эпоксидным компаундом, эпоксидным раствором или портландцементным раствором после грунтования поверхности эпоксидным компаундом. Для раннего и быстрого использования могут быть изготовлены покрытия из полимера или смолы. Их можно использовать раньше, так как они быстрее затвердевают. Поскольку они не имеют стыков, они более гигиеничны и устойчивы к химическому воздействию.
Материалы:
Класс эпоксидных, полиэфирных и акриловых смол известен как термореактивные материалы из-за того, что при отверждении их молекулярные цепи постоянно соединяются.Эти материалы не плавятся при нагревании, как термопласты. Эти материалы теряют прочность при повышении температуры. Обычно они поставляются в виде двух- или трехкомпонентной системы в виде смолы, отвердителя и наполнителя.
Классификация смол :
В целом смолы классифицируются следующим образом:
(а) Эпоксидные смолы
(б) Ненасыщенные реактивные полиэфирные смолы
(c) Ненасыщенные акриловые смолы.
Система акриловой смолы образует высокопрочные материалы. Они основаны на мономерах с очень низкой вязкостью или на смеси мономеров и мономеров метилметакрилата.
Полиэфирные и акриловые смолы содержат легковоспламеняющиеся летучие компоненты. Большинство акриловых смол легко воспламеняются с температурой вспышки ниже 10 ° C. Их пары также вызывают токсическую реакцию.
Свойства обычно используемых смол :
(a) Эпоксидные смолы:
Ниже приведены свойства эпоксидных смол:
(i) Их сила очень высока
(ii) Их связывающие характеристики хорошие.
(iii) Обладают высокой ударопрочностью
(iv) Обладают высокой химической стойкостью
Их можно использовать для придания нескользкой поверхности:
(b) Полимерные смолы:
Эти смолы имеют лучшую термостойкость, поэтому их можно укладывать в более широком диапазоне температур. Они смешиваются с цементом и мелким твердым заполнителем и могут укладываться толщиной до 15 мм.
(c) Поливинилацетат (PVAC):
Когда эти перекрытия из раствора накладываются на существующий бетон, они используются в качестве адгезива.Жидкость можно наносить прямо на чистую, прочную поверхность и дать ей высохнуть. Незначительное повторное эмульгирование пленки при повторном увлажнении путем нанесения свежего строительного раствора обеспечивает хорошее сцепление.
(d) Натуральный каучук Латекс:
Эта добавка имеет отличные адгезионные свойства, но ее трудно смешивать с обычным портландцементом. Обычно он используется с менее щелочным цементом с высоким содержанием глинозема для ямочного ремонта или для укладки полов, на которые следует укладывать виниловую плитку.
(e) Бутадиен-стирольный каучук (SBR):
Это хорошая и эффективная альтернатива поливинилацетату (ПВА). Он очень водостойкий. Однако высохшая пленка не дает хорошего сцепления при повторном смачивании. Таким образом, если дать высохнуть, он будет действовать как слой отслаивания. Следовательно, раствор следует наносить, пока клейкое покрытие SBR еще не высохло.
(е) Акриловые смолы:
Эти добавки при смешивании со строительными растворами развивают отличную водостойкость и улучшенную прочность сцепления.С помощью этого типа смол можно легко получить бесшовные, не пылящиеся тонкие перекрытия полов.
(г) Стиролакриловые смолы:
Смесь прочного стирола с акриловой смолой с использованием цементно-песчаного раствора в соотношении 1: 3 может использоваться для изготовления износостойких напольных покрытий при умеренных затратах.
Порядок ремонта :
(a) Использование полимерного раствора:
Требования к подготовке поверхности такие же, как и при ремонте на цементной основе.Компоненты материала на основе смолы необходимо тщательно перемешать в механических смесителях или мешалках. Большинство отказов при ремонте на основе смолы повторялись либо из-за неправильного перемешивания, либо из-за неправильного дозирования. Для небольших ремонтных работ, необходимых для правильного дозирования, компоненты обычно доступны в предварительно расфасованных упаковках.
После подготовки поверхности на только что обнаженную поверхность бетона и арматуры наносится грунтовочный слой или клейкий слой из ненаполненной смолы.Обычно достаточно одного слоя, но если субстрат пористый, потребуется два слоя. В случае нанесения двух слоев второй слой следует наносить, пока первый слой остается липким.
Заплаточный материал следует наносить, пока грунтовка еще липкая, и каждый последующий слой следует наносить до того, как предыдущий слой слишком сильно затвердеет. Материалы на основе смолы отверждаются или затвердевают в результате химической реакции, которая начинается, как только смешиваются составляющие материалы. Таким образом, у них мало жизнеспособности i.е. период перемешивания очень короткий. Следовательно, количество материалов, которые необходимо смешать в одной партии, следует предварительно рассчитать, чтобы его можно было использовать до того, как оно станет слишком жестким. Пластыри на основе смолы следует хорошо уплотнить, чтобы они стали непроницаемыми.
При использовании смол и отвердителей необходимо соблюдать обычные меры безопасности, т. Е. Следует носить перчатки и смывать брызги с кожи, но не следует использовать для этого растворители. Следует обеспечить соответствующую вентиляцию, а также курить, есть и пить. быть запрещено при нанесении материалов на основе смол.
(b) Инъекции смолы:
Впрыск полимера под давлением гарантирует, что герметизирующий материал или герметик проникает на всю глубину трещины.
Процедура:
Отверстия для впрыска просверливаются с близкими интервалами по длине трещины, и эпоксидная смола вводится под давлением в каждое отверстие по очереди до тех пор, пока инъекционный материал не начнет вытекать из следующего отверстия. Затем вводимое отверстие закрывается и обрабатывается следующее отверстие.
Меры предосторожности:
Перед нанесением эпоксидной смолы необходимо убедиться, что трещина на поверхности между отверстиями заделана быстрозатвердевающей смолой.
Ремонт трещин в массивных конструкциях:В этом случае просверливается серия отверстий диаметром обычно 20 мм и глубиной 20 мм, расположенных с интервалом от 150 до 200 мм, пересекающих трещину в нескольких точках, а затем в эти отверстия вводится эпоксидная смола для герметизации трещины.Метод успешно применяется при ремонте трещин в плотинах, опорах, зданиях и других подобных конструкциях.
Однако, если причина трещин не будет устранена, трещины могут снова появиться где-то в конструкции. Этот метод не считается эффективным, если трещины постоянно протекают и не могут быть высушены. Закачка эпоксидной смолы — это узкоспециализированная работа, которая требует высокого уровня навыков для удовлетворительного выполнения работы.
Этапы впрыска эпоксидной смолы :
Для инъекции эпоксидной смолы используются следующие этапы:
1. Подготовка поверхности:
Трещины очищаются путем удаления всей грязи, масла и жира, мелких частиц бетона и т. Д. Эти элементы могут препятствовать проникновению эпоксидной смолы и развитию связи между заполнителем и поверхностью трещин. Загрязнения желательно удалять, промывая поверхность водой или растворителем. Затем растворитель выдувают сжатым воздухом или сушкой на воздухе.
Чтобы проверить вытекание эпоксидной смолы до того, как она загустеет или затвердеет, следует заделать поверхностные трещины.Поверхность можно загерметизировать, нанеся эпоксидную смолу кистью по поверхности трещин и дав ей затвердеть. Если для впрыскивания эпоксидной смолы требуется очень высокое давление, то впрыскивание эпоксидной смолы следует проводить через канавку V-образной формы глубиной 12 мм и шириной 20 мм. После заливки эпоксидной смолы в канавку ее следует удалить заподлицо с поверхностью.
2. Установка входных портов или устройства:
Входное отверстие или ниппель — это отверстие, позволяющее впрыскивать клей прямо в трещину без утечки.Расстояние между отверстиями для впрыска зависит от многих факторов, таких как глубина и ширина трещин, изменение ширины трещины в зависимости от ее глубины, вязкость эпоксидной смолы, давление впрыска и т. Д. Выбор расстояния фактически зависит от опыта.
В случае V-образной канавки трещин, отверстие диаметром 20 мм на глубину от 12 до 25 мм ниже вершины секции с V-образной канавкой должно быть просверлено в трещине, и корма клапана шины приклеивается эпоксидным клеем. в дыре. В случае трещин другой формы, кроме V-образной канавки, входное отверстие обеспечивается путем соединения фитинга, имеющего шляпообразное поперечное сечение, с отверстием наверху для заполнения клея.Этот фитинг устанавливается заподлицо с бетонной поверхностью над трещиной.
3. Смешивание эпоксидной смолы:
Смешивание может производиться как периодическим, так и непрерывным способом. При периодическом смешивании компоненты клея предварительно смешиваются в определенных пропорциях с помощью механической мешалки в количествах, которые могут быть использованы до начала отверждения материала. По мере отверждения материала нагнетание под давлением становится более трудным. В системе непрерывного смешивания два жидких компонента клея проходят через дозирующий и приводной насосы, а затем проходят через автоматическую смесительную головку.Система непрерывного смешивания позволяет использовать клеи с быстрым схватыванием и коротким сроком службы.
4. Впрыск эпоксидной смолы:
В простейшей форме инъекционное оборудование представляет собой резервуар или воронку, прикрепленную к длинной гибкой трубке. Эта система создает гравитационный напор для текущего материала. При небольшом количестве ремонтных материалов обычно наиболее экономичным является небольшое ручное оружие. Эти небольшие пистолеты могут поддерживать постоянное давление, что снижает вероятность повреждения поверхностного уплотнения.
Для больших работ часто используются насосы с механическим приводом для впрыска. Следует тщательно выбирать давление, которое необходимо приложить для введения материала. Использование чрезмерного давления может увеличить количество трещин, что приведет к дополнительным повреждениям. Давление впрыска зависит от глубины и ширины трещин, вязкости смол и редко превышает 0,1 МПа.
Мелкие трещины предпочтительно вводятся под низким давлением, чтобы позволить материалу втягиваться в бетон капиллярным актином.Для увеличения давления впрыска в процессе работы обычной практикой является преодоление повышенного сопротивления потоку, поскольку трещина заполняется материалом. Для относительно более широких трещин может хватить гравитационного напора в несколько сантиметров.
В случае вертикальных и наклонных поверхностей процесс впрыска должен начинаться с впрыска эпоксидной смолы во входное отверстие на самом нижнем уровне, пока уровень эпоксидной смолы не достигнет входного порта выше. Затем инъекционная трубка удаляется и нижнее входное отверстие закрывается.Чтобы загнать эпоксидную смолу в тонкие трещинки, на которые нанесена линия волос, на порт, из которого была извлечена инъекционная трубка, может быть приложено давление до 0,7 МПа на период от 1 до 10 минут с использованием инертного газа. Процесс повторяется на последовательно расположенных портах, расположенных выше, до тех пор, пока трещины не будут полностью заполнены и все порты не будут закрыты.
Для горизонтальных трещин инъекцию следует начинать от одного конца трещины до другого таким же образом. Если поддерживаемое давление остается постоянным, это означает, что трещина заполнена.Если давление не остается постоянным, это означает, что эпоксидная смола все еще течет на незаполненные участки или вытекает из трещины.
5. Удаление поверхностного уплотнения:
После отверждения введенной эпоксидной смолы поверхностное уплотнение можно удалить шлифованием или другим подходящим способом. Фитинги и отверстия на входных портах следует покрасить эпоксидным герметиком.
6. Меры предосторожности в отношении здоровья и безопасности:
Эпоксидные материалы токсичны и вызывают раздражение кожи.Следовательно, всегда следует избегать контакта с кожей, вдыхания их паров и проглатывания.
Необходимо соблюдать следующие меры предосторожности:
(a) Все лицо должно быть закрыто, и во время всех операций смешивания и смешивания следует использовать защитные очки.
(b) Следует использовать резиновые перчатки, полиэтилен или защитный комбинезон.
(c) Для защиты кожи можно использовать крем для кожи.
(d) Должна быть обеспечена соответствующая противопожарная защита.
Распространенные виды ремонта бетонных конструкций:и. Герметизация трещин:
Каждая бетонная конструкция имеет стыки и трещины, поэтому соединения и герметики для трещин очень важны в бетонных конструкциях. Герметики трещин должны обеспечивать структурную целостность и работоспособность. Они также должны обеспечивать защиту от проникновения или попадания вредных жидкостей и газов.
ii. Метод запечатывания:
Для герметизации трещины ее следует увеличить по длине на открытой поверхности.Процесс увеличения трещины известен как преследование или продвижение трещины. После увеличения трещины ее закрывают подходящим герметиком для швов, как показано на рис. 26.11.
Работа без маршрутизации может повлиять на постоянство ремонта. Операция фрезерования заключается в прорезании достаточно большой канавки для размещения герметика на поверхности. Паз можно вырезать пилой по бетону или ручным инструментом. Минимальная ширина фрезерования 6 мм достаточна, так как ремонт более узких канавок затруднен. Перед нанесением герметика или герметика поверхность фрезерованного стыка следует очистить струей воздуха и дать высохнуть.
Функции герметика :
Ниже приведены функции герметика или скаляра:
1. Для предотвращения утечки воды на арматуру.
2. Предотвратить развитие гидростатического давления внутри соединения.
3. Проверить появление пятен на поверхности бетона.
4. Чтобы предотвратить развитие проблем с влажностью на обратной стороне элемента.
Часто в качестве герметика используют эпоксидные компаунды. Когда внешний вид не важен и не требуется водонепроницаемость шва, применяют герметики для швов горячей заливки. Уретаны, которые остаются эластичными в широком диапазоне температур, успешно используются для заделки трещин шириной до 20 мм и значительной глубины.
Гибкое масштабирование :
Для ремонта активной трещины необходимо обеспечить ее непрерывное движение i.е. его движение не проверяется. Этого можно достичь, проследив за трещиной по ее длине, этот процесс известен как раскрой или преследование трещины. Поверхность трещины подготавливается, как описано выше, и заполняется подходящим гибким герметиком, отформованным на месте. Деформационная способность герметика должна быть того же порядка, что и у материала трещин.
Широкая трещина распространяет движение на большую ширину, так что возникающая деформация совместима с используемым герметиком. Герметик должен прилипать к сторонам паза или фрезерования, но не должен приклеиваться снизу, чтобы движение в трещине распространялось на всю ширину паза.Это может быть достигнуто за счет обеспечения разрыва склеивания или отсоединения полос материала, такого как полиэтилен или чувствительная к давлению лента, в нижней части оправки перед нанесением герметика.
Эта отклеивающая полоска не связывает герметик во время или до отверждения или отверждения герметика и позволяет герметику изменять свою форму без концентрации напряжения на дне. Вид в разрезе типичного деформационного шва или гибкого уплотнения показан на рис. 26.12. С увеличением ширины паза движение трещины, которое вызывает растяжение или сдвиг в герметике, будет оказывать значительно меньшее напряжение на границе раздела клея с бетоном, что позволяет лицевой уплотнитель, чтобы справляться с обширными движениями.
Предоставление дополнительной стали:
Трещины в железобетонных элементах, обычно настилах мостов, можно успешно отремонтировать с помощью инъекции эпоксидной смолы и арматурных стержней.
Порядок действий следующий:
(a) 1-я трещина заделывается эпоксидной смолой.
(b) После заделки трещины просверливаются отверстия диаметром 20 мм под углом 45 ° к поверхности элемента, пересекающие плоскость трещины примерно под прямым углом.
(c) Арматурные стержни диаметром от 12 до 16 мм помещаются в просверленные отверстия. Эти стержни должны выступать не менее чем на 50 см с каждой стороны трещины. Расстояние между этими стержнями может быть принято в соответствии с потребностями или в соответствии с конструкцией.
(d) Отверстия и плоскость трещины заполняются эпоксидной смолой под низким давлением от 0,35 до 0,55 МПа. Эпоксидная смола связывает стержни со сторонами отверстия и заполняет плоскость трещины. Таким образом, поверхность бетона с трещинами приобретает монолитную форму.
Для успешного ремонта необходим эластичный герметик для наружных трещин. Для этой цели нашли применение гелевые эпоксидные герметики для трещин. Эти герметики следует наносить равномерным слоем толщиной от 1,5 до 2,5 мм, доходя примерно до 20 мм с каждой стороны трещины.
Для местного упрочнения наиболее практичным и экономичным оказалось приклеивание смолой плоских стальных пластин к внешней поверхности критического элемента конструкции моста или здания.
Зашивание трещин :
Процесс сшивания трещин используется, когда прочность элемента на растяжение должна быть восстановлена по основным трещинам. Строчка не закрывает трещину, а только предотвращает ее дальнейшее распространение. Сшивание имеет тенденцию к увеличению жесткости конструкции, что может сконцентрировать общую структурную сдержанность, вызывая образование трещин в бетоне где-то еще. Таким образом, необходимо, чтобы участок, прилегающий к строчке, был усилен с помощью внешнего армирования, встроенного в подходящую накладку.
Порядок прошивки :
Собачка для шитья представляет собой П-образный металлический блок с короткими ножками.
Порядок действий следующий:
(a) Отверстия просверливаются с обеих сторон трещины в шахматном порядке.
(b) Отверстия полностью очищаются струей воздуха или другим способом.
(c) Теперь скобки вставляются в отверстия, подготовленные поперек трещины.
(d) Отверстия со скобами для сшивания заполняются либо безусадочным цементным раствором, либо системой склеивания на основе эпоксидной смолы.
Собачка для шитья должна быть переменной длины и ориентации или и того, и другого. Он должен быть расположен так, чтобы напряжение, передаваемое через трещину, не концентрировалось в одной плоскости с в сечении, а распространялось на большую площадь. Расстояние между сшивающими скобами около концов трещины должно быть уменьшено.
В случае изгибаемых элементов сшивание должно выполняться на натяжной поверхности, где происходит движение. В случае, если элемент находится под осевым натяжением, то скобки должны быть размещены симметрично, даже если необходимо прибегнуть к сносу или выемке грунта, чтобы получить доступ к противоположной стороне секции.
В этом случае собачки должны быть относительно тонкими и длинными. Эти собаки не переносят большой силы сжатия. В случае, если трещина имеет тенденцию к закрытию, а также к открытию или распространению, собаки должны быть укреплены путем заключения в покрытие. В случае водоудерживающих конструкций трещины сначала герметизируются перед началом сшивания.