Усадка газобетона происходит за счет потери адсорбированной воды из материала и имеет важное значение для газобетона из-за его высокой общей пористости (40 ± 80%) и значительной поверхности пор (около 30 м2/г). 1 Уменьшение размера пор в газобетоне, а также более высокий процент пор меньшего размера приводит к увеличению усадки газобетона. Структурная модель усадки газобетона Нильсона 2 объясняет возникновение усадки за счет сжатия материала вакуумом гидравлического происхождения в порах газобетона. Капиллярная теория усадки газобетона предполагает уменьшение объема блоков ячеистогобетона за счет капиллярного поверхностного натяжения между стенок пор. 3 Усадка газобетона на основе исключительно цементного связующего значительно выше, чем усадка газобетона на основе извести или смеси извести с цементом. Усадка газобетона на основе смеси извести и цемента — наименьшая. С увеличением количества активного кремния усадка увеличивается и достигает максимального значения при замене 30 ± 60% диоксида кремния замены, а затем начинает снижаться. 4 Применение инертных заполнителей (зола) уменьшает величину усадки газобетона. На величину усадки влияют технологические особенности производства газобетона: продолжительность и способ отверждения газобетона, давление в автоклаве, химический состав кремнесодержащих заполнителей, размер и форма блоков и условия их хранения. Добавление в рецепт смесей суперпластификаторов и молотых кремнесодержащих веществ практически не влияет на величину усадки. Таким образом, усадка при высыхании газобетона больше зависит от физической струкутуры материала, а не от его химического состава. 5 ![]() При нормальных условиях автоклавного газобетона (Aeroc) составляет менее 0,3 мм/м при уменьшении влажности газобетона от 35% до 5% по массе. Усадка газобетона может длиться до 2 лет после окончания строительства. При высушивании газобетонных блоков до влажности ниже 2% и далее — усадка газобетонных блоков значительно возрастает и для уменьшения влажности от 5% до 0% составляет около 2 мм/м. Это свойство нужно учитывать при кладке из газобетонных блоков или панелей (новая форма товарного газобетона фирмы Hebel) ограждений каминов, дымоходов, сушильных камер и подобных им конструкций, подвергающихся длительному воздействию сухого горячего воздуха и высоких температур. Нормативная усадка при высыхании ячеистых бетонов, изготовленных на песке, не должна превышать 0,5 мм/м — для автоклавных бетонов марок D400-D1600 и 3,0 мм/м — для неавтоклавных бетонов марок D300-D1600.9
При чрезмерном нагреве при пожаре может происходить быстрая усадка газобетона. Огнестойкость газобетона гораздо выше, чем обычного тяжелого бетона. 11 Это в значительной мере обусловлено гомогенной структурой газобетона без разнородных включений, как в тяжелом бетоне, что приводит к образованию трещин из-за разного расширения элементов тяжелого бетона при нагревании. Лучшей устойчивостью к огню из-за меньшей газопроводимости и теплопроводности обладают ячеистые бетоны с закрытой ячеистой структурой (пенобетон). Ячеистый бетон автоклавного твердения относится к негорючим (НГ) материалам в соответствии с ГОСТ 30244. Многочасовой пожар в здании из газобетона ведет к снижению влажности всей толщи кладки и развитию усадки газобетона до максимальных значений 2 мм/м, что приводит к появлению мелких усадочных трещин на поверхности газобетонных блков, не влияющие на прочностные характеристики газобетонной стены в целом.12 Согласно данным Таблицы 3 Пособия к СНиП II-2-80 13 перегородка из ячеистого бетона плотностью 800 кг/м3 при толщине 75 мм имеет предел огнестойкости 2,5 часа, а толщиной 80 мм – 3 часа. ![]() |
1 Ziembika H. Effect of micropore structure on cellular concrete shrinkage. //Cem Concr Res 1977;7:323-332. 2 Nielsen A. Shrinkage and creep-deformation parameters of aerated, autoclaved concrete. In: Wittmann FH, editor. Pro ceedings Autoclaved Aerated Concrete, Moisture and Properties. Amsterdam: Elsevier; 1983. p. 189±205. 3 Tada S. Pore structure and moisture characteristics of porous inorganic building materials. In: Wittmann FH, editor. Proceedings Advances in Autoclaved Aerated Concrete. A.A. Balkema, 1992:53±63 4 ACI Committee 516. High pressure steam curing: Modern practice and properties of autoclaved products. J Am Concr Inst 1965; Title no. 62±53 5 Narayanan N. Influence of composition on the structure and properties of aerated concrete. M.S thesis. IIT Madras, 1999. 6 Tada S, Nakano S. Microstructural approach to properties of moist cellular concrete. In: Wittmann FH, editor. Proceedings Autoclaved Aerated Concrete, Moisture and Properties. Amsterdam: Elsevier; 1983. p. 71±89 7 Alexanderson J. Relations between structure and mechanical properties of autoclaved aerated concrete. Cem Concr Res 1979;9:507±14 8 Schubert P. Shrinkage behaviour of aerated concrete. In: Wittmann FH, editor. Autoclaved Aerated Concrete, Moisture and Properties. Amsterdam: Elsevier; 1983. p. 207±17 9 П.4.4.1 СТО 501-52-01-2007 «Проектирование и возведение ограждающих конструкций жилых и общественных зданий с применением ячеистых бетонов в Российской Федерации». 10 Там же: П.4.4.2. 11 Valore RC. Cellular concretes-physical properties. //J Am Concr Inst 1954;25:817-836. 12 Aeroc: руководство пользователя. – СПб.:Aeroc.-2009. 13 Пособие по определению пределов огнестойкости конструкций, пределов распространения огня по конструкциям и групп возгораемости материалов к СНиП II-2-80. ![]() |
Усадка в доме из газобетона — АлтайСтройМаш
Усадка газобетона – довольно интересная тема, потому как производители то и дело говорят о том, что газоблоки не подвергаются усадке. Мы знаем о газобетоне всё и готовы дать окончательный вердикт: усадка газобетонных блоков – частое явление!
Усадка дома из газобетона: причины
Все материалы, которые в своём составе имеют цемент, дают усадку. Но плохо ли это? Существуют строительные нормы, регулирующие степень допустимой усадки материала. Что касается газобетона, усадка не более 3.0 мм на метр квадратный. Это в 4 раза меньше, чем усадка у дерева.
Что происходит с материалом, почему он усаживается? В своём составе газобетонные блоки имеют воду, и она понемногу испаряется в процессе эксплуатации дома. Обычно усадка происходит вплоть до двух лет, поэтому нет смысла ждать, чтобы вставлять двери и окна — это очень долгий процесс.
Самую большую усадку дают деревянные дома, а при строительстве газобетонного дома можно ставить окна сразу. Если проёмы выполнены верно, применено армирование и качественно сделаны перемычки над окнами, то всё пройдет хорошо, и не стоит беспокоиться о появлении трещин.
Что влияет на усадку дома из газобетона?
Во-первых, есть большая разница, когда выполнять работы. Если начинать строительство летом, то усадка займет примерно в 2 раза больше времени, чем, если бы постройка совершалась зимой. В первые месяцы особенно видно, что усадка происходит, а затем это уже очень незаметный процесс.
Во-вторых, важно, где именно происходит стройка, в какой местности. Ваше строительство может находиться как на солнечном пространстве, так и быть скрыто в тени. В зависимости от этого материал либо быстрее сохнет, либо медленнее отдает влагу, поэтому сроки усадки могут быть разными.
Близко растущие деревья тоже влияют на процесс строительства, ускоряя усадку дома.
В-третьих, влияющим фактором является техника возведения здания.
Итак, лучше всего вести строительство на открытой и ровной местности, где солнечные лучи и тени равномерно распределены. А посадкой деревьев спокойно можно заняться уже после усадки, то есть, в идеале, через год-полтора.
Последствия усадки дома из газобетона: трещины
Из-за процесса усадки в доме из газобетона могут появиться трещины: как маленькие, так и большие по всему периметру здания.
Как можно обезопасить себя от такого?
Конечно же, основа дома, фундамент, должен быть сделан качественно. Если фундамент заложен неверно, то даже малейшая усадка даст знать о себе появлением трещин, причем сам газоблок здесь ни при чём: на неровном фундаменте покосится всё здание, из чего бы оно ни было.
Но появление трещин – это не беда, потому как с ними легко можно справиться. Как именно? Читайте в нашей статье: «Трещины в доме из газобетона: раскол неминуем?»
К тому же, если строительство выполнено с умом, то и усадка дома пройдет для вас без последствий.
Производить газобетон самостоятельно и быть спокойным за его качество можно с помощью оборудования от компании “АлтайСтройМаш”. Производственные линии бывают разных размеров и легко транспортируются в любой регион России, а также страны СНГ: Казахстан, Узбекистан, Кыргызстан и другие.
Усадка пенобетона — статьи от Bonolit
Усадка пенобетона представляет собой комплекс различных изменений структуры материала в процессе отвердения, которые при нарушении технологии могут привести к существенному ухудшению технических характеристик блоков, что следует учитывать как на стадии изготовления и сушки, так и при строительстве. Если Вы решили использовать для возведения дома этот вид материалов, перед тем как купить пеноблоки от производителя, будет полезно узнать, какие существуют мероприятия по предотвращению негативного воздействия усадки на свойства блоков и конструкции здания в целом.
Специалисты выделяют четыре основных вида структурных изменений пенобетона: контракционная, карбонизационная, температурная и влажностная усадка. В данной статье мы рассмотрим более подробно каждый из них. Это поможет правильно подобрать материалы для строительства, в том числе и клей для газобетона или пенобетонных блоков.
Контракционная усадка
Контракционная усадка свойственна всем видам строительных материалов, в число ингредиентов для изготовления которых входит цементный раствор. Ее особенность заключается в том, что при отвердении и образовании камня происходит уменьшение объема смеси. Избежать существенного изменения структуры блоков можно при условии значительного снижения пропорционального количества цемента. При этом такая манипуляция оказывает негативное влияние на прочностные характеристики пенобетона. В случае с ячеистыми бетонами это приводит к потере не только прочности, но и ухудшению теплопроводности. Несмотря на это, контракционная усадка оказывает наименьшее влияние на эксплуатационные параметры материала по сравнению с другими видами структурных изменений.
Карбонизационная усадка
Карбонизационная усадка происходит в процессе воздействия углекислого газа на известь цементного камня. Это приводит к образованию мела, что сопровождается уменьшением общего объема блока. Данный усадочный эффект начинается сразу же после формирования пенобетона и продолжается на протяжении всего эксплуатационного периода постепенно разрушая его. На скорость развития карбонизационной усадки влияет плотность и сорбционная влажность материала.
Температурная усадка
Температурная усадка является последствием особенности изготовления материала. Она возникает при экзотермическом процессе создания цементного камня. Отливка блоков сопровождается значительным нагревом сырья, а интенсивное охлаждение верхнего слоя приводит к возникновению температурного деформационного напряжения. Из-за этого в пенобетоне возникают мелкие трещины, которые в процессе эксплуатации развиваются дальше, тем самым снижая прочность материала.
Влажностная усадка
Влажностная усадка пенобетона происходит как в процессе его эксплуатации, так и на стадии изготовления. В первом случае процедура носит цикличный характер. Материал намокает и расширяется, затем сужается, испаряя влагу. В итоге это приводит к возникновению мелких трещин, которые углубляются при каждом цикле. Способствовать этому может обустройство слабой изоляционной защиты или ее отсутствие.
Как правило, в процессе эксплуатации влажностная усадка проходит достаточно медленно. Более значимое деформационное напряжение образуется на этапах изготовления материала. При производстве пенобетон подвергается интенсивному высушиванию, из-за чего возникают первичные дефекты, которые могут дальше развиваться в процессе эксплуатации при определенных условиях.
Снизить последствия влажностной усадки можно методом регулярного увлажнения поверхности пенобетона при сушке или с помощью экранирования. Для этого используется полиэтиленовая пленка. Технология изготовления качественного материала включает стадию выдержки на складах, в процессе которой происходит полный контроль высыхания. При монолитном домостроении пенобетон накрывают полиэтиленом и выдерживают определенное время. Вышеописанные операции требуют дополнительных временных и финансовых затрат, из-за чего ими часто пренебрегают, особенно при кустарном производстве.
Наиболее уязвимые зоны пенобетонных блоков
Наибольшей деформации подвергаются углы блоков. Это объясняется наименьшей толщиной материала на данных участках. Высыхание в этих зонах происходит максимально интенсивно. Усиление эффекта достигается благодаря анизотропии свойств пенобетона. Для снижения этого воздействия в раствор подмешивают различные гидрофобные добавки. К сожалению, в неавтоклавных ячеистых бетонах такой способ модификации не дает должного эффекта. Проблема заключается в естественном высыхании. Испарение влаги формирует значительную сеть капилляров, а применяемые добавки не обладают необходимыми свойствами для заполнения образовавшегося пространства без наличия определенного уровня влажности.
причины возникновения и способы устранения с сайта ПЕНОБЛОКЕР
Много нареканий вызывают усадочные явления пенобетонных изделий, которые сопровождаются образованием трещин. Между тем, усадочные явления можно минимизировать, используя грамотный подход к решению этой проблемы.Усадка является характерной особенностью материалов, содержащих в своем объеме цемент. Специалисты делят ее на несколько составляющих, усадку контракционную, влажностную и карбонизационную. Подверженность ячеистых и поризованных легких бетонов усадке не оспаривается. Причина в пористо-ячеистой структуре легких бетонов, которая способствует ускоренному высыханию. В этом имеется часть вины самих производителей, которые для сокращения процесса, исключают из технологии так называемое, влажностное выдерживание.
Сушить пенобетон ytong происходит послойно, более влажный внутренний объем и поверхностные слои обладают разными свойствами, что неминуемо приводит к образованию напряжений и появлению трещин. Быстрее всего теряют влагу кромки и углы, поэтому большая часть трещин образуется на этих участках.Этот недостаток материала может компенсироваться более продолжительной сушкой под влагонепроницаемой пленкой, исключением компонентов и присадок, способствующих ускорению твердения.
Причина основных проблем
- Влажностное выдерживание заключается в твердении материала в условиях повышенной влажности, на протяжении 28 дней. За это время пенобетон набирает около70% заданной прочности и становится пригодным для кладки.
- На протяжении этого времени усадочные явления практически останавливаются. Остаточная усадка, составляющая менее 0,1%, заканчивается одновременно с остаточным твердением, для которого требуется, в зависимости от внешних условий, от 8 до 12 месяцев.
Это явление позволяет производителям утверждать, что пенобетон аэростон с течением времени приобретает дополнительную прочность.
На практике, твердеющие блоки, для экономии места на стеллажах и ускорения сушки, устанавливают на ребро. В оптимальном варианте, изделия необходимо периодически переворачивать, но объем работы и необходимость ручного труда, вынуждают производителей это условие игнорировать. В лучшем случае, поверхность блоков увлажняются. Обильная поливка так же, нежелательна, на прочности материала это не отражается, но процесс сушки может существенно притормозить. По мере твердения, интенсивность увлажнения снижается.
Скорость сушки определяется несколькими факторами;
- температурой и влажностью окружающей среды,
- особенностями структуры материала,
- наличием дополнительных компонентов и присадок,
- маркой цемента и качеством песка.
Основные проблемы
Основная проблема производителя – создание, для пенобетонных полуфабрикатов, оптимальных условий для созревания. Любое
неквалифицированное изменение технологии, в частности, использование ускоряющих твердение присадок, обработка теплым воздухом, неизбежно приводит к ухудшению эксплуатационных свойств материала, нарушению геометрии, образованию трещин и сколов при транспортировке.
Проблема частично решается армированием пенобетона. Такой материал, известный на строительном рынке под названием фибропенобетона. Для повышения трещиностойкости, улучшения прочностных характеристик в состав материала вводится полимерное, чаще всего, полипропиленовое волокно, в количестве от 0,5-2% от общего объема. Армирование способствует равномерному распределению локальных нагрузок, повышает стойкость фибропенобетона к воздействию влаги
Усадка дома из газобетона
Это важно не только при сооружении фундамента и стен, но и при проведении отделочных работ.
Процесс усадки проходят практически все стройматериалы, в том числе и газобетонные блоки.
Поэтому после кладки из них стен нужно выждать определённое время, необходимое для его окончательного высыхания и уплотнения.
Если этого не сделать, то штукатурка начнёт деформироваться и осыпаться, под ней начнёт накапливаться влага, что может спровоцировать появление плесени.
Чтобы этого не произошло, необходимо подождать, когда окончится процесс усадки, и только после этого начинать работу по отделке стен.
Только так можно будет избежать проблем во время последующей эксплуатации дома, стены которого останутся на долгие годы целыми и ровными.
Каждый строительный материал имеет свои сроки усадки, хотя зависят они от многих факторов: структуры самого материала, способа его производства, времени года и погодных условий, при которых шло строительство дома.
Всё это относится и к газобетонным блокам также.
На время усадки газобетонных блоков в первую очередь влияет их пористая структура, в ячейках которой остаётся влага после производства блоков на заводе.
Эта влага уходит в естественных условиях, выдуваясь ветром, высыхая на солнце.
На газобетоне можно проводить отделочные работы, когда вместимость влаги в нём уменьшится до 8%.
Занимает этот процесс примерно шесть месяцев.
На сроки начала отделки влияет и дата окончания строительства.
Если дом был возведён зимой, то отсчёт времени для усадки начинается сразу же по окончании строительных работ.
Окончание же работ летом растягивает время ожидания усадки газобетона до года – нужно будет переждать все последующие после возведения здания сезоны, до следующего лета.
На то, сколько времени будет идти усадка газоблоков, очень влияет их состав. Так, дольше всего сохнут известково-цементные блоки, для них этот срок может длиться два года.
Усадка газобетонных блоков сильно влияет на сроки отделочных работ, а вот устанавливать двери и окна можно сразу же, окончив работу по монтажу коробки.
Это является большим преимуществом стен из газобетона, так как для кирпичных построек устанавливать двери и окна можно не раньше, чем через год после окончания возведения стен.
Автоклавный и неавтоклавный газобетон — что лучше?
Автоклавные блоки формируются при большой температуре и давлении, неавтоклавные — твердеют при атмосферном давлении или в условиях нагревания. Что лучше и почему?
Главные отличия АВТОКЛАВНОГО и неавтоклавного ГАЗОБЕТОНА:
- Качество. Автоклавные блоки изготавливаются только в заводских условиях. Производить автоклавный газобетон в подпольных условиях невозможно, а неавтоклавный — твердеет в естественной среде, поэтому изготовлять его можно в «кустарных» условиях;
- ГОСТ. Автоклавный газобетон производится согласно ГОСТу 2007 года — ГОСТ 31360-2007, такие блоки имеют сертификат качества. Клиенты могут быть уверены в качестве покупаемой продукции. Неавтоклавный газобетон изготавливается по ГОСТу 25485-89 и уже долгое время технология и качество не изменяется.
- Прочность. Ячеистые бетоны изготавливают разной плотности: от 400 до 800 кг/м3 классом. Наш самый ходовой блок является D500, при этом его плотность имеет класс по прочности на сжатие В2,5. Прочность неавтоклавного бетона может быть меньше В1,5, конструкция на таких блоках может не выдержать нагрузки;
- Крепление. Автоклав значительно повышает прочность газобетона. В основание из автоклавного газобетона можно закрепить не только шкафы и полки, но и бойлеры, кондиционеры, вентиляционные фасады;
- Усадка не страшна. В сравнение с неавтоклавным газобетоном, автоклавные блоки полностью набирают свою прочность уже в процессе производства. Поэтому усадка им не страшна. Для автоклавного газобетона показатель усадки не превышает 0,5 мм/м, тогда как для неавтоклавных материалов он составляет от 1 до 3 мм/м.
Неавтоклавные блоки дают большую усадку, она достигает до 0,23— 0,34 мм/м. Это может сильно повлиять на конструкцию здания;
- Экологичность. Мы не устанем говорить, что наш автоклавный газобетон полностью экологичный материал. Микроклимат в постройке из автоклавных блоков можно сравнивать с климатов деревянного дома. Газобетон изготавливается из материального сырья, поэтому он не поддается гниению. А его способность регулировать влажность, исключает вероятность появления плесени и грибков. В составе неавтоклавного газобетона чаще всего добавляют смесь шлаков и золы. В результате химической реакции, полученный состав выделяет сферические поры;
- Геометрия. Точность геометрии блоков из автоклава регулируется современным ГОСТом. Геометрия неавтоклавный блоков разнородна. Блоки начинают крошиться и скалываться;
- Теплоизоляция. По сравнению с неавтоклавными блоками и кирпичом, автоклавный газобетон обладает на 30% лучшим показателем по теплоизоляции.
Давайте подведем итоги:
- Неавтоклавные блоки дешевле, чем бетон из автоклава;
- Газобетонные блоки автоклавного твердения отличаются физико-механическими свойствами
- Богатый выбор марок по прочности. Прочность автоклавных газоблоков выше в полтора-два раза неавтоклавных материалов;
- Производят автоклавные блоки только на современных заводах;
- Автоклавные блоки лишены такого недостатка, как усадка;
- Соответствие параметров ровности автоклавных блоков;
- Блоки из автоклава абсолютно экологичны.
Как мы видим, автоклавный газобетон превосходит неавтоклавный практически по всем показателям. На нашем заводе ПТЖБ изготавливаются газоблоки из автоклава. Только так мы можем быть уверенны в качестве своих изделий. Здания из таких блоков получаются более прочные, а постройка проходит легче и проще.
Усадка газобетона » Строительно-информационный портал
Состав газобетона оказывает большое влияние не только на его прочностные показатели, но и на усадку.
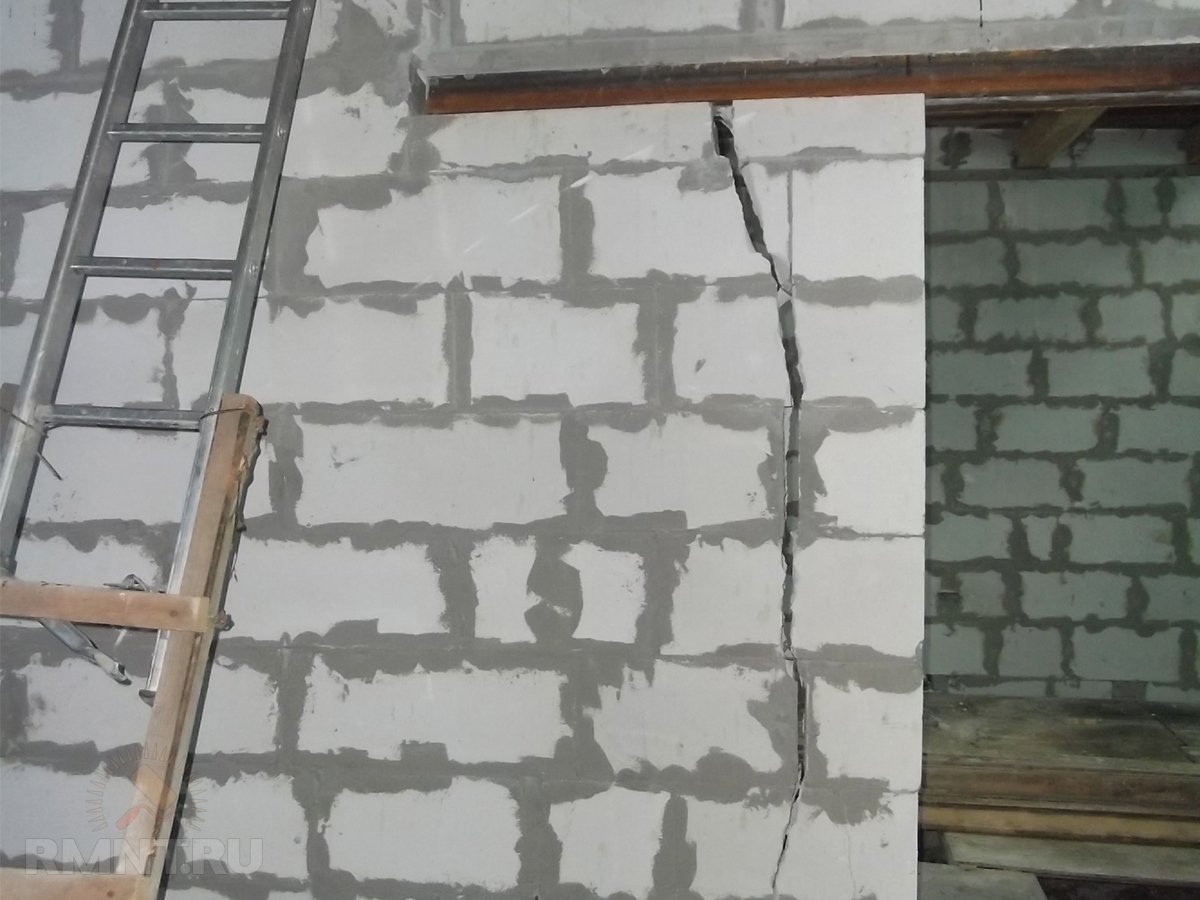
Результаты наших исследований по усадке ячеистого бетона разного состава объемным весом 700—800 кг/м3 показали, что эта величина колеблется от 0,45 до 0,6 мм/м.
На рис. 96 приведены данные по прочности и усадке газобетона объемным весом 1000 кг/м3 разных составов. Величину усадки определяли после запаривания на образцах размером 220х70х70 мм, которые помещали в приборе с индикатором. Цена деления индикатора составляла 0,01 мм. Первые нулевые отсчеты производили на образцах сразу же после запаривания, последующие — через 10, 20, 30, 60 и 90 суток. Образцы находились в помещении, в котором относительная влажность колебалась от 70 до 80%, а температура — от 17 до 24° С.
Данные исследований позволяют сделать следующие выводы. Значительное увеличение усадки во всех образцах наблюдается в первые 30 суток после запаривания и составляет в среднем 70% конечных значений. Через 60 суток после автоклавной обработки усадка практически прекращается. Она может быть снижена путем введения в состав газобетона немолотого песка. При добавке его в количестве 12% усадка газобетона снижается на 30%, не вызывая заметного снижения прочности.
Усадка газошлакобетона и газокукермита имеет примерно такие же значения, как и газобетона на клинкерном вяжущем. Усадка газосиликата, замеренная на аналогичном приборе, при хранении образцов в условиях с относительной влажностью 60—75% к 12 месяцам достигает 0,5 мм/м.
Аналогичные показатели по усадке имеет газобетон фирмы «Сипорекс». В докладе Баве на Втором международном конгрессе по бетону отмечается, что усадка газобетона незначительна и составляет 0,5 мм/м.
Неренст в своем докладе на Втором международном конгрессе по бетону привел данные исследований по усадке ячеистого бетона, которые проводились в лаборатории датского общества «Газобетон» по следующей методике: «. .. Испытываемые образцы хранятся в стальных емкостях при постоянной температуре и неизменной относительной влажности. В одной из этих емкостей поддерживается 100%-ная относительная влажность. Взятые непосредственно после автоклавной обработки образцы поглощают определенное количество воды и в 2-месячном возрасте показывают удлинения примерно 0,3 мм/м. Если же образцы, испытываемые непосредственно после автоклавной обработки, помещаются в среду с 45%-ной относительной влажностью, то после хранения их в течение 8 месяцев наблюдается усадка 0,1 мм/м. Эти значения относятся к газобетону без добавки золы-уноса. Таким образом, общая разность между разбуханием при 100% относительной влажности составляет 0,4 мм/м.
Влияние состава и отверждения на усадку газобетона при высыхании
Валор Р. К., «Ячеистые бетоны. Физические свойства», Журнал Американского института бетона 25 (1954) 817–836.
Google Scholar
Зиембика, Х., «Влияние микропористой структуры на усадку ячеистого бетона», Cement and Concrete Research 7 (1977) 323–332.
Артикул Google Scholar
Невилл А. М. Свойства бетона (Джон Вили и сыновья, Нью-Йорк, 1981).
Google Scholar
Хансен, В. и Альмудаихим, Дж. А., «Предельная усадка бетона при высыхании — влияние основных параметров», ACI Materials Journal 84 (1987) 217–223.
Google Scholar
Шуберт П., «Характеристики усадки газобетона», в «Автоклавный газобетон, влажность и свойства», (Elsevier, 1983) 207–217.
Georgiades, A. and Ch. Фтикос, «Влияние микропористой структуры на усадку газобетона в автоклаве», Cement and Concrete Research 21 (1991) 655–662.
Артикул Google Scholar
Нильсен А., «Усадка и ползучесть — параметры деформации акритированного автоклавного бетона», в «Автоклавный акрированный бетон, влажность и свойства» (Elsevier, 1983) 189–204.
Тада, С., «Пористая структура и влажностные характеристики пористых неорганических строительных материалов», в «Достижения в автоклавном ячеистом бетоне» (А. А. Балкема, 1992) 53–64.
Houst, Y., Alou, F. и Wittmann, FH, «Влияние влажности на механические свойства автоклавного газобетона», в «Автоклавный газобетон, влажность и свойства» (Elsevier, 1983 ) 219–233.
Тада С. и С. Накано., «Микроструктурный подход к свойствам влажного ячеистого бетона», в «Автоклавный газобетон, влажность и свойства» (Elsevier, 1983) 71–89.
Александерсон Дж. «Взаимосвязь между структурой и механическими свойствами автоклавного газобетона», Cement and Concrete Research 9 (1979) 507–514.
Артикул Google Scholar
Комитет ACI 516, «Отверждение паром под высоким давлением — Современная практика и свойства автоклавированных продуктов», Журнал Американского института бетона 62 (1965) 868–907.
Google Scholar
Рекомендуемая практика RILEM. Автоклавный газобетон — Свойства, испытания и дизайн (E and FN SPON, 1993).
Хоббс, Д. У. и Мирс, А. Р., «Влияние геометрии образца на изменение веса и усадку образцов воздушно-высушенного раствора», Magazine of Concrete Research 23 (1971) 89–98.
Google Scholar
ASTM C 596, «Стандартный метод испытания усадки при высыхании раствора, содержащего портландцемент». (Американское общество испытаний и материалов, Филадельфия, 1989 г.).
Google Scholar
IS 6441 — Часть II, «Методы испытаний автоклавного ячеистого бетона — Определение усадки при высыхании» (Бюро индийских стандартов, Нью-Дели, 1972).
Google Scholar
Фултон, Ф. С., «Скоординированный подход к испытаниям на усадку бетонов и строительных растворов», Magazine of Concrete Research 13 (1961) 133–140.
Google Scholar
ASTM C 618, «Стандартные спецификации для золы-уноса и сырого или кальцинированного природного пуццолана для использования в качестве минеральной добавки в портландцементном бетоне» (Американское общество испытаний и материалов, Филадельфия, 1989).
Google Scholar
Нараянан Н., «Влияние состава на микроструктуру и свойства газобетона», М.S. Thesis (ИИТ Мадрас, июнь 1999 г.).
Лохнер, Р. Х. и Матар, Дж. Э., Проектирование для качества, (Чепмен и Холл, 1990).
Кьельсен, К. О. и Атласси, Э. Х., «Пористая структура цементно-кремнеземных дымовых систем — наличие полых пор оболочки», Cement and Concrete Research 29 (1999) 133–142.
Артикул Google Scholar
(PDF) Характеристики усадки пенобетона
Ссылки
ASTM (1989).«Стандартные технические условия на золу-унос и сырой или кальцинированный природный пуццолан
для использования в качестве минеральной добавки в портландцементном бетоне», ASTM C 618, Филадельфия,
1989.
ASTM (1998). «Стандартный метод испытаний на изменение длины затвердевшего раствора гидроцемента
и бетона». ASTM C 157, Филадельфия, 1998.
Бюро стандартов Индии (1972). «Методика испытаний автоклавного ячеистого бетона —
Определение усадки при высыхании».IS 6441-часть II, Нью-Дели.
Бюро стандартов Индии (1987). «Технические условия на цемент Портланд обыкновенный марки 53,
». I S 12269, Нью-Дели.
Cebeci OZ (1981). «Пористая структура затвердевшего цементного теста с воздухововлекающими добавками». Цемент и
Исследование бетона
, 11, 257-265.
Concrete Society Technical Report 18 (2002), «Руководство по выбору добавок для бетона
», The Concrete Society, Беркшир, Великобритания.
Georgiades A и Ch.Фтикос (1991). «Влияние микропористой структуры на усадку автоклавного газобетона
». Исследование цемента и бетона, 21, 655-662.
Яннаку А. и Джонс М.Р. (2002). «Возможности пенобетона для улучшения тепловых характеристик
малоэтажных жилых домов», Proceedings Innovations and Development
в Concrete Materials and Construction
, Dhir RK., Hewelett PC и Csetenyi LJ, eds,
Thomas Telford, UK , 533-544
Hansen W и Almudaiheem JA (1987).«Предельная усадка бетона при высыхании —
Влияние основных параметров». Журнал материалов ACI, 84, 217-223.
Джонс М.Р. и Маккарти А. (2005). «Предварительные оценки возможностей пенобетона
как конструкционного материала».
Журнал исследований бетона, 57, 21-31.
Джонс MR, Маккарти MJ и McCarthy A (2003). «Продвигая использование летучей золы в бетоне
вперед: перспектива Соединенного Королевства». Материалы Международного симпозиума по утилизации ясеня
2003 г.
, Центр прикладных исследований энергетики, Университет Кентукки, 20-
22.
Намбияр Э.К.К. и Рамамурти К. (2006a). «Влияние типа наполнителя на свойства пенобетона
».
Цементно-бетонный композит, 28, 475-480.
Nambiar EKK и Ramamurthy K (2006b). «Характеристики свежего состояния пенобетона
». Журнал ASCE по материалам в гражданском строительстве (принято).
Nambiar EKK и Ramamurthy K (2006c). Сорбционные характеристики пенобетона,
Исследование цемента и бетона, (принято).
Рукопись статьи «Поведение пенобетона в свежем состоянии»
Журнал материалов в гражданском строительстве, ASCE, Vol. 21, № 11, 2009. 631–636
10.1061 / • ASCE • 0899-1561 • 2009 • 21: 11 • 631 •
Исследование эффективности кладки из различных блоков из пенобетона
[1] Ли Хайчжоу.Исследование механизма усадки, растрескивания и образования пустот в стене из автоклавного газобетона. Чжэцзянский университет, Чжэцзян (2011 г.).
[2] Пэн Цзюньчжи.Исследование формирования, характеристики и воздействия пор автоклавного газобетона. Университет Чунцина, Чунцин, (2011 г.).
[3] Сунь Линчжу.Ключевая технология борьбы с растрескиванием стен из газобетона. Новые строительные материалы. 2 (2006) 54-58.
[4]
Ван Хэ, Сюй Гобинь. Анализ и предотвращение выбоин и трещин в оштукатуренной стене из газобетонного блока. Архитектура Технолой. 4 (2006) 248-249.
[5] Ван Джайчунь и др.Экспериментальное исследование растрескивания стены из пенобетона под действием невысокой циклической горизонтальной силы. Журнал Сычуаньского университета (издание технических наук). 1 (2013) 47-51.
Микроструктура и поведение усадки автоклавного пенобетона (AAC) — Сравнение вьетнамских и японских AAC -, Журнал передовых технологий бетона
Мы исследовали микроструктуру и усадку автоклавного газобетона (AAC) от нескольких производителей во Вьетнаме по сравнению с японским AAC.Три типа вьетнамских ААС и один тип японских ААС использовались для порошковой дифракции рентгеновских лучей, сканирующей электронной микроскопии, порозиметрии с проникновением ртути и испытаний на усадку. Результаты экспериментов показывают, что основными продуктами гидратации ААС, в котором в качестве кремнеземного материала использовалась летучая зола, является полукристаллический гидрат силиката кальция, а другими продуктами — тоберморит; но кристаллы тоберморита в AAC от некоторых производителей во Вьетнаме имеют неупорядоченную структуру и отсутствие взаимосвязи между кристаллами тоберморита.Распределение пор по размеру всех вьетнамских ААС является однопиковым, тогда как японское ААС является бимодальным.
中文 翻译 :
蒸压 加 气 混凝土 (AAC) 的 微观 结构 和 收缩 行为 — 越南 和 日本 AAC 的 比较 —
调查 了 几家 制造 商 AAC 高压 釜 加 气 混凝土 (AAC) 的 结构 和 收缩 行为。 三种 类型 的 越南 AAC 一种 类型 AAC 用于 X 射线 衍射 , 扫描电子 显微镜 法 收缩 测试。 表明 , 以 粉煤灰 为 二氧化硅 原料 的 AAC 的 主要 水合 产物 为 半 结晶 硅酸钙 水合物 辉 石 制造 的 生产AAC 的 雪 晶体 结构 混乱 , 并且 晶体 之间 缺乏 互锁。 所有 AAC 的 孔径 分布 均为 单 峰 , AAC。 中等 相对 (RH) 下 , AAC AAC 的 收缩 张力 是 高 相对 (约 65 %) 下 AAC 材料 湿度 引起 日本 AAC 局部收缩 的 主要 收缩 机理 , 而 表面 自由 能 的 变化 在 低 相对 湿度 条件 下 占 主导 地位。
Влияние добавки дигидрата сульфата кальция на сушку автоклавного газобетона
Качество автоклавного газобетона (АКБ) сильно зависит от химического состава сырья, а также от процесса гидротермальной реакции во время автоклавирования.Рабочие параметры зависят от структуры материала: мелкодисперсная пористость матрицы микронного размера, создаваемая упаковкой тонких пластин тоберморита, и крупные поры аэрации, возникающие при вспенивании влажной смеси. В данном исследовании связующее варьировалось по содержанию дигидрата сульфата кальция (CaSO 4 ⋅2H 2 O). Было изготовлено пять серий образцов ААС с содержанием гипса 0; 0,55; 1,15; 2,3 и 3,5% сухой массы соответственно. Установки AAC производились по технологии UNIPOL. В исследовании представлены экспериментальные результаты стабилизации влажности ААК.Начальное содержание влаги определяли сразу после автоклавирования. Более медленный процесс высыхания наблюдался для образцов, содержащих более 2% гипса. В то время как другие рабочие параметры, прочность на сжатие и растяжение, а также водопоглощение и капиллярный подъем были значительно лучше по сравнению с эталонными образцами AAC.
1 Введение
В любом строительном процессе важно своевременно стабилизировать влажность встроенных материалов, чтобы максимально быстро получить заявленные свойства изделий.Многие кладочные материалы имеют повышенную влажность в результате влажных производственных процессов, и часто это состояние отрицательно сказывается на параметрах строительных перегородок. Это обычная практика для встраивания влажных материалов из-за неправильного хранения или из-за влажности после производственного процесса.
AAC широко используется для строительства каменных стен во многих странах, особенно в Европе. Продукция AAC имеет разную влажность при кладке, а также разнообразна динамика их стабилизации влажности.Блоки из ячеистого бетона после процесса автоклавирования имеют влажность около 50%, и они часто являются встроенными с содержанием влаги более 40%. Построенная стена может иметь содержание воды около 15%.
AAC представляет собой пористый материал и поглощает влагу из окружающей среды, когда относительная влажность превышает 70%. Время, необходимое для стабилизации влажности в перегородке из ячеистого бетона, составляет от 1,5 до 2 лет, а в крайне неблагоприятных условиях от 2 до 3 лет. Первые цифры в обоих случаях относятся к AAC, произведенному с использованием кремнистого песка, а вторые цифры — к агрегатам с летучей золой. Обследование стен AAC в зданиях через 30-40 лет подтвердило, что влажность перегородок из песчаных AAC составляет около 2,5%, а перегородок из летучей золы AAC — около 4,5%. При таком влагосодержании перегородки, построенные из блоков AAC, демонстрируют хорошие теплоизоляционные свойства [1]. Европейский стандарт EN 771-4 допускает рабочую влажность блоков AAC на уровне 4-8% [2].
Прочность на сжатие зависит от содержания влаги в материале и уменьшается с увеличением влажности.Существует тесная зависимость прочности на сжатие, водопоглощения и других физических свойств от пористости материала и распределения пор по размерам. Влага является ключевой характеристикой, определяющей прочность, усадку, карбонизацию и теплопроводность [3]. Особенно неблагоприятно влияние влажности на прочность на сжатие и коэффициент теплопроводности λ [4, 5, 6]. Авторы [7] описывают задачу определения коэффициента теплопроводности в различных условиях влажности на основе стандарта ISO 10456 [8] и экспериментальных исследований.Лабораторные испытания показали, что в диапазоне влажности до 5% стандартная зависимость (экспоненциальная функция) верна. Выше 5% ход изменений близок к линейному.
«Белые» ААС обычно производятся из смеси тонкоизмельченных кварцевых песков, портландцемента, извести, гипса (дигидрата сульфата кальция) и воды. Добавление алюминиевого порошка развивает его ячеистый или вспененный характер.
AAC производится по разным технологиям, и пропорции вяжущих в бетоне также различаются.Фаза C-S-H, связывающая частицы песка, играет важную роль в формировании структуры ячеистого бетона и его прочности на сжатие [9]. Типичный процесс производства AAC включает гидротермальную обработку бетонной смеси при высоких температурах (обычно 180-200 ° C) под давлением насыщенного пара. В процессе гидротермальной обработки образуются пластинчатые кристаллы тоберморита (5CaO⋅6SiO 2 ⋅5H 2 O) как основной компонент упрочненного АКУ [9,10, 11, 12, 13].
В технологиях AAC источником сульфатов, помимо цемента, обычно является сульфат кальция в форме гипса или ангидрита. Чаще всего используется дигидрат гипса (гидратированный сульфат кальция) как один из компонентов вяжущего для бетона. Сульфаты в газобетонной смеси регулируют схватывание смеси. Выделение водорода в литой газобетонной массе происходит медленнее, а микроструктура бетона лучше. Сульфаты влияют на форму кристаллов тоберморита — они более крупные и плоские [13].
Эта добавка использовалась в технологии AAC в течение многих лет для улучшения свойств этого материала. Уменьшение содержания сульфатов в смесях ААС приводит к увеличению усадки и снижению прочности на сжатие [14]. Сульфат кальция в AAC во время гидротермальной обработки ускоряет образование тоберморита и фазы C-S-H, что, в свою очередь, увеличивает прочность конечного продукта [12]. В результате структура бетона становится более плотной, а сорбция бетона снижается сразу после гидротермального процесса, так как содержание гипса в смеси увеличивается.Однако важно помнить, что встроенные кондиционеры часто имеют содержание воды до 40%, и по мере увеличения герметичности бетона процесс высыхания стен из газобетона замедляется. Целью данного исследования было оценить процесс сушки образцов AAC в зависимости от содержания сульфата кальция в связующем.
2 Описание метода производства и состава образцов AAC
образцов AAC были изготовлены на заводе по производству песка UNIPOL с использованием следующего сырья: цемент, известь, гипс, кварцевый песок, алюминиевый порошок.В этом способе одним из технологических процессов является комбинированный сухой помол цемента, извести и кварцевого песка в шаровой мельнице до удельной поверхности 400-600 м 2 / кг [9]. Кварцевый песок вводится в мельницу после просеивания крупногабаритных зерен. При измельчении компонентов температура составляет 80-90 ° C, что является результатом трения и экзотермической реакции воды из влажного песка с активным оксидом кальция CaO, содержащимся в негашеной извести.
Для исследовательских целей были разработаны и изготовлены пять составов бетона с разным содержанием гипса.Расчетная плотность в сухом состоянии для всех серий AAC составляла 520 кг / м 3 3 . Для производства использовались портландцемент ЦЕМ I, известь средней обожженной и кварцевый песок, содержащий более 90% кремнезема SiO 2 . В таблице 1 показан состав конкретной серии AAC.
Таблица 1Состав АКУ на 1 м 3 смеси
Серия | AAC0 | AAC1 | AAC2 | AAC3 | AAC4 |
---|---|---|---|---|---|
Гипс (дигидрат сульфата кальция) [% от сухой массы] | 0 | 0.55 | 1,15 | 2,30 | 3,50 |
Цемент + известь [кг] | 143,0 | 145,0 | 141,0 | 136,0 | 133,0 |
Кварцевый песок [кг] | 348,0 | 350,0 | 347,0 | 345,0 | 340,0 |
Добавленный гипс [кг] | 0 | 2.7 | 5,6 | 11,1 | 16,6 |
Гипс в цементе [кг] | 3,7 | 3,8 | 3,7 | 3,5 | 3,5 |
Общее содержание гипса [кг] | 3,7 | 6,5 | 9,3 | 14,6 | 20,1 |
Алюминиевый порошок [кг] | 0.![]() | 0,42 | 0,42 | 0,42 | 0,42 |
Соотношение вода / сухой компонент | 0,49 | 0,50 | 0,50 | 0,51 | 0,50 |
При производстве использовался классический метод гидротермальной обработки (без вакуума на первом этапе). Весь гидротермальный процесс длился 12 часов.Образцы для эксперимента отбирали сразу после автоклавирования.
3 Экспериментальные методы
Плотность образцов бетона в сухом состоянии определялась согласно [15], а прочность на сжатие — согласно [16]. Испытание на прочность на разрыв проводилось в соответствии со стандартной процедурой [17] на высушенных образцах куба диаметром 100 мм, приготовленных таким же образом, как и для испытаний на прочность на сжатие — вырезанных из блоков кладки в трех зонах: верхней, средней и нижней. Отдельные образцы нагружали перпендикулярно направлению роста массы путем приложения нагрузки через 2 штуки.Стальные стержни шириной 0 см, расположенные в середине стены куба. Тест на влажность проводился согласно [18].
Данные о скорости капиллярного водопоглощения были получены с использованием стандартной процедуры [19], в которой кубики 100 × 100 × 100 мм изначально сухого материала помещались в контакт с водой (5 ± 1 мм) в мелкой тарелке. Боковые грани заделаны эпоксидной смолой. Вода впитывалась через нижнюю поверхность 100 × 100 мм. Прирост веса образца измеряли через 10, 30 и 90 минут.Коэффициент водопоглощения каменных блоков из-за капиллярного действия определяется по формуле:
C
ш
s
знак равно
м
s
о
,
s
—
м
d
р
y
,
s
А
S
т
s
о
∙
10
6
[
грамм
/
(
м
2
×
s
0
,
5
)
]
(3. 1)
где: C ws — коэффициент водопоглощения каменных блоков за счет капиллярного действия, [г / (м 2 * s 0,5 )]; м сухой, с — сухой [г]; m so, s — масса после времени насыщения t [г]; A s — площадь контактной поверхности [м 2 ]; t so — время насыщения [с].
Процедуры, описанные в стандарте [17], применялись для определения максимального водопоглощения и капиллярного подъема.
Испытание на максимальное водопоглощение бетона было выполнено в соответствии со следующей процедурой:
- —
образцы сначала на 24 часа помещали в воду на 1/3 высоты образца;
- —
через 24 часа уровень грунтовых вод увеличился до 2/3 высоты образца еще на 24 часа;
- —
, затем образцы были полностью погружены в воду еще на 24 часа;
- —
через 72 часа было определено максимальное водопоглощение.
Состояние полного насыщения имитирует ситуацию, когда материал полностью погружен в воду, например, из-за наводнений или длительного воздействия дождевой воды.
Для испытания капиллярного подъема призмы 100 × 100 × 200 мм сушили до постоянной массы при 105 ± 5 ° C, а затем после охлаждения помещали в контакт с водой (30 мм). Уровень воды поддерживался постоянным на протяжении всего эксперимента. Измерения капиллярного подъема производились через 1, 7, 24, 48 и 72 часа.Высота подъема измерялась от ватерлинии в центре каждой из четырех боковых граней призмы образца. Капиллярный подъем отдельных образцов определяли как среднее арифметическое измерений на четырех боковых гранях образцов. Образцы были приготовлены из целых блоков кладки, по три образца от каждого блока, таким же образом, как и для испытаний на плотность и прочность.
Температура и относительная влажность (RH) в процессе сушки бетона были выбраны исходя из того, что в рабочих условиях отапливаемые помещения для постоянного проживания имеют температуру 20 ± 2 ° C, а средняя RH составляет 50-65%.Проверка скорости сушки от остатка влаги после процесса автоклавирования проводилась в лабораторных условиях при температуре 22 ± 1 ° C и относительной влажности в пределах 50-55%.
Из-за значительного содержания влаги в бетоне в результате полного насыщения его пор водой, испытание на сушку проводилось в лабораторных условиях при 25 ± 1 ° C и относительной влажности 30 ± 1% в лабораторной печи с принудительной циркуляцией воздуха. . Образцы сушили до достижения стабилизированной влажности около 6%.
4 Результаты экспериментов и обсуждение
Результаты проведенных исследований представлены в таблице 2. Взаимосвязь между содержанием гипса и прочностью на сжатие образцов AAC приведена на рисунке 1.
Рисунок 1
Зависимость между содержанием гипса и прочностью на сжатие
Таблица 2Результаты испытаний образцов AAC
Серия | AAC0 | AAC1 | AAC2 | AAC3 | AAC4 | |
---|---|---|---|---|---|---|
Плотность в сухом состоянии [кг / м 3 ] | 548 | 520 | 510 | 514 | 541 | |
Прочность на сжатие в сухом состоянии [Н / мм 2 ] | 3.![]() | 4,16 | 4,31 | 5,46 | 5,60 | |
Прочность на сжатие при стабилизированной влажности [Н / мм 2 ] | 2,70 | 3,19 | 3,13 | 3,83 | 4,34 | |
Предел прочности на разрыв [Н / мм 2 ] | 1,1 | 1,1 | 1,3 | 1.4 | 1,6 | |
Стабилизированная влажность [%] | 5,1 | 4,4 | 4,8 | 5,4 | 4,9 | |
Время стабилизации влажности [ч] | 21,0 | 25,0 | 30,0 | 44,0 | 58,0 | |
Максимальное водопоглощение [%] | 64.0 | 59,7 | 61,8 | 56,4 | 60,1 | |
после 10 ‘ | 185,4 | 148,1 | 151,4 | 91,6 | 116,1 | |
Водопоглощение [г / (м 2 с 0,5 )] | после 30 ‘ | 150,8 | 113.5 | 120,3 | 77,9 | 94,3 |
после 90 ‘ | 125,0 | 91,3 | 95,1 | 65,9 | 74,7 | |
через 1 час | 2,3 | 1,9 | 1,6 | 1,3 | 1,7 | |
через 7 часов | 4.![]() | 3,1 | 2,3 | 1,8 | 2,3 | |
Капиллярный подъем [см] | через 24 часа | 6,2 | 4,7 | 3,8 | 2,7 | 3,1 |
через 48 часов | 8,6 | 6,5 | 5,4 | 3,8 | 3,9 | |
через 72 часа | 7.4 | 10,0 | 7,3 | 4,4 | 4,4 | |
Изменение влажности в результате высыхания от влаги после производственного процесса [%] | через 0 ч | 29,6 | 28,2 | 29,8 | 26,9 | 29,6 |
через 24 часа | 19.1 | 20,4 | 21,8 | 22,3 | 24,8 | |
через 48 ч | 12,0 | 12,8 | 14,4 | 16,0 | 18,4 | |
через 72 ч | 9,2 | 9,9 | 11,5 | 13,1 | 15,6 | |
через 96 ч | 7.7 | 8,3 | 9,9 | 11,8 | 14,0 | |
через 120 ч | 6,1 | 6,5 | 8,1 | 9,9 | 12,2 | |
через 144 ч | 5,2 | 5,2 | 6,8 | 8,5 | 10,8 | |
через 168 ч | 4.![]() | 4,4 | 5,6 | 7,3 | 9,6 | |
через 184 ч | 3,8 | 3,8 | 4,8 | 6,6 | 8,7 | |
через 200 ч | 3,6 | 3,4 | 4,4 | 6,0 | 8,2 | |
через 224 ч | 3.3 | 2,8 | 3,5 | 4,9 | 6,9 | |
через 264 ч | 3,1 | 2,4 | 2,9 | 4,1 | 6,1 | |
через 0 ч | 64,0 | 59,7 | 61.8 | 56,4 | 60,1 | |
через 6 ч | 59,2 | 54,4 | 57,7 | 52,4 | 55,5 | |
через 12 ч | 51,7 | 45,8 | 50,9 | 45,9 | 48,5 | |
через 18 ч | 44.3 | 38,2 | 45,1 | 39,8 | 42,1 | |
Изменение влажности в результате высыхания | через 24 ч | 36,6 | 31,0 | 38,8 | 34,4 | 36,3 |
вне максимального содержания воды [%] | через 30 ч | 28,4 | 24,4 | 32.1 | 28,8 | 31,5 |
через 36 ч | 22,5 | 20,0 | 26,2 | 24,8 | 27,5 | |
через 42 ч | 17,7 | 16,9 | 22,0 | 21,8 | 24,5 | |
через 48 ч | 14.![]() | 14,3 | 19,1 | 19,6 | 22,3 | |
через 54 ч | 12,3 | 12,8 | 17,1 | 17,9 | 20,5 |
Прочность на сжатие, испытанная как на высушенных, так и на стабилизированных образцах влажности, а также предел прочности на растяжение увеличивается с увеличением содержания гипса.Это увеличение является значительным, когда содержание гипса превышает 2% от сухого веса.
Не наблюдалось значительного влияния добавления сульфата на максимальное водопоглощение образцов AAC через 72 часа, хотя все образцы, содержащие гипс, имеют более низкое поглощение по сравнению с эталонным бетоном.
Эффект от добавления гипса проявляется в случае абсорбции через 10, 30 и 90 минут и капиллярного подъема. На рисунке 2 показаны экспериментальные результаты скорости поглощения w * (выраженной как совокупная поглощенная масса на единицу площади притока по сравнению с t 0.5 ). В течение 90 минут была протестирована только первая стадия водопоглощения — ранняя стадия, на которой скорость поглощения w * линейна в t 0,5 . Очевидно, что даже небольшое количество добавленного гипса снижает сорбционную способность ААЦ. Кривая, построенная для контрольных образцов, более крутая, а общее увеличение массы почти в два раза выше, чем для образцов с содержанием сульфата более 2% от сухой массы.
Рисунок 2
Капиллярное водопоглощение образцов AAC (кумулятивное поглощение w * по сравнению с t 0.5 ) в зависимости от содержания гипса
Существует сильная зависимость между подъемом капилляров и дозировкой гипса (рис. 3). Как и в случае с механическими свойствами, эффект более значительный, когда гипс дозируется более 2% от сухой массы. Подъем капилляров после 72-часового теста снизился примерно на 40% по сравнению с контрольными образцами.
Рисунок 3
Капиллярный подъем образцов АКК в зависимости от содержания гипса
Однако было замечено, что скорость высыхания от остатков влаги после производственного процесса бетонов, содержащих гидратированный сульфат кальция, была медленнее по сравнению с контрольными образцами (Рисунок 4).Содержание влаги в образцах, содержащих 3,5% гипса, было примерно в два раза выше, чем в контрольном бетоне после 264 часов сушки при 22 ± 1 ° C.
Рисунок 4
Влияние дозировки гипса на процесс сушки AAC при 22 ° C от влажности, возникающей в процессе производства, до стабилизированного содержания влаги
Содержание влаги в образцах с 3,5% гипса было более чем на 60% выше, чем в контрольной серии (20.5 против 12,3%) после 54 часов сушки в печи от максимального водопоглощения, хотя начальная точка была ниже (60,1 против 64,0%).
Известно, что кристалличность тоберморита в значительной степени влияет на физические свойства ААЦ. Различия в микроструктуре испытанных образцов ААС, приводящие к различным характеристикам, обусловлены составом связующего. Очевидно, добавление дигидрата сульфата кальция привело к изменению микроструктуры материала.
5 Выводы
AAC, который был предметом данного исследования, был произведен в промышленных масштабах, что минимизировало возможные ошибки в процессе дозирования, смешивания компонентов или гидротермальной обработки.Весь процесс контролировался автоматически. Изменяя состав вяжущих для бетона, мы можем изменять свойства ячеистого бетона и, следовательно, свойства элементов кладки, предназначенных для строительства перегородок.
Образцы AAC, в которых содержание дигидрата сульфата кальция превышало 2% от сухой массы, имели, по сравнению с образцами без гипса:
- —
прочность на сжатие выше примерно на 40% в сухом состоянии и на 60% выше при стабилизированной влажности;
- —
прочность на разрыв выше примерно на 40%,
- —
- —
капиллярный подъем ниже примерно на 40%.
Однако было замечено, что, когда содержание гипса было выше 2% от сухой массы, сушка от остатка влаги после производственного процесса была медленнее, и через 264 часа содержание влаги все еще оставалось выше 4%. Сульфат кальция влияет на процесс кристаллизации тобермита и фазы C-S-H, что подтверждается результатами испытаний на прочность. В результате образцы AAC3 и AAC4 характеризуются другой структурой пористости по сравнению с эталонным бетоном.
Исследование частично поддерживалось проектами № S / WBiIS / 1/2016, а финансовую поддержку — Министерством науки и высшего образования Польши.
Ссылки
[1] Zapotoczna-Sytek G., AAC летучей золы в стратегии устойчивого развития, Цемент-Известь-Бетон, 2006, 3, 193-201 Искать в Google Scholar
[2] PN-EN 771 -4 Технические характеристики каменных блоков — Часть 4: Каменные блоки из автоклавного газобетона Поиск в Google Scholar
[3] Scheffler G.А., Плагге Р., Методы определения влагозапасных и транспортных свойств автоклавного газобетона. Цемент-известь-бетон, специальный выпуск, 2011 г., 70-77 Поиск в Google Scholar
[4] Унчик С., Стругарова А., Хлавинкова М., Сабова А., Балкович С., Влияние объемной плотности и влажности на свойства газобетона в автоклаве, Цемент-Известь-Бетон, 2013, 4, 189-196 Искать в Google Scholar
[5] Лоран Дж. П., Геррешали К., Влияние влажности и температуры на теплопроводность автоклавного газобетон, матер. Struct., 1995, 28, 464–72 Искать в Google Scholar
[6] Джерман М., Кепперт М., Выборный Дж., Черны Р., Гигрические, термические свойства и долговечность автоклавного газобетона, Констр. Строить. Матем., 2013, 41, 352–359 Искать в Google Scholar
[7] Шох Т., Крефт О., Влияние влаги на теплопроводность AAC, В: Материалы 5-й Международной конференции по креплению автоклавного пенобетона. устойчивое будущее (Быдгощ, Польша), Быдгощ, 2011, 361-369.Искать в Google Scholar
[8] PN EN ISO 10456: 2009 Строительные материалы и изделия — Гигротермические свойства — Табличные расчетные значения и процедуры для определения заявленных и расчетных тепловых значений Искать в Google Scholar
[9] Kurdowski W., Chemia Cementu i betonu, Wydawnictwo SPC и Wydawnictwo Naukowe PWN, 2010 Поиск в Google Scholar
[10] Кикума Дж., Цунашима М., Исикава Т., Мацуно С., Огава А., Мацуи К., In situ time- Решенная дифракция рентгеновских лучей процесса синтеза тоберморита в гидротермальных условиях, Матем.Sci. Eng., 2011, 18 (2), 022017, 10.1088 / 1757-899X / 18/2/022017 Искать в Google Scholar
[11] Кикума Дж., Цунасима М., Исикава Т., Мацуно С., Огава А. ., Мацуи К. и др., In situ Дифракция рентгеновских лучей с временным разрешением процесса образования тоберморита в условиях автоклава, J. Am. Ceram. Soc., 2010, 93 (9), 2667–2674. Поиск в Google Scholar
[12] Мацуи К., Огава А., Кикума Дж., Цунашима М., Исикава Т., Мацуно С., Влияние добавления соединения Al и гипс на образовании тоберморита в автоклавном ячеистом бетоне, изученном с помощью in situ рентгеновской дифракции, В: 5-я Международная конференция по автоклавному газобетону, обеспечивающая устойчивое будущее (Быдгощ, Польша), Быдгощ, 2011, 147-154 Поиск в Google Scholar
[13] Хеланова Е., Дрочитка Р. Черный В. Влияние гипсовой добавки на образование тоберморита в автоклавном ячеистом бетоне // Ключевые слова. Матем., 2016, 714, 116-121 Искать в Google Scholar
[14] Штумм А. , Автоклавный газобетон без цемента и сульфатов, Цемент-известь-бетон, специальный выпуск 2011, 26-28 Искать в Google Scholar
[ 15] PN-EN 772-13: 2001 Методы испытаний каменных блоков. Часть 13: Определение чистой и брутто сухой плотности каменной кладки (кроме природного камня). Искать в Google Scholar
[16] PN-EN 772-1: 2011 Методы испытаний формовых блоков.Часть 7: Определение прочности на сжатие. Искать в Google Scholar
[17] PN-B-06258: 1989 Автоклавный газобетон. Искать в Google Scholar
[18] PN-EN 772-10: 2000 Методы испытаний каменных блоков. Часть 10: Определение влажности силиката кальция и блоков из автоклавного ячеистого бетона. Искать в Google Scholar
[19] PN-EN 772-11: 2011 Методы испытаний каменных блоков. Часть 11: Определение водопоглощения заполнителя бетона, автоклавного газобетона, искусственного камня и блоков кладки из натурального камня за счет капиллярного действия и начальной скорости водопоглощения блоков кладки из глины.Искать в Google Scholar
Поступила: 2017-6-8
Принято: 2017-7-5
Опубликовано в сети: 4 ноября 2017 г.
© 2017 Д.Малашкевич и Я. Хойновски
Эта работа находится под лицензией Creative Commons Attribution-NonCommercial-NoDerivatives 4.0 License.
Сертификаты ASTM — Автоклавный газобетон Aercon AAC
ASTM C1693 — 09e1 Стандартные спецификации для автоклавного ячеистого бетона (AAC)
Аннотация
Область применения
1.1 Настоящая спецификация распространяется на автоклавный газобетон (AAC), цементирующий продукт на основе гидратов силиката кальция, в котором низкая плотность достигается за счет включения агента, образующего макроскопические пустоты, и в котором отверждение осуществляется с использованием пара высокого давления.
1.2 Сырьем, используемым при производстве газобетона в автоклаве, является портландцемент или смешанные цементы, кварцевый песок, вода, известь, гипс или ангидрит, а также агент, образующий макроскопические пустоты. Кварцевый песок, используемый в качестве сырья, может быть заменен кремнеземистым мелким заполнителем, отличным от песка, и обычно перед использованием измельчается до мелкого порошка. Летучая зола может использоваться в качестве замены песка. Заливное сырье тщательно перемешивают, образуя суспензию. Суспензия разливается в стальные формы. Из-за химических реакций, происходящих внутри суспензии, объем увеличивается. После схватывания и перед затвердеванием масса разрезается на станки различных размеров. Затем устройства отверждаются паром под давлением в автоклавах, где материал превращается в твердый силикат кальция.
1.3 Значения, указанные в единицах дюйм-фунт, считаются стандартными. Значения, указанные в скобках, представляют собой математические преобразования в единицы СИ, которые приведены только для информации и не считаются стандартными.
1.4 Данный стандарт не претендует на полноту описания всех мер безопасности, если таковые имеются, связанных с его использованием. Пользователь настоящего стандарта несет ответственность за установление соответствующих правил техники безопасности и охраны здоровья и определение применимости нормативных ограничений до его использования.См. Разделы 6, 7 и 8.
ASTM C1691 — 09 Стандартные технические условия для неармированных блоков из автоклавного пенобетона (AAC)
Аннотация
В данной спецификации рассматриваются допуски на размеры, максимальные пределы усадки при высыхании, а также требования к транспортировке и обращению с твердыми неармированными каменными блоками, изготовленными из автоклавного ячеистого бетона (AAC). Каменные блоки должны полностью состоять из материала AAC и классифицироваться в соответствии с их классом прочности.Агрегаты должны соответствовать требованиям к прочности на сжатие, насыпной плотности в сухом состоянии и усадке при высыхании, которые должны определяться в соответствии со ссылочными документами ASTM.
Область применения
1. 1 Настоящая спецификация распространяется на сплошные неармированные каменные блоки, изготовленные из автоклавного газобетона (AAC), цементного продукта. В данной спецификации рассматриваются допуски на размеры, максимальные пределы усадки при сушке, а также транспортировка и транспортировка.
1.2 Значения, указанные в единицах дюйм-фунт, считаются стандартными. Значения, указанные в скобках, представляют собой математические преобразования в единицы СИ, которые приведены только для информации и не считаются стандартными.
1.3 Данный стандарт не претендует на полноту описания всех мер безопасности, если таковые имеются, связанных с его использованием. Пользователь настоящего стандарта несет ответственность за установление соответствующих правил техники безопасности и охраны здоровья и определение применимости нормативных ограничений до его использования.
ASTM C1694-09 Стандартные технические условия для армированных элементов из автоклавного пенобетона (AAC)
Область применения
1.1 Настоящая спецификация распространяется на армированные твердые элементы, изготовленные из газобетона в автоклаве (AAC), цементирующего продукта, указанного в Спецификации. В спецификации рассматриваются допуски на размеры, максимальные пределы усадки при высыхании, требования к стальной арматуре, а также транспортировка и транспортировка.
1.2 Значения, указанные в единицах дюйм-фунт, считаются стандартными. Значения, указанные в скобках, представляют собой математические преобразования в единицы СИ, которые приведены только для информации и не считаются стандартными.
1.3 Данный стандарт не претендует на полноту описания всех мер безопасности, если таковые имеются, связанных с его использованием. Пользователь настоящего стандарта несет ответственность за установление соответствующих правил техники безопасности и охраны здоровья и определение применимости нормативных ограничений до его использования.
Стандартные технические условия на строительный раствор с тонким слоем для кладки из автоклавного ячеистого бетона (AAC)
Область применения
1. 1 Настоящая спецификация применяется к тонкослойному раствору для кладки из газобетона автоклавного твердения (AAC).
1.2 Испытательная лаборатория, выполняющая эти методы испытаний, должна быть оценена в соответствии с Практикой C 1093.
1.3 Значения, указанные в единицах дюйм-фунт, считаются стандартными. Значения, указанные в скобках, представляют собой математические преобразования в единицы СИ, которые приведены только для информации и не считаются стандартными.
1.4 Этот стандарт может касаться опасных материалов, операций и оборудования. Этот стандарт не претендует на полноту описания всех мер безопасности, если таковые имеются, связанных с его использованием. Пользователь настоящего стандарта несет ответственность за установление соответствующих правил техники безопасности и охраны здоровья и определение применимости нормативных ограничений до его использования.
Высокопроизводительный тонкослойный раствор сухой смеси для автоклавных блоков из пенобетона
[1] Юшэн Тао.Инновации в стеновых материалах и энергосбережение в зданиях. 2007 (9): 53-56 (на китайском языке).
[2] Свидетельство об аттестации строительной отрасли.
[2008]
№ 015 (на китайском языке).
[3] Чуньлинь Шэнь.Полимерцементный водостойкий раствор [M] Пекин: Химическая промышленность Press, 2007, 8 (на китайском языке).
[4] Сюэмао1 Гуань, Шуцюн Луо и др.. Журнал строительных материалов. 2007, 10 (3): 302-306 (на китайском языке).
[5] Сян Цзи. Структурирован по характеристикам трещиностойкости сухих строительных смесей.Университет Хохай, 2007 г. (на китайском языке).
[6] Шэнфэй Тан, Сяофан Ху. Журнал Университета Наньхуа (научное и инженерное издание) 2004 г., 18 (2): 67-69 (на китайском языке).
.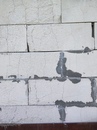