оборудование и технология. Разновидности рубероида.
Рубероид – кровельный материал, изготовленный из картона, стекла и нефтесодержащей жидкости (битума). Все крупные производители придерживаются государственного стандарта, но это не является обязательным условием, поэтому мелкие бизнесмены изготавливаю рубероид по техническим условиям.
Имея средства на изготовлении кровельного материала необходимо закупить хотя бы минимальный набор оборудования, наладить технологическую схему производства, а также определиться с выпускаемыми видами.
Оборудование для производства рубероида.
Для изготовления рубероида необходим хотя бы такой минимальный набор оборудования:
- Установка для размотки основы, которая выпускается в рулонах.
- Подъёмное устройство.
- Битумосмеситель. Это оборудование, в котором происходит процесс дробления и перемешивания битума.
- Битумоварка (электрическая, газовая). Существует для быстрого расплавления битума до нужной температуры с последующей передачей его в насосную станцию.
- Насосная станция. Откачивает расплавленный битум и поставляет его на линию производства.
- Линия главного производственного процесса. На ней будет осуществляться пропитка, посыпка стеклом и мелкозернистой крошкой, сушка.
- Установка для намотки готового рубероида в рулоны.
- Пульт управления.
Технология производства рубероида.
Для выпуска рулонного кровельного материала необходимо:
- Нефтяной битум (в зависимости от вида рубероида).
- Кровельный картон в рулонах.
- Гидросиликат магия (тальк).
- Песок.
Схема изготовления рубероида представлена в таком виде:
- Фиксирование рулонной основы (картона) в размоточной установке.
- Подъём на необходимую высоту с помощью домкратного устройства.
- Заход на линию, где происходит пропитка картона расплавленным битумом (жидким, а затем более твёрдым).
- Выход пропитанного битумами картона и посыпка мелкозернистой крошки во избежание слипания в рулонном виде.
- Сушка на охлаждённом столе.
- Обрез и намотка в рулоны.
При изготовлении материала используется несколько видов битума: для пропитки (кровельный, дорожный) и покровного слоя.
Мелкозернистая крошка служит для предотвращения попадания влаги и света, имеет отличные показатели теплостойкости.
Разновидности рубероида.
Поскольку классический рубероид не отличается особой износостойкостью, и спустя несколько лет он будет выглядеть потресканым и вздутым, производители стараются изобрести более качественный и долговечный материал. Именно поэтому и появляются новые виды рубероида:
- Еврорубероид. В основу битумной пропитки входят специальные присадки (добавки). Они улучают гибкость, повышают износостойкость и герметичность кровельного материала.
- Стеклорубероид. В основе лежит не картон, а стекловолокно, которое с двух сторон покрывается битумом и посыпается мелкозернистой крошкой.
- Рубемаст. В основе также лежит кровельный картон, только тыльная сторона более мощно обрабатывается битумом, поскольку укладка производиться с помощью подплавления этого слоя.
- Пергамин – материал для пароизоляции, в основе которого лежит картон, пропитанный с двух сторон нефтяным битумом. Маркировка имеет числовой индекс, который определяет плотность картона.
Также вам будет полезно:
- Толь. Это картон, просмолённый с двух сторон дёгтем и усыпанный мелкозернистой крошкой.
Он очень лёгкий и дешёвый, поэтому пользуется популярностью, как и классический рубероид.
Также посмотрите интересное видео о производстве рубероида
ТвитнутьОборудование для производства рубероида
Оборудование для производства рубероида это основа производства перерабоки битумных продуктов. На сегодняшний день такой материал как рубероид получил довольно широкое распространение в разных сферах промышленности, производства и строительства. Дело в том, что данный материал обладает прекрасными водонепроницаемыми, изолирующими, свойствами. Предназначается для кровли, гидроизоляции и т.д.
Характеристики оборудования для производства рубероида
Данный материал является прочным, износостойким и главное, довольно дешевым. Именно поэтому повсеместно стали открываться цеха, которые обустроены специализированным оборудованием по производству рубероида. Для того, чтобы производить рубероид важно наличие такого оборудования, как: стол на котором происходит размотка основы, непосредственно сама производственная линия по изготовлению рубероида, и стол, на котором происходит намотка готового материала. Среди основных характеристик оборудования для производства рубероида является надежность всех узлов и агрегатов. Поэтому при выборе оборудования следует уделять этим показателям особое внимание.
Оборудование для производства рубероида — эксплуатация и технология
Рассмотрим более подробно, как происходит сам производственный процесс на оборудовании для производства рубероида. Линия по производству рубероида так же состоит из отдельных элементов, весь процесс начинается с того, что специальный для изготовления рубероида материал – пергамин – в виде большой свернутой в рулон бобины, устанавливается на станке для размотки. Далее происходит сам размоточный процесс, в результате которого уже частично размотанный материал поступает на следующую стадию обработки. Ей является подсушка, затем происходят процессы насыщения и далее полотно подвергают нанесению первого слоя битумного материала.
Все действие происходит непрерывно, движение обеспечивается посредством крутящихся барабанов. Таким образом, пласт картона, склеенный со слоем рубероида, двигаясь в обоих направлениях за счет барабанов, подсушивается, поскольку происходит испарение влаги. После окончания всех вышеперечисленных процедур, материал подается в специальную ванну для пропитки, где производится пропитывание полотна, горячим битумом. Для равномерности пропитки материал движется посредством крутящихся валов, которые с одной стороны подают материал на пропитку, а затем производят отжим полотна, посредством вытягивающих валов.
После прохождения процедуры отжима, на полотне остается легкая битумная пленка, таким образом, происходит накладывание уже второго слоя. Далее практически готовый материал поступает на процесс допропитки, здесь также работают два барабана, которые заставляют полотно ходить взад-вперед, обеспечивая при этом равномерное покрытие материала битумом.
Далее готовое, пропитанное средствами полотно проходит стадию охлаждения, после чего на обе стороны материала наносят специальный сыпучий минерал, дабы предотвратить склейку поверхности при заматывании в рулон. Затем посредством специальных валиков для прикатки, данные минеральные материалы вдавливаются в полотно. Уже подготовленный таким образом рубероид, в остывшем виде подается на запасный магазин. Отсюда он порционно выдается на намоточный стол, где происходит формовка рубероида в рулоны. Намоточный стол это практически финальный этап производства рубероида на технологическом оборудовании.
Специальный измеритель регулирует подачу нужной длины рубероида из запасного магазина. Таким образом, все рулоны, выходящие из намоточного стола, имеют одинаковый размер и длину и ширину. После скатывания в рулон, рубероид проходит стадию упаковки и штамповки. Упаковка рубероида на специальном оборудовании, которое имеет разматывающее бумагу автоматическое устройство. Отрезанный по заданным размерам бумажный лист, покрывается тонким слоем битума, для того чтобы произошло склеивание.
Таким образом оборудование для производства рубероида имеет ряд агрегатов и механизмов, которые объединяются в единый технологический процесс.
Технология производства битумов, пригодных для получения конкурентоспособного рубероида, на основе госсиполовой смолы
Технология производства битумов, пригодных для получения конкурентоспособного рубероида,на основе госсиполовой смолы
Жуманиязов Максуд Жаббиевич, доктор технических. наук, профессор;
Курамбаев Шерзод Раимберганович, кандидат технических наук, доцент;
В данном материале приводятся результаты физико-химических и технологических исследований по разработке битума госсиполовой смолы-отхода масложировых комбинатов, а также возможности использования его для производства рубероида с улучшенными физико-механическими и технологическими показателями.
Ключевые слова: рубероид, госсиполовая смола; модернизация, лактам, старение битума, кровельный материал; пожаробезопасность, водостойкость, коррозионостойкость, термоокисления; уротропин.
Рубероид является самым популярным, экономически выгодным кровельным и гидроизоляционным материалом, имеет высокую прочность на разрыв, гибкость, эластичность, водонепроницаемость, прост в изготовление и укладке. Несмотря набольшое количество производимых разнообразных современных кровельных материалов, не дает снижения объема выпуска и не влияет на популярность рубероида, успешность конкурирования с эффективными аналогами.
Однако есть существенные недостатки, которые заставляют задуматься о целесообразности выбора рубероида. Рубероид имеет довольно маленькую прочность, относительно низкую устойчивость к воздействию высоких и низких температур. При повышении температуры содержащиеся рубероид начинает плавиться, а при ее снижении битумные слои могут растрескаться, это значительно отразится на защитных свойствах рубероида, а также он имеет свойство легко воспламеняться, поэтому во время эксплуатации материала не рекомендуется разжигать открытый огонь вблизи кровли, срок эксплуатации небольшой, который составляет не более 4–5 лет.
Главной причиной недостатков рубероида является использование несоответствующего нефтяного битума для пропитки и покрытия кровельного картона. Качество нефтей служит определяющим фактором в обеспечении качества битумов. Основной проблемой битумов несоответствия является использование при производстве низкокачественного и нестабильного состава нефти парафинового основания. Именно этот недостаток приводит к снижению физико-механических свойств, таких как пластичность, термостойкость, долговечность, склонность к старению и ухудшению ряда других эксплуатационных показателей битумов. На сегодняшний день около 70 % выпускаемых в странах СНГ битумов не соответствуют качеству современного рубероида. Малейшие изменения в исходном сырье и технологии его переработки ведут к изменению состава битума и его свойств.
В научно-технической литературе имеется множество сведений и рекомендаций по модернизации нефтяного битума. Многочисленные попытки получения стандартных нефтяных битумов пригодных для производства рубероида до сих пор не увенчались успехом. Основные недостатки рубероида остаются навсегда, если его получают на основе нефтяного битума.
С другой стороны, по данным статистики во всем мире наблюдается снижение запасов нефти, а потребность битумов во всех странах мира непрерывно растет. В связи с ограниченностью запасов нефти, высокие темпы роста потребности на битум и изоляционные материалы на его основе настоятельно требуют необходимость поиска нетрадиционных источников сырья и разработки новых способов получения на их основе. Одним из таких альтернативных источников сырья битума вполне могут служить госсиполовая смола- отход масложировых комбинатов.
Выбор госсиполовой смолы обусловливается тем, что химический состав почти сходится с составом битума, главное в ее составе отсутствует парафин, который содержит в нефтяных битумах, ухудшает их свойства, а также госсиполовая смола имеет жирные кислоты в форме лактамов, так как лактамы укрепляют прочность полимера и замедляют процесс старения битума. Важнейшим фактором, обусловливаю-щим долговечность материала является старение — изменение состава и свойства битума под действием солнечного света и кислорода воздуха. Одной из доминирующих причин стареения битумов считается их окисление. Однако до сих пор не изучен вопрос о влияя-нии природы сырья и битумов на старение [1]. Процессы старения нефтяного битума под влиянием солнца и влаги ускоряются, и это приводит к разрушению структуры рубероида.
Исследования, проводимые в сфере настоящей работы, предусматривают создание технологии получения битума на основе госсиполовой смолы и докажут возможность использования его в производстве конкурентоспособного рубероида.
Для осуществления поставленной цели были решены следующие задачи- проведены теоретические и экспериментальные исследования и показана возможность синтеза битума из многотоннажного отхода госсиполовой смолы, определены технологические параметры производства, разработаны технические условия на новые виды продукции, наработаны опытно-промышленные партии битумных материалов, проведены опытные и натурные испытания по получению рубероида на их основе, в результате которых выявлен положительный эффект и дана технико-экономическая оценка целесообразности создания производства. Полученные новые научные и практические данные позволили обосновать целесообразность и перспективность вовлечения госсиполовой смолы в сферу производства строительного битума, новизна технических решений которых защищена патентами РУз [2].
При получении битума кроме госсиполовой смолы применяли также резиновую крошку — отход изношенных покрышек, кубовый остаток моноэтаноламиновой очистки, строительную негашеную известь, уротропин и мочевину, мас. %: госсиполовая смола — 88,0–90,0; резиновая крошка — 4,0–5,0; кубовой остаток моноэтаноламиновой очистки — 3,5–4,0; мочевина –0,45–0,50; негашеная известь –0,5–1,0; уротропин –0,04- 0,05.
В составе госсиполовой смолы присутствуют также полифенолы, углеводороды, азот- и фосфорсодержащие соединения — реакционно-способные с высокими комплексо-образующими свойствами, а также продукты превращения госсипола. Добавление к составу мочевины и уротропина делает продукты модификации госсиполовой смолы термо-, хемо- и коррозионно -устойчивыми. Она во многих отношениях с успехом может заменить дорогостоящие нефтяные битумы, дефицит которых ощущается с каждым годом. При этом введение уротропина и мочевины, проявляющее в предлагаемом составе комплексообразующие свойства позволяет упорядочить и упрочнить структуру поликонденсированных молекул.
В результате такого взаимодействия всех составляющих ингредиентов, получен-ный из этого состава продукт приобретает свойства необходимые для строительных битумов: уменьшение глубины проникания иглы, водонасыщенность, увеличение температуры размягчения и вспышки, что приводит к достижению поставленной задачи — повышению пожаробезопасности, водостойкости, коррозионостойкости и твердости покрова. Таким образом, повышаются физико-механические характеристики битумно-резиновой композиции на основе госсиполовой смолы — расширяется температурный интервал пластичности, увеличивается морозостойкость, устойчивость к циклическим деформациям при отрицательных температурах, повышается срок их службы.
Технология получения битума пригодных для производства рубероида заключает термоокислении госсиполовой смолы кислородом воздуха, перемешивании резиновой крошки с добавлением в полученную смесь кубовых осадков моноэтаноламиновой очистки, негашеной строительной известь, мочевины и уротропина.
На основании комплекса химических, физико-химических и технологических исследований нами разработаны научные основы и технология получения строительного битума на базе госсиполовой смолы — многотоннажных отходов масложировой промышленности. Принципиальная технологическая схема представлена на рисунке.
Технология получения битума на основе госсиполовой смолы и рубероида на его овнове осуществляется следующим образом. Госсиполовая смола из емкости (1) через вентиль (2) с помощью насоса (3) подается в реактор (4) снабженный барботером и мешал-кой, где происходит процесс обезвоживания (при 120 оС) термоокисление кислородом воздуха при 250оС, в течение 120 мин. При этом расход воздуха составляет 100 м3/час. После окончания процесса термоокисленый состав поступает в основной реактор (6).
Рис. Принципиальная технологическая схема получения рубероида с использованием битума на основе госсиполовой смолы: 1-емкость для госсиполовой смолы; 2- вентили; 3-насосы; 4- реактор для обезвоживания госсиполой смолы; 5- дымоход для выделения газов; 6- реактор для получения битума; 7- бункер для СаО; 8- емкость резиновой крошки; 9- емкость кубового остатка моноэтаноламиновой очистки; 10- емкость соапстока; 11- распылительная установка битума; 12 — ролики для полиэтилена; 13- емкость битума для пропитки картона; 14 — уплотнительные ролики; 15- компрессор; 16- распредитель холодного воздуха; 17- компрессор
При заданной скорости перемешивания (120 обр/мин) из бункеров (7), (8) постепенно засыпают СаО, резиновую крошку и перемешивают до равномерного распределения по объему. После этого дают выдержку 30 мин времени для набухания и деструкции резиновой крошки в госсиполовой среде. После чего постепенно добавляют из емкости (9) кубовый осадок моноэтаноламиновой очистки, также постепенно перемешивают и дают выдержку по времени 20 минут до окончания пенообразования. Массу охлаждают кислородом воздуха до 1350С и добавляют остальное количество модификатора, а именно мочевину и уротропин и выдерживают массу до завершения газовыделения. Технологический процесс получения битума на основе госсиполовой смолы заканчивается после полного отделения прореагировавшей газовой фазы. Готовый продукт разливают в емкость (13) для пропитки картона. Битум для покрова подается с помощью распылительной установки (11). Просыпка талька, бора и камешек и. д. осуществляется по традиционной технологии. Для охлаждения рубероида используют распредительхолодного воздуха (16), который обеспечивается воздухом с помощью компрессора (17).
Битум для покрова рубероида получается по такой же технологии, меняя процентный состав содержимым. Композиция не содержит открытых пор и существенных по размерам газовых включений, она получается однородной, без посторонних включений и не содержит частиц резиновой крошки, не покрытых битумом. Физико-механические показатели полученных битумов на основе госсиполовой смолы и аналогов представлены в нижеследующей таблице.
Таблица
Сравнение физико-механических свойств нефтяных битумов и составов полученных на основе госсиполовой смолы
Наименование показателей |
Норма для марки |
Метод испытания |
|||
БНК -40/180 |
Состав № 1, для пропитки |
БНК — 90/30 |
Состав № 2 для покрова |
||
Глубина проникания иглы при 25°С, мм |
160–210 |
170,0 -220,0 |
25–35 |
30–40 |
ГОСТ 11501 |
Температура размягчения по Кольцу и Шару, °С |
37,0–44,0 |
40,0–45,0 |
80–95 |
90–95 |
ГОСТ 11506 |
Растяжимость при 25 °С, не менее |
35–40 |
45,0 -50,0 |
0,50 |
1,0 |
ГОСТ 11505 |
Температура вспышки, оС |
240 |
315 |
240 |
315 |
ГОСТ 4333 |
Температура хрупкости, оС |
- |
— 20 |
-10 |
-15 |
ГОСТ 11507 |
Растворимость в толуоле, % |
99,5 |
99,8 |
99,50 |
99,7 |
ГОСТ 20739 |
Массовая доля воды, % |
Следы |
0,1 |
Следы |
0,1 |
ГОСТ 2477 |
Массовая доля парафина |
5,0 |
- |
3,0 |
- |
ГОСТ 17789 |
Из данных таблицы видно, что физико-механические показатели полученных битумных композиций выше показателей аналогов вследствие высоких механических характеристик и эластичности, что обеспечивает более высокую долговечность покрытий, возникающих на границе раздела битума и картона, при эксплуатации в условиях минусовых температур и при резких колебаниях температур. Покрытия на основе такой композиции обладают более высокими виброгасящими свойствами, что также важно для увеличения срока службы рубероида. Перечисленные выше эффекты достигнуты без увеличения стоимости материала в сравнении с аналогами.
По данным проведенных экспериментов полученные битумные материалов на основе госсиполовой смолы хорошо сопротивляются действию щелочей с концентрацией до 40 %, фосфорной кислоты до 85 %, а также серной с концентрацией до 50 %, соляной до 25 % в течение одной недели.
Таким образом, полученные научные и практические результаты подтвердили целесообразность, перспективность и необходимость использования госсиполовой смолы — отхода масложировых комбинатов при получении битума пригодного для производства рубероида, что приводит к решению крупной народнохозяйственной задачи. Убедительно доказано, что полученные битумы приводят к увеличению гибкости, пластичности, морозостойкости, пожаробезопасности и срока службы рубероида.
Литература:
- Гун Р. Б. Нефтяные битумы. М., «Химия». 1973. 432 с.
- Патент РУз. № IAP 04550. Битумополимерная композиция на основе госсиполовой смолы и способ ее получения. Жуманиязов М. Ж., Марахимов А. Р., Курамбаев Ш. Р. Узб. Заявлен.15.02.2010. Опубл. 04. 07. 12.
Производство — рубероид — Большая Энциклопедия Нефти и Газа, статья, страница 1
Производство — рубероид
Cтраница 1
Производство рубероида состоит из следующих основных операций: подогрева пропиточной и покровной массы в котлах до температуры 180 — 200 С или окисления в конверторах; подготовки посыпочных материалов; пропитки полотна картона в пропиточной ванне; отжима валками машины излишнего битума; протягивания пропитанного картона через другую ванну с более тугоплавким битумом ( с наполнителем, имеющим температуру размягчения не ниже 85 С по КиШ) для нанесения покровного слоя; посыпки минеральным порошком или другим посыпочным материалом с одной или обеих сторон; охлаждения материала на цилиндрах с водяным или иным охлаждением; окончательного охлаждения в петлях магазина запала; резки ленты на куски стандартной длины и свертывания их в рулоны. Схема рубероидной машины показана на ркс.
[2]
В производстве рубероида вода расходуется в основном на охлаждение холодильных цилиндров, конденсаторов битумоокислительной установки, компрессоров и холодильников в компрессорной, подающих воздух на окисление битума. [3]
Основные технологические процессы производства рубероида следующие. [4]
Строительные битумы применяются в производстве рубероида и толя, при изготовлении изоляционных покрытий для трубопроводов и для защиты сооружений от грунтовых вод и сырости. Они выпускаются в твердом виде и отличаются между собой по твердости, температуре размягчения и другим показателям. [5]
В настоящее время снижается объем производства рубероида, и его заменяют новыми рулонными материалами — наплавляемыми битумно-полимерными и комбинированными. В них в качестве основы используются стеклохолсты, стеклоткани, нетканые синтетические и другие материалы. При использовании битумов они модифицируются полимерными веществами. Расширяется производство и безосновных рулонных материалов с применением в них кроме битума бутилкаучука и некоторых других полимеров.
[6]
Основные требования к битумам, используемым в производстве рубероида и пергамина, — высокие погодостойкоеть и пластичность пои низких температурах. [7]
Применение биостойкого гудрокама в качестве пропиточного и покровного материала в производстве рубероида на рубероидных заводах позволяет получить рулонный гидроизоляционный материал, не подверженный гнилостным процессам. Прочность на разрыв рубероида на гудрокаме значительно выше, чем у рубероида на нефтебитуме вследствие того, что гудрокам при нормальной температуре более прочно склеивает волокна кровельного бумажного картона.
[8]
Битум БН-VK применяют в кровельном деле как покровный слой на картоне при производстве рубероида. [9]
Битум БНК-5 применяют в кровельном деле, как покровный слой на картоне при производстве рубероида, как гидроизоляционный материал с различного рода наполнителями, как теплоизоляционный и звукоизоляционный материалы при различном строительстве. [10]
На основе химических продуктов переработки ПКГ в РФ выпускается свыше 200 наименований продукции, в том числе, полимерные материалы, минеральные удобрения, химические средства защиты растений, растворители и др. Остающиеся при переработке фракций КУС масла используются в производстве рубероида, асфальта, для пропитки деревянных конструкций. На основе пека получают угольные электроды и анодные массы.
[12]
Основными отечественными мягкими кровельными материалами, изготовляемыми с применением битума, являются рубероид и пергамин. Технология производства рубероида состоит в следующем: специальные виды картона пропитывают мягким битумом и пропитанный картон покрывают с одной или двух сторон тугоплавким окисленным битумом. [13]
Для повышения водонепроницаемости лист и швы дополнительно промазывают битумом. При производстве рубероида, для которого требуется поддержание заданной температуры расплава, и сооружении одно — или многослойной кровли следует использовать нагревательные устройства, работающие на СНГ. [14]
На заводах картоно-рубероидного производства сточные воды поступают от охлаждения подшипников, от холодильников и компрессоров, картоноделательных машин, охлаждения дымососов, продувки котлов и водоочистки. На заводах по производству рубероида на привозном картоне сточные воды поступают от тех же операций, кроме того, они поступают от холодильников окислительной установки, обогрева паром оборудования главного корпуса и обогрева складов пропиточной массы и антраценового масла.
[15]
Страницы: 1 2
Производство и Характеристики- Обзор +Видео
Частая ошибка начинающих кровельных мастеров — это неверные подготовительные работы на поверхности под гидроизоляционный материал.
Существуют ошибочные мнения о том, что нет необходимости укладывать подкладочные виды рубероида, а достаточным будет укладка двух слоев мастичной массы или расплавленного битума, а затем уже основной рубероид. Это чаще применяется для крыши с маленьким уклоном до 10-12 градусов и доживает только до первых жарких дней либо больших морозов.
Подкладочный рубероид как и пергамент важен, но он намного толще и прочнее, его покрытие многослойное и устойчивое к атмосферным явлениям. Он может быть использован и как самостоятельный кровельная основа достаточно длительный срок. В этой статье мы поговорим о материале — рубероид рпп 300.
Рубероид рпп 300 является подкладочным гидроизоляционным материалом, имеющим двустороннюю пылевидную посыпку, обладающим гибкостью и легкостью при применении. Он применяется в качестве подкладочного материала при укладывании мягкой кровли.
Изготовление рубероида
Для производства рубероида за основу берется плотный картон, который пропитывают с помощью битума. Внутренний слой битума мягкий, имеющий температуру смягчения до пятидесяти градусов Цельсия. Далее следует нанесение наружного битумного слоя, имеющего температуру плавления не менее восьмидесяти градусов.
Рубероид, используемый в качестве подкладочного материала, обсыпают пылеобразной посыпкой. А наружные виды посыпаются с наружней стороны более крупной крошкой.
Маркировка
Разные разновидности рубероида, производимые по ГОСТ в соответствии со строгим регламентом, имеют специальную буквенную маркировку. С помощью этих символов любой покупать может определиться с основными параметрами продукта.
Первым символом обозначается название материала, т. е. Р — рубероид. Вторым указывается на тип использования(К -кровельный, П -подкладочный). Третьим обозначается посыпка (К-крупнозернистая, П-пылевидная, М-мелкозернистая, Ч-чешуйчатая). Цифры в конце — это значение показателя плотности картона, измеряемый в г/м2.
Значение рубероида РПП-300
Подкладочный рубероид является самым недорогим, надежным и легким в укладке материалом при отделке крыши.
рпп300 выполняет несколько основных функций, таких как:
Функции:
- Сцепляетсяс бетонным основанием намного лучше, чем обычная битумная мастика
- Припроизводстве рпп 300 картон частично насыщают битумом.
Клей, битумы или мастичная масса при длительном нахождении на солнце способны к потере некоторых компонентов, и в итоге крошатся. Так, как в картоне имеются смягчители, покров не только меньше портится, но и становится более стойким к морозам; - Данныйподкладочный материал совместно с основным способны создать достаточно надежное покрытие.
К сведению: В районах, где преобладают очень низкие температуры, преимущественно используется специальная морозостойкая марка рпм 300.
Технические характеристики
Рубероид рпп 300 выпускается от двух с половиной до трех миллиметров толщиной. Толщина зависит от вида посыпки. Например, молотый песок либо тальк, нанесение может быть быть как с одной стороны, так и с обеих.
В основном такой рубероид считается самым не дорогим, используемым как расходный материал. Им и бронируется опалубка фундамента, и изолируют плиты под балкон, а также он очень хорошо горит, моментально вспыхивая.
По сравнению с аналогичными материалами для отделки кровли , имеющие бумажную основу, рубероид рпп 300 обладает следующими характериатиками:
- Тонкий менее прочный, в среднем на тридцать процентов хуже других марок;
- По влагостойкости битумного слоя не уступает наружным маркам;
- Нетеряет свою гибкость и мягкость значительно дольше аналогов. Это происходит за счет его производства из мягкого пористого картона, что способствует большему пропитыванию основы.
Он универсален как строительный, подкладочный и изоляционный материал. Его часто используют в обмотке коммуникационных труб из-за хороших гидроизоляционных свойств с целью экономии.
Подкладочный рпп является основой для изготовления практически всей листовой гидроизоляции при внутренних строительных работах домов, однако это не очень хорошо. Все же при строительстве жилого дома нужно пользоваться стеклотканевой гидроизоляцией. Так как более легкий сорт очищенного битума достаточно дорогостоящий, а неочищенные пропитанные битумом материалы содержат много продуктов его разложения такие, как бензол и толуол. Но определить какую же пропитку использовали на предприятии сложно даже с имеющимися сертификатами.
Некачественный рпп возможно различить, на срезе будет видно неравномерное окрашивание и он жестче и тверже. Однако, действительную гибкость можно определить при температуре ни ниже пяти градусов. При сгибании под углом до тридцати миллиметров цвет не должен меняться, как и не должны происходить изломы и трещины.
Укладывание рубероида
Перед укладыванием рпп поверхность кровли очищается.
Основным правилом при укладке рубероида любого типа является то, что после наклейки полотен, на них нельзя наступать хотя бы 15 минут.
На заметку: Чем меньше мастичный слой, тем сцепление с основанием будет качественнее.
Слишком толстые слои клеящего материала могут усыхать со временем и растрескиваться, что приведет к проникновению влаги. Поэтому тонкий слой клеевой основы будут значительно долговечнее и прочнее.
Наклеивание подкладочного рубероида по принципу не имеет отличий от укладывания верхнего слоя. Для большей мягкости и гибкости, перед укладыванием, рубероид следует расстелить на солнце. Как правило, рулон раскатывается после промазанных нескольких метров основания крыши, но если погода жаркая, то поверхность просто можно залить расплавленной битумной мастикой и последовательно раскатывать рулоны. Стыки подчищаются от клеящего материала, а швы проходят валиком.
Компания ООО «ТД МКМ Север» реализует рубероид собственного производства.
Рубероид (МПК КРЗ) РПП, РКП, РКК — рулонный кровельный и гидроизоляционный материал, изготовляемый пропиткой кровельного картона легкоплавкими нефтяными битумами, с последующим покрытием его (с обеих сторон) слоем тугоплавкого битума и защитной посыпкой асбестом, тальком и т. п. Производится по ТУ. Имеет возможность применения при любых уклонах и формах кровли. |
Характеристики
Рубероид РКП-350, РКП-350 — традиционный мягкий кровельный рулонный материал. Применяется для верхнего и нижнего слоев кровельного ковра, для рулонной гидроизоляции строительных конструкций.
Рубероид РПП-300. Рубероид подкладочный с пылевидной посыпкой. Применяется для нижних слоев кровельного ковра. Посыпка из песка не наносится.
Укладка рубероида
Мягкие рулонные кровельные материалы следует укладывать на чистую и сухую основу, потому делать это лучше в хорошую погоду. Перед укладкой рубероид разматывают и выдерживают в таком виде около суток. Если для кровли выбран обычный рубероид на картонной основе, то специалисты советуют укладывать его не менее чем в четыре слоя. К тому же таким рубероидом желательно покрывать только плоскую крышу без изгибов. Для внутренних слоев кровельного «ковра» подходит рубероид с более гладкой поверхностью, а вот на самом верху обязательно должен быть материал с крупной посыпкой. Если нижняя часть рубероида покрыта мелкозернистой посыпкой или полиэтиленовой пленкой, то для наклейки рубероидного «ковра» обычно применяют особые битумные мастики.
Различают «горячую» и «холодную» технологии нанесения мастики. До недавних пор использовался главным образом «дедовский» метод, когда мастику надо было предварительно разогревать. Теперь ее можно приобрести уже готовую к применению. Работы по устройству рулонной кровли начинают с огрунтовки настила. Грунтовку можно приготовить, растворив битум в бензине или керосине. Но, чтобы не тратить лишнее время, готовую грунтовку лучше просто купить. После высыхания огрунтованного настила на него наносят мастику и наклеивают рубероид. Полотнища накладываются с напуском 70-100 мм. В последних слоях полосы смещают на треть ширины. По окончании наклейки последний пласт покрывают слоем мастики толщиной 3-5 мм и посыпают крупным песком или мелким гравием, утапливая его в мастику.
Показатели пожарной опасности РУБЕРОИД РКП-350, РУБЕРОИД РКК-350, РУБЕРОИД РПП-300
Группа горючести Г4 по ГОСТ 30244
Группа воспламеняемости 83 по ГОСТ 30402
Производство рубероида | Азбука строительства и ремонта
В настоящее время существует много различных кровельных покрытий, но, пожалуй, самым распространенным был и остается рубероид. Что же такое рубероид? Это гидроизоляционный и кровельный материал, при изготовлении которого используют пропитку картона мягкими легкоплавкими нефтяными битумами, обе стороны которого покрывают тальком, асбестом или схожим материалом.
Существует несколько видов рубероида: еврорубероид, рубемаст, стеклорубероид, толь.
В основе изготовления еврорубероида лежит стекловолокно, так называемая стеклоткань или синтетическая основа, более известная, как полиэстер. На основу наносится покровный слой, который состоит из смеси битума и полимерных добавок, от 2 до 5 кг на 1 кв.м. Срок службы еврорубероида сравнительно большой, это обусловлено высокими качественными показателями. Еврорубероид наносится методом наплавления.
Рубемаст, как и еврорубероид, наносится методом наплавления и в его основе лежит кровельный картон, с повышенным содержанием вяжущего битума с нижней стороны полотна. Это позволяет рубемасту иметь улучшенную пластичность и более высокую стойкость к образованию трещин, тем самым увеличивая срок службы кровли. Способ укладки рубемаста – термическое подплавление нижнего покровного слоя, либо метод пластификации растворителями.
Стеклорубероид имеет те же характеристики и принципы, что и рубемаст, но роль основы этого вида играет стеклоткань.
Толь имеет простые характеристики в изготовлении. Это, по сути, картон, который пропитан каменноугольным, либо сланцевым дегтевым продуктом с минеральной посыпкой с каждой из сторон.
У нас в России производят следующие виды рубероидов: РКП-300, РКП-350; РКП-350У; РПП-300; РКК-400, П300, П350.
Для гидроизоляции при строительстве, а также для верхнего и нижнего слоев кровли применяют РКП-300 и РКП-350. Для рубероида РКП-350У характерно то, что он при желании потребителя может быть изготовлен с увеличением массы покровного состава (1.500-2.000 г/кв.м.).
Для нижних слоев кровельного ковра применяется РПП-300. Это подкладочный материал с пылевидной посыпкой. Наличие песка в посыпке отсутствует. Рубероид РКК-400 – кровельный материал, применяющийся для верхних слоев кровельного ковра. В его изготовлении применяется крупнозернистая посыпка.
Для нижних слоев кровельного ковра и для пароизоляции, используют кровельный пергамин П300, П350, который получается благодаря пропитке кровельного картона нефтяными битумами. Это беспокровный рулонный материал, который к тому же нередко используется и для упаковки оборудования.
Для изготовления рубероида используют специальное оборудование – линию для производства рубероида. Технология изготовления этого материала выглядит следующим образом. В специально пропитывающей ванне находится легко-плавный нефтяной битум, с температурой размягчения 34-50 гр. Основу будущего рубероида протягивают через эту ванну, где она тщательно пропитывается. После пропитки основа поступает в покровную, где с обеих сторон покрывается более твердоплавким кровельным битумом. В заключении, на внешний слой наносится посыпка. Рубероид готов!
Читайте также:
Обзор методов производства кровельных материалов для жилых помещений (Технический отчет)
Акбари, Хашем, Левинсон, Роннен и Бердал, Пол.
Обзор методов производства кровельных материалов для жилых помещений . США: Н. П., 2003.
Интернет. DOI: 10,2172 / 860887.
Акбари, Хашем, Левинсон, Роннен и Бердал, Пол. Обзор методов производства кровельных материалов для жилых помещений . Соединенные Штаты. https://doi.org/10.2172/860887
Акбари, Хашем, Левинсон, Роннен и Бердал, Пол. Солнце .
«Обзор методов производства кровельных материалов для жилых помещений». Соединенные Штаты. https://doi.org/10.2172/860887. https://www.osti.gov/servlets/purl/860887.
@article {osti_860887,
title = {Обзор методов производства кровельных материалов для жилых домов},
author = {Акбари, Хашем и Левинсон, Роннен и Бердал, Пол},
abstractNote = {Битумная черепица, черепица и металлические изделия составляют более 80% (по площади крыши) кровельного рынка Калифорнии (54-58% черепицы из стекловолокна, 8-10% бетонной черепицы, 8-10% глиняной черепицы, 7% металла, 3% древесной смеси и 3% шифера). В климатических условиях со значительным спросом на охлаждающую энергию увеличение коэффициента отражения солнечного света от крыши снижает потребление энергии в зданиях с механическим охлаждением и улучшает комфорт жителей в зданиях без кондиционирования. В этом отчете рассматриваются методы производства черепицы из стекловолокна, бетонной черепицы, глиняной черепицы и металлической кровли. В отчете также обсуждаются инновационные методы увеличения коэффициента отражения солнечного света этими кровельными материалами. Мы сосредоточились на этих четырех кровельных продуктах, потому что они обычно окрашены пигментными покрытиями или добавками.Лучшее понимание текущих практик производства цветных кровельных материалов позволило бы нам творчески и более эффективно разрабатывать холодные цветные материалы.},
doi = {10.2172 / 860887},
url = {https://www.osti.gov/biblio/860887},
журнал = {},
номер =,
объем =,
place = {United States},
год = {2003},
месяц = {6}
}
Процесс производства кровельной черепицы: основное объяснение
Процесс производства кровельной черепицы:
Наша группа экспертов здесь, в American Standard Roofing, решила поговорить о производственном процессе, через который проходит кровельная черепица. Как профессиональные подрядчики, выполняющие много кровельных работ, мы хотим, чтобы наши читатели и клиенты знали основы производства черепицы.
Основы кровельной черепицы:
Существует два разных типа битумной черепицы: на органической основе и на основе стекловолокна. В последние годы у многих производителей черепицы возникли проблемы с ранней порчей черепицы на органической основе, поэтому большинство продуктов, которые вы можете купить сейчас, изготавливаются на основе стекловолокна. У нас есть много изделий на основе стекловолокна.
- Битумная черепица для органической черепицы: битумная черепица на органической основе начинается с мата (также известного как основа) из целлюлозных волокон, таких как переработанная бумага или дерево. Волокна смешивают с водой, чтобы получить целлюлозу, сушат в листы, а затем наматывают на длинный рулон. Затем он проходит через резервуар, заполненный асфальтом, так что войлок покрывается слоем асфальта и минеральных гранул с керамическим покрытием.
- Битумная черепица для черепицы из стекловолокна: черепица на основе стекловолокна немного отличается тем, что мат состоит из стекловолокна.Затем этот мат покрывается слоем асфальта и гранул, как и на органической основе. Они легче органической черепицы и обладают большей огнестойкостью.
Добавление гранул:
Гранулы, которые приклеиваются к черепице, служат нескольким целям. Они защищают крышу от УФ-лучей, повышают огнестойкость и придают цвет черепице. Для повышения устойчивости к водорослям и пятнам их часто смешивают с медью.
Кровельная черепица Упаковка:
Последний шаг — упаковка.После того, как маты покрыты асфальтом и гранулами, их разрезают и сортируют в связки. После тестирования эти комплекты упаковываются, маркируются и отправляются в ближайший к вам склад.
Мы готовы удовлетворить все Ваши потребности в кровельной черепице!
Мы — сертифицированные и лицензированные кровельные подрядчики. Мы знаем предысторию каждого кровельного материала, который мы используем. У нас также более 36 лет опыта работы в отрасли. За этим стоит компания American Standard Roofing. Наша репутация важна для нас.Мы также поддерживаем наши услуги на протяжении всего срока службы продукта, как трудовые, так и материальные. Вот почему мы — кровельщики метро Детройта №1. Обязательно позвоните нам по телефону (248) 350-2323 для всех ваших потребностей в кровле, сайдинге и водоотводе.
Наш производственный процесс | Металлические кровельные системы Classic
Главная »О нас» Наш производственный процесс
Шаги к созданию вашей классической крыши
Красота и экологичность металлической кровли Classic — это результат нашего узкоспециализированного и запатентованного производственного процесса.Глубокие линии и аутентичные канавки классической металлической черепичной крыши создаются, когда алюминиевая катушка со специальным покрытием проходит через серию штампов в крупноформатном высокотоннажном штамповочном прессе, аналогичном тому, который использовался для изготовления кузова автомобиля. водить машину. Наш производственный процесс отличается точностью и уникальностью. Многим нашим клиентам нравится знать, как это работает, поэтому, помимо видеоролика с экскурсией по фабрике, здесь рассказывается, как производится ваша классическая крыша.
Наш алюминий
Использованный алюминий, включая банки для напитков и другие предметы, собирают для переработки и отправляют на алюминиевый завод, где очищают, плавят и формуют в гигантские металлические плиты.Затем он скатывается в рулоны алюминия, чтобы удовлетворить наши требования к толщине и ширине. На комбинате каждая сляб и рулон металла изготавливаются в соответствии с нашими стандартами. Каждой катушке присвоен кодовый номер, который указывает, когда и как она была изготовлена.
Наши покрытия
Рулоны алюминия затем направляются в установку для нанесения покрытий, где применяется наша усовершенствованная система покрытия Kynar 500 или Hylar 5000. Металл без покрытия помещается на линию непрерывного нанесения покрытия, где он очищается и специально обрабатывается для приема краски перед нанесением и пропеканием многослойной системы. В конце каждого цикла окраски проверяется цвет и качество покрытия, чтобы убедиться, что они соответствуют нашим стандартам качества.
Гарантия качества
После того, как алюминий с покрытием поступает на наши производственные предприятия в Огайо или Техасе, мы снова проверяем его качество, цвет и прочность. Катушки не отправляются на наш производственный цех, пока они не пройдут повторные проверки качества одним из наших инженеров по обеспечению качества. Мы знаем, что условия на вашей крыше могут быть ужасными. Используемый металл должен соответствовать нашим ведущим отраслевым стандартам.Установленные нами стандарты были определены процедурами ASTM, Ассоциацией металлических конструкций (MCA), Национальной ассоциацией по нанесению покрытий на катушку и нашей командой инженеров. Мы — одна из четырех компаний, производящих продукцию, соответствующую программе сертифицированных металлических кровельных панелей, проводимой MCA.
Наш производственный процесс
После того, как рулон алюминия поступает в производство, он проходит через один из наших крупноформатных высокотоннажных штамповочных прессов. Каждый пресс содержит серию штампов, которые придают металлу определяющую форму и характер.По мере прохождения черепицы через каждую матрицу (от пяти до восьми в зависимости от продукта) внешний вид черепицы создается с возрастающей степенью сложности. Инструменты и процессы, которые мы используем, являются одними из самых сложных в металлообрабатывающей промышленности. Наши операторы тщательно контролируют прессы от 350 до 1500 тонн, чтобы гарантировать аутентичный внешний вид нашей кровельной системы. Каждая черепица немедленно проверяется на качество системы запирания, а также на цвет, внешний вид и целостность.После прохождения проверки черепица тщательно упаковывается, чтобы обеспечить безопасную транспортировку, чтобы ее можно было установить на вашей крыше, чтобы сохранить красоту и защиту на всю жизнь!
Наша постобработка
Весь наш машинный лом тщательно собирается, упаковывается и продается обратно на алюминиевый завод, чтобы его можно было переработать в новые рулоны металла для окраски, испытаний и изготовления алюминиевой кровли, продолжая цикл переработки.
(PDF) Разработка экологически безопасных кровельных материалов из отходов
1
Разработка экологически безопасных кровельных материалов из отходов
U.D.G.U.C Udagama, A. K. Kulatunga
Аннотация: — Кровельные материалы — один из важнейших строительных материалов любого здания. За
века кровельные материалы были заменены с возобновляемых кровельных материалов с низким сроком службы, таких как
, как плетеный кокосовый лист, лист пальмиры, рисовой соломы и т. Д., На кровельные материалы с более длительным сроком службы, такие как глина
черепица, листы из цементного волокна (асбест) и оцинкованные или оцинкованные металлические листы. Из-за более длительного срока службы и легкости
, а также эстетики почти во всех домах даже в сельской местности Шри-Ланки используются современные материалы, а кровельные листы из асбеста
и глиняная черепица являются наиболее популярными и распространенными методами кровли в
Шри-Ланке. При переходе от традиционных экологически чистых кровельных материалов к современным кровельным материалам
, воздействие на окружающую среду также возрастает из-за обширных требований к обработке до
, повышая долговечность и производительность и т. Д. Было обнаружено, что некоторые распространенные типы кровельных материалов
, такие как цементные асбестовые волокна, армированные и покрытые металлическими листами и т. д., оказывают значительное воздействие на окружающую среду
не только во время производства, но и на этапах использования и утилизации.И наоборот,
— это множество отходов, образующихся в результате различных процессов, которые можно заменить цементом
и кровельными материалами на основе глины. Важность этого вида кровельных материалов будет высока, особенно
, поскольку современная среда строительства постепенно движется в сторону устойчивости или концепции зеленого строительства
. Поэтому в данном исследовании основное внимание уделяется разработке экологически безопасного кровельного материала с использованием
различных отходов, таких как тканевые отходы, кокосовое волокно, полимерные материалы и человеческие волосы в качестве армированного материала
. Было проведено несколько экспериментов с использованием лабораторных форм и механизмов прессования
, и текущие результаты показывают, что тип армированного материала обеспечивает более высокий изгиб
и сжимающие напряжения.
Ключевые слова: кровельные материалы, отходы, устойчивая застроенная среда, экологичное производство
и воздействие на окружающую среду
1. Введение
Кровельные материалы являются одними из важных строительных материалов
.
помимо основной функции кровельного материала
ожидали безопасности, красоты конструкции, легкости и прочности
. Глиняная черепица и асбестовый цементный лист
являются в основном используемым кровельным материалом
на Шри-Ланке. Учитывая вышеупомянутые материалы
, глиняная черепица имеет относительно
стоимость и не является легким. Асбестовое волокно
является наиболее опасным материалом, который используется для производства
листов асбестоцемента. Когда
вдыхает воздух, содержащий волокна асбеста,
может привести к заболеваниям, связанным с асбестом. Это
, в основном, рака грудной клетки и легких, и
не являются лекарством от этих болезней. Обычно между первым воздействием
волокон асбеста и постановкой диагноза болезни проходит длительный промежуток времени
.
Из-за такого рода факторов развитые страны
уже отказываются от асбестоцементного листа.
Недавно развитые страны разработали
менее вредных для окружающей среды, легких, красочных
и хороших функциональных кровельных материалов, которые являются
хорошими для безопасности и здоровья человека.Некоторые из
из них — это бамбуковая черепица, цементные кровельные листы
, сделанные из цемента, древесной массы, кварцевого песка,
кровельная черепица из дерева и кровельная черепица из глины
. Но только несколько исследований
было проведено для разработки этого вида кровельного материала в
Шри-Ланке. С другой стороны, в Шри-Ланке чаще всего используется кровельный материал
— это асбестоцементный лист
, который влияет на безопасность человека и
здоровья.Это основная причина, по которой
проводят исследования такого рода, и ожидается, что
разработает экологически безопасный кровельный материал с использованием
отходов с хорошими свойствами и на
меньшего воздействия на безопасность и здоровье человека. Это
сократит количество отходов и поможет управлять отходами
. В Шри-Ланке
швейных фабрик, которые ежедневно производят большое количество отходов ткани в размере
.Ткань
может использоваться как армированный материал вместе с кокосовым волокном
. Кроме того, многие натуральные волокна и синтетические волокна
также могут использоваться в качестве армированного материала
. В Шри-Ланке большинство вышеуказанных материалов
можно найти как отходы. Таким образом, данное исследование
направлено на выявление различных армирующих материалов
из обрабатывающих производств и
Взгляд в прошлое на подъем кровельной промышленности
Это
сообщение является частью ежемесячного
серия, в которой исследуются исторические применения строительных материалов и
системы, используя ресурсы из Библиотеки наследия строительных технологий (BTHL),
онлайн-коллекция каталогов, брошюр, коммерческих публикаций и многого другого. BTHL — это проект Ассоциации технологий сохранения,
международная организация по сохранению зданий. Подробнее про архив здесь.
Роль крыши трудно переоценить. Он защищает внутренние помещения здания и его жителей от сил природы, защищает жизненно важные инженерные системы и помогает определить внешний вид здания.
эстетический. Необходимость крыши привела к ее повсеместному распространению и, благодаря
расширение, способствовало развитию сильного рынка кровельных материалов с различными эксплуатационными и физическими характеристиками.
Те
материалы имеют долгую историю, и их эволюция во многом определялась характеристиками. Преобладающим выбором кровли были деревянная и шиферная черепица и глиняная черепица.
до середины 19 века, когда металлические и битумные кровельные системы сделали пологими.
возможны приложения. В течение 20 века было разработано несколько новых материалов.
для крыш с низким и крутым уклоном. Среди них была галька асфальта,
который появился на сцене на рубеже 20-го века и продолжает оставаться лучшим кровельным материалом для домов. После периода рыночных экспериментов с различными формами, узорами и текстурами, битумная черепица превратилась в форму с тремя выступами.
популярная сегодня версия.
Композиты, такие как асбест и фиброцемент, конкурируют с асфальт какое-то время, предполагая лучшую производительность при попытке копировать традиционные материалы, такие как сланец или глиняная плитка. Имитация впоследствии стал темой в категории кровли, ранними примерами из которых были металл. черепица, имитирующая внешний вид глиняной плитки, и битумная черепица, имитирующая соломенную черепицу.В 20 веке также появились кровельные материалы. материалы с разным уровнем прочности и огнестойкости, а также внедрение компонентов, связанных с кровлей, таких как желоба, водосточные трубы и гидроизоляция.
В
следующие брошюры, проспекты и журналы из Digital Building
Библиотека технологического наследия исследует эволюцию кровельных систем в
20 век.

H.M. Reynolds Shingle Co. , 1910 год: компания H.M. Компания Reynolds из Гранд-Рапидс, штат Мичиган, в начале 20-го века заявила, что изобрела кровельную черепицу. Это трудно доказать, как и в случае со многими широко распространенными продуктами. Однако рулонный асфальт, покрытый гранулами сланца, был доступен к концу 19 века, так что нетрудно увидеть, как этот материал мог быть использован для изготовления отдельных черепиц вскоре после этого — это также еще более затрудняет определение того, кто именно , сделал это первым.К 1910 году битумная черепица была широко доступна и быстро заменила деревянную черепицу из-за их экономичности и огнестойкости.

Справочник Барретта по кровельным и гидроизоляционным покрытиям для архитекторов, инженеров и строителей , Barrett Manufacturing Co.

Republic Steel Roofing Products , Republic Steel Co., c. 1939: большие стальные кровельные панели были особенно популярны для сельскохозяйственных и промышленных зданий. Гофры позволили панелям перекрывать большие расстояния, что уменьшило объем материала и вес каркаса, а гальваническое покрытие продлило срок службы панелей. Материал, возникший в 19 веке, широко используется и сегодня.
Certigrade Handbook of Red Cedar Shingles , Red Cedar Shingle Bureau, 1957 г .
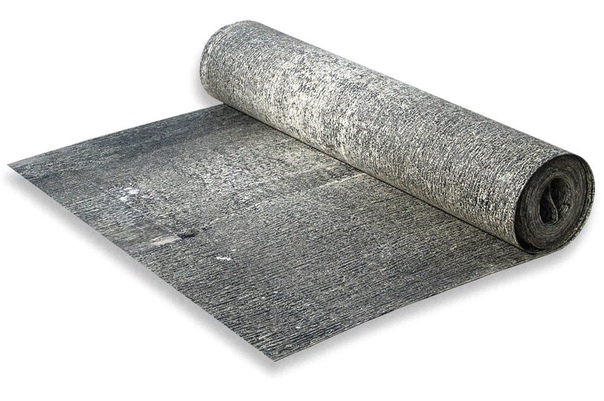
The Book of Roofs , Johns Manville, 1923: Комбинация асбеста и цемента привела к получению фиброцемента, который при применении в качестве кровельной черепицы стал чрезвычайно прочным продуктом, который весит значительно меньше, чем глиняная и шиферная черепица . Фиброцементная черепица, имитирующая вид сланца и глины, была особенно распространена.Одним из популярных вариантов был крупномасштабный гексагональный форм-фактор с характерным узором.
Строительные материалы из листового металла , W. F. Norman Manufacturing Co., 1936: Черепица из штампованного листового металла, имитирующая глиняную черепицу, была популярна в начале 20 века. Компания W. F. Norman Manufacturing Co. из Невады, штат Миссури, была одним из первых производителей этого продукта и до сих пор производит две простые версии металлической черепицы.

Основы асфальтовой кровли
Джо Хобсона
Начав со скромных продаж рулонной кровли в 1893 году, индустрия асфальтовых кровель на протяжении многих лет неуклонно росла до такой степени, что сегодня она широко признана в качестве ведущего поставщика кровельной продукции в стране.Производство асфальтовых кровель оценивается примерно в 12 миллиардов долларов.
Большая часть асфальта в США используется для мощения (87 процентов) или кровли (11 процентов). К продуктам и системам асфальтовой кровли относятся черепица и рулонная кровля, слоистый войлок, системы сборной кровли (BUR), пропитанный войлок, используемый в качестве подложки для черепицы, и модифицированные системы.
Последовали инновации в продукции и кровельных системах. Первая самоуплотняющаяся битумная черепица была представлена в 1953 году.Затем, в 1970-х годах, появилась многослойная или ламинированная черепица.
Разработка битумной черепицы на основе стекловолокна, еще одна инновация 1970-х годов, привела к продукции из битумной черепицы с еще более высокой огнестойкостью. И с годами до настоящего времени битумная черепица является наиболее широко используемым кровельным покрытием для строительства и реконструкции новых домов — она используется в четырех из пяти домов в США.
Марки кровельного покрытия
Основные марки кровельного асфальта:
- Асфальт насыщенного сорта, неокисленный или окисленный асфальт, используемый для изготовления насыщенных войлочных свай, используемых при строительстве систем BUR, органической войлочной черепицы и других кровельных материалов, таких как рулонная кровля;
- Асфальт для покрытий, окисленный асфальт, используемый для производства кровельных материалов для различных кровельных систем, таких как битумная черепица, полимерно-битумная кровля, армирующий и подкладочный войлок, а также рулонный кровельный материал; и
- Асфальт для швабры, окисленный асфальт, который плавится и используется при строительстве систем BUR и модифицированных битумов.
Битумная черепица
Популярная в начале 20 века, удовлетворяет потребность в экономичном огнестойком кровельном покрытии. С годами битумная черепица становится все более популярной как экономичный, пожаробезопасный и эстетичный продукт, сочетающий в себе красоту, долговечность, долговечность и ценность.
«Стандартная» битумная черепица — это квадратная битумная черепица, удлиненная по форме и доступная с одним или тремя выступами. Этот продукт изготовлен из основного мата или органического материала (волокна целлюлозы) или неорганического материала (стекловолокна).Органический мат пропитывают и покрывают асфальтом, а затем покрывают непрозрачными минеральными гранулами с керамическим покрытием.
Процесс пропитывания не требуется для битумной черепицы на основе стекловолокна, для которой требуется только асфальтовое покрытие. Асфальтовое покрытие обеспечивает атмосферостойкость. Минеральные гранулы защищают черепицу от солнечных ультрафиолетовых лучей, придают черепице цвет и дополнительную защиту от огня.
Рулонная кровля
Рулонная кровля, как следует из названия, производится, упаковывается и отправляется в рулонах.Он бывает самых разных размеров и веса. Рулонные кровельные материалы производятся либо с гладкой поверхностью, либо с минеральной поверхностью, последняя содержит минеральные гранулы, встроенные в верхнюю часть листа. Рулонная кровля используется не только в качестве кровельного покрытия, но и в качестве гидроизоляционного материала.
Подложки
Эти изделия состоят из войлока или мата (стекловолокна или полиэстера), который может быть пропитан или покрыт асфальтом, стабилизированного асфальтового покрытия и модифицированного полимером асфальта, неасфальтового полимерного покрытия или комбинации этих материалов.В основном они используются в качестве подложки для битумной черепицы, рулонной кровли и других кровельных материалов. Некоторые из этих видов продукции также можно использовать в качестве обшивочной бумаги.
Сборные кровельные системы
Сборные кровельные материалы были представлены в конце 1800-х годов и остаются самой популярной кровельной системой для коммерческих и промышленных зданий на новых и модернизируемых рынках.
Застроенные кровельные мембраны состоят из слоев битума или холодного клея, которые служат в качестве погодозащитного компонента мембран.Армирующие сваи, такие как органический войлок, лист из стекловолокна и лист из полиэстера, устанавливаются в каждый слой битума или клея холодного нанесения. Битумные мембраны устанавливаются в многослойную конфигурацию с битумом или холодным клеем между слоями или слоями армирования мембран для создания «наростной» мембраны.
Производственный процесс
Производство кровельных изделий из асфальта — это непрерывный процесс, выполняемый на кровельной машине, который начинается с одного конца рулоном материала сердечника и заканчивается на другом конце готовым продуктом. Эта последовательность операций создает продукт поэтапно, добавляя материалы по ходу дела и контролируя их работу. График ниже иллюстрирует последовательность событий.
Преимущества изделий из асфальта
Доминирование изделий из асфальтовой кровли на протяжении многих лет не произошло случайно. Он основан на проверенных характеристиках продукта, которые выходят за рамки основных требований к кровле и обеспечивают покрытие, защищающее жителей здания от погодных условий.По характеристикам асфальтобетонных покрытий, завоевавших лидирующую позицию, можно выделить следующие:
- Устойчивость к погодным условиям. Кровельные материалы из асфальта доказали свою устойчивость к солнечному свету, жаре, холоду, воде и льду.
- Огнестойкость. Кровельные изделия из асфальта производятся в соответствии со стандартами ASTM International и / или Underwriters Laboratories (UL) по огнестойкости.
- Ветровое сопротивление. Кровельные материалы из асфальта соответствуют ветроустойчивым стандартам Underwriters Laboratories.
- Экономика. Эффективное крупносерийное производство плюс относительно низкая стоимость применения приводят к экономии, которую сложно сопоставить с конкурирующими кровельными материалами. Умеренные затраты на установку в сочетании с длительным сроком службы обеспечивают очень низкие годовые затраты или затраты за весь срок службы асфальтобетонных кровельных материалов.
- Простота применения. Кровельное покрытие из асфальта считается самым простым в применении из всех стандартных кровельных материалов.
- Адаптивность. Благодаря своей гибкости и прочности, асфальтовые кровельные материалы могут применяться на кровлях самых разных типов.
- Эстетика. Кровельное покрытие из асфальта доступно во многих привлекательных цветах, формах и глубине размеров, что придает крышам выразительный вид.
Широкий ассортимент асфальтовых кровельных материалов, представленный в последние годы, предлагает гораздо большую гибкость при выборе внешнего вида здания, чем это доступно с большинством других типов кровельных материалов.
- Соответствие стиля. Кровельное покрытие из асфальта идеально подходит для большинства архитектурных стилей, будь то современные, современные или традиционные.
- Низкие эксплуатационные расходы. Правильно подобранные и нанесенные кровельные материалы из асфальта практически не требуют ухода, а в случае повреждения легко отремонтируют.
Джо Хобсон — директор по коммуникациям и обслуживанию членов Ассоциации производителей асфальтовых кровель (ARMA). |
ARMA — это североамериканская торговая ассоциация, представляющая производителей и поставщиков кровельных материалов из битумной черепицы для жилых и коммерческих помещений и из органического асфальта, рулонных кровель, сборных кровельных систем и модифицированных битумных кровельных систем. Для получения дополнительной информации свяжитесь с ARMA или посетите сайт www.asphaltroofing.org.
Краткая история производства и использования кровельной плитки
Вулси Гранат Вустер
Эдвард Ортон-младший, Соавтор и редактор
1910
Общие
Происхождение кровельной черепицы окутано неизвестностью. Однако его можно проследить за несколько веков до Рождества Христова. В начале своей карьеры он, несомненно, жил в таких пещерах и естественных убежищах, какие есть в горной стране, но по мере того, как он мигрировал с места на место, могло случиться так, что естественные укрытия не всегда можно было найти. Побуждение и предложение для него построить временные пещеры или убежища из плит и кусков камня были бы совершенно естественными и, несомненно, повторялись много раз в разных местах и у разных народов в развитии человеческого рода.Эти ранние дома, без сомнения, были покрыты каким-то соломенным или каменным кровельным материалом; в горных странах, естественно, можно было бы попробовать плоские камни. Опыт, несомненно, вскоре научил этих первых строителей домов ценить наклонную крышу над плоской для защиты от дождя.
Согласно Морзе, 1 на древность покатой крыши намекают находки гробниц в виде хижин и, следовательно, известных как хижины-урны. Они были найдены в Италии, Саксонии и других частях южной Европы.Считается, что они были созданы до эпохи железа.
Скошенная крыша должна была предшествовать черепице на много веков. Вначале использовались кора, солома, солома, необработанные камни и подобные материалы, пока не были созданы более совершенные устройства, которые, наконец, привели к созданию черепицы из терракоты. Самый старый из известных видов глиняной черепицы, безусловно, является наиболее распространенной формой, используемой в настоящее время в мире.
Большинство природных камней крошатся, а металлы окисляются или ржавеют, но изделия из твердой обожженной глины почти не подвержены влиянию гниения.Таким образом, часто терракотовая черепица является единственной сохранившейся реликвией доисторического строения. Непреходящая природа этих объектов может в конечном итоге позволить нам проследить пути, по которым следуют расы плиточников в их различных миграциях.
Хотя фактическое происхождение кровельной черепицы неизвестно, вполне вероятно, что ее использование было известно очень рано в Малой Азии и, конечно, очень рано в Китае. Исходя из высокого мастерства гончаров и большой древности художественного искусства в Китае, а также использования художественной черепицы в этой стране в зданиях, возведенных несколько веков назад, можно легко предположить, что именно в Китае использование кровельной черепицы.
Гребер в своих мемуарах «Terra-kotten am Gieson» описывает то, что он считает самой ранней известной терракотовой черепицей. Они были найдены в руинах Храма Геры в Олимпии почти за тысячу лет до Рождества Христова. Эта древняя плитка состояла из двух элементов: широкой нижней части (тегула), слегка изогнутой, и узкой, полуцилиндрической части (имбрекс), которая была помещена в перевернутом положении, чтобы покрыть перевернутые края двух соседних тегул. Хотя плитки из Храма Геры, вероятно, так же стары, как и любые другие достоверные образцы в других местах, не следует предполагать, что греки сразу же возникли из соломенной хижины пастуха диких овец до уровня, указанного этим эффективным. система черепичной кровли.Известно, что истоки других искусств, гончарного дела, обработки металла, ювелирных изделий, скульптур и т. Д., Были заимствованы из более древних цивилизаций в Малой Азии или других местах, и что хотя гений греков вскоре развил все эти искусства самолету, никогда ранее не известному в мире, нельзя приписать их первое открытие.
Рисунок 1 — Плитка из храма Геры.
Среди материалов, которые использовались при строительстве ранних крыш, обработанная мраморная черепица по образцу терракотовой черепицы была изготовлена за 650 лет до нашей эры.
Во всех частях старого мира можно найти плитки или их фрагменты, доказывающие нам, что использование плитки было универсальным в тот или иной период.
Габаритные чертежи 2 (рис. 2) в общих чертах представляют типы и разновидности кровельной черепицы с указанием их возраста и распространения.
Рис. 2 — Дизайн обычной или азиатской плитки. Сверху вниз:
Восток, Древняя Греция и Италия.
Китай и Италия.
Восток, Азия и страны Средиземноморья.
Греция, Италия (Древняя и современная).
Следует понимать, что прошлые и настоящие колонии обычно придерживаются той формы кровельной черепицы, которая используется в их родительских странах. В качестве иллюстрации, 3 плоская черепица, изготовленная в округе Монтгомери, штат Пенсильвания, около 1735 года, прослеживается до старых немецких поселенцев. В Вифлееме, штат Пенсильвания, моравцы занимались изготовлением плитки еще в 1740 году. 4 Плитка, обнаруженная докторомC. C. Abbott 5 на острове Берлингтон, в реке Делавэр, на месте очень старого дома, который, как говорят, был построен в 1668 году Питером Джагоном, ясно указывает на голландского поселенца как на его автора. В Калифорнии и Мексике обычные или полукруглые плитки, используемые в миссиях, были сделаны ранними испанскими завоевателями.
Рисунок 2 — Продолжение. Пан или конструкции Belgic Tile.
Вверху: Англия и Скандинавия.
Два средних: Бельгия, Голландия, Скандинавия, Ява и Япония.
Внизу: Современные, разные страны.
Считается, что черепица, найденная в вышеописанных местах, представляет собой первое применение черепицы в этой стране. Вполне возможно, что некоторые из первых использованных плиток были привезены из дома колонистами из своих стран.
Огайо
Если обратиться к истории производства кровельной черепицы в Огайо, то обнаружилось, что проследить ее развитие не так важно.
На ответвлении Северной железной дороги Цинциннати, примерно в тридцати милях к северо-востоку от Цинциннати, находится причудливая старая деревня Джермантаун, которая, судя по записям, является местом первого производства и использования кровельной черепицы в Огайо.
В 1814 году 6 г-н Филип Гюнкель заложил деревню и назвал ее в честь Джермантауна, пригорода Филадельфии, который до сих пор сохраняет это название. Примерно в это же время мистер Джон Робинсон связался с первыми поселенцами маленького городка и начал производство кирпича из глины, собранной на близлежащем поле. Желая построить себе дом, который превзошел бы дом своих соседей-пионеров, мистер Робинсон сделал глиняную черепицу в количестве, достаточном для покрытия своего дома и конюшни.На рис. 3 очень четко показаны форма и очертания плитки, изготовленной мистером Робинсоном. Эти плитки, несомненно, были сделаны из той же глины и обожжены в тех же печах, что и кирпич, который изготовил мистер Робинсон. Дом давно был разрушен, но старая конюшня выдерживала разрушительное воздействие времени и штормов до 1907 года. Ее снесли, чтобы освободить место для прекрасного здания библиотеки. Фотография, показанная на рисунке 4, была сделана незадолго до начала работ по разрушению старого здания.
На виде конюшни видна крыша в полуразрушенном состоянии не из-за разрушения черепицы или кирпича в конструкции, а из-за гниения деревянных балок и стропил, так что они больше не могли нести свою нагрузку.
Рисунок 3 — Плитка Робинсона, сделанная в Джермантауне, штат Огайо, около 1814 года.
Справа на снимке — угол нового здания библиотеки, на котором видна черепица современного производства. Вряд ли можно было найти более разительный контраст: одна черепица показывает следы времени и примитивные методы производства столетней давности, а другая представляет собой крышу наших дней.
Плитка Робинсона в Джермантауне была, вероятно, единичным случаем и, вероятно, не означает появления этой отрасли, поскольку у нас нет доказательств того, что он производил плитки для других целей, кроме своих собственных.
Безусловно, следующий шаг в производстве кровельной черепицы в Огайо был взят Zoarites, немецкой религиозной сектой, которые поселились в Таскаровас около 1820 г. , и построил город, который они назвали Zoar. Эти люди производили черепицу в гораздо большем масштабе, чем первые усилия мистера Робинсона в Джермантауне, поскольку практически все их здания были облицованы черепицей. Достаточно взглянуть на множество старых крыш, которые все еще можно увидеть стоящими сегодня в Зоаре, чтобы понять, что использование кровельной черепицы не было новостью для жителей Зоара.Они прибыли из страны, где черепица использовалась веками, прежде чем они отплыли, чтобы построить свою Утопию в пустыне, где они могли бы свободно следовать своим собственным убеждениям. Сообщество Зоар распалось примерно после восьмидесяти лет совместного существования, но их честное мастерство и забота оставили здания и крыши, которым хватит на многие десятилетия.
Рис. 4 — Около 1814 года здание покрыто плиткой, изготовленной в Джермантауне, штат Огайо.
Эти плитки Zoar представляют собой гальку с узором, известным как «Бобровый хвост», очертания и стиль которого можно проследить до их родного города, Вюртембурга. Все плитки были сделаны вручную; глину выкапывали на близлежащих полях, волами тащили на плиточные дворы, сбрасывали в ямы, куда добавляли воду и давали глине отстояться до размягчения. После замачивания в течение дня и ночи мужчины топтали глину босыми ногами до тех пор, пока она не была должным образом замешана или вытащена. Затем он был покрыт соломой, утяжелен рельсами или досками, таким образом сохраняя глиняный пластик до тех пор, пока он не понадобится формовщикам. Затем его разложили и вручную отнесли к маленьким верстакам формовщиков.Использовались деревянные формы, предварительно намоченные, а затем посыпанные песком. Сначала формовщик взял кусок глины и скатал его в длинный конусообразный рулон, по форме напоминающий буханку ржаного хлеба. Затем этот рулон глины бросали или с силой ударяли в центр формы, и формовщик, используя предплечье и руку, молотил или манипулировал глиной, пока она полностью не заполнила форму. Затем излишки глины соскребали палкой с прямым концом. Обычно плитка на этом этапе считалась бы готовой, но, наблюдая за плитками, показанными на иллюстрациях, можно увидеть, что на их лицевых сторонах есть желоба или линии, идущие вдоль плитки.
Эти бороздки делались руками рабочих, каждый заканчивая свою плитку линиями, которые казались ему наиболее подходящими.
Рис. 5 — Кровельная черепица, изготовленная сообществом Zoar.
Эти канавки преследовали двоякую цель: во-первых, они нарушали монотонность простой плитки, а во-вторых, они служили средством отвода дождевой воды от боковых швов.
Плитки несли мальчики со скамейки для лепки на стеллажи для сушки или на полы, где их выгружали из форм и оставляли сушиться.Форму отнесли обратно на верстак, где ее сначала окунули в воду, а затем посыпали песком для подготовки к следующей операции.
Обжиг производился в печах с восходящей тягой, аналогичных обжиговым печам с восходящей тягой, используемым производителями мягкого глиняного кирпича в настоящее время.
Эти причудливые люди занимались производством плитки примерно до 1852 года, когда оно было прекращено. Как и в Джермантауне, плитки, изготовленные в Зоаре, не предназначались для коммерческих целей, а просто использовались на мельницах, складских помещениях, магазинах, домах и амбарах сообщества Зоар, составляющих в целом значительное количество построек.
Следующий шаг в развитии производства кровельной черепицы в Огайо и, вероятно, самое раннее создание отрасли на коммерческой основе в Соединенных Штатах, произошел в 1871 году, когда г-н Дж. Б. Хьюз из Терре-Хот, штат Индиана, получил писем о выдаче патента на кровельную черепицу взаимосвязанной конструкции и, в то же время, на машину для производства такой черепицы.
Рисунок 6 — Старая церковь в Зоаре, штат Огайо.
Одним из первых, кто заинтересовался плиткой Хьюза, был Джон У.Конрад из Зейнсвилля, штат Огайо, который в 1873 году приобрел право на производство плитки Hughes. Осенью того же года г-н Конраде открыл небольшой завод, а следующей зимой продолжил производство плитки. Однако крыши не были покрыты до весны 1874 года, когда из этой черепицы была построена резиденция г-на А. Х. Уоттса в Зейнсвилле. Фабрика Conrade проработала недолго.
Вскоре после запуска завода Conrade в Зейнсвилле г.Эдвин Беннетт из Балтимора, штат Мэриленд, начал производство кровельной черепицы. Вначале завод Bennett также работал по патентам Hughes. Мистер Беннет, без сомнения, был вторым человеком в этой стране, который занялся производством кровельной черепицы в промышленных масштабах. Его завод был открыт в 1876 году и продолжал работать до лета 1908 года, когда из-за смерти г-на Беннета работа была остановлена, и с тех пор он был демонтирован.
Прибыв в эту страну в 1841 году из Вудвилля, Дербишир, Англия, г.Беннетт 7 присоединился к своему брату Джеймсу Беннетту в Восточном Ливерпуле, штат Огайо, в небольшой гончарной мастерской, которая была начата в 1839 году в тот момент и которая, несомненно, была первой гончарной посудой, построенной в Восточном Ливерпуле, и основанием огромного промышленность, которая там развита.
Рис. 7. Плитка Конрада, взятая из дома Уоттс, Занесвилл, Огайо.
В 1846 году г-н Эдвин Беннет разорвал свои связи в Восточном Ливерпуле и переехал в Балтимор, где основал керамическую посуду, которая успешно работает и сегодня. Но, заинтересовавшись кровельной черепицей в 1876 году, он начал небольшой бизнес. Его вход в эту область был интересен тем, что обозначил линию роста, очень необычную для того времени и до сих пор. Английский гончар, как правило, очень гордится своим ремеслом и соразмерным отвращением относится к другим отраслям производства глины, особенно к кирпичам и черепице, которые он рассматривает как находящиеся в совершенно ином плане, чем его собственный. Но видение г-на Беннета было пророческим, поскольку он видел исключительную важность кровельной черепицы и уверенность в ее использовании в огромных количествах, и он решил применить свои знания о производстве глины в этой новой линии.К сожалению, его усилия были в значительной степени преждевременными, поскольку рынки вообще не были обучены использованию плитки.
Примерно через год, в 1877-78 гг., Мистер Харрис Б. Кэмп в Кайахога-Фолс, штат Огайо, занялся производством укорененной плитки.
У мистера Кэмпа была очень интересная личность. Он владел фабрикой по производству канализационных труб и пустотелых изделий, а также значительным механическим цехом, где он занимался индивидуальной торговлей, а также строил и ремонтировал собственное глиняное оборудование.Он был изобретательным гением высокого уровня, но того редкого типа, который оправдывает его идеи. Он постоянно экспериментировал, редко выполняя одно и то же дважды, даже в случае успеха. Перед смертью он стал очень богатым. Усилия г-на Кэмпа в области производства кровельной черепицы были направлены на изготовление хорошо известного ромбовидного узора, изобретенного Куртуа во Франции до 1856 года. Он проработал в этой отрасли производства глины лишь короткое время, когда продал свои доли Г-н Дж. К. Юарт из Акрона, штат Огайо.
Г-н Юарт взялся за работу с большой верой и энергией и, несомненно, сделал столько же или больше, чем любой другой человек, для продвижения использования кровельной черепицы в Соединенных Штатах. Завод, который он построил в Акроне в конце семидесятых, постепенно укреплялся и в течение многих лет оставался крупнейшим и практически единственным успешным заводом такого рода в этой стране, о чем завод Беннетта никогда не предполагал. больших размеров и не был широко известен в торговле.Успех г-на Юарта в своем бизнесе был полностью обусловлен его энергией и целеустремленностью. Он сделал то, что делал, почти полностью своими силами, очень мало полагаясь на обмен идеями с другими глиняными мастерами. Он решил свои собственные проблемы по-своему, и сделал это еще до того, как обработка глины начала свое современное расширение и контроль по химическим и механическим направлениям. Его методы, и особенно его исключительность, не позволили ему сохранить контроль над бизнесом, который он обеспечил большим трудом.Началась оппозиция, и в конечном итоге его положение стало тяжелым. Он окончательно ушел из бизнеса несколько лет назад, завод перешел в собственность нынешней фирмы, The Akron Vitrified Roofing Tile Co.
Только через несколько лет после запуска завода в Акроне бизнесом по производству кровельной черепицы занялись другие производители по всему штату. Среди них была компания Repp Roofing Tile Co., Нью-Филадельфия, штат Огайо, около 1893 года; Barnard Tile Co. , Беллэр, Огайо, в 1893 году; Zanesville Roofing Tile Co.в Зейнсвилле, штат Огайо, в 1895 году; еще один — в Оттаве, штат Огайо, в 1900 году. Ни один из вышеупомянутых заводов не проработал дольше трех или четырех лет, и ни один не смог создать успешные отрасли. Примерно в то же время т. е., в 1895 году г-н Якоб Фройнд, вдохновленный, как и многие наши граждане Германии, искренней любовью и признательностью, основал завод под названием Cincinnati Roofing Tile and Terra Cotta Co. в Winton Place, недалеко от Цинциннати. хорошей черепичной кровли.
Начав очень скромно, этот завод постепенно строили его основатель и сотрудники.Проблемы производства здесь изучались независимо и решались по-своему, как на заводе в Акроне, и, хотя продукт имел другую форму и дизайн, бизнес постепенно становился успешным. Он был основан на прочном опыте на каждом этапе пути и преуспевал там, где другие растения его возраста терпели неудачу, главным образом потому, что это не было копией какого-либо другого растения, и потому, что оно развивало свои собственные методы.
В 1902 году завод по производству черепицы в Нью-Лексингтоне, штат Огайо, был построен компанией, из которой г.А. В. Браун был президентом. Этот завод на момент своего строительства был спроектирован по широким направлениям, с широкими возможностями для расширения и за свою короткую восьмилетнюю карьеру превратился в следующий по величине, если не самый крупный завод по производству черепицы в России. Соединенные Штаты.
Вслед за заводом в Нью-Лексингтоне в Лиме, штат Огайо, был построен завод National Roofing Tile Co., построенный г-ном А. Б. Клеем, уроженцем Швейцарии. Он родился и вырос в стране, где черепичные крыши на протяжении веков были основным предметом заботы, поэтому было вполне естественно, что господинКлай должен увидеть большие возможности кровельной черепицы в этой стране.
После сбора полевых заметок для этого отчета летом 1908 года в Кантоне была сформирована компания для строительства завода в Спарте, штат Огайо, по производству кровельной черепицы методом сухого прессования.
Другие государства
Учитывая открытие заводов за пределами Огайо, Mitchell Clay Co. 8 в течение 1866 года взяла на себя производство черепицы в Сент-Луисе. Однако они опередили время и примерно через пять лет прекратили производство этой линии товаров.
Другие попытки были предприняты в нескольких точках по всей стране, ни одна из которых не увенчалась успехом до основания компании Celadon Terra Cotta Co. в Альфреде, штат Нью-Йорк, построенной в 1888 году г-ном Гео. Бэбкок. Этот завод был одним из пионеров и непрерывно работал с момента его постройки. В настоящее время это один из заводов, принадлежащих Ludowici Celadon Co., Чикаго, Иллинойс. 9 В 1890 году в Оттаве, штат Иллинойс, был построен завод по производству кровельной черепицы., и известная как Chicago Terra Cotta Roofing and Siding Tile Co., она находилась в ведении различных владельцев около двенадцати лет, а затем была демонтирована.
Примерно в 1893 году в этой стране была основана компания Ludowici Roofing Tile Company, которая построила завод в Чикаго-Хайтс, штат Иллинойс. Это растение стабильно росло с самого начала и до сегодняшнего дня является одним из самых крупных.
Следующими важными заводами были Standard Roofing Tile Company, Сент-Луис, построенная в 1895 году, и Ohio Valley Clay Shingle Company, ныне Huntington Roofing Tile Company из Хантингтона, Западная Вирджиния, построенная в 1899 году.В следующем, 1900 году, компания Ludowici Roofing Tile Company построила завод в Либерти-Сити (ныне Людовичи), штат Джорджия.
Только через три года были построены другие заводы. В течение 1903 года было построено три завода: The United States Roofing Tile Company, Паркерсбург, Западная Вирджиния, The Mound City Roofing Tile Company, Сент-Луис, штат Миссури, и Western Roofing Tile Company, Коффивилль, Канзас. В следующем году или в течение 1904 года компания Murray Roofing Tile Company была построена в Кловерпорте, Кентукки; Следом за этой компанией в 1906 году было здание компании Detroit Roofing Tile Company.
Последней компанией, вышедшей на рынок кровельной черепицы, является New York Roofing Tile Company в Согертисе, штат Нью-Йорк.
Другими компаниями, производящими или производившими кровельную черепицу отдельно или в сочетании с другими изделиями из глины, являются: The Alfred Clay Company, Альфред, Нью-Йорк; Бернс и Рассел, Балтимор, Мэриленд; Golden Press Brick Company, Голден, Колорадо, Los Angeles Pressed Brick Company, Лос-Анджелес, Калифорния; Gladding, McBean & Co., Линкольн, Калифорния; Компания Steiger Terra Cotta & Pottery Co., Южный Сан-Франциско, Калифорния; N. Clark & Sons Co., Аламеда, Калифорния; The Carnegie Brick & Pottery Co., Тесла, Калифорния; The Clay Shingle Company, Монтесума, Индиана; Spillman Brick Company, Спиллман, Западная Вирджиния, и, вероятно, ряд других.
Статус производства за пределами США
Кровельная черепица теперь производится во всех частях света, населенных цивилизованными расами. На Дальнем Востоке мы находим хорошо развитые предприятия в Китае, Японии, Яве, Индии и на островах азиатского побережья.Производство плитки в этих странах, возможно, в настоящее время не так хорошо, как в прошлом, из-за частой замены превосходной плитки, сделанной много лет назад их предками, на современные конструкции.
О китайцах можно сказать, что они превосходят все другие расы в мире в умении использовать кровельную черепицу. Поместья и жилые дома обычно ограничены высокими кирпичными стенами, увенчанными плиткой, и даже в самых распространенных загородных домах есть ворота, покрытые плиткой, в то время как храмы, магазины и все здания лучшего класса покрыты плиткой в целях курс.Более того, Китай, Корея и Япония относились к кровельной черепице так артистично, как никакие другие страны, за исключением Греции и Италии.
Переходя к Персии, Египту и странам, граничащим с южным и восточным побережьями Средиземного моря, мы обнаруживаем, что многие плитки все еще используются, и что они по большей части сохраняют старый нормальный узор.
В Италии, Швейцарии, Испании, Малой Азии, Австрии, Норвегии, Швеции, Бельгии и Голландии есть много тысяч черепичных крыш, но эти страны правильно не называть крупными производителями черепицы.Они не производят много плитки сверх того, что необходимо для домашнего использования. С другой стороны, Германия, Франция и Англия являются крупными производителями плитки. Ежегодно они производят множество квадратов для экспорта в Южную Африку, Южную и Центральную Америку и на острова Вест-Индии. Некоторые плитки производятся в этих последних странах, но их поставки большей частью импортируются. В Маракайбо, Венесуэла, есть два завода по производству плитки: The Eastern Brick and Roofing Tile Co., которая работает последние пятнадцать лет и производит кровельную черепицу с помощью французского ручного пресса, и Western Brick & Плитка Co., используя аналогичное оборудование. Совокупный объем производства этих двух заводов, естественно, невелик, и, следовательно, большая часть спроса должна удовлетворяться за счет импорта.
В Монтевидео, Уругвай, г-н Джон В. О’Хара, консул США, сообщает, что большинство крыш в этой стране плоские, как и полы, вымощены или покрыты плоской черепицей, как английские «карьеры», местные жители называют «Baldosas». Многие тысячи из них используются ежегодно, и он сообщает, что за шесть месяцев было импортировано 2 537 000 штук, в основном из Англии.
Огромный объем бизнеса в этих южных странах ежегодно теряется для Соединенных Штатов, отчасти из-за нехватки заводов по производству кровельной черепицы в этой стране, особенно на наших южных, юго-восточных и юго-западных морских территориях. В настоящее время у нас есть только один завод на этой огромной территории, а именно в Лудовичи, Грузия. Эта ситуация, несомненно, также в значительной степени связана с нашими недостаточными и нерегулярными линиями связи с этими странами. Американские корабли в этих водах встречаются редко, и большая часть американского экспорта на них идет иностранными судами.Другая причина — незнание нашими американскими производителями того, что хотят эти южные соседи, и в целом склонность к нетерпению по поводу их требований к особым формам и стилям. Англичане и немцы обеспечили торговлю, узнав, что требуют обычаи страны, и предоставив их, в то время как американцы в некоторых случаях приняли политику «бери или оставь», которая очень неудачна для обеспечения торговли.
Некоторые плитки производятся на Кубе и в Мексике, но только медленным и примитивным способом, привнесенным испанцами триста лет назад.
В Австралии многие заводы по производству плитки были введены в эксплуатацию английскими, немецкими и французскими поселенцами.
Статус производства в США
Хотя первое производство черепицы в этой стране, как было показано на предыдущих страницах, было не недавним, тем не менее, здесь это относительно новая отрасль. Мы медленно начали использовать кровельную черепицу по нескольким причинам, которые подробно обсуждаются чуть позже. В настоящее время, однако, американская изобретательность в этой области, как и во многих других, восторжествовала над временем и традициями.Несмотря на то, что мы медленно входили в эту область, наш прогресс с момента входа в нее был быстрым, и сегодня американские плитки имеют много точек превосходства, а некоторые — превосходства. Из сырых прессов, привезенных в эту страну из Германии, Англии и Франции, наши изобретатели разработали новое оборудование для кровельной черепицы, которое является мировым лидером по простоте, прочности и производительности. За последние несколько лет было сделано много улучшений в материалах, из которых изготовлены штампы, а также в конструкции штампов, и до сих пор проверенные временем штампы для гипса можно найти лишь на немногих заводах по производству кровельной черепицы.Основным возражением против гипсовых штампов было то, что их нужно обновлять ежедневно из-за быстрого износа мягкой штукатурной поверхности, в результате чего плитка, нанесенная на них, имеет очень грубую и неровную поверхность, которая улавливает пыль и грязь, и скоро представляет что угодно, только не привлекательный вид. Чтобы преодолеть эти возражения, наши производители использовали матрицы, изготовленные из таких материалов, как чугун, сталь, латунь, оружейный металл, алюминий и различные сплавы, и все они используются с большим или меньшим успехом.
Рис. 8 — Карта США, на которой показано распределение заводов по производству кровельной плитки.
За последние тридцать лет мощность заводов по производству черепицы в этой стране выросла с незначительной суммы — с двадцати пяти до пятидесяти квадратов в день, что примерно равно производительности одного среднего завода, — до девятисот или тысячу квадратов в день, если работать полный рабочий день. Другими словами, производительность увеличена с количества плитки в день, достаточного для покрытия одного здания среднего размера, до количества, которое может охватывать, грубо говоря, около двадцати зданий такого же размера.
Из Рисунка 8 видно, что, за двумя исключениями, предприятия расположены в центре. Также можно заметить, что Огайо занимает первое место по количеству заводов, а Западная Вирджиния и Нью-Йорк — второе.
Таблица № 1.
Государство | № Активные растения | № Строительство | Нет. Неактивный |
---|---|---|---|
Огайо | 4 | 1 | 0 |
Западная Вирджиния | 2 | 0 | 0 |
Нью-Йорк | 2 * | 1 | 0 |
Иллинойс | 1 | 0 | 0 |
Мичиган | 1 | 0 | 0 |
Кентукки | 1 | 0 | 0 |
Миссури | 1 | 0 | 1 |
Канзас | 1 | 0 | 0 |
Грузия | 1 | 0 | 0 |
Калифорния | 4 ** | 0 | 0 |
* Один из них связан с кирпичом для сухого прессования.
** Все производится на фабриках, чья продукция охватывает широкий спектр глиняных изделий. Кровельная черепица не является важным элементом ни на одном из этих заводов, хотя и производится на всех.
Огайо, в настоящее время, как всегда в прошлом, лидирует во всех других штатах по производству кровельной черепицы, как уже было показано. Первый коммерческий завод по производству кровельной черепицы в этой стране был построен в Огайо, в Занесвилле в 1873 году, и с момента открытия завода в Занесвилле Огайо никогда не обходился без производства кровельной черепицы где-то в ее границах.Производители из Огайо, как правило, идут в ногу со временем и участвовали во многих тяжелых битвах, неизбежно возникающих при внедрении новой отрасли. Перед лицом более дешевых натуральных кровельных материалов, а также выхода из строя некоторых плохо сделанных черепиц и плохо уложенных черепичных крыш в первые дни производители Огайо постоянно стремились производить больше и более качественной черепицы и доказывать самым требовательным архитектор или строитель, что нет другого кровельного материала, более совершенного, чем хорошо спроектированная и качественно сделанная черепица.
Приблизительно одна треть всей кровельной черепицы, производимой в Соединенных Штатах, сейчас производится в Огайо, и после завершения строительства завода, который сейчас находится в процессе строительства, доля, вероятно, будет несколько увеличена.
Медленное развитие промышленности в Америке
Почему плитка не использовалась более широко в Соединенных Штатах ввиду ее очень широкого применения за рубежом? В прошлом было несколько условий, которые сильно препятствовали развитию отрасли.Некоторые из этих условий все еще существуют в некоторых частях страны. Обсуждение этих условий даст ответ на поставленный вопрос.
Во первых.
Следует учитывать конкуренцию деревянной кровли. Страна относительно молодая, и большая часть ее изначально изобиловала великолепными лесами из древесины, пригодной для использования в качестве гонта. Расчищенная земля была, а на некоторых участках все еще ценится, и любое использование первобытных лесов приветствовалось. Хотя этот излишек древесины навсегда ушел в восточные и центральные части страны, которые еще не начали ощущать дефицит и осознавать ужасную расточительность прошлого, в некоторых частях Северо-Запада это все еще возможно. видеть огромное количество безжалостно сожженных дров, чтобы избавиться от них. Таким образом, в течение многих лет использование крыш, отличных от деревянных плит или черепицы, было очень ограниченным из-за их дешевизны и доступности. Со временем, когда районы превратились в поселки и поселки, произошли катастрофические пожары, которые указали на важность использования некоторых более огнестойких кровельных материалов, поскольку дом с гонтовой крышей составлял уязвимое место нападения при каждом большом пожаре в этом регионе. стране, и в тысячах небольших пожаров.Таким образом, деревянная крыша, хотя все еще широко используется, особенно в новых частях страны, обречена на все более и более быстрое исчезновение под совместным влиянием растущей скудности поставок древесины, короткого срока службы деревянных крыш при благоприятных условиях и их постоянная опасность уничтожения огнем.
Во-вторых.
Конкурс из сланца или натурального камня. Условия, описанные в отношении деревянной крыши, как правило, впервые были выполнены при использовании сланца, природного камня с высокой хрупкостью, который можно легко распилить на блоки подходящего размера и разделить на очень тонкие плиты одинаковой толщины, которые будут стойте для дальнейшей формовки и штамповки в месте использования.
Соединенным Штатам повезло иметь большие природные запасы сланца в широко распространенных местах, и эти карьеры были и всегда будут источником большого богатства для их общин. Но сланец не лишен недостатков, хотя у него много преимуществ, которые всегда позволят ему занять важное место среди кровельных материалов. Он дешев, легко наносится, пожаробезопасен и устойчив к погодным условиям при хорошем качестве. С другой стороны, он тяжелый, он не устойчив к погодным условиям, если он содержит растворимые минералы или легко окисляемые минералы, такие как пирит, или если он недостаточно твердый, т. е.э. тоже шалый. Кроме того, она не очень устойчива к ударам и деформациям, ее нелегко ремонтировать после укладки, потери при транспортировке и использовании довольно высоки, и она делает крышу очень простой, простой и неинтересной. Последняя причина является наиболее важной из них, и если бы не она, внедрение черепицы сделало бы внедрение кровельной черепицы очень медленным и убыточным предприятием. Но шифер работает только в самолетах. Его нелегко приспособить к изогнутым поверхностям, он не имеет рельефа и делает крышу без текстуры и, следовательно, лишенной характера, а ее диапазон цветов ограничен небольшим разнообразием синего, зеленого, коричневого и тускло-красного.
В-третьих.
Использование металлических крыш, таких как листовое железо, гладкое или покрытое цинком или оловом, а также использование гофрированных, гофрированных или прессованных железных листов нашло широкое применение. В некоторых случаях возможно использование других листовых металлов, таких как чистый цинк, медь или олово, но в целом это исключается из-за стоимости. Использование листового железа в его различных формах имеет преимущество дешевизны, негорючести, превосходной легкости, быстрой адаптации к структуре любой формы, чрезвычайно быстрого нанесения и легкого ремонта, а также легкости консервации при нанесении краски.С другой стороны, она очень недолговечна, если не будет тщательно защищена краской или другими покрытиями через частые промежутки времени, и совершенно неинтересна по своему внешнему виду после завершения, если прессование не дошло до степени, близкой к имитации кровельной черепицы, чтобы получить рельеф и фактура. В этом случае она дороже, чем должна быть металлическая крыша, и имеет все недостатки любого материала, который просто копирует другой.
Таким образом, область кровли из листового металла, скорее всего, станет меньше, чем увеличиваться, и, вероятно, она будет больше ограничиваться фабриками, амбарами и навесами низкого класса и меньше — зданиями, претендующими на архитектурные достоинства.
В-четвертых.
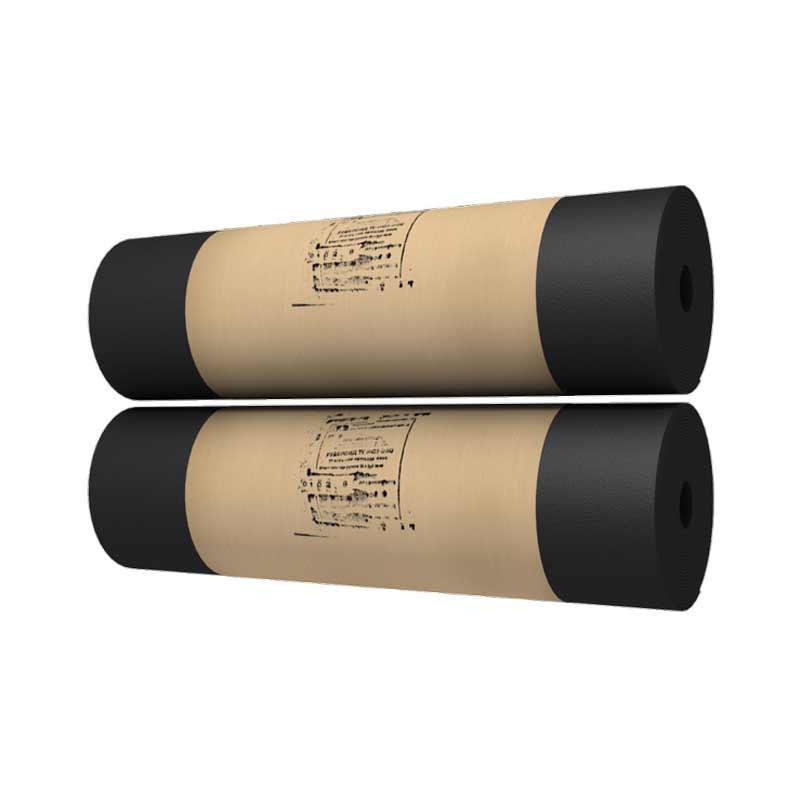
Составные крыши, сделанные из листов искусственных тканей, таких как бумага, войлок, асбест, ткань и т. Д., Гидроизолированные смолой, асфальтом, краской и многочисленными запатентованными и секретными препаратами и покрытые поверхностными покрытиями из песка или гравия, являются важный режим покрытия дешевых или временных конструкций. Такие крыши в основном устанавливаются на заводах, в магазинах с плоскими крышами и складских помещениях и редко применяются для жилых домов или важных построек любого типа. Однако они обладают достоинствами дешевизны, очень высокой водонепроницаемости даже при малых углах наклона, легкости нанесения и легкого ремонта или удаления.Они теряют эластичность, растрескиваются и протекают, если пломбировочный материал слишком долго просыхать без обновления. Они часто устойчивы к возгоранию снаружи, хотя почти всегда легко воспламеняются изнутри. Крыши из гудрона или асфальта нельзя использовать на крутых склонах из-за оттока жидкости в летнюю жару. Они ограничены сугубо утилитарными целями, ни при каких обстоятельствах не претендуя на красоту.
В-пятых.
Цементная кровля — это новый фактор на рынке, который может применяться двумя способами: во-первых, как черепица, изготавливаемая отдельно, а затем укладываемая и закрепляемая на месте, или во-вторых, в листах железобетона.Из первых, сравнение с глиняной черепицей будет сделано позже. К сильным сторонам последнего относятся его жесткость, огнестойкость и долговечность при хорошем изготовлении. Против этого лежит вероятность плохого качества изготовления (или сложность обеспечения хорошего мастерства, от которой напрямую зависят его продолжительность и прочность). Цементные изделия в целом сталкиваются с этой трудностью: по их внешнему виду нелегко сказать, хорошо они изготовлены или нет, т.е. е. скудость в материалах или изготовлении чрезвычайно трудно обнаружить, и там, где так много полагается на добросовестность, всегда вероятны частые злоупотребления.Кроме того, эта крыша очень тяжелая и требует массивной конструкции. Легкие или тонкие плиты совершенно не подходят, поскольку они трескаются при сильном сгибании или сильном ударе.
Очевидно, что в конкуренции с этими пятью классами кровельных материалов, большинство из которых хорошо зарекомендовали себя в торговой практике, кровельная черепица должна была продемонстрировать свою ценность. Черепичные крыши были необычными, поэтому их нелегко получить и часто вызывали длительные задержки в завершении строительства. Они были тяжелыми, требовали прочной конструкции и, следовательно, более дорогими.Они были уложены плохо, неквалифицированными рабочими, которые зачастую враждебно относились к новой крыше и были рады видеть, что она стала непопулярной из-за протечек или раннего ремонта. Они по своей природе были более дорогостоящими. Но, несмотря на все эти недостатки и другие, не упомянутые, использование плитки с каждым годом увеличивается все более и более быстро. Его преимущество в руках умелого пользователя в красоте формы, текстуры поверхности и цвета, а также в его полном удовлетворении при правильном проектировании, изготовлении и укладке, с точки зрения веса и водонепроницаемости, его негорючесть. характер и его фактическая устойчивость к воздействию внешнего огня или воды или того и другого, его долговечность при правильном проектировании и укладке, все эти и другие преимущества были признаны архитекторами настолько тщательно, что теперь подавляющее большинство крупных институциональных зданий, красивых жилых домов и другие, где архитектурные соображения имеют вес, используют черепичную крышу.Он еще не вторгся в сферу дешевой кровли, и в американских условиях, как в отношении рабочей силы, так и материалов, ни в коем случае нельзя быть уверенным, что он когда-либо получит широкое распространение, которое характеризует его использование в Европе и на Востоке.
Гандикапы
Некоторые недостатки, из-за которых в прошлом ограничивалось использование кровельной черепицы, со временем, несомненно, будут устранены. На месте , первом месте , конструкция черепицы, отвечающая строгим условиям современного использования, становится менее разнообразной и более определенной. Многие причудливые, непрактичные и неуклюжие плитки были «изобретены» или спроектированы различными энтузиастами, и их введение, как правило, задело причину и задержало использование практичных дизайнов. Многие из этих теорий пришлось опробовать и впоследствии пережить. Многие протекающие крыши и большая часть медленного строительства черепичной крыши были вызваны плохим дизайном, а частично — плохим качеством изготовления. Во-вторых. — Вес ранней черепичной крыши был чрезмерным. Лучшее оборудование, лучшие сушилки, лучшие печи, а также больше знаний и опыта со стороны производителей в значительной степени помогли преодолеть это возражение, и теперь черепичные крыши теперь снабжены черепичными крышами, при которых учет веса больше не имеет большого значения. В-третьих, умножение растений устранит одно из самых больших препятствий на пути роста отрасли. За счет избежания чрезмерных затрат на транспортировку и устранения задержек, вызванных длительными поставками и часто перегруженными заводскими условиями, произойдет значительное расширение использования плитки не только с экономической точки зрения, но и со стороны.
художественной красоты, недоступной никаким другим кровельным материалам. С черепицей можно получить вечную крышу любого рисунка и любого цвета.Цвет содержится в стекловидном теле, поэтому он не выгорает, что больше, чем можно сказать о любом другом красящем составе, используемом для любого типа крыши.
Цементная плитка
За последние годы получено много патентов на цементную черепицу. Время от времени по стране запускали заводы, большинство из которых были неудачными. Несколько заводов были запущены в Огайо, а именно в Колумбусе, Ланкастере и других местах. В Детройте, штат Мичиган, одно время также был завод по производству цементной плитки.Проблема заключалась в том, чтобы получить черепицу, которая не была бы слишком пористой и не треснула бы от расширения и сжатия на крыше. Чтобы преодолеть это, их обязательно сделали очень тяжелыми. Второе серьезное возражение — невозможность получить постоянные цвета. Хотя минералы и минеральные оксиды используются в качестве красителей, известно, что в течение одного года они тускнеют, приобретая совсем не привлекательный вид. Многочисленные крыши в Детройте, покрытые цветной цементной черепицей, являются тому примером.
Асбестовая плитка
В последнее время на рынке появился материал, представляющий собой асбестоцементную черепицу или плитку. Этот материал оказался намного лучше, чем обычная цементная плитка, благодаря своей чрезвычайной легкости и определенной эластичности. Против этой плитки можно выдвинуть те же возражения, что и против обычной цементной плитки, а именно, она окажется очень неудовлетворительной, если будет рассмотрен вопрос о цвете. Кроме того, известно, что они плохо деформируются под воздействием солнца. Чтобы преодолеть эту проблему, был разработан медный зажим или крепеж, который используется на более поздних крышах из этого материала.
Несомненно, для этого материала найдется область применения на больших крышах дешевой конструкции, где необходима чрезвычайная легкость, но для исключительно первоклассных и художественных работ, где требуется что-то иное, чем плоская или гофрированная черепица, глиняная черепица вряд ли подойдет смещен.
Скудное распространение заводов по производству кровельной плитки
Этот вопрос, пожалуй, самый важный в связи с продвижением бизнеса. В настоящее время всего около одного завода на три с половиной штата, поэтому неудивительно, что плитки не получили широкого распространения.Во многих частях страны черепичные крыши никогда не видели. В настоящее время на всем нашем восточном побережье нет ни одного растения. На всем Юге можно упомянуть только один завод, в то время как на Юго-Западе и Западе нет ни одного завода, производящего черепицу в качестве единственной продукции. На трех или четырех заводах в Калифорнии некоторые плитки производятся вместе с другой посудой, но плитки составляют незначительную часть от общего объема производства. Когда плиточные заводы будут разбросаны по всем частям нашей страны, тогда мы начнем видеть использование плитки как стандартного товара, как кирпичи используются сегодня.Почти каждый город имеет свой общий кирпичный двор, и почти в каждом штате есть один или несколько заводов по производству лицевого или лицевого кирпича, производящих высококачественные изделия, стоимость которых оправдывает фрахт в большие города.
Так и должно быть с черепицей. Нет ни настоящего, ни будущего шанса на поставку дешевой плитки для покрытия сараев и сараев. Они должны производиться на месте и иметься на складе у дилеров, как в европейских странах. Но лучший класс плитки, такой как испанская, глазурованная и скользящая, должен производиться более крупными заводами, где можно найти подходящий материал, и отгружаться на свои рынки на разумные расстояния, как облицовочный кирпич и терракота.
Эти условия действительно существуют сейчас в отношении характера предприятий, которые сейчас ведут бизнес. Практически в каждом случае есть хорошо построенные и тщательно обслуживаемые предприятия, которые почти всегда достигают своих рынков дальними перевозками. Но в будущем, с тремя или четырьмя такими заводами в каждом из хорошо оседлых штатов, чтобы заботиться о более тонкой торговле, и с дешевой плиткой, производимой на местных верфях для более дешевой торговли, промышленность начнет сравнивать с развитием, которое она имеет. достигнута в большей части остальной части мира.
Время от времени в журналах по торговле глиной различные писатели делают заявления, что современные производители кирпича должны заняться производством кровельной черепицы в связи с их нынешним бизнесом. Такой совет крайне необдуман. Производство кровельной черепицы — это самостоятельный бизнес, который заслуживает безраздельного внимания руководителей. Способы сушки, схватывания и обжига сильно отличаются от методов производства кирпича, и прошлые попытки обжечь кирпич и плитку в одной печи в значительной степени потерпели неудачу.Кроме того, практика неэкономична. Плитку можно обжечь за гораздо более короткое время, чем кирпич, поэтому держать плитку под огнем в ожидании необходимой термообработки — пустая трата времени и топлива.
Нет больше причин связывать производство кровельной черепицы с производством кирпича и водосточной черепицы, чем связывать производство терракоты с теми же изделиями или производство сырой керамической посуды с тонким фарфором.
Примечания
- Морс, Э.С. «О более старых формах терракотовой черепицы», Амер. Arch. и Строительные новости [1892] об. 35, стр. 197, т. 36, pp. 5, 24, 52. Эта статья свободно использовалась в различных частях этой главы, за что настоящим выражается должное признание.
- По Морзе, О старых формах терракотовой черепицы, амер. Archt. и Строительные новости, (1892), Vol. 35, стр. 198.
- Барбер, Э. А. Керамика и фарфор США, стр. 51.
- loc. соч.
- loc.соч.
- Howe’s History of Ohio., Vol. 2, стр. 301.
- Barber, op. соч., стр. 192.
- Wheeler, H.A., Mo. Geol. Surv., Vol. XI, стр. 436.
- Разрушен пожаром осенью 1909 года.
Источник: Переформатированная глава из Производство черепицы (Геологическая служба Огайо. Четвертая серия, Бюллетень 11).
.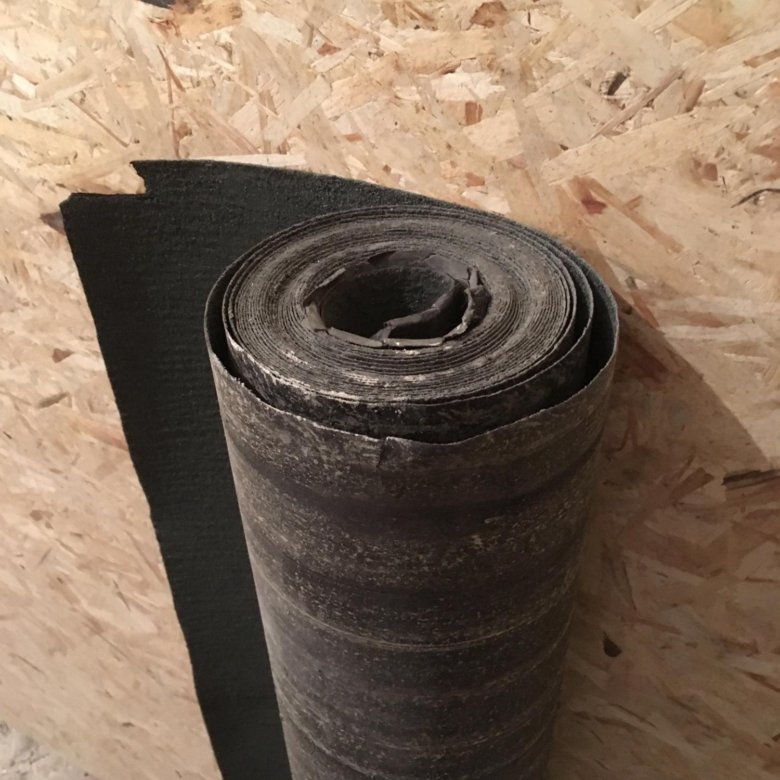