Производство газосиликатных блоков
Технология производства
Оборудование для производства стройматериалов сегодня играет важную роль, ведь от него зависит качество, надежность и долговечность сооружений. Рассмотрим полный цикл по производству газосиликатных блоков на заводе в Московской области.
Производство газосиликатных блоков основано на добавлении газообразователя в специально подготовленную смесь из молотого кварцевого песка, извести, небольшой части цемента. При взаимодействии газообразователя с известью структура смеси становится пористой. Процесс перемешивания происходит в смесеприготовительном цехе завода в специальных газобетоносмесителях.
Далее смесь поступает в формовочно-резательный цех, где происходит её заливка в формы и вспучивание. После вспучивания смеси она выдерживается на постах для того, чтобы материал приобрёл пластическую прочность сырца (0,15 – 0,04 МПа). Затем газосиликатные блоки производство переходит на резательный комплекс, где массивы разрезаются в поперечном и продольном направлениях.
Разрезанные массивы отправляются на пост комплектации, где они устанавливаются на специальные тележки и поступают в автоклав. После погрузки происходит тепловлажностная обработка материала, которая является заключительным этапом изготовления.
Область применения
Этот материал в основном применяется в малоэтажном строительстве. Газосиликатные блоки используются при возведении внутренних и наружных стен домов и подвалов, различных перегородок, при заполнении каркасных строительных конструкций. Поэтому оборудование для изготовления газобетона сильно востребовано на сегодняшний день.
Преимущества
Высокотехнологичное производство газосиликатных блоков обеспечивает строительный материал некоторыми преимуществами. Он хорошо поглощает звук и не горит. Кроме данных характеристик стройматериал имеет высокую прочность, показательную геометрию (т.е. линейные размеры стабильны не только конкретно в одной партии, но и в типоразмере всей продукции), низкие вес и теплопроводность.
Идентичные друг другу геометрические параметры блоков упрощают процесс кладки материала на клеевой состав при строительстве различных объектов. Их не нужно будет подгонять друг к другу. За счёт ровной поверхности газосиликатных блоков можно существенно экономить на строительных материалах. Помимо прочего, они просты в обработке (легко режутся, пилятся, строгаются, сверлятся).
Также этот материал не требует особого ухода. В экологическом плане он уступает дереву, но в отличие от него не гниёт и не горит.
Купить оборудование для производства блоков уже сегодня? С компанией МЕТЕМ это реально. А на все интересующие вас вопросы о цене наши специалисты подробно ответят вам по телефону.
Технические характеристики
- Масса – 400-600 кг/м3
- Показатель прочности – 10-50 кг/см3
- Теплопроводность – 0,12-0,14 Вт/м°C
- Морозостойкость – 25-35 циклов
Производство газосиликатных блоков — способы и технологии (видео)
Этот ячеистый строительный материал сегодня используется в разных сферах строительства. А производство газосиликатных блоков может стать прибыльным бизнесом.
Популярность газосиликата объясняется просто:
- материал считается экологически чистым;
- низкий вес газосиликата значительно снижает затраты на обустройство фундамента здания;
- четкая геометрия газосиликатных блоков обеспечивает простой и быстрый монтаж;
- для соединения блоков можно использовать клей, а не цемент;
- более низкая, по сравнению с кирпичом и ячеистым бетоном, цена;
- негорючесть;
- высокие тепло- и звукоизоляционные характеристики;при толщине стены в 50 сантиметров необходимость делать наружное утепление отпадает;
- легкость отделки;
- стойкость к гниению;
- простота обработки.
Можно нередко встретить сравнение газосиликата с пенобетоном. Однако, обладая одинаковой прочностью, эти материалы отличаются плотностью и теплопроводностью: у газосиликата они ниже. Если же плотность и теплопроводность равны, то блоки из газосиликата более прочные.
Все это способствует росту спроса на этот материал, соответственно, делает производство газосиликата выгодным бизнесом.
Патент на изобретение
Технология была изобретена в начале двадцатого века. А примерно в 1920 году была усовершенствована шведским архитектором Эрикссоном, который в 1924-ом получил патент международного образца на автоклавный способ производства газосиликата. Метод быстро стал популярным в Швеции, откуда распространился по другим странам.
Организация производства газосиликатных блоков, безусловно, требует определенных знаний и наличия начального капитала. Однако при грамотном подходе, как утверждают специалисты, вложения окупаются достаточно быстро.
Главное условие успеха — технология производства газосиликатных блоков должна соблюдаться досконально. Только тогда конечный продукт будет обладать заявленными характеристиками.
Также предлагаем ознакомится со статьёй, в которой мы сравним такие материалы как газобетон и пенобетон.
Работа под давлением
На первом этапе производственного цикла исходное сырье необходимо очистить от крупных включений и мусора. Это делают с помощью специального сита. Все ингредиенты — цемент, негашеная известь, кварцевый песок, газообразующая добавка (алюминиевая пудра) и вода, перемешиваются в бетоносмесителе.
Готовый состав заливается в специальные формы, которые затем проходят термическую обработку в автоклаве. Высокая температура (200˚С) и давление (10 — 12 атмосфер) провоцируют химические реакции, в результате которых выделяется газ – в материале образуются поры.
Закончив «выпекание», блоки на некоторое время оставляют в автоклаве. Это необходимо, чтобы конечный продукт набрал нужную прочность и хорошенько просох.
Точная геометрия
Затем материал разрезают на одинаковые блоки. Отходы, которые при этом получаются, можно снова пустить в работу, добавив к смесит для новой партии. Получается практически безотходная технология.
Поскольку газосиликат – материал пластичный, очень легко режется (можно резать даже болгаркой или станком для резки камня) и обрабатывается, можно делать блоки разных размеров и конфигурации. Стандартные для России габариты — 60 х 30 х 20 сантиметров. В ширину блоки могут быть от десяти до пятидесяти сантиметров. В высоту – от двадцати до тридцати.
Выгодный бизнес
Технология достаточно проста, и это становится причиной, по которой множество людей решаются организовать производство газосиликатных блоков. Видео, размещенное в интернете, позволяет подробно познакомиться с процессом и узнать о различных тонкостях изготовления этого материала. По большому счету, наладить производство газосиликата можно даже в собственном гараже или подсобном помещении на даче.
Однако без специального оборудования обойтись не удастся.
Специальное оборудование
При изготовлении газосиликата используются специальные станки – установки для производства блоков. Сейчас в продаже есть оборудование разных габаритов, в том числе – довольно компактное, для размещения которого не требуется много места. С их помощью можно работать на рынке мелкого опта. Но при желании брать крупные заказы понадобится приобрести более производительную технику.
Внутри и снаружи
Сегодня выпускается несколько видов газосиликатных блоков, которые отличаются разной плотностью материала.
Конструкционно-изоляционный газосиликат имеет плотность 500-900 кг/куб.м. Теплоизолирующий — 350-400 кг/куб.м. При плотности более 700 кг/куб.м этот строительный материал может использоваться при возведении многоэтажных зданий.
Из газосиликатных блоков делают стены внутри строений и наружные. Есть разновидности блоков, предназначенные специально для устройства проемов окон и дверей.
Газосиликатные блоки можно назвать универсальным строительным материалом, легким и теплым. Однако у него есть свои особенности: например, он очень быстро впитывается влагу, и характеризуется высокой способностью водопоглощения. Поэтому строить из него здания в слишком влажном климате, где влажность составляет более шестидесяти процентов, не целесообразно.
Рекомендуем к прочтению — характеристики пенобетонных блоков.
Производство газосиликатных блоков: технология, оборудование (станок)
Для тех, кто ищет способ создать бизнес на дому, производство газосиликатных блоков станет выгодным решением. Сегодня вы познакомитесь с особенностями изготовления газосиликата и узнаете, как открыть такой бизнес.
Коды ОКВЭД, требуемые при регистрации ИП по данному виду деятельности: 26.61: Производство изделий из бетона для использования в строительстве; 26.66: Производство прочих изделий из бетона, гипса и цемента; 51.53: Оптовая торговля лесоматериалами, строительными материалами и санитарно-техническим оборудованием.
Содержание статьи:
Технические характеристики материала
Газосиликатные блоки – высококачественный строительный материал.
Они отличаются низкой себестоимостью, экологически чистым производством и небольшим весом. Эти качества позволили материалу получить широкую популярность в строительной промышленности.
Блоки имеют высокую прочность, а благодаря ячеистой структуре, газосиликат может обладать плотностью от 300кг/м³ до 700кг/м³, равномерно распределенной по всему блоку, что так же увеличивает популярность этого товара среди строительных компаний.
Требования к производственному помещению
Помещение, отведенное под производство газосиликатных блоков своими руками, должно отвечать некоторым требованиям. Для хранения сырья и готовой продукции, понадобится специально отведенное место. Высота помещения должна составлять не менее трех метров.
Так же, тех. процесс предусматривает наличие электросетей напряжением 380В и 220В, водопровода и подъездных путей. Само помещение должно быть утепленным и очищенным от грязи и мусора.
Производство газосиликата считается безотходным, поэтому в канализации на территории мини-завода нет необходимости.
Оборудование для производства газосиликатных блоков
Чтобы организовать мини-завод в гараже или небольшом арендованном помещении, вам понадобятся следующие станки для производства газосиликатных блоков:
- Вибросито
- Автоклав промышленный;
- Формы для блоков;
- Шаровая мельница;
- Бункер-дозатор;
- Бетоносмеситель.
Цена оборудования
Где и по какой цене можно купить хорошее оборудование для производства газосиликата? Остановимся на этом вопросе поподробнее:
- Вибросито для просеивания песка. Подойдут недорогие варианты, занимающие мало места, такие как: вибросито ВО-1, производства Авер-Иркутск, мощностью 0,25 кВт – 320$, вибросито ВО-01, ООО «Строительное оборудование» — 370 долл., вибростол ВС-250, Строймашсервис-Дон – 575$, вариант без вибратора, Стройтехнополис – 125 долларов, машина от Элси-строй – 520$, ВИБРОМАШ ВО-1, Дельта-инжиниринг – 450 долларов;
- Шаровая мельница.
Уралмаш МШЦ-210*3000 – 1740 долларов, Уралмаш МСЦ-3600*4500 – 1740$, мельница шаровая МШМП-0.8 – до 5750 долл., мельница от ЗАО Паритет сухого помола – 3710 долларов; ЗАО Паритет мокрого помола – 3310$;
- Дозаторы. Бункер — дозатор БД-30 от Златоустовского завода бетоносмесительного оборудования – 5750 долл., Бункер дозатор для бетоносмесителя от НПО КСК – 1130 долларов;
- Бетоносмеситель. Варианты от компаний: Комплект-ЮГ – 90$, Б 130 «Энтузиаст» — 180 долл., Афалина Челябинск – 225 долларов, TOR 46л. От Торгового дома ТОР – 125$;
- Формы. Металлические кассетные формы для ячеистого бетона из Красноярска, компания ГК ТСК – 185 долларов, Металлическая кассетная форма Строй механика Киров – 315$, форма «Стандарт-1», на 36 блоков – 350$;
- Автоклав. Машина производства «УралЦентрКомплект» Аг-1200 тз – 43 550$, автоклав проходной АП 1,2 – 2*17, производства «Стройкомплекс Брик» — 26 135 долларов.
Чтобы купить качественный станок для производства газосиликатных блоков, придется тщательно выбирать подходящий именно вам вариант и сопоставлять их мощность и производительность.
Для сравнения цен и технических характеристик производственных машин, рекомендуется изучить и зарубежный рынок.
Особое внимание советуем обратить на технику из Китая. Такое оборудование для производства газосиликата отличает широкий ассортимент и доступная цена.
Технология производства газосиликатных блоков
Для производства, помимо оборудования, вам понадобится знание технологии изготовления и пропорции сырья.
Процесс производства газосиликатных блоков
Процесс довольно прост в исполнении. При соблюдении пропорций и правильном выполнении технологии, будет получен качественный продукт.
- С помощью вибросита отделить сыпучий материал от лишних фрагментов;
- Измельчить сырьё для производства газосиликатных блоков в шаровой мельнице;
- Соблюдая пропорции, смешать все сыпучие составляющие, кроме алюминиевой суспензии;
- Произвести повторное просеивание;
- Добавить алюминиевую пудру и воду, тщательно перемешать;
- Наполнить формы смесью на ½ от общего объема каждой из них;
- Оставить формы с массой при температуре не менее 40° на 2 часа;
- Обработать блоки с помощью автоклава;
- Оставить на 3 часа для завершения химических процессов и набора прочности.
Если вы хотите производить гозобетонные блоки в соответствии с межгосударственными стандартами, то ознакомьтесь с положениями ГОСТ 31360-2007, 21520-89, 25485–89, 31359, где описаны требования к стеновым неармированным изделиям из ячеистого бетона автоклавного твердения.
В продаже можно найти различные размеры газосиликатных блоков, но согласно ГОСТу 31360, размер каждого блока должен соответствовать следующим нормам: длинна – 625мм, ширина – 500 мм, высота – 500мм.
Пропорции ингредиентов для изготовления смеси
Рассмотрим, из чего делают газосиликатные блоки. Для производства 1 куб.м газосиликатной смеси понадобятся ингредиенты в следующих пропорциях: вода – около 450л., цемент – 60кг (от 8% до 10%), кварцевый песок – 450 кг (до 70%), гипс – 0,5 кг (до 2%), известь – 120 кг (процент извести вот 12% до 20%), а так же алюминиевая пудра – 0,5 кг (до 2%).
Чтобы достичь наибольшего показателя плотности материала, доля пор должна составлять не более 38%, такой строительный блок подходит для капитального строительства.
При среднем показателе плотности, газосиликат представляет собой материал, с долей пор не более 52%.
Наибольшая допустимая пористость легкого ячеистого материала составит до 92%. В последнем случае, применение газосиликатных блоков допустимо только для теплоизоляции.
Производство газосиликатных блоков в домашних условиях
Такое производство возможно, при наличии помещения, отвечающего соответствующим требованиям.
Блоки, изготовленные в домашних условиях, уступают по качеству товару, выпущенному на производственной линии.
Прежде всего, это обусловлено техническими характеристиками используемой техники. Но следует заметить, что газосиликат, произведенный небольшим частным заводом, пользуется не меньшим спросом, чем заводской, благодаря доступной цене и небольшой разнице в качестве строительного материала.
Подсчет рентабельности
Подсчитаем сроки окупаемости и прибыльность небольшого домашнего завода по производству газосиликатных строительных блоков.
Инвестиции
Вибросито – 450 долларов;
Шаровая мельница – 5 750$;
Бункер-дозатор для бетоносмесителя – 1 130 долл.;
Бетоносмеситель – 225 долларов;
Формы – 350$;
Автоклав – 26 135 долларов.
Итого: 34 040 долл.
Затраты на 1 кубометр сырья
Вода – 450л. – 0,6$;
Цемент – 60кг – 2,5 долл.;
Кварцевый песок – 450кг – 7,8 долларов;
Гипс – 0,5кг – 0,1$;
Известь – 120кг — 6,2 долл.;
Алюминиевая пудра – 0,5кг – 0,1$.
Итого: 17,3 долларов/1 куб. м.
Объем производства на нашем мини-заводе составит 1500 куб. м. в месяц, продажная цена 1м³ — 45$. При полной реализации, ежемесячный доход составит 67 500 долларов. Чистая прибыль – 24 250$ в месяц. С учетом сопровождающих изготовление и реализацию товара факторов, вложения в небольшой частный завод окупятся за 3 месяца работы.
Подведем итоги. Анализируя объем прибыли и срок окупаемости инвестиций, можно сказать, что газосиликатные блоки как бизнес, являются доходным предприятием с высоким коэффициентом рентабельности.
Понравилась статья? Поделитесь с друзьями:
Производство газосиликатных блоков: оборудование, цены
Все большую популярность в качестве строительного материала в наши дни набирают газосиликатные блоки. Выбор в их пользу делают как частные лица, так и строительные компании. Основными причинами такого необыкновенного спроса являются надежность этого материала и экономическая выгода, обусловленная крайне низкой ценой на газосиликатные блоки и, весьма небольшими затратами при его использовании для строительства зданий. Кроме этого, они позволяют быстро и качественно организовать строительство дома из газосиликатных блоков своими руками.
Стоит отметить, что для разных случаев применения используются различные виды силикатных блоков:
- В качестве утеплителя используются блоки, плотность которых составляет 350 кг/м.
- Для строительства домов с тремя и менее этажами применяются блоки плотностью 400 кг/м.
- Выше трех этажей – 500 кг/м.
- Высокоэтажные сооружения строятся из блоков, плотность которых составляет 700 кг/м.
Фото: дом из газосиликатных блоков
Процесс изготовления блоков в заводских условиях
Газосиликатные блоки изготавливают в заводских условиях. Самые крупные и известные компании, выпускающие эти изделия, применяют самое совершенное оборудование для производства газосиликатных блоков, произведенное в Германии. Данные линии способны контролировать каждую стадию процесса изготовления блоков, начиная с самых первых этапов и заканчивая проверкой теплоизоляционных свойств готового изделия.
Что касается технологии, то здесь используются известь, вода, цемент и кварцевый песок, смешанные в строго определенных пропорциях. Кроме этого, для создания пористой структуры в смесь добавляется алюминиевая пудра, которая является образователем газа. Во время перемешивания происходит химическая реакция, приводящая к вспениванию смеси. Технологичная аппаратура способна даже регулировать диаметр этих пузырьков для получения пор нужного размера.
Производство газосиликатных блоков полностью автоматизировано, позволяет получать изделия максимально высокого качества с минимальным количеством брака.
Весь процесс изготовления газосиликатных блоков состоит из ряда последовательных этапов, для каждого из которых используется свое оборудование.
Система измельчения и дробления сыпучих материалов
В данной системе используется больше всего различного оборудования:
- Бункер для песка.
- Элеватор.
- Бункер для хранения извести.
- Хранилище для извести.
- Шаровая мельница.
- Электронные приборы для взвешивания порошка.
- Ленточный конвейер.
- Автоматический смеситель.
- Дробилка.
На данном этапе происходит перемешивание песка и воды до состояния жидкой смеси. Полученное вещество направляется в смесительное отделение. Там в него добавляются и остальные компоненты смеси в строго определенной пропорции и последовательности. После тщательного перемешивания добавляется алюминиевая суспензия и снова происходит перемешивание, которое контролируется электронными системами.
Заливка и дозирование
В этой системе используется следующее оборудование:
- Заливочная платформа.
- Система газораспределения.
- Заливочный смеситель.
Здесь происходит заливка смеси в формы и транспортировка в зону созревания. В течение нескольких часов происходит бурная реакция с выделением водорода и появляется необходимая пористая структура.
Резка и группировка
Используются:
- Захват для переворачивания.
- Машина для резки.
Полученный массив газосиликата разрезается с получением системы гребень-паз. Применяемое оборудование позволяет производить нарезку практически с ювелирной точностью. Самое интересное, что полученные после нарезки отходы можно отправлять на переработку и использовать в получении новой смеси. Это делает производство газосиликатов безотходным.
Набор прочности в автоклаве
Оборудование:
- Паровой котел.
- Рельсы.
- Автоклав.
В автоклаве нарезанные блоки набирают прочность путем постепенного выпаривания при высоком давлении. После этого давление уменьшается и блоки выезжают с платформы.
Упаковка
Используется следующее оборудование:
- Кран.
- Колодки.
- Приборы, замеряющие точность нарезки.
- Упаковочная линия.
С помощью крана происходит захват ряда блоков и выкладывание для дальнейшего остывания. Затем на автоматической линии происходит упаковка блоков. Одновременно с упаковкой происходит выписка документов, содержащих всю необходимую информацию об изделии.
В качестве примера можно сказать, что цена линии для изготовления газосиликатных блоков, производительностью 300 тыс.
м3/год составляет примерно 900 тысяч долларов.
Конечно, можно изготавливать блоки и на более простом оборудовании, которое стоит дешевле, но и себестоимость такого производства будет значительно выше, что в некоторых случая попросту нецелесообразно.
Видео
Производство газосиликатных блоков как идея бизнеса
Изготовление и продажа
Газосиликатные блоки – популярный и востребованный строительный материал, по теплопроводности, шумоизоляционным характеристикам, экологичности они занимают второе место, уступая только натуральной древесине.
Кроме того ГСБ обладают легким весом, хорошими водоотталкивающими и противопожарными показателями, высокой прочностью (выдерживают нагрузки от 10 до 40 кг на кв.см.), при этом имеют легкий вес.
Сфера применения в строительстве – в кладке стен, в качестве изоляционного материала, как утеплитель.
На изготовлении газосиликатных блоков можно построить прибыльный бизнес, процесс производства достаточно прост, спрос на конечный продукт очень высок, по соотношению «цена-качество» — это идеальный материал, в приобретении которого заинтересованы многие строительные организации.
Инвестиции в реализацию бизнес-идеи — средние и составляют порядка 125-130 тысяч долларов. А вот срок окупаемости бизнес-проекта очень привлекательный – 3-4 месяца при грамотно налаженном сбыте и хорошей маркетинговой компании.
Производственный процесс
Изготовление газосиликатных блоков (ГСБ) включает 6 основных этапов:
- закупку и подготовку сырья – отделение нужных пропорций, просушка, просеивание на виброситах;
- смешивание компонентов в специальных смесителях – добавление к сыпучим веществам воды;
- формовку – на данном этапе происходят химические реакции, как следствие, выделение газов, в результате чего весь раствор вспенивается, его масса увеличивается, после чего полученная пористая основа застывает;
- остужение, изъятие из форм, порезку на куски нужных размеров;
- термообработку в автоклавах;
- упаковку готовых блоков.
Фотоэкскурсия на завод по производству газосиликатных блоков
Производство можно считать практически безотходным, так как обрезки, крошка и неиспользованные мелкие куски отправляются на вторичную переработку для изготовления новой партии блоков.
Помещение
Аренда помещения, пожалуй, самая существенная статья расходов в данном виде деятельности. Связано это с тем, что подпроизводство потребуется около 1 000 кв.м.
Площадь делится на технологические зоны (смесеприготовительную, формовочную, цех порезки, упаковочную), выделяются помещения под склад для материалов и готовой продукции.
Оборудование для производства блоков
Перечень основных узлов для производства газосиликатных блоков и их стоимость приведены ниже:
- Вибросито – 780-800 долларов;
- Смеситель для растворов – 1600 у.е.;
- Мельница шаровая – от 21 000$;
- Автоклав – 950 у.е.;
- Блочные формы – 1500$ за штуку;
- Дозаторы автоматические – 1000$;
- Станок фрезерный – от 2000$;
- Парогенератор для влагообработки блоков – 15000$;
- Дополнительное оборудование – емкости, пилы, ножи, погрузчик.
Видео производство газосиликатных блоков
Сырье и материалы
Газосиликатные блоки состоят из таких «ингредиентов», выдержанных в определенных пропорциях: кварцевого песка (ценаза тонну — 30 долларов), цемента ( 90-100 $ за 1 т.), воды, извести, гипса (90 у.е. за 1000 кг), алюминиевой пудры (200 дол./кг).
Персонал
Для обслуживания технологической линии потребуется 4 сотрудника на смену – бригадир и трое неквалифицированных рабочих.
Помимо зарплаты этих специалистов, к текущим статьям затрат стоит отнести оплату коммунальных услуг – водоснабжения и электроэнергии.
Себестоимость
Себестоимость изготовления одного кубометра газосиликатных блоков составляет в среднем 65$, цена реализации такого же объема — от 88$ оптом и до 100-120 у.е. в розницу.
Просмотров: 639
Заводское производство газосиликатных блоков Бонолит.
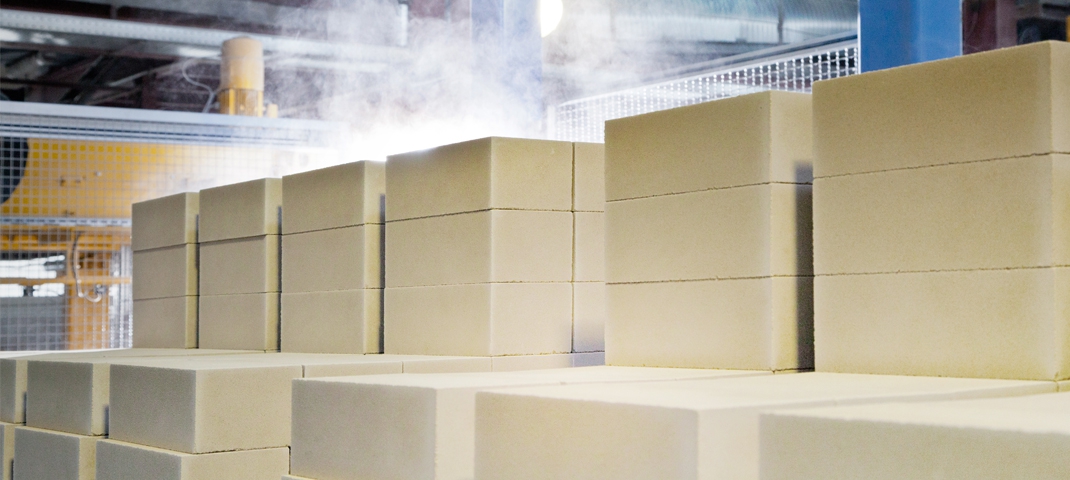
Газобетонные блоки Бонолит – уникальный строительный материал из ячеистого бетона, который объединяет в себе все необходимые для возведения современных зданий свойства и характеристики. Газобетонные блоки Бонолит идеальны для создания стен любой формы, арок, колон и различных архитектурных решений.
Предприятие запустило производство газобетонных блоков Бонолит летом 2011 года. Завод Бонолит расположен не в далеке от МКАД по направлению Горьковского шоссе в городе Старая Купавна. Завод сертифицирован в соответствии с европейской программой управления выпуском продукции и качеством. Производство оснащено одной из наиболее производительных технологических линий, разработанных в Германии – HESS AAC Systems B.V. Завод изготавливает газобетонные блоки Бонолит :пазогребневые газобетонные блоки , обычные ровные блоки, U-блоки, плотность которых : D400, D500, D600
Газобетонные блоки, сходящие с заводских линий, имеют ровную геометрию ( с отклонением не более 1 мм), а также уникально высокие показатели морозостойкости (F50) и, теплоизоляции. Помимо высоких теплоизоляционных свойств, газобетонные блоки Бонолит обладают высокими характеристиками по звукоизоляции в сравнении с гипсовыми перегородками, деревом, кирпичом и бетоном. Поэтому газосиликатные блоки толщиной 100-200 мм являются самым лучшим современным материалом для строительства внутренних перегородок. А морозостойкость F50 и F100 гарантирует полное сохранение свойств газобетонных блоков Бонолит при 50 и 100 циклах полного замораживания.
Купить газобетоные блоки во Владимире на сегодняшний день можно у официальных представителей завода Бонолит компании Боносторой. Цена на газобетонные блоки зависит от плотности, геометрических размеров и партии поставки. С наступлением строительного сезона, цена на газосиликатные блоки возрастает, поэтому лучше это сделать заранее. Доставка газобетонных блоков Бонолит осуществляется автотранспортом на поддонах размером 1200х1000х1600 мм. Загрузка поддона – 1,8 м³ блоков. В машину входит 32,4м3 газобетонных блоков Бонолит.
Свои вопросы по материалу, техническим, физическим характеристикам, по технологии строительства Вы можете задать по телефону : 8-4922-60-11-89-представителям завода Бонолит компании Бонострой в городе Владимире, и получить квалифицированный ответ консультантов.
Как сделать газосиликатные блоки в домашних условиях
Постройка собственного дома требует вливания значительных денежных средств, поэтому большинство строительных материалов люди научились делать самостоятельно. В нашей статье мы поговорим об изготовлении газосиликатных блоков в домашних условиях.
Перед началом производства, следует ознакомиться с основными нюансами этого дела. Важным моментом считается соблюдения последовательности процессов, так как базовый состав материала может разниться. Основными вариантами сырья считается цемент с кварцевым песком или портландцемент в сочетании с древесной золой. В качестве порообразователя выступает алюминиевый порошок, а вода позволяет связывать все компоненты смеси.
В промышленных условиях газосиликатные блоки проходят автоклавную обработку (под воздействием высокого давления и температуры), но дома проводить рассматриваемые процессы не предоставляется возможным, поэтому технология производства немного меняется. В любом случае нужно соблюдать такую пропорцию сырьевых компонентов, при которой получатся блоки максимальной прочности.
На данный момент известно множество способов резки газобетона, но при самостоятельном производстве смесь рекомендовано заливать в специальную форму, предварительно смазанную маслом. Чтобы упрочнить изделие, в ёмкость можно уложить металлическую проволоку диаметром не более 6-ти миллиметров.
Материалы для изготовления газосиликатных блоков
Перед изготовлением газосиликатных блоков, необходимо подготовить следующие компоненты и материалы. Для пробного замеса потребуются:
- 2 килограмма цемента марки 500;
- 1,4 литра горячей воды;
- ёмкость для смешивания и готовых материалов;
- 2 килограмма просеянного кварцевого песка;
- 20 грамм соли;
- 3 грамма алюминиевого порошка;
- 20 миллилитров пластификатора;
- средства защиты.
Процесс производства газосиликата
Для начала необходимо подготовить газообразующую смесь. С этой целью в небольшой ёмкости перемешивают стиральный и алюминиевый порошок с небольшим количеством воды. Размешивают компоненты на протяжении 3 минут, в результате реакций может подняться столб пыли, поэтому ингредиенты нужно перемешивать в средствах защиты: перчатках, респираторе и очках.
Пока наша суспензия будет настаиваться в ёмкости, можно приготовить основной раствор. Для этого песок вместе с цементом засыпают в форму и тщательно перемешивают до однородной консистенции. Операция проводится при помощи дрели со специальной насадкой. В дальнейшем в сухую смесь добавляют пластификатор, соль и 1,2 литра воды. После недолгого перемешивания, на протяжении 20-25 секунд раствор оставляют для пропитывания жидкостью, затем добавляют суспензию и остатки воды, перемешивают до появления на поверхности серебристой плёнки.
Следует заметить, что форма заполняется смесью лишь наполовину, остальной объём газосиликатного блока добавится самостоятельно.
Силикат кальция — обзор
15.5 Гидравлические цементы
Портландцемент — это гидравлический цемент, получаемый путем измельчения клинкера, состоящий в основном из гидравлических силикатов кальция с сульфатом кальция (гипсом) в качестве добавки в грунт. Клинкер получают путем нагревания глинистых материалов с известью при высоких температурах (> 1500 ° C) с образованием конкреций (диаметром 5–25 мм). Низкая стоимость и широкая доступность известняка и природных источников кремнезема делают портландцемент одним из самых дешевых материалов, используемых во всем мире.Производство и состав портландцементов, процессы гидратации, а также химические и физические свойства цемента были тщательно изучены.
Портландцемент состоит в основном из извести (60–65 мас.% CaO), кремнезема (21–24 мас.% SiO 2 ), глинозема (3–8 мас.% Al 2 O 3 ) и оксид железа (3–8 мас.% Fe 2 O 3 ), но также содержит небольшие количества магнезии (0–2 мас. % MgO), триоксид серы (1–4 мас.% SO 3 ) и другие оксиды, представленные в виде примесей из сырья, используемого при его производстве.
Основными фазами, присутствующими в негидратированном портландцементе, являются алит (Ca 3 SiO 5 -силикат трикальция), белит (Ca 2 SiO 4 — β-дикальций силикат), алюминат (Ca 3 Al 2 O 6 — алюминат трикальция), феррит (Ca 4 (Al, Fe) 2 O 7 — алюмоферрит тетракальция).
В таблице 15.1 показаны составы и сокращения этих соединений.
Таблица 15.1. Основные соединения в портландцементе
Соединение | Оксидный состав | Сокращение |
---|---|---|
Силикат трикальция | 3CaO · SiO 2 | C 3 S |
a Силикат дикальция 2 · SiO 2 | C 2 S | |
Алюминат трикальция | 3CaO · Al 2 O 3 | C 3 A |
2 Тетракальций 609 Aluminoferritea O 3 · Fe 2 O 3 | C 4 AF |
Ранняя гидратация цемента в основном контролируется количеством и активностью C 3 A, сбалансированной количеством и вид сульфатной грунтовки с цементом. C 3 A быстро гидратирует и влияет на характеристики раннего склеивания. Аномальная гидратация C 3 A и плохой контроль его гидратации с помощью сульфата могут привести к таким проблемам, как схватывание, потеря осадки и несовместимость цемент-добавка. На основе этой информации был разработан ряд цементов с различной прочностью или высокой начальной прочностью. Пять признанных типов портландцемента перечислены в Таблице 15.2. Типичные составы коммерческих портландцементов приведены в Таблице 15.3.
Таблица 15.2. Типы портландцемента и их применение
Тип цемента | Используйте |
---|---|
I | Цемент общего назначения, когда нет смягчающих условий |
II | Помощь в обеспечении умеренной устойчивости к сульфатной атаке |
III | Когда требуется высокая ранняя прочность |
IV | Когда требуется низкая теплота гидратации (в массивных конструкциях) |
V | Когда требуется высокая сульфатостойкость |
Таблица 15. 3. Состав (мас.%) Коммерческих портландцементов
Тип цемента | C 3 S | C 2 S | C 3 A | C 4 AF | Прочие |
---|---|---|---|---|---|
I | 50 | 24 | 11 | 8 | 7 |
II | 42 | 33 | 5 | 13 | 7 |
III | 60 | 13 | 9 | 8 | 10 |
IV | 26 | 50 | 5 | 12 | 7 |
V | 40 | 40 | 4 | 7 | 7 |
Тип I, называемый нормальным портландцементом или обычным портландцементом (OPC), наиболее часто используется, когда особые свойства других типов не требуются, например Например, когда он не подвержен сульфатному воздействию отходов или когда тепло, выделяемое при гидратации цемента, не вызывает неприемлемого повышения температуры. Цементы типа I обычно имеют прочность на сжатие (раздавливание) через 7 дней> 19 МПа, измеренную на 50-миллиметровых кубиках раствора.
Тип II, модифицированный портландцемент с пониженным содержанием C 3 S и C 3 A, имеет более низкую скорость гидратации, чем тип I, и медленнее выделяет тепло. Он также обладает повышенной устойчивостью к воздействию сульфатов и предназначен для использования там, где важны дополнительные меры предосторожности против умеренного воздействия сульфатов.
Тип III, высокопрочный цемент с высоким содержанием C 3 S и более низким уровнем C 2 S, быстро набирает прочность благодаря высокому содержанию трикальцийалюмината и трикальцийсиликата.Однако такое быстрое нарастание прочности сопровождается высокой скоростью выделения тепла, что может препятствовать использованию цемента типа III для массивных монолитов из отходов / цемента.
Тип IV, низкотемпературный цемент с низким уровнем C 3 S и C 3 A и, следовательно, высоким уровнем C 2 S, может использоваться в первую очередь для массивных отходов / цементных монолитов. Низкая скорость тепловыделения в этом типе цемента объясняется высоким содержанием силиката дикальция и соответствующим низким содержанием силиката трикальция и алюмината трикальция.
Тип V — сульфатостойкий цемент из-за низкого содержания трикальцийалюмината. Это специальный цемент, предназначенный для использования в монолитах, подвергающихся сильному воздействию сульфатов. Он имеет более медленную скорость набора прочности, чем обычный портландцемент.
Портландцемент типов I, II и III обычно используется для иммобилизации радиоактивных отходов. В то время как тип II обладает повышенной устойчивостью к воздействию сульфатов, растворы сульфата натрия успешно затвердевают, причем все три типа имеют примерно одинаковые нагрузки.Водные отходы, содержащие борную кислоту, могут затвердеть, если в цемент добавить щелочной материал (например, гашеную известь или NaOH) или силикат натрия, а также при увеличении щелочности раствора до pH 8–12. Было показано, что типы I, II и III работают с такими добавками. Тип III предпочтительнее для жидких отходов борной кислоты из-за характеристик быстрого отверждения этого цемента (Раздел 15.6), который во многих случаях противодействует эффектам замедления гидратации, вызванным борной кислотой (Раздел 15.8).
3 Карбонизация минералов для производства строительных материалов | Утилизация потоков газообразных углеродных отходов: состояние и потребности исследований
EPA (Агентство по охране окружающей среды США). 2016. Продвижение устойчивого управления материальными потоками: отчет по переработке экономической информации (REI) за 2016 год. Доступно по адресу https://www.epa.gov/smm/recycling-economic-information-rei-report (по состоянию на 10 октября 2018 г.).
Фернандес Бертос, М., С. Дж. Р. Симонс, К. Д. Хиллс и П.Дж. Кэри. 2004. Обзор технологии ускоренной карбонизации при обработке материалов на основе цемента и секвестрации CO 2 . Журнал опасных материалов 112 (3): 193-205.
Флейшер М. 1953. Последние оценки содержания элементов в земной коре . Геологическая служба США.
Galan, I., C. Andrade, P. Mora, and M. A. Sanjuan. 2010. Связывание CO 2 путем карбонизации бетона. Наука об окружающей среде и технологии 44 (8): 3181-3186.
Герке Н., Х. Кёльфен, Н. Пинна, М. Антониетти и Н. Нассиф. 2005. Надстройки кристаллов карбоната кальция путем ориентированного прикрепления. Рост и дизайн кристаллов 5 (4): 1317-1319.
Glasser, F. P., G. Jauffret, J. Morrison, J.-L. Гальвез-Мартос, Н. Паттерсон и М. С.-Э. Имбаби. 2016. Разделение CO 2 путем минерализации в полезные продукты на основе несквехонита. Frontiers in Energy Research 4 (3) . DOI: 10.3389 / fenrg.2016.00003.
Глобальная инициатива CO 2 . 2016. Утилизация углекислого газа (CO2U): Дорожная карта МИЭФ 1. 0.
Горачи, Г., М. Монастерио, Х. Янссон и С. Червени. 2017. Динамика наноразмерной воды в портландцементе: сравнение с синтетическим гелем C-S-H и другими силикатными материалами. Научные отчеты 7 (1): 8258.
Kashef-Haghighi, S. и S. Ghoshal. 2013. Физико-химические процессы, ограничивающие поглощение CO 2 бетоном при ускоренном карбонизационном отверждении. Промышленные и инженерные химические исследования 52 (16): 5529-5537.
Kelemen, P. B., and J. Matter. 2008. Карбонизация перидотита на месте для хранения CO 2 . Proceedings of the National Academy of Sciences of the United States of America 105 (45): 17295-17300.
Миньярди, С., К. Де Вито, В. Феррини и Р. Ф. Мартин. 2011. Эффективность связывания CO 2 посредством карбонатной минерализации с моделированием сточных вод высокой солености. Журнал опасных материалов 191 (1): 49-55.
Монтес-Эрнандес, Г., Р. Перес-Лопес, Ф. Ренар, Х. М. Ньето и Л. Шарле. 2009. Минеральное связывание CO 2 путем водной карбонизации летучей золы при сжигании угля. Журнал опасных материалов 161 (2): 1347-1354.
Монтес-Эрнандес, Г., Р. Кириак, Ф. Тош и Ф. Ренар. 2012. Газо-твердая карбонизация частиц Ca (OH) 2 и CaO в неизотермических и изотермических условиях с использованием термогравиметрического анализатора: последствия для улавливания CO 2 . Международный журнал по контролю за парниковыми газами 11: 172-180.
Monkman, S., and Y. Shao. 2006. Оценка карбонизации вяжущих материалов. Журнал материалов в гражданском строительстве 18 (6): 768-776.
Мурхед Д. Р. 1986. Цементация карбонизацией гашеной извести. Исследование цемента и бетона 16 (5): 700-708.
Морс, Дж. У. и Ф. Т. Маккензи. 1990. Геохимия осадочных карбонатов .Амстердам: Эльзевир.
Никульшина В., М. Э. Гальвес, А. Стейнфельд. 2007. Кинетический анализ реакций карбонизации для улавливания CO 2 из воздуха через солнечный термохимический цикл Ca (OH) 2 –CaCO 3 –CaO. Журнал химической инженерии 129 (1): 75-83.
Oelkers, E.H., S.R. Gislason, and J. Matter. 2008. Минеральная карбонизация CO 2 . Элементы 4 (5): 333-337.
Пеннер, Л., У.О’Коннор, Д. Далин, С. Гердеманн и Г. Раш. 2004. Карбонизация минералов: затраты энергии на варианты предварительной обработки и выводы, полученные в результате исследований реакции контура потока. DOE / ARC – 2004-042.
Покровский О.С. 1998. Осаждение карбонатов кальция и магния из гомогенных перенасыщенных растворов. Журнал роста кристаллов 186 (1): 233-239.
Портлендская цементная ассоциация. 2013. Портлендская цементная промышленность США: сводная информация о заводе. Скоки, Иллинойс: Ассоциация портландцемента.
Э. Поссан, У. А. Томаз, Г. А. Алеандри, Э. Ф. Феликс и А. С. П. душ Сантуш. 2017. Потенциал поглощения CO 2 из-за карбонизации бетона: тематическое исследование. Примеры из строительных материалов 6: 147-161.
Ricci, M., W. Trewby, C. Cafolla, and K. Voïtchovsky. 2017. Прямое наблюдение за динамикой одиночных ионов металлов на границе раздела с твердыми телами в водных растворах. Научные отчеты 7 : 43234.
Санна А., М.Уйбу, Дж. Караманна, Р. Куусик и М. Марото-Валер. 2014. Обзор технологий карбонизации минералов для секвестрации CO 2 . Обзоры химического общества 43 (23): 8049-8080.
Максимальное поглощение CO2 в карбонизации бетонных блоков
Максимальное поглощение CO2 в карбонизации бетонных блоков Йиксин Шао1 *, Яодун Цзя1, Чжэнь Хе2 и Лян Ху31 Кафедра гражданского строительства, Университет Макгилла, Монреаль, Канада h4A 2K6 2 Школа водных ресурсов и гидроэнергетики, Уханьский университет, Ухань, Китай 430072 33H Company, Лексингтон, Кентукки, США 40511 * Автор, ответственный за переписку: [email protected] Реферат: Бетонные изделия на основе портландцемента хорошо известны своей реакционной способностью по отношению к диоксиду углерода. Именно соединения кальция в цементе вступают в реакцию с CO2 и образуют термодинамически стабильные карбонаты кальция. Было подсчитано, что при полной карбонизации, когда весь CaO вступает в реакцию с диоксидом углерода, поглощение CO2 цементом может достигать 50% от массы цемента, то есть одна тонна цемента может поглощать полтонны CO2. Полная карбонизация может произойти при карбонизации бетона в результате выветривания более чем через 30 лет, когда атмосферный CO2 медленно, но постепенно вступает в реакцию с продуктами гидратации в созревшем бетоне. Тем не менее, это нежелательная реакция, поскольку продукты гидратации разлагаются и прочность бетона снижается. С другой стороны, ранняя карбонизация во время отверждения бетона обеспечивает идеальное технологическое окно для утилизации CO2. Это ускоренная гидратация, которая может значительно улучшить долговечность бетона. В отличие от отверждения паром, которое хорошо продается, отверждение методом ранней карбонизации никогда не применялось в больших масштабах. Одним из ограничивающих факторов является стоимость газа CO2. В ближайшем будущем в результате регулирования выбросов в больших количествах может появиться недорогой CO2 высокой чистоты.Это дает возможность коммерческого применения диоксида углерода на ранних этапах карбонизации бетона, что объединит улавливание, использование и хранение углерода (CCUS) в один процесс, а также продемонстрирует экономические и технические преимущества. В этой статье представлен новый процесс карбонизации, который включает предварительную настройку гидратации перед ранней карбонизацией.
Бетонные изделия с высоким отношением воды к цементу, сформированные путем виброуплотнения, могут быть использованы в качестве продуктов-кандидатов для улавливания и утилизации углерода.Поскольку способность поглощать CO2 уникальна для каждого продукта и связанного с ним процесса, бетонный блок будет использован в качестве примера для подтверждения концепции. Бетонные блоки нашли широкое применение в строительстве. По прогнозам, в 2014 году рынок бетонных блоков и кирпичей в США вырастет до 4,3 миллиарда единиц в год. Бетонные блоки изготовлены из силикатно-кальциевого цемента, пористого по своей природе и производятся серийно. Блочные заводы также демографически распределены и стратегически расположены недалеко от источников CO2, таких как электростанции и цементные заводы.В настоящее время бетонные блоки производятся методом парового твердения. Если паровой процесс можно заменить отверждением CO2, бетонные блоки могут служить поглотителем CO2 для хранения углерода за счет использования.
Это также является стимулом для демонстрации сравнения энергии между системами пара и CO2. В статье сначала будет представлен процесс карбонизации бетонного блока, который включает гидратацию и карбонизацию в различной последовательности, на основе которой предлагается модель реакции для оценки теоретического максимального поглощения CO2 в пределах технологического окна.Кинетика реакции четырех цементных фаз: трикальцийсиликата (3CaO · SiO2 или C3S), дикальциевого силиката (2CaO · SiO2 или C2S), трикальцийалюмината (3CaO · Al2O3 или C3A), тетракальциевого алюмоферрита (4CaOAl2O3 или четырех гидратированных CaOAl2O3Fe2O3 и четырех гидратов. продукты: гидроксид кальция, силикат-гидрат кальция, алюминат-гидрат кальция, феррит-гидрат алюмината кальция. На основе кинетики реакции модель дополнительно подтверждается карбонизацией цементного раствора, которая представляет идеальные условия реакции, а также карбонизацией легкого и легкого бетона.Теоретический максимум поглощения CO2 в течение 24-часового технологического окна был оценен и сравнен с экспериментальным поглощением CO2 карбонизацией бетонных блоков. Сочетание предварительной настройки гидратации и карбонизации помогло повысить эффективность реакции. Предварительная установка гидратации 4-18 часов может удалить 40-60% свободной воды, чтобы создать путь для диффузии CO2, освободить место для осаждения карбонатов и произвести продукты ранней гидратации для карбонизации. Наилучшее поглощение CO2 было получено при относительно высоком содержании воды в исходной смеси с последующими 18-часовыми предварительными настройками и 2–4-часовой карбонизацией.В бетонах с нормальной массой она составила 18,3%, в легких — 24,2%. Это окно процесса практически осуществимо. Теоретический максимум поглощения CO2 был оценен на основании предположения, что на ранней стадии карбонизации только C3S, C2S и их продукты гидратации реагировали с CO2. Вкладом алюминатной и ферритной фаз пренебрегли. Также предполагалось, что после предварительной настройки гидратации оставшиеся C3S и C2S полностью карбонизировались до C-S-H и CaCO3. На основе этих предположений было вычислено теоретическое максимальное поглощение CO2.Это было 19,7% без предварительной настройки и 27,1% с 18-часовой предварительной настройкой. Результаты согласуются с карбонизацией цементного раствора. Поглощение CO2 в бетоне с нормальным весом достигло 67% эффективности реакции после 2-часовой карбонизации, а CO2 в легком бетоне достигло 89% после 4-часовой карбонизации. Более высокая скорость поглощения легким бетоном также была связана с активными шлаковыми агрегатами. Если вычесть поглощение заполнителями из общего поглощения, легкий бетон показал бы значение, близкое к бетону с нормальным весом.Карбонизация в течение длительного времени и при высоком давлении может способствовать большему поглощению CO2. В этих случаях C-S-H, образованный карбонизацией, а также фазы алюнимата кальция и феррита алюмината кальция также могут быть карбонизированы. Однако полной карбонизации с поглощением 50% CO2 так и не удалось достичь даже после продолжения реакции в течение двух дней. Карбонизация бетонных блоков повысит ценность СО2 как товара для строительной индустрии и будет постоянно хранить СО2 в термодинамически стабильных карбонатах кальция.Бетонный блок — лишь один из многочисленных строительных продуктов на основе цемента. Годовое производство портландцемента в США составляет около 100 тонн. Если бы половину ее продукции можно было бы обрабатывать карбонизацией со скоростью поглощения CO2 10-25%, использование CO2 только в бетонной промышленности могло бы достичь 5-12 т / год.
Расшифровка: Химия в ее элементе: кремний(Promo) Вы слушаете Химию в ее элементе, представленную вам Chemistry World , журналом Королевского химического общества. (Конец промо) Мира Сентилингам На этой неделе мы вступаем в мир научной фантастики, чтобы исследовать жизнь в космосе. Вот Андреа Селла. Андреа Селла Когда мне было около 12 лет, мы с друзьями прошли этап чтения научной фантастики. Это были фантастические миры Айзека Азимова, Ларри Нивена и Роберта Хайнлайна, включающие невозможные приключения на загадочных планетах — успехи космической программы Аполлона в то время только помогли нам приостановить наше недоверие.Одной из тем, которые я помню из этих историй, была идея о том, что инопланетные формы жизни, часто основанные на элементе кремний, распространены в других местах Вселенной. Почему кремний? Что ж, часто говорят, что элементы, близкие друг к другу в периодической таблице, обладают схожими свойствами, и поэтому, соблазненные извечным отвлекающим маневром, что «углерод является элементом жизни», авторы выбрали элемент под ним, кремний. Я вспомнил об этих чтениях пару недель назад, когда пошел на выставку работ двух моих друзей.Названный «Каменная дыра», он состоял из потрясающих панорамных фотографий, сделанных с чрезвычайно высоким разрешением в морских пещерах в Корнуолле. Когда мы бродили по галерее, мне в голову пришла мысль. «Можно ли представить мир без кремния?» Неудивительно, что на каждой фотографии преобладали породы на основе кремния, и это было мощным напоминанием о том, что кремний является вторым по распространенности элементом в земной коре, уступая первое место кислороду, элементу, с которым он неизменно связан. . Силикатные породы — те, в которых кремний окружен тетраэдрически четырьмя атомами кислорода — существуют в удивительном разнообразии, различия определяются тем, как соединяются друг с другом строительные блоки тетраэдров и какие другие элементы присутствуют, чтобы завершить картину. Когда тетраэдры соединяются друг с другом, получается сумасшедший клубок цепочек, похожий на огромный горшок со спагетти — структуры, которые можно получить в обычном стекле. Самым чистым из этих цепочечных материалов является диоксид кремния — кремнезем, который довольно часто встречается в природе в виде бесцветного минерального кварца или горного хрусталя.В хорошем кристаллическом кварце цепи расположены красивыми спиралями, и все они могут закручиваться влево. Или вправо. Когда это происходит, полученные кристаллы являются точным зеркальным отображением друг друга. Но не накладываются друг на друга — как левая и правая туфли. Для химика эти кристаллы хиральны — свойство, которое когда-то считалось исключительным свойством элемента углерода, а хиральность, в свою очередь, считалась фундаментальной чертой самой жизни. Но вот он, в холодном неорганическом мире кремния. Самое грандиозное, что можно создавать пористые трехмерные структуры — немного похожие на молекулярные соты — особенно в присутствии других тетраэдрических линкеров на основе алюминия. Эти впечатляющие материалы называются цеолитами или молекулярными ситами. Тщательно подбирая условия синтеза, можно создать материал, в котором поры и полости имеют четко определенные размеры — теперь у вас есть материал, который можно использовать, как ловушки для омаров, для улавливания молекул или ионов подходящего размера. А как насчет самого элемента? Освободить его от кислорода сложно, он висит как мрачная смерть и требует жестоких условий.Хамфри Дэви, химик и шоумен из Корнуолла, первым начал подозревать, что кремнезем должен быть соединением, а не элементом. Он применил электрический ток к расплавленным щелочам и солям и, к своему удивлению и восторгу, выделил некоторые чрезвычайно активные металлы, в том числе калий. Теперь он двинулся дальше, чтобы посмотреть, на что способен калий. Пропуская пары калия над кремнеземом, он получил темный материал, который затем можно было сжечь и превратить обратно в чистый кремнезем. Куда он толкал, другие следовали за ним. Во Франции Тенар и Гей-Люссак провели аналогичные эксперименты с фторидом кремния.За пару лет великий шведский аналитик Йенс Якоб Берцелиус выделил более существенный объем материала и объявил его элементом. Кремний не имеет свойств ни рыба, ни мясо. Темно-серого цвета и с очень глянцевым стекловидным блеском, он выглядит как металл, но на самом деле является довольно плохим проводником электричества, и во многих отношениях кроется секрет его окончательного успеха. Проблема в том, что электроны захватываются, как части на черновой доске, в которой нет свободных мест.Особенность кремния и других полупроводников заключается в том, что можно переместить один из электронов на пустую доску — зону проводимости — где они могут свободно перемещаться. Это немного похоже на трехмерные шахматы, в которые играет остроухий доктор Спок из «Звездного пути». Температура имеет решающее значение. Нагревая полупроводник, позвольте некоторым электронам прыгнуть, как лосось, в пустую зону проводимости. И в то же время оставшееся пространство, известное как дыра, тоже может двигаться. Но есть другой способ заставить кремний проводить электричество: это кажется извращенным, но намеренно вводя примеси, такие как бор или фосфор, можно незаметно изменить электрическое поведение кремния.Такие уловки лежат в основе функционирования кремниевых чипов, которые позволяют вам слушать этот подкаст. Менее чем за 50 лет кремний превратился из любопытного любопытства в один из основных элементов нашей жизни. Но остается вопрос, ограничивается ли значение кремния только миром минералов? Перспективы не кажутся хорошими — силикатные волокна, такие как волокна синего асбеста, имеют как раз тот размер, который подходит для проникновения глубоко внутрь легких, где они пронзают и разрезают внутреннюю оболочку легких.И все же из-за его необычайной структурной изменчивости химия кремния использовалась биологическими системами. Силикатные осколки прячутся в колючках крапивы и ждут, чтобы порезать мягкую кожу неосторожного путешественника и ввести небольшое количество раздражителя. И в почти невообразимых количествах тонкие силикатные структуры выращиваются множеством крошечных форм жизни, лежащих в основе морских пищевых цепей, диатомовыми водорослями. Можно ли найти кремниевых пришельцев где-нибудь в космосе? Моя догадка, вероятно, была бы нет.Конечно, не как элемент. Он слишком реактивен, и всегда можно обнаружить, что он связан с кислородом. Но даже связанное с кислородом, это кажется маловероятным, или, по крайней мере, не в тех мягких условиях, которые мы находим на Земле. Но опять же, нет ничего лучше сюрприза, чтобы заставить задуматься. Как сказал генетик Дж. Б. С. Холдейн: «Вселенная не страннее, чем мы думаем. Она страннее, чем мы можем предположить». Я живу надеждой. Meera Senthilingam Итак, хотя маловероятно, что в космосе могут таиться сюрпризы на основе кремния.Это была всегда обнадеживающая Андреа Селла из Университетского колледжа Лондона, занимавшаяся жизнедеятельностью кремния. На следующей неделе мы узнаем о рентгении, элементе, который нам нужно получить правильно. Саймон Коттон Идея заключалась в том, чтобы заставить ионы никеля проникать в ядро висмута, чтобы два ядра слились вместе, образуя атом большего размера. Энергию столкновения необходимо было тщательно контролировать, потому что, если ионы никеля не будут двигаться достаточно быстро, они не смогут преодолеть отталкивание между двумя положительными ядрами и просто оторвутся от висмута при контакте.Однако, если бы ионы никеля обладали слишком большой энергией, образовавшееся «составное ядро» имело бы такой избыток энергии, что оно могло бы просто подвергнуться делению и распасться. Уловка заключалась в том, чтобы, как и в случае с кашей Златовласки, быть «в самый раз», чтобы произошло слияние ядер, просто. Мира Сентилингам. Присоединяйтесь к Саймону Коттону, чтобы узнать, как удачные столкновения были созданы основателями элемента рентгениум в программе Chemistry in its Element на следующей неделе. А пока я Мира Сентилингам, и спасибо за внимание. (промо) (конец промо) |
Глава 1 — Зола-унос. Технические материалы. Факты о золе-уносе для дорожных инженеров.
Факты о летучей золе для дорожных инженеров
Глава 1 — Летучая зола — Технические материалы
Почему летучая зола?
Что такое летучая зола? Летучая зола — это мелкодисперсный остаток, образующийся при сгорании пылевидного угля и переносимый из камеры сгорания выхлопными газами.В 2001 году было произведено более 61 миллиона метрических тонн (68 миллионов тонн) летучей золы.
Откуда взялась летучая зола? Летучая зола производится угольными электрическими и парогенераторными установками. Как правило, уголь измельчается и вдувается воздухом в камеру сгорания котла, где он немедленно воспламеняется, выделяя тепло и выделяя расплавленный минеральный остаток. Котельные трубы отводят тепло от котла, охлаждая дымовой газ и заставляя расплавленный минеральный остаток затвердевать и образовывать золу.Крупные частицы золы, называемые зольным остатком или шлаком, падают на дно камеры сгорания, в то время как более легкие мелкие частицы золы, называемые летучей золой, остаются взвешенными в дымовых газах. Перед выпуском дымовых газов летучая зола удаляется устройствами контроля выбросов твердых частиц, такими как электрофильтры или рукавные фильтры из фильтровальной ткани (см. Рисунок 1-1).
Где используется летучая зола? В настоящее время более 20 миллионов метрических тонн (22 миллиона тонн) летучей золы ежегодно используется в различных инженерных приложениях.Типичные области применения в дорожном строительстве включают: портландцементный бетон (PCC), стабилизацию грунта и основания дороги, текучие засыпки, растворы, конструкционный наполнитель и асфальтный наполнитель.
Чем полезна летучая зола? Летучая зола чаще всего используется в качестве пуццолана в приложениях PCC. Пуццоланы представляют собой кремнеземистые или кремнеземистые и глиноземистые материалы, которые в мелкодисперсной форме и в присутствии воды реагируют с гидроксидом кальция при обычных температурах с образованием вяжущих соединений.
Уникальная сферическая форма и гранулометрический состав золы-уноса делают ее хорошим минеральным наполнителем в горячих асфальтовых смесях (HMA) и улучшают текучесть текучей засыпки и цементного раствора. Постоянство и обилие летучей золы во многих областях открывает уникальные возможности для использования в строительных засыпках и других дорожных покрытиях.
Экологические преимущества. Утилизация летучей золы, особенно в бетоне, имеет значительные экологические преимущества, включая: (1) увеличение срока службы бетонных дорог и конструкций за счет повышения долговечности бетона, (2) чистое сокращение энергопотребления и выбросов парниковых газов и других вредных выбросов в атмосферу во время полета. зола используется для замены или вытеснения производимого цемента, (3) уменьшения количества продуктов сгорания угля, которые должны быть захоронены на свалках, и (4) сохранения других природных ресурсов и материалов.
Рис. 1-1: Метод переноса летучей золы может быть сухим, влажным или и тем, и другим.
Производство
Летучая зола образуется при сжигании угля в электрических котлах или промышленных котлах. Существует четыре основных типа котлов, работающих на угле: пылевидный уголь (ПК), топка с топкой или подвижная колосниковая решетка, циклон и котлы сжигания в псевдоожиженном слое (FBC). Котел ПК является наиболее распространенным, особенно для крупных электрогенерирующих агрегатов. Остальные котлы чаще встречаются на промышленных или когенерационных предприятиях.Летучая зола, производимая котлами FBC, в этом документе не рассматривается. Летучая зола улавливается из дымовых газов с помощью электростатических пылеуловителей (ESP) или в коллекторах из фильтровальной ткани, обычно называемых рукавными фильтрами. Физические и химические характеристики летучей золы различаются в зависимости от методов сжигания, источника угля и формы частиц.
Миллион метрических тонн | Миллион коротких тонн | Процент | |
---|---|---|---|
Произведено | 61.84 | 68,12 | 100,0 |
Использовано | 19,98 | 22,00 | 32,3 |
Как показано в Таблице 1-1, из 62 миллионов метрических тонн (68 миллионов тонн) летучей золы, произведенной в В 2001 году было использовано только 20 миллионов метрических тонн (22 миллиона тонн), или 32 процента от общего объема производства. Ниже приводится разбивка использования летучей золы, большая часть которой используется в транспортной отрасли.
Миллион метрических тонн | Миллион коротких тонн | Процент | |
---|---|---|---|
Цемент / бетон | 12.16 | 13,40 | 60,9 |
Текучая насыпка | 0,73 | 0,80 | 3,7 |
Структурная насыпка | 2,91 | 3,21 | 14,6 |
Дорожное основание / основание | 0,93 | 1,02 | 4,7 |
Модификация почвы | 0,67 | 0,74 | 3,4 |
Минеральный наполнитель | 0,10 | 0.11 | 0,5 |
Горнодобывающая промышленность | 0,74 | 0,82 | 3,7 |
Стабилизация / отверждение отходов | 1,31 | 1,44 | 6,3 |
Сельское хозяйство | 0,02 | 0,02 | |
Разное / Другое | 0,41 | 0,45 | 2,1 |
Итого | 19,98 | 22,00 | 100 |
Обработка
Собранная летучая зола обычно пневматически транспортируется из бункеров ЭЦН или фильтрующей ткани в силосы для хранения, где она остается сухой до утилизации или дальнейшей обработки, или в систему, где сухая зола смешивается с водой и транспортируется (промывается) в хранилище. -площадь водохранилища.
Сухая собранная зола обычно хранится и обрабатывается с использованием оборудования и процедур, аналогичных тем, которые используются для работы с портландцементом:
- Летучая зола хранится в силосах, куполах и других бестарных хранилищах
- Летучая зола может транспортироваться с помощью воздушных шиберов, ковшовых конвейеров и винтовых конвейеров, или ее можно транспортировать пневматически по трубопроводам в условиях положительного или отрицательного давления
- Летучая зола транспортируется на рынки в автоцистернах, железнодорожных вагонах и баржах / судах
- Зола-унос может быть упакована в супер-мешки или мешки меньшего размера для специальных применений
Сухая собранная летучая зола также может быть увлажнена водой и смачивающими веществами, если применимо, с использованием специального оборудования (кондиционированного) и транспортироваться в крытых самосвалах для специальных применений, таких как заполнение конструкций.Водную летучую золу можно складировать на стройплощадках. Открытый складированный материал необходимо поддерживать во влажном состоянии или накрывать брезентом, пластиком или аналогичными материалами для предотвращения выброса пыли.
Характеристики
Размер и форма. Летучая зола обычно мельче портландцемента и извести. Летучая зола состоит из частиц размером с ил, которые обычно имеют сферическую форму и обычно имеют размер от 10 до 100 микрон (рис. 1-2). Эти маленькие стеклянные сферы улучшают текучесть и удобоукладываемость свежего бетона.Тонкость помола — одно из важных свойств, определяющих пуццолановую реакционную способность летучей золы.
Рис. 1-2: Частицы летучей золы при 2000-кратном увеличении.
Химия. Летучая зола состоит в основном из оксидов кремния, алюминия, железа и кальция. Магний, калий, натрий, титан и сера также присутствуют в меньшей степени. При использовании в качестве минеральной добавки в бетоне летучая зола классифицируется как зола класса C или класса F в зависимости от ее химического состава.Американская ассоциация государственных служащих автомобильного транспорта (AASHTO) M 295 [Спецификация C 618 Американского общества испытаний и материалов (ASTM)] определяет химический состав летучей золы классов C и F.
Зола класса C обычно получают из полубитуминозных углей и состоят в основном из алюмосульфатного стекла кальция, а также кварца, трехкальциевого алюмината и свободной извести (CaO). Зола класса C также называется летучей золой с высоким содержанием кальция, поскольку она обычно содержит более 20 процентов CaO.
Зола класса F обычно получают из битуминозных и антрацитовых углей и состоят в основном из алюмосиликатного стекла, в котором также присутствуют кварц, муллит и магнетит. Класс F или зола-унос с низким содержанием кальция содержит менее 10 процентов CaO.
Компаунды | Зола уноса класса F | Зола уноса класса C | Портлендский цемент |
---|---|---|---|
SiO 2 | 55 | 40 | 23 |
Al 2 0 3 | 26 | 17 | 4 |
Fe 2 O 3 | 7 | 6 | 2 |
CaO (Известь) | 9 | 24 | 64 |
MgO | 2 | 5 | 2 |
SO 3 | 1 | 3 | 2 |
Цвет. Летучая зола может быть от желтовато-коричневой до темно-серой в зависимости от ее химических и минеральных компонентов. Коричневый и светлый цвет обычно ассоциируется с высоким содержанием извести. Коричневатый цвет обычно связан с содержанием железа. Цвет от темно-серого до черного обычно связан с повышенным содержанием несгоревшего углерода. Цвет летучей золы обычно одинаков для каждой электростанции и источника угля.
Рисунок 1-3: Типичные пепельные цвета
Качество летучей золы
Требования к качеству летучей золы различаются в зависимости от предполагаемого использования.На качество летучей золы влияют характеристики топлива (уголь), совместное сжигание топлива (битуминозные и полубитуминозные угли) и различные аспекты процессов сжигания и очистки / сбора дымовых газов. Четыре наиболее важных характеристики летучей золы для использования в бетоне — это потери при возгорании (LOI), тонкость помола, химический состав и однородность.
LOI — это измерение количества несгоревшего углерода (угля), остающегося в золе, и является важной характеристикой летучей золы, особенно для бетонных применений.Высокий уровень углерода, тип углерода (то есть активированный), взаимодействие растворимых ионов в летучей золе и изменчивость содержания углерода могут привести к значительным проблемам с воздухововлечением в свежем бетоне и могут отрицательно повлиять на долговечность бетона. AASHTO и ASTM определяют пределы для LOI. Однако некоторые государственные транспортные департаменты устанавливают более низкий уровень для LOI. Углерод также можно удалить из летучей золы.
ППП не влияет на некоторые виды использования летучей золы. Наполнитель в асфальте, текучий наполнитель и конструкционные наполнители могут принимать летучую золу с повышенным содержанием углерода.
Тонкость помола летучей золы наиболее тесно связана с рабочим состоянием угольных дробилок и измельчаемостью самого угля. Для использования летучей золы в бетонных изделиях тонкость помола определяется как процент по массе материала, удерживаемого на сите 0,044 мм (№ 325). Более крупная градация может привести к менее реакционной золе и может содержать более высокое содержание углерода. Пределы дисперсности регулируются ASTM и спецификациями государственного транспортного департамента. Летучая зола может быть обработана просеиванием или воздушной классификацией для улучшения ее дисперсности и реакционной способности.
Некоторые небетонные области применения, такие как строительные засыпки, не зависят от степени измельчения летучей золы. Однако другие применения, такие как асфальтный наполнитель, в значительной степени зависят от степени измельчения летучей золы и ее гранулометрического состава.
Химический состав летучей золы напрямую связан с минеральным составом исходного угля и любых дополнительных видов топлива или добавок, используемых в процессах сгорания или дожигания. Используемая технология контроля загрязнения также может влиять на химический состав летучей золы.Электростанции сжигают большие объемы угля из нескольких источников. Угли могут быть смешаны, чтобы максимизировать эффективность производства или улучшить экологические характеристики станции. Химический состав летучей золы постоянно проверяется и оценивается для конкретных применений.
Некоторые станции выборочно сжигают определенные угли или изменяют состав своих добавок, чтобы избежать ухудшения качества золы или придать желаемый химический состав и характеристики летучей золы.
Однородность характеристик летучей золы от отгрузки к отгрузке является обязательной для обеспечения стабильного продукта.Химический состав и характеристики летучей золы обычно известны заранее, поэтому бетонные смеси разрабатываются и испытываются на эксплуатационные характеристики.
ACI 229R | Контролируемый низкопрочный материал (CLSM) |
---|---|
ASTM C 311 | Отбор проб и испытание летучей золы или природных пуццоланов для использования в качестве минеральной добавки в портландцементном бетоне |
AASHTO M 295 ASTM C 618 | Зола-унос и необработанный или кальцинированный природный пуццолан для использования в качестве минеральной добавки в портландцементном бетоне |
ASTM C 593 | Зола-унос и другие пуццоланы для использования с известью |
ASTM D 5239 | Стандарт Практика определения летучей золы для использования в стабилизации почвы |
ASTM E 1861 | Руководство по использованию побочных продуктов сгорания угля в конструкционных насыпях |
Обеспечение качества и контроль качества Критерии различаются для каждого использования летучая зола от штата к штату и от источника к источнику.В некоторых штатах требуются сертифицированные образцы из силоса на определенной основе для тестирования и утверждения перед использованием. Другие ведут списки утвержденных источников и принимают сертификаты поставщиков проектов на качество летучей золы. Степень требований к контролю качества зависит от предполагаемого использования, конкретной летучей золы и ее изменчивости. Требования к тестированию обычно устанавливаются отдельными агентствами.
Рис. 1-4: Микроскопические фотографии летучей золы (слева) и портландцемента (справа).
Класс F | Класс C | |||
---|---|---|---|---|
Требования к химическим веществам | SiO 2 + Al 2 O 3 + Fe 2 O 3 | мин.% | 70 1 | 50 |
SiO 3 | макс% | 900 55 | ||
Влагосодержание | макс.% | 3 | 3 | |
Потери при воспламенении (LOI) | макс.% | 5 1 | 5 1 | |
Дополнительные химические требования | Доступные щелочи | макс.% | 1.5 | 1,5 |
Физические требования | Тонкость помола (+325 меш) | макс.% | 34 | 34 |
Пуццолановая активность / цемент (7 дней) | мин.% | 75 | 75 | |
Пуццолановая активность / цемент (28 дней) ) | мин.% | 75 | 75 | |
Потребность в воде | макс.% | 105 | 105 | |
Расширение автоклава | макс.% | 0.8 | 0,8 | |
Единые требования 2 : плотность | макс.% | 5 | 5 | |
Единые требования 2 : Тонкость помола | макс.% | 5 | 5 | |
Дополнительные физические требования | Множественный коэффициент (LOI x тонина) | 255 | — | |
Увеличение усадки при сушке | макс.% | .03 | .03 | |
Требования к однородности: Воздухововлекающий агент | макс.% | 20 | 20 | |
Цемент / щелочная реакция: Расширение раствора (14 дней) | макс.% | 0,020 | — — |
Примечания:
- Требования ASTM — 6 процентов
- Плотность и тонкость отдельных образцов не должны отличаться от среднего значения, установленного 10 предыдущими испытаниями, или всеми предыдущими испытаниями, если число меньше 10, более чем на указанный максимальный процент.
Березовский комбинат силикатных изделий наладил выпуск плит большого формата
Плитка тротуарная повсюду. И это неудивительно: хорошо выглядит и долго служит. Единственным недостатком является то, что цветовая гамма ограничена, а установка занимает много времени. Но Березовский комбинат силикатных изделий взял на себя эту задачу и приступил к выпуску относительно нового для Беларуси материала — широкоформатных декоративных плит.Попытки уйти от «серого очарования города» делали в основном небольшие компании, производящие или импортирующие цветную тротуарную плитку, которая востребована в основном для украшения частных объектов.
Теперь широкоформатные вибропрессованные декоративные плиты самых разнообразных цветов и фактур производятся в Березе на современной немецкой линии мощностью 300 тыс. М² в год: глянцевые или с шероховатой поверхностью, с эффектом «апельсиновой корки». »(Отличная антискользящая версия) и др.
« Это не те серые бетонные тротуары, которыми украшали дворы в старых районах Минска. Это красивый, современный, качественный материал, который открывает новые возможности в планировке помещений и ландшафтном дизайне.Причем цена за метр наших плит сопоставима с ценой на традиционную тротуарную плитку, а большой формат также позволяет сэкономить на укладке », — рассказали представителям компании Stroyka.by.
Плиты бывают двух размеров (300 × 300 × 35 и 400 × 400 × 50 мм) и могут использоваться для мощения тротуаров, а также для облицовки зданий.
Результатом модернизации Березовского комбината силикатных изделий стало также создание нового цеха по производству газосиликатных блоков.Линия немецкого производителя Masa-Henke позволяет изготавливать блоки с практически идеальной геометрией и улучшенными прочностными характеристиками.
Автор: Екатерина Кулабухова, Stroyka.by
http://stroyka.by/news/2015/04/29/berezovskiyKSI_plity
Возможность пересчитать каждый блок — Masonry Magazine
Технологии в кладке
Скотт Биггар и Челси Код-Макнил
Технологический прогресс не ограничен — проведение исследований и разработок неизбежно ведет к открытиям, продвигающим вперед инновации.Компания CarbonCure Technologies не новичок в этом цикле. Технология компании началась, когда их генеральный директор Роберт Нивен начал исследовать химическую реакцию между углекислым газом (CO2), цементом и водой, когда получил степень магистра в Университете Макгилла в Монреале, Канада.
Позже это исследование стало основой для разработки CarbonCure в течение следующих восьми лет и превратилось в то, что сейчас является жизнеспособным решением для производителей бетона по переработке отработанного CO2 в их бетонных смесях.
Рис. 1 — Химия, связанная с добавлением СО2 в бетонную смесь. (Любезно предоставлено CarbonCure Technologies)Двуокись углерода, известный парниковый газ и способствующий изменению климата, быстро становится главной темой для строительной отрасли. Архитекторы и застройщики на протяжении десятилетий совершенствовали строительные системы и технологии, чтобы снизить выбросы CO2, связанные с их зданиями. Однако этот подход затрагивает только один конец дымовой трубы, и разрабатываются новые технологии, позволяющие использовать CO2 для производства новых строительных материалов.
В основе технологии CarbonCure лежит химическая реакция, называемая минерализацией. Реакция происходит, когда CO2 вводится в процессе производства бетонных блоков (CMU). Газ CO2 вступает в реакцию с ионами кальция, содержащимися в цементе, и подвергается обратной реакции обжига (рис. 1), в результате чего образуется минерал карбонат кальция (известняк).
CMU, который поступает на объект, изготовленный с использованием технологии CarbonCure, имеет точно такие же физические свойства и внешний вид, что и традиционный CMU.Разница в том, что CMU CarbonCure забрал CO2 и удержал его внутри, откуда он больше не может быть выпущен. Поскольку газ был преобразован в карбонат кальция, он больше не влияет на изменение климата.
Дизайнеров и архитекторов постоянно просят приоритизировать свойства материалов, чтобы функционально оставаться верными мотивам своих клиентов. При рассмотрении использования КМУ в проекте в пользу материалов складывается множество свойств: долговечность, прочность, огнестойкость и тепловая масса.Все эти свойства материалов способствуют устойчивости здания, и с появлением стандарта LEED v4 вводятся новые меры для поощрения материалов, способных противостоять климатическим воздействиям.
Несмотря на материальные преимущества кирпичной кладки, в CMU есть один ингредиент, который несет значительный углеродный след: цемент. Строительная промышленность уже много лет знает о выбросах CO2 при производстве цемента и подталкивает производителей к поиску решений для уменьшения этого воздействия.
Там, где некоторые считают выброс CO2 из бетона проблемой, CarbonCure рассматривает его как возможность для адаптивного повторного использования. Каждый блок — это возможность сохранить небольшое количество углерода, шанс уменьшить часть выбросов цементной промышленности и вернуть их в бетон.
Brampton Brick, производитель кирпичной кладки, ведущий свою деятельность на юге Онтарио, был одним из первых, кто применил технологию CarbonCure в Северной Америке, впервые заключив партнерские отношения с компанией в 2013 году. В сентябре 2015 года Brampton принял решение установить технологию еще на двух заводах. свои заводы, ссылаясь на желание начать производство всей своей продукции с переработанным CO2.
«Все, что мы производим сегодня, содержит CO2, — сказал Дэйв Картер, генеральный директор Brampton Brick. Он указывает на стандарты зеленого строительства, такие как LEED, как на движущие силы тенденции.
Рис. 2 — Пакетный оператор, использующий интерфейс HMI CarbonCure.(любезно предоставлено CarbonCure Technologies)
Использование CMU в качестве емкости для хранения углерода не сильно увеличило общие затраты Brampton Brick и не изменило их производственную практику. Но Картер не рекламирует блоки с впрыском CO2 своей компании как серебряную пулю для бетонной промышленности.
«Это всего лишь часть головоломки», — сказал он, указав также на растущее использование в цементной и бетонной промышленности альтернативных видов топлива и материалов.
Добавление CarbonCure в состав смеси не влияет на вес, цвет и требования ASTM. С 2013 года CarbonCure установила свою технологию на 22 заводах в США и Канаде.
Разработчики и архитекторы в США начинают узнавать о перспективах хранения углерода в бетонных блоках. Kimco Realty, крупнейший в Северной Америке владелец и оператор торговых центров под открытым небом, недавно построила в Орегоне первый проект с использованием блока CarbonCure.Блок был изготовлен и поставлен компанией Mutual Materials, недавним партнером CarbonCure.
Рис. 3 — Строящаяся торговая точка Kimco. (Предоставлено Kimco Realty) |
Рис. 4 — CMU CarbonCure, предоставленный Mutual Materials. (Предоставлено Kimco Realty) |
«Добавление CarbonCure в наш проект Sunset Mall было довольно простым делом», — сказал Тим Хаманн, директор по строительству Kimco Realty.
В новом торговом центре разместятся два ресторана и магазин розничной торговли, строительство которых будет осуществлять компания Lanphere Construction and Development.
«У нашего генерального подрядчика и каменщиков не было никаких проблем с блоком», — сказал Хаманн. «Проект был выполнен так же, как и обычная кладка. Рециркуляция CO2 в этом проекте была как раз тем, что соответствовало целям Kimco в области устойчивого развития ».
Интеграция технологии CarbonCure в блочную установку также очень проста.После того, как производитель наладил поставку промышленного CO2 местного производства, инженеры CarbonCure устанавливают его оборудование и работают с группой контроля качества завода, чтобы интегрировать CO2 в свои бетонные смеси.
В эпоху, когда инновации имеют решающее значение как для окружающей среды, так и для устойчивости отрасли, производители бетона ищут способы улучшить как свои производственные процессы, так и брендинг своей компании. Добавление технологии CarbonCure обеспечивает небольшую, но новаторскую настройку существующих производственных операций, помогая при этом ответить на глобальный призыв к решениям для хранения углерода.