Состав пенобетонных блоков — Портал о цементе и бетоне, строительстве из блоковПортал о цементе и бетоне, строительстве из блоков
Дата: 23.04.2014
Использование пенобетона для возведения сооружений разного назначения достаточно распространенное явление в современном строительстве. Профессиональные строители отмечают отличные качества строительного материала — пеноблока, его экологичность и экономность. В состав пеноблока входят пенообразующие добавки и цементный раствор. Возведенные из пенобетона дома сохраняют зимой тепло, а летом прохладу, отличаются высоким показателем звукоизоляции, огнестойкости, теплоизоляционными свойствами.
Состав пенобетона
Для приготовления прочного пенобетона необходимо тщательно подбирать все компоненты, входящие в его состав, правильно задавать объемный вес, режим влажности бетона и тепловлажностной обработки.
Производство пеноблоков выполняется согласно нормативам и технологиям с подбором составляющих по ГОСТ 25485-89.
Согласно ГОСТ 8736 входит песок с 75% содержанием кварца.
Портландемент выбирается по ГОСТ 10178.
Пенообразователь на сосновой канифоли должен соответствовать ГОСТ 191113. Если в основе пенообразователя находится костный клей, он должен быть выбран по ГОСТ 2067. ГОСТ 3252 применяют при выборе пенообразователя на мездровом клее. ГОСТ 2263 применяют для пенообразователя с техническим натром.
Воду проверяют на соответствие с ГОСТ 23732.
Составы пенобетонных смесей могут быть приготовлены с разным соотношением компонентов, что позволяет производить пеноблоки разных классов. От класса пенобетона зависит, где будут использованы готовые изделия. Пеноблоки используют для кладки термоизоляционных крыш, междуэтажных термо- и звукоизоляционных покрытий, внутренних перегородок и наружных стен.
Прочность бетона, минимальную усадку при высыхании, повышенную морозостойкость, сниженную теплопроводность получают путем введения комплексных добавок.
Формовой пенобетон
В пеногенераторе на воде взбивается пенообразователь. В смесителе песок и цемент смешиваются с пеной. Во время замеса при помощи компрессора увеличивается давление. Сметаноподобная паста из смесительного бункера по высоким давлением разливается в разделенные на секции формы.
Резанный пенобетон
Для получения бетона этого вида используют большую форму, а затем застывшую массу разрезают на блоки нужных размеров. Готовые блоки нужно выдержать до 25 дней и лишь только потом отправлять на продажу.
Состав пенобетона в отличии от газобетона не содержит известь и алюминиевую пудру, выполняющую роль порообразователя при изготовлении газоблоков. И тот и другой стройматериал обладает прекрасными качествами и успешно используется в строительстве.
Преимущества использования пенобетона:
- Экономия на отоплении составляет до 30% благодаря минимальной теплопроводности строительных пеноблоков.
- Закрыто-пористая структура сделала материал влагостойким и морозостойким.
- Высокий коэффициент огнестойкости позволяет противостоять открытому огню свыше 3 часов.
- Отличный показатель звукоизоляции делает дома комфортными и защищенными от внешних звуков.
- Для здания из пенобетона не нужно возводить фундаменты повышенной прочности, поскольку пенобетон имеет небольшой вес и здание из него дает меньшую нагрузку на фундамент.
- Экологически чистый материал без содержания химических вредных веществ.
- Быстрый и легкий монтаж возможен благодаря большим размерам блоков и их легкому весу.
- Идеальная поверхность блоков дает возможность сэкономить на связующем растворе.
Какие компоненты входят в состав пенобетона?
Основным отличием пенобетона от бетона стандартного можно считать пористую структуру, легкость. Состав пенобетона играет большую роль для получения дышащего, водонепроницаемого, легкого материала.
Описание состава
Состав пенобетона должен соответствовать нормативным документам.
Раствор включает: цемент, песок, воду, образователи пены, дополнительные составляющие. Все ингредиенты должны отвечать стандартам. В зависимости от пропорций создают пенобетон разных марок, прочности.
Вернуться к оглавлению
Вяжущие
Вяжущей составной частью выступают известь, портландцемент — главное вещество, используемое строителями для возведения любого объекта. Соответствует ГОСТу 10178-85.
Вернуться к оглавлению
Цемент
Портландцемент твердеет под воздействием воды, воздуха. Представляет собой состав из известняка, глины, которые изначально поддали обжиганию. После спекания смеси происходит обогащение силикатом кальция.Качество клинкера — гранул смеси, влияет на прочность, устойчивость, долговечность сооружения. К нему добавляют гипс, позволяющий контролировать период схватывания стандартного цемента.
Портландцемент делится на 3 вида:
- D0 — отсутствуют добавки;D5 — смеси имеют меньше пяти процентов минеральных добавок активного действия;D20 — количество добавок варьирует от пяти до двадцати процентов, включая 10 % добавок — минералов гидравлического происхождения.
Марка цемента, используемого для пенобетона, плотностью 500 кг / м3, 400 кг / м3 с нулевым количеством примесей. Иногда используют марку 400 — 500, добавки в который составляют больше 5 %.
Вернуться к оглавлению
Известь
Иногда основным вяжущим компонентом выступает известь.
Использование извести зависит от технологии изготовления ячеистого бетона. Основные требование к веществу: равномерный обжиг, общая активность выше 75 %, магния в составе меньше полутора процента. Общая активность извести определяется количеством активных окисей кальция, магния.
Известь могут использовать в виде молотой кипелки, пушонки. В замес добавляют двудонный гипс, замедляющий скорость гашения извести. Также применяют полуводный гипс с поташом.
Вернуться к оглавлению
Наполнители
В качестве наполнителей выступают песок, зола, другие вещества (трепел, драгомит и т п).
Пенобетон марки 500 делают, исключая наполнители. Применение наполнителей тонкого помола возможно. Пеноблок плотнее отметки 600 кг / м3 изготовляется с использованием песка.
Вернуться к оглавлению
Песок
Чем мельче песок, тем качественнее пенобетон.
Должен отвечать ГОСТу 8736: кварц в составе должен превышать семьдесят пять процентов, домеси — меньше трех процентов.
Песчинки должны быть как можно меньше. Их размер влияет на качество пенобетона — менее прочный, неравномерный пеноблок, сделанный из крупнозернистого песка. Используют песок из рек, оврагов — он промытый.
Вернуться к оглавлению
Зола
Может частично или полностью заменить песок в пенобетоне, около тридцати процентов цемента экономится. Во многих регионах используют золу-унос — отходы работы теплоэлектростанций. Повысит прочность пеноблоковна основе золы термовлажностная обработка.
Вернуться к оглавлению
Другие
Известняк тонкого помола добавляют пропорцией 20 до 30 процентов от массы цемента. Он играет роль наполнителя на микроскопическом уровне, позволяющего снизить внутреннюю напряженность во время затвердения. Такая примесь придает составу пенобетона дополнительную морозостойкость, понижает его себестоимость.
Микрокремнезем применяют для придания прочности пенобетону.Добывается в процессе плавки ферросилиция в электрической печке в виде конденсата из шаровидных микрочастиц пыли.
Полипропиленовая фибра защищает пенобетон от пластичных изменений на первом этапе затвердения смеси, предотвращая появление микроскопических трещин. Длина используемой фибры для пенобетона 0,6 — 2 см. Пеноблоки с фиброй отличаются прочностью, морозостойкостью, четкими крепкими гранями.
Вернуться к оглавлению
Пенообразователь
Для создания пористости материала добавляют пенообразователь, состав которого включает: костный и мездровый клей, канифоль, каустическая сода, паста скрубберная.
Пенообразователь делится на:
- искусственные;натуральные — белковые;клеекремневые.
Качество немецких и итальянских производителей натуральных образователей пены доказано. Стоимость таких добавок будет выше. В конечном результате пенобетон выровняет себестоимость при меньших затратах на портландцемент.
Вернуться к оглавлению
Вода
Вода должна соответствовать стандартам.
Применяют чистую воду без жира, масла, керосина температурой выше 10 градусов, не больше 60. Теплая вода позволяет в холодную пору года повысить скорость гидратации, снизить возможность трещин. Для разведения смеси пенобетона вода должна быть более мягкой, чистой, чтоб образовалось нужное количество пены.
Вернуться к оглавлению
Добавки
Часто используют составы пенобетонов с присадками: антифризовыми, ускорителями твердения, пластификаторами. Необходимость применения добавок определяется технологией, материалами, желаемым результатом.
Вернуться к оглавлению
Ускорители
Ускорители нужны для повышения сохнущих способностей на начальных этапах твердения, особенно при необходимости возведения прочного каркаса. Ускорители:
- электролиты — повышают способность разведения цемента;нитрат, нитрит кальция, поташ — повышают плотность;гидросульфоалюминат кальция повышает кристаллизацию;хлористый кальций позволяет быстро твердеть, имеет низкую стоимость, для нужного эффекта достаточно низкой дозы.
Ускорение должно отвечать требованием:
- не должно быть чересчур быстрым, чтоб качественно выложить раствор;низкая стоимость добавок;простота в использовании.
Добавление в раствор силикатного стекла должно быть 2,4 % от количества цемента. Имея такую дозировку, он делает смесь более плотной. При большей дозе, вызывает быстрое схватывание в момент замеса, снижает прочность пенобетона.
Вернуться к оглавлению
Пластификаторы
Введения таких добавок позволяет смеси стать более пластичной, гибкой. Они позволяют снизить температуру технического воздействия на конструкцию, помогают лучше переносить раствору морозы, при этом снижают способность сохранять тепло.
Требования, выдвигаемые к пластификаторам:
- совместимость со всеми ингредиентами;низкий уровень летучести;отсутствие какого-либо аромата;химически неактивные вещества;не должны растворять полимеры в составе.
Вернуться к оглавлению
Противоморозные добавки
Данные вещества позволяют проводить работы связанные с бетонными растворами в зимнее время. Предотвращают замораживание воды в бетоне, таким образом, он не разрушается морозами сохраняет прочность.
Вернуться к оглавлению
Пропорции для получения 1 м3 пенобетона
Марки D400
Отличается низкими прочностными особенностями, применяется в качестве утеплителя. Имеет пропорции:
- портландцемент — 300 кг;песок 120 кг;образователи пены — 850 г;вода 155 л.
Вернуться к оглавлению
Марки от D600 до D1000
Создают хорошую конструкцию, держат тепло, подходят для строительства домов. Имеет пропорции:
- портландцемент — 325 кг;песок — 205 кг;пенообразователь — 1,05 кг;вода — 182 л.
Вернуться к оглавлению
Марки D800
Пропорции:
- портландцемент — 390 кг;песок — 335 кг;пенообразователь — 1 кг;вода — 225 л.
Вернуться к оглавлению
Вывод
Пенобетон — качественный строительный материал, пользуется большим спросом. Имеет простой состав, обеспечивающий его положительные особенности, экологическую безопасность.
Состав пенобетона
Состав пенобетона интересует людей дела, которые хотят наладить производство и сделать на этом свой бизнес. Из чего делают пеноблоки состав и правила производства мы рассмотрим ниже. Будет предложена инструкция, по которой вы без проблем просчитаете затраты на производство и определите, на сколько будет выгодно производство.
Что входит в состав пенобетона
Химический состав пеноблока довольно прост, надо приобретать качественные материалы и тогда с качеством продукции не будет проблем. Тем более вся работа вполне может быть сделана и своими руками, тогда и себестоимость будет гораздо ниже.
Пенобетон и пеноблоки состав по плотности материала
Внимание: Для производства высококачественного пенобетона нужно с особой осторожностью выбирать необходимые компоненты, верно определять объем, вес, соблюдать требуемые правила влажности изделия, тепловой обработки.
Воспроизводство пенобетона осуществляется в соответствии с установленными нормами и правилами, выбор необходимых составляющих изделия соответствует государственному стандарту № 25485-89 (см. Пеноблок: технические характеристики и другие важные параметры). В соответствии с государственным стандартом № 8736, в состав пеноблоков входит песок, содержащий 75 % кварца.
- Портландемент устанавливается по государственному стандарту № 10178.Пеноблоки химический состав включают в себя канифоль по государственному стандарту № 191113. Если в составе присутствует клей, то его выбор должен быть осуществлен по государственному стандарту № 2067.

Пеноблок химический состав может быть довольно разным, все зависит от добавок. Он может готовиться из различных комбинаций ингредиентов.
Все это способствует производству различных видов материала.
От видовой принадлежности пенобетона зависит их целевое использование. Пенобетонные блоки применяются при кладке звукоизолирующих перегородок (см. Как делается перегородка из пеноблоков), стен зданий.
Не большая цена и прекрасные показатели морозоустойчивости сделали его популярным. Но у него есть и существенный недостаток, жилое помещение надо будет облицевать, а это затраты. Но слой утеплителя можно будет делать и не большой, ведь у блоков высокая теплоемкость.
Формовой пенобетон. В пеногенераторе происходит взбивание пенной основы.
В специальной емкости происходит смещение песка с цементом. При осуществлении данного процесса под влиянием компрессора повышается давление. Масса, по своей консистенции напоминающая сметану, под давлением заливается в подготовленные формы.
Выпуск пенобетонных блоков
Процесс производства блоков из пенобетона предусматривает ряд основных этапов. К ним относят: создание жидкого пенобетонного состава, разлив его по формам, высушивание, распалубка, распиловка, термическая обработка, упаковывание, отправка на склад и дальнейшая реализация.
Выпуск пеноблоков схематически
В зависимости от выбранного способа производства изделий из пенобетона и используемой техники, применяются разнообразные последовательности указанных этапов. Пеноблоки состав смеси будет определяться видом материала, который вы хотите производить. Рассмотрим каждый этап по прядку.
Создание жидкого пенобетонного состава
На сегодняшний день производственный процесс пенобетонного состава может осуществляться двумя способами: баротехнологичный и пеногенераторный. Каждый из методов имеет свои достоинства и недостатки.
Первый метод отличается достаточной простотой и экономичностью. Второй метод более затратный, нежели первый. Однако полученный таким способом материал обладает повышенным качеством.
Формирование пенобетонных блоков
Сегодня действуют два метода осуществления технологического процесса, результатом которых является получение готовых пенобетонных изделий: литьевой и резательный. Состав пенообразователя для пеноблоков вы будете определять в зависимости от используемого оборудования.
Литьевой метод
Литьевой метод выпуска пеноблочных изделий сильно схож с изготовлением железобетонной продукции.
Бетонный состав заливается в форму из металла (см. Формы для пеноблоков: какие лучше использовать), высушивание его производится до того момента, пока он не приобретет необходимую прочность. Далее он извлекается из форм и попадает к конечному потребителю.
Изготовление литьевым методом
При выпуске пенобетона данным способом, применяются формы кассетного типа, имеющие вид металлического поддона с разъемными ограждениями, разделяющими поддон на индивидуальные отсеки. Аналогичная форма для заготовки ледяных кубиков имеется в каждой современной холодильной камере.
Похожая форма применяется на заводах по изготовлению блоков, только большего объема со съемными перегородками. В большинстве случаев их высота составляет 60 сантиметров.
Основными недостатками литьевого способа являются:
Отсутствие четкости размеров готовых изделий. Ширина, высота, длина пенобетонных блоков способны колебаться из-за того, что перегородки кассеты неустойчивы и непроизвольно сдвигаются. Это объясняется тем, что бортики выполнены из тончайшего металла и могут смещаться, что сказывается на неточных размерах готовой продукции.
Но имеют свое существование и формы, отличающиеся особым качеством с толстыми, не деформирующимися стенками. Но у подобных форм есть один важный недостаток – высокая цена. Поэтому мелкие компании в целях экономии закупают дешевые аналоги с тонкими перегородками, что заметно сказывается на качестве готовой продукции;Присутствие неровностей на поверхности блока. Они появляются сверху залитой в форму пенобетонной смеси.
Явным примером может послужить тот же ледяной кубик, поверхность которого сверху не отличается гладкостью. Аналогичным образом на готовом блоке образуются неровности. Многие наверняка смогут вспомнить верхнюю поверхность плит перекрытий, все части которой гладкие, кроме одной – верхней.
Неровность пенобетонных блоков, произведенных по описанной технологии, всегда можно заметить на одном из фронтонов;Обязательное применение специальных кассетных бортов, расточенных под определенный размер блоков. Для производства нескольких видов пеноблоков, отличающихся по размеру, компания должна иметь в своем арсенале несколько типов бортов с различными размерами;Распалубка кассет немного повреждает уголки и верхнюю часть готовых пенобетонных изделий. Это объясняется тем, что пенобетон приклеивается к стенкам формы, ввиду недостаточной прочности на момент проведения данной процедуры.
Небольшая порча блоков происходит из-за недостаточного смазывания формы перед заливанием состава, ввиду экономии. Производитель старается сэкономить всеми доступными способами, нередко жертвуя качеством выпускаемых изделий. Для смазки кассет предприятия часто применяют отработанные масла.
К достоинствам рассмотренной технологии выпуска пеноблочных элементов относят относительную экономию денежных средств компании. Она проявляется в экономии на дорогом оборудовании, хотя для покупателя это не имеет никакого значения.
Резательный метод
Данный метод выпуска пеноблочных изделий предполагает два этапа: отлив пенобетонной массы в большую емкость и ее распалубка с дальнейшим разрезанием на блоки установленного размера. Данный процесс осуществляется с использованием дорогостоящего специализированного оборудования.
Изготовление резательным методом
Разные виды оборудования способны выдавать различные размеры готовых блоков. При этом применяются разнообразные типы режущих конструкций. К примеру, множество видом струн, пилящих механизмов.
Резательный способ выпуска пеноблочных элементов имеет ряд достоинств, к числу которых можно отнести следующее:
- Точность размеров, соответствующая государственному стандарту № 21520-89 гладкость поверхности изготавливаемых пенобетонных блоков.
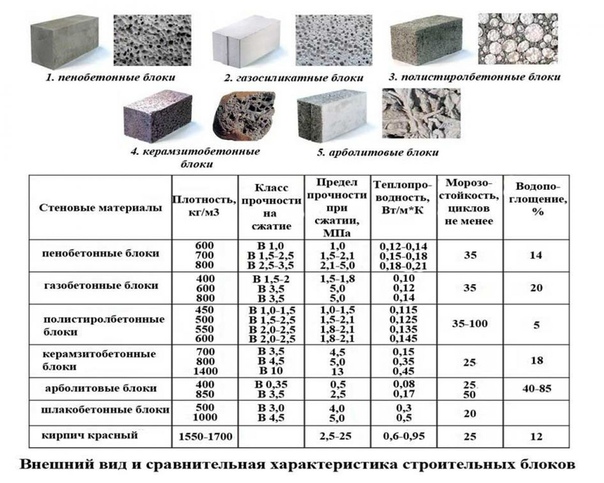
Эта тонкость крайне необходима для снижения затрат времени и финансов при последующем монтаже стен:
- В результате того, что при данном методе производства пеноблоков не используются смазочные материалы, готовая пенобетонная продукция отличается хорошим сцеплением с другими поверхностями, а также приятным видом. Он особой роли не играет, чего нельзя сказать об адгезии, являющейся важным критерием осуществления качественных работ по шпатлевке, штукатурке стен;Способность производить блоки необходимых размеров. Современные технологии позволяют нарезать пеноблоки в соответствии с индивидуальными запросами каждого потребителя;Посредством обрезания пенобетона с каждой стороны, пропадают ненавистные неровности и шероховатости на поверхности блоков.
Технологический процесс, осуществляемый рассматриваемым методом, имеет и слабые стороны.
Процесс нарезки пенобетона специализированными режущими инструментами должен происходить в соответствии с четкими правилами и требованиями.
При осуществлении резки струнным оборудованием, нужно с наибольшей точностью выбирать нужный момент, когда пенобетон уже подсох, но еще не приобрел излишнюю прочность.При осуществлении нарезки блоков в неподходящее время, режущая струна не будет следовать по указанной траектории, что негативным образом отразится на правильности блочных размеров.При выполнении нарезки блоков с помощью пил, пенобетон наоборот должен затвердеть как можно сильнее. Данное условие необходимо из-за того, что при осуществлении процесса резки блоки неоднократно переворачивают. При низкой степени прочности, бетон способен трескаться и крошиться.
Приведенные недостатки доставляют огромные неудобства производителям пеноблоков, чего не сказать о покупателях.
Высушивание изделий из пенобетона и уровень прочности
При осуществлении производственного процесса блоков литьевым методом применяются два вида высушивания блочных элементов:
Естественная сушка пеноблоков
- Первый способявляется самым простым и подразумевает естественное высыхание пенобетона, помещенного в емкость, в течение десяти часов с его дальнейшей нарезкой.
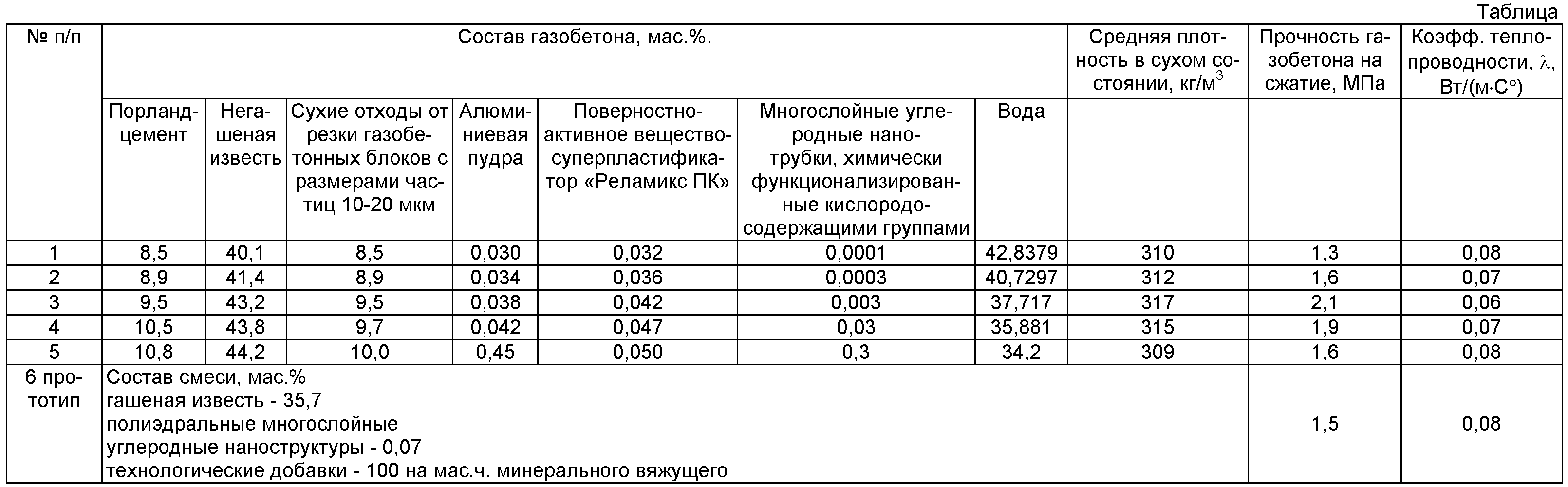
Внимание: Стоит отметить, что аналогичный вариант высушивания применяется при изготовлении конструкций из железобетона. Резательный способ изготовления блоков предполагает естественный процесс высыхания понобетонной смеси с последующей его распалубкой.
Конечный состав пеноблоков вы определите в зависимости от требуемых характеристик. На видео в этой статье и фото вы сможете узнать дополнительную и нужную информацию. Так что сделать пеноблоки самостоятельно вполне возможно и конечная цена будет не высокой.
- Дата: 09-03-2015Просмотров: 228Комментариев: Рейтинг: 35
В сравнении с бетоном классическим, пенобетон имеет более низкий вес. Его легкость обусловливается пористой структурой, причем большинство воздушных пор в ней закрыто.
Это выгодно отличает изделие от газобетона, имеющего большое количество пор сквозных. Правильно подобранный состав и тщательное соблюдение технологии производства позволяют получить дышащий строительный материал, имеющий в то же время высокие гидроизоляционные характеристики. Благодаря насыщенности пузырьками воздуха он ощутимо снижает нагрузку на фундамент и уменьшает вес строения в целом.
Пенобетон уже много лет благодаря своим качествам и достаточно низкой стоимости является самым популярным материалом для строительства зданий.
Основные компоненты и стандарты, определяющие их свойства
Свойства материала определяет ГОСТ 25485-89, в соответствии с которым производится классификация.
В нем указаны основные требования к составу пенобетона и технические характеристики различных его марок. Кроме того, каждый из ингредиентов также должен соответствовать определенному стандарту. Вот список основных компонентов, из которых создается материал:
- цемент;песок;вода;пенообразователь;разнообразные необязательные добавки.

Рецепт семеси для пенобетона.
Вяжущим ингредиентом, участвующим в создании пенобетона, является портландцемент марок М500 Д20, М400 Д0, М400 Д20 (ГОСТ 10178). В качестве заполнителя используют песок, который должен содержать не менее 75% кварца (ГОСТ 8736). В песке допускается присутствие не более 3% примесей, содержащих ил и глину.
Свойства воды определяет ГОСТ 23732. Пенообразователи могут быть как синтетическими, так и белковыми. Натуральные пенообразователи являются экологически чистыми, а изделия, в состав которых они входят — особо прочными.
Характеристики отдельных компонентов пенообразователя определяются следующими стандартами:
- сосновая канифоль — ГОСТ 191113;костный клей — ГОСТ 2067;мездровый клей — ГОСТ 3252;едкий натр (технический) — ГОСТ 2263;скрубберная паста — ТУ 38-107101.
Что касается необязательных добавок, то они у каждого производителя свои. К примеру, на некоторых заводах в пенобетон добавляют фиброволокно.
Благодаря этому почти на четверть повышается прочность материала. Грани его блоков имеют четкий контур и практически не подвержены разрушению. В состав материала может входить и мелкодисперсная зола, образующаяся после сгорания твердого топлива.
Самые крупные ее частицы не превышают 0,14 мм. Такая добавка позволяет увеличить прочность перегородок между отдельными порами материала и сэкономить до 30% цемента. К прочим добавкам относятся ускорители твердения, пластификаторы, биологически разлагаемые смазочные материалы для форм, красители.
Вернуться к оглавлению
Пенобетон имеет пористую структуру, за счет которой он имеет легкий вес.
К основным видам пенобетона относятся: теплоизоляционный, конструкционно-теплоизоляционный, конструкционный. Каждому из видов соответствует несколько марок, характеризуемых средней плотностью.
Данный показатель зависит от количественного соотношения отдельных ингредиентов, входящих в состав конечного продукта. Смеси невысокой плотности, как правило, песка не содержат. В частности, для приготовления 1 м3 материала плотностью М400 используется 300 кг цемента, 160 л воды и 0,85 кг пенообразователя.
Прочность пенобетона увеличивается по мере роста его плотности. Чем тяжелее материал, тем большую нагрузку он способен выдержать. Для создания изделий М600 необходимо взять 330 кг цемента, 210 кг песка, 180 л воды и 1,1 кг пенообразователя.
В состав материала М800 входит 400 кг цемента, 340 кг песка, 230 л воды и 1,1 кг пенообразователя. Добавление в смесь золы позволяет уменьшить коэффициент теплопроводности изделия. Чем выше марка продукции, тем ощутимее эффект от этой добавки.
Из вышеизложенного следует, что при одном и том же количестве пенообразователя увеличение количества цемента и песка приводит к возрастанию плотности материала. При этом увеличивается и его прочность.
В отличие от классического бетона, при производстве пенобетона не используются такие заполнители, как щебень и гравий. Однако на некоторых заводах в его состав вводят легкие заполнители: полистирол или частицы керамзита. Они при той же плотности позволяют увеличить как прочность, так и теплоизоляционные характеристики материала.
Вернуться к оглавлению
Разумеется, чем выше марка портландцемента, тем более прочным получится и производимый из него пенобетон.
Но не последнюю роль в смеси играет и тонкость помола вяжущего ингредиента. Если был использован цемент более крупного помола, чем указано в ГОСТ 10178, его количество потребуется увеличить на 10%. Отклонение от стандарта приведет к тому, что состав будет затвердевать значительно дольше, а это, в свою очередь, потребует введения дополнительных добавок, ускоряющих твердение.
Составляющие, которые используют для производства пенобетона влияют на его прочность.
С увеличением плотности пенобетонадля его изготовления используют песок более высокой зернистости.
К примеру, зернистость песка для марок плотностью 400-1200 кг/м3 составляет от 0 до 2 мм, а при плотности 1400-1600 кг/м3 требуется песок зернистостью от 0 до 4 мм. В то же время использование мелкозернистого песка с размером частиц менее 1 мм позволяет увеличить прочность состава при той же плотности. Однако подобная практика применяется довольно редко, так как материал, отвердевая, дает повышенную усадку.
Использование в производстве пенобетона обычной водопроводной воды может привести к снижению качества, если она не соответствует установленному стандарту по кислотности или содержанию минеральных солей. Особой чистоты требует вода, в которой разводится сухой пенообразователь. Температура жидкости должна находиться в диапазоне от 10 до 60°С, хотя многие специалисты считают, что воду теплее 25°С лучше не использовать.
Чтобы снизить содержание жидкости в материале и тем самым повысить его прочность, в состав обычно вводят разнообразные пластификаторы. Тем не менее соотношение воды и цемента не должно быть ниже 0,4. В противном случае цемент станет забирать воду из раствора пенообразователя.
Данный компонент обходится несколько дороже синтетических аналогов, но и расходуется более экономно, да и пену образует более стабильную. Иногда недобросовестные производители при выпуске синтетического состава используют пенообразователь, который был изготовлен для пожаротушения. Его применение приводит к значительному снижению характеристик получаемого материала.
Причин, по которым рекомендуется использовать для пенобетона белковый, а не синтетический пенообразователь, существует достаточно много. Основной из них является безопасность для человека ввиду полного отсутствия ядовитых испарений.
Вернуться к оглавлению
Для получения пенобетона особой прочности на многих предприятиях в смесь вводят тонкомолотый известняк. Он не приводит к возникновению трещин, как другие добавки, не утяжеляет изделие, как песок, позволяет сэкономить цемент.
Карбонизация раствора повышает устойчивость изделия к механическим нагрузкам. Масса известковой муки может составлять до 20-30% от массы цемента. Такой состав после твердения обеспечивает более высокую морозостойкость, чем смесь компонентов без добавок.
Противоморозные добавки вводятся для того, чтобы предотвратить промерзание раствора при низких температурах. Они делают его более пластичным, увеличивают скорость связывания цемента, обеспечивают ускоренное выделение тепла, образуемого при гидратации, снижают на 7-10% массу воды, необходимой для состава. Чтобы улучшить водонепроницаемость, увеличить устойчивость к повышенной температуре и кислотности, в раствор добавляют микрокремнезем.
Гидрофобизаторы и воздухововлекающая смола предназначены для снижения расслаивания пенобетона при транспортировке, улучшения таких характеристик, как водонепроницаемость, морозостойкость и удобоукладываемость.
Добавление 0,5 кг полипропиленовой фибры на 1 м3 смеси значительно снижает количество бракованной продукции при производстве, а также потерь при транспортировке. Фибра повышает устойчивость к ударам и механическим нагрузкам, предупреждает растрескивание. С введением в состав до 1 кг фибры повышается марка конечной продукции.
Источники:
- kladembeton.ru
- kladka-info.ru
- ostroymaterialah.ru
Состав пенобетона, характеристики, виды, используемые в строительстве марки
В последнее время появилось большое разнообразие строительных материалов, о которых раньше люди даже не представляли. Одним из таких материалов является пенобетон. Его используют как при возведении несущих стен, так и при строительстве межкомнатных перегородок. Также этот материал используется для теплоизоляции стен, полов и крыш.
Из чего состоит пенобетон
Пенобетон представляет собой ячеистые блоки. Благодаря пенообразователям они имеют пористую структуру. Это позволяет блокам несмотря на небольшой вес иметь высокую прочность и хорошие показатели по теплоизоляции.
В состав монолитного пенобетона или блоков, главным образом входит портландцемент марок М500 и М400. Конечно, при использовании портландцемента более высоких марок пенобетон будет прочнее. Также немаловажную роль имеет тонкость помола цемента. Например, используя материал крупного помола, его количество следует увеличить на 10%, а если этого не сделать, процесс затвердевания займет больше времени. Во избежание этого в состав смеси нужно будет добавлять ускоряющие твердение материалы.
youtube.com/embed/2Xglgt7JbQ8?rel=0″ allowfullscreen=»allowfullscreen»/>
Также в состав пеноблока входит песок. В зависимости от плотности материала используется разный песок. Содержание глинистых минералов и других примесей в песке не может превышать 3%.
Часто используемые марки в строительстве
Для часто используемых марок плотностью от 400 кг/м3 до 1200 кг/м3 зернистость песка не должна превышать 2 мм, а для марок более высокой плотности зернистость может быть большей — до 4 мм. Если использовать мелкозернистый песок (до 1 мм), это позволит повысить прочность пеноблоков, однако в процессе застывания материал может дать усадку, поэтому такую практику применяют не часто.
В процессе изготовления пенобетона также важную роль играет качество используемой воды. Если вода из водопровода не соответствует необходимым стандартам по содержанию минеральных солей и кислотности, ее не следует использовать в состав пенобетона, так как она может привести к ухудшению качества материала. Также особенно качественной должна быть вода, в которой разводиться пенообразователь. Оптимальная температура жидкости для добавления составляет 10-25ºС.
Для чего нужен пенообразователь
Также при изготовлении пенобетона состав обязательным образом содержит пенообразователи. Они бывают двух видов: натуральные и синтетические. Первые изготавливаются из экологически чистых материалов, поэтому полученные пеноблоки не имеют ограничений в использовании. Если говорить о синтетических пенообразователях, их используют главным образом чтобы уменьшить стоимость получаемой продукции.
При изготовлении блоков также могут добавлять золу. Это позволяет уменьшить расход цемента, не потеряв в прочности материала. Однако это приводит к уменьшению теплозащитных свойств.
Неотъемлемая часть – строительное волокно
Еще одним компонентом, который добавляют при изготовлении пенобетона, является строительное волокно. Такой микроармирующий материал позволяет повысить прочность на 25%.
Если брать технические характеристики пеноблок обладающий повышенной прочностью используется только в случае очень высокой нагрузки на стены. В остальном достаточным будет использовать блоки, имеющие стандартный состав.
Классификация пенобетона
Если брать пенобетон характеристики полученного материала определяются в первую очередь плотностью. Именно этот параметр и служит главным в классификации пеноблоков.
Далее приведена таблица названий разновидностей пенобетона в зависимости от марок.
Марка | Название |
d150-d400 | Теплоизоляционные |
d500-d900 | Конструкционно-теплоизоляционные |
d1000-d1200 | Конструкционные |
d1300-d1600 | Конструкционно-поризованные |
Теплоизоляционные марки пенобетона имеют плотность соответственно названию от 150 до 400 кг/м3. Прочность пенобетона d400 составляет 9 кг/см2. Морозостойкость таких блоков не нормируется. Прочность на сжатие составляет В0,75. Марки ниже d400 не нормируются на прочность. Такие блоки имеют низкую теплопроводность.
Конструкционно-теплоизоляционные марки пенобетона являются часто используемыми в строительстве. Прочность на сжатие материала возрастает пропорционально маркам. Если пеноблок d600 имеет прочность 16,0 кг/см2, то d900 — 35,0 кг/см2.
d600 – характеристики
Пеноблок d600 технические характеристики которого являются одними из наиболее подходящих для частного строительства имеет класс по прочности на сжатие В1-В2, морозостойкость — от F15 до F35, теплопроводность 0,14 Вт/(м*°С), а коэффициент паропроницаемости 0,17.
Пеноблок д600 используется как для строительства несущих стен, так и для возведения перегородок. Для несущих стен в малоэтажных зданиях применяются стандартные блоки 60*30*20 см. Если же говорить о перегородках, то здесь могут быть использованы блоки меньшего размера — 60*30*10 см.
Когда нужно дополнительное утепление
Конструкционные пеноблоки уже не используются в теплоизоляционных целях. Они имеют большую теплопроводность и меньшую паропроницаемость. Поэтому, здания, сооруженные из пеноблока марок d1000-d1200, при высокой теплопередаче требуют дополнительного утепления. Если говорить о прочности такого материала, он очень высок. Именно такие марки пенобетона используются в многоэтажном строительстве.
Конструкционно — поризованные блоки не производятся серийно, поэтому не имеют регламентированных ГОСТом характеристик. Высокая плотность такого материала позволяет с его помощью возводить здания, не ограниченные по этажности.
Изготовление блоков
Если брать во внимание пропорции для изготовления пенобетона, то каждый производитель имеет свои собственные «рецепты». Но есть приблизительные стандарты для наиболее используемых пеноблоков. Его изготовка может содержать или нет песок, также иметь разное количество пенообразователя и других компонентов.
Для изготовки материала марки d400 необходимо 300 кг портландцемента, 160 литров воды и 850 г вспенивателя. Песок для данной марки не используется.
Для получения марки d600 используется 330 кг портландцемента, 210 кг песка, 180 литров воды и 1100 г вспенивателя. Для получения необходимой порции материала, можно увеличивать или уменьшать количество ингредиентов в пропорции.
Марка d800 пенобетона получается при следующем количестве исходных материалов: 400 кг цемента, 400 кг песка, 230 литров воды и 1100 г вспенивателя.
Советы по выбору и использованию пеноблоков
- Выбирая пеноблоки следует обратить внимание на цвет материала, он должен быть серым (тон может светлее или темнее) и обязательно однородным. Блоки белого цвета являются не качественными.
- Также следует проверить герметичность ячеек пеноблока. Структура блока должна быть одинаковой как внутри, так и снаружи. Ячейки должны быть круглыми, не соединенными друг с другом. Также блоки не должны иметь трещины или сколы.
- Проверить также следует и геометрию блока, ведь если какая-то из сторон будет отличаться, это может затруднить процесс кладки материала.
- Если вы приобрели свежий материал, не следует его использовать до обретения им необходимой прочности, а это происходит на 28 день после изготовления пенобетона.
- Класть пеноблоки лучше не на обычный раствор, а на клей на цементной основе. Благодаря этому гораздо более тонкие швы между блоками не станут мостиками холода.
Подведем итог
Как видно, при одинаковом количестве пенообразователя, увеличение массы портландцемента и песка приводит к повышению плотности пенобетона. Чем больше плотность пенобетона ожидается в конечном итоге, тем выше должен быть показатель зернистости используемого песка.
Хотя далеко не все, кто пользуются блоками из пенобетона в строительстве зданий, изготавливают их самостоятельно. Все же понимание пропорции поможет при покупке материала ориентироваться в его прочности и других характеристиках.
Состав и пропорции для пенобетона
Пенобетон, как и газобетон, относится к ячеистым бетонам. Кроме того, их сходство заключается в том, что оба эти стройматериала имеют пористую структуру, которая служит хорошим теплоизолятором, но, тем не менее, технология их изготовления существенно отличается друг от друга и, соответственно, каждый из них, за счет этого, приобретает свои персональные свойства.
Пенобетон, в отличии от газобетона, можно сделать своими руками.
Оборудование для производства
В процессе производства газобетона, его твердение должно происходить в автоклавных условиях (в среде, насыщенной паром, и при давлении, которое должно быть выше атмосферного), что требует наличия специального дорогостоящего оборудования. Словом, его целесообразней производить в заводских условиях.
Пенобетон же, создается неавтоклавным (затвердевание происходит в естественных условиях) способом, и по этой причине его возможно изготовить своими руками, что существенно экономит расходы.
Формы для блоков можно приобрести в строительном магазине, а можно сделать и самостоятельно.
Его производство настолько несложное, что, если зная пропорции для пенобетона, данный материал можно сделать даже в домашних условиях. Для этого понадобится приобрести или самостоятельно смастерить такое оборудование, как:
- формы для отливки блоков;
- растворомешалку;
- компрессор, который должен быть рассчитан на переменное напряжение 220 Вт, иметь мощность 0,3 – 0,5 м3 и давление 6 Атм;
- пеногенератор.
Пропорции компонентов
Изготовление пенобетонных блоков включает в себя соблюдение точных пропорций, а также четкой последовательности добавления компонентов в процессе всего производства. Несоблюдение этих правил может отрицательно сказаться на качестве пеноблока. Кроме того, чтобы получить стабильный результат от каждой выпускаемой партии понадобиться приобрести навык, поскольку от температуры и влажности окружающей среды, видов применяемых пенообразователей, способов получения пены, метода добавления пены в смесь, формовки и сушки уже готовых изделий будет зависеть конечный результат. Прежде чем приступать к производству пенобетона, необходимо подготовить такие компоненты, из которых он состоит:
- цемент;
- песок;
- вода;
- пенообразователь.
Далее, когда материал и оборудование подготовлено, необходимо изучить пропорции компонентов для производства пенобетона, которые определяются в зависимости от требуемой марки ячеистого материала. Так, изменяя соотношение компонентов и его состав, можно производить различные виды пенобетона, которые, в зависимости от этого, используются либо для строительства внешних стен, либо при изготовлении внутренних перегородок, термоизоляции крыш, либо для термо- и звукоизоляции междуэтажных покрытий.
Например, для производства пеноблока марки D400 в количестве 1 куб. м, который имеет низкий класс прочности и из-за этого используется только в качестве теплоизоляционного материала, соотношение компонентов будут иметь такие показатели:
- Цемент – 300 кг.
- Песок – 120 кг.
- Пенообразователь – 0,85 кг.
- Вода – 160 л.
К более прочному и универсальному стройматериалу относятся пеноблоки маркой от D600 до D1000, которые считаются конструкционно-теплоизоляционными видами. Они отлично подходят для строительства небольших домов и коттеджей, а также для возведения зданий в регионах с невысокой сейсмической опасностью. Так, для производства 1 м куб. пенобетона марки D600 понадобится:
- Цемент – 330 кг.
- Песок – 210 кг.
- Пенообразователь – 1,1 кг.
- Вода – 180 л.
В состав 1 м куб. пеноблока марки D800 входят компоненты с такой пропорцией:
- Цемент – 400 кг.
- Песок – 340 кг.
- Пенообразователь – 1,1 кг.
- Вода – 230 л.
Из вышенаписанного можно сделать вывод: чем больше добавляется цемента и песка в нужной пропорции, тем пенобетон приобретает выше марку и, соответственно, его прочность и другие качества улучшаются. Но, опять же, при его производстве учитываются и другие факторы, которые включены в технологию изготовления данного стройматериала и влияют на конечный результат продукции.
ПЕНОБЕТОН И ПЕНОБЛОКИ — оборудование производства пенобетона и пеноблоков
Производство пенобетона
Пенобетон — стеновой и теплоизоляционный материал для строительства зданий.
Производство пенобетона организуют в соответствии с требованиями ГОСТ 25485-89 «Бетоны ячеистые».
Оборудование для производства пенобетона
Комплект оборудования для производства пенобетона с ручной загрузкой сырья. Состав:
|
|
Комплект оборудования производства пенобетона с автоматической загрузкой сырья. Состав:
|
Производство пеноблоков
Пеноблоки предназначены для кладки наружных, внутренних стен и перегородок зданий.
Производство пеноблоков организуют в соответствии с требованиями ГОСТ 21520-89 «Блоки из ячеистых бетонов стеновые мелкие».
Оборудование для производства пеноблоков
Оборудование для производства пеноблоков по резательной технологии обеспечивает высокую точность геометрических размеров, качество поверхностей и ребер пенобетонных блоков, а также уменьшение себестоимости продукции за счет механизации производства.
Линия для производства пенобетона и пеноблоков
Осуществляем изготовление, поставку, шеф-монтаж линии производства пеноблоков :
- производительностью до 30 м.куб/ в смену,
- производительностью до 50 м.куб/ в смену.
- производительностью до 70 м.куб/ в смену,
- производительностью до 100 м.куб/ в смену,
Состав линииВ состав линии входит:
|
Преимущества покупки линии у RusBlok:
|
Если вы решили открыть производство пеноблоков или модернизировать уже имеющееся, у нас вы сможете купить все необходимое. Связавшись с нами, вы сможете задать любой интересующий вас вопрос по организации производства пеноблоков, уточнить цену оборудования и оформить заказ.
Состав и материалы для производства пенобетона
В зависимости от технологии производства применяются разные цементы, заполнители, пенообразователи и добавки. Далее мы подробно рассмотрим каждый компонент и приведем список всех пенообразователей и добавок.
Перечень добавок и пенообразователей:
- Пенообразователь ПБ-2000
- Протеиновый пенообразователь Laston
- Белковый пенообразователь GreenFroth
- Ускоритель твердения пенобетона бетона и пенобетона Асилин-12
- Смазка форм Компил
- Немецкое фиброволокно (фибра — полипропиленовое волокно)
- Микрокремнезем
- Суперпластификатор С-3
Для производства пенобетона используется цемент, заполнитель, вода, пенообразователь и добавки (если требуются). В зависимости от технологии производства применяются разные цементы, заполнители, пенообразователи и добавки. Далее мы подробно рассмотрим каждый компонент и приведем список всех пенообразователей и добавок.
1. Цемент
Для производства пенобетона используется обычный портландцемент. При использовании баротехнологии (ее иногда называют кавитационной или без пеногенераторной) обязательно использовать цемент марки М500Д0. Это цемент дорогой и дефицитный. Причем даже при его использовании получение пенобетона удовлетворяющего ГОСТ по баротехнологии сопряжено с большими затратами и технологическими трудностями. Если пенобетон производится по классической технологии, то возможно использовать цемент М500Д20, М400Д0, М400Д20.
2. Заполнитель
В качестве заполнителя в большинстве случаев используется песок. Он должен удовлетворять ГОСТ 8736-93 ПЕСОК ДЛЯ СТРОИТЕЛЬНЫХ РАБОТ. Также в качестве заполнителя могут использоваться различные отходы производств — зола уноса ТЭЦ, известняковая мука, доломитовая мука и т.п. Зачастую использование подобных отходов позволяет значительно снизить себестоимость и при этом увеличить качество продукции. При покупке оборудования завода Строй-Бетон, покупатели получают полную информацию о возможных заполнителям и помощь в их подборе.
3. Вода
Для производства пенобетона используется обычная питьевая или техническая вода. Вода должна удовлетворять требованиям ГОСТ 23732-79 ВОДА ДЛЯ БЕТОНОВ И РАСТВОРОВ. Температура воды подбирается исходя из технологии.
4. Пенообразователи
Пенообразователи бывают 2 видов — синтетические и белковые. Синтетические используются в баротехнологии (установки Санни), белковые в классической технологии (установки Фомм-Проф). Белковые пенообразователи считаются более совершенными и позволяют получать пенобетон удовлетворяющий ГОСТ 25485-89 БЕТОНЫ ЯЧЕИСТЫЕ без особых затрат. Подробнее можно прочитать в статье Причины использования белкового (протеинового) пенообразователя.
5. Добавки
В зависимости от технологии и используемых материалов периодически требуется использование специальных добавок. Добавки применяются для того, чтобы получить продукцию удовлетворяющую ГОСТ. Подбор добавок сложен и требует экспериментов. Для клиентов завода Строй-Бетон добавки подбираются бесплатно.
Рецепт пенобетона при использовании белкового пенообразователя
Плотность пенобетона в сухом состоянии. |
400 |
600 |
800 |
1000 |
1200 |
1400 |
1600 |
Песок (до 2мм, содержание глина не более 2%). |
— |
210 |
400 |
560 |
750 |
950 |
1100 |
Цемент марки М500Д0. |
300 |
310 |
320 |
350 |
360 |
380 |
400 |
Вода для приготовления раствора. |
110 |
130 |
150 |
180 |
210 |
240 |
300 |
Вода для приготовления пены литров. |
64 |
57 |
50 |
45 |
37 |
30 |
23 |
Количество пены (литров). |
800 |
715 |
630 |
560 |
460 |
370 |
290 |
Количество пенообразователя кг (не литров!). |
1,2 |
1,1 |
1 |
0,95 |
0,9 |
0,7 |
0,6 |
Вес сырой пенобетонной массы кг. |
474 |
707 |
920 |
1135 |
1357 |
1600 |
1823 |
Рецепт пенобетона при использовании синтетического пенообразователя
Плотность кг/куб.м. |
Песок |
Цемент |
Пенообразователь Ареком-4 |
|
1200 |
900 |
250 |
0,80 |
|
1100 |
740 |
360 |
0,88 |
|
1000 |
667 |
333 |
0,96 |
|
900 |
375 |
450 |
1,03 |
|
800 |
330 |
400 |
1,12 |
|
700 |
290 |
350 |
1,14 |
|
650 |
270 |
325 |
1,15 |
|
600 |
250 |
300 |
1,16 |
|
550 |
458 |
1,17 |
||
500 |
417 |
1,18 |
Влияние пеноблоков на здоровье человека
Влияние пеноблоков на здоровье человека
Легкий, долговечный, удобный в эксплуатации материал по экологическим свойствам сравним лишь с деревом, но все равно таит в себе опасности для здоровья человека.
Состав пеноблока
Для производства пеноблоков используется пена, состоящая из животного и растительного сырья, что означает ее полную безопасность для здоровья. При этом в состав бетона входят наполнители – гранит и пенобетономатериалы, которые относятся к магматическим породам и содержат радионуклиды в большом количестве. Именно ингредиенты для бетона могут представлять опасность для человека.
Осадочные породы (кварцевый песок, известняк, мел) содержат небольшую концентрацию естественных радионуклидов (ЕРН). Довольно большое количество ЕРН содержат глинистые материалы и непосредственно глина, но при этом они обладают хорошими адсорбционными свойствами. В состав качественных пеноблоков входит не гранитный камень, а кварцевый песок или известь, соответственно, концентрация естественных радионуклидов очень мала и не может нанести вред.
Качество песка, используемого для изготовления пеноблоков, должно соответствовать государственным стандартам. Ответственность за применение загрязненных ЕРН материалов полностью лежит на производителе. Для того, чтобы пеноблоки не нанесли здоровью вред, строительные материалы необходимо закупать у крупных производителей, которые свободно предоставляют потребителю сертификаты качества и сопроводительную документацию.
Чем опасны естественные радионуклиды?
Радионуклиды способны накапливаться в человеческом организме и облучать его изнутри. Излучение оказывает серьезное негативное влияние на репродуктивную и иммунную системы человека. Заболевания на раннем этапе не проявляются – мигрень и усталость это единственное, что может наблюдаться в начале облучения. В последствие радионуклиды провоцируют развитие таких патологий:
• тахикардия и аритмия, являющиеся симптомами инфаркта;
• вегетососудистая дистония, повышающая вероятность инфаркта миокарда или инсульта;
• проблемы с ЖКТ;
• цирроз печени.
Приобретая пеноблок, необходимо проверять качественную документацию. Если производитель отказывает покупателю в предоставлении сертификата на дешевую продукцию, стоит задуматься о причинах этого. Экономия на стройматериале способна сыграть злую шутку со здоровьем проживающих в новом доме людей.
Возврат к списку
Внимание! При копировании информационных материалов прямая ссылка на наш сайт обязательна!
Все тексты сайта охраняются законом — Об авторском праве от 09.07.1993 г. N 5351-1.
Пеностекло
— обзор
5.7 Пеностекло
Еще одна технология переработки стекла — пеностекло. Существует множество патентов на производство пеностекла еще с 1930-х годов. Несмотря на наличие множества патентов, лишь некоторые из них были приняты на коммерческой основе. Пеностекло, также называемое пеностеклом, изначально производилось из специально разработанной стеклянной композиции с использованием только чистого стекла. В настоящее время существует ряд заводов по производству пеностекла, которые используют до 98% бытовых отходов стекла в своей продукции.Основной принцип производства пеностекла — это образование газа в стекле при температуре от 700 ° C до 900 ° C. Газ расширяется, образуя структуру ячеек, образуя пористое тело. Пеностекло может быть изготовлено либо из расплавленного стекла, либо из частиц спеченного стекла. Последний процесс требует смешивания матового стекла с пенообразователем, затем при нагревании пенообразователь выделяет газ и расширяет расплавленную массу стекла.
Основные производители пеностекла в Европе, Японии и Северной Америке в настоящее время используют высокий процент переработанного стекла после потребления в своей продукции.В настоящее время существует три основных типа пеностекла:
- •
Пеностекло для рассыпного пеностекла: непрерывное производство листов пеностекла, которые затем разбиваются на неплотный заполнитель пеностекла и калибруются.
- •
Блоки и формы: Обычно непрерывное производство блоков и форм в формах, которые затем разрезаются и формуются. Также может изготавливаться серийным способом.
- •
Гранулирование: непрерывное производство сферических гранул пеностекла, которые затем используются в производстве блоков, панелей и плит.
Пеностекло лучше всего подходит в качестве жесткого изоляционного материала. Благодаря своим превосходным структурным свойствам, он подходит для использования в качестве изоляции на крышах, стенах и в зонах движения, таких как плоские крыши или полы, где другие изоляционные материалы могут быть сжаты, что приведет к неровной поверхности и потере изоляционных свойств. Пеностекло обладает превосходными огнестойкими свойствами, а его очень низкое водопоглощение и пропускание водяного пара означает, что, в отличие от многих других типов изоляции, оно имеет тенденцию сохранять свои изоляционные свойства даже во влажном состоянии.Он также используется в качестве промышленной изоляции для ряда второстепенных целей, таких как сэндвич-панели, или используется как продукт в экстремальных условиях окружающей среды.
Пеностекло в течение ряда лет производилось в основном в США и Европе как легкий высокопрочный изоляционный материал. Основным стимулом для использования пеностекла было требование высоких стандартов энергоэффективности для строительства зданий, которые касаются энергосбережения. Основным строительным элементом всех этих правил является значение общего коэффициента теплопередачи.Это скорость потери тепла, выраженная в ваттах на квадратный метр на градус разницы температур (Вт / м 2 K). Использование пеностекла при строительстве жилья и зданий может значительно снизить потребление энергии.
Помимо потенциальной экономии энергии за счет использования пеностекла, существуют и другие, менее очевидные преимущества, связанные с легкостью материала. К ним относятся гибкость конструкции, производительность строительства, меньшее количество ручных операций, более низкие транспортные расходы и более низкие затраты на фундамент.Также он устойчив к грызунам, огнестойкий, эффективный звукопоглотитель, нетоксичен и не впитывает воду.
Пеностекло как строительный строительный материал составляет конкуренцию изоляционным полимерным и волокнистым материалам, поскольку является хорошим изолятором. Однако пеностеклу также присущи прочностные свойства. Характеристики пеностекла низкой горючести, термической стабильности и высокой химической стойкости являются явным преимуществом перед полимерными материалами, которые имеют плохую огнестойкость. Пеностекло также имеет то преимущество, что не содержит волокнистого материала.Волокнистые изоляционные материалы, такие как стекловолокно, требуют особых процедур обращения с ними для защиты пользователя от вдыхания волокон и раздражения кожи.
Желательными свойствами пеностекла являются высокая прочность, низкая плотность и низкая теплопроводность. Обычно эти свойства достигаются за счет наличия большого количества маленьких пузырьков одинакового размера с тонкими стенками между ними. Поскольку продукт сделан из стекла, он естественно инертен в большинстве сред по отношению к биологическому, термическому, химическому разложению и деградации окружающей среды.
Механизм пеностекла
Принцип процесса пеностекла заключается в том, что при температуре от 700 ° C до 900 ° C стеклянный порошок превращается в вязкую жидкость, а затем пенообразователь разлагается с образованием газа, который, в свою очередь, образует пузырьки. Стекло должно иметь достаточную вязкость, чтобы пузырьки газа не поднимались сквозь массу тела, но оставались на месте во время цикла нагрева вспенивания. Если температура слишком высока, пузырьки поднимутся, и тело схлопнется, а не образует пену.Контроль скорости нагрева — один из наиболее важных факторов при оптимизации изделия из пеностекла. Быстрый нагрев может вызвать растрескивание исходного материала для пеностекла, тогда как медленный нагрев приведет к раннему выделению газа из пенообразователя до того, как вязкость стекла станет достаточно низкой, чтобы стекло могло расшириться.
Еще одна сложность заключается в том, что сырье для пеностекла является относительно изоляционным из-за плотности упаковки 80%, и когда сырье расширяется от верхней поверхности, это дополнительно изолирует материалы, находящиеся ниже.Следовательно, существует вероятность перегрева верхней поверхности, чтобы нагреть нижнюю часть исходного материала. Этот перегрев может привести к разрушению верхних ячеек, что приведет к получению некачественного продукта.
Тонко измельченный стеклянный порошок смешивают с пенообразователем, который является сырьем для вспенивающей печи. Подходящими вспенивающими агентами могут быть сульфат кальция (CaSO 4 ), уголь, стеклянная вода, алюминиевый шлак или карбонат кальция (CaCO 3 ). При использовании CaSO 4 теплопроводность будет ниже, однако с CaCO 3 легче работать.Это связано с образованием сернистых газов из CaSO 4 в процессе вспенивания. SO 2 имеет более низкую теплопроводность, чем CO 2 ; однако образование SO 2 требует большего контроля, поскольку это ядовитый газ. Карбид кремния (SiC) также используется в качестве пенообразователя, что обеспечивает контролируемый и точный размер ячеек. Считается, что SiC является наиболее широко используемым пенообразователем из соображений контроля и воспроизводимости. SiC реагирует с SO 3 внутри структуры стекла с образованием CO 2 и S.
Гипс является легкодоступным источником CaSO 4 , а известняк — легкодоступным источником CaCO 3 . Если воздух в печи в зоне вспенивания заменить на SO 2 или CO 2 , это снизит теплопроводность пеностекла. Летучая зола, которая сама по себе является отходом угольных электростанций, использовалась в качестве пенообразователя. Основными составляющими летучей золы являются SiO 2 , Al 2 O 3 , Fe 2 O 3 , CaO и SO 3 .SO 3 — это активный пенообразователь, выделяющийся при температуре SO 2 с образованием пеностекла. Однако летучая зола является отходами мусоросжигательных заводов и, следовательно, может содержать токсичные соединения и тяжелые металлы.
Размер частиц пенообразователя влияет на размер ячеек, что влияет на рабочие характеристики и характеристики пеностекла. Это, в свою очередь, определяет плотность продукта. Чем больше размер ячейки, тем ниже плотность продукта и ниже теплопроводность, что обеспечивает лучшие теплоизоляционные свойства.Чем меньше размер ячеек, тем выше прочность на сжатие корпуса из пеностекла. Следовательно, прочность на сжатие обратно пропорциональна теплоизоляции.
Производство пеностекла
Стеклобой подается в шаровую мельницу для измельчения. Очень тонкий стеклянный порошок размером от 100 до 500 микрон смешивают с пенообразователем и нагревают до температуры вспенивания от 700 до 900 ° C. На рисунке 5.19 показана технологическая схема от «стеклобоя» из отработанного стекла до производства типичного пеностекла.На свойства пеностекла влияют следующие факторы:
РИСУНОК 5.19. Технологическая схема производства пеностекла
- •
Размер частиц: существует прямая пропорциональная зависимость между плотностью изделий из пеностекла и начальным размером частиц стеклянного порошка.
- •
Количество пенообразователя в исходной смеси: Между плотностью пеностекла и количеством угля в исходной смеси существует обратная пропорциональная зависимость.
- •
Время и температура нагрева: существует прямая зависимость образования и плотности пеностекла от времени и температуры нагрева.
Пенополиуретан с сетчатой структурой | UFP Technologies
Пористость сетчатой пены очень важна при разработке нестандартного компонента или продукта. Технический опыт UFP Technologies поможет вам при выборе подходящего материала для вашего компонента.
Технология пенывключает манипуляции с тысячами пластиковых пузырьков (называемых ячейками) точно контролируемого размера.Ретикуляция — это постпроцесс при производстве пены, при котором удаляются оконные мембраны ячейки. Ячейки, из которых состоит пена, могут иметь множество вариаций, которые также можно точно контролировать. Различные пены имеют разную структуру ячеек и характеристики, но пены из одного и того же семейства материалов также могут быть изготовлены с совершенно разными характеристиками плотности и твердости, что сильно повлияет на их характеристики.
Существует два метода ретикуляции: термический, называемый « закалка », и химический, называемый « закалка ».»Чтобы узнать о различиях между этими двумя методами, ознакомьтесь с нашим сообщением в блоге здесь.
Области применения
Сетчатая пена доступна в двух основных типах: полиэфир и полиэстер, а также различные плотности и цвета. Мелкопористая сетчатая пена 100 PPI (пор на дюйм) используется в самых разных областях, таких как:
- Звукопоглотитель в безэховых камерах
- Микрофоны
- Стекло ветровое
- Фильтры
- Маски для лица
- Салфетки и аппликаторы
Сетчатая пена может действовать как фильтр.Фильтровальная пена — это сетчатая полиуретановая пена, специально адаптированная для фильтрации воздуха и жидкостей, в диапазоне контролируемых ячеек от 10 пор на дюйм до 100 PPI. Пенопласт со средней пористостью 45 PPI работает как фильтр с глубокой загрузкой, в отличие от фильтра с поверхностной загрузкой, улавливая частицы пыли внутри своей ячеистой структуры. Поскольку в процессе ретикуляции остается каркасная структура пены, остается 97% объема пустот, что дает ему большую площадь поверхности для столкновения с частицами пыли.Сетчатый поролоновый фильтр с его однородной и однородной структурой ячеек может быть спроектирован с учетом падения давления и эффективности фильтрации за счет изменения размера пор. Сетчатая пена с крупной пористостью, 10 PPI, эффективна в качестве шумоглушителя, скруббера, моющейся фильтрующей среды для кондиционеров, печей, небольших двигателей и автомобильных воздухоочистителей, а также для многих других применений.
При сжатии сетчатой пены материал приобретает новый набор свойств, идеальный для других применений, требующих больших объемов пустот, однородной пористости, ненаправленных характеристик, исключительной воздухопроницаемости и однородной текстуры.Сетчатую пену часто сжимают и используют для создания чернильных валиков, фильтров крови и других продуктов, требующих впитывающих свойств.
Полиэфирная пена
Сетчатая полиэфирно-уретановая пена имеет трехмерную каркасную структуру прядей, которая сводит к минимуму возможность открытых каналов и обеспечивает отличные фильтрующие свойства. Полиэфирная пена представляет собой гибкий пенополиуретан с открытыми порами, который является пористым и имеет однородную структуру ячеек. Он имеет равномерно распределенную ячеистую структуру с высокой долей закрытых ячеек или «окон», отражающих свет.Большое количество окон делает пенополистирол идеальным для герметизации, поскольку он естественным образом препятствует потоку воздуха. Единая структура ячеек, присущая полиэфирной пене, также делает ее идеальной для процесса ретикуляции. Пенополиэфир можно легко сжать, образуя листы фиксированной желаемой толщины. Добавки, вводимые во время производства, могут изменять свойства пены, делая ее огнестойкой, антимикробной, антистатической, проводящей и / или рассеивающей электростатический заряд (ESD). Войлочная фильтрующая пена из полиэстера имеет сильно ограниченную структуру ячеек и в основном используется для фильтрации воздуха и жидкостей.
Полиэфирная пена
Сетчатые полиэфир-уретановые пены были разработаны для повышения гидростатической стабильности. Полиэфирная пена — это гибкий, сжатый пенополиуретан с открытыми ячейками и гладкой текстурой. Полиэфирная пена производится путем смешивания простых полиэфирполиолов с катализаторами и вспенивающим агентом с образованием свободно поднимающейся пенистой пены, которая затвердевает в течение нескольких минут, в результате чего получается булочка из полиэфирной пены, готовая к изготовлению. Защитные и амортизирующие свойства вспененного полиэстера делают его идеальным материалом для упаковки.Он обладает высокой вязкостью, превосходной растворимостью и устойчив к истиранию и порезам. Он широко используется в медицинской, швейной и спортивной промышленности.
продуктов Acousti — AcoustiPack ™ EXTRA
Новый AcoustiPack ™ EXTRA Foam Blocks Набор содержит 3 акустических пеноблока. Их можно использовать внутри любых свободных отсеков для дисков, чтобы увеличить поглощение нежелательной звуковой энергии. После установки пеноблоки также помогают уменьшить внутренний объем воздуха внутри вашего ПК или корпуса сервера, что, в свою очередь, может улучшить скорость воздушного потока и эффективность охлаждения.
Блоки изготовлены из плотной акустической пены профессионального уровня, имеющей сертификат огнестойкости UL94-HF1. Пена особенно эффективна для поглощения высокочастотного звука, такого как вой HDD , или высокочастотный шум от компонентов материнской платы. Пена черного цвета и достаточно гибкая, чтобы ее можно было втиснуть в пустые отсеки для дисков размером 5¼ или 3½ дюйма и под давлением.
Обзор — Блоки из пеноматериала AcoustiPack ™ EXTRA
Код продукта: APExtB
Что в коробке? | ||
3.5 дюймовый блок отсека для дисковода (для жесткого диска или отсека для дисковода дисковода) | 1 | |
5,25 дюйма Блок отсека для дисковода (для отсеков для оптических дисководов, например DVD, CD-ROM) | 2 | |
ИТОГО Число Листов: | 3 | |
Пользователь продукта Инструкции: | Включено | |
3.5-дюймовый блок Размеры: (ШxГxВ) | 140 x 103 x 26 мм | |
Блок 5,25 дюйма Размеры: (ШхГхВ) | 180 x 147 x 41 мм | |
Воспламеняемость Сертификат: | UL94-HF1 (Материал, внесенный в список UL) | |
Сертификат RoHS | ДА |
Эта упаковка подходит для:
Подходит для любого ПК со свободным 3½-дюймовым отсеком для дисковода и / или свободным 5-дюймовым отсеком для дисковода.
ПРИМЕЧАНИЕ: Блоки нельзя использовать непосредственно против теплых компонентов — всегда обеспечивайте адекватную циркуляцию вокруг соседних компонентов, таких как жесткие диски.
Упаковка — блоки AcoustiPack ™ EXTRA
Ассортимент продукции AcoustiPack ™ был разработан для доставки конечному потребителю без необходимости в дополнительной упаковке. На индивидуальной упаковке продукта нет печати на одной стороне, и она достаточно прочная, чтобы выдерживать нормальное обращение во время транспортировки.Картон имеет минимальное содержание вторичного сырья 35%.
Упаковка | ||
Индивидуальная упаковка продукта: | APExtB x1 | |
Вес упаковки: | 0,30 кг (0,66 фунта) | |
Внешние размеры упаковки: (ШxГxВ) | 195 x 160 x 115 мм | |
Упаковка нескольких продуктов: | APExtB x12 | |
Кол-во в транспортной коробке: | 12 | |
Вес транспортной коробки: | 3,63 кг (8 фунтов) | |
Транспортная коробка Внешние размеры: (ШxГxВ) | 500 x 400 x 250 мм | |
Информация о дистрибьюторе и реселлере: | Блоки AcoustiPack ™ EXTRA | |
Штрих-код продукта: (EAN-13) | 5060087740324 |
Рекомендации по фитингу
Корпус компьютера можно смонтировать от начала до конца примерно за 30-45 минут в зависимости от сложности корпуса.Рекомендации по установке содержатся в инструкции по эксплуатации, прилагаемой к упаковке, и доступны для загрузки здесь:
Руководство пользователя AcoustiPack ™ (90 КБ)
Пожалуйста, внимательно прочтите рекомендации по установке перед установкой этого продукта. Установщик устанавливает эти материалы на свой страх и риск.
верх
Вы можете рассмотреть этот продукт вместе с AcoustiPack ™ LITE (APL) или AcoustiPack ™ ULTIMATE (APU).
Продукт EXTRA Foam Blocks увеличивает площадь внутренней поверхности комплекта акустических материалов и помогает поглощать дополнительную акустическую энергию внутри ПК или корпуса сервера.
Подробнее о ULTIMATE.
Подробнее о LITE.
верх
Исследователи показывают, что металлическая пена может блокировать радиацию | Инженерный колледж
1 марта 2016 г. | Инженерные коммуникации
Др.Афсане Рабиеи, профессор механической и аэрокосмической техники, и ее коллеги работают над исследованиями, которые показывают, что легкие композитные металлические пены эффективны при блокировании рентгеновских лучей, гамма-лучей и нейтронного излучения и способны поглощать энергию сильных столкновений.
«Эта работа означает, что есть возможность использовать композитный металлический пенопласт для разработки более безопасных систем транспортировки ядерных отходов, более эффективных конструкций космических кораблей и ядерных структур, а также новой защиты для использования в компьютерных томографах», — сказал Рабие.
Сначала она разработала прочную и легкую металлическую пену для использования на транспорте и в военных целях, а позже она хотела определить, можно ли использовать пену для ядерных или космических исследований, где она могла бы обеспечить структурную поддержку и защиту от сильных ударов и ударов. радиация.
Rabiei и ее коллеги решили провести несколько тестов, чтобы увидеть, насколько эффективна пена в блокировании рентгеновских лучей, гамма-лучей и нейтронного излучения. Затем характеристики материала сравнивали с характеристиками сыпучих материалов, которые в настоящее время используются в экранирующих приложениях, с использованием образцов одинаковой поверхностной плотности — это означает, что каждый образец имел одинаковый вес, но различался по объему.
Наиболее эффективный композитный пеноматериал против всех трех форм излучения называется «сталь-сталь с высоким Z» и состоит в основном из нержавеющей стали, но содержит небольшое количество вольфрама. Однако структура пены с высоким Z была изменена, так что композитная пена, содержащая вольфрам, не была плотнее металлической пены, полностью изготовленной из нержавеющей стали.
Путем тестирования различных видов гамма-излучения исследователи обнаружили, что пена с высоким Z была сопоставима с объемными материалами по блокированию высокоэнергетических гамма-лучей, но была намного лучше, чем объемные материалы — даже объемная сталь — в блокировании низкоэнергетических гамма-лучей и он превзошел другие материалы в блокировании нейтронного излучения.Хотя, когда дело дошло до блокирования рентгеновских лучей, свинец все равно не победил.
«Однако мы работаем над изменением состава металлической пены, чтобы она была еще более эффективной, чем свинец, блокируя рентгеновские лучи — и наши первые результаты многообещающие», — сказал Рабие. «Преимущество наших пен в том, что они нетоксичны, а это означает, что их легче производить и перерабатывать. Кроме того, исключительные механические и термические свойства композитных металлических пен и их способность поглощать энергию делают этот материал хорошим кандидатом для различных ядерных структурных применений.”
Вернитесь к содержанию или загрузите журнал NC State Engineering, весна / лето 2016 (PDF, 3 МБ).
Архив журналов
Руководство по выбору пен и пеноматериалов
Пены и пеноматериалы изготавливаются из эластомеров низкой плотности, пластмасс и других материалов с различной пористостью. Они используются в различных архитектурных, промышленных, медицинских и бытовых приложениях.
Существует шесть основных типов пен и пеноматериалов:
- Открытая ячейка
- Закрытая сотовая
- гибкий
- Жесткий
- Ретикуляр
- Синтаксический
Пенопласты с открытыми порами имеют взаимосвязанные поры или ячейки и подходят для фильтрации.Пенопласты с закрытыми порами не имеют связанных между собой пор или ячеек, но используются для обеспечения плавучести или плавучести. Гибкие пены могут сгибаться, сгибаться или поглощать удары без растрескивания и расслоения. Сетчатые пены имеют очень открытую структуру с матрицей, состоящей из взаимосвязанной сети тонких материальных нитей. Жесткие пенопласты имеют матрицу с очень небольшой гибкостью или вообще без нее. Синтаксические пены состоят из жестких микросфер или стеклянных микрошариков, скрепленных пластиковой или полимерной матрицей.
Доступные пеноматериалы
Пены и пеноматериалы доступны в различных формах. Некоторые продукты содержат металл, металлический сплав или керамические материалы. Другие содержат пластмассы, полимеры, эластомеры, термореактивные пластмассы, термореактивные смолы или термопласты.
Смолы для литья
Смолы для литья — это пластмассовые или эластомерные смеси, используемые для литья деталей или форм или формирования конструкций на месте. Обычно они состоят из двух частей (A + B), где A — смола, а B — катализатор или отвердитель.Смолы для литья доступны в виде пены для распыления, пенных пакетов и текучих материалов.
Смолы для литья под давлением также доступны, но в форме гранул. Эти изделия из пластика и эластомера подходят для изготовления деталей путем литья под давлением, компрессионного формования, выдувного формования или экструзии пленки, реактивного литья под давлением (RIM) и литья под давлением (RTM).
Формы заготовки
Формы заготовок для пен и пеноматериалов включают бруски, доски, блоки, булочки, пленку, стержни и листы.
Пенохимические системы
Существует множество химических систем для пен и пеноматериалов.
- Акрилонитрил-бутадиен-стирол (ABS) — твердый, жесткий термопластичный полимер, который обеспечивает хорошую химическую стойкость и сопротивление ползучести.
- Акрил обеспечивает отличную устойчивость к воздействию окружающей среды и быстрое схватывание по сравнению с другими системами смол.
- Эпоксидные смолы демонстрируют высокую прочность и низкую усадку во время отверждения.
- Фторполимеры используются там, где требуется превосходная химическая стойкость.
- Стирол-изопрен-стирол (SIS) и стирол-бутадиен-стирол (SBS) используются в клеях, чувствительных к давлению.
- Синтетические каучуки или эластомеры основаны на различных системах, таких как силикон, полиуретан и неопрен.
- Нитриловый каучук обеспечивает хорошую стойкость к нефтяным углеводородам и топливу.
- Пластмассы или эластомеры , изготовленные из натурального или растительного сырья, такого как натуральный каучук (полиизопрен) или вулканизированные волокна, также доступны.
- Смолы на водной и водной основе и латексные материалы не содержат летучих органических соединений (ЛОС).
- Химические системы для пен и пеноматериалов включают сополимер этилена, вспененный полиэтилен, поликарбонат, полиэфир, простой полиэфир, полиэфиримид, полиимид, полиолефин, полипропилен, фенол, полимочевину и винил.
Видео предоставлено: BJB Enterprises, Inc. / CC BY-SA 4.0
Технические характеристики
Важные спецификации для пен и пеноматериалов включают:
- Насыпная плотность
- Прочность на разрыв
- Модуль упругости при растяжении
- Удлинение
- Прочность на разрыв
- Использовать температуру
- Теплопроводность
- Диэлектрическая прочность
Объемная или кажущаяся плотность зависит от теоретической плотности пены и ее фактической пористости после упаковки.Прочность на растяжение — это максимальная величина напряжения, необходимая для разрушения или разрушения пены в условиях растягивающей нагрузки. Модуль Юнга или модуль упругости — это постоянная материала, которая указывает на изменение деформации, возникающей под действием приложенной растягивающей нагрузки.
Относительное удлинение — это процент деформации, возникающей во время испытания на растяжение или другого механического испытания. Теплопроводность — это линейная теплопередача на единицу площади через материал при заданном температурном градиенте. Диэлектрическая прочность — это максимальное поле напряжения, которое материал может выдержать до того, как произойдет электрический пробой.
Стандарты
ASTM D3574 — Стандартные методы испытаний гибких ячеистых материалов — плиты, склеенные и формованные уретановые пены
ASTM D6826 — Стандартные спецификации для распыляемых суспензий, пен и местных материалов, используемых в качестве альтернативного ежедневного покрытия для полигонов твердых бытовых отходов
ASTM F2038 — Стандартное руководство по силиконовым эластомерам, гелям и пенам, используемым в медицинских целях. Часть I. Составы и неотвержденные материалы
Изображение кредита:
Промышленные клеи и ленты 3M Канада | BJB Enterprises
Прочитать информацию о пенах и пеноматериалах для пользователей
Вспененный полипропилен (EPP)
Вспененный полипропилен (EPP) — это универсальный пенопласт с закрытыми порами, который обеспечивает уникальный набор свойств, включая превосходное поглощение энергии, множественную ударопрочность, теплоизоляцию, плавучесть, водо- и химическую стойкость, исключительно высокое отношение прочности к весу и 100%. % пригодности к вторичной переработке.EPP может быть изготовлен в широком диапазоне плотностей от 15 до 200 граммов на литр, которые трансформируются путем формования в плотности от 18 до 260 граммов на литр. Отдельные бусинки сливаются в конечную форму продукта в процессе формования парового сундука, в результате чего получается прочная и легкая форма.
Хотите купить EPP?
Как обрабатывать EPP
Производственный процесс сложен и требует как технических знаний, так и специализированного оборудования.Полипропиленовая смола комбинируется с другими ингредиентами в запатентованном многоступенчатом процессе. В строго контролируемых условиях экструдированные гранулы расширяются, превращаясь в шарики из вспененного полипропилена постоянной формы. Другие специализированные производственные технологии могут использоваться для получения вариаций в форме конечного продукта.
Гранулы пенопласта EPP затем впрыскиваются в формы. Во многих случаях используются недорогие алюминиевые формы с несколькими полостями. Давление и тепло пара превращают шарики в готовую форму.Готовая деталь из вспененного полипропилена становится ключевым компонентом в узлах, входящих в состав оригинального продукта производителя оборудования.
Недвижимость
Доступные марки
EPP доступен в сортах, необходимых для широкого спектра применений, в зависимости от технических требований. Марки с высокой плотностью используются там, где важно управление энергопотреблением, например, в автомобильных бамперах и компонентах внутренней безопасности пассажиров.Марки низкой плотности используются для упаковки, а марки средней плотности находят применение в мебели и других потребительских товарах.
Марки с низким уровнем выбросов сводят к минимуму выделение летучих органических соединений для внутренних деталей автомобилей. Доступны антистатические, рассеивающие и проводящие классы, обычно используемые для специальных требований к упаковке.
Уникальные рабочие характеристики
Пористый EPP состоит из полипропиленовых шариков цилиндрической формы, которые добавляют воздушное пространство между шариками в окончательной формованной форме, что усиливает полезные звукоизолирующие эффекты и снижает вес. EPP обычно окрашивается в черный цвет для автомобильной промышленности, хотя часто встречается в белом цвете для упаковки продуктов. EPP доступен от некоторых поставщиков в ярких цветах, подходящих для текстурированной поверхности презентационного уровня. |
Физические свойства Диапазон плотности EPP, от 20 г / л до 200 г / л Предел прочности (кПа) от 270 до 1930 Прочность на сжатие (кПа) Набор для сжатия (%) | Химическая стойкость Экспозиционная среда Погружение на 7 дней при 22 ° C Бензин / бензин 2 |
Приложения
EPP широко используется производителями автомобилей из-за его преимуществ в отношении управления энергопотреблением, легкости, расширенной функциональности, долговечности и возможности вторичной переработки.Применения включают сиденья, бамперы, системы хранения, дверные панели, стойки, выравниватели пола, полки для пакетов, подголовники, наборы инструментов, солнцезащитные козырьки и множество наполнителей.
Многоразовая промышленная упаковка, известная как dunnage, часто изготавливается из EPP из-за ее прочности и присущей ей способности поглощать энергию при транспортировке. EPP все чаще используется в мебели, игрушках, таких как модели самолетов, и других потребительских товарах из-за его универсальности в качестве конструкционного материала и его легкого веса, а также других эксплуатационных характеристик. |
EPP одобрен для использования с пищевыми продуктами. Его теплоизоляционные свойства и структурная прочность делают его подходящим для контейнеров, таких как контейнеры для доставки еды, охладители напитков и тому подобное. EPP не поддерживает рост микробов и может быть стерилен с помощью очистки паром.
История EPP
EPP был впервые разработан в 1970-х годах в результате исследований новых форм полипропилена.Первые применения этого материала были в автомобильной продукции в Японии в 1982 году. Спрос на EPP с тех пор резко вырос во всех регионах мира, частично из-за потребности автопроизводителей в улучшении функций управления энергопотреблением при одновременном снижении веса и улучшении экологических преимуществ. Первым автомобильным применением EPP был элемент, поглощающий энергию, в системе бампера. В настоящее время EPP широко используется для многих других автомобильных деталей и систем, включая сиденья и другие внутренние компоненты.
Backer Rod Mfg. & Bay Foam Products Inc. :: Ultra Block®
ULTRA BLOCK ® — это предварительно разработанное, запатентованное текстильное стекловолокно с матовой стекловолоконной облицовкой, содержащее примерно 30% по массе невспученного вермикулита. ULTRA BLOCK ® в основном используется в огнестойких строительных швах.
Особые области применения:
Конструкционная противопожарная защита была создана в 1917 году, когда комитет ASTM учредил ASTM E19. Сегодня E19 превратился в ASTM E119 и ANSI / UL2079. Согласно Международным строительным нормам и правилам требуется документация, согласно которой строительные сборки, компоненты и элементы конструкций проходят огнестойкие испытания в соответствии с процедурами испытаний, изложенными в ASTM E119 и ANSI / UL2079. Все системы проектирования ULTRA BLOCK® UL соответствуют Международным строительным нормам.
Когда архитекторы проектируют конструкцию, они проектируют и устанавливают механические, компенсационные / строительные швы. Швы должны компенсировать продолжающееся повседневное расширение и сжатие, которое должно выдерживать здание. Когда кодекс требует, чтобы эти конструкции были огнестойкими, установленная система компенсационных швов должна иметь такой же уровень огнестойкости, как и смежная конструкция. Система компенсаторов должна быть способна открывать и закрывать конструкцию стыка и оставаться на месте для выполнения своей проектной функции огнестойкости, если и когда она когда-либо понадобится.
Ограничения:
Все системы компенсаторов ULTRA BLOCK ® представляют собой как минимум двухкомпонентную конструкцию. Глубина ULTRA BLOCK ® контролирует теплоотвод или повышение температуры от горячей стороны к холодной стороне конструкции. Добавление эластомерного герметика номинальной толщиной 1/2 дюйма с одной или обеих сторон сдерживает дым, токсичные пары и несгоревшие газы.
Каждый крупный производитель герметика в США испытывал один или несколько своих герметиков. в системе с классом UL ULTRA BLOC K®.
|
|
ULTRA BLOCK ® будет установлен в соответствии со стандартной конструкцией сжатия. Соединение «C&D» Clean & Dry необходимо для обеспечения полного прилегания герметика к сторонам шва.
Состав и материалы:
Все системы ULTRA BLOCK ® производятся в соответствии с требованиями проекта. При однослойной установке следующие размеры «A» и «B» могут отличаться.
- «А», сложенная пополам, становится глубиной. Глубина определяет рейтинг огня.
- «A» 6 дюймов в сложенном и установленном состоянии — 3 дюйма равны 2 часам огнестойкости.
- «A» 8 дюймов, сложенные и установленные — 4 дюйма равны 3 часам огнестойкости.
- «A» 12 дюймов, сложенная и установленная — 6 дюймов.равняется 4 часам огнестойкости.
Используйте следующий выбор толщины стола:
Ширина шва | Использовать | Длина рулона |
1/2 » | 3/8 дюйма толщ. | 70 LF |
3/4 дюйма | 1/2 «толщ. | 60 LF |
1 » | 3/4 дюйма толщ. | 40 LF |
1-1 / 2 » | толщиной 1 дюйм. | 30 LF |
Швы шириной 2 дюйма или более требуют наших многослойных конструкций. Подрядчик должен сообщить нам ширину шва, почасовую огнестойкость и требуемую конфигурацию.
Технические данные
Под руководством и под руководством Underwriters Laboratories, Нортбрук, Иллинойс , Backer Rod Mfg. Inc. создала наш главный файл R13729.Все наши испытания проводились в ПОЛНОМ МАСШТАБЕ, площадь поверхности поддона 180 кв. Футов, и каждое испытанное соединение было 12 футов в длину. Наше тестирование действительно включало часть струи из шланга. Стандарт испытаний был ANSI / UL2079, ASTM E119, UL 263, NFPA 251. Полномасштабное испытание принесло нам классификацию UL по всем горизонтальным и всем вертикальным швам, а также соответствие Международным строительным нормам. Многие из них представляют собой многопользовательские списки, которые включают проекты «От пола до пола», «От пола до стены», «От стены до стены» и «Начальник отдела стены».
Системы ULTRA BLOCK ® позволяют механическому компенсатору / конструкционному соединению функционировать и выполнять цель, для которой он был разработан, «ДВИЖЕНИЕ.»
Структурные испытания конструкций ULTRA BLOCK ® были выполнены компанией Hauser Research, Боулдер, Колорадо. Наши системные испытания проводились на перемещении +/- 50% для 28 775 открытий и закрытий. При расширении и сжатии один раз в день, Это соответствует 78 годам службы. Стандарт испытания движения — ASTM E1399.
Сейсмические испытания конструкции ULTRA BLOCK ® были проведены Калифорнийским университетом, Сан-Диего, Калифорния. Сейсмическое испытание «Землетрясение» было названием проекта «TCCMAR» спонсируется США и Японией. ULTRA BLOCK ® настолько хорошо проявил себя в своей 2-этажной конструкции, что был назван единственным источником для использования во втором тесте, 5-этажной конструкции.
Все системы ULTRA BLOCK ® покрыты эластомерным герметиком с номинальной глубиной 1/2 дюйма (см. Список производителей). Конструкции системы могут варьироваться от 1 часа, 2 часа, 3 часа или 4 часа. номинальные характеристики и ширина шва от 1/2 до 7 дюймов. Мы просим вас убедиться, что выбранный вами герметик соответствует конструкции нашей системы.
Применимые стандарты:
- IBC — Международный строительный кодекс
- ANSI / UL2079 — Стандарт UL для огнестойких испытаний на огнестойкость строительных соединительных систем
- ASTM E 119 — Метод огнестойких испытаний строительных конструкций и материалов
- ASTM E 814 — Методы испытаний на огнестойкость ступеней сквозного огня
- ASTM E 84 — Метод испытания характеристик горения строительных материалов на поверхности
- ASTM E 136 — Метод испытаний поведения материалов в вертикальной трубчатой печи при 750 ° C
- ASTM E 90 — Метод испытаний для лабораторного измерения потерь при передаче воздушного звука перегородками здания
- NFPA 251 — Испытание на огнестойкость строительных строительных материалов
- NFPA 255 — Характер горения строительных материалов
- ASTM E 1399 — Циклический метод испытания Перемещение и измерение минимальной и максимальной ширины швов системы архитектурных швов
- ASTM C 719 — Метод испытаний для A Дгезия и когезия эластомерных герметиков при циклическом движении.
- ASTM C 920 — Спецификация эластомерных герметиков для швов
- UL 263-92 — Стандарт UL для огнестойких испытаний строительных конструкций и материалов
- UL 2079 — Стандарт UL для испытаний на огнестойкость систем строительных швов
- UL 1479 — Стандарт UL для испытаний огнестойкости сквозных противопожарных заглушек
- UL 723 — Стандарт UL для испытаний на огнестойкость строительных материалов на горение поверхности
Физические свойства:
ULTRA BLOCK ® представляет собой непрерывное волокно из текстильного стекловолокна и может вызвать раздражение кожи и глаз.При обращении и / или применении надевайте длинные рукава, перчатки и шапочку. Надевайте защитные очки (очки, защитные очки). MSDS подтверждает, что ULTRA BLOCK®: не включен в список, не регулируется и не классифицируется как канцероген. Это относится как к установке, так и к удалению в случае пожара.
.