Станок для шлакоблока своими руками
Использование шлакоблоков в строительстве позволяет снизить расходы на сооружение стен в несколько раз. Для изготовления данного материала требуется специальное оборудования, покупка которого является довольно затратным процессом. Предлагаем изучить рекомендации о том как сделать станок для шлакоблоков своими руками.
Оглавление:
- Шлакоблок — особенности материала и его назначение
- Станок для шлакоблоков: особенности изготовления
- Оборудование для производства шлакоблоков и технология их изготовления
- Производство шлакоблоков — общие требования к выполнению работ
- Шлакоблоки своими руками: инструкция по изготовлению
Шлакоблок — особенности материала и его назначение
Шлакоблоком называют строительный материал, по внешнему виду схож с камнем, который изготавливают с применением метода вибро пресса. Для его производства используется наполнитель в виде шлака, а связующим веществом выступает цементный раствор.
Существует два варианта производства шлакоблоков:
- промышленный;
- самостоятельный или домашний.
Чтобы изготовить шлакоблок своими руками применяют вибростанки малогабаритного типа, которые способны изготовить небольшие партии данного материала.
В соотношении с основными составляющими шлакоблока, а именно шлаком, в его состав входит один из материалов в виде:
- шлака;
- вулканического пепла;
- гранитного отсева;
- гранитного щебня;
- речной щебенки;
- песка;
- кирпичного камня;
- цемента;
- керамзита и т.д.
Материал, об изготовлении которого поговорим далее, имеет более низкие качественные характеристики и долговечность. Он отлично подойдет для сооружения построек хозяйственного назначения, сараев, складских сооружений.
Домашнее изготовление шлакоблока не позволяет провести весь технологический процесс в соотношении со всеми требованиями, которые к нему предъявляются.
Для того, чтобы шлакоблок приобрел необходимую жесткость требуется выдержать пропаривание, с помощью которого происходит насыщение его влагой и нагревание до определенной температуры, которая повышает прочность цемента. Хотя с помощью блоков, изготовленных на домашнем вибростанке получится отличное одноэтажное здание, срок службы которого составит минимум 25 лет.
Станок для шлакоблоков: особенности изготовления
Чтобы соорудить такого рода станок, следует иметь навыки работы со сварочным аппаратом и слесарским инструментом.
В качестве главной детали самодельного станка для шлакоблока выступает матрица, которая имеет форму для установки раствора. Матрица имеет вид металлического короба, в котором имеются определенные элементы, обеспечивающие пустоты в уже изготовленном изделии.
Именно матрица и является своего рода станком, для изготовления которого потребуется наличие:
- сварочного аппарата;
- болгарки;
- тисков;
- слесарного инструмента.
В качестве материалов потребуется приобрести:
- лист металла, толщиной в 3 мм, размером в 1 м²;
- один метр стальной трубы, диаметром от 7,5 до 9 см;
- стальной полосы толщиной 3 мм, а длиной в 30 см;
- электрического мотора, мощностью до 0,75 кВт;
- крепежи в виде болтов и гаек.
Инструкция по изготовлению станка для шлакоблока своими руками:
1. Сначала определитесь с размерами изделия, которое необходимо для строительства. Возможен вариант измерения уже готового шлакоблока, промышленного производства.
2. Из металлического листа вырежьте боковые участки станка, их должно быть две штуки, а между ними присутствует перегородка. Получится короб, имеющий две равные части.
3. В пустотах остается донная стенка, толщина которой минимум 3 см. Таким образом, удастся определить высоту цилиндра, который будет ограничивать пустоты.
4. Разрежьте трубу на шесть частей, длина которых будет равняться высоте пустоты.
5. Чтобы сделать каждый из цилиндров конусообразным, необходимо произвести надрезы каждого из них до центра, а затем сжать с помощью тисков и приварить друг к другу сваркой. При этом размер диаметра станет на два миллиметра меньше.
6. Приварите цилиндры с двух сторон и соедините их между собой с длинной стороны блока. Они должны быть расположены таким образом, чтобы пустоты, которые будут образовываться в точности копировали пустоты промышленного производства.
7. К крайним участкам добавляется по пластине, размером в 3 см. Она должна иметь отверстие, которое обеспечит ее фиксацию на поверхности проушин.
8. На центральной части каждого из матричных отсеков пропилите поверхность и к ней приварите проушины. Они помогу обеспечить возможность в временном креплении ограничителей для образования пустоты. Получится механизм, с помощью которого будут производиться шлакоблоки как монолитного или и не монолитного типа.
9. Выберите одну поперечную стенку, на которую приварите болты, в количестве четырех штук. Они выступают в качестве крепежей, для фиксации мотора.
10. В стороне загрузки смеси следует приварить детали в виде фартука и лопастей.
11. Произведите зачистку и полировку всех компонентов под дальнейшее их окрашивание.
12. Сделайте пресс, форма которого будет точно такой как и сам механизм, Для его сооружения понадобится пластина, отверстия которой будут больше диаметра цилиндра на четыре миллиметра. Она должна с легкостью помещаться в короб на высоту минимум 5 см.
13. Для обеспечения удобства работы с прессом, приварите к нему детали в виде ручек.
14. Покройте все составляющие механизма с помощью антикоррозийной грунтовки, а после ее высыхания установите мотор.
15. Далее производится проверка системы на работоспособность.
Для того, чтобы из стандартного электрического двигателя сделать мотор вибрационного характера следует установить на его валовые участки приваренные болты в виде эксцентриков. Они должны совпадать в осевом пространстве. На болтах устанавливаются гайки, от величины накрута которых зависит скорость и тип вибрации.
Чертежи станка для шлакоблока:
С помощью такой матрицы изготавливают как шагающий, так и дистанционный тип станка. Чтобы ее усовершенствовать требуется иметь хороший слесарский инструмент и опыт работы с ним.
Для изготовления такого рода блоков подойдет любой материал в виде глины, опилкобетона, керамзитбетона и т.д. Стандартная смесь должна состоять из одной части песчаного наполнителя, одной части цемента и трех частей шлаковых отходов.
Очень важную роль играет коэффициент влаги, которая содержится в готовой смеси. Для ее оптимального определения достаточно осмотреть состав, он не должен разваливаться, но в то же время должен быть эластичным и хорошо держащим форму.
Именно такую заготовку укладывают в матрицу для получения готового шлакоблока. Для образования пустот рекомендуется использование стеклянных бутылок, битого кирпича или остроугольного камня.
Учтите, что перед началом работы на станке для производства шлакоблоков, следует все детали смазать с помощью масла, таким образом удастся предотвратить прилипание готовой смеси к металлу. Включение вибратора возможно на любой из стадий производства, но лучше всего это делать перед прессовкой готового блока. Кроме того, электромотор следует надежно изолировать, с помощью фартука предотвращается попадание раствора на поверхность мотора.
Уже готовые шлакоблоки должны выдерживаться на улице, летом, при температуре от +12 до +30 градусов. Для того, чтобы блоки не пересушились, их накрывают полиэтиленовой пленкой.
Оборудование для производства шлакоблоков и технология их изготовления
Изготовления шлакоблока начинают с подготовки бетонного раствора, который состоит из цемента, воды и шлака. Все компоненты смешиваются между собой бетономешалкой или смесителем. Ручной замес раствора осуществляется дольше и требует огромных физических усилий, для его осуществления.
Все работы проводят исключительно при плюсовой температуре воздуха, так как при морозе происходит застывание воды. Когда раствор готов, его засыпают в форму, которая бывает пустотной или монолитной. Стандартный размер каждого блока 39х19х18.
Далее производится уплотнение готового раствора. Данную операцию проводят с помощью пресса или вибрирования. Срок проведения вибропресса занимает минимум 30 секунд.
Когда блок имеет уже уплотненную структуру, с него снимают форму, а сам блок устанавливается на пол или на поддон. Процедура высыхания шлакоблока длится при естественной температуре воздуха, которая не должна быть менее двадцати градусов. Таким образом, удастся получить материал, пригодный для дальнейшего строительства. Во избежание пересыхания материала следует обеспечить максимальную влажность воздуха.
После высыхания шлакоблоков они приобретают дополнительную прочность и отправляются на хранение в сухое место в виде складского помещения.
В качестве сырья используются разнообразные по составу материалы. На выбор того или иного сырья влияют возможности оборудования, на котором изготавливается шлакоблок и тип сооружения, которое будет из него возводиться.
Самыми распространенными вариантами наполнителей для изготовления шлакоблоков своими руками выступают материалы в виде:
- кирпичных отходов;
- песка;
- щебня;
- золы;
- керамзита и т.д.
Количество того или иного ингредиента зависит от требований к конечной продукции.
Довольно частым составляющим для изготовления шлакоблока выступает пластификатор, который улучшает технические характеристики готового материала. Кроме того, использование пластификаторов увеличивает прочность готового здания его устойчивость перед морозом и влагой.
После изготовления шлакоблоков предстоит процесс строительства и непосредственного возведения стен из шлакоблоков. Еще один важный фактор, влияющий на качество конструкции из шлакоблока — финишная отделка и утепление готового здания.
Стандартный состав приготовления смеси для шлакоблоков состоит из:
- одной части цемента;
- девяти частей шлака;
- 50% от количества цемента воды.
Еще один вариант изготовления шлакоблоков предполагает использование:
- четырех частей мелкого отсева;
- четырех частей гранитного шлака;
- одной части цемента на 50% воды.
Производство шлакоблоков — общие требования к выполнению работ
Для изготовления качественного шлакоблока следует придерживаться таких правил:
- знать четкую рецептуру и состав смеси;
- следовать технологии изготовления шлакоблоков;
- иметь достаточно профессиональное оборудование.
Кроме того, залогом качественного шлакоблока, изготовленного в домашних условиях является использование крупного песка, доменного шлака, качественного цемента с минимальной маркой в 400. Кроме этого, требуется наличие специального оборудования, имеющего вибропресс.
Для изготовления шлака отлично подходит перегоревший уголь, который используется в качестве наполнителя. Одним из важных требований к производству шлакоблоков выступает соблюдение симметричной и ровной геометрической формы готового изделия. Так как от количества неровностей и изъянов шлакоблока зависит количество раствора, который требуется для возведения готового здания. Во избежание появления данного дефекта, следует наполнять форму до верха и даже больше, так как при проведении вибрации готовая смесь уплотняется и уменьшается в размере.
Включение виброформы происходит каждый раз с интервалом в 6-15 секунд. Далее происходит прекращение вибрации и оценка готового изделия. Если раствор находится ниже, чем крайняя черта матрицы, то на него устанавливается прижимная крышка и снова включается вибрация. Далее происходит упирание прижима в ограничитель, вибрация выключается, а форма вытаскивается с устройства.
Шлакоблоки своими руками: инструкция по изготовлению
При самостоятельном изготовлении шлакоблоков следует подбирать состав смеси исходя из типа шлакоблочного станка. Так как качество вибрации напрямую определяет свойства конечного продукта.
Предлагаем вариант стандартного рецепта для изготовления шлакоблоков:
- семь ведер шлакового наполнителя;
- два ведра песка;
- два ведра гравия;
- полтора ведра цемента;
- от полтора до трех ведер воды.
Учтите, что количество воды влияет на структуру и качество блоков. Раствор после прессования не должен растекаться. Если готовую смесь кинуть на землю и при этом она растечется, а в кулаке — снова соединится, то именно такой тип раствора подойдет для изготовления шлакоблоков.
Если для изготовления шлакоблоков используется помещение, то в нем должен присутствовать ровный пол и хорошая вентиляция, но все же, рекомендуется производить шлакоблоки на открытом воздухе.
Самодельные станки для шлакоблоков предполагают изготовление данного материала по нижеприведенной инструкции:
1. Налейте раствор в форму для шлакоблоков. Включите вибратор на пять секунд. При недостаточном количестве раствора добавляется еще немного смеси. Установите прижим, и включите вибратор еще раз. Когда прижимное устройство находится на ограничителях, то процесс изготовления считается завершенным.
2. Происходит включение виброформы еще на 8 секунд и далее форму вынимают без выключения вибратора.
3. Сушка блоков занимает период времени от четырех до девяти дней. Полная прочность достигается по истечению месяца. Главными условиями их хранения выступает высокая влажность и температура.
4. Транспортировка блоков в помещение происходит по истечению минимум дня, после их изготовления. При наличии пластификатора в составе для приготовления шлакоблоков, их транспортировка происходит через шесть часов, после изготовления.
5. Хранение шлакоблоков происходит в виде пирамиды. По истечению нескольких месяцев, они становятся пригодными к строительству.
| |||||
| |||||
Коса – заточка, отбивка, крепление и использование | Своими руками
Косить вручную обычной косой я начал в 12 лет – этому искусству меня научил отец. Сейчас мне 75, полностью обработать свой участок таким способом мне уже не под силу, и я перешел на кошение газонокосилкой собственной конструкции.
Но старушку косу не выбросил!
Время от времени, чтобы вспомнить молодость и немного размяться, беру ее в руки. Думаю, она всегда пригодится на даче, хотя бы для кошения крупных сорняков которые не возьет н игазонокосилка ни триммер. Поэтому хочу поделиться опытом кошения.
Прежде всего, нужны начальные сведения о самой косе. Это инструмент, состоящий из ножа, косовища, ручки и крепежного устройства ножа на косовище (рис. 1 и 2).
Нож согласно ГОСТу (который, несмотря на все события последних десятилетий, никто не отменял) должен изготовляться из инструментальных сталей марок У7А, У8 и У8А. Он должен быть термически обработан. Сам нож включает в себя элементы, показанные на рис. 3. Однако качество ножа не всегда бывает на высоте (вот они, результаты нового времени). Поэтому перед приобретением надо внимательно осмотреть его. На поверхности не должно быть трещин, расслоений, углублений или выступов.
Полотно ножа должно быть ровным и одинаковой толщины в сечениях.
Это проверяется приложением к полотну каких-нибудь небольших ровных пластинок, например металлических уголков.
Далее нужно проверить термообработку. Удерживая нож за пятку, ударьте его по обушку массивным деревянным предметом. Чистый ясный звук говорит о хорошем качестве металла. Если звон глухой и прерывистый, то такой нож вряд ли сослужит вам хорошую службу.
Еще одно испытание: взяв нож за пятку, уприте его носиком в деревянную поверхность и слегка надавите на него. Если полотно изогнется равномерно, а после снятия нагрузки примет исходную форму, то все в порядке. Если же останется прогиб, значит, термообработка ножа была выполнена из рук вон плохо. Можно проверить ее и с помощью гвоздя. Проведите им поперек лезвия. Если металл хорошо закален, то с гвоздя снимется небольшая стружка. Если же он скользит и стружки нет, то такой нож лучше не брать. Изготовители могут сэкономить и на заточке лезвия.
Проверить это просто: плоским надфилем мелкого рифления проведите по лезвию. Если все нормально, надфиль скользит, если нет – снимает с металла стружку.
Не найдет коса на камень
Косовище должно быть упругим и прочным. Покупая готовое, обратите внимание, чтобы на нем не было искривлений, сучков и других дефектов. Длина его должна быть 1700-2000 мм, сечение – 40×40 с фасками по длине до утолщения. Посередине утолщения устанавливается ручка в сторону, противоположную скосу, под установку ножа – на уровне пупка косаря, с небольшим наклоном вправо от плоскости среза (рис. 4).
Смотрите также: Косилка, электромотоблок, мельница-крупорушка своими руками – чертежи
Можно сделать косовище своими руками
Лучший материал – молодая ель. Ее сушат в вертикальном положении в тени. Клин изготовляют из прочного сухого дерева (акации или дуба).
Ручку можно сделать подвижной (рис. 5). Для этого используют свежесрезанную ветку ивы или черемухи. Затем ее изгибают по косовищу круглого сечения и закрепляют шпагатом. Внизу косовища делают срез под установку пятки ножа.
Его наклон выбирают таким образом: ставят косовище насровную поверхность в положении кошения и предварительно установленным ножом. Подъем лезвия должен составлять 10-20 мм. После выполнения скоса прикладывают пяту ножа и отмечают, где должен утапливаться шипик (рис. 6 и 7).
Захват косы имеет большое значение. Он зависит от твердости, густоты и сочности травы и устанавливается при помощи шнура (рис. 8). Для более мягких трав устанавливается положительный захват в пределах от 0 до 20 мм. Для твердых трав захват устанавливают отрицательный. В этом случае косить можно с меньшими усилиями и качественнее.
Читайте также: Как правильно наточить инструменты
Заточка и отбивка косы своими руками
Вначале производят предварительную заточку лезвия с нижней стороны на ширину 15-20 мм и до половины первичной толщины ножа на мелкозернистом абразивном круге. При этом металл нужно постоянно охлаждать водой, не допуская перегрева. Частота вращения абразивного круга должна быть небольшой. После этого нож нужно отбить.
Как отбить косу
Эта сложная и ответственная операция. Косу отбивают с лицевой стороны полотна на ширину 1,5-2,5 мм с помощью специального узкого отбойного молотка и широкой бабки (рис. 9J. Отбивку начинают от пятки и ведут, смачивая носок молотка в воде, к самому кончику.
В результате отбивки лезвие получается тонким по всей длине и уплотняется за счет наклепа. Поверхность бабки и бойка должны быть отшлифованы. При отбивке нож лучше снимать с косовища.
Удары нужно наносить параллельно лезвию полотна, смещая на шаг (около 1 мм) и не прикладывая усилий. Нельзя наносить удары поперек полотна, наискось или несколько раз по одному и тому же месту.
Опыт отбивки приходит при тщательном внимании и терпении.
Восполнит отсутствие опыта косо-отбой, который вы можете приобрести в магазине или на рынке.
Во время работы нужно иметь при себе брусок для подточки и мусат (специальный металлический стержень) для правки лезвия.
В заключение хочется сказать о приемах кошения. Учатся этому много лет у опытных мастеров. Приемы у каждого свои, и описать их трудно. Общие указания – это не «рубить», а делать плавные движения. При взмахе пятка должна идти почти по поверхности, а носок – быть слегка приподнятым. Правая нога выставляется вперед, а левая приставляется. Туловище слегка наклоняют вперед. Взмах сопровождается небольшим поворотом туловища и по времени примерно в два раза продолжительнее резания травы.
Заточка, отбивка и насадка косы
Рис 1. Устройство косы:
1-нож. 2-косовище, 3-ручка. 4-клин, 5 – кольца, 6 – утолщение.
Вариант крепления ножа к косовищу 2-мя винтами и скобой:
1 – косовище, 2 – пятка ножа, 3-скоба, 4-винт М6, 5 – гайка М6, б – шайба пружинная.
Вариант крепления ножа скобой: 1 – скоба, 2 – планка, 3 – винт Мб -1. Рис. 2. Крепление ножа косы
Рис. 3. Устройство ножа: 1 – полотно, 2 – обушок, 3-лезвие, 4-пятка, 5 – носик, 6-шипик.
Рис. 4. Устройство косовища: 1 – косовище, 2 – утолщение, 3 – ручка,4 – скос.
Рис. 5. Ручка: 1 – ручка прямая, 2 – ручка изогнутая, 3- шпагат, 4 – косовище, 5 – фаска, 6 – выборка под шпагат, 7 – выборка для изгиба.
Рис. 6. Высота подъема лезвия: 1 – косовище, 2 – лезвие ножа, 3 – полотно ножа,
4 – опорная поверхность.
Рис 7. Выборка под шипик: 1 – косовище, 2 – пятка ножа, 3 – шипик, 4 – скос косовища, S – выборка под шипик.
Рис 8. Установка захвата косы: 1 – косовище, 2 – нож, 3- ручка, 4-шнур.
Рис 9. Инструмент для отбивки косы: 1 – бабка с широкой наковальней, 2 – молоток с узкими бойками, 3-емкость с водой.
С.Л ПРОХОРОВ.
На заметку
Затачивать лезвие косы в полевых условиях нужно с помощью оселка – продолговатого бруска-«наждачки».
Заточку производят по диагонали от пятки к носку, при этом брусок должен находиться под небольшим углом к плоскости лезвия, обрабатывать которое надо попеременно с обеих сторон.
Косы, руки и мотор
Вверху автор много полезного написал о настройке косы, но я все-таки хочу немного дополнить его рассказ.
Мое детство прошло в селе. В пору сенокоса мужиков из колхоза направляли косить вручную там, где механические косилки не могли взять траву. И мы, пацаны, всегда сбегались туда. Интересно нам было. А когда самого знатного косаря, видавшего виды деда, сажали клепать косы (а при постоянной работе каждую надо было править по три-четыре раза в день), то начиналось настоящее преставление. Так вот тот дед клепает и нам подробно рассказывает про каждую деталь, что и как с ней надо делать. После таких уроков даже самые ленивые и непонятливые из нас начинали управляться с этим делом. Эх, где бы сегодня таких учителей найти… Косил тот дед – как в балете танцевал, красиво работал. После него лужок вроде как выбритый был.
Итак, начинать все нужно с правильного выбора косы.
Самой ходовой, то есть, можно сказать, универсальной, считается №6. Это означает, что длина лезвия у нее 60 см. Коса №7 тоже неплоха, но она больше подходит для ровной местности, да и управляться с ней тяжелее. Есть еще №8 и 9, ими все срезать можно, но работать с ними могут только физически очень крепкие люди. Номера, кстати, ставят на пятках косы, рядом с клеймами. Ну, значит, выбрали себе инструмент – пора готовить косу к работе.
Тут вот в чем суть: косу надо начинать клепать только с середины, а нес пятки или носка, иначе ее поведет волнами и тогда пиши пропало. И самое главное – два раза бить по одному месту нельзя!
Значит, кладем косу на бабку плужком вниз, мелом отмечаем примерный центр и средней силы ударами молотка клепаем в направлении носика. Затем опять с середины к пятке. С каждым заходом удары делаем все слабее и слабее, а последний так совсем легонький. Если коса забита (то есть ее давно не клепали), проходим по ней молотком 8-10 раз. Во время этой операции заодно можно узнать и то, на что коса способна. Если за два-три прохода металл расклепывается, значит, она оставляет желать лучшего.
От выбора косовища тоже многое зависит. Лучшее для него дерево – осина или ель, а оптимальная его длина – 2 м. На уровне пупка крепим к нему ручку. В идеале ее нужно не покупать в магазине, а делать самому, чтобы она, как говорится, по руке была. И если все сделано как надо, то косить вручную – одно удовольствие. Правда, мне уже за 60 лет, и скашивать большие площади во время сенокоса (особенно если это нужно сделать быстро из-за надвигающейся непогоды) стало затруднительно. В этом случае хороший вариант – мотокоса.
Дело техники
Работая этим инструментом, я не устаю совсем, да и клепать ее не нужно. И про частое затачивание оселком можно тоже забыть. Ручной косой кошу, пока роса (не зря же раньше говорили: «Роса долой – и мы домой»), иначе не скашивать будешь, а рубить. Мотокосой же в любое время можно работать. Это и обсудим.
Прежде чем покупать мотокосу, нужно четко осознать, для чего она вам нужна. Для заготовки сена лучше всего подойдет агрегат мощностью 1,2-1,5 кВт и объемом движка не менее 30 куб. см, иначе густую высокую траву будет проблематично срезать.
Можно, конечно, и более мощную косу купить, но тогда расход бензина увеличится. Тут уже вам решать, что удобнее и выгоднее. А вообще-то, один работник с мотокосой заменяет почти троих косарей с ручным инструментом.
Для небольшого участка подойдет коса китайского производства – она дешевле. Должен сказать, что если фирма-производитель действительно чисто китайская (это по названию сразу можно понять), то качество ее продукции вполне себе нормальное. Но если планируется интенсивная эксплуатация, то тогда лучше подкопить денежек и купить фирменную в фирменном же магазине. И с этим делом нужно быть крайне осторожным и внимательным, потому что именно подделки под громкие марки качеством точно не блещут. Мне известен случай, как мужик купил подобный инструмент за бешеные деньги, а через неделю там все заклинило. Отнес агрегат в гарантийку, и только там ему сказали, что он приобрел подделку. Вообще, нынче подделывают так искусно, что кто не знает нюансов, то примет все за чистую монету.
Например, на оригинальных изделиях обязательно должен быть выбит серийный номер. Нет его – остерегайтесь.
И хочу сказать об одной важной вещи, о которой многие дачники просто забывают или не обращают на нее внимания. Когда закончился сезон и вы убираете мотокосу до следующей весны, то обязательно удалите из бачка все топливо. Сливать его не нужно (зачем загрязнять землю?), просто заведите мотор, и пусть он работает, пока не остановится. Заодно и карбюратор таким образом прочистите, иначе присадки, которые содержатся в бензине, за зимние месяцы повредят эластичную мембрану. Пару раз забудете это сделать – и меняйте карбюратор, а это треть стоимости косы. В общем, приятной всем работы с косами -ручными и бензиновыми!
© Автор: Юрий Григорьевич ТЕМНЕНКО. г. Смела Черкасской обл.
ИНСТРУМЕНТ ДЛЯ МАСТЕРОВ И МАСТЕРИЦ, И ТОВАРЫ ДЛЯ ДОМА ОЧЕНЬ ДЕШЕВО. БЕСПЛАТНАЯ ДОСТАВКА. ЕСТЬ ОТЗЫВЫ.Ниже другие записи по теме «Как сделать своими руками — домохозяину!»
Подпишитесь на обновления в наших группах и поделитесь.
Будем друзьями!
Лучшая машина для измельчения древесных опилок для экономии времени и ресурсов Местное послепродажное обслуживание
Если вы думаете о повышении эффективности дробления и обработки древесины, большой набор. Станок для опилок представит вам идеальные решения. Безупречный. Станок для опилок древесины бывает разных типов, включающих множество моделей и размеров. Таким образом, вы можете найти наиболее подходящие модели для вашего личного использования или крупномасштабных приложений. Станок для опилок подходит как для малых, так и для крупных работ.
Материалы, из которых изготовлен. Станок для опилок древесины исключительно прочные и надежные, что обеспечивает им долгий срок службы и прекрасное обслуживание. При работе с любым типом оборудования безопасность операторов является критическим фактором. Файл. Станок для опилок на Alibaba.com может похвастаться звездными механизмами, которые защищают операторов от любого вида риска. Благодаря передовым технологиям и новейшим изобретениям они. Станок для опилки древесных опилок в зависимости от марки обеспечивает отличную топливную и электрическую энергоэффективность. Соответственно, вы можете существенно сэкономить на счетах за топливо и электроэнергию.
The. Станок для опилок , доступный здесь, позволяет множеству людей беспрепятственно решать свои задачи благодаря простоте установки и обслуживания. Их дизайн отличается заметными деталями, которые позволяют пользователям запускать их без технических сбоев. Легко доступные запасные части и ремонт делают их еще более удобными. опилочная машина . Благодаря невероятным характеристикам шумоподавления расширение. Станок для опилок также чрезвычайно удобен в работе.
Станьте свидетелем оптимального соотношения цены и качества, испытав непреодолимые атрибуты. Просмотрите Alibaba.com и найдите что-то интересное. Станок для опилок предлагает самые подходящие предложения в соответствии с вашими требованиями. Время, которое вы сэкономите, и эффективность, которую вы поймете, продемонстрируют, почему эти заманчивые продукты стоят каждого доллара по своей цене.
Электрическая молотковая дробилка для древесины для производства опилок
Зачем нужна электрическая молотковая дробилка по дереву?
Как мы все знаем, машина для производства древесных гранул является ключевым элементом для производства биопеллет из опилок. Хотя не все материалы подходят для непосредственного гранулирования, некоторые материалы диаметром более 5 мм необходимо сначала измельчить до опилок или частиц порошка. Электрическая молотковая мельница для дерева может помочь измельчить большие деревянные ветки или стебли соломы до мелких ячеек.Мы поставляем два типа молотковых дробилок для дерева, разница между электрической молотковой дробилкой для дерева и дизельной молотковой дробилкой . заключается в двигателе, первый — в двигателе, а второй — в дизельном двигателе. Вы можете выбрать любого, исходя из вашего более дешевого энергоресурса. Кроме того, вы также можете выбрать дробилку древесины в зависимости от вашего сырья. Если ваш материал представляет собой бревна, вам необходимо использовать дробилку древесины для предварительной обработки перед дробилкой древесины или молотковой дробилкой для дерева.
CF158 молотковая мельница по дереву | CF198 молотковая мельница по дереву | CF500B молотковая мельница для дерева |
Характеристики и преимущества электрической молотковой дробилки для дерева
1. Экономия электроэнергии: самая маленькая мощность молотка по дереву составляет всего 2,2 кВт, лучший выбор для домашнего использования.
2. Безопасный в эксплуатации, низкий уровень шума, стабильная работа.
3. Низкая частота отказов, простота эксплуатации и низкие затраты на техническое обслуживание.
4. Может обрабатывать сырье различного или нестандартного размера до древесных частиц одинакового размера.
Применение электрической молотковой дробилки для дерева
1. Сырье: Электрическая молотковая мельница для дерева подходит для обработки относительно мягкого сырья, такого как древесная ветка, солома пшеницы, стебли кукурузы, стебли хлопка и т. Д.
2. Электрическая молотковая дробилка для древесины может использоваться в производстве древесных гранул , производстве брикетов из биомассы, производстве гранул для кормов для животных или в бумажной промышленности.
Технические характеристики дробилки для дерева
Модель | CF158 | CF198 | CF420 | CF-420C | CF500B |
Мощность | 2. | 4 кВт | 7,5 кВт | 11 кВт | 22 кВт |
Напряжение | однофазный / трехфазный 220 В / 50 Гц | трехфазный 380 В / 50 Гц | трехфазный 380 В / 50 Гц | трехфазный 380 В / 50 Гц | трехфазный 380 В / 50 Гц |
Вместимость | 60-120 кг / ч | 200-300 кг / ч | 200-500 кг / ч | 200-700 кг / ч | 800-1100 кг / ч |
Размер экрана | 360 * 160 мм | 510 * 200 мм | 680 * 280 мм | 680 * 280 мм | 820 * 390 мм |
Поперечный размер | 48 * 58 * 63 см | 97 * 75 * 64 см | 112 * 82 * 107 см | 112 * 82 * 107 см | 124 * 97 * 106 см |
Машина для производства древесного угля для продажи
Станок для производства древесного угля Beston способен превращать опилки в высококачественный древесный уголь и не наносить вреда окружающей среде. Поскольку древесные опилки широко используются в повседневной жизни человека и в обрабатывающей промышленности, опилки имеют большой потенциал для вторичной переработки. В основном древесные опилки могут быть превращены в активированный уголь или с помощью машины для производства древесного угля для производства древесных брикетов.
Все отходы биомассы, которые вы можете себе представить, такие как древесина, скорлупа кокосов, скорлупа пальм, жмых сахарного тростника, можно карбонизировать в древесный уголь. Поскольку использование древесного угля из опилок очень велико, эта машина считается очень прибыльной на рынке.
Использование древесных опилок
- Повседневная жизнь: после брикетирования может широко использоваться в сфере общественного питания, например, в качестве топлива для барбекю и топлива в других местах, таких как обогреватель
- Сельское хозяйство: Может использоваться в качестве удобрения для улучшения качества почвы и увеличения урожайности зерна
- Промышленность: дальнейшая переработка в активированный уголь; используется как строительный кирпич с глиной; используется в качестве топлива на металлургических заводах, заводах по производству керамики и т.
д.
Помимо древесного угля, в процессе производства опилок образуются также биогаз, древесный уксус и деготь.Биогаз также можно использовать в качестве топлива. Древесный уксус можно использовать для производства пестицидов, а смола — сырье для производства резиновых изделий, красителей, пестицидов и т. Д.
Тарвудский уксусБиога использует«Один огонь — два шага» — новый дизайн отопительной конструкции
Помимо рентабельности, машины для производства древесного угля Beston обладают конкурентоспособной высокой производительностью и низким потреблением энергии благодаря новой системе отопления. Эта система нагрева, как следует из названия, использует один огонь для нагрева двух основных частей машины, системы сушки и печи карбонизации.Чтобы повысить эффективность нагрева, мы используем «Durable Layer Design» для двух частей с сушильным узлом снаружи и печью для карбонизации внутри него. Следовательно, огонь может нагревать систему карбонизации напрямую, а остаточное тепло от процесса карбонизации можно использовать для нагрева сушильной машины одновременно.
Характеристики машины для производства древесного угля Beston
- Высокая эффективность работы.
- Энергосбережение. Система отопления «One Fire Two Steps» и конструкция Durable Layers позволяют сэкономить много топлива, чтобы снизить расходы клиентов.
- Экологичность. Отработанный газ и дым будут очищены от серы, очищены от пыли и охлаждены перед выпуском. Мы следим за тем, чтобы выбросы соответствовали Европейскому стандарту выбросов в окружающую среду.
- Очень безопасно работать. Мы добавляем специальный кожух для сушильного узла и узла карбонизации, чтобы операторы не травмировались.Клиенты могут выбрать центральную систему управления для разделения оператора и машины для карбонизации опилок. У нас есть стандартная система управления мощностью, чтобы гарантировать безопасную работу машины. Кормление и разгрузка происходят в закрытой среде, чтобы обеспечить безопасные и хорошие условия для работы.
Как сделать древесный уголь из опилок
- Устройство подачи постоянного веса перемещает опилок в узел карбонизации машины с помощью ленточного конвейера.Во внешнем слое опилки сушатся, а затем свободно падают на внутренний слой для карбонизации. Или клиенты могут выбрать независимый сушильный агрегат для процесса сушки, который проиллюстрирован выше.
- В печи карбонизации опилки превращаются в карбид в результате высокотемпературного разложения. После выпуска дыма и выделения серы древесный уголь обуглится из опилок.
- Затем древесные опилки будут выгружены из порта выгрузки порошка.В процессе карбонизации остаточное тепло будет использоваться для нагрева сушильной машины для экономии энергии.
- В связи с тем, что Beston Group уделяет большое внимание охране окружающей среды, мы уделяем большое внимание выбросам в процессе производства. Горючий газ, образующийся в процессе пиролиза опилок, поступит в гидрозатвор и удалит серу и пыль, а затем после распыления воды и очистки они попадут в конденсатор и разделятся на древесный уксус и деготь.
Основные параметры
Машина для производства древесного угля из опилок для продажиМодель | БСТ-05 | БСТ-10 | БСТ-30 | БСТ-50 |
Вместимость | 0,3-0,5 т / ч | 0,8-1т / ч | 2,5-3т / ч | 4,5-5т / ч |
Метод работы | Полностью непрерывный | |||
Сырье | 1.Все виды отходов биомассы, такие как опилки, скорлупа кокосов, скорлупа оливок, скорлупа пальм, бамбук и т. Д. | |||
2. Гражданский ил, городской ил, промышленный ил и т. Д. | ||||
3. Твердые бытовые отходы, пищевые отходы. | ||||
Размер реактора | Φ820 мм | Φ1000 мм | Φ1300 мм | Φ1700 мм |
Нагревательные материалы | Древесный уголь, древесина, дизельное топливо, природный газ, сжиженный нефтяной газ, биомасса и т.![]() | |||
Энергопотребление | 45 кВт / ч | 65 кВт / ч | 90 кВт / ч | 125 кВт / ч |
Размеры | 28 м * 10 м * 6 м | 33 м * 13 м * 7 м | 40 м * 15 м * 8 м | 50 м * 16 м * 10 м |
Масса | 28 т | 35 т | 45т | 54т |
Рабочее давление | Незначительное отрицательное давление | |||
Срок службы | 5-8 лет |
Как один из ведущих поставщиков оборудования для производства древесного угля в мире, Beston может предложить вам разумную цену.Все наши заводы по переработке вторсырья отличаются высокой производительностью и хорошей репутацией на мировом рынке. Если вы ищете хороший способ переработать отходы биомассы в древесный уголь, наша угольная машина станет для вас идеальным выбором. Мы обещаем внимательное послепродажное обслуживание и верим, что клиенты получат прибыль от предоставляемого нами оборудования.
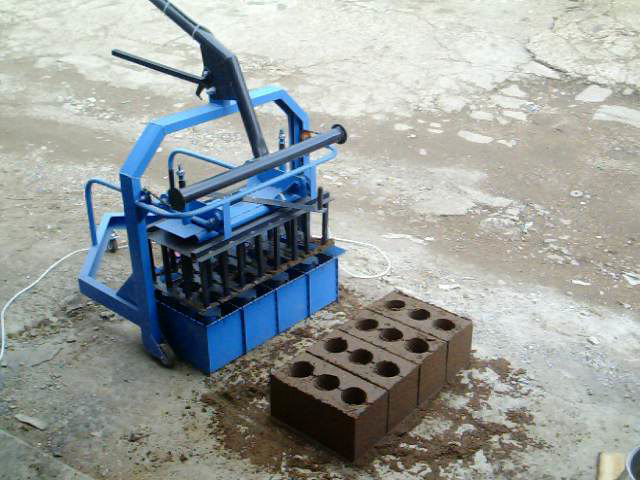
Оценка стоимости производства и качества сырья, производимого опилочной машиной
https: // doi.org / 10.1016 / j.biombioe.2017.06.010Получить права и контентОсновные характеристики
- •
Гусеничный опилочный станок может быть экономичным вариантом при производстве опилок толщиной 2–4 мм.
- •
Измерялось качество измельчаемого сырья. Средняя геометрическая длина частиц составляла от 4,4 до 5,3 мм.
- •
Насыпная плотность опилок колебалась от 235,87 до 281,55 кг / м 3 .
- •
Использованные ножи из вольфрамового сплава не изношены при измельчении 60 зеленых метрических тонн.
Реферат
Использование лесных остатков в качестве сырья древесной биомассы для производства биоэнергии и биопродуктов требует обработки (т. Е. Измельчения) в соответствии со спецификациями сырья, такими как содержание влаги и размер частиц. Целью данного исследования было определить влияние стеблей обработанной твердой древесины (SH) малого и большого диаметра (SS и LS) на производительность и стоимость гусеничной машины для обработки опилок, производящей опилки.Кроме того, оценивали содержание влаги, гранулометрический состав, насыпную плотность и влияние износа ножей. Двигатель опилочной машины мощностью 298 кВт был способен измельчать все типы материалов, кроме левого ствола. Производительность машины варьировалась от 18,3 до 26,7 метрических тонн в сухом состоянии (BDmT) / производительный машинный час (PMH) при стоимости 5,3 и 3,6 доллара США за BDmT соответственно. Влажность материала, использованного в исследовании, составляла от 26 до 36%. Средняя геометрическая длина частиц для SH, SS и LS составляла 4.7, 5,3 и 4,4 мм соответственно. Машина не может обрабатывать LH материалы из-за ограниченной мощности. Насыпная плотность производимого сырья варьировалась от 234 до 281 кг / м 3 . Анализ показал, что износ ножей не оказал значительного влияния на производительность измельчения и качество исходного сырья при измельчении 60 сырых метрических тонн (GmT) лесных остатков.
Результаты этого исследования показывают, что эта установка для опилок может быть полезна при производстве сырья для новых технологий преобразования биомассы, которые требуют небольших однородных частиц.
Ключевые слова
Древесная биомасса
Биоэнергетика
Микро-измельчитель
Измельчение
Рекомендуемые статьиЦитирующие статьи (0)
Полный текст© 2017 Elsevier Ltd. Все права защищены.
Рекомендуемые статьи
Ссылки на статьи
Всего один комплект опилок превратит древесные бревна в опилки напрямую.
I. Введение: Благодаря применению передовых технологий наша установка для обработки опилок может обрабатывать бревна, ветки, корни деревьев, бамбук, плиты, деревянные блоки и любые виды твердого пластика, ПВХ, бумажных труб, химических материалов и т. Д.Отличающаяся простотой эксплуатации и обслуживания, эффективной производительностью, широким спектром применения, высокой степенью автоматизации и т. Д., Установка для опилок может эффективно измельчать вышеуказанное сырье до мелких частиц размером 3-5 мм.
Станок для опилок SMX
Вид сбоку на опилочную машину
Я Я . Технические данные:
Модель | SMX-210 | SMX-350 |
Основная мощность (кВт) | 37 | 132 |
Производительность (т / ч) | 2-3 т / ч | 5-6 т / ч |
Размер загрузочного отверстия (мм) | 210×210 | 350×350 |
Фрезерный барабан (мм) | 420×225 | 600×380 |
Размер фрезы | 5 * 6 * 45 мм | 5 * 6 * 45 мм |
Напряжение | 380 В / 50 Гц | 380 В / 50 Гц |
Размер (мм) | 1800x900x1400 | 3000x1850x1800 |
Я Я Я .

1. Энергосбережение с гидравлической системой подачи;
2. Бесплатная эксплуатация и обслуживание;
3. Низкий уровень шума;
4. Высокая прочность и стабильное производство;
5. Высокая производительность с немецкими ножами.
Обзор опилочной машины
Пояс для кормления
Бревно
Опилки
Дробилка для опилок
на продажу, Производитель измельчителя древесных опилок
Дробилка для опилок Продажа
1- Измельчитель древесных опилок: Измельчитель древесины может одновременно перерабатывать древесину, ветки и другое сырье в опилки, что подходит для измельчения толстых материалов, блоков твердых материалов и материалов высшего класса.
2- Применяемые материалы: Остаточные материалы обработки (такие как ветви, ветки, лист, рейки, сердцевина круглой древесины, отходы фанеры, древесные отходы и т. Д.)
3- Мощность: 15кВт-55кВт | Производительность: 1-4т / ч
Модель | GY-600 | GY-800 | GY-1000 |
Диаметр ножевого ролика (мм) | 600 | 800 | 1000 |
Дробилка балок кол-во | 32 | 42 | 52 |
Количество лезвий для стружки | 3 | 4 | 4 |
Длина балды | 200 | 250 | 340 |
Питающий порт | 160 × 180 | 200 × 220 | 300 × 320 |
Скорость (об / мин) | 1400 | 1200 | 1000 |
Мощность двигателя | 15-18.![]() | 30 кВт | 55 кВт |
Дизель | 32HP | 40 л.с. | 75HP |
Вместимость | 1-2т / ч | 2-3 тонны / ч | 3—4 тонны / ч |
Размеры: Д * Ш * В (см) | Д130 × Ш98 × В73 | Д200 × Ш100 × В230 | L230 × W175 × h330 |
Вес (кг) | 800 | 1400 | 2200 |
Нажмите, чтобы увидеть GY216 / GY218 Барабанная дробилка для древесины на продажу (Мощность: 55–110 кВт | Производительность: 5-10 т / ч)
Нажмите, чтобы увидеть Продается измельчитель древесины с большим интегрированным барабаном (Мощность: 110–315 кВт | Производительность: 15-40 т / ч)
Стационарный интегрированный измельчитель древесины
Гусеничная мобильная интегрированная дробилка древесины
Интегрированный измельчитель древесины с резиновыми шинами
Принцип работы измельчителя древесных опилок
Машина для опилок использует ножевую резку и высокоскоростной воздушный поток, а также интегрирована функция двойного ударного дробления, которая может одновременно выполнять отделение и обработку микроматериалов. В процессе резки и шлифования лезвия ротор создает высокоскоростной воздушный поток, который вращается вдоль направления резания лезвия, и материал ускоряется в потоке воздуха, и повторное воздействие подвергает материал двойному измельчению при в то же время, тем самым увеличивая скорость измельчения материала.
Характеристики
1. Весь комплект оборудования приводится в движение только одним двигателем, простой по конструкции и компактной компоновки, дешевый по цене, стабильный в работе, низкое энергопотребление, высокая производительность, хорошее качество готовой продукции из опилок и низкая стоимость обработки. .Его можно использовать для резки бамбука, соломы, стеблей кукурузы, стеблей сорго и т. Д. Станок для опилок также может использоваться в качестве сырья для ДСП и опилок.
2. Станок для опилок в основном состоит из устройства для резки стружки, устройства для измельчения и вентилятора, и особенно подходит для обработки опилок в среде для выращивания съедобных грибов. Размер древесной стружки после резки устройством для резки стружки невелик, и ее можно отправить в устройство дробления для дальнейшего измельчения без сушки.
Сопутствующая машина для продажи
Дробилка для садовых веток Продажа
Дробилка для пней на продажу
Enerpat UK Scrap Wood опилок для продажи на продажу
Приложения для этого продукта
дрова
журналов
древесный лом
ветка
лом Мебель
Характеристики этого продукта
- Эта машина для опилок предназначена для производства древесных опилок желаемого и подходящего размера, чтобы иметь возможность использовать их во многих областях применения.древесные опилки могут использоваться для создания механизма древесного угля, выращивания грибов, выращивания черных грибов, обработки грибов Agaricus bisporus, обработки МДФ, обработки древесностружечных плит, обработки древесноволокнистых плит, производства благовоний дзен и противомоскитных спиралей, сырья для бумажной массы, изготовления древесного угля и другие функции.
- Автоматическая машина для производства древесных опилок enerpat ESM-55 — это одна приводная машина мощностью 55 кВт, используемая для производства древесины из дров, бревен и древесных отходов. Наша машина для опилок поставляется с функцией автоматической переустановки при подаче древесины большого размера в машину , которые не могут обрабатываться, функция повторной установки защитит машину и вернет древесину.
- Эта машина для производства опилок специально производит опилки от древесного бревна до опилок всего за один этап, без молотковой мельницы и измельчения, всего за одну измельчительную мельницу. Мельница для измельчения производит частицы размером 2-4 мм или по требованию клиента размер не более 10 мм. Многие европейские производители древесных гранул меняются и используют там процесс древесных гранул вместо молотковой мельницы. Он прост и удобен в эксплуатации, а барабанный нож ремонтируется быстро, а срок службы ножа измельчительной мельницы составляет 1000 часов, доступный на обычной шлифовальной машине для бритья камня.
Производительность измельчителей (опилок) составляет от 25 м3 / ч до 75 м3 / ч, в зависимости от вашей производительности по разгрузке.
Почему выбирают этот продукт
- Модный дизайн
- Высокое качество с CE и ISO
- Конкурентоспособная цена
- Многофункциональность для конечных продуктов: оригинальные материалы для древесных плит; источники тепла.
Технические характеристики данного продукта
Модель | ESM-55 |
Блок питания | 2x380V 50 Гц 37A |
Мощность двигателя (кВт) | 55 |
Уровень шума (дБ) | 65-68 |
Размер подачи | 210 х 210 |
Дробильная камера ДхШ (мм) | 420 х 220 |
Пропускная способность (м3 / ч) | 10 |
Насос (мл / об) | 5 |
Объем масла (л) | 100 |
Тип масла | ISO № 46 |
Длина станка (мм) | 5300 |
Ширина машины (мм) | 900 |
Высота машины (мм) | 1400 |
Масса станка (т) | 3.![]() |