Арболитовые блоки своими руками: пропорции для производства
В условиях, когда цены на все растут, люди все чаще прибегают к старым проверенным «дедовским» методам. Не обошла эта тенденция и строительство.
Стоимость теплоизоляции растет вместе с ценой и на другие стройматериалы. Поэтому в последние два-три года былая популярность возвращается к арболиту, который также еще называют древобетоном. Причина не только в его изоляционных качествах, но и в относительной дешевизне. И, конечно же, в том, что изготовить арболитовые блоки можно своими руками.
Арболитовые блоки своими руками
Содержание статьи:
Арболит: достоинства и недостатки
Арболит – это легкие стеновые блоки, сделанные из смеси деревянной щепы, цемента и химических смесей-уплотнителей.
Арболит использовался в СССР еще в 60-х годах прошлого века и ценился советскими строителями за легкость и неприхотливость. Но рынок диктует свои условия: со временем древобетон заменили более современные виды теплоизоляционных блочных материалов. Сейчас технология изготовления реанимируется, и арболит стал снова появляться в магазинах. Однако не всегда получается найти его в свободной продаже. Поэтому актуальна тема, как делать арболитовые блоки своими руками.
В состав древобетона входит четыре основных компонента:
- Цемент.
- Древесная щепа.
- Вода.
- Химические связывающие присадки.
ВАЖНО: не надо путать арболит с опилкобетоном. Это разные материалы с различными параметрами и областями применения. В опилкобетоне основным заполнителем являются, как понятно из названия, опилки. В арболит тоже входят отходы древообработки. Но это древесная щепа строго определенных размеров – не более 40х10х5 см. Такие параметры прописаны в ГОСТ 19222-84.
Разберемся с несколькими основными параметрами арболита:
- Теплопроводность .
В зависимости от плотности блока, теплопроводность материала варьируется от 0,08 до 0,14 Вт/м°C (чем выше плотность – тем выше теплопроводность). Эта характеристика значительно превосходит теплопроводность керамического кирпича (0,06-0,09 Вт/м°C). Поэтому дом, утепленный арбоблоками, будет теплым. Для зон с умеренным климатом вполне хватит толщины кладки в 30-35 см.
- Водопоглощение. Оно находится в пределах 40-85% (опять же в зависимости от марки и плотности арболита). Это очень высокий показатель: блок помещенный в воду способен впитать в себя несколько литров влаги. Соответственно при строительстве необходимо продумывать гидроизоляцию. Кладку нужно отсекать как от фундамента, так и от внешней среды с помощью наружной отделки.
- Гидроскопичность (способность накапливать водяной пар из воздуха). За счет высокой пропускающей способности (вентилируемости) древобетон практически не скапливает водяной пар. Поэтому арболит отлично подходит для утепления домов при влажном климате – теплоизоляционный материал не будет сыреть.
- Морозостойкость. Она составляет от 25 до 45 циклов. Существуют особо плотные марки арболита с морозостойскостью до 50 циклов. Для частных домов, в которых живут круглый год этот показатель не играет особой роли. А вот для дачных и других сезонных строений подобный показатель морозостойкости означает, что блоки выдержат минимум 25-кратное замерзание и оттаивание. Что говорит о довольно высоких сроках эксплуатации зданий.
- Усадка. У древобетона она одна из самых низких – не более 0,5%. Геометрия арболитовых стен практически не изменяется со временем от нагрузок.
- Прочность при сжатии. Диапазон здесь большой – от 0,5 до 5 МПа. То есть, если вы уроните арболитовый блок, и на нем образуется глубокая вмятина, то спустя какое-то время она исчезнет – блок примет первоначальный вид. Таким образом, арболит крайне тяжело разрушить.
- Прочность на изгиб – 0,7-1 МПа. В принципе, этот показатель считается выше среднего. Арболит прощает множество ошибок при заливке фундамента – если он будет садиться, то кладка не лопнет и скроет перекос конструкции.
- Огнестойкость класса Г1. Древобетон не поддерживает горение, что делает его одним из наиболее безопасных материалом среди конкурентов.
Все вышеперечисленное позволяет судить о плюсах и минусах арболита. Начнем с недостатков. По сути, их только два:
- Высокая степень водопоглощения. Эта проблема решается отсечной гидроизоляцией, а также водоустойчивой наружной отделкой.
- Арболит любим грызунами за натуральность и способность удерживать тепло. Избавиться от этого эксплуатационного недостатка поможет цоколь высотой от полуметра и более.
А теперь перейдем к преимуществам древобетона:
- Высокие технические показатели, перечисленные выше.
- Низкая стоимость.
- За счет пористой органической структуры арболит практически не пропускает внешние шумы. То есть, со звукоизоляцией проблем тоже не будет.
- Легкость материала – от 400 до 900 кг на кубический метр. Это достоинство позволяет сэкономить не только на транспортировке к месту строительства, но и на фундаменте.
Арболитовому дому попросту не нужно тяжелое основание из-за небольшого веса несущей коробки.
- Арболит отлично подходит для возведения зданий в зонах повышенной сейсмической активности. Из-за пластичности и высоких амортизационных свойств нагрузки нагрузки не вызовут разрушение здания.
- Экологичность. За счет состава и паропроницаемости в древобетоне на образуются грибок или плесень. Как уже отмечалось, единственной проблемой могут стать грызуны. К тому же арболит аморфен – он не вступает в реакцию с атмосферой или декоративными строительными смесями, не выделяет токсичные вещества.
- Высокая степень адгезии – стена из арболита не требует дополнительного армирования и отлично подходит практически для всех видов наружной отделки.
- Простота обработки арболитовых блоков – он отлично пилится без специальных средств (обычной ножовкой), не крошится при сверлении, держит саморезы и гвозди.
- Если вы делаете арболитовые блоки своими руками, то благодаря пластичности исходной массы можете сформировать элементы практически любой формы и размера.
Что дает простор для дизайна геометрии помещений.
Видео — изготовление арболитовых блоков своими руками
Делаем древобетон сами: инструкция для начинающих
Перед тем, как перейти непосредственно к пошаговому изготовлению арбоблоков, стоит оговорить несколько нюансов:
- Для арболита НЕЛЬЗЯ использовать опилки. Только щепу.
- Для получения заполнителя подойдут практически любые отходы деревообработки – горбыль, сучья, обрезки бруса, верхушки деревьев.
- Если вы планируете использовать в конструкции здания крупногабаритные арболитовые блоки (например, длинные поперечные балки), то стоит позаботиться об их дополнительном армировании. Речь идет не только о каркасе прочности, но и о такелажных петлях для облегчения транспортировки.
Обратите внимание: лучшей древесиной для арболитовых блоков считаются хвойные породы: сосна, ель.
Из лиственных подойдут береза, тополь, осина. Категорически не рекомендуется использовать для изготовления древобетона отходы из лиственницы, бука, карагача.
Состав
Для арболита используют цемент высоких марок – М-400 и М-500. Обязательно следите за свежестью и сухостью цемента.
Щепа, как уже упоминалось, должна быть измельчена до определенных размеров – 25х8х5 мм (оптимум) или 40х10х5 (максимум) мм. Старайтесь избегать высокой концентрации пересорта – из-за него конечная прочность арбоблока будет снижаться.
В качестве химических добавок используются:
- Пищевая добавка Е509 – хлорид и нитрат кальция.
- Сернокислый алюминий.
- Жидкое стекло.
- Вода используется питьевая (из-под крана). Не стоит делать арболитовую смесь, используя воду из водоемов – грязь и другие примеси дестабилизируют соединительные связи между компонентами блока, что вызовет его преждевременное разрушение.
ВАЖНО: Соблюдайте порядок действий при смешивании ингридиентов. Крепко запомните: сначала смешиваем воду и химические примеси, потом добавляем туда щепу и только после ее равномерного намокания добавляем цемент.
Размерность арболитовых блоков
Арбоблоки классифицируют по плотности на:
- Конструкционные – от 500 до 850 кг/м3.
- Теплоизоляционные – до 500 кг/м3.
Какие блоки вы будете применять, напрямую зависит от возводимого здания. Для здания в два этажа или же одноэтажного дома с цоколем или мансардой следует использовать конструкционные блоки плотностью от 600 кг/м?. Для обычного одноэтажного строения без дополнительных уровней подойдут самые легкие конструкционные блоки – 500 кг/м3. Теплоизоляционные блоки обычно не используют для возведения стен. Их используют в качестве дополнительной защиты от холода, обкладывая стены из других материалов.
Стандартный размер арболитового блока – 50х20 см. А вот толщина варьируется от 10 до 50 см. Но вы сами можете предусмотреть другие габариты, которые подойдут непосредственно для вас.
С типовыми габаритными параметрами блоков из древобетона вы можете из приведенной ниже таблицы:
Также стоит учитывать прочность арболитовых блоков сделанных своими силами. Она делится на классы. Если вы планируете своими руками возводить из арболита жилой дом, то вам нужен максимальный класс прочности В2,5:
Видео изготовление арболитовых блоков
Пошаговая инструкция
Итак, приступаем к производству арболитовых блоков своими руками.
Пропорции для смешивания компонентов берем из данной таблицы:
Обратите внимание: древесная стружка (щепа) должна быть избавлена от сахара, иначе он начнет бродить и вызовет разрушение блока. Его, конечно, можно вывести химическим путем.
Но обычно щепе просто дают три месяца полежать на воздухе. Помните это при подготовке сырья для арболитовой смеси.
- Вам понадобиться бетономешалка принудительного типа. Можно использовать обычную «грушу», но качество перемешивания будет ниже.
- Добавьте химические присадки в воду в необходимой пропорции. Тщательно перемешайте.
- Высыпайте опилки. Немного перемешайте. Дождитесь, чтобы они полностью намокли, не оставалось сухих «островков».
- Начинайте порционно добавлять цемент. Ни в коем случае не засыпайте весь объем сразу – будет очень сложно справиться с комкованием.
- Чередуя перемешивание и добавление цемента, добиваемся равномерного обволакивания опилок получаемой смесью. Это возможно только в том случае, когда опилки достаточно намокли.
- Когда у вас получится однородная смесь, ее можно начинать раскладывать в формы.
- Если у вас есть формовочный станок с вибромотором, то процесс значительно упрощается. Вам остается только загружать сырье, ждать и извлекать готовый блок.
- Но в кустарных условиях чаще всего пользуются самодельными формами и ручным прессованием (в лучшим случае — вибростолом).
- Форма представляет собой металлический ящик без дна. Его ставят на ровную поверхность (доску, к примеру) и начинают заливать смесь. Если вы используете ручное прессование, то делать это следует слоями. Количество слоев зависит от высоты формы. Обычно делают не меньше четырех-пяти слоев.
- Каждый слой трамбуют металлической площадкой с ручкой (желательно, чтобы она совпадала по площади с сечением формы). Чтобы из смеси лучше выходил воздух его протыкают в нескольких местах арматурой, после чего снова трамбуют.
- Мы советуем вам сделать (или приобрести) рычажный механизм для прессования. Тогда вы сможете лучше регулировать плотность получаемого на выходе блока. К тому же в этом случае можно заливать сразу весь объем смеси в форму. Это значительно ускорит процесс изготовления.
- Если вам необходимы блоки высокой плотности, то в процессе трамбовки чередуйте слабый и сильный нажим.
При такой методике распрессовка (изменение формы из-за упругости раствора) проявляется слабее, блоки получаются более прочными.
- После окончания трамбовки уберите излишки раствора металлическим скребком.
- Вибрация еще больше способствует прочности готового строительного материала. Если у вас есть вибростол, то рычажный механизм не нужен. Просто ставите на поверхность стола форму, загружаете арболитовую смесь, помещаете сверху груз и включаете вибрацию.
- После окончания формирования блока, его переносят к месту сушки. Когда у вас достаточно плотная смесь, с сырого блока можно снять форму. Но при изготовления низкоплотных блоков из древобетона раствор слишком жидкий и теряет свою геометрию. В этом случае озаботьтесь созданием достаточного количества форм для того, чтобы не терять время.
- Летом сушить арбоблоки можно и на улице на протяжении 15-20 дней. Но по технологии им положено двухсуточное выдерживание в помещении с температурой 60 °C.
После всего этого блоки, в принципе, готовы к использованию в строительных работах. При необходимости их можно подвергнуть механической обработке для придания нужной формы.
Вместо послесловия
В завершение мы подготовили вам небольшой дайджест из нюансов, которые помогут вам сделать арболитовые блоки своими руками:
- Щепу для арболитовых блоков можно произвести самостоятельно при наличии необходимых станков – рубительной машины и дробилки. Но можно ее приобрести на близлежащих деревообрабатывающих предприятиях или в цехах по производству арбоблоков.
- Для того, чтобы легче вынимать блоки, обейте внутренние стенки формы линолеумом или другим гладким и тонким материалом.
- Когда нужно изготовить конструкционный арболит максимальной прочности, следует провести гидратацию. Для этого положите готовый блок под пленку на 10 дней при 15 C.
- Если вы используете арболит не для возведения стен, а для утепления уже построенного здания, некоторыми точностями в технологии изготовлении смеси и блоков можно пренебречь. Но не переусердсвуйте.
- Если вы избавляетесь от сахара в стружке посредством выдерживании на воздухе, не забывайте ее перемешивать.
- Существует способ сразу же подготовить арболитовые блоки к наружной отделки. Для этого после трамбовки на верхнюю часть блока наносят слой штукатурки и равняют шпателем.
- Если у вас нет специального помещения для сушки с нужным температурным режимом, то высыхание блоков на открытом воздухе займет не менее двух недель.
Состав смеси и пропорции для арболитовых блоков
По мере того как технический прогресс двигается вперед, появляются все новые материалы для строительства домов своими руками. Если раньше дело ограничивалось деревом, камнем или кирпичом, то сегодня существуют различные виды бетона, которые превосходят другие материалы по характеристикам. Одним из таких материалов является арболит. Это уникальный материал, который вместил в себе преимущества как бетона, так и древесины. Его состав достаточно прост, и вы можете приготовить раствор своими руками. Примечательно, что он может использоваться как обычный бетон, путем заливки смеси в опалубку, а может быть, сделан в виде блоков, для обычной кладки. Арболитовые блоки можно купить в специализированном магазине, или приготовить раствор своими руками, сделав блоки из готовой смеси.
Все что нужно – знать точный состав арболита, пропорции для смешивания смеси и технологию его приготовления. Давайте рассмотрим все детальней.
Арболитовый блок – из чего он состоит
Арболит, из которого формируют арболитовые блоки для кладки, состоит из 3 основных компонентов:
- заполнитель;
- минеральное вяжущее;
- химические добавки и вода.
Путем соединения всех этих элементов получается арболитовый раствор, который впоследствии используется для формирования блоков. Состав достаточно простой и каждый сможет сделать материал для своих целей. Сам по себе материал легкий, поэтому блоки идеально подходят для кадки. Их достоинством, по сравнению с газоблоками и пеноблоками, является большая граница прочности. Они стойкие к трещинам и ударам.
Несмотря на то что главным компонентом является древесные опилки (щепа), арболит высоко ценится и не уступает по характеристикам традиционным материалам. Наоборот, арболитовые блоки хорошо сохраняют тепло и создают хороший микроклимат в помещении.
Органический заполнитель
Львиную долю в составе арболитных блоков занимает древесная щепа. Это основной материал, который входит в его состав. Такой органический заполнитель легко можно приобрести за небольшие деньги. Стоит обратиться в местную пилораму, где есть отходы деревообработки и договориться с работниками. Преимущественно используют хвойные породы дерева и твердолиственные. Пихта, сосна, ель, осина, бук, береза и тополь идеально подходят, чтобы сделать из них арболитовый раствор. Также можно использовать костру льна.
Чаще всего применяется древесный заполнитель: дробленка, стружка с опилками, в пропорции 1:1 или 1:2, щепа, стружка и опилки, в пропорции 1:1:1. Все пропорции измеряются в объеме. К примеру, если нужно добиться соотношения 1:2, то берется 1 ведро древесных опилок и 2 ведра стружки. Опилки легко заменяются кострой льна или конопляными стеблями, на состав это не повлияет.
Какие требования к заполнителю? Прежде всего, важно правильно подобрать их размер. Крупные опилки использовать не рекомендуется, ведь когда изделия вступят в контакт с водой, они могут увеличиться в объеме. В результате блок может разрушиться. Если же использовать слишком мелкие частицы, то увеличивается расход цементной смеси. Рекомендуемый размер частиц – 15 или 25 мм длинной и не больше 2–5 мм шириной. Сырье не должно иметь листья и другие примеси.
Предупреждение! Лиственница и свежесрубленная древесина любых пород в состав арболитовых растворов не добавляется. Это запрещено!
Костра льна
Полноценным заполнителем, добавляющимся в раствор, является костра льна. Так как в ней присутствует сахар, обязательно применяются химические добавки. Чтобы улучшить качества готовой смеси для блоков, костра заранее обрабатывается известняковым молоком, в пропорции: 200 кг костры на 50 кг извести. Затем все выдерживается несколько дней в куче, после чего все готово для производства арболита. Благодаря такой технологии расход цемента значительно уменьшается. На 1 м3 арболита требуется 50–100 кг цемента.
Важно! Если костра льна используется в обычном виде, то конопляные стебли требуют некой обработки. Их нужно предварительно измельчить.
За счет того, что в составе отходов органики есть вещества, растворимые водой, среди которых смоляные кислоты и сахар, это препятствует хорошей адгезии между частицами. Для устранения сахара, древесные щепки требуется выдержать на воздухе 3 или больше месяцев, или обработать его известняком. Во втором случае смесь выдерживается 3–4 дня. Содержимое перемешивается 2 раза на день.
Минеральное вяжущее
Вам никак не сделать раствор своими руками без вяжущего компонента. Он делает арболитовые блоки прочными и пригодными для кладки. В качестве вяжущего вещества используется портландцемент марки М400, М500 или еще выше.
Его расход зависит от вида заполнителя, крупности частиц, марки цемента, характеристик и т. д. Чтобы немного ориентироваться, можно определить расход таким образом: коэффициент 17 нужно умножить на требуемую марку арболита. К примеру, вам нужно приготовить раствор, маркой 15 (B1). В таком случае на 1 м3 арболита потребуется 255 кг цемента.
Химические добавки
Свойства, которые имеют арболитовые блоки, напрямую зависят от химических добавок. Их использование обязательно в любом случае, неважно, в каком климате выполняются работе. Благодаря добавкам, заполнитель можно использовать без выдержки, ведь они нейтрализуют сахар и другие вещества, что улучшает качество готовых блоков.
В качестве таких добавок может использоваться:
- жидкое стекло (силикат натрия). Закрывает все поры в древесине, поэтому влага не попадет внутрь.
Используется после удаления сахара;
- гашеная известь. Она расщепляет сахар и убивает микроорганизмы в опилках;
- сернокислотный алюминий. Отлично расщепляет сахар. Благодаря компоненту состав быстрее набирает прочность;
- хлористый кальций. Убивает все микроорганизмы и придает древесине противогнилостных свойства.
Сернокислотный алюминий и хлористый кальций считаются лучшими добавками. Пропорции добавок – 2–4% от массы цемента, или от 6 до 12 кг на 1 м3. Добавки можно сочетать между собой.
Пропорции для арболитовых блоков
Чтобы сделать арболитовые блоки своими руками важно знать не только состав, но и пропорции. Соотношение всех компонентов между собой следующее: 4:3:3 (вода, древесная щепа, цемент). Химические добавки – 2–4% от общей массы.
Для изготовления 1 м3 арболита своими руками, из которого будут сделаны блоки для кладки, вам потребуется:
- 300 кг древесных отходов;
- 300 кг портландцемента;
- 400 л воды.
В раствор добавляется хлористый кальций или другой химикат. Это классический состав, который легко можно сделать своими руками. Все что потребуется: бетономешалка или большая емкость для размешивания, ведра, лопаты, вилы (для перемешивания вручную) и все компоненты арболита. Процесс выполнения работ следующий:
- Наполнитель (щепу) засыпают в емкость и смачивают водой. Тогда сцепление с цементом будет лучше.
- Затем, постепенно добавляется цемент с добавками. Содержимое тщательно перемешивается в бетономешалке или своими руками, при помощи вил.
- Настало время добавлять воду, в которой уже растворены химические добавки. Все снова перемешивается.
- Как цемент, так и воду требуется добавлять не сразу, а понемногу, небольшими порциями. Так смесь будет легче перемешивать и компоненты будут лучше соединяться между собой.
- После того как сделан раствор, его нужно поместить в подготовленные формочки, чтобы они обрели вид блоков для кладки.
Это состав и пропорции смеси арболитовых блоков, которые можно сделать своими руками. Все что требуется – быть внимательным и четко придерживаться инструкций по его приготовлению. Ниже приводится таблица, которая поможет вам разобраться в том, какие есть марки арболита и каковы пропорции компонентов для его приготовления.
Какой раствор используется для кладки
Это логичный вопрос. Ведь если арболит специфический материал, то может для кладки арболитовых блоков потребуется специфический раствор? Нет. Арболитовые блоки кладутся на обычный цементный раствор, который под силу сделать любому. Он состоит из цемента, песка и воды. Соотношение компонентов – 3:1. Вода добавляется до тех пор, пока раствор не приобретет нужной консистенции. Эта смесь идеально подходит для кладки блоков своими руками.
Итак, зная состав, пропорции и технологию замешивания арболитового раствора, вы можете делать блоки для ваших целей.
Мицар, строительная компания, г.
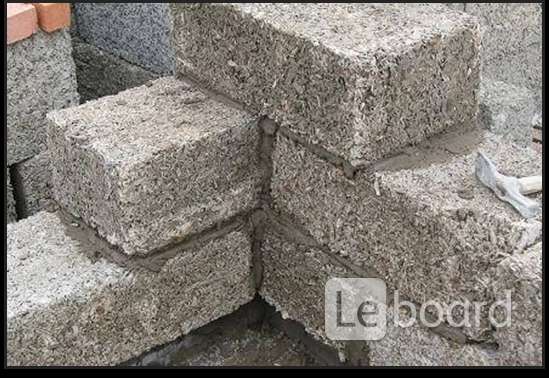
Здравствуйте уважаемые читатели!
Газобетонные блоки это один из популярных материалов в строительстве. Наряду с преимуществами: низкая стоимость, низкий вес, легкость обработки; газобетон обладает и несомненными минусами: гигроскопичность, низкая морозостойкость, хрупкость, слабое сопротивление механическим воздействиям. Если в строительном проекте эти недостатки станут критичными, то следует рассмотреть альтернативные варианты материалов для замены газобетонных блоков.
Такой заменой могут стать арболитовые блоки.
Из чего же их делают?
Основным компонентом естественно является цемент. Притом, очень важно использовать качественный цемент марки М500, в крайнем случае из цемента М400, но из максимально свежего и сохранившего качественные свойства.
Второй по значимости компонент, придающий арболитовым блокам их основные свойства, это щепа дерева. ГОСТ не регламентирует древесину, а только фракцию, она должна быть строго 40*10*5мм. Абсолютно не допускается замена щепы опилками, стружками или соломой.
При замешивании рабочего раствора в воду добавляют специальные химические добавки повышающие адгезию щепы с цементом.
В зависимости от плотности, арболитовые блоки разделяют на теплоизоляционные с удельным весом до 500 кг на кубический метр, и конструкционные – от 550 до 700 кг на кубометр.
Одно из главных преимуществ арболитовых блоков хорошие теплоизоляционные свойства. ГОСТ считает достаточной толщину стены из арболита всего 380мм, для надежного сохранения тепла зимой в средней полосе.
Интересны свойства этого материала при попадании влаги. Вода легко проходит сквозь ячеистую структуру блока, не задерживаясь, что позволяет арболиту быстро высыхать и избегать температурных разрушений.
Арболит имеет схожую с другими типами ячеистых блоков прочность на сжатие, но в разы прочнее на изгиб. Модуль упругости арболитовых блоков 2200 – 2300МПа, что позволяет избегать образования трещин при подвижках грунта.
Подходит для использования во влажной среде, так как минерализованная щепа не поглощает воду, а пористая структура обеспечивает быстрое высыхание влаги. Как следствие, арболит выдерживает большое количество циклов замораживания и размораживания.
У арболитовых блоков почти полностью отсутствует усадка. Редкое уменьшение (в основном из-за быстрого перехода блока из производства в строительство) не превышает 0,5%, что никак нельзя назвать критичным.
Соответствует всем нормам пожарной безопасности – малогоорючий, трудновоспламеняемый и малодымный материал.
Хорошая паропроницаемость – до 35 процентов. Это позволяет избегать сырости, запотевания и образования конденсата.
В отличие от газобетона, арболит хорошо справляется с механическими и силовыми нагрузками. Разнонаправленное положение щепы в блоках повышают несущую способность материала. Можно без опаски вкручивать саморезы и забивать гвозди.
Идеальных строительных материалов пока не существует, поэтому арболитовые блоки тоже имеют свои недостатки.
Два главных минуса связаны непосредственно с производством блоков. Например, отступление от технологий может вызвать снижение всех характеристик материала. Также, очень сложно выдерживать точную геометрию. Поэтому выбирайте блоки только проверенных производителей.
Эксплутационных недостатка тоже два: нужно защитить материал от постоянного воздействия воды во избежание вымывания цемента, и использовать для отделки материалы с хорошей воздухопроницаемостью.
Какие можно сделать выводы?
Арболитовые блоки отличная альтернатива газобетону и позволяют действительно сэкономить средства при строительстве, в сравнении с традиционными кладочными материалами. Но это верно только при условии качественного производства с соблюдением всех необходимых технологий.
До свидания и удачи Вам при выборе строительного материала!
Себестоимость арболита и калькуляция
Перед запуском производства необходимо рассчитать материальную себестоимость продукта, который будет выпускаться.
Рассмотрим подробнее каждое направление. Брать за рекомендацию на 100% данное описание не стоит, так как в каждом регионе ввиду индивидуального развития, может быть иная картина, как на строительном рынке, так и в оптово-розничной торговле строительных материалов. И назвать более точные сроки окупаемости собственного производства, можно будет только при тщательном изучении рынка и детальном расчете себестоимости выпускаемого продукта. Если по первому направлению все понятно, то есть известна цена на комплекс оборудования и остается заложить срок окупаемости в месяцах, чтобы разделить сумму потраченных средств на данный срок, то со вторым и третьим направлением разберемся подробнее.
Распределение средств на аренду или приобретение производственного помещения закладывает хозяин производства по своему усмотрению. Факторов влияющих на данное направление предостаточно. В первом разделе нашей статьи, мы подробно описали все тонкости в выборе производственного помещения. Когда помещение выбрано, и мы знаем, сколько оно нам обходится ежемесячно, приступаем к его запуску. Для запуска производства необходимо провести предварительный детальный анализ на бумаге — произвести размещение основного и вспомогательного оборудования, необходимых помещений, зон для хранения, складирования сырья, рабочей оснастки и выпущенной продукции, рабочих мест для выполнения тех или иных рабочих операций. Также необходимо заранее обеспечить беспрепятственный въезд и выезд рабочей техники для ввоза и вывоза сырья и продукции. При работе рохлями и самоходными штабелерами необходимо произвести выравнивание поверхностей по направлению движения данных средств. Необходимо обеспечить хорошее освещение и наличие точек с напряжением 220/380 вольт для подключения вспомогательного оборудования. После того как произведен анализ, необходимо рассчитать стоимость материалов и работ на ваше производство. Данный расчет, как и первая цифра — стоимость комплекса оборудования, пойдет второй цифрой к дальнейшей калькуляции.
Третье направление самое большое по числу статей расходов к нашей калькуляции. Не будем заниматься полным описанием каждой статьи расходов, а затронем основные. В основе выпуска арболитовой продукции лежит сырьевая база, состоящая из цемента, древесной щепы и минерализатора щепы – сульфата алюминия или хлористого кальция. Каким должно быть сырье для качественного арболита, опишем чуть подробнее.
Цемент необходимо применять как можно качественней, его качество будет определять основные технические показатели будущего арболита, сэкономить на цементе – неизбежно выпустить брак. Марка должна быть не менее 500 и желательно без добавок. Есть возможность использовать более высокомарочные цементы с маркой более 500, не пугайтесь, их использование не приведет к повышению себестоимости. Расход с увеличением марки цемента снижается, а вот выгода растет, а именно позволяет арболиту в короткие сроки схватиться, что данному материалу так необходимо. Чем дольше происходит схватывание, тем больше не до растворимых сахаров находящихся в щепе будет выходить, и препятствовать схватыванию, выгода очевидна, быстрее схватывание, выше оборачиваемость форм, больше выпуск продукции. В цену цемента обязательно должна быть включена доставка, а работа, например на наливном цементе снизит цену куба готовой продукции до 20%. Работать необходимо только на свежем цементе. Ежемесячно лежалый цемент теряет марку от 50 до 100 единиц, а это увеличение сроков схватывания и набора прочности, как итог резкое снижение качества готового продукта, особенно в зимний период.
Из чего строить? Обзор арболитовых блоков.

Рассматривая в предыдущей статье тему недостатков газобетонных блоков, я получил интересный комментарий от читателя Павла: в нем он говорит о применении им в строительстве домов «арболита», т.е. арболитовых блоков. Я считаю эту тему интересной и предлагаю Вам ознакомится в этой статье с достоинствами и недостатками данного материала.
Здравствуйте уважаемые читатели!
Рассматривая в предыдущей статье тему недостатков газобетонных блоков, я получил интересный комментарий от читателя Павла: в нем он говорит о применении им в строительстве домов «арболита», т.е. арболитовых блоков. Я считаю эту тему интересной и предлагаю Вам ознакомится в этой статье с достоинствами и недостатками данного материала. Итак, начнем.
Немного остановимся на процессе изготовления этого материала, т.к. от качества изготовления зависит очень многие характеристики данного материала. Для изготовления арболитовых блоков используются следующие материалы: древесная щепа, химические добавки, вода, цемент.
1) Древесная щепа: очень важно, чтобы для производства использовалась именно щепа (размеры регламентированы ГОСТ, обычно 40х10х5мм). Опилки, стружка, солома и т.д. НЕ ПОДХОДЯТ.
2) Химические добавки: необходимы для хорошей адгезии цемента (точнее цементного молочка) с щепой.
3) Вода: здесь все понятно.
4) Цемент: достаточная для применения в строительстве прочность материала достигается только при применении цемента с маркой не ниже 400. Цемент имеет свойство быстро терять марку при хранении. Даже на выходе с завода цемент часто не соответствует заявленным характеристикам. Поэтому лучше, когда арболитовые блоки, изготавливаются из 500-го цемента.
Естественно, что при изготовлении необходимо соблюдать дозировку компонентов и технологию (с чем у нас проблема в России).
Арболит бывает двух типов: конструкционный (550-700кг/м3) и теплоизоляционный (до 500кг/м3). Теплопроводность для арболита является одним из ключевых параметров. Рекомендованная ГОСТом толщина ограждающих конструкций из арболита в умеренных широтах составляет 38 см. Но стены такой толщины возводятся редко. На практике для стен жилых домов блоки 500×300×200 мм кладут плашмя в один ряд. Вместе с внутренней и наружной отделкой этого достаточно для поддержания комфортной температуры в помещениях без появления проблем с выпадением конденсата.
В характеристиках арболита указывают величину водопоглощения до 85 % для теплоизоляционных блоков и до 75 % для конструкционных. Структура блока представляет собой склеенные цементным камнем разрозненные зерна щепы. Они ориентированы относительно друг друга случайным образом.
Итак, переходим к достоинствам данного материала:
Вода, наливаемая на поверхность блока, свободно протекает сквозь него. Естественно, что при окунании вода способна вытеснить большой объем содержащегося внутри блока воздуха. Если блок вытащить из воды, вода вытекает, а цементный камень быстро высыхает. Постепенное разрушение изделий при замораживании и размораживании происходит в результате расширения замерзающей в пустотах воды. Чем больше воды в них содержится, тем меньше циклов замораживания — размораживания способен выдержать материал без разрушения.
1) Прочность арболита на сжатие типична для ячеистых бетонов. Важным отличием является прочность блоков на изгиб, которая составляет от 0,7 до 1,0 МПа. Модуль упругости элементов может доходить до 2300 МПа. Такие величины делают арболит особенным среди ячеистых бетонов. Если для пенобетона и газобетона велика вероятность трещинообразования, то для арболита такая проблема не стоит.
2) Арболитовые блоки находящиеся в естественной среде, например в стене дома, фактически не накапливают в себе влагу из окружающего воздуха. Это происходит благодаря очень низкой сорбционной влажности материала, т. к. минерализованные щепа и цемент являются негигроскопичными и слабо смачивающимися материалами. Именно это стало причиной популярности использования материала для строительства бань.
3) Постепенное разрушение изделий при замораживании и размораживании происходит в результате расширения замерзающей в пустотах воды. Чем больше воды в них содержится, тем меньше циклов замораживания — размораживания способен выдержать материал без разрушения. Низкое сорбционное влагопоглощение дает арболиту хорошую стойкость к промерзанию.
4) Считается, что арболит совершенно не подвержен усадке. Но небольшие усадочные процессы в первые месяцы все же присутствуют. В основном они прекращаются еще на этапе созревания блока на производстве. Некритичное уменьшение размеров блока (на 0,4 — 0,8 %) возможно уже после укладки блоков в конструкцию.
5) Материал не горючий (группа горючести — Г1, т. е. это трудногорючий материал; группа воспламеняемости — В1, трудновоспламеняемый материал; по дымообразующей способности — Д1, малодымообразующий материал.
6) Арболит это дышащий материал степень его паропроницаемости составляет до 35 %. Именно поэтому в домах построенных из данного материала не бывает сырости, а микроклимат комфортный как в холодное так и в теплое время года.
7) Легко монтируется. В арболит можно вбивать гвозди и вкручивать саморезы, как в дерево (несущая способность гораздо выше, чем у пеноблока и газобетона).
Теперь о недостатках, которые тоже присутствуют, как и любого другого материала:
1) Нарушение технологии производства, что влечет за собой непредсказуемые последствия для характеристик материала.
2) Необходимость защиты от прямого воздействия влаги
3) Недостаточная точность геометрии блоков (вызывает увеличение толщины кладочных швов, и как следствие, промерзание).
4) Необходимо сочетать с арболитовой кладкой только «дышащие» варианты отделки.
Подводя итог мы получаем вполне хороший материал для строительства, но с одной принципиальной оговоркой – в процессе производства блоков не было допущено отклонений от технологии. К сожалению, этот момент никак не проверить, поэтому следует отдавать предпочтение надежным и проверенным поставщикам.
До свидания и удачи Вам в выборе строительного материала!
Оригинал статьи Вы можете прочитать здесь.
Нашли опечатку в тексте? Выделите её и нажмите ctrl+enter
Дом из арболита — есть ли будущее у блока из щепы
В соответствии с деуствующим законодательством, В России бетон с органическими заполнителями может использоваться в малоэтажном строительстве
Материал арболит — легкий бетон с органическими заполнителями (до 80-90% объема). Его изобрели голландцы примерно в 30-е годы прошлого века. Однако на самом деле идея использовать в качестве заполнителя в бетоне органику — опилки, щепу, солому и так далее — имеет более долгую историю.
В Средней Азии традиционно строили дома из самана — смеси глины и рубленой соломы. Кстати, саман до сих пор производят в частных подворьях. Из смеси глины и соломы изготавливали кирпичи, которые сушились на солнце. Так же были популярны стеновые блоки похожие формой на дыню под названием «гуваля». Они изготавливались из того же материала. Такие кирпичи и «блоки» не обладали достаточной прочностью. Но в условиях местного климата со скудными осадками они служили достаточно долго и надежно.
В СССР арболит стал популярен в 60-е годы. Был разработан ГОСТ, скопированный с технологии изготовления голландского материала под торговой маркой DURISOL. К этому времени арболит уже завоевал место на рынках Европы и Америки благодаря своей экологической чистоте, хорошим тепло- и звукоизолирующим свойствам и малому удельному весу готовой стеновой конструкции. За рубежом этот материал называется по-разному: «дюрисол» — в Голландии и Швеции, «вудстоун» — в США и Канаде, «пилинобетон» — в Чехии, «чентерибоад» — в Японии, «дюрипанель» — в Германии, «велокс» — в Австрии. Его применяют при возведении не только частных домов, но и высотных зданий промышленного назначения.
Виды блоков из арболита
Состав и тенология арболита очень просты — цемент, специальная щепа, воздухововекающая добавка. Для промышленного производства необходимо оборудование — щепорез, бетоносмеситель, формы.
Советский аналог «дюрисола» прошел все технические испытания, был стандартизирован и сертифицирован. В СССР работали более ста арболитовых заводов. Кстати, материал был использован для строительства зданий даже в Антарктиде. На станции «Молодежная » из арболитовых панелей были построены три служебных здания и столовая. Толщина стен составила всего 30 см. Минусов у такого материала практически нет, зато много плюсов. Фундаменты под него требуются такие же как и под газобетон.
Дома из арболита достаточно теплые и прочные, ведь изготавливаются такие строительные блоки в соответствии с технологией. Цена такого дома сопоставима с ценой дома из пено- газо-бетона. Но по своей сути эти дома более экологичны.
Однако в Советском Союзе арболит не стал материалом массового применения. Был взят курс на строительство крупносборных бетонно-блочных домов, для которого арболит из-за своих характеристик не подходил. В 90-е годы индустрия производства арболита в России пришла в упадок. Но состояние строений, построенных из арболита 60 лет назад, показывает, что материал вполне пригоден для использования в строительстве. Тем более, что технологии не стоят на месте.
Щепорез для арболита Оборудование для арболита
Сегодня некоторые иностранные производители выпускают арболит на основе калиброванной щепы хвойных пород с использованием бетона специальных марок. Есть технология по выводу из органики сахаров, которые «поощряют» гниение древесины, специальные способы сушки щепы. Применяются спецдобавки, повышающие прочность и долговечность арболита, улучшающие его потребительские свойства. Так что изначальные преимущества арболита — доступность компонентов и экологичность — могут быть дополнены новыми. Своими руками изготовить качественный арболит сложно, но вполне вероятно. Купить качественный арболит можно по цене 3000 — 3400 руб/м3.
В нашей стране, богатой лесом, арболит может быть отличным материалом для малоэтажного индивидуального строительства
Технология производства арболита — Каменный лес
Качественный арболит можно получить только из качественного сырья, при применении правильных технологий и специального оборудования. При этом производство арболита совершенно не похоже на производство любого другого легкого бетона, к которому он относится.
Арболит состоит из древесной щепы, химических добавок, цемента и воды. Такой нехитрый состав и простота производства не отменяют трудоемкости процесса, ведь изначально деревянные элементы материала несовместимы с цементом. Между ними нет цепкости, вследствие чего материал может рассыпаться, распадаться, ломаться. Но этого не происходит. Единство между такими разными элементами достигается посредством особых технологических моментов, которые соблюдаются не просто для получения хороших блоков, а высококачественных, соответствующих требованиям ГОСТа 19222-84
За высоким качеством щепы нужно следить
Особое внимание при изготовлении арболита требует щепа. Оптимальный вариант – это еловая и сосновая щепа. При этом ГОСТ позволяет использовать измельченную древесину, хвойные и лиственные деревья, рисовую солому, коноплю, лен, хлопчатник.
Щепа, которая используется для производства арболита, обязана обладать конкретной формой и соответствовать целому ряду требований, от конкретной длины частичек до процентного соотношения примеси листьев и коры.
Дробленный материал не может быть гнилым или заплесневелым, как и грязным, то есть – с примесью чужеродных веществ, вроде глиняного налета, земляных комков, крошки камня, песочных пещинок, льда и снега. Дробленая древесина должна иметь форму иглы определенного размера (длина, толщина), который важен для соблюдения абсолютного значения влажностных деформаций каждого волокна.
Любой цемент для арболитовых блоков не подойдёт!
Для изготовления арболита следует использовать цемент самых высоких марок. При этом следует учитывать, что характеристики цемента обычно ниже тех, что заявляет производитель. Разница порой равна 50-100 единицам.
Между щепой и цементом отсутствует сцепление. Чтобы оно появилось, щепу подвергают специальной обработке химическими веществами. Они удаляют из древесной щепы сахар, являющийся главным препятствием для сцепления двух компонентов арболита. Также химические добавки позволяют добиться более быстрого затвердевания бетона. Так, щепа может смешиваться с хлоридом кальция, сернокислым глиноземом, силикатом-глыбой, жидким стеклом, известью. Мы применяем только безопасный и химически нейтральный сульфат алюминия (пищевая добавка Е520).
Самым менее затратным, а значит, экономным способом производства арболита, считается ручная утрамбовка на полу. Изготовление таким методом требует наличия смесителя принудительного типа (который позволяет получать улучшенные блоки с добавлением композитной фибры), мерных емкостей для химических добавок, стальных форм для утрамбовки, тележки для транспортировки к формам, ровной поверхности для формирования блоков, поддонов для укладки готовых изделий.
Смешивать арболит нужно правильно
Начинается изготовление арболита с разбавления и смешивания химических веществ. Параллельно производится засыпание щепы в смеситель. При этом следует использовать только вылежавшуюся не менее пары месяцев щепу, свежую использовать ни в коем случае нельзя.
Пока щепа перемешивается, к ней добавляется водный раствор с химическими веществами. После тщательного перемешивания содержимого, в емкость засыпается цемент. Причем его следует вводить так, чтобы он максимально покрыл получаемым из него тестом всю арболитовую щепу. Когда цемент и остальные составные смеси становятся единой массой, ее заливают в формы, которые предварительно размещают на поддонах. На этом процесс производства арболита завершается.
Раздельные бетонные блоки — RCP Block & Brick
Раздельные бетонные блоки
Splitface Concrete Blocks имеет глубокий текстурированный рельеф, который придает глубину блоку, а также обнажает внутренние агрегаты. Это поддается настройке за счет использования заполнителей разного цвета. Доступны как структурные, так и неструктурные бетонные блоки Splitface. Бетонные блоки Splitface доступны как обычных, так и специальных размеров.
- Конструкционные элементы соответствуют ASTM C90, ACI 530, Калифорнийскому строительному кодексу (CBC), глава 21, и Международному строительному кодексу (CBC)
- Неконструкционные элементы соответствуют ASTM C129
- Доступны индивидуальные цвета, вес и сильные стороны дизайна
- По вопросам, связанным с конкретным проектом, обращайтесь в RCP Block & Brick
Цвета блока Splitface
ПРИМЕЧАНИЕ. Цвета могут отличаться от отображаемых в Интернете.Чтобы убедиться в этом, запросите образцы цветных чипов, обратившись в службу поддержки RCP Block & Brick Architectural Support .
Цвета на складе:
Пользовательские цвета:
Размеры и формы блоков Splitface
ПРИМЕЧАНИЕ: Все размеры являются номинальными
Технические характеристики
- Конструкционные элементы: Соответствуют ASTM C90, Спецификации для несущих кирпичных элементов, средний вес.Также соблюдайте последние редакции ACI 530 и главу 21 Строительного кодекса Калифорнии (CBC) и Международного строительного кодекса (IBC).
- Неструктурные блоки: Соответствуют ASTM C129, Спецификации для ненесущих бетонных блоков.
- Для достижения среднего веса промышленного стандарта, RCP Block производит из черного вулканического пепла, который соответствует ASTM C331, Спецификации для легких заполнителей для бетонных блоков.
- По специальному заказу доступны различные веса и конструктивные особенности.
- Стандартные блоки запускаются для каждого задания и доступны со сроком выполнения от четырех до шести недель.
- Пользовательские цвета и формы могут зависеть от: минимального количества заказа, увеличенного времени ожидания, платы за пресс-формы и соглашения о закупке всех единиц из производственного цикла.
Ресурсы для продукта
Бетонные блоки для оседания — блоки и кирпичи RCP
Бетонные блоки для осадки
Slump Block — это бетонный блок, который извлекается из формы до того, как он успеет полностью застыть.Это заставляет бетонный блок сохранять обвисший вид, как сырцовый кирпич. Доступны как структурные, так и неструктурные бетонные блоки с противоскользящим покрытием. Бетонные блоки с противоскользящим блоком доступны как обычных, так и специальных размеров.
- Конструкционные элементы соответствуют ASTM C90, ACI 530, Калифорнийскому строительному кодексу (CBC), глава 21, и Международному строительному кодексу (CBC)
- Неконструкционные элементы соответствуют ASTM C129
- Доступны индивидуальные цвета, вес и сильные стороны дизайна
- По вопросам, связанным с конкретным проектом, обращайтесь в RCP Block & Brick
Цвета скользящих блоков
ПРИМЕЧАНИЕ. Цвета могут отличаться от отображаемых в Интернете.Чтобы убедиться в этом, запросите образцы цветных чипов, обратившись в службу поддержки RCP Block & Brick Architectural Support .
Цвета на складе:
Пользовательские цвета:
Размеры и формы опорных блоков
ПРИМЕЧАНИЕ: Все размеры являются номинальными
Технические характеристики
- Конструкционные элементы: Соответствуют ASTM C90, Спецификации для несущих кирпичных элементов, средний вес.Также соблюдайте последние редакции ACI 530 и главу 21 Строительного кодекса Калифорнии (CBC) и Международного строительного кодекса (IBC).
- Неструктурные блоки: Соответствуют ASTM C129, Спецификации для ненесущих бетонных блоков.
- Для достижения среднего веса промышленного стандарта, RCP Block производит из черного вулканического пепла, который соответствует ASTM C331, Спецификации для легких заполнителей для бетонных блоков.
- По специальному заказу доступны различные веса и конструктивные особенности.
- Стандартные блоки запускаются для каждого задания и доступны со сроком выполнения от четырех до шести недель.
- Пользовательские цвета и формы могут зависеть от: минимального количества заказа, увеличенного времени ожидания, платы за пресс-формы и соглашения о закупке всех единиц из производственного цикла.
Ресурсы для продукта
(PDF) ПРИГОДНОСТЬ БЕТОННЫХ БЛОКОВ РУЧНОЙ ФОРМОВКИ ДЛЯ ОДНОЭТАЖНЫХ ДОМОВ по
Исходя из значений, приведенных в Таблице 4, можно
предложить прочность блочной кладки равной 0.9 Нзмм? для стен
из блоков HMCC. В одноэтажных домах
расчетное напряжение стены будет в основном состоять из вклада
за счет собственного веса, а оставшаяся часть
будет зависеть от веса крыши и потолка
(максимальное расчетное значение около l 0,0 кН / м
2
с
как статической, так и приложенной нагрузкой). Если стена поддерживает пролет крыши 4,0 м
, результирующее напряжение будет только 0.04 Н / мм «.
Как правило, высота стены в одиночном
-этажном доме среднего размера будет иметь максимальную высоту около 4,0 м.
Это даст напряжение около 0,092 Н · мм + с плотностью
из 23 кН / м
3.
Если ввести частичный коэффициент запаса прочности
, он составит около 0,49 Н / мм2 (0,092 x 1,4
x 3,5 +0,04). достаточный запас
при характеристической прочности 0,9 Н · мм », чтобы учесть
любых эффектов гибкости и эффектов отверстий.
Это может быть дополнительно поддержано за счет использования характеристической прочности
, необходимой для двухэтажных домов с несущими стенами
.
I
т было показано с подробным исследованием
, что прочность стены 1,5 Н / мм2 была достаточной
для двухэтажной несущей кирпичной стены с
монолитными железобетонными плитами (Jayasinghe, 1998).
Таким образом, можно предположить, что стены
, построенные из блоков HMCC (смесь 1: 8: 14) и цементно-песчаного раствора 1: 5
, будут иметь достаточную прочность для
одноэтажных конструкций.
7.0 Аспекты стоимости
Возможность производить вручную лепные бетонные блоки
имеет особое преимущество для определенного сектора
населения. Это группы с низким доходом на
, которым небольшие ссуды на сумму около рупий. 25,000 / = до 50,000 / =
предоставлены различными правительственными и не
правительственными организациями. Некоторые из этих кредитов
выдаются с небольшими взносами, что делает невыгодным
для получателей покупать блоки напрямую на рынке
.В таких случаях блоки HMCC предоставляют хорошую возможность
, поскольку для этого нужна только пресс-форма для изготовления блоков
, но не машина для изготовления блоков. Время, затрачиваемое на изготовление около 30 блоков
, составляет два часа, когда задействовано два человека
; один для производства бетонной смеси
и другой для изготовления блоков. При таких темпах для изготовления всех блоков (около
1500-2000), необходимых для дома площадью около 50 м,
2
,
,
, работая только 2 часа в день, потребуется менее двух месяцев. на неполной ставке.
Таким образом, затраты рассчитываются на основе
неоплачиваемого труда и оплачиваемого труда.
Это
было установлено при реальных измерениях, что из мешка
цемента, можно сделать 67 штук блоков толщиной 125 мм
. Общая стоимость этих 67 блоков была рассчитана
рупий. 812 / = с ценами на мешок цемента, 1 м «
песка или карьерной пыли и 1 рубль 6-8 мм стружки как
350 / =, 500 рупий / = и рупий.600 / = соответственно. Следовательно,
стоимость блока толщиной 125 мм составляет около рупий. 12 / = и рупий.
9,50 / = для блоков толщиной 100 мм.
Поскольку два неквалифицированных рабочих могут производить около
15 блоков в час, стоимость рабочей силы на блок рассчитывается на основе
рупий. 250 / = в день на одного работника. При восьми
часов рабочего времени в день стоимость рабочей силы может составить
рупий. 4,00 за блок. Следовательно, стоимость блока
с наемным трудом будет рупий.13,50 и рупий. 16.00 для 100
блоков толщиноймм и 125 мм соответственно. Это можно рассматривать как
как цену, сравнимую с ценой на блоки из цементного песка
, доступные на рынке.
8.0 Выводы
В подробной программе испытаний показано, что
бетонных блоков из формованной стружкишириной 125 мм и 100
мм можно использовать для внешних и внутренних стен одноэтажных домов
, соответственно. Для любой конструкции конструкции
можно с уверенностью принять характеристическую прочность
0.9 Н / м «для стен из щебеночных блоков толщиной
100 или 125 мм. Рекомендуемая смесь: цемент
1: 8: 14, мелкий заполнитель и щепа для блочной кладки
. Одно из основных преимуществ блоков из щебеночного бетона
состоит в том, что он может быть изготовлен на месте до требуемой толщины
. Это можно использовать, чтобы избежать штукатурки
, используя блоки толщиной 125 мм для внешних стен
. Для внутренних стен 100 Можно использовать блоки толщиной
мм.Исследование стоимости показало, что стоимость блоков HMCC
может быть сопоставима с теми, которые доступны на рынке
.
Благодарность
Автор выражает благодарность Комитету Сената по исследованиям
Университета Моратува за финансирование
этого исследования. Технический директор, г-н С.Л. Капуруге
успешно координировал исследовательскую работу с большой самоотдачей
. Особая благодарность за Research
Assistant Mr.У. К. Виданагамараччи и технический персонал
Помощник г-на У. С.
П.
Кумара.
Ссылки
BS 5628: Часть 1: 1992, Использование кирпичной кладки. Конструктивное использование неармированной кирпичной кладки
, 56 стр.
Строительные нормы (1985), «План развития города Коломбо
«, том
II,
Муниципальный совет Коломбо,
74p.
Chandrakeerthy, S.RDeS., Fonseka, M.C.M., Kodikara,
c.w.,
Jayawardane, S.JKLL, (1985), «Производство
блоков для многоэтажных несущих каменных конструкций»,
Труды Института инженеров, 1985.
29
Как каратэ ломает бетонные блоки
Как может слабая смертная рука уязвимы для заусениц, перегретых пакетов с попкорном и острых как бритва кусочков картофельных чипсов, зажатых между клавишами обычной компьютерной клавиатуры, проходят через бетонные блоки и деревянные доски?
Беглый просмотр интернета или музыкального тренинга из фильма о боевых искусствах восьмидесятых годов делает очевидным, что разбить бетон или дерево голыми руками возможно.На самом деле у некоторых читателей есть знакомые, которые из-за длительного обучения или большого количества алкогольного опьянения попробовали это сами и добились успеха. Конечно, у этих читателей есть друзья, которые из-за сильного опьянения упали и сильно поранились о дерево или бетон. Главный вопрос: в чем разница между успехом и травмой? Какие факторы влияют на то, чтобы ударить по куску бетона и расколоть его надвое, вместо того, чтобы рука, ударившая по нему, взорвалась ливнем красной слизи, как перезрелый помидор?
Для начала важно нанести удар в нужную точку.Лучшая точка находится не только в узкой средней точке блока. Широкий удар отбрасывает много сил, так как нужно только сломать блок в одном месте, чтобы сломать его. Также важно быстро нанести удар по поверхности блока. Большинство ударов — это частично соединительный шлепок, а частично — толчок. Это наносит наибольший урон при борьбе с плотью, но помогает защитить бетон или дерево. Бетон и дерево обладают хорошим сочетанием жесткости и эластичности. Материалы будут изгибаться и даже изгибаться назад, как резинка, но пределы их пластичности намного ниже.Сгибание и резкое огибание могут нанести им больше вреда, чем вещи, которые сгибаются легче. Благодаря быстрому удару и оттягиванию ударник сильнее всего ударяет по блоку и позволяет материалу максимально изгибаться. Последующий толчок не даст материалу отломиться и защелкнуться.
Все в порядке, но редко можно увидеть, как кто-то пробивает здание пополам или выбивает трещины в тротуаре, даже если их форма идеальна. Посмотрите на картинку ниже.
G / O Media может получить комиссию
Между каждой бетонной плитой есть небольшие перегородки. Редко можно найти разделители между слоями тротуара. Это то, что отделяет трещины от пятен. Пробить кусок бетона сложно, но пробить кусок бетона, лежащий на земле, практически невозможно. Материал должен дать трещину. То же свойство наблюдается и у более легких и гибких материалов. Держите лист бумаги за обе стороны в воздухе, и нож, приложенный к середине, прорежет его насквозь.Положите его на ровный бетонный пол, и будет намного сложнее разрезать лист бумаги тем же ножом.
Как и все остальное в жизни, ломка — это просто примитивная, выродившаяся форма изгиба. Бумага не сгибается, поэтому не поддается. Бетонный блок работает точно так же.
Так что помните, если вы должны пробить бетонный блок (вы не должны), убедитесь, что вы делаете это (не делайте этого) с блоком (максимум из пенополистирола), который удерживается в воздухе (кем-то, кто оторвет его, если вы сделаете что-то глупое, например, попытаетесь сломать его рукой), а не упадете на землю (как вы будете кататься взад и вперед в агонии, и это не будет моей ошибкой, черт возьми.Я тебя предупреждал).
Через Straight Dope and Discover.
Отколы бетонного основания от ремонта фундамента JES
Это правда, что сколы в бетоне могут быть косметическими или структурными. Если это косметический вид, вы, вероятно, легко сможете это исправить; если он структурный, исправить это может быть намного сложнее. Способность различать эти два элемента имеет решающее значение для вашего бетона.
Это вопросы, которые вам следует задать, чтобы определить значимость, когда дело доходит до выкрашивания бетонной сколы и выкрашивания фундамента.
Какой у вас фундамент?
Если вы смотрите на фундамент с зазубринами, чрезвычайно важно отметить, какой у вас тип фундамента. Процесс ремонта выкрашивания фундамента может отличаться в зависимости от типа фундамента.
Два типа бетонных фундаментов обычно представляют собой заливной фундамент или бетонный блок. В то время как залитый фундамент может справиться с гораздо большим количеством сколов, прежде чем он станет серьезной проблемой, бетонный блок не справится с этой проблемой.
Любой, у кого есть фундамент из бетонных блоков, который подвергается растрескиванию, должен как можно скорее связаться со специалистом JES. Если оставить это без внимания, это может легко перерасти в структурную проблему, даже если изначально она не возникла.
Как давно вы имеете дело с тонким слоем?
Если вы столкнулись с серьезными проблемами со сколами, вам следует как можно раньше связаться со специалистом. К сожалению, некоторые люди не берутся за дело раньше, а просто ждут, пока ущерб не станет слишком серьезным, чтобы его можно было игнорировать.
Это особенно важно, если вы сначала работали с небольшим количеством сколов, но с тех пор оно увеличилось. Как и любая проблема, которая игнорируется, проблема, которая вначале была небольшой и управляемой, могла перерасти в серьезную структурную проблему.
Особенно, если это происходит уже давно, стоит обратить внимание на сколы бетона и их значение. Не ждите, пока бетон полностью разрушится. Вместо этого поговорите со специалистом по JES.
Есть ли трещины вокруг выкрашивания фундамента?
Выкрашивание фундамента само по себе может быть просто косметической проблемой, но оно также может стать препятствием для возникновения других структурных проблем. Если вы начинаете видеть трещины вокруг скола, это свидетельствует о серьезной проблеме.
Цикл замораживания-оттаивания вызывает не только растрескивание и мелкие проблемы. Если он застрянет глубоко внутри бетона, то замерзание и таяние могут начать создавать и увеличивать фактические трещины внутри вашего фундамента, которые вы увидите отраженными вокруг скола.
В общем, независимо от причины трещин, вам следует связаться со специалистом по ремонту бетонных фундаментов из JES, как только вы начнете видеть трещины шириной более одной восьмой дюйма. Трещины в фундаменте могут потребовать внимания, если они станут шире шестнадцатой дюйма.
Где сколы в бетоне?
Как упоминалось ранее, сколы снаружи встречаются гораздо чаще, чем сколы внутри. Более вероятно, что у вас есть структурные проблемы, если вы столкнулись с внутренними сколами, а не с внешними, потому что проблемы, скорее всего, будут более глубокими и лежат в вашем фундаменте.
Однако даже внутри область вашего фундамента, в которой наблюдается скалывание, имеет значение. Это на уровне земли? Это где-то посередине стены или к желобу? Плохой дренаж может вызвать избыток воды, что может привести к большему растрескиванию фундамента.
В этих случаях, особенно если нет серьезных трещин, может потребоваться просто удлинить водосточную трубу и обратить внимание на дренаж. Конечно, если вы начнете замечать серьезные трещины или это не решит проблему, поговорите со специалистом.
Насколько глубоко растрескивается фундамент?
Это один из самых важных вопросов. Мелкие участки сколов основы, скорее всего, будут чисто косметическими. Это потому, что эти пятна недостаточно глубоко проникают в фундамент, чтобы повлиять на саму основу. Откол можно сравнить с обдиранием кожи на колене или царапиной. Если поражен только верхний слой кожи, то в основном косметический. Однако, если царапина глубже, она будет кровоточить сильнее и может быть опасной или даже смертельной.
Насколько глубоко это должно быть, прежде чем следует обращаться к эксперту? Это может варьироваться в зависимости от фактического бетона. Однако проблемы с поверхностью обычно затрагивают только очень мелкую и малодоступную часть бетона, а это означает, что вы обычно не увидите косметических проблем на всем протяжении фундамента.
Хорошее практическое правило — поговорить со специалистом, когда вы начнете видеть трещины или сколы в фундаменте размером в одну восьмую дюйма или больше. Для фундаментов с повышенным риском обращайтесь в контакт, если площадь составляет одну шестнадцатую дюйма или больше.
Видны ли пятна на сколе фундамента?
Это наиболее типично для выкрашивания фундамента внутри. Когда вы начнете видеть скол, оглянитесь вокруг. Вы видите белый меловой порошок или коричневые пятна внутри или по краям сколов фундамента?
Белый меловой порошок — высолы, коричневое окрашивание — кислотное повреждение. Если вы видите что-то из этого, это означает, что в эту зону попадает вода снаружи из-за гидростатического давления.Значит, пора поговорить со специалистом по гидроизоляции.
Есть ли у вас какие-либо из этих потенциальных причин, которые могут привести к сколам в бетонной стене?
Бетон низкокачественный
Это наименее вероятная причина, по которой у вас может быть скол в бетоне, но это все же возможно. Если бетон был плохо перемешан или строительная бригада не залила его должным образом, у вас могут возникнуть проблемы с отслаиванием бетона.
Если у вас бетон низкого качества, вы, вероятно, заметите эти проблемы гораздо больше, чем просто одну или две стены.У вас могут быть сколы в бетоне на многих стенах или очень серьезные сколы в одних местах и меньше — в других.
Хотя это маловероятно, важно отметить, что это возможно. Обсуждая ремонт отслаивания фундамента, убедитесь, что вы исследуете возможность того, что бетон просто плохо стартовал.
Цикл замораживания-оттаивания
Это гораздо более распространенная проблема, вызывающая скалывание бетона. Это особенно часто встречается, когда речь идет о проездах и другом наружном бетоне, потому что цикл замораживания-оттаивания имеет тенденцию непропорционально влиять на внешний бетон.
Вот как цикл замораживания-оттаивания может повлиять на вас. Если у вас есть вода в бетоне или вокруг него, эта вода может замерзнуть, так как область вокруг бетона замерзнет. Когда он замерзает, он расширяется, оказывая давление на бетон и отщепляя куски.
Если вы испытываете сколы в фундаменте, трещины в бетоне на подъездной дорожке или бетонные сколы на стенах дома, причиной может быть циклическое замораживание-оттаивание. Если это так, вы могли бы поддерживать свой бетон, просто компенсируя сколы от замерзания-оттаивания в бетоне.
Избыточная вода
Конечно, проблема циклического замораживания-оттаивания усугубляется избытком воды в бетоне. Если ваш бетон заполнен водой, больше воды начнет замерзать, что повысит вероятность появления сильных трещин и сколов.
Избыточная вода — это не просто стоячая вода. Если у вас слишком много влаги в подвале или в подвале, эта влага может начать конденсироваться и образовывать воду на стенах. Если у вас есть трещины в фундаменте, это также может позволить воде просочиться внутрь.
Лучший способ избежать в будущем сколов фундамента из-за избытка воды — это в первую очередь избегать этого избытка воды. Фактически, удаление воды должно быть одним из ваших главных приоритетов в целом. У JES есть специальные системы, которые удаляют избыток воды и отводят ее от вашего дома.
Первое, что нужно узнать, это что такое скалывание бетона. Выкрашивание бетона, также называемое «отслаиванием» или «образованием окалины», — это то, что происходит, когда верхний слой бетона начинает отслаиваться, обнажая бетон под ним.
Это может быть косметический или структурный характер. Важно знать разницу между ними. Глядя на сколы в бетоне, вы должны понимать, является ли это косметической проблемой или проблемой конструкции. Косметическая проблема на самом деле не имеет никакого значения, в то время как структурная проблема — это то, что вам нужно немедленно решить.
Если у вас есть сколы, вам не нужно просто решать проблему. На самом деле, существует несколько вариантов ремонта откола. Вариант, который лучше всего подходит для вас, может варьироваться в зависимости от множества факторов, в том числе от того, насколько велик урон и как рано вы его поймаете.
Как правило, вы столкнетесь с аналогичными решениями этих проблем с растрескиванием. Это самые распространенные.
Шлифовка бетона
Если у вас растрескивание бетона только на поверхности и не вызвано какими-либо проблемами, вы можете инвестировать в шлифовку бетона. Это означает добавление дополнительного бетона поверх текущего бетона, обычно небольшого участка, который сохранит прочность бетона.
Насколько может помочь шлифовка бетона? Типичное правило состоит в том, что вы можете выполнить ремонт поверхности, если выкрашивание меньше 1/3 толщины бетона.Конечно, это также означает, что вы должны атаковать его как можно раньше.
Лучше всего при шлифовке бетона решить проблему на ранней стадии. Как только вы начнете видеть сколы в фундаменте, превышающие очень маленькую и неглубокую поверхность, обратитесь к специалисту JES. Возможно, у вас получится простое решение.
Полная замена или восстановление
К сожалению, если вы оставите проблему до тех пор, пока она не станет слишком глубоко укоренившейся, вам может потребоваться полностью заменить или восстановить бетон. Это намного сложнее и дороже, но это может быть единственный вариант для бетонной поверхности с глубокими дефектами.
Если это действительно ваше решение, будьте уверены, что талантливый эксперт все еще может решить эту проблему. Лучше связаться с экспертом пораньше, но если у вас не было возможности сделать это, ваш дом не потерян из-за этого. Проблема все еще может быть решена.
Неужели растрескивание фундамента начало разъедать ваш фундамент глубже? Ремонт выкрашивания фундамента заключается в том, чтобы как можно раньше устранить проблему. Обращение к эксперту JES позволит вам узнать, насколько серьезна проблема и каково ее решение.
Вторичные проблемы
Некоторые проблемы отслаивания фундамента возникают из-за вторичных проблем. Например, избыток воды обычно откуда-то берется, а это значит, что вам нужно перекрыть источник.
Эти второстепенные проблемы необходимо исправить, если вы собираетесь решить проблему в целом. Простая шлифовка бетона или даже полное восстановление может не решить проблему в целом, если вы не решите истинную проблему. Он просто вернется.
Вместо того, чтобы просто наложить повязку на проблему, важно исправить ее в корне, чтобы не повторить ее снова.Эксперт JES может дать вам дополнительную информацию о причинах возникновения проблемы, чтобы вы могли сделать правильный выбор.
Как отремонтировать наружные стены из шлакоблоков с лепниной
Как отремонтировать наружные стены из шлакоблоков с лепниной
Скотт Арнольд на How To
Как отремонтировать наружные стены из шлакоблоков с лепниной
С начала 19 века штукатурка использовалась для покрытия менее привлекательных строительных материалов, таких как бетон, металл и шлакоблок.Созданный для наружного использования, строители начали использовать его только в конце 19 века и во внутренних помещениях.
Старые обветшавшие стены действительно могут вызвать раздражение. Чаще всего они становятся центром вашего двора, даже если у вас самая красивая недвижимость в вашем районе. Это похоже на аварию на шоссе, ты знаешь, что не хочешь пялиться, а мы всегда делаем!
Недавно у меня был клиент, у которого были серьезные проблемы с некоторыми стенами патио на заднем дворе.Они любят развлекаться, но избегают барбекю и вечеринок из-за пары уродливых стен из шлакобетона. С приближением дня рождения сына они решили отделать стены штукатуркой, чтобы сделать их более привлекательными.
Шаг 1 — Подготовка
Первый шаг в штукатурке стен — правильно их подготовить. Убедитесь, что вы удалили все крошащиеся блоки и мусор. Отрежьте кусочек и кусок, который может выступать больше, чем другие, чтобы обеспечить вам хорошее обслуживание квартиры. Очистите стены щеткой, удалив всю пыль и грязь.В таких случаях, как у меня, в стенах были некоторые куски блоков, которые полностью отсутствовали из-за плохого дренажа. Залейте их раствором и дайте высохнуть. Перед нанесением штукатурки необходимо убедиться, что вы находитесь как можно ближе к уровню / ровной поверхности.
При нанесении новой штукатурки на существующий бетон необходимо нанести связующее. В нашем случае мы использовали Quikrete Bonding Agent, приобретенный в местном магазине Home Depot. Вместо черновой обработки уже существующего бетона вы просто наносите средство валиком или кистью.В инструкции указано, как нанести новую штукатурку в течение трех часов после нанесения.
Шаг 2 — Смешивание штукатурки
Теперь, когда ваши стены подготовлены и вяжущее вещество высыхает, вам нужно приступить к смешиванию штукатурки. Штукатурка состоит из четырех основных компонентов: портландцемента, песка, извести и воды. Соотношение смешивания может варьироваться в зависимости от того, кого вы спрашиваете. Для наших стен мы использовали три части песка, одну часть извести и одну часть портландцемента. Добавляем воду до консистенции кирпичного раствора.
Будьте осторожны при замешивании строительного раствора, так как он может быстро высохнуть. Мое эмпирическое правило — микширование стоит около 90 минут. Все, что больше этого, высыхает слишком быстро, и вы постоянно добавляете в него больше материалов, чтобы вернуть его к работоспособной консистенции. Еще одна вещь, которую следует учитывать, — это температура. Жаркие и влажные дни ускоряют процесс сушки и, как правило, замедляют вашу работу. В жаркие влажные дни я обычно смешиваю только небольшое количество за раз.
Шаг 3 — Нанесение лепнины
Первый слой
Обычно я наношу 2 слоя штукатурки на стены, которые покрываю.Первый слой — это мой наполнитель или нижнее покрытие, а второй слой — это мое готовое покрытие. Обработайте штукатуркой большие трещины и щели, прежде чем приступить к нанесению штукатурки на всю стену. Если вы просто начнете наносить его и игнорируете большие зазоры или трещины, у вас возникнут проблемы, когда вы затирете их. Лепнина плохо держится. Поэтому я рекомендую сначала поразить их.
После нанесения первого слоя возьмите Stucco Float и сбейте неровности.Он не обязательно должен быть идеальным. Прибереги это для своего готового пальто. Не забудьте очистить рабочее место после нанесения первого слоя. Штукатурка — грязная работа, убирайте ее, пока штукатурка еще влажная, это позволит избежать царапин в дальнейшем.
Готовое пальто
После высыхания штукатурки можно приступать к нанесению финишного покрытия. С этим пальто вы хотите сделать его максимально гладким. Я считаю, что для меня лучше всего работать снизу вверх.
После того, как я нанесу штукатурку, я даю ей немного застыть, прежде чем использовать губку, чтобы разгладить ее. Используя губку, используйте много воды, разгладьте штукатурку, убедившись, что вы уделяете пристальное внимание своей внешности, если она у вас есть. Кажется, это будет видно, если вы не распушите их должным образом. Точно так же, как грязь и лента на гипсокартоне, ваши швы имеют решающее значение и обычно являются первым местом, где выходит из строя.
Сделай сам или нет?
Достаточно ли легко справиться с лепниной для домашнего мастера? Абсолютно! При оштукатуривании мало что нужно знать.Убедитесь, что у вас есть подходящие материалы и инструменты, и все готово. Кроме того, можно ли сделать стену хоть сколько-нибудь уродливее, чем она есть, не так ли?!?!
Штукатурку можно сделать за выходные, а если у вас все хорошо получается, вы можете прибить ее за день. Не торопитесь, убедитесь, что ваша смесь идеальна, ваши швы гладкие, а ваша область поддерживается в чистоте, и вы станете профессионалом в области штукатурки, прежде чем узнаете об этом!
Badger Block в Гранд-Джанкшен, CO
БАДЖЕРНЫЙ БЛОККирпичный завод2021-07-07T10: 58: 35-06: 00Вы ищете блок особого цвета, который, по вашему мнению, доступен только с добавленной стоимостью фрахта из Денвера или Солт-Лейк-Сити? Принесите нам свой образец цвета, и мы подберем его для вас.Мы добились больших успехов в нашем отделе цветного и серийного дизайна и создали цвета, которыми остались очень довольны наши клиенты. Если вы ищете качественный продукт с исключительным обслуживанием клиентов, мы просим вас попробовать нас. Мы хотим предоставить вам блок для следующей большой работы в вашем списке. Избавьте себя от неприятностей и ДУМАЙТЕ ЛОКАЛЬНО. Изготавливаем стандартные и специальные блоки, подпорные стены, садовые стены и брусчатку. Если для крупной работы вам нужен продукт, который мы в настоящее время не производим, свяжитесь с нашим отделом продаж на BRICKYARD, мы сделаем все возможное, чтобы удовлетворить вас.
Посетите нашу фотогалерею , чтобы увидеть здания, для которых мы построили кварталы в Гранд-Вэлли, а также по всему Западному Колорадо и Восточной Юте. Если вы хотите лично увидеть какое-либо из этих зданий или стен, свяжитесь с нами. Выбирайте из БЛОКОВ ЗДАНИЙ, БЛОКОВ СТЕНЫ и MICS. БЛОКИРОВКА ПРОДУКТОВ.
Что касается подпорных стен, у нас есть потрясающий выбор стилей и цветов. В настоящее время мы изготавливаем сегментные подпорные стенки как с прямой, так и с выпуклой скошенной поверхностью.У нас есть пять стандартных цветов подпорных стенок, которые доступны в ящиках для образцов цементной крошки. Пожалуйста, позвоните, если хотите. Мы также можем изготовить специальные цвета для наших блоков подпорных стен для крупных проектов с менее строгими временными ограничениями. См. ПОДДЕРЖИВАЮЩИЕ СТЕНЫ для получения дополнительной информации об этих продуктах.
В нашей линейке легких блоков у нас есть в общей сложности 15 предварительно разработанных специальных цветов, доступных по запросу для более крупных работ.