Станина токарного станка это
Тока́рный стано́к — станок для обработки резанием (точением) заготовок из металлов, древесины и других материалов в виде тел вращения. На токарных станках выполняют черновое и чистовое точение цилиндрических, конических и фасонных поверхностей, нарезание резьбы, подрезку и обработку торцов, сверление, зенкерование и развёртывание отверстий и т. д. Заготовка получает вращение от шпинделя, резец — режущий инструмент — перемещается вместе с салазками суппорта от ходового вала или ходового винта, получающих вращение от механизма подачи.
Значительную долю станочного парка составляют станки токарной группы. Она включает, согласно классификации Экспериментального НИИ металлорежущих станков, девять типов станков, отличающихся по назначению, конструктивной компоновке, степени автоматизации и другим признакам.
Применение на станках дополнительных специальных устройств (для шлифования, фрезерования, сверления радиальных отверстий и других видов обработки) значительно расширяет технологические возможности оборудования.
Токарные станки, полуавтоматы и автоматы, в зависимости от расположения шпинделя, несущего приспособление для установки заготовки обрабатываемой детали, делятся на горизонтальные и вертикальные. Вертикальные предназначены в основном для обработки деталей значительной массы, большого диаметра и относительно небольшой длины.
Самые распространённые токарные станки в советское время — 1К62 и 16К20.
Содержание
История создания [ править | править код ]
Токарный станок — древний инструмент. Самое раннее свидетельство о токарном станке восходит к Древнему Египту около 1300 года до нашей эры [1] . Есть также незначительные доказательства его существования в микенской цивилизации, начиная с 13-го или 14-го века до нашей эры [2] .
Четкие свидетельства изготовленных на станке артефактов были обнаружены в 6 веке до нашей эры: фрагменты деревянной чаши в этрусской гробнице в Северной Италии, а также две плоские деревянные тарелки с декоративными изготовленными на станке ободами в современной Турции [3] .
В период враждующих государств в Китае, около 400 г. до н. э., древние китайцы использовали токарные станки для заточки инструментов и оружия в промышленных масштабах [4] .
Первая известная картина, на которой изображен токарный станок, датируется 3 веком до нашей эры в Древнем Египте [5] .
Токарный станок был очень важен для промышленной революции. Он известно как «мать станков», поскольку это был первый станок, который привел к изобретению других станков [6] .
В 1717 году «придворный токарь Его Величества Император Петра Великого» Андрей Константинович Нартов впервые изобрёл токарно-винторезный станок с механизированным суппортом и набором сменных зубчатых колёс [7] . В токарных станках той эпохи резец зажимался в особом держателе, который перемещали вручную, прижимая к обрабатываемому предмету. Качество зависело только от точности рук мастера, тем более, что в то время токарные станки уже применялись для обработки металлических, а не деревянных изделий. Нарезать резьбу на болты, наносить сложные узоры на обрабатываемый предмет, изготовить зубчатые колеса с мелкими зубчиками мог только очень искусный мастер. В своем станке Нартов не просто закрепил резец, но и применил следующую схему: копировальный палец и суппорт приводились в движение одним ходовым винтом, но с разным шагом нарезки под резцом и под копиром. Таким образом было обеспечено автоматическое перемещение суппорта вдоль оси обрабатываемой заготовки. Станок позволял вытачивать сложнейшие рисунки почти на любых поверхностях. Как это ни парадоксально, невзирая на все дальнейшие усовершенствования придуманного Нартовым механизированного суппорта, принцип его действия остался таким же и в наше время [8] . Первые токарные станки Нартова хранятся в коллекции Эрмитажа, как шедевры инженерного искусства XVIII в [9] .
Первый полностью задокументированный токарный цельнометаллический токарный станок был изобретен Жаком де Вокансоном около 1751 года. Он был описан в «Энциклопедии».
Важным ранним токарным станком в Великобритании был горизонтальный сверлильный станок, который был установлен в 1772 году в Королевском Арсенале [en] в Вулвиче. Он работал на лошадиной тяге и позволял производить гораздо более точные и мощные пушки, которые с успехом использовались в американской войне за независимость в конце 18-го века. Одной из ключевых характеристик этого станка было то, что заготовка вращалась в противоположность инструменту, что делало её технически токарным станком. Генри Модслей, который позже много совершенствовал токарные станки, работал в Королевском Арсенале с 1783 года [10] . Подробное описание токарного станка Вокансона было опубликовано за десятилетия до того, как Модслей усовершенствовал свою версию. Вполне вероятно, что Модсли не знал о работе Вокансона, поскольку в его первых версиях упора для скольжения было много ошибок, которых не было в токарном станке Вокансона.
Во время промышленной революции механизированная энергия, генерируемая водяными колесами или паровыми двигателями, передавалась на токарный станок посредством линейного вала, что позволяло быстрее и легче работать. Металлообрабатывающие токарные станки превратились в более тяжелые станки с более толстыми и жесткими деталями. Между концом 19 и серединой 20 веков отдельные электродвигатели на каждом токарном станке заменили линейный вал в качестве источника энергии. Начиная с 1950-х годов сервомеханизмы применялись для управления токарными станками и другими станками с помощью числового управления, которое часто сочеталось с компьютерами для создания числового программного управления (ЧПУ). Сегодня в обрабатывающей промышленности сосуществуют токарные станки с ручным управлением и ЧПУ.
Виды токарных станков [ править | править код ]
Доступны различные формы токарных станков в разных форматах и спецификациях. Есть деревообрабатывающие токарные станки, металлообрабатывающие станки и машины, используемые для декоративного точения, обработка стекла и алмазная обработка. Существуют легкие токарные станки, которые полезны для мягких работ, например, в мини-инструментальных комнатах или для практических применений или демонстраций. Существуют мощные токарные станки, используемые для массового производства на электростанциях, сталелитейных и бумажных фабриках, судостроительной и автомобильной промышленности, горнодобывающей промышленности, текстильной промышленности.
Первый в истории человечества механический токарный станок был изобретен в XVIII веке отечественным умельцем А.К.Нартовым. Уникальность его состояла в наличии суппорта — революционного устройства, освобождающего руки рабочего. Сегодня на токарных станках обрабатывается до 70% всех металлических деталей. Это один из самых востребованных видов промышленного оборудования. Постепенно обычные станки вытесняются оборудованием с числовым программным управлением, более эффективным и точным.
Устройство токарного станка
Чтобы лучше понять принцип работы оборудования изучим строение его главных механизмов:
- передняя шпиндельная бабка;
- станина;
- гитара сменных колес;
- фартук;
- коробка подач;
- суппорт;
- задняя бабка;
- коробка с электрооборудованием.
Передняя бабка металлообрабатывающего станка представляет собой металлическую деталь, обычно из чугуна, в которой располагается переключатель скоростей и главная рабочая часть — шпиндель. На бабке крепится болванка будущей детали. Коробка скоростей принуждает деталь вращаться. Основной компонент передней бабки — это вал в виде металлической трубки — шпиндель. Вал оканчивается резьбой особого размера для крепления патрона (используются поводковые, а также кулачковые типы) либо планшайбы, которая удерживает деталь. Здесь же находится прорезь в виде конуса для установки переднего центра. В шпинделе есть сквозное отверстие, сюда вставляют прут при необходимости его обработки. Для вращения шпинделя в передней бабке установлены подшипники, движение передается заготовке.
Подшипники не должны иметь люфта, работать легко и равномерно, удерживать шпиндель крепко и устойчиво. Два подшипника обеспечивают надежное крепление и вращение: задний и передний.
На внешней стороне стойки находится переключатель скоростей и информационная таблица. В таблице разъясняется, в какое положение устанавливать переключатель, чтобы получить требуемую скорость (число оборотов за минуту) вращения шпинделя.
Переключение скоростей производится после полной или частичной остановки инструмента, иначе зубчатые колеса передачи быстро выйдут из строя.
Гитара сменных колес это устройство, контролирующее характер шагового движения при нарезке резьбы. Каждый тип нарезки соответствует определенному набору зубчатых сменных колес. Такой механизм можно обнаружить на токарно-винторезном оборудовании старого образца. Он управляет движением резцедержателя.
Коробка подач — одна из основных частей механизма передачи, которая от шпинделя подает движение на суппорт. На этом участке скорость кручения движущихся элементов меняется, благодаря чему суппорт передвигается с необходимой скоростью в поперечном или продольном направлении.
Фартук — преобразовывает вращение вала хода в движение суппорта в обоих направлениях.
Станина (подставка) — основание машины, обычно выполняется из тяжелого металла (чугуна). Крепится на пару толстых столбов. Верхние части подставки — пара гладких рельс и пара направляющих в виде призмы, по ним перемещаются задняя бабка и суппорт.
Суппорт — это устройство токарного станка по металлу , передвигающее резцедержатель вместе с вставленным инструментом в любом направлении по отношению к оси токарного механизма: продольном, наклонном или поперечном. Наличие суппорта освобождает токаря от необходимости удерживать инструмент в руках. Движение в нужную сторону инструменту можно придать вручную или механически. Части суппорта:
- устройство поперечных салазок;
- каретка, двигающаяся по рельсам подставки;
- фартук с устройством преобразования кручения валов хода и винта в перемещение суппорта;
- устройство резцовых салазок;
- устройство резцедержателя.
Задняя бабка нужна чтобы закрепить свободный конец крупной детали из металла во время работы. На нее крепятся и дополнительные инструменты, например, сверла.
Задняя бабка может быть с обычной или крутящейся встроенной серединой. Встроенную крутящуюся середину используют в механизмах для ускоренного резания.
Короб с электрическими частями содержит кнопки, рукоятки и тумблеры для пуска и остановки металлообрабатывающего станка, электромотора, управления устройствами подач и оборотов, надзора над устройством фартука.
Кроме перечисленных частей в механизме токарного станка могут применяться хомуты, цанги, планшайбы, оправки, люнеты. Не в каждом станке присутствуют описанные выше части. Так, в станках для нарезки резьбы на детали нет коробки подач, вместо нее работает гитара и зубчатые колеса. У других устройств узел подач состоит из пары механизмов.
Технические характеристики и принцип работы
Независимо от устройства, станок характеризуется несколькими показателями:
- максимальная толщина (диаметр) болванки из металла для обработки;
- максимальное расстояние между серединами бабок;
- наибольшая толщина заготовки, которая устанавливается над суппортом.
В крепления на задней бабке устанавливается инструмент, которым будет производиться обработка детали. Бабка перемещается по рельсам станины на расстояние, определяемое длиной обрабатываемой заготовки. Суппорт располагается между передней и задней бабками, во время работы каретка двигается по рельсам и перемещает резак вдоль заготовки. Устройство резцедержателя зависит от металла детали и степени нагрузки на инструмент. Если работа не слишком сложна, достаточно будет одиночного держателя. На токарных станках современных моделей обычно устанавливают головки резцов. Это достаточно устойчивое устройство, способное удержать до четырех инструментов одновременно.
В качестве двигателя используется электрический мотор с ременной передачей. Ремень идет от двигателя к шкиву токарного станка, основное внимание следует уделять его натяжке, обеспечивающей хороший ход. Ремень изготавливается из брезентовой ленты, прорезиненной ткани или другого прочного материала.
Видео о том, как правильно выбрать токарный станок по металлу:
Вы здесь
Оглавление
Токарные станки используются для обработки деталей цилиндрической формы. Они включают в себя множество разновидностей, которые отличаются по размеру и наличию дополнительных функций. Такие промышленные модели как, токарный станок 16К20 очень распространены и широко используются в современной промышленности. Чтобы устройство нормально функционировало, требуется знать все особенности его деталей.
Станина токарного станка служит для закрепления практически всех механизмов и узлов, которые применяются на данном оборудовании. Зачастую ее отливают из чугуна, чтобы получить массивную и прочную конструкцию, которая смогла прослужить длительный срок. Это связано с тем, что она будет подвергаться большим нагрузкам. Не стоит также забывать об устойчивости, так как массивные большие модели используют огромную энергию во время работы и основание должно хорошо сопротивляться нагрузкам.
фото:станина токарного станка
Станина и направляющие станка крепятся при помощи болтов к тумбам или парным ножкам. Если устройство короткое, то применяется две стойки. Чем оно длиннее, тем больше стоек может потребоваться. Большинство тумб имеет дверцы, что позволяет их использовать в качестве ящиков. К направляющим следует очень внимательно относиться и оберегать их возможности повреждения. Не желательно оставлять на них инструменты, заготовки и прочие изделия. если все же приходится располагать на них металлические предметы, то перед этим следует положить деревянную подкладку. Для лучшего ухода, перед каждым применением станка, станину требуется протирать и смазывать. Когда работа завершена, следует удалять с нее стружку, грязь и прочие лишние предметы.
Особенности конструкции станины металлорежущих станков могут отличаться в зависимости о конкретной модели, так как они разрабатываются для удобного и безопасного размещения всех узлов оборудования. Но основные положения во многих случаях остаются одинаковыми, так что на примере популярных моделей можно рассмотреть основы.
Устройство чугунной станины
фото:устройство чугунной станины
- Продольное ребро;
- Продольное ребро;
- Поперечное ребро, служащее для связи продольных ребер;
- Призматические направляющие продольных ребер;
- Плоские направляющие, которые служат для установки задней и передней бабки, а также для передвижения по ним суппорта;
Стоит отметить, что у направляющих станины поперечное сечение может иметь различные формы. Обязательным правилом является соблюдение параллельного расположения, так что все должно быть равноудаленным от оси центров. Это требует точной фрезеровки или строгания. После этого осуществляется операция по шлифовке и шабрению. Все это обеспечивает точную обработку изделий, а также ликвидацию проблем с передвижением суппорта и возникновением толчков.
Виды станин станков
фото:виды станин станков
- Станина токарного станка по металлу, которая представлена на рисунке «а» под номерами 1 и 2, имеет трапецеидальное сечение направляющих. В данном случае основной упор сделан на большую опорную поверхность.
Они обладают большой износостойкостью, что позволяет долго оставлять свою точность. В то же время, для перемещения по ним суппорта нужно прилагать множество усилий, особенно, если он перекосился.
- На рисунке «б» представлена станина с плоским прямоугольным сечением направляющих. В отличие от предыдущего, они имеют уже по два ребра жесткости, а не одному, что делает их крепче.
- Рисунок «в» демонстрирует станину с направляющими треугольного сечения. С учетом того, что здесь используется достаточно малая опорная поверхность, с большим весом работать получается сложно, так что данный вид используется преимущественно для малых станков.
- На рисунке «г» показана станина с треугольным сечением и опорной плоскостью. В данном случае она также применяется для станков мелких размеров.
Если станина предназначается для тяжелого станка, то она имеет не только большое сечение, но и большее сопротивление на изгиб. Одними из наиболее распространенных является такой вид, как представлен на рисунке «г». Здесь каретка суппорта делает упор на призму №3 спереди, а сзади упирается на плоскость №6. Чтобы не произошло опрокидывание, ее удерживает плоскость №7. При задаче направления основную роль играет призма №3, тем более, что она воспринимает на себя большую часть давления, осуществляемого резцом.
Если на станине возле передней бабки имеется выемка, то она служит для тог, чтобы обрабатывать изделия большого диаметра. Если же происходит обработка изделия, радиус которых меньше высоты центров, то выемку перекрывают специальным мостиком.
Ремонт станины токарного станка
Шабрение станины токарного станка является технологическим процессом во время которого станина выверяется для закрепления коробки подач при помощи рамного уровня. Благодаря этому можно будет в дальнейшем легко установить перпендикулярность поверхности крепления суппорта и фартука к коробке подач.
- Первым делом станина устанавливается на жесткий фундамент и проверить продольное направление по уровню вдоль поверхности, а поперечное направление по рамному уровню.
Допустимые отклонения составляют не более 0,02 мм на 1 метр длины изделия.
- Шабрят верхние поверхности направляющей, сначала с одной стороны, используя поверочную линейку на краску. Во время этого процесса желательно периодически проверять извернутость направляющих.
- Затем шабрят поверхность второй направляющей. Максимальный допуск отклонений здесь остается таким же 0,02 мм на 1 метр длины изделия.
Шлифовка станины токарного станка
Шлифовка станины токарного станка состоит из следующих процедур:
- Необходимо провести зачистку и запиливание задиров и забоин имеющихся на поверхности;
- Станина устанавливается на столе продольно-строгального станка и надежно закрепляются там;
- Далее идет проверка извернутости направляющих, которая производится уложенного на мостике задней бабки уровня;
- Во время установки станины получается небольшой прогиб изделия, который следует исправить путем максимально плотного соприкосновения со столом;
- Повторно проверяется извернутость направляющих, чтобы результаты совпадали с тем, что было до закрепления;
- Только после этого приступают к шлифовке всех контактных поверхностей изделия. Процедура проводится при помощи торца круга чашечной формы. его зернистость должна быть К3 46 или КЧ 46, а твердость соответствовать СМ1К.
определение, виды, устройство, назначение, ремонт
У самого маленького настольного станка и огромного прокатного стана есть общая деталь — это станина. На нее крепятся все его подвижные и неподвижные узлы и детали. Станины изготавливают из прочных сплавов, ведь они выдерживать не только вес танка, но и усилия, возникающие в процессе его работы. Со временем станины изнашиваются, для продления жизни станка их подвергают обновляющему ремонту.
Что такое станина
Станина — это основа конструкции станка. На нее крепятся все остальные подвижные и неподвижные детали и узлы. Через нее механизм опирается на фундамент. Станина воспринимает на себя все усилия, возникающие при воздействии инструмента на заготовку. От определенных точек на станине, выбранных началом координат, отсчитываются перемещения движущихся частей станка. В нее входят такие компоненты, как:
- корпусные элементы;
- поперечные, продольные и вертикальные крепления и ребра жесткости;
- направляющие.
Станина – наиболее долгоживущая часть станка, рассчитанная на все время его эксплуатации. Двигатели, привода и рабочие органы могут много кратно заменяться по мере износа, направляющие лишь подвергается периодическому ремонту. Направляющие служат для продольного, поперечного или вертикального перемещения подвижных узлов механизма.
Направляющие бывают двух видов:
- незамкнуты, применяемые при обработке деталей большой и средней массы и небольших опрокидывающих моментах;
- замкнутые, используются при средних массах деталей и значительных опрокидывающих моментах.
Подвижные узлы могут перемещаться, скользя по направляющим, либо использовать роликовые или шариковые опоры.
Кроме передачи, распределения и компенсации усилий, станина также должна быть способной гасить колебания различной частоты, возбуждающиеся в механизме во время его работы.
Виды станин станков
Различают два основных вида изделия:
- горизонтальные опоры;
- вертикальные стойки.
Для горизонтальных их форма и сечение выбираются исходя из следующих факторов:
- оптимальное размещение узлов и деталей;
- автоматизированное или ручное удаление стружки и других отходов производства;
- минимальные помехи для подведения передач и коммуникаций к двигателям, приводам, рабочим органам;
- отведение охлаждающей жидкости и стружки;
- обеспечение расчетных показателей прочности, жесткости, вибропоглощения и шумоподавления;
При проектировании вертикальных стоек максимальное внимание уделяют их жесткости. Для этого выбирают наилучшую форму сечения, комбинируя полые объемы со сплошным литьем, вводя дополнительные стенки, перегородки и ребра жесткости.
При проектировании люков и ревизий, через которые осуществляется диагностика и техническое обслуживание механизмов, приходится достигать компромисса между удобством сервисных работ и требованиями сохранения жесткости.
При выборе сечения станин для фрезерного станка предпочтения отдают трапециевидным формам, наилучшим образом передающим и распределяющим как весовые, так и рабочие нагрузки от деталей и узлов крупных и тяжелых механизмов.
Для станин более легких станков становятся доступны и прямоугольные, и даже треугольные сечения.
Станины также разделяются на монолитные и сборные, состоящие из нескольких отдельно отливаемых и обрабатываемых деталей, которые соединяются в единое целое разъемными либо неразъемными соединениями.
Технические требования к станинам
Технические требования формируются с целью достижения соответствия фактических эксплуатационных качеств станка и проектных требований. Требуется также обеспечить баланс между показателями производительности и себестоимостью изготовления изделия.
Отдельный важный раздел технических требований- это требования к материалам, из которых должна быть изготовлена одна из самых важных деталей станка. Регламентируются:
- марка сплава;
- физико-механические и химические свойства;
- однородность структуры, прочность и упругость как в общем, как и отдельно в наиболее важных и нагруженных местах;
- твердость материала направляющих.
Еще один раздел требований — геометрия конструкции. От точности соблюдения размеров, особенно направляющих, зависит точность работы всего станка. Они служат для перемещения рабочих органов, непосредственно обрабатывающих изготовляемое изделие. Не менее важно соблюдение точности изготовления рабочих столов, разметочных плит и других видов оснастки для размещения, закрепления и перемещения заготовок.
Станина станка является точкой (или точками) отсчета координат при разметке и обработке изделия.
Геометрическими требованиями регламентируются как сами размеры, так и их предельные отклонения, параллельности поверхностей, предельно допустимые показатели изогнутости направляющих, углы уклона и радиусы сопряжения.
Немаловажный раздел требований относится к вибропоглощению и шумоизоляции. В нем описываются предельно допустимые показатели по механическим колебаниям конструкций станка на различных частотах, уровни передаваемых на фундамент вибраций. Для шумопоглощения используются специальные покрытия, наносимые как на наружные, так и на внутренние поверхности корпуса и ребер.
Металлы для производства станины и их основные свойства
Из какого материала делают станины станков? Традиционно основными материалами для изготовления станин различного оборудования служили металлы и их сплавы.
В XVII-XX веках наибольшей популярностью пользовался чугун. Он и сегодня сохраняет лидирующее положение, но постепенно отступает под натиском различных сортов стали, сплавов легких металлов, пластиков и композитных материалов.
Учитывая общую тенденцию к снижению массы и габаритов оборудования и повышению их эффективности, перед прогрессивными материалами открываются широкие перспективы.
Для станин легких и средних станков такая замена проходит опережающими темпами. Для тяжелого оборудования значительная часть функций станин переходит к армированному современными материалами железобетону фундамента.
Однако для высоконагруженных станков и производственных комплексов, таких, как прокатные станы, тяжелые прессы, кузнечные станки и сталелитейное оборудование, специальные марки чугуна по-прежнему вне конкуренции.
Его уникальная способность выдерживать большие статические нагрузки, высокая прочность направляющих и коррозионная стойкость выгодно отличают чугун от конкурирующих материалов. Чугунные сплавы с шаровидным графитом, модифицированные с помощью цериевых присадок, обладают такими же эксплуатационными характеристиками, как сталь и существенно дешевле в производстве.
Устройство станины
Основные компоненты конструкции станины токарного станка видны из чертежа станины в разрезе:
- опорная поверхность;
- продольные ребра;
- поперечные ребра, связывающие между собой продольные;
- направляющие, имеющие форму призмы;
- плоские направляющие, предназначенные для крепления бабок и перемещения суппортов.
Ребра формируются в процессе отливки заготовки под станину станка
Сечение призматических направляющих может принимать различные формы, исходя из направлений возникающих в процессе работы усилий и их величины. Обе направляющих обязательно должны быть строго параллельны в пространстве и иметь идеально гладкую и ровную опорную поверхность. В противном случае о точности обработки деталей на станке не может быть и речи.
Для достижения такого результата их подвергают высокоточной фрезеровке либо обрабатывают на строгальном станке. Далее проводится шлифовка и шабрение. В ходе этой обработки осуществляется неоднократный контроль геометрических показателей на соответствие требованиям технических условий. Окончательная проверка осуществляется после сборки станка и установки на него подвижных деталей и узлов.
Основное назначение
Назначение станины определяется ее ролью среди компонентов станка.
Она является одной из основных деталей и предназначена для выполнения следующих функций:
- крепление и размещение в определенном пространственном порядке всех остальных деталей и узлов изделия;
- восприятие, распределение и передача на фундамент статических и динамических нагрузок, вызываемых весом деталей и возникающих в процессе работы станка;
- создание условий для перемещения рабочих органов станка и заготовок с необходимой точностью по направляющим и рабочим столам.
Кроме того, она выполняет и вспомогательные функции — защиту элементов конструкции от воздействия внешней среды.
Ремонт станины
Несмотря на высокое качество материалов и точность изготовления, во время работы станина испытывает значительные нагрузки и неминуемо изнашивается. Наиболее заметны эти процессы на поверхности направляющих, теряющей свои геометрические и прочностные свойства.
Для восстановления рабочих свойств проводится периодический или внеплановый ремонт направляющих. Для выполнения операции шабрения со станка снимаются движущиеся части, а сама станина закрепляется на жестком массивном фундаменте. Далее операция проводится в следующей последовательности:
- проверяется линейность продольного и поперечного профиля с использованием рамного уровня;
- если отклонение превышает 0,02 мм на погонный метр, проводят шабрение одной из направляющих с применением линейки и краски для поверки;
- параллельно контролируется степень извернутости;
- после доведения отклонения до заданных значений переходят ко второй направляющей.
После шабрения проводят шлифовку поверхности.
Шлифовка направляющих
В ходе шлифовки выполняют операции в такой последовательности:
- запиливают и зачищают поверхностные забоины и задиры;
- станину закрепляют на плите продольно — строгальной установки;
- уложенным на уровне задней бабки уровнем измеряют степень извернутости направляющих;
- при необходимости корректируют провисание конструкции с помощью компенсирующих прокладок и клиньев;
- повторно измеряется извернутость, результаты измерений должны совпасть с первоначальными;
- поверхность направляющих шлифуется мелокоабразивной шлифовальной чашей.
После восстановления поверхности направляющих станок монтируется на собственный фундамент и на него крепятся ранее снятые подвижные части.
За срок службы станка такую операцию выполняют несколько раз, возвращая его к активному производственному применению
Станина токарного станка по металлу:фото,виды,шабрение и шлифовка
Устройство чугунной станины
фото:устройство чугунной станины
- Продольное ребро;
- Продольное ребро;
- Поперечное ребро, служащее для связи продольных ребер;
- Призматические направляющие продольных ребер;
- Плоские направляющие, которые служат для установки задней и передней бабки, а также для передвижения по ним суппорта;
Стоит отметить, что у направляющих станины поперечное сечение может иметь различные формы. Обязательным правилом является соблюдение параллельного расположения, так что все должно быть равноудаленным от оси центров. Это требует точной фрезеровки или строгания. После этого осуществляется операция по шлифовке и шабрению. Все это обеспечивает точную обработку изделий, а также ликвидацию проблем с передвижением суппорта и возникновением толчков.
Виды станин станков
фото:виды станин станков
- Станина токарного станка по металлу, которая представлена на рисунке «а» под номерами 1 и 2, имеет трапецеидальное сечение направляющих. В данном случае основной упор сделан на большую опорную поверхность. Они обладают большой износостойкостью, что позволяет долго оставлять свою точность. В то же время, для перемещения по ним суппорта нужно прилагать множество усилий, особенно, если он перекосился.
- На рисунке «б» представлена станина с плоским прямоугольным сечением направляющих. В отличие от предыдущего, они имеют уже по два ребра жесткости, а не одному, что делает их крепче.
- Рисунок «в» демонстрирует станину с направляющими треугольного сечения. С учетом того, что здесь используется достаточно малая опорная поверхность, с большим весом работать получается сложно, так что данный вид используется преимущественно для малых станков.
- На рисунке «г» показана станина с треугольным сечением и опорной плоскостью. В данном случае она также применяется для станков мелких размеров.
Если станина предназначается для тяжелого станка, то она имеет не только большое сечение, но и большее сопротивление на изгиб. Одними из наиболее распространенных является такой вид, как представлен на рисунке «г». Здесь каретка суппорта делает упор на призму №3 спереди, а сзади упирается на плоскость №6. Чтобы не произошло опрокидывание, ее удерживает плоскость №7. При задаче направления основную роль играет призма №3, тем более, что она воспринимает на себя большую часть давления, осуществляемого резцом.
Если на станине возле передней бабки имеется выемка, то она служит для тог, чтобы обрабатывать изделия большого диаметра. Если же происходит обработка изделия, радиус которых меньше высоты центров, то выемку перекрывают специальным мостиком.
Ремонт станины токарного станка
Шабрение станины токарного станка является технологическим процессом во время которого станина выверяется для закрепления коробки подач при помощи рамного уровня. Благодаря этому можно будет в дальнейшем легко установить перпендикулярность поверхности крепления суппорта и фартука к коробке подач.
- Первым делом станина устанавливается на жесткий фундамент и проверить продольное направление по уровню вдоль поверхности, а поперечное направление по рамному уровню. Допустимые отклонения составляют не более 0,02 мм на 1 метр длины изделия.
- Шабрят верхние поверхности направляющей, сначала с одной стороны, используя поверочную линейку на краску. Во время этого процесса желательно периодически проверять извернутость направляющих.
- Затем шабрят поверхность второй направляющей. Максимальный допуск отклонений здесь остается таким же 0,02 мм на 1 метр длины изделия.
Шлифовка станины токарного станка
Шлифовка станины токарного станка состоит из следующих процедур:
- Необходимо провести зачистку и запиливание задиров и забоин имеющихся на поверхности;
- Станина устанавливается на столе продольно-строгального станка и надежно закрепляются там;
- Далее идет проверка извернутости направляющих, которая производится уложенного на мостике задней бабки уровня;
- Во время установки станины получается небольшой прогиб изделия, который следует исправить путем максимально плотного соприкосновения со столом;
- Повторно проверяется извернутость направляющих, чтобы результаты совпадали с тем, что было до закрепления;
- Только после этого приступают к шлифовке всех контактных поверхностей изделия.
Процедура проводится при помощи торца круга чашечной формы. его зернистость должна быть К3 46 или КЧ 46, а твердость соответствовать СМ1К.
Устройство токарного станка по металлу – схема и основные узлы
По сути, устройство токарного станка, вне зависимости от его модели и уровня функциональности, включает в себя типовые конструктивные элементы, которые и определяют технические возможности такого оборудования. Конструкция любого станка, относящегося к категории оборудования токарной группы, состоит из таких основных элементов, как передняя и задняя бабка, суппорт, фартук устройства, коробка для изменения скоростей, коробка подач, шпиндель оборудования и приводной электродвигатель.
Основные части токарного станка по металлу
Как устроены станина и передняя бабка станка
Станина является несущим элементом, на котором устанавливаются и фиксируются все остальные конструктивные элементы агрегата. Конструктивно станина представляет собой две стенки, соединенные между собой поперечными элементами, придающими ей требуемый уровень жесткости. Отдельные части станка должны перемещаться по станине, для этого на ней предусмотрены специальные направляющие, три из которых имеют призматическое сечение, а одна – плоское. Задняя бабка станка располагается с правой части станины, по которой перемещается благодаря внутренним направляющим.
Литая станина токарного станка усилена ребрами жесткости и имеет отшлифованные и закаленные направляющие
Передняя бабка одновременно выполняет две функции: придает заготовке вращение и поддерживает ее в процессе обработки. На лицевой части данной детали токарного станка (она также носит название «шпиндельная бабка») располагаются рукоятки управления коробкой скоростей. При помощи таких рукояток шпинделю станка придается требуемая частота вращения.
Для того чтобы упростить управление коробкой скоростей, рядом с рукояткой переключения располагается табличка со схемой, на которой указано, как необходимо расположить рукоятку, чтобы шпиндель вращался с требуемой частотой.
Рычаг выбора скоростей станка BF20 Yario
Кроме коробки скоростей, в передней бабке станка размещен и узел вращения шпинделя, в котором могут быть использованы подшипники качения или скольжения. Патрон устройства (кулачкового или поводкового типа) фиксируется на конце шпинделя при помощи резьбового соединения. Именно данный узел токарного станка отвечает за передачу вращения заготовке в процессе ее обработки.
Направляющие станины, по которым перемещается каретка станка (нижняя часть суппорта), имеют призматическое сечение. К ним предъявляются высокие требования по параллельности и прямолинейности. Если пренебречь этими требованиями, то обеспечить высокое качество обработки будет невозможно.
Назначение задней бабки токарного оборудования
Задняя бабка токарного станка, конструкция которой может предусматривать несколько вариантов исполнения, необходима не только для фиксации деталей, имеющих значительную длину, но и для крепления различных инструментов: сверл, метчиков, разверток и др. Дополнительный центр станка, который устанавливается на задней бабке, может быть вращающимся или неподвижным.
Устройство задней бабки: 1, 7 – рукоятки; 2 – маховичок; 3 – эксцентрик; 4, 6, 9 – винты; 5 – тяга; 8 – пиноль; А – цековка
Схема с вращающимся задним центром используется в том случае, если на оборудовании выполняется скоростная обработка деталей, а также при снятии стружки, имеющей значительное сечение. При реализации этой схемы задняя бабка выполняется с такой конструкцией: в отверстие пиноли устанавливаются два подшипника – передний упорный (с коническими роликами) и задний радиальный, – а также втулка, внутренняя часть которой расточена под конус.
Осевые нагрузки, возникающие при обработке детали, воспринимаются упорным шарикоподшипником. Установка и фиксация заднего центра оборудования обеспечиваются за счет конусного отверстия втулки. Если необходимо установить в такой центр сверло или другой осевой инструмент, втулка может быть жестко зафиксирована при помощи стопора, что предотвратит ее вращение вместе с инструментом.
Вращающийся центр КМ-2 настольного токарного станка Turner-250
Задняя бабка, центр которой не вращается, закрепляется на плите, перемещающейся по направляющим станка. Пиноль, устанавливаемая в такую бабку, передвигается по отверстию в ней при помощи специальной гайки. В передней части самой пиноли, в которую устанавливают центр станка или хвостовик осевого инструмента, выполняют коническое отверстие. Перемещение гайки и, соответственно, пиноли обеспечивается за счет вращения специального маховика, соединенного с винтом. Что важно, пиноль может перемещаться и в поперечном направлении, без такого перемещения невозможно выполнять обработку деталей с пологим конусом.
Шпиндель как элемент токарного станка
Наиболее важным конструктивным узлом токарного станка является его шпиндель, представляющий собой пустотелый вал из металла, внутреннее отверстие которого имеет коническую форму. Что примечательно, за корректное функционирование данного узла отвечают сразу несколько конструктивных элементов станка. Именно во внутреннем коническом отверстии шпинделя фиксируются различные инструменты, оправки и другие приспособления.
Чертеж шпинделя токарно-винторезного станка 16К20
Чтобы на шпинделе можно было установить планшайбу или токарный патрон, в его конструкции предусмотрена резьба, а для центрирования последнего еще и буртик на шейке. Кроме того, чтобы предотвратить самопроизвольное откручивание патрона при быстрой остановке шпинделя, на отдельных моделях токарных станков предусмотрена специальная канавка.
Именно от качества изготовления и сборки всех элементов шпиндельного узла в большой степени зависят результаты обработки на станке деталей из металла и других материалов. В элементах данного узла, в котором может фиксироваться как обрабатываемая деталь, так и инструмент, не должно быть даже малейшего люфта, вызывающего вибрацию в процессе вращательного движения. За этим необходимо тщательно следить как в процессе эксплуатации агрегата, так и при его приобретении.
В шпиндельных узлах, что можно сразу определить по их чертежу, могут устанавливаться подшипники скольжения или качения – с роликовыми или шариковыми элементами. Конечно, большую жесткость и точность обеспечивают подшипники качения, именно они устанавливаются на устройствах, выполняющих обработку заготовок на больших скоростях и со значительными нагрузками.
Строение суппорта
Суппорт токарного станка – это узел, благодаря которому обеспечивается фиксация режущего инструмента, а также его перемещение в наклонном, продольном и поперечном направлениях. Именно на суппорте располагается резцедержатель, перемещающийся вместе с ним за счет ручного или механического привода.
Суппорт с кареткой станка Optimum D140x250
Движение данного узла обеспечивается его строением, характерным для всех токарных станков.
- Продольное перемещение, за которое отвечает ходовой винт, совершает каретка суппорта, при этом она передвигается по продольным направляющим станины.
- Поперечное перемещение совершает верхняя – поворотная – часть суппорта, на которой устанавливается резцедержатель (такое перемещение, за счет которого можно регулировать глубину обработки, совершается по поперечным направляющим самого суппорта, имеющим форму ласточкиного хвоста).
Резцедержатель быстросменный MULTIFIX картриджного типа
Резцедержатель, который также называют резцовой головкой, устанавливается в верхней части суппорта. Последнюю при помощи специальных гаек можно фиксировать под различным углом. В зависимости от необходимости на токарных станках могут устанавливаться одно- или многоместные резцедержатели. Корпус типовой резцовой головки имеет цилиндрическую форму, а инструмент вставляется в специальную боковую прорезь в нем и фиксируется болтами. На нижней части резцовой головки имеется выступ, который вставляется в соответствующий паз на суппорте. Это наиболее типовая схема крепления резцедержателя, используемая преимущественно на станках, предназначенных для выполнения несложных токарных работ.
Электрическая часть токарного станка
Все современные токарные и токарно-винторезные станки по металлу, отличающиеся достаточно высокой сложностью своей конструкции, приводятся в действие при помощи привода, в качестве которого используются электродвигатели различной мощности. Электрические двигатели, устанавливаемые на такие агрегаты, могут быть асинхронными или работающими от постоянного тока. В зависимости от модели двигатель может выдавать одну или несколько скоростей вращения.
Электрическая схема токарного станка 1К62 (нажмите для увеличения)
На большинстве моделей современных токарных станков по металлу устанавливаются двигатели с короткозамкнутым ротором. Для передачи крутящего момента от двигателя элементам коробки передач станка может использоваться ременная передача или прямое соединение с его валом.
На современном рынке также представлены модели токарных станков, на которых скорость вращения шпинделя регулируется по бесступенчатой схеме, для чего используются электродвигатели с независимым возбуждением. Регулировка скорости вращения вала такого двигателя может осуществляться в интервале 10 к 1. Однако из-за больших габаритов и не слишком экономичного потребления электроэнергии применяются такие электродвигатели крайне редко.
Двухскоростной двигатель со шкивом под плоский ремень передачи
Как уже говорилось выше, в качестве привода токарных станков могут использоваться и электродвигатели, работающие на постоянном токе. Именно такие электродвигатели, отличающиеся большими габаритами, обеспечивают бесступенчатое изменение скорости вращения их выходного вала.
Электродвигатель является основной частью электрической системы любого токарного станка, но она также включает в себя массу дополнительных элементов. Все они, функционируя в комплексе, обеспечивают удобство управления станком, а также эффективность и качество технологических операций, которые на нем выполняются.
Инструкция по выбору токарного станка с ЧПУ
НаправляющиеНаправляющие в токарных станках бывают в основном двух типов: качения или скольжения.
Как правило, направляющие скольжения имеют более высокую точность позиционирования, чем направляющие скольжения. Кроме того, направляющие качения имеют большую максимальную скорость перемещений. Это обусловлено использованием шариковых подшипников, которые имеют меньшее сопротивление при перемещениях.
Направляющие скольжения имеют более прочную и надежную конструкцию, так как их конструкция проще и не имеет таких слабых мест, как подшипники качения, которые часто выходят из строя. Высокая нагрузочная способность и жесткость конструкции позволяют добиться большей повторяемости и стабильности в сравнении с направляющими качения. Кроме того, срок службы направляющих скольжения в несколько раз превышает аналогичный показатель у направляющих качения.
В токарных станках SMEC используются направляющие скольжения Rexroth (Bosh group, Германия) коробчатого типа, сравнительно более широкие (в 1,2 раза шире чем у большинства конкурентов). Это преимущество станков SMEC гарантирует увеличенный срок службы, так как нагрузка на направляющие распределяется по большей площади соприкосновения.
Торможение направляющих коробчатого типа быстрее на 0,1 секунды чем направляющих линейного типа. Незначительная цифра в человеческом понимании играет огромную роль в машинной работе, поскольку позволяет снизить уровень вибраций станка, вследствие чего инструмент изнашивается медленнее, что снижает расходы на ТО в долгосрочной перспективе. Коробчатые направляющие имеют 6 плоскостей соприкосновения. Эта технология позволяет сохранить точность обработки даже после столкновений подвижных узлов станка.
Турситовое покрытие направляющих снижает трение и изнашивание станка. Уровень высокочастотной термической обработки поверхности направляющих SMEC более чем в два раза выше, чем у конкуренотов (2,7 мм у SMEC, против 1,3 мм у большинства станков).
Станины токарных станков сварные — Энциклопедия по машиностроению XXL
На фиг. 268 показана сварная конструкция станин токарного станка. Все элементы сварной станины, кроме направляющих и планок под рейку, изготовлены из листового проката толщиной 3, 4 и 6 мм. Передние и задние направляющие сварной станины изготовляют из специального профильного [c.347]Станины токарных станков обычно отливаются из чугуна (СМ. стр. 178—188), реже выполняются сварными. Для повышения износоустойчивости направляющих применяются закалка направляющих кислородно-ацетиленовым пламенем или токами высокой частоты накладные стальные направляющие. [c.253]
Теперь представьте себе обычный серийный кран-экскаватор, с которого снята стрела. Вместо стрелы установлена рама, в которую входит сварная ферма из двух стальных труб. Ферма может кататься только строго по вертикали, ибо она опирается на две пары чугунных роликов, v встроенных в раму. Вдоль фермы, зацепившись своими лапами за направляющие, как суппорт за станину токарного станка, в свою очередь, строго вертикально ползет буровой механизм типа ТМ. Он состоит из электромотора на сто киловатт, получающего питание по кабелю, планетарного редуктора и дробящего породу долота. Опуская и поднимая сварную ферму лебедкой, можно регулировать глубину проходимой траншеи.
[c.231]
Примером полного использования штамповочных и сварочных способов может служить штампо-сварная станина токарного станка. [c.160]
На фиг. 121 показаны сварные конструкции станин токарных станков. Они выполнены из стальных листов толщиной 4 мм по сравнению с литыми станинами в классическом испол- [c.192] В качестве другого примера на фиг. 308 показан процесс формообразования заготовок корпуса заднего моста грузового автомобиля при изготовлении их из трубы (фиг 308, а) и листа (фиг 308, б) с последующей приваркой фланцев и других частей, на которые предварительно была разделена заготовка. Примером могут служить также штампо-сварные конструкции станин токарных станков, показанные ранее (см. стр. 371). [c.428]Станины изготовляются преимущественно из серого чугуна благодаря его способности при отливке получать сложные профили. Сварные конструкции станин из стали применяются значительно реже. Общий вид литой станины токарного станка приведен на фиг. 32. [c.51]
Подвижные соединения обеспечивают движение ОДНОЙ детали относительно другой (например, соединение вала с подшипниками, суппорта токарного станка со станиной, зубчатое зацепление и др.). Неподвижные соединения жестко скрепляют две или несколько деталей (например, сварные, резьбовые [c.44]
Более спорной является применимость сварных конструкций в станкостроении. Это в известной степени объясняется тем, что для повышения жесткости сварных станин необходимо вводить в кон- струкцию дополнительные элементы, увеличивающие расход металла при одновременном увеличении трудоемкости сварных работ например, для изготовления сварной станины одного из токарных станков потребовалось 122 отдельных элемента — 90 наименований при общей протяженности всех сварных швов в корпусе станины 36,4 м. Трудоемкость механической обработки сварной станины «В 2,23 раза выше трудоемкости литой чугунной вследствие необходимости дополнительной обработки, вызываемой закалкой стальных направляющих. Припуск на шлифование направляющих в этом случае доходит до 1,5 мм при длине станины 3500 мм вместо нор-
[c.186]
Пример конструктивного оформления литой базовой детали — стойки агрегатного станка приведен на рис. 92, а конструкция сварной стойки карусельного станка показана на рис. 93. Пример оформления железобетонной конструкции показан в виде поперечного разреза станины тяжелого токарного станка (рис. 94). [c.112]
Сталь. Хотя чугун все еще остается тем материалом, из которого изготовляется большая часть станин станков, в современном станкостроении наблюдается тенденция к замене литых станин сварными из прокатной стали. Станины последнего типа почти полностью вытеснили литые, например, в протяжных станках. В период 1935 — 1940 гг. появились также фрезерные, токарные, долбежные, круглошлифовальные и другие станки со стальными сварными станинами, а в области плоскошлифовальных станков такие станины встречаются в моделях, построенных более 20 лет тому назад. Отмеченная тенденция обусловлена рядом технических и экономических причин. [c.125]
В токарно-винторезном станке модели 1К62 за последние годы внедрены взамен литых 25 наименований тонкостенных штампо-сварных деталей различного назначения и степени нагруженности защитные детали (футляры, жалюзи, протекторы, экраны), детали узла охлаждения (корыта, лотки), детали узла электрификации станка, а также крышки, кронштейны и др. Завод Красный пролетарий успешно проводит испытания образца тонкостенной штам-по-сварной станины токарного станка модели 1К62.
[c.39]
Станины чаще всего выполняются из серого чугуна (ГОСТ 1412-54) станины малых и средних станков — из чугуна СЧ21-40, а станины средних и тяжелых станков — из чугуна СЧ32-52. Станины из чугуна легче обрабатываются и дают более низкую себестоимость станка при серийном производстве. Кроме того, станки с чугунной станиной имеют большую виброустойчивость. Однако чугунные направляющие недолговечны — они быстро изнашиваются, а вес литой чугунной станины велик. Во избежание этих недостатков все шире начинают применять стальные сварные станины, а для тяжелых уникальных токарных станков иногда используют железобетонные станины. [c.52]
НИНЫ ограничены преимуп1ественно плоскостями, представляя более или менее сложный многогранник. Для литых станин характерны, напротив, плавные, закру -лениые пгреход1.1 между поверхностями, труднее осуп1ествимые при пользовании прокатной сталью (фиг. 99, а — токарный станок со сварной станиной, б — тот же станок с литой станиной). [c.146]
Токарные станки с наклонной станиной
Ни для кого не секрет, что большинство лидеров мирового станкостроения выпускает токарные станки с направляющими, расположенными в плоскости под углом относительно опорной поверхности станка и верхним расположением резцедержателя. Такая компоновка именуется наклонной станиной. Эти тенденции, безусловно, знакомы всем, кто сталкивался с необходимостью покупки токарного станка с ЧПУ. Наряду с очевидными плюсами, при точении и измерении деталей, отводе стружки и т.д. существует один весомый минус. Стоимость отливки станины и стоимость её обработки, а как следствие цена станка, зачастую ставят вопрос о целесообразности приобретения токарного станка с наклонной станиной. Именно этот фактор предопределил отсутствие токарных станков с наклонной станиной на складе нашей компании. Многолетний опыт работы на Российском рынке и статистика продаж станков токарной группы на рынках стран таможенного союза констатировали, что большинство предприятий работает с заготовками из сортового проката или отливками, полученными методом литья в земляные формы. Это в свою очередь подразумевает работу с большим припуском, низкими частотами вращения и ударной нагрузкой. Именно поэтому, большинство покупателей выбирает хорошо зарекомендовавшие себя токарные станки типа 16А20Ф3 или 1М63Ф3 и их аналоги. В нашей линейке токарных станков это CK6150, CK6150S и CK6163.
На рынках стран Евросоюза, США, Японии и Тайваня давно применяются методы получения заготовок, позволяющие минимизировать припуски под обработку, а значит увеличить производительность, скорость и точность механической обработки. В связи с этим большинство крупных и всемирно известных производителей, как правило, не выпускают станков с прямой станиной, а концентрируются на выпуске станков с наклонной станиной. Так же, одним из основных факторов, влияющим на изменения в технологии производства токарных станков с ЧПУ, являются новые разработки в области режущего инструмента, позволяющие увеличить скорости резания при точении, что в свою очередь требует большей частоты вращения, что делает бессмысленным использование ступенчатого переключения диапазонов частот вращения. Для изменения частоты вращения и увеличения её предельных значений применяются серводвигатели шпинделя с ременной передачей крутящего момента на шпиндель или высокоскоростные мотор-шпиндели (прямой привод шпинделя). Так же становится необходимым увеличение скорости подачи, однако высокие скорости перемещения инструмента не достижимы при использовании направляющих скольжения. Поэтому, для высокоскоростной обработки применяются направляющие качения шарикового или роликового (для тяжёлых условий обработки) типов. Кроме того, всё большее применение находят токарно-фрезерные станки, позволяющие производить не только точение, но и фрезерование без перестановки детали. Также получили широкое распространение токарно-фрезерные центры. Практически все станки, предусматривающие токарно-фрезерную обработку, базируются именно на наклонной станине.
Однако, время не стоит на месте и в современных условиях производства всё больше находят применение методы получения точных заготовок с минимальным припуском под обработку и в нашей стране. Производство высокоточных деталей становится всё более востребованным. Отсюда и необходимость в оборудовании, соответствующем уровню современных технологий стала проявляться и среди небольших частных производственных компаний, которые были, есть и будут оставаться нашим основным сегментом рынка. Это подтолкнуло нас во многом пересмотреть подход к выбору складской программы станков, которые мы предлагаем Вашему вниманию.
На выставке «Металлообработка-2018» в Москве, мы представим новый вид продукции, который всегда можно будет увидеть и приобрести из наличия у компании Иствестпарт, а именно токарные станки с наклонной станиной. В 2018 году станки с наклонной станиной на складе ООО «Иствестпарт». Мы рады предложить нашим потенциальным заказчикам и партнёрам следующие разновидности токарных станков с наклонной станиной.
1. Токарные станки с наклонной станиной без задней бабки моделей TCK6330 (Ø точения 300 мм), TCK6336 (Ø точения 360 мм), TCK6336S (Ø точения 360 мм), TCK6340 (Ø точения 400 мм), TCK6350(Ø точения 500 мм). Их назначение- точение коротких заготовок без поджатия задним центром. На сегодняшний день это самые дешёвые станки с наклонной станиной. При этом уровень точности и производительности не уступает большинству европейских, американских и тайваньских токарных станков.
2. Токарные станки с наклонной станиной моделей TCK36 (Ø точения 360 м), TCK46 (Ø точения 460 м), TCK520 (Ø точения 520 м), TCK56 (Ø точения 560 м), TCK66 (Ø точения 360 м). Эти станки могут применяться для обработки валов длинной до 1000 мм. Имеют все необходимые возможности и функции, начиная от гидравлических поддерживающих люнетов и заканчивая функцией приводного инструмента для токарно-фрезерной обработки.
3. Токарные трубонарезные станки с наклонной станиной, серии YPT. Основным их отличием является большой диаметр сквозного отверстия в шпинделе (от190 мм). Так же РМЦ может составлять 2000 мм. Перемещение суппорта на данных станках производится по направляющим скольжения.
4. Тяжёлые токарные станки с ЧПУ с наклонной станиной серии CKY. Так же как и трубонарезные станки с наклонной станиной, они оснащены направляющими скольжения.
Мы надеемся, что в ближайшее время Российские промышленники по достоинству оценят эти новинки. С образцами данного вида оборудования Вы сможете ознакомиться во время выставки Металлообработка-2018, которая будет проходить с 14-18 мая 2018 года в ЦВК «Экспоцентр» г. Москва. Будем рады видеть Вас на нашей экспозиции, располагаемой во 2-павильоне, зал №3.
вернуться назад
Станина токарного станка — Примечания к инструментам
Введение
Станина токарного станка является основным конструктивным элементом токарного станка. Станина служит фундаментом для путей, которые, в свою очередь, несут каретку, заднюю бабку и другие компоненты, такие как люнеты и упоры каретки.
Станина является основным конструктивным элементом токарного станка.Кровать
Станины или просто направляющие — это линейные опорные элементы, обеспечивающие траекторию движения каретки и задней бабки токарного станка.Кровать может иметь несколько конфигураций, включая коробчатую направляющую, V-образную направляющую, направляющую «ласточкин хвост» и может использоваться с шариковыми или роликоподшипниками на некоторых станках.
Боковые проемы — это прецизионные отшлифованные поверхности, обеспечивающие движение каретки и задней бабки.Стеллаж
Рейка представляет собой плоский зубчатый элемент, который используется вместе с ведущей шестерней для обеспечения движения каретки при токарных операциях. Мощность передается на ведущую шестерню через подающий стержень. На токарных станках с ЧПУ мощность может подаваться непосредственно на ведущую шестерню через серводвигатель.
Подающая штанга
Подающий стержень представляет собой цилиндрический стержень с вырезанной на нем шпоночной канавкой. Червячная шестерня скользит по этому штоку и передает мощность либо на ведущую шестерню каретки, либо на поперечную шестерню в зависимости от положения рычага выбора механической подачи.
Примечание. На некоторых токарных станках подающая штанга и ходовой винт объединены в один и тот же компонент.
Подающий стержень передает мощность от передней бабки к каретке для выполнения операций подачи питания в каретке или в направлении поперечного скольжения.Ходовой винт
Ходовой винт представляет собой стержень с резьбой, который используется для подачи питания на каретку при нарезании резьбы. Ходовой винт часто имеет резьбу ACME. Ходовой винт передает мощность на каретку, когда рычаг с половинной гайкой задействован.
Габаритные станки со станиной
Максимальный диаметр обрабатываемой детали на токарном станке определяет угол поворота токарного станка. Некоторые токарные станки включают функцию увеличения поворота токарных станков.(Обычно) съемный сегмент станины, известный как зазор, можно вынуть, чтобы разместить необычно большую заготовку. При выборе размера токарного станка обязательно знайте, является ли размер качания колебанием над станиной, над зазором или над поперечным суппортом.
Поворот токарного станка — это заготовка самого большого диаметра, которая может быть обработана на нем. Токарный станок со станиной с зазором может обрабатывать заготовку большего диаметра с удаленным зазором.Станина с раздвижной щелью (видео пример)
Токарные станки с наклонной станиной
Станки с наклонной станиной имеют наклонную станину.Угловая ориентация позволяет стружке не мешать. Такое расположение может также увеличить расстояние между путями для обеспечения большей устойчивости.
Токарный станок с наклонной станинойСписок литературы
Роджерс, Барри. «Покупка токарного станка: наклонные станины и многозадачные конфигурации». Современный механический цех. 17 августа 2018 г. По состоянию на 17 мая 2019 г. https://www.mmsonline.com/blog/post/buying-a-lathe-slant-beds-and-multitasking-configurations.
Что такое токарный станок ?.Один из старейших станков — это… | by mechstuff4u
Один из старейших станков — токарный станок. В 1797 году англичанин Генри Модслей сконструировал первый токарно-винторезный станок, который является предшественником современного высокоскоростного высокопроизводительного токарного станка.
Функции токарного станка:
Удаление металла с детали для придания ей необходимой формы и размера — основная функция токарного станка.
Для этого нужно надежно и жестко удерживать изделие на станке, а затем повернуть его против режущего инструмента, который удалит металл в виде стружки.
Типы токарных станков:
1. Скоростной токарный станок
- Деревообработка
- Центрирование
- Полировка
- Прядение
2. Токарный станок для двигателя
- Ременный привод
- Индивидуальный моторный привод
- Токарный станок с зубчатой передачей
3. Стационарный токарный станок
4. Инструментальный токарный станок
5. Токарный станок с револьверной головкой и револьверной головкой
6. Специальный
- Колесный токарный станок
- Токарный станок со станиной с зазором
- Т-токарный станок
7.Автоматический токарный станок
Описание и назначение деталей токарного станка:
1. Станина
Станина токарного станка образует основание станка, передняя и задняя бабки расположены на обоих концах станины, а каретка опирается на станина токарного станка и скользит по ней.
Станина токарного станка является направляющим элементом токарного станка, поэтому она должна удовлетворять следующему условию.
- Он должен быть достаточно жестким, чтобы предотвратить прогиб
- Он должен быть массивным, иметь достаточную глубину и ширину для поглощения вибрации
- Он должен сопротивляться скручиванию
- Чтобы избежать деформации
С этой точки зрения, материал станины должен иметь высокую прочность на сжатие, быть износостойкими и поглощать вибрацию.
Чугун, легированный никелем и хромом, является хорошим материалом для станины токарного станка.
2. Передняя бабка
Передняя бабка постоянно закреплена на внутренних направляющих на левом конце станины токарного станка.
По сути, он состоит из полого шпинделя и механизма для приведения в движение и изменения скорости шпинделя.
3. Задняя бабка
Задняя бабка расположена на внутренних направляющих на правом конце станины.
Он имеет два основных назначения:
- Он поддерживает другой конец работы
- Он содержит инструмент для выполнения таких операций, как сверление, развертывание, нарезание резьбы и т. Д.
4. Каретка
Каретка токарного станка имеет различные части, которые служат для поддержки, перемещения и управления режущим инструментом. Ниже представлены следующие детали:
- Седло
- Поперечные салазки
- Составные салазки
- Стойка для инструмента
- Фартук
Седло представляет собой H-образную отливку, которая надевается на станину и скользит по направляющим. Он нес поперечный суппорт и резцедержатель.
Поперечный суппорт состоит из отливки, обработанной на нижней стороне для крепления к седлу, и имеет место на верхней поверхности для резцедержателя или составной опоры.
Составная опора установлена на верхней части поперечной салазки, которая используется для получения угловых пропилов и короткого конуса.
Резцедержатель, расположенный в верхней части компаундной опоры, для удержания инструмента и возможности его установки в рабочее положение.
Тип резцедержателя:
- Резцедержатель с одним винтом
- Стержень для инструмента с четырьмя болтами
- Боковой резцедержатель открытый
- Четырехходовой резцедержатель
Фартук прикреплен к седлу и висит над передней частью станины .
Фартук содержит шестерни, муфты и рычаги для ручного управления кареткой и механических подач.
5. Механизм подачи
Подача — это движение инструмента относительно работы.
Токарный инструмент может иметь три типа подачи:
Токарный станок работает:
Токарный станок — это станок, который удерживает обрабатываемую деталь между двумя жесткими и прочными опорами, называемыми центрами, или в патроне или планшайбе, которая вращается. .
В стойке для инструмента, которая подается против вращающейся части, режущий инструмент жестко удерживается и поддерживается.
Если режущий инструмент подается параллельно или под прямым углом к рабочей оси, выполняются обычные операции резания.
Операция, которая выполняется на токарном станке с удержанием заготовки между центрами или с помощью патрона, следующая:
- Прямое точение
- Обработка уступов
- Снятие фаски
- Нарезание резьбы
- Лицевая сторона
- Накатка
- Наполнение
- Точение конуса
- Эксцентриковое точение
- Полирование
- Обработка канавок
- Прядение
- Обмотка пружины
- Формовка
Операция, которая выполняется путем удержания заготовки с помощью патрона, планшайбы или угловой пластины: следующие:
- Сверление
- Развертка
- Расточка
- Зенковка
- Конусное растачивание
- Нарезание внутренней резьбы
- Нарезание резьбы
- Подрезка
- Отрезка
Операция, выполняемая с использованием специальных приспособлений, следующие: 90 047
Скорость резания:
Скорость резания токарного станка — это скорость, с которой инструмент удаляет металл из заготовки.
На токарном станке — окружная скорость работы за режущим инструментом, выраженная в метрах в минуту.
Скорость резания = Πdn / 1000 м / мин
Где
d = диаметр заготовки (мм)
n = об / мин работы
Подача:
При работе на токарном станке подача режущего инструмента — это расстояние, на которое инструмент продвигается за каждый оборот работы.
Подача выражается в миллиметрах на оборот.
Глубина резания:
Глубина резания — это расстояние по перпендикуляру от поверхности станка до неизрезанной поверхности заготовки.
Глубина резания = d1-d2 / 2
Где,
d1 = диаметр поверхности до обработки
d2 = диаметр обработанной поверхности
Глубина резания изменяется обратно пропорционально скорости резания.
Для общего назначения соотношение глубины резания и подачи варьируется и обычно составляет 10: 1.
Время обработки:
Время обработки на токарном станке можно рассчитать для конкретной операции, если известны скорость выполнения задания, длина подачи задания.
Время обработки = л / с * n мин
Где
l = длина задания в мм
с = подача задания в мм
n = об / мин работы
Безопасность токарного станка меры предосторожности:
При использовании токарного станка необходимо соблюдать меры безопасности, чтобы избежать несчастного случая. Когда мы работаем на токарном станке, нужно помнить следующее.
- Не поддерживайте обрабатываемую деталь руками. Используйте удерживающее приспособление.
- Вместо руки используйте щетку для очистки стружки.
- Нет регулировки во время работы машины.
- Не пытайтесь измерять вращающиеся детали.
- Перед началом работы убедитесь, что все детали надежно закреплены в токарном станке.
- Никогда не кладите инструменты на сверлильный стол.
- Носите защитные очки и избегайте свободной одежды.
- Не держитесь за ручку патрона, прикрепленную к патрону, и она вылетает в момент поворота токарного станка.
- Не касайтесь таблицы байтов вращающимся патроном — есть шанс повредить не только байт, но и сам стол.
Токарный станок — один из самых универсальных станков, используемых сегодня в промышленности. Это важный станок в обрабатывающей промышленности из-за своей универсальности. На одной детали можно изготовить ряд профилей на токарном станке.
Ознакомьтесь со статьями по теме:
Введение в токарный станок
Функции токарного станка
Детали и функции токарного станка
Типы токарных станков
Токарный станок в рабочем состоянии
Работа на токарном станке
Типы режущего инструмента для токарного станка
Сигнатура режущего инструмента
Меры безопасности на токарном станке
Скорость резания на токарном станке
Глубина подачи резания и время обработки токарного станка
Изучение различных частей токарного станка
Токарный станок — это основной станок, используемый в обрабатывающей промышленности.Среди прочего, с его помощью можно резать, шлифовать и точить заготовки. Не путать с фрезерными станками, токарные станки предназначены для вращения заготовки относительно инструмента. Заготовка вращается относительно неподвижного инструмента, такого как лезвие или сверло. Хотя существуют разные типы токарных станков, большинство из них имеют несколько основных деталей, облегчающих их работу.
Кровать
Станина — это большая горизонтальная конструкция или балка, которая используется для поддержки других частей токарного станка, таких как передняя бабка и задняя бабка.За исключением токарных станков по дереву, почти все станки имеют станину. Это длинная платформа, на которой установлены эти детали.
Передняя бабка
На краю кровати находится передняя бабка. После зажима до конца передняя бабка обеспечивает вращательную силу для операций токарного станка. Он содержит подшипники, используемые токарным станком для вращения заготовки относительно резца.
Задняя бабка
Как вы уже догадались, задняя бабка находится на конце токарного станка, противоположном передней бабке.Задняя бабка, также известная как «свободная головка», оснащена невращающимся цилиндром, который можно использовать для различных целей, например, для удержания насадок или поддержки заготовок во время их вращения.
Каретка
Токарные станки также имеют каретку, которая расположена между передней и задней бабками. Каретка отвечает за направление резца при резке заготовки или других манипуляциях с ней.
Ноги
Конечно, ноги — это вертикальные конструкции на токарном станке, которые обеспечивают повышенную рабочую поверхность.Однако токарные станки используют не только ножки любого типа. Из-за большого веса токарные станки коммерческого класса обычно имеют ножки, которые крепятся болтами к полу, на котором он установлен. Прикручивание ножек вниз позволяет токарному станку оставаться устойчивым даже при большой нагрузке.
Поперечный суппорт
Поперечный суппорт — это деталь, находящаяся в верхней части токарного станка, которая позволяет резцу перемещаться вперед и назад.
Седло
Седло находится на вершине токарного станка. Технически седло является частью каретки.Имея H-образную форму, он отвечает за поддержку поперечных движений скольжения.
Фартук
Фартук — это часть токарного станка, закрепленная на опоре. Он предназначен для удержания шестерен, рычагов и других компонентов, которые толкают поперечный суппорт. Наряду с седлом фартук является ключевым компонентом каретки, которая, как упоминалось выше, используется для направления резца токарного станка.
Нет тегов для этого сообщения.
Какие материалы использовать для изготовления станины токарного станка
Токарный станок может быть изготовлен из различных материалов для каждого компонента, например, станины токарного станка.Правильный выбор материалов важен для его устойчивости и долговечности.
Снижение вибрацииМатериалы, которые вы используете, должны подходить для многократного использования и быть долговечными. Одно из основных соображений — это демпфирование. Работа на токарном станке вызывает вибрации, вызванные шумом, механическими колебаниями или переменным током. Демпфирование снижает вибрации за счет рассеивания энергии.
Ниже приводится информация о каждом типе материала, который вы можете использовать, о его качестве демпфирования, а также о его преимуществах и недостатках.
ЧугунЧугун обычно используется для изготовления корпусов оборудования или оснований из-за стабильной структуры материала. Он также известен тем, что сохраняет свою форму, когда подвергается сжатию и расширению из-за колебаний температуры. Это идеально подходит для станины токарного станка, а также используется для изготовления кастрюль для приготовления пищи.
Этот материал обеспечивает хорошее демпфирование, его легко обрабатывать, и его можно производить в различных размерах. Старение материала может занять до года и может быть дороже, чем другие доступные материалы.
Вариант чугуна — Durabar. Он имеет некоторые из свойств обычного чугуна, но материал предварительно состарен, что делает его более дорогим. Он поставляется в стандартных размерах, что может сделать его непрактичным для домашнего использования.
ДеревоСтанина токарного станка по дереву сконструирована как полый ящик. Его легко собрать и недорого сделать. Материал обеспечивает естественное демпфирование.
Древесина имеет некоторые недостатки, так как для изготовления станины токарного станка требуется просверлить и нарезать резьбу много отверстий. Дерево также может коробиться при воздействии экстремальных температур или влаги.
Алюминий — легкий в обработке материал, его можно производить в различных размерах. Его легкий вес облегчает транспортировку токарного станка, однако он обеспечивает плохое демпфирование.
Стальной валИспользование стального вала придает станине токарного станка жесткую и стабильную конструкцию. Размер можно регулировать, и его легко и быстро собрать. Его стоимость умеренная, и он обеспечивает некоторое демпфирование.
Если вы используете этот материал для станины токарного станка, вам нужно будет проделать точное растачивание хвостовой части, передней бабки, хвостовой опоры и каретки.
Бетонная трубаБетонная труба обычно имеет прямоугольную форму. Такая форма позволяет ему быть очень стабильным и жестким, а также иметь различные размеры. Компоненты токарного станка легко прикрепляются. Для обеспечения демпфирования необходимо заполнить внутреннюю полость трубки. Самый эффективный метод будет с бетоном.
ГранитГранит — недорогой материал для станины токарного станка.Он очень жесткий, устойчивый и обеспечивает хорошее демпфирование. Однако, поскольку это натуральный камень, в нем могут быть непредвиденные дефекты. Для любого навесного оборудования токарного станка потребуются анкеры.
Скручивание станины токарного станка | Международная ассоциация пентурнеров
Крис,Поскольку у вас есть индикатор, попробуйте следующее; при пустом гнезде шпинделя,
как в случае отсутствия оправки или мертвой точки, поместите наконечник индикатора ВНУТРИ шпинделя
конус Морзе и проверьте биение там.Это отправная точка для вашего
приводные аксессуары, а если не сразу, то нужно починить = плохие подшипники или дефект
шпиндель.
Если проверка прошла успешно, тогда поставьте свою мертвую точку (вы сказали, что поворачиваете
между центрами) и проверьте биение на центральном наконечнике, прямо там, где втулка
сидит.
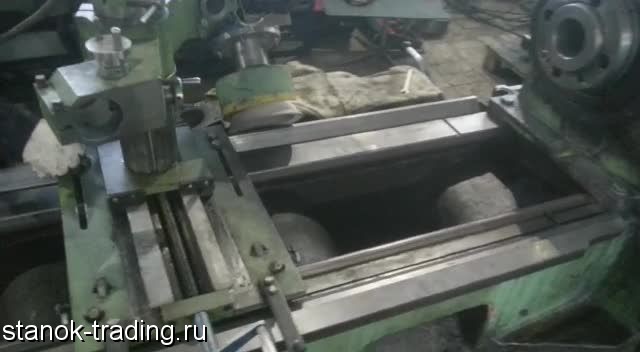
или рифленый? опять же, это может быть проблемой.
На задней бабке проверьте свой живой центр на биение, вам нужно будет осторожно повернуть вручную
с индикатором на кончике.
есть какие-то проблемы? также, как мертвая точка; изношены, рифленые? свободно поворачиваются?
Что касается совмещения передней бабки с задней бабкой, большинство токарных станков не идеальны, на моем
Самолеты Jet 1014 оторваны задней бабкой из стороны в сторону, если смотреть прямо на них.
также был люфт на всей задней бабке, поэтому я решил, что
каждый раз перед фиксацией тяните или поворачивайте его до наилучшего положения.
Достаточно разницы, чтобы не забывать делать это каждый раз.
Полезный совет для задней бабки. Не вытягивайте перо больше, чем необходимо, так как они
изнашиваются, они могут накапливаться, провисать или плавать (как у моего старшего), в результате чего
небольшие проблемы с перекосом.
Я думаю, что Jet хочет, чтобы вы «крутили» или тянули станину токарного станка, чтобы выровнять центры, — это
что это пластырь от основной проблемы.
Я вижу подводные камни (ЕСЛИ это возможно сработало), что происходит, когда
деревянный верстак, который вы тянули к изменениям температуры / влажности / времени года?
также, если вы переезжаете или хотите переместить токарный станок на улицу, чтобы насладиться погодой?
Еще одна проблема, допустим, у вас есть твердый стальной верстак, и вы действительно можете использовать его, как
. попытаться исправить положение.Угадайте, что .. станина токарного станка чугунная и она по
г. ПРИРОДА ХРУПКОЕ. Литой чугун не выдержит ударов или нагрузок, как сталь, а вы могли бы. возможно, в конечном итоге он сломается, если не сначала, то в будущем, поскольку он сидит с натянутым на него напряжением. Интересно, заменит ли Jet его треснувшей кроватью?
Биение оправки могло быть вызвано грязным конусом шпинделя, конусом Морзе
Фитинги на мужских и женских частях должны быть действительно чистыми и без заусенцев.

У вашего OOR много причин, но давайте сначала выровняем ваш токарный станок.
надеюсь, что это некоторая помощь.
Токарный станок с наклонной станиной CNE Серия токарных станков с ЧПУ SUN MASTER Производитель
МОДЕЛЬ | CNE-20 | CNE-26 | ||
---|---|---|---|---|
Вместимость | Кол-во оси управления | 2 оси | ||
Качели над станиной | Ø630 мм (24,8 дюйма) | |||
Стандартный диаметр поворота | h20 …. Ø230 мм (9,05 «) / h22 …. Ø300 мм (11,81 дюйма) | |||
Максимальный диаметр поворота | h20 …. Ø300 мм (11,81 «) / h22 …. Ø340 мм (13,38») | |||
Рабочая длина | 600 мм (23,62 дюйма) | 580 мм (22,83 дюйма) | ||
Передняя бабка и главный шпиндель | Носик шпинделя, внутренний конус | A2-6, Ø69 Конус 1/20 | A2-6, Ø81 Конус 1/20 | |
Отверстие шпинделя | Ø65 мм (2.56 дюймов) | Ø78 мм (3,07 дюйма) | ||
Вместимость прутка | Ø52 мм (2,04 дюйма) | Ø65 мм (2,56 дюйма) | ||
Гидравлический патрон | Ø210 мм (8 дюймов) | Ø254 мм (10 дюймов) | ||
Диапазон частоты вращения шпинделя | 45-4500 об / мин. | 35-3500 об. / Мин. | ||
Идент. Переднего подшипника. шпинделя | Ø100 мм (3,937 дюйма) | Ø120 мм (4.724 «) | ||
Поперечный суппорт (ось X) и каретка (ось Z) | Поперечный ход суппорта (ось X) | h20 .![]() | ||
Продольное перемещение (ось Z) | 610 мм (24 дюйма) | 590 мм (23,23 дюйма) | ||
Серводвигатель переменного тока (ось X) | 1,6 кВт 8 Нм ~ FANUC α8 / 3000i | |||
Серводвигатель переменного тока (ось Z) | 3.0 кВт 12 Нм ~ FANUC α12 / 3000i | |||
Диаметр. шарикового винта (ось X) | Ø32 мм (1,26 дюйма) P5 C3 | |||
Диаметр. шарикового винта (ось Z) | Ø40 мм (1,57 дюйма) P10 C3 | |||
Скорость ускоренного хода (ось X) | 15 м / мин (590 ipm.) | |||
Скорость ускоренного хода (ось Z) | 20 м / мин (787 ipm.) | |||
Подача резания (обе оси) | 0.001-500мм / об. | |||
Револьвер | Инструментальная станция (произвольная) | h20 …. 10 инструментов / H 12 …. 12 инструментов | ||
Размер внешнего токарного инструмента | х20 …. ☐25мм / ч22 …. ☐20мм | |||
Диаметр расточной оправки | h20 …. Ø40 мм (1,575 «) / h22 …. Ø32 мм (1,26») | |||
Задняя бабка | Диаметр пиноли | Ø85 мм (3,346 дюйма) | ||
Пиновый ход | 120 мм (4.72 «) | |||
Конус центра | MT. № 4 | |||
Ход задней бабки | 550 мм (21,65 дюйма) | |||
Двигатель | Главный шпиндель (продолжительный режим) | СТАНД.![]() | СТАНД. AC11кВт (15 л.с.) ОПТ. AC15кВт (20 л.с.) | |
Главный шпиндель (30 мин. Номинал) | СТАНД. AC11кВт (15 л.с.) ОПТ. AC15кВт (20 л.с.) | СТАНД.AC15кВт (20л.с.) ОПТ. 18,5 кВт (25 л.с.) переменного тока | ||
Насос гидравлического масла | 2,2 кВт (3 л.с.) | |||
Насос охлаждающей жидкости | 375 Вт (0,5 л.с.) | |||
Емкость бака | Гидравлический бак | 65 литров (14,3 галлона) | ||
Бак охлаждающей жидкости | 180 литров (39,6 галлона) | |||
Размеры | Вес (нетто / брутто) Прибл. | 5200 кг / 5700 кг | 5500 кг / 6000 кг | |
Размеры упаковки | Длина | 400 мм (157.5 «) | ||
Ширина x высота | Ширина 1890 мм (74,41 дюйма) x высота 2230 мм (87,8 дюйма) |
Технические характеристики могут быть изменены без предварительного уведомления.
Реставрация станины токарного станка | The Hobby-Machinist
Мои мысли, и я не эксперт, но у меня также есть токарный станок с плоскими направляющими (Myford ML7), на котором можно немного поработать, поэтому я подумал о нем с точки зрения среднего возраста. моего 57-летнего токарного станка. Хотя верхние горизонтальные поверхности путей наиболее очевидны и заметны, они наименее важны.Любой износ здесь приведет к тому, что инструмент будет подниматься и опускаться, что приведет только к небольшой разнице в диаметре обрабатываемой детали.
Любой износ вертикальной направляющей поверхности, однако, приведет к перемещению инструмента по направлению к работе и от нее, что приведет к изменению диаметра, равному удвоенному износу. 2) i.е. если исходный диаметр составляет 25 мм, а инструмент перемещается на 1 мм вниз, то новый диаметр равен 25,08 мм.
Итак, я хочу сосредоточиться на вертикальных поверхностях путей. Этот износ также вызывает у меня проблему, заключающуюся в том, что, когда упор седла регулируется так, чтобы он был красивым и твердым на зажимном конце станины, он застревает при перемещении к концу задней бабки, поэтому вы в конечном итоге настраиваете его для неизношенного конца задней бабки и живете на конце патрона он более рыхлый, чем идеальный. Чтобы исправить это, мне нужно удалить немного материала по ширине пути на конце задней бабки, чтобы привести его в соответствие с шириной самой узкой (наиболее изношенной) области.
Я не знаком с Atlas, но когда производился Myford, все четыре вертикальные поверхности направляющих были обработаны, однако на моем только две используются для направления седла (только передняя часть). Две внутренние вертикальные поверхности используются для направления задней бабки. Таким образом, задняя поверхность заднего хода остается нетронутой и является чистой эталонной поверхностью. Некоторые токарные станки «широкий гид» (в том числе и более поздних моделей ML7s) и использовать два внешних способа направлять седло, поэтому было бы один из внутренних вертикальных поверхностей пути, который был лучшим отсчетной поверхности.
Определите, какая у вас наименее изнашиваемая поверхность, и измерьте все относительно этой поверхности, чтобы определить, сколько материала вам нужно удалить, чтобы вернуть все обратно в прямое и параллельное положение. Я подключил свой микрофон, и мне нужно было бы снять максимум 0,05 мм с каждой стороны передней части.
В моем случае я подумываю о том, чтобы следовать методу, который я читал о том, где делается приспособление для работы по эталонной поверхности и шлифования изношенных вертикальных поверхностей обратно до параллельности — я не ищу идеального, но он должен быть в состоянии внести улучшения (и я никак не могу оправдать трату таких денег, которые потребуются на профессиональную переточку).