Технология производства газобетонных блоков | Полезная информация о газобетоне завода ДСК Грас
В 60-х годах прошлого века, когда развивалось производство автоклавных бетонов, существовали разные способы их изготовления. Одни из них подразумевали использование цементных, другие — известковых, третьи — смешанных вяжущих составов. В те годы был распространён термин «газосиликатный бетон», который применяется и в наши дни — но уже ошибочно: силикатные ячеистые бетоны ушли в прошлое как класс. Промышленность XXI века не выпускает чистых газосиликатов — сегодня распространены более долговечные бетоны на цементном и смешанном вяжущем составе. Поэтому те, кто в наши дни говорят «газосиликат», в большинстве случаев имеют в виду автоклавный ячеистый газобетон.
За последние 15 лет среднегодовой ввод жилья в России вырос в 2,5 раза. Выпуск автоклавного газобетона за этот же период увеличилось в 12 раз. Он стал самым массовым материалом для возведения стен, применяемым в строительстве.
В последние годы растёт популярность газобетонных блоков — в частности, марок низких плотностей, например, D350. Стоит отметить, что сегодня в России ежегодно выпускается более 1,5 млн м3 блоков низких плотностей. Всё чаще звучит вопрос: как производится этот материал? Развёрнутый ответ на него — в этой статье.
Подготовка сырья
Для изготовления блоков из ячеистого бетона используется смесь цемента, гипса, песка, извести и воды. В неё в небольших объёмах добавляется алюминиевая паста. За точное дозирование всех компонентов отвечает автоматизированная установка.
Формование
Из миксера сырьё поступает в формы большого объёма. Здесь смесь находится несколько часов при температуре, составляющей приблизительно 50º С. Идёт реакция, и массив поднимается, напоминая дрожжевое тесто. Возникает огромное количество ячеек (пор), которые и дают стройматериалу его название. После того, как массив приобрёл требуемый объём, нужно еще некоторое время, чтобы он предварительно отвердел.
По окончании процесса смесь подаётся на участок резки.
Резка на блоки
На очередной стадии массив, сохраняя вертикальное положение, движется по участку резки. Здесь с применением ножей и струн он режется по заранее заданным размерам.
Интересный факт
Отходы материала, образующиеся при резке, вновь поступают в производство. Технологический процесс выпуска ячеистого бетона, таким образом, становится безотходным.
Обработка в автоклаве
Нарезанные блоки помещаются в автоклав — камеру с температурой 180-190ºС, давлением около 12 бар и насыщенным паром. Здесь будущий стройматериал выдерживается в течение 12 часов. За это время в блоках формируется кристаллическая структура, выгодно отличающая автоклавный газобетон от других материалов и придающая ему достойные практические свойства.
После обработки в автоклаве готовый стройматериал с применением крана-делителя выкладывается для остывания.
Упаковывание
На последнем этапе блоки из ячеистого бетона — например, марки D300 — аккуратно запаковываются в перфорированную термоусадочную пленку с помощью автоматического оборудования.
Упакованные газобетонные блоки транспортируются на склад с помощью вилочных погрузчиков. С этого момента они готовы к реализации.
Отличительные особенности применяемого оборудования
Для производства автоклавного ячеистого газобетона на нашем заводе применяется оборудование марки HESS AAC Systems B.V., отвечающее самым строгим международным стандартам.
Система подачи сыпучих материалов. В ней используется запатентованная технология Lahti Precision, реализованная только в линиях HESS, в основе которой — псевдоожижение (флюидизация) материалов. Система разгружает силоса и дозирует подачу сыпучих материалов в псевдоожиженном состоянии, создаваемом с помощью воздуха.
Устройство кантования массива. Массив перед резкой кантуется в форме в вертикальное положение, после чего корпус формы удаляется. Массив не подвергается механическому захвату манипулятором, что положительно влияет на качество конечного продукта. Предотвращается появление трещин, исключается деформация массива, сохраняются прочностные и геометрические характеристики блоков.
Устройство вертикальной, предварительной и окончательной боковой резки. Обрезает материал по трём измерениям, позволяет регулировать толщину снимаемого слоя или выравнивать поверхность массива после предварительной резки. Линия оснащена системой, следящей за обрывом струн. Обрезки массива отбрасываются в шлам-канал, промываемый водой. Отсюда они поступают в ёмкость с размалывающим устройством и мешалкой, расположенную под линией резки. Из ёмкости шлам транспортируется в шламбассейн для дальнейшего использования. Такое решение даёт экономию сырья и служит частью концепции «Безотходное производство».
Система разделения массива. В ней реализована уникальная технология разделения «зелёного» массива, позволяющая расслаивать его непосредственно после резки — до автоклавирования. Массив подается в автоклав разделённым на слои. Благодаря этому пропаривание выполняется максимально равномерно и качественно, и газобетон приобретает предельно возможную прочность. В отличие от традиционных технологий, подразумевающих резку вертикально стоящего массива и разделение «белого» продукта, слипания слоёв при пропаривании не происходит. Поэтому не требуется и дополнительного разделения блоков после автоклавирования. Благодаря этому сохраняется привлекательный вид блоков, исключается появление сколов, отверстий и трещин, обеспечивается идеальная геометрия конечного продукта.
Технология изготовления автоклавного газобетона | gazobeton.org
Газобетон – это легкий искусственный материал, полученный в результате твердения поризованной смеси, состоящей из гидравлических вяжущих веществ, тонкомолотого кремнеземистого компонента, воды и добавки газообразователя.
Для изготовления изделий из ячеистого бетона можно применять различные сырьевые материалы, но наибольшее распространение получили следующие:
— портландцемент ПЦ 400 – ПЦ 500, без активных минеральных добавок;
— известь негашеная кальциевая с содержанием CaO не менее 70%;
— кварцевый песок с содержанием кварца SiO2 не менее 85%, а глинистых примесей не более 3%;
— газообразователь алюминиевая пудра (паста) с содержанием активного алюминия не менее 80%.
Технологический процесс изготовления автоклавного газобетона включает в себя:
— прием и подготовку сырьевых материалов;
— приготовление газобетонной смеси;
— формование массивов газобетона;
— разрезку массивов на изделия;
— автоклавную обработку;
— упаковку изделий.
Сырьевые материалы могут поступать на завод различными видами транспорта (чаще всего автомобильным и железнодорожным). Хранение вяжущих предусматривается в специальных силосах. Количество и объем силосов выбирается в зависимости от мощности завода, удаленности от поставщиков материалов и вида транспорта.
Кварцевый песок выгружаются в приемный бункер, откуда по ленточному конвейеру поступает на помол для приготовления шлама. Помол производится в шаровых мельницах. Далее песчаный шлам транспортируется в шламбассейны, где гомогенизируется с помощью постоянного механического перемешивания.
Негашеная известь на предприятие поступает в тонкомолотом или комовом виде.
В первом случае, тонкомолотая негашеная известь хранится, по аналогии с портландцементом, в силосах и уже готова к употреблению. Во втором случае, если поступает комовая негашеная известь, на предприятии используется технология приготовления известково-песчаного вяжущего путем совместного сухого помола в шаровых мельницах извести и кварцевого песка.
Приготовление газобетонной смеси производится в дозаторно-смесительном отделении. Портландцемент, известь (известково-песчаное вяжущее), песчаный шлам, шлам из отходов резки, вода и алюминиевая суспензия дозируются в соответствии с установленной рецептурой в специальный смеситель, обеспечивающий высокую гомогенность смеси.
Процесс формования включает разгрузку (заливку) смеси из смесителя в форму и вспучивание смеси. Окончание процесса формования наступает после достижения максимальной высоты вспучивания смеси и прекращения активного газовыделения.
После вспучивания формы с газобетонной смесью выдерживаются на постах, желательно при температуре воздуха не менее +15-20oС до приобретения требуемой пластической прочности сырца. Для ускорения процесса набора первоначальной прочности формы со смесью могут выдерживаться в специальных термокамерах при температуре до +70-80oС. Время выдержки при использовании термокамер уменьшается.
После достижения сырцом пластической прочности 0,04-0,12 МПа (в зависимости от технологии) формы подаются на резательный комплекс. Газобетонный массив калибруется со всех сторон и разрезается проволочными струнами в продольном и поперечном направлениях на изделия требуемых размеров. Метод резки газобетонных массивов в полупластическом состоянии с помощью тонких проволочных струн хорошо зарекомендовал себя и на современных резательных машинах позволяет получать изделия точных размеров с отклонениями от номинальных до ±1,0-1,5 мм. Такая точность позволяет осуществлять кладку блоков на тонкослойную клеевую смесь вместо традиционного цементно-песчаного раствора.
Разрезанные на изделия массивы устанавливаются на автоклавные тележки и загружаются в автоклав. После полной загрузки автоклава начинается тепловлажностная обработка по определенному режиму, включающему плавный набор температуры и давления, изотермическую выдержку при температуре около 190°С и давлении 12 атм, плавный спуск давления и подготовка изделий к выгрузке.
Из компонентов CaO и SiO2, вяжущих материалов и кварцевого песка, а также воды, в условиях автоклавной обработки (высокое давление и температура) происходит образование новых минералов – низкоосновных гидросиликатов кальция, что предопределяет более высокие физико-механические характеристики автоклавного газобетона в сравнении с неавтоклавными ячеистыми бетонами (пенобетон, газобетон).
После завершения цикла тепловлажностной обработки изделия подаются на участок деления и упаковки, а затем на склад готовой продукции.
Основные моменты технологии производства блоков из автоклавного газобетона показаны на видео одного из участников ассоциации ВААГ:
Технология производства газобетона
Газобетонные блоки, как и пенобетонные изделия, являются одной из разновидностей ячеистых бетонов. Пористая структура придает этому материалу хорошие тепло и шумоизоляционные свойства, малый вес при больших размерах и достаточную прочность, что качественно выделяет его среди остальных стеновых материалов, широко использующихся при строительстве перегородок, гаража, дачи и др. Кроме этого, сама технология производства газобетона довольно проста, при этом она не требует больших затрат, а цена готового продукта приятно удивляет.
Виды изготовления
Существует 2 разновидности технологии производства газобетонных блоков, а именно: автоклавного твердения и естественной выдержки. В первом случае используют специальные камеры – автоклавы, снабженные регулятором давления и температуры. Газобетон, получаемый таким способом более качественный и прочный, нежели тот, который был высушен в естественных условиях, но зато вторая технология приемлема для тех, кто хочет изготовить блоки в домашних условиях, хоть он получится не настолько надежный как хотелось бы, но он все равно будет пригоден для строительства малоэтажных частных домов.
Сырьевые компоненты
Для изготовления газобетонных блоков по любой технологии понадобятся следующие его составляющие:
Вода
Для блоков пригодна любая питьевая и техническая чистая вода, однако она должна отвечать всем требованиям ГОСТ 23732-79. Вода с температурой 45, качественно увеличит скорость твердения, прочность и производительность линии изготовления. Подогрев воды поможет снизить количество применяемого цемента, за счет искусственной стимуляции его активности.
Песок
Подойдет любой речной или карьерный, главное, чтобы в нем содержалось минимальное количество глинистых и илистых частиц, а максимальная крупность зерен не превышала 2 мм.
Портландцемент
Предпочтительно вяжущее марок М 400 и М 500, лучший цемент тот, который по всем критериям удовлетворяет требования ГОСТ 10178-85.
Газообразователь
В его качестве используется алюминиевая пудра марок ПАП-1 или ПАП-2.
Оборудование
Технологическая линия изготовления газоблоков подразумевает наличие специального оборудования, которое приобретается в комплексе у производителя. Как правило, такой комплекс представляет собой автоматизированный мини–завод, который имеет довольно компактные размеры. Некоторые производители, бонусом к приобретаемому оборудованию предоставляют услуги временного технолога, который обучит вас, настроит производственную линию и подберет оптимальный состав газобетонной смеси.
Основные этапы
Конкретный алгоритм производства зависит от специфики приобретенного оборудования, но в общем он подразумевает 3-этапное производство газоблоков:
- Первым делом происходит точная дозировка компонентов и их перемешивание, в среднем этот цикл длится не более 10 минут.
- После чего, приготовленную бетонную массу, посредством специального оборудования, выгружают в заранее смазанные формы ровно до половины. Далее, в течении 4-часов смесь «растет» и заполняет весь объем форм, еще через 2 часа излишки смеси убираются.
- И третий, завершающий этап – распалубка изделий после 16-часовой выдержки и складирование их на поддоны для дальнейшего набора отпускной прочности, которая происходит в течение 2 или 3 суток, после чего изделия отправляются на склад. Марочной прочности газобетонные блоки достигают на 28 сутки.
Вывод
Чтобы получить на выходе хороший газобетон, нужно приобрести надежное оборудование и качественное сырье. Также обязательно следование всем правилам технологии, и только три эти составляющие в совокупности помогут не только окупить вложения, но и принести хорошую прибыль.
Удачной стройки!
ведущий производитель и реализатор газобетонных блоков и пенобетона
Завод Биктон
В 2008 году ООО «Волжский завод строительных материалов» совместно с государственной корпорацией «Внешэкономбанк» (г. Москва) приступил к реализации инвестиционного проекта, связанного со строительством современного производства по изготовлению газобетона под торговой маркой BIKTON. Запуск завода состоялся в июне 2010 года.
Расположение будущего производства продумывалось с особой тщательностью. В результате новый завод появился на границе республик Татарстан и Марий Эл — в городе Волжск. Причиной окончательного определения места расположения завода стала совокупность факторов: это наличие подъездных железнодорожных путей, низкая стоимость подключения к электроэнергии, а также наличие на площадке доступа к большому объему газа. Потому что именно эти факторы оказывают большое влияние на эффективность производства. Также сыграла роль близость к таким крупным городам Поволжья как Казань, Чебоксары и Йошкар-Ола, что дало возможность большому числу потребителей доставить материал на стройплощадку непосредственно со склада предприятия.
При строительстве завода использовались последние достижения и технологии. За счет рационального использования высокотехнологичного импортного оборудования фирмы «MASA-Henke» (Германия), применения новой технологической концепции ударных воздействий на структуру газобетона при формовке, продукция имеет более высокие физико-механические характеристики по сравнению с аналогичной продукцией, которая уже нашла свое массовое применение на строительных объектах Российской Федерации.
«Наша задача — создать экономичный и суперэффективный материал, — рассказывает технический директор завода Андрей Валентинович Полянчиков, — поэтому при выборе технологии мы остановились на ударном принципе». Внедрение ударной технологии и системы автоматизированного управления процессом дозирования бетонной смеси позволяет выпускать газобетонные блоки объемной плотностью 400-700 кг/м3 с обеспечением равномерности технических характеристик на уровне самых высоких мировых стандартов.
Благодаря использованию точнейшего резательного комплекса блоки имеют идеальные геометрические размеры, что позволяет вести кладку на специальный клей с толщиной шва до 3 мм. Такой способ исключает образование «мостика холода», ведь конструкция становится практически однородной.
Клей для кладки газобетонных изделий производится на отдельной, автоматизированной линии фирмы «Вселуг» также на этой линии выпускаются штукатурные, клеевые, шпатлевочные сухие смеси с широкой областью применения. Произведенная продукция укладывается на качественные ровные поддоны, сверху с помощ ью упаковочной линии «Стретчхуд» обтягивается защитной пленкой, остывает, отстаивается, набирает прочность, после чего поступает на склад готовой продукции.
Склад общей площадью 30654,88 м2 позволяет постоянно содержать в наличии в достаточном количестве широкий ассортимент типоразмеров и плотностей газоблоков.В связи с повышенным спросом на продукцию во избежание перебоев в поставках, а также увеличением оперативности доставки на заводе организована круглосуточная погрузка.
Управление и обслуживание производственного процесса производится квалифицированным персоналом, который прошел европейские программы обучения технологиям производства и по эксплуатации оборудования для производства газобетона.
Завод Биктон сегодня:
Эффективный строительный материал
100% соответствие ГОСТ 31360-2007;
Широкий ассортимент продукции всегда в наличии на складе;
Высокие технические показатели и их равномерность;
Идеальная геометрия блоков – экономия на кладочном и штукатурном составах;
Низкая отпускная влажность;
Линейка сухих строительных смесей и клеев;
Собственная испытательная лаборатория, осуществляющая входной контроль сырья и испытания готовой продукции;
Производственная мощность газобетонных блоков — 360 тыс. м3 в год, сухих строительных смесей – 38 тыс. тонн в год;
Поставки осуществляются в более 10 регионов РФ;
Собственная логистическая база и автопарк – возможность обеспечить бесперебойную доставку больших объемов одновременно;
Строительство;
Проектирование;
Комплексная система сервиса.
Это стало возможным благодаря:
Высокой автоматизированной технологической оснащенности;
Финансовой надежности и стабильности предприятия;
Эффективному руководству и профессионализму сотрудников.
Линия газобетона — Оборудование из Китая
Газобетонный завод из КитаяОборудование из Китая для производства автоклавного газобетона характеризуется высокой степенью автоматизации, рациональным размещением.
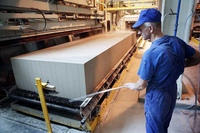
Наш завод является лидером в области производства оборудования для изготовления автоклавного газобетона. Технические специалисты всегда готовы оказать всем клиентам профессиональную помощь и поддержку. Благодаря комплексной системе поставок сырьевого материала (закупка, анализ качества, хранение и транспортировка) вместе с передовым производственным оборудованием, позволяют нам производить станки высокого качества и доставлять ее заказчику. Перед отправкой заказчику, газобетонное оборудование проходит строжайший анализ качества. Каждый станок сопровождается технической документацией.
Автоклавный газобетон – материал, изготавливаемый путем термической обработки в автоклаве. Сырьевые ингредиенты: цемент, кварцевый песок и специализированные газообразователи, известь. В состав смеси добавляют гипс, золу и шлаки металлургических производств. В качестве специализированных газообразователей используются алюминиевые пасты и суспензии. В ходе химической реакции смесь вспенивается, и внутри образуются поры разной величины, заполненные воздухом.
Благодаря многолетнему опыту работы в сфере изготовления линий производства бетонных изделий, наша компания предлагает Вам широкий выбор промышленных линий производства с ежегодной производительностью от 150-350 тыс. м3.
Приобретая наши производственные линии, наша компания также предлагает Вам различные виды вспомогательного оборудования, а также резательные комплексы. Например, если Вы решили приобрести линию производства газобетонных блоков размерами 240 мм, мы рекомендуем Вам приобрести также станок резки с формой размерами 4.8×1.2м. В отличие от формы размерами 5×1.2м, данная форма позволит отделять большее количество излишек бетонного массива для последующей переработки и использования.
Параметры газобетонных линий
Параметры | Ед. | 200,000 м³ | 300,000 м³ | 350,000 м³ |
Производ-ть | м³ | 200,000 | 300,000 | 350,000 |
Форма | м | 4.8×1.2×0.6 | 6.0×1.2×0.6 | 6.0×1.5×0.6 |
Сырье |
|
|
|
|
Песок | т/г | 84,000 | 126000 | 147000 |
Известь | т/г | 20,400 | 30600 | 35700 |
Гипс | т/г | 3,600 | 5400 | 6300 |
Цемент | т/г | 12,000 | 18000 | 21000 |
Мощность | кВт | ≈1,200 | ≈1600 | ≈1650 |
Электро- энергия в год | 10,000 kWh | ≈271. | ≈362.3 | ≈373.62 |
Вода в год | т | ≈108,000 | ≈162000 | ≈178500 |
Газ в год | т | ≈36,000 | ≈54000 | ≈52500 |
Площадь завода | га | ≈3.5 | ≈45 | ≈50 |
Площадь | м2 | ≈7,000 | ≈9200 | ≈10000 |
Складская площадь | м2 | ≈8,000 | ≈10000 | ≈12000 |
1. Подготовка сырьевых материалов
После дробления известь и гипс хранятся в вертикальном силосе. Затем гранулы извести и гипса направляются в шаровую мельницу по ленточному транспортеру. Песок размалывается во влажной шаровой мельнице до консистенции шлама и перекачивается в шламобассейн.
2. Дозирование, смешивание и заливка бетонной смеси
В определенных пропорциях происходит добавление песчаного шлама, цемента в смеситель. Путем подачи пара происходит нагрев сырьевого материала до температуры 40-45 градусов и смешивание. После завершения цикла смешивания 3 ~ 4 минуты, открывается загрузочный клапан алюминиевой пасты и добавляется в смеситель. Происходит дальнейшее перемешивание около 40 секунд. Полученную смесь заливают в формы. Весь цикл составляет 6 ~ 8 минут. Формы перевозятся в зону вспенивания и отверждения (созревания) при температуре 40-45 градусов. Время отверждения составляет 90-150 минут. После чего формы перевозят в зону резки.
3. Резка бетонного массива
От зоны созревания форма передвигается под кантовочный манипулятор, который поднимает ее, разворачивает на 90° и устанавливает на резательные платформы. На тележке резательной линии борт (платформа) с массивом двигается через секции линии резки. Вначале устройство предварительной обрезки срезает излишки, образовавшиеся в верхней части массива во время созревания. Затем блоки обрезаются по длине и ширине будущего продукта. При необходимости вырезается контур (паз и гребень). Потом горизонтальный режущий автомат разрезает блоки по толщине. Автоматический станок вертикальной резки осуществляет точную обрезку блоков по высоте и длине. Проволочные струны обрабатывают массив сверху донизу. Все срезанные остатки и обрезки массива сбрасываются в шламканал и отправляются обратно в шламбассейн для последующего использования.
4. Автоклавная обработка газобетонных блоков
Вагонетки вталкивается в автоклав. После закрытия крышки в автоклаве создается вакуум и нпри температуре 190оС, давлении пара 1.2 мРа происходит процесс твердения газосиликата. Эти параметры сохраняются несколько часов. В конце автоклавного цикла давление снижается до атмосферного. Цикл автоклавирования составляет 11-12 ч. После завершения процеса крышка автоклава открывается. Автоклавные вагонетки вытягиваются передаточной платформой и толкаются на отдельный путь для разгрузки. Конденсат, образованный при разнице температуры дренажируется, охлаждается и направляется на повторное использование.
Автоклавированные блоки перемещаются на делитель и по очереди разделяются. Формы отвозятся в зону очистки и последующей заливки. Отходы собираются вместе и затем перемешиваются со свежей шламовой массой в определенных пропорциях. Полученная смесь используется в дальнейшем.
1. Весь процесс производства газобетонных блоков, начиная с подготовки сырьевого материала и заканчивая упаковкой, проходит слаженно и без задержек. Формы для выдерживания смеси-сырца, транспортные и автоклавные тележки двигаются по индивидуальным накопительным путям, что позволяет им без преград осуществлять транспортировку материала и возвращаться к рабочей зоне для последующего цикла. Каждый этап обработки зеленого массива выполняется своевременно, без перерывов и вмешательства в последующие этапы. Таким образом, применение нашей производственной линии – это залог изготовления качественного продукта и безопасность эксплуатации.
2. Распалубочная машина, укладчик для бетонных заготовок, делитель и разгрузочный манипулятор работают на базе гидравлики и портального крана, которые способны разворачивать бетонные блоки в различных направлениях. Применение данной технологии упрощает процесс производства, устраняет необходимость использования тяжеловесных промышленных кранов, упрощает процесс проектирования заводского помещения и снижает затраты на его постройку.
3. Запатентованный кантующий манипулятор оснащен специальными скребками, которые удаляют излишки массива со всех шести сторон.
4. Транспортные тележки оборудованы цепным приводом, а также механизмом позволяющим ей автоматически двигаться в заданном направлении, позволяя полностью автоматизировать процесс транспортировки материала.
5. Сортировочная установка осуществляет сортировку и транспортировку массива к делителю, который, в свою очередь, выполняет разделение одного слоя массива вдоль намеченных швов.
6. Разгрузочный манипулятор выполняет погрузку блоков на деревянные паллеты, расположенные на упаковочной линии. После того как этап упаковки завершен, блоки погружаются на автопогрузчик и транспортируются на склад готовой продукции. Применение данного вида оборудования позволило перейти на автоматизированную транспортировку готовой продукции и снизить нагрузку операторов.
7. Система центрального управления линией производства может быть разделена на несколько источников управления, каждый из которых будет самостоятельно выполнять свою функцию и позволит операторам вести визуальный контроль над производством. Такая система позволит улучшить эффективность производства, качество продукции, снизит нагрузку операторов и коэффициент субъективных ошибок.
Мы будем рады проконсультировать Вас и ответить на все Ваши вопросы. Мы предложим Вам линию, полностью соответствующую Вашим потребностям и пожеланиям.
- Оборудование производства газобетонных блоков
Заводы по производству газобетонных блоков
Для возведения зданий все чаще используется такой строительный материал, как газобетон. Его прочность и легкость достигаются благодаря процессу автоклавирования, в ходе которого смесь из цемента, алюминиевой пудры, извести, кварцевого песка и воды подвергается воздействию высокой температуры и повышенного давления.
Такой метод используется всеми ведущими предприятиями. Познакомиться с их продукцией и получить о ней максимум полезной информации вы сможете из нашей статьи.
Ytong
С 2007 года введен в эксплуатацию завод по производству газобетонных блоков в Московской области (г. Можайск), где реализована фирменная технология по автоклавного твердения под маркой Ytong®.
Специалистами компании осуществляется постоянное внедрение инновационных производственных методов, основанных на собственных научных разработках. Также обеспечивает постоянный контроль качества, благодаря чему продукция соответствует критериям ГОСТ, а также требованиям по экологической/радиационной безопасности и огнестойкости.
Bonolit
Востребована также продукция такой компании, как Bonolit. Она производится на современной технологической линии HESS AAC Systems B.V. В перечень выпускаемых товаров входят такие разновидности, как:
- Стеновые;
- Для навесных фасадов;
- Перегородочные;
- П-образные;
- Арочные и пр.
Компанией автоматизированы все технологические процессы, которые в обязательном порядке контролируются высококвалифицированными специалистами. Предельно допустимое отклонение в геометрии газоблоков составляет +-1 мм. Согласно заявлениям производителя, производимый им материал сохраняет эксплуатационные свойства до 100 лет даже при отсутствии дополнительной фасадной облицовки.
Калужский газобетон
Предприятие, расположенное к Калужской области, оборудовано современной технологической линией фирмы WKB. Им производятся автоклавные газобетонные блоки, плотность которых составляет D300, D400, D500 и D600. В ассортименте присутствуют и U-образные варианты.
Продукция может использоваться для возведения таун-хаусов, промышленных/коммерческих сооружений, дачных домов и коттеджей. Она востребована и в многоэтажном строительстве при заполнении железобетонных каркасов, а также при ремонте и реконструкции. Товары соответствуют требованиям по тепловой защите сооружений СНиП 23-02-2003.
Костромской силикатный завод
Был основан ещё 8 декабря 1930 года. Это один из старейших заводов Костромской области.
В 2013 году был введен в эксплуатацию новый гидравлический пресс для производства силикатного кирпича.
Сегодня на предприятии выпускаются не только газоблоки и кирпич, но и освоено производство элементов мощения включающих в себя: плиты бетонные тротуарные, бордюрный камень, водосток. Акционерное общество обладает широким парком автомобильной техники, способной доставить продукцию в любой регион Российской Федерации.
Егорьевский ЗСМ
Среди заводов-производителей газобетонных блоков особое место принадлежит этому предприятию. Оно предлагает газоблоки минимальной толщиной 200 мм и в четырех основных разновидностях. Это гладкие и пазогребневые блоки, которые могут быть с захватом либо без него. На официальном сайте компании представлена необходимая информация об ассортименте и предоставлены сертификаты качества.
На производстве установлена высокотехнологичная линия Masa Henke (Германия), обеспечивающая выпуск качественной продукции. Она соответствует жестким нормам экологической безопасности, огнестойкости, прочности и морозостойкости.
Кто лучше?
Кому из заводов-производителей газобетонных блоков отдать предпочтение, однозначно сказать сложно. Каждый из вышеперечисленных брендов может похвастаться отличными товарами, чье качество подтверждается соответствующими протоколами и сертификатами. При выборе стоит обратить внимание на точные эксплуатационные характеристики, а также на стоимость предложенных вариантов.
Производство блоков из газобетона | Технологии изготовления газобетонных блоков PORITEP
Технологический цикл производства газобетона предусматривает проведение сложных операций, невозможных без современного дорогостоящего оборудования. Автоклавная обработка увеличивает прочность материала, а технология производства обеспечивает равномерность распределения пор.
Мы предстваляем Вашему вниманию стеновой материал из ячеистого бетона автоклавного твердения под торговой маркой PORITEP, изготовленный по традиционной рецептуре на современном и полностью автоматизированном оборудовании немецкой компании Wehrhahn. Производственная линия ecoPLUS с проектной мощностью 285 000 м³ в год, установленная на предприятии, позволяет выпускать стеновые блоки различных плотностей от 300 до 600 кг/м³. Линия резки дает возможность производить блоки толщиной от 50 до 500 мм с шагом 5 мм.
Для Вашего удобства мы подготовили для Вас видео производства и представили по отдельности все этапы производства блоков PORITEP.
Сырьевые материалы
Автоклавный газобетон производится из смеси кремнеземистого компонента, цемента, извести, гипса, воды и газообразователя.
Сырье сопровождается постоянным входным и пооперационным контролем, осуществляемым заводской лабораторией, оснащенной самым современным оборудованием, аттестованной на проведение испытаний и анализ всех видов сырья, а также определение конечных характеристик готовой продукции.
|
||
Кремнеземистый компонент и гипсовый камень хранятся на закрытом складе завода. Кремнезёмистый компонент является экологическим чистым основным составляющим элементом в производстве блоков. В процессе подготовки к производству он проходит очистку от натуральных природных примесей, что существенно повышает его качественные характеристики.
Силоса сыпучих материалов |
Цемент и известь, в виде порошка, завозятся автотранспортом и разгружаются напрямую в рабочие силоса сыпучих материалов.
Введение извести сокращает расход цемента и одновременно увеличивает щелочность раствора, обеспечивая энергичное протекание реакции газообразования. Материалы, применяемые для изготовления ячеистых бетонов, соответствуют требованиям ГОСТ.
Компания работает с крупнейшими поставщиками сырьевых материалов в России, что дает гарантию высокого качества основных компонентов. Дополнительно, входной контроль сырьевых материалов исключает возможные отклонения технических параметров компонентов от требований технологического процесса производства. Жесткое соблюдение рецептуры позволяет получать конечный продукт по заявленным характеристикам выше требований ГОСТ.
Вода для производственного процесса берется из Новомичуринского водохранилища, которое является искусственным водоемом. Сегодня его используют для летнего отдыха – рыбалки, подводного плавания и пр.
Помол и смешивание компонентов
Кремнеземистый компонент и гипс загружаются фронтальным погрузчиком в питающие бункера, с которых транспортируются ленточным транспортером и подаются в шаровую мельницу , где подвергаются мокрому помолу.
Приготовленный прямой шлам подается в бассейны для накопления
Дозирование компонентов
Главный смеситель |
Дозирование компонентов в главный смеситель осуществляется в автоматическом режиме. Сначала подается прямой и обратный шлам с весов жидких компонентов, горячая и холодная вода (двигатель смесителя работает на малых оборотах), затем двигатель начинает работать на больших оборотах, происходит подача цемента и извести. После перемешивания компонентов добавляется заданное количество алюминиевой суспензии, смесь дополнительно перемешивается.
Подача цемента и извести |
Заливка форм
Содержимое миксера заливается в большие формы через отверстие в нижней части мешалки при помощи заливочного рукава.
Заливка в форму |
Формы до заливки проходят предварительную очистку и смазку минеральным маслом, для предотвращения сцепления смеси с металлом форм.
Смазка формы |
Равномерность смеси гарантируется за счёт воздействия высокочастотных виброигл, которые кратковременно опускаются в форму.
Виброиглы |
Важнейшей технологической особенностью получения высококачественных газобетонных изделий максимальной пористости и достаточной прочности является создание оптимальных условий для двух одновременно протекающих процессов газовыделения и газоудержания. Необходимо обеспечить соответствие между скоростью реакции газовыделения и скоростью нарастания структурной вязкости цементного теста или раствора. При этом выделение газа должно как можно полнее закончиться к началу схватывания системы цемент — вода. Протекание процесса газообразования определяется большим количеством различных факторов. Наибольшее влияние на скорость этого процесса оказывают вид, количество и свойства газообразователя, щелочность и температура среды и т. д.
Перемешивание газобетонной массы должно продолжаться 2-3 мин. В настоящее время применяют высокоскоростные пропеллерные мешалки. Тщательное перемешивание массы обеспечивает однородность смеси и равномерность вспучивания. Излишняя продолжительность смешивания вредна, так как возможно начало интенсивного газообразования в мешалке. При этом теряется часть выделившегося газа и при заливке в формы газобетонная масса не даст нужного вспучивания.
Созревание массива
Через некоторое время бетонная смесь поднимается и заполняет форму. Происходит формирование ячеистой структуры будущего газобетона. После того, как массив поднимется, необходимо еще некоторое время для его предварительного твердения, которое проходит около 180 мин на участке созревания, при температуре не ниже 50°C. Это необходимо для набора определенной структурной прочности массива, достаточной для последующей его распалубки и резки на блоки. Срок созревания зависит как от технических параметров сырьевых компонентов, так и от внешних условий. Как только массив приобретет достаточную твердость для последующей резки, форма автоматически транспортируется из зоны созревания на кантующий манипулятор.
Форма перед камерой созревания |
Плотность ячеистого бетона и его пористость зависят и от расхода пороообразователя, и степени использования его порообразующей способности. Некоторое влияние на них оказывают температура смеси и количество воды, принятое для затворения смеси, т. е. водотвердое отношение В/Т (отношение объема воды к массе вяжущего вещества и кремнеземистой добавки). Увеличение В/Т повышает текучесть смеси, а следовательно, улучшает условия образования пористой структуры, если обеспечивается достаточная пластичная прочность смеси к концу процесса газообразования.
Резка
Массив, находящийся в форме в горизонтальном положении освобождается от корпуса формы и переворачивается на 90º с помощью универсального кантователя. В результате массив ставится на специальный автоклавный поддон в вертикальном положении, который в свою очередь устанавливается на транспортную вагонетку линии резки.
Освобождение массива от корпуса формы |
Сама форма проходит через станцию автоматической смазки, на которой распылителями наносится тонкий слой разделительного масла, и затем форма подается для заливки в начало нового цикла.
Линия резки – это сердце газобетонного завода. Технология WEHRHAHN совершенствовалась десятилетиями, и сегодня она обеспечивает точность резки, с допусками по толщине и высоте не более 0,5 мм. Массив обрабатывается на линии резки с помощью тонких струн и ножей исключительно в вертикальном положении — это гарантирует самую высокую точность.
Резательная линия |
Массив находится на отдельном автоклавном поддоне и перемешается через отдельные секции линии резки.
- Устройство вертикальной, предварительной и последующей боковой резки обрезает массив по длине, высоте и ширине до размеров 6000 х 1200 х 625 мм. Оно оборудовано боковым триммером с режущими струнами и ножами. На этом этапе также может осуществляться резка с профилем «паз-гребень». Разрезанный массив кантуется в горизонтальное положение и проходит на автоклавном поддоне через установку удаления нижнего слоя. Затем массив снова кантуется в вертикальное положение и возвращается на линию.
Поперечная резка зеленого массива |
- Горизонтальная резка осуществляется посредством пневматически натянутых стационарно установленных струн
- Автомат поперечной резки производит точный вертикальный разрез массива посредством пневматически натянутых струн. Режущая рама со струнами двигается сверху вниз и обеспечивает точную резку блока по высоте.
После вакуумный колпак поднимает верхний срезанный слой и сбрасывает его в шлам-канал под линией резки.
Горизонтальная и поперечная резка осуществляется пневматически натянутыми проволочными струнами толщиной 0,6; 0,8 мм. Натяжение струн производится пневматическим натяжным устройством для каждого элемента, которое позволяет произвести простую настройку в пределах шага 5 мм. Линия резки оборудована системой контроля над обрывом струн.
Все срезанные остатки и обрезки массива сбрасываются в шлам-канал. Обратный шлам направляется в ёмкости под линией резки, оборудованные мешалками и размалывающими устройствами, из которых затем перекачивается в шлам-бассейны обратного шлама с помощью шламового насоса (рис. 9) для последующего использования.
Удаление верхнего слоя |
Удаление нижнего подрезного слоя |
Автоклавирование
Накопительные пути |
На следующем этапе производственного процесса многофункциональный манипулятор переносит поддон с массивом в зону накопительных путей. Таким образом, на один путь собираются в тупиковом порядке восемь тележек, каждая с четырьмя массивами, образуя «состав» в 144 м³.
Автоклав (внутри завода) |
Когда один автоклав (длина: 49,7 м; диаметр: 3 м) готов к принятию тележек, начинается загрузка. Операция загрузки и разгрузки автомата занимает примерно один час. Накопительные пути оборудованы приводами, которые двигают тележки по отдельности к траверсному транспортёру, который в свой очередь перемещается поперечно перед автоклавами и толкает тележку в соответствующий. Операция повторяется до окончательной загрузки, и после закрытия автоклава начинается автоклавная обработка.
Выдержка блоков в автоклаве обычно длится 12 часов, однако это время зависит от характеристик сырья и объемной плотности продукта. После закрытия крышки создается вакуум в -0,5 бар. В течение 1,5–2 часов происходят подъемы температур до 190°C и давления до 12 атмосфер, которые поддерживаются приблизительно в течение шести часов. Вывод автоклава из рабочего режима длится около 1,5–2 часов. По окончании этой фазы крышку можно открывать.
Зона остывания |
При автоклавировании образуется уникальная кристаллическая структура. Именно за счет нее автоклавный газобетон становится существенно более прочным по сравнению с неавтоклавным материалом.
После автоклавной обработки массивы направляются в зону ожидания для остывания.
Упаковка
Из зоны ожидания массивы подаются на линию механического разделения, затем в зону накопления для последующей упаковки.
Разгрузочный кран переносит массивы на столешницу с последующей укладкой непосредственно на деревянные поддоны, которые подаются в автоматическом режиме. Затем поддоны с блоками упаковываются в stretch hood пленку и перевозятся вилочным погрузчиком на склад готовой продукции.
Упаковка в пленку |
Склад готовой продукции |
(PDF) Исследование производства газобетонных блоков в Бангладеш
IJISET-МеждународныйЖурналинновационныхнауки, Инжиниринга и Технологии, Vol. 2Issue3, March2015 .
www.ijiset.com
ISSN2348 – 796
200
Исследование производства газобетонных блоков в
Бангладеш
Ahsan Habib, Hosne Ara Begum, Eng. Rubaiyet Hafiza
Жилищно-строительный научно-исследовательский институт
Дарус-Салам 120/3, Мирпур, Дакка-1216, Бангладеш
РЕЗЮМЕ
Основная цель этой статьи — представить
потенциальных возможностей и методов формирования газированных
бетон в контексте Бангладеш.В этом эксперименте
для процесса аэрации использовался метод получения газообразного водорода
. В этом методе газификации
тонкоизмельченный алюминиевый порошок
был добавлен к суспензии обычного портландцемента с
различных процентных соотношений, таких как 0,05%, 0,1%, 0,15%,
0,2% и 0,25%. Чтобы определить влияние алюминиевого порошка
на свойства конечного продукта,
было проведено несколько испытаний, таких как плотность, водопоглощение
и испытание на прочность при сжатии.Однако было замечено, что бетон, содержащий 0,15% алюминиевого порошка
, способствует повышению прочности
пенобетона.
Ключевые слова- Автоклавный газобетон, Алюминиевый порошок.
ВВЕДЕНИЕ
Обычные строительные материалы недоступны для большинства населения Бангладеш
из-за их низкой доступности по цене
. Помимо роста стоимости строительных материалов на
, рост экологических проблем
в связи с интенсивной эксплуатацией природных ресурсов
, связанных с общим строительством и другими
жилищного строительства, требует поиска
альтернативных технологических вариантов.В этой статье делается попытка
найти устойчивую и доступную альтернативу
материалу для замены обычных кирпичей для основных строительных приложений
. С этой целью было проведено исследование
на газобетоне. Газобетон
, также известный как газобетон в автоклаве
(AAC), автоклавный ячеистый бетон (ACC) или
Легкий бетонв автоклаве (ALC)
(1)
, было изобретено
в середине 1920-е годы шведского архитектора
и изобретателя Йохана Акселя Эрикссона
(2) (3)
.
Автоклавный газобетон (AAC) — популярный строительный материал
, который используется во всем мире. Его
имеет успешную 50-летнюю историю, может использоваться во всех
средах для всех типов зданий (Wittmann,
1983, 1992)
(4) (5)
.
Это легкий сборный строительный материал
, который одновременно обеспечивает структуру, изоляцию
, огнестойкость и устойчивость к плесени. В зависимости от плотности
до 80% объема блока AAC составляет
воздуха.Низкая плотность AAC также объясняет его низкую прочность конструкции на сжатие
. Он может выдерживать нагрузки от
до 8 МПа (1160 фунтов на квадратный дюйм), что составляет примерно 50% от прочности на сжатие
обычного бетона
(6)
. AAC
был впервые коммерчески произведен в Швеции в 1923 году.
С тех пор производство и использование пенобетона
распространилось в более чем 40 странах на всех континентах
, включая Северную Америку, Центральную и
Южную Америку Европа, Ближний Восток, Дальний Восток
и Австралия.Благодаря этому обширному опыту было произведено
многочисленных тематических исследований использования в различных климатических условиях и
в соответствии с различными строительными нормами. В США
современных применений AAC началось в 1990 году для жилых
и коммерческих проектов в Юго-восточных штатах.
Производство простых и усиленных ААС в США началось в 1995 году на юго-востоке страны
и с тех пор распространилось на другие
частей страны. Общенациональная группа производителей AAC
была сформирована в 1998 году как Ассоциация по производству газобетонных изделий Autoclaved
(AACPA, www.aacpa.org). Положения по проектированию и строительству
для кирпичной кладки AAC приведены в Кодексах и спецификациях MSJC
. AACPA включает одного производителя
в Монтеррее, Мексика, и многие технические материалы
доступны на испанском языке. AAC
одобрен для использования в категориях сейсмического проектирования A, B
и C Дополнением 2007 г. к Международным строительным нормам
, а в других географических точках —
с одобрения местного строительного органа
(7)
.Многие
исследователей были выполнены на AAC. Johan
Alexanderson (1979) изучил взаимосвязь между структурой
и механическими свойствами газобетона автоклава
и обнаружил, что прочность газобетона
, особенно цемента и извести,
увеличивается с увеличением количества гидратов и
с уменьшающейся пористостью. П.Г. Burstrom (1980)
изучал герметики между элементами из пенобетона
и сообщил, что из-за низкой прочности на разрыв
газобетона герметизация стыков между такими элементами
вызывает особую проблему.Cabrillac R et al.
(1996) сообщили о проблемах оптимизации пористости и свойств газобетона
. N.
Narayanan, K. Ramamurthy (2000) изучили около
микроструктурных исследованийна ячеистом бетоне и
сообщили, что причины изменений прочности на сжатие
и усадки при высыхании объясняются со ссылкой на
на изменения микроструктуры. . Хуля Кус
и Томас Карлссон (2003) изучили около микро
структурных исследований естественного и искусственно выдержанного автоклавного газобетона
.Хуля Кус и
,и др. (2004) сообщили об оценке эксплуатационных характеристик
стен из газобетона
из гипсокартона путем долгосрочного мониторинга влажности. A. Laukaitis
и B Fiks (2006) сообщили об акустических
свойствах газобетона автоклавного твердения и обнаружили
, что оценка акустических качеств AAC составляет
на основе воздухопроницаемости и пористости материала.
A. Laukaitis et al (2009) сообщили о влиянии
волокнистых добавок на свойства автоклавированных газобетонных смесей
и прочностные характеристики
изделий. Обработка в автоклаве, выполняемая при высокой температуре и давлении
экономически выгодна
Обзор процесса производства блоков AAC
Автоклавный газобетон (AAC) — это легкий, похожий на бетон материал с множеством небольших закрытых внутренних пустот. AAC обычно весит от одной шестой до одной трети веса обычного бетона и составляет от одной шестой до одной трети прочности. Подходит для несущих стен и стен с низким и средним этажом.Его теплопроводность составляет одну шестую или меньше, чем у обычного бетона, что делает его энергоэффективным. Его огнестойкость немного выше, чем у обычного бетона такой же толщины, что делает его полезным в приложениях, где важна огнестойкость. Из-за своих внутренних пустот AAC имеет низкую передачу звука, что делает его полезным с акустической точки зрения.
Блоки и панели из AAC становятся популярными строительными материалами из-за их легкости и высокой прочности. AAC производится из обычных материалов: извести, песка, цемента, воды и небольшого количества разрыхлителя.AAC экономически и экологически превосходит более традиционные конструкционные строительные материалы, такие как бетон, дерево, кирпич и камень. AAC предлагает невероятные возможности для повышения качества строительства и в то же время снижения затрат на строительной площадке.
Процесс производства газобетона в автоклаве несколько отличается на разных производственных предприятиях, но принципы схожи. Процесс производства блоков AAC включает следующие этапы:
Подготовка сырья: Ключевым ингредиентом для производства блоков из автоклавного газобетона (AAC) является богатый кремнеземом материал, такой как летучая зола, прудовая зола или песок.Большинство компаний в Индии используют летучую золу для производства блоков AAC. Летучая зола смешивается с водой с образованием суспензии летучей золы. Образовавшаяся таким образом суспензия смешивается с другими ингредиентами, такими как порошок извести, цемент, гипс и алюминиевый порошок, в количествах, соответствующих рецепту. В качестве альтернативы для изготовления блоков AAC также можно использовать песок. «Мокрая» шаровая мельница мелко измельчает песок с водой, превращая его в песчаную суспензию. Суспензия песка смешивается с другими ингредиентами так же, как и суспензия летучей золы.
Дозирование и смешивание: Блок дозирования и смешивания используется для формирования правильной смеси для производства блоков из автоклавного газобетона (AAC).Суспензия летучей золы / песка перекачивается в отдельный контейнер. После того, как желаемый вес налит, перекачивание прекращается. Аналогичным образом известковый порошок, цемент и гипс разливаются в отдельные емкости с помощью винтовых конвейеров. После того, как необходимое количество каждого ингредиента заполнено в отдельные контейнеры, система управления отправляет все ингредиенты в смесительный барабан. Смесительный барабан похож на гигантскую чашу с вращающейся внутри мешалкой для правильного перемешивания ингредиентов. В установку также может подаваться пар для поддержания температуры в диапазоне 40-42oC.Конструкция чаши меньшего размера, используемая для подачи алюминиевого порошка, также является частью смесительного устройства. После того, как смесь взбита в течение установленного времени, ее можно разливать в формы с помощью дозатора. Дозатор выпускает эту смесь в заданных количествах в формы для вспенивания. Процесс дозирования и смешивания выполняется непрерывно, потому что, если между загрузкой и выгрузкой ингредиентов будет большой промежуток, остаточная смесь может начать затвердевать и забить все устройство.
Литье, подъем и предварительная обработка: Перед литьем формы покрываются тонким слоем масла. Это сделано для того, чтобы зелень не прилипала к формам. Пока суспензия смешивается и разливается в смазанные маслом формы, алюминий реагирует с гидроксидом кальция и водой с образованием водорода. В результате этой реакции выделяются миллионы крошечных пузырьков водорода. Это приводит к образованию крошечных несвязанных ячеек, вызывающих расширение суспензии. Такое расширение может быть вдвое больше первоначального объема.Этот процесс называется подъемом. Эти ячейки являются причиной легкости и изоляционных свойств блоков AAC. После того, как процесс выращивания закончится, зеленому пирогу дают возможность осесть и затвердеть в течение некоторого времени. Это обеспечивает прочность резки, необходимую для резки проволокой.
Обычно процесс подъема и предварительного отверждения занимает около 1-4 часов. Рост зависит от состава сырья и погодных условий. Поскольку на реакцию влияют погодные условия, рекомендуется поддерживать постоянную температуру в зоне предварительного отверждения.В связи с этим предварительное отверждение также называют «предварительным отверждением в обогреваемой комнате». Этого можно добиться, установив излучающие трубы для косвенного нагрева. Необходимо следить за тем, чтобы зеленый пирог не подвергался вибрации во время предварительного отверждения, иначе на нем могут образоваться трещины.
В конце процесса предварительного отверждения зеленый пирог достаточно твердый, чтобы его можно было разрезать проволокой в соответствии с требованиями. Предварительное отверждение — несложный процесс, но за ним следует постоянно следить. Дефекты преформы (растрескивание, проседание и т. Д.) В основном возникают во время процесса.
Извлечение из формы и резка: В более раннем процессе суспензия может подняться и набрать прочность. Когда зеленый пирог достигнет прочности на разрез, его можно вынуть из формы и разрезать в соответствии с требованиями. Извлечение из формы и резка — очень важные процессы при производстве блоков AAC. Эти два процесса играют важную роль в определении количества брака, а также точности размеров конечного продукта.
Хотя все предыдущие процессы, такие как подготовка сырья, дозирование, смешивание и литье, практически одинаковы для всех технологий, процессы извлечения из формы и резки сильно различаются в зависимости от поставщика технологии.
Как только форма выходит из камеры предварительного отверждения, ее поднимают краном или катят по рельсам для операции извлечения из формы. В первую очередь процесс резки можно разделить на лепешки и лепешки на основе того, как зеленый пирог извлекается из формы и отправляется на линию резки. Наиболее часто используемой технологией является технология тентового пирога. Обычно в технологии тентового пирога используются две режущие машины. Горизонтальный отрезной станок используется на первом этапе, а вертикальный отрезной станок используется на втором этапе.
Хотя в большинстве случаев зеленый пирог отправляется в очередь автоклава после операции резки, в некоторых случаях он отправляется на наклонный стол.Наклоняемый стол используется для удаления верхнего и нижнего слоя корки на зеленой стадии. Эта корка может быть переработана, отправив ее в резервуар для переработки. При отсутствии наклонного стола корку, возможно, придется отделить на белой стадии, что может привести к повреждению конечного продукта из-за использования таких инструментов, как долота.
Автоклавирование: После резки блоки транспортируются в большой автоклав (большой сосуд высокого давления, обычно стальная труба), где процесс отверждения завершается. Автоклавирование необходимо для достижения желаемых структурных свойств и стабильности размеров.Во время этого процесса кварцевый песок реагирует с гидроксидом кальция с образованием гидрата силиката кальция, который придает AAC его высокую прочность и другие уникальные свойства. Процесс занимает от 8 до 12 часов при давлении около 174 фунтов на квадратный дюйм (12 бар) и температуре около 360 ° F (180 ° C), в зависимости от марки производимого материала.
После автоклавирования материал готов к немедленному использованию на строительной площадке. В зависимости от плотности до 80% объема блока AAC составляет воздух.Низкая плотность AAC также объясняет его низкую прочность конструкции на сжатие. Он может выдерживать нагрузки до 8 МПа (1160 фунтов на квадратный дюйм), что составляет примерно 50% прочности на сжатие обычного бетона.
АВТОМАТИЧЕСКАЯ ЛИНИЯ ПО ПРОИЗВОДСТВУ ПЕРИОДИЧЕСКИХ БЕТОННЫХ БЛОКОВ С ЗОЛЕНЫМ ЗАПОЛНИТЕЛЕМ. Производительность 50 м3 / смену
Технические характеристики линии
Емкость | 50 м 3 / смену (100 м 3 / сутки) |
Потребляемая мощность | 54 кВт / ч (без водяного отопления) |
Использование воды | ~ 13 тн / смену |
Утилизация цемента | ~ 12,5 тн / смену |
Утилизация летучей золы | ~ 10,5 тн / смену |
Производство | мелкие стеновые блоки по ГОСТ 21520-89 |
Требуемая площадь производственного помещения | 500-1000 м 2 |
Высота потолка в зоне смешивания | не менее 6 м * |
Высота потолка в производственной зоне | не менее 3 м * |
Температура окружающей среды | не ниже +15 o С |
Требуемый персонал | 6 рабочих, 1 начальник производства / прораб |
ПРЕИМУЩЕСТВА
Автоматизация управления процессами
На производственных линиях используются электронные системы для управления загрузкой и дозированием сырья в зоне смешивания.В системах управления предусмотрены функции регистрации и контроля сырья. Зона смешивания контролируется одним оператором. В зоне раскроя имеется отрезной станок, которым также управляет один оператор. Процесс демонтажа формы и укладки блоков автоматизирован.
Точность дозирования
Сырье подается на весы с тензодатчиками и весовым контроллером, который обеспечивает точное дозирование.
Высокая вместимость
Высокая производительность обеспечивается автоматизированной системой загрузки и дозирования сырья, а также высокой скоростью заполнения смесителя водой и сырьем.Высокопроизводительный отрезной станок обеспечивает высокую скорость резки монолита на блоки заданного размера.
Высокое качество
Система автоматизации процессов обеспечивает высокое качество продукции и гарантирует точность дозирования, а также стабильный и однородный состав, что позволяет нам выпускать качественную и конкурентоспособную продукцию.
СЫРЬЕ ДЛЯ ПРОИЗВОДСТВА ПЕТРОБЕТОНА
- Папка. Портландцемент ПЦ-500 Д0, ПЦ-400 Д20 ГОСТ 30515 и ГОСТ 10178 применяется как вяжущее для газобетонных изделий.
- Кремнеземный компонент. Зола уноса применяется для ТЭЦ с содержанием SiO2 не менее 45%, CaO не более 10%, R2O не более 3%, SO3 не более 3%.
- Вода для замешивания. Вода соответствует требованиям ГОСТ 23732.
- Смазка для форм. Смазки для форм SDF или другие антиадгезионные агенты используются для обеспечения эффективного удаления плесени.
- Армирующие средства. Полипропиленовые волокна диаметром 12 мм используются в качестве армирующего агента.
- Модификаторы. ГОСТ 24211
- Газообразующие агенты. Алюминиевый порошок или пыль на его основе используются в качестве газообразующего агента.
ОБЗОР ПРОЦЕССА
1. Производство газобетонной смеси
Смеситель заполнения водой
Для дозирования воды используется электронный водомер.Оператор зоны смешивания вводит необходимое количество воды и запускает цикл загрузки миксера.
Загрузка сырья в смеситель
Контроллер веса используется для загрузки сырья (цемент, летучая зола) в весы и реагентов в весы химических добавок. Цемент, летучая зола и примеси транспортируются шнековыми конвейерами. Цемент и летучая зола выгружаются из весов в смеситель. Раствор перемешивают 2–3 минуты до однородности.Когда раствор будет готов, в смеситель выгружают добавки и снова перемешивают газобетонную смесь в течение 1–2 минут.
Оператор контролирует все процессы в зоне смешивания в режиме реального времени. Оператор может использовать панель управления для корректировки или изменения рецепта, времени смешивания и других параметров процесса.
Оборудование поддерживает как ручной, так и автоматический режимы.
2. Монолитный багет
По готовности газобетонную смесь выгружают до 0.85 м 3 пресс-форма через смесительный клапан. Форма заполняется за один раз. Состоит из основы и съемных сменных бортов. Перед заполнением форма смазывается и транспортируется в зону смешивания для заполнения.
3. Отверждение монолита из пенобетона
Заполненная форма транспортируется по перилам в зону отверждения (в камеру термообработки), где монолит достигает своей прочности на отрыв. Заказчику рекомендуется устраивать герметичные туннельные камеры с полной теплоизоляцией по всем поверхностям.Температура в камере должна быть +30 … + 40 о С. Достижение прочности снятия изоляции может занять от 3 до 5 часов и зависит от плотности газобетона, активности, типа кремнезема, температуры и т. Д.
4. Демонтаж форм и вырезание массивов
После того, как массив наберет необходимую прочность, форма, содержащая массив, по железным дорогам переносится на демонтажную машину, основание формы фиксируется на пути. Затем четыре стенки формы снимаются и поднимаются захватом.После демонтажа формы основание формы и массив переносятся в секцию резки. Затем свободные стены накладываются на свободное основание, которое находится на прилегающей железной дороге. Форма в кожухе отправляется на участок разливки. Массив разрезают на блоки заданных размеров режущим агрегатом АРК-004. На участке резки находятся два отдельных последовательных модуля для вертикальной и горизонтальной резки массива.
Основание пресс-формы фиксируется захватом на вертикальном модуле, в то время как оператор запускает вертикальный модуль.Двигаясь по направляющим, модуль разрезает массив в вертикальной плоскости и обрезает его с обоих концов. После вертикальной резки опалубка с массивом переносится в зону горизонтального модуля, фиксируется захватом, после чего разрезается в горизонтальной плоскости на блоки заданных размеров, а также нижний слой и верх срезан. Пока горизонтальный модуль работает, следующий массив подается в зону вертикального модуля. Таким образом, одновременно производится резка двух массивов, что обеспечивает высокую пропускную способность линии.
5. Укладка блоков на поддоны, упаковка и хранение
Опалубка с вырезанным массивом переносится в блок штабелирования блоков. Основание пресс-формы закреплено на рельсе. Затем половину среза массива с помощью захвата укладывают на поддон. Для комплектации поддона вручную устанавливаются восемь блоков. Затем укладывается вторая половина массива, а также восемь блоков вручную (в зависимости от их размеров).Поддон с блоками обматывают стрейч-пленкой.
6. Блок термовлагообработки
В зависимости от климатической зоны и типа производимого материала блоки, уложенные на поддоны, могут набирать марочную прочность на складе готовой продукции или при термовлагообработке. Для ускорения набора прочности блоков необходима термовлагообработка блоков. При термовлагообработке блоки выдерживаются в камере от 8 до 12 часов при температуре от +40 до 60оС.Режим термовлагообработки также зависит от плотности материала, активности цемента и определяется заказчиком для каждого конкретного вида выпускаемой продукции.
7. Утилизация отходов резки
Режущие модули вырезают монолит с обоих концов, вверху и внизу. Инновационным решением является использование измельчителя отходов ДГ-1 для переработки отходов резки. Позволяет измельчать отходы газобетона до частиц размером до 0–30 мм.Грунт может быть использован как сыпучий утеплитель для крыш, чердаков, пола и т. Д. Измельчитель делает производство бетона практически безотходным.
ТЕХНИЧЕСКИЕ ХАРАКТЕРИСТИКИ ЛИНИЙ
N | Имя | Количество |
Участок хранения, подготовки и отгрузки сырья | ||
1 | Шнековый транспортер цемента (L = 6 м *, мотор-редуктор (Италия), N = 4 кВт) | 1 |
2 | Шнековый транспортер летучей золы (L = 6 м *, мотор-редуктор (Италия), N = 4 кВт) | 1 |
Зона смешивания | ||
1 | Электронная система управления (со встроенным водосчетчиком + подкачивающим насосом) | 1 |
2 | Весовой дозатор (тензодатчики, пневмоклапан, макс.600 кг) | 1 |
3 | Дозатор химических добавок ДХД-1 (N = 0,5 кВт) | 1 |
4 | Смеситель для газобетона ГБ-0.85 (N = 11 кВт, V = 0,85 м3 3 ) | 1 |
5 | Компрессор C200LB40 (500 л / мин, 8–10 атм.) | 1 |
Участок резки монолита | ||
1 | Автомат раскройный АРК-004 (Н-19.5 кВт) | 1 |
2 | ФМ-0,91 м 3 опалубка для монолита из газобетона (V = 0,91 м 3 ). | 55 |
3 | Транспортная тележка | 4 |
4 | Комплекс для демонтажа форм (N = 2,0 кВт) | 1 |
5 | Комплекс для укладки блоков на поддоны (N = 2.5 кВт) | 1 |
Зона измельчения стружки | ||
1 | Измельчитель ДГ-1 (N = 4,5 кВт) | 1 |
РАСХОД МАТЕРИАЛА * НА 1 м
3 ИЗ НЕАУТОКЛАВИРОВАННОГО ПЕРИОДИЧЕСКОГО БЕТОНА D-600Материал | Количество |
Цемент (ПЦ500 Д0), кг | 250 |
Летучая зола, кг | 210 |
Вода, л | 250 |
Газообразующий агент, кг | 0,5-1,5 |
Клетчатка, кг | 0,6 |
Химические добавки, кг | ** |
* Рецепты корректируются с учетом свойств сырья, выбранного заказчиком.
** Тип и количество добавок определяется на этапе проектирования бетона.
ОБЩАЯ ИНФОРМАЦИЯ
Для снижения затрат заказчика линия поставляется без силоса для цемента, бункера для песка и перил для транспортировки форм. Заказчику предоставляются чертежи раздельного изготовления этих узлов.
Кроме того, заказчик несет ответственность за подогрев воды до +35 … + 40 ° C и устройство камер пропаривания.Для работы линии в 2 смены необходимы дополнительные опалубки.
Гарантийный срок на поставляемое оборудование — 12 месяцев. Компоненты каждой единицы оборудования указаны в контракте, паспорте оборудования и акте приема-передачи.
Специалисты ООО «Сибирские строительные технологии» (СКТ) разрабатывают компоновку оборудования на производственном объекте заказчика. Установка оборудования согласно схеме осуществляется заказчиком и за его счет.Заказчику предоставляется схема (чертежи) оборудования соответствующих помещений и подробная иллюстрированная инструкция по установке.
После того, как заказчик завершит установку и подключение оборудования, SCT выполняет следующие работы:
• пуско-наладка оборудования;• конструкция из газобетона;
• оптимизация технологии производства;
• обучение персонала заказчика.
Заказчик несет ответственность за соблюдение всех правил техники безопасности, требований по охране труда и окружающей среды, а также других местных нормативных актов.
Все расходы по транспортировке и размещению персонала SCT на период проведения работ берет на себя заказчик. Оптимизация технологии включает оптимизацию состава бетона в зависимости от сырья, предоставленного заказчиком. SCT предоставляет услуги поддержки.
После ввода оборудования в эксплуатацию заказчику предоставляется техническая документация, в том числе:
• технический регламент на производства;• Диаграмма процесса;
• описание вакансии;
• правила техники безопасности;
• ГОСТы.
УСЛОВИЯ ПОСТАВКИ
Стоимость указана для EXW-Новосибирск (Россия) и не включает стоимость растаможки и отгрузки. Срок изготовления оборудования: от 30 рабочих дней с момента получения предоплаты.УСЛОВИЯ ОПЛАТЫ
Оплата 1—70% от стоимости контракта в течение 5 дней с момента подписания контракта.
Оплата 2–30% от стоимости контракта в течение 5 дней с момента получения подтверждения о готовности оборудования к отгрузке.
Процесс производства газобетона
Автоклавный газобетон
Автоклавный газобетон. В настоящее время нет торговой ассоциации, представляющей промышленность по производству автоклавного газобетона. Производство AAC все еще существует в Северной Америке. Мы предлагаем вам поискать в Интернете представителей дилеров, которые могут помочь вам с потенциальной доступностью продукта в вашем регионе.
Подробнее +Автоклавный газобетон (AAC) Производство
07.06.2016 · Процесс производства изделий из автоклавного ячеистого бетона (AAC) на заводе Aircrete Mexico, крупнейшем заводе AAC в Латинской Америке. Aircrete Europe de
Подробнее +Газобетон в автоклаве, AAC, Aircrete
Процесс производства газобетона в автоклаве несколько отличается на разных производственных предприятиях, но принципы схожи. Предположим, что смесь содержит цемент, известь и песок; они смешиваются, образуя суспензию. Также в растворе присутствует
Подробнее +Аэрированные композитные материалы, способы по
Изобретение предлагает новые аэрированные композитные материалы, которые обладают превосходными физическими и эксплуатационными характеристиками пористого бетона, а также способы их производства и применения.Эти композитные материалы могут быть легко произведены из широко доступного недорогого сырья с помощью процесса, подходящего для крупномасштабного производства с улучшенным энергопотреблением, желаемым углеродным следом и
Подробнее +производство бетонных изделий
Производство бетона — это процесс смешивания различных ингредиентов — воды, заполнителя, цемента и любых добавок — для производства бетона. Производство бетона зависит от времени. После того, как ингредиенты смешаны, рабочие должны положить бетон на место до того, как он затвердеет.
Подробнее +Аэрированные композитные материалы, способы
Изобретение обеспечивает новые пористые композитные материалы, которые обладают превосходными физическими и эксплуатационными характеристиками пористого бетона, а также способы их производства и применения. Эти композитные материалы могут быть легко произведены из широко доступного недорогого сырья с помощью процесса, подходящего для крупномасштабного производства с улучшенным энергопотреблением, желаемым углеродным следом и
Подробнее Машина для производства бетонных блоков для сравнения цен на строительные материалы, получите Китайскую машину для производства газобетонных блоков в автоклаве для сравнения цен на строительные материалы от машин для производства блоков, производителей и поставщиков машин для производства кирпича на видеоканале Made-in-China. Подробнее +Производство бетона — обзор | ScienceDirect
Производство бетона — это высокоинтенсивный энергоемкий процесс, который в настоящее время сталкивается с рядом проблем, направленных на сокращение углеродного следа и повышение его экономичности. Экологичные технологии в обслуживании бетонных конструкций становятся серьезной проблемой. Микробиологически индуцированное карбонатное осаждение (MICP) было разработано как новый и устойчивый метод улучшения
Подробнее +AAC Production process_production
В соответствии с различными основными материалами, мы можем спроектировать производственную линию, которая способна производить ежегодно От 100 000 до 400 000 м3 угольной золы или газобетонных блоков из автоклавного песка.Ниже представлен процесс производства линии по производству блоков из автоклавного газобетона. Линия по производству газоблоков, процесс 1 、 Хранение сырья
Подробнее +Производство газобетона в автоклаве
Производство газобетона в автоклаве Masa Group. 2020-4-5 · Производство газобетона в автоклаве требует высоких стандартов для смешивания и дозирования заполнителей, контроля процесса ферментации и контроля каждого этапа производства.
Подробнее +Блоки из пенобетона в автоклаве (блоки AAC)
В автоклаве Пенобетон выдерживают в автоклаве — большом сосуде под давлением. Автоклав обычно представляет собой стальную трубу диаметром 3 м и длиной 45 м. Пар подается в автоклав под высоким давлением, обычно достигающим давления от 800 кПа до 1200 кПа и температуры 180 ° C. Рис. 3:
Подробнее +Введение — Aercon AAC Autoclaved Aerated
AERCON — это экологически чистый продукт, изготовленный из песка, извести, цемента, воды и поднимающих веществ. При этом не образуются загрязняющие вещества или опасные отходы. производитель сборных изделий из автоклавного газобетона.
Подробнее +Производство бетонных блоков | Masa Group
Производство изделий из газобетона в автоклаве требует высоких стандартов для смешивания и дозирования заполнителей, контроля процесса ферментации и контроля каждого этапа производства. Установки газобетона Masa — это проверенные передовые технологические процессы, разработанные в соответствии с конкретными требованиями клиентов.
Подробнее +Процесс производства газобетона.
Процесс производства газобетона. Производство газобетона, измельчение материалов в шаровой мельнице. — Загрузите из более чем 148 миллионов высококачественных стоковых фотографий, изображений, векторов и стоковых видео. Зарегистрируйтесь сегодня бесплатно. Видео: 193729791
Подробнее +AAC Production process_production
Линия по производству газированных блоков Процесс 1 、 Хранение сырья Летучая зола или песок, цемент, известь, гипс, алюминиевая паста должны храниться отдельно на складе материалов, транспортировать их в мастерскую при их использовании.2 、 Процесс обращения с сырьем Поместите летучую золу или песок в шаровую мельницу для измельчения через конвейерную ленту, после измельчения поместите суспензию в резервуар для хранения суспензии на
Подробнее +Bulkbuy Автоклавный газобетонный блок
Bulkbuy Машина для производства газобетонных блоков в автоклаве для сравнения цен на строительные материалы, получите Китайскую машину для производства газобетонных блоков в автоклаве для сравнения цен на строительные материалы от Машины для производства блоков, производители и поставщики машин для производства кирпича на видеоканале Made-in-China.
Подробнее +Установка для производства блоков AAC — автоклавирование
Газобетон затвердевает под давлением пара в специальных герметичных резервуарах под давлением, автоклавах, таким образом достигается его окончательная прочность. Давление пара составляет ок. 12 бар, температура ок. 192 ° C. Обычно время отверждения составляет от 10 до 12 часов.
Подробнее +Газобетон. Особенности материала
Технология производства пенобетона Ячеистая структура составляет почти 85% всего объема блока, поэтому этот материал отличается очень легким весом.Все компоненты (кварцевый песок, цемент, известь) закрываются обычной водой и перемешиваются в специальном миксере в течение 5 минут.
Подробнее +Бетон — Газобетон в автоклаве
Процесс производства газобетона в автоклаве немного отличается на отдельных производственных предприятиях, но принципы схожи. Существуют различия в материалах, используемых для создания исходной суспензии, и в условиях, при которых контролируется часть процесса «зеленый пирог».
Подробнее +Автоклавный газобетон
Автоклавный газобетон. В настоящее время нет торговой ассоциации, представляющей промышленность по производству автоклавного газобетона. Производство AAC все еще существует в Северной Америке. Мы предлагаем вам поискать в Интернете представителей дилеров, которые могут помочь вам с потенциальной доступностью продукта в вашем регионе.
Подробнее +AAC — Производитель завода по производству автоклавного газобетона из Ахмедабада
Метод | Автоклав с газом | |||||
Уровень автоматизации | Автоматический | |||||
Производительность | 50000-300000 м3 / год | |||||
Марка | Laxmi 9030 | Напряжение -440 В | ||||
Расход воды | 300 л / м3 |
Система дозирования: Разливочная и перемешивающая машина является основным оборудованием в цехе дозирования разливочного покрытия производственной линией AAC.После дозирования различные виды сырья и воды будут залиты в цилиндр этой разливочно-смесительной машины, а затем все они будут смешаны вместе в ожидаемую суспензию, которая будет подходящей для последующей заливки. После открытия разгрузочного дроссельного клапана суспензия будет вылита в форму для предварительного отверждения.
Опрокидывающийся кран: Опрокидывающийся кран поворачивает блок (с формой и боковой пластиной) на 90 градусов в воздухе, затем подвешивается на платформе для резки или тележке для резки, для извлечения из формы и резки.Кроме того, групповые формы после извлечения из формы и боковые пластины возвращаются обратно. После группировки они подвешиваются к возвратной линии разливки для выполнения цикла разливки.
Группирующий кран: После резки, подъемный кран для полуфабрикатов вручную блокирует машину паровой полимеризации и группирует перед тем, как поместить ее в автоклав. Это устройство имеет простую конструкцию, удобное управление, хорошее качество и простоту обслуживания. Сгруппируйте перегрузочный пирог крана, паровую тележку, боковую пластину в нужное положение без повреждения пирога.
Коробка для пресс-формы: Пресс-форма является ключевым оборудованием, включенным в производственную линию AAC. Когда суспензия выливается в форму, она будет подвергнута предварительному отверждению с возникновением пены, после чего будет доступен «пирог», готовый для последующей резки.
Боковая пластина: Боковая пластина — это инструмент, который сочетается с формовочной коробкой для процесса заливки и предварительного отверждения. А еще несем торт для готовой нарезки и отправляем в автоклав. Мы также можем сказать, что боковая пластина используется для переноски блока AAC для резки стека и пара.
Тележка для пара: Тележка для пара — это инструмент, с помощью которого можно вынимать из автоклава боковые пластины пресс-формы, а также корпус блока. Паровая тележка выдерживает высокие температуры и давление, поэтому требуются высокотемпературные подшипники, а также тяжелая конструкция.
Станок для резки: Станок для резки является ключевым оборудованием производственной линии AAC, принцип работы заключается в том, что подвеска для плитки поворачивает форму на 90 градусов в воздухе, открывает форму и устанавливает блок на тележку для резки вместе с боковая пластина.Режущая машина приводилась в движение двигателем. Блок будет приводиться в движение для горизонтальной и вертикальной резки. Тележка для резки перемещается к подъемнику для полуфабрикатов, а подъемник загружает обрезанный блок в тележку перед автоклавом для группирования. Тележка для резки вернется для новой круглой резки.
Автоклав: Автоклав AAC — это разновидность крупномасштабного парового оборудования. Автоклав — это одно из большинства устройств для процесса AAC, которое может влиять на прочность и полноту продуктов путем отверждения паром и под высоким давлением.Автоклав AAC — это сосуд под давлением и ключевое оборудование в производстве пенобетона и автоклавного кирпича. Он применим для отверждения разрезанного тела или кирпича при высокой температуре и высоком давлении. Рабочая среда — насыщенный водяной пар.
Основные части сделаны автоклавного корпус, крышка с ручным приводом редуктор, Безопасный запорное устройство, поддержка седлом, и клапан Meter и т.д. Корпус представляет собой принцип и цилиндрическое устройство, изготовленное из стали. Мы производим широкий ассортимент автоклавов, которые предпочитают из-за их высокой прочности на разрыв и лучшего срока службы.Изготовленные с помощью передовых технологий, эти устройства проходят тщательную проверку качества для обеспечения лучших результатов.
Яма для приготовления навозной жижи: Это резервуар для суспензии летучей золы, в котором мы храним суспензию летучей золы с низкой скоростью вращения, поэтому она может препятствовать выпадению навозной жижи.
Дополнительная информация:
- Условия режима оплаты: T / T (банковский перевод)
- Производственная мощность: 30 — 1000 кубических метров
- Срок поставки: 3 месяца
Оценка жизненного цикла автоклавированной газированной золы и бетонного блока производство: пример из Китая
Бенетто Э., Руссо П., Блонден Дж. (2004) Оценка жизненного цикла побочных продуктов угля на основе сценариев производства электроэнергии.Топливо 83 (7-8): 957–970
Артикул CAS Google ученый
Бланкендаал Т., Шур П., Вурдейк Х. (2014) Снижение воздействия бетона и асфальта на окружающую среду: сценарный подход. J Clean Prod 66: 27–36
Статья Google ученый
CABEE (Китайская ассоциация энергоэффективности зданий) (2018) Отчет об исследовании потребления энергии в зданиях в Китае в 2017 году.http://www.cabee.org/site/content/22542.html. По состоянию на 1 августа 2018 г.
CACA (Китайская ассоциация по производству пенобетона) (2016 г.) Руководство по развитию промышленности по производству пенобетона (2016–2020 гг.). http://www.cacajq.cn/info_main/20161213/586.html. По состоянию на 20 мая 2018 г.
CCPA (Китайская ассоциация по производству бетона и цементных изделий) (2017) Отчет о развитии летучей золы в 2016 г. http://www.ccement.com/news/content/9301050184546.html. По состоянию на 20 мая 2018 г.
CSC (Государственный совет Китая) (2016) Комплексный рабочий план по энергосбережению и сокращению выбросов в 13-м пятилетнем плане.http://www.ndrc.gov.cn/zcfb/zcfbqt/201701/t20170105_834500.html. По состоянию на 20 мая 2018 г.
Deng NS, Wang XB (2003) Оценка жизненного цикла. Химическая промышленность Press, Пекин
Google ученый
EPA (Агентство по охране окружающей среды США) (2016) Реестр выбросов и стоков парниковых газов в США: 1990–2014 гг. https://www.epa.gov/ghgemissions/inventory-us-greenhouse-gas-emissions-and-sinks. По состоянию на 3 июня 2018 г.
Fang M (2013) Оценка жизненного цикла типичных стеновых материалов.Пекинский технологический университет (оригинальное название на китайском языке)
Flower D, Sanjayan G (2007) Выбросы парниковых газов при производстве бетона. Int J Life Cycle Ass 12 (5): 282–288
Статья CAS Google ученый
Гао Ю. (2010) Оценка жизненного цикла системы водной среды в кольцевом промышленном парке. Сианьский университет архитектуры и технологий (оригинальное название на китайском языке)
GAQSIQ (Главное управление контроля качества, инспекции и карантина), SAC (Управление стандартизации Китая) (2006) Стандарт для блоков из пенобетона в автоклаве.Стандарты Пресс Китая, Пекин
Google ученый
Habert G, Roussel N (2009) Исследование двух стратегий разработки бетонных смесей для достижения целей по снижению выбросов углерода. Цементный бетон Res 31 (6): 397–402
Артикул CAS Google ученый
Хаммонд Дж., Джонс С. (2008) Инвентаризация углерода и энергии: группа исследователей устойчивой энергетики. Кафедра машиностроения в Университете Бата
Хуанг Й, Чиу Т., Ло Л. (2016) Влияние повторного использования летучей золы на окружающую среду и стоимость жизненного цикла.Resour Conserv Recy 123: 255–260
Статья Google ученый
IPCC (Межправительственная группа экспертов по изменению климата Изменение климата) (1995) Наука об изменении климата: резюме для политиков и техническое резюме доклада Рабочей группы I. Женева
ISO (Международная организация по стандартизации) (2006a) Экологический менеджмент — оценка жизненного цикла — принципы и рамки (ISO 14040-2006). Международная организация по стандартизации, Женева
Google ученый
ISO (Международная организация по стандартизации) (2006b) Экологический менеджмент — оценка жизненного цикла — требования и руководящие принципы (ISO 14044-2006).Международная организация по стандартизации, Женева
Google ученый
Jr SH, Maranduba HL, Ja DAN, Rodrigues LB (2016) Оценка жизненного цикла процесса производства сыра в небольшой молочной промышленности в Бразилии. Environ Sci Pollut Res 24 (4): 3470–3482
Google ученый
Kamble SJ, Chakravarthy Y, Singh A, Chubilleau C, Starkl M, Bawa I. (2017) Система почвенной биотехнологии для очистки сточных вод: технические, гигиенические, экологические LCA и экономические аспекты.Environ Sci Pollut Res 24 (15): 1–20
Статья CAS Google ученый
Lamnatou C, Ezcurra-Ciaurriz X, Chemisana D, Plà-Aragonés LM (2016) Экологическая оценка системы свиноводства на северо-востоке Испании с упором на питание свиней на протяжении всего жизненного цикла. J Clean Prod 137: 105–115
Статья Google ученый
Liu Z, Wu D, Yu H (2018) Полевые измерения и численное моделирование комбинированных режимов работы солнечного отопления для жилых зданий на примере Цинхай-Тибетского плато.Energ Buildings 167: 312–321
Статья Google ученый
Mehta K (2001) Снижение воздействия бетона на окружающую среду. Concr Int 23: 61–66
Google ученый
MOHURD (Министерство жилищного строительства и городского и сельского развития) (2015) Национальный план по энергосбережению в зданиях и развитию зеленого строительства на период 13-й пятилетки (2016–2020). http: // www.mohurd.gov.cn/wjfb/201703/t20170314_230978.html. По состоянию на 20 мая 2018 г.
MOHURD (Министерство жилищного строительства и городского и сельского развития) (2018) Статистический анализ развития строительной отрасли в 2017 г. http://www.mohurd.gov.cn/xytj/tjzljsxytjgb/xjxxqt /. По состоянию на 20 мая 2018 г.
NBS (Национальное бюро статистики) (2017) Статистический ежегодник индустрии строительных материалов Китая. Статистическая пресса Китая.
NDRC (Национальная комиссия по развитию и реформам) (2015) Руководство по внедрению стороннего контроля за загрязнением окружающей среды на угольных электростанциях.http://www.ndrc.gov.cn/zcfb/zcfbtz/201601/t20160121_771945.html. По состоянию на 3 июня 2018 г.
O’Brien KR, Menache J, Moore O (2009) Влияние содержания летучей золы и расстояния транспортировки летучей золы на воплощенные выбросы парниковых газов и потребление воды в бетоне. Int J Life Cycle Ass 14 (7): 621–629
Статья CAS Google ученый
Oss HG, Padovani AC (2003) Производство цемента и окружающая среда, часть II: экологические проблемы и возможности.J Ind Ecol 7: 93–126
Статья Google ученый
Озкан Э., Эльгиноз Н., Гермирли Б.Ф. (2017) Оценка жизненного цикла завода по производству печатных плат в Турции. Environ Sci Pollut Res 3: 1–8
Google ученый
Proske T, Hainer S, Rezvani M, Graubner CA (2013) Экологичные бетоны с пониженным содержанием воды и цемента — принципы расчета смеси и лабораторные испытания.Cem Concr Res 51: 38–46
Статья CAS Google ученый
Пурнелл П., Блэк Л. (2012) Внедрение двуокиси углерода в бетоне: изменение общих проектных параметров смеси. Cem Concr Res 42 (6): 874–877
Статья CAS Google ученый
Refiner M, Rens K (2006) Зольный бетон с большим объемом: анализ и применение. Практический период Struct Des Constr 11 (1): 58–64
Статья Google ученый
Ren C, Wang W, Li G (2017a) Получение высокоэффективных вяжущих материалов из твердых промышленных отходов.Constr Bulid Mater 152: 39–47
Статья CAS Google ученый
Ren C, Wang W, Mao Y, Yuan X, Song Z, Sun J (2017b) Сравнительная оценка жизненного цикла производства сульфоалюминатного клинкера, полученного из твердых промышленных отходов и обычного сырья. J Clean Prod 167: 1314–1324
Статья CAS Google ученый
Sjunnesson J (2005) Оценка жизненного цикла бетона.Lund University
Tang Y, Li Y, Wang Q, Yuan X, Zuo J (2018) Оценка экологических и экономических последствий процесса производства предварительно обожженных анодов: тематическое исследование в провинции Шаньдун, Китай. J Clean Prod 196: 1657–1668
Статья Google ученый
Тейшейра Э.Р., Матеус Р., Камоэс А.Ф., Браганса Л., Бранко Ф.Г. (2016) Сравнительный экологический анализ жизненного цикла бетонов с использованием биомассы и угольной летучей золы в качестве материала для частичной замены цемента.J Clean Prod 112: 2221–2230
Артикул CAS Google ученый
Toniolo S, Mazzi A, Pieretto C, Scipioni A (2016) Стратегии распределения при сравнительной оценке жизненного цикла для переработки: соображения из тематических исследований. Resour Conserv Recyl 117: 249–261
Статья Google ученый
Ван Ц., Дин Дж. (2007) Исследование по оценке жизненного цикла бетона из летучей золы.Ind Safe Environ Prot 33 (1): 39–42 (исходное название на китайском языке)
CAS Google ученый
Wang T, Wang J, Wu P, Wang J, He Q, Wang X (2018a) Оценка экологических издержек и выгод от отходов сноса с использованием оценки жизненного цикла и готовности платить: тематическое исследование в Шэньчжэне. J Clean Prod 172: 14–26
Статья Google ученый
Wang Q, Liu W, Yuan X, Tang H, Tang Y, Wang M (2018b) Анализ воздействия на окружающую среду и оптимизация процесса аккумуляторных батарей на основе оценки жизненного цикла.J Clean Prod 174: 1262–1273
Артикул CAS Google ученый
Уоррелл Э., Прайс Л., Мартин Н., Хендрикс С., Мейда ЛО (2001) Выбросы двуокиси углерода от мировой цементной промышленности. Annu Rev Energy Environ 26: 303–329
Статья Google ученый
Ядав П., Самаддер С.Р. (2017) Глобальная перспектива распределения доходов и его влияние на оценку жизненного цикла управления твердыми бытовыми отходами: обзор.Environ Sci Pollut Res 24 (10): 9123–9141
Статья Google ученый
Yu H, Wang Q, Zhang H (2011) Модель расчета выбросов углерода предварительно смешанного бетона на основе жизненного цикла. Летучая зола 23 (6): 42–46 (исходное название на китайском языке)
Google ученый
Yuan X, Tang Y, Li Y, Wang Q, Zuo J, Song Z (2018) Оценка экологического и экономического воздействия процесса производства бетонного тротуарного кирпича и водопроницаемого кирпича — тематическое исследование в Китае.J Clean Prod 171: 198–208
Статья Google ученый
дробилка оборудования добычи гранита, каменная дробилка Индия
известняка1988 Год основания 1988
69+ Патенты и сертификаты
400+ Количество сотрудников
13350+ Обслуживаем клиентов
Звездные продукты
Системы дробильно-сортировочной установкипродуманы до мельчайших деталей, и весь процесс всегда находится в руднике.
Онлайн чатПолные квалификационные аттестаты
C&M Mining Machinery — это частная китайская компания, занимающаяся проектированием, производством и поставкой мобильных решений для дробления и сортировки по всему миру для строительной, горнодобывающей, карьерной и перерабатывающей промышленности.
Передовые производственные технологии и оборудование
C&M Mining Machinery владеет более чем 50 запатентованным оборудованием собственной разработки, обеспечивающим оцифровку вырубки, автоматизацию сварки и сборочного формования, а также строгий контроль качества продукции на протяжении всего процесса.
Котельная по индивидуальному заказу
C&M Mining Machinery имеет сильную команду разработчиков котлов и построила полную систему исследований и разработок.
Комплексное и профессиональное послепродажное обслуживание
C&M Mining Machinery имеет профессиональные группы послепродажного обслуживания, которые предоставляют техническое руководство для всего процесса установки и бесплатное обучение для эксплуатационного и обслуживающего персонала..
Добро пожаловать в компанию
C&M Mining Machinery — высокотехнологичная инженерная группа. Мы специализируемся на исследованиях, разработке и производстве оборудования для промышленного дробления, измельчения порошков, обогащения полезных ископаемых и других сопутствующих устройств.
Узнать больше[randpic] бизнес-план по эксплуатации гранитного карьераПлан по добыче гранита в индии каменная дробилка для продажи.Сейчас в чате http // производитель печей для обжига извести leawaysschool com / solution html Свяжитесь с нами h
Читать дальше [randpic] Двухвалковая дробилка — JXSC Machine20-02-2019 · Двухвалковая дробилка предназначена для мелкого дробления горных пород средней твердости с прочностью на сжатие ≤160 МПа, таких как руда, порода, кокс
Читать дальше [randpic] конусная дробилка для russiasale конусная дробилка в европе россия thegurukulinstitute…. 4 октября 2017 г. В отчете о рынке конусных дробилок содержится подробное исследование … 2017 · 2016 Мобильная дробилка Fo
Читать дальше [randpic] станок для измельчения известнякового порошка Нигерия Станок для измельчения порошка известняка Нигерия Станок для измельчения известнякового порошка Нигерия — Станок для измельчения известнякового порошка Нигерия, Kern River Parkway Ind
Читать дальше .