Арболит плюсы и минусы. Недостатки арболитовых блоков
Арболит плюсы и минусы.
Наше время характеризуется не только обилием технологий строительства, но и большим выбором материалов, которые можно использовать для сооружения домов для постоянного проживания. Несколько десятилетий назад частным застройщикам приходилось делать выбор из двух материалов. Они выбирали между кирпичом и деревом. В зависимости от своих финансовых возможностей они приобретали наиболее подходящий материал.
В условиях существующей действительности выбор невероятно огромный. Помимо дерева застройщики могут выбирать пеноблок или делать выбор в пользу газобетона. Помимо этого строить дома можно и из материалов на основе керамзита.
В последнее время популярность стал приобретать такой материал, как арболит. Плюсы и минусы этого материала мы и рассмотрим.
Арболит составПлюсы арболита.
Итак, арболит, он же опилкобетон (щепобетон) или деревобетон. Блоки из него стоят недорого и при этом обладают большим набором эксплуатационных характеристик.
Свойства этого материала во многом и обусловили ситуацию, когда многие застройщики отдают предпочтение именно в его пользу. Построив дом из этого материала, можно получить надежное строение, которое не окажет никакого влияния на здоровье и при этом обойдется недорого. Многим не нравится серый вид таких строений. Однако данная проблема легко решается, если выполнить отделочные работы фасадных стен с использованием современных материалов, которые в широком ассортименте предлагаются в строительных магазинах.
Арболит фактурныйНеобходимо понимать, что ни один из строительных материалов, предлагаемых в настоящий момент, не лишён недостатков. Хотя у блоков из арболита имеется немало плюсов, тем не менее, этот уникальный материал имеет и недостатки.
Минусы арболита. Недостатки материала.
Одним из главных его минусов является то, что влагу он не переносит. Поэтому при возведении сооружения стены помещений, в которых будет присутствовать высокая влажность, необходимо делать из другого более влагостойкого материала, но не арболита.
Всё дело в том, что этот материал изготавливается из древесной щепы, а всем известно о том, что дерево влагу плохо переносит. Поэтому и стоит отказаться от идеи в помещениях с высокой влажностью применять данный материал. Если же вы пренебрежете данной рекомендацией и, например, в ванной комнате сделаете стены из этого материала, то вы столкнетесь с определенными проблемами. Материал впитает в себя влагу, и в конечном итоге это приведет к тому, что его эксплуатационные характеристики заметно снизятся. В результате срок службы строения заметно сократится.
Однако отметим, что есть возможность устранить данный недостаток. Для этого можно выполнить отделку стен из арболитовых блоков с использованием современного отделочного материала. Отличным вариантом будет использование штукатурки.
Еще один минус, о котором следует знать, состоит в том, что блоки арболита имеют слабую стойкость к воздействию газов с агрессивной средой.
Помимо этого, у данного строительного материала имеются и другие минусы. Цоколь дома, который построен из арболитовых блоков, необходимо отделывать дополнительно. Главная цель этой работы заключается в том, что необходимо добиться максимальной сухости. В этом случае вы сможете обеспечить длительный срок службы строения.
Следует не забывать о том, что на 90% из дерева состоят блоки арболита. По этой причине регулярно необходимо следить за состоянием цоколя. В зимнее время необходимо регулярно его осматривать и обеспечить эффективный отвод воды, а также следить за тем, чтобы у цоколя не было снега.
Еще одним недостатком материала является то, что идеальной геометрии такие блоки не имеют. Однако заметим, что на скорость строительных работ этот недостаток никакого влияния не оказывает. Но все же необходимо при выполнении кладок сделать выбор в пользу раствора на основе цемента и песка. В этом случае неровности, которые имеют используемые в ходе строительства блоки, будут нивелироваться за счёт раствора.
Дом из арболита. Минусы арболита. Реальный видео отзыв.
Арболит плюсы и минусы. Недостатки арболитовых блоков
В условиях существующей действительности выбор невероятно огромный. Помимо дерева застройщики могут выбирать пеноблок или делать выбор в пользу газобетона. Помимо этого строить дома можно и из материалов на основе керамзита.
В последнее время популярность стал приобретать такой материал, как арболит. Плюсы и минусы этого материала мы и рассмотрим.
Арболит состав
Плюсы арболита.
Итак, арболит, он же опилкобетон (щепобетон) или деревобетон. Блоки из него стоят недорого и при этом обладают большим набором эксплуатационных характеристик. Многие люди, которые хотят построить экологичный дом, делают выбор именно в пользу этого материала. Несмотря на то, что блоки арболита по большей части состоят из древесной щепы, тем не менее, они радуют своей надежностью и прочностью.
Арболит фактурный
Свойства этого материала во многом и обусловили ситуацию, когда многие застройщики отдают предпочтение именно в его пользу. Построив дом из этого материала, можно получить надежное строение, которое не окажет никакого влияния на здоровье и при этом обойдется недорого. Многим не нравится серый вид таких строений. Однако данная проблема легко решается, если выполнить отделочные работы фасадных стен с использованием современных материалов, которые в широком ассортименте предлагаются в строительных магазинах.
Арболит фактурный
Необходимо понимать, что ни один из строительных материалов, предлагаемых в настоящий момент, не лишён недостатков. Хотя у блоков из арболита имеется немало плюсов, тем не менее, этот уникальный материал имеет и недостатки. Если вы всерьез рассматриваете арболит в качестве материала для сооружения своего нового жилища, то, конечно же, вам стоит узнать о главных недостатках этого материала.
Минусы арболита. Недостатки материала.
Одним из главных его минусов является то, что влагу он не переносит. Поэтому при возведении сооружения стены помещений, в которых будет присутствовать высокая влажность, необходимо делать из другого более влагостойкого материала, но не арболита.
Всё дело в том, что этот материал изготавливается из древесной щепы, а всем известно о том, что дерево влагу плохо переносит. Поэтому и стоит отказаться от идеи в помещениях с высокой влажностью применять данный материал. Если же вы пренебрежете данной рекомендацией и, например, в ванной комнате сделаете стены из этого материала, то вы столкнетесь с определенными проблемами. Материал впитает в себя влагу, и в конечном итоге это приведет к тому, что его эксплуатационные характеристики заметно снизятся. В результате срок службы строения заметно сократится.
Однако отметим, что есть возможность устранить данный недостаток. Для этого можно выполнить отделку стен из арболитовых блоков с использованием современного отделочного материала. Отличным вариантом будет использование штукатурки.
Еще один минус, о котором следует знать, состоит в том, что блоки арболита имеют слабую стойкость к воздействию газов с агрессивной средой.
Помимо этого, у данного строительного материала имеются и другие минусы. Цоколь дома, который построен из арболитовых блоков, необходимо отделывать дополнительно. Главная цель этой работы заключается в том, что необходимо добиться максимальной сухости. В этом случае вы сможете обеспечить длительный срок службы строения.
Следует не забывать о том, что на 90% из дерева состоят блоки арболита. По этой причине регулярно необходимо следить за состоянием цоколя. В зимнее время необходимо регулярно его осматривать и обеспечить эффективный отвод воды, а также следить за тем, чтобы у цоколя не было снега.
Еще одним недостатком материала является то, что идеальной геометрии такие блоки не имеют. Однако заметим, что на скорость строительных работ этот недостаток никакого влияния не оказывает. Но все же необходимо при выполнении кладок сделать выбор в пользу раствора на основе цемента и песка. В этом случае неровности, которые имеют используемые в ходе строительства блоки, будут нивелироваться за счёт раствора.
Как появился арболит на нашем рынке?
В середине 50-х годов прошлого века в США начались активные разработки нового строительного материала из-за резкого снижения доходов граждан и уменьшения спроса на дорогостоящую недвижимость. Главными требованиями к нему были – невысокая цена, прочность и хорошие теплоизолирующие качества. За основу американские разработчики взяли зарубежные образцы, созданные по технологии DURISOL, внедренные в Голландии в 30-х годах. В результате кропотливой работы инженеров, строителей и архитекторов появился арболит. Этот строительный материал был произведен из цементно-древесной композиции и на то время в США получил название «woodstone». Он очень быстро зарекомендовал себя с положительной стороны, а потому правительство начало его производство в промышленных масштабах.
Приход арболита на постсоветское пространство
Новинку строительного рынка быстро заприметило руководство СССР. Уже в первой половине 60-х годов ВНИИдрев, МЛТИ, НИИЖБ, Гипролеспром тщательно изучили состав арболита, после чего начали подгонять его под климатические условия страны. Но специалисты были несколько ограничены в своих действиях из-за небольшого ассортимента строительных материалов. Все, что им было доступно – цемент с максимальной маркой прочности М400 и минерализатор в виде технического сернокислого алюминия, который использовался для удаления сахаров из щепы с целью улучшения ее связывающих качеств. Правда, недостатка в щепе не было.
Спустя несколько лет специалисты предоставили общественности щепобетон (такое название носил арболит в советские годы). Он производился в виде несущих и ограждающих конструкций, одно- и трехслойных стеновых панелей, блоков, плит перекрытий, конструкций, комбинированных с железобетоном. Материалы прошли все необходимые испытания, а также процедуру сертификации и стандартизации по ГОСТу. После этого академику Исааку Хисковичу Наназашвили было поручено ведение строительства заводов по изготовлению панелей из щепобетона по всей территории СССР. Под его бдительным руководством было возведено более 100 подобных промышленных объектов. На каждом из них был оборудован специальный навес для сушки щепы на открытом воздухе. Согласно утверждениям специалистов, только при таком подходе можно максимально снизить количество сахаров и получить материал оптимальной влажности.
С введением в эксплуатацию заводов по производству панелей из щепобетона в СССР началось строительство из арболита. Такие дома 1979 года постройки можно до сих пор увидеть в эксплуатации в Московской области. Но самым большим достижением для Советского Союза было возведение зданий в Антарктике. Еще в 60-е годы здесь были построены столовая и три здания служебного назначения. При толщине стен всего 32 см эти сооружения показали хорошие эксплуатационные качества в условиях сурового арктического климата. С этого момента цементно-древесная композиция стала еще более востребованной в строительстве промышленных объектов. Но постепенно арболит потерял свою актуальность в связи с распадом СССР и возникновением экономических проблем во всех странах, которые ранее были единым целым.
Второй приход арболита
Возрождение щепо-бетонного материала пришлось на 90-е годы. Этому поспособствовали:
- тяжелая экономическая ситуация;
- высокая потребность в недорогом и качественном строительном материале;
- развитие частного предпринимательства.
Кстати, именно мелкие предприниматели начали изготовление мелкоштучных стеновых блоков и их вывод на строительный рынок. Но большинство из них производство вели с использованием ручного труда, что затрудняло масштабный выпуск продукции и сдерживало ее развитие и распространение.
Спустя несколько лет в продаже появилось специальное оборудование, которое позволило увеличить количество выпускаемого арболита, а также улучшить его качество. С его внедрением началось активное строительство загородных домов из подобного материала, который используют как для кладки несущих стен, так и перегородок.
Постепенно арболит вытесняет традиционные строительные материалы в связи с тем, что ему присущи высокие теплоизоляционные качества, небольшой вес, устойчивость к возгоранию и хорошие показатели по сцеплению со штукатурными растворами. В малоэтажном индивидуальном домостроении он становится более востребованным и оправданным. Тем не менее, все же есть факторы, которые препятствуют широкому распространению материала. К ним относится отсутствие соответствующей нормативной базы, крупных предприятий по его производству и масштабной рекламной кампании по продвижению.
Но перспективы к развитию есть и будут, поскольку строители просто не могут оставить в стороне материал, который имеет массу преимуществ перед другими.
как сделать щепорез своими руками по чертежу? Выбор древесной дробилки для производства арболитовой щепы
Арболит как строительный материал был запатентован еще в первой половине XX века. В нашей стране широко применяться он стал в последние годы.
Арболит или деревобетон (щепобетон) выпускается в виде блоков. Используется для возведения малоэтажных строений. Как следует из названия, в качестве наполнителя выступает древесная щепа. В ход идут отходы деревьев хвойных и лиственных пород.
Арболит относится к недорогим строительным материалам, отличающимся высокой экологичностью, малым весом блоков, отличной способностью удерживать тепло. Древесные отходы в составе смеси деревобетона составляют более трех четвертей – от 75 до 90 процентов.
Что это такое?
Отходы деревообработки являются ценным строительным материалом. После измельчения до определенных размеров они становятся наполнителем бетонных смесей. Используется щепа для арболита или как его именуют щепобетона. Арболитовые блоки имеют массу достоинств. Доступная стоимость играет немалую роль. Кроме того, дом, построенный из арболита, практически не требует дополнительного утепления.
Есть у щепы и иные достоинства. Материал пригоден для использования в качестве:
- топлива для печей – в чистом виде или в виде гранул;
- декора – дизайнеры предлагают его в окрашенном и естественном виде для оформления дачных участков и даже парков;
- составляющей для изготовления и украшения мебели;
- ингредиента, используемого при копчении различных продуктов питания.
В производстве мелкие фракции идут на изготовление других стройматериалов: картона, гипсокартона, ДСП и ДВП.
Из чего делают?
Для производства щепобетона подходит практически любая древесина. И все же предпочтительно использование хвойных пород, к примеру, ели или сосны. Из лиственных более качественная щепа получается из березы. Подходят и другие твердолиственные породы: осина, дуб и тополь.
При выборе древесины для арболита нужно знать ее состав. Так, лиственница не подходит для данного строительного материала из-за высокого содержания веществ, негативно влияющих на цемент. Ядом для цемента являются сахара. Кроме лиственницы, они в большом количестве имеются в древесине бука. Следовательно, отходы этого дерева использовать тоже нельзя.
Очень важный момент – срок рубки леса. Щепу нельзя делать сразу после вырубки. Материал должен вылежаться в течение трех – четырех месяцев.
Практически все отходы могут стать исходниками для изготовления щепы.
- ветки и сучки;
- верхушки деревьев;
- горбыль;
- остатки и обломки;
- вторичные отходы.
Допускается наличие в общей массе древесины для производства щепы хвои и листьев – не более 5%, а коры – не более 10%.
Наиболее часто щепу изготавливают из елей и сосен. Выбор в пользу хвои неслучаен. Дело в том, что любая древесина содержит в себе такие вещества, как крахмал, сахара и прочие вещества, способные существенно повлиять на снижение качества арболита. В процессе производства приходится выводить вредные составляющие. Поскольку в хвое их меньше, именно на эти породы приходится меньше усилий, времени и материальных затрат на подготовку щепы.
Какой должна быть щепа?
Древесный наполнитель для арболита имеет свой ГОСТ. На уровне государственного стандарта для щепы установлены жесткие требования.
Выделены три основных параметра:
- длина не больше 30 мм;
- ширина не больше 10 мм;
- толщина не больше 5 мм.
Обозначены и оптимальные размеры по ширине и длине:
- длина – 20 мм;
- ширина – 5 мм.
Новые требования появились с принятием ГОСТ 54854-2011. До этого существовал другой ГОСТ с меньшими требованиями. Тогда допускалось использование более длинной щепы – вплоть до 40 мм. В 2018 году «вольности» в размерах наполнителя не допускаются.
Стандарт регламентирует и наличие примесей: коры, листьев, хвои. Материал следует очищать от земли, песка, глины, а в зимнее время – от снега. Наличие плесени и загниваний недопустимо.
Выбор оборудования для изготовления
Наиболее подходящим оборудованием для получения щепы требуемой формы и размеров является специальный деревообрабатывающий шредер. Однако стоимость станка настолько высока, что вне производства приходится искать другие варианты.
Арболит вполне возможно изготавливать в домашних условиях. Для этого и щепу нужно делать самостоятельно. Измельчителем древесины в условиях подсобного хозяйства становится щеподробильный станок. Щепорезы бывают трех типов.
- Дисковые рубильные машины обрабатывают древесину различной формы. За счет регулировки наклона режущего инструмента можно получать заготовки требуемого размера.
- В барабанных щепорезах измельчают всевозможные отходы: лесозаготовительные, мебельного производства, обрезков после строительства. Сырье загружают в объемный бункер, откуда оно попадает в камеру и разрезается ножами с двусторонними лезвиями.
- Роторные дробилки молоткового типа выпускаются с двумя или одним валом. Основные элементы устройства – молотки и отбойники.
Сначала древесина измельчается ударным способом, затем готовая продукция просеивается сквозь сито. От величины ячеек сита зависит размер получаемой щепы.
Во всех перечисленных устройствах предусмотрена только ручная загрузка материала.
Принцип производства
Принцип работы щепорезов сводится к нескольким этапам.
Сначала отходы – доски, горбыль, обрезки, сучки и другое сырье – закладываются в загрузочный бункер. Оттуда все это подается в закрытую камеру, где на валу вращается мощный диск. На плоском диске имеются прорези. На нем, кроме того, закреплены несколько ножей. Ножи движутся под углом. За счет этого обрабатываемая древесина разделяется на небольшие пластины с косым резом.
Сквозь дисковые прорези пластины проникают в барабан, где стальные пальцы производят дальнейшее измельчение. Пальцы и пластины крепятся на том же валу, что и диск. Пластины установлены очень близко к барабану. Они перемещают размолотую щепу по внутренней поверхности барабана.
Нижняя часть барабана снабжена сеткой с ячейками, обеспечивающими заданные размеры щепы. Размер ячейки варьируется от 10 до 15 мм в диаметре. Как только готовая к использованию щепа попадает в нижнюю зону в вертикальном направлении, она проходит сквозь сетку в поддон. Оставшиеся частицы проворачиваются, удерживаемые пластинами, еще круг. В это время их положение постоянно меняется. Достигнув низа в нужном направлении, они также оказываются в поддоне.
Щепорезы могут иметь как электрический, так и бензиновый приводы. Мощность двигателя небольшого устройства находится в пределах четырех – шести киловатт, в более солидных доходит до 10-15 кВт. От мощности зависят способности устройства. С ее увеличением растет объем продукции за час работы механизма.
Как сделать щепорез своими руками?
Тем, кто захочет сделать собственный щепорез, потребуется чертеж устройства, материалы, определенные знания и навыки. Чертеж можно найти в интернете, к примеру, тот, что прилагается.
Узлы и детали придется делать и собирать самостоятельно.
Один из основных элементов механизма – диск диаметром порядка 350 мм и толщиной примерно 20 мм. Если ничего подходящего в хозяйстве не имеется, придется вытачивать из листа. Для посадки на вал потребуется сделать хорошо центрированное отверстие с пазом под шпонку. Кроме того, нужно будет выпилить три паза, сквозь которые древесина станет попадать под молотки, и нужное количество монтажных отверстий.
Несколько проще обстоят дела с ножами. Их делают из автомобильных рессор. На ножах просверливаются по два отверстия под крепеж. Кроме сверла, потребуется зенкер. Зенковка позволит утопить потайные головки крепежных деталей. Плотно прикрепить ножи к диску не составит труда любому взрослому мужчине.
Молотки представляют собою обычные стальные пластины, имеющие толщину около 5 мм. Крепятся они на роторе с шагом 24 мм. Купить молотки можно в магазине.
Сито для щепореза – это длинный (около 1100 мм) цилиндр (Д= 350 мм), свернутый и сваренный из листа. Примечательно, что отверстия в сите должны иметь не ровные, а рваные края. Поэтому их не высверливают, а вырубают, к примеру, пробойником с диаметром от 8 до 12 мм.
Все режущие и вращающиеся детали должны закрываться кожухом. Кожух, как и приемный бункер, изготавливают из листовой стали. Отдельные детали вырезают по картонным шаблонам и сваривают в единое целое. Для жесткости конструкции к листам приваривают ребра жесткости из труб или уголков. В корпусе следует предусмотреть все отверстия: для вала, загрузочного бункера и для выхода щепы.
Готовые детали собираются в механизм. На рабочий вал насаживается диск, молотки и подшипники. Вся конструкция закрывается кожухом. Диск ни в коем случае не должен касаться корпуса. Зазор должен составлять порядка 30 мм.
Привод монтируется на заключительном этапе. Самодельный щепорез может работать от электродвигателя напряжением 220 или 380 В. Допускается работа от бензинового или дизельного мотора.
Электродвигатели обладают небольшой мощностью, зато малошумные и более экологичные. Двигатели внутреннего сгорания более производительны, но их работа сопровождается выделением вредных выхлопных газов.
Самодельные щепорезы выгодны при изготовлении арболита для частного строительства.
О том, как сделать щепорез своими руками, смотрите в следующем видео.
Золотое Руно
Арболи́т (от фр. arbre «дерево») — лёгкий бетон на основе цементного вяжущего, органических заполнителей (до 80-90 % объёма) и химических добавок. Также известен как древобетон. (wikipedia)
Опилкобетон стал первой ступенькой в процессе изготовления бетонов на основе органического сырья. Этот материал, в отличие от гипса или извести был более прочным. Его производили достаточно простым способом: основной компонент смешивали с песком и добавляли опилки, которые позволяли снизить вес конструкции, одновременно улучшая ее теплоизоляционные свойства. Поскольку к теплопроводности материала тогда не было столько требований, сколько их выдвигают в наши дни, опилкобетон долгое время оставался основным материалом, в производстве которого использовали древесные отходы. Однако эксперименты с материалами на основе дерева по-прежнему проводились, и в конце 19 века появились первые образцы фанеры. Ее появление стало новым витком в области производств стройматериалов с использованием дерева. Создателем фанеры стал ученый — изобретатель Костович О.С., который для связки древесных пластин применил альбуминно-казеиновый клей, предназначенный, в первую очередь для изготовления материала, получившего название «арборит» (arbor в переводе с латыни обозначает дерево).
Официально считается, что арболит изобрели голландцы в 30-е годы прошлого столетия (технология DURISOL). С развитием промышленности и появлением специальных деревообрабатывающих машин, использование отходов деревообработки в строительстве получило ещё более широкое распространение. До конца 19 века в качестве вяжущего вещества для производства подобных стройматериалов использовали глину, известь или гипс. Позже их сменил цемент, который используется для изготовления стройматериалов с использованием отходов деревообрабатывающей промышленности и в наши дни.
Основой современного арболита стал материал на основе цемента и древесной щепы. Первые образцы были получены в первой половине прошлого века в США, а в его названии соединились названия основных компонентов – дерева (с англ. wood) и камня (с англ. stone). Новинку строительного рынка быстро заметило руководство СССР. И уже в первой половине 60-х годов ВНИИдрев, МЛТИ, НИИЖБ, Гипролеспром тщательно изучили состав арболита, после чего начали подгонять его под климатические условия страны. Спустя несколько лет специалисты предоставили общественности щепобетон (такое название носил арболит в советские годы). Он производился в виде несущих и ограждающих конструкций, одно- и трехслойных стеновых панелей, блоков, плит перекрытий, конструкций, комбинированных с железобетоном.
Но специалисты в СССР были несколько ограничены в своих действиях из-за небольшого ассортимента строительных материалов. Все, что им было доступно – цемент с максимальной маркой прочности М400 и минерализатор в виде технического сернокислого алюминия, который использовался для удаления сахаров из щепы с целью улучшения ее связывающих качеств. Не было лишь недостатка в щепе . По всей территории СССР было множество заводов, которые работали с различной древесиной. Но ее приходилось предварительно высушивать и только потом пропитывать минерализаторами.
В 60-х годах 20 века «вудстоун» в Советском Союзе переименовали в ЦДК (цементно-древесная композиция) и в СССР началось строительство заводов для производства панелей из щепобетона. Поскольку щепу и цемент достаточно сложно совместить в одном материале, к тому же сахара, которые входят в состав сырой древесины способствовали разрушению структуры материала, ухудшая тем самым его качество, работы по усовершенствованию ЦДК не прекращались. Благодаря многочисленным экспериментам исследователям удалось установить, что качество арболита зависит не только от наличия сахаров в щепе, но и от влажности, размеров и даже пород деревьев, используемых для ее производства. Поскольку наилучших результатов удалось достичь, используя сухую щепу, на территории заводов по производству арболита позже строили специальные навесы, где щепу сушили на открытом воздухе. За три месяца естественной сушки щепа избавлялась от сахаров и влаги и хорошо впитывала все компоненты минерализаторов, после чего намного лучше смешивалась с цементом. Таким образом, удалось получить теплый, надежный и экологично чистый материал.
Однако производители столкнулись с еще одной проблемой: при соединении компонентов для производства арболита щепа разбухала. Этот процесс длился около 12 часов, в то время как цементный камень, схватывался гораздо быстрее. Одновременное протекание разноскоростных процессов стало причиной того, что продолжая набухать, щепа разрывала цементный камень, а это, в свою очередь, сказывалось на прочности арболита. Решением проблемы стали специальные металлические формы, закрывающие изделие со всех сторон. Их называют несъемными, и благодаря им, формирование арболита происходит в условиях замкнутого пространства, что не дает щепе возможности увеличиваться в объеме.
Сейчас в качестве органического заполнителя обычно применяется измельчённая древесина (щепа хвойных пород), также может использоваться костра льна или конопли (костробетон), дроблёная рисовая солома или дроблёные стебли хлопчатника. Для минерализации наполнителя, исключения гниения и возможности появления грибка используют сульфат алюминия (пищевая добавка E520 — применяется для производства фильтров для воды). Также допустимо использование хлорида кальция (пищевая добавка E509), нитрата кальция, жидкого стекла или иных веществ, блокирующих негативное действие органических веществ на затвердевание цемента.
Разработка ГОСТа по производству Арболита была скопирована с зарубежного образца DURISOL (ДЮРИСОЛ). Полученный в результате многочисленных экспериментов высококачественный материал, стал поводом для строительства многочисленных арболитовых заводов, где выпускали панели, получившие широкое распространение в строительстве жилых и промышленных строений. Академику Исааку Хисковичу Наназашвили было поручено ведение строительства заводов по изготовлению панелей из щепобетона по всей территории СССР. Под его руководством было возведено более 100 подобных промышленных объектов.
С введением в эксплуатацию заводов по производству панелей из щепобетона в СССР началось строительство из арболита. Такие дома 1979 года постройки можно до сих пор увидеть в эксплуатации в Московской области. Но самым большим достижением для Советского Союза было возведение зданий в Антарктике.
Еще в 60-е годы здесь были построены столовая и три здания служебного назначения. При толщине стен всего 32 см эти сооружения показали хорошие эксплуатационные качества в условиях сурового арктического климата. С этого момента цементно-древесная композиция стала еще более востребованной в строительстве промышленных объектов. Но постепенно арболит потерял свою актуальность в связи с распадом СССР и возникновением экономических проблем во всех странах, которые ранее были единым целым.
В масштабном домостроении до середины 90-х годов Арболит не получил массового применения в связи с ориентацией на строительство крупносборных бетонно-блочных домов и его высокие энергосберегающие, теплосберегающие, звукопоглощающие свойства не принимались во внимание. В начале 90-х одни заводы, выпускавшие этот материал, были развалены, другие — перепрофилированы, а индустрия производства композитных строений разрушена. Но здания, построенные из арболита более 60 лет тому назад, и сегодня — в хорошем состоянии, что показало его надежность и долговечность, высокие гигиенические и эксплуатационные свойства.
Возрождение щепо-бетонного материала пришлось на конец 90-х. Этому поспособствовали:
• тяжелая экономическая ситуация;
• высокая потребность в недорогом и качественном строительном материале;
• развитие частного предпринимательства.
Именно мелкие предприниматели начали изготовление мелкоштучных стеновых блоков и их вывод на строительный рынок. Но большинство из них производство вели с использованием ручного труда, что затрудняло масштабный выпуск продукции и сдерживало ее развитие и распространение.
Спустя несколько лет в продаже появилось специальное оборудование, которое позволило увеличить количество выпускаемого арболита, а также улучшить его качество. С его внедрением началось активное строительство загородных домов из подобного материала, который используют как для кладки несущих стен, так и перегородок.
Производство Арболита основано на нормативных требованиях ГОСТ 19222-84, который является межгосударственным стандартом на территории стран СНГ, а также ГОСТ Р 54854-2011, действующим на территории Российской Федерации.
Постепенно арболит вытесняет традиционные строительные материалы в связи с тем, что ему присущи высокие теплоизоляционные качества, небольшой вес, устойчивость к возгоранию и хорошие показатели по сцеплению со штукатурными растворами. В малоэтажном индивидуальном домостроении он становится более востребованным и оправданным. Тем не менее, все же есть факторы, которые препятствуют широкому распространению материала. К ним относится отсутствие соответствующей нормативной базы, крупных предприятий по его производству и масштабной рекламной кампании по продвижению.
Но перспективы к развитию есть и будут, поскольку строители просто не могут оставить в стороне материал, который имеет массу преимуществ перед другими.
Методы производства
Существует несколько методов производства стеновых блоков для наружных и внутренних ограждающих конструкций. Каждый из этих методов производства арболита имеет свои технологические особенности. Стеновые блоки, в основном, изготавливаются либо методом вибропрессования (вибролитья), либо методом прямого прессования.
Технология прямого прессования является сравнительно молодой и менее затратной с точки зрения применяемого оборудования. Прямое прессование предполагает выдержку арболитовой смеси в форме в течение до одних суток. Однако технология имеет ряд недостатков связанных с пространственной ориентацией щепы в смеси во время формирования изделия, что может приводить к внутренним напряжениям в готовом блоке.
Технология вибролиться (или вибропрессования) — это традиционная технология, которая получила распространение в 60-е годы ХХ века и проверена временем. Основным преимуществом данной технологии является получение однородной арболитовой массы в изделии при отсутствии внутренних напряжений в готовом блоке после схватывания цемента.
Качество готовых изделий зависит не только от метода производства блоков, но и от соблюдения требований ГОСТ, предъявляемых к материалам, которые входят в состав арболитовой смеси.
Арболитовые блоки имеют оптимальное соотношение теплопроводности, теплоемкости, веса, биостойкости, негорючести и прочности.
История арболита — Балтийский Арболит
Первые известные разработки появились в Нидерландах, в 1930-х годах.
Голландцы, наверное и подумать не могли, насколько долгая и успешная история ждет их изобретение.Через пару десятилетий технологию начали применять американские строители. И тогда, арболит, можно сказать выручил большой строительный сектор страны. Дело вот в чем.
В середине 1950-х годов, в США случились проблемы в экономике. Как следствие — доходы людей резко упали, а за ними и продажи недвижимости. Да, спрос на жилье есть почти всегда, но доступно оно далеко не всем. А в период кризиса — тем более.
Чтобы не экономить на качестве и квадратных метрах, а соблюдать высокие американские стандарты жилья, решили работать с основой — материалом стен.
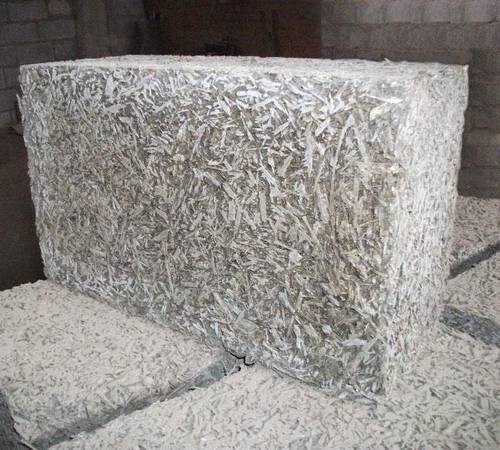
Главным фактором такого выбора, была его невысокая себестоимость. Но, одного этого — мало. Стройматериал должен соответствовать всем нормам эксплуатации — в штатах с этим строго. Поэтому, к работе подключились инженеры, строители, архитекторы и доработали изобретение голландцев. Арболит стал ещё лучше! Настолько, что правительство США организовало его выпуск в промышленных масштабах. Пожалуй, этот период и стал «звездным» для арболита.
И ведь по заслугам: выгодный, биостойкий, негорючий, легче бетона, просто обрабатывается, имеет высокие теплоизолирующие показатели, долговечен.Даже не удивительно, что такая интересная новинка быстро разошлась по строительным рынкам всего мира. И по сей день изделия из арболита активно используют в малоэтажном строительстве. Кроме США, под своей торговой маркой и по своей технологии, его стали выпускать: Чехия, Австрия, Япония, Швейцария, Германия.

А что у нас?
В 1960-х годах, наш «герой» преодолел «железный занавес» — попал в СССР. О том, как сложилась судьба арболита в Союзе, стоит сказать подробнее.
В целом, события развивались по американскому сценарию. Специалисты профильных НИИ изучили состав, свойства, и сделали свою доработку под наши климатические условия. По итогам этой работы, общественности был представлен новый стройматериал: щепобетон. Нормальный, советский нейминг).
Он без проблем прошел все необходимые испытания, а также процедуру сертификации и стандартизации по ГОСТу. Руководство страны отметило не только свойства и выгоды щепобетона, но и гигантские перспективы.
И началось!
«О неотложных мерах по созданию важнейших предприятий производственной базы строительства, осуществляемого в сельской местности Нечерноземной зоны РСФСР», и «О дальнейшем развитии заводского производства деревянных панельных домов и комплектов деревянных деталей для домов со стенами из местных материалов для сельского жилищного строительства».Проще говоря, специалистам строительной индустрии поставили задачу: срочно разработать заводское оборудование, чтобы начать выпускать серийные конструкции и изделия из арболита. В сельскохозяйственной отрасли планировался огромный объем малоэтажного строительства. А это жилые дома, хозпостройки, административные здания, базы, школы. Да практически всё!![]()
Для понимания — речь в постановлениях идет о налаживании выпуска полутора миллионах кубометров арболита в год! Большая страна — большие потребности.
В стране, с колоссальным объемом отходов деревообработки, было построено более 150 заводов по производству арболитовых изделий. Так, арболит помог превратить подходящую для производства часть отходов — в практичный стройматериал.
Ассортимент советских изделий был довольно большим. Вот неполный список:
— несущие и ограждающие конструкции,
— одно и трехслойные стеновые панели,
— блоки,
— плиты перекрытий,
— конструкции, комбинированные с железобетоном.
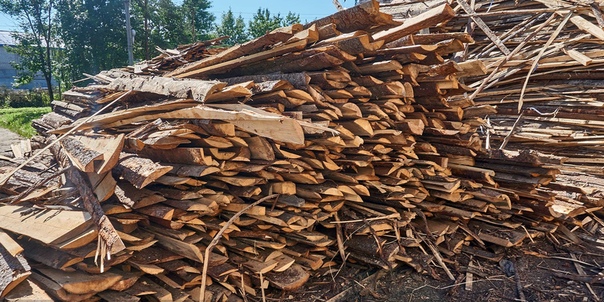
Современный же ассортимент продукции на основе арболита — ещё больше. Добавились: основания под линолеум и паркет, пространственные конструкции, плиты теплоизоляции и т.д.
Кстати, вот убедительный факт о теплоизоляции: в свое время, советские строители возвели из арболита столовую и три служебных помещения — в Антарктиде! При толщине стен всего 32 см., эти здания обеспечили достойные качества эксплуатации. Так что полярники спокойно жили и работали в таких суровых условиях.Когда с развалом СССР рухнула почти вся промышленность страны, то и производство арболита тоже стало неактуальным. Но, нельзя просто взять и забросить такие серьезные наработки по этому стройматериалу. Тем более, что границы открылись, и люди (в т.ч. предприниматели-строители) могли лично увидеть, что Европа, Азия и Америка по прежнему используют арболит. Да, у нас было общее падение спроса вообще на всё, но…
…даже в непростые 90-е годы жизнь продолжалась.

Сначала малый бизнес начал производить и выводить на рынок небольшие партии блоков — потому что было много ручного труда. А под растущий спрос начало появляться современное производственное оборудование. Оно, конечно, было практичнее и производительнее советского — объем арболита среди стройматериалов значительно вырос. И продолжает увеличиваться.
Сейчас производители арболита есть в большинстве регионов страны. А в крупных городах, по несколько таких компаний. И главное для нас всех — безупречно соблюдать технологию. Ведь, чем качественней будет наш продукт — тем больше людей предпочтут жить в теплых, экологичных, надежных домах из арболита!
P.S. Можно ли поменять свойства бетона или дерева? Например, сделать структуру дерева еще теплее? Без утеплителя — нет.
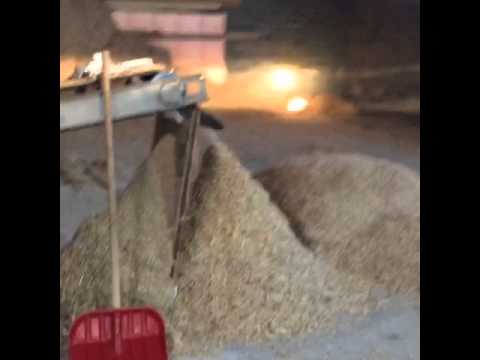
А мы, компания “Балтийский арболит”, продолжаем работать над улучшениями своей продукции, чтобы ваш будущий дом радовал вас комфортом, год за годом. И это тоже часть нашего вклада в историю арболита!
Как производится арболит? | Арболитовые блоки Смоленск
Для того, чтобы получить качественный арболит необходимо понимать, что производство арболита кардинально отличается от производства всех других видов бетонов, как легких (полистиролбетон, керамзитобетон), так и ячеистых (газобетон и пенобетон).Компоненты арболита:
1) древесная щепа.
2) цемент.
3) хим. добавки.
4) вода.
Несмотря на небольшое количество компонентов и кажущуюся простоту изготовления, производство арболита является трудоемким процессом в виду того, что щепа и цемент по своей природе не сцепляются друг с другом. И для того, чтобы получить единый материал (арболит-щепобетон), необходимо соблюсти целый ряд технологических моментов, иначе у вас не получится арболит. При этом надо понимать, что в данном разделе речь идет о получении качественного арболита, который соответствует всем требованиям ГОСТ 19222-84.
! ВАЖНО: производство арболита в холодное время года возможно при стабильной круглосуточной температуре внутри помещения не ниже +12+15 градусов. При более низкой температуре возникает проблема с гидратацией цемента и соответственно с качеством блока.
! ВАЖНО: круглогодичное производство арболита требует наличие оборотного капитала, который позволит производить арболит в течение минимум 2-3 месяцев в период, когда спрос либо отсутствует полностью, либо минимален.
Щепа (вид леса). Для получения качественного арболита наилучшим образом подходит щепа хвойных пород, в первую очередь сосны и ели. Согласно ГОСТ 19222-84 п.1.4.2. «В качестве органических заполнителей должны применяться: измельченная древесина из отходов лесозаготовок, лесопиления и деревообработки хвойных (ель, сосна, пихта) и лиственных (береза, осина, бук, тополь) пород, костра конопли и льна, измельченные стебли хлопчатника и измельченная рисовая солома. » Также арболит можно изготавливать на основе щепы лиственницы. Но использование щепы лиственницы требует кардинального увеличения объемов хим. добавок на обработку щепы, как минимум в 2 раза по сравнению с сосной.
Отбойный молоток и другие инструменты для разрушения бетона
Голдситни / Shutterstock.
В то время как старая добрая кувалда справляется со своей задачей, правильный электроинструмент значительно упрощает и ускоряет разрушение бетона.
Перейти к конкретному инструменту:
Отбойный молоток
Отбойные молотки — это легкие ручные дробилки для бетона, которые можно легко установить для разрушения вертикальных и потолочных поверхностей. Предлагая контролируемое измельчение, эти молотки позволяют операторам точно откалывать только определенные участки.
Самые маленькие отбойные молотки с электрическим, пневматическим или гидравлическим приводом обычно весят от 5 до 30 фунтов. Как правило, хорошим показателем мощности инструментов является их вес. Чем тяжелее инструмент, тем он может быть мощнее. Отрубное действие этого типа оборудования быстрое, от 900 до 3000 ударов в минуту.
Найдите местных подрядчиков по бетону, которые могут вырвать ваш старый бетон и заменить его новым красивым декоративным бетоном.
Поскольку отбойные молотки чаще всего используются для разрушения бетона на вертикальных и надземных поверхностях, они должны быть легкими. Они маневрируют, взявшись за ручку на задней стороне инструмента и взяв инструмент за вал другой рукой. У некоторых инструментов есть вторая ручка сбоку. Это дает операторам возможность контролировать вес инструмента и направлять его стружку под разными углами.
Предлагая контролируемое дробление, эти молотки позволяют операторам точно откалывать только определенные участки.
Производители предлагают больше возможностей для своих отбойных молотков, чем когда-либо, включая вращающиеся, амортизирующие рукоятки и тепловые экраны.
Демолитонный молот
Отбойные молотки похожи на перфораторы и используются таким же образом в отношении ударов молотков. Однако отбойные молотки обеспечивают ударное воздействие только , в отличие от перфораторов, которые также могут использоваться для бурения скважин.
Что не хватает отбойным молоткам в этом отношении с точки зрения универсальности, тем не менее, они компенсируют удар.Отбойный молоток может наносить более мощные удары, чем перфораторы, поскольку они обычно обладают примерно на 35% большей мощностью. Это связано с меньшим количеством деталей в отбойном молотке, а иногда и с более длинным ходом поршня.
Хотя отбойный молоток производит меньше ударов в минуту, чем перфоратор, повышенная прочность инструмента фактически делает его более быстрым и эффективным средством для сноса бетона и кирпичной кладки.
Рекомендуемые товары
Алмазная канатная пила
Канатные пилы были впервые разработаны в камнеобрабатывающей промышленности, а алмазные канатные пилы использовались в работах по сносу бетона для резки железобетона с начала 1980-х годов.
Петля из алмазного каната, установленная на маховике с приводом от гидравлического или электрического двигателя. Гидравлические приводы, приводимые в действие электрическими, бензиновыми или дизельными агрегатами, обычно предпочтительны на канатных пилах при резке железобетона, поскольку они оба реверсивны и обеспечивают плавно регулируемую скорость. На разрез наносится вода, чтобы охладить его и промыть.
Алмазные канатные пилы более эффективны, чем дисковые пилы, и могут резать бетон практически любой толщины. Это делает их очень полезными для тяжелого сноса мостов, плотин и толстых бетонных конструкций.Кроме того, они создают мало пыли, шума и вибрации, что делает их идеальными для работ по сносу жилых построек.
Алмазный канат
Реальная сила, стоящая за алмазной канатной пилой, — это сам алмазный канат, стальной несущий трос, продетый через стальные валики, к которым прикреплен алмаз. Существует три основных типа проводов:
- Гальванические борта с пружинными шайбами из сжатой стали.
- Пропитанные бусины с пружинными шайбами из сжатой стали
- Пропитанные шарики с промежутками из пластика, полученного литьем под давлением
Также существуют две основные системы крепления алмазных шариков: гальваническая и импрегнированная.Гальваника проволоки включает прикрепление одного слоя алмаза к стальному валику. Пропитанная связующая система больше похожа на пропитанную систему на циркулярной пиле, в которой металлический порошковый сплав смешивается с алмазом, затем прижимается и спекается к стальной ленте, обеспечивая несколько слоев алмаза для резки.
Гидравлическая дробилка для бетона
Гидравлические дробилки для бетона используются для методичного и эффективного разрушения бетона. Бетонные дробилки, также называемые измельчителями, уплотнителями, переработчиками, вторичными дробилками и измельчителями, используются для измельчения бетона на более мелкие, легко поддающиеся обработке или переработке, а также для отделения стальной арматуры от бетона.
Сменные челюсти в некоторых дробилках, включая трещинные челюсти, режущие челюсти и измельчающие челюсти, часто используются для работы вместе с различными типами и конфигурациями зубьев челюстей, чтобы лучше приспособить дробилку к конкретной работе.
Дробилки для вторичного бетона обычно оснащены челюстями для измельчения и используются на работах, где первичный снос выполняется с помощью молотков, дробилок, взрывных работ, шаровых кранов или пил. В этом случае при первичном сносе образуется большое количество бетонного щебня, который вторичная дробилка дополнительно измельчает, отделяя бетон от арматуры.
Гидравлический сплиттер
Гидравлические разделители прикладывают поперечные силы к внутренней части просверленных в бетоне отверстий, чтобы разбить бетон с минимальным шумом и летящими обломками.
Размером примерно с отбойный молоток, в инструменте используется вал, известный как узел «заглушка и перо», который, когда вставляется в просверленное отверстие и толкается вниз поршнем инструмента, создает боковые силы, разрушающие бетон. Для образования трещины не используются сильные удары, она быстро и без шума распространяется между предварительно просверленными отверстиями, пока бетон не разделится на небольшие части.
Типичный гидравлический разделитель создает усилие от 150 до 400 тонн, в зависимости от марки и модели. Как и в случае с большинством единиц оборудования этого типа, модели меньшего размера с допустимым усилием на нижнем конце шкалы используются для более легких работ или там, где с оборудованием должно быть легче обращаться, например, в горизонтальном или верхнем положении. Работа. Модели с большей грузоподъемностью способны раскалывать массивный бетон и твердые породы.
Гидравлические сплиттеры могут быть доступны в моделях с газовым и электрическим приводом, но большинство подрядчиков предпочитают гидравлические насосы с пневматическим приводом, поскольку инструменты воздушного компрессора также могут использоваться для приведения в действие сверл, используемых для формирования отверстий в бетоне. Можно настроить несколько гидравлических расколовщиков для работы бок о бок с одним и тем же гидравлическим насосом, что позволяет увеличить комбинированное усилие раскалывания, что полезно при дроблении особенно толстого или плотного бетона.
Для правильной эксплуатации разделителя отверстия должны быть просверлены прямо в бетоне с точным диаметром, указанным для разделителя, и должны быть достаточно глубокими, чтобы в них могла поместиться пробка при полном выдвижении. Пробку и перья необходимо хорошо смазывать, чтобы они оставались в рабочем состоянии.
Отбойный молоток
Ручные отбойные молотки можно рассматривать как своего рода тяжелую версию отбойного молотка.
Разница в том, что отбойные молотки — это более тяжелые и мощные инструменты, которые обычно работают перпендикулярно земле. Из-за этого Т-образная ручка является наиболее распространенной конструкцией для гидромолотов. Некоторые легкие отбойные молотки имеют D-образную ручку, которая позволяет оператору поднимать отбойный молоток и управлять им в горизонтальном положении.
Как и отбойные молотки, отбойные молотки имеют гидравлический, электрический или пневматический привод. Удары отбойных молотков обычно немного медленнее, чем отбойные молотки, от 800 ударов в минуту до почти 2000 ударов в минуту.
Дробилки весят от 30 до 99 фунтов. Хорошим показателем мощности выключателя является его вес.
Дробилки весом от 40 до 50 фунтов особенно полезны для удаления бетона при частичном ремонте дорожного покрытия.Вес этих инструментов дает им силу, необходимую для разрушения нескольких дюймов бетона, не будучи настолько тяжелыми, что они разрушают всю мостовую.
Дробилки весом 60 фунтов и больше могут выполнять работы по сносу средних и тяжелых зданий с использованием железобетона и используются для сноса тротуаров, дорог и толстого бетона. Одним из примеров типа работ, которые выполняют самые тяжелые отбойные молотки, является снос высокопрочного бетона, обнаруженного на взлетно-посадочных полосах аэропортов.
Перфоратор
Большие перфораторы известны как перфораторы SDS-max или шлицевые, в зависимости от того, подходят ли они к битам SDS-max или шлицевым хвостовиком.
Универсальность перфоратора позволяет ему разрушать бетон только с помощью молотка или выполнять перфорацию для сверления отверстий в бетоне. Это делается в режиме перфоратора путем забивки спиральных сверл и корончатых коронок или в режиме только перфоратора, чтобы использовать все, от плоских долот до приводных стержней.
Однако такая универсальность имеет свою цену, поскольку перфораторы имеют дополнительный привод, который вращает буровые долота в режиме перфоратора. Это откачивает энергию и снижает эффективность в режиме работы только с молотком.
В перфораторах используется таран, который плавает внутри цилиндра и запускается и поднимается поршнем. Амортизирующее воздушное пространство между плунжером и поршнем сжимает и толкает плунжер вперед по мере продвижения поршня, а затем втягивает его обратно, когда поршень втягивается.
Гидравлический молот
Гидравлический молот следует выбирать не только на основании вылета, устойчивости или необходимой гидравлической мощности, но и на основе транспортного средства, на котором будет установлен инструмент.Имейте в виду, что для определенного вылета, чем тяжелее молот, тем тяжелее должно быть транспортное средство. Вес транспортного средства предотвращает опрокидывание, когда отбойный молоток находится на максимальном вылете стрелы. Выбор легкого держателя уменьшает вылет стрелы и может привести к несчастному случаю опрокидывания.
Также помните, что хотя большинство гидравлических систем работают под давлением 2000 фунтов на квадратный дюйм, скорость потока меняется. Для легких молотов требуется всего 5 галлонов в минуту. Для тяжелых молотов необходимо подавать более 100 галлонов в минуту.Опять же, сверьтесь с литературой производителей молотка и держателя, чтобы согласовать молот с транспортным средством. При необходимости доступны дополнительные гидравлические силовые агрегаты для увеличения расхода.
Навесные выключатели
Скорость, универсальность и энергия удара установленных отбойных молотков широко используются подрядчиками для сноса сильно армированных стен, плит и настилов.
Экскаваторные отбойные молотки могут производить более 1100 кубических ярдов неармированного бетона в день.Производительность зависит от множества факторов, включая тип бетона, доступность и навыки оператора.
В дополнение к разрушению бетона многие молотки могут быть оснащены инструментами особой формы, которые позволяют им забивать сваи и листы, уплотнять почву, краевые траншеи, проникать в мерзлую землю и резать асфальт.
Энергия удара молота является наиболее важным критерием выбора при выборе навесного отбойного молотка для конкретной работы, поскольку молот должен иметь возможность ударить по бетону с достаточной силой, чтобы его сломать.Только когда энергия удара достаточна, скорость удара (ударов в минуту) становится фактором.
При учете энергии удара важен вес молота, но иногда это сбивает с толку. Некоторые производители указывают вес молота с кронштейном стрелы, окружающим корпусом (люлькой) и рабочим инструментом. Другие сообщают только о весе молота.
Вот почему сравнение диаметров инструмента может быть самым простым и точным средством определения степени энергии удара молотка.Измеряя диаметр инструмента в самой нижней точке внутри молотка и сравнивая его с диаметром других инструментов, можно надежно измерить энергию удара. Это связано с тем, что диаметр инструмента прямо пропорционален размеру поршня.
Агенты для расширенного сноса
Расширяющий разрушающий агент представляет собой цементный порошок. С помощью дрели с насадкой для смешивания порошок перемешивается в ведре и засыпается или утрамбовывается в просверленные отверстия. По мере того, как смесь затвердевает и расширяется, между просверленными отверстиями в бетоне появляются трещины.По мере того, как на плите развиваются микротрещины, они переходят друг в друга и расширяются, пока плита буквально не развалится под действием расширяющей силы, которая может превышать 12000 фунтов на квадратный дюйм.
При правильном использовании расширяющиеся средства для сноса оставляют мало пыли и мусора. Единственный труд, который требуется, — это просверлить отверстия, перемешать и нанести средство, а затем вытащить разбитые куски бетона.
Одно предостережение: При использовании экспансивных средств для сноса возникает явление, известное как «взрыв».«Это происходит, если порошковая смесь становится слишком горячей и вступает в реакцию с водой слишком быстро, чтобы материал мог расшириться вбок. Результат может варьироваться от клубов дыма до громкого огнестрельного звука, который может отправить затвердевшую смесь на 30 футов в воздух. .Поскольку выбросы непредсказуемы, процедуры безопасности требуют, чтобы рабочие держались подальше от просверленных отверстий после того, как в них была залита смесь. Однако, если выброс все же происходит, он обычно мало влияет на проект, поскольку оставшаяся смесь в отверстии обычно достаточно эффективна для растрескивания бетона.
Пневматический молот
Хотя когда-то в Соединенных Штатах пневматические молоты считались передовыми, они составляют лишь небольшую часть от общего числа молотов, используемых сегодня. Тем не менее, использование пневмомолотов по-прежнему имеет ряд преимуществ. К ним относятся:
Они могут быть установлены на более легких носителях, поскольку их внешний воздушный компрессор устраняет дополнительные гидравлические требования к гидравлическому молоту
Для установки пневмоударника требуются только механические изменения, без гидравлических соединений, систем для обслуживания или сантехнических комплектов
Пневматические молоты лучше работают в ограниченном пространстве, чем гидравлические молоты, из-за их высокого отношения веса к мощности.
Пневматические молоты больше подходят для подводного использования, так как у них мало уплотнений, если они вообще есть
Как разбить и удалить бетон
Невероятно, но почти постоянство простой трехкомпонентной смеси бетона становится проблемой, если вам нужно разбить и удалить ее. Чтобы разбить и удалить бетон, вам понадобится здоровый аппетит к тяжелой работе и несколько ключевых инструментов, которые помогут вам справиться с этим.
Мы расскажем, как использовать правильные инструменты в нужных обстоятельствах.
- Перед тем, как начать копать, позвоните по телефону 811 или в службу «Dig Safe» . При использовании землеройного оборудования надевайте защитное снаряжение.
- Отбойный молоток для разрушения толстого бетона. Если вы пытаетесь удалить бетон на глубину 3 дюйма или более, вам подойдет отбойный молоток.Сдающиеся в аренду электрические агрегаты, скорее всего, выбьют тот ветхий тротуар в конце подъездной дорожки или небольшого патио.
- Вес и вывоз бетона. Бетонные куски быстро превращаются в тонны. Как часть вашего расчета на его разбиение, включите затраты, усилия и оборудование, необходимые для его удаления. Универсальный прицеп 6×10 может безопасно перевозить около тонны (проверьте полную массу).
Инструменты для разрушения бетона
Бетон можно найти в самых разных местах, например, по краям патио или вдоль фундамента подвала; иногда вы можете столкнуться с кусками земли, закопанными в результате давнего сноса.
Использование перфоратора для разрушения бетона
Решением для успешного удаления, в большинстве подобных случаев, является перфоратор с функцией измельчения. Перфоратор — это не перфоратор; это разные инструменты, которые делают похожие вещи — перфоратор — это, по сути, ручной отбойный молоток. Хотя перфораторы бывают разных размеров, рядный инструмент с D-образной рукояткой исключительно эффективен.
Их насадки, называемые «утюгами», эффективно разрушают небольшие количества бетона и сбивают с поверхности отливы и другие загрязнения с помощью долота шириной ¾ дюйма.Лопата диаметром 1 ½ дюйма смертельна для родственника бетона — тонкого раствора — и отлично справляется с удалением плитки с чернового пола. Перфораторы отлично подходят для снятия стен CMU (бетонных блоков), блок за блоком.
Использование бруса для разрушения бетона
Штанга для копания также может подойти, если вы обнаружите в земле бетон (также мягкий камень, невероятно плотную глину, корни) во время установки забора или почтового ящика. По сути, это отбойный молоток с приводом от человека.
Он может создать линию разлома в бетоне, удар за ударом, и быть ключевым игроком в вашем арсенале инструментов для удаления бетона.Слово мудрым: как и со всем землеройным оборудованием, надевайте перчатки; штанги для копания — это инструменты для изготовления пузырей.
Разбить бетон кувалдой
Кувалды почти никогда не следует использовать в помещении. Заметным исключением являются плиты подвала в старых домах, где можно установить отстойник или водосток по периметру. Плиты подвала часто бывают тонкими — всего дюйм бетона над субстратом, как угольные шлаки.
Здесь отбойный молоток или перфоратор мгновенно пробивает поверхность, а затем может вклиниваться в грязь.Для тонкого, хрупкого бетона часто лучше всего тупое усилие. Это большая работа, но ударная волна стали по бетону разрушается за несколько ударов сильнее, чем другие инструменты могут нанести острым концом долота.
Разрушение бетона химикатами
Существует также так называемый расширяющийся раствор — химический агент, который помогает разрушать бетон. В зависимости от условий площадки может потребоваться отбойный молоток; перфоратор точно. Смешайте, налейте и ждите. Затирка расширяется и разрушает бетон.Планируйте заранее и ознакомьтесь с инструкциями производителя для правильного использования.
Как вырезать набор столбов в бетоне
Иногда бетон мешает, например, при снятии и замене установленных в нем столбов забора. В таких ситуациях часто бывает проще удалить несколько дюймов грязи вокруг основания стойки, а затем разрезать ее ниже уровня земли с помощью сабельной пилы.
Конечно, это означает, что подземная часть столба останется препятствием. Чтобы обойти это, по возможности сместите расположение столбов забора так, чтобы можно было выкопать новые ямы.Например, начните с половины панели вместо полной, перекрывая существующие местоположения постов.
Как избавиться от бетона
Основными транспортными средствами для перемещения бетона являются тачка или ручная тележка. Для небольших битов и / или удаления из дома трудно превзойти два 5-галлонных ведра. Как ни странно, носить по одному в каждой руке легче, чем нести только одно ведро.
Для более крупных проектов вы можете рассмотреть возможность аренды мусорного контейнера. Некоторым возчикам не нравится бетон в ящиках, поэтому обязательно спросите, поскольку они могут отказаться от работы или настоять на том, чтобы вы наполняли мусорный контейнер только частично.
В качестве альтернативы местный каменщик или ландшафтный дизайнер может возить бетон и переработать его — или даже, возможно, использовать его в проекте, где требуется заливка.
Chip System — Webfoot Concrete Coatings
Лучшее напольное покрытие — Broadcastted Chip System
Наша система напольных покрытий из стружки с технологией вещания привносит стиль и функциональность в жилые, коммерческие или гаражные помещения с высокой проходимостью.
Когда дело доходит до инвестиций в пол, будь то дом или бизнес, одной силы недостаточно — эстетика и стиль имеют значение! Чтобы защитить и украсить широкий спектр внутренних и внешних территорий, Webfoot Concrete Coatings с гордостью устанавливает наши упругие и визуально привлекательные полы из стружки.Разработанные не только для настила полов в гараже, наши системы идеально подходят практически для любого жилого, коммерческого или промышленного применения. Наши инновационные полы из стружки просты и включают однодневную укладку с максимальным временем отверждения 48 часов.
Универсальные настилы на базе микросхем для многоцелевого примененияБлагодаря своей текстурированной поверхности и многомерному внешнему виду, пол из системы Chip является отличным выбором для участков с интенсивным пешеходным движением, включая полы в гаражах и террасах бассейнов.Полы из стружки также отлично подходят для коммерческих помещений, таких как рестораны, выставочные залы, склады, офисы, салоны и магазины розничной торговли. При укладке наших надежных полов вы можете рассчитывать на ряд замечательных функций и преимуществ:
- Надежная адгезия : Наша формула создает прочную связь между покрытием и вашим бетонным полом; вам не нужно беспокоиться о шелушении, отслаивании или сколах.
- Rapid Curing : Покрытия нашей системы чипов специально изготовлены для быстрого отверждения; Вы можете снова ходить по этажам всего за 12 часов!
- Долговечность : Благодаря красивой конструкции из 100% полимочевины наши универсальные напольные покрытия устойчивы к ударам, истиранию и химическим веществам.
- Устойчивость к ультрафиолетовому излучению : Существенной особенностью напольных покрытий на открытых площадках, включая патио, веранды или террасы у бассейнов, должна быть устойчивость к ультрафиолету. Покрытие нашей системы микросхем не ухудшится и не потускнеет даже после многих лет воздействия элементов.
Если вы готовы защитить свои вложения с помощью надежного и долговечного напольного покрытия, которое выдержит испытание временем, позвоните в Webfoot Concrete Coatings сегодня! Чтобы поговорить с одним из наших специалистов по напольным покрытиям и получить бесплатное и без обязательств ценовое предложение, заполните нашу онлайн-форму сейчас.
Индивидуальные чип-системы с длительной прочностью
Наслаждайтесь преимуществами красивого и функционального пространства с напольными покрытиями, созданными с учетом стиля, прочности и ценности.
Есть несколько преимуществ, которые вы ищете при обновлении поврежденных бетонных полов, включая улучшение стиля, долговечность и простоту обслуживания. В Platinum Concrete Coatings от ProPaint Systems мы предлагаем системы микросхем от Penntek предоставляет все необходимое, включая быструю установку и гарантию вашего полного удовлетворения.
Как местная компания в Балтиморе с более чем 18-летним опытом работы в отрасли, Platinum Concrete Coatings от ProPaint Systems знает, как улучшить внешний вид ваших полов, не обойдясь вам в целое состояние.
Мы стремимся обеспечить целостность, профессионализм и беспроблемное обслуживание каждого проекта бетонного покрытия, который мы берем на себя, и наши системы микросхем — один из лучших вариантов, когда вам нужен максимальный стиль и впечатляющая долгосрочная перспектива. устойчивость.
Красота и прочность с системой напольных покрытий Chip Garage
В отличие от традиционного эпоксидного покрытия для гаражных полов, наши системы на основе полимочевины обеспечивают впечатляюще быстрое время отверждения и лучшую защиту от повреждений и интенсивного движения.Это делает их идеальными для всего: от выставочных залов, школ и от туалетов до этажей жилых гаражей, нуждающихся в повышении стиля и защиты.
Platinum Concrete Coatings от ProPaint Systems предлагает только лучшее для наших клиентов в Балтиморе, и каждая система на базе микросхем Penntek, которую мы устанавливаем, имеет следующие преимущества:
Трехслойная конструкция: Наши системы напольных покрытий из стружки устанавливаются в три слоя для создания стабильной красивой поверхности, включая базовое покрытие из полимочевины, специальные хлопья для стружки и верхнее покрытие из полиаспарагиновой полимочевины.
Устойчивость к повреждениям: Независимо от того, нужна ли вам система покрытия пола в гараже или решение для вашего коммерческого или промышленного здания, наши напольные покрытия разработаны таким образом, чтобы противостоять истиранию, разливу химических веществ, УФ-лучам и ударов.
Впечатляющая внешняя привлекательность: покрытия для полов из стружки изготавливаются по индивидуальному заказу с использованием виниловых хлопьев, которые можно смешивать для создания идеального пола, и у нас есть варианты, соответствующие вашему личному стилю и бизнес-потребностям.
Быстрая установка: Лучшее в обновлении бетонных полов с помощью системы покрытия стружкой — это то, насколько быстро вы видите результаты! Наши квалифицированные монтажники, прошедшие обучение на заводе-изготовителе, в кратчайшие сроки восстановят покрытие вашего пола. Полное использование полов можно вернуть менее чем за 24 часа.
Узнайте больше о преимуществах напольных покрытий из стружки для вашей собственности
Стандартные бетонные полы могут оставить грязные, поврежденные и опасные поверхности, но Platinum Concrete Coatings от ProPaint Systems может дать вам превосходное решение, необходимое для улучшения внешнего вида и характеристик вашего пола.Наши бетонные напольные покрытия Baltimore полностью адаптированы к потребностям и стилю вашего помещения, так почему бы не позвонить нам сегодня, чтобы узнать, что мы можем для вас сделать? Вы также можете заполнить нашу онлайн-форму сейчас, и мы поможем вам настроить с бесплатным предложением и консультацией!
Система чипов— Прецизионные бетонные покрытия
Универсальное, красивое и долговечное решение для покрытия — идеально подходит для широкого спектра напольных покрытий
Chip System от Penntek — это очень эстетичное напольное покрытие, которое идеально подходит для применений, где требуется, чтобы пол имел долговечный внешний вид.После нанесения это покрытие приобретает текстуру апельсиновой корки с имитацией гранита. Несмотря на то, что он добавляет визуальный элемент в комнату, он прочен, а текстура важна, особенно при использовании в коммерческих целях или в местах с высокой проходимостью.
Его использоваликомпаний в Миннеаполисе, Сент-Поле и городах-побратимах. Фактически, компании по всей стране имеют Chip System
.МНОГИЕ ПРЕИМУЩЕСТВА
Покрытие полов от Penntek’s Chip System имеет множество преимуществ.Преимущества:
- Глянцевое покрытие
- Предварительно тонированные
- Устойчивый к УФ-излучению
- Гибкий
- Химическая стойкость
- Устойчивость к истиранию
- Текстурированная поверхность
- Быстрое отверждение
- Чрезвычайная адгезия
- Выбор скорости излечения
- Широкий спектр применения
- Выдерживает высокие нагрузки
- Установка за один день
Chip System приобретает свою долговечность благодаря тому, что она изготовлена из 100% твердой полимочевины с использованием уникальной технологии, обеспечивающей превосходную адгезию.Вы также получаете быстрое лечение и максимальное время трансляции.
Мы знаем, что для ваших клиентов очень важно как можно скорее вернуться к работе. Простой может стоить вам денег, поэтому мы предоставляем продукт, который позволяет как можно скорее вернуться к нормальной работе. Это лучшее для вас и лучшее для клиентов, которые полагаются на вас.
И часть того, что делает возврат к эксплуатации быстрым, — это время лечения. Максимальное время перекрытия также способствует простоте нанесения для установщика.Когда укладка напольного покрытия несложная, на это уходит меньше времени.
РАЗНООБРАЗИЕ СМЕСЕЙ
Виниловые крошки, придающие покрытию уникальный вид, представлены в нескольких смесях, поэтому их можно смешивать и сочетать с выбранным вами цветом базового покрытия. Это позволяет сделать покрытие уникальным в соответствии с вашими потребностями. Вместо того, чтобы менять цвет комнаты в соответствии с полом, вы выбираете пол, соответствующий цвету комнаты. Это один из аспектов, который делает Chip System такой популярной.Еще одна причина, по которой он популярен, — это количество приложений, в которых его можно использовать.
ПРИМЕНЕНИЕ СИСТЕМЫ ЧИПОВ
Общие приложения системы микросхем:
- Туалеты
- Этаж гаража
- Офисные здания
- Выставочные залы
- Раздевалки
- Производственные площади
- Районы с высокой проходимостью, в том числе торговые площади
- Ветеринарная клиника
- Полы автосалона
- школы
- Больницы и медицинские учреждения
Отделка полов из бетонной стружки за один день
Когда дело доходит до напольного покрытия в местах с высокой посещаемостью вашего дома, одной долговечности недостаточно — вам также нужны красота и стиль! Чтобы защитить и украсить широкий спектр внутренних и наружных территорий, TSR Concrete Coatings с гордостью устанавливает упругие и эстетически привлекательные полы из систем стружки.Хотя изначально наши системы были разработаны для полов в гаражах, наши системы — это гораздо больше, чем просто покрытия для полов в гаражах; они идеально подходят практически для любого домашнего, коммерческого или промышленного применения. Наши инновационные полы с системой микросхем, разработанные для беспроблемной укладки за один день, быстро укладываются, но рассчитаны на длительный срок службы.
Общие области применения напольных покрытий чип-систем
Благодаря своей слегка текстурированной поверхности и многогранному облику гранита, полы из чиповой системы особенно популярны в зонах с высокой проходимостью, включая полы в гаражах и террасах бассейнов, а также в коммерческих помещениях, таких как офисы, выставочные залы и магазины.Где бы наши специалисты ни установили ваш пол из системы чипов, вы можете рассчитывать на ряд краткосрочных и долгосрочных преимуществ:
- Превосходная адгезия : Инновационная химическая формула наших покрытий для пола гаража создает прочную связь между покрытием и полом. Вам не придется беспокоиться о шелушении или шелушении.
- Быстрое отверждение : Покрытия нашей системы чипов специально изготовлены для беспроблемного нанесения и отверждения за один день, а наши монтажные бригады обучены эффективному обслуживанию.
- Долговечность : Благодаря красивому глянцевому верхнему слою и конструкции из 100% полимочевины наши покрытия для пола гаража устойчивы как к химическим веществам, так и к истиранию.
- Устойчивость к УФ-излучению : Особенно важной характеристикой полов бассейнов и других открытых площадок является устойчивость к УФ-излучению. Даже после нескольких лет нахождения под прямыми солнечными лучами покрытие нашей системы микросхем не ухудшается и не ухудшается.
Узнайте больше о наших универсальных покрытиях для гаражных полов и многом другом
Если вы готовы получить прочный, но дизайнерский пол, который выдержит интенсивное движение и суровые погодные условия, тогда позвоните компании TSR Concrete Coatings прямо сейчас! Чтобы запросить бесплатную цену без каких-либо обязательств, заполните нашу онлайн-форму сейчас.
Чиповая система| Покрытие пола гаража
Когда дело доходит до эффективного и привлекательного укладки напольного покрытия, стиль так же важен, как и сила, и система микросхем Penntek Industrial Coatings предлагает лучшее из обоих! Специально разработанная и разработанная опытными подрядчиками по укладке полов, наша система микросхем использует три отдельных слоя для обеспечения высочайшей прочности и устойчивости. Многослойная конструкция и индивидуальные цветовые схемы делают полы из нашей системы микросхем идеальными для любого жилого или коммерческого помещения с интенсивным движением, в том числе:
- Этаж гаража
- Зоны обслуживания
- Офис
- школы
- Выставочные залы
- Производственные площади
- Ветеринарная клиника
- Туалеты
Преимущества нашей системы покрытия пола гаража
Независимо от того, нужна ли вам система покрытия пола в жилом гараже или долговечная отделка для вашего торгового помещения, наша система чипов предлагает функции и преимущества, которые вы ищете:
- Долговечность : В отличие от эпоксидного покрытия для пола гаража, в нашей системе чипов используется полимочевина — материал, который намного прочнее и гибче.Благодаря базовому и финишному слоям из полимочевины наши полы из стружки устойчивы к истиранию, химическим веществам и УФ-излучению.
- Безопасность : Эта система напольного покрытия, состоящая из небольших виниловых крошек, имеет легкую текстуру, напоминающую апельсиновую корку, что добавляет сопротивление скольжению и дополнительное сцепление для обеспечения безопасного использования.
- Style : виниловая крошка может быть индивидуально смешана практически с любым цветом, позволяя вашему новому полу гаража соответствовать вашему существующему декору!
- Удобство : Наши полы из стружки могут быть установлены всего за один день обученными и сертифицированными специалистами Penntek по напольным покрытиям.
- Покрытие : Наша система микросхем имеет пожизненную гарантию, а также 15-летнюю гарантию на продукцию в жилых домах — так что вам никогда не придется беспокоиться о качестве вашего пола в долгосрочной перспективе.
Запросите бесплатную оценку для пола вашей новой системы микросхем!
При создании напольных покрытий в вашем новом доме или офисе вы можете положиться на универсальность и надежность нашей высококачественной системы микросхем. Для получения дополнительной информации об этой инновационной системе напольных покрытий позвоните в Penntek Industrial Coatings и поговорите со знающим экспертом по напольным покрытиям.Если вы готовы начать с бесплатной оценки и консультации на месте, просто заполните нашу онлайн-форму сейчас!
Загрузить брошюру .