Температура укладки асфальтобетонной смеси
Для получения доброкачественного асфальтобетона каменные материалы должны быть хорошо просушены и нагреты до температуры 180—250°, обеспечивающей хорошее перемешивание их с вяжущим.
При низкой температуре перемешивание происходит медленно, материал комкуется, крупные частицы каменного материала плохо обволакиваются вяжущим. Слишком высокая температура изменяет свойства вяжущего, а в некоторых случаях почти полностью уничтожают его клеящую способность, вследствие чего перегретая асфальтобетонная смесь не создает плотного монолитного покрытия при укатке.
При перегреве играет роль не только степень нагрева, но и продолжительность его. Если смесь в течение продолжительного времени находилась при температуре хотя бы и незначительно превышающей установленные нормы, могут произойти более сильные изменения свойств вяжущего, чем при кратковременном воздействии более высокой температуры.
Кроме того, имеет значение и количество вяжущего в смеси.
От температуры выпускаемой смеси зависят также укладка и укатка ее: низкая температура затрудняет равномерное распределение смеси по основанию, горячая смесь легко раскладывается, но замедляет укатку. Особенно затрудняет укатку неравномерный нагрев смеси, когда один замес выходит при верхнем пределе, а следующий при нижнем пределе температуры. Такая смесь формально не может считаться браком, но в покрытии при этом нередко получается брак.
Температурный режим регулируется форсункой и продолжительностью нагрева. Время нагрева зависит от влажности каменных материалов, от их свойств, от погодных условий.
Качество смеси в значительной степени зависит от качества перемешивания. При недостаточном перемешивании вяжущий материал распределяется неравномерно, образуя комочки, отдельное частицы остаются необработанными.
Непромешанная смесь, уложенная в покрытие, образует неровную раковистую поверхность. Даже при вполне доброкачественны|х материалах и правильно подобранном составе смеси вследствие неравномерного распределения частиц каменных материалов и битума отдельные участки покрытия могут получаться различной пористости, жесткости, пластичности и т. д. Это вызовет неравномерный и быстрый износ и разрушение покрытия. Для получения доброкачественного покрытия смесь должна быть хорошо перемешана.
Выпуск доброкачественной асфальтобетонной смеси не должен снижать производительности смесителей. Поэтому при приготовлении должно быть подобрано наилучшее время для каждого вида асфальтобетона, которое зависит от температуры каменных материалов и вяжущего, а также от работы мешалок.
Крупнозернистый асфальтобетон — National Production Group
Укладка крупнозернистого асфальтобетона
Укладка крупнозернистого асфальтобетона для конструктивных слоев дорожных одежд производится с применением современного высокопроизводительного механизированного асфальтоукладчика.
Перед укладкой крупнозернистого асфальтобетона производится битумная обработка поверхности нижнего слоя, для этого применяется битумная эмульсия, или нагретый жидкий битум.
При доставке и укладке готовых асфальтобетонных смесей, специалистами нашей компании строго контролируется температурный режим и состав асфальтобетонной смеси – на объекте Вы получаете асфальт, прогретый до температуры 150-160 °С, что соответствует требованиям ГОСТ 9128-84 и ГОСТ 12801-84.
Для устройства основания нижних и верхних конструктивных слоев дорожных одежд, мы используем:
1. Асфальтобетонную смесь крупнозернистую КЗ тип A, M1 — зерно до 40 мм;
2. Асфальтобетонную смесь крупнозернистую КЗ тип Б, M1 — зерно до 40 мм;
3. Асфальтобетонную смесь крупнозернистую КЗ тип Б, М2 — зерно до 40 мм;
При выборе крупнозернистого асфальтобетонного покрытия мы рекомендуем учитывать интенсивность движения по каждой категории транспортных средств. Все виды асфальтобетона имеют разные эксплуатационные характеристики с точки зрения долговечности поверхности, износа шин автомобилей, эффективности торможения и шума на дороге.
Применение крупнозернистых асфальтобетонных смесей в верхнем слое дорожного покрытия влечёт за собой увеличение шума от проезжей части.
Наша компания производит оперативную доставку и укладку асфальтобетонных смесей по всей территории Москвы и Московской области — без ограничений. В не зависимости, от требуемого объема асфальтобетона и расстояния до объекта заказчика — Мы всегда предложим оптимальную цену на материал и произведем укладку точно в срок.
Экспертизу качества провели на более 1,2 тыс. отремонтированных дорогах Подмосковья
В Московской области провели экспертизу качества на более 1,2 тысячи отремонтированных дорогах, что составляет 70% от общего плана ремонта на этот год, сообщили в пресс-службе Министерства транспорта и дорожной инфраструктуры Московской области.«В этом ремонтном сезоне недочеты и брак не превышают 7% от общего объема ремонтных работ, при этом на региональных дорогах — это не более 5%. Уже устранены замечания на 40 тысячах квадратных метрах покрытия. Завершить экспертизу всех отремонтированных дорог и устранить замечания планируется до конца сентября, некачественно выполненные работы не будут оплачены», — заявил министр транспорта и дорожной инфраструктуры региона Алексей Гержик.
В ведомстве отметили, что ремонт региональных дорог ведется в рамках национального проекта «Безопасные и качественные автодороги».
В Подмосковье осуществляется всесторонний контроль ремонта дорог: проверяется качество поставляемых материалов на заводы, соблюдение технологии укладки асфальтобетонных смесей, включая температурный режим. Все данные заносятся в автоматизированную систему контроля и планирования работ в области дорожной инфраструктуры (СКПДИ).
«Ежедневно для проведения экспертизы ремонта дорог выезжает около 20 экипажей лаборатории. Места забора проб определяет рондомным способом СКПДИ, что позволяет сделать более «прозрачным» процесс экспертизы. В ходе проверки отремонтированных участков выполняется отбор кернов. По результатам чего фиксируется толщина слоя асфальтобетонного покрытия, далее в лаборатории определяют качество уплотнения и свойства асфальтобетонной смеси. В среднем экспертиза занимает несколько суток», — рассказал директор производственной лаборатории по испытанию дорожно-строительных материалов «Лабрадор» Антон Батаев.
В случае отсутствия замечаний и получения положительного заключения экспертизы, подрядная организация наносит разметку и завершает работы по обустройству обочин. При выявлении брака, подрядчик за свой счет переделывает работы.
Всего в этом году в области отремонтируют порядка 1,7 тысячи участков автодорог протяженностью две тысячи километров, в том числе благодаря нацпроекту «Безопасные и качественные автодороги» обновят покрытие на свыше 400 региональных дорогах длиной более 1,4 тысячи километров.
Поможем разобраться: как работает льготная «Стрелка»>>
Решение: 01211000073/10.03.2015/3817 — Ставропольское УФАС
РЕШЕНИЕ
по делу № РЗ-198-2015 о нарушении законодательства о закупках
16.03.2015 года г. Ставрополь
Комиссия Управления Федеральной антимонопольной службы по Ставропольскому краю по контролю в сфере закупок (далее – Комиссия) в составе:
Председателя комиссии – заместителя руководителя Управления Федеральной антимонопольной службы по Ставропольскому краю Золиной Г. В.,
Членов комиссии:
ведущего специалиста-эксперта отдела контроля закупок Управления Федеральной антимонопольной службы по Ставропольскому краю Рошевский С.И.,
специалиста-эксперта отдела контроля закупок Управления Федеральной антимонопольной службы по Ставропольскому краю Напсо Б.Ш.,
В присутствии представителей:
от государственного заказчика – Петросян А.Г.
от заявителя жалобы уведомленного надлежащим образом — представитель на рассмотрение не прибыл, каких либо ходатайств в материалы дела не представил.
Рассмотрев жалобу, ООО «Стройка» на действия государственного заказчика – Управления муниципального хозяйства администрации города Минеральные Воды по факту определения поставщиков (исполнителей, подрядчиков) путем проведения аукциона в электронной форме № 0321300009615000009 «выполнение работ по ямочному ремонту дорог в городе Минеральные Воды»,
УСТАНОВИЛА:
В Ставропольское УФАС России поступила жалоба ООО «Стройка» на действия государственного заказчика – Управления муниципального хозяйства администрации города Минеральные Воды по факту определения поставщиков (исполнителей, подрядчиков) путем проведения аукциона в электронной форме № 0321300009615000009 «выполнение работ по ямочному ремонту дорог в городе Минеральные Воды».
Заявитель в своей жалобе указывает, что в техническом задании в требовании к асфальтобетонной смеси. Заказчик устанавливает: Смесь требуется мелкозернистая, плотная и горячая, укладываемая с температурой не менее 120°С.
Смеси асфальтобетонные выпускаются в настоящее время по ГОСТ 9128-2013. В пункте 4.1.2 ГОСТ 9128-2013. указывается: «Смеси в зависимости от вязкости используемого битума и температуры при укладки подразделяют: на горячие, приготовляемые с использованием вязких и жидких нефтяных дорожных битумов и укладываемые с температурой не менее 110°С. Таким образом требования заказчика не соответствуют требованиям действующего ГОСТа. Нарушено право участников размещения заказа предложить смеси мелкозернистые, плотные и горячие, укладываемые с температурой 110°С.
Представитель заказчика поддержала доводы, указанные в представленных письменных объяснениях, устно пояснила, что документация закупки составлена в соответствии с требованиями Закона №44-ФЗ.
Комиссия Ставропольского УФАС России по контролю закупок, проанализировав имеющиеся в деле документы, проведя в соответствии со ст. 99 Закона внеплановую проверку, выслушав доводы представителей заказчика и исследовав в совокупности представленные документы, установила следующее:
Согласно п. 1 и п. 2 ч. 1 ст. 33 Закона №44-ФЗ заказчик при описании в документации о закупке объекта закупки должен руководствоваться следующими правилами:
1) описание объекта закупки должно носить объективный характер. В описании объекта закупки указываются функциональные, технические и качественные характеристики, эксплуатационные характеристики объекта закупки (при необходимости). В описание объекта закупки не должны включаться требования или указания в отношении товарных знаков, знаков обслуживания, фирменных наименований, патентов, полезных моделей, промышленных образцов, наименование места происхождения товара или наименование производителя, а также требования к товарам, информации, работам, услугам при условии, что такие требования влекут за собой ограничение количества участников закупки, за исключением случаев, если не имеется другого способа, обеспечивающего более точное и четкое описание характеристик объекта закупки. Документация о закупке может содержать указание на товарные знаки в случае, если при выполнении работ, оказании услуг предполагается использовать товары, поставки которых не являются предметом контракта. При этом обязательным условием является включение в описание объекта закупки слов «или эквивалент», за исключением случаев несовместимости товаров, на которых размещаются другие товарные знаки, и необходимости обеспечения взаимодействия таких товаров с товарами, используемыми заказчиком, а также случаев закупок запасных частей и расходных материалов к машинам и оборудованию, используемым заказчиком, в соответствии с технической документацией на указанные машины и оборудование;
2) использование, если это возможно, при составлении описания объекта закупки стандартных показателей, требований, условных обозначений и терминологии, касающихся технических и качественных характеристик объекта закупки, установленных в соответствии с техническими регламентами, стандартами и иными требованиями, предусмотренными законодательством Российской Федерации о техническом регулировании. Если заказчиком при описании объекта закупки не используются такие стандартные показатели, требования, условные обозначения и терминология, в документации о закупке должно содержаться обоснование необходимости использования других показателей, требований, обозначений и терминологии.
1. В техническом задании, являющимся неотъемлемой частью аукционной документации, в пункте 9 «Показатели позволяющие определить соответствие закупаемых товара, работы, услуги, установленным заказчиком требованиям (в т. ч. требования к товарам (материалам) используемым при выполнении работ, оказании услуг)» установлено требование (технические характеристики) к используемым материалам.
Обжалуемая позиция: «Смесь требуется мелкозернистая, плотная и горячая, укладываемая с температурой не менее 120 °C. Тип смеси необходим Б. Марка требуется II.»
Действительно, смеси асфальтобетонные выпускаются на данный момент актуальному ГОСТ 9128-2013. В пункте 4.1.2 ГОСТ 9128-2013 указывается «Смеси в зависимости от вязкости используемого битума и температуры при укладки подразделяют: на горячие, приготовляемые с использованием вязких и жидких нефтяных дорожных битумов и укладываемые с температурой не менее 110 °C »
Однако, необходимо учитывать тот факт, что ГОСТ 9128-2013 устанавливает общие требования к изготовлению асфальтобетонных смесей и асфальтобетона, полимерасфальтобетонных смесей с применением полимерно-битумных вяжущих на основе блоксополимеров типа СБС и полимерасфальтобетона из этих смесей (указано абз. 1 главы 1 «Область применения» ГОСТ 9128-2013).
В доводах жалобы Заявитель ссылается на ГОСТ 9128-2013 где указана минимальная температура укладки 110°C (п. 4.1.2) Данный пункт ГОСТа обобщает температуру укладки всех видов горячих смесей без учета применяемых при изготовлении марок битумов и без учета дорожно-климатической зоны.
Требования и правила к производству и контролю качеству работ устанавливаются в СНиП 3.06.03-85«Автомобильные дороги».
Таким образом, ГОСТ 9128-2013 регламентирует и устанавливает общие требования к изготовлению асфальтобетонных смесей, их технические характеристики, такие как, размеры минеральных зерен, количество содержания щебня или гравия в смеси, показатели водостойкости и другие, т.е. общие значения и показатели используемого материала.
В свою очередь СНиП 3.06.03-85 «Автомобильные дороги» устанавливает технологический порядок и правила организации дорожностроительных работ, в целом требования к производству работ, учитывая сопоставимость применяемых материалов, климатические условия и другие показатели.
Так же поясняем, что установленные требования к минимальному температурному режиму укладки асфальтобетонной смеси (плотной, горячей, типа Б, марки II) 120С°, что соответствует требованиям СНиП 3.06.03-85 на производство данного вида работ. Согласно СНиП 3.06.03-85 пункта 10.13. и таблицы № 14, для асфальтобетона типа Б и применяемых в IV в дорожно-климатической зоне битумов, температура укладки должна составлять 120-160С°.
Согласно п. 10.13 СНиП 3.06.03-85 «Автомобильные дороги» продолжительность транспортирования асфальтобетонных смесей должна устанавливаться из условия обеспечения температуры при укладке, указанной в
Таблице 14.
Вид смеси | Марка битума | Температура смеси в начале уплотнения, °С, для | |
|
| плотного асфальтобетона типов А и Б, пористого и высокопористого асфальтобетонов с содержанием щебня (гравия) более 40 % массы | плотного асфальтобетона типов В, Г и Д, пористого и высокопористого асфальтобетонов с содержанием щебня (гравия) менее 40 % массы и высокопористого песчаного |
Горячая | БНД 40/60, БНД 60/90, БНД 90/130, БН 60/90, БН 90/130 | 120 — 160 | 100-130 |
Теплая | БНД 130/200, БНД 200/300, БН 130/200, БН 200/300 | 100- 140 | 80-110 |
| СГ 130/200, МГ 130/200, МГО 130/200 | 70-100 | |
Холодная | СГ 70/130, МГ 70/130, МГО 70/130 | Не ниже 5 |
В соответствии с п. 10.22. СНиП 3.06.03-85 «Автомобильные дороги» уплотнение смесей следует начинать непосредственно после их укладки, соблюдая при этом температурный режим, указанный в табл. 14.
Действия Заказчика — Управления муниципального хозяйства администрации города Минеральные Воды, обоснованы, установленный температурный режим укладки 120 С°, соответствует дорожной-климатической зоне IV (на территории которой находится г. Минеральные Воды), так как асфальтобетонная смесь используемая при выполнении работ по ямочному ремонту, типа Б марки II укладывается при температуре конкретно не менее 120 С, что соответствует требованиям СНиП 3.06.03-85 «Автомобильные дороги» и не противоречит ГОСТ 9128-2013.
Тем самым, доводы Заявителя о нарушении Заказчиком требований ГОСТ 9128-2013, не обоснованны, так как, при составлении технического задания и требований к используемым материалам, учтены все технические показатели материалов и условия выполняемых работ.
2. В статье 8 Федерального закона № 44-ФЗ раскрыто содержание принципа обеспечения конкуренции. Понятие «конкуренция» определено в п. 7 ст. 4 Федерального закона от 26 июля 2006 г. № 135-ФЗ «О защите конкуренции» как соперничество хозяйствующих субъектов, при котором самостоятельными действиями каждого из них исключается или ограничивается возможность каждого из них в одностороннем порядке воздействовать на общие условия обращения товаров на соответствующем товарном рынке, в связи с чем, действия заказчика основаны на соблюдении принципа добросовестной ценовой и неценовой конкуренции между участниками закупок в целях выявления лучших условий поставок товаров, выполнения работ, оказания услуг.
Принимая во внимание вышесказанное, доводы о нарушении Федерального закона от 26 июля 2006 г. № 135-ФЗ «О защите конкуренции», являются так же безосновательными, ввиду того, что Заказчиком установлена определенная марка и тип асфальтобетонной смеси которую необходимо укладывать при установленном температурном режиме, для всех участников закупки.
На основании вышеизложенного, документация закупки № 0321300009615000009 «выполнение работ по ямочному ремонту дорог в городе Минеральные Воды» соответствует требованиям Закона №44-ФЗ.
Комиссия, руководствуясь ст. 99, ст. 105 Федерального закона от 05.04.2013 года № 44-ФЗ «О контрактной системе в сфере закупок товаров, работ, услуг для обеспечения государственных и муниципальных нужд»
РЕШИЛА:
1. Признать жалобу ООО «Стройка» на действия государственного заказчика – Управления муниципального хозяйства администрации города Минеральные Воды по факту определения поставщиков (исполнителей, подрядчиков) путем проведения аукциона в электронной форме № 0321300009615000009 «выполнение работ по ямочному ремонту дорог в городе Минеральные Воды»– необоснованной;
Настоящее решение может быть обжаловано в судебном порядке в течение трех месяцев со дня его принятия.
Председатель комиссии Г.В. Золина
Члены комиссии С.И. Рошевский
Б. Ш. Напсо
ОДМ 218.5.002 Перегружатели
ОДМ 218.5.002 Перегружатели
- Details
- Published on 2019-05-23
О внесении дополнений в распоряжение Федерального дорожного
агентства от 28.07.2009 № 271-р
1.1. Раздел 6 дополнить абзацем следующего содержания: «в) При проведении работ по укладке верхних слоев асфальтобетонного покрытия, необходимо обеспечить следующие показатели равномерности температуры за асфальтоукладчиком.
Разность температур температурного профиля укладываемого асфальтобетонного покрытия, измеренного на расстоянии 0,3-1,0 м от плиты асфальтоукладчика должно составлять не более 10оС.
Определение температурного профиля осуществляется в соответствии с приложением Г».
1.2. Раздел «Содержание» дополнить пунктом «Приложение Г (справочное) «Определение температурного профиля укладываемого асфальтобетонного покрытия».
1.3. Добавить приложение Г в соответствии с приложением к настоящему распоряжению.
2. Контроль за исполнением настоящего распоряжения оставляю за собой
И.о. руководителя Н.В. Быстров
Приложение к распоряжению
Федерального дорожного агентства
от 29.05. 2013 г. № 717-р
Приложение Г
«Определение температурного профиля укладываемого асфальтобетонного покрытия».
- Температурный профиль покрытия определяется с целью контроля температурного расслоения асфальтобетонной смеси с целью недопущения неравномерности уплотнения верхних слоев асфальтобетонного покрытия.
- Температурный профиль покрытия может определяться с использованием бесконтактных термометров, а так же тепловизоров с погрешностью до 3оС.
- Измерение температурного профиля асфальтобетонного покрытия производится на расстоянии от 0,3 до 1,0 м от плиты асфальтоукладчика.
- Каждый температурный профиль должен включать не менее 3 поперечных замеров температур через каждые 15 метров.
- Каждый замер должен содержать не менее 3 точек вдоль линии перпендикулярной оси дороги (один по центру и два 0,4 м от края). Расстояние между точками замеров не может превышать 1.5 м.
- Разность температур профиля определяется как разница между наиболее низким и наиболее высоким значением измерения температуры укладываемого покрытия.
В случае если разность температур составляет более 10 оС, организация, осуществляющая укладку должна принять меры по устранению температурного расслоения асфальтобетонной смеси.
В случае выявления сегрегации более 15 оС укладка слоя должна быть приостановлена, а участок покрытия должен быть заменен на новый, соответствующий вышеуказанным требованиям.
ОДМ 218.5.002-2009
ОТРАСЛЕВОЙ ДОРОЖНЫЙ МЕТОДИЧЕСКИЙ ДОКУМЕНТ
Утверждены
распоряжением Росавтодора
от 28.07.2009 г. № 271-р
МЕТОДИЧЕСКИЕ РЕКОМЕНДАЦИИ ПО УСТРОЙСТВУ АСФАЛЬТОБЕТОННЫХ СЛОЕВ С ПРИМЕНЕНИЕМ ПЕРЕГРУЖАТЕЛЕЙ СМЕСИ
________________________________________________________________________________________________
ФЕДЕРАЛЬНОЕ ДОРОЖНОЕ АГЕНТСТВО
(РОСАВТОДОР)
Москва 2009
Предисловие
1 РАЗРАБОТАН Московским автомобильно-дорожным институтом (Государственный технический университет), Центром метрологии, испытаний и сертификации МАДИ (ГТУ) при участии АНО «НИИ ТСК».
2 ВНЕСЕН Управлением научно-технических исследований, информационного обеспечения и ценообразования Федерального дорожного агентства.
3 ПРИНЯТ И ВВЕДЕН В ДЕЙСТВИЕ на основании распоряжения Федерального дорожного агентства от 28.07.2009 г. № 271-р.
4 ИМЕЕТ РЕКОМЕНДАТЕЛЬНЫЙ ХАРАКТЕР.
Раздел 1. Область применения
Настоящий отраслевой дорожный методический документ (далее – ОДМ) распространяется на работы по устройству асфальтобетонных слоев на основе применения перегружателей асфальтобетонной смеси (на примере машин «Roadtec SB-2500 Shuttle Buggy») при строительстве, реконструкции и всех видах ремонтаавтомобильных дорог и устанавливает порядок и рекомендации к их выполнению.
В соответствии с данным ОДМ могут использоваться и другие перегружатели асфальтобетонной смеси с аналогичными техническими возможностями.
Раздел 2. Нормативные ссылки
В настоящем ОДМ использованы ссылки на следующие стандарты:
ГОСТ 9128-97 Смеси асфальтобетонные дорожные, аэродромные и асфальтобетон. Технические условия.
ГОСТ 12801-98 Материалы на основе органических вяжущих для дорожного и аэродромного строительства. Методы испытаний.
Раздел 3. Термины и определения
В настоящем ОДМ применяются следующие термины с соответствующими определениями:
Фракционная сегрегация – неоднородность зернового состава асфальтобетонной смеси в различных точках ее объема.
Температурная неоднородность – неоднородность температуры асфальтобетонной смеси в различных точках ее объема.
Раздел 4. Основные технологические операции с применением машин – перегружателей асфальтобетонной смеси
а) Устранение фракционной и температурной сегрегации достигается путем применения в технологической цепочке укладки асфальтобетонной смеси дополнительной машины – перегружателя асфальтобетонной смеси (далее – перегружателя), являющейся промежуточным звеном между автомобилем-самосвалом и асфальтоукладчиком.
б) Технологические особенности перегружателя:
— непрерывная перегрузка асфальтобетонной смеси с устранением контакта грузовика и укладчика при ее выгрузке из кузова автомобиля-самосвала;
— дополнительное перемешивание асфальтобетонной смеси трехшаговым шнеком;
— обеспечение накопления асфальтобетонной смеси в бункере перегружателя; кроме того, при наличии бункера-вставки асфальтоукладчика – до 20 т в бункере асфальтоукладчика;
— увеличение скорости разгрузки автомобилей-самосвалов;
— увеличение скорости укладки смеси;
— возможность подачи относительно малого количества асфальтобетонной смеси к рабочим, использующим ручной инструмент при работе на небольших площадях;
— возможность забора материала с поверхности;
— использование асфальтоукладчиков в тоннелях, под мостами, под контактной сетью и там, где невозможна разгрузка самосвалов из-за ограничения по высоте;
— возможность отклонения конвейера от центра в обе стороны.
в) Принципиальная схема перегружателя приведена в Приложении А.
г) Принципиальная схема устройства трехшагового шнека приведена в Приложении Б.
Раздел 5. Порядок устройства асфальтобетонных слоев на основе применения перегружателей асфальтобетонной смеси
Укладка асфальтобетонной смеси при использовании в составе машин перегружателя производится в следующем порядке:
а) Оператор перегружателя подает сигнал на подход автомобиля-самосвала с асфальтобетонной смесью. Автомобиль-самосвал задним ходом подают к отвальному бункеру перегружателя до касания колесами упорных валиков.
б) При работе одного перегружателя смесь из автомобиля-самосвала выгружают в отвальный бункер перегружателя. В процессе выгрузки автомобиль-самосвал либо разгружается в неподвижный перегружатель, если приемный бункер асфальтоукладчика заполнен, либо перемещается вместе с перегружателем, если одновременно происходит выгрузка смеси из перегружателя в асфальтоукладчик.
в) При работе двумя перегружателями один из перегружателей разгружается в приемный бункер асфальтоукладчика, в то время как второй находится под загрузкой и автомобили-самосвалы разгружаются в него без движения. В результате работы двумя перегружателями достигается сокращение сроков разгрузки и увеличение скорости укладки смеси. Особенно данный способ эффективен при укладке асфальтобетонной смеси одним асфальтоукладчиком шириной 9-16 м и более.
г) Смесь из отвального бункера при помощи расположенных в нем вибраторов поступает на сходящийся трехшаговый шнек, который, перемешивая асфальтобетонную смесь, перемещает материал прямо по заднему конвейеру в промежуточный бункер; затем смесь с помощью двух трехшаговых шнеков, находящихся в нижней части промежуточного бункера, перемешивается и подается на задний конвейер, тем самым устраняя фракционную сегрегацию и температурную неоднородность.
д) Асфальтобетонная смесь с заднего конвейера поступает непосредственно в приемный бункер асфальтоукладчика, оснащенный специальным устройством (вставкой) для массовой подачи материала прямо на пластинчатый конвейер укладчика.
План потока при устройстве асфальтобетонных слоев на основе применения двух перегружателей приведен в Приложении В.
Раздел 6. Контроль качества
а) Устройство асфальтобетонного покрытия с применением перегружателей должно производиться в соответствии с [1].
б) Основные геометрические параметры и характеристики уложенного асфальтобетонного слоя должны соответствовать требованиям [1], в частности:
ширина слоя;
толщина слоя;
ровность;
поперечный уклон;
высотные отметки по оси;
коэффициент уплотнения;
коэффициент сцепления шины автомобиля с покрытием (для верхних слоев).
Примечания:
1 Температура асфальтобетонной смеси при укладке в покрытие должна быть не ниже 120оС. Допускается ее снижение на 20оС при условии использования ПАВ или активированных минеральных порошков.
2 Коэффициент уплотнения через 1-3 суток после укатки должен быть не ниже:
— 0,99 для плотного асфальтобетона из горячих смесей типов А и Б;
— 0,98 для плотного асфальтобетона из горячих смесей типов В, Г и Д, пористого и высокопористого асфальтобетона;
3 Верхний слой асфальтобетонного покрытия должен иметь ровную однородную шероховатую поверхность без разрывов и раковин, с ровными кромками. Дефектные места не допускаются.
в) Операционный контроль качества представлен в таблице 1.
г) Отбор проб осуществляют согласно ГОСТ 12801.
д) Физико-механические показатели материала устроенного асфальтобетонного слоя должны соответствовать требованиям
ГОСТ 9128.
Таблица 1
№ п/п |
Основные операции, подлежащие контролю |
Проверка основания передукладкой асфальтобетонной смеси. Разбивочные работы |
Устройство слоя покрытия |
Уплотнение асфальтобетонной смеси |
1 |
Состав контроля |
1. 2. Ширина основания 3. Высотные отметки основания |
1. Температура смеси при укладке 2. Ровность слоя 3. Толщина уложенного слоя покрытия 4. Соблюдение поперечного уклона и ширины |
1. Степень уплотнения смеси 2. Поперечный уклон верхнего слоя покрытия 3. Ровность верхнего слоя покрытия 4. Высотные отметки |
2 |
Метод и средства контроля |
Визуальный, инструментальный 1. Визуально 2. Мерная лента, стальная рулетка 3. Нивелир, копирная струна |
Инструментальный визуальный 1. Термометр 2. 3-метровая рейка, клин 3. Мерник толщины 4. |
Инструментальный лабораторный 1. Контрольный проход тяжелого катка, вырубка образцов 2, 3. 3-метровая рейка 4. Нивелир, мерная лента, стальная рулетка |
3 |
Режим и объем контроля |
1. Вся захватка. В начале смены 2. Не реже чем через 100 м 3. Не реже чем через 100 м |
1.В каждом автомобиле самосвале 2. Не реже чем через 100 м 3. Не реже чем через 100 м 4. Не реже чем через 100 м |
1. Пробы (не менее трех на 7000 м2) 2, 3. После двух-трех проходов катка 4. По окончании уплотнения |
4 |
Лицо, контролирующее операцию |
Мастер |
Мастер |
Мастер, лаборант, геодезист |
5 |
Лицо, ответственное за организациюи осуществление контроля |
Прораб |
Прораб |
Прораб |
6 |
Привлекаемые для контроля подразделения |
– |
– |
Лаборатория Геодезическая служба |
7 |
Где регистрируются результатыконтроля |
Общий журнал работ |
Общий журнал работ |
Общий журнал работ, журнал лабораторных работ, журнал нивелировки |
Библиография
[1] СНиП 3. 06.03-85 Автомобильные дороги
Ключевые слова: устройство асфальтобетонных слоев, перегружатель асфальтобетонной смеси, основные технологические операции, контроль качества
Приложение А
(справочное)
Принципиальная схема перегружателя асфальтобетонной смеси
1 – отвальный бункер перегружателя; 2 – конвейер;
3 – бункер, оснащенный трехшаговым шнеком; 4 – задний конвейер
Приложение Б
(справочное)
Принципиальная схема трехшагового шнека
1 – трехшаговый шнек; 2 – ленточный скребковый конвейер; 3 – асфальтобетонная смесь;
4 – стенка бункера перегружателя
Приложение В
(справочное)
План потока при устройстве асфальтобетонных слоев на основе применения двух перегружателей
1 – поливомоечная машина; 2 – автогудронатор; 3 – автомобиль-самосвал;
4 – перегружатели асфальтобетонной смеси; 5 – асфальтоукладчик;
6 – отряд катков согласно выбранному режиму уплотнения
Содержание |
|
Раздел 1. |
3 |
Раздел 2. Нормативные ссылки |
3 |
Раздел 3. Термины и определения |
3 |
Раздел 4. Основные технологические операции с применением машин – перегружателей асфальтобетонной смеси |
3 |
Раздел 5. Порядок устройства асфальтобетонных слоев на основе применения перегружателей асфальтобетонной смеси |
4 |
Раздел 6. Контроль качества |
5 |
Библиография |
7 |
Ключевые слова |
8 |
Приложение А (справочное) Принципиальная схема перегружателя асфальтобетонной смеси |
9 |
Приложение Б (справочное) Принципиальная схема трехшагового шнека |
10 |
Приложение В (справочное) План потока при устройстве асфальтобетонных слоев на основе применения двух перегружателей |
11 |
Технологии укладки асфальта.

Дороги считаются «артериями» сложного «организма» любой страны. От их качества в первую очередь зависит процент возникновения аварийных ситуаций. При проектировании дороги учитывается целый ряд факторов: будущая нагрузка от автотранспорта, природные условия, близость залегания грунтовых вод и даже хозяйственная деятельность человека в районе прокладки дорожного полотна. Мало просто уложить хороший асфальт, его необходимо своевременно ремонтировать и осуществлять грамотное обслуживание. Налаженное транспортное сообщение провоцирует к возникновению новых населенных пунктов или возрождения старых, строительству промышленных и коммерческих объектов, а так же развитию хозяйственной и культурной деятельности человека. Соответственно новые дороги играют роль активного участника в развитии общества по разным направлениям. Существует несколько вариантов укладки дороги, а процесс ее строительства является сложным и многоэтапным. Рассмотрим в действительности или нет, сложна технология асфальтирования дорог.
Виды асфальтирования
На данный момент технология асфальтирования дорог бывает двух видов. Эти виды получили свои названия в соответствии с температурой асфальтобетонной смеси, которая при них используется.
- Горячий метод.
- Холодный метод.
Разница в степени вязкости битума в разных типах смесей, что и определяет температурный режим укладки. Метод с применением холодной смеси применяется все чаще. Он имеет ряд своих преимуществ:
- Его можно использовать зимой и в дождливую погоду.
- Температуру смеси постоянно поддерживать не нужно.
Но, к сожалению, этот способ удобен только для текущего ремонта. При строительстве новой дороги или во время капитального ремонта специалисты все же используют старый, верный способ горячего асфальтирования. Именно горячая смесь по поверхности распределяется лучше и хорошо уплотняется, соответственно можно говорить о более длительных сроках эксплуатации такого дорожного покрытия. Горячая асфальтобетонная смесь до момента использования должна быть строго определенной температуры (не ниже 120 градусов). Для ее поддержания используется специальная техника. При снижении температуры до определенного уровня смесь считается испорченной и непригодной к применению.
Интересно знать: кстати, ранее существовала еще и третья технология асфальтирования дорог, но в нулевых это определение исчезло из официальных терминов. Введение нового ГОСТа оставило место только двум технологиям, признав третью малоэффективной, а потому и нежизнеспособной. «Теплое» асфальтирование осуществлялось при температуре смеси не ниже 70 градусов. В качестве жидкой основы в этих смесях использовались жидкие и вязкие битумы.
Особенности материалов
Асфальтобетон является смесью, используемой в строительстве дорожных покрытий, состав которой оптимально подобран на основе минералов. В качестве минералов используются: песок, щебень, жидкий битум или битумная эмульсия, минеральный порошок. В соответствии с ГОСТом в зависимости от того, какой каменный материал лежит в ее основе, смесь классифицируется на три типа:
- Песчаные.
- Гравийные.
- Щебеночные.
Существует еще одна классификация, которая основывается на размерах минеральных зерен в смеси:
- Мелкозернистые.
- Песчаные.
- Крупнозернистые.
При этом холодные смеси могут быть исключительно песчаными или мелкозернистыми. Так же выделяют еще три группы по проценту содержания гравия или щебня (каменной составляющей):
- Группа В около 30-40%.
- Группа Б около 40-50%.
- Группа А около 50-60%.
Именно твердые «ингредиенты» асфальтной смеси после укатывания заполняют собой все образующиеся воздушные полости.
Также существует исключительно «горячая» классификация по остаточной пористости материала, то есть по процентному объему «пор» в материале после его уплотнения. Она, как вы уже поняли, используется только для горячих асфальтобетонных смесей:
- Пористые.
- Плотные.
- Высокопористые.
- Высокоплотные.
Асфальтобетонную смесь применяют не только в качестве основы для дорожных покрытий, хотя здесь она себя зарекомендовала, как один из наиболее надежных и экономичных материалов. Асфальт используют для покрытия площадей, аэродромов, садовых дорожек, частных дворов и полов в помещениях промышленного назначения.
Интересно знать: все виды асфальта подразделяются на два типа: натуральные и искусственные. Искусственные применяются повсеместно. Проезжая по городу вы имеете дело именно с искусственно созданным асфальтом. Натуральные образуются после испарения нефти и состоят из ее тяжелых остатков.
Горячий способ
Горячая смесь известная своей «выносливостью». Она способна выдерживать колоссальные нагрузки, поэтому применяется для строительства и ремонта оживленных дорог, с высокой проходимостью автотранспорта. Для приготовления смеси необходимо обеспечить температуру 100-130 градусов. Превышать или занижать температурную планку категорически запрещено, поэтому без специальной техники в этом деле не обойтись. При засыпании минерального порошка и щебня температура уже должна достигать 100 градусов. Параллельно битум разогревается до кипения. Компоненты непрерывно перемешиваются. Смесь сразу же доставляется к месту проведения работ или замешивается сразу же «не отходя от кассы». Укладывать асфальт тоже нужно быстро. Недопустимо создание «швов». Последующие слои должны укладываться на еще горячий предыдущий. Во время работы с горячей смесью возможно ее «прилипание» к катку. Чтобы этого избежать, покрытие постоянно смачивают водой. Для применения такого «чувствительного» материала необходима команда специалистов, которая обеспечит слаженную работу.
Холодный способ
Холодный способ начал применяться не так давно, но его удобство уже успели оценить большинство компаний по ремонту и строительству дорог. Использование холодной смеси позволяет сразу же после укладки эксплуатировать покрытие, что наиболее удобно для срочного ремонта в районах оживленных участков дорог: перекрестков, крупных дорожных развязок, перед светофорами. Такая технология асфальтирования дорог позволяет применять смесь в плохую погоду. Дождь или снег не станет помехой для укладки холодного асфальта. Эта смесь выдерживает и сильные температурные перепады: от +50 и до -25 градусов.
Как вы видите, ни лютые морозы, ни «адская жара» не станет помехой для проведения качественных дорожных работ. Холодная смесь просто хранится в специальной упаковке при комнатной температуре. Никаких манипуляций с ней проводить не нужно, она уже готова к использованию. Используется этот материал только для ремонтных работ. Он отличается довольно высокой стоимостью. К сожалению, его прочность тоже оставляет желать лучшего, поэтому при строительстве автострад и основных дорог холодная смесь не применяется. Хотя в характеристиках материала и заявлена возможность укладки при высоких температурах, прочность покрытия сильно «страдает» именно летом.
Какие этапы включает в себя технология асфальтирования дорог
Ремонт или строительство новой дороги всегда начинается с проектирования. Этот этап самый первый и один из наиболее важных. Неверно составленный проект дороги впоследствии может привести к необходимости ее замены и повторному строительству. Поэтому, чтобы не пополнить ряды тех самых скупцов, которые платят дважды, лучше не экономить на проектировании. Затем место под дорогу тщательно расчищают от растительности. Затем с помощью погрузчиков и бульдозеров снимают верхний слой грунта. Грейдерами разравнивают поверхность образовавшейся «траншеи». В соответствии с отметками формируют так называемое дорожное корыто и хорошенько уплотняют его.
Следующим этапом станет формирование дорожной подушки. Именно она в будущем будет отвечать за равномерную нагрузку от транспорта и предотвратит проседания дорожного полотна. «Подушка» состоит нескольких слоев «наполнителя»:
- Песок или смесь гравия и песка.
- Крупный щебень.
- Мелкий щебень.
Щебень засыпается для упрочнения всей «подушки», а мелкий щебень необходим для заполнения пустот. Все слои обязательно трамбуются грейдером. Толщина слоя щебня будет напрямую зависеть от назначения будущего полотна. К примеру, для пешеходных дорожек достаточно и 5 см, а для дорог, по которым будет следовать грузовой транспорт толщина слоя должна достигать 30 см. Бортовой камень устанавливают по бокам будущей дороги. После завершения формирования «подушки» ее проливают битумом для лучшего закрепления будущего покрытия.
На заключительном этапе строители приступают непосредственно к укладке самой асфальтобетонной смеси. Ее либо готовят сразу же на месте работ (чаще всего в случаях масштабного строительства), либо привозят на специальной технике. Смесь равномерно распределяют по «подушке», а затем трамбуют несколькими асфальтоукладчиками. Укладывают асфальтобетон в несколько слоев, что добавит прочности покрытию.
Интересно знать: если речь идет не о строительстве новой дороги, а о ремонте, то этап подготовки грунта заменяется этапом снятия старого асфальта.
Покрытие обрабатывается фрезой, и его поврежденные куски вырезаются. В дальнейшем их либо собирают и вывозят, либо используют на вторичной переработке в специальной машине — рециклере.
Заключение
Качественная технология асфальтирования дорог зависит от множества факторов, среди которых можно выделить качество сырья и его правильный подбор, технологию укладки асфальта, разработку правильного проекта и привлечение высококвалифицированных специалистов. Недопустимо укладывать горячий асфальт в морозы прямо на снег или осуществлять ремонт дорожного покрытия «кирпичной кладкой». Многие видели примеры подобного «головотяпства», которое говорит о полной профнепригодности некоторых «специалистов». Грамотная технология асфальтирования дорог по всем правилам позволит сэкономить не только на ее ремонте, но значительно продлит сроки эксплуатации. Одна из трех главных российских бед по-прежнему остается актуальной, несмотря на скачок в развитии современных технологий и инновационные разработки, связанные с составом сырья и дополнительной техникой, которая позволяет совершать вторичную переработку старого асфальта.
07.08.2017
Принципы уплотнения.
Уплотнение асфальтового покрытия происходит слоями. При соблюдении технологии уплотненный асфальт состоит нескольких слоев:- нижний слой;
- связующий слоя;
- слой износа.
Асфальтобетон должен быть уплотнен до такой степени, чтобы повысилась плотность или снизилась пористость асфальтового слоя. Количество воздушных полостей должно быть снижено до рекомендованных значений, чтобы достичь требуемой степени уплотнения.
В результате обеспечивается улучшенная стабильность слоя и, таким образом, повышается его сопротивляемость деформации. От степени уплотнения также зависит износоустойчивость поверхностного слоя.
Вместе с уплотнительными работами, должна одновременно происходить выравнивание, чтобы обеспечить комфорт во время езды, поэтому слой износа должен иметь сплошную и гладкую поверхность, но обеспечивать максимальное сцепление колес с дорогой.
Асфальтовая смесь может быть различной по составу в зависимости от предназначения (необходимо учитывать характер нагрузки на дорожное полотно) и климатических условий. Именно поэтому рецептура асфальтовых смесей меняется, а вместе с ней и уплотнительные свойства асфальта. На свойства влияет прежде всего состав и размер включаемых в ее состав минеральных компонентов. Еще одним важным компонентом, от которого зависит вязкость, является битум и его температура.
Для дорог с интенсивной эксплуатацией используют смеси с высокой устойчивостью к деформации при нагрузках. Как правило, в такие смеси включают крупноразмерные минералы, т.е. они содержат большое количество камней крупных фракций, дробленых камней в дробленом песке и густой битумный раствор. Такие смеси весьма тяжелы в уплотнении и требуют большое количество усилий и тяжёлую технику.
При накатке дорог с низкой интенсивностью эксплуатации используют смеси с меньшим содержанием камней и значительно большим количеством песка, а также мягкий битумный раствор. Такие смеси легко уплотняются, однако из-за своих характеристик легко могут быть деформированы при укладке, поэтому требуют особого контроля и время на застывание. При нарушении технологического цикла может происходить смещение самого материала или формирование волн на дорожном полотне.
Влияние температуры смеси на уплотнение
На усилия, требуемые для укладки асфальта влияет температура смеси. Как правило уплотнение начинают, когда температура падает до 140-100 градусов и закончено, когда смесь остынет до 100-80 градусов. Такие требования к температуре обусловлены свойствами битума, входящими в состав смесей: чем ниже температура битума, тем больше его вязкость и тем больше усилий потребуется катку для уплотнительных работ. При высоких температурах битум действует как смазка и снижает трение между вальцами катка и минеральными включениями.Способы уплотнения
На первоначальном этапе предварительное уплотнение производится асфальтоукладчиком. Предварительное уплотнение с помощью этого типа техники оказывает отличное влияние на первоначальный слой и его характеристики, а также способствует более качественной последующей укатке катком, пока температура смеси достаточно высокая.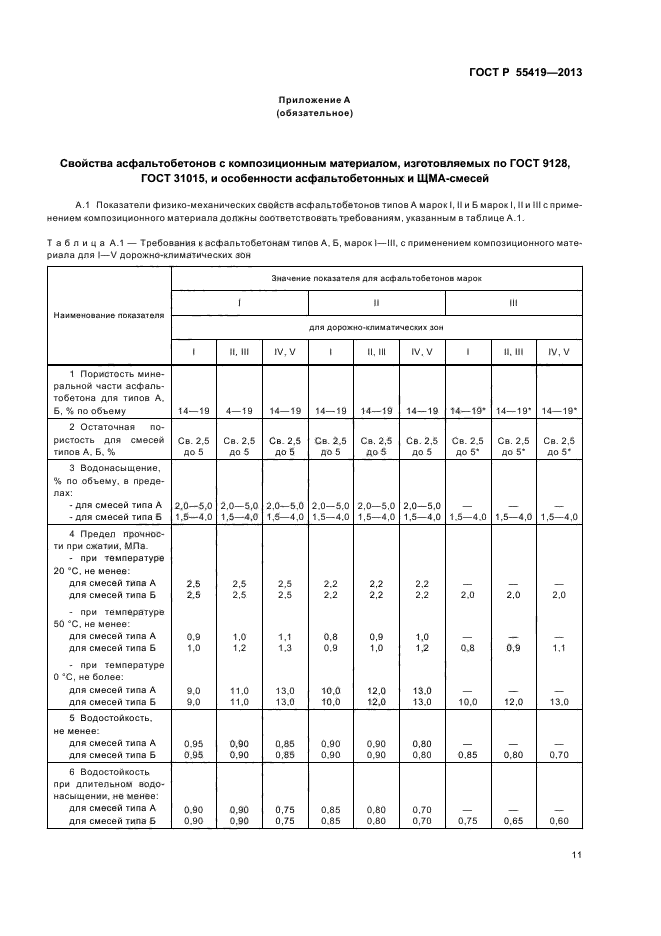
Если приступить к укатке без предварительного уплотнения, то можно нарушить раномерность покрытия, если каток окажется слишком большой массы, а то и вызвать смещение материала. Если все-таки производится укладка катком, то рекомендуется в первые два прогона тандемными катками не использовать режим вибрации.
За счет собственной массы катка, происходит статическое уплотнение асфальта, для этих целей используют и тандемные и катки на пневмоколесах, однако они дают довольно слабое уплотнение по сравнению с вибрационными катками. Тандемные катки уплотняют за счет линейной нагрузки (кг/см) вальца, а пневмоколесные за счет нагрузки от колес (т) и давления воздуха в колесах (Мпа).
Использование этих двух типов целесообразно только после предварительно уплотнения асфальтоукладчиком, или при необходимости уложить тонкий слой (слой износа) или асфальт с высокой пористостью.
Пневматические катки хорошо показали себя на предварительном профилировании и уплотнении мягких смесей или для уплотнения покрытия дорог с малой интенсивностью движения. В ходе работы пневмокатка смесь равномерно распределяется, а поверхностные поры заполняются.
Вибрационные катки широко применяются за счет отличных рабочих характеристик и качественного уплотнения. Им требуется меньшее количество проходов., за счет чего значительно экономится время. Вибрация от катка снижает трение материала внутри смеси, а за счетмассы катка и динамической нагрузки плотность асфальтового покрытия растет. Таким образом для виброкатка ключевыми показателями являются масса и показатели вибрации: частота и амплитуда.
Если предстоит уплотнить покрытие из нескольких слоев, то использую тяжелые тандемные виброкатки, которые способны выдавать различные амплитуды и частоты вибрации вальцов.
Рабочая скорость для таких катков колеблется от 3 до 6 км/ч.
Однако использовать виброкатки нужно с осторожностью, так как большое количество проходов может привести к разрыхлению материала и нарушению структуры покрытия за счет избыточной вибрации.
Уплотнение катками с использованием автоматизированной системой контроля степени уплотнения (АСФАЛЬТ МЕНЕДЖЕР) ASPHALT MANAGER
Для контроля степени уплотнения и регулировки требуемого усилия используются автоматизированные системы.Благодаря такому инструменту, оператор имеет возможность работать в автоматическом режиме без дополнительных регулировок в ходе работы. Уплотнительная техника с АСФАЛЬТ МЕНЕДЖЕР регулируется автоматически и непрерывно отслеживает текущие условия и при необходимости изменяет величину и амплитуду вибрации. Как следствие, применение системы дает возможность избежать повреждения слоя основания и разрушения структуры асфальтового слоя. Помимо автоматического режима, каток позволяет оператору выбирать определенное направление вибрации в ручном режиме, их всего шесть (от вертикального до горизонтального (подобно осцилляции).
Катки с системой АСФАЛЬТ МЕНЕДЖЕР способны выполнять широкий спектр задач по уплотнению асфальтовых покрытий. Благодаря возможности выбирать различные режимы, такие катки могут использоваться при работах вблизи или внутри зданий чувствительных к вибрациям (например, многоуровневые паркинги). Для уплотнения асфальтовых покрытий мостов рекомендуется ручной режим с горизонтально направленной вибрацией.
Основные преимущества: Универсальное применение, качественное уплотнения без разрушения материала основания, уплотнение равномерным слоем благодаря непрерывному изменению усилия уплотнения, гладкость и однородность структуры асфальтового слоя, возможность уплотнения участков, расположенных у края дорожного полотна, а также стыков. Отлично подходит для укладки асфальтовых покрытий на мостах, а также в непосредственной близости от чувствительных к вибрациям сооружений. Есть возможность измерения степени уплотнения и температуры во время работы.
Оборудование для уплотнения
Ручное оборудование для уплотнения | |
| Вибротрамбовки (трамбовки) относятся к средствам малой механизации.![]() |
| Виброплиты также относятся к малой механизации и используются для уплотнения небольших площадок в ограниченном пространстве, они бывают прямоходные и реверсивные, их масса колеблется в диапазоне 50-150кг, а рабочая ширина- от 45 до 60 см. Они оснащаются бензиновыми или дизельными двигателями. Вибратор направленного действия приводится в действие через клиновой ремень и центробежную муфту. Управление движением происходит за счет регулировки направления действия вибратора. |
| Масса сопровождаемых катков составляет 600-1000 кг, а рабочая ширина – от 60 см до 75 см.![]() |
| Легкие с рамой на шарнирном соединении выпускаются массой от 1,3 до 4.2 т, рабочей шириной от 80 см до 138 см. оба вальца катка оснащены гидростатическим приводом и вибросистемой. |
| В основе конструкции вибровалец и комплект колес. Они отлично подходят для уплотнения асфальта на поверхностях под уклоном, а также для ремонтных работ и укатки пешеходных дорожек и автостоянок. Комбинированные катки производятся массой от 1,5 до 2,5т, а также от 7 до 10 т. |
| Управляемая/качающаяся передняя осью и неподвижный задний мост – преимущество конструкции пневмоколесных катков. Для увеличения массы может быть задействован балласт массой до 10т, при этом общая масса может быть увеличена до 24-27 т соответственно. Уплотнение происходит статически, за счет собственной массы машины, а также перемешивания смеси и прогибанию колес.![]() |
| У масса может достигать 7-14т при рабочей ширине 1,50 м, 2,00м и 2,13 м; они предназначены для средних и крупных строительных объектов. Вибрация может осуществляться на передний, задний или сразу на оба вальца, а сами они могут быть цельные и разрезные. Они всегда следуют один за другим, даже при выполнении поворотов(влево/вправо). В стандартном исполнении вальцы оснащены крабовым ходом со смещением самих вальцов до 120 мм в обе стороны. Крабовый ход значительно облегчает уплотнение у краев покрытия, а также дает возможность огибать боковые препятствия. |
| Тандемные катки с управляемыми вальцами выпускаются массой от 7 до 10 т, рабочей шириной 1,50 м и 1,68 м. Такие катки оснащены гидростатическим приводом вальцов и вибросистемы. Вибрация может передаваться на передний и /или задний валец, а сами вальцы могут быть цельные и разрезные. Катки с управляемыми вальцами оснащены электрической системой управления с возможностью выбора настроек: Диагональный ход (влево/вправо), поочередная работа передним \ задним управляемым вальцом, синхронное работа обоими вальцами, или управление передним \задним вальцом в автоматическом режиме, в зависимости от направления движения |
На катках с управляемыми вальцами они могут поворачиваться одновременно (синхронное управление) или каждый по отдельности (передний или задний), а также позволяют двигаться крабовым ходом (со смещением вальцов до 120 мм).
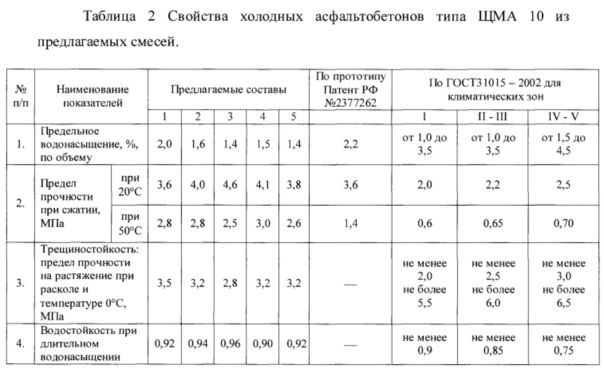
У катков с управляемыми вальцами возможность движения «крабовым ходом» является преимуществом. «Крабовый ход» позволяет распределять массу катка на большую площадь, при этом сам каток не сильно заглубляется. При использовании такого метода, значительно упрощается начальное уплотнение чувствительных материалов с высокой температурой асфальта, а также возможна «утюжка» больших участков, а сам центр тяжести катка смещен от нестабильного края асфальтового покрытия.
В тандемных катках с шарнирно-сочлененной рамой вальцы соединены между собой с помощью центрального шарнира.
Конструкция позволяет вальцам двигаться по одной траектории даже при выполнении поворотов. В режиме «крабового хода» задний валец смещен относительно переднего влево или вправо. Из-за особенностей конструкции вальцы могут быть смещены относительно друг друга.
Выгоды от использования «крабового хода» очевидны: это и возможность работы вблизи бордюрных камней или вплотную к стенам зданий или ограждениям, рациональная работа с конусом уплотнения края покрытия, а также возможность избежать образование следов от вальца с острыми кромками на поверхности асфальта.
Асфальт пока остается самым популярным видом покрытия для дорог, не смотря на постоянное появление на рынке современных дорожных материалов. Он практичен в применении, долговечен, износоустойчив и стоек к воздействию окружающей среды. Правильно заасфальтированные дорога или даже садовая дорожка будут служить верой и правдой владельцу участка много лет, не требуя ремонтных и восстановительных работ.
Как положить асфальт своими руками
Если вам нужно положить асфальт, можно воспользоваться услугами специализированной фирмы, а можно выполнить все работы своими руками. Специализированную фирму можно выбрать на любой площадке по предоставлению данного вида услуг . Выбор зависит от того насколько вы уверены в своих силах и опыте. Неправильно уложенное покрытие может быстро разрушиться, деформироваться и пойти трещинами. Чтобы положить асфальт, например, на даче необходимо выполнить несколько этапов.
1. Подготовительные работы: нужно разметить места дорожек, учитывая местонахождение подземных коммуникаций.
2. Земляные работы: верхний плодородный слой грунта нужно снять. Для дорожек можно снять от 10 до 25 см, для дороги для автомобиля сделать котлован глубже. Чем больше будет планируемая нагрузка на дорогу, тем глубже должен быть котлован.
3. Подготовка основы: дно котлована необходимо уплотнить (лучший вариант — виброплита). Для того, чтобы на дорогу не действовали силы пучения, необходимо засыпать гравийную подушку — слой гравия крупной фракции толщиной до 15 см для дороги и до 10 см для пешеходных дорожек. Этот слой нужно также утрамбовать. Второй слой заключается в насыпании мелкофракционного гравия толщиной до 10 см и сверху речного песка. Все эти слои необходимо обильно пролить водой. Можно послойную подготовку заменить монолитной бетонной плитой — этот вариант обойдется дороже.
4. Покупка асфальта: асфальт лучше купить на ближайшем асфальтобетонном заводе в готовом состоянии. Так, даже с доставкой, он обойдется дешевле, чем если его готовить самостоятельно. 1 тонны асфальтобетона в среднем хватает на асфальтирование 10 кв.м. толщиной 10 см.
5. Укладка асфальтобетона: укладку нужно производить в солнечный день, в который не ожидается осадков сразу после доставки. Асфальт закидывают лопатой, а потом его уплотняют той же виброплитойили трамбовкой. В зависимости от нагрузки на будущую асфальтную поверхность укладка проводится в 1 или нескольких слоев. Для подъезда к дому достаточно уложить от 5 до 7 см., а для дорожек хватит и 3-4 см.
6. Уплотнение асфальтобетона — операция трудоемкая и необходимая. От качества уплотнения будет зависеть долговечность службы дороги. Уплотнять дорогу или дорожки можно различными ручными устройствами — виброплитой или ручным катком. Асфальт должен иметь температуру не ниже 105 градусов. Каток очень важно вести правильно в одном направлении.
Как положить положить тротуарную плитку на асфальт
Асфальт можно использовать в его первоначальном виде — как он есть. Но в этом случае он имеет небольшой недостаток — в летнюю жару он перегревается и начинает специфически пахнуть или может деформироваться при заезде на него тяжелых механизмов. Вдобавок все-таки это традиционное покрытие, которое может иногда надоесть. Для придания большей эстетичности дорожкам, их можно покрыть тротуарной плиткой.
Обычно, если хочется на асфальт положить тротуарную плитку сверху, прямо на покрытие кладут цементный раствор до 5 см. Примерно 1 часть цемента на 4 части песка — пропорция раствора. Уложенная цементная стяжка хорошо разравнивается длинным правилом. И уже на ней укладывается сверху тротуарная плитка. Уже за 3-7 дней в зависимости от погоды такой слоеный пирог асфальт-цементная стяжка-тротуарная плитка застывает настолько прочно, что можно возобновить движение автомобилей по ней или парковать автомобиль на этой площадке.
Если не хочется мучиться
Положить асфальт просто так легко и быстро самому не получится. Необходимо иметь специальное оборудование — ту же виброплиту или ручной каток, нужно уметь ими хорошо пользоваться, чтобы покрытие получилось ровным, а не ребристым и со швами. Необходимо быстро разбрасывать асфальтовую смесь после её приготовления, потому что иначе она остынет, а остывший асфальт придется дольше и тщательнее утрамбовывать. Вдобавок не забывайте, чтобы дорога или тротуар прослужили долго необходимо предусмотреть наличие дренажа, стока для воды, бордюров. Все это нужно делать одновременно с укладкой. Может возникнуть резонный вопрос: сколько стоит асфальтирование. На самом деле это не настолько огромная цифра из-за которой стоит рисковать качеством укладки и эстетикой будущих подъездов к дому.
Сколько стоит положить асфальт
Если вы ищете информацию сколько стоит асфальтирование дороги, необходимо учитывать, что стоимость зависит от объема выполняемых работ. Поэтому достаточно узнать сколько стоит асфальтирование 1 м2. Стоимость асфальтирования можно узнать по любой ссылке из выдачи поиска, например.
Советы мастера
Пред След
Чтобы масляная краска при хранении не засыхала и чтобы на ней не образовывалась пленка, положите на поверхность краски кру жок из плотной бумаги и»залейте его тонким слоем олифы.
» Полиэтиленовую пленку, укрывающую балкон или теплицу, предо хранит от обрыва ветром бечева, натянутая с обеих сторон с про межутками 10-15 см. «
» Чтобы работать с бетонной смесью было легче, в нее обычно добав ляют глину, но глина снижает прочность смеси. Добавьте в нее ложку стирального порошка из расчета на ведро воды. «
» Чтобы винт, головка которого скрыта за преградой, не вращался вместе с затягиваемой гайкой, нужно накинуть на него несколько витков нитки или тонкой проволоки и слегка натянуть концы. За счет трения винт хорошо удерживается на месте. Концы нити по сле затяжки можно обрезать. «
» Вырезать леток скворечника можно и без коловорота. Достаточно расколоть лицевую сторону доски по центру и вырубить стамеской или топориком полуотверстия необходимого размера, после чего вновь соединить половинки. «
Деревянные пробки для шурупов рассыпаются и выпадают из сте ны. Не торопитесь вырезать новую пробку. Плотно набейте отвер стие в стене капроном от старого чулка. Нагретым докрасна гвоз дем подходящего диаметра выплавьте отверстие для шурупа. Ра сплавившийся капрон превратится в прочную пробку.
» Плотницкий уровень нетрудно превратить в теодолит, снабдив его прицельным устройством из прорези и мушки. «
» Чтобы две полосы линолеума легли встык, удобно воспользоваться самоклеющейся декоративной пленкой, подложив ее,под основу ли нолеума. «
» Чтобы гвоздь шел в нужном направлении и не гнулся при заби вании в глубокое отверстие или паз, следует поместить его внутрь трубки, зафиксировав с помощью мятой бумаги или пластилина. «
Перед тем как долбить отверстие в бетонной стене, закрепите чуть
ниже листок бумаги. Пыль и осколки бетона не будут разлетать
ся по комнате.
» Чтобы отрезать трубу точно под прямым углом, советуем посту пить так. Возьмите ровную полоску бумаги и наверните ее на трубу по линии отпиливания. Плоскость, проходящая через кром ку бумаги, будет строго перпендикулярна оси трубы. «
» Ворочать бревна или деревянные балки поможет несложное при способление — отрезок мотоциклетной или велосипедной цепи, до полненный крюком с одной стороны и закрепленный к лому хому том с другой стороны. «
» Для того чтобы одному можно было работать двуручной пилой, советуем использовать простой прием: переставить ручку пилы из верхнего положения в нижнее. «
Вырезать кусок шифера необходимого размера можно пилой, но лучше и проще пробить по линии предполагаемого разреза гвоздем дырки с частотой 2-3 см, после чего обломить шифер на опоре.
» Лучший способ приклеить кафель к стене: взять битум, расплавить и капнуть всего четыре капли по углам плитки. Приклеивается на мертво. «
Фасонные отверстия при изготовлении фигурных оконных налични ков удобнее всего выпиливать ножовкой с обточенным полотном.
» Изготовление витражей — дело долгое и нелегкое. Можно сделать быструю имитацию витража. Для этого берут тонкие реечки или прутья лозы, приклеивают к листу стекла, а затем раскрашивают стекло и покрывают его лаком. «
» Если под рукой не оказалось дюбеля, его можно изготовить из куска пластмассовой трубки. Для этого может подойти и корпус шари ковой ручки. Отпилив кусочек нужной длины, сделайте продоль ный надрез, примерно до половины, и дюбель готов. «
» Известно, как трудно навесить дверь, работая в одиночку. Но вот достаточно укоротить нижний штырь на 2-3 мм и работать станет гораздо проще. «
» Очень прочная, безусадочная и достаточно водостойкая шпаклевка получается из бустилата, смешанного с любым порошком — ме лом, гипсом, цементом!, опилками и т. д. «
» Если нужно ввернуть в торец древесно-стружечной плиты шуруп, высверлите отверстие чуть меньше диаметра шурупа, заполните отверстие клеем «Момент» (только не эпоксидным!), через сутки вверните шуруп. Плита не расслаивается. Однако под нагрузку полученное соединение можно ставить только через сутки. «
» Закреплять портреты, фотографии, картины в деревянные рамки со стеклом удобнее не гвоздиками, а с помощью канцелярских кно пок, согнутых под прямым углом. Кнопки мягко вдавливают отверт кой. По сравнению с гвоздями опасность расколоть тонкие рамки сводится до минимума. «
» Завернуть шуруп в твердые породы дерева не так-то просто. Если наколоть шилом отверстие для шурупа, а сам шуруп обильно на тереть мылом, то после такой операции работа пойдет как по маслу. «
В целях экономии времени кромку обоев можно обрезать острым ножом, не разворачивая рулона. Для этого надо предварительно выровнять торец рулона и простым карандашом обвести снаружи границу Кромки. Работая ножом, рулон необходимо постепенно поворачивать в направлении свертывания.
Для переноски в домашних условиях больших листов фанеры, стек
ла или тонкого железа удобно пользоваться проволочным держа
телем с тремя крючками внизу и ручкой вверху. н»тЪ на 1/3 высоту зубьев.
Если на переднюю часть станка лучковой пилы прикрепить груз весом примерно килограмм, то работать станет легче. Груз нужно делать съемным, чтобы пилой можно било выполнять и другие работы.
» Покрытие, напоминающее восковое, можно получить, окрасив по верхность разведенным клеем ПВА. Чтобы получить нужный цвет, нужно развести клей водой, подкрашенной акварелью. «
» Сделать чехол на лезвие топора- проще простого. Берется кусок, резиновой трубки, разрезается вдоль и надевается на лезвие. От соскакивания ее предохраняет кольцо, вырезанное из старой авто мобильной камеры. «
» Обойтись без струбцин при склеивании деревянных рам поможет бельевой шнур. Следует надеть четыре короткие петли на углы рамы и двумя длинными стянуть рамы по диагонали. Углы регу лируются с помощью палок, которыми скручиваются средние петли. «
» Как заставить замолчать скрипящую половицу? Между половица ми нужно просверлить отверстие под углом 45° диаметром 6-8 мм, забить в него деревянный штифт, смазанный столярным клеем, сре зать стамеской выступающий конец и зашпаклевать поверхность пола. «
» Чтобы облегчить циклевку пола, покрытого лаком или краской, прогладьте его утюгом через влажную тряпку — и работать ста нет легче. «
» Небольшое загнивание на древесине можно ликвидировать так: пораженную древесину удаляют от здорового слоя, а затем пропи тывают 10-процентным раствором формалина. После высыхания участок зашпаклевывают и закрашивают. «
Самым популярным методом покрытия дорог и тротуаров, отвечающим современным понятиям о качественном покрытии и цена которого, к тому же, сравнительно невысока, можно назвать асфальтирование. Но помимо самой смеси надёжность и эффективность укладки примерно, на 50% зависит от подготовительных работ, то есть от подушки, служащей черновым основанием для лицевого слоя.
Ниже мы поговорим о технологии данного производства, а также обратим внимание на демонстрацию тематического видео в этой статье, касающегося нашей темы.
Асфальт на дороге
Примечание. Название происходит от греческого ἄσφαλτος что подразумевает горную смолу, где 60%-75% битума смешаны с минералами.
В искусственном варианте битум ограничен количеством от 13% до 60%, а наполнителем служит гравием/щебнем, песком и минеральным порошком.
Этапы производства
- В первую очередь технология укладки асфальтобетонной смеси, впрочем, как и другие строительно-монтажные работы, зависит от планировки, следовательно, перед началом производства должен быть составлен технический проект и финансовая смета . Затем следует разметка с привязкой к особенностям рельефа данной местности, чтобы обеспечить возможность отвода сточных вод и проходящих вблизи подземных и наземных коммуникаций. Кроме того, большое значение имеет наличие больших деревьев с развитой корневой системой — при необходимости их вырубают, чтобы в дальнейшем не возникало проблем.
- По окончании подготовительных работ снимается верхний, влажный слой грунта с помощью экскаватора или бульдозера, где глубина, в первую очередь, будет зависеть от эксплуатационного назначения данного участка . Например, для асфальтирования тротуара или садовых дорожек вполне достаточно 10-25 см глубины, но для проезжей части этого, конечно, недостаточно — чем больше планируемая нагрузка, тем глубже придётся закладывать основание.
- Кроме того, технология укладки асфальтобетона подразумевает обязательное устройство дренажной системы — вода не должна скапливаться ни на покрытии, ни под ним . В связи с этим очень важно убрать весь грунт, который был снят при подготовке основания, чтобы в период дождей его не размыло, и он не забил дренажную систему.
- После окончания проведения земляных работ возможна укладка асфальта на бетонное основание (жёсткая подушка) или на щебневое (гравийное) с песком (нежёсткая подушка) и это опять-таки зависит от будущей степени нагрузки при эксплуатации участка по СНиПу 06.03-85 . Например, для пешеходных дорожек высота песочно-щебневой подушки может составлять всего 5-10 см, но если это проезжая часть с малой интенсивностью движения (подъезд к дому или воротам), то здесь уже высота составит от 10 см и более. Причём, при условии, что во время эксплуатации предвидятся большие нагрузки, подушка укладывается по слоям — вначале гравий (фракция 40-60 мм), затем, щебень (фракция 20-40 мм), а поверх них — крупный речной песок.
Примечание. Для того чтобы ускорить усадку подушки перед укладкой асфальта, её обильно поливают водой. Когда подсыпка усаживается, она, к тому же, приобретает дополнительную прочность. Утрамбовка производится виброплитами, катками, а в домашних условиях это можно даже делать своими руками с помощью какой-либо биты.
- В тех случаях, когда на проезжей части предусматривается очень интенсивное движение и, следовательно, большая механическая нагрузка, тогда для основания применяется бетонирование или укладка железобетонных плит, как это показано на верхнем фото . В связи с высокой стоимостью такого типа покрытий в нашей стране их делают крайне редко и по большей части такие конструкции ограничиваются применением для взлётно-посадочных полос или испытательных полигонов.
- Наиболее выгодно использовать в качестве подсыпки строительный мусор — битый кирпич, камень, старые битые плиты, блоки и перекрытия, цементно-песочную штукатурку и так далее . Примечательно, что при достаточной трамбовке таких материалов они ничуть не уступают тому же щебню или гравию, при этом себестоимость подушки резко уменьшается — ведь мусор, вместо его утилизации, используют, как строительный материал. Но здесь, безусловно, значительно увеличивается трудоёмкость процесса — ведь такие отходы, как правило, имеют очень большую фракцию и из-за этого их сложнее утрамбовывать (приходится разбивать).
Примечание. Закладка основания ( подушки) подразумевает наличие отбортовки, которая выполняется из камней или специальных железобетонных бордюров — это позволяет формовать будущее покрытие. Кроме того, формовки также требует и укладка асфальта, следовательно, высота бордюра должна быть рассчитана на лицевое покрытие.
Технология укладки
В настоящее время укладка асфальта в Российской Федерации производится в согласии с ГОСТ 9128-2009 по асфальтобетонным дорожным и аэродромным смесям, причём инструкция, данная в этом документе применима и для укладки подобных покрытий в частном порядке (на дачных и загородных участках). Обычно асфальтобетон заказывают на ближайшем пункте его изготовления — это предпочтительнее кустарного производства.
Асфальтных заводов, в том числе и небольших, достаточно много, так что покупка готовой смеси обойдётся гораздо дешевле, нежели её самостоятельное изготовление, к тому же, пропорции Госстандартов проще соблюдать при поточном производстве, нежели при разовом изготовлении.
Важно учитывать, что температура воздуха на улице, должна быть не ниже 5ᶛC, причём производственный процесс должен осуществляться в сухую погоду — монтаж во время дождя категорически запрещён! При нарушении данных условий уже на следующий год после укладки будет наблюдаться растрескивание и эрозия покрытия, к тому же износостойкость асфальта значительно понизится.
Чтобы вычислить количество расходуемого материала на определённом объекте, вам нужно будет вычислить площадь участка и определиться с его толщиной — для слоя асфальта высотой 10 см и площадью 10м 2 понадобится одна тонна раствора.
Порядок укладки и уплотнение
Технология укладки асфальта на бетонное основание или на песочно-щебневую подушку подразумевает выполнение работ без малейшего промедления после того, как самосвал с раствором прибыл на строительный участок — это одна из важнейших граней требований ГОСТов и СНиПов.
Для большого объёма, например, автомобильной дороги, при монтажных работах применяются специальные автоукладчики и большие самоходные катки, но при обустройстве тех же тротуаров приходится использовать лопаты и швабры. Кроме того, малые участки не всегда можно утрамбовать даже маленьким самоходным катком, поэтому, в таких случаях используются вибрационные плиты.
Если вы производите подобные работы на приусадебном участке, то вряд ли вы станете приглашать туда проектировщика, но, тем не менее, вам придётся придерживаться определённых параметров толщины покрытия. Поэтому, для садовых дорожек можете выдерживать слой высотой 3-4 см, в то время как для подъездных путей (если там не предусмотрена стоянка тяжёлых автотранспортных средств) потребуется толщина 5-7 см.
Качество укладки асфальтобетона и его эксплуатационный ресурс во многом зависят от правильного и вовремя сделанного уплотнения покрытия. Такой процесс можно осуществить тремя методами, это вибрация, укатка и трамбовка. Для этого можно использовать автоматический или ручной каток, вибрационный каток и вибрационную плиту.
По ГОСТ 9128-2009 температура укладки асфальтобетонной смеси должна выдерживаться не ниже 105ᶛC — это одна из предпосылок хорошего уплотнения укладываемого слоя — чем холоднее асфальтобетон, тем сложнее его утрамбовывать (больше проходов катком). Чтобы избежать налипания раствора на каток или вибрационную плиту, их можно смочить водой.
Чтобы вся поверхность получилась одинаковой, вам придётся следить за количеством проходов катка — оно должно быть одинаковым, к тому же, следует избегать реверсных движений, чтобы не нарушить целостность монолита.
Примечание. Если вам приходится производить укладку асфальта на склоне, то движение катка при уплотнении должно осуществляться только снизу вверх и никак иначе. Для разравнивания (ликвидации) образующихся в таких случаях швов движение катка осуществляется почти перпендикулярно — с тем же преимуществом движения снизу вверх.
Уход за асфальтным покрытием
Категорически запрещено допускать заезд тяжёлой гусеничной техники на такие покрытия — оно достаточно мягкое и траки обязательно оставят вмятины, которые, в свою очередь, будут способствовать разрушению. Кроме того, в жаркое время года противопоказан заезд тяжёлой колёсной техники, так как при таких температурах асфальт размягчается и опять-таки будет разрушен.
При необходимости следует вовремя заделывать все выбоины и трещины, чтобы они не вызывали дальнейшее разрушение структуры.
Виды асфальтобетона
Все асфальтобетонные смеси можно разделить на три основные группы, по виду минерального наполнителя — щебневые, гравийные и песочные. Кроме того, в соответствии с вязкостью используемого и укладочной температуры растворы могут быть горячими и холодными.
Так, горячие производятся с использованием дорожных вязких и жидких битумов и стелятся при температуре не менее 120ᶛC, в то время как холодные, с использованием тех же битумов — при температуре не менее 5ᶛC.
Асфальты могут быть крупнозернистыми, когда фракция наполнителя достигает 40 мм, мелкозернистыми, с фракцией до 20 мм и песочными, с фракцией наполнителя до 5 мм. При этом холодные смеси бывают только мелкозернистыми или песочными (крупный речной песок).
В соответствии с величиной остаточной пористости горячая асфальтовая смесь может быть: а) высокоплотным — остаточная пористость 1-2,5%; плотным — 2,5-5%; пористым — 5-10%; высокопористым — 10-18%. Для холодного асфальтобетона остаточная пористость допускается от 6% до 10%.
В зависимости от содержания щебня и гравия в горячей смеси их можно классифицировать по типам:
- А — содержит от 50% до 60% щебня;
- Б — от 40% до 50%;
- В — от 30% до 40%.
Кроме того, в зависимости от содержания гравия классифицируются на типы Бх и Вх. Горячие и холодные растворы могут быть типа Г и Гх, то есть, это песок из отсевов дробления или смесь с натуральным песком, если последнего не менее 30%. Типы Д и Дх основаны на натуральном песке или если он смешан с отсевом дробления, но при этом, его содержание не менее 70%.
Таблица маркировки смесей и асфальтобетонов
Примечание. Обработка застывшего асфальта практически идентична таким действиям, как резка железобетона алмазными кругами и алмазное бурение отверстий в бетоне. Но в этом случае лучше ориентироваться на прохладную погоду, так как при жаре битум будет налипать на круги, свёрла и корончатые фрезы, что создаст определённые неудобства в работе.
Заключение
Если укладка асфальтобетонной смеси производится у вас дома — на участке или возле него, то, скорее всего, вам не понадобятся высокоплотные асфальты первой марки. Тем не менее, как мы уже упоминали об этом выше, чтобы максимально продлить эксплуатационный ресурс, важно уделить особое внимание укатке и трамбовке не застывшего раствора.
Садовые дорожки должны иметь не только красивый внешний вид, но и обладать высокой прочностью, что бы по ним можно было перемещать тележку со стройматериалами и т.д. На сегодняшний день существует широкий ассортимент материалов для мощения дорожек, но большинство из них имеют высокую цену. Именно поэтому часто лучше всего заасфальтировать садовую дорожку, ведь асфальт является одним из наиболее дешевых стройматериалов. О том, как правильно асфальтировать дорожку, читайте далее!
Преимущество асфальтированных дорожек
Говоря об асфальте, сразу хочется сказать о том, что данный стройматериал имеет больше недостатков, чем преимуществ по отношению к дачному участку.
Асфальтное покрытие имеет всего несколько главных достоинств – дешевизна, высокая прочность, простая технология создания и универсальность. Часто асфальт выбирают только из-за того, что он имеет наиболее низкую цену, по сравнению с такими материалами для мощения садовых дорожек, как тротуарная плитка, брусчатка, деккинг, и т.д.
Недостатками асфальта являются очень весомые факторы, которые влияют не только на ландшафтный дизайн садового участка. Среди наиболее весомых недостатков выделают:
- В жаркое время асфальт испаряется и подвергает организм человека влиянию вредных веществ. Помимо этого сам неприятный запах не позволит насыщенно отдохнуть в саду, что нам и нужно.
- Асфальтное покрытие практически не обладает декоративной способностью, поэтому для украшения участка оно не только не подойдет, но и наоборот, ухудшит положение. Асфальтированные дорожки практически не вписываются в садовые стили, что тоже очень плохо. Единственное исключение – цветной асфальт, в который добавляются различные пигменты, благодаря чему покрытие может быть не только привычного серого цвета, но и зеленого, розового, синего и т.д.
- При некачественной укладке асфальт быстро разрушается в зимний период: вода попадает в трещины, замерзает, и когда размерзается – разрушает покрытие.
- Во время жары асфальт плавится.
Как вы видите, недостатки асфальтированного покрытия весомее преимуществ, но, несмотря на это, дорожки из асфальта рекомендуется сооружать на функциональных узлах сада: к примеру, между и . Категорически запрещается сооружать асфальтированные дорожки вблизи , из-за вредности асфальта.
Как положить асфальт своими руками?
Для того, что бы положить асфальт на даче своими руками необходимо тщательно подготовить местность, знать технологию укладки асфальта и иметь как минимум самодельный ручной каток для асфальтирования.
Следует сразу же обратить ваше внимание на то, что самостоятельно сделать асфальт очень трудно, т.к. необходимо разогревать битум, смешивать его с щебнем и добавками и знать правильные пропорции. Так как асфальт стоит не дорого, лучше всего заказать готовую смесь на предприятии по ремонту дорог. В данном случае вы потеряете не много денег, за то асфальт привезут вам прямо к месту укладки в горячем виде, останется только быстро разровнять его, утрамбовать и укатать.
Итак, перейдем ближе к делу!
Первым делом размечаем границы будущей дорожки из асфальта. На данном месте необходимо снять слой грунта (не менее 30 см, все зависит от предназначения дорожки) и позаботиться о том, что бы вблизи будущей дорожки не проходили корни деревьев, иначе вскоре они начнут разрушать асфальт. Если корни имеются, их вырубываем топором. После этого по всему периметру дорожки устанавливаем бордюры, которые и будут границами. Роль бордюр это не только предотвращение расползания асфальта, но и декоративная функция. Что бы установить бордюры выкапываем небольшую ровную траншею и садим их на цементный раствор в эту траншею. Для создания ровного бордюра натягиваем веревку от начала и до конца сторон дорожки и ориентируемся по этой веревке. В качестве бордюра можно использовать кирпичи, укладываемые не только на боковые грани, но и накось.
Далее приступаем к созданию подушки под асфальт. Дно траншеи для дорожки тщательно утрамбовываем, засыпаем в него первый слой – щебня (толщиной 10-15 см, фракция крупная) и опять-таки утрамбовываем. На этот слой засыпаем еще один слой щебня, но только уже более мелкой фракции, толщина слоя не более 10 см. Ну и последний слой – песчаный, около 5-10 см. Как только подушка будет создана, заливаем ее водой и, используя каток тщательно укатываем.
Для того, что бы вода не собиралась на асфальтированной дорожке, заранее сделайте небольшой слив: дорожку сооружайте под наклоном в 1-2 градуса и обзаведите ее небольшими дренажами, направляющими сток воды в почву.
Как мы уже говорили ранее, асфальт целесообразнее заказывать на заводе. После того, как асфальт доставят к вам на участок, необходимо немедленно переходить к его укладке, потому что раствор быстро застывает.
Первым делом раскидываем асфальт с помощью лопаты по всей площади дорожки, делая равномерное заполнение. Далее, используя швабру-движок, разравниваем асфальт по всей дорожке, при этом в ямы докидывая асфальт, а бугры разравнивая. Следует обратить внимание на то, что минимальная толщина асфальтного покрытия должна составлять не менее 5 см для обеспечения прочности , поэтому необходимо соблюдать данное требование.
Как говорилось ранее, асфальт быстро застывает, поэтому для создания дорожки лучше пригласить несколько помощников, что бы процесс осуществлялся быстрее.
Как только часть дорожки будет распланирована, берем ручной каток и начинаем укатывать данный отрезок, в то время как остальные дальше планируют дорожку.
Обязательное требование: перед тем как укатывать дорожку, смажьте каток соляркой, что бы асфальт не прилипал к нему и дорожка была идеально ровной. Соляркой так же можно смазать лопаты, что бы легче было бросать асфальт на дорожку.
Еще один вариант – залить поверх асфальтного покрытия бетонную стяжку. Это вариант является более простым, но в то же время бетонная дорожка станет далеко не идеальным дополнением садового декора, в отличие от дорожки из тротуарной плитки.
Это и все, что хотелось рассказать о том, как правильно укладывать асфальт своими руками, а так же как его ремонтировать либо заменять. Надеемся, что наша статья поможет вам в создании асфальтированной дорожки своими руками!
Рекомендуем также
В Подмосковье проверили качество 70% дорог от годового плана по ремонту
В Московской области провели экспертизу качества на более 1200 отремонтированных дорогах, что составляет 70% от общего плана ремонта на этот год. Отметим, ремонт региональных дорог ведется в рамках нацпроекта «Безопасные и качественные автодороги».
«В этом ремонтном сезоне недочеты и брак не превышают 7% от общего объема ремонтных работ, при этом на региональных дорогах – это не более 5%. Уже устранены замечания на 40 тысячах квадратных метрах покрытия, – сообщил министр транспорта и дорожной инфраструктуры региона Алексей Гержик. – Завершить экспертизу всех отремонтированных дорог и устранить замечания планируется до конца сентября, некачественно выполненные работы не будут оплачены».
В Подмосковье осуществляется всесторонний контроль ремонта дорог: проверяется качество поставляемых материалов на заводы, соблюдение технологии укладки асфальтобетонных смесей, включая температурный режим. Все данные заносятся в автоматизированную систему контроля и планирования работ в области дорожной инфраструктуры (СКПДИ).
«Ежедневно для проведения экспертизы ремонта дорог выезжает около 20 экипажей лаборатории. Места забора проб определяет рондомным способом СКПДИ, что позволяет сделать более «прозрачным» процесс экспертизы, — рассказал директор Производственной лаборатории по испытанию дорожно-строительных материалов «Лабрадор» Антон Батаев. – В ходе проверки отремонтированных участков выполняется отбор кернов. По результатам чего фиксируется толщина слоя асфальтобетонного покрытия, далее в лаборатории определяют качество уплотнения и свойства асфальтобетонной смеси. В среднем экспертиза занимает несколько суток».
В случае отсутствия замечаний и получения положительного заключения экспертизы, подрядная организация наносит разметку и завершает работы по обустройству обочин. При выявлении брака, подрядчик за свой счет переделывает работы. Всего в этом году в Московской области отремонтируют порядка 1,7 тысячи участков автодорог протяженностью 2 тысячи километров, в том числе благодаря нацпроекту «Безопасные и качественные автодороги» обновят покрытие на свыше 400 региональных дорогах длиной более 1,4 тысячи километров.
Современное исследование старения асфальтовых смесей и использования антиоксидантных добавок
Пагубные последствия твердения асфальтовых покрытий были впервые признаны первопроходцами в области дорожных покрытий в 1900-х годах и широко изучались в течение последних 70 лет. Этот процесс отверждения, называемый старением асфальта, обычно определяется как изменение реологических свойств битумных вяжущих / смесей из-за изменений химического состава во время строительства и срока службы.Старение приводит к тому, что асфальтовый материал становится жестким и хрупким, что влияет на его долговечность и приводит к высокому риску растрескивания. В данной статье представлены современные достижения в области старения асфальта и асфальтобетонных смесей и использования антиоксидантных добавок для замедления старения. Также обсуждаются картина сложной молекулярной структуры асфальта и ее изменений из-за атмосферных условий и различные протоколы, используемые для моделирования старения в лабораторных условиях. Особое внимание уделяется недавним исследованиям моделирования старения асфальтовых смесей, поскольку исследования смесей по сравнению с асфальтовым вяжущим были ограничены.Наконец, в этой статье представлено применение методов защиты от старения и его механизм, использование различных типов антиоксидантных добавок для замедления старения асфальта и, следовательно, улучшения характеристик асфальтовых покрытий.
1. Введение
Асфальт является наиболее широко используемым вяжущим материалом для дорожных покрытий во всем мире. Приблизительно 95% асфальта, который производится во всем мире каждый год, используется в дорожной промышленности [1]. Асфальт, по сути, действует как связующее для минеральных заполнителей с образованием асфальтобетонных смесей, также называемых асфальтобетонными или битумными смесями.Первое использование асфальта в строительстве дорог в эпоху Набопаласара, царя Вавилона (625–604 гг. До н.э.), было упомянуто Авраамом [2]. Однако битум практически исчез с тротуаров до тех пор, пока не были обнаружены европейские источники природного битума, что привело к развитию современных применений этого материала [1]. Дороги с асфальтовым покрытием эксплуатируются в Европе с 1850-х годов [3] и в США около 125 лет [4]. Инженеры-новаторы в области дорожного покрытия [2, 5] наблюдали сильное влияние температуры на его консистенцию и вскоре поняли, что твердение или старение асфальта происходит во время смешивания, строительства и эксплуатации, что влияет на характеристики асфальтового покрытия [6].
Термин «старение» может применяться для описания нескольких механизмов в битумном вяжущем / смеси. Следовательно, представляется необходимым уточнить терминологию, используемую инженерами по дорожным покрытиям. В дорожном строительстве изменение реологических свойств асфальтобетонных вяжущих / смесей связано с изменениями химического состава в процессе строительства и в течение срока его службы.
Старение асфальтобетонных вяжущих происходит во время производства асфальтобетонных смесей и в процессе эксплуатации под воздействием окружающей среды.Первая стадия старения происходит очень быстро, когда асфальтобетонная смесь производится при очень высокой температуре. Этот этап часто называют кратковременным старением. На этом этапе очень тонкая пленка асфальта подвергается воздействию воздуха при повышенных температурах, что приводит к значительному изменению реологических свойств битумных вяжущих. Такие изменения проявляются в повышенной вязкости и повышенной жесткости [7]. Вторая стадия старения происходит, когда асфальт подвергается воздействию окружающей среды в качестве дорожного покрытия в процессе эксплуатации при относительно более низкой температуре в течение длительного времени.Скорость затвердевания зависит от содержания воздушных пустот и окружающей среды.
На рис. 1 показан типичный отклик отверждения немодифицированного битумного вяжущего. Наблюдается скачок вязкости битумного вяжущего из-за кратковременного старения (Фаза 1), в то время как наблюдается линейное увеличение с более низкой постоянной скоростью со временем (Фаза 2). Фаза 2 представляет собой упрочнение из-за длительного старения.
Есть несколько факторов, влияющих на старение асфальта. К внешним факторам относятся тип установки, температура перемешивания и время хранения в бункере при кратковременном старении, а также полевые условия (т.е., температура, ультрафиолетовые (УФ) лучи и осадки) и время при длительном старении. Скорость и степень старения также зависят от свойств смеси, таких как источник и тип асфальта, градация и абсорбция заполнителя, содержание пустот / проницаемость и толщина пленки асфальтового связующего на заполнителе. В таблице 1 приведены различные факторы и их влияние на кратковременное и долгосрочное старение асфальта. Недавнее исследование Morian et al. [9] сообщили, что эффективное содержание связующего в смесях является самым надежным индикатором характеристик старения асфальтовой смеси, независимо от типа гранулированного заполнителя.
|
Старение вызывает несколько изменения свойств асфальтовой смеси, которые отражаются на характеристиках асфальтового покрытия.Результаты экспериментальных исследований [33] показали, что пластичность и проницаемость асфальтового вяжущего снижаются, в то время как температура размягчения и температура воспламенения повышаются в результате старения. В конечном итоге вязкость асфальта увеличивается и он становится более жесткой асфальтовой смесью. Увеличение вязкости до 10 раз из-за 5-летнего старения месторождения в условиях Ближнего Востока наблюдалось, как показано на Рисунке 2 [34].
Что касается механических свойств, модуль жесткости также увеличивается из-за старения (Рисунок 3), и это увеличение может быть до 4 раз в зависимости от типа асфальта [35].Это может привести к тому, что смесь станет чрезмерно твердой и хрупкой, а также подверженной разрушению и усталостному растрескиванию при низких температурах [36–38]. Старение также может сделать смесь менее прочной, чем исходная смесь, с точки зрения износостойкости и восприимчивости к влаге [39]. В результате снижается устойчивость асфальтового слоя к повреждению, и многие эксплуатируемые покрытия автомобильных дорог и аэродромов выходят из строя преждевременно. Однако старение не обязательно является отрицательным явлением, поскольку сопротивление асфальтовой смеси остаточной деформации и несущая способность улучшаются за счет повышенной жесткости и когезии.В некоторых случаях старение также может помочь смеси достичь оптимальных свойств [6].
В этой статье представлен всесторонний обзор старения асфальтобетонных покрытий со следующими ключевыми направлениями: (1) Всестороннее определение старения асфальта и обзор химии асфальта (2) Критическое обсуждение механизмов старения, соответствующих изменений в молекулярной структуре структура, и ее влияние на свойства асфальтовых материалов (3) Существующие методы испытаний, протоколы и методы оценки старения асфальтобетонных покрытий с акцентом на недавние исследования старения асфальтовых смесей (4) Методы защиты от старения и различные типы добавки и их механизм для замедления старения асфальта с целью улучшения характеристик асфальтового покрытия.
2. Химия асфальта и механизмы старения
Асфальт получают либо из природных отложений, либо как остаток сырой нефти или продукт экстракции нефти растворителем. Он имеет переменный и сложный элементный состав, который зависит в первую очередь от его исходного сырья. Асфальт в основном состоит из углерода (обычно 80–88%) и атомов водорода (10–12%), что дает содержание углеводородов около 90% [41, 42]. Остальная часть состоит из двух типов атомов: гетероатомов и металлов.Гетероатомы включают азот (0–2%), кислород (0–2%) и серу (0–9%). Атомы металлов представляют собой ванадий, никель и железо, и эти атомы присутствуют в следовых количествах, обычно намного меньше 1% [43, 44]. В таблице 2 показан элементный анализ 8 различных керновых битумов различного происхождения.
|
Углеводороды составляют основную структуру асфальта, тогда как атомы металла служат признаком или характеристикой асфальтного сырца. Гетероатомы вносят свой вклад во многие уникальные химические и физические свойства асфальта, взаимодействуя с молекулами. Например, сера легче, чем углерод и водород, реагирует на включение кислорода в структуру асфальта, что приводит к окислительному старению асфальта [45].
Согласно методу Корбетса [46], эти химические элементы объединяются, чтобы сформировать четыре основных компонента или фракции асфальтового цемента: асфальтены, насыщенные углеводороды, нафталиновые ароматические углеводороды и полярные ароматические углеводороды (или смолы), каждый из которых придает асфальту различные характеристики. Асфальтены и насыщенные углеводороды обычно несовместимы и объединяются ароматическими соединениями. Асфальтены в основном ответственны за вязкость (т. Е. За эффекты упрочнения), тогда как обилие ароматических углеводородов и насыщенных веществ снижает пластичность (т.е.е., упругие эффекты). Некоторые исследователи разделяют асфальт на две широкие химические группы в соответствии с методами осаждения Ростлера [47], а именно асфальтены и мальтены с низким молекулярным весом. Мальтены представляют собой вязкие жидкости, состоящие из смол и масел [48]. При химическом и физическом взаимодействии между этими фракциями образуется сложная смесительная система асфальта [49–52]. Компонентный анализ различных типов асфальта представлен в таблице 1.
Исследователи [53, 54] использовали гель-проникающую хроматографию высокого давления (HP-GPC) для разделения асфальта на различные фракции и независимо изучили влияние процесса старения на асфальт. компоненты.Исследования химического состава асфальта в результате старения показывают, что содержание асфальтенов увеличивается, а содержание смол и ароматических углеводородов снижается. В результате увеличения содержания асфальтенов асфальт становится более твердым (то есть более жестким), что может легко проявляться в уменьшении проникновения и повышении температуры размягчения и вязкости [55]. На рис. 4 показано влияние старения на химический состав типичного асфальтового вяжущего. Исследователи также указали, что из-за старения соотношение асфальтенов / мальтенов изменяется, вызывая увеличение вязкости битума, становясь более твердым и хрупким [1].
Физические и химические свойства битумов со временем меняются из-за воздействия различных условий окружающей среды в полевых условиях в течение срока их службы. С 1930-х годов исследования продолжали развивать понимание механизмов, способствующих краткосрочному и долгосрочному старению [56]. Механизмы, вызывающие старение связующего, включают окисление, улетучивание, тиксотропию (или стерическое упрочнение), полимеризацию под действием актиничного света и конденсационную полимеризацию под воздействием тепла [6, 10, 51, 57].Среди них окисление, улетучивание и стерическое упрочнение считаются основными механизмами, связанными с процессом старения асфальтовых смесей [51, 57–59]. Во время производства, укладки и уплотнения асфальтобетонная смесь подвергается воздействию более высоких температур, что вызывает старение из-за окисления и потери летучих соединений. Напротив, длительное старение во время эксплуатации происходит при более низкой температуре, в первую очередь из-за механизма окисления [60].
2.1. Окисление
Многие исследователи занимались химией окисления связующего [8, 52, 61–63].Окисление — это необратимая химическая реакция между молекулами кислорода и компонентами сыпучего асфальта, приводящая к значительным изменениям желаемых физических и / или механических свойств асфальта. Окислительное старение асфальта, как полагают, вызвано образованием кислородсодержащих полярных химических функциональных групп на молекулах асфальта, что, в свою очередь, может вызывать агломерацию между молекулами из-за увеличения химиофизических связей, таких как водородные связи, сила Ван-дер-Ваальса и кулоновская сила [ 41, 64, 65].
Влияние окисления вяжущего в дорожной одежде на ее характеристики весьма противоречиво. Сложные органические компоненты асфальта вступают в реакцию с кислородом воздуха и ультрафиолетовым (УФ) излучением, и, как следствие, поверхность дорожного покрытия становится твердой, что приводит к образованию трещин. Кунс и Райт [66] сообщили, что окисление связующего происходит только в верхнем дюйме дорожного покрытия и ниже верхнего дюйма; на связующее практически не влияют годы использования и годы воздействия окружающей среды. Недавно разработанное «Механистическое эмпирическое руководство по проектированию дорожной одежды» [67] также предполагает в своих расчетах, что связующие окисляются только в верхнем дюйме.Как следствие, окисление вяжущего и связанное с этим увеличение жесткости покрытия на самом деле может иметь положительное и благотворное влияние на усталостную долговечность покрытия [8].
Однако Walubita et al. [68] и Валубита [69] указали, что окисление вяжущего в дорожных покрытиях может иметь очень значительное негативное влияние на усталостную долговечность дорожного покрытия. Более веские доказательства твердения дорожного покрытия глубоко под поверхностью были получены на основе обширных данных Glover et al. [70] и Аль-Азри и др. [71], где на большом количестве тротуаров в Техасе был нанесен сердечник, вяжущее было извлечено и восстановлено, а затем испытано для определения жесткости вяжущего как функции возраста покрытия.Сообщается о повышении жесткости и снижении пластичности асфальтовых смесей из-за окисления, которое может снизить их сопротивление усталостному растрескиванию [72].
Окисление асфальта вызывает изменения химического состава асфальта. Насыщенные вещества остаются практически неизменными из-за их низкой химической активности, тогда как другие три фракции демонстрируют значительные вариации [73, 74]. В результате в молекулах асфальта образуются функциональные группы (т.е. карбонильные и сульфоксидные группы), что приводит к уменьшению ароматических фракций и увеличению фракций асфальтенов [1].Было предпринято множество попыток количественной оценки окисления для лучшего понимания старения асфальта. Лю и др. [75] указали, что площадь карбонильной области (CA) в ИК-Фурье спектрах является прямой мерой окисления связующего, и процент карбонильных соединений может использоваться для оценки изменений, вызванных окислительным старением [8]. Содержание карбонила зависит от температуры и парциального давления кислорода.
Скорость реакции карбонила описывается формулой [8], где = скорость реакции карбонила, = коэффициент частоты, = давление, = порядок реакции, = энергия активации, = газовая постоянная, и = абсолютная температура.Исследования показывают, что значения, и различаются для разных типов асфальта.
2.2. Улетучивание
Улетучивание — еще один важный механизм, который происходит во время горячего перемешивания и изготовления асфальтового цемента. При высоких температурах более легкие молекулярные массы могут испаряться и улетучиваться в атмосферу [1, 10]. Это может иметь большее значение при приготовлении модифицированных битумных вяжущих, когда маслоподобные соединения испаряются из асфальта. Когда тонкая асфальтовая пленка вступает в контакт с заполнителями при температуре 150 ° C или выше, ароматические фракции быстро испаряются, а фракции асфальтенов обычно увеличиваются между 1 и 4% [76].В результате этой реакции образуются пары и пары в зависимости от площади поверхности контакта между асфальтовой пленкой и заполнителями [77]. В результате потери веса свойства текучести асфальта снижаются, то есть на вязкость влияет улетучивание, особенно с учетом скорости, с которой происходит улетучивание [78, 79]. Исследователи [6, 80] обнаружили, что вязкость увеличивается от 150 до 400%. Значительное увеличение модуля и уменьшение фазового угла наблюдались из-за улетучивания [81].Андерсон и Бонаквист [60] предположили, что количественная оценка потери летучих соединений имеет важное значение для лучшего понимания твердения асфальта во время кратковременного старения.
2.3. Стерическое упрочнение
Стерическое упрочнение, также известное как физическое упрочнение, происходит со временем, когда асфальтовые цементы подвергаются воздействию низкой температуры. В этом процессе молекулярная структура асфальта реорганизуется, что влияет на его асфальтеновые фракции [82]. Последствиями стерического твердения являются повышенная вязкость, небольшое сокращение объема и, в конечном итоге, твердение асфальта [10, 83].Стерическое упрочнение более выражено при температурах, близких к 0 ° C, и его следует учитывать при испытании асфальта при очень низкой температуре. Поскольку это упрочнение является результатом структурной реорганизации молекулы при низких температурах [51], оно может быть обращено вспять посредством нагрева или механической работы [84].
3. Лабораторное ускоренное старение и методы оценки
Асфальт выдерживается в лабораторных условиях более быстрыми темпами за счет применения тепла и воздуха для моделирования старения в полевых условиях и, следовательно, для прогнозирования характеристик асфальтового покрытия.Самая ранняя работа по моделированию старения в лаборатории была сделана Доу [5], который использовал расширенный тест на нагрев. С тех пор множество исследований [6, 10, 27, 50, 57, 85–99] было посвящено оценке влияния старения на характеристики асфальтовых материалов. После обработки для ускорения старения образцы обычно изучаются для количественной оценки изменений свойств битумного вяжущего / смеси до и после обработки старением (обычно известного как индекс старения). Свойства, исследуемые в ходе исследований старения, как правило, включают потерю веса, вязкость, пенетрацию, пластичность, предел прочности на разрыв и модуль жесткости.
Обработку асфальта или испытания, связанные со старением асфальтовых материалов, можно условно разделить на две категории, а именно: испытания, проводимые на асфальтовом вяжущем, и испытания, проводимые на асфальтовых смесях. Поэтому обсуждение работы представлено в следующих двух разделах: исследования вяжущего и исследования смесей.
3.1. Binder Studies
Исследователи разработали несколько методов испытаний для определения свойств асфальтовых вяжущих путем моделирования старения асфальта на заводе по производству горячей смеси и в течение срока службы дорожного покрытия.В большинстве этих исследований использовались тонкопленочные печи для старения асфальта с применением процедуры длительного нагрева и продувки воздухом (или окисления). Наиболее часто используемыми и стандартными испытаниями для моделирования старения горячей смеси асфальта являются испытание в тонкопленочной печи с прокаткой ((RTFOT) ASTM D2872 [100], AASHTO T240 [101]) и испытание в тонкопленочной печи ((TFOT) ASTM D1754 [102], AASHTO T179 [103]). Сосуд для выдерживания под давлением (PAV) используется для моделирования длительного старения битумного вяжущего, которое наблюдается в полевых условиях [104]. Согласно текущим спецификациям вяжущего Superpave, оцениваемое асфальтовое вяжущее должно быть подвергнуто RTFOT для кратковременного старения при 163 ° C в течение 85 минут с последующим процессом PAV для имитации старения в полевых условиях в течение нескольких лет.
TFOT был впервые введен Льюисом и Велборном [105] для моделирования кратковременного старения путем воздействия температуры 163 ° C на асфальт с толщиной пленки 3,2 мм в течение 5 часов. Однако исследователи подвергли критике TFOT из-за того, что толщина пленки намного больше, чем обычно наблюдается в полевых условиях, и за неравномерное старение по всей глубине асфальта [58]. Многие исследователи пытались разработать или улучшить методы испытаний для выдерживания асфальта с более репрезентативной толщиной пленки. Одной из таких попыток было испытание модифицированной тонкопленочной печи, проведенное Эдлером и др.[106], которые использовали толщину пленки 100 мкм мкм с дополнительным увеличенным временем воздействия до 24 часов. Исследователи также предложили некоторые другие методы тестирования, такие как тест на микропленку Shell [107], испытание на прокатной микропленке в печи [108], испытание на долговечность в наклонной печи [23] и испытание на ускоренное старение тонкой пленки [92] для лучшего моделирования старения битумного вяжущего.
Наиболее значительной модификацией TFOT был RTFOT, разработанный Калифорнийским отделением шоссе [109], где восемь стеклянных бутылок, каждая из которых содержит 35 г асфальта, выдерживаются путем нагревания и окисления тонких пленок 1.25 мм. Этот метод обеспечивает равномерное старение асфальта без образования корки и достаточно хорошо коррелирует с затвердеванием асфальта с наблюдаемым в процессе горячего перемешивания [110]. Однако несколько исследователей [111–113] выявили ряд недостатков (например, выливание из бутылок с RTFOT) в RTFOT, особенно при тестировании модифицированных битумных вяжущих. Чтобы преодолеть эти ограничения, исследователи разработали усовершенствованные методы тестирования, такие как испытание в модифицированной тонкопленочной печи с прокаткой ((RTFOTM), Bahia et al. [96]), модифицированная немецкая вращающаяся колба [111, 114] (MGRF) и испытание на поток перемешиваемого воздуха [ 115] (SAFT) для оценки кратковременного старения чистого и модифицированного битумного вяжущего.
Хотя испытания в тонкопленочной печи могут адекватно имитировать кратковременное старение битумного вяжущего, они не дают точного прогнозирования длительного старения в течение срока службы дорожного покрытия. Для прогнозирования длительного старения был предпринят ряд попыток сочетания испытаний в тонкопленочной печи с окислительным старением, таких как испытание на долговечность в Айове [32], окислительная бомба под давлением [106], устройство для испытания на ускоренное старение [116], PAV [80] , 117] и испытание на старение под высоким давлением [118]. Среди них лечение ПАВ считается наиболее надежным методом имитации длительного старения.В этом процессе асфальт, выдержанный методом RTFOT, подвергается воздействию температуры 100 ° C в течение 20 часов при давлении 2,07 МПа для воспроизведения эффектов старения в полевых условиях. Как правило, он моделирует старение за 8–10 лет службы дорожного покрытия в соответствии со стандартами США [79]. Однако 20 часов кондиционирования в PAV может быть недостаточно для суровых погодных условий, таких как на Ближнем Востоке, где может потребоваться до 70 часов кондиционирования для имитации полевого старения 5-летнего асфальтового покрытия (Рисунок 5).
В недавнем исследовании NCHRP (проект № 9-36) Андерсон и Бонаквист [60] попытались разработать улучшенную процедуру для замены RTFOT и PAV одним устройством для моделирования кратковременного и длительного старения.Они исследовали как MGRF, так и SAFT, но с разными условиями эксплуатации. Попытки использовать MGRF не увенчались успехом, однако SAFT с модифицированным рабочим колесом оказался в некоторой степени успешным для моделирования как краткосрочного, так и длительного старения асфальтового вяжущего.
Атомно-силовая микроскопия (АСМ) часто используется для изучения старения битумного вяжущего на микроскопическом уровне и оценки изменения микромеханических и микрореологических свойств. АСМ — это инструмент неразрушающей визуализации, который может предоставить информацию о топографии поверхности, жесткости, липкости и молекулярном взаимодействии на микроуровне материалов [119, 120].На изображениях АСМ отмечается пчелиная структура (черные и желтые полосы), которая указывает на асфальтеновую фазу в битуме [121, 122]. Наличие таких микроструктур отчасти определяет макроуровневые свойства битума, такие как жесткость, вязкоупругость, пластичность, адгезия, излом и характеристики заживления. Эволюция этих микроструктур по мере старения и связанная с результирующей механической реакцией находится в центре внимания, чтобы лучше понять долгосрочные свойства битумов.
В последние дни АСМ стал популярным методом и используется многими исследователями [123–126] для характеристики влияния кратковременного, длительного старения и ультрафиолетового (УФ) излучения на морфологию асфальтовых вяжущих.Об увеличении микроструктуры в форме пчелы при старении ПАВ сообщили Huang и Pauli [127], Wu et al. [128] и Zhang et al. [123]. Zhang et al. [123] показали, что моделируемое в лаборатории старение значительно влияет на морфологию битума, и эти изменения морфологии сильно коррелируют с физическими свойствами, а также химическим составом связующих до и после старения. Общая поверхностная жесткость увеличилась, и поверхность битума стала более твердой [123]. Как содержание асфальтенов, так и размер микроструктур играют роль в определении микромеханических свойств асфальта [129].Аллен и др. Сообщили о важной взаимосвязи между микроструктурными изменениями, отображаемыми на изображениях АСМ, и изменениями вязкоупругих свойств композита, полученными в результате измерений. [124]. Das et al. [126] обнаружили снижение липкости вяжущего при старении, и в результате адгезия образцов асфальтового вяжущего ухудшилась, что привело к разрыву адгезионного соединения между вяжущим и заполнителями. Исследователи сообщили, что модуль микроструктуры всегда выше модуля матрицы при измеренной температуре, как показано на рисунке 6.Также было отмечено, что увеличение модуля из-за воздействия УФ-излучения выше, чем при окислении, и наивысшее значение всегда получалось после комбинированного воздействия УФ-излучения и окисления. Аналогичное наблюдение было обнаружено для 3 разных связующих из разных источников. АСМ также использовался для исследования влияния старения на модифицированные битумные вяжущие по сравнению с контрольными вяжущими [127, 128, 130].
3.2. Исследования смесей
По сравнению с исследованиями асфальтового вяжущего, исследований старения асфальтовых смесей было сравнительно мало.Большая часть ранних работ по старению асфальта проводилась исключительно на связующих, без использования смесей [6, 131]. В конце концов, были предприняты попытки проанализировать старение системы смеси асфальт-заполнитель путем измерения изменений проницаемости и вязкости извлеченных и восстановленных связующих [91, 132–134]. Исследования, представленные в NCHRP Project 9-6 [134], включали измерения и сравнение вязкости и проницаемости связующих, извлеченных и извлеченных из смесей, выдержанных в лаборатории в различных условиях, с таковыми из смесей, произведенных в полевых условиях.Испытания на ограниченный модуль упругости были также проведены на прессованных в лаборатории образцах. Однако характеристики длительного старения, имитирующие 5-10 лет эксплуатации, пришлось экстраполировать из имеющихся данных за 2 года. Более реалистичный подход к моделированию старения асфальтовой смеси состоит в том, чтобы подвергнуть асфальтовые смеси различным условиям старения, измерить физические свойства состаренных смесей и затем сравнить их с образцами, подвергнутыми старению в полевых условиях [57, 135, 136].
В недавних исследованиях асфальтовых смесей исследователи показали, что старение асфальтобетонных смесей в условиях неравномерного поля по глубине и поверхность асфальтового покрытия стареют быстрее, чем дно [34, 137].О охрупчивании асфальтовой смеси из-за старения сообщили Rahmani et al. [38] и Elwardany et al. [138]. Хрупкость увеличивается с периодом выдержки при всех режимах старения и со временем в полевых условиях эксплуатации [139]. В результате снижается сопротивление усталостному растрескиванию и долговечность асфальтобетонных смесей, что становится более заметным при повышении температуры [140]. Gao et al. [141] показали, что деградация модуля упругости асфальтовой смеси увеличивается с увеличением периода старения.Азри и Мохсени [142] показали, что разные асфальтовые смеси стареют по-разному, и это существенно влияет на их краткосрочные и долгосрочные характеристики колейности. Старение увеличивает сопротивление остаточной деформации с точки зрения потока, как сообщает Islam et al. [139] и Бабадопулос и др. [143].
3.2.1. Протокол моделирования старения асфальтовой смеси
Текущая практика, рекомендованная Американской ассоциацией государственных служащих автомобильных дорог и транспорта (AASHTO), заключается в отверждении асфальтовых смесей в течение нескольких часов и дней для краткосрочного и долгосрочного старения соответственно.Процедура тестирования, основанная на работе, проделанной Von Quintus et al. [90] охватывает три типа кондиционирования и представлено в стандартной процедуре AASHTO R30 [144]: ) Длительное кондиционирование для имитации старения, которое происходит после процесса строительства и в течение всего срока службы покрытия
В соответствии с этой стандартной практикой смесь выдерживают в печи с принудительной тягой в течение разных периодов времени и при разных температурах, как показано на Таблица 3.
| |||||||||||||||||||||
Указанная температура уплотнения и тип смеси (заводского производства, повторно нагретая , так далее.). |
3.2.2. Протокол краткосрочного старения
Были проведены исследования по оценке протокола краткосрочного старения для моделирования старения асфальтовой смеси во время производства, укладки и строительства слоя асфальтового покрытия. Хотя результаты эксплуатационных испытаний смеси, произведенной в лаборатории и на заводе, не были точным совпадением, в прошлом существовало общее мнение, что лабораторное старение является репрезентативным для полевого старения [145]. Однако в связи с недавними разработками в технологии асфальта и изменениями в компонентах смеси, обработке смеси и конструкции установки, обоснованность текущих методов проектирования смеси для удовлетворения ожиданий в отношении производительности подвергается сомнению.
В комплексном исследовании Bell et al. [57] оценили старение асфальтовой смеси и обнаружили, что протокол краткосрочного старения AASHTO достаточно хорошо моделирует старение асфальтовой смеси, за исключением нескольких консервативных прогнозов. Исследования, проведенные Калифорнийским университетом в Беркли совместно с Университетом штата Орегон и Austin Research Engineers, Inc. [57], также показали, что протокол является адекватным на основании модуля упругости и результатов испытаний на непрямое растяжение. Ашенбренер и Фар [18] провели обширное исследование по всему Колорадо, кондиционировали смеси при температуре уплотнения в полевых условиях в течение различной продолжительности (0–8 часов) и обнаружили, что протокол краткосрочного старения эквивалентен 2–4 часам на основе теоретической максимальной плотности и асфальта. впитывание и 1–3 часа на основе результатов гамбургского теста на отслеживание колес.Исследователи рекомендовали кондиционировать смеси, полученные в лаборатории, в течение 2 часов при температуре уплотнения в полевых условиях, чтобы имитировать старение и абсорбцию асфальта в процессе производства. Эппс Мартин и др. [31] также оценили различные протоколы краткосрочного старения, и окончательная рекомендация заключалась в том, чтобы выдержать лабораторную смесь при 135 ° C в течение 2 часов перед уплотнением.
3.2.3. Протокол долговременного старения
Исследователи использовали различные процедуры кондиционирования (длительный нагрев, окисление и обработка УФ / инфракрасным излучением) для исследования долговременного старения асфальтового покрытия.Кондиционирование также может проводиться как на рыхлой смеси, так и на уплотненном образце. Старение в печи уплотненного образца обычно используется для моделирования длительного старения асфальтобетонных смесей. Однако в уплотненном образце сообщалось о существовании градиента окисления в радиальном направлении и по высоте образца [27]. Поэтому исследователи [90, 138, 146–149] иногда предпочитали кондиционирование рыхлой смеси при повышенной температуре из-за однородности и эффективности старения. Однако уплотнение кондиционированного образца рыхлой смеси часто оказывалось проблематичным, поскольку смесь становилась слишком жесткой из-за потери летучести связующего [148].Значительно большое число вращений, поэтому требовалось более высокое напряжение сдвига для уплотнения образца сыпучих смесей, что приводило к деградации агрегатных структур, следовательно, меняло свойства смеси [148, 150]. Температура, при которой происходит старение, также важна. Более высокая температура (> 95 ° C) может вызвать оседание / деформацию и повлиять на распределение воздуха в уплотненном образце [148]. Температура старения сыпучей смеси более 135 ° C приводит к значительному изменению взаимосвязи между реологией и химическим составом битумного вяжущего и влияет на характеристики смеси [151].Оптимальная температура старения сыпучей смеси 95 ° C предложена исследователями [138].
Ряд исследований [90, 138, 146, 147, 149, 152] показали, что протокол длительного старения может варьироваться в зависимости от климатических условий, метода лабораторного старения, температуры лабораторного старения или типа асфальта. Более того, большинство этих исследований оценивают только долгосрочное старение асфальтовой смеси без надлежащей проверки полевых результатов, особенно на уровне компонентов. Стандартный протокол для моделирования старения в полевых условиях — это кондиционирование уплотненного образца при 85 ° C в течение 5 дней в соответствии с AASHTO R30.
В протоколе используется одна температура и не учитываются различные условия окружающей среды или свойства смеси. Таким образом, применимость протокола к различным климатическим условиям (например, как на Ближнем Востоке) сомнительна без полевой проверки. Асфальтовое покрытие испытывает тяжелые погодные условия при высоких температурах (часто превышающих 40 ° C в летние месяцы) в регионе Персидского залива. Кроме того, летом здесь нет осадков, а в остальное время года их очень мало.Эти повышенные температуры значительно увеличивают окисление вяжущего, что может привести к усталостному растрескиванию и, в конечном итоге, к разрушению дорожного покрытия при большой и повторяющейся нагрузке от движения транспорта. Предыдущие исследования также демонстрируют необходимость разработки протокола старения, учитывающего климатические условия, объем движения и свойства смеси [27, 57, 136, 153]. Эти исследования рекомендовали учитывать эти изменения еще на стадии проектирования, чтобы улучшить анализ характеристик асфальтовых покрытий.
В таблице 4 представлены ключевые исследования, посвященные протоколу моделирования длительного старения.Bell et al. [57] включили различные климатические зоны для оценки протокола длительного старения асфальтовых смесей. Экспериментальные результаты предполагают кондиционирование уплотненного образца в течение 2 дней при 85 ° C или 1 дня при 100 ° C для моделирования длительного старения новых покрытий (возрастом от 1 до 3 лет). Смесь необходимо выдерживать в течение более длительного времени (от 4 до 8 дней при 85 ° C или от 2 до 4 дней при 100 ° C), чтобы прогнозировать старение на 9-10 лет полевого старения. Однако авторы предложили избегать более высокой температуры 100 ° C, поскольку кондиционирование смесей при этой температуре может привести к повреждению образцов.Что еще более важно, исследователи рекомендовали дальнейшие исследования для достижения лучшей проверки и моделирования для более широкого диапазона климатических зон. Исследователи также рекомендовали разработать модель для моделирования старения полей с использованием входных данных, описывающих климатические зоны и движение транспорта. Возможные исходные данные могут включать интенсивность движения, максимальную и минимальную температуру воздуха, среднее количество осадков, возраст тротуаров и возраст лабораторных смесей.
|
Ромеро и Роке [156] указали, что использование процедур длительного старения с использованием уплотненных смесей может быть не лучше, чем применяемые в настоящее время краткосрочные Следует прекратить процедуры выдержки в печи и, следовательно, длительную выдержку в печи с использованием образцов уплотненного асфальта.Хьюстон и др. [27] выполнили долгосрочное исследование старения для разных участков в Соединенных Штатах, а также для разных агрегатов и связующих. Исследователи рассматривали возможность кондиционирования образца при различных температурах (80 ° C, 85 ° C и 90 ° C) в течение 5 дней. Сообщалось о высокой вариабельности данных с выбранных участков, и из-за этой вариабельности и неспособности учесть различные переменные, такие как условия окружающей среды и свойства смеси, исследователи не смогли разработать новую процедуру или пересмотреть существующую в течение длительного времени. срок кондиционирования асфальтобетонных смесей.Был сделан вывод, что текущая стандартная процедура недостаточна для реального моделирования и прогнозирования длительного старения асфальтобетонных смесей в полевых условиях. Весьма желательна разработка новой процедуры, которая учитывает различные условия окружающей среды и свойства смеси, такие как содержание пустот в воздухе. Кроме того, они рекомендовали включать различные типы материалов: немодифицированные вяжущие, модифицированные вяжущие, резиновые вяжущие и восстановленное асфальтовое покрытие. В недавнем исследовании Yin et al. [156] предложили протоколы долгосрочного старения: 2 недели при 60 ° C и 5 дней при 85 ° C. Получили смеси с эквивалентным старением в полевых условиях в течение 7–12 месяцев и 12–23 месяцев, соответственно, с учетом технологии WMA, переработанных. материалы, абсорбция заполнителя, связующее, модифицированное полимером, и температура производства.Сирин и др. [29] указали на сильное старение асфальтовых покрытий в регионе Ближнего Востока из-за суровых условий окружающей среды. Для таких условий потребуется 45 и 75 дней при 85 ° C на уплотненном образце, чтобы смоделировать 5-летнее старение в полевых условиях для износа и основного слоя, соответственно. Чтобы избежать такого длительного периода кондиционирования, исследователи предложили в качестве альтернативы кондиционирование рыхлой смеси и обнаружили, что потребуется 2-3 и 1-2 дня при 135 ° C, чтобы смоделировать одинаковый уровень старения для ношения и основного курса. соответственно.
4. Антиоксидантные добавки
Контроль старения асфальта важен, потому что старение вызывает жесткость и хрупкость, которые могут привести к растрескиванию и преждевременному разрушению асфальтового покрытия. Как обсуждалось в предыдущих разделах, существует несколько механизмов упрочнения асфальта. Окисление во время производства, уплотнения и эксплуатации асфальтобетонной смеси является основным и считается наиболее понятным и наиболее простым для моделирования в лаборатории [157, 158]. Поэтому исследователи попытались уменьшить / минимизировать окислительное твердение с помощью химических добавок, чтобы получить более долговечное покрытие и существенную экономию в стоимости жизненного цикла.
Добавки, которые используются для модификации асфальта и замедления старения, называются антиоксидантами. Когда антиоксиданты добавляются к асфальту в качестве модификаторов, они контролируют окисление, улавливая или удаляя свободные радикалы, которые ответственны за инициирование и / или распространение окисления. Эти антиоксиданты (например, диамилдитиокарбамат свинца (LDADC)) действуют как жертвенные частицы, которые окисляются вместо асфальтовых связующих [158, 159]. Некоторые другие антиоксиданты действуют за счет реакции с полярными соединениями и / или катализаторами окисления, такими как металлы, присутствующие в асфальтах.
На рынке имеется множество антиоксидантов для битума асфальта. В зависимости от способа контроля окисления антиоксиданты можно разделить на четыре основные группы: первичные антиоксиданты, вторичные антиоксиданты, хелаторы металлов и светостабилизаторы [158, 160]. Первичные антиоксиданты имеют реактивные группы ОН или NH и действуют как поглотители свободных радикалов, отдавая или принимая электроны от свободных радикалов и тем самым нарушая цепные реакции окисления. Вторичные антиоксиданты включают соединения серы и фосфора, такие как сульфиды, тиоэфиры, дисульфиды и фосфаты.Они действуют как разлагатели пероксида или гидропероксида, восстанавливая их до стабильных соединений. Хелаторы металлов действуют, улавливая следы металлов, таких как ванадий, никель и железо, которые, как полагают, ускоряют образование свободных радикалов, действуя как катализаторы на стадии распространения [160]. Наконец, светостабилизаторы используются для предотвращения деградации за счет поглощения вредной лучистой энергии.
4.1. Исследования антиоксидантных добавок для замедления старения асфальтовой смеси
В нескольких исследованиях сообщалось о преимуществах использования связующих, модифицированных антиоксидантами.Хотя большинство этих исследований довольно старые, некоторые антиоксиданты (например, гашеная известь, свинцовые антиоксиданты и технический углерод) дают многообещающие результаты [50, 88, 160–164]. В этих исследованиях исследователи использовали различные добавки для замедления окислительного твердения асфальтовых вяжущих и оценили антиоксидантные системы, определяя ухудшение физических свойств асфальта, в основном вязкости и пластичности. Однако большинство этих систем для замедления окислительного твердения не работают удовлетворительно в полевых условиях из-за таких проблем, как разложение, летучесть и потеря антиоксиданта из асфальтовой системы.
Несколько недавних исследований были проведены для изучения влияния использования антиоксидантных добавок на характеристики связующего (таблица 5). Мохамед [165] оценил потенциал CRABit (CR30 и CR50) в качестве модификатора антиоксиданта для использования в плотных асфальтовых смесях (ACW14). Исследователь провел исследование в два этапа; Первый этап заключался в испытании реологических характеристик нового продукта с использованием влажной смеси с помощью реометра динамического сдвига (DSR), а второй этап включал приготовление смеси ACW14, содержащей основу и модифицированный битум, путем сухой смеси и их тестирование для определения основных свойств (т.е., модуль упругости, сопротивление непрямому растяжению, ползучести и усталости) до и после старения образца. Исследователь обнаружил улучшение инженерных свойств и производительности с модификацией, особенно с CR30.
|
Apeagyei et al.[166] оценили потенциал растрескивания асфальтовых смесей, содержащих различные уровни антиоксидантов. Исследователи рассмотрели два уровня старения в печи с принудительной тягой, чтобы моделировать краткосрочные и долгосрочные условия старения в печи (STOA и SLOA, соответственно). Кроме того, использовались два уровня антиоксидантной модификации: фурфурол (ароматический альдегид) и дилаурилтиодипропионат (DLTDP — антиоксидант и термостабилизатор) с асфальтовыми связующими. Процент смешивания варьировался от 0,2% до 10% мас. / Мас. Базового асфальта, который вводили в базовый асфальт с использованием смесителя Barnant с 2-дюймовыми лопастями, работающего со скоростью 750 об / мин.Результаты показали, что асфальтовые смеси, модифицированные антиоксидантами, работают лучше, чем смеси немодифицированных битумов. Связующие, модифицированные антиоксидантами, показали, по меньшей мере, примерно на 50% более низкую жесткость на изгиб по сравнению с немодифицированным асфальтовым вяжущим при низкой температуре (от примерно -4 ° C до примерно -58 ° C), что указывает на улучшенное сопротивление усталости. Также было обнаружено, что модификация дает по меньшей мере примерно на 18% более высокую жесткость по сравнению с немодифицированным асфальтовым вяжущим при высокой температуре (от примерно 46 ° C до примерно 82 ° C), что указывает на лучшую устойчивость к колейности.В отдельном исследовании Apeagyei [167] оценил AOXADOUR как антиоксидантную добавку с базовым связующим PG 64-22 и обнаружил более высокий динамический модуль, улучшенное сопротивление колееобразованию с точки зрения податливости к ползучести, более высокую прочность на разрыв при низкой температуре (-10 ° C), и меньшее влияние старения на поведение разрушения для образцов, обработанных как STOA, так и LTOA. Асфальтовая смесь, модифицированная AOXADUR, показала меньшее сокращение прогнозируемого срока службы при старении и потребовалось больше времени до критического растрескивания по сравнению с контролем (Рисунок 7).
Комбинации различных антиоксидантов были также оценены Apeagyei [59], чтобы определить, существует ли синергетическое поведение между любыми из антиоксидантов.Эти добавки включали DLTDP / фурфурол, гашеную известь, витамин E, технический углерод, Irgafos P-EPQ и Irganox 1010. DSR использовали для исследования реологических свойств необработанных и модифицированных антиоксидантами связующих. Результаты этого исследования показывают, что комбинация добавок фурфурола и DLTDP имела самый низкий индекс старения по сравнению с другими модификаторами. Эта специфическая комбинация обеспечила 40-процентное снижение старения / затвердевания по сравнению с немодифицированными связующими. В общем, связующие, модифицированные антиоксидантами, имели более низкий модуль жесткости и жесткость при изгибе по сравнению с необработанными связующими, которые, как ожидается, будут иметь лучшее сопротивление растрескиванию.Автор рекомендовал провести дальнейшие исследования для подтверждения результатов с использованием дополнительных вяжущих и для оценки свойств как асфальтобетонных смесей, так и вяжущих.
Рейес [168] оценил потенциал использования витамина Е в качестве модификатора антиоксиданта с двумя типами связующего: немодифицированным (PG 64-22) и модифицированным (PG 70-22). Поскольку витамин Е имеет низкую вязкость, две добавки на основе кальция (гидратированная известь и летучая зола) использовались в качестве стабилизирующих агентов для увеличения жесткости связующего. Исследователь использовал смеситель с высокой скоростью сдвига при 2100 об / мин в течение 1 часа для смешивания каждого образца.Результаты этого исследования показывают, что использование витамина Е снижает вязкость связующих веществ. Кроме того, использование стабилизирующих агентов, таких как летучая зола и гашеная известь, улучшило жесткость связующих, модифицированных антиоксидантом витамином Е. Модифицированные связующие с витамином Е обладали желаемыми характеристиками, которые не допускали бы усталостного растрескивания; тем не менее, были опасения по поводу устойчивости к колейности. Связующее, модифицированное антиоксидантом витамином Е, имело пониженный модуль жесткости и увеличенный фазовый угол. Автор предложил провести эксперименты для определения оптимального процентного содержания антиоксидантов и стабилизаторов для достижения лучших показателей при старении.
Pan et al. [52] выполнили химиофизический анализ на атомистической основе, чтобы облегчить фундаментальное понимание механизмов старения и антиокисления и, таким образом, разработать стратегии против старения. В этом исследовании были изучены химические и физические основы окисления асфальта, а также механизм антиокисления лигнина кониферилового спирта. Исследователи разработали хемофизическую среду, основанную на квантовой химии, и изучили различные химические реакции между компонентами асфальта и кислородом и возникающие в результате физические изменения в отличие от традиционного метода оценки ухудшения физических свойств асфальта (т.е. вязкость и пластичность). Были идентифицированы две отдельные стадии старения асфальта; Первоначально асфальты демонстрируют высокую тенденцию к разрыву цепи и высокую реакционную способность с кислородом, вызывая быстрый всплеск образования легкомолекулярных алканов, кетонов и сульфоксидов, за которым следует более медленная скорость окисления и твердения. Авторы предположили, что лигнин кониферилового спирта может быть использован в качестве антиоксиданта для нефтяного асфальта с максимальной эффективностью улавливания радикалов, достигаемой в неокислительном состоянии лигнина (например,g., <130 ° C при парциальном давлении кислорода 1 атм).
Williams [169] оценил потенциал сельскохозяйственных лигнинсодержащих побочных продуктов этанола для использования в качестве антиоксиданта в связующем асфальте. Исследователь использовал четыре побочных продукта, смешанных с четырьмя различными типами асфальтовых вяжущих в диапазоне 3–12%, что дало 52 комбинации обработки. Три побочных продукта содержали лигнин, переработанный из кукурузы, из которого из четвертого лигнина был удален и служил контролем для измерения антиоксидантной активности трех других побочных продуктов лигнина.Тестирование производительности каждой комбинации состояло из DSR и реометра изгибающейся балки (BBR), совпадающего с испытаниями на моделирование старения в полевых условиях с использованием RTFOT и PAV. Результаты показали, что лигнинсодержащие побочные продукты обладают полезной антиоксидантной активностью и повышают жесткость связующего на всех этапах старения. Исследователь предложил провести дополнительные испытания на разделение, чтобы оценить влияние таких переменных, как физический размер и химический состав побочных продуктов.
В зависимости от климатических условий в асфальтовом покрытии наблюдаются два различных типа явлений, связанных со старением.При низкой температуре жесткость асфальта увеличивается, и в результате гибкость асфальтобетона уменьшается, вызывая растрескивание покрытия из-за усталости или термических напряжений. С другой стороны, более высокая температура смягчает асфальт и, следовательно, снижает жесткость асфальтобетона, делая смесь более восприимчивой к образованию колей. Некоторые виды антиоксидантной обработки являются многообещающими для снижения жесткости связующего, но все же склонны к размягчению при более высоких температурах, затвердеванию при более низких температурах или выщелачиванию со временем.
В 2006 году группа исследователей из Университета Иллинойса в Урбане-Шампейне разработала антиоксидантное средство с использованием AOXADUR, которое состоит из трех добавок: альдегида, тиоэфира и кальализатора. Реакция конденсации альдегида с асфальтом с образованием новолаков, которые могут действовать как антиоксиданты, приводит к снижению восприимчивых к старению полярных ароматических соединений в связующем. Тиоэфир служит вторичным антиоксидантом, который очень эффективен против окислительного разложения углеводородов.Лабораторные испытания более 40 связующих в Университете Иллинойса показали, что связующее, модифицированное AOXADUR, дает самый низкий индекс старения и резкое увеличение высокотемпературной жесткости и существенное снижение низкотемпературной жесткости. Исследователи сообщили, что улучшение свойств связующего как при высоких, так и при низких температурах приводит к меньшему термическому напряжению и снижению потенциала растрескивания.
5. Выводы
Ниже приведены основные моменты, обсуждаемые в этой статье.(i) Старение асфальта — сложное явление, которое влияет на характеристики асфальтового покрытия, вызывая функциональное повреждение асфальта. Обычно это определяется как изменение реологических свойств асфальтовых вяжущих / смесей из-за изменений химического состава во время строительства и в течение срока его службы. На старение влияют внутренние и внешние переменные: внутренние переменные включают типы смесей асфальтового вяжущего, заполнитель, пустотность и толщину пленки, а внешние переменные — температуру смешивания и условия окружающей среды.Старение влияет на асфальтовое покрытие по-разному, делая его хрупким, менее устойчивым к повреждениям и менее прочным. В результате дорожное покрытие становится восприимчивым к разрушению и растрескиванию при низких температурах. (Ii) Сложная молекулярная структура асфальта и его химические компоненты изменяются в результате воздействия колебаний температуры и атмосферных условий, что приводит к изменению свойств асфальта. Основными механизмами старения асфальта являются окисление, улетучивание и стерическое упрочнение.Во время строительства битумное вяжущее подвергается более высокой температуре, что вызывает старение из-за окисления и потери летучих соединений. Напротив, длительное старение во время периодов эксплуатации происходит при более низких температурах, в первую очередь из-за механизма окисления. Стерическое упрочнение происходит во время длительного старения при относительно более низкой температуре. (Iii) Продолжительный нагрев в тонкопленочной печи и окисление продувкой воздухом являются основными методами моделирования старения битумного вяжущего в лабораторных условиях. Наиболее часто используемые тесты для моделирования старения битумного вяжущего — это тесты RTFOT и PAV.В этом процессе оцениваемое асфальтовое вяжущее должно быть подвергнуто RTFOT для кратковременного старения при 163 ° C в течение 85 минут с последующим процессом PAV при 85 ° C в течение 5 дней для имитации нескольких лет полевого старения. ( iv) Стандартный протокол для моделирования старения асфальтовой смеси заключается в отверждении асфальтовых смесей в течение 4 часов при 135 ° C для кратковременного старения и 5 дней при 85 ° C для длительного старения. Однако эти стандартные протоколы старения имеют ограничения и не могут применяться в различных условиях окружающей среды.Следовательно, крайне желательна разработка и проверка новой процедуры моделирования старения, которая учитывает различные условия окружающей среды и свойства смеси, такие как содержание воздушных пустот. дорожное покрытие и существенная экономия стоимости жизненного цикла. Одно из наиболее желательных свойств асфальтовой смеси — хорошо работать при более высоких температурах против образования колеи, а также при более низких температурах против растрескивания из-за усталости.Результаты экспериментальных исследований показали, что некоторые присадки хорошо работают при более высоких температурах, в то же время демонстрируя плохие характеристики при более низких температурах или наоборот. Необходимы дальнейшие исследования различных антиоксидантных добавок для получения более эффективной и устойчивой асфальтовой смеси, которая может одинаково хорошо работать как при высоких, так и при низких температурах.
Конфликт интересов
Авторы заявляют об отсутствии конфликта интересов.
Благодарности
Эта статья стала возможной благодаря гранту NPRP (NPRP 6-773-2-320) Катарского национального исследовательского фонда (член Катарского фонда).Заявления, сделанные в данном документе, являются исключительной ответственностью авторов.
Теплая асфальтовая смесь | Ассоциация асфальтовых покрытий штата Орегон
Теплый асфальтобетон (WMA) — это величайший прорыв в технологии асфальта со времен вторичной переработки, который имеет революционные последствия для асфальтобетонной промышленности и окружающей среды. Снижая температуры, при которых асфальтобетонные смеси производятся и укладываются на дорогу, на 50–100 ° F, WMA приносит пользу производителю за счет сокращения расхода топлива и затрат при одновременном снижении производства парниковых газов.
Что делает WMA уникальным, так это то, чем он не является! Это не другой или особый тип асфальтобетона, это способ производства обычных асфальтовых смесей — ВСЕХ асфальтовых смесей — при более низких температурах.
Большая часть приведенной ниже информации любезно предоставлена веб-сайтом Федерального управления шоссейных дорог «Каждый день на счету».
Что такое теплая асфальтовая смесь?
Горячий асфальтобетон (HMA) — это традиционный процесс строительства асфальтовых покрытий.HMA производится на центральном смесительном предприятии (обычно называемом заводом горячего смешивания) и состоит из высококачественного заполнителя и асфальтобетона. Их нагревают и смешивают в горячем состоянии, чтобы полностью покрыть заполнитель асфальтовым цементом. Заполнители и асфальтовый цемент нагреваются до температуры выше 300 ° F во время смешивания и остаются горячими во время транспортировки грузовиком, укладки (когда он распределяется по проезжей части с помощью асфальтоукладчика) и уплотнения (когда он уплотняется серией асфальта). роликовые машины) асфальтобетонной смеси.После уплотнения смесь охлаждается, образуя асфальтовое покрытие.
WMA — это общий термин для различных технологий, которые позволяют производить, укладывать и уплотнять материал дорожного покрытия HMA при более низких температурах без ущерба для качества или производительности. Это проверенная технология, которая может:
- Снижение затрат на укладку
- Продлить сезон мощения
- Улучшить уплотнение асфальта
- Разрешить транспортировку асфальтовой смеси на большие расстояния
- Улучшение условий труда за счет снижения воздействия топливных выбросов, дыма и запахов
- Сократить выбросы парниковых газов
Более низкие температуры, более низкие затраты, больше возможностей
В методах производстваWMA используются температуры на 30–120 ° F ниже, чем при традиционном HMA.Поскольку для нагрева асфальтовой смеси требуется меньше энергии, для производства WMA требуется меньше топлива. Расход топлива при производстве WMA обычно снижается на двадцать процентов (20 процентов).
При укладке дорожного покрытия, чем больше разница между температурой асфальтобетонной смеси и внешней температурой, тем быстрее смесь остывает. Поскольку более быстрое охлаждение обеспечивает долговечность, низкие температуры окружающей среды отрицательно влияют на HMA. По сравнению с HMA, WMA охлаждается медленнее, что позволяет успешно размещать WMA при более низких температурах.В результате WMA продлевает сезон укладки. Это также делает более целесообразным ночное мощение.
Кроме того, WMA экономит время при производстве, а также при укладке дорожного покрытия. Поскольку WMA упрощает уплотнение, экономия средств достигается за счет сокращения времени и трудозатрат на уплотнение смеси. Более низкие температуры также позволяют перевозить больше асфальтовой смеси на большие расстояния, что снижает транспортные расходы.
Как это работает?
Для производства WMA было разработано множество различных технологий, некоторые из которых являются модификациями установки, а другие — добавками к смеси и / или асфальтовому вяжущему.«Процесс вспенивания» является наиболее распространенным типом технологии модификации установки WMA, когда небольшое контролируемое количество воды вводится в горячее асфальтовое связующее по мере его смешивания с частицами заполнителя. Горячее связующее превращает воду в пар, который, в свою очередь, заставляет асфальтовое связующее быстро расширяться и превращаться в пену (как при нажатии кнопки на банке крема для бритья). Увеличение объема вяжущего в 16 раз приводит к появлению (и свойствам) «чрезмерного асфальтирования» смеси, что облегчает укладку и уплотнение.Это увеличение объема связующего сохраняется до тех пор, пока температура не упадет ниже точки кипения воды, что приведет к схлопыванию пузырьков пара и застыванию смеси.
WMA также может быть произведен путем добавления специально разработанных присадок, многие из которых уменьшают вязкость (толщину) битумного вяжущего, так что на асфальтовые заполнители можно наносить покрытие при более низких температурах. Другие удерживают внутреннюю влагу и достигают того же типа вспенивания, что и упомянутые выше модификации установки.Эти добавки могут быть введены на асфальтовом заводе или приобретены у поставщика вяжущего уже в составе вяжущего. Ключевым моментом является добавление добавок (на водной основе, органических, химических или гибридных) к асфальтовой смеси. Добавки позволяют смешивать битумные вяжущие и асфальтовые заполнители при более низких температурах. Снижение вязкости также облегчает манипулирование смесью и делает ее более плотной при более низкой температуре.
Также можно комбинировать различные технологии WMA для повышения производительности.Например, многие асфальтовые заводы, оборудованные системами пенопласта, также используют химические добавки WMA для еще большего снижения температуры, добавки для уплотнения и противоскользящей обработки.
Лучшая производительность с WMA
Правильное уплотнение имеет решающее значение для хорошего состояния дорожного покрытия. Одним из признаков правильного уплотнения является плотность. Достижение надлежащей плотности важно, потому что большинство дорог с асфальтовым покрытием, финансируемых из федерального бюджета, принимаются на основе их плотности.WMA — это инструмент для уплотнения, который может помочь достичь надлежащей плотности и улучшить эксплуатационные характеристики дорожного покрытия.
WMA также универсален. Он успешно используется для покрытия различной толщины. Он достаточно прочен, чтобы выдерживать высокие нагрузки. WMA используется во всех типах асфальтобетона: плотного, с каменной матрицей, пористого и мастичного асфальта. Доступно несколько технологий WMA, поэтому выбор может быть адаптирован к требуемым температурам и материалам.
WMA успешно используется в Европе более 10 лет. В Соединенных Штатах проекты WMA сейчас реализуются более чем в 40 штатах.
Хорошо для рабочих, не вредно для окружающей среды
С WMA условия труда намного лучше. Как на производственном предприятии, так и на строительной площадке рабочие вдыхают гораздо меньше дыма и пыли. Это снижение особенно важно в туннелях, где снижена вентиляция.
WMA также производит меньше выбросов, что позволяет укладывать дорожное покрытие в некоторые дни, когда качество воздуха обычно мешает укладке дорожного покрытия. Представитель государственного транспортного сообщения недавно засвидетельствовал, что «в дни недостижения, когда качество воздуха плохое, мы часто отключаемся и не можем асфальтировать. Но с теплой смесью [асфальта], поскольку выбросы уменьшены, мы сможем укладывать асфальт даже в дни, когда качество воздуха не самое лучшее ».
Международное признание
WMA, несомненно, является важной технологией 21 века.Программа обучения людей, растений и дорожного покрытия «Мир асфальта» сосредоточила внимание на WMA, на конференции 2010 года было проведено несколько сессий. По крайней мере 14 государственных дорожных агентств приняли спецификации для размещения WMA, и более чем в 40 штатах дороги вымощены WMA. Эта зеленая технология повышает качество наших дорог и окружающей среды.
Министерство транспорта штата Вирджиния было лидером в принятии и использовании технологии WMA, реализовав разрешительную стратегию для всех асфальтовых смесей VDOT более пяти лет назад.Производительность была отличной, и нет никаких известных проблем с его использованием в Содружестве. Сегодня большинство производителей асфальта в Вирджинии используют одну или несколько технологий WMA для производства почти всех своих асфальтовых смесей VDOT.
Дополнительная информация о WMA
границ | Новый метод создания смесей для холодной заделки асфальтобетонной смеси
Введение
Горячий асфальтобетон широко используется при укладке и ремонте дорог благодаря его отличным характеристикам в качестве дорожного покрытия (Yang et al., 2011). Однако в процессе смешивания, транспортировки и укладки горячей асфальтовой смеси необходимая температура и ее контроль относительно высокие и строгие, соответственно (Li et al., 2017). Высокая температура вызывает не только большое потребление энергии, но и серьезное загрязнение окружающей среды (Diaz, 2016). Плохой контроль температуры приведет к старению асфальтовой смеси, что влияет на ее усталостные характеристики и срок службы (Khan et al., 2016; Liu et al., 2020). Горячую асфальтобетонную смесь нельзя производить при низких температурах и в дождливую погоду.Повреждения дорожного покрытия зимой можно отремонтировать только после апреля следующего года, что не только усугубляет повреждение дороги, но и влияет на ее комфорт и безопасность (Ling et al., 2007). Ввиду этих проблем, асфальтобетонная смесь для холодного ямочного ремонта (CPAM) очень популярна при ремонте дорожных покрытий благодаря своим превосходным характеристикам, таким как экологичность, низкая стоимость энергии, удобная процедура укладки и экологичность, а также тот факт, что она почти всегда готова к использованию. использовал.
В настоящее время на рынке представлено множество видов CPAM.По типу раствора их можно разделить на три типа: тип растворителя, тип эмульсии и тип реакции (Doyle et al., 2013). В существующих исследованиях CPAM в стране и за рубежом основное внимание уделяется повышению производительности. Подходы включают разработку влагостойкого CPAM, высокопрочного CPAM и стойкого к трещинам CPAM. Бентонит (разновидность наноглины с сильным водопоглощением) или осаждение микробного карбоната (MCP) были добавлены в CPAM с целью улучшения его способности к влагостойкости.Кроме того, эти добавки улучшают характеристики осушения и предотвращения повреждения водой, связанные с CPAM (Ling et al., 2016; Dong et al., 2018; Alenezi et al., 2019; Attaran Dovom et al., 2019). Кроме того, такого же эффекта можно добиться применением вяжущего материала вместо эмульсии. Обычно цемент добавляют в CPAM, когда от этой асфальтовой смеси требуется высокая прочность (Shanbara et al., 2018). Волокно добавляется к CPAM с целью значительного повышения его модуля упругости (Gómez-Meijide and Pérez, 2014).Улучшение свойств при растяжении играет жизненно важную роль в замедлении роста трещин в асфальтовой смеси, а остаточная деформация также значительно снижается. Асфальтобетонная смесь для холодного ямочного ремонта широко использовалась при реальном ремонте дорожного покрытия и достигла определенных результатов (Guo et al., 2014; Ma et al., 2016). Однако исследования, связанные с CPAM, не столь зрелы, как исследования, связанные с горячим ямочным ремонтом асфальтовой смеси. Ранняя производительность CPAM хуже, чем у горячей асфальтовой смеси. На механические свойства смеси сильно влияют последовательность перемешивания и образующаяся граница раздела.Стабильность скелета агрегата и прочность связи между агрегатом и связующим положительно связаны с сопротивлением колейности (Ma et al., 2018; Zhang et al., 2019; Chen et al., 2020). Не существует зрелого метода для разработки набора пропорций смеси для CPAM (Song et al., 2014; Saadoon et al., 2017). В настоящее время в большинстве исследований используется метод расчета пропорции смеси горячей асфальтобетонной смеси (метод расчета смеси Маршалла) для расчета CPAM (Li et al., 2010; Dash and Panda, 2018).Кроме того, методы эмпирических формул Калифорнийского университета и Университета Тонгжи также используются для расчета количества холодного битумного вяжущего (Song and Lv, 1998). Битумная смесь холодного ямочного ремонта отличается от горячей асфальтовой смеси тем, что не требует подогрева во время строительства. Метод расчета смеси Маршалла не подходит для проектирования CPAM, а параметры расчета смеси Маршалла (стабильность и величина потока) слабо коррелируют с дорожными характеристиками CPAM (Xu et al., 2018). На метод эмпирических формул сильно влияют градации и местный климат, а в методе расчета отсутствует контроль индекса объема, поэтому трудно гарантировать долговечность смеси (Meng et al., 2011).
Основываясь на характеристиках CPAM, в этом исследовании метод расчета смеси Маршалла был изменен. Были проверены дорожные характеристики трех видов CPAM, разработанных с использованием модифицированного метода расчета смеси Маршалла, метода расчета смеси Маршалла и метода эмпирических формул. Сравнительный анализ подтвердил полезность модифицированного метода расчета смеси Маршалла, который служит справочным материалом для разработки CPAM.
Материалы и методы
Сырье
Объектом исследования данного исследования является растворитель, используемый в CPAM, который состоит из чистого асфальта или модифицированного асфальта, разбавителя, добавки и заполнителя.
Чистый асфальт
Чистый асфальт, использованный в этом исследовании, — это дорожный нефтяной асфальт Sinopec Donghai 70PG #; были получены его основные технические характеристики, результаты представлены в таблице 1.
Таблица 1. Результаты испытаний технических показателей базового асфальта.
Разбавитель
Разбавитель может снизить вязкость асфальта, так что CPAM имеет хорошую обрабатываемость при низких температурах. Разбавитель должен хорошо растворяться в асфальте.Учитывая безопасность, летучесть и экономичность, разбавителем, использованным в этом исследовании, было дизельное топливо.
Добавка
Добавки для холодного ремонта обычно запатентованы производителем. В этом исследовании была оптимизирована добавка PR-JW03A. PR-JW03A был произведен компанией Shenzhen Jiashengwei Chemical Technology Co., Ltd. Эта добавка представляет собой специальный полимерный химический продукт, состоящий из различных полимеров, которые могут улучшить свойства асфальта при добавлении к обычному дорожному асфальту. Его технические показатели представлены в таблице 2.
Таблица 2. Технические показатели битумной добавки для холодного ремонта PR-JW03A.
Крупный заполнитель
Крупный заполнитель играет важную поддерживающую роль в каркасе смеси и является основной частью нагрузки на дорожное покрытие. В данном исследовании известняк использовался в качестве крупного заполнителя. Согласно требованиям спецификации получены соответствующие технические показатели крупного заполнителя; результаты испытаний приведены в таблице 3.
Таблица 3. Механический показатель крупного заполнителя.
Мелкий заполнитель
Мелкозернистый заполнитель заполняет зазоры, образованные крупным заполнителем, для получения плотной каркасной структуры, повышая долговечность дорожного покрытия. Мелким заполнителем, использованным в этом исследовании, был известняк.
Минеральный наполнитель
Минеральный наполнитель может не только заполнить промежутки между заполнителями, но также улучшить водостойкость CPAM. Кроме того, добавление минерального наполнителя увеличивает долю структурного асфальта, что увеличивает прочность CPAM.В данном исследовании выбранный минеральный наполнитель был получен путем измельчения известняка, и его основные свойства соответствовали требованиям спецификации, как показано в Таблице 4.
Таблица 4. Результаты испытаний минерального порошка.
Подготовка асфальта для холодной заделки
Основным инструментом для приготовления холодного ямочного асфальта является высокоскоростной диспергатор с диапазоном скоростей 0–10 000 об / мин. Также использовались электрическая печь, термометр, духовка, электронные весы и другие вспомогательные инструменты.
Лучшее соотношение для холодного ямочного асфальта, определенное в результате этого исследования, было добавка: асфальт: разбавитель = 1,8: 100: 25. Подготовительные шаги были следующими.
1) Нагрейте чистый асфальт в печи при 135 ° C в течение 2 часов, затем выньте его и нагрейте в электрической печи, чтобы поддерживать температуру около 135 ° C.
2) Добавьте добавку в (1), запустите диспергатор, вращайте со скоростью 200 об / мин и перемешивайте в течение получаса.
3) Добавьте дизельное топливо в (2), контролируйте температуру около 110 ° C и перемешивайте в течение 30 минут.
4) Подготовка завершена.
Подготовка асфальта для холодного ремонта и принцип действия показаны на Рисунке 1.
Рис. 1. Приготовление холодного ямочного асфальта с помощью диспергатора и соответствующий принцип. (A) Блок-схема приготовления асфальта при холодном ямочном ремонте. (B) Принцип приготовления асфальта при холодном ямочном ремонте.
Смешанный дизайн CPAM
Метод расчета смеси Маршалла был использован для определения доли каждого элемента, составляющего горячую асфальтобетонную смесь.Используя этот метод, исследователи накопили богатый практический опыт и данные. Асфальтовая смесь для холодного ямочного ремонта должна иметь не только хорошие дорожные характеристики на более позднем этапе, но и отличную обрабатываемость при низких температурах. На основе метода расчета смеси Маршалла были протестированы показатели теста Маршалла для CPAM. Кроме того, учитывая требования к производительности CPAM, был рассмотрен индекс низкотемпературной обрабатываемости. Объемные параметры готового образца были преобразованы в параметры, относящиеся к исходному образцу.В соответствии с соотношением между каждым индексом и соотношением заполнителей асфальта было определено наилучшее соотношение заполнителей асфальта для CPAM.
Градация
Как правило, для определения номинального максимального размера агрегата CPAM используется соотношение глубины покрытия h и максимального размера D заполнителя. Обычно считается, что h / D должно быть больше или равно 2. Толщина верхнего слоя асфальтового покрытия рассчитана на 4 см, а номинальный максимальный размер зерна верхнего слоя обычно составляет 13.2 мм. Учитывая характеристики поверхности раздела новой и старой смеси и согласно расчету h / D , номинальный максимальный размер заполнителя был определен как 13,2 мм.
В соответствии с Техническими спецификациями для строительства дорожных асфальтовых покрытий (JTG F40–2004,2004) в данном исследовании была принята градация LB-13. Оценка показана в Таблице 5.
Таблица 5. Градация LB-13.
Подготовка образцов по Маршаллу
В данном исследовании для формирования образца использовался второй метод уплотнения.Для этого сначала нужно уплотнить обе стороны по 50 раз. Затем образец помещают в форму для испытаний в печь при определенной температуре на 24 ч, стоя на боку. После извлечения образца из печи обе стороны сразу же уплотняют по 25 раз и извлекают из формы. Высота образца измеряется штангенциркулем и должна соответствовать критерию 63,5 ± 1,3 мм. Согласно Техническим условиям для строительства дорожных асфальтовых покрытий (JTG F40–2004,2004), начальная температура отверждения образца в этом исследовании была равна 110 ° C, но было обнаружено, что образец был рыхлым и отслоившимся. после отверждения.Этот факт показывает, что температура отверждения 110 ° C была слишком высокой, и она не подходила для CPAM типа растворителя. Поэтому, учитывая скорость улетучивания разбавителя внутри образца и целостность образца, были предварительно выбраны четыре различных температуры отверждения: 60, 75, 90 и 100 ° C. После отверждения была получена стабильность образца по Маршаллу, результаты показаны на рисунке 2.
Рисунок 2. Стабильность CPAM при различных температурах отверждения.
Как видно из рисунка 2, стабильность увеличивается с повышением температуры. Значение быстро увеличивается от 60 до 90 ° C, а затем медленно увеличивается от 90 до 100 ° C. Согласно техническим условиям для строительства дорожных асфальтовых покрытий (JTG F40–2004,2004), устойчивость CPAM по Маршаллу не должна быть менее 3 кН, и образец может соответствовать этому требованию, когда температура отверждения превышает 90 °. С. Принимая во внимание скорость роста стабильности по Маршаллу с температурой, целостность образца для испытаний, а также экономические факторы и факторы затрат на энергию, конечная температура отверждения, принятая в этом исследовании, была равна 90 ° C.
Определение отношения заполнителя асфальта
В соответствии с уровнем улетучивания разбавителя в CPAM, стадия формирования CPAM может быть разделена на два состояния: исходное и окончательно сформированное состояния. Разбавитель внутри CPAM в окончательно сформированном состоянии в основном испарился. Однако разбавитель в CPAM в первоначально сформированном состоянии еще не начал улетучиваться, поэтому CPAM в этом состоянии можно рассматривать как типичную горячую смесь. При постепенном испарении разбавителя объемные параметры CPAM в окончательно сформированном состоянии могут быть получены путем использования всех объемных параметров первоначально сформированного образца.Следовательно, оптимальное содержание связующего в CPAM можно определить не только по параметрам окончательно сформированного образца. Параметр объема, который следует использовать, — это параметр объема первоначально сформированного образца, который можно рассматривать как обычную горячую смесь (Gu, 2017).
Наиболее очевидной характеристикой CPAM является то, что он может быть разработан в нормальных и низкотемпературных условиях. Следовательно, CPAM должен быть рыхлым при низкой температуре, что удобно для разбрасывания и уплотнения.В данном исследовании при разработке смесей учитывались показатели низкой температуры и удобоукладываемости.
Преобразование параметров объема
Все измеренные объемные параметры окончательно сформированного образца были преобразованы в объемные параметры первоначально сформированного образца. Перед уплотнением регистрировали качество м p смеси в каждой испытательной форме.
Объемный удельный вес r pf первоначально сформированного образца был рассчитан по формуле (1),
rpf = mpmf-mw (1)
, где m f и m w — поверхностная сухая масса образца и водная масса образца, соответственно, г.
Теоретический максимальный удельный вес r pt первоначально сформированного образца был рассчитан по формуле (2),
rpt = rt (ma-mw) + (mp-ma) (ma-mw) + (mp-ma) = rt (ma-mw) + (mp-ma) (mp-mw) (2).
, где м a — воздушная масса образца, г и r t — теоретический максимальный удельный вес.
По формулам (3) — (5) рассчитывается процент пустот в минеральном заполнителе pvma , процент воздушных пустот pvv и процент пустот в минеральном заполнителе, заполненном асфальтом pvfa ,
pvma = (1-rpfrsb × пс) × 100 (3)
pvv = (1-rpfrpt) × 100 (4)
pvfa = pvma-pvvpvma × 100 (5)
, где r sb — объемная плотность синтетического материала, г / см 3 и p s — отношение качества минерального заполнителя к общему качеству асфальтовой смеси,%.
Объемные параметры изначально сформированного образца получены по приведенной выше формуле. Была получена взаимосвязь между каждым параметром объема и долей асфальтового заполнителя. В соответствии с методом определения оптимального соотношения асфальтового заполнителя горячей смеси асфальтобетонной смеси, было определено оптимальное соотношение асфальтового заполнителя CPAM.
Определение оптимального отношения заполнителя асфальта
Результаты испытаний по Маршаллу готовых формованных образцов показаны в таблице 6.
Таблица 6. Результаты испытаний объемных параметров и механических показателей готовых формованных образцов.
Сохраняя стабильность неизменной, объемные параметры окончательно сформированного образца были преобразованы в объемные параметры первоначально сформированного образца. Результаты расчетов представлены в таблице 7.
Таблица 7. Объемные параметры и результаты механического индекса исходно сформированных образцов.
На рис. 3 показана взаимосвязь между долей заполнителя асфальта и каждым показателем первоначально сформированного образца.
Рис. 3. (A) Взаимосвязь между долей заполнителя асфальта и rpf; (B) соотношение между долей асфальтового заполнителя и PVV; (C) соотношение между долей асфальтового заполнителя и PVFA; (D) взаимосвязь между долей заполнителя асфальта и стабильностью.
Суммируя, можно сказать, что коэффициент заполнителя асфальта a 1 , a 2 , a 3 , a 4 , соответствующий максимальной устойчивости, максимуму r pf , среднему расчетному диапазону pvv и средний диапазон pvfa были определены из рисунка 3.Согласно формуле (6), среднее значение четырех соотношений заполнителей асфальта является начальным значением OAC 1 оптимального соотношения заполнителей асфальта.
OAC1 = (a1 + a2 + a3 + a4) / 4 = (5,56% + 5,65% + 5,43% + 4,98%) / 4 = 5,405% (6)
На основании результатов испытаний каждого индекса был определен диапазон содержания асфальта, соответствующий техническим стандартам. В соответствии с Техническими условиями для строительства дорожных асфальтовых покрытий (JTG F40–2004,2004) устойчивость по Маршаллу должна быть не менее 3 кН. pvma и pvfa относятся к стандарту испытаний Маршалла для горячей асфальтовой смеси. Следовательно, для pvv требуется, чтобы коэффициент асфальтового заполнителя был выше 5,3%. Доля асфальтового заполнителя должна быть выше 5% для pvfa .
CPAM должен иметь отличную обрабатываемость при комнатной температуре. Поэтому в данном исследовании основное внимание уделяется обрабатываемости в условиях низких температур. Битумная смесь холодного ямочного ремонта была приготовлена с вариациями 0.2% в соотношении асфальтового заполнителя. В соответствии с Техническими спецификациями для строительства дорожных асфальтовых покрытий (JTG F40–2004,2004), CPAM помещали в холодильник при -10 ° C на 24 часа. Если в смеси нет явного явления агломерации, ее можно легко перемешать лопатой. Битумная смесь холодного ямочного ремонта была извлечена из холодильника и показала хорошую обрабатываемость при низких температурах. Результаты испытаний представлены в таблице 8.
Таблица 8. Результаты испытаний низкотемпературной работоспособности CPAM.
Согласно результатам испытаний, приведенным в Таблице 8, доля заполнителя асфальта должна составлять 5,2–5,4% для низкотемпературной обрабатываемости. Начальное значение оптимальной доли асфальтового заполнителя OAC 2 было рассчитано по формуле. (7).
OAC2 = (OACmin + OACmax) / 2 = (5,3% + 5,4%) / 2 = 5,35% (7)
Оптимальный коэффициент асфальтобетонной крошки CPAM рассчитывается по формуле (8),
OAC = (OAC1 + OAC2) / 2 = (5.405% + 5,35%) / 2 = 5,38% (8)
Оптимальная доля асфальтового заполнителя в CPAM, полученная с использованием модифицированного метода расчета смеси Маршалла, составила 5,38%.
Проверка ходовых качеств
В этом исследовании оптимальное соотношение заполнителей асфальта в CPAM, полученное с использованием традиционного метода расчета смеси Маршалла, было равно 5,52%. Кроме того, эмпирическая формула, предложенная Л.В. Вэйминь из Университета Тунцзи, была использована для определения оптимального соотношения заполнителей асфальта для CPAM. Формула расчета следующая.
P = 0,021a + 0,056b + 0,099c + 0,12d + 1,2 (9)
, где P — доля заполнителя асфальта,%, a — массовый процент заполнителя с размером частиц более 2,36 мм,%, b — массовый процент заполнителя с размером частиц от 0,3 до 2,36 мм,%, c — массовый процент заполнителя с размером частиц от 0,075 до 0,3 мм,%, а d — массовый процент заполнителя с размером частиц менее 0,075 мм,%.
Согласно формуле. Согласно (9) коэффициент заполнителя асфальта, рассчитанный с использованием эмпирической формулы, составил 4,5%.
Чтобы проверить полезность модифицированного метода расчета смеси Маршалла, предложенного в этом исследовании, были проведены испытания дорожных характеристик CPAM, разработанного различными методами. Блок-схема испытания показана на Рисунке 4.
Рисунок 4. Блок-схема теста дорожных характеристик CPAM.
Метод испытаний
Начальная сила
На ранней стадии CPAM разбавитель не улетучивается, и сцепление между минералами невелико.Первоначальная прочность в основном поддерживается интеркалированием и трением между агрегатами (Nassar et al., 2016). Чтобы покрытие могло выдержать неплотное повреждение, вызванное качением транспортных средств на начальном этапе ремонта, необходимо убедиться, что начальная прочность CPAM достигает определенного значения.
Метод испытания начальной прочности был следующим: берут около 1100 г CPAM (в зависимости от высоты образца, соответствующей 63,5 ± 1,3 мм) и помещают его в форму для испытаний по Маршаллу.Упакуйте верхнюю и нижнюю стороны соответственно 75 раз с помощью автоматического компактора Маршалла. Стабильность можно проверить после демонтажа из формы.
Предел прочности при формовании
Метод испытания формовочной прочности следующий. Возьмите 1100 г CPAM (в зависимости от высоты образца, соответствующей 63,5 ± 1,3 мм) и поместите его в форму для испытаний по Маршаллу. Упакуйте верхнюю и нижнюю стороны соответственно 75 раз с помощью автоматического компактора Маршалла. После этого образец с формой для испытаний выдерживают в печи при 90 ° C в течение 24 часов, затем вынимают из печи и уплотняют с обеих сторон 25 раз.После демонтажа из формы проводится испытание на стабильность по Маршаллу.
Стабильность хранения
CPAM можно разделить на CPAM горячего смешивания и CPAM холодного смешивания в соответствии с условиями смешивания. Горячую смесь CPAM можно хранить около двух лет (Dulaimi et al., 2017). В процессе хранения следует убедиться, что CPAM не испытывает высокой степени агломерации, чтобы облегчить его размещение и уплотнение во время строительства. В этом исследовании CPAM хранился и герметизировался в течение 0, 3, 7 и 28 дней при нормальной температуре.Затем была проверена начальная прочность, и описанный выше метод был использован для оценки удобоукладываемости через 28 дней.
Устойчивость к воде
Стабильность CPAM в воде была оценена путем проведения иммерсионного теста Маршалла и теста на расщепление при замораживании-оттаивании. Испытание следует проводить в соответствии со Стандартными методами испытаний битума и битумных смесей для дорожного строительства (JTG E20–2011,2011).
Высокотемпературные характеристики
В этом исследовании гамбургский тест на колейность использовался для оценки высокотемпературных характеристик CPAM.В соответствии с методом формирования образца колейности горячей смеси асфальта в сочетании с характеристиками CPAM формирование образца колейности выполняли следующим образом.
Возьмите CPAM, поместите его в испытательную форму и сначала выполните ручное уплотнение. Затем скатайте CPAM два раза в одном направлении и 12 раз в другом, используя гидравлическую колейную машину. Поместите CPAM с испытательной формой в печь при 90 ° C на 24 часа, затем выньте ее и проведите вторую прокатку в соответствии с первым методом прокатки.Гамбургское испытание на колейность должно проводиться в соответствии со Стандартными методами испытаний битума и битумных смесей для дорожного строительства (JTG E20–2011,2011).
Результаты и обсуждение
Начальная сила
Была протестирована начальная сила трех видов CPAM (метод расчета эмпирических формул, метод расчета смеси Маршалла и модифицированный метод расчета смеси Маршалла). Результаты испытаний показаны на рисунке 5.
Рисунок 5. Результаты для начальной численности CPAM.
Из рисунка 5 видно, что CPAM с долей асфальтового заполнителя 5,38% имеет наибольшую начальную прочность. Начальная прочность 4,5% асфальтового заполнителя самая низкая. Это связано с тем, что количество связующего вещества невелико, а прочность смеси в основном поддерживается трением между агрегатами. Нет никаких конкретных требований к начальной силе CPAM. В США и Сун Цзяньшэн, Китай, требуется начальная сила более 2 кН.Начальная прочность CPAM с долей асфальтового заполнителя 5,38 и 5,52% равна 2,84 и 2,53 кН соответственно, что соответствует этому требованию. Коэффициент асфальтового заполнителя, полученный методом эмпирических формул, слишком низок, так что начальная прочность слишком мала и не соответствует требованиям.
Формовочная прочность
Прочность при формовании трех видов CPAM была измерена в соответствии с методом испытаний, описанным в разделе «Прочность при формовании». В этом разделе сравнивается начальная прочность и прочность при формовании; результаты показаны на рисунке 6.
Рисунок 6. Результаты формообразования CPAM.
Формирующая сила складывается из когезии и внутреннего трения. Из рисунка 6 можно заметить, что формовочная прочность трех CPAM в основном вдвое превышает исходную прочность. Это связано с тем, что вязкость связующего увеличивается, а когезия CPAM увеличивается в результате улетучивания разбавителя. Формовочная прочность CPAM с долей асфальтового заполнителя 5,38% достигает наивысшего значения, равного 6.13 кН. Формовочная прочность CPAM с долей асфальтового заполнителя 4,5% имеет наименьшее значение, поскольку количество связующего слишком мало, а когезия недостаточна. Когда доля асфальтового заполнителя равна 5,52%, содержание связующего в CPAM слишком велико, и имеется большое количество свободного асфальта. Большая или меньшая доля асфальтового заполнителя неблагоприятна для формообразования CPAM. По сравнению с двумя другими методами, прочность формования CPAM, разработанная с использованием модифицированного метода расчета смеси Маршалла, формируется быстрее.
Стабильность хранения
Три CPAM были подготовлены с использованием трех различных методов проектирования. Затем разработанные образцы CPAM хранились и запечатывались в течение определенного периода времени, а затем были проверены их первоначальная прочность и удобоукладываемость. Результаты испытаний представлены в Таблице 9.
Таблица 9. Результаты тестирования производительности хранилища для CPAM.
Согласно Таблице 9, соотношение между начальной мощностью и временем хранения трех CPAM является согласованным.Начальная прочность увеличивается с увеличением времени хранения во всех случаях. После 28 дней хранения сила трех видов CPAM мало меняется; отклонение составляет менее 0,2 кН. Начальная прочность относительно стабильна. Степень удобоукладываемости CPAM, разработанного с использованием метода расчета смеси Маршалла, была равна 4, что означает, что его обрабатываемость при низких температурах была плохой. Результаты показывают, что содержание асфальта в CPAM, разработанном с использованием метода расчета смеси Маршалла, слишком велико, и он легко агломерируется.Тем не менее, работоспособность при низких температурах CPAM, разработанная с использованием модифицированного метода расчета смеси Маршалла, была приемлемой.
Устойчивость к воде
Испытание Маршалла иммерсией и испытание на расщепление при замораживании-оттаивании проводились с целью тестирования трех видов CPAM с различным соотношением заполнителей асфальта. Изучена водостойкость CPAM с различным соотношением заполнителей асфальта и сравнивается с таковой горячей асфальтовой смеси. Результаты иммерсионного теста Маршалла показаны на рисунке 7, а результаты теста разделения замораживания-оттаивания показаны на рисунке 8.
Рис. 7. Результаты иммерсионного теста Маршалла для CPAM.
Рис. 8. Результаты теста на раскалывание при замораживании-оттаивании для CPAM.
Из рисунка 7 видно, что остаточная стабильность образцов CPAM с долей заполнителя асфальта 5,38 и 5,52% соответствует требованиям остаточной стабильности для горячей асфальтовой смеси. Остаточная стабильность CPAM с долей асфальтового заполнителя 4,5% низкая. Это связано с отсутствием связующего и большим процентом воздушных пустот.Из рисунка 8 можно заметить, что соотношение прочности на раскалывание при замораживании-оттаивании трех CPAM соответствует требованиям для горячей асфальтовой смеси. Порядок соотношений прочности при замораживании-оттаивании следующий: 5,38% CPAM> 5,52% CPAM> 4,5% CPAM. Это показывает, что CPAM, разработанный с помощью модифицированного метода расчета смеси Маршалла, имеет лучшую водостойкость. Остаточная стабильность и коэффициенты прочности при раскалывании при замерзании и таянии трех видов CPAM ниже, чем у горячей асфальтовой смеси.Поскольку разбавитель не испарился полностью, CPAM не полностью сформирован, и, следовательно, его характеристики плохие.
Высокотемпературные характеристики
Гусеничные доски были сформированы по методике, описанной в разделе «Высокотемпературные характеристики». Гамбургский тест на колейность был проведен для тестирования трех видов CPAM, результаты показаны на Рисунке 9.
Рис. 9. Результаты теста на высокотемпературную стабильность CPAM.
Из рисунка 9 видно, что динамическая стабильность CPAM, разработанного с использованием модифицированного метода расчета смеси Маршалла, была немного выше, чем у CPAM, разработанной с помощью двух других методов.Динамическая стабильность CPAM с долей асфальтового заполнителя 4,5% показывает наименьшее значение, потому что количество связующего слишком мало, а когезия плохая, что приводит к тому, что смесь имеет сухую текстуру. Динамическая стабильность CPAM с долей асфальтового заполнителя 5,52% ниже, чем у CPAM с долей заполнителя 5,38%. Это может быть связано с тем, что прежний CPAM имеет большее количество связующего и толстую асфальтовую пленку. Увеличение свободного асфальта приводит к перемещению и пластической деформации при высокой температуре.Общая динамическая стабильность CPAM низкая, поскольку прочность смеси еще не сформирована. Устойчивость к колейности в этих условиях не является окончательной характеристикой CPAM.
Заключение
Метод расчета смеси Маршалла был изменен с целью разработки CPAM. Была проведена серия испытаний дорожных характеристик CPAM, разработанных с использованием метода расчета смеси Маршалла, метода эмпирических формул и модифицированного метода расчета смеси Маршалла.Испытания включали испытание на начальную прочность, испытание на прочность при формовании, испытание на стабильность при хранении, испытание на водостойкость и испытание на стабильность при высоких температурах. Результаты сравнительного анализа подтвердили полезность и осуществимость модифицированного метода расчета смеси Маршалла. На основании результатов этого ограниченного лабораторного исследования можно сделать следующие выводы.
• В этой статье рекомендуемая температура отверждения для образца CPAM составляла 90 ° C. Оптимальный коэффициент асфальтового заполнителя CPAM, полученный с использованием модифицированного метода расчета смеси Маршалла, был равен 5.38%. Это значение находилось между оптимальным соотношением заполнителей асфальта, полученным с использованием традиционного метода расчета смеси Маршалла, и значением, полученным с использованием метода эмпирических формул.
• Дорожные характеристики CPAM, разработанного с использованием модифицированного метода расчета смеси Маршалла, были лучше, чем у модели CPAM, разработанной с использованием традиционного метода расчета смеси Маршалла и метода эмпирических формул. Модифицированный метод расчета смеси Маршалла осуществим.
• Сила CPAM увеличивается со временем.Формовочная прочность была примерно в два раза выше начальной прочности.
• Структура микширования CPAM должна учитывать его собственные характеристики. В этой статье преобразование параметров объема и добавление требования к низкотемпературной обрабатываемости позволяют улучшить дизайн CPAM. Рекомендуется использовать модифицированный метод расчета смеси Маршалла в качестве процедуры расчета смеси для CPAM.
Заявление о доступности данныхВсе наборы данных, созданные для этого исследования, включены в статью / дополнительный материал.
Авторские взносы
SL руководил всем процессом написания рукописи. SW, CX и CL провели эксперименты и анализ данных. Все авторы проанализировали результаты и внесли свой вклад в написание рукописи.
Конфликт интересов
Авторы заявляют, что исследование проводилось при отсутствии каких-либо коммерческих или финансовых отношений, которые могут быть истолкованы как потенциальный конфликт интересов.
Финансирование
Эта работа была поддержана Национальным фондом естественных наук Китая (51578081, 51608058), Научно-технологическим инновационным проектом провинции Хунань для аспирантов университетов (CX2019B ∗∗∗ ), Проектом открытого фонда Национальной инженерной лаборатории (kfh260102 ), Провинция Хунань — Транспортные строительные проекты науки и технологий (201701), Транспортные проекты Департамента транспорта и транспорта Автономного района Внутренней Монголии (NJ-2016-35, HMJSKJ-201801), Национальная программа ключевых исследований и разработок Китая ( 2018YFB1600100), Фонд естественных наук провинции Хунань (2018JJ3550), Департамент образования провинции Хунань (18B144) и Проект науки и технологий Департамента транспорта провинции Хэнань (2016Z2).
Благодарности
Мы хотим поблагодарить рецензентов и редакторов за советы по поводу этой статьи.
Список литературы
Аленези, Т., Норамбуэна-Контрерас, Дж., Доусон, А., и Гарсия, А. (2019). Новый тип материала для дорожного покрытия из холодной смеси, состоящий из альгината кальция и заполнителей. J. Clean. Продукт. 212, 37–45. DOI: 10.1016 / j.jclepro.2018.11.297
CrossRef Полный текст | Google Scholar
Аттаран Довом, Х., Мохаммадзаде Могхаддам, А., Карраби, М., и Шахнаваз, Б. (2019). Повышение устойчивости к воздействию влаги холодных асфальтовых смесей, модифицированных экологически чистыми микробными карбонатными осадками (MCP). Констр. Строить. Матер. 213, 131–141. DOI: 10.1016 / j.conbuildmat.2019.03.262
CrossRef Полный текст | Google Scholar
Чен, Т., Луан, Ю., Ма, Т., Чжу, Дж., Хуанг, X., и Ма, С. (2020). Механические и микроструктурные характеристики различных поверхностей раздела в смеси холодного вторичного использования, содержащей цемент и битумную эмульсию. J. Clean. Продукт. 258: 120674. DOI: 10.1016 / j.jclepro.2020.120674
CrossRef Полный текст | Google Scholar
Дэш, С.С., Панда, М. (2018). Влияние параметров смеси на конструкцию холодной битумной смеси. Construct. Строить. Матер. 191, 376–385. DOI: 10.1016 / j.conbuildmat.2018.10.002
CrossRef Полный текст | Google Scholar
Диас, Л. Г. (2016). Оценка ползучести смесей для ремонта асфальта холодной смеси. Внутр. Дж.Тротуар Res. Technol. 9, 149–158. DOI: 10.1016 / j.ijprt.2016.04.002
CrossRef Полный текст | Google Scholar
Донг, К., Юань, Дж., Чен, X., и Ма, X. (2018). Снижение влаговосприимчивости холодной асфальтовой смеси с добавками портландцемента и бентонитовой наноглины. J. Clean. Продукт. 176, 320–328. DOI: 10.1016 / j.jclepro.2017.12.163
CrossRef Полный текст | Google Scholar
Дойл, Т.А., Макнелли, К., Гибни, А., и Табакович, А.(2013). Разработка методов оценки зрелости битумных материалов холодных смесей. Construct. Строить. Матер. 38, 524–529. DOI: 10.1016 / j.conbuildmat.2012.09.008
CrossRef Полный текст | Google Scholar
Дулайми А., Аль-Нагейм Х., Раддок Ф. и Сетон Л. (2017). Высокоэффективная холодная асфальтобетонная смесь для вяжущего слоя с использованием щелочно-активированного бинарного вяжущего наполнителя. Construct. Строить. Матер. 141, 160–170. DOI: 10.1016 / j.conbuildmat.2017.02.155
CrossRef Полный текст | Google Scholar
Гомес-Мейиде, Б., и Перес, И. (2014). Предлагается методика глобального исследования механических свойств холодных асфальтобетонных смесей. Mater. Проект 57, 520–527. DOI: 10.1016 / j.matdes.2013.12.079
CrossRef Полный текст | Google Scholar
Гу, С. (2017). Структурные характеристики и оценка испытаний битумной смеси холодного ремонта. Магистерская диссертация, Юго-Восточный университет, Нанкин.
Google Scholar
Го М., Тан Ю. и Чжоу С. (2014). Многоуровневое испытание свойств межфазной адгезии холодного асфальта. Construct. Строить. Матер. 68, 769–776. DOI: 10.1016 / j.conbuildmat.2014.06.031
CrossRef Полный текст | Google Scholar
JTG E20–2011 (2011 г.). Стандартные методы испытаний битума и битумной смеси для дорожного строительства. Пекин: China Communications Press.
Google Scholar
JTG F40–2004 (2004 г.). Технические условия на строительство автомобильных дорог с асфальтовым покрытием. Пекин: China Communications Press.
Google Scholar
Хан А., Ределиус П. и Крингос Н. (2016). Оценка адгезионных свойств поверхностей раздела минерал-битум в холодных асфальтобетонных смесях. Construct. Строить. Матер. 125, 1005–1021. DOI: 10.1016 / j.conbuildmat.2016.08.155
CrossRef Полный текст | Google Scholar
Ли, Ф., Хуан, С. К., Сюй, Дж., И Цинь, Ю.С. (2010). Исследования по составлению асфальтобетонных смесей холодного ямочного производства. J. Wuhan Univ. Sci. Technol. 32, 79–82.
Google Scholar
Ли, Дж. Х., Нан, Б. З., и Гао, Дж. Т. (2017). Исследование состава и характеристик битумной смеси холодного ямочного ремонта. шоссе трансп. Technol. 13, 199–200 227.
Google Scholar
Линг, К., Ханц, А., и Баия, Х. (2016). Измерение чувствительности асфальта холодной смеси к влаге с помощью модифицированного теста на кипение, основанного на цифровых изображениях. Construct. Строить. Матер. 105, 391–399. DOI: 10.1016 / j.conbuildmat.2015.12.093
CrossRef Полный текст | Google Scholar
Линг, Дж. М., Чжоу, З. Ф., и Пэн, Дж. К. (2007). Приготовление и выполнение хранения асфальтовой смеси для ремонта дорожного покрытия. J. Build. Матер. 10, 195–200.
Google Scholar
Лю, К. К., Львов, С. Т., Пэн, X. Х., Чжэн, Дж. Л., и Ю, М. (2020). Анализ и сравнение различных воздействий старения и частоты нагружения на характеристики усталости асфальтобетона. J. Mater. Civ. Англ. 32: 04020240. DOI: 10.1061 / (ASCE) MT.1943-5533.0003317
PubMed Аннотация | CrossRef Полный текст | Google Scholar
Ма, К. Х., Син, Х. Т., Сюй, Х. С., Ли, Дж. З., и Фэн, Х. Х. (2016). Приготовление и анализ характеристик холодного ямочного ремонта асфальтобетонной смеси. J. S. Univ. 46, 594–598.
Google Scholar
Ма, Т., Чжан, Д., Чжан, Ю., Ван, С., и Хуанг, X. (2018). Имитационное моделирование теста слежения за колесом для асфальтобетонной смеси с использованием моделирования дискретных элементов. Road Mater. Дизайн дорожной одежды 19, 367–384. DOI: 10.1080 / 14680629.2016.1261725
CrossRef Полный текст | Google Scholar
Мэн, У. З., Янг, Л., Ся, З., Ван, X. Y., Сюэ, Дж., Ву, Дж. Й. и др. (2011). Приготовление и свойства асфальтовой смеси холодного ямочного ремонта. J. Wuhan Univ. Англ. 33, 49–53.
Google Scholar
Нассар А. И., Том Н. и Парри Т. (2016). Оптимизация конструкции смеси холодных битумно-эмульсионных смесей с использованием методологии поверхности отклика. Construct. Строить. Матер. 104, 216–229. DOI: 10.1016 / j.conbuildmat.2015.12.073
CrossRef Полный текст | Google Scholar
Саадун, Т., Гарсия, А., Гомес-Мейджиде, Б. (2017). Динамика испарения воды в холодных асфальтобетонных смесях. Mater. Проект 134, 196–206. DOI: 10.1016 / j.matdes.2017.08.040
CrossRef Полный текст | Google Scholar
Шанбара, Х. К., Раддок, Ф., и Атертон, В. (2018). Лабораторное исследование высокоэффективных холодных асфальтобетонных смесей, армированных натуральными и синтетическими волокнами. Construct. Строить. Матер. 172, 166–175. DOI: 10.1016 / j.conbuildmat.2018.03.252
CrossRef Полный текст | Google Scholar
Сонг, Дж. С., и Львов, В. М. (1998). Исследование по составу асфальтобетонной смеси для хранения. J. Tongji Univ. 26, 664–668.
Google Scholar
Сонг, X.F., Fan, Z.H., и Wang, Y.F. (2014). Изучение таких же условий твердения бетона большого объема на основе методов зрелости. Adv. Матер. Res. 893, 593–596.DOI: 10.4028 / www.scientific.net / AMR.893.593
CrossRef Полный текст | Google Scholar
Сюй, В., Мэй, Х., Луо, Р., Го, X. Л., и Ван, X. (2018). Конструкция материала и характеристики смеси для холодного ямочного асфальта. J. Wuhan Univ. Sci. Technol. 42, 1049–1054.
Google Scholar
Янг, Л., Мэн, В. З., Ван, X. Х., Ся, З., Ван, X. Y., Сюэ, Дж., И др. (2011). Влияние неорганического наполнителя на прочность асфальтобетонной смеси холодного ремонта. Дж.Wuhan Univ. Англ. 33, 47–51.
Google Scholar
Чжан, Ю., Ма, Т., Линг, М., Чжан, Д., и Хуанг, X. (2019). Прогнозирование динамического модуля сдвига асфальтобетонных мастик с использованием дискретных элементов моделирования и механизмов армирования. J. Mater. Civil Eng. 31: 04019163. DOI: 10.1061 / (ASCE) MT.