Изготовление арболита своими руками: технология производства и самостоятельные работы
Поэтапная технология изготовления арболита предвидит подготовку основания, определения компонентов и состава блочного материала. В данной статье рассмотрим особенности производства своими руками с применением необходимого оборудования, расчета массы и заливки.
Оглавление:
- Преимущества и недостатки арболита
- Технология производства арболита
- Подготовка основания для работы
- Компоненты и состав арболита
- Процесс и принципы изготовления
- Оборудование: применение на практике
- Блочные формы для арболита
- Процесс производства своими руками
- Советы экспертов при изготовлении блоков своими руками
Преимущества и недостатки арболита
Для многих строителей арболитные блоки являются ценным и качественным материалом для возведения домов.
1. Прочность материала составляет 600-650 кг/м3, что по компонентной структуре не уступает иному строительному материалу. Главной особенностью является пластичность, что формируется в результате использования древесины, которая качественно армирует блоки. Таким образом, арболит не трескается под тяжестью иных материалов, а может только слегка деформироваться сохраняя общую систему конструкции.
2. Стойкость к низким температурам, что очень важно в процессе возведения дома и его эксплуатации. Дело в том, что если здание нагреется и замерзнет несколько раз, то это не повлияет на качество материала. Фактически дом из арболита может простоять минимум 50 лет в любые погодные условия. Конструкции из пеноблоков не имеют подобных свойств, ведь при постоянном замораживании они быстро потеряют свою функциональность.
3. Арболит не поддается воздействию углекислого газа, так что не стоит беспокоиться о карбонизации блоков, ведь их структура не позволит превратиться материалу в мел.
4. Теплопроводность блоков свидетельствует о популярности материала. Сравнивая показатели, стоит отметить, что стена из арболита в 30 см равняется 1 метру толщины кирпичной кладке. Структура материала позволяет сохранять тепло внутри помещения даже в самые холодные зимы, что весьма экономично при строительстве.
5. Звукоизоляционные свойства свидетельствуют о высоком коэффициенте поглощения арболита, который составляет от 0,7 до 0,6. Для сравнения древесина имеет показатели 0,06 -0,1, а кирпич немного больше около 0,04-0,06.
6. Легкость материала, что позволяет сэкономить средства на заливку фундамента.
7. Арболит является экологически чистым и долговечным строительным материалом, что определяет компонентный состав блоков. После возведения дома он не образует плесень и грибок на стенах.
8. Материал является безопасным, так он не воспламенятся.
9. Арболитные блоки легко применять в строительных работах, поскольку без труда в них можно забить гвозди, просверлить отверстие, использовать шурупы и так далее. Внешняя структура материала позволяет покрывать его штукатуркой без использования специальных сеток и дополнительных утеплителей.
Мы рассмотрели преимущества арболитных блоков, но для полного воссоздания картины о данном строительном материале приведем некоторые недостатки:
1. Стеновая панель может не выделяться точными геометрическими параметрами, от чего для восстановления ровности стены используют вагонку, сайдинг или гипсокартон, а сверху все отделяют штукатуркой.
2. Блоки не являются дешевым строительным материалом, ведь изготовление щепы для арболита требует некоторых затрат. Делая расчеты по сравнению из газобетоном, данный строительный материал обойдется только на 10-15 процентов дороже, что не формирует полное преимущество.
Технология производства арболита
Изготовление арболита требует следованию технологиям производства с расчетом состава и объема для одного блока. Арболитные блоки представляют собой строительный материал простой по компонентному составу, в который входят древесина, вода, опилки, цемент и другие предметы.
Главной основой для производства считается древесная щепа. Составная часть арболитового блока определяет его прочность и устойчивость к повреждениям, что высчитывается высшим уровнем, чем у пено- или газоблоков. Производство в домашних условиях осуществить не сложно, однако необходимо придерживаться распределения массы предмета и следовать инструкции.
Подготовка основания для работы
Основной составляющей для изготовления щепы для арболита является соотношение пропорций стружки и опилок – 1:2 или 1:1. Все предметы хорошо высушивают, для чего их помещают на 3 – 4 месяца на свежий воздух, время от времени обрабатывая известью и переворачивая.
Примерно на 1 кубический метр средства потребуется около 200 литров извести 15-ти процентной. В них помещают все щепы на четыре дня и перемешивают их от 2 до 4 раз на день. Все работы проводятся с целью убрать сахар с древесины, который может спровоцировать гниение блоков. Щепу приобретают в готовом виде, однако, с помощью щепорезов можно сделать самостоятельно.
Компоненты и состав арболита
Компонентный состав арболита является самым важным этапом технологии производства и требует внимательного соотношения всех материалов. При изготовлении блоков важно следить за качеством и разновидностью приобретаемых материалов, которые определяют готовый строительный материал. После процесса изготовления в щепу добавляют следующие материалы, такие как:
- известь гашеную;
- жидкое стекло растворимое;
- портландцемент;
- хлористый калий;
- алюминий и сернокислый кальций.
Производство арболита в пропорциях представлено в таблице 1. Стоит учесть, что для всех компонентов масса рассчитана на четыре процента доли цемента. Данная компоновка помогает сохранить огнеупорность предмета и придает пластичности.
Таблица 1. Состав арболита по объему
Марка арболита | Цемент (М400) | Кол-во извести | Кол-во песка | Кол-во опилок | Получаемая плотность (кг/м3) |
5 | 1 | 1,5 | — | 15 | 300-400 |
10 | 1 | 1 | 1,5 | 12 | 600-700 |
15 | 1 | 0,5 | 2,5 | 9 | 900-1000 |
25 | 1 | — | 3 | 6 | 1200-1300 |
Процесс и принципы изготовления
Оптимальные параметры блоков для технологии производства арболита составляют 25х25х50 сантиметров. Установленные размеры удобны при кладке стен домов, а также в процессе промышленности. Заливка блока состоит из трех рядов смеси и арболита, после каждого этапа необходимо уплотнять раствор молотком, отделанным жестью.
Излишняя масса свертывается при содействии шпателя. Выдерживается блок при температуре 18 градусов тепла на раскрытом воздухе. По истечении суток арболит выстукивается из формы на ровную поверхность, где он скрепляется на протяжении 10 дней.
Оборудование: применение на практике
Для производства необходимо разное снабжение, например, станки для изготовления арболита, которые выбираются в соответствии с объемом продукции и количества сырья. Технология промышленного процесса должна отвечать требованиям и критериям СН 549-82 и ГОСТу 19222-84. В качестве основного материала для выработки выступают хвойные деревья. Раздробление древесины происходит с помощью рубильных машин, таких как РРМ-5, ДУ-2, а более скрупулезное дробление осуществляется на оборудовании ДМ-1.
Арболитовую смесь подготавливают со смесителями и растворителями различного цикличного воздействия на материал. Подвозят большие объемы обработанной смеси к формам с помощью приспособления в качестве бетонораздатчиков или кюбелей. Подъем или опускание машины должно осуществляться при параметрах 15о по верхнему подъему и 10о по нижнему, а скорость оборудования рассчитывается в 1 м/с. Разлив арболитовой смеси по формам делают на высоте до 1 метра.
Уплотнения раствора производят с содействием вибропреса или ручной трамбовки. Для производства небольшого количества блоков нужно применить мини-станок. Изготовление своими руками арболита не представляет особых трудностей, однако на промышленных объектах применяется специальное оборудование по смешиванию, изготовления блоков. На некоторых заводах присутствуют тепловые камеры с ИК-излучением или ТЭНом, что позволяет определить нужную температуру для высыхания блоков.
Блочные формы для арболита
Существуют разные блочные формы для обработки арболита, а примерные величины могут составлять: 20х20х50 см или 30х20х50 см.
В зависимости от класса арболитовые блоки применяют в малоэтажном строительстве для возведения несущих стен, перегородок, а также для теплоизоляциии и звукоизоляции конструктивных элементов здания.
Процесс производства своими руками
Рассмотрев технологию изготовления состава арболита, можно приступать к выполнению работы самостоятельно. Для начала потребуются некоторые материалы и оборудование:
- специальный лоток для смеси;
- падающий и вибрирующий стол;
- стол с ударно-встряхивающим эффектом;
- разъемные формы и подставки;
- поддон из металла для форм.
Производить арболит своими руками очень сложно без использования необходимых инструментов, станков и оборудования. Как правило, на производстве потребуются некоторые приспособления:
1. Для получения качественного раствора необходимо применить бетономешалку. Разумеется, в процессе можно все сделать своими руками, однако придется, много времени потратить на получение раствора необходимой консистенции.
2. Для формирования структуры блоков важно приобрести формы соответствующих размеров. Как правило, арболит имеет прямоугольную форму, а в производстве используются пластиковые формы.
3. При помощи станка вы профессионально измельчите щепу.
4. Используя пресс можно получить хорошую плотность материала при трамбовке, при этом важно убрать воздух из консистенции. В качестве приспособлений применяется вибростол.
5. Обязательное наличие камеры для сушки арболита, что позволит его превратить в твердую однокомпонентную структуру.
6. В домашних условиях понадобится лопата для загрузки смеси в формы, а для скрепления блоков используют армирующую сетку.
При наличии выше перечисленных приспособлений можно производить в день около 350 – 450 м3 строительного раствора в месяц. Места для монтажа потребуется около 500 квадратных метров, а затрат на электроэнергию пойдет 15-45 кВт/ч. Для самостоятельного процесса органические средства заливаются водой, а также цементом до образования однородной смеси. Все пропорции и расчеты отображены в таблице 1, главное чтобы вышедшая смесь была сыпучей.
Перед заливкой раствора в формы, их обмазывают с внутренней стороны молочком известковым. После этого, средство скрупулезно и аккуратно укладывают и утрамбовывают специальными приспособлениями. Верхняя часть блока выравнивается с помощью шпателя или линейки и заливается раствором штукатурки на слой в 2 сантиметра.
После образованной формы арболита его потребуется тщательно уплотнить с помощью деревянной конструкции, оббитой железом. Прочными и надежными считаются блоки, которые выстоялись и схватились на протяжении десяти дней при температуре 15о. Чтобы арболит не пересох, рекомендуется периодически поливать его водой.
Технология изготовления арболита своими руками не представляет определенной сложности, а поэтому все работы провести легко при наличии необходимых инструментов и приспособлений. При соблюдении правил и критериев производства, правильного расчета компонентов строительный материал получится качественным и прочным для применения.
Советы экспертов при изготовлении блоков своими руками
Рекомендации специалистов по производству арболитных блоков основаны на практике их использования и применения. Чтобы достичь высокого качества продукции необходимо следовать некоторым факторам. В производстве рекомендуется применять не только большую щепу, но и использовать опилки, стружку из дерева. Обработка консистенции и выдавливание из него сахара позволяет избежать дальнейшего вспучивания строительного материала, что не приспускается при сооружении дома.
В процессе изготовления раствор следует тщательно перемешивать, чтобы все части оказались в цементе. Это важно для качественного и прочного скрепления древесины и иных материалов в блоке. В производстве не менее важным остается добавление следующих компонентов, таких как алюминий, гашеная известь и так далее. Весь состав образует дополнительные свойства арболита, например жидкое стекло не позволяет впитывать влагу блокам, а известь служит в качестве антисептика.
Хлористый калий способствует уничтожению микроорганизмов и других веществ, что не благотворно влияют на структуру. При добавлении всех компонентов стоит следить за таблицей пропорциональности, чтобы готовый раствор соответствовал требованиям производства арболитных блоков.
Изготовление арболита своими руками: технология производства и самостоятельные работы
Поэтапная технология изготовления арболита предвидит подготовку основания, определения компонентов и состава блочного материала. В данной статье рассмотрим особенности производства своими руками с применением необходимого оборудования, расчета массы и заливки.
Оглавление:
- Преимущества и недостатки арболита
- Технология производства арболита
- Подготовка основания для работы
- Компоненты и состав арболита
- Процесс и принципы изготовления
- Оборудование: применение на практике
- Блочные формы для арболита
- Процесс производства своими руками
- Советы экспертов при изготовлении блоков своими руками
Преимущества и недостатки арболита
Для многих строителей арболитные блоки являются ценным и качественным материалом для возведения домов. Главная особенность теплоизоляционных свойств позволяет из раствора производить напольные листы. Технология изготовления и принципы выдержки и сушки блоков предоставляют арболиту некоторые преимущества:
1. Прочность материала составляет 600-650 кг/м3, что по компонентной структуре не уступает иному строительному материалу. Главной особенностью является пластичность, что формируется в результате использования древесины, которая качественно армирует блоки. Таким образом, арболит не трескается под тяжестью иных материалов, а может только слегка деформироваться сохраняя общую систему конструкции.
2. Стойкость к низким температурам, что очень важно в процессе возведения дома и его эксплуатации. Дело в том, что если здание нагреется и замерзнет несколько раз, то это не повлияет на качество материала. Фактически дом из арболита может простоять минимум 50 лет в любые погодные условия. Конструкции из пеноблоков не имеют подобных свойств, ведь при постоянном замораживании они быстро потеряют свою функциональность.
3. Арболит не поддается воздействию углекислого газа, так что не стоит беспокоиться о карбонизации блоков, ведь их структура не позволит превратиться материалу в мел.
4. Теплопроводность блоков свидетельствует о популярности материала. Сравнивая показатели, стоит отметить, что стена из арболита в 30 см равняется 1 метру толщины кирпичной кладке. Структура материала позволяет сохранять тепло внутри помещения даже в самые холодные зимы, что весьма экономично при строительстве.
5. Звукоизоляционные свойства свидетельствуют о высоком коэффициенте поглощения арболита, который составляет от 0,7 до 0,6. Для сравнения древесина имеет показатели 0,06 -0,1, а кирпич немного больше около 0,04-0,06.
6. Легкость материала, что позволяет сэкономить средства на заливку фундамента.
7. Арболит является экологически чистым и долговечным строительным материалом, что определяет компонентный состав блоков. После возведения дома он не образует плесень и грибок на стенах.
8. Материал является безопасным, так он не воспламенятся.
9. Арболитные блоки легко применять в строительных работах, поскольку без труда в них можно забить гвозди, просверлить отверстие, использовать шурупы и так далее. Внешняя структура материала позволяет покрывать его штукатуркой без использования специальных сеток и дополнительных утеплителей.
Мы рассмотрели преимущества арболитных блоков, но для полного воссоздания картины о данном строительном материале приведем некоторые недостатки:
1. Стеновая панель может не выделяться точными геометрическими параметрами, от чего для восстановления ровности стены используют вагонку, сайдинг или гипсокартон, а сверху все отделяют штукатуркой.
2. Блоки не являются дешевым строительным материалом, ведь изготовление щепы для арболита требует некоторых затрат. Делая расчеты по сравнению из газобетоном, данный строительный материал обойдется только на 10-15 процентов дороже, что не формирует полное преимущество.
Технология производства арболита
Изготовление арболита требует следованию технологиям производства с расчетом состава и объема для одного блока. Арболитные блоки представляют собой строительный материал простой по компонентному составу, в который входят древесина, вода, опилки, цемент и другие предметы.
Главной основой для производства считается древесная щепа. Составная часть арболитового блока определяет его прочность и устойчивость к повреждениям, что высчитывается высшим уровнем, чем у пено- или газоблоков. Производство в домашних условиях осуществить не сложно, однако необходимо придерживаться распределения массы предмета и следовать инструкции.
Подготовка основания для работы
Основной составляющей для изготовления щепы для арболита является соотношение пропорций стружки и опилок – 1:2 или 1:1. Все предметы хорошо высушивают, для чего их помещают на 3 – 4 месяца на свежий воздух, время от времени обрабатывая известью и переворачивая.
Примерно на 1 кубический метр средства потребуется около 200 литров извести 15-ти процентной. В них помещают все щепы на четыре дня и перемешивают их от 2 до 4 раз на день. Все работы проводятся с целью убрать сахар с древесины, который может спровоцировать гниение блоков. Щепу приобретают в готовом виде, однако, с помощью щепорезов можно сделать самостоятельно.
Компоненты и состав арболита
Компонентный состав арболита является самым важным этапом технологии производства и требует внимательного соотношения всех материалов. При изготовлении блоков важно следить за качеством и разновидностью приобретаемых материалов, которые определяют готовый строительный материал. После процесса изготовления в щепу добавляют следующие материалы, такие как:
- известь гашеную;
- жидкое стекло растворимое;
- портландцемент;
- хлористый калий;
- алюминий и сернокислый кальций.
Производство арболита в пропорциях представлено в таблице 1. Стоит учесть, что для всех компонентов масса рассчитана на четыре процента доли цемента. Данная компоновка помогает сохранить огнеупорность предмета и придает пластичности.
Таблица 1. Состав арболита по объему
Марка арболита | Цемент (М400) | Кол-во извести | Кол-во песка | Кол-во опилок | Получаемая плотность (кг/м3) |
5 | 1 | 1,5 | — | 15 | 300-400 |
10 | 1 | 1 | 1,5 | 12 | 600-700 |
15 | 1 | 0,5 | 2,5 | 9 | 900-1000 |
25 | 1 | — | 3 | 6 | 1200-1300 |
Процесс и принципы изготовления
Оптимальные параметры блоков для технологии производства арболита составляют 25х25х50 сантиметров. Установленные размеры удобны при кладке стен домов, а также в процессе промышленности. Заливка блока состоит из трех рядов смеси и арболита, после каждого этапа необходимо уплотнять раствор молотком, отделанным жестью.
Излишняя масса свертывается при содействии шпателя. Выдерживается блок при температуре 18 градусов тепла на раскрытом воздухе. По истечении суток арболит выстукивается из формы на ровную поверхность, где он скрепляется на протяжении 10 дней.
Оборудование: применение на практике
Для производства необходимо разное снабжение, например, станки для изготовления арболита, которые выбираются в соответствии с объемом продукции и количества сырья. Технология промышленного процесса должна отвечать требованиям и критериям СН 549-82 и ГОСТу 19222-84. В качестве основного материала для выработки выступают хвойные деревья. Раздробление древесины происходит с помощью рубильных машин, таких как РРМ-5, ДУ-2, а более скрупулезное дробление осуществляется на оборудовании ДМ-1.
Арболитовую смесь подготавливают со смесителями и растворителями различного цикличного воздействия на материал. Подвозят большие объемы обработанной смеси к формам с помощью приспособления в качестве бетонораздатчиков или кюбелей. Подъем или опускание машины должно осуществляться при параметрах 15о по верхнему подъему и 10о по нижнему, а скорость оборудования рассчитывается в 1 м/с. Разлив арболитовой смеси по формам делают на высоте до 1 метра.
Уплотнения раствора производят с содействием вибропреса или ручной трамбовки. Для производства небольшого количества блоков нужно применить мини-станок. Изготовление своими руками арболита не представляет особых трудностей, однако на промышленных объектах применяется специальное оборудование по смешиванию, изготовления блоков. На некоторых заводах присутствуют тепловые камеры с ИК-излучением или ТЭНом, что позволяет определить нужную температуру для высыхания блоков.
Блочные формы для арболита
Существуют разные блочные формы для обработки арболита, а примерные величины могут составлять: 20х20х50 см или 30х20х50 см. Выпускаются предметы и прочих размеров, особенно для постройки вентиляционных систем, покрытий и так далее. Формы можно приобрести в строительных магазинах или же подготовить все своими руками. Для этого, используют доски толщиной в 2 сантиметра, которые скрепляют до образования определенной конструкции. Внешне форма отделывается фанерой, или пленкой.
В зависимости от класса арболитовые блоки применяют в малоэтажном строительстве для возведения несущих стен, перегородок, а также для теплоизоляциии и звукоизоляции конструктивных элементов здания.
Процесс производства своими руками
Рассмотрев технологию изготовления состава арболита, можно приступать к выполнению работы самостоятельно. Для начала потребуются некоторые материалы и оборудование:
- специальный лоток для смеси;
- падающий и вибрирующий стол;
- стол с ударно-встряхивающим эффектом;
- разъемные формы и подставки;
- поддон из металла для форм.
Производить арболит своими руками очень сложно без использования необходимых инструментов, станков и оборудования. Как правило, на производстве потребуются некоторые приспособления:
1. Для получения качественного раствора необходимо применить бетономешалку. Разумеется, в процессе можно все сделать своими руками, однако придется, много времени потратить на получение раствора необходимой консистенции.
2. Для формирования структуры блоков важно приобрести формы соответствующих размеров. Как правило, арболит имеет прямоугольную форму, а в производстве используются пластиковые формы.
3. При помощи станка вы профессионально измельчите щепу.
4. Используя пресс можно получить хорошую плотность материала при трамбовке, при этом важно убрать воздух из консистенции. В качестве приспособлений применяется вибростол.
5. Обязательное наличие камеры для сушки арболита, что позволит его превратить в твердую однокомпонентную структуру.
6. В домашних условиях понадобится лопата для загрузки смеси в формы, а для скрепления блоков используют армирующую сетку.
При наличии выше перечисленных приспособлений можно производить в день около 350 – 450 м3 строительного раствора в месяц. Места для монтажа потребуется около 500 квадратных метров, а затрат на электроэнергию пойдет 15-45 кВт/ч. Для самостоятельного процесса органические средства заливаются водой, а также цементом до образования однородной смеси. Все пропорции и расчеты отображены в таблице 1, главное чтобы вышедшая смесь была сыпучей.
Перед заливкой раствора в формы, их обмазывают с внутренней стороны молочком известковым. После этого, средство скрупулезно и аккуратно укладывают и утрамбовывают специальными приспособлениями. Верхняя часть блока выравнивается с помощью шпателя или линейки и заливается раствором штукатурки на слой в 2 сантиметра.
После образованной формы арболита его потребуется тщательно уплотнить с помощью деревянной конструкции, оббитой железом. Прочными и надежными считаются блоки, которые выстоялись и схватились на протяжении десяти дней при температуре 15о. Чтобы арболит не пересох, рекомендуется периодически поливать его водой.
Технология изготовления арболита своими руками не представляет определенной сложности, а поэтому все работы провести легко при наличии необходимых инструментов и приспособлений. При соблюдении правил и критериев производства, правильного расчета компонентов строительный материал получится качественным и прочным для применения.
Советы экспертов при изготовлении блоков своими руками
Рекомендации специалистов по производству арболитных блоков основаны на практике их использования и применения. Чтобы достичь высокого качества продукции необходимо следовать некоторым факторам. В производстве рекомендуется применять не только большую щепу, но и использовать опилки, стружку из дерева. Обработка консистенции и выдавливание из него сахара позволяет избежать дальнейшего вспучивания строительного материала, что не приспускается при сооружении дома.
В процессе изготовления раствор следует тщательно перемешивать, чтобы все части оказались в цементе. Это важно для качественного и прочного скрепления древесины и иных материалов в блоке. В производстве не менее важным остается добавление следующих компонентов, таких как алюминий, гашеная известь и так далее. Весь состав образует дополнительные свойства арболита, например жидкое стекло не позволяет впитывать влагу блокам, а известь служит в качестве антисептика.
Хлористый калий способствует уничтожению микроорганизмов и других веществ, что не благотворно влияют на структуру. При добавлении всех компонентов стоит следить за таблицей пропорциональности, чтобы готовый раствор соответствовал требованиям производства арболитных блоков.
Изготовление арболита своими руками: технология производства и самостоятельные работы
Поэтапная технология изготовления арболита предвидит подготовку основания, определения компонентов и состава блочного материала. В данной статье рассмотрим особенности производства своими руками с применением необходимого оборудования, расчета массы и заливки.
Оглавление:
- Преимущества и недостатки арболита
- Технология производства арболита
- Подготовка основания для работы
- Компоненты и состав арболита
- Процесс и принципы изготовления
- Оборудование: применение на практике
- Блочные формы для арболита
- Процесс производства своими руками
- Советы экспертов при изготовлении блоков своими руками
Преимущества и недостатки арболита
Для многих строителей арболитные блоки являются ценным и качественным материалом для возведения домов. Главная особенность теплоизоляционных свойств позволяет из раствора производить напольные листы. Технология изготовления и принципы выдержки и сушки блоков предоставляют арболиту некоторые преимущества:
1. Прочность материала составляет 600-650 кг/м3, что по компонентной структуре не уступает иному строительному материалу. Главной особенностью является пластичность, что формируется в результате использования древесины, которая качественно армирует блоки. Таким образом, арболит не трескается под тяжестью иных материалов, а может только слегка деформироваться сохраняя общую систему конструкции.
2. Стойкость к низким температурам, что очень важно в процессе возведения дома и его эксплуатации. Дело в том, что если здание нагреется и замерзнет несколько раз, то это не повлияет на качество материала. Фактически дом из арболита может простоять минимум 50 лет в любые погодные условия. Конструкции из пеноблоков не имеют подобных свойств, ведь при постоянном замораживании они быстро потеряют свою функциональность.
3. Арболит не поддается воздействию углекислого газа, так что не стоит беспокоиться о карбонизации блоков, ведь их структура не позволит превратиться материалу в мел.
4. Теплопроводность блоков свидетельствует о популярности материала. Сравнивая показатели, стоит отметить, что стена из арболита в 30 см равняется 1 метру толщины кирпичной кладке. Структура материала позволяет сохранять тепло внутри помещения даже в самые холодные зимы, что весьма экономично при строительстве.
5. Звукоизоляционные свойства свидетельствуют о высоком коэффициенте поглощения арболита, который составляет от 0,7 до 0,6. Для сравнения древесина имеет показатели 0,06 -0,1, а кирпич немного больше около 0,04-0,06.
6. Легкость материала, что позволяет сэкономить средства на заливку фундамента.
7. Арболит является экологически чистым и долговечным строительным материалом, что определяет компонентный состав блоков. После возведения дома он не образует плесень и грибок на стенах.
8. Материал является безопасным, так он не воспламенятся.
9. Арболитные блоки легко применять в строительных работах, поскольку без труда в них можно забить гвозди, просверлить отверстие, использовать шурупы и так далее. Внешняя структура материала позволяет покрывать его штукатуркой без использования специальных сеток и дополнительных утеплителей.
Мы рассмотрели преимущества арболитных блоков, но для полного воссоздания картины о данном строительном материале приведем некоторые недостатки:
1. Стеновая панель может не выделяться точными геометрическими параметрами, от чего для восстановления ровности стены используют вагонку, сайдинг или гипсокартон, а сверху все отделяют штукатуркой.
2. Блоки не являются дешевым строительным материалом, ведь изготовление щепы для арболита требует некоторых затрат. Делая расчеты по сравнению из газобетоном, данный строительный материал обойдется только на 10-15 процентов дороже, что не формирует полное преимущество.
Технология производства арболита
Изготовление арболита требует следованию технологиям производства с расчетом состава и объема для одного блока. Арболитные блоки представляют собой строительный материал простой по компонентному составу, в который входят древесина, вода, опилки, цемент и другие предметы.
Главной основой для производства считается древесная щепа. Составная часть арболитового блока определяет его прочность и устойчивость к повреждениям, что высчитывается высшим уровнем, чем у пено- или газоблоков. Производство в домашних условиях осуществить не сложно, однако необходимо придерживаться распределения массы предмета и следовать инструкции.
Подготовка основания для работы
Основной составляющей для изготовления щепы для арболита является соотношение пропорций стружки и опилок – 1:2 или 1:1. Все предметы хорошо высушивают, для чего их помещают на 3 – 4 месяца на свежий воздух, время от времени обрабатывая известью и переворачивая.
Примерно на 1 кубический метр средства потребуется около 200 литров извести 15-ти процентной. В них помещают все щепы на четыре дня и перемешивают их от 2 до 4 раз на день. Все работы проводятся с целью убрать сахар с древесины, который может спровоцировать гниение блоков. Щепу приобретают в готовом виде, однако, с помощью щепорезов можно сделать самостоятельно.
Компоненты и состав арболита
Компонентный состав арболита является самым важным этапом технологии производства и требует внимательного соотношения всех материалов. При изготовлении блоков важно следить за качеством и разновидностью приобретаемых материалов, которые определяют готовый строительный материал. После процесса изготовления в щепу добавляют следующие материалы, такие как:
- известь гашеную;
- жидкое стекло растворимое;
- портландцемент;
- хлористый калий;
- алюминий и сернокислый кальций.
Производство арболита в пропорциях представлено в таблице 1. Стоит учесть, что для всех компонентов масса рассчитана на четыре процента доли цемента. Данная компоновка помогает сохранить огнеупорность предмета и придает пластичности.
Таблица 1. Состав арболита по объему
Марка арболита | Цемент (М400) | Кол-во извести | Кол-во песка | Кол-во опилок | Получаемая плотность (кг/м3) |
5 | 1 | 1,5 | — | 15 | 300-400 |
10 | 1 | 1 | 1,5 | 12 | 600-700 |
15 | 1 | 0,5 | 2,5 | 9 | 900-1000 |
25 | 1 | — | 3 | 6 | 1200-1300 |
Процесс и принципы изготовления
Оптимальные параметры блоков для технологии производства арболита составляют 25х25х50 сантиметров. Установленные размеры удобны при кладке стен домов, а также в процессе промышленности. Заливка блока состоит из трех рядов смеси и арболита, после каждого этапа необходимо уплотнять раствор молотком, отделанным жестью.
Излишняя масса свертывается при содействии шпателя. Выдерживается блок при температуре 18 градусов тепла на раскрытом воздухе. По истечении суток арболит выстукивается из формы на ровную поверхность, где он скрепляется на протяжении 10 дней.
Оборудование: применение на практике
Для производства необходимо разное снабжение, например, станки для изготовления арболита, которые выбираются в соответствии с объемом продукции и количества сырья. Технология промышленного процесса должна отвечать требованиям и критериям СН 549-82 и ГОСТу 19222-84. В качестве основного материала для выработки выступают хвойные деревья. Раздробление древесины происходит с помощью рубильных машин, таких как РРМ-5, ДУ-2, а более скрупулезное дробление осуществляется на оборудовании ДМ-1.
Арболитовую смесь подготавливают со смесителями и растворителями различного цикличного воздействия на материал. Подвозят большие объемы обработанной смеси к формам с помощью приспособления в качестве бетонораздатчиков или кюбелей. Подъем или опускание машины должно осуществляться при параметрах 15о по верхнему подъему и 10о по нижнему, а скорость оборудования рассчитывается в 1 м/с. Разлив арболитовой смеси по формам делают на высоте до 1 метра.
Уплотнения раствора производят с содействием вибропреса или ручной трамбовки. Для производства небольшого количества блоков нужно применить мини-станок. Изготовление своими руками арболита не представляет особых трудностей, однако на промышленных объектах применяется специальное оборудование по смешиванию, изготовления блоков. На некоторых заводах присутствуют тепловые камеры с ИК-излучением или ТЭНом, что позволяет определить нужную температуру для высыхания блоков.
Блочные формы для арболита
Существуют разные блочные формы для обработки арболита, а примерные величины могут составлять: 20х20х50 см или 30х20х50 см. Выпускаются предметы и прочих размеров, особенно для постройки вентиляционных систем, покрытий и так далее. Формы можно приобрести в строительных магазинах или же подготовить все своими руками. Для этого, используют доски толщиной в 2 сантиметра, которые скрепляют до образования определенной конструкции. Внешне форма отделывается фанерой, или пленкой.
В зависимости от класса арболитовые блоки применяют в малоэтажном строительстве для возведения несущих стен, перегородок, а также для теплоизоляциии и звукоизоляции конструктивных элементов здания.
Процесс производства своими руками
Рассмотрев технологию изготовления состава арболита, можно приступать к выполнению работы самостоятельно. Для начала потребуются некоторые материалы и оборудование:
- специальный лоток для смеси;
- падающий и вибрирующий стол;
- стол с ударно-встряхивающим эффектом;
- разъемные формы и подставки;
- поддон из металла для форм.
Производить арболит своими руками очень сложно без использования необходимых инструментов, станков и оборудования. Как правило, на производстве потребуются некоторые приспособления:
1. Для получения качественного раствора необходимо применить бетономешалку. Разумеется, в процессе можно все сделать своими руками, однако придется, много времени потратить на получение раствора необходимой консистенции.
2. Для формирования структуры блоков важно приобрести формы соответствующих размеров. Как правило, арболит имеет прямоугольную форму, а в производстве используются пластиковые формы.
3. При помощи станка вы профессионально измельчите щепу.
4. Используя пресс можно получить хорошую плотность материала при трамбовке, при этом важно убрать воздух из консистенции. В качестве приспособлений применяется вибростол.
5. Обязательное наличие камеры для сушки арболита, что позволит его превратить в твердую однокомпонентную структуру.
6. В домашних условиях понадобится лопата для загрузки смеси в формы, а для скрепления блоков используют армирующую сетку.
При наличии выше перечисленных приспособлений можно производить в день около 350 – 450 м3 строительного раствора в месяц. Места для монтажа потребуется около 500 квадратных метров, а затрат на электроэнергию пойдет 15-45 кВт/ч. Для самостоятельного процесса органические средства заливаются водой, а также цементом до образования однородной смеси. Все пропорции и расчеты отображены в таблице 1, главное чтобы вышедшая смесь была сыпучей.
Перед заливкой раствора в формы, их обмазывают с внутренней стороны молочком известковым. После этого, средство скрупулезно и аккуратно укладывают и утрамбовывают специальными приспособлениями. Верхняя часть блока выравнивается с помощью шпателя или линейки и заливается раствором штукатурки на слой в 2 сантиметра.
После образованной формы арболита его потребуется тщательно уплотнить с помощью деревянной конструкции, оббитой железом. Прочными и надежными считаются блоки, которые выстоялись и схватились на протяжении десяти дней при температуре 15о. Чтобы арболит не пересох, рекомендуется периодически поливать его водой.
Технология изготовления арболита своими руками не представляет определенной сложности, а поэтому все работы провести легко при наличии необходимых инструментов и приспособлений. При соблюдении правил и критериев производства, правильного расчета компонентов строительный материал получится качественным и прочным для применения.
Советы экспертов при изготовлении блоков своими руками
Рекомендации специалистов по производству арболитных блоков основаны на практике их использования и применения. Чтобы достичь высокого качества продукции необходимо следовать некоторым факторам. В производстве рекомендуется применять не только большую щепу, но и использовать опилки, стружку из дерева. Обработка консистенции и выдавливание из него сахара позволяет избежать дальнейшего вспучивания строительного материала, что не приспускается при сооружении дома.
В процессе изготовления раствор следует тщательно перемешивать, чтобы все части оказались в цементе. Это важно для качественного и прочного скрепления древесины и иных материалов в блоке. В производстве не менее важным остается добавление следующих компонентов, таких как алюминий, гашеная известь и так далее. Весь состав образует дополнительные свойства арболита, например жидкое стекло не позволяет впитывать влагу блокам, а известь служит в качестве антисептика.
Хлористый калий способствует уничтожению микроорганизмов и других веществ, что не благотворно влияют на структуру. При добавлении всех компонентов стоит следить за таблицей пропорциональности, чтобы готовый раствор соответствовал требованиям производства арболитных блоков.
Завод, производитель арболита в Новосибирске
Производство арболита в Новосибирске — «Сибирский Арболит».
Арболит завод в Новосибирске на протяжении многих лет специализируется на производстве и продаже арболитовых блоков высшего качества, а также разработке технологий для реализации проектов строительства домов из арболита.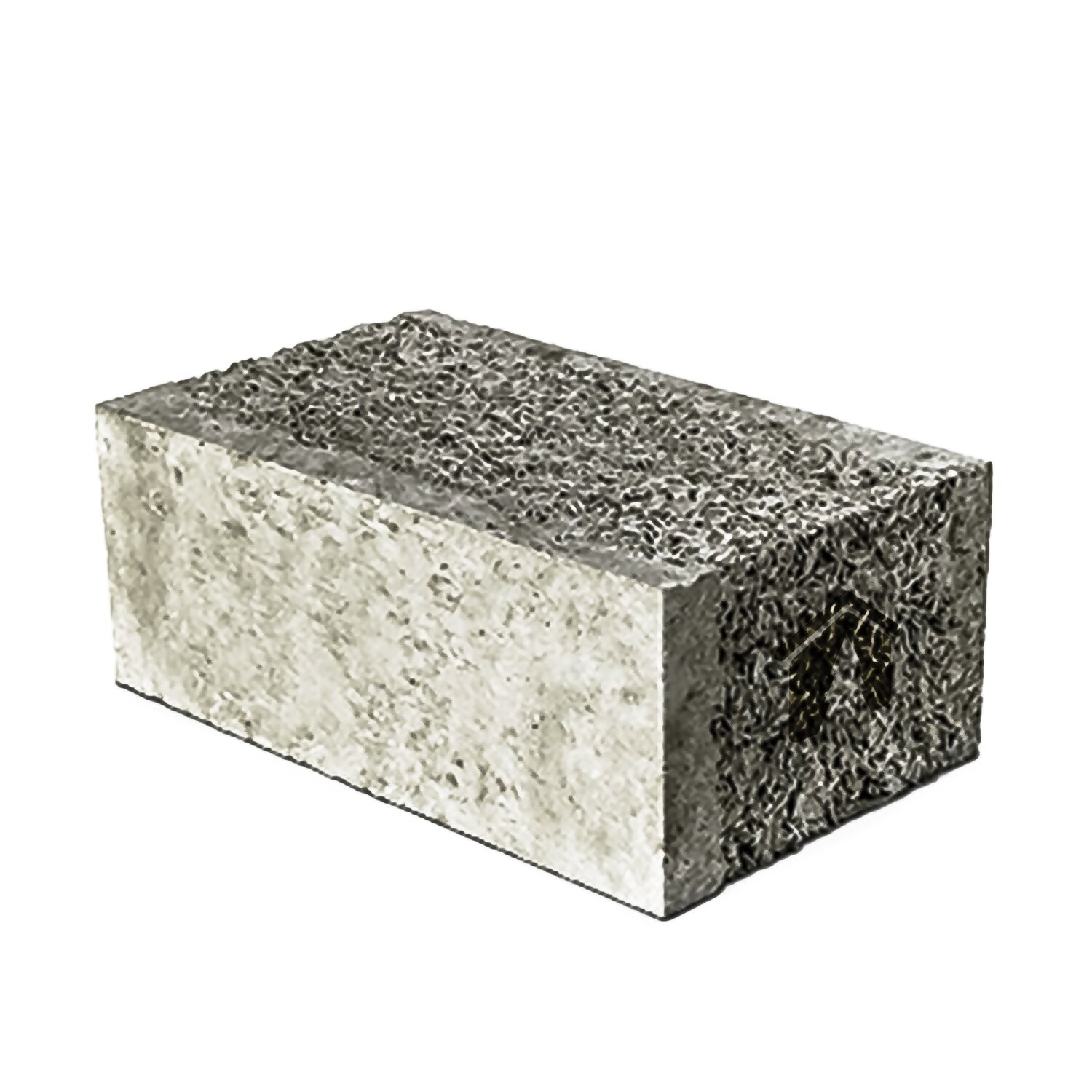
Современное производство арболита в Новосибирске.
Производители арболита для создания строительной продукции в блоках используют натуральный материал из хвойных пород древесины, цемент высшей категории и химические добавки, придающие готовому материалу уникальные функциональные свойства. Производство арболита в Новосибирске рассчитано на различные категории клиентов: частные и физические лица, строительные компании и организации по продаже стройматериалов.Изготовление арболита по всем стандартам позволяет создать стройматериалы для возведения несущих стен, любых перегородок, а также с целью максимальной звукоизоляции и теплоизоляции. Арболит имеет максимальный класс огнестойкости и устойчивости к влиянию биологических факторов: размножению грибков, микроорганизмов и плесени. Благодаря таким качествам арболитовые блоки соответствуют стандартам экологичного строительства.
Где заказать арболитовые блоки?
Прежде чем оформить крупный заказ на поставки строительных блоков из арболита, стоит подробнее узнать, сколько стоит арболитовый блок в Новосибирске. Ознакомиться с ценами можно на страницах сайта, где представлены все виды блоков в различных размерах и конфигурациях. Арболитовые блоки отзывы владельцев получают исключительно положительные не только благодаря высокому качеству стройматериалов, но и по причине отличного сервиса компании:- Наличие собственного мощного производства основных компонентов, а также арболитовых блоков;
- Идеальная геометрия блоков всех размеров;
- Закупки цемента у престижных производителей;
- Строгий контроль всей продукции на соответствие государственным стандартам, наличие сертификатов качества;
- Гарантийные обязательства на все виды продукции.
Производство арболитовых блоков в Новосибирске предлагает не только жителям Новосибирска, но и обитателям всей страны заказать блоки из арболита по выгодной цене.

Читать далее
Производство арболита » SpecAvto — Спецавто — Бетононасосы
Собственно говоря, арбалит, это нечто иное как работа древесной промышленности. Все — что не дает нам дерево — В том числе щепки, опилки, стружки – все это идет в строительство. Именно из этого, часто изготовляют самые хорошие материалы, из которых в последующие несколько десятилетий дом спокойно стоит. Это и утеплители и блоки, и чего еще там нет, разве что дома из продуктов древесной промышленности не строят .
В общем, из арболита делают блоки, которые потом можно использовать в строительстве в различных целях .К тому они имеют несколько отличительных свойств, которые гарантируют ему непременный выход на рынок, причем без боязни того, что он не найдет свое место под солнцем между многочисленными конкурентами. Во – первых – это очень легкий материал, он очень легкий, даже легче чем другие блоки, выполнены с помощью химического синтеза, и с применением цемента и прочих неполезных материалов. Во вторых та как он делается из щепок –то он экологически чист, что сейчас очень важно, та как большинство, следуя за европейскими тенденциями, хотят только экологически чистые дома, в экологически чистом районе или месте.
Теперь немного о производстве арболита.
Этот материал стал довольно распространенным в наши дни, именно поэтому существует несколько способов изготовление блоков, однако все они имеют незначительное отличие. И лучше всего написать общие стороны, которые есть в производстве арболита, потому что разные технологии могут предусматривать и наличие специальной техники, которая в принципе не очень – то и нужна, особенно при изготовлении арболита . Итак, сначала нужны щепки, причем хорошего, даже высшего качества и порой,то, что осталось после отходов производства совсем не подходит по качеству. Потом из щепок удаляют весь сахар, а также и возможность насекомых заинтересоваться таким набором мягких опилок. Потом все щепки обрабатываются специальным раствором. Позже их всех закладывают в формы .Они лежат немного в формах, чтобы распределиться и заполнить все пространство, потом начнется процесс прессования. Он обычно длиться недолго, и, в конце концов, мы получаем арболит.
Сделаем вывод о том, как производится арболит. Технология изготовления арболита очень проста и довольно экологична. Все дело в том, что же может повлиять на качество деревьев, из которых делают щепки. Если возможно, что лес заражен лесной болезнью, то такие щепки и для костра не годятся, нужны первоклассные деревья. Потом следует изготовить специальные формы, которые и будут заполнены этими опилками. Потом, после того, как по ним пройдется пресс, они должны полежать.
Производство арболита
Производство нашей продукции основано на проверенных технологиях и современной производственной базе, мы выпускаем только качественные арболитовые блоки.
Производство арболитовых блоков предполагает использование вибропресса, с его помощью смесь плотно утрамбовывается, равномерно распределяется по форме. В результате блок имеет идеально ровные поверхности, препятствующие образованию мостиков холода.
Наш производственный участок с установкой «Сфера-1»Высокая степень механизации производства позволяет нам снизить издержки и предложить клиенту низкую цену на арболит высокого качества.
Дробилка опилок Доктор АрболитДля получения качественных арболитовых блоков при производстве должны соблюдаться определенные условия. Так, например, важное значение имеет величина древесной щепы, мы используем щепу оптимальных размеров – длина от 10 до 40 мм, ширина от 5 до 10 мм, толщина не больше 5 мм.
При производстве арболита используется щепа из хвойной древесины. Сначала она измельчается на нашем оборудовании до необходимой фракции, затем обрабатывается сульфатом алюминия, это позволяет нейтрализовать сахара, содержащиеся в древесине и позволяет получить материал, который не боится разрушительного воздействия микроорганизмов
Для арболитовых блоков при производстве необходим цемент, мы используем высококлассный портландцемент. Данный вид цемента применяется также в промышленном строительстве при возведении ответственных конструкций, к которым предъявляются жесткие требования по таким качествам, как водостойкость, долговечность, морозоустойчивость.
Устойчивость арболита к внешнему воздействию зависит от того, насколько правильно было соблюдено время выдержки после изготовления блока. Изделие необходимо выдержать в форме сутки, за это время происходит застывание структуры, увеличивается плотность изделия, и соответственно его теплоизоляционные характеристики.
Вид на производственный участок с формами для выдержки блоков и партией свежей продукцииПолучить арболитовые блоки идеальной геометрической формы нам позволяет использование специальных форм из металла. Для того чтобы исключить прилипание смеси к стенкам формы, мы обрабатываем их минеральным маслом, не содержащим вредных примесей.
Арболитовые блоки от нашей компании отличаются идеальной геометрией и оптимальной плотностью – 650-700 кг на 1 м3. Добиться подобных результатов помогает тщательно выверенная технология изготовления.
Всё производство и хранение находится в отапливаемом помещении. Благодаря равномерной сушке наши арболитовые блоки имеют равномерную структуру и соответствуют требованиям стандартов.
Готовая продукция арболита на пандусе для погрузкиКаждая партия арболита изделий имеет сертификаты соответствия, протоколы испытаний, заключение санитарно-эпидемиологической службы.
Tecolit — О материале — Арболитовые блоки
Арболит (деревобетон) — это легкий бетон, получаемый на основе органического заполнителя (до 90% всего состава), минерального вяжущего (высокосортный цемент), воды и минеральных добавок. В качестве органического заполнителя наиболее широкое применение находит древесина, а именно, отходы лесопиления и деревообработки: технологические дрова, неделовой горбыль, рейки, срезки, станочная стружка. Также используются отходы переработки сельскохозяйственных культур: костра льна, стебли конопли, хлопчатника, сечка камыша и др.
Арболит – это экологически чистый строительный материал, в котором сочетаются лучшие качества камня и дерева. За рубежом данный строительный материал известен, как: «дюрисол» в Швеции, «вундстроун» в США, «пилинобетон» в Чехии, «чентерибоад» в Японии, «дюрипанель» в Германии, «велокс» в Австралии.
В западных странах арболит нашел активное применение, как в качестве строительного, так и теплоизоляционного материала. Например, в Швейцарии и Германии для термоизоляции жилых домов используют плиты из арболита: стоимость стен из арболита приблизительно в два раза ниже, чем из кирпича и панелей, утепленных минераловатой.
В России широкое распространение арболит получил в 60-х годах 20 века. К 1980-му году на территории бывшего СССР насчитывалось несколько десятков заводов по производству арболитовых плит. Арболит использовали при строительстве домов и объектов промышленного назначения на всей территории центральной части России, Сибири и даже в Антарктиде. В 1990-е годы материал нашел активное применение в индивидуальном и малоэтажном строительстве. Массового применения в России арболит не получил только в связи с ориентацией стройиндустрии на сборное панельное строительство. На сегодняшний день интерес к строительному материалу возродился, в частности за счет его уникальных свойств и характеристик, а также экономичности и экологичности.
На практике арболит зарекомендовал себя как отличный стеновой материал. Благодаря своей структуре он обладает хорошей звуко- и теплоизоляцией, например, теплозащитные качества арболита в 2-3 раза превосходят керамзитобетон и в 4-5 раз кирпич, обеспечивает нормальный микроклимат в помещениях, не конденсирует влаги на поверхности ограждающих конструкций.
Арболит имеет относительно небольшую объемную массу (конструкционный 600—700, теплоизоляционный 400— 500 кг/м3), обладает рядом характеристик, заметно выделяющих его на фоне других строительных материалов: хорошо пилится, сверлится, гвоздится, обрабатывается режущим инструментом; трудносгораем, водостоек, биостоек и морозостоек; применим в любых климатических районах (например, строительство в Антарктиде при температуре минус 50—600С).

Технология строительства из арболита: качественно, быстро, экономно
Технология возведения зданий из арболита представляет собой технологию строительства с применением систем несъемной опалубки. Установка блоков происходит «сухим» способом, без применения выравнивающего раствора с последующим армированием и замоноличиванием пустот бетоном.
В отличие от технологии монолитного строительства со съемной опалубкой блоки из арболита не демонтируются после достижения бетоном необходимой прочности, а становятся частью стены. За счет этого достигаются повышенные эксплуатационные свойства конструкции. Внешние и внутренние отделочные работы проводятся с применением любых материалов.
За счет высокой скорости монтажа конструкций из арболита сроки возведения здания сокращаются в два раза. Теплоизоляционные свойства материала позволяют проводить работы по бетонированию при минусовых температурах, что позволяет применять технологию в различных климатических условиях.
Экологичное здание: Самый популярный новый материал — это дерево
Архитекторы, строители и защитники устойчивого развития все недовольны новым строительным материалом, который, по их словам, может существенно сократить выбросы парниковых газов (ПГ) в строительном секторе, сократить отходы, загрязнение и затраты, связанные со строительством, и создать более физически, психологически и эстетически здоровая искусственная среда.
Этот материал известен как дерево.
Деревья использовались для строительства сооружений с доисторических времен, но особенно после бедствий, таких как Великий чикагский пожар 1871 года, древесина стала рассматриваться как небезопасная и нестабильная по сравнению с двумя материалами, которые с тех пор стали основными продуктами строительной индустрии во всем мире: бетон и сталь.
Однако новый способ использования дерева снова привлек внимание к этому материалу. Шумиха сосредоточена на конструкционной древесине или, как ее чаще называют, «массивной древесине» (сокращенно от «массивной древесины»). Короче говоря, он заключается в склеивании кусков мягкой древесины — обычно хвойных, таких как сосна, ель или пихта, но также иногда и лиственных пород, таких как береза, ясень и бук, — вместе для образования более крупных кусков.
Да, самая популярная вещь в архитектуре этого века — это «дерево, но как лего.”
Массивная древесина — это общий термин, который охватывает изделия различных размеров и функций, такие как клееный брус (клееный брус), клееный брус (LVL), клееный брус с гвоздями (NLT) и брус, клееный дюбелями (DLT). Но наиболее распространенная и наиболее известная форма массивной древесины, открывшая самые новые архитектурные возможности, — это кросс-клееная древесина (CLT).
Arch DailyДля создания CLT обрезанные и высушенные в печи пиломатериалы наклеиваются друг на друга слоями, крест-накрест, при этом волокна каждого слоя обращены к волокнам соседнего слоя.Укладывая доски вместе таким образом, можно получить большие плиты, толщиной до фута и размером от 18 футов в длину на 98 футов в ширину, хотя в среднем это примерно 10 на 40. (На данный момент размер равен плиты ограничены в меньшей степени производственными ограничениями, чем ограничениями транспортировки.)
Деревянные плиты такого размера могут соответствовать характеристикам бетона и стали или превосходить их. Из CLT можно делать полы, стены, потолки — целые здания. Самое высокое массивное деревянное сооружение в мире, высотой 18 этажей и более 280 футов, было недавно построено в Норвегии; для Чикаго предлагается 80-этажная деревянная башня.
Я разговаривал со множеством людей, которые чрезвычайно воодушевлены массовым лесом, как из-за его архитектурных качеств, так и из-за его потенциала для обезуглероживания строительного сектора, и некоторые из них высказали важные предостережения. Мы сразу же рассмотрим все преимущества и недостатки. Но сначала давайте кратко рассмотрим историю массового производства древесины и ее нынешнее положение.
Haut, самое высокое деревянное жилое здание в Нидерландах. ArupМассовая древесина (наконец) поступает в Америку
CLT была впервые разработана в начале 1990-х годов в Австрии, где лесоводство хвойных пород является чрезвычайно распространенным явлением. Ее поддержал исследователь Герхард Шикхофер, который все еще активен и в прошлом году получил престижную награду в области лесоводства за свою работу по стандартизации и обеспечению общественной поддержки нового материала.
В Австрии и в Европе в целом, где он распространился в 2000-х годах, CLT был разработан для использования в жилищном строительстве.Европейцам не нравится хрупкая конструкция деревянного каркаса, используемая для строительства многих домов в США; они предпочитают более прочные материалы, такие как бетон или кирпич. CLT был призван сделать жилищное строительство более устойчивым.
Но в США CLT (пока) не может конкурировать с конструкцией со стержневой рамой, которая является дешевой и широко распространенной. Только когда у североамериканских архитекторов появилась идея использовать CLT в больших зданиях в качестве замены бетона и стали, он начал появляться в Северной Америке в 2010-х годах.
В 2015 году CLT был включен в Международный строительный кодекс (IBC), который в юрисдикциях США принят по умолчанию. Принят ряд новых изменений, которые позволят создавать массовые деревянные конструкции высотой до 18 этажей, и ожидается, что они будут формализованы в новейшем кодексе IBC в 2021 году.
Некоторые юрисдикции в США агрессивно поддерживают массовую заготовку древесины, в том числе Вашингтон и Орегон (которые заблаговременно приняли новые изменения в IBC; Орегон включил CLT в качестве «альтернативного метода для всего штата» в 2018 году).
Кондоминиумы Carbon 12 в Портленде, штат Орегон. Хотеть. Углерод 12Тихоокеанский Северо-Запад по понятным причинам взволнован возможным переходом на деревянные строительные материалы, так как здесь есть густые леса и простаивающие лесопилки.
«Заготовка древесины на [северо-западном тихоокеанском регионе] значительно снизилась в результате слабого внутреннего спроса во время жилищного кризиса, который имел разрушительные последствия для лесной промышленности», — говорится в недавнем исследовании выбросов в течение жизненного цикла CLT.«В штате Вашингтон объем производства пиломатериалов снизился на 17% в период с 2014 по 2016 год, и по сравнению с 10 годами назад лесопилки (крупнейший сектор по потреблению древесины) производили на треть меньше досок».
В масштабах страны леса настолько переполнены, что Департамент лесного хозяйства выделяет 9 миллионов долларов в виде грантов на новые идеи по использованию древесины. Многие местные сообщества приветствовали бы новый спрос.
В то время как CLT продолжает бурно развиваться в Европе и ускоряется в Канаде, в США ему по-прежнему мешают анахроничные и чрезмерно предписывающие строительные нормы, ограниченное внутреннее предложение и консервативное мышление строительной отрасли.
Что касается поставок, Vaagen Brothers, известная вашингтонская лесопилка, уже выделила вторую компанию, специализирующуюся на CLT; ожидается, что другие заводы последуют этому примеру. Компания под названием Katerra недавно открыла крупнейший в Северной Америке завод по производству CLT в Спокане, штат Вашингтон, и законодатели штата готовы отметить это событие. Это может помочь в массовом производстве древесины в регионе.
На данный момент существует ряд ярких разовых проектов CLT в США: инновационный центр Catalyst в Спокане, офисное здание T3 в Миннеаполисе, кондоминиумы Carbon 12 в Портленде, штат Орегон, начальная школа Франклина в Западной Вирджинии и более.Но поскольку они разовые, они требуют много дополнительной работы по тестированию, проектированию и получению разрешений. И не хватает как подходящих материалов, так и знакомых с ними подрядчиков и строителей. «Это еще не развитая отрасль», — говорит архитектор Майкл Грин, чье основополагающее выступление на TED Talk 2013 года о массовом производстве древесины помогло поднять интерес в США. (Примечание: Катерра недавно приобрела Michael Green Architecture.)
Тем не менее, растущий энтузиазм строителей и защитников, похоже, ослабляет сопротивление.Почему они так настроены?
Преимущества массового бруса
1. Хорошо работает в условиях пожара
Особенно в США люди ассоциируют дерево в зданиях с конструкцией стержневого каркаса, 2X4 и фанеру, которые являются легковоспламеняющимися AF. Ничего не помогает и то, что в последнее время в средствах массовой информации пестрят изображениями горящих домов и жилых кварталов в Калифорнии. О массовых лесах это первый вопрос: а как насчет огня?
Дело в том, что большие, твердые, сжатые куски дерева на самом деле довольно трудно поджечь.(Поднесите спичку к большому бревну какое-то время.) В случае пожара внешний слой массивной древесины будет иметь тенденцию обугливаться предсказуемым образом, что эффективно самозатухает и защищает внутреннюю часть, позволяя ей сохранять структурную целостность в течение долгого времени. несколько часов даже при сильном огне.
Отчеты об испытаниях CLT на огнестойкость поступают от Лесной службы США, Совета по международным кодексам и Фонда исследований противопожарной защиты. (Лесная служба также провела обширные взрывные испытания CLT, которые она успешно прошла, открыв дверь для его использования на военных объектах.Суть в том, что все строительные материалы должны соответствовать нормам, а CLT — нормам пожарной безопасности.
Интересное замечание: большинство людей не осознают, что «сталь ужасна в огне», — говорит Грин. «Как только он достигает умеренной температуры, это становится очень непредсказуемым, и дело сделано. Ваше здание должно быть снесено ». Когда Грин действительно использует сталь, он часто окружает ее CLT, чтобы защитить ее в случае пожара.
2. Снижает выбросы углерода
Примерно 11 процентов мировых выбросов парниковых газов приходится на строительные материалы и строительство; еще 28 процентов приходится на строительные работы, которые в основном связаны с использованием энергии.По мере того как в ближайшие годы энергия станет чище, материалы и конструкции будут представлять все большую долю углеродного воздействия на здания. Именно на это и направлена масса древесины.
Определение воздействия массивной древесины на выбросы углерода в течение всего жизненного цикла — непростая задача. Необходимо подсчитать не менее трех углеродных эффектов.
Во-первых, некоторые выбросы парниковых газов производятся цепочкой поставок, начиная с лесного хозяйства. При лесозаготовках нарушается и высвобождается почвенный углерод, образуются растительные и древесные отходы, которые в конечном итоге гниют и выделяют углерод, а выбросы производятся транспортными средствами и механизмами, необходимыми для распиловки древесины, транспортировки ее на комбинат и обработки.Примечательно, что в большинстве традиционных анализов жизненного цикла поставки древесины считаются углеродно-нейтральными, если предполагается, что они поступают из устойчиво управляемых лесов; как мы увидим позже, это не всегда надежное предположение.
Во-вторых, некоторое количество углерода содержится в самой древесине, где он удерживается в зданиях, которые могут прослужить от 50 до сотен лет. Хотя точное количество будет зависеть от породы деревьев, методов ведения лесного хозяйства, транспортных расходов и ряда других факторов, Грин говорит, что хорошее практическое правило (подтвержденное этим исследованием) заключается в том, что один кубический метр древесины CLT связывает примерно одну тонну (1 .1 тонна США) СО2.
(Опять же, как мы увидим позже, это зависит от некоторых предположений о лесном хозяйстве.)
Это имеет значение. ShutterstockВ-третьих, что наиболее важно, замена бетона и стали массивной древесиной позволяет избежать включения углерода в эти материалы, что является существенным. На производство цемента и бетона приходится около 8 процентов мировых выбросов парниковых газов, больше, чем любая другая страна, кроме США и Китая.На долю мировой черной металлургии приходится еще 5 процентов. Примерно полтонны CO2 выбрасывается для производства тонны бетона; При производстве тонны стали выбрасывается 2 тонны CO2. Все эти воплощенные выбросы избегаются при замене CLT.
То, как эти три углеродных эффекта уравновешиваются, будет зависеть от индивидуальных случаев, но исследования показывают, что для всех, кроме самых плохо управляемых лесов, общим воздействием использования CLT вместо бетона и стали будет сокращение выбросов парниковых газов.В исследовании 2014 года, опубликованном в Journal of Sustainable Forestry, был глубоко рассмотрен вопрос о углеродных последствиях крупномасштабной замены древесных продуктов на альтернативы и сделан вывод: «В глобальном масштабе можно устойчиво заготавливать как достаточное количество дополнительной древесины, так и потребность в достаточной инфраструктуре зданий и мостов. будут построены так, чтобы сократить годовые выбросы CO2 на 14–31% и потребление FF на 12–19%, если часть этой инфраструктуры будет сделана из дерева ». По его словам, наибольшее сокращение выбросов CO2 произошло за счет «отказа от избыточной энергии [ископаемого топлива], используемой для изготовления стальных и бетонных конструкций.”
Совсем недавно группа из Вашингтонского университета попыталась провести полный комплексный анализ жизненного цикла, сравнивая «гибридное, среднеэтажное коммерческое здание из кросс-клееной древесины (CLT)» с «железобетонным зданием с аналогичными функциями. характеристики.» Подсчитав все факторы, они пришли к выводу, что здание CLT представляет «26,5% -ное снижение потенциала глобального потепления».
Это, вероятно, неплохая оценка, основанная на практическом опыте, хотя, опять же, эта цифра может быть увеличена в любом направлении за счет лучших или худших методов ведения лесного хозяйства, транспорта, фрезерования, строительства и утилизации.
3. Позволяет строить здания быстрее, с меньшими затратами на рабочую силу и меньшими отходами
Вместо того, чтобы заказывать материалы в массовых количествах, разрезать по размеру на месте и собирать, как при традиционном строительстве, большая часть труда и изготовления зданий из CLT выполняется на заводе, часто с использованием станков с числовым программным управлением (ЧПУ). для точных разрезов.
Если архитекторы и дизайнеры предоставят подробные планы, фабрика может изготовить, e.g., стена CLT точно по спецификации, с дверными и оконными проемами в нужных местах и с местом для водопровода и электричества. Это практически исключает отходы материала — нет вырезов в дверях и окнах, которые можно было бы выбросить, потому что древесина никогда не закладывалась в них. При производстве под управлением компьютера древесина укладывается только там, где это необходимо.
Поскольку эти сборные элементы могут быть собраны по несколько за раз, последовательно, с относительно небольшими трудозатратами, они могут быть доставлены на строительную площадку точно в срок, что позволяет избежать массовых запасов на месте и минимизировать затраты на месте. срыв.Строительные проекты можно втиснуть в тесные, своеобразные городские пространства.
Даже высокие башни можно построить за несколько недель с низкими затратами на рабочую силу. По данным производителей пиломатериалов из хвойных пород, «массивные деревянные дома строятся примерно на 25% быстрее, чем бетонные, и требуют на 90% меньше строительных перевозок».
Заводское производство «создаст высокий уровень повторяемости, который приведет к сокращению отходов и потраченных впустую затрат» обычного строительства, говорит Грин, что в конечном итоге сделает что-то вроде набора запчастей для дома невероятно дешевым.
Действительно, в статье для National Geographic журналист Сол Элбейн пишет о Джоне Кляйне, архитекторе из Массачусетского технологического института, который считает, что «его фирма могла бы предложить многолюдным городам 2020-х годов линейку стандартизированных, настраиваемых квартир средней этажности и офисных зданий. , по большей части изготовленные из модульной массивной древесины, которую разработчики могли заказать в спецификациях, как диваны IKEA ».
Прямо сейчас, говорит Кляйн, «каждое здание — это прототип», спроектированный и построенный один раз. Массовая древесина поможет это изменить.
4.Это фантастика при землетрясениях
Эффективность массивной древесины при землетрясениях была многократно проверена (и проверена и проверена) и оказалась чрезвычайно хорошей.
В то время как бетон просто трескается при землетрясениях, что означает, что бетонные здания необходимо сносить и заменять, деревянные здания можно ремонтировать после землетрясений.
Массивная древесина также легче и может быть построена на городских землях, например. заброшенные поля, не подходящие для тяжелого бетонного строительства.
5. Это эстетически и даже духовно привлекательно
Древесина часто остается открытой в массовых деревянных зданиях — ее не нужно обертывать или укреплять, чтобы соответствовать нормам — и нет ничего более красивого, чем большие участки открытой древесины. Это привлекательно на первичном уровне, это связь с природой. По словам Грин, дерево — это «отпечаток пальца природы в зданиях», который оказывает глубокое успокаивающее действие.
Архитектор Сьюзан Джонс из Atelierjones LLC руководила строительством одной из первых односемейных резиденций CLT — ее дома в Сиэтле, построенного пять лет в соответствии с суперэффективными стандартами пассивных домов.(Об этом было рассказано в журнале Dwell Magazine.) «Нам нравится там жить», — говорит она. Интерьер полностью отделан деревом, и «акустика невероятно богатая, есть красивый тон, в воздухе все еще чувствуется легкий запах сосны, а то, как он улавливает свет, просто волшебно». Джонс говорит, что, учитывая все обстоятельства, строительство ее дома с использованием CLT увеличило общие затраты примерно на 8 процентов.
Внутри дома CLT Сьюзан Джонс. Ателье Джонс(См. Также этот очень крутой дом CLT в Атланте, который вы можете арендовать через Airbnb.)
Массивная древесина также является хорошим естественным изолятором: «Хвойная древесина в целом имеет примерно одну треть теплоизоляционной способности сопоставимой толщины стекловолоконной изоляции, но примерно в 10 раз больше, чем у бетона и кирпичной кладки, и в 400 раз больше, чем цельная сталь. ” Это делает его особенно подходящим для окон и дверей.
6. Это может помочь заплатить за хорошее управление лесным хозяйством на государственной земле
Леса на Западе превратились в пороховые бочки отчасти из-за изменения климата, а отчасти из-за многих лет плохого управления.Они заполнены деревьями мертвыми или ослабленными от нашествия сосновых жуков. Десятилетия чрезмерно усердной противопожарной защиты заставили их задыхаться от густых деревьев небольшого диаметра. В последнее время, когда вокруг все это возжигание, «так много топлива, что интенсивность огня стирает все с лица земли», — говорит Хилари Франц, уполномоченный по делам общественных земель в штате Вашингтон. Земля постоянно покрыта шрамами.
Леса на государственных землях остро нуждаются в прореживании, но средств всегда не хватает. Это натолкнуло Франца на мысль: использовать слабые и маленькие деревья, для которых нет другого рынка, для массового производства древесины.(Подойдут бревна с вершиной всего 4,5 дюйма.) Достаточно большой рынок массивной древесины создаст финансирование для прореживания этих деревьев. В качестве бонуса Франц хочет использовать массивную древесину для строительства недорогого доступного жилья на государственной земле.
7. Он может создать рабочие места в неблагополучных сельских районах
Хвойные (в основном сосновые, еловые или пихтовые) леса в США в основном встречаются на северо-западе и юго-востоке, и общины, которые живут и работают в них, испытывают трудности, особенно после жилищного кризиса и большой рецессии.
Новый спрос на древесину хвойных пород может помочь открыть некоторые из закрытых заводов и возродить некоторые из этих сообществ, согласовав их интересы с программой национального возрождения в стиле Green New Deal.
8. Другого выбора нет
В своем выступлении на TED Грин отмечает, что миллиарды людей во всем мире не имеют дома — полмиллиона в Северной Америке — и в грядущем столетии им придется жить, в основном в городах. Если все это городское жилье будет построено из бетона и стали, климат будет омрачен.
«В течение следующих 20 лет будет построено более половины новых зданий, ожидаемых к 2060 году», — сообщает Программа ООН по окружающей среде (ЮНЕП). «Что еще более тревожно, две трети этих дополнений, как ожидается, произойдут в странах, которые в настоящее время не имеют обязательных строительных норм в области энергетики».
Необходимо найти более устойчивую альтернативу. А древесина — единственный материал, в достаточном количестве и возобновляемый, чтобы выполнять эту работу. Нам нужно выяснить, как заставить его работать.«У нас нет выбора, — сказал мне Грин. «Это единственный вариант».
«Улыбка», общественный павильон из CLT, спроектированный и построенный в Лондоне в 2016 году архитектором Элисон Брукс. Архитекторы Элисон БруксОговорки о массовой древесине
Из всего, что я читал и среди всех, с кем я говорил о массовом дереве, я не встречал ничего, кроме энтузиазма по поводу его архитектурных свойств. Единственным исключением может быть коалиция Build With Strength, которая выступила против массового включения древесины в IBC, охарактеризовав ее как шаткую, легковоспламеняющуюся и экологически неустойчивую.Но Build With Strength, кхм, спонсируется бетонной промышленностью.
В целом, архитекторы и строители в восторге от массового производства древесины, равно как и лесозаготовительные предприятия и сообщества, политики лесных штатов, климатические ястребы, обеспокоенные углеродным воздействием зданий, и городские власти, ищущие способы ускорить декарбонизацию (и выиграть что-то хорошее). PR).
Не все шло гладко — несколько панелей CLT треснули и рухнули во время строительства здания Университета штата Орегон в марте 2018 года; планы строительства деревянной башни в Портленде, штат Орегон, провалились, но попутный ветер, стоящий за массивной древесиной, очень силен.Материал, который можно выращивать в изобилии, создает рабочие места в сельской местности, снижает строительные отходы и затраты на рабочую силу, а также замедляет рост бетона и стали, кажется беспроигрышным вариантом.
Существующие добросовестные оговорки касаются цепочки поставок, и они бывают двух форм.
Во-первых, защита и правильное управление лесами — это огромная часть борьбы с изменением климата и сохранения пригодного для жизни мира. Нетронутые лесные экосистемы обеспечивают не только связывание углерода, но и экосистемные услуги, среду обитания диких животных, отдых и красоту.
Сплошная рубка в Орегоне. ShutterstockЭкологи опасаются, что леса Северной Америки недостаточно защищены, чтобы выдержать резкий скачок спроса. Совет по защите природных ресурсов представил ужасающий отчет о (систематически заниженном) количестве парниковых газов, выбрасываемых в результате сплошных рубок в бореальных лесах Канады, поскольку нетронутые экосистемы заменяются управляемыми лесными монокультурными культурами. (Подробнее о повреждении бореальной зоны в этом отчете.В Oregon Wild есть аналогичный отчет об устаревших правилах лесного хозяйства в этом штате, которые являются одними из самых слабых в стране.
Существует два конкурирующих стандарта сертификации заготавливаемой древесины: Инициатива устойчивого лесного хозяйства (SFI), спонсируемая отраслью, и Лесной попечительский совет (FSC), независимый орган, созданный защитниками окружающей среды. Неудивительно, что стандарты FSC значительно строже в отношении сплошных рубок, использования пестицидов и многого другого. Хотя у SFI есть свои защитники и недавно были проведены реформы, на экологов это не произвело впечатления, и несколько архитекторов и строителей, с которыми я разговаривал, решительно предпочли использовать древесину FSC.(Джонс сказала, что предлагает это клиентам, но это добавляет 10-процентную надбавку, поэтому они не всегда идут на это.)
Во-вторых, некоторые защитники окружающей среды обеспокоены тем, что преимущества древесины как строительного материала в отношении секвестрации переоцениваются.
Международный институт устойчивого развития опубликовал в прошлом году отчет, в котором рассматриваются пробелы и недостатки в анализе жизненного цикла применительно к строительным материалам, в частности к дереву. Они обнаружили, что «существующие LCA дают сильно различающиеся результаты даже для аналогичных зданий», что существуют широкие региональные различия в характеристиках зданий, и, что особенно важно, что LCA имеет тенденцию преувеличивать важность «воплощенного углерода» в древесине, игнорируя или недооценка выбросов в других частях жизненного цикла.
В частности, говорится в сообщении, наиболее неопределенные части большинства ОЖЦ связаны с углеродом, секвестрированным в древесине , и углеродом, высвобождающимся в конце срока службы — двумя вопросами, имеющими центральное значение для массового производства древесины.
Многочисленные экологические группы, возглавляемые Sierra Club, подписали в 2018 году открытое письмо официальным лицам штата Калифорния, призывая с осторожностью относиться к массовой древесине. Примечательно, что они не возражали категорически. Они утверждали, что благодаря современным методам ведения лесного хозяйства его климатические преимущества преувеличены.«CLT не может быть экологически безопасным, если он не исходит из экологически безопасного лесного хозяйства», — заявили они.
В письме приводится краткий список принципов, которыми следует руководствоваться в экологически безопасном лесном хозяйстве, в том числе: «Вырубка оставшихся спелых и девственных лесов мира, а также непроходимых / неосвоенных и других нетронутых лесных ландшафтов должна быть прекращена». И: «Посадки деревьев не должны создаваться за счет естественных лесов».
Хотя это и не идеально, они пришли к выводу, что «FSC-сертификация частных лесных угодий может способствовать прогрессу в правильном направлении.”
«Нет никаких сомнений в том, что [FSC] является золотым стандартом, — говорит Джонс, — но все это лучше, чем ничего не делать».
Массовая древесина должна сочетаться с устойчивым лесным хозяйством
Что мы должны сделать из всего этого?
Есть много способов уменьшить воздействие строительного сектора на окружающую среду и климат, некоторые из которых, возможно, более важны, по крайней мере на данный момент, чем воплощенный углерод материалов. К ним относятся плотные городские засыпки и мультимодальные перевозки, более устойчивые цепочки поставок и методы строительства, электрификация систем отопления и охлаждения, а также более высокие характеристики зданий (эффективное тепло, свет и циркуляция воздуха).
Но, тем не менее, математика ясна: это будет катастрофа, если мы попытаемся приспособить растущее, урбанизирующееся население 21-го века зданиями из бетона и стали, точно так же, как это будет катастрофой, если мы попытаемся сделать это с помощью генерируемой энергии. из ископаемого топлива.
Массовая древесина представляется единственной жизнеспособной альтернативой. И это круто! Это сокращает отходы и затраты, открывает возможность массового производства недорогого жилья на заводе и пробуждает интерес и творческий потенциал строительного сообщества.»Это так весело!» Джонс говорит.
T3 Bayside в Торонто — после завершения строительства в 2021 году, самая высокая офисная башня из дерева в Северной Америке. 3XNКак бы круто это ни было, было бы катастрофой, если бы переход на массовую древесину привел к дальнейшей потере зрелых лесов и усилению сплошных рубок. Воздействие неустойчивого лесного хозяйства может свести на нет остальные выгоды.
Для меня моральные, экономические и стратегические аргументы указывают на одно и то же: массовая древесина стоит прославлять и поддерживать, но она всегда и везде должна идти рука об руку с новым акцентом на экологически безопасное лесное хозяйство.По крайней мере, каждый, кто выступает за массовую древесину или участвует в ее производстве, должен добиваться того, чтобы стандарты сертификации FSC стали нормативным уровнем, а не добровольным потолком.
Дров достаточно; По оценкам Грина, 20 лесам Северной Америки требуется около 13 минут, чтобы в совокупности вырастить достаточно древесины для 20-этажного здания. Но если мы хотим, чтобы леса сделали для нас больше, чтобы обеспечить все наши квартиры, офисы и дома, мы должны заботиться о них, чтобы они могли делать то же самое для будущих поколений.
Дополнительная литература
Некоторые подробные ресурсы для людей, которые хотят заняться массовым лесным хозяйством:
- Отраслевая группа Think Wood имеет руководство по CLT, которое охватывает «производство, конструктивное проектирование, соединения, пожарные и экологические характеристики, а также подъем и перемещение элементов CLT». Он также предлагает множество страниц по конкретным темам, связанным с таймером массы, например, CLT.
- Фирма Fast + Epp, занимающаяся проектированием строительных конструкций, имеет Руководство разработчика по массивной древесине, «краткий обзор различных типов массивной древесины, примеры недавних массовых деревянных башен, маркетинговые возможности, а также преимущества и риски строительства.”
- В журнале Canadian Architect есть чрезвычайно подробный учебник по массивной древесине с точки зрения строительной инженерии. У
- Central City Association of Los Angeles есть красивый технический документ, обобщающий массовый таймер. У
- Utility Dive есть интервью с архитектором Эндрю Цэем Джейкобсом, которое он называет «массовой древесиной 101».
Несколько хорошо сделанных и доступных для СМИ знакомств с массовой древесиной:
И не пропустите выступление Майкла Грина на TED Talk.
Бетон из дерева — ScienceDaily
Дома могут быть деревянными, как раньше, или бетонными, как сегодня. Чтобы построить завтрашний день, комбинируются два метода строительства: эти гибридные конструкции, содержащие как деревянные, так и бетонные элементы, становятся все более популярными в современной архитектуре.
В контексте Национальной ресурсной программы «Ресурс древесины» (NRP 66) швейцарские исследователи разработали еще более радикальный подход к сочетанию дерева и бетона: они производят несущий бетон, который сам состоит в основном из дерева.Во многих смесях объемная доля древесины превышает 50 процентов.
Изделия из древесины на цементной основе существуют уже более ста лет. Однако раньше они использовались только для ненесущих целей, например, для изоляции. Дайя Цвикки, руководитель Института строительных и экологических технологий Школы инженерии и архитектуры Фрибурга, задалась вопросом, не пришло ли время для более амбициозного использования деревянного бетона.
Плавающий бетон
Вместе со своей командой Цвикки экспериментировал с составом и зернистостью древесины, а также с различными добавками, а затем подверг различные смеси строгим испытаниям.Основное отличие от классического бетона в том, что щебень и песок заменены мелко измельченной древесиной. Другими словами, с цементом примешиваются не мелкие камни, а опилки. Благодаря высокому содержанию древесины новые строительные материалы обладают хорошей огнестойкостью и действуют как теплоизоляция. «Они весят почти половину того, что весит обычный бетон — самые легкие из них даже плавают!» — говорит Цвикки. Более того, поскольку материалы в основном основаны на возобновляемых ресурсах, после демонтажа их можно повторно использовать в качестве источника тепла и электричества.Древесину можно сжигать при сжигании отходов, хотя для повседневного использования она соответствует стандартам противопожарной защиты.
Первоначальные стресс-тесты 1: 1 показывают, что новый бетон на древесной основе также подходит для плит и стеновых элементов и может выполнять несущие функции в строительстве. Этот процесс также подходит для сборных блоков. В этом контексте, в частности, группа Фрибург хотела бы углубить свой опыт с помощью более широкого спектра тестов. Исследователи хотят выяснить, какой древесно-бетонный композит лучше всего подходит для каких областей применения и как его можно эффективно производить.
«Пройдет несколько лет, прежде чем мы увидим первые здания, в которых легкий бетон, содержащий дерево, играет важную роль в строительстве», — говорит Цвикки. «Уровень знаний, необходимый для широкого применения, все еще слишком ограничен».
История Источник:
Материалы предоставлены Швейцарским национальным научным фондом (SNSF) . Примечание. Содержимое можно редактировать по стилю и длине.
(PDF) ИСПОЛЬЗОВАНИЕ ПЕРЕРАБОТАННЫХ ДРЕВЕСНЫХ ОТХОДОВ В ПРОИЗВОДСТВЕ ЛЕГКОГО БЕТОНА
7.Хайруддин, С.А.А., Рахман, Н.А., Джамалуддин, Н., Джайни, З.М., Эламин, А., Рум, Р.Х.М. (2020). Связь
Прочность пустотелого профиля, заполненного бетоном, модифицированным волокнистым пенобетоном. Archives of Civil
Engineering, стр.97-108 ..
8. Адебакин И., Адейеми А. (2012). Использование опилок в качестве добавки при производстве недорогих и легких блоков
Пустотелый песчаник. Американский журнал научных и промышленных исследований, 3 (.6), 458-463.
9.Магесвари М. и Видивелли Б. (2010). Использование золы из опилок в качестве замены мелкого заполнителя в бетоне.
Journal of Environment Research and Development, 3 (3), 720–726.
10. Парамасивам П. и Локи Ю. О. (1980). Этюд-опилки-бетон. Международный журнал цемента
Композиты и легкий бетон. Международный журнал легкого бетона., 2 (1), 57-61.
11. Сейлз, А. С., Сантос, Ф. Р., Цимер и В. М. (2010). Легкий композитный бетон, полученный с использованием воды
Шлам и опилки: термические свойства и потенциальное применение.Строительство и строительство
Материалы, 24 (12), 2446-2453.
12. Цзянь, Х. (2014). Применение опилок в бетоне. Advanced Materials Research, 941-944,
849-853. DOI: 10.4028 / www.scientific.net / AMR.941-944.849
13. Абердин. (1971). Отходы в бетоне — можно ли сделать бетон из битого стекла? опилки? пластмассы?
шахтные отходы? мусорная фритта? Бетонное строительство.
14. Ансари, Ф., Махер, А., Люк, А., Юн Чжан, Г., и Szary, P. (2000). Вторичные материалы в портландцементе
Бетон. Заключительный отчет. Федеральное управление автомобильных дорог США, 11-37.
15. Бдейр, Л. М. Х. (2012). Изучение некоторых механических свойств строительного раствора с опилками как частичная замена
песка. Анбарский журнал технических наук, 5 (1), 22-30.
16. Taoukil, D., bouardi, A. E., Ezbakhe, H., and Ajzoul, T. (2011). Тепловые свойства бетона, облегченного древесными заполнителями
. Исследовательский журнал прикладных наук, техники и технологий.
17. Феликс Ф., Удоеё. И Дашибил П. У. (2002). Опилки золы как бетонный материал. Журнал материалов гражданского строительства
, машиностроение, 14, 173-176. DOI: 10.1061 // asce / 0899-1561 / 14: 2/173.
18. Ганирон Т. младший (2014). Влияние опилок как мелкого заполнителя в бетонной смеси для строительства.
Международный журнал передовых наук и технологий, 63, 73-82. DOI: 10.14257 / ijast.63.07
19. ASTM C469. (2014). Метод испытания статического модуля упругости и коэффициента Пуассона бетона при сжатии
, ASTM International.
20. Код ACI 318. (2019). Требования строительных норм для конструкционного бетона, Американский институт бетона ..
21. Комитет кодекса ACI 213R. (2019). Руководство для конструкционного легкого заполнителя. Американский институт бетона
.
22. ASTM 293. (2016). Прочность бетона на изгиб (с использованием простой балки с точечной нагрузкой). Ежегодный
Книга стандартов ASTM, 4 (2).
23. ASTM C496. (2017). Стандартный метод испытания прочности на разрыв цилиндрического бетона
образцов.Ежегодная книга стандартов ASTM, 4 (2).
СПИСОК ЦИФР И ТАБЛИЦ:
Рис. 1. Обзор методологии исследования
Рис. 2. Тип древесных отходов (2)
Рис. 3. Тип древесных отходов (2)
Рис. 4. Цилиндр, Кубики, призмы и образцы из легкого бетона.
Рис. 5. Процедура заливки
Рис. 6. Контрольно-измерительные приборы
Рис. 7. Прочность цилиндра на сжатие ݂
ᇱ (МПа) с процентным содержанием древесных отходов для всех смесей
с разным временем отверждения
Рис.8. Прочность цилиндра на сжатие
ᇱ (МПа) (МПа) с плотностью для всех смесей с разным твердением
время
Рис. 9. Зависимость модуля упругости бетона от прочности на сжатие ݂
௨ ( МПа)
Рис. 10. Зависимость модуля разрыва бетона от прочности на сжатие ݂
௨ (МПа)
ИСПОЛЬЗОВАНИЕ ПЕРЕРАБОТАННЫХ ДЕРЕВЯННЫХ ОТХОДОВ В ПРОИЗВОДСТВЕ ЛЕГКОГО БЕТОНА 687
Бетон, сталь или дерево: поиск нуля -Нет-углеродные конструкционные материалы
Для продвижения своих проектов легких конструкций Бакминстер Фуллер спросил: «Сколько весит ваше здание?» Сегодня, когда архитекторы понимают, что необходимы как структурная, так и углеродная эффективность, возникает вопрос: «Сколько углерода содержит ваше здание?»
Многие архитекторы настаивают на сокращении или устранении воплощенных выбросов углерода, как это уже происходит с эксплуатационной энергией.Например, начиная с 2020 года, глобальная архитектурная и инженерная компания HOK планирует провести оценку жизненного цикла конструкций всех своих новых целостных строительных проектов и «искать возможности для оптимизации наших спецификаций», — говорит Аника Ландрено, доц. . AIA, директор по устойчивому дизайну.
Действительно, строительная конструкция и подконструкция — хорошие места для охоты, потому что вместе они составляют более половины углеродного следа коммерческого здания. Более того, архитекторы и разработчики должны искать возможности для повторного использования и обновления существующих конструкций, чтобы не тратить впустую энергию, уже израсходованную (и уже выделенный углекислый газ), на их создание.Палитра углеродных интеллектуальных материалов от Architecture 2030 и калькулятор воплощенного углерода в строительстве, или EC3, инструмент, разработанный Форумом углеродного лидерства, C Change Labs и Skanska, — отличные места для изучения влияния выбора материалов как для проектов модернизации, так и для новых строительных проектов. .
Источник: Carbon Leadership Forum. Пример диаграммы Сэнки доступных сокращений на основе текущей цепочки поставок, взятой из калькулятора Embodied Carbon in Construction. Источник: Carbon Leadership Forum. Вставка для точки данных стальной арматуры в приведенном выше примере диаграммы СанкиПри взвешивании вариантов стали, бетона или дерева необходимо учитывать такие факторы, как местоположение проекта, масштаб, ожидаемый срок службы, возможность повторного использования и даже сравниваемые показатели материалов (см. «Как измерить воплощенный углерод»).По мере роста осведомленности о воплощенном углероде отрасли стремятся сделать свою продукцию более привлекательной. Сами по себе архитекторы не могут сократить воплощенный углерод в своих проектах, но они, скорее всего, будут прислушиваться к клиенту и могут повлиять на цепочку поставок через свои спецификации. Прежде чем принимать окончательные решения по материалам, воспользуйтесь все более удобными для пользователя инструментами сравнения и вовлеките в диалог строителей и поставщиков — чем раньше, тем лучше.
Мировой сталелитейный сектор имеет огромный углеродный след, на который приходится более 10% глобальных выбросов углекислого газа.«Крупные сталелитейные компании очень хорошо осведомлены о требованиях общества по сокращению выбросов и ищут способы отреагировать на это», — говорит Мэтью Венбан-Смит, исполнительный директор международной некоммерческой организации ResponsibleSteel. базируется в Вуллонгонге, Новый Южный Уэльс, Австралия.
Производство новой стали из железной руды энергоемко. В кислородных печах (кислородных конвертерах), которые являются нормой для большинства развивающихся стран, требуется кокс — очищенная версия угля — для извлечения железа из руды и легирования ее углеродом.Затем полученный чугун перерабатывается в низкоуглеродистую сталь, которая содержит около 25% переработанного чугуна и стального лома. Производители экспериментируют со способами замены угля и кокса не ископаемыми веществами, такими как водород и электролиз на конвертерных фабриках.
Источник: EPD International. Образец шаблона экологической декларации продукции (EPD)По оценкам Американского института стальных конструкций, 98% конструкционной стали из снесенных зданий восстанавливается и перерабатывается в новые стальные изделия.Таким образом, отечественная конструкционная сталь, которая производится на заводах с электродуговыми печами (EAF), может похвастаться содержанием вторичного сырья 93%, согласно утвержденной UL экологической декларации продукции (EPD), составленной AISC в 2016 году. стальную балку, транспортный контейнер или старый холодильник можно продать на металлолом и превратить в стальную балку с широкими полками, которая перейдет в новый небоскреб », — говорит советник AISC Люк Джонсон.
Поскольку заводы EAF работают на электричестве, они в основном так же экологичны, как и их источник энергии.В сентябре прошлого года сталелитейный завод в Колорадо XIX века, принадлежащий российскому конгломерату Evraz, заключил сделку с местной энергетической компанией о строительстве прилегающей солнечной батареи мощностью 240 мегаватт, которая будет обеспечивать значительную часть энергии комбината. Сталелитейная компания Nucor строит в Миссури завод стоимостью 250 миллионов долларов, который будет полностью работать за счет ветра. Другие похожие проекты находятся в разработке.
ResponsibleSteel недавно опубликовала первую версию своего одноименного стандарта, добровольного международного эталонного теста, предназначенного для поддержки «ответственного поиска поставщиков и производства стали» и разработанного в рамках процесса с участием многих заинтересованных сторон с участием производителей, таких как ArcelorMittal, и групп по защите окружающей среды, таких как Могучая Земля.Сертификация основана на стороннем аудите и одобрении независимой комиссии.
Венбан-Смит, который помогал разработать стандарты устойчивого развития в лесном хозяйстве до того, как сосредоточить внимание на стали, хочет сделать сталь одним из самых чистых материалов в мире: «Когда энергетический след для ЭДП становится нейтральным, мы можем думать о стали в полностью замкнутой экономике. ,» он говорит. Осуществление этой мечты, если возможно, скорее всего, произойдет сначала в развитых странах, где большое количество металлолома доступно для вторичной переработки.
Что спрашивать при указании стали
- Доступна ли сталь на электростанциях с электродуговыми печами и, в частности, на станах, работающих на возобновляемых источниках энергии?
- Можно ли использовать в конструкции скрепленные рамы вместо стойких к моменту рам, чтобы уменьшить требуемую массу стали?
- Можете ли вы закупить сталь, сертифицированную ResponsibleSteel?
Люди ненавидят бетон почти так же сильно, как любят его использовать. Как самый распространенный в мире строительный материал, на него приходится от 6% до 11% глобальных выбросов углекислого газа.Большая часть этих выбросов связана с производством вяжущего, портландцемента, который составляет в среднем около 10% бетонной смеси по весу. Производство заполнителя — песка и щебня, которые в среднем могут составлять от 70% до 80% смеси — также требует энергии, но в гораздо меньшей степени. Добыча песка может нанести ущерб речным и прибрежным экосистемам.
Почти половина выбросов углекислого газа цементом возникает в результате сжигания ископаемого топлива для нагрева цементных печей примерно до 2500 F. Достижения в области производства чистой энергии могут помочь сократить эти выбросы: прототипы цементных заводов на солнечных батареях в Калифорнии и Франции, разработанные Heliogen и Solpart соответственно, успешно нагрели печи до температуры около 1800 F с использованием огромных массивов зеркал.Однако большая часть выбросов углекислого газа происходит в результате химических реакций, присущих производству цемента: в процессе, называемом кальцинированием, известняк распадается на углекислый газ, который уходит в атмосферу, и негашеную известь, составляющую цемента.
Некоторые компании связали углекислый газ в бетоне, в том числе компания CarbonCure в Дартмуте, Канада, и Blue Planet в Лос-Гатосе, Калифорния. Эти процессы остаются исключением и на сегодняшний день не полностью компенсируют выбросы углерода при производстве бетона.
Предоставлено Carbon Leadership Forum Скриншот из инструмента EC3 (Embodied Carbon in Construction Calculator) Предоставлено Carbon Leadership Forum Скриншот из инструмента EC3 (Embodied Carbon in Construction Calculator)В настоящее время самый простой способ уменьшить углеродный след бетона — это использовать меньше цемента, как ясно показывает палитра углеродных интеллектуальных материалов. В так называемых смешанных цементах при производстве цемента используется некальцинированный известняк и другие дополнительные вяжущие материалы (SCM) вместо части клинкера — твердые гранулы, полученные в печи, которые измельчаются и смешиваются с другими ингредиентами.Включая природные пуццоланы, такие как зола рисовой шелухи, и промышленные побочные продукты, такие как летучая зола, доменный шлак и микрокремнезем, SCM могут улучшить структурные характеристики бетона, а также снизить содержание в нем углерода.
Северная Америка отстает от Европы в использовании цемента с добавками, говорит Джули Баффенбаргер, старший научный сотрудник и директор по вопросам устойчивого развития компании Beton Consulting Engineers из Мендота-Хайтс, штат Миннесота. Спецификации — хороший способ сделать бетонное строительство более эффективным, отмечает она, но слишком строгие предписания могут привести к обратным результатам.Вместо того, чтобы диктовать пропорции ингредиентов в бетонной смеси, она предлагает проектным группам указать критерии эффективности с точки зрения измеримых пластических и твердосплавных свойств, «чтобы производитель мог предоставить варианты в рамках ограничений». Имейте в виду, что SCM могут увеличивать время, необходимое для достижения требуемых показателей прочности.
Что спрашивать при указании бетона
- Можно ли уменьшить количество цемента в бетонной смеси?
- Можно ли уменьшить общую массу бетона в проекте?
- Какая цементная печь является наименее энергоемкой из имеющихся на местном уровне?
- Какие методы улавливания углерода агрегатами или смесями могут быть включены?
Инновации в области массового производства древесины, в частности, отечественное производство конструкционных изделий, таких как древесина, клееная поперечно, клеем, гвоздями и дюбелями, подогревают надежды на то, что строительство с нулевым выбросом углерода станет возможным в больших масштабах.Согласно отраслевым исследованиям, деревья, вырубленные и замененные для производства массивной древесины, могут улавливать больше углерода во время своего роста, чем то, что выбрасывается при производстве, транспортировке и строительстве. Повышенный спрос на древесину из экологически чистых источников может стимулировать лесовозобновление. «Мы должны заново покрыть часть этой планеты лесами», — говорит Ландрено из HOK. «Мы можем повлиять на это, выбрав деревянную конструкцию, где это возможно».
Спроектированные деревянные панели могут заменить стальные настилы и бетонные перекрытия в коммерческих структурах, а клееные колонны могут выдерживать нагрузку на среднеэтажные и высотные конструкции от своих стальных и бетонных аналогов.Эти деревянные изделия также могут быть огнестойкими и быстро монтируемыми. «В тот день, когда они будут установлены и подключены к несущей конструкции, они смогут нести полную проектную нагрузку», — говорит Кеннет Бланд, вице-президент American Wood Council.
Но соответствует ли массовая древесина требованиям, предъявляемым к экологической устойчивости?
По данным Министерства сельского хозяйства США, общий объем деревьев, произрастающих в лесах США, с 1953 года увеличился на 60%. По мере роста спроса на конструкционные изделия из древесины, леса, которые производят массовую древесину, должны будут управляться устойчиво, с повторной посадкой деревьев. после сбора урожая.Различия в методах ведения лесного хозяйства приводят к большим различиям в количестве улавливаемого углерода, поэтому важно знать, где и как были произведены ваши лесоматериалы.
Требуются дополнительные исследования выбросов углерода при заготовке, переработке и транспортировке изделий из древесины. Новые среднеотраслевые EPD для древесины и изделий из нее ожидаются в первом квартале 2020 года, но заявления конкретных производителей древесины будут еще более полезными. Помимо углерода, содержащегося в самой древесине, существуют выбросы от воздействия почвы и леса, а также от производства смол и клеев, связывающих массивные слои древесины.
Наконец, преимущество массового хранения углерода в древесине сохраняется только в том случае, если балки и панели остаются в эксплуатации или не допускаются к разложению, которое приведет к выбросу углерода обратно в атмосферу. Чтобы деревянные конструкции были долговечными, они должны быть защищены от проникновения воды, насекомых или грибков, возможно, за счет использования герметиков в сочетании с продуманным дизайном и деталями ограждающей конструкции. Для многоразового использования деревянные элементы должны соединяться съемными креплениями.
Что спрашивать при выборе древесины
- Рекуперируется ли ваша деревянная продукция? Если нет, то происходит ли это из устойчивого лесного хозяйства?
- Можно ли собрать конструкцию с помощью съемных креплений, чтобы можно было повторно использовать элементы?
- Используются ли в проекте эффективные методы обрамления, позволяющие минимизировать требуемую массу древесины?
[Ознакомьтесь с этими советами и инструментами для измерения воплощенного углерода, а также посетите палитру углеродных интеллектуальных материалов.]
Эта статья появилась в выпуске за январь 2020 года под названием «Проблема конструкционных материалов».
Проблема углерода
Цемент на основе дерева с высокой прочностью и многофункциональностью
Формирование и трехмерная архитектура из древесного цемента.а) Схематические изображения микромеханизмов образования древесного цемента в процессе замораживания, оттаивания и отверждения. б) Объемные визуализации XRT цемента с ледяной структурой, полученного из цементных растворов со значениями W / C 0,4 и 1,3, с показателями березовой древесины Betula schmidtii для сравнения. Поры в материалах обозначены синим цветом. FD и GD представляют направление замерзания льда и направление роста древесины соответственно. Кредит: Advanced Science, DOI: 10.1002 / advs.202000096Природа часто вдохновляет на создание биомиметических искусственных материалов. В новом отчете, опубликованном в журнале « Advanced Science », Фахенг Ван и группа ученых в области передовых материалов, инженерии и науки в Китае разработали новые цементные материалы на основе однонаправленной пористой архитектуры для имитации конструкций из натурального дерева. Полученный в результате древесный цементный материал показал более высокую прочность при одинаковой плотности, наряду с многофункциональными свойствами, обеспечивающими эффективную теплоизоляцию, водопроницаемость и легкую регулировку отталкивания воды.Команда одновременно достигла высокой прочности и многофункциональности, что сделало древесный цемент новым многообещающим строительным материалом для создания древесно-имитирующих конструкций с высокими эксплуатационными характеристиками. Они представили простую процедуру изготовления для повышения эффективности при массовом производстве с приложениями, подходящими для других систем материалов.
Разработка биоинспирированных древесных материалов
Пористые материалы на основе цемента обладают низкой теплопроводностью для теплоизоляции, высокой звукопоглощающей способностью, отличной проницаемостью для воздуха и воды при сохранении небольшого веса и огнестойкости.Тем не менее, ключевой задачей по-прежнему остается достижение одновременного улучшения как механических, так и многофункциональных свойств, включая механическую поддержку, эффективную транспортировку и хорошую теплоизоляцию. Поэтому очень желательно создавать материалы с улучшенными механическими и многофункциональными свойствами, чтобы активно реализовывать принципы проектирования натурального дерева. В ходе экспериментов Wang et al. разработан древесный цемент с однонаправленной пористой структурой, сформированной методом двунаправленной обработки замораживанием.Процесс позволил сформировать мосты между составляющими конструкции, а затем команда оттаяла полностью замороженные тела, пока лед постепенно не растаял, а цемент не затвердел. Последующий процесс гидратации произвел новые минералы и гели в цементе, включая гидроксид кальция в форме шестиугольника, игольчатый эттрингит и гели силиката-гидрата кальция. Фазы в основном образовывались в цементных пластинах и перерастали в промежутки между ними в процессе оттаивания и отверждения для лучшей структурной целостности с улучшенными взаимосвязями ламелей во время образования пористого цемента.Затем с помощью рентгеновской томографии (XRT) команда выявила образование однонаправленных микропор в цементе с ледяной структурой.
Микроструктурные характеристики древесного цемента. а) СЭМ-изображения поперечного сечения цемента с ледяной структурой, полученного из суспензий с W / C 1,3. б – г) СЭМ-изображения взаимосвязей между цементными пластинами. б) Мосты и пересечения, образованные в процессе замораживания, как показано желтыми стрелками, вместе с минеральными продуктами реакций гидратации в) гидроксида кальция и г) эттрингита.д) Схематическое изображение различных типов взаимосвязей и пор в цементе с ледяной структурой. Кружками обозначены элементы A и L для определения прочности с использованием подхода эквивалентных элементов. е) Вариации общей пористости Ptotal, открытой пористости Popen и межламеллярной пористости Пинтера в цементе с W / C в исходных цементных растворах. Данные на панели (f) получены по крайней мере из трех измерений для каждого набора образцов и представлены в виде среднего значения ± стандартное отклонение.Кредит: Advanced Science, DOI: 10.1002 / advs.202000096. Понимание микроструктурыWang et al. использовали изображения сканирующей электронной микроскопии (СЭМ), чтобы выявить однонаправленные поры между пластинами в цементе с ледяной структурой, которые охватывают большое количество межсоединений, соединяющих ламели. Команда классифицировала взаимосвязи на три типа: (1) мосты и пересечения, образованные из-за частиц цемента, захваченных кристаллами льда в процессе замерзания, (2) гидроксид кальция шестиугольной формы и (3) игольчатый эттрингит.Последние минералы являются результатом реакций гидратации цемента во время процессов оттаивания и отверждения. Цементные ламели содержали обильные поры, образовавшиеся в процессе сушки цемента из-за обезвоживания гелей и удаления воды. Ученые классифицировали поры в древесном цементе на три типа, включая (1) межламеллярные открытые поры, (2) внутриламеллярные открытые поры и (3) внутриламеллярные закрытые поры. Межламеллярная пористость в основном определяется содержанием воды, которая играет роль порообразователя.
- Механические свойства древесного цемента. a, b) Типичные кривые напряжения-деформации сжатия древесно-подобного цемента, изготовленного из суспензий с различным соотношением W / C а) без и б) с добавками SF. c, d) Вариации в c) деформации разрушения, d) плотности поглощения энергии, представленной с использованием площади под кривой зависимости напряжения от напряжения до пикового напряжения, и удельной прочности (вставка на панели (d)) как функции общей пористости. Ptotal. Общие изменяющиеся тенденции обозначены пунктирными кривыми для ясности.д) Зависимость прочности на сжатие от относительной плотности древесного цемента. е) Интерпретация прочности согласно подходу эквивалентных элементов с учетом различных типов пор. Данные на панелях (c) — (f) получены по крайней мере из трех измерений для каждого набора образцов и представлены в виде среднего значения ± стандартное отклонение. Кредит: Advanced Science, DOI: 10.1002 / advs.202000096.
- Многофункциональные характеристики древесного цемента.а) Изменения коэффициента теплопроводности древесного цемента в поперечном профиле в зависимости от номинальной плотности. 0,4-C указывает на цемент, изготовленный из жидких растворов с В / Ц 0,4, но без обработки льда. Данные для пористых цементных материалов с произвольными ячейками также показаны для сравнения. [35, 36] б) Инфракрасные изображения цемента, изготовленного из растворов с различными значениями W / C 0,4, 0,9, 1,6 и 2,4, помещенного на нагревательную пластину. 100 ° С. в) Зависимость коэффициента водопроницаемости в вертикальном направлении от общей пористости Ptotal древесного цемента.Установка, используемая для измерения водопроницаемости, показана на вставке. г) Изображения и схематические иллюстрации, показывающие водопроницаемую и отталкивающую природу цемента до и после гидроизоляционной обработки, а также эффекты капиллярного притяжения и отталкивания внутренних поверхностей из-за гидрофильных и гидрофобных характеристик. Данные на панелях (а) и (с) получены по меньшей мере из трех измерений для каждого набора образцов и представлены в виде среднего значения ± стандартное отклонение.Общие изменяющиеся тенденции обозначены пунктирными кривыми для ясности. Кредит: Advanced Science, DOI: 10.1002 / advs.202000096.
Механические и многофункциональные свойства материала
Группа получила характерные кривые напряжения-деформации сжатия древесного цемента с добавками паров кремния или без них в его состав.Прочность на сжатие монотонно снижалась с увеличением соотношения вода / цемент в растворах, используемых для разработки материала, что в конечном итоге привело к увеличению пористости цемента. Поскольку деформация разрушения материала увеличивалась с увеличением общей пористости, прочность пористого твердого тела можно было определить по его пористости. Затем команда измерила коэффициент теплопроводности древесного цемента с ледяной структурой, чтобы показать уменьшение теплопроводности с увеличением пористости материала.Они также использовали инфракрасные (ИК) изображения для четкого наблюдения за прочными теплоизоляционными свойствами цементного материала с ледяной структурой. Для регулирования эффективности теплоизоляции Wang et al. регулировали твердую нагрузку в цементных растворах, увеличивая содержание воды / цемента. Полученный цементный материал впитывает воду из-за гидрофильного (водопривлекательного) характера его внутренних поверхностей. Напротив, они могут предотвратить проникновение воды в поры за счет гидроизоляции поверхностей кремнийорганическим агентом; такие усилия по гидрофобности могут даже заставить материал плавать на воде.Таким образом, способ может облегчить переключаемые применения в качестве проницаемых или водонепроницаемых конструкций, подходящих в качестве строительных материалов.
Сравнение древесного цемента с натуральным деревом и другими пористыми цементными материалами. [3-8, 31, 43, 53, 59-61] a) Прочность на сжатие и плотность для широкого диапазона пористых материалов на основе цемента, демонстрирующих относительно более высокую прочность современного древесного цемента при одинаковой плотности. LAC: легкий агрегатный контент; OPC: обычный портландцемент; ПФ: полипропиленовое волокно; ПК: портландцемент; CSA: бетонный осадок; S / C: соотношение песка и цемента по весу.б) Схематические иллюстрации стратегий проектирования натурального дерева и древесного цемента для оптимизации их механических и многофункциональных свойств, связанных с однонаправленными пористыми архитектурами. Данные по прочности и плотности современного древесного цемента на панели (а) представлены в виде среднего значения ± стандартное отклонение. Кредит: Advanced Science, DOI: 10.1002 / advs.202000096.Перспективы древесных цементных материалов
Таким образом, Фахенг Ван и его коллеги представили технику создания ледяных шаблонов как жизнеспособный подход к созданию однонаправленных микропор для применения в керамике, полимерах, металлах и их композитах.Ученые разработали процесс обработки сублимационной сушкой, основанный на самоотвердевающем поведении цемента при контакте с реакциями гидратации. Полученная в результате структура древесного цемента содержала множество пор в открытых или закрытых формах и множество соединений, соединяющих их ламели. Когда пористость увеличивалась, прочность цемента снижалась. Древесный цемент также отличался более низкой теплопроводностью и хорошей водопроницаемостью. Команда могла изменить цементный материал на водоотталкивающий или водоотталкивающий с помощью гидрофобной или гидрофильной обработки соответственно.Простая и практичная стратегия разработки материалов в сочетании с самозатвердевающей природой его составляющих может значительно улучшить временную и экономическую эффективность метода ледового моделирования для формирования устойчивого бетона с потенциалом для переноса этого метода на другие системы материалов.
Цемент с применением наноинженерии перспективен для герметизации газовых скважин с утечками
Дополнительная информация: Ван Ф.и другие. Цемент под дерево с высокой прочностью и многофункциональностью, Advanced Science , doi: doi.org/10.1002/advs.202000096
Монтейро П. и др. На пути к устойчивому бетону, Nature Materials , doi.org/10.1038/nmat4930
Рой Д. М. Новые прочные цементные материалы: химически связанная керамика, Science , 10.1126 / science 235.4789.651
© 2021 Сеть Science X
Ссылка : Цемент на основе дерева, обладающий высокой прочностью и многофункциональностью (2021 г., 5 января) получено 10 октября 2021 г. с https: // физ.org / news / 2021-01-на основе дерева-цемент-высокопрочная-многофункциональность.html
Этот документ защищен авторским правом. За исключением честных сделок с целью частного изучения или исследования, никакие часть может быть воспроизведена без письменного разрешения. Контент предоставляется только в информационных целях.
Какой строительный материал (дерево, сталь, бетон) оказывает наименьшее общее воздействие на окружающую среду? — Обсуждение науки
Дерево — фундаментальная часть строительства.Это универсальный строительный материал, потому что его можно найти повсюду. Ранние поселенцы в Северной Америке использовали древесину для строительства бревенчатых хижин, поскольку это было более эффективно, чем транспортировка других материалов из Европы. (Росманиц, 2013 г.) Древесина не требовала обширных инструментов для производства строительного материала. В то время древесина была самым надежным строительным материалом. Дерево настолько надежно, что дома, построенные более 800 лет назад, все еще стоят сегодня (Hoibo, Hansen, & Nybakk, 2015).С течением времени древесина по-прежнему остается предпочтительным методом строительства домов. Однако через некоторое время стал доступен новый материал. Бетон использовался в нескольких древних цивилизациях, а именно в Риме и Египте, где ресурсы ограничены, а древесина не может быть найдена. Сегодня мы видим, что бетон используется в основном в подвалах, мостах и в крупных промышленных сооружениях, потому что из большинства материалов он является одним из самых непроницаемых и рентабельных.
Оглядываясь вокруг, вы можете утверждать, что сегодня в строительстве наиболее часто используются бетон и сталь.Однако, в отличие от дерева, бетон производится с использованием нерациональных методов. Древесину можно сносить для повторного использования, но бетон нельзя утилизировать, и его оставляют там, где его сносят. Сталь — новейший из трех материалов. Сталь стала популярным строительным материалом во время промышленной революции из-за своей прочности. В это время большинство людей начали переходить со строительства из дерева на сталь. Обладая текущими знаниями общества, мы знаем, что древесина — лучший вариант с точки зрения устойчивости. Развитие бетона и стали не может привести к наиболее устойчивому пути.
Принимая во внимание серьезные угрозы глобального изменения климата, устойчивое строительство — это путь вперед, на котором строительная промышленность может сыграть свою роль в достижении устойчивого и более здорового мира. Можно просто определить устойчивость как строительство для удовлетворения потребностей нынешнего поколения без ущерба для способности будущих поколений удовлетворять свои потребности. Ученые и эксперты сходятся во мнении, что деятельность человека способствует изменению климата. Лишь недавно реальность экологической катастрофы из-за неестественного вмешательства человека в окружающую среду стала более очевидной.Один конкретный процент вовлеченности — это строительная отрасль. В конечном счете, на здания приходится треть общих глобальных выбросов парниковых газов, в первую очередь за счет использования ископаемого топлива на этапе их эксплуатации (Huovila, Ala-Juusela, Melchert, & Pouffary, 2009). Чрезмерные выбросы углерода представляют собой реальную угрозу для мира и могут вызвать серьезные проблемы в будущем. Только в Северной Америке на строительный сектор приходится около 37% двуокиси углерода (CO 2 ) и 40% в Европе, и это, вероятно, сохранится в последующие годы (Beyer, 2012).Кроме того, если мы продолжим строить из неустойчивых материалов, в конечном итоге у нас закончатся материалы для строительства. Быстро приближается переломный момент, когда в мире заканчиваются ресурсы и энергия. Эта причинно-следственная связь повлияет не только на текущее поколение, но и на каждое последующее поколение придется иметь дело с созданными проблемами. Однако для достижения желаемых целей устойчивого и экологичного строительства строительная промышленность должна с гораздо большей серьезностью решать проблемы выбросов в строительном секторе.
Aciu (2014) объясняет, что весь жизненный цикл здания влияет на окружающую среду. Это оценивается с помощью функционального инструмента под названием «Оценка жизненного цикла» (LCA) или сквозного подхода. LCA используется для выполнения оценки, в которой материалы, конструкция, использование и снос здания количественно выражаются в воплощенной энергии и эквиваленте углекислого газа, наряду с представлением потребления ресурсов и высвобожденных выбросов. Эти результаты полезны для архитекторов, инженеров-строителей, подрядчиков и владельцев, заинтересованных в прогнозировании воздействия на окружающую среду на протяжении всего срока службы конструкции.Жизненные циклы строительных материалов должны быть лучше поняты, прежде чем их воздействие на окружающую среду можно будет уменьшить, и LCA стала эффективным инструментом в ответах на важные вопросы по актуальным темам, вызывающим обеспокоенность общественности, таким как выбросы парниковых газов (Hsu, 2010).
Производство, транспортировка и установка строительных материалов, таких как сталь и бетон, требуют большого количества энергии, несмотря на то, что они составляют минимальную часть конечных затрат в здании в целом.Эксперты называют энергию, потребляемую всеми процессами, воплощенной энергией (EE) (Høibø et al, 2015). Небольшое количество воплощенной энергии (углерода) в одной тонне бетона, умноженное на огромное количество используемого бетона, приводит к тому, что бетон является материалом, который содержит наибольшее количество углерода в мире. ЭЭ для бетона, который является самым высоким, составляет 12,5 МДж / кг ЭЭ, для стали — 10,5 МДж / кг ЭЭ, а самый низкий — для древесины с ЭЭ 2,00 МДж / кг. (Сюй, 2010). Воплощенное энергосодержание каждого строительного материала сильно различается, особенно бетона, потому что производство цемента чрезвычайно энергоемко и требует использования ископаемого топлива, что делает его одним из ведущих производителей выбросов углекислого газа, способствующих глобальному потеплению (Shams et al, 2011).
Рассматривая воплощенную энергию бетона и стали, можно сделать вывод, что их воздействие на окружающую среду чрезвычайно велико. С другой стороны, с точки зрения углеродного следа, деревянным зданиям требуется меньше энергии от добычи ресурсов посредством производства, распределения, использования и утилизации по окончании срока службы, и они несут ответственность за гораздо меньшие выбросы парниковых газов, загрязнение воздуха и воды. Shams et al. (2011) сравнили среднюю школу Эльдорадо в Арканзасе, построенную из дерева, с другими зданиями, построенными из стали или бетона.Авторы обнаружили, что экологичная конструкция деревянного здания, также называемая зеленым зданием, состоит примерно из 153 140 кубических футов пиломатериалов, панелей и конструкционной древесины можно сравнить с 2184 автомобилями, находящимися вне дорог в течение года. Для этого объема древесины ASTF (Альянс за сохранение лесов) предполагает, что леса вырастут столько древесины за 13 минут, и углерод, поглощенный древесиной, составляет примерно 3660 метрических тонн CO 2 и, что более важно, предотвращенные выбросы парниковых газов 7780 метрических тонн. СО 2 .Это подтверждает, что древесина является лучшим возобновляемым, биоразлагаемым, нетоксичным и энергоэффективным строительным материалом. В ответ древесина получила практический импульс от правительств и промышленности в таких богатых лесом регионах, как Австрия и Скандинавия, а недавно Министерство сельского хозяйства США объявило конкурс деревянных многоэтажных домов и объявило об инвестициях в 1 миллион долларов для обучения архитекторов и строителей навыкам. работа с деревом (Хамфрис, 2015).
Часто эксперты принимают во внимание производство строительных материалов, когда говорят о факторах, которые делают упор на экологичность.Этот фактор оценивается с помощью LCA. Некоторые строительные материалы, такие как сталь, создать сложнее, и как практически невозобновляемые ресурсы они вносят больший вклад в общее потребление материалов (Kim et al, 1998). Сталь — новейший из трех материалов. Сталь стала популярным строительным материалом во время промышленной революции из-за своей прочности. В это время большинство людей начали переходить со строительства из дерева на сталь. К сожалению, тогда еще не было известно о вреде его изготовления.Производство стали, цемента и стекла требует температуры до 3500 градусов по Фаренгейту, что достигается за счет большого количества энергии на основе ископаемого топлива. С другой стороны, дерево производится с использованием энергии солнца (Shams, Mahmud, & Amin 2011). Переход от экологически чистых строительных материалов, таких как бетон и сталь, к экологически чистым строительным материалам, таким как дерево, в офисных и коммерческих зданиях может существенно снизить негативное воздействие, которое здание оказывает на окружающую среду. .
Если говорить о производстве строительных материалов, древесина имеет одно большое экологическое преимущество перед сталью и бетоном. Дерево — поистине натуральный материал, способный к повторному росту и воспроизводству. Деревья можно собирать так же, как и любую культуру, и легко превращать их в каркас. Лесные фермы — это доступный вариант для массового производства конструкционного материала. Они способны быть эффективными и устойчивыми, однако от них не требуется соблюдать какие-либо законы устойчивости. Это прискорбно, но с введением в действие новых законов мы можем сделать наиболее экологичные материалы еще более экологичными.Мы могли бы сделать это обязательным по закону, чтобы оно было сертифицировано Системой американских лесных ферм. Если это необходимо, то больше нет оправданий тому, почему дерево не является самым устойчивым материалом. (Стандарты сертификации, 2016 г.)
Для получения сертификата American Tree Farm System необходимо соблюдать восемь стандартов. Первый стандарт — это приверженность устойчивому ведению лесного хозяйства. Фермеры, выращивающие деревья, могут сделать это с помощью разработки плана управления лесным хозяйством и внедрения устойчивых методов.Второй стандарт — соблюдение законов. Этот стандарт просто требует, чтобы землевладелец соблюдал все соответствующие правила. Третий стандарт — лесовозобновление и облесение землевладельца. Четвертый стандарт — это защита воздуха, воды и почвы. Этот стандарт является устойчивым, поскольку требует от землевладельца поддерживать или улучшать качество земли. Пятый стандарт — это здоровье вашего леса и животных, которые считают его своим домом. Шестой стандарт — эстетика леса. Седьмой стандарт — защита специальных сайтов.Особые места должны иметь исторические, археологические, культурные, геологические, биологические или экологические характеристики. Последний стандарт, стандартный восемь, — это заготовка лесной продукции и другие виды деятельности. Это восемь стандартов, которым вы должны следовать, чтобы получить сертификат Американской системы лесоводства (Стандарты сертификации, 2016). Все стандарты доказывают общественности, что даже те лесные фермы, которые используются для материальных целей, по-прежнему вносят свой вклад в экологическое здоровье района.Фермы будут постоянно присутствовать, возможно, от 50 до 80 лет. Это количество времени укрепляет постоянный доход и, таким образом, защищает эту территорию от дальнейшего развития. Мир гораздо больше выиграет от леса, который приносит деньги, чем от электростанции, которая приносит деньги. Баланс индустриализации и здоровья лесов создает очень устойчивую систему.
Вторым важным моментом в стоимости энергии для строительного материала является его поломка. Если материал не может быть эффективно переработан, он не может быть экологически безопасным.Когда мы разрушаем бетон, его невозможно снова использовать для строительства. Сталь требует огромного количества энергии, чтобы нагреть сталь и превратиться в новый материал. Каждый раз, когда сталь перерабатывается, ее необходимо плавить при высоких температурах, чтобы превратить ее в новый материал. Энергия, необходимая для переработки стали, требует энергии, получаемой из ископаемого топлива. Повторное использование стали по-прежнему вредит окружающей среде. Древесина — это материал, который требует мало энергии для утилизации и может быть легко использован для строительства.Восстановленная древесина — термин, который используется для обозначения пиломатериалов из старых построек, — может быть добыт под водой, если древесина не сгнила. [BJ1] Одно из преимуществ использования регенерированной древесины вместо свежей новой древесины дает нам возможность использовать более крупные куски пиломатериалов там, где новая древесина не может вырасти такой высокой из-за времени. Новой древесине также нужно время, чтобы сжаться в размерах, когда она начинает высыхать, поскольку регенерированная древесина не гниет, она может быть намного более надежной, чем новая древесина (Erhlich, 2011).
Восстановленная древесина не только снижает углеродный след при строительстве, но и экономически дешевле], чем покупка новой древесины, посадка и выращивание которой требует денег. Рынок вторичных строительных материалов дешевле, чем покупать новенькие. Восстановленная древесина дала людям возможность создать свои рабочие места и выйти на новый рынок. Люди ищут компании, которые специализируются на заготовке древесины, и связываются с ними, чтобы избавиться от материала (Martin, E., & Schendel, E., 2014). Ежедневно строятся новые здания и сносятся старые.Из-за этого люди всегда стремятся утилизировать старые материалы, такие как дерево. Не весь материал можно спасти, но немногое имеет значение. (Мартин Э. и Шендель Э., 2014 г.) Возможность постоянной переработки и повторного использования материалов создает длительный цикл. Требуется меньше деревьев, свалки не будут заполнены древесиной, пригодной для повторного использования, и это будет дешевле для потребителя, так как затраты на рабочую силу будут намного меньше.
Несмотря на то, что древесина имеет экологические преимущества по сравнению с другими материалами, она все еще не используется в необходимом количестве.Однако в настоящее время есть люди, которые настаивают на продвижении зеленого строительства. Некоммерческий совет по экологическому строительству США (USGBC) разработал LEED, или «Лидерство в энергетическом и экологическом проектировании», в марте 2000 года. Это означает, что для получения сертификата LEED строитель должен нести ответственность за окружающую среду и эффективно использовать ресурсы. Они применили свои стандарты в более чем 83 тысячах проектов по всему миру. (LEED, 2016)
Одна вещь, которую требует сертификация LEED, — это низкая воплощенная энергия проекта.Воплощенная энергия — это общее количество энергии, необходимое для доставки материалов на место работы. Если мы говорим о древесине, это включает в себя газ, необходимый для работы бензопилы, транспортировку на лесопилку / строительную площадку, а также энергию, необходимую для распиловки древесины и превращения ее в материал для каркаса. Чтобы получить сертификат LEED, необходимо учитывать, как далеко находится поставщик. Если цена на древесину ниже у поставщика, находящегося в 100 милях, по сравнению с поставщиком, находящимся в 10 милях, LEED все равно потребует, чтобы вы использовали ближайшего поставщика, чтобы снизить объем воплощенной энергии (LEED, 2016).Система LEED эффективно способствует экологичному строительству и созданию устойчивой инфраструктуры.
Исследования и примеры, представленные в статье, показывают, что древесина в конечном итоге является наиболее экологически безопасным продуктом для строительства. Древесина пригодна для повторного использования и очистки, чтобы превратить ее в строительный материал. Лесные фермы могут помочь противодействовать растущей проблеме обезлесения. Обществу необходимо перейти от строительства, в основном, из бетона и стали, к строительству из дерева. Для этого правительство должно стимулировать использование экологически чистых материалов.Ничего не будет достигнуто, пока не будут установлены конкретные правила и пока подрядчики не будут вознаграждены за соблюдение требований устойчивости. Поощрения могут включать сертификаты и снижение налогов. Главное, что нужно сделать, — это снизить стоимость устойчивости и увеличить стоимость неустойчивости. Простое получение положительных вознаграждений за использование древесины. Общество могло бы продолжить давнюю традицию использования дерева в качестве наиболее распространенного строительного материала.
Сертификат дает значительные стимулы для устойчивого строительства.Добавление награды LEED к зданию — отличный маркетинговый инструмент в его резюме. Эти награды позволяют подрядчикам находить больше клиентов. Дополнительный факт, что это зеленые здания, выделяет их в общей структуре строительства, что делает их достойными вложений. Исследование Вьерры (2014) показывает, что устойчивое строительство создает более крупные пулы инвесторов, экономит деньги за счет снижения энергии, затрачиваемой на его создание, и даже дает дополнительную выгоду в виде налоговых льгот. Показано, что количество экологически чистых зданий увеличится до 6.6% на возврат инвестиций. Сертифицированное строительство также увеличило заполняемость на 3,5% и арендную плату на 3% (Vierra, 2014). Строительство — это бизнес, и бизнес работает на доход. Получение сертификата увеличивает количество покупателей и, таким образом, увеличивает сумму дохода, и уже само по себе это должно стать серьезным толчком к тому, чтобы больше подрядчиков строили экологически рационально.
В Соединенных Штатах есть федеральные налоговые льготы, предоставляемые компаниям, построенным из материалов с низким энергопотреблением. Если конструкция считается энергоэффективной, подрядчику и покупателю предоставляются многочисленные налоговые льготы.Стимулирование зеленого строительства с обещанием снижения затрат — один из лучших способов изменить традицию. (Vierra, 2014) Например, Закон об энергетической политике 2005 года содержит вычет налога на прибыль предприятий. Этот налоговый вычет может уменьшиться до 1,80 доллара на квадратный фут, если бизнес использует энергоэффективное оборудование или материалы (DiPeso, 2007). В конечном итоге это может сэкономить предприятиям невероятную сумму денег. Лучший и наиболее эффективный способ изменить строительную отрасль — это создать систему, которая в конечном итоге исключает использование неустойчивых строительных материалов.Создавая больше налоговых льгот и больше правил для зеленого строительства, строительство может начать двигаться вперед к будущему, основанному исключительно на устойчивости.
Неустойчивое строительство негативно влияет на окружающую среду, однако переход от строительных материалов, таких как бетон и сталь, к экологически чистым строительным материалам, таким как дерево, в офисных и коммерческих зданиях продвигает строительную отрасль к более здоровому миру. В прошлом бетон и сталь привлекали внимание к самым инновационным строительным материалам.Во время промышленной революции и до сих пор большие серые здания были основой цивилизации и прогресса. Судя по показанным исследованиям, это уже не так. Эти льготы инициировали такие программы, как LEED и ATFS. Они являются отличной отправной точкой на пути к устойчивости. Они устанавливают основные правила и модель зеленого строительства и управления. LEED и ATFS являются важными ступенями, однако необходимо сделать больше сертификатов и получить более сильные награды. Зеленое строительство используется как символ современной инфраструктуры, но это не самый распространенный метод.При наличии большего количества стимулов статус-кво строительства может начать прогрессировать.
Список литературы
Aciu, C., & Mandea, D. (2014). Влияние выбора строительных материалов на окружающую среду в контексте устойчивого развития. Бюллетень Университета сельскохозяйственных наук и ветеринарной медицины Клуж-Напока . 71 (2), 125-132. DOI: 10.15835 / buasvmcn-agr: 10649
Бейер, Г. (2012). Древесина и изменение климата. Борьба с изменением климата .Получено с http://www.cei-bois.org/files/BuildWithWood.PDF
.ДиПесо, Дж. (2007). Энергия, окружающая среда и налоги. Управление качеством окружающей среды , 17 (1), 91-96. Получено с http://web.a.ebscohost.com/ehost/pdfviewer/pdfviewer?sid=4b8f0d44-3058-456a-a222-f3ef3d8d717f%40sessionmgr4005&vid=7&hid=4104
Эрлих, Б. (2011, ноябрь / декабрь). Многоликая мелиорированная древесина. Новости экологического строительства , 20 (11). Получено с https: // www2.buildinggreen.com/article/many-faces-reclaimed-wood
Хёйбо, О., Хансен, Э., и Нюбакк, Э. (2015). Предпочтения в строительных материалах с акцентом на
древесина в городском жилищном строительстве: долговечность и воздействие на окружающую среду. Канадский журнал
Forest Research , 45 (11), 1617-1627. DOI: 10.1139 / cjfr-2015-0123
Хамфрис, К. (2014, 6 июля). Будут ли города будущего построены из дерева? Бостон Глоуб. Получено с https://www.bostonglobe.com/ideas/ 2014/07/05 / will-cities-future-built-wood / 1iunF28vau8i0FQutgSv0L / story.html
Хуовила П., Ала-Джусела М., Мелхерт Л. и Пуффари С. (2009). Здания и изменение климата. Программа Организации Объединенных Наций по окружающей среде. Получено с http://www.unep.org/sbci/pdfs/SBCI-BCCSummary.pdf
Hsu, S.L. (2010, июнь). Оценка жизненного цикла материалов и конструкций в коммерческих структурах: изменчивость и ограничения. Массачусетский технологический институт. Получено с http://web.mit.edu/cron/project/concrete-sustainability-hub/Literature%20Review/Building%20Energy/Thesis/Libby%20Hsu%20Thesis.pdf
Ким Дж. И Ригдон Б. (1998). Качество, использование и примеры экологичных строительных материалов. Модуль устойчивой архитектуры , 10-43. Получено с http://www.umich.edu/~nppcpub/resources/compendia/ARCHpdfs/ARCHsbmIntro.pdf
(2016). LEED. Совет по экологическому строительству США. Получено с http://www.usgbc.org/leed
Мартин Э. и Шендель Э. (2014, 7 мая). Зарабатывает на жизнь продажей мелиорированной древесины. SW Новости . Получено с http: // www.swnews4u.com/archives/21450/
Росманиц, К. Дома и жилые дома. Английский онлайн . Получено с http://www.english-online.at/art-architecture/houses-and-homes/houses.htm
.Шамс, С., Махмуд, К., и Амин, М.А. (2011). Сравнительный анализ строительных материалов для устойчивого строительства с акцентом на снижение выбросов CO2. Международный журнал окружающей среды и устойчивого развития IJESD , 10 (4), 364-374. DOI: 10.1504 / ijesd.2011.047767
(2016).Стандарты сертификации. Стандарты устойчивости лесных хозяйств для сертификации лесов. Получено с https://www.treefarmsystem.org/certification-american-tree-farm-standard
Сталь, дерево и бетон: сравнение
ширина: 80%;}
]]>
Какие материалы чаще всего используются в строительстве?
Конструктивное проектирование зависит от знания материалов и соответствующих им свойств, чтобы мы могли лучше предсказать поведение различных материалов при нанесении на конструкцию.Как правило, три (3) наиболее часто используемых строительных материала — это сталь марки , бетон и древесина / древесина . Знание преимуществ и недостатков каждого материала важно для обеспечения безопасного и экономичного подхода к проектированию конструкций.
Конструкционная сталь
Сталь — это сплав, состоящий в основном из железа и углерода. Другие элементы также примешиваются к сплаву для получения других свойств. Одним из примеров является добавление хрома и никеля для создания нержавеющей стали.Увеличение содержания углерода в стали имеет предполагаемый эффект увеличения прочности материала на разрыв. Увеличение содержания углерода делает сталь более хрупкой, что нежелательно для конструкционной стали.
Преимущества конструкционной стали
- Сталь имеет высокое соотношение прочности и веса. Таким образом, собственный вес металлоконструкций относительно невелик. Это свойство делает сталь очень привлекательным конструкционным материалом для высотных зданий, длиннопролетных мостов, сооружений, расположенных на земле с низким содержанием грунта и в районах с высокой сейсмической активностью.
- Пластичность. Перед разрушением сталь может подвергаться значительной пластической деформации, что обеспечивает большой резерв прочности.
- Прогнозируемые свойства материала. Свойства стали можно предсказать с высокой степенью уверенности. На самом деле сталь демонстрирует упругие свойства до относительно высокого и обычно четко определенного уровня напряжения. В отличие от железобетона свойства стали существенно не меняются со временем.
- Скорость возведения. Стальные элементы просто устанавливаются на конструкцию, что сокращает время строительства.Обычно это приводит к более быстрой окупаемости в таких областях, как затраты на рабочую силу.
- Простота ремонта. Стальные конструкции в целом можно легко и быстро отремонтировать.
- Адаптация заводской сборки. Сталь отлично подходит для заводского изготовления и массового производства.
- Многократное использование. Сталь можно повторно использовать после разборки конструкции.
- Расширение существующих структур. Стальные здания можно легко расширить, добавив новые отсеки или флигели. Стальные мосты можно расширять.
- Усталостная прочность. Металлоконструкции обладают относительно хорошей усталостной прочностью.
Недостатки конструкционной стали
- Общие расходы. Сталь очень энергоемкая и, естественно, более дорогая в производстве. Стальные конструкции могут быть более дорогостоящими в строительстве, чем другие типы конструкций.
- Противопожарная защита. Прочность стали существенно снижается при нагревании до температур, обычно наблюдаемых при пожарах в зданиях. Сталь также довольно быстро проводит и передает тепло от горящей части здания.Следовательно, стальные конструкции в зданиях должны иметь соответствующую противопожарную защиту.
- Техническое обслуживание. Сталь, подвергающаяся воздействию окружающей среды, может повредить материал и даже загрязнить конструкцию из-за коррозии. Стальные конструкции, подверженные воздействию воздуха и воды, такие как мосты и башни, регулярно окрашиваются. Применение устойчивых к атмосферным воздействиям и коррозионно-стойких сталей может устранить эту проблему.
- Склонность к короблению. Из-за высокого отношения прочности к весу стальные сжимающие элементы, как правило, более тонкие и, следовательно, более подвержены короблению, чем, скажем, железобетонные сжимающие элементы.В результате требуется больше конструктивных решений для улучшения сопротивления продольному изгибу тонких стальных компрессионных элементов.
Программное обеспечение SkyCiv Steel Design
Рис. 1. Обзор стальных конструкций
Железобетон
Бетон представляет собой смесь воды, цемента и заполнителей. Пропорция трех основных компонентов важна для создания бетонной смеси желаемой прочности на сжатие. Когда в бетон добавляют арматурные стальные стержни, эти два материала работают вместе с бетоном, обеспечивающим прочность на сжатие, и сталью, обеспечивающей прочность на растяжение.
Преимущества железобетона
- Прочность на сжатие. Железобетон имеет высокую прочность на сжатие по сравнению с другими строительными материалами.
- Прочность на разрыв. Благодаря предусмотренной арматуре железобетон также может выдерживать значительную величину растягивающего напряжения.
- Огнестойкость. Бетон обладает хорошей способностью защищать арматурные стальные стержни от огня в течение длительного времени. Это выиграет время для арматурных стержней до тех пор, пока пожар не будет потушен.
- Материалы местного производства. Большинство материалов, необходимых для производства бетона, можно легко найти на месте, что делает бетон популярным и экономичным выбором.
- Прочность. Система здания из железобетона более долговечна, чем любая другая система здания.
- Формуемость. Железобетон, изначально как текучий материал, можно экономично формовать в практически неограниченном диапазоне форм.
- Низкие эксплуатационные расходы. Железобетон является прочным, с использованием недорогих материалов, таких как песок и вода, которые не требуют обширного обслуживания.Бетон предназначен для того, чтобы полностью покрыть арматурный стержень, так что арматурный стержень не будет нарушен. Это делает стоимость обслуживания железобетонных конструкций очень низкой.
- В конструкции, такой как фундаменты, плотины, опоры и т. Д., Железобетон является наиболее экономичным строительным материалом.
- Жесткость. Он действует как жесткий элемент с минимальным прогибом. Минимальный прогиб хорош для удобства эксплуатации зданий.
- Удобство в использовании. По сравнению с использованием стали в конструкции, при строительстве железобетонных конструкций может быть задействована менее квалифицированная рабочая сила.
Недостатки железобетона
- Долгосрочное хранение. Бетон нельзя хранить после смешивания, так как цемент вступает в реакцию с водой и смесь затвердевает. Его основные ингредиенты нужно хранить отдельно.
- Время отверждения. Бетон выдерживает тридцать дней. Этот фактор сильно влияет на график строительства здания. Это снижает скорость возведения монолитного бетона по сравнению со сталью, однако ее можно значительно улучшить с помощью сборного железобетона.
- Стоимость форм. Стоимость форм, используемых для отливки ЖБИ, относительно выше.
- Поперечное сечение большее. Для многоэтажного здания секция железобетонной колонны (RCC) больше, чем стальная секция, так как в случае RCC прочность на сжатие ниже.
- Усадка. Усадка вызывает развитие трещин и потерю прочности.
Программное обеспечение SkyCiv RC для проектирования
Рис. 2. Типичный пример железобетона
Древесина
Древесина — это органический, гигроскопичный и анизотропный материал.Его тепловые, акустические, электрические, механические, эстетические, рабочие и т. Д. Свойства очень подходят для использования, можно построить комфортный дом, используя только деревянные изделия. С другими материалами это практически невозможно. Очевидно, что дерево — это и распространенный, и исторический выбор в качестве конструкционного инженерного материала. Однако в последние несколько десятилетий произошел отход от дерева в пользу инженерных продуктов или металлов, таких как алюминий.
Преимущества древесины
- Прочность на разрыв.Поскольку дерево является относительно легким строительным материалом, он превосходит даже сталь по длине разрыва (или длине самонесущей конструкции). Проще говоря, он может лучше выдерживать собственный вес, что позволяет использовать большие пространства и меньше необходимых опор в некоторых конструкциях зданий.
- Электрическое и тепловое сопротивление. Он обладает естественным сопротивлением электропроводности при сушке до стандартного уровня содержания влаги (MC), обычно от 7% до 12% для большинства пород древесины. Его прочность и размеры также не подвержены значительному влиянию тепла, обеспечивая устойчивость готового здания и даже безопасность при определенных пожарных ситуациях.
- Звукопоглощение. Его акустические свойства делают его идеальным для минимизации эха в жилых или офисных помещениях. Дерево поглощает звук, а не отражает или усиливает его, и может помочь значительно снизить уровень шума для дополнительного комфорта.
- Из местных источников. Дерево — это строительный материал, который можно выращивать и повторно выращивать с помощью естественных процессов, а также с помощью программ пересадки и лесного хозяйства. Выборочная уборка и другие методы позволяют продолжить рост, пока собираются более крупные деревья.
- Экологически чистый. Одна из самых больших проблем многих строительных материалов, включая бетон, металл и пластик, заключается в том, что когда они выбрасываются, они разлагаются невероятно долго. В естественных климатических условиях древесина разрушается намного быстрее и фактически пополняет почву.
Недостатки бруса
Усадка и разбухание древесины — один из ее основных недостатков.
Дерево — гигроскопичный материал.Это означает, что он будет поглощать окружающие конденсируемые пары и терять влагу в воздух ниже точки насыщения волокна. Еще один недостаток — его износ. Агенты, вызывающие порчу и разрушение древесины, делятся на две категории: биотические (биологические) и абиотические (небиологические). Биотические агенты включают гниющие и плесневые грибы, бактерии и насекомые. К абиотическим агентам относятся солнце, ветер, вода, некоторые химические вещества и огонь.
Программное обеспечение SkyCiv Wood Design
Рисунок 3.Деревянный конструкционный каркас
Сводка
Для лучшего описания стали, бетона и дерева. Обобщим их основные характеристики, чтобы выделить каждый материал.
Сталь очень прочна как на растяжение, так и на сжатие и, следовательно, имеет высокую прочность на сжатие и растяжение. Сталь имеет предел прочности от 400 до 500 МПа (58 — 72,5 ksi). Это также пластичный материал, который поддается или прогибается перед разрушением. Сталь выделяется своей скоростью и эффективностью в строительстве.Его сравнительно легкий вес и простота конструкции позволяют сократить рабочую силу примерно на 10-20% по сравнению с аналогичной строящейся структурой на бетонной основе. Металлоконструкции также обладают отличной прочностью.
Бетон чрезвычайно прочен на сжатие и, следовательно, имеет высокую прочность на сжатие от 17 МПа до 28 МПа. С более высокой прочностью до 70 МПа или выше. Бетон позволяет проектировать очень прочные и долговечные здания, а использование его тепловой массы, удерживая его внутри оболочки здания, может помочь регулировать внутреннюю температуру.Также в строительстве все чаще используется сборный железобетон, что дает преимущества с точки зрения воздействия на окружающую среду, стоимости и скорости строительства.
Древесина устойчива к электрическим токам, что делает ее оптимальным материалом для электроизоляции. Прочность на разрыв также является одной из основных причин выбора древесины в качестве строительного материала; его исключительно сильные качества делают его идеальным выбором для тяжелых строительных материалов, таких как конструкционные балки.Дерево намного легче по объему, чем бетон и сталь, с ним легко работать, и его легко адаптировать на стройплощадке. Он прочен, дает меньше тепловых мостиков, чем его аналоги, и легко включает в себя готовые элементы. Его структурные характеристики очень высоки, а его прочность на сжатие аналогична прочности бетона. Несмотря на все это, древесина все шире используется для жилых и малоэтажных построек. Его редко используют в качестве основного материала для высотных конструкций.
Это самые распространенные строительные материалы, используемые для строительства.У каждого материала есть свой уникальный набор достоинств и недостатков. В конце концов, они могут быть заменены материалами, которые практически не имеют ограничений с технологическими достижениями будущего. Тем не менее, наши нынешние строительные материалы будут оставаться актуальными еще многие десятилетия.
.