§ 1.3. Штукатурная гидроизоляция из растворов и мастик (ч. 2)
Штукатурные покрытия из цементных растворов (ч. 2). Коллоидный цементный раствор (КЦР) разработан ВНИИГом в содружестве с ИФХ АН СССР для штукатурной гидроизоляции на основе высокодисперсного цемента М-500, тонкомолотого порошка-наполнителя и более крупного песка-заполнителя при пониженном содержании воды (В/Ц = 0,35) и повышенных добавках гидрофилизирующих ПАВ (ССБ или СДБ) [27, 41, 111].
П 02–73. ВНИИГ. Временные указания по применению коллоидного цементного раствора и активированного торкрета для гидроизоляции энергетических сооружений
Дубинин И.С, Климова М.М. Коллоидные цементные растворы и другие виды цементной гидроизоляции для гидротехнического строительства
Дисс. Урьев Н.Б. Образование и разрушение дисперсных структур в условиях действия вибрации и поверхностно-активной среды. ИФХ АН СССР, 1974 (докт. дис.).
Для КЦР характерна высокая водонепроницаемость при пониженных усадочных деформациях, что обеспечивает трещиноустойчивость покрытий.
Наиболее существенным недостатком КЦР является его слишком густая консистенция во время нанесения, вследствие чего при В/Ц > 0,35 в покрытии образуются усадочные трещины; поэтому раствор приходится наносить либо вручную, либо ручным аппаратом — виброрастворометом, строго соблюдая дозировку воды и правила ухода за покрытием.
Коллоидный полимер цементный раствор (КПЦР) отличается добавками (3—5 % от массы цемента) латексов, полиэтиленовой эмульсии, эпоксидной эмульсионной пасты, которые повышают подвижность КЦР настолько, что даже при В/В = 0,2 его можно наносить растворонасосом. Кроме того, добавки эластомеров резко увеличивают трещиноустойчивость покрытий, что видно из табл. 1.23.
Таблица 1.23
Технико-экономические характеристики цементной штукатурной гидроизоляции
Характеристики | Из цементных растворов | Из коллоидных цементных растворов | Стеклоцементная | |||
1:2 В/Ц—0,4 | с добавками | торкрет | КЦР | КПЦР | ||
Толщина покрытия, мм | 25—30 | 25—30 | 30—50 | 10 | 10 | 10 |
Водонепроницаемость МПа | 0,2—0,3 | 0,5—1,5 | 0,8—1,0 | 1,0—1,6 | 1,0—1,6 | 0,5—1,0 |
Прочность, МПа: при сжатии растяжении изгибе (Ra), не менее | 30—40 3,6—4 5 | 20—40 1,5—2,7 5 | 20—45 2,5—5 7 | 35—45 3,5—5 7 | 25 2,5—3,5 8 | 35—50 3,8—8 12 |
Адгезия к бетону, МПа | 0,7—0,9 | 0,5—0,6 | 0,5—0,6 | 0,8—1,0 | 1,0—1,2 | 3,0—3,5 |
Морозоустойчивость, более циклов | 50 | 100 | 100 | 200 | 300 | 200 |
Усадка (Ус), мм/м, через 1 мес.![]() То же, через 6 мес. | 0,5—0,7 0,5—0,75 | 1,0—1,1 1,2 | 1,1 1,2 | 0,5 0,7 | 0,75 0,80 | 0,1—1,0 0,5—0,7 |
Растяжимость (εн) %, не более | 0,01 | 0,03 | 0,01 | 0,01 | 0,05 | 0,05 |
Модуль деформации (Еи), Мпа | 1·104 | 5·103 | 2·104 | 3,5·104 | (0,5÷2)·104 | 3·104 |
Коэффициент трещиноустойчивости | 7·10–5 | 2,9·10–5 | 3,3·10–6 | 2·10–5 | 2·10–4 | 3,8·10–5 |
Осадка конуса СтройЦНИЛ, см | 6—8 | 8—10 | — | 2—3 | 6—8 | 2—3 |
Расход материалов, кг/м2 В том числе: цемента песка + наполнителя добавок ПАВ, полимеров | 50—60 10—20 | 50—60 10—15 | 60—100 25—40 | 20 4,2 | 20 4,0 | 20 14 |
Стоимость покрытия руб/м2 | 0,60 | 1,05 | 1,6—4,6 | 1,15 | 1,35 | 1,7—2,35 |
Трудозатраты, чел.![]() | 0,03 | 0,05 | 0,16—0,42 | 0,16 | 0,05—0,1 | 0,25 |
Весьма эффективна добавка ПАВ — пенообразователя ОП-7 (оксиэтилированного алкилфенола) в количестве 5—8 % от массы вводимого эластомера или 0,15 % от массы цемента. Такая добавка играет роль стабилизатора латекса, эмульгатора полимера и воздухововлекающей пептизирующей добавки в цементном растворе. В результате становится возможной комплексная механизация приготовления и нанесения КПЦР с помощью обычного оборудования (рис. 1.5, б). Зимой эту гидроизоляцию наносят в тепляках.
Растворы КЦР и КПЦР применяются в следующих случаях:
- а) на напорных гранях гидротехнических сооружений в суровых климатических условиях — применены на насосных станциях Троицкой и Гусиноозерской ГРЭС, в плавательных бассейнах в Ленинграде, на напорных водоводах Артемьевского гидроузла и других объектах;
- б) на поверхностях, подвергающихся абразивному воздействию, например бункеров гидрозолоудаления на Троицкой ГРЭС, на очистных устройствах Череповецкого металлургического комбината, водосбросах Варцихской ГЭС;
- в) в условиях отрывающего напора воды, например в подвалах жилых домов, Смольного и Преображенского соборов, дворца Меншикова в Ленинграде, на вагоноопрокидывателях Павлодарской ГРЭС, в шандорохранилище Верхнекамской ГЭС, на насосной станции Шамской ГЭС при напоре до 20 м и т.
п.
Недостатком штукатурной гидроизоляции из КПЦР является низкая ее трещиноустойчивость, из-за чего ее нельзя применять на трещиноватом основании при раскрытии трещин более 0,15 мм и на сборных конструкциях. Однако простота технологии, надежность покрытий, недефицитность и безвредность исходных компонентов, небольшая стоимость и трудоемкость покрытий открывают широкие возможности для использования КПЦР.
Стеклоцементная гидроизоляция разработана ВНИИНСМом и ВНИИСТом в содружестве с ИФХ АН СССР также на основе коллоидного цементного клея с армированием покрытия рубленым стекловолокном [22]. В данном случае технология немного видоизменена: виброизмельченная и виброактивированная цементно-песчаная смесь набрызгивается слоями толщиной по 1 мм с армированием путем набрызга рубленого стекловолокна; поэтому для создания надежного гидроизоляционного покрытия требуется нанести восемь-десять наметов (рис. 1.6, в). Долговечность покрытия достигается сочетанием глиноземистого цемента и алюмоборосиликатного стекловолокна или портландцемента и щелочестойкого стекловолокна ЖС 23/60. Предусмотрена также добавка до 10 % латекса, что намного удорожает гидроизоляционное покрытие (табл. 1.23).
ВСН 2-79–76. Миннефтегазстрой СССР. Инструкция по составам н технологии нанесения гидроизоляционных покрытий для железобетонных конструкций
Все упомянутые работы по созданию коллоидных цементных растворов значительно опережают аналогичные разработки зарубежных фирм. Можно указать на применяемый в ФРГ цементно-песчаный раствор «колькрет», приготавливаемый в турбулентных двухбарабанных смесителях со скоростью вращения 2200 об/мин, безусадочный цемент «торосил» в США.
Эпоксидная смола для заливки ОЛИМП
Двухкомпонентный суперпрозрачный эпоксидный состав для декоративных и столярных работ – для заливки столов-рек, столешниц, дизайнерских полов, панно, фотографий, картин, сувениров, брелоков, украшений, для защитной и декоративной отделки, склеивания различных поверхностей. Хорошо поддается окраске, монтажу, механической обработке и шлифовке.
Торговая марка: OLIMPДоступность: Доступно к заказу через 1-3 дня
Артикул:
Габариты (Д x Ш x В), вес брутто:
Гарантия лучшей цены
3 899,00 ₽
≈1 728,15 ₽ за 1 кг
Стоимость доставки:По Москве в пределах МКАД — от 300₽ за 3 часа!
По Московской области — от 1000₽ за 5 часов!
По Москве и МО при заказе от 5000₽ — БЕСПЛАТНО!
По России* при заказе от 10000₽ — БЕСПЛАТНО!
* ознакомьтесь с условиями или рассчитайте доставку в Телеге
В список желаний
ОСОБЕННОСТИ- Двухкомпонентный состав (эпоксидная смола и отвердитель)
- Применяется для заливки столов-рек, дизайнерских полов, ювелирных украшений, фотографий, защитного и декоративного лакирования, склеивания различных материалов, для пропитки стекловолокна и углеволокна
- Идеально подходит для древесины, металла, стекла, керамики, бетона, некоторые виды пластиков
- Не предназначен для внутренней отделки емкостей под хранение пищи, питьевой воды и поверхностей, подверженных нагреву
- После застывания и полимеризации создает прочное покрытие, выдерживающее умеренные механические и тепловые нагрузки
- Можно колеровать пигментными пастами для эпоксидных красок при смешивании компонентов
- Хорошо поддается окраске, монтажу, механической обработке и шлифовке
- Отличается высокой прозрачностью
ПОДГОТОВКА ПОВЕРХНОСТИ
Поверхности, подлежащие заливке, и емкости для смешивания компонентов должны быть чистыми, сухими и обезжиренными. Рекомендуется использовать широкие полиэтиленовые или стеклянные емкости.
При проведении работ и в течение отверждения температура состава, заготовки и окружающей среды не должна опускаться ниже 22-24°С. Соотношение компонентов определяется по весу и составляет 100 частей смолы (А) к 35 частям отвердителя (Б). Рекомендуем использовать точные весы для правильного взвешивания компонентов. Важно! Нельзя измерять компоненты по объему. Тщательно перемешайте смесь компонентов в течение 3-7 минут. В процессе перемешивания необходимо периодически очищать состав со стенок и дна емкости. Не используйте для перемешивания высокооборотистые миксеры. Перед заливкой перелейте смесь в чистую емкость и перемешайте повторно. Заливайте смесь равномерной струей, направленной в нижнюю точку формы. Равномерное течение смеси поможет избежать захватывания в смесь воздуха. Объемные заливки делать в несколько слоев, толщина одного слоя не более 4 см. Дайте смеси выровнять свой уровень. При необходимости для удаления пузырьков воздуха из заливки допускается применение направленного нагрева с помощью строительного фена.
ОТВЕРЖДЕНИЕ И ПОЛИМЕРИЗАЦИЯ
Время отверждения зависит от температуры окружающей среды, массы состава и конфигурации изделия. Примерное время полного отверждения при температуре 22°С – от 24 до 36 часов. Полная полимеризация и достижение полной механической прочности происходит в течение 7 суток. Поверхность полученного изделия может быть подвергнута шлифовке. При механической обработке или шлифовке необходимо использовать респиратор и очки для предотвращения попадания пыли в дыхательные пути и глаза.
МЕРЫ ПРЕДОСТОРОЖНОСТИ
Работы проводить в хорошо проветриваемом помещении. Использовать индивидуальные средства защиты: перчатки, защитные очки, халат, респиратор типа У-2К. При проведении работ не курить и не принимать пищу. В случае попадания на кожу удалить состав мягкой тканью, смоченной 5% содовым раствором и смыть теплой водой с мылом. Не использовать для мытья рук ацетон или другие органические растворители. При попадании в глаза немедленно промыть большим количеством воды и обратиться к врачу. Беречь от детей!
Эпоксидные фуги. Преимущества и особенности.
В данной публикации речь пойдет об эпоксидных затирочных смесях (фугах). Это относительно новая продукция на рынке строительных и отделочных материалов, но популярность ее стабильно растет. И это неудивительно – по своим характеристикам эпоксидные фуги значительно превосходят традиционные затирочные смеси на цементной основе. Данное превосходство с лихвой компенсирует более высокую цену на эпоксидные составы. Главным «тормозом» в распространении эпоксидных фуг стало расхожее заблуждение о «капризности» этого материала и сложности его применения. Надеемся, что прочитав нашу статью, вы согласитесь с тезисом, что работа с эпоксидной фугой не намного сложнее, чем с любым другим материалом – стоит лишь соблюдать немногие правила и, возможно, «набить руку».
Прежде чем начать отвечать на вопрос «почему характеристики эпоксидной фуги лучше, чем у цементной?», следует понять, что из себя представляют эти два материала в принципе. С затирками на основе цемента все просто и понятно – это смесь из цемента, наполнителя (обычно кварцевого песка), пигментов и полимерных добавок. В процессе использования данная смесь обычно разводится водой (в некоторых случаях могут использоваться эмульсии или латексы), а сам процесс застывания в принципе ничем не отличается от такового у бетона. Вода в данном случае является ключевым реагентом, который активирует схватывание цемента и полимерных добавок, и, сделав свое дело, постепенно уходит из фуги при высыхании, оставляя после себя поры. Характеристики цементных фуг разных производителей отличаются за счет применения различных марок цементов, различных фракций наполнителя, различных пигментов и добавок, но неизменным остается участие воды в процессе использования раствора.
Перейдем к фугам на эпоксидной основе. В их состав обычно входят эпоксидная смола, наполнитель и пигмент. Ключевым отличием от цементных фуг является использование эпоксидной смолы в качестве главного связующего элемента. Именно это и объясняет радикальные отличия по характеристикам, а также все плюсы и минусы применения эпоксидных фуг. Схватывание эпоксидного состава происходит в результате химической реакции между эпоксидной смолой и специальным затвердителем. Поэтому все составы на основе эпоксидных смол поставляются в виде двух раздельных компонентов, что объясняет распространенность названия «двухкомпонентные фуги». Как правило, первый компонент это паста, состоящая из эпоксидной смолы, наполнителя и пигментов. Второй компонент – затвердитель. Зачастую, для достижения различных декоративных эффектов, в фугах на эпоксидной основе могут также использоваться различные добавки, являющиеся, по сути, третьим (а в некоторых случаях и четвертым) компонентом.

Поры в фуге. Как было сказано ранее, цементные фуги независимо от производителя затворяются водой или водным раствором (эмульсией) латексных смол. В процессе затвердевания раствора вода испаряется, оставляя множество пор и пустот. Таким образом, после высыхания структура цементной фуги напоминает губку. Количество пор, их размеры могут быть разными – на это влияет множество параметров, но наличие их неизбежно. Схватывание же эпоксидной смолы происходит за счет химической реакции с затвердителем. В данной реакции задействованы оба компонента и оба компонента остаются в затвердевшем составе, а, следовательно, после застывания эпоксидная фуга по структуре является монолитной и не имеет пор. Теперь рассмотрим, как наличие либо отсутствие пор влияет на потребительские характеристики зафугованных швов.


эпоксидная фуга не намокает и не впитывает влагу | вода попадает в поры цементной фуги |
Вторая «хроническая болезнь» пористых составов для заполнения швов в облицовке – устойчивость к загрязнениям. В поры наряду с водой так и норовят попасть мельчайшие частички пыли и грязи, что со временем приводит к весьма удручающему изменению первоначального цвета. В качестве контрмеры для цементных фуг обычно применяются гидрофобизаторы, создающие на поверхности шва защитную пленку, однако, при интенсивной нагрузке (например, облицовка пола в общественных зонах) срок жизни данной пленки очень непродолжителен.
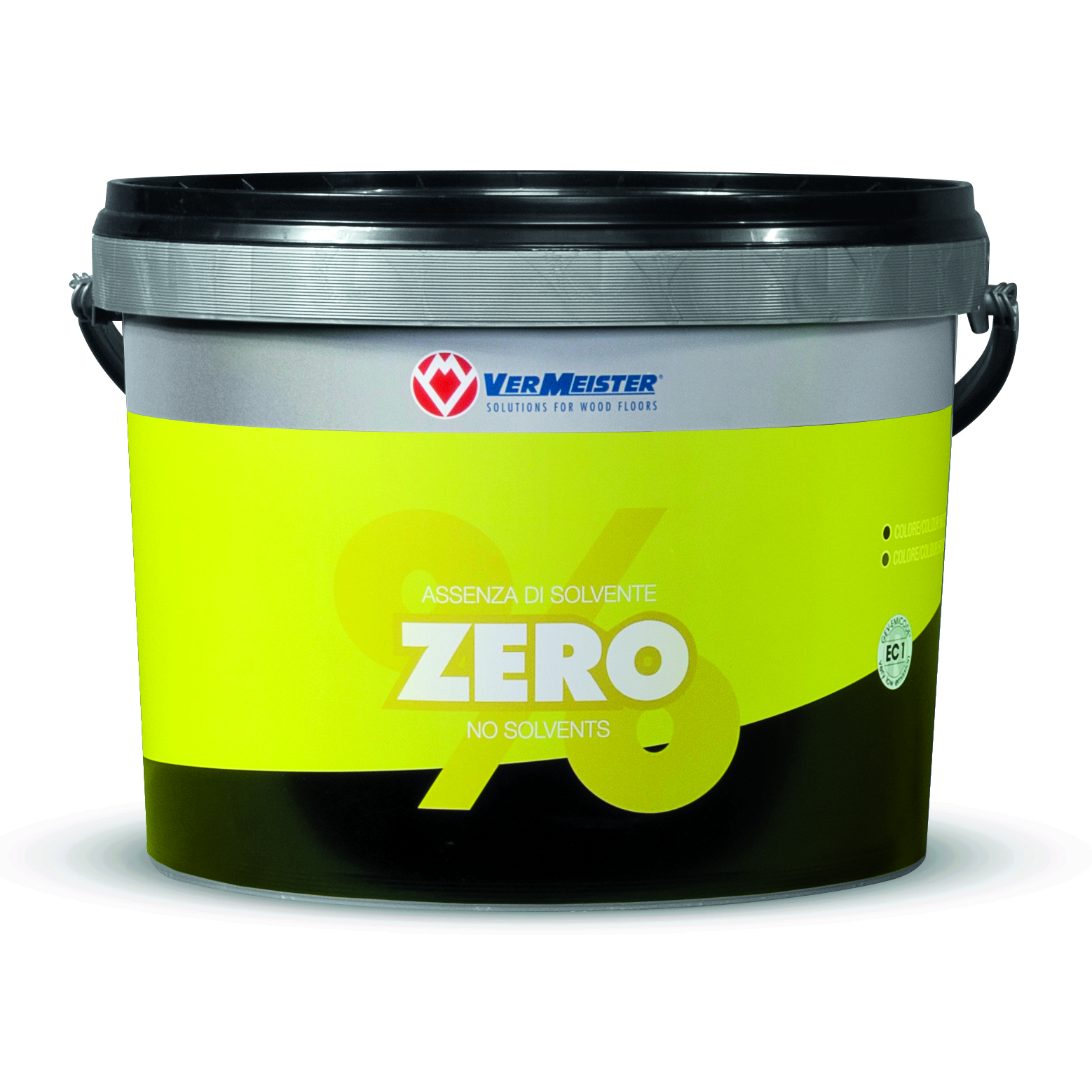
эпоксидная фуга имеет стойкий и стабильный цвет | цементная фуга со временем загрязняется |
Классический пример демонстрации преимущества эпоксидных составов для заполнения швов перед цементными – устойчивость к цветным жидкостям, объединяет и гигроскопичность, и устойчивость к загрязнениям. На первый взгляд экзотика? Оказывается, нет! Цветных жидкостей, способных необратимо испортить внешний вид швов в облицовке, полно на каждой кухне. Это и чай, и кофе, и всевозможные соки. Попадая на пористую поверхность цементного шва, эти жидкости впитываются и надежно его окрашивают. С эпоксидной фуги жидкость просто вытирается, не оставляя следов.
эпоксидная фуга устойчива к образованию пятен от кофе, соков и т.д. | Неустранимые загрязнения цементной фуги в швах |
Чтобы перейти к третьему неприятному последствию пористого материала для затирки швов, необходимо суммировать два, уже рассмотренных. Сырость + грязь. У вас это сочетание никаких ассоциаций не вызывает? Правильно! Именно эта комбинация приводит к такому неприятному для каждой хозяйки последствию как плесень и грибок. На гладкой поверхности плитки вся эта микрофлора не приживается. Достаточно регулярно протирать с бытовым чистящим средством. А вот в швах… И причина все та же – поры. Именно там вредоносные микроорганизмы любят гнездиться, и убрать их оттуда ой как не просто. Поверхность шва, заполненного эпоксидной фугой, такая же монолитная, как и у плитки, а, следовательно, грибок или плесень в швах с эпоксидной фугой будут чувствовать себя крайне неуютно и не задержатся.
Разобравшись с порами и вызванными ими неприятностями, перейдем к следующему блоку характеристик эпоксидных и цементных фуг. Это прочностные характеристики. Как было сказано выше, основным связующим в цементных фугах является цемент, а в эпоксидных – эпоксидная смола. Эти два материала обладают различными характеристиками, причем эпоксид побеждает с большим отрывом. Чтобы не перегружать вас большим объемом непонятных параметров, приведем несколько, наиболее актуальных. Устойчивость к истиранию. У большинства цементных затирочных смесей данный параметр находится в районе 1000 мм3. У эпоксидных фуг устойчивость к истиранию не превышает 250 мм3, то есть в 4 раза выше! Возможно, для ванной комнаты в квартире это не так и важно, но при выборе фуги для торгового центра данный показатель может оказаться критическим. Механическая устойчивость к изгибу для цементной фуги порядка 3,5 Н/мм2, у эпокидной фуги – более 30 Н/мм2, то есть выше в 8,5 раз. Это важно, если ваша облицовка лежит на деформируемом основании (например пол с подогревом). Примерно такая же статистика и у остальных параметров, характеризующих физическую прочность материала.
Наряду с физической прочностью, в некоторых применениях не малую роль играет и химическая стойкость материала. Например, такой важный параметр при строительстве некоторых производств, как устойчивость к воздействию кислот. Сделать действительно стойкую к кислоте фугу на основе цемента практически невозможно, в то время как эпоксидные фуги устойчивы к большинству кислот, щелочей, растворителей и ГСМ.
И о прекрасном! Сравнение потребительских характеристик цементных и эпоксидных затирочных смесей закончим рассмотрением не физики и химии, но эстетики. Ведь именно эстетика, а не параметры двигают нами при выборе плитки или мозаики, равно как и фуги к ним. Поверхность любой цементной фуги матовая и слегка шершавая. Поверхность эпоксидной фуги более гладкая и глянцевая. В полиграфии хорошо известно, что цвета выглядят более сочно и насыщенно именно при печати на глянцевой бумаге. Тот же эффект наблюдается и на швах, зафугованных эпоксидной фугой. Интересный визуальный эффект появляется и вследствие того, что эпоксидная смола в отличие от цемента не является абсолютно непрозрачной. За счет этого, при использовании декоративных добавок-блесток (глиттеров) становятся видны блестки не только на поверхности шва, но и на некоторой глубине, а сам шов приобретает своеобразную объемность. К слову о блестках – некоторые производители умудряются добавлять их в фуги на цементной основе, скромно указывая мелким шрифтом, что со временем возможно их осыпание. Блестки, добавленные в эпоксидную фугу, прочно с ней связаны и осыпанию не подвержены. Полупрозрачность эпоксидных составов позволяет выпускать уникальные фуги наподобие LitokolStarlikeCrystal. Эта фуга специально разработана для многоцветных мозаичных панно. Не имея собственного цвета (вернее имея собственный нейтральный цвет) Crystal«впитывает» лучи света, прошедшие через цветное стекло и окрашивается в тона мозаичных чипов, расположенных рядом.
образцы эпоксидной фуги с добавленными блестками (глиттером) |
Настало время поговорить о технических аспектах эпоксидных составов для затирки швов. Под техническими мы понимаем те вопросы, которые связаны не с процессом эксплуатации, а с процессом применения, то есть с процессом заполнения швов. Именно этот блок характеристик и послужил формированию у эпоксидных фуг репутации «капризного» и «сложного» материала. На самом деле большинство претензий вызвано скорее консерватизмом профессионалов от строительства, нежели объективными причинами.

Необходимость точно соблюдать дозировку при подготовке состава. В отличие от предыдущего, наиболее объективного, данный недостаток является самым надуманным. К сожалению, среднестатистический мастер-отделочник привык работать «на глазок». Возможно, раньше, когда строительные технологии были проще, подобный метод и имел право на жизнь. Но время вносит свои коррективы. Современные технологии требуют все большей аккуратности и точности при выполнении строительных и отделочных работ. Те же традиционные материалы (клей для плитки, цементная фуга) содержат все больше сложных полимерных добавок, которые предъявляют повышенные требования и к количеству добавляемой воды и ко времени жизни раствора. А теперь попытайтесь вспомнить, когда вы видели строителя, отмеряющего воду перед затворением клея? Скорее всего, никогда! Как обычно – просто льют, пока не получат раствор, удовлетворяющий их по консистенции, не думая о пропорции, установленной производителем. А потом долго выясняют, почему плитка отвалилась, и, как правило, «клей плохой!» Эпоксидная фуга, как новое поколение строительных материалов, еще более требовательна к соблюдению пропорций подготовки раствора. Строго говоря, одна упаковка содержит точно дозированное количество пасты и затвердителя для подготовки готовой смеси. Проблема в том, что, как правило, это достаточно большое количество. Например, ведерка фуги объемом 2,5 кг при работе с плиткой 300х300х8 мм и шириной шва 3 мм должно хватить ровно на 10 м. кв. облицовки. И это не самая крупная плитка и не самый узкий шов (то есть достаточно высокий расход). Выработать такое количество фуги параллельно с замывкой одному человеку за час (время жизни раствора) практически нереально. Необходимо разделить упаковку как минимум на два замеса. И вот тут начинаются самые большие проблемы у наших горе-отделочников. Чтобы сделать это корректно, необходимы (внимание!) весы. И взвешивать пасту и затвердитель нужно (о ужас!) с точностью до грамма.
Иначе вы в лучшем случае получите раствор, который схватится не через час, а через 40 минут (если затвердителя будет больше нормы), а в худшем случае – раствор, который вообще не затвердеет. Вот именно этот момент (всего лишь нормальное соблюдение технологии) вызывает больше всего проблем у некоторых мастеров. К счастью, появляется все больше отделочников, для которых электронные весы становятся таким же привычным инструментом, как кельма или миксер. Новичкам, впервые работающим с эпоксидной фугой, настоятельно рекомендуем прочитать инструкцию до начала работ, а не когда возникнут проблемы.
Несколько отличающаяся от работы с цементными фугами последовательность операций. Достаточно объективная претензия, имеющая в корне все-таки консерватизм. Как правило, при работе с цементными фугами, работа делится на собственно фуговку и последующую очистку-замывку плитки от остатков фуги. Эти этапы могут быть достаточно сильно разнесены по времени. Иногда очистка производится на следующий день после фуговки. Сначала фугуется большой объем, потом очищается. При работе с эпоксидной фугой заполнение швов и замывка поверхности должны проводиться практически одновременно – готовый состав живет недолго, а после схватывания его тяжело отчистить. Необходимость постоянно чередовать два вида работ вызывает чувство дискомфорта у некоторых мастеров. Зато при бригадной работе, когда различные операции выполняются различными людьми, вопросов возникает меньше. И, тем не менее, в данном случае очень важно, чтобы мастер, впервые работающий с эпоксидной фугой, прочитал инструкцию до начала работ, а не когда возникнут вопросы.
Повышенные требования к чистоте на рабочем месте. Также является поводом для субъективных претензий к эпоксидной фуге со стороны строителей, правда вслух они это редко озвучивают. Дело в том, что эпоксидная фуга после отвердения превращается практически в пластик, причем чуть-чуть полупрозрачный. И если в этот пластик попадет пыль или грязь, то удалить ее будет очень сложно, а иногда и невозможно. Зато видно будет очень хорошо, особенно если цвет светлый. Вот и получается, что перед работой с эпоксидной фугой мастеру нужно навести чистоту на площадке (опять кошмар!). Помыть и пропылесосить. И в грязной обуви по свежей фуге ходить нельзя – то есть нужно работу спланировать. Ну и инструкцию почитать.
Необходимость работать специальным инструментом и использовать специальные средства для очистки. Объективно-субъективный недостаток. С одной стороны строители, работая с цементными фугами, обходятся только водой. С другой стороны чистящей химией вовсю пользуются клининговые специалисты, приходящие на площадку после строителей. А что касается инструмента – мы ведь считаем нормальным, что для работы с цементной фугой требуются шпатель и губка. Так для работы с эпоксидной фугой тоже требуются по сути шпатель и губка, только специальные.
Подводя итог написанному выше, хочется отметить, что с точки зрения потребителя эпоксидная фуга, несомненно, «бьет» традиционные составы на основе цемента. С токи зрения профессионала есть некоторые нюансы, но большинство их сводится к аккуратности и точному соблюдению технологического процесса (главное – инструкцию в первый раз прочитать и не бояться, а том пойдет, как по маслу!). Возникает закономерный вопрос «Почему же тогда на рынке до сих пор процветает и преобладает цементная фуга? Более того, регулярно появляются новые торговые марки и новые продукты!». Однозначного ответа на этот вопрос, пожалуй, нет. Определенную роль играет новизна материала – далеко не все потребители знают о существовании эпоксидной фуги как материала. В какой-то степени влияние оказывает и консерватизм строителей, которые боятся брать на себя ответственность, применяя незнакомый материал. Есть и более прозаическая причина. При всех своих преимуществах эпоксидная фуга имеет более высокую стоимость. В определенной степени это закономерно – более высокое качество требует более высоких затрат. С другой стороны далеко не во всех ситуациях характеристики эпоксидной фуги оказываются объективно востребованными.
Проводя сравнение цементной и эпоксидной фуги в статье, мы слегка слукавили, перечислив те ситуации, в которых эпоксидный состав однозначно лучше цементного. Существует масса приложений, в которых фуги на цементной и эпоксидной основе одинаково имеют право на применение и выбор между ними определяется исключительно бюджетом отделки.
Данная публикация является интеллектуальной собственностью СЗАО «М-Витреа». Перепечатка или иное воспроизведение статьи или ее фрагмента без письменного разрешения СЗАО «М-Витреа» является нарушением «Закона о защите авторских прав».
Затирка для плитки – виды, свойства и характеристики
Опубликовано 24 Апрель 2015 в 12:20
Практически во всех случаях при укладке кафельного покрытия возникают вопросы по поводу того, какая затирка для плитки в ванной лучше, и как затирать межплиточные швы. Поэтому стоит более детально ознакомиться с разновидностями затирочных смесей и с самой техникой ее использования.
Что такое затирка?
Затирка – это специальная строительная смесь, представляющая собой цементный раствор, который до использования находится в порошкообразном виде. Перед применением его разводят необходимым количеством жидкости, после чего полученной субстанцией заполняют межплиточные швы.
В настоящее время все затирочные составы имеют свойство хорошо впитывать влагу. Поэтому проводить сам процесс заполнения швов нужно с некоторым усилием, чтобы материал был вдавлен максимально плотно.
Самыми лучшими смесями на сегодняшний день являются материалы брендов «Ceresit» (Церезит) или «Atlas» (Атлас). Они имеют большое разнообразие цвета, надежно заполняют швы и доступны практически в любом магазине стройматериалов.
Виды затирочных смесей
Современная паста для заполнения швов между плиткой бывает двух основных видов:
- Цементная.
- Эпоксидная.
На основе цемента
Данный вид смеси имеет свои подкатегории:
- На основе портландцемента.
- На основе портландцемента и песка.
Сухие смеси
Стандартная затирочный материал – это цементная смесь с некоторыми возможными добавками, за счет которых она получает определенные характеристики (скорость схватывания, растекаемость и т.д.). Для заделки швов данный состав разводят с водой или жидким латексом.
Использование стандартной цементной пасты возможно только в случае, если швы имеют ширину не менее 5 мм. Допустимая ширина швов и тон цвета указывается на упаковке материала.
Цементная затирка с добавлением песка (двухкомпонентная) имеет лучшие показатели прочности. При выборе такой смеси надо обращать внимание на ее зернистость и ширину межплиточного шва. Чем больше расстояние между плитками, тем крупнее зернистость должна быть у затирочного состава. Что касается его цвета, то он может быть только белым или серым. Другие цветовые гаммы, к сожалению, не предусмотрены.
У обеих разновидностей смесей есть некоторые общие особенности. Например, их можно использовать как на эмалированной плитке, так и неэмалированной. При покупке всегда надо обращать внимание, для какой плитки предназначен затирочный состав. Если поверхность покрыта эмалью, то двухкомпонентная смесь большой зернистости не подойдет – на эмали останутся царапины.
Чаще всего цементные пасты идут вместе с сухим полимером. Но если его нет, то воду надо заменить латексной добавкой. Это необходимо для сохранения первоначального цвета затертых межплиточных швов.
Эпоксидная смесь (на основе смолы)
Эпоксидная смесь
В состав данной затирки входит эпоксидная смола. Дополнительными компонентами этого состава являются отвердитель и красящие пигменты, предназначенные для увеличения плотности, показателей влагостойкости и устойчивости к химическим веществам.
Стоит отметить, что такой вид затирки будет стоить дороже, чем цементные смеси, описанные выше. Но все же высокую цену компенсирует качество.
Есть у данного материала для швов некоторые недостатки, которые создают определенные трудности при работе с ним. Это касается вязкости смеси, из-за которой ее сложно вдавить в шов. Также есть некоторые трудности и при очистке плитки от такой затирки. Поэтому здесь нужно снова обращать внимание на ширину швов. Если данный параметр менее 6 мм, то эпоксидная масса не подойдет. Более того, ее нежелательно использовать на плитке, толщина которой меньше 12 мм – будет сложно заполнить швы смесью.
Также как и цементные пасты, эпоксидные могут иметь в своем составе портландцемент. За счет этого, свойства такой смеси становятся ближе к стандартным цементным затиркам. Но такой двухкомпонентный материал отличается хорошей устойчивостью к загрязнениям в виде пятен, а также он очень прочен по своей структуре.
Если говорить об устойчивости описываемого состава к химическим веществам, то он идентичен цементным затиркам. А вот применять данный материал можно лишь в том случае, если у плитки ровные края.
Затирочная смесь на основе фурановой смолы
Процесс затирки
Эпоксидная паста имеет еще один вид, созданный на основе фурановой смолы. Этот вариант смеси максимально устойчив к любым химическим веществам. Он не боится даже сильных кислот.
Двухкомпонентная паста на основе фурановой смолы содержит в своем составе тот же вид цемента, что и обычные смеси. Также есть варианты с добавлением латекса.
Независимо от того, какие компоненты содержатся в составе затирки, она всегда имеет только черный цвет. Так что принимать решение о покупке такого материала для домашнего ремонта надо обдуманно, приняв во внимание рисунок, цветовую гамму плитки, а также общий стиль кухни. Чаще всего такую затирку используют в промышленных помещениях.
При работе с эпоксидным материалом надо покрывать всю поверхность плитки воском. А остатки смеси смываются только горячим паром. Поэтому и сам процесс заделки межплиточных швов становится не только трудным, но и затратным.
Цветные затирочные смеси
Существует ряд вариантов как сделать из пасты цветную смесь. Для этого достаточно провести процесс смешивания самого материала с краской. Однако такой подход не отличается эффективностью, так как со временем швы потускнеют и потеряют свой исходный цвет. По этой причине и была придумана цветная затирка.
Цветная от польского производителя
Здесь смесь также может быть эпоксидная, цементная или двухкомпонентная. Все параметры, свойства и особенности идентичны вышеописанным смесям, кроме созданных на основе фурановой смолы. Цвет затирки не потеряет своей четкости и будет сохраняться долгое время. На внешний вид шва не повлияет даже ежедневная уборка влажным способом или агрессивные химические вещества.
При выборе таких смесей лучше останавливать внимание на затирке для плитки под маркой «Церезит» или «Атлас». Выбор должен основываться, во-первых, на особенности плитки. То есть нужно учитывать рисунок, основной цвет и форму. Если хочется подчеркнуть геометрию темного рисунка, то здесь надо использовать светлую затирку. При плитке пастельных тонов можно применить темную смесь. А если сложно определиться, то есть нейтральный вариант – натуральный цвет цемента.
Нейтральный цвет пасты лучше всего использовать для плитки с неправильными или нестандартными формами. Слишком контрастные цвета будут сильно выделять неровности материала, и это будет выглядеть не совсем привлекательно. Хотя здесь также надо смотреть по ситуации.
Из качественных цветных смесей стоит отметить:
- «Церезит» – эпоксидные и цементные затирочные пасты, которые без труда можно найти в любом специализированном магазине и с огромным выбором цветовой гаммы.
- «Атлас» – также относится к стандартным затиркам с разными составами, но с меньшим количеством цветов.
Оба варианта подходят для ремонта жилых помещений и имеют различный ценовой диапазон, что делает их доступными.
Технология и особенности затирки плитки
Нанесение между швами
Перед тем как начать проводить заполнение швов пастой, нужно проверить купленную смесь. То есть определить, не будет ли она закрашивать плитку и подходит ли вообще по цвету. Для этого достаточно нанести небольшое количество затирочной смеси на поверхность одной плитки, дать ей время высохнуть и посмотреть какой результат получился. Если итог проверки удовлетворительный, то можно приступать к работе, если нет, то затирку надо поменять на смесь другого цвета.
Для затирки потребуется:
- Небольшой резиновый шпатель.
- Готовая смесь.
- Влажная тряпка или губка.
- Емкость с водой.
- Расшивка.
Первые две вещи надо купить в магазине, а остальные всегда можно найти дома.
Теперь на резиновый шпатель берем немного смеси. Все это переносим на поверхность плитки, держа главный инструмент под наклоном в 30°, и ведем в сторону соседней плитки. При этом, когда шпатель со смесью доходит до шва, надо приложить больше усилий и как бы вдавить затирку в промежуток между плитками. Таким способом нужно заделать все швы.
Заполнение швов должно проходить не менее трех раз. При этом, заполняя каждый шов нужно постоянно прилагать усилия. Тогда затирочная смесь надежно заполнит все пространство между плитками и будет иметь высокую плотность. И в данном случае неважно эпоксидная это затирка или цементная. Также нет разницы «Церезит» это или «Атлас» Прилагать усилия все равно нужно.
Процесс удаления затирки
Вытирание лишнего
Удалять затирочную смесь с поверхности плитки, можно только после того, как затирка в швах схватилась и успела высохнуть. К примеру, «Атлас» схватывается и высыхает за несколько часов – все зависит от густоты раствора.
Существует два варианта удаления затирки:
- Влажное.
- Сухое.
Для влажного удаления понадобится емкость с водой и обычная тряпка или губка. Тряпку надо смочить, хорошо выжать и круговыми движениями протереть облицовочную поверхность. Например, все тот же «Атлас» после высыхания хорошо отмывается, поэтому трудностей в данном процессе возникнуть не должно.
Обязательно надо вовремя смачивать губку и менять воду, чтобы не оставить грязных разводов на плитке.
Сухое удаление пасты – это финишная работа по выравниванию формы швов. Здесь надо взять расшивку (специальная палка с расточенным концом) и с усилиями протянуть ею по каждому шву. В результате затирка приобретет ровные формы.
Заключение
Выбирая затирочную смесь, лучше всего, если это будет затирка для плитки «Ceresit», так как данный производитель за долгое время успел зарекомендовать и показать себя с положительной стороны на отечественном рынке строительных материалов.
Автор:Поделиться материалом:
Комментарии и отзывы к материалу
Узнайте о эпоксидной затирке
29.12.2019 Новости партнеровМногие из нас хотят видеть стены кухни в очень практичной керамической плитке, которая сохраняет прекрасный вид в течении не одного десятилетия, при условии простой, но своевременной ее чистки. Поскольку укладка плитки предполагает наличие большого количества швов, возникает необходимость их заполнения. Наиболее распространенным заполнителем считается цементный раствор, который после высыхания может иметь трещины и к тому же предрасположен к поглощению грязи. Альтернативой ему стала затирка для плитки эпоксидная.
Самым большим плюсом ее являются высокие защитные свойства: устойчивость к кислотам и щелочам, не подверженность грибку и случайным механическим воздействиям, антиусадочный и водоотталкивающий эффект. Кроме того, затвердевшая смесь прекрасно переносит перепады температуры и практически не изменяет свой цвет. В простом понимании такая затирка примером которой является конкурирующая с заграничными аналогами ее версия «Диамант» состоит из двух составляющих – эпоксидной смолы со стеклянными микрошариками – наполнителями и омыляющего отвердителя.
Поскольку покупка названного заполнителя швов обходится гораздо дороже, чем приобретение составляющих для раствора на цементной основе, то нет смысла покупать его излишек. Для этого существует норма расхода затирки для плитки, узнать которую рекомендуется у менеджеров продающей компании. Можно и сразу рассчитать при помощи специального калькулятора, находящегося на ее интернет — ресурсе необходимое количество уникального твердеющего материала, который заполняет даже самые малые промежутки между плитками.
Стоит обратить внимание, что эпоксидной затирке можно придать практически любой оттенок. Это уже используют многие строительные фирмы, укладывающие настенную или напольную плитку в квартирах обывателей или учреждениях различного толка, следуя колеровочной технологии «ДИАМАНТ COLOR». Она заключается в добавлении пигментного красителя желаемого цвета, в том числе и с блестками в отвердитель, а затем смешивание последнего с эпоксидной пастой. Как правильно, пошагово пользоваться затиркой «Diamant» рассказывает инструкция на https://diamantzatirka.ru.
Цементная и эпоксидная затирка: сравнение
ТЕХНОЛОГИЧЕСКАЯ КАРТА
на двухкомпонентную эпоксидную затирку (шовный заполнитель) «Диамант для стеклянной мозаики, керамической плитки и изделий из камня», разработанную и произведенную в России, ООО Компания «Антураж» г. Москва Данная технологическая карта разработана для потребительского рынка и строителей, осуществляющих укладку плит из натурального и искусственного камня, керамической плитки и керамогранита, мозаики всех видов, при проведении ремонта с использованием эпоксидной затирки для заполнения швов. В технологической карте даны основные положения по технике безопасности, организации и проведению работ с эпоксидной двухкомпонентной затиркой «Диамант», а также основные характеристики двухкомпонентной эпоксидной затирки «Диамант».
Содержание:
1. Область применения.
2. Основные характеристики эпоксидной двухкомпонентной затирки «Диамант».
3. Организация и технология производства работ с затиркой.
4. Техника безопасности при работе с шовным заполнителем.
1. ОБЛАСТЬ ПРИМЕНЕНИЯ
Двухкомпонентную эпоксидную затирку можно применять для затирания швов, для внутренних и для наружных работ, в санузлах, на кухнях, во влажных помещениях, в бассейнах, в хамамах, в щелочной и кислотной среде, в производственных цехах, в пищевых цехах, в больницах, в местах общего пользования, в выставочных комплексах с высокой проходимостью. Так же эпоксидную затирку «Диамант» рекомендуется использовать в качестве клея для наклеивания тонкой мозаики (для изделий толщиной менее 5мм), что уменьшает трудозатраты по очистке и подготовке швов для дальнейшего их затирания, а также снижает общий расход материала (клей + затирка).
ВНИМАНИЕ :
1. Бесцветная затирка «Хамелеон» при использовании для наружных работ при воздействии УФ-лучей склонна к пожелтению. При проведении наружных работ рекомендуется использовать только цветные затирки. Пигментная добавка в цветных затирках является дополнительным УФ-фильтром, и защищает швы от пожелтения.
2. Не рекомендуется использовать бесцветную затирку «Хамелеон» и цветную «Титан» для затирания швов светлой плитки с темными неглазурованными торцами ввиду высокой светопропускающей способности наполнителя (стеклянные микрошарики). Проявляется эффект изменения цвета затирки (потемнение затирки).
3. Перед затиркой поверхностей из природного камня и пористых материалов необходимо провести пробный тест в незаметном месте и убедиться, что поверхность не окрашивается.
4. При работе с поверхностью из природного камня и пористых материалов возможно образование эффекта «мокрого камня», приводящего к изменению цветового оттенка поверхности. На пористых материалах не всегда есть возможность удалить образовавшуюся эпоксидную пленку, которая проникает глубоко в структуру камня.
Технологическую карту можно использовать как инструкцию по применению затирки в строительно-ремонтных работах при соблюдении ряда обязательных условий.
2. ОСНОВНЫЕ ХАРАКТЕРИСТИКИ ПРОИЗВОДИМОЙ ПРОДУКЦИИ
Двухкомпонентная затирка (шовный заполнитель) «Диамант» представляет собой смесь высококачественных компонентов – эпоксидной смолы, кристаллического светопреломляющего сферического наполнителя и омыляющегося отвердителя. Она производится согласно техническим условиям ТУ 2312-001-31724482-14. Затирка «Диамант» представлена 26 цветами.. По желанию потребителя затирку можно смешивать с металлизированными цветными добавками , которые усиливают блеск затирки и придают эффект серебристого, золотого, медного, бронзового напыления и т. д. Производитель поставляет 20 различных цветов металлизированной добавки.
!!! Внимание!!! Добавление металлизированной добавки в цветные затирки может существенно изменить итоговый цвет смеси. Поэтому, для лучших результатов, металлизированный наполнитель рекомендуется сочетать с бесцветной затиркой (Хамелеон).
Допустимая ширина швов от 1 до 15 мм на горизонтальной поверхности и от 1 до 10 мм на вертикальной поверхности. Затирка «Диамант» легко наносится резиновым шпателем, благодаря кремообразной консистенции и легко очищается водой в течении 60 минут с момента приготовления смеси. Она обладает высокой эластичностью и прочностью, не дает усадку, не растрескивается. Затирка обладает высокой пластичностью и не вытекает из вертикальных швов. Время отверждения затирки до начала хождения по обработанной поверхности – 24 часа, если на момент затирания швов температура была +23С. Время набора полной механической прочности – 5 суток при температуре +23С. Более низкая температура окружающего воздуха увеличивает время полимеризации материала
3.

В состав работ, рассматриваемых технологической картой, входят:
1. подготовительные работы
- Удалить остатки цементного клея из швов (При работе с затиркой швы должны быть очищены от клея на глубину не менее чем 2/3 от толщины плитки)
- Очень тщательно очистить поверхность материала от пыли, клея, защитных химических и восковых покрытий;
- Очень тщательно очистить швы от пыли и воды парогенератором, тонкой кистью, или пылесосом.
- Плиточный клей должен быть полностью высохшим (смотреть инструкцию производителя клея). Швы должны быть чистыми и сухими.
- Основание должно быть тщательно подготовленным и иметь однородный цвет и не иметь различного рода цветовых различий (ВАЖНО при работе с бесцветной затиркой «Хамелеон» ввиду высокой степени светопропускания данной затирки).
Любая поверхность при заполнении швов должна быть защищена от воздействия прямых солнечных лучей, при относительной влажности воздуха не более 60%. Температура обрабатываемой поверхности должна быть НЕ выше +30С. Температура окружающего воздуха должна быть от + 12С до + 30С.
Лучший результат достигается при температуре от +18С до +23С.
!!! Внимание!!! Не рекомендуется использовать бесцветную затирку «Хамелеон» и полупрозрачную «Титан» для наружных работ на поверхностях подверженных УФ излучению (под солнечным светом). Возможно появление эффекта пожелтения эпоксидной смолы. Для наружных работ рекомендуется использовать только цветную затирку. Не проводить работ под прямыми солнечными лучами, а также необходимо защитить затертую поверхность от солнечных лучей минимум на 24 часа, до момента полной полимеризации затирки.
2. основные работы – приготовление материалов для заполнения швов, заполнение швов затиркой «Диамант» и очистка их после заполнения.
2.1. Для приготовления шовного заполнителя надо добавить компонент В (отвердитель) в емкость с компонентом А (затирочная паста) и тщательно перемешать до получения однородного состава. Для перемешивания смеси можно использовать металлический шпатель или электродрель с насадкой «миксер», для емкостей 2,5 кг. Для перемешивания смеси в емкостях 1 кг. можно использовать металлический шпатель или металлическую ложку. В случае использования металлизированной добавки рекомендуется добавлять:
- на банку 1 кг – 66 гр. (1 пакет 66 гр.металлизированной добавки)
- на банку 2,5 кг – 166 гр. (1 пакет 66 гр. + 1 пакет 100 гр.)
!!!Внимание!!! Увеличение количества металлизированной добавки приводит к сгущению затирочной массы и уменьшению ее пластичности и времени жизни смеси.
2.2. Заполнить швы приготовленным составом. Заполнение швов необходимо производить резиновым шпателем, выполнения движения по диагонали относительно швов, при этом удаляя излишки состава тем же шпателем.
2.3. Швы и поверхность необходимо очистить от излишков состава до его затвердения, не позднее 60 минут с момента его приготовления. Для очистки поверхности использовать смоченную в воде комбинированную целлюлозную губку. Первоначально убрать основные излишки поролоновым слоем и далее использовать целлюлозный слой для формирования швов. Формировать швы круговыми движениями.
При работе с мозаикой, удаление остатков можно начинать сразу после заполнения швов затиркой. При работе с керамической плиткой и керамогранитом, для лучшего формирования шва, начинать удаление остатков примерно через 30-40 минут после приготовления смеси при температуре +230С. Увеличение температуры сокращает время полимеризации смеси.
!!!Внимание!!! со временем поролон разрушается от воздействия эпоксидной смолы. В среднем одна губка рассчитана на 10 м2 обрабатываемой поверхности.
3. заключительные работы.
Остатки затирочного состава (эпоксидную пленку) необходимо удалить с поверхности плитки в течение 12 часов с помощью специального чистящего состава для эпоксидных смол «Диамант+ Light» или «Диамант+» (в соответствии с инструкциями Производителя). Для удаления эпоксидной пленки использовать целлюлозную губку или специальный белый абразивный пад.
!!! Внимание!!! Не использовать абразивный Пад с легко царапающейся мозаикой.
Оптимальное время удаления эпоксидной пленки с использованием очистителя — через 4 часа с момента приготовления затирочной смеси.
!!! Внимание!!! При использовании эпоксидной затирки «Диамант» для затирки мозаики, плитки, камня или керамогранита с матовой шероховатой поверхностью применение очистителя «Диамант+» и целлюлозной губки для удаления эпоксидной пленки обязательно!!!. При работе с такой поверхностью рекомендуется применить смывку через 2 часа с момента приготовления затирочной смеси. Смывку «Диамант+» разбавить водой в соотношении 1:2 (на 1 часть смывки добавить 2 части воды). Рекомендуется использовать белый абразивный пад.
После работы с затиркой руки и инструменты очистить водой и очистителем, пока состав свежий.
4. ТЕХНИКА БЕЗОПАСНОСТИ ПРИ РАБОТЕ С ШОВНЫМ ЗАПОЛНИТЕЛЕМ Эпоксидная затирка «Диамант», после полимеризации является абсолютно безопасной для людей и окружающей среды.

Эпоксидные смолы, а также отвердители, до момента полимеризации, токсичны и вредно действуют на кожу и слизистую оболочку. Поэтому при работе с ними необходимо соблюдать определенные правила техники безопасности, которые заключаются в следующем:
1. Использовать средства индивидуальной защиты (резиновые перчатки средства защиты глаз и органов дыхания)Хранить исходные материалы в открытом виде в жилом помещении запрещается.
2. Беречь от огня
3. Беречь от детей и домашних животных;
4. Производить работы в хорошо проветриваемом помещении
5. Не выбрасывать в окружающую среду
6. Вызывает раздражение кожи. Может вызывать аллергические реакции на коже
7. При попадании на кожу промыть большим количеством воды
8. При попадании в глаза тщательно промыть большим количеством воды
9. При необходимости обратиться к врачу
ИНСТРУКЦИЯ ОЧИСТИТЕЛЬ ДЛЯ ЭПОКСИДНЫХ МАТЕРИАЛОВ ДИАМАНТ+
ОПИСАНИЕ: «ДИАМАНТ+» это жидкий гелеобразный очиститель для удаления остатков, пятен и разводов от эпоксидной затирки. Очиститель может использоваться в неразбавленном виде, а также разбавляться водой во всех соотношениях в зависимости от характеристики и типа загрязнений, подлежащих удалению. Не рекомендуется использовать очиститель «ДИАМАНТ+» ранее 2 часов после заполнения швов затиркой. Оптимальное время удаления эпоксидных остатков- через 4 часа после приготовления затирочной смеси. (Время указано для температуры окружающей среды +230С и влажности воздуха 60%).
ПРИМЕНЕНИЕ: Очиститель «ДИАМАНТ+» предназначен для очистки от эпоксидных остатков любых типовкерамических покрытий, в том числе и керамогранита, а также мозаики,стекломозаики, всех видов натурального камня. Перед применением рекомендуется произвести тест в незаметном месте.
НЕ ПРИМЕНЯТЬ: На основаниях, являющихся неустойчивыми к воздействию щелочей.
Перед применением рекомендуется защитить двери, окна, резиновые уплотнители, мебель, лакированные предметы, ванны и душевые поддоны из синтетических материалов, таких как: акрил, ПВХ и т. д. и все поверхности, которые могут подвергаться воздействию прямого контакта или паров продукта. Благодаря гелеобразной консистенции производить работы можно как на горизонтальных, так и вертикальных поверхностях.
1. Для удаления свежих остатков затирки,а также пленки, пятен и разводов от эпоксидной затирки рекомендуемся разбавить очиститель с водой в соотношении от 1:1 до 1:5 (одна часть очистителя на 5 частей воды).
Концентрацию раствора лучше подбирать опытным путем,в зависимости от поверхности затираемого материала и времени, прошедшего с момента приготовления затирки и температуры окружающей среды. Необходимо учитывать, что при увеличении температуры окружающей среды скорость полимеризации эпоксидной затирки увеличивается. Очиститель обязателен для применения с плиткой или керамогранитом, имеющим шероховатую матовую поверхность (для таких поверхностей концентрацию раствора увеличить). Разбавленный раствор перемешать.
Для удаления свежих эпоксидных остатков, пятен и разводов использовать целлюлозную губку. Очистку поверхности проводить плавными движениями, сильно не нажимая на губку во избежание повреждения швов. Не допускать взаимодействие свежезатёртой эпоксидной затирки с очистителем«ДИАМАНТ+» более 2-3 минут. Далее всю обработанную поверхность ОБЯЗАТЕЛЬНО смыть тёплой мыльной водой. Если остатки эпоксидной затирки остались на поверхности, повторить процедуру.
2. Для удаления застаревших эпоксидных остатков, использовать неразбавленный очиститель. Нанести очиститель на поверхность кисточкой или губкой, покрывая все остатки. Оставить действовать примерно на 30 минут. Это время может меняться, в зависимости от устойчивости эпоксидных остатков. Если остатки очень устойчивы – оставить средство воздействовать в течении более продолжительного времени. Удалять остатки послойно до получения необходимого результата.
ТЕХНИЧЕСКИЕ ДАННЫЕ:
Внешний вид бесцветная гелеобразная жидкость
Температура применения от +9°С до +35°С.
Хранение ≈ 12 месяцев в оригинальной упаковке
Температура хранения от +5°С до +35°С.
Примечания беречь от мороза, предохранять от непосредственного воздействия солнечных лучей и источников тепла упаковка бутылка 0,5 л
Соотношение смешивания с водой — в любых пропорциях
pH ≈ 11,5
МЕРЫ БЕЗОПАСНОСТИ:
Хранить в недоступном для детей и домашних животных месте. Продукт может вызывать раздражение. Работы с «ДИАМАНТ+» производитьв средствах индивидуальной защиты (резиновые перчатки, средства защиты глази органов дыхания) При попадании средства на кожу или глаза смыть большим количеством воды. При необходимости обратитесь за медицинской консультацией (помощью). Во время работы не оставлять упаковку вскрытой.
ИНСТРУКЦИЯ ОЧИСТИТЕЛЬ ДЛЯ ЭПОКСИДНЫХ МАТЕРИАЛОВ ДИАМАНТ+Light
ОПИСАНИЕ: «Диамант + Light» это жидкий очиститель для удаления свежих остатков от эпоксидной затирки (не более 12 часов после нанесения затирки на обрабатываемую поверхность), пятен и разводов от эпоксидной затирки. Использовать в неразбавленном виде. Не рекомендуется использовать очиститель «Диамант + Light» ранее 2 часов после заполнения швов затиркой. Перед применением рекомендуется произвести тест в незаметном месте.
НЕ ПРИМЕНЯТЬ: На основаниях, являющихся неустойчивыми к воздействию щелочей
Перед применением рекомендуется защитить двери, окна, резиновые уплотнители, мебель, лакированные предметы, ванны и душевые поддоны из синтетических материалов, таких как: акрил, ПВХ и т.д. и все поверхности, которые могут подвергаться воздействию прямого контакта или паров продукта. Благодаря гелеобразной консистенции производить работы можно как на горизонтальных, так и вертикальных поверхностях.
ПРИМЕНЕНИЕ: предназначен для очистки от эпоксидных остатков любых типов керамических покрытий, в том числе и керамогранита, а также мозаики, стекломозаики, всех видов натурального камня. Производить работы можно как на вертикальных, так и горизонтальных поверхностях. Перед применением хорошо взболтать флакон с жидкостью. Для удаления свежих эпоксидных остатков, пятен и разводов предпочтительно использовать целлюлозную губку. Сначала использовать жесткую губку с небольшим количеством очистителя«Диамант + Light», потом используйте мягкую сторону губки и также с небольшим количеством очистителя. Очистку поверхности проводить плавными движениями, сильно не нажимая на губку, во избежание повреждения швов. Не допускать взаимодействие свежезатёртой эпоксидной затирки с очистителем «Диамант + Light» более 3 минут. Далее всю обработанную поверхность ОБЯЗАТЕЛЬНО смыть мыльной тёплой водой. Если остатки эпоксидной затирки остались на поверхности, повторить процедуру.
ТЕХНИЧЕСКИЕ ДАННЫЕ:
Внешний вид бесцветная гелеобразная жидкость
Температура применения от +9°С до +35°С.
Хранение ≈ 12 месяцев в оригинальной упаковке
Температура хранения от +5°С до +35°С.
Примечания беречь от мороза, предохранять от непосредственного воздействия солнечных лучей и источников тепла упаковка бутылка 0,5 л спрей
Соотношение смешивания с водой — в любых пропорциях pH ≈ 9,0
Расход л. /кв.м.: 0,2
МЕРЫ БЕЗОПАСНОСТИ:
Хранить в недоступном для детей и домашних животных месте. Продукт может вызывать раздражение. Работы с «Диамант + Light» производить в средствах индивидуальной защиты (резиновые перчатки, средства защиты глаз и органов дыхания)
При попадании средства на кожу или глаза смыть большим количеством воды. При необходимости обратитесь за медицинской консультацией (помощью) Срок хранения 12 месяцев в оригинальной фирменной упаковке.
Сверхбыстрая бетонная эпоксидная шпатлевка
Описание
Superfast Concrete Epoxy Putty Stick — это простая в использовании эпоксидная шпатлевка в форме карандаша, которая используется в качестве наполнителя при реставрации и для быстрого ремонта бетона и кирпичной кладки.
После затвердевания Superfast Concrete приобретает серый цвет, а внешний вид и текстура похожи на бетон. Его можно использовать для высокопрочного соединения бетона с бетоном, что позволяет ремонтировать сломанные или расколотые украшения, статуи или надгробные плиты. Он также связывает бетон с деревом, металлами, стеклом и многими пластиками.
Superfast Concrete можно использовать для заполнения трещин и щелей в дорожках, ступенях и перилах. Ремонт плитки, полов и надгробий. Его можно использовать для заделки отверстий под стяжные шпильки, для анкеровки креплений в бетоне и подходит для внутреннего или внешнего использования.
Устойчив к воде, химикатам и перепадам температур, быстро действует, затвердевает в течение 5-10 минут.
Как использовать Superfast Concrete Epoxy Putty Stick для ремонта и восстановления бетонных шпатлевок
Superfast Concrete поставляется в предварительно отформатированной палочке размером 11 г / г диаметром 22 мм и длиной 175 мм.Для использования достаточно просто отрезать от палочки необходимое количество шпатлевки и замесить вручную.
Шпаклевке, пока она мягкая, можно придать форму и использовать ее по мере необходимости. При нанесении наполнителя его вставляют в отверстия и трещины, где он застывает, чтобы заполнить поврежденную область. Для склеивания вы наносите замазку и с ее помощью соединяете детали, требующие ремонта, вместе.
Superfast Concrete составляет около 4 минут. В течение 5-10 минут он затвердеет и образует прочную связь. После отверждения его можно нарезать резьбой, просверлить, распилить, подпилить и покрасить.
Не содержит растворителей или летучих органических соединений, не воспламеняется и не выделяет ядовитых паров. Он не сжимается и не отрывается, а неиспользованная часть Concrete Stick остается свежей для использования в будущем при сохранении в оригинальной упаковке.
Для более сложного ремонта бетонной шпатлевки или адгезива, требующего замазки с более длительным временем отверждения, см. Sylmasta AB Original. AB Original рассчитан на 2 часа работы, что позволяет смешивать, формировать и наносить больше шпатлевки, не беспокоясь о преждевременном отверждении.
Преимущества эпоксидной шпатлевки для бетона Sylmasta
- По внешнему виду и структуре напоминает бетон после затвердевания
- Ремонт занимает менее 10 минут
- Простота использования — срезать шпатлевку, замесить вручную, нанести
Приложения
- Заполнение отверстий в бетонных дорожках, ступенях и плитке
- Ремонт сломанных стен и статуй
- Склеивание фрагментов бетонных украшений вместе
- Высокопрочная связь между бетоном и деревом, металлами и большинством пластмасс
- Анкеровка крепежа в бетоне и заделка отверстий для анкерных шпилек
Взаимодействие между цементной пастой и эпоксидным клеем — ScienceDirect
https: // doi.
Реферат
В области гражданского строительства долговечность бетонных сборок с использованием клея в значительной степени зависит от свойств поверхности раздела между смолой и минеральной основой (бетон ). В этом контексте мы сначала изучили молекулярные взаимодействия на границе раздела между эпоксидной смолой и цементными пастами с помощью нескольких подходов, основанных на XPS и ИК спектроскопии, DSC и обратной газовой хроматографии (IGC).XPS показал доказательства сшивания полимера на поверхности затвердевшей цементной пасты. Химические сдвиги XPS пика N1s от адсорбированного отвердителя свидетельствовали о существовании межфазных донорно-акцепторных взаимодействий между цементом и отвердителем. Такое специфическое взаимодействие, вероятно, является причиной повышения температуры стеклования ( T g ) клея вблизи поверхности цементной основы. Изучение FTIR взаимодействий эпоксидного клея с основными гидратами, взятыми отдельно (а именно, C – S – H, эттрингитом и портландитом), позволило лучше понять сложную межфазную систему цементный клей – клей. Было обнаружено, что определяемые IGC дисперсионные и кислотно-основные компоненты поверхностной энергии цементных паст после нанесения покрытия уменьшаются, что коррелирует с данными о химическом составе поверхности. Анализ XPS небольшой площади межфазной поверхности между цементным тестом и адгезивом выявил на прототипе цементной пасты и адгезивного соединения модификации областей Ca2p и N1s, что позволяет предположить, что эта зона является локусом химических реакций, способствующих адгезии минерального субстрата и смолы. XPS небольшой площади убедительно показал наличие диффузной межфазной границы, а не резкой границы раздела цементный клей и клей.
Ключевые слова
Цементная паста
C – S – H
Эттрингит
Портландит
Клеи
Адгезия
Смачивание
Поверхностная энергия
Стеклование полностью Copyright © 2010 Elsevier Ltd. Все права защищены.
Рекомендуемые статьи
Цитирующие статьи
Эпоксидная паста для заполнения трещин под водой для ремонта бетона и кирпичной кладки
ИНСТРУКЦИЯ ПО СМЕШИВАНИЮ И НАНЕСЕНИЮ
1) ХРАНЕНИЕ ПРОДУКТА : Храните продукт в таком месте, чтобы довести материал до нормальной комнатной температуры перед использованием. Температура непрерывного хранения должна составлять 50-90 ° F. Избегайте низких температур и больших колебаний температуры при хранении, так как эти условия могут вызвать возможную кристаллизацию продукта. 2) ПОВЕРХНОСТЬ ПОДГОТОВКА : Вся грязь, посторонние загрязнения, масляные загрязнения и цементное молоко должны быть удалены, чтобы обеспечить надежное соединение с основанием. Этот продукт предназначен для микротрещин и других трещин шириной до 1/8 дюйма. Удалите весь непрочный бетон из трещины, которую необходимо отремонтировать, и тщательно удалите весь мусор из трещины. 3) PRIMER : Грунтовка не требуется. 4) СМЕШИВАНИЕ ПРОДУКТА: Этот продукт имеет соотношение смешивания 2 частей A к 1 части B по объему. Чтобы перемешать, просто отмерьте соответствующие объемы материала и тщательно перемешайте их вместе с помощью низкоскоростного смесительного оборудования, такого как миксер, шпатель или шпатель, пока материал не станет полностью перемешанным и однородным по цвету.
Смешивайте только то количество материала, которое можно использовать в течение отведенного периода жизнеспособности. Неправильное смешивание может привести к выходу продукта из строя.Для достижения наилучших результатов смешивания и правильного смешивания частей A и B рекомендуется дрель-миксер Jiffy Mixer. 5) НАНЕСЕНИЕ ПРОДУКТА: Смешанный материал можно наносить краевым шпателем, шпателем или любым другим подходящим оборудованием. Важно тщательно нанести пасту на место ремонта, чтобы удалить воду из зоны ремонта. Этот продукт можно использовать под водой, а также в любой области, где поток воды невозможно контролировать. 6) ПОВТОРНОЕ ПОКРЫТИЕ ИЛИ ПОВЕРХНОСТНОЕ ПОКРЫТИЕ: При ремонте под водой мы не рекомендуем наносить верхнее покрытие.Однако в тех областях, где может произойти загрязнение водой во время процесса отверждения, но после нанесения верхнего покрытия, наш NP600L можно эффективно использовать. Ознакомьтесь с техническими данными NP600 перед использованием или свяжитесь с вашим торговым представителем для получения более подробной информации.
Перед нанесением верхнего покрытия дайте NP601 стать свободным от липкости. Наносить NP601 в несколько слоев можно, и они легко склеиваются. 8 ) ОЧИСТКА ПОВЕРХНОСТИ : Осторожно! Некоторые чистящие средства могут повлиять на цвет нанесенного геля быстрого схватывания. Испытайте каждый очиститель на небольшом участке, используя вашу технику очистки.Если никаких побочных эффектов не наблюдается, вы можете продолжить очистку с помощью протестированного продукта и процесса. 9) ОГРАНИЧЕНИЯ : Ограничьте использование пола легким движением и не агрессивными химическими веществами до полного отверждения покрытия (см. Технические данные в разделе «Полное отверждение»). Лучше всего, чтобы пол оставался сухим в течение полного цикла отверждения. В зависимости от фактического применения системы в целом поверхность может быть скользкой, особенно если она влажная или загрязненная; держите поверхность чистой и сухой.
- Стабильность цвета может зависеть от условий окружающей среды, таких как погружение, температура или химическое воздействие.
- Цвета могут отличаться от партии к партии.
- Этот продукт не является устойчивым к УФ-излучению и обесцвечивается под воздействием УФ-лучей или некоторых внутренних источников освещения, например, натриевых ламп.
- Весь новый бетон должен быть выдержан не менее 30 дней перед нанесением.
- Рекомендуется разместить тестовые пластыри перед проведением ремонта под водой или при загрязнении водой, чтобы убедиться в совместимости продукта и поверхности.
- Температура воды может увеличивать или уменьшать время отверждения материала в зависимости от температуры воды.
- Физические свойства, перечисленные в этом техническом паспорте, являются типичными значениями, а не спецификациями.
УВЕДОМЛЕНИЕ ДЛЯ ПОКУПАТЕЛЯ: ОТКАЗ ОТ ГАРАНТИЙ И ОГРАНИЧЕНИЙ НАШЕЙ ОТВЕТСТВЕННОСТИ Мы гарантируем, что наши продукты производятся в строгом соответствии со спецификациями обеспечения качества и что предоставленная нами информация является точной, насколько нам известно. Такая информация о наших продуктах не является представлением или гарантией. Он предоставляется при условии, что вы проведете свои собственные испытания, чтобы определить пригодность нашего продукта для вашей конкретной цели.Ответственность за любое использование или приложение, отличное от рекомендованного в данном документе, является исключительной ответственностью пользователя. Перечисленные физические свойства являются типичными и не должны рассматриваться как спецификации. НИКАКИХ ГАРАНТИЙ НЕ ПРЕДОСТАВЛЯЕТСЯ, ЯВНЫХ ИЛИ ПОДРАЗУМЕВАЕМЫХ В ОТНОШЕНИИ ДРУГОЙ ИНФОРМАЦИИ, ДАННЫХ, НА КОТОРЫХ ЕГО ОСНОВАНА, ИЛИ РЕЗУЛЬТАТОВ, КОТОРЫЕ ВЫ ПОЛУЧИТЕ В РЕЗУЛЬТАТЕ ЕГО ИСПОЛЬЗОВАНИЯ. ГАРАНТИЯ НЕ ПРЕДОСТАВЛЯЕТСЯ, ВЫРАЖАЕТСЯ ИЛИ ПОДРАЗУМЕВАЕТСЯ, ЧТО НАША ПРОДУКЦИЯ ДОЛЖНА БЫТЬ ТОВАРНОЙ ИЛИ НАША ПРОДУКЦИЯ ПОДХОДИТ ДЛЯ ЛЮБЫХ КОНКРЕТНЫХ ЦЕЛЕЙ. НЕ ПРЕДОСТАВЛЯЕТСЯ ГАРАНТИИ, ЧТО ИСПОЛЬЗОВАНИЕ ТАКОЙ ИНФОРМАЦИИ ИЛИ НАШЕГО ПРОДУКТА НЕ ЯВЛЯЕТСЯ НАРУШЕНИЕМ НИКАКИХ ПАТЕНТОВ.Мы не несем ответственности за случайные или косвенные убытки, прямые или косвенные.
Наша ответственность ограничивается чистой продажной ценой нашего продукта или заменой нашего продукта, по нашему выбору. Принятие доставки нашего продукта означает, что вы приняли условия этой гарантии, независимо от того, содержат ли заказы на покупку или другие документы условия, которые отличаются от данной гарантии. Ни один представитель не уполномочен делать какие-либо заявления, давать гарантии или брать на себя какие-либо другие обязательства от нашего имени при продаже наших продуктов.Наши продукты содержат химические вещества, которые могут вызвать СЕРЬЕЗНЫЕ ФИЗИЧЕСКИЕ ТРАВМЫ. ПЕРЕД ИСПОЛЬЗОВАНИЕМ ПРОЧИТАЙТЕ ПАСПОРТ БЕЗОПАСНОСТИ МАТЕРИАЛА И СОБЛЮДАЙТЕ ВСЕ МЕРЫ ПРЕДОСТОРОЖНОСТИ, ЧТОБЫ ПРЕДОТВРАТИТЬ ВРЕД ДЛЯ ТЕЛА.
Эпоксидный цемент — Производитель эпоксидного цемента из Ахмедабада
ЛИДЕРЫ В ТЕХНОЛОГИЯХ СВЯЗИ
BOND –AD-04
ЭПОКСИДНЫЙ КЛЕЙ ОБЩЕГО НАЗНАЧЕНИЯ ЭПОКСИДНЫЙ КЛЕЙ 9000 ЭПОКСИДНЫЙ КЛЕЙ общего назначения, не имеющий отношения к общему назначению. сила.Оба доступны в жидкой консистенции, легко смешиваемой, и готовы к немедленному применению. Универсальный клей , подходящий для склеивания, заливки, герметизации, сантехники, заливки, герметизации, оснастки, покрытия и т. Д. Для промышленных и бытовых применений, таких как Текстильная, литейная, электротехническая, электронная, строительная, инженерная, автомобильная и морская . Он может связывать что угодно с чем угодно, начиная от дерева, резины,
стекла, фарфора, волокна, кожи, бумаги, камня, керамики, металла (черных и цветных), слоновой кости, гранита, асбеста, картона, фарфора и т. Д. большинство пластиков, кроме некоторых пластиков и тефлона. Успех эпоксидного клея обусловлен их низкой усадкой, высокой прочностью сцепления, хорошей светостойкостью, хорошей механической стойкостью к воздействию тепла, влажности и химикатов.
СООТНОШЕНИЕ СМЕШИВАНИЯ И СРОК СЛУЖБЫ: —
Части A и B должны быть смешаны в соотношении 10:08 по весу или (1: 1 по объему), когда меньшая пропорция Части- B, химическая стойкость выше, но сцепление немного ниже. Более высокая доля Части B соответствует соотношению компонентов 1: 1 по объему и обеспечивает максимальную прочность сцепления.
Два компонента необходимо смешать перед использованием. Жизнеспособность зависит от комнатной температуры, температуры смеси. Чем выше темп. и чем больше смесь, тем короче ее жизнеспособность. Хорошего компромисса можно достичь, регулируя температуру и количество смеси. Так что жизнеспособности хватит для применения. Обычно при смешивании 50 граммов каждого из вышеперечисленных веществ обеспечивают жизнеспособность от 30 до 60 минут приблизительно при комнатной температуре.
Количество смеси должно быть как можно меньшим, чтобы продлить срок службы системы смешивания.Смешанное количество более 100 грамм сокращает жизнеспособность.
Дополнительная информация:
- Порт отгрузки: Нхавашива Пипавав
- Производственная мощность: 10000 кг
- Срок поставки: 15 дней
Взаимодействие между цементной пастой и эпоксидным клеем | Запрос PDF
Влияние 50% заполнения эпоксидной смолы ЭД20 исходным и водоочищенным строительным вяжущим — цементом М400 (в исходном и водоотвержденном состоянии) на прочность, морфологическую структуру и физико-механические свойства композитов. исследуется.Обнаружено повышение таких показателей, как модуль упругости, огнестойкость, термостойкость, стойкость к ацетонсодержащим органическим растворителям. Методами оптической и СЭМ микроскопии выявлено различие в структуре составов и полимерных композитов с дисперсными частицами исходного и водоотвержденного цемента. Несмотря на это, при мягкой или нормальной термообработке (50-60 и 100-110 ° С) прочностные характеристики в основном сохраняются. После жесткой обработки при 250 ° C для наполненных композитов был обнаружен эффект, который мы назвали «упрочнение эпоксидных композитов термическим разрушением».Это значительное увеличение прочности (или пластичности) после температур 250-300 ° C (разложение обычных ненаполненных полиэпоксидов). Ключевые слова: эпоксидный композит, исходный цемент, водоотвержденный цемент, прочность на сжатие / изгиб, модуль, истирание, отрывная адгезия, огнестойкость, набухание, термическое упрочнение, термопластичность, терморазрушающее твердение. Выводы.
1. Введение в эпоксидную смолу дисперсий цемента и гипса позволяет получать темные седиментационно-стойкие хорошо сформированные массы, отверждаемые в обычном режиме.Морфологически составы представляют собой агрегатную смесь со своей структурой наполнителя и редкими воздушными включениями. 2. После отверждения микроструктура композитов отличается от исходного и водоотверждаемого цемента. Исходный (неотвержденный) цемент дает плотную непористую массу, разделенную на области размером 100-500 микрон, а затвердевший — пористую массу без пескоструйной обработки, что характерно для инертных микронаполнителей. 3. Во всех случаях наблюдается заметное (на 25-70% и более) увеличение адгезии при отрыве, микротвердости и модуля при изгибе.Введение цемента дает увеличение модуля (при сжатии и изгибе), сопротивления истиранию и практически сохраняет исходный показатель прочности на сжатие для композитов с мягкой (55 ° C) термообработкой. 4. Характер предварительной обработки взятых наполнителей существенно влияет на изменение модулей упругости.
Так, модуль изгиба увеличивается примерно в 1,6-3 раза (очень сильно) для композитов с исходными наполнителями, а с затвердевшими — примерно в 1,5 раза. Напротив, модуль сжатия увеличивается незначительно (на 5-15%), но у предварительно гидратированного цемента он выше.5. Заполнение лишает композит пластичности, переводя его в упруго-хрупкое состояние, о чем свидетельствует изменение типа диаграмм сжатия (с двухступенчатых на одноступенчатые) и модуля упругости. Характер предварительной обработки наполнителя не влияет на его влияние на вязко-хрупкое поведение во время разрушения при сжатии. 6. Введение этих наполнителей позволяет значительно повысить стойкость композита к агрессивному растворителю (смесь ацетон-этилацетат).Однако устойчивость к кислой водной среде (25% азотная кислота) снижается. Заливка цементом в обеих формах не приводит к заметному изменению водопоглощения. 7. Армирующий эффект цемента хорошо заметен после нагрева составов при экстремальных температурах. После 250 ° C прочность на сжатие композитов с исходным цементом практически не меняется, а с предварительным отверждением увеличивается, а ненаполненный полимер заметно (на треть) теряет прочность.
После прогрева до 250 ° C стойкость к истиранию заметно увеличивается (уменьшается масса истираемой массы), а у ненаполненной — уменьшается.Эти эффекты получили название термического упрочнения и термической пластификации композитов. Они показывают хорошие резервы для повышения термической прочности эпоксидов простым добавлением водосвязывающих веществ. 8. В работе показаны большие перспективы заливки эпоксидов водоотверждающими связующими для упрочнения и придания новых свойств. Обнаруженные эффекты термического упрочнения и термопластификации показывают, что такая шпатлевка придает эпоксидной смоле ранее нехарактерные свойства, которые очень важны в ряде ответственных применений в промышленности, ремонте и создании новых материалов.
Сверхбыстрый эпоксидный цемент Elmer :: Направления для меня
- Дом
- Клей / Клей
- Сверхбыстрый эпоксидный цемент Elmer
Проезд
Применение: поверхности должны быть чистыми, сухими, обезжиренными и обезжиренными. 1. Удалите таблетки и выдавите равномерное количество смолы и отвердителя на чистую поверхность для смешивания.
2. После тщательного перемешивания нанесите эпоксидную смолу на склеиваемую поверхность и прочно скрепите детали в течение 5-10 минут.Нанесите цемент на одну из склеиваемых поверхностей.
3. Подождите 12-24 часа для полного высыхания.
Сохраните эту карту на весь срок службы продукта.
Описание
Сверхбыстрый эпоксидный цемент Elmer’s®. Быстрое отверждение, жесткое, прочное соединение. Адгезия к пластику, металлу + дереву. Без усадки. Внутри снаружи. Без растворителей — без летучих органических соединений. Установить время 5 мин. Время отверждения 1 час. Сохнет янтарь, негорючий. 1 жидкая унция 29,5 мл.Другое Описание
Применение: быстрое и прочное склеивание пластмасс, дерева или металла.Заказать E1009. 1-888-516-2502. www.elmers.com. © 2006 Elmer’s Products, Inc.Состав
Содержит: три (диметиламиноэтил) фенол, трис (диметиламиноэтил) фенол, эпоксидную смолу.
Предупреждения
Предупреждение: может причинить вред при проглатывании, контакте с кожей или проглатывании. Раздражает глаза или кожу. Воздействие может вызвать аллергические реакции. См. Заднюю панель.Меры предосторожности: избегать контакта с кожей и проглатывания. Вымойте руки сразу после использования. При использовании надевайте непроницаемые защитные перчатки.Беречь от глаз.
Храните в недоступном для детей месте.
Первая помощь: при попадании в глаза промыть проточной водой в течение 5-10 минут. Если раздражение не проходит, обратитесь за медицинской помощью. При попадании на кожу промойте водой с мылом в течение 5 минут. При проглатывании немедленно обратитесь за медицинской помощью.
Для получения дополнительной информации о состоянии здоровья обратитесь в токсикологический центр или позвоните по бесплатному телефону 1-888-516-2502.
Дистрибьютор
Продукты Элмера, ИнкКолумбус, штат Огайо 43219
1-888-516-2502
www.

UPC
00026000010092
Когда использовать эпоксидную смолу вместо суперклея и других адгезивов
Вы, наверное, слышали поговорку: «Если она двигается и не должна двигаться, используйте изоленту». Забавно, но это тоже срабатывает… иногда. Не так уж и смешно то, что, когда это не работает, он терпит неудачу. Когда дело доходит до склеивания, существует множество вариантов клея для различных материалов и уровней нагрузки. Как они сравниваются? Эпоксидная смола по сравнению с суперклеем (цианоакрилат) или силиконом, вулканизирующимся при комнатной температуре (RTV), например, у всех есть свои лучшие — и худшие — применения.
Два типа клея Помимо металлических деталей, легковые и грузовые автомобили и аксессуары изготавливаются из пластика, резины, кожи и поликарбонатов, а также других материалов. Когда компонент смещается, замена — хорошее решение, но иногда вам нужно более быстрое решение, пока вы не сможете добраться до ремонтной мастерской. Эпоксидная смола, суперклей и клейкая лента — отличные временные решения, но что лучше всего подходит для вашей ситуации? Ключи к пониманию того, использовать ли эпоксидную смолу или нет.суперклей или силикон по сравнению с уретаном — это совместимость и применение.
Есть два типа клеев. Эпоксидная смола, суперклей, уретан, полиуретан и силикон — это реактивные клеи, отверждающиеся химически. Строительный клей и контактный цемент, с другой стороны, являются «инертными» клеями, отверждаемыми испарением. После испарения растворителя оставшийся клей склеивает детали.
Различные клеи также имеют дополнительные нюансы в своих химических процессах. Например, двухкомпонентные клеи начинают отверждаться, когда две части смешиваются вместе, склеивая части.И наоборот, однокомпонентные клеи, такие как суперклей и силикон, реагируют на воздействие ультрафиолетового (УФ) света, тепла или влаги.
Эпоксидная смола и суперклей на разных материалах Чтобы получить максимальную отдачу от ремонта, выберите клей в соответствии с материалом, с которым вы работаете. Вот краткое руководство:
- Эпоксидная смола: металл, резина, стекло, пластик, стекловолокно и пластик, армированный стекловолокном (FRP)
- Акрил: металл, резина, стекло, пластик, стекловолокно, FRP и поликарбонат (PC)
- Уретан : металл, резина, поливинилхлорид (ПВХ), стекло, пластик, стекловолокно, FRP и ПК
- Полиуретан: металл, резина, ткань, кожа и холст
- Цианакрилат: металл, пластик, ткань, кожа и холст
- Силикон: металл, резина, стекло, холст, стекловолокно и FRP
- Контактный клей: резина, ткань, кожа и холст
- Строительный клей: металл, ткань, кожа и холст
Обратите внимание на одно предостережение при ремонте с использованием пластика: большинство клеев работают только хорошо с одним пластиком, например, акрилонитрилбутадиенстиролом (АБС) или полипропиленом (ПП).Для достижения наилучших результатов выберите совместимый клей. Например, цианоакрилат несовместим с акрилом, ABS и некоторыми смесями PE (полиэтилена), PP и PC. На наклейке будет более подробная информация.
Подбирая клей с вашим материалом, пора подумать о применении, требуемой прочности и воздействии.
- Эпоксидная смола является самым сильным из реактивных клеев и устойчива к высоким температурам, растворителям, ультрафиолетовому излучению и ударам.Эпоксидная смола застывает от 2 до 60 минут (чем дольше, тем прочнее), а полная прочность достигается за 24 часа.
- Акрил требует меньшей подготовки поверхности, чем эпоксидная смола, но он слабее. Он затвердевает за 3–20 минут, а для достижения полной прочности требуется до 48 часов.
- Силикон затвердевает в присутствии влаги, затвердевает через 20-40 минут и набирает полную прочность через 1-3 дня. Лучше всего он работает в качестве герметика между двумя компонентами, например, в установках с уплотняющими прокладками (FIPG).
- Уретановый клей прочный и эластичный.Лучше всего использовать его для склеивания и герметизации лобовых стекол современных автомобилей.
Он ударопрочный: полимеризация занимает до двух часов, а полная — до недели.
- Цианакрилат быстрый и прочный, но хрупкий. Лучше всего использовать его для точной подгонки, например, для треснувшего пластика или металла, где капиллярное действие может втягивать клей в ремонт. Обычно это лучший выбор для склеивания небольших неподвижных деталей с низким напряжением.
- Строительный клей — это прочный, слегка эластичный клей, для высыхания которого требуется от 10 до 30 минут и от 12 до 24 часов для полного отверждения.Он также обладает высокой устойчивостью к перепадам температуры, воздействию воды и химикатов.
Перед тем, как приступить к нанесению, убедитесь, что в вашей рабочей зоне нет ничего, что может быть повреждено при контакте с клеем. Также не забудьте внимательно прочитать инструкции, даже если они кажутся очевидными. У каждого продукта будет немного другой процесс.
Не забывайте всегда использовать подходящий клей для выполняемой работы и сохраняйте изоленту для временного ремонта!
Ознакомьтесь со всеми химическими продуктами, доступными на NAPA Online, или доверьтесь одному из наших 17 000 пунктов обслуживания AutoCare NAPA для текущего обслуживания и ремонта.