Состав пенобетонных блоков — Портал о цементе и бетоне, строительстве из блоковПортал о цементе и бетоне, строительстве из блоков
Дата: 23.04.2014
Использование пенобетона для возведения сооружений разного назначения достаточно распространенное явление в современном строительстве. Профессиональные строители отмечают отличные качества строительного материала — пеноблока, его экологичность и экономность. В состав пеноблока входят пенообразующие добавки и цементный раствор. Возведенные из пенобетона дома сохраняют зимой тепло, а летом прохладу, отличаются высоким показателем звукоизоляции, огнестойкости, теплоизоляционными свойствами.
Состав пенобетона
Для приготовления прочного пенобетона необходимо тщательно подбирать все компоненты, входящие в его состав, правильно задавать объемный вес, режим влажности бетона и тепловлажностной обработки.
Производство пеноблоков выполняется согласно нормативам и технологиям с подбором составляющих по ГОСТ 25485-89.
Согласно ГОСТ 8736 входит песок с 75% содержанием кварца.
Портландемент выбирается по ГОСТ 10178.
Пенообразователь на сосновой канифоли должен соответствовать ГОСТ 191113. Если в основе пенообразователя находится костный клей, он должен быть выбран по ГОСТ 2067. ГОСТ 3252 применяют при выборе пенообразователя на мездровом клее. ГОСТ 2263 применяют для пенообразователя с техническим натром.
Воду проверяют на соответствие с ГОСТ 23732.
Составы пенобетонных смесей могут быть приготовлены с разным соотношением компонентов, что позволяет производить пеноблоки разных классов. От класса пенобетона зависит, где будут использованы готовые изделия. Пеноблоки используют для кладки термоизоляционных крыш, междуэтажных термо- и звукоизоляционных покрытий, внутренних перегородок и наружных стен.
Прочность бетона, минимальную усадку при высыхании, повышенную морозостойкость, сниженную теплопроводность получают путем введения комплексных добавок.
Формовой пенобетон
В пеногенераторе на воде взбивается пенообразователь. В смесителе песок и цемент смешиваются с пеной. Во время замеса при помощи компрессора увеличивается давление. Сметаноподобная паста из смесительного бункера по высоким давлением разливается в разделенные на секции формы.
Резанный пенобетон
Для получения бетона этого вида используют большую форму, а затем застывшую массу разрезают на блоки нужных размеров. Готовые блоки нужно выдержать до 25 дней и лишь только потом отправлять на продажу.
Состав пенобетона в отличии от газобетона не содержит известь и алюминиевую пудру, выполняющую роль порообразователя при изготовлении газоблоков. И тот и другой стройматериал обладает прекрасными качествами и успешно используется в строительстве.
Преимущества использования пенобетона:
- Экономия на отоплении составляет до 30% благодаря минимальной теплопроводности строительных пеноблоков.
- Закрыто-пористая структура сделала материал влагостойким и морозостойким.
- Высокий коэффициент огнестойкости позволяет противостоять открытому огню свыше 3 часов.
- Отличный показатель звукоизоляции делает дома комфортными и защищенными от внешних звуков.
- Для здания из пенобетона не нужно возводить фундаменты повышенной прочности, поскольку пенобетон имеет небольшой вес и здание из него дает меньшую нагрузку на фундамент.
- Экологически чистый материал без содержания химических вредных веществ.
- Быстрый и легкий монтаж возможен благодаря большим размерам блоков и их легкому весу.
- Идеальная поверхность блоков дает возможность сэкономить на связующем растворе.
Влияние пеноблоков на здоровье человека
Влияние пеноблоков на здоровье человекаЛегкий, долговечный, удобный в эксплуатации материал по экологическим свойствам сравним лишь с деревом, но все равно таит в себе опасности для здоровья человека.
Состав пеноблока
Для производства пеноблоков используется пена, состоящая из животного и растительного сырья, что означает ее полную безопасность для здоровья. При этом в состав бетона входят наполнители – гранит и пенобетономатериалы, которые относятся к магматическим породам и содержат радионуклиды в большом количестве. Именно ингредиенты для бетона могут представлять опасность для человека.
Осадочные породы (кварцевый песок, известняк, мел) содержат небольшую концентрацию естественных радионуклидов (ЕРН). Довольно большое количество ЕРН содержат глинистые материалы и непосредственно глина, но при этом они обладают хорошими адсорбционными свойствами. В состав качественных пеноблоков входит не гранитный камень, а кварцевый песок или известь, соответственно, концентрация естественных радионуклидов очень мала и не может нанести вред.
Качество песка, используемого для изготовления пеноблоков, должно соответствовать государственным стандартам. Ответственность за применение загрязненных ЕРН материалов полностью лежит на производителе. Для того, чтобы пеноблоки не нанесли здоровью вред, строительные материалы необходимо закупать у крупных производителей, которые свободно предоставляют потребителю сертификаты качества и сопроводительную документацию.
Чем опасны естественные радионуклиды?
Радионуклиды способны накапливаться в человеческом организме и облучать его изнутри. Излучение оказывает серьезное негативное влияние на репродуктивную и иммунную системы человека. Заболевания на раннем этапе не проявляются – мигрень и усталость это единственное, что может наблюдаться в начале облучения. В последствие радионуклиды провоцируют развитие таких патологий:
• тахикардия и аритмия, являющиеся симптомами инфаркта;
• вегетососудистая дистония, повышающая вероятность инфаркта миокарда или инсульта;
• проблемы с ЖКТ;
• цирроз печени.
Приобретая пеноблок, необходимо проверять качественную документацию. Если производитель отказывает покупателю в предоставлении сертификата на дешевую продукцию, стоит задуматься о причинах этого. Экономия на стройматериале способна сыграть злую шутку со здоровьем проживающих в новом доме людей.
Возврат к списку
Внимание! При копировании информационных материалов прямая ссылка на наш сайт обязательна!
Все тексты сайта охраняются законом — Об авторском праве от 09.
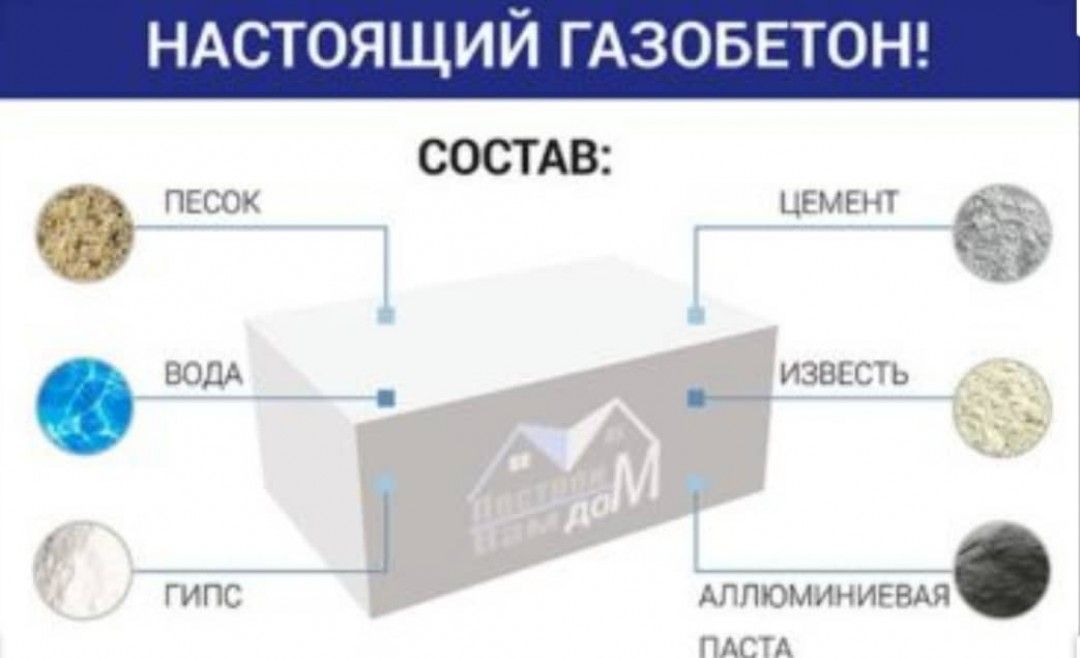
Применение пеноблока, состав, храние — СПО Облстрой
Наиболее часто пенобетон применяется в строительстве:
монолитно-каркасном,
сборном,
оболочечном.
- Пенобетонные блоки – самый дешевый и теплый стройматериал 21 в. Он отвечает нормативным требованиям стройматериалов по деформативности, прочности, морозостойкости. Благодаря легкости и правильности форм блоков достаточно просто выполняется кладка стен, и реализуются сложные архитектурные формы.
- Изменяя соотношение компонентов пенобетона, можно получить разные его типы относительно применения:
- для внутренних перегородок;
- для термоизоляции крыш;
- для термоизоляции трубопроводов;
- для наружных стен;
- для термовкладышей;
- для изоляции междуэтажных перекрытий.
Строительство из пеноблоков — отличное решение для тех, кто не рискует иметь дело с древесиной, склонной к гниению и возгоранию, или кирпичом и не обладающим высокими теплоизоляционными характеристиками.
При выборе пеноблока требуется соблюдать максимальную внимательность и осторожность. Ведь вы занимаетесь строительством жилища, в котором, вероятно, будут проживать разные поколения вашего семейства. На строительном рынке существует огромное количество недобросовестных поставщиков и фирм. В особенности, в самый разгар сезона строительства, когда они способны продать продукцию низкого качества, завлекая клиентов, в частности, низкой стоимостью. В этом случае пеноблоки не будут удовлетворять заранее предъявленным характеристикам. Важно не забывать о том, что хорошее настроение ввиду низкой стоимости продукции продлится очень недолго, а вот разочарование будет продолжительным.
Чтобы вы не купили пеноблок, который нельзя использовать для строительства несущих стен, мы попытаемся емко изложить некоторые важные моменты.
Нельзя покупать кота в мешке
Прежде чем вы заплатите за продукцию, следует ее хорошо осмотреть. У пеноблока должна быть правильная форма, ее нужно оценить с помощью рулетки, померяв диагонали блока. Они обязаны быть равными. Кроме того, вы можете прикоснуться к блоку, чтобы определить, не проминается ли он.
Цемент
Следует поинтересоваться,какой цемент применяется. Не следует бояться спрашивать документ, в котором будет представлена информация об уровне качества цемента. Такой документ выдают на все партии. В документе важно обратить свое внимание на дату, когда был отгружен цемент, и марку. Дело в том, что спустя месяц после приготовления он утрачивает 20-25 процентов своей прочности, то есть ПЦ 500 спустя месяц трансформируется в ПЦ 400. Для изготовления пеноблока высокого качества применяется цемент марки ПЦ 500 Д0. Оптимальным считается сухоложский либо горнозаводской цемент.
Отсев
При изготовлении применяется отсев. Отсев должен быть очень мелким (уровень крупности должен не превышать полтора миллиметра), кварцевым (оттенок желтый немного блестящий).
Соблюдение необходимых пропорций
Важно обратить внимание на тот факт, каким образом выполняется загрузка в смеситель цемента, воды и песка. Когда компоненты грузят ведрами, их пропорции в пенобетонной смеси могут отличаться в определенную сторону при любом из замесов. Это связано с тем, что нельзя на глаз гарантировать точные пропорции, т.е. будет существенно нарушено соотношение цемента и воды. Это приводит к нестабильности качества блоков. Чтобы получить пенобетонную смесь высокого качества, дозирование составляющих необходимо производить с помощью электронных весов и специальных дозаторов.
Хранение является важным фактором
От того, в каких условиях хранится блок после его распалубки, будет напрямую зависеть его надежность. Пеноблок должен быть не высохшим, а застывшим. Застывание является медленной химической реакцией, в ходе которой формируются довольно сложные соединения с водой. С этой целью его требуется обернуть стрей-пленкой, способной предохранить от стремительного испарения влажности. Если во время осмотра вам доведется увидеть, что блок имеет серый цвет, это означает, что его или изготовили три-четыре месяца назад, или он пребывал на протяжении двух-трех дней без пленки. Оптимальной является ситуация, когда в процесс «созревания» не вторгаются природные факторы, такие как ветер, солнечный свет либо дождь. По этой причине желательно, чтобы блок становился прочнее не на открытом воздухе, а в условиях склада.
Дата изготовления
Не стоит приобретать чересчур свежие блоки. Им необходимо постоять минимум неделю на складе. В противном случае имеется вероятность повреждения еще не успевшего набрать необходимую прочность блока в процессе транспортировки. В области каждого поддона необходимо наличие ярлыка, где представлена дата производства и характеристики блока. В кладку вы можете использовать пеноблок, который должен набрать прочность в течение хотя бы десяти суток. Полная прочность достигается за 4 недели.
Смазывание форм
Существуют изготовители, которые с целью смазывания форм пользуются отработанным маслом из находящегося поблизости автосервиса. Часто его отдают бесплатно. При этом блок будет темным. На характеристиках его прочности это не отражается, но когда вам придется штукатурить, по причине сформировавшейся пленки жира на блоке, штукатурка не станет липнуть к нему.
Качество
Уважающий себя и своего клиента производитель обязан располагать документами, способными подтвердить высокое качество продаваемого товара. Вы можете попросить протокол, в котором будут отражены лабораторные исследования, а кроме того копию аттестата, подтверждающего аккредитацию лаборатории, в которой проводились испытания.
Каталог пеноблока
Оставить заявку
Насколько плохо то, что у вас под розами?
Флорист Рита Фельдманн обеспокоена воздействием широко используемой цветочной пены на окружающую среду. Кредит: Джейсон Саут
«Вероятно, он не будет очень токсичным, но вы просто добавляете больше инертных материалов в водный поток, которые потенциально могут иметь побочные эффекты. Не потому, что они токсичны, но организмы могут съесть это вещество. »
Г-жа Фельдманн и растущее число флористов, собравшихся вокруг аккаунта Instagram @nofloralfoam, обеспокоены воздействием пены на здоровье и окружающую среду, которая ежегодно используется в огромных количествах, а затем быстро выбрасывается.
«Это повсюду. Вы идете в супермаркет, берете букет цветов, он внизу. На скачках, свадьбах все это пена», — сказала она.
«К сожалению, действительно очень трудно найти какое-либо научное исследование, которое либо развеет, либо подтвердит наши подозрения в отношении цветочной пены», — сказал Шейн Коннолли, флорист британской королевской семьи и организовавший мероприятие для герцога и герцогини Кембриджских в 2011 году. свадьба.
«Что мы знаем точно, так это то, что он не поддается биологическому разложению и что он содержит известные канцерогены. «
Сам материал называется фенолформальдегидной пеной, и это один из старейших видов пластика. Его получают путем взаимодействия фенола и формальдегида друг с другом с образованием пластика.
Затем добавляют воздух, чтобы превратить его в пену.
Эта пена обработана моющими средствами, чтобы придать ей уникальную способность впитывать воду.
Пена состоит из двух токсичных химикатов, но не обязательно вредна.
В готовом продукте почти не остается фенола или формальдегида. — менее 0.1 процент каждого химического вещества.
«Пена не особо токсична. Формальдегид используется в производстве, но в отличие от бытовой теплоизоляции, где есть большие куски, из которых потенциально может вытекать формальдегид, эти блоки пены обычно очень маленькие », — сказал доктор Масгрейв. вдыхать пыль, образующуюся при резке, — но это обычные меры предосторожности для любого пластика, сказал он.
Профессор Ян Рэй, химик из Мельбурнского университета, предположил, что пена может представлять опасность, если большие ее количества хранятся в холодильнике. запечатанный участок на долгое время.
«Но в паспорте безопасности материала (поставляемом флористам вместе с пеной) сказано, что его следует хранить в хорошо проветриваемом помещении. Я понюхал и не почувствовал запаха формальдегида, — сказал он.
Г-жа Фельдманн сказала, что потребители должны сами просить цветы без пены.
«Я делаю огромные воздушные инсталляции, и я просто вложил средства в простые части [обрамления] и повторно использовал их для свадеб. И я, наверное, сэкономил сотни килограммов пены.
«Конечно, есть некоторые дизайны, которые невозможно было бы сделать без него, но у нас были цветы до того, как появилась пена.”
Пенополиуретан — обзор
4) Изготовление изделий из многослойной полиуретановой пены
Пенополиуретан имеет простой процесс вспенивания, а полиуретановая смола обладает превосходными адгезионными свойствами. Поэтому при изготовлении с его помощью сэндвич-конструкций его смеси часто заливают в полость конструкции для непосредственного вспенивания. При изготовлении изделий с многослойной структурой этим методом механическая обработка пенопласта может быть сведена к минимуму. Более того, при заполнении изделий внутреннего каркаса пена не только заполняет всю полость изделий, но и прочно соединяется с каркасом, образуя прочную жесткую структуру.
В авиационной промышленности для уменьшения веса конструкции толщина покрытия многослойных конструкций обычно делается очень тонкой. При вспенивании пенополиуретана его внутреннее давление может составлять от 0,2 МПа до 0,3 МПа. Чтобы справиться с давлением, мы используем пресс-формы ограниченного использования. Это сохраняет неискаженную форму контура продукта в процессе вспенивания.
Ограниченная форма изготавливается из алюминиевого сплава, стали или других материалов, а ее структура определяется формой контура и внешними размерами продукта.Нагревание может осуществляться паром или электрическим нагревателем для непосредственного воздействия на стенку формы. Как вариант, мы можем нагреть форму в духовке. Независимо от того, какой метод используется, главное — нагревать равномерно, потому что качество пены во многом зависит от температуры нагрева.
На примере воздушного обтекателя мы сделаем простое введение и иллюстрацию процесса формирования многослойной конструкции.
В конструкции воздушного обтекателя его внешний слой состоит из полиэстера или другого полимера FRP, образованного при низком давлении, а в качестве его сердцевины выбран пенополиуретан.При изготовлении продукта в основном используются две процедуры: изготовление оболочки из стеклопластика; заполните полость между внутренней и внешней оболочкой пеной. Технологическое оборудование — это, в основном, мужская форма, внутренняя форма, оборудование для извлечения из формы и так далее. Подробное описание технологического процесса показано ниже.
Сначала мы наносим силиконовое масло или разделительный агент, например поливиниловый спирт, на форму. Во-вторых, мы наклеиваем внутреннюю оболочку обтекателя с помощью охватываемой формы, а внешнюю оболочку — с помощью охватывающей формы. Чтобы крышка легко приклеивалась, металлический каркас удерживает резиновую крышку (контур металлического каркаса хорошо совпадает с внутренней формой), на которую наклеивается стеклоткань определенной толщины.Затем мы снимаем каркас, помещаем его в матрицу вместе с резиновым покрытием и вулканизируем методом компрессионного формования. При изготовлении внутренней и внешней оболочки давление обычно составляет от 0,09 МПа до 0,35 МПа, температура составляет от 120 ° C до 170 ° C, точное состояние зависит от смолы.
Внутренняя и внешняя оболочки после изготовления все еще остаются на форме. Разделительный агент, контактировавший с резиновым покрытием, удаляется. Затем наносим фенолацеталь или полиуретановый клей на поверхность, которая была аккуратно отполирована наждачной бумагой.После сушки при комнатной температуре в течение от 20 до 30 минут мы выливаем указанную и равномерно перемешанную пену на внешнюю оболочку матрицы. Мы быстро закрываем охватываемую форму, имеющую внутреннюю оболочку (см. Рис. 7.14). Вся операция должна быть завершена в пределах от 3 до 5 минут. Смесь пены заливается в форму, которую следует предварительно нагреть от 35 ° C до 45 ° C, чтобы смесь была равномерно заполнена всей полостью между внутренней и внешней оболочками. Это можно наблюдать через отверстие в штампе.Примерно через 15-25 минут, когда пена выйдет из отверстия, мы закрываем отверстие. Затем нагреваем, чтобы полимер застыл. Условия отверждения должны определяться в зависимости от рецептуры пены, толщины заполняющих слоев, формы заготовки и методов нагрева. Обычное обстоятельство состоит в том, что температура повышается с 60 ° C до 80 ° C до 120-150 ° C постепенно в течение 4-6 часов. Наконец, он вынимается из формы после того, как остынет до температуры от 20 ° C до 40 ° C. При извлечении из формы мы должны прикладывать тянущее усилие равномерно по периферии, чтобы гарантировать целостность продукта.Для облегчения извлечения из формы на корпусе продукта обычно делается фланец, к которому может быть приложено усилие извлечения из формы.
После извлечения из формы мы разрезаем фланец и обрабатываем излишки дисковой пилой или ленточной пилой, а затем декорируем, чтобы получить продукт.
Рис 7.14. Принципиальная схема наполнения пенополиуретана трехслойным конструктивным воздушным обтекателем: 1-оболочка из стеклопластика; 2-пенопласт; 3-гнездовой слепок; 4-нагревательная камера; 5-мужская форма.
Зеленая альтернатива цветочной пене
Юлия ИсаеваGetty Images
Цветочная пена — зеленые блоки из губчатой пены, также известной как Oasis, — очень любима флористами за удобство.Но независимо от того, являетесь ли вы профессиональным флористом или просто отправляете букет для скорейшего выздоровления любимому человеку, задумывались ли вы когда-нибудь о влиянии цветочной пены на окружающую среду?
К сожалению, пена для цветов содержит столько же пластика, сколько 10 пластиковых пакетов для покупок, не поддается биологическому разложению, не подлежит переработке и токсична как для людей, так и для животных. Это такая проблема, что RHS запретит использование водопоглощающего блока во всех своих садах и садоводческих выставках, которые состоятся в 2021 году.
Элис Томлинсон, Getty Images
Что такое цветочная пена?
Цветочная пена была изобретена дизайнером В.Л. Смитерсом (основателем OASIS®) 60 лет назад. С тех пор это незаменимый инструмент в цветочном дизайне, который делает процесс расстановки цветов более простым, быстрым и творческим.
Это так полезно для цветоводов, потому что это источник воды (примечательно, что он выдерживает до 50-кратного веса в воде) и стабилизатор, благодаря которому ваш букет будет выглядеть свежим и энергичным на срок до 12 дней.
Более того, он легкий, прочный, его легко резать и формовать. Это упрощает транспортировку приспособлений к церкви / шатру / порогу целиком, экономя время, деньги и воду, плещущуюся по пути.
belchonockGetty Изображения
Почему цветочная пена вредна для окружающей среды?
Цветочная пена способствует растущему кризису пластиковых загрязнений. Благодаря мшистой текстуре, зеленому оттенку и тому факту, что он используется с цветами, его легко принять за натуральный продукт.
На самом деле, он сделан из синтетического пластика, не подлежащего переработке, и состоит из комбинации углеродной сажи, формальдегида и фенольной пены, которые все токсичны.
Несмотря на то, что цветочная пена крошится, она не растворяется полностью в воде и не разлагается на свалках или в почве. Вместо этого он распадается на все более мелкие микропластики. Для их полного превращения в природные элементы могут потребоваться тысячи лет, и они представляют реальную угрозу для окружающей среды, загрязняя нашу морскую жизнь и пищевые цепи.
«Цветочная пена использует микропластики и в настоящее время не подлежит вторичной переработке. Имея это в виду, мы пришли к решению запретить использование цветочной пены на выставках RHS с 2021 года и попросили цветочных дизайнеров на показах RHS в этом году испытать альтернативные продукты, где это возможно », — говорит Хелен Петтит, директор выставок RHS.
dottedhippoGetty Images
Как правильно утилизировать использованную пену для цветов?
Его трудно утилизировать с экологической точки зрения, и он может серьезно загрязнить компост, садовые отходы и воду, если его фрагменты окажутся в неправильном месте.Итак, вот что вам нужно знать о его утилизации:
- Поместите его вместе с мусором, отправленным на свалку.
- Не кладите его в компост или в сад.
- Воду, содержащую кусочки пены, нельзя выливать в раковины, туалеты или канализацию.
- Вылейте его через старую наволочку, ткань или кухонное полотенце, чтобы захватить как можно больше фрагментов пены. Поместите остатки в мусорную свалку и вылейте процеженную воду в ямку в саду.
Последний в настоящее время является наилучшей экологической практикой для безопасного удаления остатков воды от цветочной пены.Если вы вылейте его в раковину, унитаз или в канализацию, только процент микропластика будет улавливаться при обработке сточных вод. Остальные проходят через фильтр и остаются в воде, которая затем используется для удобрения сельскохозяйственных угодий. Или он загрязняет нашу морскую жизнь, достигая рек, ручьев и, в конечном итоге, океанов.
Getty Images
Какие альтернативы цветочной пене?
Вот несколько экологически чистых советов и советов…
- Используйте гальку, песок, гравий, глину, мрамор, древесную осину, плотный мох или даже фрукты для поддержки цветочных композиций.
- Подрезайте цветочные букеты и регулярно меняйте воду, чтобы продлить жизнь цветов.
- Используйте кензан или цветочную лягушку — металлические приспособления, которые помещаются в вазу или миску и закрепляют стебли металлическими иглами или направляют их в отверстия — винтажные приспособления доступны на Etsy.
- Податливые веточки также служат хорошей опорой для опоры цветов.
- Куриная проволока или металлические булавки отлично подходят для закрепления стеблей и служат в качестве поддерживающей решетки при размещении прямо в вазах или кашпо.
- Будьте осторожны с «биоразлагаемой» цветочной пеной, она не разлагается полностью и может просачивать в воду больше токсичных соединений, чем обычная цветочная пена.
M&S Flowers Spring
Коллекция Giant Scented Stocks
Коллекция Belle Rose Bouquet
Коллекция Luxury Tulips Posy
Понравилась статья? Подпишитесь на нашу рассылку новостей , чтобы получать больше подобных статей прямо на ваш почтовый ящик.
Этот контент создается и поддерживается третьей стороной и импортируется на эту страницу, чтобы помочь пользователям указать свои адреса электронной почты. Вы можете найти больше информации об этом и подобном контенте на сайте piano.io.
Преимущества цветочной пены
Цветочная пена действительно поможет создать красивую и профессиональную цветочную композицию. Его правильное использование может позволить вам создавать цветочные композиции, которые в противном случае было бы очень трудно поддерживать. Кроме того, цветочная пена продлевает жизнь вашим цветочным композициям, давая им надежный и стабильный источник воды. Здесь мы подробно рассмотрим, как использовать цветочную пену, что делает цветочная пена, и рассмотрим некоторые часто задаваемые вопросы относительно ее использования.
Проще говоря, пена для цветов — это плотный, легкий и пористый материал, которому можно придать практически любую форму.Он сохраняет свою форму во влажном состоянии и обеспечивает воду и поддержку ваших срезанных цветочных композиций. Плотность цветочной пены означает, что она удерживает большое количество воды, что, в свою очередь, увеличивает срок службы ваших цветов. Он также обеспечивает усиленную поддержку стеблей цветов, давая вам больше контроля над вашими композициями.
Кроме того, пена для цветов сбалансирована по pH. Это означает, что кислотность среды, в которой находятся цветы, остается на оптимальном уровне, что в конечном итоге способствует сохранению ваших цветов.Еще одна важная особенность цветочной пены — это то, насколько быстро она впитает воду.
Цветочная пена была изобретена в 1954 году компанией Smithers-Oasis. Торговая марка Oasis ® из пенопласта с цветочным рисунком признана во всем мире. Компания Koch & Co разработала бренд Strass ® Floral Foam как еще один отличный вариант для австралийского рынка цветов. Продукты из пеноматериала со стразами — это проверенная и экономичная альтернатива цветочной пене Oasis, обеспечивающая отличные результаты.
Меры предосторожности Чаще всего цветочная пена производится из фенольной пены.Это синтетическое вещество производится из различных материалов, включая технический углерод и формальдегид. Эти вещества токсичны, поэтому при обращении с пеной для цветов важно соблюдать осторожность. Рекомендуется избегать воздействия, надев перчатки и избегая контакта с кожей. Маски для глаз можно использовать, чтобы избежать раздражения глаз, если слишком много пыли. Если вы сами формируете пену для цветов, убедитесь, что помещение хорошо проветривается, и наденьте респиратор, чтобы не вдыхать частицы пены.
Общие советы по работе с пеной для цветов:
— Хранить в сухом и прохладном месте, избегать попадания прямых солнечных лучей.
— Вымойте руки после работы с пеной.
— Не вдыхать пыль.
— Не глотать пену.
— Хранить в низком месте, избегая контакта с глазами.
Для некоторых композиций, например, в традиционной вазе, пена не требуется. Однако, используя пену, вы можете создать фантастические цветочные композиции, которые без прочной основы невозможно поддержать. Например, шары из пенопласта позволяют создавать потрясающие висячие цветочные композиции. Круглые формы отлично подходят для создания зрелищных центральных элементов, а специальные формы, такие как кресты и надгробные летучие мыши, прекрасно подходят для создания красивых аранжировок для похорон и многих других религиозных мероприятий.
Цветочная пена не только дает основу для этих композиций, но и позволяет обеспечить постоянный источник воды для цветов, удерживая воду внутри пены. Это продлевает срок службы срезанных цветов, повышая ценность как для вас, так и для ваших клиентов.
Использовать цветочную пену очень просто. Вот пошаговое руководство, и вы также можете посмотреть наше пошаговое видео о том, как замачивать цветочную пену.
Во-первых, с помощью готовой формы, такой как венок или декор для стола, или той, которую вы вырезали сами, погрузите пену в воду, пока она полностью не пропитается.При замачивании соблюдайте эти простые правила:
• Убедитесь, что вы выбрали емкость для замачивания, достаточно большую, чтобы вместить весь кусок пены, с которым вы работаете. Вы не хотите, чтобы углы или края торчали из воды.
• Чтобы правильно пропитать пену, не поддавайтесь желанию окунуть ее в воду. Это кажется логичным, но на самом деле создает воздушные карманы, из-за которых цветы могут засохнуть раньше срока. Вместо этого аккуратно поместите цветочную пену на воду (сначала она будет плавать), а затем погрузитесь в воду.
Весь процесс занимает около минуты. Обязательно дождитесь, пока весь кирпич пропитается, так как любые воздушные карманы, оставшиеся в кирпиче, уменьшат воду для ваших цветов и, следовательно, уменьшат их срок службы. Когда ваша пена полностью погрузится в воду, она потемнеет и будет готова к использованию. Как только пена намокнет, поместите ее на водонепроницаемую рабочую поверхность или в любой контейнер, который вы выбрали для своей композиции.
Если вы используете плетеную корзину или другой негерметичный контейнер, сначала выстелите его пластиком или используйте пластиковую вазу для цветов и защитный кожух, чтобы не было капель. Ваза для цветов и ограждение станут водонепроницаемым резервуаром и пластиковой клеткой, которая будет поддерживать вашу цветочную композицию. (Хотя цветочная пена очень впитывает и удерживает почти всю воду, которую впитывает, водонепроницаемые контейнеры — разумная мера предосторожности. Вы также можете использовать пластиковые вкладыши, где это возможно. К счастью, формы, которые не позволяют использовать вкладыш, например как шар, вообще не капает.)
Затем расположите цветы, как в вазе, вдавливая каждый стебель в пену на нужную глубину.Пена прекрасно подходит для создания драматических многоуровневых композиций, потому что стебли можно расположить в шахматном порядке или вдавить на разную глубину.
Создавайте цветочные композиции, которые иначе невозможно было бы поддержать с помощью цветочной пены.
Различные формы для разных случаев Одна из лучших особенностей пены для цветов — это большое разнообразие доступных форм. Это разнообразие открывает мир творческих возможностей. Некоторые из самых популярных форм цветочной пены включают кирпичи, круглые плоские подушечки и сферы.Другие разновидности цветочной пены включают кресты, особые формы для свадебных букетов, клетки и подносы для больших алтарей или сценических композиций, а также венки, которые можно использовать плоско для центральных элементов или вертикально для красивых висящих букетов. Помните, что кирпичи легко разрезать с помощью обычных инструментов флориста, и им можно придать любую форму, которая вам нужна. Попробуйте цветные кирпичи или кубики из пенопласта с цветочным рисунком в современных композициях, где вам не нужно прикрывать или скрывать пену.
Когда вы овладеете основами, цветочная пена станет отличным способом проявить творческий подход к работе.Вы получите массу вдохновения от множества доступных готовых форм, но не останавливайтесь на достигнутом. Вырезая и придавая собственные формы, вы можете создавать поистине уникальные творения, которые придадут долговечную красоту любому случаю.
А как насчет искусственных цветов и искусственных растений?
Если у вас есть искусственные цветы или искусственные растения, вы все равно можете использовать цветочную пену — просто используйте сухую! Очевидно, что это искусственные комнатные растения, они не нуждаются в солнечном свете или воде, поэтому вам не понадобятся дополнительные преимущества, которые предлагает влажная пена Oasis.
Для создания композиций из искусственных цветов и искусственных растений просто следуйте тем же советам, что и выше, без воды! Вы можете купить все наши поддельные комнатные растения, искусственные растения и искусственные цветы онлайн в Koch & Co уже сегодня!
Свойства пенополиуретана с пенообразователем четвертого поколения
Изменение климата требует использования материалов с минимальным потенциалом глобального потепления. Пенообразователь четвертого поколения HCFO-1233zd-E является одним из них.Использование HCFO позволяет производить пенополиуретан с низкой теплопроводностью. Теплопроводность, как и другие свойства пены, зависит не только от плотности, но и от ячеистой структуры пены. Ячеистая структура, в свою очередь, зависит от технологических параметров производства пенопласта. Сравнение заливочной и распыляемой пен с одинаковой низкой плотностью показало, что ячеистая структура распыляемой пены состоит из ячеек с гораздо меньшими размерами, чем заливочная пена. Из-за небольшого размера ячеек распыляемая пена имеет более низкую излучающую составляющую в проводимости пены и, как следствие, более низкую общую теплопроводность, чем заливочная пена.Водопоглощение распыляемой пены из-за мелкой ячеистой структуры также ниже, чем у заливной пены. Пена для заливки с более крупными ячейками имеет более высокую прочность на сжатие и модуль упругости в направлении подъема пены. Напротив, аэрозольная пена с мелкопористой структурой имеет более высокую прочность и модуль в перпендикулярном направлении. Также было изучено влияние старения пены на теплопроводность.
Пенополиуретан с низким потенциалом глобального потепления и вспенивающим агентом с низким потенциалом разрушения озонового слоя.
1 Введение
Для получения жестких пенополиуретанов (PUR) необходимо добавлять вспениватели вместе с полиолом и полиизоцианатом. С развитием понимания воздействия вспенивателей на различные экологические процессы в химии и технологии PUR сменилось несколько поколений вспенивателей. Первым поколением были полностью галогенированные хлорфторуглероды — жидкости с высоким озоноразрушающим потенциалом (ODP). Второе поколение — гидрохлорфторуглероды (1).Эти пенообразователи имеют низкий ODP и высокий потенциал глобального потепления (GWP). Третье поколение — это гидрофторуглероды (ГФУ) с нулевым ОРП (2,3). Согласно Киотскому протоколу к Рамочной конвенции Организации Объединенных Наций об изменении климата и другим соответствующим документам, в ближайшем будущем на практике будут применяться пенообразователи и хладагенты четвертого поколения. В отличие от пенообразователей третьего поколения, они должны иметь не только нулевой ODP, но и минимальный GWP. Свойства новых пенообразователей обсуждаются в ссылках (4–7).Они также используются в технологии пенополиуретана (8,9,10,11,12). Одним из них является гидрохлорфторолефин HCFO-1233zd-E, имеющий ODP около нуля, GWP 1 и негорючий. Под торговым названием Solstice ® Liquid Blowing Agent (LBA) он зарекомендовал себя как идеальная замена вспенивающим агентам третьего поколения при нанесении распыляемой пены (13). Низкая температура кипения (19 ° C) и скрытая теплота испарения при температуре кипения (194 кДж · кг -1 ) могут способствовать получению пен с низкой плотностью без использования дополнительного вспенивателя — воды, что увеличивает теплопроводность конечного продукта.Низкая теплопроводность пара HCFO-1233zd-E (10,2 мВт · (м · К) −1 при 20 ° C) способствует созданию изоляции с минимальной общей теплопроводностью (14).
В ранних работах (15,16,17,18,19) было показано, что общая или эффективная проводимость пены ( λ F ) можно выразить суперпозицией следующих механизмов теплопроводности через пену:
(1) λF = λm + λg + λr + λc
где λ м — теплопроводность пенополимерной матрицы, λ г — теплопроводность газов внутри ячеек пены, λ r — лучистая теплопроводность, а λ c — конвективная проводимость газов. Размеры ячеек пены обычно достаточно малы. Таким образом, конвективным переносом тепла можно пренебречь (17,18,19). Каждая из этих составляющих теплопроводности, как и многие другие рабочие характеристики пенопласта, сильно зависит от количества и геометрического распределения полимера в ячеистом пластике. Эти переменные, в свою очередь, зависят от технологии производства и химического состава пенообразователя.
Ячеистая структура пенопласта низкой плотности представляет собой многогранники-ячейки, состоящие из распорок, узлов и стенок ячеек.В частности, теплопроводность через полимерную матрицу зависит от того, какая часть распорок и стенок ячеек распределена в направлении подъема пены, а какая — в перпендикулярном направлении. Поскольку, как правило, ячейки пены вытянуты в направлении подъема пены, соответственно, масса стоек и стенок в этом направлении больше, чем в перпендикулярном направлении. Следовательно, при прочих равных условиях теплопроводность в направлении подъема пены больше, чем в перпендикулярном (20,21).Естественно, что чем меньше плотность пенопласта, тем ниже его теплопроводность. В то же время пористая структура оказывает очень значительное влияние на физико-механические свойства материала, и необходимо найти баланс между оптимальной теплоизоляцией и механическими свойствами (22,23).
Воздействие излучающей составляющей на общую теплопроводность сильно зависит от размеров ячеек. Как в теоретических, так и в практических работах было показано, что уменьшение размеров ячеек приводит к меньшему вкладу излучения в теплопроводность (16,18,24,25,26).
Тип вспенивающего агента (газ) определяет не только значение соответствующей составляющей теплопроводности, но также скорость изменения теплопроводности пены во время старения (27,28,29). К сожалению, большинство опубликованных данных о старении пен относится к пенам с вспенивающими добавками второго или третьего поколения.
Описанные и апробированные композиции разработаны в рамках коммерческого проекта. Целью данного исследования было оценить влияние технологии производства пенопласта на его ячеистую структуру, а также физико-механические свойства пенополиуретана, полученного с использованием пенообразователя четвертого поколения.
2 Материалы и методы
2.1 Материалы
Полиэфирные и полиэфирные полиолы BASF, диэтиленгликоль в качестве удлинителя цепи, IXOL B 251 (Solvay Fluor GmbH, Германия) в качестве реактивного антипирена, а также добавка антипирена TCPP (трис- (1-хлор-2-пропил) фосфат) (Albemarle GmbH, Германия), поверхностно-активное вещество Silicone L-6915LV (Momentive Performance Materials, Германия) и катализатор на основе висмута использовали в основной смеси полиолов (таблица 1).Полимерный 4,4′-метилендифенилизоцианат (PMDI) Desmodur ® 44V20L (Covestro AG, Германия) с содержанием группы NCO 31,5% и средней функциональностью 2,7 использовали в качестве изоцианатного компонента в обоих составах PUR. Для заливки полиуретановой композиции предварительно были использованы 0,5 весовых частей (весовых частей) аминсодержащего катализатора и 41 весовая часть вспенивающего агента HCFO-1233zd-E под торговым наименованием Solstice ® LBA (Honeywell Fluorine Products Europe BV, Нидерланды). добавлен к основной смеси полиолов.Для распыления композиции PUR к основной смеси полиолов добавляли 6 мас.ч. аминсодержащего катализатора и 45 мас.ч. HCFO-1233zd-E.
Таблица 1Составы пенополиуретана низкой плотности в частях по массе
Компонент | Гидроксильное число | Заливочный состав | Состав для спрея | Композиция с солканом |
---|---|---|---|---|
(мг КОН · г -1 ) | (pbw) | |||
Полиолы простых полиэфиров | 600 | 25 | ||
Полиол полиэфирный | 240 | 30 | ||
Диэтиленгликоль | 1,057 | 25 | ||
IXOL B 251 | 300 | 20 | ||
TCPP | 15 | |||
Силикон L-6915LV | 1.5 | |||
Висмутсодержащий катализатор | 0,2 | |||
Аминсодержащий катализатор | 0,5 | 6,0 | 6,0 | |
HCFO-1233zd-E | 41 | 45 | – | |
Солкане 365/227 (87:13) | – | – | 30 | |
PMDI | 147 |
2.2 Приготовление образцов пенополиуретана
Разливные блоки пенополиуретана со свободным подъемом были приготовлены с использованием лабораторного смесителя со скоростью мешалки 2000 об / мин и открытых форм размером 250 мм × 250 мм × 100 мм. Были рассчитаны доли компонентов A и B, чтобы получить толщину пеноблоков около 60 мм. Температура компонентов составляла 20 ° C. Время перемешивания, время крема, время гелеобразования и время вспенивания разливочной композиции составляли 5, 11, 24 и 30 с соответственно.
Для напыления пенопластовых панелей использовались «дозирующая система MH VR» высокого давления и пистолет-распылитель «Probler P2 Elite» (GlasCraft, Великобритания).При распылении компоненты A и B нагревали в машине и шлангах до 40 ° C. Рабочее давление компонентов составляло 120–140 бар. Производительность этих устройств с минимальной камерой смешения составила 1,5 кг · мин -1 . Панели из вспененного полиуретана были нанесены распылением на алюминиевые листы, покрытые разделительным агентом. Температура алюминиевых листов составляла 22 ° C. Время схватывания распыляемой композиции по металлу — 4 с. Толщина панелей, наносимых распылением, составляла 50–60 мм.
2.3 Испытание пенополиуретана
Образцы пенополиуретанадля испытаний были вырезаны из сердцевины залитых блоков и напыленных панелей.Коэффициент теплопроводности λ 10 пен определяли с использованием термического анализатора Linseis HFM 200 (Linseis GmbH). Измерение λ 10 проводилась по направлению подъема пены. Размер образцов составлял 200 мм × 200 мм × 35 мм, температура верхней пластины 20 ° C и температура нижней пластины 0 ° C. Во время старения образцы пенопласта хранили в помещении при 20–22 ° C, избегая попадания прямых солнечных лучей.
Объемное содержание закрытых клеток определяли согласно методу 2 ISO 4590: 2016, используя образцы размером 100 мм × 35 мм × 35 мм.Для обоих тестов использовались три образца.
Водопоглощение пен определяли согласно ISO 2896: 2001 с использованием образцов размером 50 мм × 50 мм × 50 мм. В каждой серии было испытано по пять образцов. Образцы выдерживали в воде до 30 суток.
Для испытаний пенопласта на сжатие использовалась машина для статических испытаний материалов Zwick / Roell Z010 TN (10 кН) (Германия) с дополнительной силовой ячейкой 1 кН и базовая программа testXpert II. Испытание проводилось в соответствии с требованиями EN 826 с использованием образцов размером 35 мм × 35 мм × 35 мм.Испытание проводилось в двух направлениях: параллельно ( x ) и перпендикулярно ( x ) к подъему пены. В каждой серии использовалось восемь образцов.
Ячеистую структуру пенополиуретана контролировали с помощью сканирующего электронного микроскопа (SEM) Tescan 5536M (Чехия). Разрешение — 3 нм (в высоком вакууме 5 × 10 −3 Па), увеличение 100 ×.
3 Результаты и обсуждение
3.1 Теплопроводность пен
В составах пенополиуретана низкой плотности с низкими значениями теплопроводности обычно используется комбинация физических и химических вспенивающих агентов.Так, в рецептурах Elastopor ® H 1622/5 (Elastogran BASF Group) для пены плотностью 35 кг · м −3 используется комбинация HFC-365mfc с водой. Свойства пенообразователей третьего и четвертого поколений приведены в таблице 2.
Таблица 2Свойства пенообразователей (30,31)
Химический вспениватель | Вспениватели третьего поколения | Пенообразователь четвертого поколения | |||
---|---|---|---|---|---|
Пенообразователь | CO 2 | ГФУ-245fa | ГФУ-365mfc | HFC-227ea | HCFO-1233zd-E |
Химическая формула | CO 2 | C 3 H 3 F 5 | C 4 H 5 F 5 | С 3 HF 7 | C 3 H 2 F 3 Класс |
Молекулярная масса (г · моль -1 ) | 44 | 134 | 148 | 170 | 130 |
Температура кипения (° C) | −78.5 | 15,3 | 40,2 | −16,5 | 19,0 |
Теплопроводность пара при 25 ° C (мВт · (м · К) −1 ) | 16,3 | 12,2 | 10,6 | 13,3 | 10,5 |
Наряду с HFC-365mfc также используется смесь HFC-365mfc и HFC-227ea в массовом соотношении 87/13 под торговой маркой Solkane 365/227 (87:13).Температура кипения и теплопроводность пара этой смеси составляют 24 ° C и 10,9 мВт · (м · K) -1 , соответственно.
Поскольку теплопроводность физических вспенивающих агентов в паровой фазе меньше, чем у CO 2 , общая теплопроводность полиуретановых пен, выдутых с помощью физических вспенивающих агентов, ниже, чем у пен, выдутых только с CO 2 . Кроме того, теплопроводность пенополиуретана, вспененного только физическим вспенивающим агентом, будет меньше, чем у пен, где в качестве дополнительного вспенивающего агента используется вода.Использование HCFO-1233zd-E позволило получить пену плотностью около 35 кг · м −3 без использования дополнительного вспенивателя — воды.
Поскольку потери легкокипящего вспенивающего агента во время распыления немного больше, чем при заливке композиции PUR, для получения такой же плотности пены было использовано немного более высокое содержание вспенивающего агента в композиции распыляемой пены. Благодаря этой компенсации, плотность пенопласта у залитых блоков и панелей, нанесенных распылением, была примерно одинаковой, а именно 34.0 и 34,5 кг · м −3 для заливки и распыления пены соответственно. Обе пены имели структуру с закрытыми ячейками. Объемное содержание закрытых ячеек в заливочной и напыляемой пенах было практически одинаковым — 95 об.%.
Вариация коэффициента теплопроводности λ 10 испытанных заливочных и напыляемых пен при старении представлена на рисунке 1. За начальное значение коэффициента его значение было взято в первые сутки, когда образцы были вырезаны из изготовленных блоков и панелей через 24 ч. их лечения и снятия стресса.
Рисунок 1
Изменение коэффициента теплопроводности заливочной и распыляемой пены при старении.
Было обнаружено, что при практически одинаковой плотности начальное значение коэффициента теплопроводности заливной пены было на 10% выше, чем у распыляемой пены (17,1 мВт · (м · К) -1 против 15,4 мВт · ( м · К) −1 ). Это соотношение между двумя коэффициентами пены сохранялось во время старения обеих пен на 7-й и 180-й дни, а именно 17.6 мВт · (м · К) −1 против 16,0 мВт · (м · К) −1 и 20,4 мВт · (м · К) −1 против 18,5 мВт · (м · К) — 1 соответственно. Лишь в нескольких статьях представлены характеристики теплопроводности с пенообразователями четвертого поколения, и наш результат намного более конкурентоспособен, чем тот, который представлен в исх. (12) — 23,0 мВт · (м · К) -1 .
Коэффициент теплопроводности изменялся наиболее быстро, когда пены были новыми, и градиенты давления между ячейками, заполненными пенообразователем, и окружающим воздухом, способствующие диффузии, имели максимальные значения.По мере уменьшения градиента давления скорость изменения коэффициента теплопроводности уменьшалась. Дальнейшее увеличение коэффициента произошло за счет диффузии газообразных пенообразователей и воздуха через стенки ячеек под действием градиентов парциального давления. В результате за 180 суток теплопроводность заливочной и распыляемой пены увеличилась практически одинаково — на 19% и 20%. Изменение теплопроводности пен с большой надежностью (коэффициент детерминации 0.99) можно аппроксимировать полиномиальными линиями тренда четвертого порядка. Например, приближенное уравнение для распыляемой пены:
. (2) y = −6 × 109×4 + 3 × 10−6×3−0,004×2 + 0,0417x + 15,604
R -квадратное значение = 0,994.
Значения теплопроводности обеих пен, выдутых с помощью HCFO-1233zd-E, были ниже, чем у ранее изученной распыляемой пены с вспенивающим агентом третьего поколения Solkane 365/227 (87:13), обозначенным на рисунках как Solkane.Однако плотность этой пены также была выше, а именно 48 кг · м -3 (32). Коэффициент теплопроводности распыляемой пены на 180-е сутки был ниже значения, указанного в техническом паспорте (20 мВт · (м · К) -1 ) Elastopor ® H 1622/5 с плотностью сердцевины 35 кг. · М -3 , который производится с использованием комбинации вспенивателя третьего поколения и воды. Начальные значения теплопроводности заливных и распыляемых пен с HCFO-1233zd-E были ниже, чем у пен, продуваемых HFC-365mfc (36 кг · м −3 ) или HFC-245fa (33 кг · м ). −3 ), исследованная в (33), имевшая начальное значение теплопроводности 18 мВт · м −1 .
3.2 Водопоглощение пен
Водопоглощение испытанной пены в значительной степени повторяет модели теплопроводности пены. Водопоглощение заливочной пены было выше, чем у распыляемой пены. Однако разница значений водопоглощения в конце выдержки была больше, чем теплопроводности, и составила 40%. Водопоглощение распыляемой пены было ниже, чем у распыляемой пены с вспенивающим агентом третьего поколения Solkane 365/227 (87:13), обозначенным на Фигуре 2 как Solkane, несмотря на его более высокую плотность (32).Величина водопоглощения распыляемой пены была на том же уровне (2,2 об.%), Что и у лучших образцов жестких пенополиуретанов низкой плотности на биологической основе, где также присутствовал пенообразователь Solkane 365/227 (87:13). использовали (34).
Рисунок 2
Водопоглощение заливочных и распылительных пен.
3.3 Свойства пен при сжатии
При примерно одинаковой плотности заливочная пена по сравнению с распыляемой пеной имела более высокую прочность ( σ z ) и модуля упругости ( E z ) при сжатии в направлении подъема пены (таблица 3).Напротив, распыляемая пена по сравнению с заливной пеной имела более высокую прочность ( σ x ) и модуля упругости ( E x ) при сжатии в перпендикулярном направлении. Следовательно, заливочная пена низкой плотности имела более высокую степень анизотропии прочности ( σ z / σ x ), равный 1.86 против 1,14 для распыляемой пены. Степень анизотропии модуля ( E z / E x ) было даже больше, а именно 2,06 для заливной пены по сравнению с 1,17 для распыляемой пены той же плотности.
Таблица 3Свойства заливочной и распыляемой пены на сжатие
Пена | Плотность | σ z | σ x | E z | E x |
---|---|---|---|---|---|
(кг · м −3 ) | (кПа) | (кПа) | (МПа) | (МПа) | |
Заливка | 34.0 ± 0,3 | 130 ± 10 | 70 ± 5 | 3,70 ± 0,50 | 1,80 ± 0,30 |
Распылитель | 34,5 ± 0,2 | 114 ± 9 | 100 ± 6 | 2,55 ± 0,13 | 2,18 ± 0,12 |
3.4 Микроструктура пен
Изучение ячеистой структуры пенопласта позволило объяснить многие наблюдаемые физические и механические эффекты. Пены примерно одинаковой плотности имели совершенно разные ячеистые структуры. Ячеистая структура заливочной пены была более однородной и состояла из ячеек гораздо большего размера (рис. 3а). Ячеистая структура распыляемой пены была менее однородной и состояла из мелких ячеек (рис. 3b). Длина, ширина и соотношение L / W ячеек для заливки и распыления пены указаны в таблице 4.Средние значения длины и ширины ячеек были рассчитаны по измерениям 100 ячеек. Но все мелкие дефекты ячеистой структуры изолированы замкнутыми ячейками вокруг дефектов. Следовательно, распыляемая пена имела примерно такое же значение измеренных закрытых ячеек и более низкую теплопроводность. Влияние этих дефектов на механические свойства трудно идентифицировать отдельно от влияния размеров и удлинения ячеек.
Рисунок 3
Поперечное сечение заливки (а) и разбрызгивания (б) пеноблоков в направлении подъема пены при 100-кратном увеличении SEM.
Таблица 4Размеры ячеек заливочной и распыляемой пены (мкм)
Пена | Длина | Ширина | Д / Ш |
---|---|---|---|
Заливка | 622 ± 63 | 467 ± 52 | 1.33 |
Распылитель | 221 ± 51 | 155 ± 29 | 1,43 |
При вспенивании разливаемой пенополиуретановой композиции с низкой концентрацией аминового катализатора время схватывания и время гелеобразования композиции были достаточно большими. Следовательно, при вспенивании композиции было достаточно времени для образования крупных ячеек.Напротив, при вспенивании аэрозольной композиции пенополиуретана с высоким содержанием аминного катализатора время кремации и время гелеобразования были намного короче, и не было достаточного времени для образования больших ячеек.
Ячейки, образовавшиеся во время заливки и распыления пены, имели примерно одинаковую степень удлинения в направлении подъема пены ( L / W ). Однако из-за разницы в абсолютных размерах степень механической анизотропии при заливке пенополиуретана была больше.С другой стороны, из-за гораздо меньшего размера ячеек аэрозольная пена PUR имела гораздо более низкую теплопроводность. Это прямое следствие уменьшения радиационной составляющей в общей теплопроводности пены (24,25,26).
4 Заключение
Вспенивающий агент четвертого поколения HCFO-1233zd-E может использоваться для получения пены низкой плотности с низкой теплопроводностью. Для получения пены с наименьшей теплопроводностью предпочтительно использовать метод распыления, позволяющий получать пену с малым размером ячеек, а значит, более низким коэффициентом теплопроводности и низким водопоглощением.Из-за небольшого размера ячеек анизотропия механических свойств этих пен также ниже, чем у пенопласта той же плотности с более крупными ячейками. При старении в нормальных условиях за счет взаимной диффузии газов пенообразователя и окружающего воздуха теплопроводность пены увеличивается на 20% за 180 дней, но при этом она ниже, чем у пенополиуретанов, полученных третьим. пенообразователь поколения.
Список литературы
(1) Pranav Mehta PB, Chidambaram ASP, Selwynt W.Технические сравнения пен с использованием различных смесей вспенивающих агентов, содержащих HCFC-141b, HFC-245fa, жидкий вспениватель Solstice® и углеводороды в бытовых приборах. Труды технической конференции по полиуретанам; 2014 22–24 сентября; Даллас, Техас, США; 2014. с. 162–72. Искать в Google Scholar
(2) Ховард П., Рункель Дж., Банерджи С. Вспенивающие агенты третьего поколения для пенопластовой изоляции. Вашингтон, округ Колумбия: Агентство по охране окружающей среды США; 1998. EPA / 600 / R-98/133 (NTIS PB99-122095).Искать в Google Scholar
(3) Ву Дж., Албуи А., Мутон Д. Оценка вспенивающих агентов на основе ГФУ следующего поколения в жестких пенополиуретанах. J Cell Plast. 1999. 35 (5): 421–37. 10.1177 / 0021955X9
(4) Wuebbles DJ, Ван Д., Паттен К.О., Олсен СК. Анализ новых короткоживущих заменителей ГФУ с большим ПГП. Geophys Res Lett. 2013. 40 (17): 4767–71. 10.1002 / grl.50908. Искать в Google Scholar
(5) Molés F, Navarro-Esbrí J, Peris B, Mota-Babiloni A, Barragán-Cervera A, Kontomaris K.Альтернативы HFC-245fa с низким ПГП в органических циклах ранкина для низкотемпературной рекуперации тепла: HCFO-1233zd-E и HFO-1336mzz-Z. Appl Therm Eng. 2014; 71 (1): 204–12. 10.1016 / j.applthermaleng.2014.06.055. Искать в Google Scholar
(6) Валлингтон Т.Дж., член парламента Сулбек Андерсен, Нильсен О.Дж. Атмосферная химия короткоцепочечных галоолефинов: фотохимические потенциалы образования озона (POCP), потенциалы глобального потепления (GWP) и потенциалы разрушения озона (ODP). Chemosphere. 2015; 129: 135–41.10.1016 / j.chemosphere.2014.06.092. Искать в Google Scholar
(7) Рао ПК, Гейджи СП. Атмосферное разложение HCFO-1233zd (E), инициированное радикалом ОН, атомом Cl и молекулой O3: кинетика, механизмы реакции и последствия. J. Fluorine Chem. 2018; 211: 180–93. 10.1016 / j.jfluchem.2018.05.001. Искать в Google Scholar
(8) Мота-Бабилони А., Махнач П., Ходабандех Р. Недавние исследования по замене ГФУ синтетическими альтернативами с более низким ПГП: Акцент на энергетические характеристики и воздействие на окружающую среду.Int J Refrig. 2017; 82: 288–301. 10.1016 / j.ijrefrig.2017.06.026. Искать в Google Scholar
(9) Гроссман Р.С. Облегчение автокресла с использованием жидкого вспенивателя Solstice® (HFO 1233zd (E)). SAE Int J Mater Manuf. 2016; 9: 794–800. 10.4271 / 2016-01-0521. Искать в Google Scholar
(10) Brondi C, Maio ED, Bertucelli L. Влияние фторорганических добавок на морфологию, теплопроводность и механические свойства жестких пенополиуретанов и полиизоцианурат.J Cell Plast [Препринт]. 2021 [цитируется 17 января 2021 года]. 10.1177 / 0021955X20987152. Искать в Google Scholar
(11) Аль-Моамери Х.Б., Набхан Б.Дж., Васми Т.М., Али Абдулрехман М. Влияние смесей вспенивающих агентов на термические и механические свойства пенополиуретана. AIP Conf Proc. 2020; 2213: 020177. 10.1063 / 5.0000153. Искать в Google Scholar
(12) Чан Р., Ли Й, Сон К. Х., Ким В. Н.. Влияние зародышеобразователя на теплопроводность и деформацию ползучести жестких пенополиуретанов, выдутых экологически чистым пенообразователем.Macromol Res. 2021; 29: 15–23. 10.1007 / s13233-021-9003-х. Искать в Google Scholar
(13) Богдан М., Уильямс Д. Результаты последних полевых испытаний распыляемой пены жидкого вспенивающего агента solstice®. Труды технической конференции по полиуретанам; 2014 22–24 сентября; Даллас, Техас, США; 2014. с. 638–49 Искать в Google Scholar
(14) Жидкий пенообразователь Solstice. Техническая информация. © Honeywell International Inc; 2017. Доступно по адресу: https://www.fluorineproducts-honeywell.ru / blowingagents / wp-content / uploads / 2013/09 / honeywell-solstice-lba-1233zd-Technical-brochure.pdf Искать в Google Scholar
(15) Norton FJ. Теплопроводность и срок службы пенополимеров. J Cell Plast. 1967. 3 (1): 23–37. 10.1177 / 0021955X6700300101. Искать в Google Scholar
(16) Болл Г.В., Херд Р., Уокер М.Г. Теплопроводность жестких пенополиуретанов. J Cell Plast. 1970. 6 (2): 66–75. 10.1177 / 0021955X7000600202. Искать в Google Scholar
(17) Пейдж MC, Glicksman LR.Измерения коэффициентов диффузии альтернативных вспенивателей в пенопластовой изоляции с закрытыми порами. J Cell Plast. 1992. 28 (3): 268–83. 10.1177 / 0021955X9202800304. Искать в Google Scholar
(18) Гликсман ЛР. Теплообмен в пенах. В: Hilyard NC, Cunningham A, редакторы. Ячеистые пластики низкой плотности. Дордрехт: Спрингер; 1994. стр. 104–52. 10.1007 / 978-94-011-1256-7_5. Искать в Google Scholar
(19) Бидерманн А., Кудоке С., Мертен А., Миноуг Е., Ротермунд Ю., Эберт Х.П. и др.Анализ механизмов теплопередачи в жестком пенополиуретане. J Cell Plast. 2001. 37 (6): 467–83. 10.1106 / KEMU-LH63-V9h3-KFA3. Искать в Google Scholar
(20) Хардинг Р. Взаимосвязь между структурой ячеек и свойствами жесткого пенопласта. J Cell Plast. 1965; 1 (3): 385–94. 10.1177 / 0021955X6500100304. Искать в Google Scholar
(21) Mathis N, Chandler C. Теплопроводность, зависящая от ориентации и положения. J Cell Plast. 2000. 36 (40): 327–36. 10.1177 / 0021955X0003600406.Искать в Google Scholar
(22) Gong W, Jiang TH, Zeng XB, He L, Zhang C. Экспериментально-численные исследования влияния структуры ячеек на механические свойства пенополипропилена. Е-полимеры. 2020; 20: 713–23. 10.1515 / epoly-2020-0060. Искать в Google Scholar
(23) Гуо А., Ли Х, Сюй Дж, Ли Дж, Ли Ф. Влияние микроструктуры на свойства микропористого вспененного материала из полистирола. Е-полимеры. 2020; 20: 103–10. 10.1515 / epoly-2020-0012. Искать в Google Scholar
(24) Фанг В, Тан И, Чжан Х, Тао В.Численные прогнозы эффективной теплопроводности жесткого пенополиуретана. J Wuhan Univ Technol. 2017; 32: 703–8. 10.1007 / s11595-017-1655-1. Искать в Google Scholar
(25) Wu JW, Sung WF, Chu HS. Теплопроводность пенополиуретана. Int J Heat Mass Tran. 1999. 42 (12): 2211–17. 10.1016 / S0017-9310 (98) 00315-9. Искать в Google Scholar
(26) Лим Х, Ким Ш., Ким Б. Влияние кремниевого поверхностно-активного вещества на жесткие пенополиуретаны. Express Polym Lett.2008. 2 (3): 194–200. 10.3144 / expresspolymlett.2008.24. Искать в Google Scholar
(27) Хардинг Р. Некоторые эффекты переноса газа на характеристики жесткой пены. J Cell Plast. 1965; 1 (1): 224–8. 10.1177 / 0021955X6500100128. Искать в Google Scholar
(28) Брандрет Д.А. Факторы, влияющие на старение жесткого пенополиуретана. J Therm Insul. 1981; 5 (1): 31–9. 10.1177 / 109719638100500103. Искать в Google Scholar
(29) Бомберг М.Т., Кумаран М.К., Аскоу М.Р., Сильвестр Р.Г.Влияние времени и температуры на коэффициент теплопередачи жесткой пенополиуретановой изоляции, изготовленной с использованием альтернативных пенообразователей. J Therm Insul. 1991. 14 (3): 241–67. 10.1177 / 10971963
(30) СОЛКАН 365 — Пенообразователи. Solvay Fluor GmbH. Доступно по адресу: https://www.solvay.com/sites/g/files/srpend221/files/tridion/documents/SOLKANE_365_Foaming_Agents_0.pdf Поиск в Google Scholar
(31) Zipfel L, Börner K, Krücke W. HFC-365mfc: универсальный вспениватель для жестких пенополиуретанов.J Cell Plast. 1999. 35 (4): 328–44. 10.1177 / 0021955X9
(32) Кабулис Ю., Якушин В., Фишер ВПП, Рунданс М., Севастьянова И., Деме Л. Жесткие пенополиуретаны в качестве внешнего резервуара Криогенная изоляция для космических ракет-носителей. IOP Conf Series Mater Sci Eng. 2019; 500: 012009. 10.1088 / 1757-899X / 500/1/012009. Искать в Google Scholar
(33) Doerge HP. Пенообразователи HFC с нулевым ODP для пенопласта. J Cell Plast. 1997. 33 (3): 207–18. 10.1177 / 0021955X9703300302.Искать в Google Scholar
(34) Гайдукова Г., Ивдре А., Фридрихсон А., Веровкин А., Кабулис Ю., Гайдуков С. Полиуретановые жесткие пенопласты, полученные из полиолов, содержащих биологические и переработанные компоненты и функциональные добавки. Ind Crop Prod. 2017; 102: 133–43. 10.1016 / j.indcrop.2017.03.024. Искать в Google Scholar
Получено: 2021-06-02
Доработано: 2021-08-31
Принято: 2021-09-01
Опубликовано онлайн: 2021-10-06
© 2021 Владимир Якушин и др. ., опубликовано De Gruyter
Это произведение находится под лицензией Creative Commons Attribution 4.0 International License.
Исследование с помощью экспериментального и численного моделирования
Abstract
Механические свойства разрушения жесткого пенополиуретана, обработанного при случайной вибрации, были изучены экспериментально и с помощью численного моделирования. Случайные вибрационные обработки проводились в частотном диапазоне 5–500 Гц, 500–1000 Гц и 1000–1500 Гц соответственно. Влияние частоты вибрации, массы блока и ускорения на механические характеристики жесткого пенополиуретана было дополнительно исследовано с помощью испытаний на сжатие.Результаты экспериментов показали, что компрессионные характеристики и поглощение энергии пенами меньше всего снижаются между 500–1000 Гц. Кроме того, в диапазоне 5–500 Гц скорость снижения характеристик сжатия и поглощения энергии увеличивалась с увеличением блока вибрационной массы и ускорения. Полученное моделирование показало, что степень деформации образца была наиболее серьезной в условиях 5–500 Гц. С увеличением деформации повреждаемость образца в процессе вибрации увеличивалась, что приводило к снижению компрессионных свойств и поглощения энергии жесткого пенополиуретана.Это дополнительно объясняет механизм изменения производительности теста на сжатие.
Ключевые слова: жесткий пенополиуретан , случайная вибрация, характеристики сжатия, свойства поглощения энергии, численное моделирование, модальный анализ
1. Введение
В качестве ячеистого материала пенополиуретан часто используется в аэрокосмической, нефтехимической промышленности, упаковке и т. Д. и транспортировка благодаря отличным механическим свойствам и свойствам поглощения энергии [1].Пенополиуретан в большинстве случаев применяется против сжимающих нагрузок [2,3]. Поэтому важно изучить характеристики пенополиуретана при сжатии. Мезоскопическая структура пен имеет важное влияние на его характеристики сжатия [2,4]. Л. Дж. Гибсон и М. Ф. Эшби пришли к выводу, что жесткость вспененного материала с закрытыми порами в основном обусловлена краем ячейки, за которой следует вклад сжатия газа в ячейке [2]. Когда прикладывались сжимающие нагрузки, обтюраторные пены имели явления изгиба краев ячеек и складывания стенок ячеек.Кроме того, плотность пены, скорость деформации и температура окружающей среды также влияют на компрессионные характеристики пенополиуретана [4,5,6]. Принимая во внимание эти факторы, исследователи создали серию надежных конститутивных моделей, таких как упруго-пластическая конститутивная модель [5], конститутивная модель упругой / разрушаемой пены [7] и конститутивная модель гиперупругой / сверхпеной [8]. Кроме того, на основе этих основных моделей с помощью программного обеспечения для анализа методом конечных элементов было предсказано поведение пенополиуретана при сжатии.Например, Tae-Rim Kim et al. изучили поведение пенополиуретана при сжатии с помощью ABAQUS UMAT, который скомпилировал упруго-пластическую конститутивную модель в определяемую пользователем подпрограмму материала [5].
В то же время в области практического машиностроения на пенополиуретан неизбежно воздействуют свет, температура, влажность, нагрузка и другие факторы, что приводит к изменению его химического состава и структуры пенопласта, а затем ухудшению его механических свойств. [9,10,11,12].Термическое разложение кислорода, вызванное внешними факторами, является одной из наиболее частых причин разрушения пенополиуретана [10,11,13]. По мере прогрессирования окислительной деградации молекулярная цепь полиуретана будет гидролизоваться, и пена будет меняться от вязкости к хрупкости, что приведет к разрыву пены в процессе деформации [11]. С другой стороны, усталостное разрушение пенополиуретана при внешней нагрузке (например, циклической нагрузке) было одной из причин разрушения, что проявлялось в деградации жесткости и изменениях рассеивания энергии пеноматериалов [12,14,15].Механизм разрушения, вызванный исходной трещиной, вызывает хрупкое разрушение под действием нагрузки [16,17], а вязкость разрушения при различных нагрузках может быть измерена с помощью испытания на трехточечный изгиб и испытания на сдвиг.
Форма нагрузки в практической инженерии часто бывает сложной и неопределенной, среди которых случайная вибрационная нагрузка является типичной формой нагрузки. Случайная вибрация относится к вибрации, которая не может быть описана детерминированной функцией, но имеет определенные статистические правила [18].Обычная случайная вибрация в повседневной жизни — это вибрация, вызванная вождением автомобиля. Мягкий пенополиуретан часто использовался в качестве подушки для автомобилей [19,20,21], которая могла уменьшить и изолировать вибрацию автомобилей и сделать пассажиров более комфортными во время вождения. Гибкие пенополиуретаны обладают нелинейным и демпфирующим действием. Нелинейные параметры жесткости и вязкоупругости гибких пенополиуретанов могут быть получены с помощью вибрационных испытаний и испытаний на сжатие [19,20]. Однако, помимо этого, пенополиуретан также часто использовался в качестве материала сердцевины для изготовления сэндвич-панелей [22,23] и сотовых панелей [24] из-за его хороших характеристик поглощения вибрации и изоляции.Чтобы понять вибрационные характеристики пеноматериалов, исследователи изучили плотность, прочность и вязкоупругость пеноматериалов [25,26]. Lyes Dib et al. С помощью 3D COMSOL Multiphysics было обнаружено, что модуль Юнга, коэффициент Пуассона, коэффициент демпфирования и плотность пенополиуретана изменяют коэффициент поглощения, тем самым влияя на характеристики звукопоглощения [25]. Метод численного моделирования методом конечных элементов может быть использован для анализа свойств пеноматериалов в условиях вибрации.
В настоящее время исследования вибрации пенополиуретана в основном сосредоточены на нелинейном, демпфирующем эффекте, а также на поглощении и изоляции вибрации мягкого пенополиуретана. Однако исследование вибрационного разрушения пенополиуретана не было систематическим и достаточным. В частности, характеристики разрушения жесткого пенополиуретана (RPUF) при случайной вибрации и численное моделирование процесса случайной вибрации RPUF еще не сообщалось. В этой статье механизм случайного вибрационного разрушения RPUF был должным образом изучен с помощью экспериментального и конечно-элементного моделирования.Случайные колебания различных частотных диапазонов, масса блока и виброускорение были разработаны для моделирования реальной рабочей среды RPUF. Степень разрушения RPUF из-за вибрации оценивалась путем определения характеристик сжатия и поглощения энергии. Микроструктуру RPUF в направлении колебаний анализировали с помощью автоэмиссионного сканирующего электронного микроскопа (SEM). Более того, случайная вибрация была исследована и проанализирована с помощью программного обеспечения ABAQUS 6.16 шаг за шагом в процессе моделирования.Кривая смещения и кривая скорости в верхней части модели в различных частотных диапазонах были получены с помощью модального анализа, а механизм вибрационного разрушения модели RPUF был успешно объяснен с помощью деформации и распределения напряжений по Мизесу.
2. Экспериментальная
2.1. Материалы и вибрационная обработка
В этой статье жесткие пенополиуретаны с плотностью 200 кг / м 3 были получены из полиметиленполифенилполиизоцианата (PAPI) с изоцианатным числом (NCO%) 30.8% и полиэфирполиол с гидроксильным числом (OH%) 453,51 мг КОН / г, которые были приобретены у Shanghai Wantian Thermal Insulation Material Co., Ltd. Образцы RPUF размером 300 мм × 200 мм × 30 мм подвергали случайной вибрации. обработки, а спектр белого шума использовался для моделирования реальной вибрационной среды.
Как показано на рисунке, система испытания на случайную вибрацию состояла из шести частей: образца жесткого пенополиуретана, блока масс, наслоения, болта, датчика ускорения и испытательного стенда на высокочастотную электрическую вибрацию.Среди них массовый блок был разработан для моделирования несущей способности пеноматериала в реальных условиях работы. Целью наслоения и крепления болтами было закрепление массивных блоков и образцов пенопласта. Датчики ускорения отслеживали изменения ускорения во время вибрации. Наконец, испытательный стенд на высокочастотную электрическую вибрацию (ES-50LS4-445, Suzhou Dongling Vibration Test Instrument Co., Ltd., Сучжоу, Китай) обеспечил вибрационную среду.
Система испытания на случайную вибрацию.
Испытание на случайную вибрацию определяется четырьмя параметрами: частотным диапазоном, спектральной плотностью мощности (PSD), общим среднеквадратичным ускорением (RMS) и временем испытания. Согласно GB / T 4857.23-2012, конструкция этой экспериментальной схемы показана на. Испытание на случайную вибрацию проводилось в частотном диапазоне 5–500 Гц, 500–1000 Гц и 1000–1500 Гц соответственно. Воздействие массовых блоков и ускорений на жесткие пенополиуретаны исследовалось в диапазоне 5–500 Гц. Переменная нагрузка случайной вибрации прикладывалась в направлении оси z в течение 1 ч.
Таблица 1
Условия для испытаний на случайную вибрацию.
Номер | Диапазон частот (Гц) | Масса блока (кг) | Среднеквадратичное ускорение (г / Гц) | ||||
---|---|---|---|---|---|---|---|
1 | 5–500 | 20 | 2 | 500–1000 | 20 | 8 | |
3 | 1000–1500 | 20 | 8 | ||||
4 | 5–500 | ||||||
5–500 | 8325 | 5–500 | 10 | 8 | |||
6 | 5–500 | 20 | 2 | ||||
7 | 5–500 | 20 | 442. Характеристика и тестированиеМикроморфологию RPUF после случайной вибрации наблюдали с помощью сканирующего электронного микроскопа с полевой эмиссией (SEM, FE-SEM-4800-1, Japan Hitachi Technology Co., Ltd., Hitachi, Япония). по направлению вибрации. Образцы ППУФ разрезались на тонкие слои по направлению вибрации. Затем тонкие слои были нанесены на проводящий клей и опрысканы золотом для наблюдения. Кроме того, в соответствии с GB / T 8813-2008, были проведены испытания квазистатического сжатия RPUF после случайной вибрации.Размеры образцов на сжатие составляли 20 мм × 20 мм × 15 мм, и испытания на сжатие проводились по направлению вибрации. Электронная универсальная испытательная машина (CMT4304-QY, MTS Systems Corporation, Миннесота, США) использовалась для испытаний квазистатического сжатия со скоростью деформации 0,001 с -1 , и испытания закончились при деформации 80%. Каждый эксперимент по сжатию повторяли пять раз; среднее значение как экспериментальные результаты. Затем ударопрочность и поглощение энергии RPUF были оценены методом поглощения энергии [2,7].По методикам U.E. Ozturk и G. Anlas [27], кривая поглощенной энергии-деформации и кривая поглощения энергии-напряжения были приняты для отражения характеристик поглощения энергии RPUF в процессе сжатия. Поглощенная энергия (Вт) определяется как энергия, поглощаемая вспененным материалом на единицу объема. Работа на единицу объема может быть получена по площади, ограниченной кривой зависимости напряжения от деформации. W = ∫ε0εfσ (εf) dεf (1) Эффективность поглощения энергии (P) — это отношение поглощенной энергии вспененного материала к соответствующему напряжению. P = ∫ε0εfσ (εf) dεfσ (εf) (2) где ε0 — начальная деформация, а εf — конечная деформация. В этой статье поглощенная энергия и эффективность поглощения энергии использовались для оценки способности пеноматериалов поглощать энергию. Эти параметры в среднем в пять раз превышают поглощение энергии сжатия. 3. Численное моделированиеПроцесс случайной вибрации моделировался с помощью коммерческого программного обеспечения ABAQUS 6.16. В этой работе впервые был проведен тест на сходимость для определения наиболее подходящей плотности сетки, как показано на рис.Кривая вибрационного смещения точки А сходится с уточнением сетки, и кривая, полученная из сетки «глобальный размер = 10», близка к кривой, полученной из сетки «глобальный размер = 5». Это означает, что результаты, полученные с использованием сетки «global size = 5», сходятся. Поэтому сетка «global size = 5» была принята для точности и эффективности вычислений в этой работе. В d модель случайной вибрации представляла собой прямоугольный образец размером 300 мм × 200 мм × 30 мм, а сетка модели состояла из C3D8R (8-узловой линейный кирпич с общим количеством 14400 гексаэдрических единиц).Кроме того, точка A является вершиной конечно-элементной модели. Плотность RPUF была установлена на уровне 2 × 10 -10 т / мм 3 (200 кг / м 3 ), а направление его колебаний было осью z. Тест сходимости и схематическая диаграмма конечно-элементной модели. ( a ) Глобальный размер = 15, ( b ) Глобальный размер = 10, ( c ) Тест сходимости, ( d ) Глобальный размер = 5. В этой работе мы использовали метод E Linul et al.[7], который использовал модель упругой / разрушаемой пены в качестве модели определяющего отношения для характеристики общих механических свойств RPUF без обработки случайной вибрацией. Рабочие параметры образцов ППУФ без вибрационной обработки были получены при испытании на сжатие. Эти параметры были присвоены модели упругой / складывающейся пены для характеристики свойств материала RPUF. Модуль Юнга был установлен равным 25,61 МПа, а коэффициент Пуассона — 0,2. Модель измельчаемой пены использовалась для описания пластического состояния материалов с объемно упрочненной поверхностью текучести.Поверхности текучести развивались аналогичным образом (постоянная α), а коэффициент формы α определялся как где k — коэффициент текучести при сжатии, а kt — коэффициент гидростатического напряжения текучести. Следовательно, форму поверхности текучести можно определить путем определения значений k и kt. Предел текучести σb был установлен равным 1,67 МПа. Для получения вибрационных характеристик образцов был использован метод модального анализа для определения модальных и вибрационных режимов образцов жесткого пенополиуретана.В ABAQUS / Standard решатель Ланцоша использовался для расчета собственной частоты и соответствующих мод модели вибрации. Собственное значение собственной частоты модели незатухающих колебаний может быть выражено как где Mab — матрица качества, Kab — матрица жесткости, ϕb — характеристический вектор, a и b — степени свободы. Решатель Ланцоша может использоваться для извлечения первых шести собственных частот и мод модели вибрации с частотными диапазонами 5–500 Гц, 500–1000 Гц и 1000–1500 Гц соответственно.В этой работе движение базы ускорения использовалось в качестве граничного условия для ограничения свободы модели. Степень свободы была U 3 (Направление вибрации), а амплитуда была установлена как 0,129 g 2 / Гц, а именно спектральная плотность мощности ускорения случайной вибрации. Кроме того, напряжение образца во время случайной вибрации было смоделировано с помощью метода стационарной динамики, а моделирование случайной вибрации RPUF дополнительно объяснило изменение его испытания на сжатие. 4. Результаты и обсуждение4.1. Микроструктура жесткого пенополиуретанаМикроструктура жесткого пенополиуретана без вибрационной обработки показана на а, б. Можно было заметить, что микроструктура RPUF в основном состоит из треугольных призматических столбов и сферических тел ячеек из пеноматериала. Большинство клеточных тел RPUF имеют сферическую форму и плотно распределены. На сферическом теле клетки существует множество маленьких круглых плоскостей, которые представляют собой «маленькое окно», образованное двумя телами клетки, расположенными рядом друг с другом.Круглые «маленькие окна» имеют разные размеры, что указывает на разное расстояние между ячейками пены. Как видно из а, б, треугольные призматические столбы пенопласта образованы тремя корпусами ячеек, примыкающими друг к другу. Эти треугольные призмы являются основными несущими конструкциями и обеспечивают основную жесткость пеноматериала. Микроструктура (СЭМ) образцов RPUF. Где ( a , b ) — образец без вибрации, ( c , d ) — образец после вибрации. Кроме того, наблюдали влияние вибрационной обработки на жесткий пенополиуретан и дополнительно анализировали механизм вибрационного повреждения. Микроморфология образца после случайной вибрации в направлении вибрации показана в c, d. После случайной вибрации на призме из жесткого пенополиуретана появились крошечные трещины, а ее сферические тела ячеек были разрушены. На рисунке c микротрещины сначала зародились у столба пены, а затем распространились по стыку между ячейками.В основном это вызвано многократным сжатием ППУФ массовым блоком в процессе случайной вибрации. В качестве основной несущей конструкции края ячеек подвергались многократному изгибу до усталостного разрушения под действием многократного сжатия, после чего на краях ячеек появлялись микротрещины. В d ячейки пены лопаются сбоку, и треснувшая часть стенки пены в некоторой степени скручивается и загибается наружу. В основном это связано с давлением газа внутри пенопласта с закрытыми ячейками.Когда внешняя вибрационная нагрузка достигла предельной точки, давление внутри ячейки из вспененных материалов было больше, чем прочность стенки ячейки, что привело к крошечному разрыву тела ячейки. При непрерывной вибрации тело клетки многократно сжималось блоком массы, что приводило к росту микротрещин на теле клетки с выходом газа из тела клетки, а стенка тела клетки также сморщивалась и складывалась. Следовательно, режимы разрушения жестких пенополиуретанов в условиях случайной вибрации в основном состоят из двух форм: микротрещины ячеечной призмы и разрыва ячеек. 4.2. Характеристики сжатия жесткого пенополиуретанаКривые напряжения-деформации сжатия RPUF в различных условиях вибрации показаны на рис. Как видно из а, процесс сжатия жесткого пенополиуретана можно предварительно разделить на три стадии: линейно-упругую стадию, платформенную стадию и стадию уплотнения [7,28]. В отношении внешних ударных и сжимающих нагрузок характеристики пеноматериалов в основном зависят от способности поглощать энергию ступени платформы [7].б показаны кривые растяжения образцов после случайной вибрации трех частотных диапазонов. В пределах 500–1000 Гц напряжение платформы RPUF значительно выше, чем напряжение платформы двух других полос, которое уменьшается на 6,0% по сравнению с исходным образцом (напряжение платформы (σp) исходного образца составляет 2,01 МПа, из ). Однако платформенное напряжение образцов в диапазонах 5–500 Гц и 1000–1500 Гц снизилось на 17,4% и 13,4% соответственно. Из раздела 4.1 видно, что формы разрушения RPUF в условиях вибрации в основном включают растрескивание краев ячеек и разрыв ячеек.Деформации в основном достигаются за счет податливости клеточной призмы и сжатия тела клетки. При приложении сжимающей нагрузки края ячеек образца постепенно изгибаются, а ячейки постепенно сжимаются. В это время микротрещины на краях ячеек постепенно расширяются, и треснувшие ячейки не выдерживают внешней нагрузки, что приводит к снижению напряжения платформы. Таким образом, это указывает на то, что образцы в диапазоне 5–500 Гц имеют наибольшие повреждения при случайной вибрации, а образцы в диапазоне 500–1000 Гц — наименьшие повреждения. Кривые напряжения-деформации при сжатии RPUF, ( a ) Принципиальная схема стадии сжатия пены, ( b ) Различные диапазоны частот, ( c ) Различные блоки массы, ( d ) Различные ускорения . Жесткие пенополиуретаны при практическом применении часто страдают от случайных низкочастотных колебаний. В сочетании с результатами сравнения b; поэтому другие влияющие факторы, блок массы и ускорение компрессионных характеристик RPUF были дополнительно изучены в низкочастотном диапазоне 5–500 Гц.На c видно, что σp RPUF в диапазоне 5–500 Гц уменьшается с повышением качества массовых блоков. Если блок массы не добавлен, σp образца составляет 2,00 МПа, что уменьшается на 0,5% по сравнению с исходным образцом. При добавлении блока масс 10 кг σp образца уменьшается на 9,5%, а второе увеличение 10 кг составляет 17,4%. С увеличением массы блока скорость уменьшения напряжения платформы постепенно увеличивается. В d σp образцов с ускорением 2 g и 4 g уменьшается на 1.5% и 7,5% соответственно. В этом случае скорость уменьшения напряжения платформы невелика, и степень повреждения образца также минимальна. Уменьшение напряжения в вышеуказанной платформе объясняется уменьшением способности материалов поглощать энергию, вызванным микротрещинами в призмах пены и ячейками разрыва. Повреждение пеноматериала может напрямую проявляться изменением его механических характеристик. показывает параметры механических свойств, полученные с помощью кривых напряжения-деформации.Сжимающие свойства (модуль упругости (E), предел текучести (σb)) RPUF в некоторой степени снижаются при различных условиях вибрации. E и σb исходного образца составляют 25,61 МПа и 1,67 МПа соответственно. По сравнению с исходным образцом, E и σb образцов в группе 500–1000 Гц снизились на 6,0% и 4,2% соответственно, скорость снижения которых была наименьшей из трех частотных диапазонов. В сочетании с анализом в, было обнаружено, что напряжение платформы, модуль упругости и предел текучести образцов 500–1000 Гц снизились.Напротив, E и σb образцов с частотой 5–500 Гц уменьшились на 8,2% и 12,6% по сравнению с исходными образцами соответственно. Скорость убывания E, σb и σp выборок 5–500 Гц является наибольшей в трех диапазонах частот. Характеристики сжатия RPUF в различных условиях вибрации, ( a ) Различные диапазоны частот, ( b ) Различные блоки массы, ( c ) Различные ускорения. Кроме того, было также обнаружено, что скорость уменьшения производительности сжатия увеличивается с увеличением качества массового блока.В диапазоне 5–500 Гц E и σb образцов без массового блока уменьшаются на 1,4% и 1,2% по сравнению с исходным образцом соответственно. При добавлении блока массой 10 кг E и σb образца уменьшаются на 3,1% и 5,8%, затем они уменьшаются на 8,2% и 12,6% при блоке массой 20 кг соответственно. С другой стороны, виброускорение также влияет на механические свойства RPUF. При ускорении 2 g характеристики сжатия образцов снижаются на 4,7% и 3.6% по сравнению с исходным образцом и на 4,3% и 4,8% при ускорении 4 g соответственно. Причиной указанной выше разницы в характеристиках сжатия является разная степень повреждения образцов при различных условиях вибрации. Жесткость и прочность RPUF в основном обеспечивается ячеистой призмой на стадии линейной упругости. Когда применяется сжатие, призма ячейки постепенно изгибается до тех пор, пока не появится текучесть. Однако, согласно анализу в разделе 4.1, после случайной вибрации в пенопласте есть два дефекта: растрескивание призмы ячейки и разрыв ячейки.Как показано на, призмы образованы близостью трех соседних ячеек. При сжатии вспененного материала призма ячеек постепенно изгибается, а микротрещины расширяются в поперечном направлении и образуются в продольном направлении. В результате призма ячейки не могла эффективно противостоять внешней силе сжатия, и жесткость и прочность RPUF снизились. В этом разделе снижение компрессионных характеристик на частотах 500–1000 Гц является наименьшим, в то время как снижение на 5–500 Гц является наибольшим.В диапазоне 5–500 Гц компрессионные характеристики ППУФ снижаются с повышением качества блока масс и виброускорения. Это свидетельствует о том, что степень повреждения образцов в диапазоне 500–1000 Гц наименьшая, а степень повреждения образцов thd в диапазоне 5–500 Гц является наиболее серьезной. Кроме того, увеличение массы блока и ускорения увеличивает степень повреждения образца. Принципиальная схема форм разрушения ячеистой призмы (включая микротрещины) жесткого пенополиуретана. 4.3. Поглощение энергии жестким пенополиуретаномВибрация и столкновения часто возникают при упаковке и транспортировке. В этот момент энергия поглощается в основном за счет амортизационной деформации пенополиуретана. Деформация в основном достигается за счет текучести призмы ячейки и сжатия тела ячейки, и повреждение тела ячейки пены имеет большое влияние на деформацию. Поэтому оценка способности жесткого пенополиуретана поглощать энергию имеет большое практическое значение.Используя методы, представленные U. E. Ozturk и G. Anlas [27], были получены диаграмма поглощенной энергии-деформации и диаграмма эффективности поглощения энергии-напряжения для RPUF, обработанного в различных условиях вибрации. Эти две кривые используются для отражения поглощения энергии пеноматериалами во время сжатия. Как показано на, где a, b показывают кривую поглощенной энергии-деформации и кривую эффективности поглощения энергии-напряжения в трех диапазонах частот, c, d представляют собой образцы пенопласта с блоками разной массы в диапазоне частот 5–500 Hz и e, f показывают поглощение энергии образцами с различными виброускорениями в диапазоне частот 5–500 Гц соответственно.Можно видеть, что энергия поглощения образцов без вибрации постоянно увеличивается по мере увеличения деформации, когда деформация ниже 0,6, но она быстро увеличивается, когда деформация выше 0,6 и ниже 0,7. Это привело к переходу от платформенной стадии к стадии уплотнения между деформациями 0,6 и 0,7, что привело к резкому увеличению количества поглощенной энергии. С другой стороны, эффективность поглощения энергии образцом, который не вибрировал, резко возросла примерно на 2 МПа, а когда она достигла максимума, эффективность поглощения энергии постепенно снизилась.Это связано с тем, что RPUF постепенно деформируется с увеличением сжимающей нагрузки, а его кривая напряжения-деформации имеет стадию платформенной зоны. Величина напряжений в платформенной зоне практически не меняется с увеличением деформации. В это время больше энергии поглощается единичным напряжением. После достижения стадии уплотнения величина напряжения резко возрастает с увеличением деформации. Однако энергия, поглощаемая на единицу напряжения, уменьшается. Следовательно, существует максимальная эффективность поглощения энергии в процессе перехода от стадии платформы к стадии уплотнения, и соответствующее значение напряжения является отправной точкой стадии уплотнения. Для сравнения, из а можно найти, что наклон кривых поглощенной энергии-деформации образцов в трех диапазонах частот меньше, чем у исходных образцов, но наклон образца в диапазоне 500–1000 Диапазон Гц выше, чем у образцов в двух других частотных диапазонах. Это предполагает, что свойства поглощения энергии RPUF все уменьшаются в трех различных частотных диапазонах колебаний, а уменьшение образцов в диапазоне 500–1000 Гц было относительно меньшим.Кривые поглощенной энергии-деформации для различных блоков массы и виброускорения демонстрируют аналогичную тенденцию изменения по сравнению с кривыми для различных частот вибрации, соответственно. Из c видно, что наклон кривой поглощенной энергии-деформации образца уменьшается с увеличением массы блока в диапазоне 5–500 Гц, но наклон блока массы 10 кг в основном такой же, как что 20 кг, показывая, что влияние небольшой массы блока на свойство поглощения энергии RPUF очевидно.На рисунке e наклон кривых поглощенной энергии-деформации для образцов с ускорениями 2 g и 4 g близок к наклону для образцов без вибрации. Однако, когда ускорение составляет 8 g, наклон кривой поглощенной энергии-деформации значительно уменьшается по сравнению с образцом без вибрации, указывая на то, что только более высокое виброускорение оказывает очевидное влияние на характеристики поглощения энергии. Кривая поглощенной энергии-деформации ( a , c , e ) и кривая эффективности поглощения энергии-напряжения ( b , d , f ) RPUF в различных условиях вибрации, ( a , b ) Различные диапазоны частот, ( c , d ) Различные блоки массы, ( e , f ) Различные ускорения. Поглощение энергии RPUF в процессе сжатия в основном обеспечивается платформой. В сочетании с разделом 4.2 можно обнаружить, что тенденция изменения наклона кривой поглощенной энергии-деформации аналогична напряжению платформы. Чем выше нагрузка на платформу, тем больше энергии поглощает пена и тем выше наклон кривой поглощенной энергии-деформации. В основном это объясняется степенью повреждений, вызванных разными условиями вибрации, не одинаковыми.Ячейки разрыва неспособны поглощать внешнюю энергию, и образцы быстро переходят от стадии платформы к стадии уплотнения, что приводит к уменьшению напряжения платформы и наклона кривой поглощенной энергии-деформации. Значение напряжения, соответствующее максимальной эффективности поглощения энергии (Pm) в b, d, f, определяется как начальное напряжение (σD) на стадии уплотнения. Следовательно, начальная деформация (εD) стадии уплотнения может быть определена с помощью, а полная поглощенная энергия (WD) перед стадией уплотнения может быть получена с помощью кривой поглощенной энергии-деформации в a, c, e.В, показаны параметры эффективности поглощения энергии, полученные статистическим путем. Хорошо видно, что при различных условиях вибрации все εD на стадии уплотнения немного меньше, чем у исходного образца, что указывает на то, что стадия уплотнения образца, обработанного вибрацией, появляется несколько раньше. Точно так же по сравнению с невибрирующими образцами максимальная эффективность поглощения энергии (PD) образцов в различных условиях вибрации также немного снижается.Это связано с тем, что начальная деформация и максимальная эффективность поглощения энергии на стадии уплотнения изменяются из-за повреждения в процессе вибрации. Свойства поглощения энергии сжатия RPUF в различных условиях вибрации, ( a , b ) Различные диапазоны частот, ( c , d ) Различные блоки массы, ( e , f ) Различные ускорения. В трех различных частотных диапазонах начальное напряжение (σD) стадии уплотнения и WD образцов в группе 500–1000 Гц в начальной точке стадии уплотнения незначительно увеличиваются.Они уменьшились на 3,3% и 10,0% соответственно по сравнению с образцами без вибрации. Это объясняется изменением напряжения платформы, которое приводит к уменьшению напряжения и поглощенной энергии в начальной точке стадии уплотнения. Кроме того, также можно обнаружить, что в диапазоне частот 5–500 Гц σD и WD все уменьшаются с повышением качества блоков массы и виброускорения. При массе блока 10 кг эти два рабочих параметра равны 2.45 МПа и 1,00 × 10 6 Дж / м 3 , уменьшение на 6,4% и 6,5% по сравнению с блоком без массы (0 кг) при ускорении 8 g и времени вибрации 1 час соответственно. При одинаковой массе (20 кг) виброблока и времени вибрации (1 ч) два параметра образца с ускорением 4 g снижаются на 2,8% и 7,1% соответственно по сравнению с параметрами образца 2 г соответственно. При случайной вибрации жесткий пенополиуретан многократно сжимается массовыми блоками.По мере повышения качества массового блока постепенно усиливается инерционность массовых блоков, что усугубляет повреждение жесткого пенополиуретана. Что касается эффекта, то изменение ускорения происходит из-за увеличения ускорения, что усиливает действие давления-сжатия блока масс на жесткий пенополиуретан. Таким образом, повреждение РППФ усугубляется. Ячейки в пене на стадии платформы изгибаются и текут, а микротрещины растут, что приводит к изгибу и разрушению призмы.С одной стороны, это приводит к продвижению стадии уплотнения, и напряжение, необходимое для достижения стадии уплотнения, уменьшается. Сломанные призмы, с другой стороны, стоят в шахматном порядке, что, наоборот, приводит к увеличению количества призм под нагрузкой, что увеличивает жесткость RPUF и в некоторой степени замедляет уменьшение поглощения энергии. . 4.4. Конечно-элементное моделирование процесса вибрации жесткого пенополиуретанаСлучайный процесс вибрации RPUF в трех различных частотных диапазонах моделируется с помощью коммерческого программного обеспечения ABAQUS 6.16. Посредством модального анализа были проанализированы вибрационные характеристики RPUF в трех частотных диапазонах и получены режимы. Было обнаружено, что вершина конечно-элементной модели имела наибольшее смещение вдоль направления колебаний в каждой моде. Одна из вершин (обозначенная как точка A, см.) Конечно-элементной модели была выбрана для исследования в этой статье. Анализируя перемещение и скорость в точке A, можно получить деформацию конечно-элементной модели в трех частотных диапазонах, что закладывает основу для последующего стационарного динамического анализа.Степень деформации конечно-элементной модели в некоторой степени отражает повреждение образца в процессе случайной вибрации. Когда деформация модели серьезна, повреждение образца также является серьезным, что приводит к значительному снижению его свойств сжатия и поглощения энергии. В этой статье кривые смещения (a, c, e) и скорости (b, d, f) точки A использовались для характеристики деформации модели. В статистической зависимости между смещением и частотой и между скоростью и частотой определяется спектральная плотность мощности смещения и скорости, соответственно.На основе анализа спектральной плотности мощности смещения точки A деформация конечно-элементной модели в трех частотных диапазонах. a, c, e, на котором показано смещение спектральной плотности мощности точки A, можно получить в частотном диапазоне 5–500 Гц, 500–1000 Гц и 1000–1500 Гц соответственно. Кривые смещения ( a , c , e ) и скорости ( b , d , f ) оси z в точке A модели конечных элементов в трех диапазонах частот , ( a , b ) 5–500 Гц, ( c , d ) 500–1000 Гц, ( e , f ) 1000–1500 Гц. Для сравнения, максимальное значение смещения отклика в точке A в частотном диапазоне 5–500 Гц больше, чем в двух других частотных диапазонах, за которыми следует диапазон 500–1000 Гц. Кроме того, максимальное значение смещения отклика в точке А в диапазоне 1000–1500 Гц является наименьшим. Предварительно можно сделать вывод, что наибольшая деформация образцов ППУФ находится в диапазоне 5–500 Гц, а наименьшая — в диапазоне 1000–1500 Гц. Кроме того, также можно увидеть, что есть двойные пики и впадины в диапазоне 5–500 Гц и 1000–1500 Гц, и только одна пара пиков и впадин в диапазоне 500–1000 Гц.Это свидетельствует о том, что в диапазоне 5–500 Гц и 1000–1500 Гц смещение отклика случайной вибрации изменяется чаще; то есть времена деформации конечно-элементной модели более часты в этих двух частотных диапазонах. Однако в диапазоне 500–1000 Гц смещение отклика меняется меньше, поэтому времена деформации меньше. С увеличением степени деформации и увеличением времени деформации в процессе вибрации более вероятно возникновение трещин по краям ячеек и разрыва ячеек из-за давления массивных блоков.Поэтому повреждение модели наиболее серьезно в диапазоне 5–500 Гц, а повреждение модели наименьшее в диапазоне 500–1000 Гц. Кроме того, в диапазоне 1000–1500 Гц деформация модели минимальна, но бывают многократные деформации, которые усугубляют повреждение модели. b, d, f показывает спектральную плотность мощности скорости точки A в частотном диапазоне 5–500 Гц, 500–1000 Гц и 1000–1500 Гц соответственно. Анализируя максимальную скорость отклика модели и ширину желоба, можно сделать вывод о скорости деформации модели в трех частотных диапазонах.В диапазоне 5–500 Гц модель имеет один гребень и две впадины, среди которых впадины наиболее резкие. Это указывает на то, что модель имеет две малые и быстрые частоты деформации в диапазоне 5–500 Гц, и повреждение RPUF относительно велико. Однако есть два широких провала в диапазоне 1000–1500 Гц. Это говорит о том, что две области частот деформации модели в этом диапазоне являются широкими; то есть время деформации велико, что углубляет повреждение модели. В модели всего один желоб в диапазоне 500–1000 Гц.Проведя приведенный выше анализ, можно также сделать вывод, что повреждение моделей в диапазоне 5–500 Гц и 1000–1500 Гц является относительно серьезным, в то время как повреждение моделей в диапазоне 500–1000 Гц является относительно небольшим. . Кроме того, в, частоты точки максимального смещения в трех частотных диапазонах составили 114,5 Гц, 554,0 Гц и 1085,0 Гц соответственно. Для реализации распределения напряжений модели при максимальной деформации был проведен стационарный динамический анализ конечно-элементной модели.Для анализа моделирования случайной вибрации были выбраны три частотные точки: 114,5 Гц, 554,0 Гц и 1085,0 Гц. В с увеличением частоты форма деформации модели изменяется от одного направления изгиба до комбинации трех направлений. Модель изгибается один раз в направлении оси x с частотой 114,5 Гц. При 554,0 Гц модель изгибается дважды в направлении оси x, а при 1085,0 Гц модель изгибается сложным образом. Чем сложнее деформация, тем больше частей деформации присутствует в пене.Это означает, что чем шире диапазон деформации, тем выше вероятность разрушения образца. С другой стороны, в сочетании с образцом с простой формой деформации более вероятно возникновение большего смещения отклика. Облако напряжений Мизеса модели конечных элементов, ( a ) 114,5 Гц, ( b ) 554,0 Гц, ( c ) 1085,0 Гц. Кроме того, из этого также видно, что максимальные значения напряжения Мизеса в основном приходятся на изгибную деформацию моделей.Распределение напряжения Мизеса связано с деформацией модели. В качестве примера возьмем модель с частотой 114,5 Гц. Напряжение по Мизесу начинается с положения изгиба и уменьшается с обеих сторон. При 114,5 Гц и 554,0 Гц режим деформации модели относительно прост с меньшим количеством положений изгиба, что приводит к широкому диапазону распределения напряжений по фон Мизесу и большому количеству областей с низким напряжением. Однако при 1085,0 Гц деформация модели имеет сложную форму с большим количеством изгибаемых частей, в результате чего большая часть напряжения Фон Мизеса приходится на место деформации изгиба и несколько областей с низким напряжением.Следовательно, это означает, что распределение напряжения Фон Мизеса при 1085,0 Гц относительно центрировано, и повреждение жесткого пенополиуретана от случайной вибрации относительно велико. Среди них значения напряжения модели при 114,5 Гц и 554,0 Гц обычно намного больше, чем при 1085,0 Гц, что является причиной большой деформации жесткого пенополиуретана на этих двух частотах. Подводя итог, деформация, вызванная случайной вибрацией, является наибольшей в диапазоне 5–500 Гц, концентрация напряжений также наибольшая, а структурные повреждения RPUF являются наиболее серьезными.Однако количество деформационных изменений модели в диапазоне 500–1000 Гц наименьшее, а также наименьший диапазон концентрации напряжений. Следовательно, повреждение РППЧ в диапазоне 500–1000 Гц наименьшее. Они согласуются с результатами тестирования сжатия. Это указывает на то, что деформация и концентрация напряжений RPUF в процессе вибрации являются основными причинами разрушения пены. Пенополиуретан с сетчатой структурой | UFP TechnologiesПористость сетчатых пенопластов жизненно важна при разработке нестандартного компонента или продукта.Технический опыт UFP Technologies поможет вам при выборе подходящего материала для вашего компонента. Технология пенывключает манипуляции с тысячами пластиковых пузырей (называемых ячейками) точно контролируемого размера. Ретикуляция — это постпроцесс при производстве пены, при котором удаляются оконные мембраны ячейки. Ячейки, из которых состоит пена, могут иметь множество вариаций, которые также можно точно контролировать. Разные пеноматериалы имеют разную структуру ячеек и характеристики, но пеноматериалы из одного и того же семейства материалов также могут быть изготовлены с совершенно разными характеристиками плотности и твердости, что значительно повлияет на их характеристики. Существует два метода ретикуляции: термический, называемый « закалка, », и химический, называемый « закалка, ». Чтобы узнать о различиях между этими двумя методами, ознакомьтесь с нашим сообщением в блоге здесь. Области применения
Сетчатая пена может действовать как фильтр.Фильтровальная пена представляет собой сетчатую полиуретановую пену, специально адаптированную для фильтрации воздуха и жидкостей, в диапазоне контролируемых ячеек от 10 пор на дюйм до 100 PPI. Пенопласт со средней пористостью 45 PPI работает как фильтр с глубокой загрузкой, в отличие от фильтра с поверхностной загрузкой, улавливая частицы пыли внутри своей ячеистой структуры. Поскольку в процессе ретикуляции остается каркасная структура пены, остается 97% объема пустот, что дает ему большую площадь поверхности для столкновения с частицами пыли.Сетчатый поролоновый фильтр с его однородной и однородной структурой ячеек может быть спроектирован с учетом падения давления и эффективности фильтрации за счет изменения размера пор. Сетчатая пена с крупной пористостью, 10 PPI, эффективна в качестве шумоглушителя, скруббера, моющейся фильтрующей среды для кондиционеров, печей, небольших двигателей и автомобильных воздухоочистителей, а также для многих других применений. При сжатии сетчатой пены материал приобретает новый набор свойств, идеальный для других применений, требующих больших объемов пустот, однородной пористости, ненаправленных характеристик, исключительной воздухопроницаемости и однородной текстуры.Сетчатую пену часто сжимают и используют для создания чернильных валиков, фильтров крови и других продуктов, требующих впитывающих свойств. Полиэфирная пена Полиэфирная пена |