пропорции, технология изготовления своими руками
Пескобетон универсальный материал, который используется в большинстве строительных работ при возведении зданий и облагораживании территории, производство пескобетона не сложное, ингредиенты доступные, поэтому изготовить раствор можно в домашних условиях.
Состав пескобетона:
- Портландцемент с маркой от М300;
- Очищенный песок;
- Чистая холодная вода;
- Пластификаторы.
Специальные добавки применяются при изготовлении по желанию, они наделяют массу дополнительными свойствами.
Состав материала может и не отличается многокомпонентностью, но, несмотря на это он обладает множеством положительных свойств.
Преимущества пескобетона:
- Хорошие показатели прочности
- Долговечность;
- Устойчивость к перепадам температур и морозу;
- Водонепроницаемость;
- Отсутствие усадки.
Пескобетон практичный материал, применяется на различных этапах работ при строительстве малоэтажных зданий, при выполнении фундаментальных и монтажных работах.
Строители выделяют один вид пескобетона – пескобетон М300. Этот вид материала сочетает в себе все необходимые качества и находится в доступной ценовой категории. Кроме того, технология производства пескобетона достаточно простая и разрешает, при соблюдении нормативов, изготовить раствор пескобетона М300 своими руками.
Сфера применения пескобетона М300:
- Изготовление фундамента здания;
- Бетонирование лестничных пролетов;
- Заливка пола;
- Оштукатуривания поверхности;
- Заделка межплиточных и межблочных швов;
- Как раствор для укладки кирпичей и блоков;
- Заливка отмосток;
- Прокладка пешеходных дорожек и тротуаров;
- Изготовление тротуарной плитки и бордюров;
- Изготовление пескобетонных плит и блоков;
- Бетонирования разнообразных элементов;
- Заливка железобетонных конструкций.
Пескобетон современная альтернатива обычному бетону. Пескобетон прочный, имеет небольшой вес, что благоприятно сказывается на фундаменте, экономичный и доступный для широких масс. Изделия из пескобетона пользуются большим спросом, так как материал не требует особого ухода и прост в работе.
Давайте подробнее рассмотрим технологию по изготовлению пескобетона и его состав, а также узнаем, как сделать пескобетон своими руками.
Составляющие пескобетона
В состав пескобетона входят три компонента – цемент, песок и вода. Но, несмотря на это, каждый производитель строительных материалов пытается разработать рецепт материала, который будет более совершенен, чем у конкурентов.
Для этого в состав добавляются специальные компоненты или изменяют пропорции материала. Специальные добавки дают раствору новые качества и повышают технологические показатели бетона. В итоге получаются виды пескобетона, которые применяются в разных направлениях строительства – от кладки кирпичей до заливки тротуара.
Изготовить пескобетон самостоятельно можно, главное приобрести материалы высокого качества и соблюдать инструкцию.
Цемент
На рынке строительных материалов различается до 30 видов цементных смесей, при производстве пескобетона чаще отдают предпочтение портландцементу, основу которого составляет измельченный до порошкообразного состояния клинкер и гипс.
Важное значение имеет марка цемента, для создания качественного долговечного покрытия лучше использовать портландцемент марки М300 и выше. Этот тип цемента гарантирует такие свойства как:
- Прочность;
- Устойчивость к влаге;
- Увеличенный срок эксплуатации;
- Прочность на изгиб;
- Плотность;
- Устойчивость к внешним воздействиям;
- Высокие показатели при сжатии и растяжении.
Использование качественного цемента в составе наделяет пескобетон вяжущими свойствами, обеспечивает морозостойкость готового изделия.
Песок
От качества выбранного песка зависят характеристики готового пескобетона и сфера применения полученного раствора. Например, для работ по заливки пола или фундамента используется песок крупной фракции, а для работ, которые требуют деликатного подхода, таких как оштукатуривания или производства пескобетонных блоков используется песок значительно мельче.
Песок должен быть очищенный и тщательно просеянный. Допускается использование обычного речного песка, но на очистку от примесей уйдет много времени. При возможности, лучше приобрести строительный песок в специализированном магазине.
Покупной песок изготавливается согласно нормативам ГОСТа 8736-93 который контролирует чистоту сырья и фракцию песчинок. По стандарту размер песка не превышает 0,5 мм.
Благодаря характерным свойствам, песок устойчив к нагрузкам и распределяет давление, песок составляет основную массу пескобетона – в растворе используется 2 — 4 части на 1 часть цемента (зависит от функционала).
Пластификаторы
Для улучшения показателей материала производители часто применяют различные специальные добавки, это относится ко многим видам строительных материалов, включая производство пескобетона М300.
Они придают новые свойства, например, устойчивость к возникновению плесени и грибка, устойчивость к воде, морозостойкость и т.п. это позволяет использовать материал в различных условиях – проводить работы при отрицательных температурах, использовать в местах с повышенной влажностью.
Так же пластификаторы значительно увеличивают показатели прочности, плотности и долговечности продукта, расширяют сферу применения. При изготовлении смесей можно применять несколько типов добавок, главное предварительно изучить инструкцию.
Технология производства пескобетона своими руками
Пескобетон можно приобрести в магазине в виде готовой смеси, которую необходимо лишь разбавить водой. Можно, собрав необходимые ингредиенты изготовить, строго соблюдая пропорции, пескобетон своими руками.
Рецептура основного состава:
- Портландцемент М300 – 1 часть;
- Очищенный песок – 2 – 3 части;
- Вода и при желании пластификаторы.
Кроме основного сырья, понадобится специальное оборудование для производства пескобетона, к которым относится бетономешалка и следующие инструменты:
- Большая емкость, в которой будут смешиваться сухие компоненты;
- Большое корыто, если нет бетономешалки;
- Ведро;
- Строительный миксер или дрель со специальной насадкой;
- Лопата;
- Используется только холодная вода
Пропорции нарушать нельзя, при несоблюдении правильного процентного соотношения раствор будет не годен для использования.
Процесс приготовления раствора:
- Предварительно в отдельной емкости смешать сухие составляющие – песок и цемент, тщательно перемешать. Чтобы компоненты равномерно распределились по всей массе;
- Подготовить емкость с водой, если есть бетономешалка залить воду туда.
Количество воды рассчитывается по этому показателю – 10 кг сухой смеси/ 1,5 литра воды. Вода должна быть холодной, ее температура не больше 20 градусов.
- Если используются пластификаторы их стоит предварительно развести в воде.
- В емкость с водой постепенно вводятся сухие ингредиенты и одновременно перемешиваются, чтобы избежать возникновение комков;
- Масса тщательно перемешивается до однородного состояния, смесь должна быть пластичной и не расслаиваться.
- Полученный раствор оставляют отдохнуть минут на 5 – 10, за это время компоненты наберут необходимое количество воды и приобретут характерные свойства.
- Через это время, смесь повторно перемешивается, теперь она готова к использованию.
Если превысить количество воды смесь потеряет прочность, а готовая поверхность покроется трещинами.
Полученный раствор годен для работ в течение двух часов, спустя этот промежуток времени пескобетон затвердевает и теряет технологические качества.
Во время работы пескобетон М300 укладывается слоями толщиной 10 — 50 мм, при укладке армирующего основания слой может достигать толщины в 100 мм.
Пескобетон оптимальный выбор для строительства, изготовить раствор можно в домашних условиях, процесс работы не сложный. Можно не просто замесить раствор, но и своими руками изготовить из него, например, блоки для строительства жилых и нежилых помещений.
Для производства пескобетона оборудование не потребуется, ингредиенты продаются в любом строительном магазине по доступной цене.
состав, характеристики, область применения и производители
Дата публикации: 02.02.2019 11:24
Пескобетон представляет собой готовую сухую смесь из портландцемента, песка мелкой либо крупной фракций, а также специальных модификаторов на основе минеральных химических соединений. В процессе добавления воды исходная сухая смесь обретает пастообразную консистенцию, после укладки быстро затвердевает и сохраняет прочность на длительный период.
Несмотря на относительную новизну, этот материал уже завоевал популярность среди строителей и мастеров-ремонтников, позволяя быстро и качественно вести работы по обустройству монолитных конструкций, дорог, ремонту помещений и придомовых территорий. Пескобетон может выступать составляющим компонентом керамзитобетона и других монолитных стройматериалов.
Особенности состава пескобетона
Отечественные производители пескобетона жестко соблюдают пропорции его исходных компонентов, поскольку каждой марке материала свойственны конкретные потребительские характеристики, необходимые для определенных технологических операций. Так, самый распространенный пескобетон марки М300 имеет весовое соотношение крупнофракционного речного песка 3-4 мм и цемента марки М500 как 2,5 к 1. Количество воды подбирают по месту, для абсолютно сухой смеси потребуется около 0,2 литра на 1 кг пескобетона, после чего состав следует тщательно перемешать.
Важными составляющими материала выступают модифицирующие добавки, позволяющие привести качественные характеристики пескобетона к желаемым, сделав конечный продукт более прочным, стойким к воздействиям влаги, мороза и агрессивных химреагентов. Отдельные марки пескобетона имеют структуру разной зернистости и разный набор добавок, что отражается как на конечной стоимости смесей, так и на эксплуатационных качествах таковых. Во всех случаях материал практически не дает усадки и способен выдержать значительные механические нагрузки.
Маркировка пескобетонных смесей сходна с маркировкой строительного бетона, отображая предел прочности застывшего материала на сжатие, выраженный в килограммах на см. кв.: М200, М300 и пр. Этот параметр, хотя и важен, но не влияет на истираемость и трещиностойкость готового пескобетона. Кроме этого, материал может иметь разный размер песчаных частиц и в соответствии с этой характеристикой бывает мелкофракционным(зерно 1,2 мм), среднефракционным (зерно 1,2 — 2,5 мм) и крупнофракционным (зерно до 4 мм). Причем, среднефракционнаясмесь считается наиболее универсальной.
Применение готового пескобетона
Изготовленный в заводских условиях согласно госстандарту фасованный пескобетон находит применение в частном, промышленном и общественном строительстве, в том числе при:
- обустройстве подстилающих и чистых полов;
- изготовлении внешних отмосток, парковых дорожек и стяжек;
- заделке выбоин, швов, рустов, сколов и трещин в железобетоне;
- штукатурных и отделочных операциях;
- монтаже сборных бетонных конструкций;
- изготовлении штучных изделий и декоративных составов с введением мраморной/гранитной крошки, красителей, опила, шлаков и пр.
Материал во многом перенял свойства портландцемента — прочность, невосприимчивость к коррозии и усталости, механическую устойчивость. Благодаря этому он используется для укладки несущих бетонных слоев, крепления ЖБИ, изготовления лестниц и сточных желобов.
Практика показывает, что самостоятельное изготовление пескобетонных смесей часто дает негативный результат, поскольку среди подручных материалов не всегда найдутся песок с нормированной зернистостью, качественный цемент без золы, пластификаторы и модификаторы. Поэтому даже при возведении частного дома или наружном оборудовании дачного участка полезно приобретать заводской упакованный материал, соответствующий отраслевым нормативам и проходящий лабораторное тестирование.
Пескобетон | BETON WERK
Пескобетон
Пескобетон — это безусадочная высокопрочная сухая смесь из портландцемента, просеянного песка и добавок (при необходимости). Он незаменим не только при аварийных работах, когда важна скорость схватывания растворной смеси, но и популярен при производстве работ в новом строительстве, реконструкции или ремонте.
Портландцемент служит неорганическим вяжущим, песок – фракционным наполнителем, а минеральные добавки улучшают технологические свойства смеси. При соединении с водой и последующем схватывании, смесь начинает набирать необходимую прочность.
Пескобетон относят к мелкозернистым, а по назначению — к конструкционным бетонам.
Узнайте стоимость
Рассчитайте стоимость вашего заказа прямо сейчас с помощью онлайн калькулятора на странице «расчет стоимости».
Преимущества пескобетона:
- пластичность при укладке
- обладает свойством ускоренного затвердения
- плотность
- высокая прочность
- водонепроницаемость (это позволяет экономить на дополнительных гидроизоляциях)
- коррозионная стойкость
- морозостойкость (наивысший показатель морозостойкости достигается за счёт применения низкоалюминатного белого портландцемента)
- устойчив к усадкам (это важно при использовании пескобетона в несущих конструкциях)
- износостойкость
Применение пескобетона:
- устройство фундаментов
- устройство высокопрочных и износостойких стяжек и бетонных полов
- устройство кирпичной кладки
- замоноличивание железобетонных конструкций и узлов
- заделка стыков и швов
- изготовление пескобетонных стеновых блоков
- изготовление монолитных плит
Консультация и заказ
Получите консультацию, узнайте стоимость и сделайте заказ по телефону отдела продаж +7 (473) 240-05-04.
«BETON WERK» осуществляет обмен товарного бетона и цементного раствора на щебень и цемент.
Пескобетон изготовление: Производство пескобетона: пропорции, технология изготовления своими руками. | Пенообразователь Rospena
Состав, свойства, производство и области применения пескобетона
Пескобетон представляет собой строительный материал, применяемый для сооружения фундамента, бетонирования различных строительных конструкций, кладки стен, выполнения оштукатуривания разных поверхностей. Следует сказать, что этот строительный материал имеет различное применение. Однако в каждом конкретном случае применяется сухая смесь пескобетона определенной марки или готовые пескобетонные блоки. Как правило, пескобетонные строительные материалы обладают более низкой ценой, чем многие другие. При этом стены, сооруженные из пескобетонных блоков, отличаются легкостью по сравнению с кирпичными стенами или построенными из другого материала, а это позволяет значительно снижать нагрузку на несущие конструкции, а также уменьшать средства, затраченные на все строительство.
Пескобетон – это высокопрочная смесь портландцемента, крупного песка-наполнителя (до 3 мм) и добавок-пластификаторов (химических), предназначенных для улучшения свойств пескобетона. Пескобетон изготавливается на бетонных заводах в бетоносмесительных установках согласно предварительным расчетам, которые учитывают требуемые показатели и свойства.
Основными свойствами пескобетона являются прочность, водонепроницаемость, морозоустойчивость, коррозионная стойкость. Все они позволяют применять пескобетон при выполнении следующих строительных работ: процессе укладки несущего пола (слоя) в подвалах, промышленных сооружениях, гаражах, мастерских, цехах, при сооружении отливок и фундаментов, а также при осуществлении монтажных работ. Благодаря наличию крупных фракций песка в составе пескобетона, он пригоден для производства различных строительных конструкций, которые подвергаются большим нагрузкам.
Так как портландцемент входит в состав пескобетона, то он придает этому строительному материалу такие свойства, как плотность, прочность, морозостойкость и стойкость к коррозии. Причем наблюдается возрастание этих показателей в процессе увеличения объемной доли портландцемента в составе пескобетона.
В процессе производства пескобетона на бетонных заводах вначале выполняется процедура проектирования его состава. При этом особое внимание уделяется количественному составу всех компонентов и их обоснованию, поскольку при любом изменении пропорций происходит изменение свойств пескобетона. Далее осуществляется отмеривание специальными дозаторами всех составляющих компонентов способом отвешивания или объемного отмеривания. После этого отмеренные ингредиенты помещаются в бетоносмесительную установку, осуществляющую принудительное смешивание, которое производится из-за жесткости и вязкости пескобетона, имеющего в своем составе фракцию крупного песка. Технология приготовления пескобетона не относится специалистами к сложным процессам.
Пескобетон, который перемешан до однородного состояния, помещается в специальные емкости или бункеры, предназначенные для его транспортировки. При соблюдении технологии производства, а также правильно организованной транспортировке пескобетона его плотность, вязкость и другие физические показатели этой бетонной смеси не меняются. Хотя пескобетон, благодаря своей достаточно плотной массе, не расслаиваться, а осадка крупных фракций песка не происходит из-за вязкости портландцемента. Однако соблюдение технологии транспортировки пескобетона обязательно, а также при этом необходимо следить за состоянием транспортируемого строительного материала.
Сухая смесь пескобетон М300 и другие смеси применяются при строительстве различных элементов зданий, начиная фундаментом, а заканчивая крышей. Обычно эта смесь используется для выполнения заливки фундамента, сооружения бетонной стяжки пола, иногда и для кладки стен, а также и других строительных работ, так как она является наиболее подходящей для самых нагружаемых конструкций, как впрочем, и смесь пескобетона М400.
По уникальной и современной рецептуре Компанией «ВосЦемПродукт» разработан:
Пескобетон М 300 с МЕЛКИМ наполнителем от 0,8-1,2мм для приготовления кладочных и атмосферостойких фасадных штукатурных растворов увеличенной прочности.
Пескобетон М300 СРЕДНЕЕ зерно наполнителя от 1,8-2,2 мм для выполнения прочной стяжки пола и устройства теплых полов.
Пескобетон М-300 КРУПНЫЙ наполнитель до 4мм — максимально прочный пескобетон для заливки фундаментов, цоколей, плит перекрытий.
Увеличена пластичность раствора для улучшения текучести раствора (растекаемости).
Исключено образование трещин (усадка) и выделение извести (высолы) на готовой поверхности.
Для ремонта бетонных элементов, а также бетонирования лестниц и кладки стен чаще всего используется пескобетон М150. Смесь пескобетона М150 имеет универсальное применение, например, как специальная штукатурка. Для осуществления оштукатуривания под шпатлевку или под покраску пескобетон М150 может применяться наравне с сухой специальной смесью, имеющей маркировку М100. Обычно эти марки пескобетонных смесей чаще всего применяются небольшими партиями.
Пескобетон М300 и его применение
Бетонная смесь на мелких плотных заполнителях с фракциями до 5 мм и цементном вяжущем была обозначена, как мелкозернистый бетон (пескобетон) еще в 82 году прошлого века в ГОСТ 25192, но на текущий момент ни один из действующих стандартов достаточно полно не регламентирует все производимые в России и импортируемые из ближнего/дальнего зарубежья пескобетоны. Связано это, как с практическим отсутствием в РФ актуализированных стандартов по бетонным смесям, так и очень большим количеством разных рецептур пескобетонов, получаемых при варьировании крупностью наполнителя, качественным составом вяжущего и различными специализированными добавками.
Из пекобетонов с различными эксплуатационными свойствами строители выделяют пескобетон М300, средняя прочность которого делает смесь почти универсальной для выполнения целого перечня строительных работ. Прочность пескобетона М300 позволяет использовать бетонную смесь для кладки, покрывной наружной и внутренней штукатурки, формирования постелей под фундаменты и фундаментов, цоколей, стяжки пола и ряда готовых армированных изделий (плиты, перемычки, бордюры, еврозаборы, тротуарная плитка и т.д.). Лучшие отечественные и зарубежные производители варьируют крупностью песка и специальными добавками, получая пескобетоны М300, преимущественно ориентированные на выполнение конкретных строительных задач. Для стяжки пола и изготовления штучных армированных изделий используют пескобетон М300 на фракционированных песках с крупностью 1,8-2,2 мм, пескобетон М300 на песках мелких фракций (0,8-1,2 мм) применяют в качестве альтернативы кладочным и штукатурным растворам, пескобетон М300 на крупных песках (2,5-4,0 мм) — для работ по забивке фундаментов, цоколей, формования плит перекрытий и перемычек.
Стяжки пола выполняют из пескобетонов М300 на песках с средней крупностью фракций, причем если это фракционированные пески, а в смесь введены пластифицирующие добавки и микрокремнезем, то пескобетон М300 служит хорошей альтернативой специализированным наливным полам, образуя при заливке самонивелирующуюся поверхность. В целом многие рецептуры смеси позволяют использовать пескобетон М300 для многослойных и однослойных стяжек пола, а также теплых полов с электро или трубно-водяным подогревом. Но на практике решение всех задач стяжки пола могут реализовать только пескобетоны с хорошей удобоукладываемостью, самоуплотняемостью, отсутствием температурно-влажностной усадки и морозостойкостью, расширяющей температурный интервал проведения работ и устраняющей риски трещинообразования при воздействии отрицательных температур.
Следует отметить, что пока в стране пескобетонов М300 с полным комплексом требуемых свойств для стяжки пола, наливных и теплых полов очень мало, причем, как импортируемых, так и отечественных. Лучшим по эксплуатационным характеристикам строители (подрядчики и индивидуальные застройщики) признают пескобетон М300 QUICK BETON, изготавливаемый в виде сухой смеси на фракционированном песке и высококачественном вяжущем с комплексом добавок, оптимизирующих смесь под выполнение всех типов стяжки пола, наливных и теплых полов, а также изготовления штучных изделий.
Похожие статьи
Пескобетон: особенности строительной смеси | Статья ООО «МонолитКомплектСервис»
Пескобетон – один из самых востребованных строительных материалов высокой прочности, имеющий в составе портландцемент, песок и наполнители для повышения эксплуатационных свойств. Представляет собой самовыравнивающую быстрозатвердевающую смесь серого цвета. Пескобетон используется в строительстве на совершенно различных этапах: возведение фундамента, кладка стен, заливка стяжек на полах, бетонирование поверхностей, другие монтажные, отделочные и строительные работы. Он позволяет создавать идеально ровную поверхность независимо от ее дальнейшей обработки.
В отличие от классического бетона пескобетон имеет максимальную влагонепроницаемость, небольшой вес, практически не дает естественной усадки. Эти отличительные особенности во многих случаях делают его более предпочтительным строительным материалом. Среди прочих преимуществ пескобетона:
- простота в укладке – для работы с ним не понадобятся ни специальные инструменты и оборудование, ни профессиональные умения;
- высокая скорость проведения работ за счет быстрого отвердевания – по обработанной поверхности можно ходить уже спустя 2 суток;
- прочность и надежность – выдерживает большие нагрузки, не боится механических повреждений;
- неподверженность коррозии;
- обеспечение снижения нагрузки на грунт и конструкции за счет небольшого веса;
- устойчивость к высоким температурам, а также к их перепадам;
- пластичность готового раствора – что значительно облегчает работу;
- невысокая стоимость, которая делает его доступным для широкого круга покупателей.
Пескобетон разводится водой непосредственно на месте работ перед их началом. Совместная масса представляет собой густой бетонный раствор. Его накладывают тонким слоем на обрабатываемую поверхность, и, заполняя все неровности, он превращается в ровное и прочное покрытие.
Пескобетон марки М300 – наиболее популярный среди аналогов
Одной из самых востребованных и эффективных сухих строительных смесей является пескобетон М300. Благодаря своим высоким эксплуатационным характеристикам и универсальности он успешно задействуется в разнообразных строительных и отделочных работах, практически на всех их этапах.
Основные сферы применения пескобетона марки М300:
- Заливка и стяжка полов. Материал обеспечивает безукоризненное качество стяжки за счет устойчивости к повреждениям и большой скорости твердения (стяжка высыхает за 2 суток).
- Создание перекрытий. М300 используется в бетонировании несущих конструкций, производственных площадок на территории заводов, креплении ЖБ-конструкций.
- Аварийные и реставрационные работы. М300 – незаменимый вид пескобетона из-за оперативного затвердевания.
- Кладка садовых дорожек, изготовление бордюров, плитки для тротуаров. Высокая устойчивость к воздействию внешних факторов обеспечивает М300 хорошую укладку под открытым небом.
М300 можно использовать в строительстве зданий и конструкций разного назначения и любой сложности, особенно там, где требуется сформировать максимально прочную поверхность. Если вам нужно заказать пескобетон у производителя, компания «МонолитКомплектСервис» окажет вам грамотные консультации и поможет с выбором марки.
Пескобетон М300 «Армированный» с фиброволокном
Пескобетон М300 «Армированный» с фиброволокном используется для напольной стяжки. Позволяет создать ровный и прочный пол в жилых, производственных помещениях, гаражах. Это сухая строительная смесь, в состав которой входит микроармирующие волокна. Этот элемент увеличит прочность напольного покрытия, предупредит возникновение трещин и деформаций в дальнейшем. Для изготовления раствора для стяжки не понадобится вспомогательных компонентов.
Если используется М300 с микроармирующими волокнами, не нужно приобретать армирующую клетку. И без нее конструкция будет достаточно укреплена. Смесь предназначается для создания мелкозернистого бетона с продолжительным сроком эксплуатации. Она может применяться не только для стяжки пола, но и для иных строительных работ.
Смесь М300 отличается преимуществами:
- Экономия денег и времени, так как не потребуется монтировать арматуру.
- Минимальная усадка.
- При усадке не образуются трещины.
- Высокая прочность на изгибах и при сжатии.
Пескобетон М300 «Армированный» с фиброволокном позволяет:
- Стойкость к механическому истиранию.
- Устойчивость к возникновению коррозии, образующейся под воздействием влаги и прочих атмосферных факторов.
- Устойчивость к появлению микротрещин при влажностной и температурной усадке.
- Ударопрочность.
Это современный продукт, качественно улучающий все характеристики бетона и упрощающий строительство. Состав М300 с фибро-волокном только получает свое распространение в России. Продукцию предлагает наша компания ВосСмеси. Мы самостоятельно производим смеси. Свое производство позволяет сделать стоимость М300 со специальными микроармирующими волокнами минимальной.
Особенности применения пескобетона марки М300Для применения пескобетона М300 с микроармирующими волокнами не нужно приобретать дополнительные компоненты. Смесь просто разбавляется водой, а затем все размешивается используя бетономешалку.
Для качественного строительства нужно обеспечить максимальный уровень сцепки материалов друг с другом. Поэтому, перед стяжкой, основа очищается от масла и грязи. Снимаются остатки краски. Затем наносится акриловая грунтовка. Только потом используется М300 с микроармирующими элементами.
Пескобетон М300 с микроармирующими волокнами от «ВосСмеси» сертифицирован и соответствует ГОСТ РФ что, подтверждает ее безопасность, надежность и соответствие всем российским и международным стандартам. Смесь сухая М300 с фиброволокном предлагается в упаковках на 50 кг. Этого объема хватит для проведения достаточно обширных работ.
Полезные статьи
Расход цементно-песчаной смеси на 1 м2
Промышленный песок (М-песок) для бетона — свойства и преимущества
🕑 Время чтения: 1 минута
Технический песок (M-Sand) — заменитель речного песка для бетонных конструкций. Промышленный песок получают из твердого гранитного камня путем дробления. Дробленый песок кубической формы со скругленными краями, промытый и рассортированный как строительный материал. Размер искусственного песка (M-Sand) менее 4,75 мм. Почему используется промышленный песок? Промышленный песок — альтернатива речному песку.В связи с быстрым ростом строительной индустрии спрос на песок значительно увеличился, что в большинстве случаев привело к дефициту подходящего речного песка. Из-за истощения запасов речного песка хорошего качества, используемого в строительстве, было увеличено использование искусственного песка.
- Хорошо отсортирован в необходимой пропорции.
- Не содержит органических и растворимых соединений, влияющих на время схватывания и свойства цемента, поэтому необходимая прочность бетона может быть сохранена.
- Не содержит примесей, таких как глина, пыль и ил, увеличивает потребность в воде, как в случае речного песка, которые ухудшают сцепление между цементным тестом и заполнителем.
Таким образом повышается качество и долговечность бетона.
- M-Sand получен из особой твердой породы (гранита) с использованием современной международной технологии, таким образом, достигается требуемое свойство песка.
- M-Sand имеет кубическую форму и производится с использованием таких технологий, как ударная порода из высокоуглеродистой стали, а затем процесс ROCK ON ROCK, который является синонимом естественного процесса, протекающего в информации о речном песке.
- Для производства M-Sand используются современные и импортные машины, обеспечивающие требуемую зону сортировки песка.
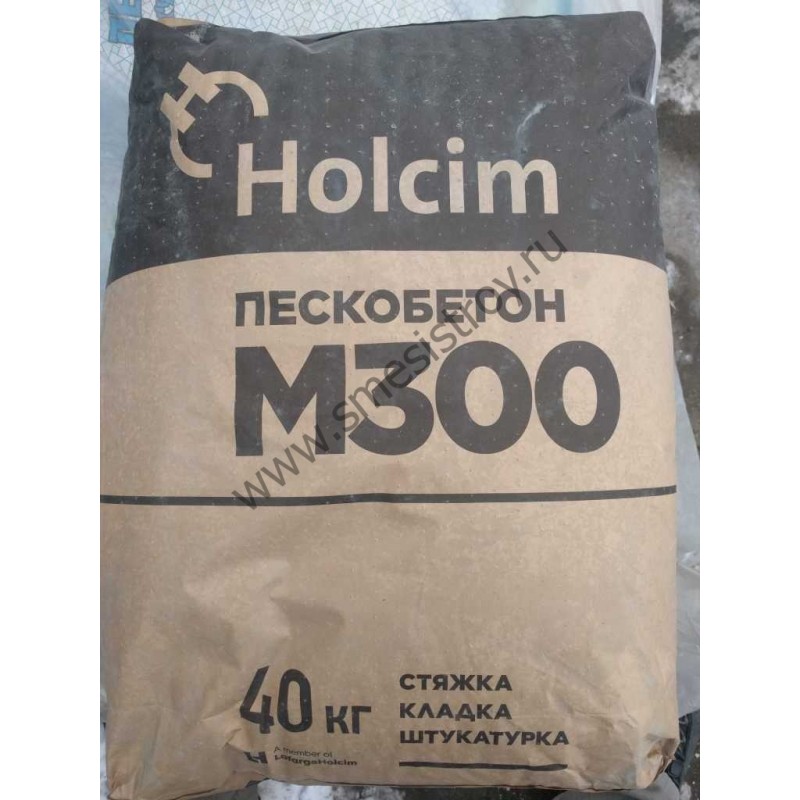
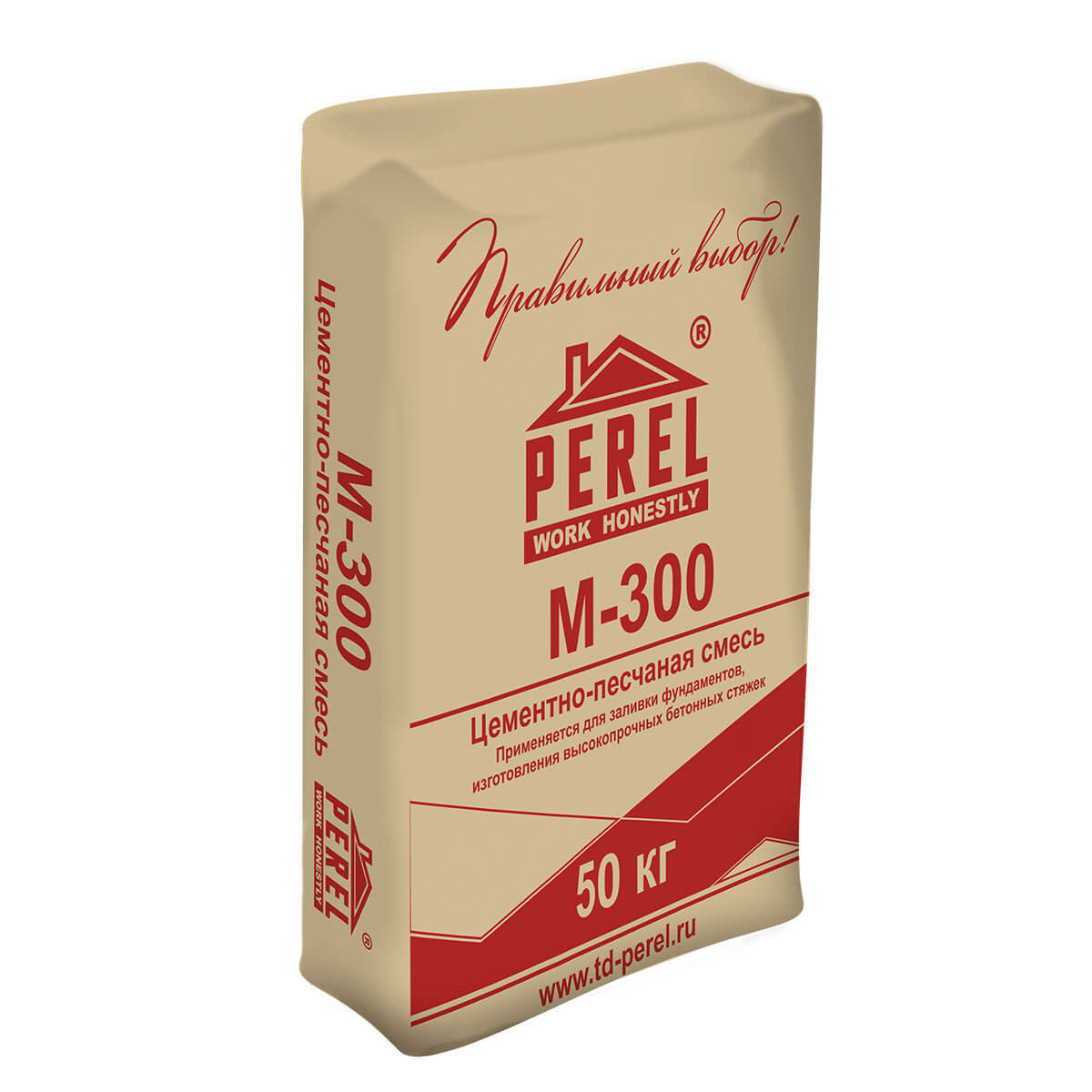

Плюсы и минусы промышленного песка
Прежде чем мы перейдем к преимуществам и недостаткам искусственного песка, что именно такое промышленный песок? Промышленный песок — это песок, полученный путем измельчения горных пород, карьерных камней или более крупных кусков заполнителя на частицы размером с песок.Природный песок, с другой стороны, представляет собой песок естественной формы, добытый из русел рек.
Производственный процесс Камни или камни из карьера подвергаются дроблению и серии циклов дробления, чтобы уменьшить размер частиц до размера природного песка.
Затем полученный песок просеивается и промывается для удаления мелких частиц и примесей, а затем проверяется на различные аспекты качества, прежде чем он будет признан пригодным в качестве строительного заполнителя. Спецификация размера искусственного песка такова, что он должен полностью проходить через сито 3/8 дюйма.
Почему промышленный песок?Существуют различные факторы, которые в настоящее время определяют производство искусственного песка:
- Глобальный дефицит природного песка : Неоправданная добыча песка и постоянное истощение природных источников заполнителя привели к введению в действие нового законодательства об охране окружающей среды / землепользования, которое сделало добычу природного песка трудной и дорогой. Дноуглубительные работы в песках облагаются высокими налогами / запрещены во многих частях мира.
- Растущий спрос на мелкие заполнители в строительстве: Примерно 65-80% объема бетонных и стяжных смесей составляет песок / заполнители.
Только рынку Великобритании требуется около 200 миллионов тонн заполнителей ежегодно для различных строительных целей.
- Удаленное расположение песчаных карьеров : Лицензированные песчаные карьеры, производящие песок требуемого качества, часто расположены в удаленных местах, что приводит к высоким затратам на транспортировку.
- Присутствие ила и глины в природном песке: Природный песок изначально богат илом и глиной. Это может повредить стяжку и бетон, если песок недостаточно обработан для снижения содержания глины и других примесей до приемлемого уровня.
- Снижение потерь малоценных побочных продуктов в карьерах: Низкокачественные агрегаты, образующиеся как побочный продукт дробления горных пород, можно эффективно использовать для создания высокоценного продукта.
- Более рентабельно, чем природный песок : Промышленный песок может производиться в районах, близких к строительным площадкам, что снижает стоимость транспортировки и обеспечивает гарантию стабильных поставок.
- Соответствует новым европейским стандартам: Технический песок может использоваться в качестве заполнителя в стяжках и бетонных смесях согласно EN13139. Его можно использовать как замену или как смесь с натуральным песком.
- Менее разрушительно для окружающей среды : Земля, используемая для добычи камня, может быть восстановлена для коммерческих / жилых целей или использована для восстановления водно-болотных угодий. Это может помочь уменьшить добычу песка из русел рек.
- Меньшие примеси и хорошие рабочие свойства: Промышленный песок не содержит частиц ила и глины и имеет более плотную упаковку частиц, чем природный песок. Он также предлагает более высокую прочность на изгиб, лучшую стойкость к истиранию, более высокий удельный вес и более низкую проницаемость.
Проблемы технологичности: Промышленный песок может иметь более крупную и угловатую текстуру, чем природный песок, который является гладким и округлым из-за естественной градации. Это может привести к увеличению потребности в воде и цементе для достижения ожидаемой удобоукладываемости, что приведет к увеличению затрат.
Большая доля микрочастиц: Промышленный песок может содержать большее количество микрочастиц, чем природный песок, благодаря процессу его производства.Это опять же может повлиять на прочность и удобоукладываемость стяжки или бетона.
Решение:Для тонкого измельчения и сепарации требуются специальные знания и технологии. Чтобы убедиться, что произведенный песок пригоден для использования по назначению, конечный продукт должен пройти ряд тестов качества, таких как:
- Ситовый анализ
- Оптический микроскоп для проверки формы частиц
- Технологичность
- Куб испытание на прочность на сжатие
- Тест на фальсификацию
Промышленный песок может быть более экономичной и более экологичной альтернативой натуральному песку. Но главное — обеспечить, чтобы песок был получен из надежного источника, и что он был надлежащим образом обработан и протестирован на соответствие требуемым спецификациям качества.
Исследование использования искусственного песка в качестве 100% замены мелкозернистого заполнителя в бетоне
Реферат
Промышленный песок отличается от природного морского и речного песка, вынутого драгой, по своим физическим и минералогическим свойствам. Они могут быть как полезными, так и вредными для свежих и затвердевших свойств бетона. В данной статье представлены результаты лабораторного исследования, в котором промышленный песок, произведенный на дробильной установке промышленного размера, был охарактеризован в отношении его физических и минералогических свойств.Влияние этих характеристик на удобоукладываемость и прочность бетона, когда искусственный песок полностью заменяет природный песок в бетоне, было исследовано и смоделировано с помощью искусственных нейронных сетей (ИНС). Результаты показывают, что изготовленный песчаный бетон, изготовленный в этом исследовании, обычно требует более высокого отношения вода / цемент (в / ц) для удобоукладываемости, равного таковому у природного песчаного бетона, из-за более высокой угловатости полученных частиц песка. Чтобы компенсировать это, можно использовать добавки, уменьшающие количество воды, если производимый песок не содержит частиц глины.При том же соотношении воды и металла прочность на сжатие и изгиб производимого песчаного бетона превышает прочность природного песчаного бетона.
ИНС оказался ценным и надежным методом прогнозирования прочности и удобоукладываемости бетона на основе свойств мелкозернистого заполнителя (ТВС) и состава бетонной смеси.
Ключевые слова: промышленный песок, бетон, искусственные нейронные сети
1. Введение
Во многих странах источники природного песка для использования в качестве заполнителя в строительстве становятся дефицитными, поскольку песчаные карьеры истощены, а законодательство по охране окружающей среды препятствует проведению дноуглубительных работ [1 , 2,3].Это вызывает потребность в источниках альтернативных заполнителей, например, из отходов строительства и сноса. Одним из возможных источников строительного заполнителя является песок, который был произведен из избыточного материала (дробильная пыль), образующегося при добыче крупного заполнителя в карьерах твердых пород. При производстве крупного заполнителя обычно получается от 25% до 45% дробильной пыли в зависимости от материнской породы, дробильного оборудования и условий дробления [2]. В карьерах Великобритании имеются значительные запасы дробильной пыли, которую можно подвергнуть дальнейшей переработке, чтобы обеспечить большую часть песка, необходимого для строительной отрасли, используя те же каналы продаж и доставки, что и сейчас для грубых заполнителей.Преимущество этого заключается в возможности указывать заполнители из карьеров, близких к месту их конечного использования, тем самым сокращая расстояния транспортировки и минимизируя загрязнение. Однако, по сравнению с природной пылью для дробления песка, пыль, как правило, имеет худшую форму и текстурные свойства, а также плохую сортировку и незнакомый минералогический состав, что влияет на свойства свежего и затвердевшего бетона.
Форма и текстура дробильной пыли в основном зависят от (i) типа дробилки [3,4]; (ii) отношение размера материала, подаваемого в дробилку, к размеру готового продукта (коэффициент измельчения) и (iii) исходной породы.Ударные дробилки разрушают породу, «ударяя» по материалу, что вызывает разрушение породы по естественным зонам ослабления вдоль границ раздела зерен [5], в результате чего образуются частицы хорошей кубической формы. Щековые и большие вращательные дробилки обычно производят частицы плохой (некубической) формы из-за того, что камера дробления редко бывает заполнена, чтобы обеспечить дробление между частицами [5]. Роторные дробилки широко используются для дробления различных пород от мягких до твердых, таких как базальт, гранит, твердый известняк. Условия нагружения ударных дробилок обычно приводят к более высокой вероятности разрушения слабых или хлопьевидных частиц, причем разрушение происходит в результате раскола, с заметным вкладом из-за истирания поверхности.В результате с помощью этого процесса дробления производится больше мелкозернистых заполнителей равных размеров по сравнению с другими методами, такими как конусная, щековая и валковая дробилки. Было показано, что чем более угловатая форма мелкого заполнителя, тем больше потребность в воде в бетоне и растворах, и поэтому использование ударных дробилок сводит к минимуму этот неблагоприятный эффект [6]. Тем не менее, исследователи также обнаружили, что прочность бетона на изгиб и сжатие выигрывает от угловатости измельченного мелкозернистого заполнителя из-за улучшенного сцепления и сцепления заполнителя по сравнению с натуральными песчаными бетоном и растворами при том же соотношении вода / цемент [6,7].
Типичный гранулометрический состав дробильной пыли редко соответствует требованиям национальных стандартов. В основном это происходит из-за избытка (> 20%) мелких частиц, проходящих через сито 63 мкм, и недостатка частиц размером от 0,3 мм до 1 мм. Пыль от дробилки может образовывать «жесткие» смеси с проблемами просачивания, если ее промывают и просеивают до установленных пределов. Поэтому, чтобы минимизировать пустоты и снизить водопотребность в бетоне, дробильная пыль смешивается с мелким природным песком, чтобы улучшить удобоукладываемость и отделочную обработку [8].Частицы, проходящие через сито 63 мкм, называемые в этой статье мелкими частицами, могут сильно повлиять на свежие свойства бетона, поскольку они увеличивают удельную поверхность мелкозернистого заполнителя, что требует увеличения дозировки воды / добавки для обеспечения постоянной удобоукладываемости [ 7]. Если материнская порода не содержит глины, можно производить приемлемые бетоны с содержанием мелких фракций от 15% до 20% [1,9]. И наоборот, присутствие глины в материнской породе и, следовательно, мелочи может иметь пагубное влияние не только на потребность в воде / добавках, но также на характеристики затвердевшего бетона [10,11].Таким образом, важно определить эффективный и быстрый метод проверки мелких частиц на потенциально вредные частицы и установить соответствующие ограничения для их использования в бетоне.
Во многих исследованиях изучали влияние частичной замены мелкозернистого заполнителя в бетоне с использованием дробильной пыли или небольших образцов измельченного песка на свойства бетона [8,12,13]. Однако по полной замене естественного мелкого заполнителя в бетоне дробильной пылью было выполнено мало работы.В ответ на это в данном исследовании был изучен ряд песков, производимых дробильной установкой KEMCO V7 промышленного размера, которая перерабатывает пыль от дробилок в модифицированной ударной дробилке и классифицирует размер частиц с помощью воздушного экрана, как более подробно описано в [ 14]. В результате этого процесса получается песчаный продукт с хорошей сортировкой и формой с наполнителем, в основном содержащим мелкие частицы. Установку можно рассматривать как дополнительную стадию дробления в карьере, которую можно использовать для переработки излишков дробильной пыли, тем самым увеличивая общий выход из карьера.
Поскольку промышленные пески обладают свойствами, отличными от природных, было бы полезно иметь возможность прогнозировать свойства получаемого бетона без обширных лабораторных испытаний. Были предприняты многочисленные попытки смоделировать влияние физических и химических характеристик заполнителей на свежие и затвердевшие свойства бетона и предоставить процедуры проектирования бетонной смеси [15,16]. Они в некоторой степени учитывают ряд характеристик заполнителя: гранулометрический состав, максимальный размер заполнителя и тип заполнителя (натуральный или дробленый).Однако, поскольку эти процедуры основаны на статистических данных для многих бетонных смесей, результаты являются обобщенными и в случае конкретного типа заполнителя, такого как дробильная пыль или промышленные заполнители, могут не дать ожидаемых конечных свойств бетона. Кроме того, оценки прочности бетона на сжатие основаны на соотношении вода / цемент, которое для типичных заполнителей может быть правильным, но для очень угловатых или очень мелких заполнителей может оказаться неточным представлением прочности.Подобные эффекты могут быть обнаружены при измерениях согласованности.
Было разработано и исследовано несколько моделей, которые оценивают упаковку частиц в агрегатных смесях [17,18,19,20]. Был сделан вывод, что они являются полезными инструментами для моделирования смесей заполнителей с минимальным содержанием пустот. Однако наиболее распространенные допущения в моделях насадки заключаются в том, что частицы имеют сферическую форму, и поэтому комбинации заполнителя и цемента с минимальным содержанием пустот не обязательно приводят к ожидаемым свойствам бетонной смеси.Модель сжимаемой насадки [21] показала себя относительно точной с различными заполнителями, включая измельченный известняковый песок с высоким содержанием наполнителя, однако она имеет тенденцию переоценивать консистенцию [22], и нет никаких ссылок на влияние глины. частиц на свойства свежего и затвердевшего бетона.
Ряд исследователей обратились к моделям ИНС для прогнозирования свойств бетона с использованием параметров состава смеси для различных типов бетона [23,24,25,26].Однако они все еще не полностью учитывают свойства агрегатов. Разработка модели ИНС, которая учитывает как совокупные свойства, так и состав смеси, может быть полезным инструментом для оценки ожидаемых характеристик свежего и затвердевшего бетона, изготовленного из промышленных заполнителей.
Основная цель данной статьи — представить метод, с помощью которого можно охарактеризовать пески, полученные из дробильной пыли, в соответствии с их физическими и минералогическими свойствами и впоследствии использовать в качестве 100% замены природного песка в бетоне.Структура статьи следующая:
В Разделе 2 представлены экспериментальные детали, связанные с использованием ряда искусственных песков с различным содержанием мелочи в качестве полной замены природного песка в бетоне.
В нем также представлен выбор и обоснование тестов для определения характеристик мелкого заполнителя, использованных в данном исследовании.
Раздел 3 представляет результаты испытаний свежего и затвердевшего бетона в сочетании с результатами определения характеристик мелкозернистого заполнителя и использует их для оценки свойств, которые делают промышленный песок пригодным для применения в бетоне.
В Разделе 4 описывается разработка, обучение и оценка модели ИНС с использованием данных, представленных в Разделе 3, и следующей серии проверочных бетонных смесей. Модель ИНС используется для прогнозирования прочности на сжатие и удобоукладываемости бетона с использованием свойств мелкозернистого заполнителя в качестве одной из основных входных переменных модели.
2. Материалы и методы
2.1. Материалы
В этом исследовании использовался цемент CEM I 52,5N (CEMEX, Rugby, UK), соответствующий стандарту BS EN 197-1: 2011 с указанным химическим составом, вместе с измельченным известняком с крупными заполнителями 4/20 мм (CA) ( CEMEX, Кардифф, Великобритания).Гранулометрический состав последнего сообщается позже в разделе 3.1. При необходимости добавлялась добавка для снижения уровня воды WRDA 90 (Grace Construction Products, Уоррингтон, Великобритания), соответствующая британскому стандарту BS EN 934-2: 2001.
Таблица 1
Оксид | Состав оксида (мас.%) | ||||||||||||||||||||||||||||||||||||||||||||||||||||||||||||||||||||||||||||||||||||||||||||||||||||||||||||||||||||||||||||||||||||||||||||||||||||||||||||||||||||||||||||||||||||||||||||||||||||||||||||||||||||||||||||||||||||||||||||||||||||||||||||||||||||||||||||||||||||||||||||||||||||||||||||||||||||||||||||||||||||||||||||||||||||||||||||||||||||||||||||||||||||||||||||||||||||||||||||||||||||||||||||||||||||||||||||||||||||||||||||||||||||||||||||||||||||||||||||||||||||||||||||||||||||||||||||||||||||||||||||||||||||||||||||||||||||||||||||||||||||||||||||||||||||||||||||||||||||||||||||||||||||||||||||||||||||||||||||||||||||||||||||||||||||||||||||||||||||||||||||||||||||||||||||||||||||||
---|---|---|---|---|---|---|---|---|---|---|---|---|---|---|---|---|---|---|---|---|---|---|---|---|---|---|---|---|---|---|---|---|---|---|---|---|---|---|---|---|---|---|---|---|---|---|---|---|---|---|---|---|---|---|---|---|---|---|---|---|---|---|---|---|---|---|---|---|---|---|---|---|---|---|---|---|---|---|---|---|---|---|---|---|---|---|---|---|---|---|---|---|---|---|---|---|---|---|---|---|---|---|---|---|---|---|---|---|---|---|---|---|---|---|---|---|---|---|---|---|---|---|---|---|---|---|---|---|---|---|---|---|---|---|---|---|---|---|---|---|---|---|---|---|---|---|---|---|---|---|---|---|---|---|---|---|---|---|---|---|---|---|---|---|---|---|---|---|---|---|---|---|---|---|---|---|---|---|---|---|---|---|---|---|---|---|---|---|---|---|---|---|---|---|---|---|---|---|---|---|---|---|---|---|---|---|---|---|---|---|---|---|---|---|---|---|---|---|---|---|---|---|---|---|---|---|---|---|---|---|---|---|---|---|---|---|---|---|---|---|---|---|---|---|---|---|---|---|---|---|---|---|---|---|---|---|---|---|---|---|---|---|---|---|---|---|---|---|---|---|---|---|---|---|---|---|---|---|---|---|---|---|---|---|---|---|---|---|---|---|---|---|---|---|---|---|---|---|---|---|---|---|---|---|---|---|---|---|---|---|---|---|---|---|---|---|---|---|---|---|---|---|---|---|---|---|---|---|---|---|---|---|---|---|---|---|---|---|---|---|---|---|---|---|---|---|---|---|---|---|---|---|---|---|---|---|---|---|---|---|---|---|---|---|---|---|---|---|---|---|---|---|---|---|---|---|---|---|---|---|---|---|---|---|---|---|---|---|---|---|---|---|---|---|---|---|---|---|---|---|---|---|---|---|---|---|---|---|---|---|---|---|---|---|---|---|---|---|---|---|---|---|---|---|---|---|---|---|---|---|---|---|---|---|---|---|---|---|---|---|---|---|---|---|---|---|---|---|---|---|---|---|---|---|---|---|---|---|---|---|---|---|---|---|---|---|---|---|---|---|---|---|---|---|---|---|---|---|---|---|---|---|---|---|---|---|---|---|---|---|---|---|---|---|---|---|---|---|---|---|---|---|---|---|---|---|---|---|---|---|---|---|---|---|---|---|---|---|---|---|---|---|---|---|---|---|---|---|---|---|---|---|---|---|---|---|---|---|---|---|---|---|---|---|---|---|---|---|---|---|---|---|---|---|---|---|---|---|---|---|---|---|---|---|---|---|---|---|---|---|---|---|---|---|---|---|---|---|---|---|---|---|---|---|---|---|---|---|---|---|---|---|---|---|---|---|---|---|---|---|---|---|---|---|---|---|---|---|---|---|---|---|---|---|---|---|---|---|---|---|---|---|---|---|---|---|---|---|---|---|---|---|---|---|---|---|---|---|---|---|---|---|---|---|---|---|---|---|---|---|---|---|---|---|---|---|---|---|---|---|---|---|---|---|---|---|---|---|---|---|---|---|---|---|---|---|---|---|---|---|---|---|---|---|---|---|---|---|---|---|---|---|---|---|---|---|---|---|---|---|---|---|---|---|---|---|---|---|---|---|---|
SiO 2 | 19,7 | ||||||||||||||||||||||||||||||||||||||||||||||||||||||||||||||||||||||||||||||||||||||||||||||||||||||||||||||||||||||||||||||||||||||||||||||||||||||||||||||||||||||||||||||||||||||||||||||||||||||||||||||||||||||||||||||||||||||||||||||||||||||||||||||||||||||||||||||||||||||||||||||||||||||||||||||||||||||||||||||||||||||||||||||||||||||||||||||||||||||||||||||||||||||||||||||||||||||||||||||||||||||||||||||||||||||||||||||||||||||||||||||||||||||||||||||||||||||||||||||||||||||||||||||||||||||||||||||||||||||||||||||||||||||||||||||||||||||||||||||||||||||||||||||||||||||||||||||||||||||||||||||||||||||||||||||||||||||||||||||||||||||||||||||||||||||||||||||||||||||||||||||||||||||||||||||||||||||
Al 2 8 | |||||||||||||||||||||||||||||||||||||||||||||||||||||||||||||||||||||||||||||||||||||||||||||||||||||||||||||||||||||||||||||||||||||||||||||||||||||||||||||||||||||||||||||||||||||||||||||||||||||||||||||||||||||||||||||||||||||||||||||||||||||||||||||||||||||||||||||||||||||||||||||||||||||||||||||||||||||||||||||||||||||||||||||||||||||||||||||||||||||||||||||||||||||||||||||||||||||||||||||||||||||||||||||||||||||||||||||||||||||||||||||||||||||||||||||||||||||||||||||||||||||||||||||||||||||||||||||||||||||||||||||||||||||||||||||||||||||||||||||||||||||||||||||||||||||||||||||||||||||||||||||||||||||||||||||||||||||||||||||||||||||||||||||||||||||||||||||||||||||||||||||||||||||||||||||||||||||||
Fe 2 O 3 | 3,1 | ||||||||||||||||||||||||||||||||||||||||||||||||||||||||||||||||||||||||||||||||||||||||||||||||||||||||||||||||||||||||||||||||||||||||||||||||||||||||||||||||||||||||||||||||||||||||||||||||||||||||||||||||||||||||||||||||||||||||||||||||||||||||||||||||||||||||||||||||||||||||||||||||||||||||||||||||||||||||||||||||||||||||||||||||||||||||||||||||||||||||||||||||||||||||||||||||||||||||||||||||||||||||||||||||||||||||||||||||||||||||||||||||||||||||||||||||||||||||||||||||||||||||||||||||||||||||||||||||||||||||||||||||||||||||||||||||||||||||||||||||||||||||||||||||||||||||||||||||||||||||||||||||||||||||||||||||||||||||||||||||||||||||||||||||||||||||||||||||||||||||||||||||||||||||||||||||||||||
CaO | 63,6 | ||||||||||||||||||||||||||||||||||||||||||||||||||||||||||||||||||||||||||||||||||||||||||||||||||||||||||||||||||||||||||||||||||||||||||||||||||||||||||||||||||||||||||||||||||||||||||||||||||||||||||||||||||||||||||||||||||||||||||||||||||||||||||||||||||||||||||||||||||||||||||||||||||||||||||||||||||||||||||||||||||||||||||||||||||||||||||||||||||||||||||||||||||||||||||||||||||||||||||||||||||||||||||||||||||||||||||||||||||||||||||||||||||||||||||||||||||||||||||||||||||||||||||||||||||||||||||||||||||||||||||||||||||||||||||||||||||||||||||||||||||||||||||||||||||||||||||||||||||||||||||||||||||||||||||||||||||||||||||||||||||||||||||||||||||||||||||||||||||||||||||||||||||||||||||||||||||||||
MgO | 1,2 | ||||||||||||||||||||||||||||||||||||||||||||||||||||||||||||||||||||||||||||||||||||||||||||||||||||||||||||||||||||||||||||||||||||||||||||||||||||||||||||||||||||||||||||||||||||||||||||||||||||||||||||||||||||||||||||||||||||||||||||||||||||||||||||||||||||||||||||||||||||||||||||||||||||||||||||||||||||||||||||||||||||||||||||||||||||||||||||||||||||||||||||||||||||||||||||||||||||||||||||||||||||||||||||||||||||||||||||||||||||||||||||||||||||||||||||||||||||||||||||||||||||||||||||||||||||||||||||||||||||||||||||||||||||||||||||||||||||||||||||||||||||||||||||||||||||||||||||||||||||||||||||||||||||||||||||||||||||||||||||||||||||||||||||||||||||||||||||||||||||||||||||||||||||||||||||||||||||||
SO 3,6 | 0,1 | ||||||||||||||||||||||||||||||||||||||||||||||||||||||||||||||||||||||||||||||||||||||||||||||||||||||||||||||||||||||||||||||||||||||||||||||||||||||||||||||||||||||||||||||||||||||||||||||||||||||||||||||||||||||||||||||||||||||||||||||||||||||||||||||||||||||||||||||||||||||||||||||||||||||||||||||||||||||||||||||||||||||||||||||||||||||||||||||||||||||||||||||||||||||||||||||||||||||||||||||||||||||||||||||||||||||||||||||||||||||||||||||||||||||||||||||||||||||||||||||||||||||||||||||||||||||||||||||||||||||||||||||||||||||||||||||||||||||||||||||||||||||||||||||||||||||||||||||||||||||||||||||||||||||||||||||||||||||||||||||||||||||||||||||||||||||||||||||||||||||||||||||||||||||||||||||||||||||
Свободный CaO | 2,3 | ||||||||||||||||||||||||||||||||||||||||||||||||||||||||||||||||||||||||||||||||||||||||||||||||||||||||||||||||||||||||||||||||||||||||||||||||||||||||||||||||||||||||||||||||||||||||||||||||||||||||||||||||||||||||||||||||||||||||||||||||||||||||||||||||||||||||||||||||||||||||||||||||||||||||||||||||||||||||||||||||||||||||||||||||||||||||||||||||||||||||||||||||||||||||||||||||||||||||||||||||||||||||||||||||||||||||||||||||||||||||||||||||||||||||||||||||||||||||||||||||||||||||||||||||||||||||||||||||||||||||||||||||||||||||||||||||||||||||||||||||||||||||||||||||||||||||||||||||||||||||||||||||||||||||||||||||||||||||||||||||||||||||||||||||||||||||||||||||||||||||||||||||||||||||||||||||||||||
Na 2 Oeq 1 | 0,7 | ||||||||||||||||||||||||||||||||||||||||||||||||||||||||||||||||||||||||||||||||||||||||||||||||||||||||||||||||||||||||||||||||||||||||||||||||||||||||||||||||||||||||||||||||||||||||||||||||||||||||||||||||||||||||||||||||||||||||||||||||||||||||||||||||||||||||||||||||||||||||||||||||||||||||||||||||||||||||||||||||||||||||||||||||||||||||||||||||||||||||||||||||||||||||||||||||||||||||||||||||||||||||||||||||||||||||||||||||||||||||||||||||||||||||||||||||||||||||||||||||||||||||||||||||||||||||||||||||||||||||||||||||||||||||||||||||||||||||||||||||||||||||||||||||||||||||||||||||||||||||||||||||||||||||||||||||||||||||||||||||||||||||||||||||||||||||||||||||||||||||||||||||||||||||||||||||||||||
LOI 2 | гранит 2 | , базальтовая и песчано-дробильная пыль перерабатывалась на заводе V7.Дробильная установка V7 может производить песок различной градации. Было произведено и испытано не менее четырех градаций произведенного песка из каждой дробильной пыли. Также для сравнения были включены фракции пыли дробилки (необработанные) 0/4 мм. В качестве контрольного мелкого заполнителя использовался морской песок, извлеченный из дноуглубительных работ, соответствующий стандарту BS EN 12620: 2002. показаны обозначения, используемые в этой статье для всех мелких агрегатов.Таблица 2
2.2. Тесты мелкого заполнителяКак обсуждалось ранее, классификация мелкого заполнителя является важным фактором, влияющим на характеристики бетона, поэтому все мелкие заполнители были протестированы на гранулометрический состав в соответствии с BS EN 933-1: 1997.Форму и текстуру песка сложно измерить напрямую, поэтому в национальных стандартах Великобритании используются преимущественно качественные тесты для определения характеристик. Однако испытание конуса потока в Новой Зеландии (NZFC) (NZS 3111: 1986), использованное в исследовании, предлагает косвенное измерение формы и текстуры путем измерения (i) времени истечения мелкозернистого заполнителя через воронку известной геометрии и (ii) ) содержание неплотных пустот в мелких заполнителях после их сбора в приемной камере.На поток материала в основном влияют форма и текстура поверхности частиц, а содержание пустот определяется классом и формой частиц [1]. Стандартный пакет технических условий, описанный в NZS 3121: 1986 для содержания пустот по сравнению с временем истечения , был разработан для определения характеристик различных природных песков в бетоне. Конверт основан на опыте властей Новой Зеландии и включен в этот документ для сравнения с промышленным песком. Также, как подчеркивалось во введении, присутствие вредных частиц, таких как глины, может иметь пагубное влияние на водопотребность свежего бетона и характеристики бетона в его затвердевшем состоянии. Поэтому требовался быстрый и эффективный метод просеивания песков. Были использованы два теста на значение метиленового синего (МБ); Британский стандартный тест (BS EN 933-9: 1999 для фракции 0/2 мм), включающий титрование раствором МБ, и тест, разработанный Grace Construction Products (ASTM WK36804) с использованием предварительно откалиброванного колориметра, позволяющий напрямую определять МБ расход раствора.В данном документе эти тесты будут называться показателем метиленового синего (MBV) и градационным показателем метиленового синего (GMBV) соответственно. Также был использован тест эквивалента песка (SE) (BS EN 933-8: 1999 для фракции 0/2 мм), который оценивает долю очень мелких частиц и частиц размером с глину во всем образце. Промышленные и дробленые пески обычно имеют более низкие значения SE, чем чистые природные пески из-за пыли трещин, образующихся в процессе дробления. Плотность частиц и водопоглощение, которые являются функциями минералогического состава заполнителя, были определены в соответствии с BS EN 1097-6: 2000.Измерение плотности в сухом состоянии использовалось при расчете пустот NZFC, а абсорбционная способность использовалась для корректировки содержания воды в различных бетонных смесях. 2.3. Бетонные испытания, отверждение и детали образцаОсновными характеристиками бетонной смеси являются ее удобоукладываемость и прочность. Поэтому свежий бетон был испытан на оседание в соответствии с BS EN 12350-2: 2009. Кроме того, были сделаны наблюдения во время смешивания, укладки и отделки образцов бетона, так как одно только испытание на осадку не полностью характеризует удобоукладываемость бетонных смесей, содержащих искусственные пески [8]. Затвердевший бетон был испытан на прочность на сжатие ( f ‘ c ) через 1, 7 и 28 дней согласно BS EN 12390-3: 2009 и прочность на изгиб ( f t ) через 28 дней согласно BS EN 12390-5: 2009. Для испытаний прочности на сжатие и изгиб использовались стандартные лабораторные формы. Они имели размеры 100 × 100 × 100 мм 3 и 500 × 100 × 100 мм 3 соответственно, что соответствовало требованиям BS EN 12390-1: 2012 к размеру формы в отношении максимального размера заполнителя.Признано, что использование этих размеров образцов для бетона, изготовленного из 20-миллиметрового крупного заполнителя, могло привести к немного большей вариабельности и незначительно более низкой прочности, чем было бы получено с более крупными образцами (например, 150 × 150 × 150 мм ). Это происходит из-за повышенной относительной неоднородности и «так называемого» эффекта стенки, который возникает, когда отношение максимального размера заполнителя к размеру образца превышает определенный предел (приблизительно 0,2) [27]. Тем не менее, между несколькими образцами, испытанными для каждой смеси, была получена хорошая согласованность, что дает уверенность в значениях, полученных в качестве меры относительной прочности для различных рассматриваемых смесей.Из каждой бетонной смеси было отлито девять 100 × 100 × 100 мм 3 куба и три 500 × 100 × 100 мм 3 балки. Через 16 часов они были извлечены из формы и помещены в резервуар для воды при температуре 20 ± 3 ° C до достижения возраста испытаний. 2.4. Состав бетонной смесиИсследование проводилось в два этапа. На первом этапе рассматривались смеси с контролируемой осадкой без добавления добавок, снижающих водоотдачу. Контрольная смесь с природным песком была приготовлена с заданной оседкой S2 (50–90 мм), как указано в BS EN 206-1: 2000.Для искусственных песков пески с обозначением -B были смешаны для достижения той же осадки S2, что и контрольный образец, и было записано необходимое соотношение вода / цемент. Это соотношение в / ц сохранялось постоянным для оставшейся градации того же карьерного песка, регистрируя изменение осадки, наблюдаемое в каждой бетонной смеси. Вторая фаза исследования включала смеси, приготовленные с постоянным соотношением вода / ц (вес / ц = 0,55) и добавление достаточного объема добавки, снижающей воду, для достижения осадки S2.Добавляли уменьшающую воду добавку с приращениями примерно по 6 мл, и испытания на оседание повторяли до тех пор, пока не было зарегистрировано оседание S2. Смеси известняка и песка достигли осадки S2 при водном соотношении 0,55 без примесей, поэтому они были смешаны при более низком водном соотношении, равном 0,50. Чтобы сравнить свойства свежего и затвердевшего бетона между смесями, замену мелкозернистого заполнителя в каждой смеси производили по весу. Это обеспечило постоянство соотношений CA / FA и FA / цемент.Кроме того, содержание увлеченного воздуха в смесях было проверено в соответствии с методом манометра в BS EN 12350-7: 2009. Состав смеси показан на. Во всех бетонных смесях масса воды и заполнителя была отрегулирована в соответствии с абсорбционной способностью и содержанием воды в мелком и крупном заполнителе, чтобы поддерживать постоянное массовое соотношение воды и заполнителя для каждого произведенного песка. Таблица 3Состав бетонной смеси.
3. Результаты и обсуждение3.1. Результаты определения характеристик мелкого заполнителяa – d показывает гранулометрический состав произведенных песков и соответствующей необработанной дробильной пыли, причем гранулометрические составы крупных и контрольных мелких заполнителей приведены в. Очевидно, что градация, полученная для фракций размером более 63 мкм для промышленных песков, очень похожа, независимо от минералогии породы, и это ключевая особенность перерабатывающей установки KEMCO V7.Предполагается, что мелочь различных минералогических песков похожа по форме и гранулометрическому составу из-за использования одного и того же производственного процесса для всех песков. Гранулометрический состав промышленного песка для базальтового песка ( a ); ( b ) Песок песчаниковый; ( c ) Песок гранитный; ( d ) Песок известняковый. Гранулометрический состав крупнозернистого заполнителя и природного песка. Содержание мелких частиц в промышленном песке варьировалось от 1% до 9%. По сравнению с необработанными материалами дробильной пыли, большинство производимых песков имели большее количество 0.Частицы размером от 3 до 1 мм, на что указывают более крутые градиенты градуированных кривых в этой области. Улучшение гранулометрического состава в этом диапазоне не было столь выраженным в известняковых песках, как в других промышленных песках. Как отмечалось ранее, этот диапазон размеров частиц часто недостаточен в песчаных щебнях [1], поэтому необходимо, чтобы они были смешаны с мелким природным песком, чтобы сделать их пригодными для использования в бетонных приложениях. Это предполагает, что, что касается гранулометрического состава, эти промышленные пески должны оказаться подходящей заменой мелкозернистым заполнителям в бетоне без необходимости смешивания с природным песком. Все промышленные пески, использованные в этом исследовании, подпадают под стандарт Новой Зеландии для природных песков, в отличие от их аналогов дробильной пыли, как показано в. Это говорит о том, что класс и форма производимых песков должны подходить для использования в бетонных приложениях. Результаты по конусу потока в Новой Зеландии. Как показано на рисунке, частицы природного песка были гладкими и округлыми, в то время как необработанная пыль дробилки состояла из плоских и удлиненных частиц, имеющих угловую форму с острыми краями.Изготовленный песок снова имел угловатую форму, но более равномерный и округлый, чем необработанная дробильная пыль. Представленные изображения типичны для всех фракций и типов дробильных порошков и технологических песков, использованных в исследовании. Результаты NZFC подтверждают, что чем более гладкий и округлый песок, тем меньше время растекания. Изображения фракций песка 4–2 мм ( a ) G-FEED ( b ) G-A ( c ) NS. Если предположить, что определяющим фактором для измерения времени истечения является форма и текстура поверхности мелкозернистого заполнителя, то есть свидетельства того, что процесс KEMCO V7 улучшает эти характеристики, поскольку время истечения необработанного материала дробильной пыли составляло от 28 до 37 с. с, тогда как для всех обработанных песков он находился в диапазоне от 21 до 27 с.Если рассматривать обработанные пески с определенным минералогическим составом, можно увидеть, что время вытекания несколько сократилось с увеличением содержания мелочи. Это уменьшение обычно составляло от 1 до 3 с для оценок -D. Следовательно, можно сделать вывод, что основная часть сокращения времени истечения может быть отнесена на счет улучшения формы частиц в результате обработки. Содержание неплотных пустот во всех базальтовых и песчаниковых песках было ниже, чем в исходном материале. Однако содержание пустот во всех гранитных песках и в самом крупнозернистом известняковом песке (L-A) было больше, чем в соответствующей пыли от дробилок.Это может быть связано с совокупным воздействием изменений в градации, а также формы конкретных песков. ИспытанияMBV и SE использовались для определения присутствия потенциально вредных частиц, в частности глин, в исследуемых мелких агрегатах. показывает, что у природных, гранитных и известняковых песков MBV ниже, чем 0,63 г / кг, тогда как у базальтовых и песчанистых песков MBV выше 1,73 г / кг. Это предполагает присутствие глин в базальтовых и песчанистых песках, что может привести к увеличению потребности в воде и добавках при использовании в бетонной смеси [11].Тем не менее, с помощью этапа воздушной классификации в производственном процессе KEMCO V7 можно удалить часть вредной мелочи, о чем свидетельствует снижение MBV для всех песков по сравнению с их необработанными аналогами из дробильной пыли. Для базальтовых и песчанистых песков MBV увеличивается с увеличением содержания мелких частиц в результате большего количества глинистых частиц в мелкодисперсной фракции, тогда как незначительное увеличение MBV, наблюдаемое для гранитных и известняковых песков, связано с небольшим увеличением в удельной поверхности мелкой фракции.Стандартные тесты MBV и GMBV показывают прямую корреляцию, и поскольку последний быстрее, чем стандартный тест MBV, он может быть ценной и надежной альтернативой. Значение метиленового синего и результаты экспресс-теста на глину Grace. показывает, что у природного песка самое высокое значение SE — 92, за ним следуют гранитные и известняковые пески, которые имеют значения SE в диапазоне от 67 до 80, базальтовые пески (от 58 до 73) и песчаниковые пески (от 27 до 31). . Как видно из результатов испытаний MBV, для определенного минералогического состава песка значения SE уменьшались по мере увеличения количества мелких частиц.Однако результаты тестов MBV и SE не показали прямой корреляции, о чем также сообщает Nikolaides et al. [28]. Это может быть связано с тем, что тест SE более чувствителен к доле пыли разрушения, чем тест MBV. Стоимость песка в эквиваленте для мелких заполнителей. Можно сделать вывод, что для материнских пород, содержащих глину, искусственный песок будет также включать определенную долю глины в мелкой фракции, тогда как, если материнская порода чистая, то мелочь представляет собой пыль трещин, образовавшуюся во время обработки. Водопоглощение (WA24) необработанной дробильной пыли было либо выше, либо таким же, как у соответствующих промышленных песков, как показано на. Обработка дробильной пыли могла вызвать разрушение частиц через доступные для воды пустоты. Это, в свою очередь, могло уменьшить количество и объем этих пустот, которые измеряются с помощью теста на водопоглощение [29]. Кроме того, в стандарте BS EN 933-1: 1997 указано, что испытуемые пески необходимо промывать через сито 63 мкм, но покрытия, такие как глины, не могут быть легко удалены промывкой, что приводит к более высоким значениям поглощения для заполнителей с более высоким начальным содержанием мелочи.Это предположение подтверждается самыми высокими значениями водопоглощения, обнаруженными для песков с высоким MBV. Было обнаружено, что плотность в сухом состоянии для необработанной дробильной пыли и соответствующих им обработанных песков была относительно постоянной. Таблица 4Результаты водопоглощения и плотности в сухом состоянии.
3,2. Конкретные результатыПрочность на сжатие смесей с контролируемой осадкой в основном определялась соотношением в / ц, как показано в.Самое низкое соотношение в / ц, равное 0,48, для природного песка обеспечило наивысшую прочность на сжатие в течение 28 дней, за ним следуют известняк, гранит, базальт и песчаник. При том же соотношении в / ц, равном 0,55, прочность на сжатие всех произведенных песчаных смесей превышала прочность на сжатие природных песчаных смесей (), в то же время сравнимая с прочностью на сжатие природных песчаных смесей с контролируемой осадкой. Точно так же прочность на изгиб всех смесей, кроме смеси G-E, превышала прочность на изгиб натурального песка при смешивании с постоянным соотношением в / ц.Прочность на сжатие и изгиб известняковых смесей при соотношении в / ц 0,50 превышала или была равна контрольной смеси природного песка. Результаты смешивания с контролируемой просадкой. Результаты смешивания с контролируемым соотношением вода / цемент и дозировка добавок. Гранит, известняк и природные пески с низкими значениями MB требовали гораздо меньшего количества воды и водной примеси для достижения осадки S2, чем песчаниковые и базальтовые пески с MBV выше 1,73, как видно на рисунках и. Это подтверждает полезность тестов MB для выявления мелких заполнителей, которые могут отрицательно повлиять на свежие свойства бетона из-за присутствия частиц глины. Эти результаты предполагают, что угловатая форма и шероховатая текстура поверхности искусственного песка способствовали прочности смеси на сжатие и изгиб благодаря сцеплению заполнителя и улучшенному сцеплению между цементной матрицей и частицами заполнителя. Аналогичные результаты были получены другими исследователями [5,8]. При водном соотношении 0,55 все изготовленные песчаные смеси за 28 дней достигли прочности на сжатие в диапазоне от 53 до 60,5 Н / мм 2 . Это говорит о том, что конкретные глины, присутствующие в песчаниках и базальтовых песках, не оказывают отрицательного влияния на прочность в течение 28 дней при том же соотношении воды и металла.Однако долгосрочное влияние стоимости МБ и глины на прочность в этом исследовании не исследовалось. Некоторые из базальтовых и песчанистых песков, смешанных при соотношении воды к цементу 0,55, не достигли осадки S2 даже при дозах добавки, превышающих рекомендованные производителем. Это говорит о том, что если требуется пригодная для обработки бетонная смесь с разумным соотношением вода / цемент, то присутствие глины в производимом песке является первым и главным ограничивающим фактором. Однако, если для данного конкретного применения допустимы высокие соотношения вода / цемент, то увеличение соотношения вода / цемент может компенсировать негативное влияние присутствия глины на удобоукладываемость бетона. сообщает о дозировке захваченного воздуха и примесей для обеих фаз. Измерение захваченного воздуха на этапе 1 колеблется от 0,45% до 1,60%. В каждой бетонной смеси она относительно постоянна, за исключением смесей G-B и GS-B. Это может быть связано либо с чрезмерной, либо с недостаточной вибрацией этих бетонных образцов соответственно. На этапе 2 измерение захваченного воздуха находится в диапазоне от 0,80% до 1,80%. Опять же, внутри каждой бетонной смеси измерения относительно постоянны и немного выше по сравнению с результатами фазы 1.Это может быть связано как с захватом воздуха в результате введения пластификатора, так и с пониженной консистенцией, что может привести к большему количеству воздушных пустот в затвердевшем бетоне. Таблица 5Дозировка захваченного воздуха и примесей для смесей фазы 1 и фазы 2.
4.3. Настройка моделиДля обучения нейронных сетей использовался алгоритм обратного распространения. Полное описание алгоритма и ИНС в целом предоставлено Фосеттом [34].показывает типичную структуру, принятую для этих моделей. После обучения ИНС полученные веса связей и «смещения» были перенесены в электронные таблицы. В них уравнение (1) использовалось для вычисления числовых значений нейронов в скрытом слое: yj = F (∑i = 0n (xi · wij) + b) (1) где y j — нейрон в скрытом слое, x i — масштабированное входное значение, w ij — вес соединения, n — количество входов и b — константа, называемая «смещением» или «порогом», которая вычисляется во время обучения сети аналогично весам соединений. F — сигмовидная функция активации, полученная из уравнения (2), которая представляет нелинейное поведение бетона. Выходные значения z k вычисляются с использованием уравнения (1), но путем замены x i на y j и w ij на w jk . Структурная схема искусственной нейронной сети. Нейронные сети были созданы с одним скрытым слоем, как было ранее продемонстрировано для успешного моделирования прочности и удобоукладываемости бетона [32,35,36].Выбор количества нейронов в скрытом слое зависит от сложности задачи и обычно определяется эмпирически. Сети с диапазоном скрытых номеров нейронов были созданы и обучены с использованием обучающих данных. Ошибки прогноза, в данном случае среднеквадратическая ошибка (RMS), данных тестирования были оценены, и была принята модель с наименьшей ошибкой. Для каждого выхода были созданы и обучены четыре нейронные сети с 2, 4, 6 и 8 скрытыми нейронами. В этой статье модели нейронных сетей обозначаются в соответствии с количеством нейронов в каждом слое «входной слой — скрытый слой — выходной слой» и рассматриваемым выходным параметром (сила или спад). Веса для каждого нейрона были рандомизированы перед обучением сети. Начальная скорость обучения составляла 0,7, которая снизилась на 1% после 7 циклов обучения. Кроме того, начальный коэффициент импульса составлял 0,7, который уменьшался на 1% после каждых 500 циклов. Использовался режим онлайн-обучения, в котором веса обновлялись после каждой записи, а данные представлялись в случайном порядке. Обучение каждой сети было остановлено после 5000 циклов. Было замечено, что RMS стабилизировалась для всех сетей примерно после 2000–3000 циклов обучения. 4.4. Оценка моделипоказывает ошибки прогноза RMS моделей для набора данных тестирования. Можно видеть, что наименьшая ошибка для прогнозирования оседания — это модель оседания 8-2-1, тогда как для прогнозирования прочности наименьшая ошибка получается при использовании модели прочности 8-6-1, и поэтому они были приняты как наиболее точные. модели для данного набора данных. Таблица 7Ошибки RMS модели ИНС для набора данных тестирования.
Чтобы проверить возможности прогнозирования четырех моделей бетонные смеси были приготовлены с тем же содержанием FA, CA и цемента, как описано в Разделе 2, но с различными дозировками воды и добавок.Эти смеси включали измельчительную пыль, которая не использовалась при обучении или тестировании моделей, природный песок, гранитный песок без глин и песчано-песчаный песок с частицами глины. Входные значения модели, взятые из смесей валидации, приведены в. Таблица 8Подтверждение входных значений смеси.
Расчетные и фактические значения осадки и прочности на сжатие для проверенных смесей показаны соответственно. Модель осадки 8-2-1 имела среднеквадратичное значение 26,61 мм и самую высокую процентную ошибку 34% для смеси NS. Следует отметить, что в диапазоне спада 50–100 мм, где располагалась большая часть обучающих данных, процентная погрешность не превышает 21%.Кроме того, принимая во внимание искусственные значения 300 мм, принятые для обрушения осадки в данных обучения, можно было ожидать, что будет завышенная оценка осадки в смесях с более высокой удобоукладываемостью. Тем не менее, завышение значения осадки предпочтительнее недооценки, поскольку для достижения желаемой удобоукладываемости смеси могут использоваться другие методы. Можно видеть, что прогнозы прочности на сжатие относительно точны с максимальной процентной ошибкой 13% и среднеквадратичным значением 4.47 Н / мм 2 для модели прочности 8-6-1. Опять же, недооценка (если таковая имеется) прогнозируемой прочности на сжатие предпочтительнее завышенной оценки, особенно в приложениях для проектирования конструкций. Прогнозируемые и фактические значения осадки для проверочных смесей. Прогнозируемые и фактические значения прочности на сжатие для проверочных смесей. Численная оценка модели может помочь подтвердить, что ИНС действительно усвоила лежащую в основе теоретическую взаимосвязь.Параметры мелкого заполнителя следует рассматривать одновременно, поскольку трудно идентифицировать влияние какого-либо одного входного параметра на удобоукладываемость и прочность на сжатие бетона из-за многопараметрического нелинейного характера взаимосвязи между переменными. a, b показывают вариацию прогнозов спада с SE и GMBV, а также значения времени потока и пустот, когда все остальные свойства сохраняются на средних значениях из набора обучающих данных (). Видно, что для жидких смесей с соотношением в / ц 0.6 и 0,7 наблюдается заметное уменьшение осадки по мере увеличения содержания глины. В то время как в жестких смесях (соотношение 0,5 в / ц) это мало влияет на прогнозы оседания. Точно так же для жестких смесей не наблюдается влияния формы и градации на осадку, тогда как для жидких смесей, чем более угловат заполнитель, на что указывает увеличение содержания пустот, тем ниже осадка, аналогично более мелкая градация, на что указывает уменьшение потока. время, тем меньше прогнозируемый спад. Вариация прогнозов осадки с ( a ) изменением SE и GMBV и ( b ) изменением содержания пустот и времени истечения. a, b показывает изменение прочности на сжатие из-за значений SE и GMBV, а также содержания пустот и времени истечения. Можно видеть, что для SE и GMBV, когда отношение w / c составляет 0,7, прогнозы прочности на сжатие относительно постоянны, тогда как для отношения w / c 0,6 и 0,5 существует оптимальный диапазон значений для SE и GMBV, которые приводят к наивысшим значениям. прочность на сжатие. Помня, что соотношение вода / цемент является доминирующим фактором, определяющим прочность бетона, можно увидеть, что для высокого отношения воды / цемента (0.7) форма, текстура или гранулометрический состав заполнителя мало влияют на прочность на сжатие, в отличие от бетонов с высокой прочностью (с низким соотношением масс. [37]. Время растекания в основном определяется гранулометрическим составом и текстурой поверхности мелкого заполнителя. Было показано Li et al. [30], что если классификация такая же, то увеличенное время истечения указывает на более грубую поверхность мелких частиц заполнителя, что увеличивает прочность на сжатие. Вариация прогнозов прочности на сжатие с ( a ) изменением SE и GMBV и ( b ) изменением содержания пустот и времени течения. Можно сделать вывод, что модели ИНС могут использоваться для оценки удобоукладываемости и прочности бетона на сжатие, когда свойства мелкого заполнителя используются наряду с составом смеси в качестве входных параметров модели ИНС. Однако у таких моделей есть ограничения, главное из которых состоит в том, что они хорошо работают только в том диапазоне входных и выходных переменных, с которым они были обучены. Можно также сделать вывод, что модели ИНС, разработанные в этом исследовании, действительны, и прогнозы в целом соответствуют теоретическим соотношениям между составом смеси, параметрами мелкозернистого заполнителя и свойствами бетона.Таким образом, этот тип модели может использоваться для уменьшения усилий, необходимых для разработки рабочих бетонных смесей, или для сравнения характеристик различных мелких заполнителей с помощью простых тестов классификации заполнителей. 5. ВыводыОсновная цель этого исследования состояла в том, чтобы представить метод, с помощью которого можно охарактеризовать пески, полученные из дробильной пыли, в соответствии с их физическими и минералогическими свойствами, и исследовать их использование в бетоне в качестве 100% замены природного песка.Результаты экспериментального исследования, представленные в этой статье, продемонстрировали, что дробильная установка V7 способна производить искусственные пески с аналогичным гранулометрическим составом независимо от минералогии материнской породы. Был предложен ряд испытаний, которые позволили косвенно измерить форму, текстуру поверхности, классификацию и наличие вредной мелочи, которые использовались для характеристики физических свойств природных песков, необработанной пыли от дробилок и промышленных песков. Из этих испытаний было очевидно, что промышленные частицы песка улучшенной формы и качества по сравнению с природным песком и необработанной дробильной пылью были произведены дробильной установкой V7, наряду с уменьшением количества глинистых частиц в мелкодисперсной части по сравнению с исходным материалом. . Подходящие для обработки бетоны были произведены с использованием искусственного песка в качестве единственного мелкого заполнителя при различных соотношениях в / ц. Присутствие глин в промышленных песках может быть ограничивающим фактором при их использовании в бетонных изделиях, где требуется высокая консистенция и относительно низкие отношения в / ц. Тем не менее, адекватный бетон, содержащий искусственный песок в качестве единственного мелкого заполнителя, может быть получен. Действительно, при том же соотношении вода / цемент прочность на сжатие и изгиб изготовленных песчаных бетонов была выше, чем у их аналогов из природного песка.Считается, что это связано с угловатой формой материала, которая положительно влияет на сцепление заполнителя и, следовательно, приводит к улучшенному сцеплению между цементом и частицами заполнителя. Присутствие глины не повлияло на 28-дневную прочность бетона, изготовленного с тем же соотношением воды и цемента с различными минералогическими свойствами искусственного песка. Таким образом, существует возможность использования глинистых заполнителей в бетоне, что ранее не приветствовалось. Оптимальное содержание мелких частиц в 7% наблюдалось для облегчения обработки, укладки и отделки произведенного пескобетона.Однако в исследованном диапазоне содержания мелких частиц от 1% до 9% не наблюдалось значительной тенденции между содержанием мелких частиц и прочностью бетона на сжатие. Таким образом, чтобы максимально повысить эффективность использования материалов, можно использовать сорта искусственного песка с более высоким содержанием мелочи, когда прочность на сжатие является контролируемым свойством. Было показано, что модели ANN могут использоваться для оценки прочности на сжатие и удобоукладываемости бетона на основе свойств мелкого заполнителя и состава смеси с разумной точностью.Такие модели вместе с описанными ранее испытаниями могут использоваться в строительной отрасли, когда на рынок выходят новые источники мелкозернистых заполнителей. Использование моделей устранит необходимость в обширных лабораторных испытаниях для выбора подходящего состава смеси и определения свойств свежего и затвердевшего бетона. Исследование использования искусственного песка в качестве 100% замены мелкозернистого заполнителя в бетонеРефератПромышленный песок отличается от природного морского и речного песка, вынутого драгой, по своим физическим и минералогическим свойствам.Они могут быть как полезными, так и вредными для свежих и затвердевших свойств бетона. В данной статье представлены результаты лабораторного исследования, в котором промышленный песок, произведенный на дробильной установке промышленного размера, был охарактеризован в отношении его физических и минералогических свойств. Влияние этих характеристик на удобоукладываемость и прочность бетона, когда искусственный песок полностью заменяет природный песок в бетоне, было исследовано и смоделировано с помощью искусственных нейронных сетей (ИНС).Результаты показывают, что изготовленный песчаный бетон, изготовленный в этом исследовании, обычно требует более высокого отношения вода / цемент (в / ц) для удобоукладываемости, равного таковому у природного песчаного бетона, из-за более высокой угловатости полученных частиц песка. Чтобы компенсировать это, можно использовать добавки, уменьшающие количество воды, если производимый песок не содержит частиц глины. При том же соотношении воды и металла прочность на сжатие и изгиб производимого песчаного бетона превышает прочность природного песчаного бетона. ИНС оказался ценным и надежным методом прогнозирования прочности и удобоукладываемости бетона на основе свойств мелкозернистого заполнителя (ТВС) и состава бетонной смеси. Ключевые слова: промышленный песок, бетон, искусственные нейронные сети 1. ВведениеВо многих странах источники природного песка для использования в качестве заполнителя в строительстве становятся дефицитными, поскольку песчаные карьеры истощены, а законодательство по охране окружающей среды препятствует проведению дноуглубительных работ [1 , 2,3]. Это вызывает потребность в источниках альтернативных заполнителей, например, из отходов строительства и сноса. Одним из возможных источников строительного заполнителя является песок, который был произведен из избыточного материала (дробильная пыль), образующегося при добыче крупного заполнителя в карьерах твердых пород.При производстве крупного заполнителя обычно получается от 25% до 45% дробильной пыли в зависимости от материнской породы, дробильного оборудования и условий дробления [2]. В карьерах Великобритании имеются значительные запасы дробильной пыли, которую можно подвергнуть дальнейшей переработке, чтобы обеспечить большую часть песка, необходимого для строительной отрасли, используя те же каналы продаж и доставки, что и сейчас для грубых заполнителей. Преимущество этого заключается в возможности указывать заполнители из карьеров, близких к месту их конечного использования, тем самым сокращая расстояния транспортировки и минимизируя загрязнение.Однако, по сравнению с природной пылью для дробления песка, пыль, как правило, имеет худшую форму и текстурные свойства, а также плохую сортировку и незнакомый минералогический состав, что влияет на свойства свежего и затвердевшего бетона. Форма и текстура дробильной пыли в основном зависят от (i) типа дробилки [3,4]; (ii) отношение размера материала, подаваемого в дробилку, к размеру готового продукта (коэффициент измельчения) и (iii) исходной породы. Ударные дробилки разрушают породу, «ударяя» по материалу, что вызывает разрушение породы по естественным зонам ослабления вдоль границ раздела зерен [5], в результате чего образуются частицы хорошей кубической формы.Щековые и большие вращательные дробилки обычно производят частицы плохой (некубической) формы из-за того, что камера дробления редко бывает заполнена, чтобы обеспечить дробление между частицами [5]. Роторные дробилки широко используются для дробления различных пород от мягких до твердых, таких как базальт, гранит, твердый известняк. Условия нагружения ударных дробилок обычно приводят к более высокой вероятности разрушения слабых или хлопьевидных частиц, причем разрушение происходит в результате раскола, с заметным вкладом из-за истирания поверхности.В результате с помощью этого процесса дробления производится больше мелкозернистых заполнителей равных размеров по сравнению с другими методами, такими как конусная, щековая и валковая дробилки. Было показано, что чем более угловатая форма мелкого заполнителя, тем больше потребность в воде в бетоне и растворах, и поэтому использование ударных дробилок сводит к минимуму этот неблагоприятный эффект [6]. Тем не менее, исследователи также обнаружили, что прочность бетона на изгиб и сжатие выигрывает от угловатости измельченного мелкозернистого заполнителя из-за улучшенного сцепления и сцепления заполнителя по сравнению с натуральными песчаными бетоном и растворами при том же соотношении вода / цемент [6,7]. Типичный гранулометрический состав дробильной пыли редко соответствует требованиям национальных стандартов. В основном это происходит из-за избытка (> 20%) мелких частиц, проходящих через сито 63 мкм, и недостатка частиц размером от 0,3 мм до 1 мм. Пыль от дробилки может образовывать «жесткие» смеси с проблемами просачивания, если ее промывают и просеивают до установленных пределов. Поэтому, чтобы минимизировать пустоты и снизить водопотребность в бетоне, дробильная пыль смешивается с мелким природным песком, чтобы улучшить удобоукладываемость и отделочную обработку [8].Частицы, проходящие через сито 63 мкм, называемые в этой статье мелкими частицами, могут сильно повлиять на свежие свойства бетона, поскольку они увеличивают удельную поверхность мелкозернистого заполнителя, что требует увеличения дозировки воды / добавки для обеспечения постоянной удобоукладываемости [ 7]. Если материнская порода не содержит глины, можно производить приемлемые бетоны с содержанием мелких фракций от 15% до 20% [1,9]. И наоборот, присутствие глины в материнской породе и, следовательно, мелочи может иметь пагубное влияние не только на потребность в воде / добавках, но также на характеристики затвердевшего бетона [10,11].Таким образом, важно определить эффективный и быстрый метод проверки мелких частиц на потенциально вредные частицы и установить соответствующие ограничения для их использования в бетоне. Во многих исследованиях изучали влияние частичной замены мелкозернистого заполнителя в бетоне с использованием дробильной пыли или небольших образцов измельченного песка на свойства бетона [8,12,13]. Однако по полной замене естественного мелкого заполнителя в бетоне дробильной пылью было выполнено мало работы.В ответ на это в данном исследовании был изучен ряд песков, производимых дробильной установкой KEMCO V7 промышленного размера, которая перерабатывает пыль от дробилок в модифицированной ударной дробилке и классифицирует размер частиц с помощью воздушного экрана, как более подробно описано в [ 14]. В результате этого процесса получается песчаный продукт с хорошей сортировкой и формой с наполнителем, в основном содержащим мелкие частицы. Установку можно рассматривать как дополнительную стадию дробления в карьере, которую можно использовать для переработки излишков дробильной пыли, тем самым увеличивая общий выход из карьера. Поскольку промышленные пески обладают свойствами, отличными от природных, было бы полезно иметь возможность прогнозировать свойства получаемого бетона без обширных лабораторных испытаний. Были предприняты многочисленные попытки смоделировать влияние физических и химических характеристик заполнителей на свежие и затвердевшие свойства бетона и предоставить процедуры проектирования бетонной смеси [15,16]. Они в некоторой степени учитывают ряд характеристик заполнителя: гранулометрический состав, максимальный размер заполнителя и тип заполнителя (натуральный или дробленый).Однако, поскольку эти процедуры основаны на статистических данных для многих бетонных смесей, результаты являются обобщенными и в случае конкретного типа заполнителя, такого как дробильная пыль или промышленные заполнители, могут не дать ожидаемых конечных свойств бетона. Кроме того, оценки прочности бетона на сжатие основаны на соотношении вода / цемент, которое для типичных заполнителей может быть правильным, но для очень угловатых или очень мелких заполнителей может оказаться неточным представлением прочности.Подобные эффекты могут быть обнаружены при измерениях согласованности. Было разработано и исследовано несколько моделей, которые оценивают упаковку частиц в агрегатных смесях [17,18,19,20]. Был сделан вывод, что они являются полезными инструментами для моделирования смесей заполнителей с минимальным содержанием пустот. Однако наиболее распространенные допущения в моделях насадки заключаются в том, что частицы имеют сферическую форму, и поэтому комбинации заполнителя и цемента с минимальным содержанием пустот не обязательно приводят к ожидаемым свойствам бетонной смеси.Модель сжимаемой насадки [21] показала себя относительно точной с различными заполнителями, включая измельченный известняковый песок с высоким содержанием наполнителя, однако она имеет тенденцию переоценивать консистенцию [22], и нет никаких ссылок на влияние глины. частиц на свойства свежего и затвердевшего бетона. Ряд исследователей обратились к моделям ИНС для прогнозирования свойств бетона с использованием параметров состава смеси для различных типов бетона [23,24,25,26].Однако они все еще не полностью учитывают свойства агрегатов. Разработка модели ИНС, которая учитывает как совокупные свойства, так и состав смеси, может быть полезным инструментом для оценки ожидаемых характеристик свежего и затвердевшего бетона, изготовленного из промышленных заполнителей. Основная цель данной статьи — представить метод, с помощью которого можно охарактеризовать пески, полученные из дробильной пыли, в соответствии с их физическими и минералогическими свойствами и впоследствии использовать в качестве 100% замены природного песка в бетоне.Структура статьи следующая:
2. Материалы и методы2.1. МатериалыВ этом исследовании использовался цемент CEM I 52,5N (CEMEX, Rugby, UK), соответствующий стандарту BS EN 197-1: 2011 с указанным химическим составом, вместе с измельченным известняком с крупными заполнителями 4/20 мм (CA) ( CEMEX, Кардифф, Великобритания).Гранулометрический состав последнего сообщается позже в разделе 3.1. При необходимости добавлялась добавка для снижения уровня воды WRDA 90 (Grace Construction Products, Уоррингтон, Великобритания), соответствующая британскому стандарту BS EN 934-2: 2001. Таблица 1
|