Шпалы железобетонные, бетонные шпалы, прайс на железобетонные шпалы ГОСТ 10629-88 – РемСтройПуть
Наименование | ГОСТ | Ед.изм. | Цена | Наличие |
---|---|---|---|---|
шт | по запросу | |||
шт | по запросу |
Шпала железобетонная, выполненная из высокотехнологичного армированного материала, уверенно вытесняет традиционные деревянные изделия. Это связано с простотой монтажа и обслуживания, долговечностью и прочностью этого типа шпал.
Ж/б шпалы Ш-1: прочность и долговечность железнодорожного пути
В процессе строительства, реконструкции или ремонта железнодорожного пути железобетонные шпалы укладываются на балластный верхний слой пути (подушку из гравия/щебня). Выполненная в соответствии со стандартами шпала ш1 принимает давление от рельсов и/или промежуточных скреплений, передает его на балластный слой или подшпальное соединение, обеспечивая тем самым неизменность расположения рельсовой нити.
На всех этапах работ в сфере обслуживания железнодорожного пути неизменной популярностью пользуются шпалы ш 1 — железобетонные изделия, выполненные из тяжелых марок бетона и дополнительно армированные стальной проволокой. Шпала является основным элементом для обустройства железнодорожных путей с шириной рельсовой нити до 1520 мм.
В зависимости от прочности, трещиностойкости, качества бетона и геометрических параметров выделяется жб шпала 1 и 2 сорта. Изделия 2 сорта применяются для обустройства станционных, малодеятельных и подъездных путей, а изделия 1 сорта актуальны при обустройстве путей с повышенной проходимостью.
Если сравнивать бетонные шпалы с деревянными аналогами, то ж/б изделия значительно выигрывают по техническим и эксплуатационным параметрам: прочность, морозостойкость, простота обслуживания и длительный период эксплуатации (не менее 50 лет).
Все жб шпалы, представленные в каталоге компании «Ремстройпуть», выполнены в полном соответствии с ГОСТ 10629-88 и отраслевыми стандартами. Каждая партия шпал из прочного железобетона сертифицирована для продажи и эксплуатации на территории РФ, стран СНГ и Таможенного Союза.
Стоимость, варианты и сроки оплаты, способ доставки — это индивидуальные предложения для каждого заказчика: самовывоз с территории складов компании или доставка любым типом транспорта, наличный/безналичный расчет и скидки для крпунооптовых покупателей.
Заказать железобетонные шпалы можно в офисе компании «Ремстройпуть» (г. Екатеринбург, ул. Таганская, д. 55 а, 3 этаж). Наши менеджеры готовы предоставить качественную консультацию при выборе шпал по телефону (343) 228-34-34, а также по электронной почте — [email protected].
Шпалы железобетонные: | |||
---|---|---|---|
Шпалы Ш 1-1 (угол наклона упорных кромок подрельсовых площадок в шпалах 55º) | применяется для раздельного клеммно — болтового скрепления КБ с болтовым прикреплением подкладки к шпале | ГОСТ 10629-88 | |
Шпалы Ш 1-2 (угол наклона упорных кромок подрельсовых площадок в шпалах 72º) | применяется для раздельного клеммно — болтового скрепления КБ с болтовым прикреплением подкладки к шпале | ГОСТ 10629-88 | |
Шпалы Ш 2-1 | применяется для нераздельного клеммно-болтового рельсового скрепления БПУ с болтовым прикреплением подкладки или рельса к шпале | ГОСТ 10629-88 | |
Шпалы Ш 3 | применяется для нераздельного клеммно-болтового скрепления ЖБР65 с болтовым прикреплением рельса к шпале | ГОСТ 10629-88 |
Шпалы ШС-АРС | применяется для анкерного рельсового скрепления | ||
Расположение арматурных элементов в железобетонных шпалах: | |||
Шпалы Ш 1-16*5 | шпалы с высокопрочной проволочной арматурой периодического профиля диаметром от 3 до 5 мм | ГОСТ 10629-88 | |
Шпалы Ш 1-4*10 | шпалы с высокопрочной стержневой арматурой периодического профиля диаметром стержней от 7 до 12 мм | ГОСТ 10629-88 |
Классификация дефектов железобетонных шпал:
Требования к старогодным железобетонным шпалам приведены в табл. 3.8
Таблица 3.8
Показатель | Требования к группе годности | |
---|---|---|
первой | второй | |
Тип рельсовых промежуточных скреплений | КБ | Всех типов |
Пропущенный по шпале тоннаж и срок ее службы с момента первой укладки | Без ограничений | Без ограничений |
Поперечные трещины в бетоне | Не допускаются | Наибольшее раскрытие трещин до 1 мм без разрушения бетона |
Продольные трещины в бетоне | Не допускаются | Наибольшее раскрытие трещин до 3 мм без разрушения бетона |
Отколы бетона: | ||
на кромках подрельсовых площадок | Допускается длиной не более 30 мм и глубиной не более 10 мм | Допускается длиной не более 100 мм и глубиной не более 30 мм |
на прочих кромках шпалы | Допускается длиной не более 100 мм и глубиной не более 30 мм без обнажения арматуры | Допускается длиной не более 300 мм и глубиной не более 60 мм |
рабочих кромок в отверстиях для закладных болтов | Не допускаются | Допускается |
Непрямолинейность подрельсовой площадки | Не более 1мм | Не более 5мм |
Толщина закладной шайбы в месте контакта с головкой закладного болта | Не менее 4мм | Не менее 2мм |
Продажа шпал — ЗАО «Ремстройпуть» +7(343) 228-34-34
Бетонная шпала и способ ее изготовления
Изобретение относится к бетонной шпале с нанесенной на нее снизу структурой с неориентированным расположением волокон и способу изготовления подобной бетонной шпалы.
В известных композитных системах из структур текстильных волокон и бетона, таких как, например, подошвы шпал из предварительно напряженного бетона или же бетона, известны решения, в которых волокна соединяются с бетонными конструкциями с силовым замыканием.
Согласно ЕР-В-1298252, например, эластичные пластиковые слои фиксируются на нижней стороне шпал посредством слоя волокон с неориентированным расположением таким образом, что текстильный слой волокон с неориентированным расположением как приклеен или приварен в пластиковый слой или на пластиковый слой, так и соединяется с бетоном за счет включения волокон в цементный раствор или отдельно наносимого композитного материала, например клея. В качестве слоев волокон с неориентированным расположением для соединения между названными в качестве примера шпалами и эластичной подошвой шпалы используются, например, геотекстильные или же нетканые материалы.
Множество известных нетканых материалов и также другие соединительные среды, например геотекстильные нетканые материалы, имеют только ограниченные свойства обеспечивающих силовое замыкание, неограниченно осуществляющих функциональность соединения нанесений.
Пластиковые сплетения с жесткими структурами волокон могут, например, не так интенсивно смещать минеральные структуры в свежем бетоне, что все соединительные структуры полностью включаются в бетон. Между соединительной средой и бетоном возникают дефекты, которые, например, ухудшают заданные эластичные характеристики, при поступлении воды приводят к эффектам всасывания и нарушают структурное состояние бетона.
Задачей изобретения является разработка бетонной шпалы с расположенной с нижней стороны пластиковой подошвой, которая может быть просто изготовлена, а ее пластиковая подошва надежно механически соединена с бетонным телом бетонной шпалы, а также способа изготовления такой бетонной шпалы.
Для решения этой задачи изобретение предлагает бетонную шпалу с расположенной с нижней стороны пластиковой подошвой, которая снабжена: бетонным телом, которое имеет нижнюю сторону, и пластиковой плитой, которая расположена на нижней стороне бетонного тела, при этом однослойная или многослойная пластиковая плита соединена с бетонным слоем посредством слоя волокон с неориентированным расположением, который имеет волокна, которые соединены с пластиковой плитой и/или утоплены в бетонное тело.
В случае этой бетонной шпалы согласно изобретению предусмотрено,
что слой волокон с неориентированным расположением имеет волокна диаметром 15 мкм — 50 мкм с плотностью 20-200 волокон на квадратный миллиметр и
что примерно от 20% до 60% волокон выполнены с утопленными в бетонное тело свободными концами, и утопленные участки других волокон выполнены в виде петель, при этом примерно от 10% до 60% утопленных в бетон свободных концов волокон изогнуты относительно нижней стороны бетонного тела на величину от 30° до 90°.
Согласно изобретению волокна имеют по существу круглое или эллипсоидное поперечное сечение, при этом соотношение сторон эллипса составляет не более чем 1:2.
Согласно еще одному предпочтительному варианту изобретения волокна являются химически сродными использованным для бетонного тела при его изготовлении компонентам.
Было установлено, что известные нетканые материалы и подобные нетканым материалы из волокон с неориентированным расположением, такие как, например, фетр (изготовленный посредством иглопрокалывания, аппретирования, прохождения волокон и форм волокон), только условно подходят для того, чтобы самостоятельно схватываться свежим бетоном за счет возникающего в процессе отвердевания бетона подсоса гидратации таким образом, что обеспечивается нанесение согласно требованиям.
В случае изобретения для изготовления бетонной шпалы с расположенной с нижней стороны пластиковой подошвой в качестве механического соединения между двумя этими элементами используется имеющий специальные волокна слой волокон с неориентированным расположением, благодаря чему концы волокон в результате подсоса гидратации бетона при его затвердевании попадают в капиллярные и/или гелевые поры бетона и в затвердевшем состоянии бетона удерживаются в нем. При этом слой волокон с неориентированным расположением с его обращенной от нижней стороны бетонной шпалы стороны может быть соединен с однослойной или многослойной пластиковой плитой, а именно либо до, либо после соединения слоя волокон с неориентированным расположением с бетонным телом.
Кроме того, изобретение предлагает бетонную шпалу, которая изготовлена согласно указанному выше способу и, предпочтительным образом, имеет в качестве подошвы с нижней стороны прочно соединенную механическим способом с волокнистым слоем пластиковую плиту.
Исходя из знания, что свежий бетон при определяемых условиях рецептуры и обработки создает подсос гидратации, согласно изобретению слой волокон с неориентированным расположением и бетон согласованы друг с другом таким образом, что подсос гидратации всасывает соединяющие волокнистые структуры в свежий бетон.
Для технического использования этого подсоса гидратации следующие бетоно-технологические, цементо-химические, текстильно-технические и специфические для нанесения критерии в их процессе воздействия определены в качестве предлагаемого решения.
Гидратация как реакция воды и цемента вызывает образование цементного камня. Некоторые из основных составных частей цемента, которые возникают при сгорании исходных веществ и в клинкерной фазе претерпевают дальнейшую модификацию, вызывают различные реакции между водой затворения и именно этими составными частями цемента.
Прежде всего, трикальциевый алюминат и трикальциевый силикат вызывают высокую скорость реакции и отверждение цементного камня. Доля сульфата кальция (гипс) влияет или же замедляет действие трикальциевого алюмината. Согласно изобретению при проверке на пригодность рецептуры бетона путем выбора сорта цемента способ следует модифицировать или же оптимизировать.
Свежий бетон из-за высокой доли трикальциевого алюмината и его взаимодействия со свойствами других составных частей клинкера (по существу с трикальциевым силикатом, дикальциевым силикатом и тетракальциевым ферритом алюмината), еще не находящегося в стадии схватывания и отвердевания свежего бетона, приобретает свойство образования мелких гидратов силиката кальция в форме волокон и пленок и малых кристаллов из гидроксида кальция.
Кроме того, при реакции алюминатов с сульфатом кальция возникают сульфатгидраты алюмината кальция в виде игольчатых трисульфатов, так называемого эттрингита.
Реакция трикальциевого алюмината с сульфатами кальция связана с увеличением объема, которое в еще не отвердевшем бетоне не имеет последствий, так как не происходит вспенивания эттрингита.
Однако увеличение объема вызывает в образующемся цементном геле и содержащихся в нем капиллярных и гелевых порах так называемый подсос гидратации.
Этот подсос гидратации, насколько известно, не используется ни в одной из известных бетонных технологий в качестве технологического преимущества. Использование подобных эффектов известно исключительно при нанесении средств дополнительной обработки при строительстве дорог с бетонным покрытием.
Согласно изобретению для целенаправленного включения волокон в поверхность свежего бетона технически и экономически используется бетонно-технологический подсос гидратации.
Гелевые поры с долей, предпочтительным образом, примерно в 25% гелевого объема и радиусом пор от 10-7 мм до 10-5 мм подходят для всасывания волокон уложенного на свежий бетон материала, если эти волокна имеют конклюдентную структуру и свойства относительно капиллярных и гелевых пор. Капиллярные и гелевые поры имеют, в общем, цилиндрическую форму и сужаются при увеличении глубины пор в так называемые бутылочные поры. Подходящие для использования подсоса гидратации волокна должны быть конклюдентными в том отношении, что согласно изобретению они могут проникать как в цилиндрическую, так и в сужающуюся часть пор. Капиллярные поры с радиусом пор, прежде всего, от 10-5 мм до 10-1 мм дополняют гелевые поры в размере пор практически без оказывающего технически невыгодное воздействие перехода.
В случае использованных на примере подошвы шпалы геотекстильных материалов используется структура волокон с неориентированным расположением из ПЭ или же ПЭТ с диаметрами волокон, прежде всего, от 20 мкм до 40 мкм. Этот диаметр волокон и использованная плотность волокон целесообразным образом от 40 до 130 нитей/мм2 обеспечивает необходимую для всасывания волокон совместимость подсоса гидратации, капиллярных и гелевых пор, диаметра волокон и плотности волокон.
В качестве дополнительных условий для эффективности самостоятельного впитывания волокон с заданной толщиной и плотностью за счет подсоса гидратации можно определить свободную длину волокон, геометрическую форму волокон и форму их поперечного сечения, а также их направление и химическое сродство к воде затворения и цементному гелю. Это касается, например, таких геотекстильных материалов или иных структур с неориентированным расположением волокон или же волокнистых материалов, которые в процессе изготовления наделяются гидрофобными свойствами или/и за счет разбрызгивания имеют несовместимое с геометрией пор гидратации, например прямоугольное, поперечное сечение.
Затем, имеющиеся для включения в бетон волокна должны иметь свободные концы в заданной доле, предпочтительным образом, от 20% до 50%. Только ограниченная доля, предпочтительным образом, менее 50% волокон должна быть выполнена в форме петли. Свободные концы волокон не должны проходить исключительно по прямой; доля, например, от 10% до 60% должна быть изогнута таким образом, что угол изгиба составляет не менее 30°, но не более 90°.
Поперечное сечение волокон должно быть округлым вплоть до эллиптического, при этом соотношение сторон эллипса должно быть не больше 1:2.
Сами волокна следует освободить от остатков изготовления волокон или трикотажных материалов, которые могут ухудшить химическое сродство к цементному клею, гелю или воде затворения. В качестве материалов для волокон могут использоваться известные пластиковые волокнистые материалы (например термопласты, такие как ПЭ и ПЭТ), металлы (металлические волокна) или также возобновляемые или же растительные сырьевые материалы.
Ниже на основании чертежа, который показывает поперечное сечение бетонной шпалы с механически закрепленной снизу посредством слоя волокон с неориентированным расположением, эластичной пластиковой плитой, пример осуществления изобретения поясняется более подробно.
На чертеже в качестве примера показана бетонная шпала 10 с армированным, слабо армированным или неармированным бетонным (сплошным) телом 12, которое на его нижней стороне имеет частично утопленный в нее слой 16 волокон с неориентированным расположением, который за счет склеивания или приваривания или иным образом механически соединен с однослойной или многослойной пластиковой плитой 18. Наличие показанного на чертеже для более наглядного представления расстояния между нижней стороной 14 бетонного тела 12 и пластиковой плитой 18 является необязательным.
В случае называемых подошвой шпалы, расположенных с нижней стороны эластичных покрытий шпал из бетона или предварительно напряженного бетона в материалы эластичного покрытия вплавляются слои волокон с неориентированным расположением с заданными свойствами волокон.
Эти слои волокон с неориентированным расположением имеют после с одной стороны примерно половинного включения в эластичные материалы не включенную, выступающую из эластичных материалов долю волокон для присоединения к бетонным шпалам.
Эта свободная доля волокон состоит из концов волокон и петель волокон. Петли волокон при прикладывании к свежему бетону находящейся в процессе изготовления бетонной шпалы обволакиваются цементным клеем и приводят к базовой прочности соединения.
С этой базовой прочностью можно достичь прочности на отрыв между бетоном и эластичным покрытием примерно от 0,3 Н/мм2 до 0,5 Н/мм2. Эти значения находятся в предельном диапазоне технических требований эксплуатирующих пути предприятий и их сводов правил.
Техническое использование подсоса гидратации для включения с силовым замыканием свободных концов волокон в свежий бетон обеспечивает прочность на отрыв более 1,5 Н/мм2 и, тем самым, позволяет обеспечивать выполнение высоких требований по качеству путей и оптимальную избыточность системы.
При диаметре волокон от прим. 25 мкм до прим. 40 мкм и плотности волокон от 40 до 130 волокон на каждый мм2 и использовании цементов с низким содержанием сульфатов кальция свободные концы волокон всасываются в образующийся эттрингит за счет подсоса гидратации. Находящийся в окружении возникающей за счет этого матрицы из волокон и цементного клея, имеющий атмосферное давление воздух только условно выступает в качестве реципиента. Имеется еще одна техническая взаимосвязь — с энергией гидратации. За счет этого также существует возможность в условиях пониженного давления воздуха (например, вакуум-бетон) наносить по этому принципу на бетонные шпалы эластичные пластики.
Выше изобретение было пояснено на примере бетонной шпалы в качестве случая применения бетонного конструктивного элемента. Само собой разумеется, что изобретение тем самым не ограничивается бетонными шпалами, а применяется везде, где бетонное тело бетонного конструктивного элемента необходимо механически соединить с пластиковой плитой.
Железобетонная шпала
Изобретение относится к верхнему строению железнодорожного пути, в частности к железобетонным шпалам, используемым преимущественно в бесстыковом пути. Цельнобрусковая железобетонная шпала предварительно напряженная содержит зубцы на выступах в подрельсовых зонах, при этом зубцы расположены симметрично относительно поперечной оси ложа шпалы. Достигается повышение фиксации шпалы в балластной призме. 5 ил.
Изобретение относится к конструкции рельсовых опор и может быть применено в конструкции шпал, в основном железобетонных, применяемых в верхнем строении железнодорожного пути, преимущественно бесстыкового.
Общеизвестна конструкция цельнобрусковой, предварительно напряженной, струнобетонной железобетонной шпалы, в которой нижняя постель плоская или в своей средней части она имеет выемку Название «струнобетонная» означает применение в рельсовых опорах не только проволочной арматуры, но также и арматуры стержневого типа.
Железобетонная шпала должна обладать высокой надежностью и долговечностью. Срок ее использования должен составлять 40-50 лет. Основным дефектом, ограничивающим срок эксплуатации рельсовых опор, является появление и развитие трещин в средней зоне, так как именно верх центральной части испытывает максимальные изгибающие моменты.
Железобетонные шпалы имеют переменное (по длине) поперечное сечение с относительно малой жесткостью в средней части по сравнению с подрельсовыми участками. Это позволяет уменьшить изгибающие моменты в междурельсовой зоне шпал, именно которая и испытывает максимальные нагрузки. Поэтому в 50-е годы прошлого века для исключения наиболее опасного из вариантов контакта со щебнем, а именно опирания шпалы на балласт своей средней частью, этот участок в конструкции рельсовой опоры специально подняли над поверхностью щебня на 10 мм, уменьшив ее высоту в этой зоне со 145 до 135 мм. Это позволило избежать или, по крайней мере, значительно ослабить растягивающие напряжения верха центральной зоны железобетонной шпалы. Для снижения давления на балласт ширина подошвы шпал у торцов была существенно увеличена — до 305 мм. В средней же части этот параметр меньше и равен 255 мм. Максимальная высота в подрельсовой зоне значительно выше, чем в центре шпалы, и составляет 229 мм. Эти изменения конструкции позволили сделать рельсовую опору высоконадежной и обеспечивающей работоспособность между капитальными ремонтами пути. В дальнейшем, после замены ГОСТ 10629-78 на ГОСТ 10629-88, габариты железобетонных шпал претерпели очень незначительные изменения.
Второй важной функцией рельсовых опор является способность оказывать сопротивление силам, вызывающим отклонение пути от проектного положения. То есть шпала должна хорошо фиксироваться в балласте и обладать значительным усилием сдвига. В противном случае всегда есть вероятность угона и выброса рельсошпальной решетки. Это особенно стало важным и необходимым после перехода на бесстыковую конструкцию пути.
В этом варианте верхнего строения железной дороги имеются очень важные особенности в поведении рельсовой плети при повышении температуры. Возникающие в ней продольные силы могут достигать 160 т. С учетом того, что шпальная решетка содержит два рельса, общее, суммарное значение усилий от их нагрева возрастает до 320 тс.
Кроме того, к этим продольным сжимающим рельсы температурным силам может добавиться и усилие от экстренного торможения поезда величиной до 70 тс и боковая сила от колесных пар, достигающая на прямых участках пути значений 6 тс, а в кривых 16 тс.
Поэтому для обеспечения устойчивости бесстыковой конструкции рельсошпальной решетки крайне необходимо значительное, принципиальное повышение усилия сдвига железобетонных шпал в балластной призме верхнего строения пути.
Для решения этой проблемы в соответствии с RU 2433218 С2 предложено выполнить выступ высотой 28 мм в средней части рельсовой опоры ее нижней постели.
Сделаем оценку эффективности этого технического решения. Если принять, что торец рельсовой опоры полностью засыпан щебнем, то эта минимальная величина заглубления составит 150 мм. Очевидно, что создание выступа увеличивает площадь поперечного сечения тела шпалы. Поэтому в этой конструкции к усилию сдвига балласта торцами рельсовой опоры необходимо добавить и усилие сдвига балласта за счет выступа. Его значение при равных значениях ширины со шпалой определяется отношением высоты выступа к стандартной величине заглубления рельсовой опоры в балласт. Таким образом, ожидаемое увеличение усилия поперечному сдвигу пути шпалой с выступом 28 мм и заглубление рельсовой опоры в балласт на 150 мм составит: (28:150)×100=18,7%.
В книге «Новые путевые машины», М., «Транспорт» 1984 г., стр. 192 под редакцией к.т.н. Ю.П. Сырейщикова на стр. 192 приведена формула по усилию сдвига Рс рельсошпальной решетки. В соответствии с ней Рс увеличивается в квадратичной зависимости от величины заглубления. Приняв это обстоятельство, в конечном итоге получим, что для шпалы, заглубленной на 150 мм и с выступом в средней части 28 мм, увеличение усилия поперечному сдвигу может составить лишь [(150+28):150]2×100%-100%=40%. Этого явно недостаточно для гарантированного исключения угона или выброса железнодорожного пути и недопустимости возникновения аварийной ситуации.
Кроме того, наличие выступа средней части рельсовой опоры требует при укладке рельсошпальной решетки на балластную призму верхнего строения пути создания ответного углубления, соответствующего по размерам высоте и длине выступа. Сделать это на щебне фракции 25-60 мм, зерна которого по размерам значительно превышают нужную величину углубления в 28 мм на поверхности балластной призмы, а тем более и на криволинейном участке пути, крайне затруднительно. Это приведет и к удорожанию строительства балластной призмы. Кроме того, наличие выступа предопределяет нежелательное и способствующее появлению дефектов опирание шпалы на щебень своей средней частью. Это означает существенное увеличение растягивающих напряжений и повышение вероятности появления трещин в верхней части центральной зоны рельсовой опоры и приведет к снижению ее долговечности, надежности и потребует значительного усиления, удорожания арматуры, воспринимающей значительно увеличившиеся изгибающие моменты.
Другой, близкой по конструкции рельсовой опорой является железобетонная шпала по SU 1772284 А1, имеющая выступ в подрельсовых зонах. Принимаем это техническое решение за прототип.
Целью предлагаемого изобретения является значительное увеличение силы сопротивления смещению шпалы в балласте и повышение надежности и трещиноустойчивости рельсовой опоры благодаря снижению изгибающих усилий в подрельсовой зоне, а также и в средней части.
Указанная цель достигается тем, что выступ содержит зубцы. Это позволяет значительно увеличить эффективность шпалы по ее сопротивлению перемещения в балласте верхнего строения пути и значительно уменьшить растягивающие кромочные напряжения по подошве и верхней части.
Осаживание, внедрение в балласт зубатой рельсовой опоры существенно облегчается.
На Фиг. 1 показана конструкция стандартной рельсовой опоры. При ремонтных работах верхнего строения пути производят выправку рельсошпальной решетки. Рассмотрим этот процесс при работе путевых машин, например, типа ВПР и Duomatig, имеющих подбивочные блоки с вертикально расположенными подбойками. При рабочем цикле происходит их заглубление в балласт. Лопатки подбоек опускаются в щебень под нижнюю поверхность шпалы и двигаясь к рельсовой опоре начинают обжимать балласт. При этом подбивка происходит только в участках, прилегающих к подрельсовой зоне подошвы. Середина не подбивается. В противном случае произойдет опасное опирание шпалы на балласт центральной частью, возникнет максимальный изгибающий момент и тогда неизбежно появление трещин в верхней средней части рельсовой опоры. В этом случае наибольшие напряжения возникают потому, что плечо действия силы Р1 и Р2 от колесной пары поезда получается максимально возможным и равным L=0,8 м. L — расстояние от продольной оси железнодорожного пути до середины головки рельса. Суммарное значение Р1+Р2=Р определяется допустимой статической нагрузкой на колпару, ее динамической составляющей при движении, ударным действием ползунов колесных пар, рельсовых стыков и составляет около 40 тс. Огромное усилие и максимально возможное плечо его действия предопределяет появление опасных напряжений в конструкции железобетонной шпалы при ее опирании на балласт своей средней частью.
Необходимо отметить, что и подрельсовая зона шпалы, в своей средней части, а именно по подошве, также испытывает растягивающие напряжения. Объясняется это тем, что лопатки подбоек путевых машин конструктивно не заходят внутрь подрельсовой зоны, а могут располагаться только справа и слева от нее. Поэтому при подъемке пути и при обжиме балласта рабочими органами подбивочного блока щебенки перемещаются из шпального ящика под подошву рельсовой опоры только в зоне расположения лопаток подбоек, то есть с торца до подрельсовой зоны и между подрельсовой зоной и средней частью шпалы. Следствием подъемки пути (обычно величина подъема 40-60 мм), локального размещения подбоек и перемещения ими щебенок не под всю подошву шпалы оказывается то, что рельсовая опора фактически опирается на четыре бугра 1…4. В подрельсовых же зонах и под средней частью рельсовой опоры образуются впадины 5…7, где балласта нет или его мало и он слабо уплотнен.
Причем углубления 5 и 7 расположены симметрично относительно действия сил Р1 и Р2. Очевидно, что нагрузка на шпалу от колесных пар величиной до 40 тс будет изгибать рельсовую опору вниз, в зону впадин 5 и 7. Именно в них вначале и образуются растягивающие напряжения. При проходе вагонов, под действием поездной нагрузки бугры сминаются, рельсошпальная решетка осаживается и глубина впадин уменьшается. Именно поэтому с течением времени впадина 6 постепенно заполняется щебенками и возникает опирание шпалы своей серединой на балласт. От этого возникают максимальные изгибные моменты в ее средней части.
Для исключения опасных напряжений в подрельсовой зоне и в центре рельсовой опоры новой конструкции (см. Фиг. 2) предназначены зубатые выступы 8, которыми предлагаемая шпала отличается от общеизвестной, стандартной и от принятой за прототип. Благодаря им незатекание, непопадание щебенок в подрельсовые зоны при подбивке пути не отражается негативно на шпалу, не приводит к появлению изгибающих моментов по подошве опоры в подрельсовой зоне и в верху ее средней части. Объясняется это тем, что шпала на балласт теперь опирается зубатыми выступами 8, а впадины 5 и 7 исчезли, самоликвидировались. Зубатые выступы 8 расположены по центру подрельсовых зон и, следовательно, соосно с нагрузкой, с направлением действия сил Р1 и Р2 от действия колесных пар. Так как плечо действия сил Р1 и Р2 становится равным 0, то и изгибающие моменты в подрельсовых зонах исчезают. В свою очередь, отсутствие выступа в средней части шпалы при проведении выправки пути и подъемке, например, на 50 мм и наличие зубатых выступов 8 приводит к появлению зазора (появлению увеличенной по сравнению с Фиг. 1 впадины 6) между балластом и этой зоной шпалы. То есть наличие углубления 6 означает отсутствие опирания центральной части рельсовой опоры. Следовательно, нет и изгибающего момента и в средней части шпалы.
Таким образом, введение зубатых выступов 8 на подошве, симметрично и соосно расположенных относительно оси действия сил Р1 и Р2, симметрично и соосно относительно колесной нагрузки, симметрично поперечной оси подрельсового участка, симметрично ложу для установки подошвы рельса позволяет теоретически полностью исключить появление опасных напряжений в любой зоне и участке опоры новой конструкции, а практически помогает значительно их уменьшить, тем самым обеспечить высокую надежность, долговечность и работоспособность предлагаемой шпалы. На выступах расположены зубцы 9. Их оптимальное количество 10 штук на шпалу.
Некоторые варианты исполнения выступов, их формы и зубцов показаны на Фиг. 3, Фиг. 4, Фиг. 5.
Можно использовать предлагаемое изменение конструкции не только при изготовлении рельсовых опор, но, и это особенно ценно, для модернизации шпал, бывших в употреблении. При этом возможно самозалечивание неопасных мелких трещин в теле старогодной шпалы при заливке ее нижней постели высокопрочным бетоном для получения создаваемых выступов. Нужно отметить, что есть решения, позволяющие при необходимости создать и предварительное напряжение в добавляемом цементном слое.
Известно, что срок службы железобетонных рельсовых опор составляет 40-50 лет. Капитальный ремонт шпальной решетки (со сменой рельсов) производят через 18-25 лет. При этом одновременно с заменой рельсов приходится заменять и рельсовые опоры, которые выработали свой ресурс всего на 50%. Изобретение позволяет модернизировать демонтированные при капитальном ремонте пути шпалы с целью придания им повышенной устойчивости за счет увеличения усилия сдвига в балласте в 3-5 раз и «залечивания» имеющихся дефектов в виде мелких трещин.
Доработка заключается в получении «зубатого» выступа на подошве в подрельсовой зоне, который можно изготовить с помощью дополнительной пресс-формы, имеющей на своей рабочей поверхности соответствующие углубления.
Выбор оптимальных размеров предлагаемого местного утолщения шпалы зависит от многих факторов: величины подъемки пути выправочно-подбивочно-рихтовочной машиной, зазора между крайней лопаткой подбивочного блока и подрельсовой зоной, величиной заглубления подбойки в щебень, степенью загрязнения балласта и некоторыми другими.
На практике, рационально выбрать выступ, по ширине примерно равный размеру подошвы наиболее применяемого рельса P65, то есть 150 мм. Длину выступа лучше выполнить равной ширине стандартной шпалы, то есть 300 мм. Высоту принять равной средней величине подъемки при текущем содержании пути, то есть 50 мм. Зубцы необязательно размещать на нижней поверхности выступа. Он сам по себе является «зубом» шпалы и существенно увеличивает ее усилие сдвига в балласте. Кроме того, дополнительные зубья могут быть размещены и на других частях нижней, торцевой или боковой поверхности рельсовой опоры. Нижняя, то есть со стороны щебня, поверхность выступа может быть расположена, как вариант, и параллельно поверхности ложа шпалы для установки подошвы рельса, то есть параллельно подрельсовой части, то есть с уклоном 1:20. В общем случае, предлагаемое изобретение эффективно также для двухшарнирных трехблочных шпал и двухблочных с металлической соединительной поперечиной. Выступ может иметь и форму клина.
Зубцы нижней поверхности выступа в поперечном сечении имеют произвольную форму с эквивалентным диаметром от 5 до 150 мм, расположены друг от друга с зазором от 0 до 50 мм и имеют высоту от 10 до 100 мм. Размещение зубцов по подошве может быть как в шахматном порядке, так и произвольным, хаотичным, или упорядоченным с заданным шагом и интервалом по выбранному направлению. Высота зубцов может быть одинаковой или разной, вычисляемой по определенному закону или быть функцией случайной величины в диапазоне от 10 до 100 мм.
Целесообразно использовать предлагаемое техническое решение совместно с изобретением RU 2378444 C2, которое предполагает принудительное осаживание пути вертикальной силой 35-100 тс во время рабочего цикла выправки. Это позволит полностью вдавить выступы на подошве 10 шпалы в балласт 11 верхнего строения железнодорожного пути, исключить появление впадин 5 и 7 и гарантированно обеспечить такое дополнительное уплотнение щебня, которое способно выдержать максимальную поездную нагрузку.
Поэтому проектное положение рельсов сохраняется, теоретически, неизменным вне зависимости от пропущенного тоннажа. Объясняется это тем, что, щебень при выправке путевой машиной, работающей по принципу RU 2378444 C2, сжат под выступом и под подошвой шпалы (за исключением средней части) с такой силой, что способен без просадки воспринимать максимально возможную нагрузку от колесной пары поезда равную 40 тс. Это означает достижение идеального качества уплотнения балласта железнодорожного пути. Поэтому просадка рельсов вниз от проектного положения не происходит при любом пропущенном тоннаже. Надо отметить, достижение этого эффекта происходит по RU 2378444 C2 без снижения производительности путевой машины, при работе ее в штатном режиме. Таким образом, отпадает необходимость использования динамического стабилизатора пути (ДСП).
Но известно, что ДСП обеспечивает уплотнение балласта всего на 20-30% и при этом снижается точность установки рельсов в проектное положение, выполненное перед работой ДСП выправочно-подбивочно-рихтовочной машиной.
Научные исследования показали, что некоторое повышение стабилизации балласта при работе ДСП объясняется повышением площади опирания шпалы, так как при ее вибрации происходит разравнивание бугров 1…4. Дополнительного же уплотнения и сжатия щебенок верхнего строения пути практически не происходит.
Применение нового технического решения позволяет значительно увеличить усилие фиксации шпал в балластной призме, оказывать эффективное противодействие сжимающим температурным силам, исключить возможность выброса и угона пути, организовать безаварийное движение поездов на высокоскоростных магистралях, повторно использовать старогодные шпалы после их доработки не только на малодеятельных, но и на главных железнодорожных путях.
Железобетонная шпала, цельнобрусковая, предварительно напряженная, имеющая выступ в подрельсовых зонах, отличающаяся тем, что выступ содержит зубцы.
Шпала железобетонная Ш-3 ОСТ 32.152.2000, ТУ 5864-091-01115863-2006, 54747-2011 / ОСТ 22-33-3332.152.2000
Шпалы железобетонные Ш-3 в наличии. Шпала железобетонная Ш-3 ОСТ 32.152.2000, ТУ 5864-091-01115863-2006, 54747-2011 / ОСТ 22-33-3332.152.2000 по доступным ценам.Шпала железобетонная Ш-3
Цена по запросу
Содержание:
Технические характеристики:
Характеристика | Значение |
Вес 1 шт, кг | 260 |
Единица измерения | шт |
Размер (д/ш/в), м | 2,7х0,3х0,230 |
Высота шпалы, мм | 230 ± 5 |
Толщина шпалы | 300 |
ГОСТ | ОСТ 32.![]() |
Длина, м | 2,7 |
Материал шпалы | железобетон |
Тип шпалы | Ш-3 |
Область применения
Предварительно напряженные ж/б шпалы Ш-3 под скрепление ЖБР-65 — нераздельное, с болтовым прикреплением рельса к шпале; либо под скрепление ЖБР-65Ш — нераздельное клеммное, с шурупами и пластмассовыми дюбелями, с рельсом Р-65. Данный тип шпал применяется на всех железнодорожных путях, по которым обращается типовой подвижной состав.
Укладывается шпала на балластный слой верхнего строения железнодорожного пути и при скреплении обеспечивает соответствующее расстояние между рельсовыми нитями.
Компания «ТехМет» предлагает на продажу Шпалы железобетонные Ш3, которые могут быть использованы на железнодорожных путях и линиях, используемые для сообщения типового подвижного состава ОАО «Российские Железные Дороги» с установленными нагрузками и скоростным режимом. Шпала железобетонная Ш3 являются предварительно напряжёнными и используются с рельсами Р65 с нераздельным клеммным скреплением ЖБР, применяя болтовое прикрепление рельса к шпале. При изготовлении шпал железобетонных Ш3 используется бетон, обладающий морозостойкостью марки не меньше F200. Категория бетона, из которого изготавливаются шпалы железобетонные Ш3 – не менее B40 (М500). В соответствии с ГОСТ 26633 для бетона шпал железобетонных Ш3 используется природный щебень или гравий фракции 5-20 мм. При эксплуатации шпал ж/б Ш-3 на мало загруженных линиях реальный срок службы составляет 50 лет.
Описание
Шпала железобетонная Ш-3 ОСТ 32.152.2000, ТУ 5864-091-01115863-2006, 54747-2011 / ОСТ 22-33-3332.152.2000 (для ЖБР)
Шпалы предназначены для применения на всех железнодорожных линиях и путях, по которым обращается типовой подвижной состав ОАО «РЖД» с установленными нагрузками и скоростями. Шпалы рассчитаны на применение с рельсами типа Р65 и нераздельного клеммного скрепления ЖБР-65Ш с шурупами по ТУ 1293-165-01124323-2003 и пластмассовыми дюбелями ТУ 2291-179-01124323-04 или ТУ 2291-207-01124323-05.
Связавшись с менеджерами из отдела продаж компании «ТехМет» по телефонам +7 (49234) 333-78, +7 (49234) 218-67, +7 (910) 778-23-77 или по электронной почте [email protected], Вы узнаете не только полную информационную справку о шпалах жб Ш3, но и о других позициях в каталоге нашей компании в случае необходимост
Чертёж / схема
Цены
Наименование товара | Цена, руб |
Шпала железобетонная Ш-3 | Цена по запросу у менеджера |
Доставка
Тип доставки | Цена, руб |
Доставка по России | Уточнить у менеджера |
Доставка по СНГ | Уточнить у менеджера |
Доставим в короткие сроки в любой регион на Ваш объект или производство. Перевезем собственным автотранспортом. Также оформляем ж/д грузоперевозки. При необходимости груз страхуем и сопровождаем.
Внимание! Обратитесь к менеджеру и получите ИНДИВИДУАЛЬНОЕ и ВЫГОДНОЕ предложение по телефонам:
+7 (499) 70-44-377
+7 (49234) 333-78
+7 (49234) 218-67
+7 (910) 778-23-77
Заказ обратного звонка
Заполните эту форму — и мы перезвоним
Вам в самое ближайшее время!
ул. Юбилейная, д. 56, оф. 1001 602263 г. Муром, Владимирская обл,
+7 (49234) 333-78, +7 (49234) 218-67, +7 (910) 778-23-77, tm377@mail.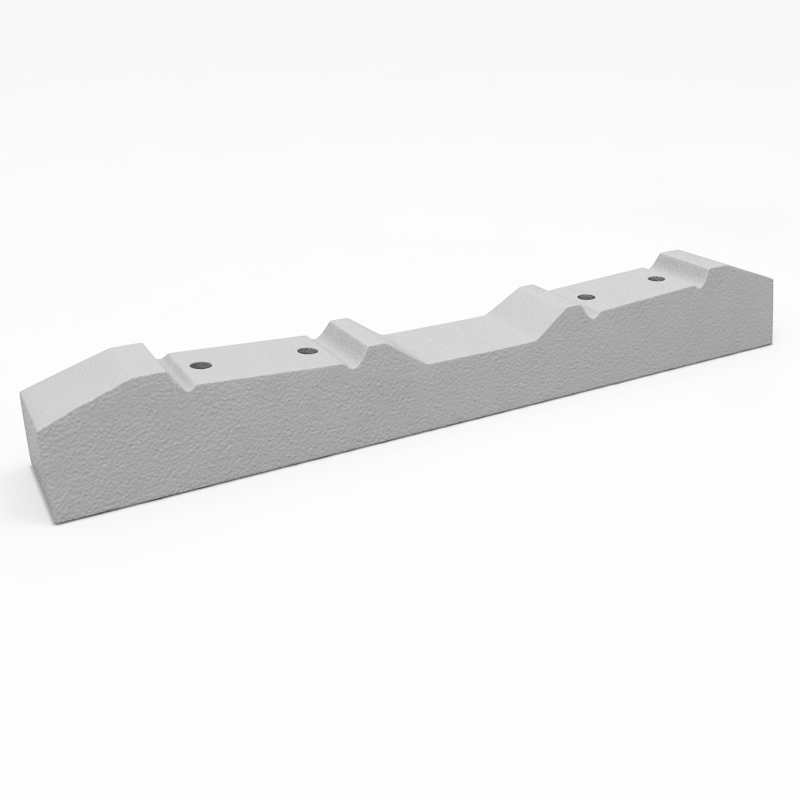
Железобетонные шпалы АРС
ТУ 3185-010-01115863-2004
РЧ АРС-04.04.010
Технические условия ТУ 3185-010-01115863-2004
Настоящие технические условия распространяются на шпалу железобетонную анкерную типа ШС-АРС для железных дорог колеи 1520 мм, предназначенную для применения с рельсами Р65 и промежуточными рельсовыми скреплениями типа АРС.
Железобетонные шпалы АРС предназначены для применения на всех железнодорожных линиях в главных, станционных и прочих путях, а также подъездных путах промышленных предприятий, по которым обращается типовой подвижной состав общей сети железных дорог Российской Федерации.
Вид климатического исполнения У1 ГОСТ 15150.
Анкеры скрепления АРС, замоноличиваемые в шпалу, должны соответствовать ТУ 3185-005-01115863-2004 и рабочим чертежам АРС-04.04.005-03, АРС-04.04.005-04.
Шпалы АРС должны удовлетворять требованиям по трещиностойкости, принятым при их проектировании, и выдерживать при испытании контрольные нагрузки, согласно ГОСТ Р 54747-2011.
Шпалу следует изготовлять из тяжелого бетона по ГОСТ 26633 класса по прочности на сжатие В40.
Требуемая передаточная прочность бетона должна быть не менее 34,2 МПа (349 кгс/см ).
Отпускная прочность бетона должна быть не менее указанной выше передаточной прочности бетона.
Марка бетона по морозостойкости должна быть не ниже F200.
Для бетона шпал следует применять щебень из природного камня или щебень из гравия фракции 5-20 мм по ГОСТ 26633. Допускается по согласованию изготовителя с потребителем применять щебень фракции 20 — 40 мм в количестве не более 10% от массы щебня фракции 5-20 мм по ГОСТ 26633.
Справочная масса железобетонной шпалы 280 кг.
Для армирования шпал должна применяться проволока из углеродистой стали периодического профиля диаметром 3 мм по ГОСТ 7348 или ТУ 14-4-1681.
Номинальное число арматурных проволок в шпале АРС 44.
Общая сила начального натяжения всех арматурных проволок в пакете должна быть не менее 358 кН (36,4 тс).
На заводах ОАО «БЭТ» выпускаются модификации железобетонной шпалы АРС
- железобетонные предварительно напряженные, с элементами охранных приспособлений для челноков, шпалы Ш-АРС-МК — для участков пути в кривых малых радиусов от 349 до 300 м включительно
Железобетонная шпала
Полезная модель относится к верхнему строению пути и может быть использовано в железных дорогах узкой колеи шахтных выработок. Задача, на решение которой направлена заявляемая полезная модель, заключается в повышении надежности, долговечности, уменьшении веса шпалы, экономии материалов. В шахтном рельсовом транспорте все более широко применяют железобетонные шпалы. Шпала железобетонная содержит армированное тело переменного сечения, имеет возвышения на верхней поверхности под рельсы, опорную площадь, увеличенную за счет уширения подошвы, в средней части шпалы вдоль ее продольной оси симметрии выполнено сквозное отверстие, а армирование выполнено в виде пространственного каркаса с зафиксированными металлическими трубками и деревянными пробками для костыльного крепления.
Полезная модель относится к верхнему строению пути и может быть использована в железных дорогах узкой колеи шахтных выработок.
Задача, на решение которой направлена заявляемая полезная модель, заключается в повышении надежности, долговечности, уменьшении веса шпалы, экономии материалов.
В шахтном рельсовом транспорте все более широко применяют железобетонные шпалы. Известна железобетонная шпала ШД-4 (Справочник. Подземный транспорт шахт и рудников. Под общей ред. Г.Я.Пейсаховича, И.П.Ремизова. — М.: Недра, 1985, с.358), преимуществом которой является значительно большой срок службы, увеличение сопротивляемости механическому износу. При железобетонных шпалах конструкция узла промежуточного скрепления имеет некоторые недостатки, связанные с устройством дюбелей в бетоне для забивки костылей или завинчивания шурупов, а также оставлением проемов для монтажа закладных болтов.
Известна шпала для железных дорог узкой колеи (Железнодорожный путь на железобетонных шпалах. Под ред. А.Ф.Золотарского. — М.: Транспорт, 1967, с.60) из обычного железобетона, имеет опорную площадь, увеличенную за счет уширения подошвы. Шпала предназначена для укладки на щебеночный балласт. Расчетное давление на подкладку 6,5 т при расчете на прочность и 4,3 т при расчете на трещиностойкость. Основная арматура — сталь марки 25Г2С периодического профиля, прочая арматура — проволока стальная. Расход металла на шпалу 6,3 кг, вес шпалы 88 кг. К недостаткам относится костыльное крепление. Во время движения поездов рельс при изгибе перед колесом приподнимается над шпалой и надергивает костыли. Костыли
время от времени добивают. Надергивание и периодическое добивание костылей приводит к быстрому падению их сопротивления на выдергивание, разрушению бетона вокруг деревянных пробок..
Известна шпала (RU 2089697, кл. Е 01 В 3/00, опубл. 1997.09.10), содержащая армированное тело, на вертикальных боковых поверхностях которого выполнены выступы и выемки, а в теле шпалы вдоль ее продольной оси симметрии выполнен канал.
К причинам, препятствующим достижению указанного выше технического результата при использовании известной железобетонной шпалы относится сложность ее конструкции.
Наиболее близким устройством того же назначения к заявленной полезной модели по совокупности признаков является железобетонная шпала (А.с. №1772284, РФ, ОПБ №40, 1992 год, принято за прототип), имеющая переменное по длине сечение, подрельсовые углубления на верхней поверхности и выступы на подошве непосредственно под подрельсовыми углублениями. Выступы конгруэнтны углублениям и выполнены с продольными пазами.
К причинам, препятствующим достижению указанного выше технического результата при использовании известной железобетонной шпалы, принятой за прототип, относится ее массивность.
Предложенная конструкция железобетонной шпалы устраняет выше перечисленные недостатки.
Сущность полезной модели поясняется чертежами (фиг.1 шпала, вид сбоку, фиг.2 шпала, вид сверху, фиг.3 пространственный каркас шпалы, вид сбоку, фиг. 4 пространственный канал шпалы, вид сверху). Шпала железобетонная содержит армированное тело 1, возвышения подрельсовые 2, нижнее основание 3, шире верхнего 4, деревянные пробки 5 в трубках 6 для крепления рельсов, сквозное отверстие 7, расширяющееся к основанию.
Сущность полезной модели заключается в следующем.
Шпала выполнена из бетона кл. В 30 на мелком щебне (фракция 5-10 мм).Армирование выполнено в виде пространственного каркаса (фиг.3, фиг.4), с зафиксированными трубками 6, с деревянными пробками 5 хвойных пород с глубокой пропиткой антисептиками для костыльного крепления рельс. Деревянные пробки после пропитки в сухом состоянии забивают в трубки до бетонирования. Шпала имеет опорную площадь 3, увеличенную за счет уширения подошвы (220 мм). Для облегчения веса шпалы и экономии материалов в среднем ее сечении выполнено сквозное отверстие 7 размерами сверху (460×60) меньшими, чем снизу (480×80).
В сравнении с прототипом предложенная железобетонная шпала обладает следующими преимуществами. Уменьшение габаритных размеров, уменьшение объема бетона, уменьшение веса рабочей арматуры, деревянные пробки находятся в металлических трубках, что сохраняет бетон при замене пробок. Предложена установка готового пространственного каркаса в металлоформу, в отличие от выполнения арматурных работ отдельными плоскими каркасами и стержнями. Сквозное отверстие в среднем сечении шпалы уменьшает вес шпалы, а также, за счет уменьшения опорной площади уменьшается воздействие упругого основания, что ведет к уменьшению изгибающего момента в середине шпалы.
Железобетонная шпала прошла испытания на трещиностойкость в подрельсовом и среднем сечении в соответствии с требованиями ГОСТ 8829-94 «Изделия строительные ж/б и бетонные заводского изготовления». Методы испытания нагруженном. Правила оценки прочности, жесткости и трещиностойкости. В подрельсовом сечении при расчетном нагружении 6,65 т нагрузка была доведена до 7 т. Нагрузка поддерживалась постоянной в течение 2 мин. Затем нагрузка доведена до 8 т (5 мин. ). Трещин нет.
В среднем сечении при расчетном нагружении 4,5 т нагрузка была доведена до 5 т. (2 мин.), нагрузка продолжена, трещины проявились при нагрузке 7,0 т.
Заключение: При контрольных нагрузках железобетонная шпала ШС1 выдержала испытания.
Сравнение предлагаемого решения с прототипом и аналогами, известными из существующего уровня техники, позволяет утверждать о соответствии этого решения критериям патентоспособности полезной модели.
Шпала железобетонная, содержащая армированное тело переменного сечения, имеющая возвышения на верхней поверхности под рельсы, опорную площадь, увеличенную за счет уширения подошвы, отличающаяся тем, что в средней части шпалы вдоль ее продольной оси симметрии выполнено сквозное отверстие, а армирование выполнено в виде пространственного каркаса с зафиксированными металлическими трубками и деревянными пробками для костыльного крепления.
Рельса и бетонная шпала крупным планом
Корзина Купить!
Изображение помещёно в вашу корзину покупателя.
Вы можете перейти в корзину для оплаты или продолжить выбор покупок.
Перейти в корзину…
удалить из корзины
Размеры в сантиметрах указаны для справки, и соответствуют печати с разрешением 300 dpi. Купленные файлы предоставляются в формате JPEG.
¹ Стандартная лицензия разрешает однократную публикацию изображения в интернете или в печати (тиражом до 250 тыс. экз.) в качестве иллюстрации к информационному материалу или обложки печатного издания, а также в рамках одной рекламной или промо-кампании в интернете;
² Расширенная лицензия разрешает прочие виды использования, в том числе в рекламе, упаковке, дизайне сайтов и так далее;
Подробнее об условиях лицензий
³ Лицензия Печать в частных целях разрешает использование изображения в дизайне частных интерьеров и для печати для личного использования
тиражом не более пяти экземпляров.
* Пакеты изображений дают значительную экономию при покупке большого числа работ (подробнее)
Размер оригинала: 4896×3264 пикс. (16 Мп)
Указанная в таблице цена складывается из стоимости лицензии на использование изображения (75% полной стоимости) и стоимости услуг фотобанка (25% полной стоимости). Это разделение проявляется только в выставляемых счетах и в конечных документах (договорах, актах, реестрах), в остальном интерфейсе фотобанка всегда присутствуют полные суммы к оплате.
Внимание! Использование произведений из фотобанка возможно только после их покупки. Любое иное использование (в том числе в некоммерческих целях и со ссылкой на фотобанк) запрещено и преследуется по закону.
Как построить подпорную стену из бетонных шпал
Подпорные стены и, в частности, подпорные стеновые блоки помогают украсить ваш дом и повысить его ценность.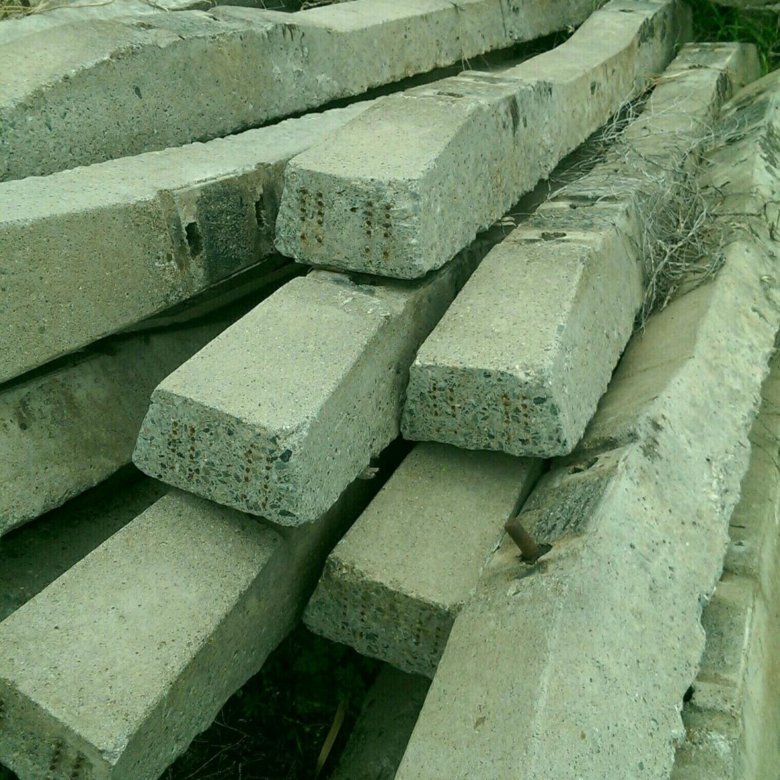
Ознакомьтесь с нашей обширной шпалой для бетона .
Планировка
Район Вы планируете озеленение или строительство подпорной стены с цемента шпал должен быть на одном уровне.Нарисуйте на поверхности веревочную линию и прикрепите веревку к колышкам. Ram колышки в землю несколько дюймов глубокой на расстоянии 500 мм от одного конца к другому концу подпорной стены. Разметьте яму для копания. Если вы используете спальное место длиной 1800 мм, вы должны разметить отверстия на расстоянии 1800 мм друг от друга.
Подготовка основания
Выкопайте землю с помощью мини-погрузчика с 300-миллиметровым шнеком. Выкопайте глубину 600 мм и круглую 450 мм для крепления кронштейнов ограждения.Убедитесь, что вы оставить минимум 200мм для засыпки подпорной стенки .
Установить опоры и залить бетоном
После того, как участок выкопан, установите столб и убедитесь, что он ровный и на одном уровне с линией веревки, используя спиртовой уровень. Продолжите с другой стойкой и держите минимум 40 мм для откидывания назад. Забетонируйте столбы, убедившись, что они находятся на одинаковом уровне. Еще раз проверьте расстояние между каждой стойкой и заполните яму бетоном, содержащим смесь цемента, гравия и песка, на высоте до 600 мм от верха.
Установить шпалы и засыпку
Подождите сутки, пока бетон высохнет. На следующий день вставьте шпалы в стойки. Отрегулируйте высоту спального места, уложив его до нижнего уровня стойки. После прорезания шпал подождите одну неделю, чтобы засыпать их щебнем. Не забудьте поставить ага трубу в задней части подпорной стенки для воды, чтобы избежать. Насыпьте гравий на глубину до 200 мм от верха нижнего шпала. Поставьте пробку для грунта и залейте стену доверху.Ваша бетонная шпальная стена готова делать свою работу.
Ознакомьтесь с нашим руководством по установке, чтобы узнать, как закрепить бетонную шпалу.
ШпалыOutback популярны для подпорных стен благодаря своей прочности и внешнему виду. Чтобы узнать цену бетонных шпал , свяжитесь с Австралийский центр укладки дорожных покрытий по телефону 1800 191 131.
границ | Количественная оценка влияния типа поезда на давление в балласте бетонных шпал с использованием обратного калькулятора условий опоры
Введение
Четвертая промышленная революция, определяемая как текущая тенденция автоматизации и обмена данными в производственных технологиях (Qian et al., 2019), внесла существенные изменения во многие отрасли современной экономики. Таким образом, железнодорожная отрасль в последнее время претерпела множество изменений и улучшений, особенно благодаря внедрению технологий для увеличения пропускной способности путей, повышения безопасности и оптимизации процессов технического обслуживания. Изменения достигаются за счет улучшения конструкции, проверки состояния и оптимизации мониторинга и / или технического обслуживания.
Распределенная движущая сила, положительное управление поездом (PTC) (Resor et al., 2005), автоматическое управление поездом (ATC) (Kim et al., 2015) и беспилотные автомобили (Bruner, 2018) являются примерами внедрения технологий для повышения безопасности и эффективности транспортных операций. И хотя датчики ударной нагрузки колес (WILD) (Van Dyk, 2014) и датчики нагретого подшипника (Tarawneh et al., 2020) существуют уже несколько десятилетий, растет интерес к анализу данных из этих систем для разработки стратегий профилактического обслуживания для подвижной состав. Автономные системы измерения геометрии пути (ATGMS) (Van Dyk, 2014; Saadat et al., 2018), беспилотные летательные аппараты (БПЛА) (Baniæ et al., 2019), а также системы машинного зрения и лазерного контроля (Ye et al., 2019; Fox-Ivey et al., 2020) разрабатываются и внедряются. для предоставления действенной информации об общем состоянии здоровья трека (Stuart et al., 2012; Saadat et al., 2014). Несмотря на эти обнадеживающие достижения, необходимы дополнительные исследования для разработки и реализации стратегий технического обслуживания путей на основе состояния для отдельных компонентов, составляющих структуру пути.Улучшение как на уровне компонентов, так и общего состояния пути может улучшить качество езды транспортного средства, уменьшить повреждение пути за счет снижения динамических нагрузок, увеличить интервалы технического обслуживания и сделать железнодорожный транспорт более экономичным и конкурентоспособным (Selig, 1994).
При рассмотрении систем инспекции и мониторинга следует отметить, что многие из них не собирают данные постоянно в зависимости от времени. Кроме того, хотя есть технологии, которые были развернуты для количественной оценки поддержки треков [e.g., георадар (GPR) (Artagan et al., 2020) и матричные сенсоры тактильной поверхности (MBTSS) (McHenry et al., 2015) и датчики давления (Xiao et al., 2020)], эти технологии обычно мешают движению поездов или in situ рельсовым путям во время установки. Например, георадарные осмотры выполняются через фиксированные интервалы, а MBTSS требует поддомкрачивания рельсов и шпал во время установки датчиков (McHenry et al., 2015), что приводит к изменениям, которые могут повлиять на окончательные результаты за счет эффекта наблюдателя (Tanathong et al. ., 2017; Rose et al., 2018). Без автоматизированной и систематической системы мониторинга владельцы инфраструктуры железнодорожных путей не имеют комплексных и экономически эффективных вариантов оптимизации операций по техническому обслуживанию (Qian et al., 2019). Таким образом, остается возможность непрерывно контролировать состояние пути без необходимости его прерывания.
Учитывая, что балластированные пути являются наиболее распространенным типом железнодорожных путей во всем мире (Hay, 1982; Köllõ et al., 2015), исследования, обсуждаемые в этой статье, сосредоточены на разработке и внедрении метода непрерывной оценки их состояния.Балласт — это критически важный компонент пути, который расположен между шпалой, под ней и вокруг нее (Hay, 1982; Kerr, 2003). Известно, что условия балластной опоры существенно влияют на реакцию бетонной шпалы на изгиб (Kaewunruen, Remennikov, 2009; Kaewunruen et al., 2016; Bastos et al., 2017; Canga Ruiz, 2018). Наряду с опорой и распределением нагрузки от шпал на основание, балласт также облегчает отвод воды, предотвращает попадание растительности на конструкцию пути и обеспечивает боковую устойчивость для удержания пути на месте во время движения поездов и смягчения движения во время движения поездов. разумный диапазон изменений продольного напряжения рельса (Solomon, 2001).
Исследователи из Университета Иллинойса в Урбана-Шампейн (штат Иллинойс) разработали новую, неинтрузивную технику для точного и непрерывного измерения состояния балластной опоры непосредственно под шпалами. Обратный калькулятор условий балластной опоры (далее именуемый «обратный-калькулятор») анализирует данные изгиба бетонной шпалы, зарегистрированные в потоке коммерческих услуг, чтобы косвенно количественно оценить как состояние балластной опоры под бетонными шпалами, так и давление на стыке балласт-шпала ( Qian et al., 2019). В этой статье используется первоначальный прогресс в разработке калькулятора для спины, чтобы расширить его функциональные возможности в качестве «умного спящего», который может количественно определять требования к изгибу спального места, балластное давление и поддержку. Данные, когда они должным образом преобразованы в полезную информацию, позволят улучшить планирование технического обслуживания железных дорог и проектирование железнодорожных путей. Особое внимание в этой статье будет уделяться количественной оценке балластного давления бетонных шпал, установленных в общем коридоре со смешанными междугородними пассажирскими поездами и грузовыми перевозками с большой осевой нагрузкой (HAL).
Фон
Обратный вычислитель — это косвенный метод оценки состояния балластной опоры спального места с использованием нагрузок на рельсовые опоры и изгибающих моментов, зафиксированных в отдельных местах вдоль спального места. Основываясь на равновесии сил и основных принципах статики, для двухмерного объекта только одна комбинация сил реакции (то есть одно условие опоры) может создать заданный профиль момента под действием набора приложенных нагрузок. Принимая во внимание этот принцип, бетонная шпала упрощается как двумерная балка, и ее состояние балластной опоры может быть рассчитано обратно на основе изгибающих моментов вдоль бетонной шпалы и соответствующих нагрузок на опору рельса, обе из которых могут быть количественно определены в ходе экспериментов ( Qian et al., 2019).
Бетонные поверхностные датчики деформации, применяемые с использованием метода, описанного Эдвардсом и др. (2017) успешно количественно оценили деформации изгиба, испытываемые бетонными шпалами, как в лабораторных, так и в полевых экспериментах по оказанию коммерческих услуг (Quirós-Orozco et al., 2018; Edwards et al., 2019; Canga Ruiz et al., 2020). Затем деформации изгиба могут быть преобразованы в изгибающие моменты при применении калибровочных коэффициентов, полученных из лаборатории, с использованием метода, описанного Эдвардсом и др. (2017). Нагрузки на седло рельса рассчитываются непосредственно с помощью локально установленных тензодатчиков или косвенно с близлежащих площадок для обнаружения ударной нагрузки на колеса (WILD) с использованием модифицированной версии рекомендованного уравнения, приведенного в Американской ассоциации инженеров железнодорожного транспорта и технического обслуживания путей [AREMA] (2017) Руководство для инженеров железнодорожного транспорта (MRE).
Упрощенная двухмерная модель шпалы, использованная в этом исследовании, показана на рисунке 1. Модель описывает типичную североамериканскую бетонную шпалу длиной 102 дюйма (260 см) и разделена на шесть дискретных бункеров по 17 дюймов (43 см). в длину. Каждый бункер содержит процент от общей силы реакции балласта, и предполагалось, что сила реакции внутри каждого бункера равномерно распределена внутри бункера. Силы реакции балласта преобразуются в балластное давление путем деления сил на площадь бункера [i.е., длина бункера, умноженная на ширину шпалы 10,3 дюйма (26 см)]. В общей сложности пять датчиков деформации поверхности бетона были установлены продольно вдоль верхней фаски шпал. Никакой формальной оптимизации расположения датчиков не проводилось. Два места для сиденья рельса и одно центральное положение колеи были выбраны, чтобы ответить на более широкие вопросы о величине сиденья рельсового рельса и центральных изгибающих моментах. Промежуточные калибры были расположены по центру между ними для сбора дополнительных данных профиля изгибающего момента.Поскольку шпала не удерживается на двух концах при любых возможных условиях балластной опоры, изгибающие моменты на двух концах равны нулю. Следовательно, при объединении этих конечных значений с пятью измеренными моментами, полученными от тензодатчиков, инструментальная шпала может выдать в общей сложности семь известных изгибающих моментов. Предполагалось, что нагрузки на рельсовые седла будут равномерно распределены по ширине каждого из 6 дюймов (15 см) сидений рельса (Qian et al., 2019).
Всего в модели используется девять входных данных обратного вычислителя, состоящих из семи известных изгибающих моментов и двух приблизительных нагрузок на седло рельса.Также включены два граничных условия. Во-первых, исходя из равновесия сил, общая сила реакции балласта должна равняться общим нагрузкам на седло рельса. Это означает, что силы во всех шести бункерах должны составлять примерно 100%. Во-вторых, значение каждого бункера не должно быть меньше нуля, поскольку нереально иметь отрицательную силу реакции для балласта (например, балласт не обеспечивает растягивающую способность).
После ввода величин нагрузки седла рельса в вычислитель спинки процесс оптимизации генерирует комбинации сил реакции, которые удовлетворяют двум граничным условиям.Для каждой комбинации сил реакции обратный вычислитель генерирует профиль изгибающего момента шпалы на основе нагрузок на опору рельса и сравнивает его с фактическим входным профилем изгибающего момента. Процесс оптимизации завершается, когда разница между расчетным и фактическим профилями изгибающего момента достигает своего минимума, и комбинация сил реакции, создавшая расчетный профиль изгибающего момента, становится результирующим условием опоры. Процесс оптимизации представлен на рисунке 2.
Рис. 2. Блок-схема системы оценки состояния балластной опоры (Qian et al., 2019).
В процессе оптимизации моделированный отжиг и биполярное распределение Парето использовались в качестве алгоритма оптимизации и генератора случайных величин. За счет одновременной реализации двух методов улучшенное решение могло быть создано за меньшее время (Englander and Englander, 2014), а сходимость по локальным оптимумам была предотвращена (Kirkpatrick et al., 1983).Для заданного набора входных данных максимальное время вычислений составляло примерно 1 мин, что было сочтено разумным для приложения.
Полевые эксперименты
Для количественной оценки условий полевого балласта при движении доходов с использованием обратного вычислителя полевые эксперименты были проведены на двухколейном участке Северо-восточного коридора (NEC) компании Amtrak в Эджвуде, штат Мэриленд, США. Полевая площадка располагалась на касательной дороге, построенной из бетонных шпал с шагом 24 дюйма.(61 см) в центре, в месте, где каждый будний день проходит около 55 региональных, междугородных и высокоскоростных пассажирских поездов, пригородных поездов и различных грузовых поездов HAL (на трассе с инструментами). Всего на трассе за 2017 год накоплено 42,6 млн брутто-тонн (МГТ) (из них 18,5 МГТ на трассе с приборами). Расположение и разнообразие транспортных потоков предоставили возможность количественно оценить влияние как тоннажа, так и типа движения на условия опоры шпал и величину балластного давления под бетонными шпалами.Смешанное движение в этом месте в основном состояло из четырех типов поездов: пассажирских поездов ACELA, междугородных поездов Amtrak, курсирующих с пассажирскими вагонами Amfleet, пригородных поездов региона Мэриленд (MARC), запряженных дизель-электрическими локомотивами, и грузовых поездов класса I HAL. с вагонами, имеющими различную максимальную общую железнодорожную нагрузку (GRL).
В дополнение к тензометрическим приборам были установлены три термопары для измерения температуры окружающей среды, а также температуры в верхней и нижней части шпалы.Тензодатчики, установленные на рельсах, использовались для количественной оценки колесных нагрузок, и эти данные были получены с близлежащего объекта WILD. Номинальная нагрузка на колесо для каждой оси (полученная из данных WILD) использовалась для аппроксимации нагрузки на седло рельса с помощью модифицированной версии рекомендованного уравнения, приведенного в Американской ассоциации инженеров железнодорожного транспорта и технического обслуживания путей [AREMA] (2017). Значение ноль (0) для ударного фактора (IF) было выбрано с учетом того, что используемые входные нагрузки на колесо были фактическими нагрузками, включающими любое динамическое влияние.Коэффициент распределения (DF) 0,505 был получен из AREMA MRE Рис. 30-4-1 , исходя из расстояния между бетонными шпалами 24 дюйма (61 см) по центру. Эти приблизительные нагрузки на седло рельса использовались в качестве входных данных для обратного вычисления условий опоры.
Данные были собраны с более чем 2550 проходов поездов в период с января по август 2017 года. Хотя с помощью обратного калькулятора было проанализировано более 23000 осей, или примерно 5750 осей для каждого типа поездов, результаты были отфильтрованы на основе двух параметров (1) максимум Среднеквадратичная ошибка (MSE), возникающая в результате процесса оптимизации и (2) разницы температур между верхом и низом шпалы.Фильтрация привела к окончательному подсчету 400 поездов, которые соответствовали вышеупомянутым спецификациям, которые были установлены для выделения конкретных интересующих переменных. Поезда варьировались по длине от 28 до 500 осей. Количество проходов оси после фильтрации обеспечивает уровень уверенности 95% в том, что результаты являются точным представлением более широкого набора данных.
Максимальное значение MSE, использованное для окончательного анализа, составляло 10 тысяч фунтов на дюйм (1,13 кН-м). Это представляет собой допуск 5 тысяч фунтов на дюйм (0,56 кН-м), положительный или отрицательный, для каждого измерения тензодатчика.Это соответствовало примерно 10% от среднего показания тензодатчика. Кроме того, было показано, что данная деформация, вызванная температурой, оказывает значительное влияние на результаты изгиба бетонных шпал (Wolf et al., 2016), она также была выбрана в качестве контрольного параметра. Более конкретно, предыдущие исследования показали, что линейная зависимость между температурным градиентом и изгибным поведением бетонных шпал, где каждое изменение на 1 градус Фаренгейта (0,56 градуса Цельсия) между верхом и низом шпалы может привести к изменению изгибающего момента примерно на 1 тысячу фунтов. -в (0.11 кН-м) (Canga Ruiz et al., 2019). Следовательно, данные, отобранные для окончательного включения в анализ, имели градиенты температуры менее ± 1 градуса по Фаренгейту (0,56 градуса Цельсия). Фильтрация была предпринята с учетом того, что целью данного исследования была оценка условий опоры и давления при работе различных типов подвижного состава, и, таким образом, были изолированы эффекты температурного градиента и последующего изгиба шпалы. Следует отметить, что диапазон фактических давлений и конфигураций условий опоры, как ожидается, превысит диапазон, продемонстрированный в этой статье, из-за эффекта теплового градиента (Canga Ruiz et al., 2019).
Существующие предельные состояния балластного давления
AREMA MRE рекомендует максимально допустимое давление балласта 85 фунтов на квадратный дюйм (586 кПа) под бетонными шпалами для путей, построенных из высококачественного, стойкого к истиранию балласта (Американская ассоциация инженеров железных дорог и технического обслуживания путей [AREMA], 2017). Это значение включает коэффициент безопасности для предотвращения разрушения несущей способности или чрезмерного проскальзывания под нагрузкой (Американская ассоциация железнодорожного машиностроения и технического обслуживания путей [AREMA], 2017).Следовательно, это значение используется для предельного состояния давления, чтобы коррелировать результаты обратного вычисления и помочь в оценке давлений, полученных в ходе полевых экспериментов.
Результаты
В следующих разделах представлены результаты полевых экспериментов, проведенных на Amtrak. Нагрузки на седло рельса, давление балласта и условия опоры количественно оцениваются и сравниваются как количественно, так и качественно. После фильтрации данные были разделены на 2 временные категории — квартал 1 (Qtr.1) и квартал 3 (квартал 3) — для анализа того, как увеличение MGT с течением времени повлияло на балластное давление. Qtr. 1 были получены в январе и феврале 2017 года, а Qtr. 3 данные получены в августе 2017 г. после накопленного тоннажа 12,2 млн тонн (12,44 млн тонн).
Нагрузка на сиденье рельса
Чтобы охарактеризовать требования к шпалам, были рассчитаны нагрузки на рельсовые сиденья для каждого типа поезда. В таблице 1 приведены медианные значения и 95-й процентиль нагрузки на рельсовые сиденья для каждого типа поездов.Таблица 1 разделена на четыре типа поездов, и каждая из этих категорий подразделяется на локомотивы и железнодорожные вагоны. Кроме того, грузовые поезда подразделяются на загруженные и порожние, чтобы лучше количественно оценить влияние конкретного движения, особенно в условиях однородности движения отдельных поездов.
Таблица 1. Медиана и 95-й процентиль нагрузки на рельсовые сиденья для каждого типа поездов.
Данные в таблице 1 демонстрируют широкий диапазон [5–23 тысячи фунтов (22–102 кН)] нагрузок, наблюдаемых на полевой площадке.Наименьшие значения нагрузки на сиденья рельсов были получены для пустых грузовых вагонов, а самые высокие — для грузовых локомотивов и загруженных грузовых вагонов.
Качественная оценка состояния опоры спального места
На рис. 3 представлены качественные выходные данные обратного калькулятора для электромобиля ACELA, пассажирского вагона ACELA и пустого грузового вагона. На рис. 4 показаны как величина, так и расположение нагрузок на посадочное место рельса, а также силы реакции балласта на шпале.
Рисунок 3. Состояние балластной опоры при проезде легкового автомобиля ACELA, пассажирского вагона ACELA и грузового порожнего вагона.
Рисунок 4. Зависимость между нагрузкой на седло рельса и максимальным балластным давлением.
Обработанные результаты обратного калькулятора указывают на отсутствие поддержки центра (Qian et al., 2019). Этот тип опоры часто ассоциируется с недавно утрамбованными путями (Bastos, 2018) и может привести к ускоренному износу балласта непосредственно под опорой рельса, если нагрузки превышают прочность балласта (Branson et al., 2019). Хорошая опора под сиденьем рельса часто рассматривается как «начальное» условие опоры, которое, вероятно, перейдет в опору, привязанную к центру, в зависимости от времени и тоннажа. Кроме того, это условие опоры приводит к увеличению положительных изгибающих моментов седла рельса и соответствующей возможности возникновения положительных трещин в седле рельса. Это условие опоры отличается от того, что предполагается Американской ассоциацией инженеров железнодорожного транспорта и технического обслуживания путей [AREMA], 2017, тем, что предполагается равномерная поддержка от конца шпалы через колею рельсового сиденья, тогда как на евро Нормах (EN) (Европейский комитет по стандартизации, 2009 г.) и Стандарт австралийского (AS) (Стандарты Австралия, 2003) это условие поддержки рассматриваются как вновь уплотненное состояние поддержки, подытоженные Y и др.(2017).
Количественная оценка давления на границе балласт-шпала
Взаимосвязь между нагрузкой на седло рельса и давлением балласта в шпале была предметом предварительного исследования. Средняя собранная нагрузка на седло рельса варьировалась от 5,1 тысячи фунтов (22,7 кН) до 20,9 тысячи фунтов (93 кН), что давало возможность исследовать влияние нагрузки на давление и сравнивать ее с различными подходами. Во-первых, мы сравним его с подходом Талбота, который указывает на прямую положительную линейную зависимость (Talbot, 1980).Второе сравнение будет связано с подходом Эйзенмана к расчету давления на границе стыковки и балласта (Eisenmann, 2004a, b; Giannakos, 2014). Таким образом, максимальное балластное давление непосредственно под шпалой было нанесено на график в зависимости от этих нагрузок на седло рельса и представлено на рисунке 4 вместе с ожидаемым давлением балласта шпалы, предсказанным Талботом (1980).
Данные показывают, что давление линейно зависит от нагрузки на седло рельса ( R 2 = 0.998), что хорошо согласуется с данными Talbot (1980) и Eisenmann (2004a, b). Однако измеренная величина всегда больше, чем у Талбота. Этот равномерный дифференциал обусловлен предположением Талбота о том, что 67% нижней части шпалы задействовано в передаче нагрузки, тогда как шпала, о которой идет речь в этой статье, занимает только 60% площади опоры. Что касается подхода Эйзенмана, если предположить, что 89% нижней части шпалы задействовано в передаче нагрузки, он очень близок к полевым результатам, полученным в этом исследовании.Рекомендуемый предел в 85 фунтов на кв. Дюйм (586 кПа), рекомендованный AREMA, превышается, когда нагрузки на седло рельса превышают приблизительно 17 тысяч фунтов (76 кН). Для справки, когда такая же нагрузка на седло рельса применяется к шпале с однородным состоянием опоры, среднее балластное давление равно примерно 30 фунтам на квадратный дюйм (207 кПа), что значительно ниже значения, установленного в American Railway Engineering and Maintenance-of-Way. Ассоциация [AREMA] (2017). Это указывает на то, что изменение условий опоры может привести к увеличению давления в балласте на 183%.
Изучая международные рекомендации по проектированию бетонных шпал на изгиб, мы обнаруживаем некоторые заметные различия. Текущий метод AREMA для анализа изгиба бетонных шпал рассматривает факторный подход, зависящий от длины шпал, расстояния между шпалами, годового тоннажа и скорости поезда, предполагая равномерную реакцию балласта вдоль шпалы (Американская ассоциация инженеров железнодорожного транспорта и технического обслуживания путей [AREMA] , 2017). Текущий метод AS для расчета изгиба шпал зависит от длины шпал, расстояния между шпалами и нагрузки на ось (Стандарты Австралии, 2003).EN 13230-1 переносит анализ расчетных изгибающих моментов на UIC 713R (Европейский комитет по стандартизации, 2009). Метод UIC 713R зависит от длины шпал, расстояния между шпалами, нагрузки на ось, затухания рельсовых подушек и скорости поезда, обеспечивая пару факторов безопасности: один для учета «вариации реакции шпалы из-за неисправностей опоры», а другой — для учета «Неравномерность опоры вдоль шпалы» (Международный союз железных дорог, 2004 г.). AS 1085.14 и AREMA отличаются от UIC 713R тем, что исключают уменьшение затухания в подушках рельсов или коэффициенты безопасности для учета неровностей или пустот в опоре (Wolf et al., 2015). Учитывая, как изменение состояния балластной опоры может еще больше увеличить напряжения в бетоне в шпале, количественная оценка фактической опоры может повысить точность конструкции, рекомендованной как AREMA, так и AS.
Чтобы количественно оценить общую потребность в балласте и подконструкции, данные о давлении в балласте были нанесены на график функции кумулятивного распределения (CDF) (Рисунок 5). Максимально допустимое поверхностное напряжение AREMA в 85 фунтов на квадратный дюйм (586 кПа) показано вертикальной пунктирной красной линией. Показаны данные из всех бункеров, проанализированных в ходе этого исследования, а также отдельные данные из рельсовых сидений, центра и конца шпалы, которые были включены для дальнейшего исследования распределения опоры и ее влияния на давление балласта вдоль шпалы. снизу (рисунок 5).
Рисунок 5. Кумулятивные распределения балластного давления для различных комбинаций бункеров.
При рассмотрении данных из всех бункеров примерно 4% зарегистрированных значений превышают допустимое давление балласта AREMA. Однако при анализе данных только из бункеров непосредственно под сиденьями рельсов это значение увеличивается до 10%. Это подтверждает гипотезу о том, что это условие поддержки будет способствовать повышению спроса на рельсовой подкладке, таким образом, создавая потенциал для ускоренного износа балласта в этом месте.При анализе давления на обоих концах и в центре шпалы можно определить, что эти бункеры испытывают сравнительно небольшую нагрузку — значительно ниже предела AREMA.
Влияние типа движения на балластное давление
Учитывая разнообразие перевозок, выполняемых на NEC Amtrak, давление было определено количественно при различных нагрузках на седло рельса (рис. 4), отслеживаемых по типу подвижного состава. На рисунке 6 показаны медианное значение и 95-й процентиль балластного давления в каждом бункере для всех классификаций подвижного состава, с разделением данных на ранее заявленную классификацию Qtr.1 и Qtr. 3 (показано по диагонали внутри каждого бункера).
Рисунок 6. Распределение балластного давления.
Данные обеспечивают четкое визуальное представление увеличенной величины балластного давления непосредственно под сиденьями рельсов для всех типов транспортных средств и отсутствия опоры в центре и на концах спального места. В то время как давление в седле рельса выше, допустимое поверхностное давление AREMA превышается только для междугородных локомотивов Amtrak, локомотивов MARC, грузовых локомотивов и загруженных грузовых вагонов.Это разумно, учитывая, что их номинальная нагрузка на колесо может создавать нагрузки на опору рельса, превышающие 17,5 тысяч фунтов (78 кН). Следовательно, если прогнозировать ухудшение балласта в этом дискретном месте, можно ожидать, что ухудшение в первую очередь произойдет под этими транспортными средствами, а не под пассажирскими вагонами или порожними грузовыми вагонами. Учитывая несоответствие требований к давлению на границе раздела шпала-балласт, можно количественно оценить степень износа, вызываемого повышенным давлением. Исходя из этого, можно провести механистико-эмпирический анализ и проектирование, чтобы в конечном итоге разработать концепцию железнодорожной техники, аналогичную концепции эквивалентной нагрузки на одну ось (ESAL) на шоссе, разработанную Американской ассоциацией государственных служащих автомобильных дорог (AASHTO). Таким образом, устанавливается связь между спросом и ущербом (Американская ассоциация государственных служащих автомобильных дорог и транспорта [AASHTO], 1993).
Данные также показывают, что давление нелинейно в зависимости от увеличенных нагрузок на седло рельса, подтверждая более раннюю работу Quirós-Orozco et al. (2018). При более низких нагрузках на седло рельса (пустой грузовой вагон) в контейнерах 1 и 5 наблюдается давление, которое составляет примерно 10% от давления в седле рельса, измеренного контейнерами 2 и 4. Однако по мере увеличения нагрузки на седло рельса (загруженный грузовой вагон) давление Бункеры 1 и 5 увеличиваются с большей скоростью, чем посадочные места рельсов; свыше 20%. Следовательно, хотя на рис. 6 показана положительная линейная зависимость между нагрузкой на седло рельса и максимальным давлением, существует нелинейность в том, как давления распределяются по дну шпалы.Также можно выявить различия между значениями, полученными в ячейках 2 и 4, причем обе ячейки расположены непосредственно под гнездами направляющих (рисунок 6). Это можно объяснить влиянием неравномерных нагрузок на посадочные места рельсов, наблюдаемых в полевых условиях (Edwards et al., 2018).
Кроме того, Рисунок 6 показывает, что условия поддержки оставались в основном постоянными после накопления 12,24 MGT в ходе этого исследования. Для сравнения данных был проведен дисперсионный анализ (ANOVA), в результате которого было установлено, что H 0 : балластное давление в третьем квартале равно балластным давлениям в первом квартале и H 1 : по крайней мере шесть балластных давлений в третьем квартале отличаются от давления в первом квартале. балластные давления ( α = 0.05). Полученное значение p составило 0,209, что означает, что нет достаточных доказательств, чтобы отвергнуть нулевую гипотезу о том, что все средние по совокупности равны. Таким образом, состояние опоры остается прежним, и нет значительного изменения значений балластного давления с накопленным тоннажем. Это подчеркивает одно из возможных применений обратного калькулятора в качестве потенциального инструмента мониторинга для прогнозирования деградации балласта и лучшей оптимизации планирования технического обслуживания.
Изменение давления балласта в пределах прохода поезда
Для дальнейшей количественной оценки распределения давлений вдоль шпалы и на протяжении всего прохождения поезда были нанесены на график значения давления под каждой осью для разных типов поездов (рис. 7).Как упоминалось ранее, количественная оценка частоты и местоположения давлений приведет к улучшенным моделям ухудшения балласта и улучшенным конструкциям путей, что послужит основой для растущих методов анализа и проектирования M-E (Quirós-Orozco, 2018).
Рисунок 7. Распределение давления в балласте для типовых проходов поездов от различных типов подвижного состава: (A) ACELA, (B) Amfleet, (C) MARC и (D) грузовые локомотивы.
Локомотивы и силовые вагоны четко видны в распределении осей и более выражены, чем пассажирские вагоны на рисунках (a), (b) и (c). Более конкретно, на рисунке 7A можно наблюдать, как силовые вагоны ACELA на обоих концах поезда прикладывают к балласту давление примерно на 30 фунтов на кв. Дюйм (207 кПа) большее, чем легковые вагоны. В отличие от пассажирского оборудования, рисунок 7D показывает, что давления, создаваемые грузовыми поездами HAL, одинаковы по всей длине поезда и в этом случае значительно выше по величине, чем любое из давлений пассажиров.В частности, при сравнении рисунков 7B – D максимальное давление легкового автомобиля 40 фунтов на квадратный дюйм (276 кПа) составляет только 35% от максимального давления грузового вагона, составляющего приблизительно 110 фунтов на квадратный дюйм (758 кПа).
Заключение
Использование тензодатчиков для поверхностного монтажа на бетонных шпалах показало, что дает надежные и точные результаты для количественной оценки напряжений, моментов и давлений без вмешательства и неразрушающего контроля. Обратный калькулятор был применен к полевым данным общего коридора и продемонстрировал эффективность в качестве надежного инструмента мониторинга для количественной оценки состояния балластной опоры на стыке шпала-балласт в анализируемом общем коридоре.Вот некоторые из конкретных выводов, которые можно сделать из его использования:
• Существует широкий диапазон нагрузок, испытываемых на NEC Amtrak, от 4 до 35 тысяч фунтов (18–156 кН) с соответствующим балластным давлением в диапазоне от 14 до 175 фунтов на квадратный дюйм (97–1 207 кПа), что является самой низкой нагрузкой на седло рельса. значения, генерируемые грузовыми порожними вагонами, и самые высокие значения, генерируемые грузовым локомотивом и грузовыми вагонами, с разницей более чем в 8 раз.
• Данные показывают, что зависимость между давлением и нагрузкой на седло рельса является линейной ( R 2 = 0.998), где площадь контакта спящего с балластом для рассматриваемого спящего в этой статье соответствует 60%.
• Рекомендуемый AREMA предел максимального балластного давления 85 фунтов на кв. Дюйм (586 кПа) превышается, когда нагрузки на седло рельса превышают примерно 17 тысяч фунтов (76 кН) при отсутствии центральной опоры.
• При рассмотрении данных из всех бункеров примерно 4% зарегистрированных значений превышают AREMA MRE. Однако при анализе данных только из бункеров непосредственно под сиденьями рельсов это значение увеличивается до 10%.При анализе давления на обоих концах и в центре шпалы можно определить, что эти бункеры испытывают сравнительно небольшую нагрузку и значительно ниже допустимого предела давления балласта AREMA. Это подтверждает гипотезу о том, что это условие поддержки будет способствовать повышению спроса на рельсовой подкладке, таким образом, создавая потенциал для ускоренного износа балласта в этом месте.
Накопление 12,24 МГТ не привело к значительному ( α = 0.05) не изменили значения балластного давления и не изменили состояние балластной опоры. Это подчеркивает одно из возможных применений обратного калькулятора в качестве потенциального инструмента мониторинга для прогнозирования деградации балласта и лучшей оптимизации планирования технического обслуживания.
Это исследование показало влияние различных типов поездов на давление под одной бетонной шпалой с исходным состоянием опоры, которое было репрезентативным для опоры сиденья рельса. В будущем авторы поощряют широкое использование обратного калькулятора на большем размере выборки спящих (включая соседних спящих) для получения различных начальных состояний поддержки в сочетании с использованием использования умных спящих.Полученные данные помогут количественно оценить частоту и местоположение чрезмерного давления на шпалы, облегчая сопоставление упомянутых давлений со скоростью износа. Это, в свою очередь, приведет к улучшенным моделям ухудшения балласта и улучшенным конструкциям путей, что будет способствовать более широкому анализу и проектированию M-E.
Заявление о доступности данныхНеобработанные данные, подтверждающие выводы этой статьи, будут предоставлены авторами без излишних оговорок.
Авторские взносы
MD и JE: концепция и дизайн исследования.MD и CS: сбор данных. MD, CS и JE: анализ и интерпретация результатов и подготовка проекта рукописи. Все авторы рассмотрели результаты и одобрили окончательную версию рукописи.
Финансирование
Финансирование сбора данных было предоставлено Национальной железнодорожной пассажирской корпорацией, ведущей бизнес как Amtrak. Эта работа также была поддержана Железнодорожным центром Национального университета, Управлением транспорта Министерства транспорта США помощника секретаря по исследованиям и технологиям Транспортного центра Университета уровня 1.Материал в этой рукописи отражает позицию авторов, а не спонсоров. JE частично поддерживался грантами для Центра железнодорожного транспорта и инжиниринга UIUC (RailTEC) от CN и Hanson Professional Services.
Конфликт интересов
Авторы заявляют, что это исследование получило финансирование от Национальной железнодорожной пассажирской корпорации Amtrak. Спонсор участвовал в исследовании следующим образом: обеспечение доступа к треку для сбора данных, а также помощь в выборе места для полевых работ.
Список литературы
Американская ассоциация государственных служащих автомобильных дорог и транспорта [AASHTO] (1993). Руководство AASHTO по проектированию конструкций дорожного покрытия, 1993. Вашингтон, округ Колумбия: AASHTO.
Google Scholar
Американская ассоциация инженеров железнодорожного транспорта и технического обслуживания путей [AREMA] (2017 г.). Учебное пособие по железнодорожному машиностроению. Ландовер, Мэриленд: Американская ассоциация инженеров железных дорог и обслуживания дорог.
Google Scholar
Артаган, С.С., Бьянкини Чамполи, Л., Д’Амико, Ф., Кальви, А., и Тости, Ф. (2020). Неразрушающий контроль и мониторинг состояния железнодорожной инфраструктуры. Surv. Geophys. 41, 447–483. DOI: 10.1007 / s10712-019-09544-w
CrossRef Полный текст | Google Scholar
Баниш, М., Мильтенович, А., Павлович, М., и Шириш, И. (2019). Инспекция и мониторинг железнодорожной инфраструктуры на основе интеллектуального машинного зрения с помощью БПЛА. Facta Univ. Сер. Мех. Англ. 17, 357–364.DOI: 10.22190 / FUME1
CrossRef Полный текст | Google Scholar
Бастос, Дж. К. (2018). Лабораторный анализ удерживающей способности колеи железобетонных шпал с центральными трещинами при различных условиях опоры | elsevier расширенный читатель. Eng. Неудача. Анальный. 94, 354–363. DOI: 10.1016 / j.engfailanal.2018.08.018
CrossRef Полный текст | Google Scholar
Бастос, Дж. К., Дерш, М. С., Эдвардс, Дж. Р., и Андравес, Б. О. (2017). Поведение бетонных шпал при изгибе при различных условиях опоры. Am. Soc. Civ. Англ. J. Transp. Англ. 143: 04017064. DOI: 10.1061 / JTEPBS.0000097
PubMed Аннотация | CrossRef Полный текст | Google Scholar
Брэнсон, Дж. М., Дерш, М. С., де Лима, А. О., Эдвардс, Дж. Р. и Сезар Бастос, Дж. (2019). Определение характеристик материала подстяжной подушки для снижения напряженного состояния. Proc. Inst. Мех. Англ. Часть F J. Скоростной железнодорожный транспорт. 234: 095440971989015. DOI: 10.1177 / 09544097198
CrossRef Полный текст | Google Scholar
Брунер, М.(2018). Австралия: attivazione del primo sistema ferroviario autonomo per il trasporto merci. Aust. Действовать. Первый Auton. Railw. Syst. Транспортировка грузов. 73, 853–854.
Google Scholar
Канга Руис, А. Э., Эдвардс, Дж. Р., Цянь, Ю., и Дерш, М. С. (2020). Вероятностная основа для оценки конструкции бетонных шпал на изгиб. Proc. Inst. Мех. Англ. Часть F J. Скоростной железнодорожный транспорт. 234, 691–701. DOI: 10.1177 / 0954409719854569
CrossRef Полный текст | Google Scholar
Канга Руис, А.Э., Цянь, Ю., Эдвардс, Дж. Р., Дерш, М. С. (2019). Анализ влияния температуры на изгиб бетонной шпалы. Constr. Строить. Матер. 196, 362–374. DOI: 10.1016 / j.conbuildmat.2018.11.065
CrossRef Полный текст | Google Scholar
Канга Руис, ÁE. (2018). Анализ конструкции компонентов верхнего строения железнодорожного пути для приложений железнодорожного транспорта. Магистерская диссертация Университет штата Иллинойс в Урбана-Шампейн, Департамент гражданской и экологической инженерии: Урбана, Иллинойс.
Google Scholar
Эдвардс, Дж., Канга Руис, А. Э., Кук, А. А., Дерш, М. С., и Цянь, Ю. (2018). Количественная оценка изгибающих моментов в железобетонных шпалах. J. Transp. Англ. Часть Syst. 144: 04018003. DOI: 10.1061 / JTEPBS.0000125
PubMed Аннотация | CrossRef Полный текст | Google Scholar
Эдвардс, Дж. Р., Гао, З., Вольф, Х. Э., Дерш, М. С., и Цянь, Ю. (2017). Количественная оценка изгибающих моментов бетонных железнодорожных шпал с помощью поверхностных тензодатчиков. Измер. — J. Int. Измер. Конфед. 111, 197–207. DOI: 10.1016 / j.measurement.2017.07.029
CrossRef Полный текст | Google Scholar
Эдвардс, Дж. Р., Лян, Ю., Бастос, Дж. К., и Дерш, М. С. (2019). «Разработка параметрической модели для прогнозирования изгибающих моментов бетонной железнодорожной шпалы», Труды 98-го Ежегодного собрания Совета по исследованиям транспорта Национальных академий (Вашингтон, округ Колумбия).
Google Scholar
Эйзенманн, Дж.(2004a). Die Schiene als Tragbalken. Доступно на сайте: / paper / Die-Schiene-als-Tragbalken-Eisenmann / 3de7f9f956e089cddf4aac9c51f9d4147017dea6 (по состоянию на 26 августа 2020 г.).
Google Scholar
Eisenmann, J. (2004b). Рельс как опорная балка. Eisenbahningenieur 55, 22–25.
Google Scholar
Энгландер, Дж. А., и Энгландер, А. С. (2014). «Настройка монотонного прыжка по бассейну: повышение эффективности стохастического поиска применительно к оптимизации траектории с малой тягой», Труды Международного симпозиума по динамике космических полетов, 2014 г., , , Laurel, MD.
Google Scholar
Европейский комитет по стандартизации (2009 г.). EN 13230-1: 2009: Железные дороги — Путь — Бетонные шпалы и опоры — Часть 1: Общие требования. Брюссель: Европейский комитет по стандартизации.
Google Scholar
Фокс-Айви, Р., Нгуен, Т., и Лоран, Дж. (2020). Расширенные полевые испытания LRAIL для автоматического обнаружения смены пути. Вашингтон, округ Колумбия: Publ. ДОТФРАОРД-2014 Департамент транспорта Федерального управления железных дорог.
Google Scholar
Яннакос, К. (2014). Расчетные нагрузки на железнодорожное основание: анализ чувствительности к влиянию жесткости крепления. Внутр. J. Railw. 7, 46–56. DOI: 10.7782 / IJR.2014.7.2.46
CrossRef Полный текст | Google Scholar
Hay, W. W. (1982). Железнодорожная техника. Второй. Нью-Йорк, Нью-Йорк: John Wiley & Sons.
Google Scholar
Международный союз железных дорог (2004 г.). UIC 713C: Конструкция шпал-моноблоков. Париж: Международный союз железных дорог.
Google Scholar
Kaewunruen, S., Ishida, T., and Remennikov, A. (2016). Анализ воздействия на отрицательные реакции на изгиб (коробление) в железобетонных шпалах из предварительно напряженного железобетона. J. Phys. Конф. Сер. 744: 012101. DOI: 10.1088 / 1742-6596 / 744/1/012101
CrossRef Полный текст | Google Scholar
Kaewunruen, S., and Remennikov, A. (2009). Влияние балластных условий на изгиб железобетонных шпал. Concr. Aust. J. Concr. Inst. Aust. 35, 57–62.
Google Scholar
Керр, А. Д. (2003). Основы железнодорожного пути. Омаха, NE: Симмонс Бордман.
Google Scholar
Ким, Дж., Чой, С. В., Сонг, Ю.-С., Юн, Ю.-К., и Ким, Ю.-К. (2015). Автоматическое управление поездом по LTE: дизайн и оценка производительности. IEEE Commun. Mag. 53, 102–109. DOI: 10.1109 / MCOM.2015.7295470
CrossRef Полный текст | Google Scholar
Köllõ, S.А., Пушкаш А. и Кёллы Г. (2015). Гусеница с балластом и гусеница без балласта. Key Eng. Матер. 660, 219–224. DOI: 10.4028 / www.scientific.net / KEM.660.219
CrossRef Полный текст | Google Scholar
МакГенри, М. Т., Браун, М., ЛоПрести, Дж., Роуз, Дж., И Сулейретт, Р. (2015). Использование тактильных датчиков на основе матриц для оценки мелкомасштабного распределения давления на стыке балласта и стяжки в железнодорожных путях. Пер. Res. Рек. 2476, 23–31. DOI: 10.3141 / 2476-2474
PubMed Аннотация | CrossRef Полный текст | Google Scholar
Цянь, Ю., Дерш, М. С., Гао, З., и Эдвардс, Дж. Р. (2019). Железнодорожная инфраструктура 4.0: разработка и применение автоматической системы оценки состояния балластной опоры. Transp. Геотех. 19, 19–34. DOI: 10.1016 / j.trgeo.2019.01.002
CrossRef Полный текст | Google Scholar
Кирос-Ороско, Р. Дж. (2018). Изменчивость опор железнодорожных шпал из предварительно напряженного бетона и их влияние на нагрузку на изгиб. Шампейн, Иллинойс: Университет Иллинойса в Урбана-Шампейн.РС. Тезис.
Google Scholar
Кирос-Ороско, Р. Дж., Эдвардс, Дж. Р., Цянь, Ю., и Дерш, М. С. (2018). Количественная оценка условий нагружения и требований к изгибу предварительно напряженных бетонных шпал в условиях эксплуатации общих коридоров. Transp. Res. Рек. J. Transp. Res. Доска 2672, 136–145. DOI: 10.1177 / 0361198118793500
CrossRef Полный текст | Google Scholar
Резор Р. Р., Смит М. Э. и Патель П. К. (2005). Позитивное управление поездом (PTC): расчет выгод и затрат на новую технологию управления железной дорогой. J. Transp. Res. Форум 44, 77–98.
Google Scholar
Роуз, Дж. Г., Уоттс, Т. Дж., Кларк, Д. Б., и Лю, К. (2018). Применение ячеек давления сыпучих материалов для измерения межфазного давления в шпалах железнодорожных путей / балласте. Thousand Oaks, CA: SAGE Publications Ltd. doi: 10.1177 / 0361198118775872
CrossRef Полный текст | Google Scholar
Саадат, С., Шеррок, Э., Захачевски, Дж. (2018). Разработка, разработка и тестирование технологии автономных измерений геометрии треков. Вашингтон, округ Колумбия: Publ. ДОТФРАОРД-1806 Департамент транспорта Федерального управления железных дорог, 139.
Google Scholar
Саадат С., Стюарт К., Карр Г. и Пейн Дж. (2014). «Развитие технологии автономных систем измерения геометрии рельсов FRA: прошлое, настоящее и будущее», в документе Объединенная железнодорожная конференция 2014 г., JRC 2014 (Нью-Йорк, штат Нью-Йорк: Американское общество инженеров-механиков, ASME), DOI: 10.1115 / JRC2014-3860
CrossRef Полный текст | Google Scholar
Соломон, Б.(2001). Техническое обслуживание железных дорог: люди и машины, поддерживающие работу железных дорог. Оцеола, Флорида: MBI PubCo.
Google Scholar
Стандарты Австралии. (2003). Материал железнодорожного пути, Часть 14: Предварительно напряженные бетонные шпалы. Сидней, Новый Южный Уэльс: Комитет по стандартам Австралии CE-002.
Google Scholar
Стюарт К., Карр Г. и Шеррок Э. (2012). Автономное измерение геометрии пути. Railw. Газ. Int. 168, 41–44.
Google Scholar
Талбот, А. Н. (1980). Напряжения в железнодорожных путях: Бюллетени Специального комитета по напряжениям в железнодорожных путях. Вашингтон, округ Колумбия: Американская ассоциация инженеров железнодорожного транспорта (ОБЛАСТЬ).
Google Scholar
Танатхонг, С., Смит, В. А. П., и Ремде, С. (2017). «Устранение эффекта наблюдателя: удаление теней в ортофотоплане дорожной сети», в материалах Proceedings of the 2017 IEEE International Conference on Computer Vision Workshops (ICCVW) , (Piscataway, NJ: IEEE), 262–269.DOI: 10.1109 / ICCVW.2017.40
CrossRef Полный текст | Google Scholar
Таравне, К., Аранда, Дж., Эрнандес, В., Краун, С., и Монтальво, Дж. (2020). Исследование эффективности и оптимизации придорожных извещателей горячего ящика. Внутр. J. Rail Transp. 8, 264–284. DOI: 10.1080 / 23248378.2019.1636721
CrossRef Полный текст | Google Scholar
Вольф, Х. Э., Маттсон, С., Эдвардс, Дж. Р., Дерш, М. С., и Баркан, К. П. Л. (2015). «Анализ на изгиб моноблочных шпал из предварительно напряженного бетона: сравнение текущих методологий и чувствительность к условиям опоры», Труды 94-го Ежегодного заседания Совета по исследованиям в области транспорта Национальных академий (Вашингтон, округ Колумбия).
Google Scholar
Вольф, Х. Э., Цянь, Ю., Эдвардс, Дж. Р., Дерш, М. С., и Ланге, Д. А. (2016). Поведение предварительно напряженного бетона под воздействием температуры и его влияние на железнодорожные шпалы. Constr. Строить. Матер. 115, 319–326. DOI: 10.1016 / j.conbuildmat.2016.04.039
CrossRef Полный текст | Google Scholar
Сяо, Дж., Ван, Ю., Чжан, Д., Чжан, X., и Го, Дж. (2020). Испытание контактного напряжения на границе балластного слоя и грунтового основания при циклическом нагружении с помощью тонкопленочного датчика давления. J. Test. Eval. 48, 2104–2117. DOI: 10.1520 / JTE201
PubMed Аннотация | CrossRef Полный текст | Google Scholar
Йе, Дж., Стюарт Э. и Робертс К. (2019). Использование 3D-модели для повышения эффективности лазерного контроля железнодорожных путей. Proc. Inst. Мех. Англ. Часть F J. Скоростной железнодорожный транспорт 233, 337–355. DOI: 10.1177 / 0954409718795714
CrossRef Полный текст | Google Scholar
Ю, Р., Ли, Д., Нгамханонг, К., Джанелюкстис, Р., и Kaewunruen, S. (2017). Метод оценки усталостной долговечности шпал из предварительно напряженного бетона. Фронт. Встроенная среда. 3:68. DOI: 10.3389 / fbuil.2017.00068
CrossRef Полный текст | Google Scholar
Продажа бетонных железнодорожных шпал
Характеристики бетонной железнодорожной шпалы
Бетонные железнодорожные шпалы имеют широкий спектр источников материалов и обладают хорошей устойчивостью рельсов. Бетонные железнодорожные шпалы также называются бетонными железнодорожными шпалами, они могут удовлетворить требования высокой скорости и большой пропускной способности на основных железнодорожных линиях.Он свободен от воздействия климата, гниения, червей и огня. Таким образом, железобетонная шпала имеет долгий срок службы. Но он имеет плохую гибкость и легко выходит из строя из-за трещины. Кроме того, его собственный вес затрудняет замену. Все желающие купить железобетонные шпалы на продажу могут обратить внимание на детали, представленные ниже.
Классификация железобетонных шпал
- A. Как различные производственные процессы: обычные бетонные железнодорожные шпалы, предварительно напряженные бетонные железнодорожные шпалы
- Б.В качестве арматуры разного диаметра используются: стальная струна (высокопрочная стальная струна) и стальной стержень (высокопрочная стальная балка)
- C. В настоящее время существует три типа бетонных шпал, которые используются вместе на разных типах железнодорожных путей.
- D. Широкая бетонная шпала
В последнее время для постоянной поддержки рельсов на полотно пути укладывают широкие бетонные железнодорожные шпалы.
а. Большая нижняя площадь может обеспечить меньшую нагрузку на единицу площади нижнего балласта, уменьшить общую просадку рельса, предотвратить неравномерное проседание и увеличение трения основания и улучшить горизонтальную устойчивость рельса (горизонтальное сопротивление вдвое больше, чем у бетонной шпалы) и интенсивность.
б. Непрерывные работы по укладке могут значительно уменьшить зазор между шпалами, что может сохранить аккуратность и красоту гусеницы и ее основание в чистоте, а также снизить соответствующую нагрузку на техническое обслуживание.
Форма железобетонных шпал
Поперечное сечение различных типов железобетонных шпал: трапециевидной формы с узкой верхней и нижней шириной. Дизайн формы является увеличение площади несущей железнодорожного галстука. В нижней части шпалы можно разместить больше стальных стержней, чтобы предотвратить появление трещин и повреждений.Между тем, на дне железнодорожной шпалы выполнены канавки для повышения силы сопротивления между полотном пути и шпалой.
Правила использования бетонной железнодорожной шпалы
Железнодорожные пути Не допускается использование бетонной железнодорожной связи: на временных линиях, дворовых линиях; стропы легко поддаются замерзанию, грязи и отсыпке, стропы с нестабильным основанием; радиус менее 200 м изогнутых линий.
По обоим концам железнодорожного моста с балластом или без балласта, стрелочного перевода, нормального перехода, в качестве переходного участка следует уложить по 15 штук деревянных шпал.Если стык деревянной шпалы и бетонной шпалы лежит в стыке рельсов, удлиним еще пять дополнительных шпал. Мы не будем укладывать два типа железнодорожных шпал поперечно-перемешиваемым способом.
Повреждения и причины бетонных железнодорожных шпал
- A. Трещины: между нижней частью бетонной шпалы и балластом в центре железнодорожной линии не должно быть зазоров.
- B. Детонационная травма: вызвана неправильной погрузкой и разгрузкой, транспортировкой, укладкой и обслуживанием
- С.Повреждение плеча: в основном это вызвано поперечной силой поезда.
- D. Травма, вызванная катанием при сходе с рельсов
- E. Повреждение штифта винта
- F. Проблема соединения между рельсами
При использовании скомпрометированной тарелки для рыбы тарелку легко сломать. Таким образом, использование анкерного крепления мостового типа необходимо одновременно, насколько это возможно.
Меры профилактики и лечения бетонной железнодорожной шпалы
- В процессах транспортировки, погрузки и разгрузки нужно обращать внимание на отсутствие ударов.
- Подъемные работы на гусеничном ходу выполнять легковесным способом. Запрещается повреждение путевым подъемником на шпале железнодорожного пути.
- Усилить подбивочные работы. Подбивка под рельсы должна быть достаточной, а средняя часть зазора должна быть оставлена в соответствии с правилами.
- Очистка полотна гусеницы согласно плану для повышения гибкости полотна гусеницы для предотвращения затвердевания и образования грязи.
- Сохранение работоспособности крепежа для предотвращения явления сползания рельсов, а также своевременное выполнение надлежащей регулировки и правильной замены крепежа с неисправностями.
- Своевременно производить замену резиновой прокладки рельса на шпале.
Продажа высококачественных железобетонных шпал
AGICO Group обладает богатым опытом и передовым оборудованием в области железнодорожной техники. Мы поможем вам решить вышеперечисленные проблемы! У нас есть в продаже высококачественные бетонные железнодорожные шпалы различных стандартов, таких как AREMA, BS, UIC, DIN и т. Д.
Как профессиональное железнодорожное предприятие, AGICO Group специализируется на производстве железнодорожной продукции хорошего качества, такой как стальные рельсы, системы крепления рельсов, накладки на рельсы, планки для крепления рельсов, рельсовые болты, железнодорожные шипы, стальные шипы и т.д. Мир. Благодаря более чем десятилетнему опыту экспорта, мы можем предложить самые конкурентоспособные цены и высочайшее качество для наших клиентов во всем мире, потому что мы являемся фабрикой. С другой стороны, мы можем свободно заниматься международным бизнесом, потому что у нас есть опытная команда в международном отделе.Они могут предложить лучший сервис для наших клиентов. Мы искренне ищем надежных партнеров за рубежом для выхода на мировой рынок. Добро пожаловать в контакт с нами!
Бетонные шпалыCove 2M STD 200 мм x 80 мм — самые прочные бетонные шпалы Австралии на Центральном побережье, Ньюкасл, Сидней, Новый Южный Уэльс
60,00 $ 44,00 $
Бетонная шпала Cove 2M STD 200 мм x 80 мм
Продукт: Бетонные шпалы Cove 2M STD 200 мм x 80 мм
Категория: Бетонные шпалы
Цвет: песчаник
Размер: 2.0 x 200 80 мм (STD)
Наши бетонные шпалы имеют все 60 МПа и недавно были обновлены, чтобы они соответствовали пересмотренному австралийскому стандарту AS3600 — Бетонные конструкции (2018).
Шпалы могут быть построены от 200 до 4 метров в высоту. Толщина шпал будет зависеть от высоты стены и инженерных требований, а необходимая сталь — это швеллер 125 × 65 и двутавровая балка 120UB65 для стен высотой до 1 м, если иное не указано инженером.
Если вы отправите электронное письмо с указанием высоты и длины стены, а также если есть углы, доставка или самовывоз, мы можем процитировать поставку шпал и стали.Если у вас есть инженеры, дайте нам знать, что инженер написал о размере стали и шпал, чтобы помочь с расценками на поставку и доставку.
Все, что превышает 1 м, должно получить одобрение совета, и для этого потребуется инженерное обеспечение. У нас есть инженерные решения для наших шпал, которые могут быть предоставлены вашим инженером по запросу, они соответствуют требованиям AS3600 / 2018 и сертифицированы.
Доступные размеры шпал:
2,0 x 200 80 мм (STD)
2,0 x 200 100 мм (HD)
2.0 x 200 x 120 мм (EHD)
2,4 x 200 x 100 мм (HD)
2,4 x 200 x 130 мм (EHD)
2,0 x 100 x 100 мм (CRIB)
2,4 x 100 x 100 мм (CRIB)
Соответствует AS3600 / 2018
В соответствии с последними австралийскими стандартами все бетонные шпалы имеют толщину 60 МПа. Бетон соответствует AS3600 / 2018. Вся арматура соответствует требованиям ACRS.
Примечание: Все подпорные стены высотой более 1 м должны иметь одобрение совета и инженерное свидетельство.
Позвоните по телефону Sales по телефону 0492 919 736 или напишите по электронной почте sales @ concretesleeperscentralcoast.com.au для покупки или установки бетонных шпал Cove.
.: Бетонные шпалы | Группа Патил:.
Бетонные шпалы
Группа Патил — крупнейший в стране поставщик бетона. поставщики индийских железных дорог. Компания производит эти шпалы из предварительно напряженного бетона (PSC) на 12 заводах, в том числе на двух новых автоматических заводах по производству страна с общей установленной мощностью 4.85 миллионов шпал на год.
Проектирование бетонных шпал постоянно велось. претерпевает изменения в связи с НИОКР индийской Железные дороги в соответствии с меняющимися требованиями. С переходом на цемент марки M60 срок службы этих шпал увеличился. При увеличении ширины базы давление в балласте увеличивалось. снижение на 10%, что приводит к пропорциональной экономии на балласте и эксплуатационные расходы.
Индийские железные дороги планируют увеличить нагрузку на ось в в ближайшие годы и новая конструкция бетонных шпал будет удовлетворить будущие потребности железных дорог.Компания также предусматривает использование специальной многопроволочной проволоки с повышенным UTS. на который общий вес стали на шпалы будет обрушился на 25%.
Компания имеет производственные предприятия, расположенные в г. Анара, г. Бхубанешвар (Кайпадар-роуд), Биласпур (Карги-роуд), Мадурай (Тирумангалам), Тумкур, Удвада и Вадиярам, пока появляются новые автоматизированные заводы в Бади Хату и Бхурвал. Компания также является первый в стране завод по производству бетона, сертифицированный ISO.
Шпалы, производимые предприятием, подходят:
- Обычная широкая колея: у этого спального места трапециевидная поперечное сечение шириной 154 мм вверху и 250 мм внизу и 210 мм на рейке сиденье.
- Points & Crossing: Эти специализированные шпалы используется для удержания переключателей, переходов CMS и направляющих рельсов для главная линия и стрелочные переводы. Скоростные поезда могут ехать эти макеты PSC с максимальной безопасностью.
- Защитный поручень: используются на подходах к балке. мосты для предотвращения опрокидывания сошедшего с рельсов поезда.
- Switch Expansion Joints: Это шпалы PSC для компенсаторы выключателя (с максимальным зазором 120 мм) для длинных сварных рельсов для рельсов 52 кг и 60 кг с использованием соответствующие стулья.
- Проверочная направляющая на поворотах: Проверочные направляющие абсолютно важно предложить внутреннюю сторону для более резких кривых, которые больше 50 во избежание схода с рельсов.
- Железнодорожные переезды: формируются в различных точках, где дорога пересекает железнодорожный путь на том же уровне и используемые здесь шпалы изготовлены из 60 кг UIC или 52 кг проверить рельс.
- Dual Gauge: Уникальный предварительно напряженный бетонный двойной Калибровочные шпалы были разработаны для обработки поезда метровой и широкой колеи, чтобы оба поезда могли бегать по той же дорожке. Все спящие изготовлены под системой стрессового стенда с очень строгие меры контроля качества.
Бетонные шпалы Сидней, Бетонные подпорные стены DIY
Я Ли Бенсон, занимаюсь установкой подпорных стен и ограждений и участвую в строительной игре более 15 лет. Я хочу помочь людям построить свои собственные подпорные стены из бетонных шпал в Сиднее, Ньюкасле, Центральном побережье и Вуллонгонг в районах Нового Южного Уэльса. В Сиднее много подпорных стен, сделанных из дерева, которое деформируется в погодных условиях, может быть съедено белыми муравьями, обесцвечивается и даже гниет. Зачем покупать то, что долго не прослужит? Для меня это не имеет смысла.
Думаете, что сможете сделать самодельную бетонную подпорную стену в Сиднее, но все же нуждаетесь в небольшой дополнительной помощи или совете? Не волнуйтесь, позвоните в команду, мы будем более чем рады ответить на ваши звонки и помочь вам построить подпорную стену, как профессионалы! Телефон: 02 8607 7164
Мы также поставляем бетонные шпалы для коммерческих и гражданских проектов высотой до 4 м, пожалуйста, позвоните нам для получения дополнительной информации.
Подпорные стены Сидней
Купить Подпорные стены из бетонных шпал Сидней, Ньюкасл, Центральное побережье и Вуллонгонг в районах Нового Южного Уэльса !! Бетон служит на всю жизнь.И я упростил самодельную бетонную подпорную стенку. Мы продаем то, что используют ремесленники и профессионалы, не попадайтесь на дешевую и неприятную систему удержания, которую вы можете приобрести на своем местном оборудовании. Наши бетонные шпалы были спроектированы (свяжитесь со мной, если вам нужны технические характеристики инженера).
Подождите, пока вы не почувствуете наши стальные балки и шпалы, когда вы держите их в руках, вы знаете, что у вас качественный продукт. Знаете ли вы, что некоторые из наших бетонных шпал можно использовать для строительства подпорных стен высотой 4 метра! Конечно, это не то, что вы можете сделать своими руками, но если вам нравится наш продукт, мы можем передать наши спецификации наших бетонных шпал вашему инженеру, и он может спроектировать вашу стену для вас, используя наш продукт высотой до 4 м, для этого потребуются специальные цитата от нас, конечно, для вашего дома в Ньюкасле, Центральном побережье или Сиднее.
Но если вы просто выполняете свою стандартную работу на заднем дворе, просмотрите наши товары для подпорных стен своими руками в Интернете, и мы можем доставить их к вашей двери.
Мы являемся поставщиком подпорных стенок в Сиднее, Ньюкасле, на Центральном побережье. Бетонные шпалы Вуллонгонга, штат Новый Южный Уэльс, производятся в Австралии и отправляются к вам домой.
Это так просто.
Подпорные стены своими руками Сидней
Не стесняйтесь звонить мне. Если вы чего-то не понимаете или нуждаетесь в помощи, позвоните мне или свяжитесь со мной по адресу sales @ gorillawall.com.au Я буду более чем счастлив помочь вам с вашими домашними принадлежностями для подпорных стен в Сиднее, Ньюкасле, Центральном побережье, Вуллонгонг, штат Новый Южный Уэльс, и предоставить вам информацию, необходимую для профессиональной работы. Телефон: 02 8607 7164
Плинтусы под забором Сидней
Мы не только поставляем бетонные шпалы в Сидней, Ньюкасл, Центральное побережье, Вуллонгонг, штат Новый Южный Уэльс, мы поставляем цоколи под заборы. Большинство ограждений в Сиднее имеют деревянные или тонкие стальные цоколи, которые ржавеют или гниют.Мы можем поставить цоколи под забором из бетона, которые имеют сопротивление 50 МПа, с двумя поперечными стержнями для прочности, и не только для того, чтобы они выглядели в 100 раз лучше и служили дольше. Я знаю, что бы использовал для своей собственности.
Построенный в Китае завод в Бангладеш начинает производство бетонных шпал для проекта мега-рельса — Синьхуа
Завод, построенный в Китае, приступил к производству бетонных шпал для проекта мегаполиса в Бангладеш, соединяющего крупнейший в стране мост Падма, который также строился китайскими фирмами.Построенный China Railway Group Limited (CREC), ведущим мировым строительным конгломератом, сборочные работы на заводе по производству шпал, первом в своем роде в Бангладеш, были завершены 22 августа, когда он начал производство в небольших масштабах. Министр железных дорог Бангладеш Нурул Ислам Суджан в среду официально открыл завод на церемонии в районе Фаридпур страны, примерно в 101 км от столицы Дакки. Завершение строительства завода по производству бетонных шпал для проекта железнодорожного сообщения моста Падма (PBRLP), который внесет значительный вклад в обеспечение связи в регионе, было завершено, несмотря на воздействие COVID-19 в стране.170-километровый PBRLP — один из самых значительных проектов, строящихся CREC. Проект стоимостью более 3 миллиардов долларов США более 80 процентов профинансирован Exim Bank of China. Проект будет в значительной степени способствовать региональному соединению и экономическому развитию. Официальные лица заявили, что на этом заводе будет произведено 370 000 шпал для гусениц PBRLP. Посол Китая в Бангладеш Ли Цзимин поздравил в письме должностных лиц CREC с оказанием помощи в создании завода по производству бетонных шпал.Завод по производству шпал может самостоятельно производить более десятка видов шпал, включая шпалы широкой колеи шириной 1676 мм, шпалы широкой колеи без балласта и шпалы двойной колеи, которые в настоящее время используются в Бангладеш.