Показатели качества асфальтобетона — водонасыщение и коэффициент водостойкости
Дата публикации: 20.04.2020
Водонасыщение — это стандартный термин, одна из особенностей любого материала (в основном строительного). Когда имеют в виду водонасыщение, говорят о способности материалов насыщаться влагой, все свои трещины и полости в структуре заполнять водой. Если мы говорим про водонасыщение асфальтобетона, то подразумеваем определенные его характеристики — уплотнение и пористость, основные показатели качества асфальтобетона.
Водонасыщение асфальтобетона — это объективный показатель, который определяют в условиях лаборатории, в соответствии с ГОСТ. Для проверки гост на асфальтобетон предполагает насыщение выбранных образцов асфальта водой в назначенном режиме.
Почему показатели качества асфальтобетона требуют определять водонасыщение асфальтобетона?
Представьте себе укладку асфальта в летнее время. Уложенный в это время года асфальт с повышенным водонасыщением не проявит себя отрицательно и качество дороги сможет оценить только специалист. В этом случае асфальтобетон, который скоро начнет крошиться, отличается незакрытыми порами. Такой асфальтобетон не обладает достаточной морозостойкостью и зимой, в осенний период и весной начнутся проблемы с покрытием — оно начнет разрушаться, трескаться, щебень начнет выходить из поверхности и повышать стираемость дороги.
Все это образует дополнительные полости и поры в которые постоянно попадает вода, особенно от атмосферных осадков. После чего в дело вступает обычная физика — попавшая в эти полости вода замерзает при низкой температуре, в процессе начинает увеличиваться в объеме, расширяясь. Ситуация похожа на знакомый со школьных времен опыт, когда бутылку заполняли водой и выставляли на мороз. Она трескалась не зависимо от толщины стекла, не выдерживая давления расширяющейся замерзшей воды.
С асфальтобетоном происходит то же самое — структура его нарушается под давлением заледеневшей водной массы.
Почему высокое водонасыщение возникает?
В первую очередь коэффициент водостойкости падает при нарушениях во время изготовления самого покрытия дорог. Например, несоблюдение температурных требований при производстве смеси асфальтобетона и во время уплотнения этой смеси.
Гост на асфальтобетон предполагает так же укладку асфальтобетона только в сухую погоду, так как дождливая погода в процессе настила покрытия значительно снижает показатели качества асфальтобетона, даже если он был произведен при соблюдении всех требований, которые описывает гост на асфальтобетон.
То же самое происходит и при укладке асфальтобетона во время морозов, да и в целом при минусовых температурах.
Показатели качества асфальтобетона так же страдают, если было произведено недостаточное количество проходов асфальтовыми катками по уложенной поверхности — уплотнения асфальтобетонной смеси в этом случае становится недостаточно, коэффициент водостойкости значительно падает. Такая же картина получается, если в процессе производства смеси и ее укладки применялась не соответствующая требованиям дорожно-строительная техника.
Водонасыщение асфальтобетона также зависит от качества самой смеси — ее четко определяет ГОСТ на асфальтобетон. Он предполагает определенный рецепт приготовление и зерновой состав смеси, который показывает достаточный коэффициент водостойкости. При нарушении технологии и отступлении от требований госта значительно повышается водонасыщение готового покрытия и показатели качества асфальтобетона не могут ни при каких обстоятельствах соответствовать требованиям, которые выдвигает ГОСТ на асфальтобетон.
Для нормальной, беспроблемной эксплуатации дорожного покрытия, продления его срока службы не допускается повышать водонасыщение асфальтобетона. Отклонения в показателях не заметны на первый взгляд, но удорожают эксплуатацию дорог, так как их постоянный ремонт и переукладка превращаются в бесконечный процесс.
Мелкозернистая смесь асфальтобетона имеет коэффициент водостойкости около 0,8-0,9, это приблизительно 30-40% от своей массы. А крупнозернистый показывает высокое водонасыщение асфальтобетона, так как отличается большим количеством пор.
Как оценить показатель водонасыщения?
Водонасыщение асфальтобетона принято оценивать в процентах. Существует так же формула вычисления, на основании которой идет сравнение с показателями, которые выдвигает к покрытию ГОСТ на асфальтобетон:
W= (m3 — m0)/(m1 — m2) 100%
W — это собственно тот самый коэффициент водостойкости, по которому определяют показатели качества асфальтобетона. Этот показатель, который отвечает за определение водонасыщение чаще всего округляют до десятых. Для получения четкой картины, показывающей водонасыщение асфальтобетона конкретных образцов требуется взять среднее число от различных результатов с образцов и использовать для расчета по формуле.
m3 — гост на асфальтобетон требует насыщение контрольных образцов водой в условиях вакуума, после чего производится замер этого показателя в воздухе
m0 — по ГОСТ на асфальтобетон в качестве этого показателя берут среднюю массу предварительно отобранного образца
m1 и m2 — это замер веса контрольного образца после пребывания в воде в течении 30 минут и масса образца, который изначально взвесили в воде.
от чего зависит и на что влияет
Водонасыщение — это одно из свойств любого материала. Его показатель формируется на основе способности к заполнению пор и трещин жидкостью. Водонасыщение для асфальтобетона зависит от его пористости. Величина увеличивается в случае недостаточного уплотнения. Показатель будет нормальным, если в точности следовать технологии производства. С полученного асфальта берется несколько образцов. Они исследуются посредством специальной методики.
Водонасыщение асфальтобетона ГОСТ 9128-2009 определяется в лабораторных условиях. Для этого предварительно производится забор материала с различных участков поверхности. В выбранном режиме поверхность заливается водой. Лаборант замеряет количество, которое будет поглощено структурой. Дополнительно выполняется замораживание. Низкие температуры негативно влияют на слой асфальта. При наличии трещин заметно увеличивается их объем. Избежать ситуации можно при дополнительном уплотнении материала.
Особенности термина
Для нормальной эксплуатации асфальта недопустимо повышенное водонасыщение. При отклонении в показателе невозможно заметить негативные изменения плоскости в летнее время. Правильно поставить оценку смогут только специалисты после проведения исследования. Повышенное водонасыщение наблюдается, если на поверхности невооруженным глазом можно обнаружить большое количество пор. На фоне этого наблюдается также скорое выкрашивание щебня из поверхности.
Повышенный показатель в несколько раз снижает морозостойкость асфальта. Покрытие испортиться при наступлении холодов и морозов. Если вода ранее успела попасть в поверхность, то она начинает расширяться. Увеличение объема приводит к ухудшению технических характеристик и целостности. Законы физики приводят к тому, что лед начинает ломать асфальт изнутри. Поверхность рвется от давления, созданного жидкостью внутри. Покрытие начинает прогрессивно разрушаться, поэтому дальнейшее использование считается нецелесообразным.
Покрытие из асфальтобетона страдает из-за длительного увлажнения. Наблюдается выкрашивание минеральных зерен. Оно быстро изнашивается, поэтому появляются выбоины. Водостойкость напрямую зависит от плотности и образования устойчивых связей между отдельными компонентами. Благодаря этому удается добиться необходимого уровня адгезии. Если водонасыщение асфальтобетона ниже нормы, то со временем можно наблюдать диффузию жидкости. Она проникает под битумную пленку и уничтожает связи. Минеральные материалы имеют положительный потенциал. Свойство позволяет препятствовать устранению битумной пленки.
Жидкость имеет свойства проникать в трещины материала. Ситуация приводит к понижению прочности веществ. Трещины ослабляют свойства структуры. Они начинают заметно увеличиваться в размере. Асфальтобетон теряет свои первоначальные свойства прочности. Жидкости также свойственна диффузия — проникновение воды внутрь материала и застаивание. Это приводит к расклинивающему эффекту. Структура намокает, а затем высыхает. Попеременное действие приводит к увеличению пористости до 7%. При этом размер зерна заметно уменьшается, а в порах начинает скапливаться большее количество жидкости.
Крупнозернистый бетон имеет много открытых пор. Для мелкозернистого их количество составляет от 30 до 40% от общей массы. Водонасыщение вычисляется после анализа набухания и вычисления коэффициента водостойкости. Показатель должен быть больше 0,9. Только при длительном водонасыщении его можно снизить до 0,8.
Морозостойкость напрямую зависит от количества открытых пор. Во внимание также следует брать созданные связи между битумом и минеральными веществами. Они страдают весной и осенью. В этот период наблюдается поочередное замерзание и размерзание. На фоне этого формируются трещины, которые увеличивается при каждом цикле.
Морозостойкость принято выражать в качестве коэффициента. Он увеличивается в каждом цикле, поэтому страдает прочность сформированной поверхности. Показатель ниже у гранита, но выше у известняка. Асфальтобетон выдерживает больше циклов только при правильной технологии формирования. Иначе разрушение можно будет наблюдать в первом сезоне. Поверхность такого образца не получиться эксплуатировать в течение долгого периода времени.
Причины изменения свойств
Строителей дорог интересует вопрос изменения водонасыщенности асфальтобетона, от чего зависит данный показатель. Выделяют следующие факторы:
- В процессе создания покрытия была нарушена технология. Работники не соблюдали необходимые требования, которые выдвигались к температурным показателям.
К примеру, укладка производилась под дождем или при низких температурах. Показатель ухудшается, если по поверхности каток не прошел достаточное количество раз. Техника также должна соответствовать требованиям, которые к ней выдвигает ГОСТ.
- Применялась смесь для асфальта низкого качества. Не допускается использовать зернистый состав. Рецепт приготовления также должен соответствовать требованиям ГОСТа.
Формула для расчета
Водонасыщение асфальтобетона измеряется в процентах. Формула для расчета водонасыщение асфальтобетона:
W= (m3 — m0)/(m1 — m2) 100%, где
m0 — масса взятого предварительно образца, если взвешивание производить в воздухе.
m2 — масса, которая получилась после взвешивания в воде.
m1 — образец предварительно держат полчаса в воде, а затем производят замер его веса в воздухе.
m3 — образец насыщают в условиях вакуума, а затем выполняют замер в воздухе.
Результат целесообразно округлить до десятичного знака. Для формирования информативной картины потребуется взять среднеарифметическое значение от нескольких результатов.
Расхождение в полученных параметрах не может быть больше 0,5%.
Способы уменьшения
Мы уже разобрались, на что влияет водонасыщение асфальтобетона. Если в результате исследования было выявлено отклонение от нормы, то целесообразно искать пути уменьшения показателя. Используется метод уплотнения каждого слоя.
На практике добиться результата можно только в верхних слоях асфальта. Для этого газовой горелкой производится его уплотнение. Дополнительно по поверхности можно пустить тяжелый пневмокаток. В летний зной асфальт начинает плавиться из-за негативного воздействия высокой температуры. Ситуация идеально подходит для дополнительного уплотнения поверхности.
Теоретические данные сложно реализовать в масштабах большого строительства.
Асфальтобетон — материал, который характеризуется зерновой структурой. Предварительно она погружается в раствор. Компоненты образуют между собой связь и получается структурное образование. От водонасыщения зависит срок службы покрытия. При нарушении технологии повышается риск образования пустот внутри поверхности.
Свойства асфальтобетона
Асфальтобетонные покрытия по сравнению с другими видами покрытий обладают рядом положительных свойств, к которым в первую очередь можно отнести прочность, устойчивость к воздействию климатических факторов и воды, гигиеничность, так как они не пылят и легко очищаются от наносной пыли и грязи, имеют ровную поверхность, медленно изнашиваются.
Асфальтобетон поглощает звук от движущегося транспорта, что уменьшает шум в городах и населённых пунктах. Технология устройства асфальтобетонных покрытий допускает механизированное строительство. К недостаткам следует отнести старение органических вяжущих, а следовательно, и самих бетонов, изменение свойств от температуры (от пластического состояния до хрупкого), практически невысокую долговечность покрытия, зависимость выполнения работ от климатических условий.
К основным свойствам асфальтобетона относят: предел прочности при сжатии и растяжении, водостойкости, химическую стойкость, удобообрабатываемость.
Прочность при сжатии определяют на гидравлических прессах при температуре 50, 20 и 0°С. С повышением температуры прочность асфальтобетона понижается. С увеличение вязкости битума в пределах рекомендуемых марок дорожных битумов прочность асфальтобетона увеличивается.
Кроме испытания на сжатие, цилиндрические образцы испытывают на сжатие по образующей – «бразильский метод», создавая давление на боковую поверхность образца. Такое испытание отражает предельное сопротивление материала растягивающим напряжениям.
Прочность асфальтобетона при растяжении в 6-8 раз меньше, чем прочность при сжатии. Предел прочности асфальтобетона при сжатии и растяжении во многом зависит от сцепления и внутреннего трения минеральных зерен между собой. Внутреннее трение зависит от величины поверхностного соприкосновения зерен в единице объема, а сцепление – от силы прилипания вяжущего к поверхности минеральных частиц и толщины битумной пленки.
Применение щебня, искусственного песка (вместо гравия и природного песка) повышает величину трения, а следовательно, и прочность асфальтобетона. Независимо от состава и качества исходных материалов на прочность асфальтобетона оказывает существенное влияние степень уплотнения смеси непосредственно в покрытиях.
Водостойкость. При взаимодействие асфальтобетона с водной средой изменяются его структурно-механические свойства – прочность, пластичность и др.
Асфальтобетоны, приготовленные с использованием основных горных пород и шлаков, имеют большую водоустойчивость, чем приготовленные с использованием кислых пород. На качество асфальтобетона значительное влияние оказывает влажность свежеприготовленной смеси: чем она выше, тем качество асфальтобетона хуже. Применение сухих и чистых материалов повышает водостойкость асфальтобетона. Минеральные материалы, обработанные активатором (известь, поверхностно-активные добавки, малые дозы дегтя), также способствуют повышению водостойкости асфальтобетона.
Химическая стойкость – способность асфальтобетона сохранять постоянный групповой состав вяжущего материала. Химическая стойкость отражает способность асфальтобетона и, в частности, его вяжущей части сопротивляться процессам старения. Процессы старения, изменение группового состава битума возникает под влиянием окисления, свата, нагревания, испарения легких фракций и др. Старение вяжущего материала снижает эксплуатационные качества асфальтобетонного покрытия, делая его более хрупким, а поэтому новее стойким к ударным нагрузкам и пониженным температурам окружающего воздуха. Старение асфальтобетона и его вяжущего компонента проверяется методами тепловой обработки или длительного прогрева, испытанием образцов на погодоустойчивость в натурных и искусственных условиях.
При проектировании следует строго учитывать условия, в которых будет работать асфальтобетон, так, например, присутствие минеральных солей в воде (сульфат магния, натрия) даже в малых количествах, например до 1%, может сравнительно быстро разрушить структуру асфальтобетона.
Удобоукладываемость.
Влияние уплотнения асфальтобетонной смеси на качество дорожного покрытия
Уплотнение асфальтобетонной смеси дорожного покрытия имеет большое значение в долговечности законченного объекта. Если уплотнение было выполнено неправильно, то как следствие появятся различные дефекты на дорожном покрытии («волны», трещины), повышается риск образования колеи, происходит шелушение покрытия.
Процесс уплотнения представляет собой увеличение плотности материала за счет приложения внешних сил. В дорожном строительстве несущая способность асфальтобетона, способность противостоять нагрузкам напрямую связана со степенью уплотнения, например, увеличение степени уплотнения на 1 % соответствует повышению прочности примерно на 10-12 %.
Асфальтобетонная смесь, произведенная на АБЗ, транспортируется к месту производства работ. В идеальном случае должен быть непрерывный поток грузовиков с асфальтобетонной смесью к асфальтоукладчику. Асфальтоукладчик необходим для распределения и предварительного уплотнения асфальтобетонной смеси.
Предварительное уплотнение асфальтобетонной смеси осуществляется асфальтоукладчиком, а окончательное производится катками. На сегодняшний день имеются различные типы катков для уплотнения, а именно: легкие вибрационные катки, пневмоколесные катки, статические гладковальцовые и вибрационные катки. После уплотнения необходимо иметь одинаковую толщину слоя и однородную степень уплотнения. Для горячей асфальтобетонной смеси на уплотняемость в большой степени влияет ее температура, температура смеси в начале уплотнения должна быть в пределах 100-145°С для различных асфальтобетонных смесей. Процесс уплотнения должен начинаться сразу же после укладки, основная часть уплотнения должна произойти при температуре выше 100° С, с целью гарантировать необходимую степень уплотнения. Например, осенью неуплотненная смесь теряет температуру на 5-7ºС в минуту. Уплотнение асфальтобетонных смесей, содержащих щебня более 50 % необходимо начинать при температуре не менее 150ºС. Уплотнение смесей при температуре 70-80ºС невозможно, за исключением смесей с содержанием ПАВ и активированного минерального порошка. А уплотнение слишком горячей смеси обычным катком может привести к образованию трещин и наплывов.
Дефекты асфальтобетонного покрытия зачастую связаны именно с недостаточным уплотнением.
Асфальтобетон приобретает необходимые физико-механические свойства только после надлежащего уплотнения. В процессе уплотнения горячей асфальтобетонной смеси происходит взаимное сближение компонентов, перераспределение битума в смеси, сближенные частицы остаются связанными между собой битумом. После процесса уплотнения асфальтобетонной смеси, повышается объемная масса, слои дорожной одежды приобретают плотность, прочность, водоустойчивость, которые оказывают существенное влияние на эксплуатационные показатели асфальтобетонных покрытий.
Контроль качества уплотнения асфальтобетонных слоев дорожных одежд производится с помощью неразрушающих и разрушающих методов. В первом случае применяются ультразвуковые приборы, определяющие значения коэффициента уплотнения непосредственно на объекте строительства, во втором необходимо производить отбор образцов для последующих испытаний в лабораторных условиях.
Стандартный метод контроля за плотностью заключается в отборе образцов-кернов с помощью буровой установки (керноотборника). Плотность и водонасыщение определяют на образцах-кернах в лаборатории. Для определения плотности отбирают керны без трещин и сколов.
Следующий этап — высушивание образцов до того момента, пока их масса не станет постоянной. Для этого производится высушивание в течение не менее 60 мин при температуре до 50°С, далее производится охлаждение в течение не менее 30 минут и взвешивание. После получения постоянной массы определяется плотность образцов и водонасыщение. Масса определяется взвешиванием, объём определяется по методике гидростатического взвешивания.
В условиях лаборатории проводят переформовку образцов–кернов с целью провести испытания на переформованных образцах.
Эффективность уплотнения асфальтобетонных покрытий зависит от многих технологических факторов, в том числе, от типа катков, режима их работы, температуры асфальтобетонной смеси, толщины уплотняемого слоя и т.д.
Для определения коэффициента уплотнения необходимо знать среднюю плотность образца из конструктивного слоя и среднюю плотность переформованного образца. Определяют коэффициент уплотнения по формуле:
Купл = рm / р´m ,
где рm — средняя плотность образца из конструктивного слоя, г/ см³;
р´m — cредняя плотность переформованного образца, г/ см³.
Полученный результат сравнивается с нормативным и на основании этого делается заключение о степени уплотнения асфальтобетона. Так его значение для конструктивных слоев дорожных одежд должно быть не ниже:
— 0,99 для плотного асфальтобетона из горячих и теплых смесей типов А и Б;
— 0,98 для плотного асфальтобетона из горячих и теплых смесей типов В, Г, Д, пористого и высокопористого асфальтобетона.
Коэффициент уплотнения является одним из важных параметров, который в обязательном порядке контролируется в ходе проверок МГСН.
Так, за 6 месяцев 2017 года органом инспекции ГБУ «ЦЭИИС» было подготовлено 98 заключений по госработе «Оценка фактических значений коэффициента уплотнения и водонасыщения асфальтобетона, применяемого в конструктивных слоях дорожной одежды требованиям технических регламентов и проектной документации», из них в 23 заключениях выявлено несоответствие требованиям нормативных документов по показателям коэффициент уплотнения и водонасыщение.
Использованная литература:
— Уплотнение и укладка дорожных материалов. Теория и практика.
— ГОСТ 12801-98 Материалы на основе органических вяжущих для дорожного и аэродромного строительства.
Исп. ведущий инженер ЛИКСДОиГ Пагнуева Е.П.
От чего зависит срок службы дорог, рассказали специалисты асфальтобетонного завода «Трилитон» – Новости Владивостока на VL.ru
Традиционно с наступлением плюсовых температур во Владивостоке, как и во всей России, в усиленном темпе начинают ремонтировать дороги. Однако несмотря на постоянные работы, в асфальте появляются новые ямы и выбоины. Почему так происходит? Дать однозначный ответ на этот вопрос нельзя: качество дорожного полотна зависит от нескольких факторов. Какие это факторы и как организована работа у «Трилитона», рассказали специалисты асфальтобетонного завода.
Качество асфальтобетонной смеси
Первое, что влияет на срок службы дороги, – качество асфальтобетонной смеси (АБ), из которой она сделана. Пропорции и нормы изготовления АБ регулируются ГОСТами, но многие производители игнорируют нормативы и используют дешевые заменители. На качестве асфальта это отображается не лучшим образом, поэтому предпочтительней заказывать товар у действительно проверенных компаний.
Чтобы асфальтобетон был качественный, соответствовал ГОСТу, асфальтобетонному заводу (АБЗ) необходимо соблюсти ряд условий: соответствующее оборудование, наличие собственной лаборатории, входящий и исходящий контроль продукции, качественные инертные материалы, возможность комфортных условий по отгрузке продукции.
«Асфальтобетонную смесь, которую в народе называют просто асфальтом, изготовляют из инертных материалов – щебня, отсева, минерального порошка и битума, – объясняет начальник АБЗ «Трилитон» Сергей Кобзев. – Вся наша продукция, кроме битума, – производства предприятий, входящих в группу компаний «Востокцемент». Также в состав АБ входит адгезионная добавка, которая улучшает сцепление материала с дорогой.
Тот факт, что мы работаем на собственных материалах, уже гарантирует высокие показатели конечного продукта и позволяет нам на самом раннем этапе отслеживать качество материала – до того, как он попадет к нам на завод».
Неукоснительное соблюдение технологий
«Процесс изготовления асфальтобетона на АБЗ «Трилитон» отточен до малейших деталей и мало чем отличается от изготовления аналогичной смеси за рубежом или в любом другом городе России, – продолжает Сергей Кобзев. – Технологии придуманы не нами и проверены временем. Однако эти знания необходимо грамотно использовать в производстве.
Щебень и отсев засыпаются в бункера погрузчиком, после попадают в сушильный барабан, где доводятся до определенной температуры – 170-180 градусов Цельсия. После этого смесь попадает на грохот, там рассеивается и подается на весы. Дальше щебень и отсев перемещаются в миксеры, туда же по конвейеру поступает минеральный порошок и битум. Материалы перемешиваются в течение 45 секунд. После этого смесь готова к выгрузке в автомобиль. Весь процесс компьютеризирован, однако большим преимуществом нашего завода перед другими является наш слаженный и профессиональный коллектив. Большинство специалистов работают с самого основания завода, благодаря их опыту и знаниям мы можем гарантировать высокое качество конечного продукта».
Как говорит Сергей Кобзев, в производстве асфальта не может быть особых нововведений: зачем изобретать асфальт, если все давно придумали до нас? «Единственное, что могу отметить: несколько лет назад мы начали производство щебеночно-мастичного асфальта (ЩМА)».
Это верхний слой асфальтобетона, он более надежный, прочный, более шероховатый, с большим количеством щебня и минерального порошка. На него существуют отдельный ГОСТ. Использование ЩМА стало необходимым после того как мы приступили к работе над федеральным проектом по строительству скоростной трассы. В техусловиях проекта было прописано, что дорога обязательно должна быть построена с использованием ЩМА. Сейчас мы используем ЩМА, например, при строительстве дороги на Народном проспекте, а также на ул. Верхнепортовой (дорога от Казанского моста)».
Контроль каждой партии
На АБЗ «Трилитон» все инертные материалы проходят обязательный входящий контроль в собственной сертифицированной лаборатории, где определяется их соответствие ГОСТам. Завод выпускает продукцию по ГОСТ 9128-2013.
Лаборатория отвечает за каждый этап производственной цепи – контроль входящих материалов, контроль производства, корректную работу завода, исходящий контроль готовой продукции и многое другое. Лаборатория оснащена всем необходимым оборудованием и находится прямо на территории завода, что позволяет оперативно следить за процессом и параллельно выдавать полный пакет документов на готовую продукцию.
«К слову, асфальтобетонная смесь проходит лабораторные испытания на такие характеристики, как водонасыщение, прочность, зерновой состав. Берутся пробы каждой машины, с каждой марки смеси, испытания ведутся ежедневно, выдается паспорт качества на каждую партию асфальта. Кроме того, когда асфальт уже уложен, важно предоставить всю документацию контролирующим органам, принимающим дороги в эксплуатацию – от сертификатов качества на входящий в состав асфальта материал и конечного продукта до бухгалтерских документов. Так как завод работает официально, нам удается оперативно и в соответствии со всеми законодательными нормами оформить все необходимые бумаги», – рассказывает Сергей Кобзев.
Советов не спрашивают
Срок службы дорог зависит и от того, каким образом укладывают асфальтобетонную смесь. Важное условие правильной укладки – соблюдение требований ГОСТ и СНИП по подготовке поверхностей. ГОСТ по укладке асфальта регламентирует все возможные нюансы, связанные со строительством такого покрытия.
«Правила укладки асфальта по большей части зависят от вида и назначения покрытия, но некоторые нормативы менять нельзя, – объясняет Игорь Лицов, начальник отдела по продаже бетона и асфальта компании «ДВ-Цемент» (сбытовой структуры завода «Трилитон»). – Такие правила четко прописаны в ГОСТ и СНИП, и именно они обеспечивают долговечность и качество будущих дорог и тротуаров. Чтобы покрытие прослужило максимальный срок даже при интенсивной нагрузке, важно выбрать надежного производителя. АБЗ «Трилитон» гарантирует скорость выполнения и соблюдение всех требований качества. Сам процесс укладки контролирует и проводит подрядчик. В основном, крупные дорожные компании и без нас знают, какой асфальт и как укладывать, советуются лишь те, кто не каждый день работают с асфальтом. Например, клиенты, которые хотят заасфальтировать парковочную зону или придомовую территорию. Мы с удовольствием им в этом помогаем».
Асфальт как завершающий штрих
Подрядчики уверяют: гладкость и прочность дорожного покрытия зависит в первую очередь от того, насколько качественно были проведены предварительные работы.
«Подготовка основания под укладку асфальта и культура самого подрядчика, – не менее важны, чем качество материала, – уверяет руководитель одной из компаний по укладке дорог Константин Филатов. – Что бы вы хотели иметь: красивую кожу или здоровые органы? Наверное, главное – все-таки иметь хорошее здоровье, тогда и кожа будет красивой. Также и с дорогой. Важно, что находится под покрытием. Асфальт – лишь завершающий штрих».
«Многое зависит от щебеночного основания и качества укладки, качества уплотнения и водонасыщения, – вторит коллеге руководитель еще одной асфальтоукладочной компании Михаил Михайлович. – Работы по укладке должны выполняться согласно нормативным документам. Необходимо проводить комплексную укладку дороги, которая учитывает рельеф местности, подводные течения, строительство водоотводов. Заменяя верхний слой дорожного полотна, нужно меньше пользоваться молотками, с помощью которых снимают АБ и оставляют микротрещины в нижнем слое асфальта, а больше – способом фрезерования. Сейчас дорожники пользуются более продвинутой техникой, на укладчиках есть датчики температуры, уклонов, система нивелирования и т. д.».
Своевременная поставка
Так как укладка асфальта – процесс трудоемкий и непрерывный, а многие улицы или объекты днем перекрывать возможности нет, «Трилитон» установил особый режим работы на своем заводе. Понимая важность своевременной доставки материала, АБЗ при необходимости функционирует круглосуточно и без выходных.
«Кроме того, мы осуществляем автодоставку. Для этого у нас есть специальный отдел, который организует поставку любого необходимого объема асфальта в нужное для клиента время, – говорит Игорь Лицов. – Отмечу, что как только у дорожников появляется потребность в продукции, мы запускаем завод – даже если это сравнительно небольшой объем работ и плюсовые температуры только начали устанавливаться. Такая же ситуация происходит и по завершению сезона, когда основные дорожные работы уже выполнены, а кто-то из подрядчиков не успел уложиться в сроки. Начинаем работать, как только у клиента возникает потребность в продукции».
Оперативное оформление заказа также важное преимущество – достаточно одного звонка в отдел продаж – и менеджеры оперативно оформят заказ. Также есть возможность оформить заказать на асфальт через Личный кабинет на сайте. Это значительно экономит время клиентам завода «Трилитон».
Телефон отдела продаж: 8 (423) 232-52-52.
На правах рекламы
Испытания асфальтобетона по ГОСТ в Москве
ispytaniya-betona
ispytaniya-zhelezobetonnykh-izdelij
ispytaniya-armatury
ispytanie-ankerov
ispytaniya-asfaltobetona
ispytaniya-shchebnya-i-smesej-iz-nerudnykh-materialov
ispytaniya-kamnya-i-gornykh-porod
ispytaniya-bituma-i-bitumnykh-emulsij
ispytaniya-mineralnogo-poroshka
ispytaniya-tsementa
ispytanie-peska-i-grunta
opredelenie-uplotneniya-osnovaniya-pesok-grunt-shcheben-na-ob-ekte
opredelenie-prochnosti-zhbk-po-gost-18105
otbor-kernov-iz-zhbk-po-gost-28570
proverka-zashchitnogo-sloya-zhbk-i-pravilnosti-raspolozheniya-armaturnogo-karkasa
opredelenie-vlazhnosti-konstruktsii
oformlenie-defektnoj-vedomosti-i-otsenka-tekhnicheskogo-sostoyaniya-zhbk
ultrazvukovoe-obsledovanie-treshchin-zhbk
nablyudenie-za-treshchinami-zhbk-s-ustanovkoj-mayakov
opredelenie-adgezii-materiala-s-osnovaniem
ispytanie-kirpichnoj-kladki
ispytanie-styazhki
ultrazvukovaya-defektoskopiya
ultrazvukovaya-tolshchinometriya
radiograficheskij-kontrol
pronikayushchimi-veshchestvami
elektricheskij-kontrol
kapilyarnyj-kontrol
vizualno-izmeritelnyj-kontrol
issledovanie-makrostruktury-metallov-i-splavov
khimicheskij-sostav-metallov-i-splavov
staticheskie-ispytaniya-na-razryv-metallov-i-splavov
ispytaniya-na-izgib-v-kholodnom-sostoyanii
opredelenie-tverdosti-metallov-i-splavov
kompleksnoe-tekhnicheskoe-obsledovanie
obsledovanie-otdelnykh-stroitelnykh-konstruktsij
monitoring-tekhnicheskogo-sostoyaniya-zdaniya
poverochnyj-raschet-konstruktsij-i-elementov-zdaniya
obmernye-raboty-zdanij-i-sooruzhenij
ispytaniya-asfaltobetona-po-gost
ispytaniya-asfaltobetona-po-pnst
opredelenie-kachestva-dorozhnoj-odezhdy-i-fakticheskoj-tolshchiny-sloev
opredelenie-ob-emov-i-raschet-stoimosti-vypolnennykh-rabot
proverka-rovnosti-pokrytiya-i-sostavlenie-defektnoj-vedomosti
poverochnyj-raschet-dorozhnoj-odezhdy
opredelenie-koeffitsienta-stsepleniya-kolesa-avtomobilya-s-dorozhnym-pokrytiem-portativnym-priborom
otsenka-prodolnoj-rovnosti-dorozhnogo-pokrytiya-s-raschetom-mezhdunarodnogo-indeksa-rovnosti-iri
opredelenie-konstruktsii-dorozhnoj-odezhdy-s-ispolzovaniem-georadara
videoregistratsiya-defektov-na-dorozhnom-pokrytii-s-posleduyushchej-pechatyu-na-bumazhnyj-nositel
opredelenie-intensivnosti-i-sostava-transportnogo-potoka
opredelenie-prochnosti-dorozhnykh-odezhd-s-primeneniem-ustanovki-dinamicheskogo-nagruzheniya
opredelenie-ostatochnogo-modulya-uprugosti-dorozhnoj-odezhdy-staticheskie-shtampovye-ispytaniya
staticheskoe-ispytanie-gruntov-svayami
dinamicheskoe-ispytanie-gruntov-svayami
staticheskoe-ispytanie-gruntov-shtampom-po-gost-20276
staticheskoe-ispytanie-gruntov-shtampom-po-odm-218-5-007-2016
staticheskoe-ispytanie-gruntov-shtampom-v-osnovanii-svaj
dinamicheskoe-ispytanie-gruntov-koeffitsient-uplotneniya
sejsmoakusticheskaya-defektoskopiya
ultrazvukovaya-defektoskopiya-svaj
geofizicheskoe-obsledovanie-konstruktsij
ispytanie-pozharnykh-lestnits
ispytanie-ograzhdenij-krovli
ispytanie-liftovykh-kryukov-i-petel
sudebnaya-ekspertiza
dosudebnoe-issledovanie-ekspertiza
retsenzirovanie-tekhnicheskikh-zaklyuchenij
ekspertiza-smetnoj-dokumentatsii
razrabotka-smetnoj-dokumentatsii-fer-ter-tsn-gesn
inzhenerno-geodezicheskie-izyskaniya
geodezicheskoe-soprovozhdenie
ispolnitelnaya-s-emka-stroitelnykh-konstruktsij-i-inzhenernykh-sistem
opredelenie-ob-emov-vypolnennykh-rabot
obmernye-raboty
topograficheskaya-s-emka-mestnosti
raschet-kartogrammy-peremeshcheniya-zemlyanykh-mass
razmeshchenie-laboratornogo-posta-na-ob-ekte
periodicheskoe-poseshchenie-ob-ekta-po-soglasovannomu-grafiku
laboratornoe-soprovozhdenie
postoyannoe-prisutstvie-na-ob-ekte
vyborochnaya-priemka-vypolnennykh-rabot
stroitelno-tekhnicheskij-audit
proverka-pravilnosti-oformleniya-tekhnicheskoj-dokumentatsii
Определение коэффициента водостойкости асфальтобетона по ГОСТ 12801—84
Водонасыщение асфальтобетона — это способность его к насыщению, заполнению всей своей структуры: пор и трещин влагой. Из этого следует, что повышенное водонасыщение асфальтобетона характеризует его пористость и (или) недостаточное уплотнение.
Показатели вотонасыщения определяют по стандартной методике в соответствии с ГОСТ. В условиях стационарной лаборатории образцы (керны) асфальта в заданном режиме насыщаются водой. Сущность этих испытаний заключается в определении количества воды, которую поглотят испытываемые образцы асфальтобетона.
Почему повышенное водонасыщение недопустимо? И регламентировано требованиями ГОСТ 9128-2013 п. 4.1.10
Дело в том, что асфальт при не нормативном (повышенном) водонасыщении уложенный летом, ни как себя внешне в отрицательную сторону не проявляет. Только специалисты могут после визуального осмотра дать предварительную оценку технического состояния покрытия. К примеру на фотографии слева — нормативное состояние, а справа асфальтобетон с незакрытыми порами. В том числе видно, что щебень из покрытия в скором времени будет выкрашиваться.
Такой дефект снижает морозостойкость асфальтобетона и проблемы начнутся при наступлении морозов в осенний, зимний и весенний период. При отрицательной температуре вода, попавшая в поры асфальта, замерзает, расширяется, увеличивается в объеме. Это закон физики. Опыт со стеклянной бутылкой заполненной водой выставленной на мороз, которая в итоге лопается, тому подтверждение. Так же и структура асфальтобетона рвется от давления воды, замерзшей в его порах. В результате, проходя несколько циклов замерзания, асфальтобетонное покрытие разрушается с прогрессией. К весне дорожное покрытие приходит в негодность.
Причины повышенного водонасыщения асфальтобетона
1. Нарушение технологии устройства дорожного покрытия: несоблюдение температурного режима асфальтобетонной смеси при уплотнении, укладка ее в дождливую погоду или при минусовой температуре, малое количество проходов вальцами катка, дорожно-строительная техника не соответствует требованиям.
2. Некачественная сама асфальтобетонная смесь, зерновой состав которой (рецепт приготовления) не соответствует требованиям ГОСТ. (Примечание: если водонасыщение в переформованных образцах нормативное, то асфальтобетонная смесь соответствует ГОСТ)
Пример лабораторных испытаний асфальтобетона
Сейчас мы попробуем объяснить результаты лаборатории, выполнив анализ показателей указанных в протоколе. См. Протокол.
Из протокола испытаний видно, что в 1, 3 и 6 кернах из покрытия повышенное водонасыщение, а в переформованных образцах все в норме, значит асфальтобетонная смесь соответствует ГОСТ, а выполненные работы по уплотнению асфальта на участках дороги, где отбирались 1, 3 и 6 керны не соответствуют нормативным требованиям. Обратите внимание, что и коэффициент уплотнения в тех же образцах не соответствует норме. Для полного понимания вышеизложенного следует знать, что такое переформованные образцы, но это уже другая тема.
Определение коэффициента уплотнения асфальта
Коэффициент уплотнения асфальтобетонного покрытия один из важных показателей качества выполняемых работ по асфальтированию. Для мелкозернистой смеси его величина не должна быть меньше, установленной ГОСТом, 0,99. По сути, коэффициент определяется отношением плотности переформованного образца асфальта к плотности его самого. Для испытания на уплотнение, отбирается проба материала с готового участка, по истечению трех суток с момента укладки. Обустройство дорог, площадей, парковок и дворовых территорий asfaltirovanie.ru
Способ определения
Выпиливаются шесть образцов с одного места с помощью обыкновенной бензопилы с диском, по бетону. Образцы тщательно очищаются металлической щеткой от пыли и грязи. Определяются их геометрические параметры и вес, с целью определения плотности каждого образца. Погрешность между шестью показателями должна быть минимальна.
Следующим шагом приступают к формованию новых образцов из отобранных с асфальтобетонного покрытия, но только уже в лабораторных условиях и согласно нормативным требованиям. Образцы разогреваются в печи при температуре от 140 до 160 градусов по Цельсию. Одновременно, подготавливают формы, которые представляют собой полые металлические цилиндры. Их также, перед формованием необходимо разогреть и смазать внутреннюю часть специальным раствором, дабы избежать прилипания смеси к стенкам цилиндра и для большего удобства при изъятии образцов из них после формования.
Разогретую до рабочей температуры смесь, послойно засыпают в цилиндр, с послойным трамбованием и устанавливают под гидравлический пресс. На прессе устанавливают нормативную нагрузку, в соответствии от типа смеси, и нагружают форму в течение трех минут. По окончанию нагрузки, получившийся образец извлекают из цилиндра и определяют его плотность. Если коэффициент уплотнения получается меньше нормативного, участок готового асфальтобетонного покрытия бракуется и переделывается заново. Оптимальным вариантом, показывающим должное качество асфальта, считается, если коэффициент равен единице.
Итог
В настоящее время введены некоторые поправки при расчете уплотнения асфальтобетонной смеси и дополнительно учитывается водонасыщение и пористость образцов. Данные показатели определяются на других лабораторных приборах и учитываются при расчете коэффициента уплотнения. Как правило, результаты с внесением данных поправок не сильно сказываются на результате, но учитывать их необходимо обязательно.
thewalls.ru
Можно ли уменьшить водонасыщение асфальтобетона
Если результаты протокола имеют водонасыщение асфальта, превышающее норму, то совершенно очевиден вопрос: можно ли его уменьшить? Что нужно, что бы его уменьшить? Ответ один: для этого нужно слой асфальта дополнительно уплотнить.
Теоретически это возможно выполнить, но лишь с небольшими участками и только верхнего слоя покрытия путем нагрева его газовой горелкой и уплотнения разогретой структуры асфальта тяжелым пневмо-катком. В конце концов в сверх жаркий летний день покрытие асфальта чуть ли не плавится и тут можно этим воспользоваться, укатав его дополнительно.
К сожалению – это все теория, на практике же в масштабах строительства крупных дорожных объектов это практически невыполнимые и труднореализуемые способы.
12 февраля, 2021 / Экспертиза асфальта
Структурно-механические свойства асфальтобетона
Асфальтобетон, как материал с обратимыми микроструктурными связями, в зависимости от температуры и условий деформирования может находиться в следующих структурных состояниях:
— упруго-хрупком, при котором минеральный остов строго фиксирован застеклованными прослойками битума. В этом случае асфальтобетон по свойствам приближается к цементобетону и другим искусственным материалам с кристаллизационными связями;
— упруго-пластичном, когда зерна минерального остова соединены прослойками битума, которые проявляют при напряжениях, не превышающих предел текучести, упругие и эластичные свойства, а при больших напряжениях — упруго-вязкие свойства;
— вязко-пластичном, при котором зерна минерального остова соединены полужидкими прослойками битума и небольшое по величине напряжение приводит к деформированию материала.
Под механической нагрузкой асфальтобетон проявляет комплекс сложных свойств: упругость, пластичность, ползучесть, релаксацию напряжений, изменение прочности в зависимости от скорости деформирования, накопление деформации при многократных приложениях нагрузки и т. д. В зависимости от проявления тех или иных свойств к асфальтобетону применимы законы теории упругости или теории пластичности. Основными свойствами, характеризующими качество асфальтобетона, являются прочность, деформативность, ползучесть, релаксация, водостойкость, износостойкость, морозоустойчивость.
Прочность — свойство асфальтобетона сопротивляться разрушению под действием механических напряжений. Теоретические основы прочности и устойчивости асфальтобетонных покрытий отражены в виде нормативов на физико-химические свойства в ГОСТ 9128-97. Показателем этих свойств в сумме прямо или косвенно характеризуют прочность при сжатии и сдвиге, трещиностойкость асфальтобетона в покрытиях.
Прочность при сжатии нормируют при 50, 20, 0°С, что соответствует температуре покрытия в жаркий летний день и осенне-зимний период.
Деформативность асфальтобетона оценивают по относительной деформации асфальтобетонных образцов при испытании на изгиб или растяжение. Покрытие будет устойчивым против образования трещин, если асфальтобетон обладает относительным удлинением при 0°С не менее 0,004…0,008, а при -20°С не менее 0,001…0,002 (при скорости деформации, близкой к 5…10 мм/мин).
Ползучесть. Испытание асфальтобетона на ползучесть позволяет установить изменение деформации во времени. Ползучесть — процесс малой непрерывной пластичной деформации, протекающей в материалах в условиях длительной статической нагрузки. При испытании на ползучесть к образцу, имеющему форму цилиндра или балочки, прикладывают постоянную нагрузку, чтобы проследить работу материала в упругой (линейной) и неупругой (нелинейной) области.
Релаксация — уменьшение напряжений в материале, величина деформации в котором поддерживается постоянной. Процесс релаксации заключается в «перерождении» упругой деформации в пластичную.
Релаксация напряжений в асфальтобетоне связана с наличием битума, обладающего гораздо меньшей прочностью и вязкостью, чем минеральные материалы. Температура и вязкость битума оказывают влияние на характер релаксации напряжений в асфальтобетоне. С понижением температуры различия в релаксационных процессах уменьшаются, с повышением — релаксационная способность материала увеличивается. На характер релаксации в значительной степени влияет напряжение, сообщаемое материалу. При высоком начальном напряжении процесс релаксации протекает интенсивно, в материале остается мало неотрелаксированных напряжений, что объясняется облегчением пластичного течения по релаксационным плоскостям.
Релаксационные процессы в асфальтобетоне зависят от скорости деформации (нагружения). Процесс нагружения рассматривают как совокупность двух одновременно протекающих процессов — роста напряжений и их релаксации, поэтому, чем медленнее растет нагрузка, тем большая часть напряжений успевает отрелаксировать в процессе нагружения.
При высоких температурах интенсивность снижения напряжений служит показателем деформационной устойчивости асфальтобетона, а при низких отрицательных — показателем трещиноустойчивости.
Водостойкость.
Асфальтобетонные покрытия при длительном увлажнении вследствие ослабления структурных связей могут разрушаться за счет выкрашивания минеральных зерен, что приводит к повышенному износу покрытий и образованию выбоин. Водостойкость асфальтобетона зависит от его плотности и устойчивости адгезионных связей. Вода, как полярная жидкость, хорошо смачивает все минеральные материалы, а это значит, что при длительном контакте минеральных зерен, обработанных битумом, возможна диффузия воды под битумную пленку. При этом минеральные материалы с положительным потенциалом заряда поверхности (кальцит, доломит, известняк) в большей степени препятствуют вытеснению битумной пленки водой, чем материалы с отрицательным потенциалом поверхности(кварц, гранит, андезит).
Пористость оказывает большое влияние на водостойкость асфальтобетона, обычно она составляет 3…7 %. Поры в асфальтобетоне могут быть открытые и замкнутые. С уменьшением размера зерен увеличивается количество замкнутых, недоступных воде пор. Водостойкость определяется величиной водонасыщения, набухания и коэффициента водостойкости Кв (отношение прочности водонасыщенных к прочности сухих образцов). Коэффициент водостойкости должен быть не менее 0,9, а при длительном водонасыщении (15 суток) не менее 0,8.
Морозостойкость. Замерзая зимой в порах асфальтобетона, вода переходит в лед с увеличением в объеме на 8-9 %, что создает в них давление свыше 29 МПа. Наибольшее разрушительное действие оказывает происходящее весной и осенью попеременное замораживание и оттаивание асфальтобетона. Знакопеременные температуры приводят к появлению трещин.
Морозостойкость асфальтобетона обычно оценивают коэффициентом KF
, показывающим снижение прочности при растяжении (и сжатия на раскол) после определенного цикла замораживания насыщенных водой образцов на воздухе при температуре -20°С и оттаивания в воде при комнатной температуре. Количество циклов принимают не менее 25. Повысить водо- и морозостойкость можно путем выбора материалов надлежащего качества, тщательного подбора составляющих, применения поверхностно-активных веществ.
Износостойкость и шероховатость асфальтобетона в покрытии. Износ асфальтобетона происходит под действием сил трения, вызываемых проскальзыванием колес автомобиля по поверхности покрытия и вакуумных сил, возникающих под движущимся автомобилем. Износ покрытия определяется: истиранием его структурных элементов; отрывом и износом с его поверхности зерен песка и раздробленных щебенок.
Износостойкость асфальтобетона тем выше, чем больше его плотность, чем выше твердость входящих в его состав минеральных материалов и выше сцепление зерен щебня и песка с битумом. Асфальтобетоны, приготовленные на гранитном щебне, более износоустойчивы, чем асфальтобетоны на известняковом щебне. Применение щебня, загрязненного глинистыми частицами, приводит к резкому снижению износостойкости за счет вырывания щебенок из поверхности покрытия.
Асфальтобетонные покрытия с ровной, сухой и чистой поверхностью (за исключением покрытий с избытком битума) обеспечивают достаточное сцепление шин автомобиля с поверхностью покрытия. При этом шероховатость поверхности покрытия не оказывает существенного влияния на сопротивление скольжению шин. На покрытиях с увлажненной поверхностью степень сопротивления скольжению шин значительно снижается из-за наличия воды в зоне контакта шин с покрытием. Степень сопротивления скольжения оценивается коэффициентом сопротивления скольжению j
(коэффициент сопротивления), представляющим собой отношение силы сопротивления скольжению к нормальной нагрузке на покрытие в зоне контакта шины с покрытием. Коэффициент сцепления на сухом и мокром асфальтобетонном покрытии имеет следующие значения:
Шероховатая поверхность: Гладкая поверхность:
сухая 0,7…0,9 сухая 0,4…0,6;
мокрая 0,5…0,7 мокрая 0,3…0,4.
При коэффициенте сцепления менее 0,4 покрытие становится недопустимо скользким и аварийность на нем резко увеличивается. Коэффициент сцепления 0,4…0,5 в большинстве случаев удовлетворяет требованиям безопасности движения. Повышение коэффициента сцепления достигается за счет применения асфальтобетона поровой и контактно-поровой структуры. Шероховатость обеспечивается при содержании щебня из труднополирующихся пород в количестве 50-65 % в зернистых смесях и 35-55 % зерен крупнее 1,25 мм — песчаных на дробленом песке из труднополирующихся пород, а также уменьшением до возможных пределов содержания минерального порошка (4-10 % в зернистых смесях и 8-10 % в песчаных). Общие зависимости между шероховатостью, качеством составляющих и составом асфальтобетонных смесей следующие: степень шероховатости покрытия пропорциональна острогранности и собственной шероховатости зерен каменного материала; долговечность шероховатости тем больше, чем труднее шлифуется каменный материал, чем выше вязкость битума; чем больше дробленых зерен в смеси и чем меньше в ней минерального порошка, тем выше шероховатость.
Чувствительность к влаге — Pavement Interactive
Восприимчивость к влаге является основной причиной повреждения дорожных покрытий из HMA. HMA не должен существенно разлагаться из-за проникновения влаги в смесь. Смеси HMA можно считать чувствительными к влаге, если внутренняя связь асфальтового вяжущего с заполнителем ослабевает в присутствии воды. Это ослабление, если оно достаточно сильное, может привести к обрыву (рис. 1).
Чтобы измерить вероятность повреждения смесей HMA влагой, можно провести испытания на чувствительность к влаге.Результаты теста на чувствительность к влаге могут быть использованы для прогнозирования возможности долгосрочного снятия изоляции и оценки добавок, препятствующих отслаиванию, которые добавляются к асфальтовому вяжущему, заполнителю или смеси HMA для предотвращения отслаивания.
Рис. 1: Усталостное растрескивание при зачистке.Фон
Повреждение из-за влаги является результатом взаимодействия влаги с адгезией битумного вяжущего и заполнителя в смеси HMA. Это взаимодействие может вызвать снижение адгезии между асфальтовым вяжущим и заполнителем (рис. 2 и рис. 3), называемое зачисткой, что может привести к различным формам повреждения дорожного покрытия HMA, включая колейность и усталостное растрескивание.
На протяжении многих лет использовалось множество различных тестов для оценки восприимчивости конкретной смеси HMA к повреждению влагой. Эти испытания варьируются от простых (например, испытание на кипение) до более сложных (например, испытание на отслеживание колес в Гамбурге). Тест на чувствительность к влаге, определяемый конструкцией смеси Superpave, обычно называется модифицированным тестом Лоттмана. Этот тест описан в разделе «Описание теста». В этом разделе, взятом в основном из работы Хикса (1991 [1] ), описывается фактический механизм повреждения от влаги, факторы, влияющие на повреждение от влаги, профилактические меры и альтернативные испытания.
Рис. 2: Образцы HMA без повреждений от влаги (слева) и повреждений от влаги (справа). Обратите внимание на количество заполнителя без покрытия на поврежденном образце. | Рис. 3. Образцы HMA без повреждений от влаги (слева) и повреждений от влаги (справа). Более тонкий пример, чем на Рисунке 2, но все же с заметным заполнителем без покрытия. |
Адгезия асфальтового вяжущего и заполнителя
Повреждение от влаги — это уменьшение адгезии между асфальтовым вяжущим и поверхностью заполнителя в смеси HMA. Чтобы понять его причины и превентивные меры, здесь представлено краткое обсуждение механизмов адгезии. Существует 4 основных способа сцепления битумного вяжущего с заполнителем:
- Механический. Асфальтовое вяжущее проникает в неровности поверхности и поры заполнителя и затвердевает, вызывая механический затор. Влага на заполнителе может препятствовать проникновению битумного вяжущего в заполнитель и уменьшать механическое сцепление, тем самым повышая склонность к отслаиванию.
- Химическая. Происходит химическая реакция между асфальтовым вяжущим и поверхностью заполнителя, вызывающая химическую адгезию. Как правило, заполнители с кислой поверхностью не так сильно реагируют с асфальтовыми связующими. Эта более слабая реакция может быть недостаточно сильной, чтобы противостоять другим факторам повреждения от влаги.
- Адгезионное натяжение. Натяжение между асфальтовым вяжущим и заполнителем на линии смачивания (когда капля растекается по поверхности, край капли является «линией смачивания») обычно меньше, чем натяжение между водой и заполнителем.
Следовательно, если все три соприкасаются, вода будет стремиться вытеснить асфальтовое связующее. Это может привести к плохому смачиванию поверхности заполнителя асфальтовым вяжущим и привести к отслаиванию. Это межфазное натяжение между асфальтовым вяжущим и заполнителем зависит от типа асфальтового вяжущего, типа заполнителя и шероховатости поверхности заполнителя.
- Молекулярная ориентация. При контакте с заполнителем молекулы асфальта имеют тенденцию ориентироваться по отношению к ионам на поверхности заполнителя, по существу создавая слабое притяжение между асфальтовым вяжущим и поверхностью заполнителя.Если молекулы воды, которые являются диполярными, более полярны, чем молекулы асфальтового связующего, они могут предпочтительно удовлетворять потребности в энергии поверхности заполнителя. Возникающая в результате слабая связь битумного вяжущего с заполнителем может привести к отслоению.
Факторы, влияющие на повреждение от влаги
Восприимчивость к влаге — сложное явление, зависящее от ранее обсужденных механизмов. Природа этих механизмов и их взаимодействие затрудняет однозначное предсказание того, будет ли конкретная характеристика определяющим фактором при определении чувствительности к влаге.В общем, восприимчивость к влаге увеличивается за счет любого фактора, который увеличивает содержание влаги в HMA, снижает адгезию асфальтового вяжущего к поверхности заполнителя или физически размывает асфальтовое вяжущее. Каждый из перечисленных ниже факторов в определенной степени влияет на чувствительность к влаге, но ни один из них не является надежным эталоном для прогнозирования чувствительности к влаге.
- Характеристики битумного вяжущего. Вязкость важна, потому что она может указывать на более высокие концентрации асфальтенов (больших полярных молекул).Полярные молекулы могут создавать большее адгезионное напряжение и адгезию молекулярной ориентации. Следовательно, более низкие вязкости, которые могут представлять более низкие концентрации асфальтенов, обычно более чувствительны к отгонке.
Отдельные компоненты асфальтового вяжущего, такие как сульфоксиды, карбоновые кислоты, фенолы и азотистые основания, также могут влиять на способность отпарки.
- Сводная характеристика (рисунок 4). Как правило, гидрофильные агрегаты (притягивающие воду) с большей вероятностью отделяются, чем агрегаты, которые являются гидрофобными (отталкивают воду).Чтобы решить эту проблему, можно либо избежать отслаивания заполнителей, либо использовать модификатор асфальтового связующего, препятствующий отслаиванию. Ключевые агрегатные свойства, определяющие эту гидрофильную / гидрофобную характеристику, следующие:
- Химия поверхности. Поверхности, которые могут более легко связываться с асфальтовым вяжущим, с меньшей вероятностью вызывают отслаивание. Как правило, более кислотная поверхность заполнителя более подвержена отслаиванию. Железо, магний, кальций и, возможно, алюминий считаются полезными, а натрий и калий — вредными (Hicks, 1991, [1] ).
- Пористость и размер пор. Размер пор является решающим фактором. Если поры достаточно велики, чтобы позволить асфальтовому вяжущему проникнуть, они могут быть одной из причин повышенной чувствительности к влаге. Высокая пористость приводит к высокой абсорбции, а это означает, что необходимо использовать больше асфальтового вяжущего для достижения желаемого эффективного содержания асфальтового вяжущего. И наоборот, если не принимать во внимание высокую пористость, для данного количества асфальтового вяжущего будет абсорбировано больше и меньше будет доступно для создания пленки асфальтового вяжущего вокруг частиц заполнителя, что приведет к более быстрому старению и, возможно, отслоению.
- Воздушные пустоты. Степень, в которой поры заполнителя поглощают асфальтовое вяжущее, влияет на объем воздушных пустот в смеси HMA. Когда воздушные пустоты HMA превышают примерно 8 процентов по объему, они могут стать взаимосвязанными и позволить воде легко проникнуть в HMA и вызвать повреждение влаги из-за порового давления или расширения льда.
Чтобы решить эту проблему, конструкция смеси HMA регулирует содержание асфальтового вяжущего и градацию заполнителя для создания проектных воздушных пустот около 4 процентов. Избыточные воздушные пустоты могут быть либо проблемой конструкции смеси, либо проблемой конструкции, и в этом разделе рассматривается только проблема конструкции смеси.
- Химия поверхности. Поверхности, которые могут более легко связываться с асфальтовым вяжущим, с меньшей вероятностью вызывают отслаивание. Как правило, более кислотная поверхность заполнителя более подвержена отслаиванию. Железо, магний, кальций и, возможно, алюминий считаются полезными, а натрий и калий — вредными (Hicks, 1991, [1] ).
- Строительная погода. Конструкция для прохладной погоды может привести к недостаточному уплотнению, что приведет к образованию больших воздушных пустот и относительно проницаемого покрытия HMA. Это увеличивает вероятность попадания воды в структуру дорожного покрытия и, как следствие, повреждения от влаги. Влажная погода также может увеличить содержание влаги в построенном HMA.
- Климат. Влажный климат, циклы замораживания-оттаивания и колебания температуры могут пропускать больше влаги в структуру HMA, тем самым увеличивая вероятность повреждения из-за влаги.
- Климат. Влажный климат, циклы замораживания-оттаивания и колебания температуры могут пропускать больше влаги в структуру HMA, тем самым увеличивая вероятность повреждения из-за влаги.
- Трафик. Если вода присутствует в конструкции HMA, повышенная транспортная нагрузка может ускорить повреждение от влаги по 2 причинам:
- Повышение порового давления. Если вода находится в порах заполнителя и не может выйти, транспортная нагрузка будет иметь тенденцию сжимать эти поры и вызывать повышение давления, которое может оттолкнуть асфальтовое вяжущее от поверхности заполнителя.
- Гидравлическая очистка. Колесо проезжает по тротуару HMA, как правило, вода перемещается по нему.Это движение вызывает чистящее действие, которое может удалить асфальтовое вяжущее с поверхности заполнителя.
- Трафик. Если вода присутствует в конструкции HMA, повышенная транспортная нагрузка может ускорить повреждение от влаги по 2 причинам:
- Сводная характеристика (рисунок 4). Как правило, гидрофильные агрегаты (притягивающие воду) с большей вероятностью отделяются, чем агрегаты, которые являются гидрофобными (отталкивают воду).Чтобы решить эту проблему, можно либо избежать отслаивания заполнителей, либо использовать модификатор асфальтового связующего, препятствующий отслаиванию. Ключевые агрегатные свойства, определяющие эту гидрофильную / гидрофобную характеристику, следующие:
Профилактические мероприятия
Могут быть предприняты различные меры для предотвращения или, по крайней мере, минимизации повреждений от влаги. Эти меры варьируются от выбора материала до практики строительства, проектирования дорожного покрытия и добавок HMA:
- Совокупный выбор.
Выбирайте заполнитель с низкой пористостью и шероховатой чистой поверхностью.
- Предотвращает попадание влаги на дорожное покрытие HMA. Уменьшите проницаемость конструкции дорожного покрытия, регулируя содержание воздушных пустот, толщину подъема и градацию (Рисунок 5 и Рисунок 6). Кроме того, обработка поверхности, такая как противотуманные уплотнения, шламовые уплотнения или битумная обработка поверхности (BST), может существенно повысить водонепроницаемость поверхности HMA.
- Заполнитель для предварительной обработки. Измените свойства поверхности заполнителя, чтобы заменить ионы, которые могут способствовать плохой адгезии битумного вяжущего и заполнителя.
- Присадки, препятствующие образованию полос. Добавьте химикаты или известь в битумное вяжущее или HMA, чтобы предотвратить повреждение от влаги (Рисунок 7).
- Химическая промышленность. Обычно работают для уменьшения поверхностного натяжения в асфальтовом вяжущем, что способствует лучшему смачиванию, а также для придания асфальтовому вяжущему электрического заряда, противоположного заряду поверхности заполнителя.
Большинство химических добавок содержат амины и добавляются в количестве примерно от 0,1 до 1,0 процента по массе асфальтового связующего. Химические добавки обычно добавляют к асфальтовому вяжущему перед смешиванием с заполнителем, но это может привести к некоторым потерям, поскольку не вся добавка гарантированно достигает критической границы раздела асфальтовое вяжущее-заполнитель.Некоторые добавки могут быть добавлены к заполнителю перед смешиванием с асфальтовым вяжущим, чтобы вся добавка находилась на поверхности заполнителя.
- Известь (рисунок 8). Работает, заменяя отрицательные ионы на поверхности заполнителя положительными ионами кальция, что приводит к лучшей адгезии битумного вяжущего и заполнителя. Также реагирует с молекулами как вяжущего асфальта (карбоновая кислота), так и с агрегатом (кислотные ОН-группы), что приводит к образованию молекул, которые легче абсорбируются на поверхности агрегата, или молекул, которые с меньшей вероятностью диссоциируют и связываются с молекулами воды.
Известь обычно добавляют в количестве от 1,0 до 1,5 процентов от общей массы заполнителя. Для активирования извести необходима влага, поэтому известь обычно добавляют в виде суспензии или добавляют к слегка влажному заполнителю.
- Химическая промышленность. Обычно работают для уменьшения поверхностного натяжения в асфальтовом вяжущем, что способствует лучшему смачиванию, а также для придания асфальтовому вяжущему электрического заряда, противоположного заряду поверхности заполнителя.
Рис. 7: Заполнитель слева имеет сильное отслоение, справа — 0,5% по массе модификатора противоскользящего действия асфальтового связующего. | Рис. 8: Известь в небольших контейнерах для добавления во время подготовки образца смеси. |
Тесты на влагочувствительность
Как правило, тесты на чувствительность к влаге не измеряют отдельные факторы, а скорее пытаются количественно оценить способность смеси HMA противостоять воздействию влаги, независимо от источника.Как правило, они способны предоставить общие или сравнительные результаты и не могут предсказать степень повреждения от влаги. Краткое описание основных тестов на чувствительность к влаге приводится ниже:
- Испытание на кипение (ASTM D 3625).
Добавьте рыхлый HMA в кипящую воду и измерьте процент от общей видимой площади поверхности заполнителя, которая сохраняет свое асфальтовое связующее покрытие. Тест прост, но субъективен, не требует определения прочности, а исследование мелкого заполнителя затруднено.
- Испытание на кипение (ASTM D 3625).
- Испытание статическим погружением (AASHTO T 182). Образец HMA погружают в воду на 16–18 часов, а затем наблюдают в воде, чтобы измерить процент от общей видимой площади поверхности заполнителя, которая сохраняет свое асфальтовое связующее покрытие. Этот тест также прост, но субъективен и не требует определения силы.
- Тест Лоттмана. Испытания 3 комплекта уплотненных образцов. Группа 1, контрольная, не кондиционирована.Группа 2, представляющая полевые характеристики через 4 года, подвергается вакуумному насыщению водой. Группа 3, представляющая полевые характеристики в возрасте от 4 до 12 лет, подвергается вакуумному насыщению и циклу замораживания-оттаивания.
Для каждого образца проводят испытание на раздельное растяжение, и отношение косвенной прочности на разрыв кондиционированных образцов сравнивают с контрольной группой в виде отношения. Минимальный коэффициент прочности на разрыв (TSR) от 0,70 до 0,80 часто используется в качестве стандарта.
- Тест Лоттмана. Испытания 3 комплекта уплотненных образцов. Группа 1, контрольная, не кондиционирована.Группа 2, представляющая полевые характеристики через 4 года, подвергается вакуумному насыщению водой. Группа 3, представляющая полевые характеристики в возрасте от 4 до 12 лет, подвергается вакуумному насыщению и циклу замораживания-оттаивания.
- Tunnicliff and Root кондиционирование. Подобно тесту Лоттмана, этот тест использует только 2 группы и исключает группу замораживания-оттаивания.
- Модифицированный Лоттман (AASHTO T 283). Комбинация тестов Lottman и Tunnicliff и Root. Он сравнивает разделенную прочность на разрыв некондиционных образцов с образцами, частично насыщенными водой. Испытуемые подвергают кондиционированную группу частичному вакуумному насыщению и дополнительному циклу замораживания-оттаивания. Хотя ожидается, что образцы, кондиционированные водой, будут иметь более низкую прочность на разрыв, слишком низкие значения указывают на возможность повреждения из-за влаги.
- Модифицированный Лоттман (AASHTO T 283). Комбинация тестов Lottman и Tunnicliff и Root. Он сравнивает разделенную прочность на разрыв некондиционных образцов с образцами, частично насыщенными водой. Испытуемые подвергают кондиционированную группу частичному вакуумному насыщению и дополнительному циклу замораживания-оттаивания. Хотя ожидается, что образцы, кондиционированные водой, будут иметь более низкую прочность на разрыв, слишком низкие значения указывают на возможность повреждения из-за влаги.
- Погружение-сжатие (AASHTO T 165). Аналогичен модифицированному испытанию Лоттмана, но кондиционированные образцы помещают только в воду (не в вакуум), и вместо испытания на раздельное растяжение используется испытание на прочность при неограниченном сжатии. Точность невысока, и образцы с явными признаками отслаивания могут дать коэффициент прочности около 1,0.
- Устройство слежения за колесами Hamburg. Уплотненные образцы ТМА испытаны под водой.Результаты дают относительный показатель чувствительности к влаге.
Все эти тесты имеют недостатки, которые приводят к постоянным поискам лучшего теста на чувствительность к влаге. Эти недостатки, в дополнение к тем, которые обсуждались выше, как правило, связаны с повторяемостью и воспроизводимостью результатов испытаний и сомнительной предсказательной способностью. Кроме того, небольшие изменения ключевых параметров HMA, таких как воздушные пустоты (Va), могут существенно повлиять на результаты испытаний.
Описание теста
Следующее описание представляет собой краткое описание теста. Это неполная процедура, и ее не следует использовать для выполнения теста. Полную процедуру тестирования можно найти по адресу:
- AASHTO T 283: Устойчивость уплотненной битумной смеси к повреждениям, вызванным влагой
- ASTM D 4867: Влияние влаги на асфальтобетонные смеси для мощения
Сводка
Два набора образцов HMA подвергаются испытанию на раздельное растяжение (часто называемому испытанием на непрямое растяжение).Один набор кондиционируется путем частичного вакуумного насыщения водой, замачивания в воде в течение 24 часов и дополнительного цикла замораживания-оттаивания. Другой набор используется в качестве контроля. Отношение средней прочности на разрыв кондиционированных образцов к средней прочности на разрыв некондиционных (контрольных) образцов выражается как коэффициент прочности на разрыв (TSR). На рисунке 9 показана установка для испытания на раздельное растяжение.
Приблизительное время испытания
Общее время тестирования может составлять до 6 дней.Основные компоненты:
- До 4 дней пробоподготовки
- 16 часов для цикла замораживания
- 24 часа для цикла оттаивания
- 2 часа на доведение образцов до температуры испытаний
- 30 минут для испытания комплектов кондиционированных и некондиционированных образцов с помощью непрямого испытания на растяжение
Основная процедура
- Приготовьте 6 образцов HMA.Образцы обычно имеют диаметр 6 дюймов (150 мм) и толщину 4 дюйма (100 мм). После перемешивания дайте HMA остыть до комнатной температуры в течение 2 часов.
Допускаются образцы других размеров. Если в HMA присутствует заполнитель размером более 1 дюйма (25 мм), следует использовать образец большего размера.
- Выдержите HMA в духовке при 140 ° F (60 ° C) в течение 16 часов.
- После отверждения поместите HMA в печь при температуре 275 ° F (135 ° C) на два часа перед уплотнением.
- Компактно замешайте до 7% воздушных пустот или до уровня пустот, ожидаемого в полевых условиях, с помощью месильного компактора SGC, California или молотка Маршалла.
- Храните уплотненные образцы при комнатной температуре от 72 до 96 часов.
- Определите теоретический максимальный удельный вес (Gmm), насыпной удельный вес (Gmb), высоту, объем и содержание воздушных пустот (Va) каждого образца.
- Разделите шесть выборок на два подмножества по три. Среднее содержание воздушных пустот (Va) для каждой подгруппы должно быть одинаковым.Одно подмножество будет «безусловным» (испытанным в сухом состоянии), а другое — «кондиционированным» (испытанным в насыщенном состоянии).
- Образцы без кондиционирования. Пока кондиционированные образцы кондиционируются, некондиционные образцы находятся при комнатной температуре.
- Оберните образцы в пластик или поместите их в прочный герметичный пакет.
- Храните образцы при комнатной температуре до проведения испытания.
- Кондиционированные образцы. Эти образцы насыщаются водой до 55-80 процентов с использованием следующей процедуры:
- Поместите каждый образец в вакуумный контейнер, поддерживаемый над дном контейнера с помощью прокладки, и наполните контейнер водой до тех пор, пока образец не покроется на 1 дюйм (25 мм) воды.
- Создайте вакуум с парциальным давлением 10–26 дюймов рт. Ст. (Абсолютное давление 13–67 кПа) в течение 5–10 минут (рис. 10).
- Снимите вакуум и оставьте образец под водой еще на 5–10 минут.
- Снимите вакуум и оставьте образец под водой еще на 5–10 минут.
- Рассчитайте объемный удельный вес (Gmb) и сравните массу SSD с массой SSD, полученной на шаге 6, чтобы определить объем поглощенной воды.
- Определите степень насыщения путем сравнения объема поглощенной воды с объемом воздушных пустот (Va), полученным на этапе 6.
Если рассчитанное насыщение образца ниже 55 процентов, повторите процедуру насыщения. Если рассчитанное насыщение образца превышает 80 процентов, образец считается поврежденным и должен быть утилизирован.
Если требуется кондиционирование замораживанием-оттаиванием, заверните каждый образец в пластик и поместите его в пластиковый пакет, содержащий 0.6 дюймов3 (10 мл) воды. Закройте пакет и поместите его в морозильную камеру при температуре 0 ° F (-18 ° C) как минимум на 16 часов.
- Образцы кондиционируют влажностью, помещая их в ванну с дистиллированной водой при 140 ° F (60 ° C) на 24 часа (Рисунок 11).
Если образцы кондиционировали замораживанием-оттаиванием, удалите пластик с образцов как можно скорее после помещения в ванну.
- Образцы кондиционируют влажностью, помещая их в ванну с дистиллированной водой при 140 ° F (60 ° C) на 24 часа (Рисунок 11).
- Поместите образцы в водяную баню с температурой 77 ° F (25 ° C) минимум на 2 часа (Рисунок 12).
- Проведите испытание на непрямое растяжение каждого образца, поместив образец между двумя несущими пластинами (Рисунок 13) в испытательной машине и приложив нагрузку с постоянной скоростью 2 дюйма в минуту (50 мм / минуту) (видео 1) .
Убедитесь, что нагрузка приложена по диаметру образца.
Рисунок 13: Образец помещен между опорными пластинами перед испытанием.Видео 1: Испытание на непрямое натяжение.
- Запишите значения прочности на разрыв, вычислите и запишите значения прочности на разрыв.
- Запишите значения прочности на разрыв, вычислите и запишите значения прочности на разрыв.
Результаты
Измеренные параметры
Конечным параметром, который необходимо измерить, является коэффициент прочности на разрыв (TSR). Однако, чтобы получить это измерение, необходимо измерить следующие другие параметры:
- Теоретический максимальный удельный вес (Гмм) каждого образца
- Насыпной удельный вес (Гмб) каждого образца
- Содержание пустот воздуха (Va) каждого образца
- Процент насыщения кондиционированных образцов
Технические характеристики
Таблица 1: Расчетная чувствительность смеси Superpave к влаге
Материал | Значение | Спецификация | Беспокойство HMA |
---|---|---|---|
HMA | Коэффициент прочности на разрыв | ≥ 0.![]() | Повреждение от влаги, снятие изоляции |
Типичные значения
Типичные значения TSR находятся в диапазоне от 0,70 до 0,90. В зависимости от типа смеси HMA нередко можно увидеть значения ниже 0,70 или выше 0,90.
Расчеты (интерактивное уравнение)
Рассчитайте предел прочности на разрыв следующим образом:
Где:
- St = предел прочности (psi)
- P = максимальная нагрузка (фунты)
- t = толщина образца (дюймы)
- D = диаметр образца (дюймы)
Выразите устойчивость к повреждению от влаги как отношение прочности на разрыв безусловного образца, которая сохраняется после кондиционирования.
Рассчитайте TSR следующим образом:
Где:
- TSR = коэффициент прочности на разрыв
- S1 = средняя прочность на разрыв некондиционных образцов
- S2 = средняя прочность на разрыв кондиционированных образцов
(PDF) Моделирование потенциала отслаивания асфальтобетона
ВЫВОДЫ
На основании программы испытаний можно сделать следующие выводы:
1- Моделирование потенциала отслаивания асфальтобетона может быть основано на свойствах прочности
, а не на визуальный рейтинг.
2- Потенциал снятия изоляции, на который указывает индекс остаточной прочности, сильно зависит от жесткости асфальтобетона.
.
3- Разработанная модель может быть использована для прогнозирования потенциала отслаивания асфальтобетона
с помощью простых тестов, обычно применяемых для контроля качества.
СПИСОК ЛИТЕРАТУРЫ
Zhou, L .; Chen, F .; Jiang, Y .; и Ци Се. (2009). «Влияние водонасыщенного состояния
на влажность асфальтовой смеси», Труды избранных статей
с Международной конференции в Гео Хунань, 2009 г., No.354, выпуск
№16.
Solaimanian, M .; Харви, Дж .; Тахморесси, М.; и Тандон, В. (2003) «Испытание
методовдля прогнозирования чувствительности асфальтовых покрытий к влаге»
Чувствительность асфальтовых покрытий к влаге, национальный семинар, 4–6 февраля,
Сан-Диего, Калифорния, TRB, тема 2. С. 77–113.
Abdul Wahhab, H .; Али, С .; Al-Swailmi, S .; и Аль-Нур А. (2002) «Зачистка
дорог Саудовской Аравии — прогнозирование и предотвращение». Материалы 6-й Саудовской
инженерной конференции, KFUPM, Дахран, Vol. 3, стр. (323-336).
Хантер Э. и Ксайбати. (2002) «Оценка влагочувствительности асфальтовых смесей
», Университет Вайоминга, Ларами, технический отчет. Вайоминг.
Канитпонг, к. и Bahia, H (2006) «Оценка повреждений от влаги HMA в
Висконсин, как это связано с характеристиками дорожного покрытия», документ № 06-1605,
Совет по исследованиям транспорта, 85-е ежегодное собрание, 22-26 января,
Вашингтон , Д.C.
Американская ассоциация государственных служащих автомобильных дорог и транспорта (AASHTO)
(2003): «Стандартные спецификации для транспортных материалов и методов отбора проб и испытаний
», 17-е издание Вашингтон, округ Колумбия
Американское общество по испытаниям и материалам ( ASTM), (2003 г.), «Дорожные и тротуарные материалы
; системы дорожных покрытий для транспортных средств», Ежегодная книга стандартов ASTM,
Раздел 4, том 04. 03.
1007 Тротуары для аэродромов и шоссе 2013: устойчивые и эффективные тротуары © ASCE 2013
Влияние полиэфирного волокна на воздушные пустоты и стойкость к низкотемпературным трещинам проницаемой асфальтовой смеси
С быстрым развитием асфальтовых покрытий дренажная способность асфальтовых покрытий становится все более требовательной.Поэтому обязательно изучить проницаемую асфальтобетонную смесь. Воздушные пустоты и связанные с ними воздушные пустоты являются основными факторами, влияющими на дренажную функцию и низкотемпературные характеристики асфальтового покрытия. Чтобы решить проблему дренажа и низкотемпературного растрескивания, предлагается включить определенное количество полиэфирного волокна в проницаемую асфальтовую смесь. В данной работе исследуются воздушные пустоты и низкотемпературные характеристики асфальтовой смеси с различным содержанием полиэфирного волокна.Сделан вывод, что с увеличением содержания полиэфирного волокна как воздушные пустоты, так и связанные воздушные пустоты сначала уменьшаются, а затем увеличиваются и достигают минимального значения, когда содержание полиэфирного волокна составляет 0,4%. В то же время сопротивление низкотемпературному растрескиванию проницаемой асфальтовой смеси из полиэфирного волокна также является наилучшим.
1. Введение
Асфальтовое покрытие обладает такими преимуществами, как гладкая поверхность, комфортное вождение, низкий уровень шума и отсутствие пыли. Он стал основным видом дорожного покрытия высокого качества.Однако обычное асфальтовое покрытие имеет плохую водопроницаемость, и вода, собранная на поверхности дороги, не может быть удалена вовремя, что приводит к снижению противоскользящих свойств дорожного покрытия и снижает безопасность вождения [1, 2]. Проницаемая асфальтовая смесь имеет большое количество пустот, что позволяет быстро удалять воду с поверхности и защищать слой конструкции дорожного покрытия от водной эрозии. Проницаемая асфальтовая смесь требует высоких характеристик асфальта; поэтому для асфальтовой смеси обычно используется модифицированный с высокой вязкостью асфальт вместо обычного асфальта.Но дорогой модифицированный асфальт с высокой вязкостью ограничивает популяризацию и применение проницаемого асфальтового покрытия.
В проницаемой асфальтовой смеси трудно удовлетворить требования к высокой вязкости, используя только обычный модифицированный асфальт, но вязкость можно увеличить, добавив полиэфирное волокно [3, 4], и его вязкость также увеличивается с увеличением содержание полиэстера [5]. Полиэфирное волокно имеет большую удельную поверхность и может поглощать некоторое количество асфальта, уменьшая потери при утечке.Кроме того, полиэфирное волокно также может поглощать насыщенные углеводороды и ароматические углеводороды в асфальтовой смеси и увеличивать силу сцепления между асфальтом и поверхностью заполнителя [6]. В последние годы было замечено, что полиэфирные волокна могут увеличивать прочность на сжатие, водостойкость и температурную чувствительность смесей SMA [7–10]. Существует большое количество битумных вяжущих с модифицированным волокном и асфальтовых смесей с модифицированным волокном, которые можно использовать для решения основных проблем с гибким покрытием, таких как колейность, усталостное растрескивание, термическое растрескивание и разрыхление [11]. Кроме того, некоторые проблемы с дренажом исследуются в пористой смеси, и результаты показывают, что включение полиэфирного волокна уменьшает проблемы с дренажом [12, 13].
Проницаемая асфальтовая смесь представляет собой разновидность специальной смеси горячего асфальта, которая имеет характеристики большого количества пустот, высокого содержания крупного заполнителя и хороших контактных характеристик заполнителя. По сравнению с плотно уложенными асфальтовыми смесями, проницаемые асфальтовые смеси имеют более высокую долю пустот, что достигается за счет уменьшения количества песка и минеральных наполнителей [14].Из-за наличия большего количества пустот покрытие будет в некоторой степени повреждено. Следовательно, процесс уплотнения должен строго контролироваться в процессе приготовления, чтобы обеспечить полное состояние контакта между агрегатами, чтобы обеспечить достаточное сопротивление разложению и остаточной деформации смеси [15–18]. Некоторые исследования показали, что содержание крупного заполнителя в проницаемой асфальтовой смеси достигает 80%, а вложение и экструзия между минеральными частицами и вяжущим с высокой силой сцепления делают его более стойким к высоким температурам, чем плотный. отсортированная асфальтобетонная смесь [19–21], но ее низкотемпературные характеристики хуже.
Проницаемая асфальтовая смесь может быстро удалить воду с поверхности дороги из-за наличия большего количества соединенных пустот, но полузамкнутые пустоты будут оставлять немного воды в пустотах, что вызовет повреждение асфальтового покрытия от морозного пучения при низкой температуре. Низкотемпературное растрескивание — одно из основных заболеваний асфальтового покрытия, которое сильно влияет на его функцию. Некоторые исследования показали, что полиэфирное волокно оказывает определенное влияние на низкотемпературную трещиностойкость асфальтобетонной смеси [22, 23].Введение полиэфирного волокна позволяет повысить ударную вязкость асфальтовой смеси, снизить чувствительность смеси к воде, улучшить трещиностойкость смеси и продлить срок ее службы при низких температурах [5, 24, 25].
Таким образом, исследования проницаемой асфальтовой смеси в основном сосредоточены на анализе поверхности контакта заполнителя смеси, а в некоторых литературных источниках изучались высокотемпературные характеристики и водостойкость проницаемой асфальтовой смеси. Однако мало исследований сообщают о влиянии полиэфирного волокна на пористость и низкотемпературные свойства проницаемых асфальтовых смесей. Таким образом, эта статья дает разумное содержание полиэфирного волокна и пустот, анализируя влияние содержания полиэфирного волокна на воздушные пустоты и низкотемпературные характеристики, а также дает рекомендации по укладке дорожного покрытия из проницаемой асфальтовой смеси.
2. Материалы, оценка и методы
2.1. Материалы
2.1.1. Заполнители
Крупные и мелкие заполнители представляют собой соответственно прокатанный известняковый гравий и механический известняковый песок, производимые Huainan, которые являются чистыми, сухими, не выветрившимися и не содержат примесей.Они обладают достаточной прочностью и износостойкостью, игольчатое содержимое небольшое, а частицы имеют угловатую форму. Наполнитель — это минеральный порошок с размером частиц менее 0,075 мм. Минеральный порошок должен быть измельчен из гидрофобного камня, такого как твердоосновная порода в известняке или магматической породе, и может свободно вытекать из силоса. Физические свойства и химический состав минерального порошка приведены в таблицах 1 и 2.
|
|
2.
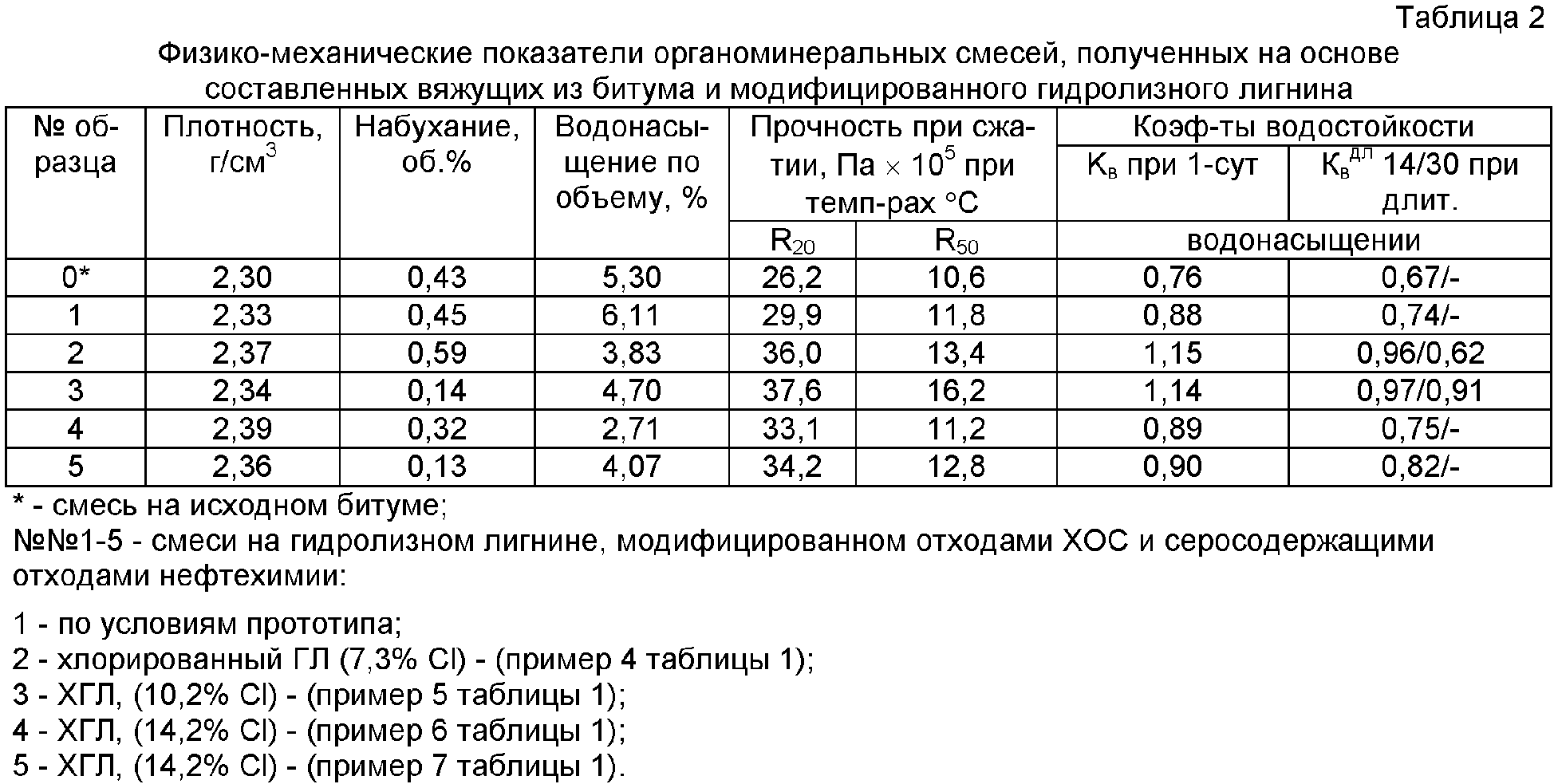
При проектировании проницаемых асфальтовых материалов для дорожного покрытия требования к асфальту высоки, и следует выбирать асфальт с высокой вязкостью. В настоящее время в Китае используются два типа битумов с модифицированной высокой вязкостью: один — это законченный битум с модифицированной высокой вязкостью, а другой — с непосредственным добавлением модификатора в асфальтовую смесь.Однако из-за относительно высокой стоимости двух типов асфальта продвижение и применение проницаемого асфальтового покрытия сильно ограничено. Таким образом, в испытании используется асфальт, модифицированный SBS [26, 27], а битум, модифицированный высокой вязкостью, получают путем добавления полиэфирного волокна для снижения стоимости водопроницаемого асфальтового покрытия. Технические показатели асфальта, модифицированного СБС, приведены в таблице 3.
|
2.1.3. Полиэфирное волокно
В асфальтовой смеси полиэфирное волокно образует трехмерную сетчатую структуру, которая в основном играет армирующую роль в увеличении толщины асфальтовой пленки на поверхности заполнителя и усиливает адгезию между заполнителем и асфальтом [4, 28].Эффект сцепления между полиэфирным волокном и инкапсулированной частицей улучшает прочность и стабильность асфальтовой смеси и снижает утечки и потери при рассеянии дренажной смеси [29]. Полиэфирное волокно, использованное в испытании, показано на Рисунке 1, а технические показатели — в Таблице 4.
| 6 900 2.2. Воздушные пустоты и сортировка
|
Из таблицы 5 видно, что при умеренной интенсивности дождя воздушные пустоты составляют 14,1% ∼18,6%. В процессе использования водопроницаемого асфальтового покрытия пыль и мусор будут перекрывать пустоты. Кроме того, после многократной прокатки грузового автомобиля коэффициент пустотности будет уменьшаться из года в год. Следовательно, при расчете коэффициента пустотности обычно берется верхний предел.Но функциональные и структурные требования к водопроницаемой асфальтовой смеси следует всесторонне учитывать при определении целевых воздушных пустот. Целевые воздушные пустоты в проницаемой смеси полиэфирного волокна и асфальта составляют 20%. [34–36].
2.2.2. Определение градации
Воздушные пустоты в проницаемой асфальтовой смеси напрямую влияют на дренажную функцию, но выбор градации минерального заполнителя определяет воздушные пустоты [37] и массовый процент 2.Сетка 36 мм и 4,75 мм оказывает важное влияние на воздушные пустоты [38, 39]. Когда оптимальный массовый процент сетки 4,75 мм составляет 15%, связанные воздушные пустоты составляют 15,4%, а воздушные пустоты — 19,7%, что близко к целевым воздушным пустотам в 20% [39]. Окончательно определено, что массовый процент минерала с размерами 2,36 мм и 4,75 мм составляет 12% и 15%. В соответствии с характеристиками движения и климатическими условиями в Китае используется мелкозернистая проницаемая асфальтобетонная смесь типа PAC-13, градационный состав которой показан на рисунке 2.
2.3. Содержание полиэфирного волокна и оптимальное содержание асфальта
Волокно может улучшить устойчивость асфальтовой смеси к погружению в воду, а эффект усиления связан с типом волокна. В эксперименте по влиянию соли на водостойкость асфальтобетонной смеси Джи [40] изучил и проанализировал такое же содержание волокон (0,3%, массовая доля асфальтовой смеси) в лигниновом волокне, полиэфирном волокне и базальтовом волокне и обнаружил что асфальтовая смесь с полиэфирным волокном (0.3%) имел лучшую водостойкость. Основываясь на испытании на дренаж вяжущего Шелленберга, испытании Маршалла и испытании на расщепление при замораживании-оттаивании, Чжан [41] изучил правила изменения потерь при утечке, показателя эффективности Маршалла, прочности на разрыв и водостойкости проницаемой асфальтовой смеси с содержанием полиэфирных волокон. 0,3% ∼0,5%. Когда количество полиэфирного волокна составляет 0,4%, истечение связующего является наименьшим, стабильность по Маршаллу и значение текучести являются максимальными, прочность на разрыв при расщеплении является наибольшей, а устойчивость к воде является наилучшей. Учитывая, что содержание полиэфирного волокна в асфальтовой смеси обычно составляет от 0,3% до 0,5% [23, 24], содержание полиэфирного волокна в этой бумаге составляет 0,3%, 0,35%, 0,4%, 0,45% и 0,5%. Между тем, те, у кого нет полиэфирных волокон, взяты за контрольную группу.
Хотя тест Маршалла обычно используется для определения пропорции асфальтобетонной смеси [42], проницаемая асфальтовая смесь представляет собой структуру, залитую множеством нитей, и оптимальное содержание асфальта не может быть получено с помощью метода испытаний Маршалла.Оптимальное количество асфальта, используемого в проницаемой асфальтовой смеси, может быть получено на основе теста на дренаж вяжущего Шелленберга [43]. В зависимости от различных инструментов, используемых в тесте [44], его можно разделить на метод стакана [43], метод эмалевого диска [45] и метод корзины [46]. В этой статье толщина асфальтовой пленки установлена равной 14 мкм м [47]. Согласно методике расчета толщины асфальтовой пленки [48, 49], оптимальное содержание асфальта в проницаемой асфальтовой смеси с содержанием полиэфирного волокна 0% определяется равным 4. 95%. Оптимальное содержание асфальта в проницаемой асфальтовой смеси при разном содержании полиэфирного волокна определяется методом химического стакана. Сравнительная таблица до и после испытания на дренаж вяжущего по Шелленбергу показана на рисунке 3. Результаты теста показаны в таблице 6. Утечка вяжущего рассчитывается по следующему уравнению: где м 0 — это масса стакана, грамм; м 1 — общая масса стакана и асфальтобетонной смеси, г; м 2 — масса стакана и асфальтового раствора, налипшего на стакан, г; Δ м — истощение связующего,%.
|
Согласно результатам испытания на дренаж вяжущего Шелленберга, чем меньше стекание вяжущего, тем больше толщина пленки асфальта на поверхности заполнителя и тем лучше связь между агрегатами. Добавление полиэфирного волокна может уменьшить стекание связующего асфальта и улучшить адгезию между заполнителем и асфальтом. Основная причина этого явления заключается в том, что полиэфирное волокно обладает характеристиками липофильности и большой удельной поверхностью и может адсорбировать свободный асфальт с образованием асфальтовой пленки и уменьшать потери дренажа связующего. Однако в случае определенного количества волокна адсорбция волокна на асфальте в основном такая же, как эффект препятствия потоку. По мере увеличения количества асфальта потери от утечки увеличиваются. Следовательно, существует определенная зависимость между количеством полиэфирного волокна и количеством асфальта. В сочетании с результатами испытаний Zhang и Wu [50] было обнаружено, что оптимальное количество асфальта, используемого в проницаемой асфальтовой смеси, пропорционально содержанию волокна, что можно увидеть на Рисунке 4.
2.4. Методы
2.4.1. Расчет воздушных пустот и связанных воздушных пустот
Существует три типа воздушных пустот, связанных воздушных пустот, полусвязанных воздушных пустот и закрытых воздушных пустот. Как показано на рисунке 5, соединенные воздушные пустоты относятся к зазору внутри смеси, который может сообщаться с внешней средой и выполнять функции дренажа и поглощения шума. Воздушные пустоты в проницаемой асфальтовой смеси из полиэфирного волокна измеряют объемным методом. Соотношение воздушных пустот и связанных воздушных пустот можно рассчитать по следующим уравнениям [51]: где VV — процент воздушных пустот в битумной смеси,%; — насыпная плотность битумной смеси; — теоретический максимальный удельный вес битумной смеси; количество воздушных пустот в образце,%; V — объем образца, см 3 ; — объем заполненных и закрытых пустот, см 3 ; d и h — диаметр и высота образца, см; A — масса высушенного образца на воздухе, г; C — масса образца в воде, г; и — плотность воды, 1.0 г / см 3 .
Размер связанных воздушных пустот напрямую определяет прочность и дренажную способность проницаемой смеси полиэфирного волокна и асфальта [52]. Следовательно, получение точного соотношения связанных воздушных пустот важно для дренажной способности дорожного покрытия.
2.4.2. Испытание на трехточечный изгиб
Испытание на изгиб является одним из основных методов оценки низкотемпературных характеристик асфальтовой смеси. Размер образца балки составляет 250 мм × 30 мм × 50 мм, он вырезан из образца пластины размером 300 мм × 300 мм × 50 мм, сформированного методом прокатки колеса, как показано на рисунке 6.Условия испытаний: −10 ° C и скорость нагружения 50 мм / мин. Если образец вышел из строя, запишите максимальную нагрузку и прогиб в середине пролета. Во время разрушения предел прочности при изгибе, максимальная деформация при изгибе и модуль жесткости при изгибе могут быть рассчитаны по следующим уравнениям: где — предел прочности при изгибе при разрушении образца, МПа; — максимальная деформация растяжения при изгибе при разрушении образца, με ; — модуль жесткости на изгиб при разрушении образца, МПа; b — ширина образца, мм; h — высота образца, мм; L — пролет образца, мм; — максимальная нагрузка при разрушении образца N ; d — прогиб в середине пролета при разрушении образца, мм.
3. Результаты и обсуждение
3.1. Влияние содержания полиэфирного волокна на воздушные пустоты и связанные воздушные пустоты
Результаты испытаний воздушных пустот и связанных воздушных пустот проницаемой асфальтовой смеси с различным содержанием полиэфирного волокна показаны в таблице 7.
|
Из таблицы 7 видно, что содержание полиэфирного волокна увеличивается с 0,3% до 0,5 %, воздушные пустоты в проницаемой асфальтовой смеси составляют 19,4%, 19,3%, 19,1%, 19,6% и 19,7% соответственно, в то время как связанные воздушные пустоты составляют 15,1%, 15,0%, 14,9%, 15,2% и 15,3%. . По сравнению с таковыми без полиэфирного волокна воздушные пустоты в проницаемой асфальтовой смеси уменьшаются на 1.5%, 2,0%, 3,0%, 0,5% и 0% соответственно, в то время как связанные воздушные пустоты уменьшаются на 1,9%, 2,6%, 3,2%, 1,3% и 0,6%. Видно, что полиэфирное волокно мало влияет на воздушные пустоты и связанные воздушные пустоты. Кроме того, минимальная воздушная полость составляет 19,1%, а минимальная присоединенная воздушная полость составляет 14,9% проницаемой асфальтовой смеси при содержании полиэфирного волокна 0,4%, что соответствует требованиям спецификации (18% ~ 25%,> 14% ) [51]. Указывается, что добавление полиэфирного волокна к модифицированному асфальту может заменить модифицированный высокой вязкостью асфальт на проницаемую асфальтовую смесь.
Согласно таблице 7 соотношение между воздушными пустотами и количеством полиэфирного волокна показано на рисунке 7. Взаимосвязь между соединенными воздушными пустотами и количеством полиэфирного волокна показано на рисунке 8.
Из рисунков 7 и 8 видно, что воздушные пустоты и связанные воздушные пустоты проницаемой смеси полиэфирного волокна и асфальта демонстрируют аналогичные тенденции. Когда полиэфирное волокно увеличивается с 0,3% до 0,5%, изменение воздушных пустот и связанных воздушных пустот в проницаемой асфальтовой смеси сначала уменьшается, а затем увеличивается.По мере увеличения содержания полиэфирного волокна с 0,3% до 0,4% воздушные пустоты и связанные воздушные пустоты постепенно уменьшаются с 19,4% и 15,1% до 19,1% и 14,9% соответственно. В то время как с увеличением содержания полиэфирного волокна с 0,4% до 0,5% воздушные пустоты и связанные воздушные пустоты постепенно увеличиваются с 19,1% и 14,9% до 19,7% и 15,3% соответственно.
Основная причина этого явления заключается в том, что в случае, когда содержание полиэфирного волокна невелико, его можно равномерно распределить в смеси, чтобы заполнить внутренние пустоты в смеси.Когда содержание полиэфирного волокна увеличивается до 0,4%, равномерное распределение полиэфирного волокна в асфальтовой смеси достигает максимума, и количество заполненных пустот также достигает максимума, а соответствующие воздушные пустоты и связанные воздушные пустоты достигают минимума. Однако при содержании полиэфирного волокна более 0,4% воздушные пустоты в асфальтовой смеси постепенно увеличиваются [53]. Поскольку полиэфирные волокна неравномерно распределены в асфальтовой смеси, между волокнами возникают агломераты и спутывания, а агломерированные волокна разделяют агрегаты и увеличивают внутренние пустоты в асфальтовой смеси.
3.2. Влияние содержания полиэфирного волокна на сопротивление низкотемпературному растрескиванию
Испытание на изгиб используется для анализа влияния полиэфирного волокна на сопротивление низкотемпературному растрескиванию проницаемой асфальтовой смеси. Результаты испытаний представлены в таблице 8.
|
8, что видно Предел прочности при изгибе проницаемой асфальтовой смеси составляет 3,57 МПа, 5,02 МПа, 5,87 МПа, 6,66 МПа, 4,48 МПа и 4,24 МПа при содержании полиэфирного волокна от 0% до 0,5%. По сравнению с пределом прочности при изгибе без полиэфирного волокна предел прочности на изгиб асфальтовой смеси из полиэфирного волокна увеличивается на 40.6%, 64,4%, 86,6%, 25,5% и 18,8% соответственно. Следовательно, полиэфирное волокно может значительно улучшить прочность смеси на изгиб и повысить устойчивость к низкотемпературным усадочным напряжениям.
Максимальная деформация при растяжении при изгибе — это показатель для измерения способности асфальтовой смеси к низкотемпературной деформации. Чем больше максимальная деформация растяжения при изгибе, тем больше диапазон деформации асфальтовой смеси и лучше сопротивление низкотемпературному растрескиванию. Из Таблицы 8 видно, что максимальная деформация растяжения при изгибе проницаемой асфальтовой смеси составляет 1575 με , 2538 με , 3308 με , 4174 με , 2014 με и 2266 με , соответственно.Когда содержание полиэфирного волокна составляет 0,4%, максимальная деформация растяжения при изгибе достигает максимума, 4174 με . В настоящее время сопротивление низкотемпературному растрескиванию проницаемой смеси полиэфирного волокна и асфальта является оптимальным. Это связано с тем, что полиэфирное волокно оказывает усиливающее и связывающее действие в смеси, что увеличивает адгезию между заполнителем и асфальтом и увеличивает трещиностойкость смеси [54].
Дренажный эффект проницаемого асфальтового покрытия зависит от содержания воздушных пустот.Чем выше содержание воздушных пустот, тем лучше дренажный эффект и хуже сопротивление низкотемпературным трещинам. Как видно из таблицы 8, когда содержание полиэфирного волокна составляет 0%, воздушные пустоты проницаемой асфальтовой смеси составляют 19,7%, что близко к целевым воздушным пустотам. Однако как предел прочности при изгибе, так и максимальная деформация растяжения при изгибе проницаемой асфальтовой смеси минимальны. Когда содержание полиэфирного волокна составляет 0,4%, воздушное пространство проницаемой асфальтовой смеси составляет 19.1%. По сравнению с содержанием полиэфирного волокна 0%, воздушные пустоты уменьшаются на 3,0%, а дренажный эффект немного уменьшается. Но предел прочности при изгибе увеличивается на 86,6%, а максимальная деформация растяжения при изгибе увеличивается на 165,0%. Следовательно, полиэфирное волокно может улучшить сопротивление низкотемпературному растрескиванию проницаемой асфальтовой смеси и немного снизить ее дренажную способность. Но он по-прежнему соответствует требованиям спецификации [51].
Согласно результатам испытаний на низкотемпературный изгиб, соотношение между пределом прочности на изгиб, модулем жесткости при изгибе и содержанием полиэфирных волокон в проницаемой асфальтовой смеси показано на рисунках 9 и 10.
Разрушение балок из асфальтосмеси при изгибе в основном вызвано растрескиванием вдоль поверхности раздела заполнителя. Крупные частицы, встречающиеся во время крекинга, вызывают экструзию и сдвиг, а также вызывают повреждение асфальтовой смеси, модифицированной SBS, в условиях низких температур. Видно, что хорошая граница раздела является важной гарантией предотвращения растрескивания смеси [53]. Кроме того, агломерация полиэфирного волокна в асфальте приводит к неравномерному распределению асфальтовой пленки и неравномерному распределению сетевой структуры полиэфирного волокна в асфальте [55].Это приводит к прерывистой фазе асфальта, модифицированного SBS, что значительно снижает прочность поверхности раздела асфальтовой смеси, модифицированной SBS. Следовательно, под действием нагрузки в асфальтовой смеси, модифицированной SBS, возникает концентрация напряжений, которая вызывает растрескивание при низкой температуре.
Из рисунка 9 видно, что с увеличением количества полиэфирного волокна предел прочности на изгиб проницаемой смеси полиэфирного волокна и асфальта сначала увеличивается, а затем уменьшается и достигает пика, когда содержание полиэфирного волокна равно 0.4%. Прочность на растяжение при изгибе является показателем для измерения влияния напряжения низкотемпературной усадки на асфальтобетонную смесь. Чем выше предел прочности при изгибе, тем выше способность смеси противостоять низкотемпературным повреждениям и лучше сопротивление низкотемпературным трещинам. Модуль жесткости при изгибе может в определенной степени отражать сложность низкотемпературного растрескивания асфальтовой смеси. Чем меньше модуль жесткости на изгиб, тем больше энергии требуется для растрескивания смеси и тем лучше сопротивление растрескиванию.Из рисунка 10 видно, что модуль жесткости при изгибе имеет минимальное значение 1594 МПа, когда содержание полиэфирного волокна составляет 0,4%, а битумная смесь из проницаемого полиэфирного волокна имеет лучшее сопротивление низкотемпературному растрескиванию.
Всесторонний анализ рисунков 9 и 10 показывает, что добавление полиэфирного волокна улучшает вязкость и жесткость битума, модифицированного SBS, и задерживает низкотемпературное растрескивание проницаемой асфальтовой смеси. Когда содержание полиэфирного волокна ниже 0.4% низкотемпературные характеристики проницаемой асфальтовой смеси постепенно повышаются, полиэфирное волокно диспергируется внутри структуры с образованием межфазного слоя, а структурный асфальт на межфазном слое имеет большую вязкость, чем свободный асфальт снаружи. Тесное сочетание заполнителя и полиэфирного волокна усиливает эффект армирования и перекрытия и улучшает низкотемпературные характеристики асфальтовой смеси. Однако при содержании полиэфирного волокна более 0.4% низкотемпературные характеристики проницаемой асфальтовой смеси начинают снижаться, а низкотемпературные характеристики асфальтовой смеси снижаются, что в основном связано с явным эффектом агломерации и снижением адгезии между асфальтом и агрегированным материалом. с непрерывным наращиванием полиэфирного волокна.
Из таблицы 8 также видно, что когда для оценки низкотемпературных характеристик асфальтовой смеси используется только максимальная деформация при изгибе или модуль жесткости при изгибе, вывод о пределе прочности при изгибе отличается.Следовательно, при оценке сопротивления низкотемпературному растрескиванию следует принимать во внимание предел прочности при изгибе, максимальную деформацию растяжения при изгибе и индекс модуля жесткости при изгибе. Если рассматривать три индекса в целом, то при содержании полиэфирного волокна 0,4% проницаемая асфальтобетонная смесь имеет наилучшую стойкость к низкотемпературным трещинам.
3.3. Влияние воздушных пустот на сопротивление низкотемпературным трещинам
Взаимосвязь между соединенными воздушными пустотами и воздушными пустотами в проницаемой смеси полиэфирного волокна и асфальта и взаимосвязь между воздушными пустотами и пределом прочности при изгибе показана на рисунках 11 и 12.
Из рисунка 11 видно, что соединенные воздушные пустоты и воздушные пустоты проницаемой смеси полиэфирного волокна и асфальта линейно связаны, а коэффициент корреляции равен 0,929. Показано, что связанные воздушные пустоты также непрерывно увеличиваются с увеличением воздушных пустот. Этот вывод аналогичен заключению исследования Pattanaik et al. [56]. Воздушные пустоты и связанные с ними воздушные пустоты определяют дренажные характеристики смеси.Следовательно, в соответствии с предпосылкой удовлетворения функции проницаемой смеси асфальта из полиэфирного волокна, следует использовать большую воздушную полость, насколько это возможно, для обеспечения дренажной функции.
Из рисунка 12 видно, что предел прочности при изгибе проницаемой смеси полиэфирного волокна и асфальта имеет хорошую линейную корреляцию с воздушными пустотами. По мере увеличения воздушных пустот прочность смеси на изгиб постоянно снижается. Он показывает, что чем больше воздушные пустоты, тем хуже способность смеси противостоять низкотемпературным повреждениям и тем хуже сопротивление низкотемпературным трещинам.Отношение между воздушными пустотами и связанными воздушными пустотами линейно увеличивается, и связанные воздушные пустоты являются ключевым фактором в управлении дренажом смеси [57]. Поэтому очень важно выбрать подходящее воздушное пространство, чтобы обеспечить низкотемпературные характеристики и дренажные характеристики асфальтовой смеси. Согласно анализу рисунков 11 и 12, можно сделать вывод, что когда воздушная пустота составляет 19,1%, это не только удовлетворяет требованиям функции дренажа, но также обеспечивает сопротивление смеси при низкотемпературном растрескивании.
4. Заключение
В данной статье в основном анализируется влияние содержания полиэфирного волокна на сопротивление низкотемпературному растрескиванию и наличие воздушных пустот в проницаемой асфальтовой смеси и делаются следующие основные выводы: (1) Воздушные пустоты и связанные воздушные полости проницаемости смеси полиэфирного волокна и асфальта сначала уменьшаются, а затем увеличиваются с увеличением содержания полиэфирного волокна; воздушные пустоты и связанные воздушные пустоты достигают минимальных значений 19,1% и 14,9%, когда содержание полиэфирного волокна равно 0.4%. (2) Предел прочности на изгиб проницаемой асфальтобетонной смеси из полиэфирного волокна достигает максимального значения, когда содержание полиэфирного волокна составляет 0,4%, что указывает на то, что смесь имеет самую высокую стойкость к низкотемпературным повреждениям и лучшую стойкость к растрескиванию при низкая температура. (3) Воздушные пустоты являются важным фактором, влияющим на предел прочности при изгибе проницаемой смеси полиэфирного волокна и асфальта. Прочность на растяжение при изгибе уменьшается с увеличением воздушных пустот. В воздушной пустоте 19.1%, предел прочности при изгибе достигает максимального значения. (4) Добавление необходимого количества полиэфирного волокна и выбор разумных воздушных пустот может улучшить сопротивление низкотемпературному растрескиванию проницаемой смеси полиэфирного волокна и асфальта.
Доступность данных
Наборы данных, созданные и проанализированные в ходе текущего исследования, доступны у соответствующего автора по разумному запросу.
Конфликт интересов
Авторы заявляют, что у них нет конфликта интересов.
Благодарности
Это исследование финансировалось Исследовательским проектом естественных наук колледжей и университетов провинции Аньхой (№ KJ2017A096).
Составляющие бетонные материалы — InterNACHI®
Ник Громицко, CMI® и Кентон Шепард
Бетон — это композитный материал, состоящий из вяжущего, которое обычно представляет собой цемент, грубые и мелкие заполнители, которые обычно представляют собой камень и песок, и воду. Они состоят из материалов, из которых состоит бетон.Но из-за множества переменных в сырье, а также в том, как они обрабатываются и комбинируются, существует много возможностей для возникновения проблем в бетоне. Наличие фундаментального понимания различных материалов и производственных процессов может помочь тем, кто исследует бетон, узнать, какие проблемы следует искать, где их искать и как их распознать.
Проще говоря:
- цемент + вода = цементное тесто;
- цементная паста + песок = раствор; и
- раствор + камень = бетон.
Добавки могут быть включены в смесь для управления параметрами настройки.
Химические реакции, происходящие при объединении различных составляющих материалов, могут различаться в зависимости от свойств отдельных материалов. Материалы могут различаться по своему химическому составу и эксплуатационным характеристикам в зависимости от того, где они были добыты или добыты, а также в зависимости от используемых методов производства и условий на заводе-изготовителе.
Связующие
Связующие представляют собой мелкие гранулированные материалы, которые при добавлении воды образуют пасту.Эта паста затвердевает и герметизирует заполнители и арматурную сталь. Сразу после добавления воды цементное тесто начинает затвердевать в результате химического процесса, называемого гидратацией. Гидратация происходит с разной скоростью в зависимости от различных свойств используемых вяжущих и добавок, соотношения воды и цемента и условий окружающей среды, в которых находится бетон. Способы воздействия вяжущих на бетон, строительный раствор и аналогичные продукты могут варьироваться в зависимости от химических и физических свойств исходных материалов, составляющих материалов, конструкции смеси и, в меньшей степени, от изменений в процессе производства цемента.
Портландцемент
Портландцемент
Существуют разные типы цемента, но портландцемент является наиболее широко используемым вяжущим. Хотя портландцемент назван в честь района в Англии, где его начали использовать, сегодня он производится во всем мире.
ASTM International определяет портландцемент как «гидравлический цемент (цемент, который образует водостойкий продукт), полученный путем измельчения клинкера, состоящего в основном из гидравлических силикатов кальция, обычно содержащих одну или несколько форм сульфата кальция в качестве добавки в грунт.”
Портландцемент изготавливается путем сплавления материалов, содержащих кальций, с материалами, содержащими алюминий. Кальций может поступать из известняка, ракушек, мела или мергеля, который представляет собой мягкий камень, или твердой грязи, иногда называемой аргиллитом, которая богата известью.
Процесс производства цемента
Основные операции цементных заводов примерно одинаковы, но могут различаться в зависимости от местоположения. В следующем производственном процессе описывается, что происходит на карьере и цементном заводе в Колорадо.
Карьерные работы
Слой известняка толщиной около 18 футов вырывает поверхность и уходит под землю. Карьерные работы следуют за ним до уровня примерно 200 футов, прежде чем его добыча становится невыгодной.
Темная порода, изображенная выше, содержит известняк и два вида сланца, все из которых используются для производства цемента. Светлоокрашенный материал называется перегрузкой, он не используется в производстве, но откладывается для замены позже во время рекультивации после того, как карьер достиг конца срока действия разрешения и будет закрыт.
Плоский участок в стене карьера, называемый подъемником или уступом, — это глубина, на которую просверливаются отверстия перед установкой зарядов для взрывных работ. Здесь он составляет около 80 футов. Из-за требований национальной безопасности большинство карьеров передают взрывные работы субподрядчикам.
После взрывных работ каменные отходы доставляются в конец карьера, где впервые началась добыча. Это будет первый материал, который будет снова заполнен в рамках процесса рекультивации. Полезный камень перевозится грузовиком и либо сбрасывается в первичную дробилку, либо складывается поблизости.
Дороги и сваи необходимо поливать водой, чтобы уменьшить количество переносимой по воздуху пыли.
Грузовики возвращаются в это здание, чтобы выгружать свои грузы в первичную дробилку.
Первичная дробилка
После того, как камень загружается в загрузочный лоток сверху, сила тяжести перемещает его вниз через дробилку, что уменьшает его диаметр примерно до 3 дюймов. Карманный фильтр помогает уменьшить количество переносимой по воздуху пыли.
Из дробилки камень перемещается на конвейерную ленту, которая доставляет его на производственный завод на расстоянии около 2 миль.
Длинные конвейерные ленты должны быть отрегулированы для надлежащего натяжения. Это делается с помощью стальных тросов для подвешивания бетонных грузов внутри башен.
В каждой точке, где конвейер меняет высоту или направление, другой рукавный фильтр помогает удалить пыль из щебня и из воздуха.
Известняк и сланец, наконец, складываются в дальний конец производственной линии.
Камень загружается фронтальным погрузчиком по одному ковшу за раз на конвейер, который переносит его в перегрузочный бункер (вверху слева).Из разгрузочного бункера камень может подаваться в систему с равномерной скоростью. Из разгрузочного бункера камень транспортируется в сушилку, которая удаляет большую часть влаги перед возвратом во вторичную дробилку (центральный бункер), где он уменьшается до примерно 3/8 дюйма в диаметре. С этого момента камень транспортируется высокоскоростным воздухом, а не ремнями с роликовыми опорами.
Высушенный щебень затем перемещается в шаровую мельницу, в которой стальные шарики превращаются в порошок.Шаровая мельница — это вращающийся цилиндр, который имеет жертвенную футеровку, удерживаемую на месте сотнями болтов, головки которых можно увидеть на фотографии выше.
В шаровой мельнице комбинируются различные материалы, поэтому именно здесь происходит первоначальное смешивание. Обычные материалы — известняк, сланец, песчаник и железо.
Из шаровой мельницы материал перемещается в башню предварительного нагрева (слева), где он нагревается примерно до 1800 ° F перед перемещением в горизонтальную цилиндрическую вращающуюся печь.
Печь (темно-серая) слегка наклонена, так что материал перемещается через нее при вращении. Труба с более крутым наклоном над печью (светло-серая) подает воздух для горения, как и U-образный канал наверху башни предварительного нагрева. Внутри печи материал нагревается примерно до 3300 ° F. Этот процесс называется спеканием. Происходят химические изменения, которые приводят к образованию вещества размером с мрамор, называемого клинкером. Создание клинкера означает использование тепла для удаления всего углекислого газа из материала.Двуокись углерода — один из основных парниковых газов.
На фотографии выше показаны открытые двери в нижнем конце печи, которая закрыта для осмотра и обслуживания. Гибкая труба диаметром 6 дюймов, наклонная влево, служит для подачи газа в горелку, которая воспламеняет пылевидное угольное топливо. Конец 8-дюймовой трубы для подачи угля можно увидеть справа от ног рабочего.
Запасы пылевидного угля, используемого в качестве топлива для печи
Клинкер перемещается в навес специальной формы для контроля его влажности.
Клинкер тонко измельчается для создания конечного цементного продукта. На фотографии выше показан клинкер размером с мрамор до измельчения и конечный продукт: цемент.
Мониторинг и управление всей операцией осуществляется с центральной консоли управления, на которой расположены многочисленные мониторы с цифровыми показаниями в реальном времени.
Варианты
Несмотря на то, что существуют стандарты ASTM, которым может соответствовать портландцемент, существует ряд факторов, которые могут повлиять на его рабочие характеристики.
Размер частиц
Размер частиц важен, потому что частицы, которые измельчаются более мелко, имеют большую площадь поверхности, на которой происходят химические реакции, и они сильно влияют на свойства цемента. Цемент с мелкими частицами будет более реактивным и наберет прочность раньше, чем начнется процесс гидратации. Общая площадь поверхности частиц в данном объеме материала называется его удельной поверхностью.
Портлендские цементы имеют удельную поверхность от 1500 до 2000 квадратных футов на фунт материала ( 2 футов / фунт), равную примерно 300–400 квадратных метров на килограмм ( 2 м / кг), в зависимости от типа.
Гипс и сульфаты
Гипс, также в виде измельченных частиц, смешивают с измельченным клинкером, чтобы замедлить процесс гидратации настолько, чтобы было время для укладки бетона, стяжки и отделки перед этим. наборы. Если гипс или сульфатные материалы добавляются к клинкеру и измельчаются вместе с ним, они могут уменьшиться в размере быстрее, чем клинкер. Такое предпочтительное измельчение может привести к более мелким частицам, что увеличивает их отношение реакционной способности по сравнению с клинкером.
Для любого конкретного цемента существует оптимальное содержание как гипса, так и сульфата. Детали того, как именно сульфаты влияют на рост прочности бетона, не совсем понятны.
Оптимальное содержание гипса и сульфатов зависит не только от типа расчетной цементной смеси, но и от:
- химических свойств как кальциевых, так и алюминиевых исходных материалов, используемых для клинкера;
- физические свойства алюминатов, такие как размер кристаллов;
- различная растворимость различных источников сульфатов;
- размер частиц;
- температура фрезерования; и
- использование добавок.
Как будто это было недостаточно сложно, оптимальное содержание сульфатов для одного свойства цемента, такого как прочность, может отличаться от оптимального содержания для другого свойства, такого как усадка при высыхании. Бетон и раствор могут иметь разный оптимальный состав, поэтому производятся разные виды цемента.
В процессе производства материалы проходят четыре испытания, чтобы предотвратить такие проблемы. Сырье проверяется перед тем, как попасть в производственный процесс, перед входом в печь, после выхода из печи и перед окончательным хранением в основных силосах хранения.
Цементные пластины, использованные в части процесса испытаний
Оборудование, используемое для испытания прочности на сжатие
Типы цемента
Спецификация ASTM C-150 содержит стандарты для восьми различных типов портландцемента :
- Тип I — цемент общего назначения, используемый в самых разных типах проектов, включая здания, мосты, перекрытия, тротуары и сборные железобетонные конструкции.
- Тип IA аналогичен типу I, но используется для проектов, требующих воздухововлечения.
- Тип II выделяет меньше тепла, выделяет тепло с меньшей скоростью и имеет умеренную устойчивость к сульфатному воздействию.
- Тип IIA идентичен типу II, но используется для проектов, требующих воздухововлечения.
- Тип III — это высокопрочный цемент, который заставляет бетон быстро схватываться и набирать прочность. Цемент типа III химически и физически подобен цементу типа I, за исключением того, что частицы более мелко измельчены.
- Тип IIIA — это высокопрочный цемент, используемый для проектов, требующих воздухововлекающих факторов.
- Тип IV развивает прочность медленнее, чем другие типы цемента, и выделяет более низкие уровни тепла во время гидратации. Он используется для крупногабаритных бетонных конструкций, из которых мало шансов отвести тепло, таких как плотины.
- Тип V используется только в бетонных конструкциях, которые будут подвергаться серьезному воздействию сульфатов, обычно в местах, где бетон подвергается воздействию почвы и грунтовых вод с высоким содержанием сульфатов.
ASTM C-1157 включает следующее:
- Гидравлический цемент типа GU используется для общего строительства.
- Тип HE — высокопрочный цемент.
- Тип MS умеренно устойчив к воздействию сульфатов.
- Тип HS обладает высокой устойчивостью к воздействию сульфатов.
- Тип MH выделяет умеренный уровень тепла во время гидратации.
- Тип LH выделяет низкий уровень тепла во время гидратации. Этот тип цемента также может быть рассчитан на низкую реактивность (вариант R) с заполнителями, реагирующими с щелочами.
ДОПОЛНИТЕЛЬНЫЕ ЦЕМЕНТНЫЕ МАТЕРИАЛЫ
Пуццоланы
Другие материалы могут быть смешаны с портландцементом в соответствии с особыми требованиями и экологическими соображениями.Некоторые из этих материалов, называемые пуццоланами, не обладают вяжущими свойствами, пока не будут смешаны с портландцементом. Когда бетон смешивается, чтобы улучшить его удобоукладываемость и текучесть, добавляется больше воды, чем необходимо для гидратации. Этот избыток воды затем присутствует в крошечных капиллярных каналах в гидратированном (затвердевшем) бетоне. Когда часть цемента заменяется пуццоланом, после гидратации происходит вторичная химическая реакция. Химические вещества, высвобождаемые из цементного теста во время гидратации, вступают в реакцию с химическими веществами в пуццолановом материале с образованием материала, который частично или полностью заполняет эти капиллярные каналы.Это делает бетон более плотным и повышает его стойкость к химическим веществам (например, тем, которые используются для операций по борьбе с обледенением), которые могут проникать в пористый бетон и вызывать коррозию арматурной стали и вызывать повреждение поверхности или растрескивание.
Растрескивание поверхности, вызванное антиобледенительными химикатами
Когда часть цемента заменяется пуццоланами, во время гидратации выделяется меньше тепла. Эта вторичная реакция выделяет некоторое количество тепла, но пиковые температуры ниже и растягиваются на более длительный период времени.Поскольку бетон сжимается (сжимается) при охлаждении, меньшее количество тепла означает меньшую общую усадку. Поскольку усадка создает напряжения, которые снимаются растрескиванием, меньшая усадка означает меньшее количество трещин. Это особенно важно для конструкций с большой массой, которые не могут легко отводить тепло, таких как плотины.
Зола-унос
Зола-унос на микроскопическом уровне
Зола-унос — промышленный побочный продукт, который иногда используется в качестве частичной замены портландцемента.Летучая зола состоит из негорючих твердых частиц, которые удаляются из дымовых газов угольных электростанций. Он может составлять до 65% массы вяжущих материалов, в зависимости от требований к характеристикам бетона и типа сжигаемого угля.
Рекуперация летучей золы для промышленного использования является экологически безопасной практикой, поскольку летучая зола удаляется из дымовых газов для улучшения качества воздуха, а ее использование в цементе означает, что то, что когда-то было отходами, теперь перерабатывается как полезный материал.По состоянию на 2005 год угольные электростанции США произвели 71 миллион тонн летучей золы, 29 миллионов тонн из которых были использованы в различных областях. Остальные 42 миллиона тонн могут покрыть акр земли на глубину 27 500 футов. Эта неиспользованная летучая зола занимает место на свалках и содержит токсины, которые могут загрязнять водоносные горизонты. В декабре 2008 года обрушилась насыпь хранилища летучей золы Tennessee Valley Authority в Кингстоне, штат Теннесси, и в реку Эмори было выброшено 5,4 миллиона кубических ярдов летучей золы.Стоимость очистки приближается к 1,2 миллиарда долларов.
Неисправность установки по локализации летучей золы в Кингстоне, Теннесси
Вот некоторые важные факты о летучей золе, используемой в бетоне:
- Летучая зола бывает типов F и C. Летучая зола типа F. сжигая старый, более твердый уголь. Это пуццолан, и при смешивании с водой не образует вяжущих соединений, если смесь не включает портландцемент. Тип C получают путем сжигания более молодого и мягкого угля и при смешивании с водой имеет некоторые вяжущие соединения.
- Очень мелкие частицы летучей золы могут улучшить характеристики текучести бетона, снизить затраты за счет замены цемента, потребовать меньше воды в смеси и сделать бетон более плотным. Крупные частицы не обладают такими же преимуществами, а крупные и мелкие частицы не всегда могут быть эффективно отделены.
- Это может увеличить время схватывания.
- Летучая зола не принимает пигменты или кислотные пятна, а также цемент, поэтому подбор существующего бетона, изготовленного без летучей золы, может быть проблемой.
- Рабочие характеристики летучей золы зависят от размера частиц, а также от химического состава угля, степени измельчения угля перед сжиганием, условий горения в печи, а также методов сбора и обращения с летучей золой. Поскольку эти факторы никогда не одинаковы на разных электростанциях и могут даже меняться в пределах одной электростанции с течением времени, свойства летучей золы могут сильно различаться, и это может быть препятствием для получения стабильно хороших результатов.
- Летучая зола имеет удельную поверхность от 1400 до 3400 футов 2 / фунт (от 280 до 700 м 2 / кг), в зависимости от типа.
Измельченный гранулированный доменный шлак
Клинкер из доменного шлака до измельчения
Измельченный гранулированный доменный шлак (GGBFS) является еще одним промышленным побочным продуктом, который иногда используется в качестве частичной замены Портландцемент. GGBFS — это стекловидный гранулированный материал, получаемый в доменных печах как побочный продукт процесса производства чугуна и стали.Это еще один пример полезного использования материала, который раньше считался отходом.
По сравнению с бетоном, изготовленным только из портландцемента, бетон, содержащий GGBFS:
- затвердевает медленнее;
- выделяет меньше тепла во время гидратации;
- продолжает набирать силу в течение более длительного периода времени; а
- производит более прочный бетон.
Более низкие температуры, создаваемые GGBFS во время гидратации, позволяют расположить контрольные суставы дальше друг от друга.GGBFS заменяется 1: 1 портландцементом и может составлять до 70% от массы цементирующих материалов. GGBFS имеет удельную поверхность от 1700 до 2900 футов 2 / фунт (от 350 до 600 м 2 / кг).
Дым кремнезема
Дым кремнезема увеличен в 10 000 раз
Дым кремнезема иногда используется для улучшения определенных свойств бетона. Это очень тонкий стекловидный порошок, собранный из дымовых газов дуговых электропечей в процессе производства металлического кремния.До введения в действие более жестких экологических законов в середине 1970-х годов кремнеземный дым не собирался. Сейчас он стал одной из самых ценных и универсальных добавок для бетона в мире. В отличие от песка — его химически подобного аналога — частицы микрокремнезема растворимы в воде, а это означает, что они могут вступать в химическую реакцию как часть процесса гидратации.
Когда количества двух гранулированных материалов равны, материалы с более мелкими частицами открывают большую площадь поверхности, на которой могут происходить реакции.Пары кремнезема примерно в 100 раз меньше, чем частицы портландцемента, поэтому его небольшой размер вместе с относительно высоким содержанием кремнезема делают его очень реакционноспособным пуццоланом. Их небольшой размер частиц также позволяет дыму кремнезема заполнять промежутки между зернами цемента, что называется уплотнением частиц, делая бетон более плотным и менее пористым или проницаемым для влаги. Он также улучшает прочность на сжатие, прочность связи между частицами, заполнителями и встроенной сталью, а также повышает устойчивость к истиранию.
Пары кремнезема могут составлять до 12% от массы вяжущих материалов. Пары кремнезема имеют удельную поверхность от 63 000 до 150 000 футов 2 / фунт (от 13 000 до 30 000 м 2 / кг).
Однородность микрокремнезема может варьироваться в зависимости от химических характеристик производимых металлических сплавов. Пары кремнезема из четырех различных печей иногда смешивают вместе, чтобы получить более однородный продукт. Влияние на бетон изменений химических свойств паров кремнезема из различных печей изучено недостаточно.Свойства микрокремнеземного бетона также различаются в зависимости от различных свойств и количества различных водоредуцирующих агентов (пластификаторов), которые обычно используются при добавлении микрокремнезема в бетон. Поскольку огромная площадь поверхности микрокремнезема требует больше воды и снижает удобоукладываемость, добавляются пластификаторы и суперпластификаторы, чтобы сделать бетон более текучим, чтобы его было легче укладывать и обрабатывать.
Бетон обычно смешивают на местных бетонных заводах перед транспортировкой на строительную площадку.Установки периодического действия обычно имеют силосы с летучей золой и часто имеют под рукой GGBFS. Постоянные хранилища кварцевого дыма встречаются реже.
Бетонный завод с двумя бункерами летучей золы
АГРЕГАТЫ
Заполнители — это сыпучие материалы, которые включают песок, гравий, щебень, речной камень и легкие промышленные заполнители, и могут занимать до 75% от общего объема бетона. Поскольку заполнители дешевле, чем цементная паста, их добавляют в бетон, чтобы снизить затраты.Свойства заполнителей могут существенно влиять на удобоукладываемость бетона в его пластическом состоянии, а также на долговечность, прочность, плотность и термические свойства затвердевшего бетона.
Откуда берутся агрегаты?
Заполнители тяжелые. Их разработка в центральном регионе и транспортировка их на большие расстояния обходятся дорого, поэтому заполнители обычно добывают на месте. Это означает, что минеральные, химические и физические свойства, вероятно, будут различаться в разных регионах в зависимости от местной геологии.Минералы с разными свойствами могут по-разному реагировать на химические процессы или условия в бетоне, поэтому заполнители являются еще одним составным материалом для бетона, который может иметь различные свойства.
Разработка карьеров заполнителя
Работа карьера заполнителя аналогична тем, которые используются для добычи камня для получения цемента. Изображенный ниже карьер, также расположенный в Колорадо, поставляет в основном гранитный заполнитель для асфальтобетонной и бетонной промышленности.
На фотографии выше показан разрабатываемый относительно новый карьер.Показано, что буровая установка бурит скважины, в которых будут установлены заряды взрывчатого вещества, в то время как грузовик загружается камнем, разрыхленным предыдущим взрывом. Грузовик доставит камень к дробилке №1.
Старые карьеры работали дольше, поэтому они глубже. Эта операция взрывает скважины, пробуренные глубиной 35 футов, в отличие от 80 футов в карьере известняка. И здесь взрывные работы выполняет субподрядчик. Эта операция включает в себя несколько карьеров в дополнение к зоне обработки, поэтому это большая операция.
Выше грузовик загружает дробилку №1, первую дробилку в серии, через которую проходит камень. Этот карьер производит 18 различных агрегатов, размер которых варьируется от валунов до песка.
Если смотреть прямо в дробилку №1, можно увидеть размер камня до того, как он попадет в дробилку. Камень движется слева направо.
Операции по дроблению и сортировке контролируются с центрального диспетчерского пункта, выходящего на рабочую зону.Ближайший к камере конвейер перемещает камень после обработки Дробилкой №1.
На фотографии выше показан вид на операционную зону, а также на элементы управления и мониторы.
На этой обзорной фотографии показаны две дополнительные дробилки рядом с центром. Несмотря на то, что огромное количество камня дробилось, транспортировалось, толкалось и сбрасывалось на склады, количество переносимой по воздуху пыли было минимальным.
Размер заполнителя
Заполнители для бетона обычно делятся на две категории: мелкие и крупные.Мелкие заполнители, как правило, представляют собой природный песок или щебень, при этом большинство частиц проходит через сито 3/8 дюйма (9,5 мм). Крупные заполнители обычно имеют диаметр от 3/8 до 1-1 / 2 дюйма (от 9,5 до 37,5 мм). Самый крупный заполнитель, используемый в бетоне, — это щебень, хотя также используется гладкий речной камень.
Недостаточное количество мелкозернистых заполнителей может вызвать чрезмерное кровотечение, затруднения при перекачивании бетона и трудности с получением гладких затертых поверхностей. На прочность сцепления мелких заполнителей не сильно влияет форма или текстура заполнителя, так как более мелкие частицы имеют большую площадь поверхности, на которой может происходить сцепление с цементным тестом.Поверхностные свойства мелкозернистого заполнителя могут влиять на количество воды, необходимое для сохранения работоспособности бетона. Имейте в виду, что чрезмерное количество воды может ослабить бетон из-за увеличения процента оставшейся капиллярной структуры, поскольку избыток воды попадает на поверхность в виде стекающей воды, а затем испаряется. На фотографиях ниже показаны заполнители, которые обычно хранятся на бетонных заводах.
1½-дюймовый гравий
¾-дюймовый гравий
Ракель
Легкий
03
0 песок
Максимальный размер заполнителя должен составлять менее одной пятой от самого узкого размера между сторонами форм, одной трети глубины плит или трех четвертей минимального расстояния между арматурными стержнями.
Иногда рекомендуется использовать заполнитель максимально возможного размера, чтобы минимизировать необходимое количество цемента, а также уменьшить усадку бетона при высыхании. Недостатком использования крупного и крупного заполнителя является то, что он увеличивает вероятность разрыва связи между поверхностью заполнителя и окружающей цементной пастой, поскольку напряжения на границе раздела между двумя материалами выше, чем при использовании заполнителя меньшего размера. Это также уменьшает общую доступную площадь склеивания поверхностей.
Также важны характеристики жесткости / деформации заполнителя. Крайние различия в свойствах заполнителя и цементного теста приводят к высоким напряжениям, которые создают микротрещины, которые могут ослабить бетон.
Сортировка заполнителя
Хорошо сортированный заполнитель является результатом использования в смеси заполнителя разных размеров. Это помогает уменьшить количество цементного теста, необходимого для заполнения промежутков или пустот между отдельными частями заполнителя. Уменьшение процентного содержания цементного теста в смеси помогает уменьшить усадку и снижает теплоту гидратации, что может привести к растрескиванию бетона.Это также увеличивает его долговечность. Количество заполнителя, используемого в смеси, называется его плотностью упаковки. Хорошо сортированный заполнитель имеет лучшую плотность упаковки, чем заполнитель с зазором. Заполнитель с зазором не имеет кусков среднего размера, что затрудняет укладку бетона и увеличивает его стоимость, и оба этих фактора могут повлиять на конечный продукт.
Содержание влаги
Различные типы заполнителей имеют разные уровни пористости; то есть они могут поглощать разное количество воды.Высокопористый камень влияет на бетон по-разному, в зависимости от того, является ли он водонасыщенным или сухим перед добавлением в смесь. Сухой камень впитает больше воды из смеси, что может сделать бетон более жестким и затруднить работу, что может проявляться в виде видимых проблем в готовом бетоне. При расчете количества воды, добавляемой в смесь, необходимо учитывать воду в пропитанном камне, иначе водное соотношение может быть слишком высоким, что приведет к ослаблению бетона.
Существует четыре уровня влажности:
- Сушка в печи (OD) означает, что вся влага удалена.
- Air-dry (AD) означает, что поверхностная влага удалена, а внутренние поры частично заполнены.
- Насыщенная сухая поверхность (SSD) означает, что поверхностная влага удалена, а все внутренние поры заполнены.
- Мокрый означает, что поры заполнены, а на поверхности есть пленка.
Из этих четырех состояний насыщенная и сухая поверхность считается лучшим состоянием влажности. При использовании SSD заполнитель находится в состоянии равновесия, поэтому заполнитель не будет поглощать цементное тесто и не отдавать воду в него.Однако получить такое состояние влажности бывает трудно.
Легкие заполнители
Завод по производству легких заполнителей
Легкие заполнители, как правило, создаются человеком и имеют высокую пористость. Глина, сланец и сланец расширяются при нагревании, как попкорн. Поскольку большинство из них пористые, они также абсорбируют влагу, что может повлиять на количество воды, используемой в смеси. На некоторых типах в процессе плавления образуется покрытие, которое снижает их впитывающие свойства; однако, если это покрытие будет повреждено во время работы, заполнитель в целом восстановит часть своей способности поглощать воду.В зависимости от процентного содержания заполнителя, повредившего покрытие, это состояние может повлиять на качество бетона, если такое изменение не допускается при проектировании смеси.
Тяжеловесные заполнители
Тяжеловесные заполнители обычно используются в зданиях, требующих защиты от излучения, и не представляют интереса для большинства инспекторов.
Отходы как совокупность
Было рассмотрено множество идей по переработке отходов, а некоторые были опробованы.Инспекторы могут столкнуться с проблемами в бетоне, вызванными неправильной заменой заполнителя материалами.
Некоторые из этих отходов включают:
- строительный мусор;
- промышленные отходы; и
- хвостохранилища.
Щелочно-агрегатная реакция (AAR)
Бетон, поврежденный ASR
Некоторые типы заполнителей плохо реагируют с щелочами из источников в бетоне или из других источников, таких как антиобледенительные соли, грунтовые воды или морская вода.Если агрегаты содержат большой процент кремнезема, реакция называется щелочно-кремнеземной реакцией (ASR). Если агрегат состоит из доломитовых карбонатных пород, это называется щелочно-карбонатной реакцией (АКР).
Во время ASR, который является наиболее распространенной из двух проблем, растворимый диоксид кремния в совокупности реагирует с растворимой щелочью с образованием щелочного силикагеля. Когда этот гель впитывает влагу, он расширяется, вызывая растрескивание бетона. После укладки бетона может пройти некоторое время, прежде чем появится ASR.Трещины в контрольных швах, усадочные трещины или микротрещины на поверхности, увеличивающиеся при замерзании, могут позволить влаге проникнуть в бетон и впитаться гелем. Некоторые агрегаты нереактивны, а другие реактивны в разной степени.
Не существует экономически эффективного метода смягчения последствий повреждения бетона в результате AAR. Исправление требует удаления и замены.
Другие проблемы, связанные с заполнителями
- Некоторые типы камня, используемые для заполнителей, могут вызывать проблемы из-за расширения и сжатия во время циклов замораживания-оттаивания из-за содержания влаги.
- Заполнители могут различаться по износостойкости.
- Примеси заполнителя, состоящие из мелких твердых частиц, могут мешать сцеплению поверхности между цементом и крупным заполнителем.
- Растворимые агрегатные примеси могут химически влиять на щелочные цементные пасты и влиять на время схватывания.
- Агрегат из карьеров в прибрежных районах следует очищать, чтобы избежать загрязнения солью, которое может химически повлиять на бетон или разрушить закладную сталь.
Инспекторы не всегда могут отнести проблемы, которые они наблюдают, к конкретным составляющим материалам. Потратив время на изучение типов сырья, используемого в их области, и типичных проблем, которые возникают в связи с этими материалами, инспекторы могут лучше понять серьезность различных дефектов, которые они обнаруживают, чтобы они могли дать соответствующие рекомендации.
************************
Эта статья является частью серии, чтобы помочь инспекторам InterNACHI понять характеристики и визуально проверить конкретный.
Испытание на моделирование динамического давления воды в асфальтобетоне
Abstract : Моделирование динамического давления воды — один из основных методов, который следует изучить для повышения устойчивости асфальтовой смеси к повреждениям, наносимым водой. В этом исследовании была разработана испытательная система, которая создает динамическое давление воды в пустотах асфальтобетона с помощью сжатого воздуха.Цилиндрический образец асфальтобетона, который имел пространство на дне и был покрыт эпоксидным клеем сбоку, был изготовлен для ориентации потока воды через пустоты асфальтобетона в установленное пространство. Таким образом, сформировался ориентированный режим водной эрозии. Анализ методом конечных элементов показал, что дренаж может снизить поровое давление в образце по его глубине, что указывает на то, что поровое давление было выше в полужестком асфальтовом покрытии с основанием, чем в асфальтовом покрытии с дренажным основанием. Результаты испытаний были следующими.Во-первых, прочность образца на раскалывание постепенно снижалась из-за водной эрозии. Во-вторых, улетучился порошок, произошло разрушение при сдвиге, и асфальтовая пленка оторвалась от поврежденной поверхности во время ориентированной эрозии на образец при 60 ℃, что указывает на значительное влияние динамического порового давления. И, наконец, в-третьих, асфальтобетонная смесь с пустотностью около 8% продемонстрировала минимальную устойчивость к повреждению водой. Эти явления показали, что метод может быть использован для оценки устойчивости асфальтобетона к повреждениям от воды.
Ключевые слова: дорожная техника асфальтовое покрытие динамическое давление воды ориентированная водная эрозия
1. ВведениеДинамическое давление воды и ее размывающий эффект напрямую связаны с нагрузкой на колеса. В настоящее время водостойкость асфальтовой смеси косвенно оценивается методом циклов замораживания-оттаивания или путем испытания асфальтовой смеси, погруженной в горячую воду [1-2] .Динамическое давление воды было смоделировано путем испытаний в условиях дорожного покрытия [3-6] . Гамбургский тест слежения за колесом [7] моделирует эффект сцепления воды и нагрузки на колесо, и считается, что вторая точка перегиба на кривой глубины колеи и числа проходов колеса подтверждает значительную связь воды с асфальтом сцепление бетона.
Однако указанные выше методы исследования имеют недостатки при моделировании динамического давления воды и режима эрозии асфальтобетона.Таким образом, в данном исследовании для испытания асфальтобетона был использован режим ориентированной водной эрозии на основе предложенной испытательной системы, которая создает динамическое давление воды сжатым воздухом.
2 Метод моделирования динамического давления воды и расчет режима эрозии асфальтобетона 2.1 Метод и принцип моделирования динамического давления водыМоделирование проводится согласно опубликованному методу [8] .Образец сначала погружают в воду, на поверхность которой оказывается давление воздуха. Давление воды равно давлению воздуха и изменяется при изменении давления воздуха. Чтобы применить динамическое давление воды, выполняется циклический управляемый процесс, который сначала пропускает сжатый воздух в камеру на 4 секунды, пока давление воздуха в ней не достигнет 0,7 МПа. Затем сжатый воздух выпускается из камеры на 1,5 с, пока давление воздуха не упадет до атмосферного. Наконец, воздух откачивается на 2.5 с, пока давление воздуха не станет -0,095 МПа. Один цикл, который длится 8 с, включает однократное чередование положительного и отрицательного давления воздуха.
В лаборатории асфальтобетонную смесь погружают в воду при атмосферном давлении, что часто приводит к образованию ненасыщенных пустот. Во-первых, давление воздуха увеличивается, так что остаточный воздух в пустотах асфальтовой смеси сжимается, заставляя воду течь в открытые пустоты, чтобы заполнить больше места. Затем к открытым пустотам прикладываются нормальные напряжения и напряжения сдвига, что способствует проникновению воды на поверхность раздела асфальта и заполнителя.Во-вторых, давление воздуха мгновенно падает до атмосферного, когда воздух в открытых пустотах расширяется и выходит за пределы открытых пустот, в результате чего вода попадает в открытые пустоты и теряется сила сцепления асфальтового камня. Наконец, когда вода вытекает из открытых пустот, применяется отрицательное давление, в результате чего остаточный воздух в закрытых пустотах расширяется и нарушает когезию асфальтового заполнителя. Повторение этих трех шагов заставляет воду течь в открытых пустотах без направления, что называется ненаправленной динамической водной эрозией.
2.2 Расчет режима направленной эрозииПри высоких нагрузках на колеса вода с поверхности дороги проникает в тротуары с направлением. Таким образом, это явление следует учитывать при моделировании. В соответствии с рисунком 1а запечатайте сторону цилиндрического образца высотой 135 мм и диаметром 150 мм эпикоте и прикрепите его к цилиндрической бутылке из нержавеющей стали, чтобы образовалось пространство под образцом. Эпикоте должен затвердеть и стать твердым перед тем, как образец будет погружен в воду.Когда на поверхность воды прикладывается давление воздуха, образец подвергается воздействию давления воды во всех направлениях, и режим уплотнения направляет поток воды через открытые пустоты внутри образца вниз в образованное пространство. Этот процесс называется режимом ориентированной эрозии. Когда давление достаточно высокое, образовавшееся пространство мгновенно заполняется водой.
Инжир.1 Режим ориентированной динамической эрозии порового давления, реализуемый образцом, запечатанным эпикотом |
До появления трещин в образце закрытые пустоты внутри образца не очищаются. После ориентированной эрозии из образца собирают цилиндрические стержни диаметром 100 мм для оценки их показателей прочности, если образец остается неповрежденным и неповрежденным. Затвердевший эпикот должен быть твердым и хрустящим при обычной температуре.
2.3 Изменение правил давления воды внутри образца при ориентированном режиме эрозииДля асфальтового покрытия с полужестким основанием просачивание воды через слои асфальтобетона не может стекать с поверхности основания; для асфальтового покрытия с дренажным основанием вода может стекать. Таким образом, режим ориентированной эрозии следует анализировать с дренажем и без него. Для ориентированной эрозии без дренажа насыщенный образец везде имеет поровое давление, равное приложенному давлению воздуха.Правило распределения порового давления для различных условий дренажа рассчитывается следующим образом.
Табл. 1 Физико-механические показатели асфальтобетона, рассчитанные методом FEM
Индекс образца асфальтобетона | Параметры, выбранные для анализа методом конечных элементов |
Модуль упругости (Па) | 1.2 × 10 8 |
Коэффициент Пуассона | 0,35 |
Плотность (кг / м 3 ) | 2 360 |
Коэффициент проницаемости (м / с) | 5,4 × 10 -3 |
Во время процесса динамической водной эрозии, когда давление воздуха достигает заданного значения и становится стабильным, давление на поверхность воды становится равномерным и передается водой на поверхность образца, что приводит к поровому давлению.Таким образом, нагрузка при анализе методом конечных элементов (МКЭ) упрощается за счет непосредственного приложения порового давления к краю образца. Это поровое давление должно быть равно давлению воздуха и изменяться вместе с ним. Параметры материала перечислены, как показано на рисунке 1. Циклическая нагрузка принята, как показано на рисунке 2. Если герметичная цилиндрическая сторона образца не определена, тогда программное обеспечение FEM предполагает, что поверхность не имеет дренажа. Однако нижняя торцевая поверхность имеет дренаж, поэтому поровое давление на ней всегда равно нулю.Для осесимметричного режима ось симметрии никогда не деформируется перпендикулярно оси. Вышеуказанная нагрузка и граничные условия показаны на рисунке 2.
Рис. 2 Осесимметричная модель, созданная для расчета порового давления. |
Табл.2 Циклическое поровое давление, устанавливаемое методом конечных элементов
Время (с) | 0 | 2 | 4 | 4,5 | 5 | 5,5 | 6,75 | 8 |
Давление (МПа) | 0 | 0,35 | 0,7 | 0,35 | 0 | 0 | -0.45 | -0,9 |
B на рисунке 2 означает, что на оси не допускается деформация, перпендикулярная оси симметрии. В правом нижнем углу рисунка 2 есть геометрические примечания для граничных ограничений. U 1 и U 3 отмечены «√» под ними, что означает, что геометрическая модель должна быть свободной в направлении x и z . U 2 не отмечен галочкой «√» под ним означает, что геометрическая модель ограничена в направлении y . θ 1 , θ 2 и θ 3 не отмечен «√» под ними означает, что вращение вокруг оси x, y и z ограничено. pp отмечен галочкой «√» под ним, что означает, что поровое давление на симметричной оси не ограничено.
Как показано кривой распределения порового давления на рисунке 3, абсолютное значение порового давления в образце уменьшается с увеличением глубины в режиме ориентированной эрозии с дренажем.Этот расчет показывает, что дорожное покрытие с полужестким основанием имеет более высокое поровое давление, чем покрытие с дренажным основанием.
Рис.3 Распределение порового давления вдоль оси образца, рассчитанное методом МКЭ. |
Цилиндрический образец высотой 135 мм и диаметром 150 мм, изготовленный с помощью вращательного компактора Superpave, используется в режиме ориентированной эрозии без дренажа, и после эрозии были собраны цилиндрические керны диаметром 100 мм и такой же высотой. Высота этих жил уменьшена вдвое для сплит-теста. Учитывая, что сторона цилиндрического образца герметизирована, открытые пустоты сбоку не размываются, поэтому эрозия не так значительна, как при неориентированной эрозии.
Образец, кондиционированный ориентированной эрозией без дренажа в течение 12 часов, демонстрирует потерю прочности на 15%, аналогичную таковой в условиях неориентированной эрозии в течение 3 часов [8] . Другими словами, ориентированная эрозия оказывает значительно меньшее влияние на прочность образца на раскалывание, чем неориентированная эрозия. Образец, обработанный ориентированной эрозией без дренирования в течение 6 ч, приобретает повышенную прочность, что можно объяснить консолидацией трехмерного, равно ограниченного давления.Как показано на рисунке 4, потеря прочности образца на двух концах практически одинакова.
Рис.4 Зависимость между остаточным сопротивлением раскалыванию и временем ориентированной эрозии |
На рис. 5 показан ленточный порошок, который выходит из образца AC-13C, смешанного с гранитным заполнителем и A-70 из-за ориентированной эрозии.Затем порошок оседает в пространстве, образованном контейнером из нержавеющей стали. Это удаление порошка, которое происходит после эрозии при обычной температуре, указывает на то, что эрозия влияет на асфальтовое вяжущее, вызывая смывание порошка с асфальта.
Рис.5 Порошок для связки в построенном пространстве из образца гранитного заполнителя асфальтобетона после ориентированной эрозии динамическим поровым давлением |
Метод создания давления воды с помощью давления воздуха имеет ограниченную рабочую частоту, которая зависит от эффективности воздушного компрессора и вакуумного насоса. Разрушение образца асфальтобетона также требует много времени. Следовательно, испытание для определения правила повреждения необходимо проводить при высоких температурах.
3.3.1 Условия испытанийОдин цикл длится 5 с, в течение которых в течение первых 4 с создается положительное давление воздуха, а в оставшиеся 1 с сбрасывается давление воздуха для получения атмосферного давления.Вакуумный насос не используется, поскольку абсолютное значение отрицательного давления невелико и мало влияет на образец. Поскольку ориентированная эрозия медленно снижает прочность образца, температуру повышают для ускорения испытания. Образец погружают в воду при 30 ℃ и нагревают в течение 3 часов, пока температура не станет постоянной 60 ℃. Впоследствии начинается эрозия. В этих условиях испытывают образец AC-13, смешанный с гранитным заполнителем и A-70, имеющий коэффициент пустотности примерно 8%.
3.3.2 Тестовые явленияНа рисунках 6 (a) и 6 (b) показано явление растрескивания образца под действием силы сдвига после ориентированной эрозии в течение 9 и 6 часов при 60 ℃ соответственно. Вылет порошка и отслоение асфальта часто происходит на краях или острых углах заполнителей. Таким образом, некоторые заполнители демонстрируют большую площадь отслаивания на торцевых поверхностях, что может быть связано с растрескиванием заполнителя во время вращательного уплотнения. Обнаружено, что отслаивание асфальта происходит на поверхности с трещинами от сдвига.Хотя два конца образца имеют прямой контакт с водой, отслоения асфальта не происходит, как показано на рисунке 7.
Рис. 6 Разрушение при сдвиге после ориентированной эрозии динамическим поровым давлением при 60 ℃ |
Инжир.7 Состояние асфальтового покрытия изломанной поверхности и косвенно эродированной поверхности образца |
Для получения образца с широким диапазоном пустотности AC13, AK13A, AM13 и AC13 с контролируемой сегрегацией уплотняют на разную продолжительность.Испытание на разделение проводится с использованием этих образцов после 3 часов неориентированной водной эрозии при 25 ℃, и результаты показаны на рисунке 8. Асфальтовая смесь с пустотностью примерно 8% демонстрирует минимальный коэффициент прочности на растяжение (TSR). и плохая водостойкость. Асфальтовая смесь с долей пустот от 3% до 5% не проницаема, тогда как асфальтовая смесь с долей пустот выше 12% обладает дренажной способностью. Во время испытания выполняется неориентированная эрозия, а не ориентированная.Результаты испытаний согласуются с предыдущими в [9].
Рис. 8 Взаимосвязь между пустотностью асфальтовой смеси и TSR при динамическом давлении воды |
Учитывая взаимосвязь между нагрузкой на колесо, поровым давлением и водной эрозией при повреждении дорожного покрытия водой, разработана система, которая создает динамическое давление воды за счет давления воздуха.Режим ориентированной динамической водной эрозии используется для проведения испытания на основе анализа состояния асфальтового покрытия. Сделаны следующие выводы. Во-первых, прочность образца на раскалывание постепенно уменьшается из-за водной эрозии. Во-вторых, порошок выходит, происходит разрушение при сдвиге и асфальтовая пленка срывается с поврежденной поверхности во время ориентированной эрозии образца при 60 ℃, что свидетельствует о значительном влиянии динамического порового давления. И, наконец, в-третьих, асфальтобетонная смесь с пустотностью около 8% демонстрирует минимальную устойчивость к повреждению водой.Эти результаты показывают, что этот метод можно использовать для оценки водостойкости асфальтобетона.
Имитационное испытание все еще требует модификации, чтобы увеличить частоту эрозии. Имитационное испытание включает в себя высокое кратковременное непостоянное давление воды, так что образец быстро насыщается водой. Механизм насыщения пустот в дорожной одежде под действием колесных нагрузок требует дальнейшего изучения.
»Промышленные тротуары
Обратите внимание — промышленные приводы бывают любой длины, ширины, условий нагрузки и использования, как и для грузовых автомобилей и автовокзалов.В этой главе рассматриваются только основы их правильных принципов проектирования и несколько особых соображений. Как промышленные приводы, так и терминалы обычно включают тяжелую нагрузку на тротуар; поэтому очень важно, чтобы они были правильно спроектированы. Асфальтобетон хорошо подходит для этого типа применения, потому что он обеспечивает универсальность различных конструкций дорожного покрытия при сохранении максимальной прочности дорожного покрытия.
Промышленные подъездные пути и зоны стоянки грузовиков должны быть правильно спроектированы и построены, чтобы они могли функционировать надлежащим образом.Эта страница содержит общие рекомендации по строительству промышленных подъездных путей и стоянок для грузовиков / автобусов. Из-за больших нагрузок, связанных с транспортными средствами, которые используют эти средства, надлежащее обследование площадки, испытания материалов и проектирование дорожного покрытия должны выполняться лицензированным инженером. Даже с учетом сложности этих покрытий асфальтобетон может обеспечить универсальность и прочность, необходимые для обеспечения длительного срока службы.
В зависимости от использования стоянок для грузовиков или автобусов, надлежащий дизайн и конструкция позволят смягчить большинство разрушений покрытия на всю глубину.Основная причина разрушения дорожного покрытия на стоянках — утечка топлива. Асфальтобетон — продукт на нефтяной основе; когда другие продукты на нефтяной основе проливаются на асфальтобетон, асфальтобетон размягчается и теряет прочность. Чтобы предотвратить повреждение от этих разливов, место для стоянки должно быть защищено стойким к растворителям герметизирующим слоем. Это покрытие следует наносить не менее чем через 30 дней после укладки, а лучше через 60-90 дней после укладки. Это позволит асфальтобетону «застыть» и затвердеть.
Следующая информация может быть использована в процессе проектирования и строительства дорожного покрытия.
Особые соображения
Хотя расчетная диаграмма в этой главе предлагает проектировщику дорожного покрытия альтернативу между асфальтобетоном и щебнем для части основания, многослойное асфальтобетонное покрытие все же рекомендуется для обоих оснований из-за экстремальных условий нагрузки на дорожное покрытие которые обычно существуют на промышленных проездах и на стоянках для автобусов и грузовиков.Для этих типов дорожного покрытия асфальтобетонные смеси типа BM-25D и IM-19D или E Департамента транспорта Вирджинии рекомендуются для всех слоев дорожного покрытия (за исключением поверхностных слоев) из-за их превосходной прочности и устойчивости к колееобразованию. В дополнение к этому компания VDOT разработала специальные высокопрочные смеси для использования в условиях тяжелых нагрузок, таких как грузовые терминалы, промышленные приводы, автобусные полосы и перекрестки.
За исключением неправильной конструкции, утечка топлива является наиболее частой причиной разрушения и ухудшения состояния дорожного покрытия, связанного с участками парковки и разгрузки грузовиков и автобусов.Поскольку асфальтобетон содержит асфальтобетон, нефтепродукты, бензин, дизельное топливо и смазочные масла, пролитые на тротуар, могут размягчить асфальт. Поэтому настоятельно рекомендуется заделывать эти тротуары эмульсией каменноугольной смолы, чтобы предотвратить проникновение этих растворителей. Однако заявки не следует подавать в течение как минимум 30 дней, предпочтительно 60-90 дней, после укладки дорожного покрытия. Это позволит испариться всем содержащимся в асфальтобетоне растворителям.
Как и в случае планирования всех типов дорожных сооружений, абсолютно необходимо, чтобы в эти объекты были встроены максимальные средства безопасности. Перекрестки под прямым углом обеспечивают лучшую видимость во всех направлениях для водителя, а также сокращают расстояние перехода. Прокладка подземной проводки для электрических и телефонных коммуникаций желательна из соображений безопасности и эстетики.
Рекомендации по проектированию
Двумя наиболее важными факторами при проектировании дорожного покрытия являются движение транспорта и дренаж.Если какой-либо из них не будет должным образом учтен при проектировании дорожного покрытия, конструкция дорожного покрытия будет либо чрезмерно спроектирована (и деньги будут потрачены впустую), либо недостаточно спроектированы (что приведет к преждевременному и постоянному обслуживанию).
Толщина покрытия, указанная в данном руководстве, является минимальной толщиной в уплотненном состоянии. Любое уменьшение значений толщины покрытия, указанных для основания или поверхности, может привести к серьезному разрушению покрытия и / или сокращению срока его службы.
Анализ дорожного движения
Все асфальтовые покрытия должны быть спроектированы с использованием надлежащих данных о нагрузках для обеспечения надлежащих характеристик покрытия.Категория «Промышленные тротуары» охватывает широкий спектр типов покрытия и погрузки — от терминалов для тяжелых промышленных грузовиков до доков для разгрузки контейнеров. Уровни движения и нагрузки на дорожное покрытие будут зависеть от типа объекта и должны быть точно учтены в процессе проектирования дорожного покрытия.
ВНИМАНИЕ: Влияние движения грузовиков на срок службы дорожного покрытия может быть значительным. Результаты испытаний показали, что один полностью загруженный грузовик массой 80 000 фунтов может вызвать износ дорожного покрытия, эквивалентный 9600 автомобилям. Хотя эти результаты испытаний могут лишь приблизительно оценить износ дорожного покрытия, вызванный тяжелыми транспортными средствами, они действительно показывают, почему оценка типа, веса и количества транспортных средств важна для определения правильной конструкции асфальтового покрытия.
В данном Руководстве по проектированию промышленные проезды и парковочные зоны терминалов рассматриваются как мощные тротуары с движением, как настоящим, так и будущим, в первую очередь для тяжелых грузовиков и автобусов. Любое отклонение от этого предположения потребует корректировки конструкции покрытия, показанной в таблице.
Владелец промышленного объекта должен знать, сколько тяжелых грузовиков и какого типа будут использовать объект. Эта информация в сочетании с информацией о прочности почвы определит окончательную толщину дорожного покрытия.
Тот же подход можно использовать с автобусными остановками. Хотя они не весят столько, сколько 5-осный грузовик, они создают большую нагрузку на дорожное покрытие. Зная вес автобуса, количество автобусов, которые будут использовать объект ежедневно, еженедельно или ежемесячно, а также прочность почвы, можно спроектировать структуру дорожного покрытия.
Слишком часто дорожное покрытие проектируется с учетом движения грузовиков с определенной скоростью, но именно медленные повороты или неподвижность приводят к сбоям, если они не учтены должным образом при выборе асфальтовой смеси и проектировании дорожного покрытия.
Дренаж
Адекватный дренаж тротуара имеет большое значение при проектировании любого покрытия. Если земляное полотно под дорожным покрытием становится насыщенным, оно теряет прочность и устойчивость и делает вышележащую структуру дорожного покрытия подверженной разрушению под воздействием приложенных нагрузок.Следует учитывать как поверхностный, так и подземный дренаж. Весь дренаж должен быть тщательно спроектирован и должен быть установлен в процессе строительства как можно раньше.
Тротуар также должен быть сконструирован таким образом, чтобы не допустить скопления воды на краю тротуара, и должны быть приняты меры для перехвата всех грунтовых вод из источников, плоскостей фильтрации и ручьев. При использовании секции бордюра и желоба должны быть настроены на истинную линию и уклон. Особого внимания требует заболоченная территория, которую следует решать на этапе планирования.
Дренаж влияет на характеристики дорожного покрытия, когда материалы земляного полотна и материалы слоя дорожной одежды пропитываются и теряют прочность. Вода, которая попадает на поверхность тротуара, должна сливаться в бордюры, водосточные системы или канавы. Вода, проникающая в тротуар с поверхности; проникновение по краям дороги или подъем из-под тротуара не должно снижать общую прочность.
Для учета отвода поверхностных вод важно, чтобы дорога была построена с гребнем или поперечным уклоном.Как правило, в центре дороги размещается венок, и тротуар имеет уклон 2% в каждом направлении. Иногда тротуар может быть очень приподнятым, если одна сторона дороги выше другой. В любом случае тротуар должен иметь уклон, чтобы вода не собиралась на поверхность.
Что касается подземных вод, подход к решению зависит от проекта. В некоторых случаях для улавливания воды, которая может протекать под тротуаром, размещаются дренажные системы. Затем этой воде позволяют вытечь в канаву или слить в систему ливневой канализации.Во многих случаях, когда земляное полотно становится слабее из-за воды, земляное полотно стабилизируется связующим, удаляется и заменяется более прочным материалом, покрывается стабилизирующей тканью перед укладкой следующего слоя дорожного покрытия или следующие слои дорожного покрытия становятся толще.
Опора грунта
Способность естественного грунта земляного полотна выдерживать нагрузки, передаваемые через дорожное покрытие, является одним из наиболее важных факторов при определении толщины дорожного покрытия. Перед строительством или разработкой планов проекта земляное полотно должно быть отобрано и испытано на прочность.Основным параметром прочности грунтового основания является коэффициент несущей способности (CBR) для Калифорнии, который определяет, насколько хорошо грунт может выдерживать транспортные нагрузки. Тест CBR обеспечивает простой и надежный показатель несущей способности грунта: чем ниже значение, тем меньше прочность грунта. Он широко используется многими департаментами автомобильных дорог, а также другими государственными учреждениями как на уровне штата, так и на федеральном уровне.
В целом, все проекты должны быть отобраны и протестированы квалифицированной инженерной фирмой.Количество образцов будет зависеть от длины дороги и изменения типа почвы. Рекомендуемые скорости тестирования можно найти в руководствах по тестированию VDOT.
Однако проектировщик должен знать об ограничениях использования усредненных значений CBR при определении данных поддержки грунта. До одной трети образцов почвы, используемых для расчета среднего CBR, будут ниже этого значения.
Пример:
Девять выборок CBR взяты на предлагаемой улице в Ричмонде, и их значения следующие:
Среднее значение CBR для этих выборок равно 10.Однако образцы № 3, 7 и 8 были значительно ниже 10. Если дорожное покрытие спроектировано на основе среднего значения CBR 10, можно ожидать разрушения покрытия в областях испытательных образцов 3, 7 и 8.
В данном руководстве рекомендуется расчетное значение CBR, равное двум третям (2/3) фактического среднего значения CBR, которое должно использоваться при выборе толщины дорожного покрытия (метод расчета Vaswani, используемый Министерством транспорта Вирджинии, также использует расчетное значение двух третей (2/3) среднего значения CBR). Это поможет обеспечить соответствие конструкции дорожного покрытия.
Как правило, расчетное значение CBR, равное 3 или меньше, указывает на плохую почву. Грунты с этим значением следует удалить на глубину от 12 до 18 дюймов и заменить более прочным материалом или стабилизировать такими добавками, как известь или цемент, на глубину от 6 до 12 дюймов.
Стандартный метод испытаний ASTM D 1883
Подготовка земляного полотна
Поскольку земляное полотно должно служить как рабочей площадкой для поддержки строительного оборудования, так и фундаментом для конструкции дорожного покрытия, очень важно следить за тем, чтобы оно было должным образом уплотнено и отсортировано .Необходимы лабораторные испытания для оценки характеристик несущей способности грунта земляного полотна. Данные испытаний для данной области можно получить в местном офисе Министерства транспорта штата Вирджиния.
Все подземные коммуникации должны быть защищены или перемещены до сортировки.
Весь верхний слой почвы должен быть удален, а низкокачественная почва должна быть улучшена путем добавления асфальта или других подходящих добавок, таких как известь или гранулированные материалы.
На площадях, которые будут вымощены, должны быть удалены все камни, мусор и растительность.Планирование и уплотнение участка следует выполнять таким образом, чтобы предотвратить просадочные участки или перекачку почвы. Земляное полотно следует уплотнить до однородной минимальной плотности 95% от максимальной теоретической плотности.
Если будет обнаружено слабое место, материал следует удалить и заменить либо шести дюймовым (6 дюймов) уплотненным щебнем, либо трехдюймовым (3 дюйма) уплотненным асфальтобетоном. В случае очень плохого земляного полотна может потребоваться удалить верхнюю часть земляного полотна и заменить ее выбранным материалом.По завершении уклонение земляного полотна не должно отклоняться от требуемого уклона и поперечного сечения более чем на полдюйма (1/2 дюйма) на десять футов (10 футов).
Конструкция основания (асфальт)
Перед укладкой асфальтобетонного основания земляное полотно должно быть выровнено в соответствии с установленными требованиями, должным образом утрамбовано и устранены все недостатки. Асфальтобетонное основание следует укладывать непосредственно на подготовленное земляное полотно одним или несколькими подъемами, разложить и утрамбовать до толщины покрытия, указанной на планах или установленной владельцем.Уплотнение асфальтобетонных смесей — одна из важнейших строительных операций, обеспечивающих надлежащие характеристики готового покрытия, независимо от толщины укладываемого слоя. Вот почему так важно иметь должным образом подготовленное земляное полотно, чтобы уплотнить перекрывающее покрытие. Асфальтобетон должен соответствовать спецификациям Министерства транспорта штата Вирджиния для указанного типа смеси.
Конструкция основания (совокупность)
Земляное полотно должно быть выровнено по требуемым контурам и уклону таким образом, чтобы обеспечить твердую, однородную, хорошо уплотненную поверхность.Все исправления недостатков земляного полотна и дренажные работы должны быть выполнены до начала строительства агрегатного основания.
Основание из щебеночного заполнителя должно состоять из одного или нескольких слоев, укладываемых непосредственно на подготовленное земляное полотно; распределить и утрамбовать до однородной толщины и плотности в соответствии с требованиями плана или установленными владельцем. Абсолютная минимальная толщина измельченного заполнителя составляет шесть дюймов (6 дюймов). Весь измельченный заполнитель должен быть одобрен Министерством транспорта штата Вирджиния и подходить для этого типа применения.
Tack Coat
Перед нанесением следующих друг за другом слоев дорожного покрытия предыдущий слой следует очистить и, при необходимости, нанести клейкий слой из разбавленного эмульгированного асфальта. Если предыдущий слой был свежим и тщательно очищен, липкое покрытие может быть удалено.
Асфальтовое покрытие
Материалом для поверхностного слоя должен быть асфальтобетон, уложенный в один или несколько подъемников до истинной линии и уклона, как показано на планах или задано владельцем. Асфальтобетон должен соответствовать спецификациям Министерства транспорта штата Вирджиния для выбранной смеси.Поверхность асфальта не должна отличаться от установленного уровня более чем на четверть дюйма (1/4 дюйма) на десять футов (10 футов) при измерении в любом направлении. Любые неровности на поверхности дорожного покрытия следует устранять непосредственно за асфальтоукладчиком. Прокатывание и уплотнение следует начинать, как только асфальтобетон может быть уплотнен без смещения, и продолжать до полного уплотнения и исчезновения всех следов катков.
Бордюр и желоб
Предназначен для обеспечения дренажа проезжей части, бордюра и желоб также очерчивают край проезжей части.Ширина желоба варьируется от одного (1 фута) до двух (2 футов) фута, при этом наиболее распространена ширина в полторы (11/2 фута) фута. Высота вертикальных бордюров составляет от пяти (5 дюймов) до восьми (8 дюймов) дюймов, при этом предпочтительны бордюры высотой шесть (6 дюймов).
Одна из наиболее распространенных ошибок при проектировании дорожного покрытия — это не указание соответствующих классов, чтобы вода не скапливалась на дорожном покрытии. У многих парковок и промышленных проездов высота тротуара ниже уровня бордюра и желоба, в результате чего тротуар переносит сток.Поскольку вода — главный враг любого покрытия, эти «сухие бордюры» приведут к ухудшению характеристик покрытия и / или сокращению срока его службы.
Структура дорожного покрытия
Структура дорожного покрытия и используемые материалы изменятся в зависимости от прочности земляного полотна и подхода к конструкции. В некоторых проектах будет использоваться асфальт на всю глубину (т. Е. Асфальт, укладываемый непосредственно на уплотненное земляное полотно), а в других будет использоваться основа из заполнителя, размещенная на уплотненном земляном полотне. Основание из заполнителя будет покрыто несколькими слоями асфальта.В таблице ниже предлагаются минимальные конструкции покрытия. Каждый слой — это уплотненная толщина. Ни в коем случае нельзя использовать менее 6 дюймов подстилающего слоя заполнителя.
Таблица 1 — Асфальтовое покрытие на всю глубину
Таблица 2 — Асфальт с заполненным основанием покрытия
Примечания:
- Расчетный CBR определяется как 2/3 значения CBR, пропитанного пропиткой .
- Спецификации VDOT для SM-9.5 и BM-25.0 можно найти в Разделе 211 Справочника спецификаций VDOT, Road and Bridges.
- Спецификации VDOT для 21B можно найти в разделе 208 Книги спецификаций VDOT, Road and Bridges.
- (1) Из-за больших нагрузок на поверхность рекомендуется более прочное асфальтовое связующее. В этих приложениях обычно используется PG 64E-22, отвечающий спецификациям VDOT, изложенным в Разделе 211 Книги спецификаций дорог и мостов VDOT 2016. Учитывая характер PG 64E-22, бригаде по укладке дорожного покрытия не следует выполнять практически никакой ручной работы. Этот материал лучше всего подходит для открытых проходов асфальтоукладчиком.Если нужна ручная работа, то следует использовать PG 64H-22. Проконсультируйтесь с вашим местным подрядчиком по укладке дорожных покрытий за помощью в определении объема ручной работы.
- (2) Из-за больших нагрузок на дорожное покрытие рекомендуется более прочное асфальтовое вяжущее. В этих приложениях обычно используется PG 64H-22 или эквивалент, который соответствует спецификациям VDOT, изложенным в Разделе 211 Книги спецификаций дорог и мостов VDOT 2016.
Рекомендации по техническому обслуживанию в будущем
Со временем разрушение покрытия может произойти из-за оседания или ослабления грунта или совокупных слоев основания.Это приведет к локальным сбоям или выбоинам. Чтобы устранить эти разрушения, необходимо вырезать пораженный участок и убрать материал дорожного покрытия до земляного полотна. Материал земляного полотна, возможно, потребуется удалить и заменить или просто повторно уплотнить. Наконец, удаленный материал дорожного покрытия следует заменить новым асфальтобетоном или постоянным материалом для ремонта асфальта.
По мере старения асфальта будут появляться усадочные трещины. Отдельные поперечные и продольные трещины должны быть заделаны материалом на основе асфальта, чтобы уменьшить количество воды, проникающей в нижележащие слои дорожного покрытия.Если растрескивание обширное, то на тротуар можно нанести новую поверхность переменного тока или отшлифовать и заменить на новую поверхность переменного тока. Накладку можно выполнять на участках без бордюра и желоба. Для участков с бордюрами и желобами может потребоваться фрезерование для поддержания дренажа с поверхности. Хотя можно выполнить фрезерование кромок, обычно шириной от 4 до 6 футов по краю тротуара, рекомендуется полное фрезерование тротуара для сохранения надлежащего поперечного уклона.
Ссылки
- Технические характеристики дорог и мостов VDOT 2016
- Специальные положения VDOT к техническим характеристикам дорог и мостов 2016 г.
- Руководство по проектированию дорожных покрытий VAA
Ссылки по теме
Определение битума
Что такое битум?
Битум, также известный в США как асфальт, представляет собой вещество, получаемое путем перегонки сырой нефти, которое известно своими водонепроницаемыми и адгезионными свойствами.При производстве битума путем дистилляции удаляются более легкие компоненты сырой нефти, такие как бензин и дизельное топливо, оставляя «более тяжелый» битум позади. Производитель часто несколько раз дорабатывает его, чтобы улучшить сорт.
Битум также может встречаться в природе: отложения природного битума образуются на дне древних озер, где доисторические организмы с тех пор разложились и подвергались воздействию тепла и давления.
Ключевые выводы
- Битум, вещество, известное своими гидроизоляционными и адгезионными свойствами, может происходить естественным путем или образовываться при перегонке сырой нефти.
- Он состоит из сложных углеводородов и содержит такие элементы, как кальций, железо, сера и водород.
- Цены на битум определяются состоянием мировой экономики, а также спросом и предложением на сырую нефть.
- Первые в мире фьючерсные контракты на битум дебютировали на Шанхайской фьючерсной бирже в октябре 2013 года.
Знакомство с битумом
Битум состоит из сложных углеводородов и содержит такие элементы, как кальций, железо, сера и кислород.Качество материала и простота производства зависят от источника и типа сырой нефти, из которой она получена.
Битум обычно используется в промышленности. Вещество впервые было использовано из-за его естественных адгезионных и гидроизоляционных свойств, помогающих связывать строительные материалы вместе, а также покрывать днища судов. Он также использовался в прошлом как лекарство.
Древние цивилизации торговали материалом, и Геродот, греческий историк V века до нашей эры, утверждал, что стены древнего Вавилона содержали битум.
В настоящее время этот материал чаще всего используют при мощении дорог. Большинство дорог в США сделаны из битума или из комбинации битума и заполнителей, таких как бетон. Ключевым преимуществом, помимо адгезионных и гидроизоляционных качеств, является то, что инженеры, заменяющие асфальтовые дороги, могут повторно использовать материал в других дорожных проектах. Битум также широко используется производителями при создании кровельной продукции.
При больших нагрузках битум может деформироваться необратимо, в зависимости от состава асфальтовой смеси, температуры окружающей среды и величины нагрузки на материал.Битум окисляется, что может сделать асфальт хрупким и привести к его растрескиванию.
Битум природного происхождения
Битум также используется для обозначения нефтеносных песков или частично уплотненного песчаника, содержащего природную смесь песка, глины и воды, насыщенную плотной и чрезвычайно вязкой формой нефти.
Битумные пески чрезвычайно распространены в Канаде, особенно в провинции Альберта, где рост цен на нефть сделал экономически выгодной добычу нефти из этих песков в больших масштабах.По оценкам Канадского института энергетических исследований (CERI), цена на сырую нефть должна составить 70,08 доллара за баррель, чтобы отдельный битумный рудник был прибыльным.
Цены на битум
Битум — это остаточный материал в процессе переработки сырой нефти в сжиженный нефтяной газ (СНГ) и бензин. Таким образом, цены на битум в значительной степени зависят от того же набора факторов, которые влияют на цены на нефть. К ним относятся спрос и предложение на нефть и геополитическая стабильность в нефтедобывающих регионах мира.
Дополнительным фактором, влияющим на цены на битум, является разница в цене между тяжелой и легкой нефтью. Битум образуется как побочный продукт в процессе перегонки тяжелой нефти; Таким образом, решение нефтепереработчиков о переработке тяжелой сырой нефти по сравнению с легкой имеет решающее значение для цен на битум.
Правительство США является крупнейшим покупателем асфальта, производимого в стране. Неудивительно, что это означает, что экономические условия оказывают вторичное влияние на цены на битум. Например, более высокий спрос на асфальт для дорог во время экономического бума может привести к росту цен.Поскольку Китай вложил значительные средства в расширение своей дорожной инфраструктуры, в последнее время он также сыграл важную роль в определении спроса и установлении цен на битум.
Фьючерсы на битум
Первые в мире фьючерсные контракты на битум дебютировали на Шанхайской фьючерсной бирже в октябре 2013 года и были нацелены на операторов нефтеперерабатывающих заводов, продавцов битума и конечных пользователей продукта.