Способ тепловой обработки силикатного декоративного кирпича
Изобретение относится к производству строительных материалов и изделий, в частности, для тепловой обработки известково-кремнеземистых изделий и силикатного декоративного кирпича.
Известен способ тепловлажностной обработки известково-кремнеземистых изделий автоклавного твердения (патент РФ №2115635, C04B 40/02), включающий подъем давления до 1,0-1,15 МПа и температуры до 183-187°C в течение 1,5-2 ч, выдержку — сначала в среде насыщенного пара в течение 1-3 ч, затем перегретого пара с температурой 200-230°C в течение 10-15 ч, снижение давления и температуры в течение 1,5-2 ч.
Недостатком способа является изменение цвета и качества внешнего вида декоративного силикатного кирпича, снижение прочности за счет вымывания извести с поверхности при запарке холодных с температурой менее 30°C кирпича-сырца.
Известен способ автоклавной обработки цветных силикатных изделий, по заявке на изобретение №2010116744/03, опубликованный 10.
Недостатком способа является недостаточная прочность кирпича, а также ухудшение его внешнего вида.
Предлагаемое изобретение направлено на улучшение качества декоративного силикатного кирпича путем повышения его прочности и сохранения внешнего вида.
Технический результат достигается тем, что в способе тепловой обработки силикатного декоративного кирпича, заключающемся в загрузке кирпича-сырца в автоклав, нагреве кирпича-сырца путем продувки острым паром при атмосферном давлении до температуры 45-50°C, последующем подъеме давления и температуры и выдержке при максимальном давлении и температуре, снижении давления и выгрузке изделий, согласно изобретению после нагрева кирпича-сырца продувкой автоклава острым паром, перед подъемом давления производят выдержку кирпича-сырца в нагретом автоклаве при атмосферном давлении без подачи пара.
Задачей, которую решает предлагаемое изобретение, является улучшение качества силикатного декоративного кирпича путем снижения конденсатообразования на кирпиче-сырце за счет конвекционного нагрева острым продувочным паром с последующим тепломассообменом от нагретого тела автоклава в течение 15 мин. Первый этап тепловой обработки холодных изделий при впуске пара в закрытый автоклав при атмосферном давлении (по прототипу) имеет важное значение, так как температура поверхности изделий ниже температуры водяного пара, теплообмен идет за счет конденсации водяных паров на поверхности изделий. На этом этапе развивается максимальный температурный перепад между средой и поверхностью изделий, равный 30-50°C, пар интенсивно отдает теплоту, но образующийся в большом количестве на поверхности кирпича-сырца конденсат имеет температуру ниже среды, растворяет в себе известь (гидроксид кальция) с поверхности и стекает под действием силы тяжести по вертикальным поверхностям кирпича, а на горизонтальных образует слой воды с известью (раствор извести).
Способ тепловой обработки силикатного декоративного кирпича осуществляется следующим образом.
Опытные партии силикатного декоративного кирпича подвергают тепловой обработке в автоклаве, снабженном источником тепла — паром, термометром и устройством, регистрирующим давление. Кирпич-сырец помещают в автоклав, закрывают крышки и начинают первый этап тепловой обработки, который выполняется в следующей последовательности.
Результаты влияния режима тепловой обработки на свойства силикатного декоративного кирпича приведены в таблице.
Для сравнения для каждого цвета декоративного силикатного кирпича в таблице приведены свойства кирпича, обработанного по способу-прототипу, т.е. в 1 этапе исключается выдержка кирпича-сырца при атмосферном давлении без подачи пара перед подъемом давления.
|
Как видно из таблицы, полученные результаты показывают увеличение прочности при тепловой обработке силикатного декоративного кирпича с предварительным нагревом кирпича-сырца до температуры 45-50°C путем продувки острым паром по изобарному процессу и выдержкой при атмосферном давлении для конвективного теплообмена от нагретого тела автоклава — на белом кирпиче на 28%, на цветных — на 27-30%. При этом кирпич после тепловой обработки имеет однородный цвет поверхности, т.е. сохраняется заданный цвет и внешний вид кирпича.
Предлагаемый способ снижает общее время тепловой обработки и легко осуществим в производственных условиях, поскольку не требует переналадки автоклавного оборудования и позволяет получить продукцию с повышенными техническим характеристиками по прочности и внешнему виду.
Способ тепловой обработки силикатного декоративного кирпича, заключающийся в загрузке кирпича-сырца в автоклав, предварительном нагреве путем продувки паром при атмосферном давлении, закрытии крышек, подачи насыщенного пара, подъеме давления и температуры, выдержке при максимальном давлении и температуре с последующим снижением давления и выгрузке изделий, отличающийся тем, что после продувки автоклава острым паром в течение 0,5 час и нагрева кирпича-сырца острым паром до температуры 45-50°C производят выдержку кирпича-сырца в нагретом автоклаве при атмосферном давлении без подачи пара в течение 15 мин перед подъемом давления.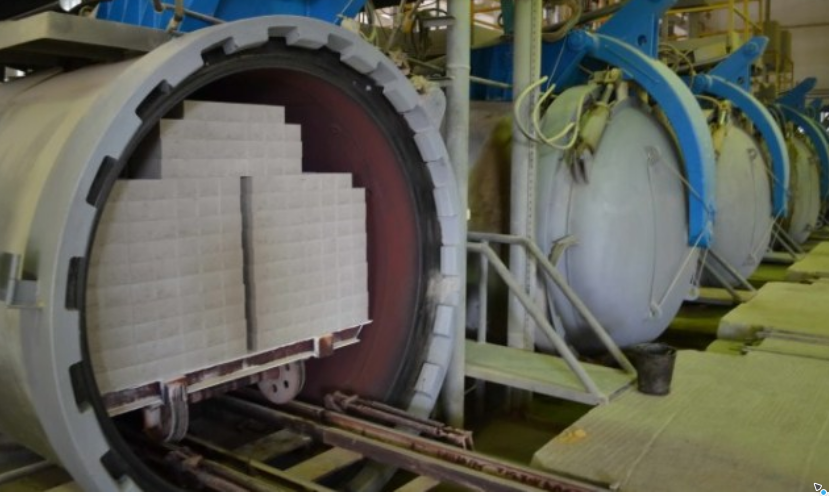
Оборудование для производства силикатного кирпича (с автоклавной обработкой)
|
Технология производства
Краткое описание технологической цепочки изготовления силикатного кирпича (Гиперпрессование):
1. Приём песка и комовой извести(негашёной)
Песок и комовая известь (негашёная) самосвалом выгружаются в бункер, в приямке(на улице). С этого бункера песок или комовая известь(негашёная) автоматически по перекидному наклонному транспортёру и далее по наклонныму транспортёру подаётся на щековую дробилку, где происходит дробление и далее через вибросито по наклонному транспортёру подаётся на верхний перекидной транспортёр и далее на верхний раздаточный транспортёр с которого песок и дроблённая известь (негашёная) при помощи плужковых сбрасывателей поступают в: а) песок в бункера-накопители, б) дроблённая известь(негашёная) в бункер-накопитель извести дроблённой(для измельчения), в) песок в бункер-накопитель песка( для измельчения).
2. Приготовление тонкомолотого песка.
С бункера-накопителя песка(для измельчения) песок по нижнему транспортёру и далее по наклонному транспортёру песок автоматически подаётся в шаровую мельницу где происходит помол до тонины помола 3500-4000кв. см/г. и далее полученный тонкомолотый песок, по пневмоподаче подаётся в бункер-накопитель тонкомолотого песка.
3. Приготовление тонкомолотой извести(негашёной).
С бункера-накопителя по нижнему транспортёру и далее по наклонному транспортёру дроблённая известь(негашёная) автоматически подаётся в шаровую мельницу, где происходит помол до тониты помола 3500-4000кв.см./г. И далее полученная тонкомолотая известь(негашёная),по пневмоподаче подаётся в бункер-накопитель тонкомолотой извести(негашёной).
4. Подача всех компонентов: воды, песка, тонкомолотого песка, тонкомолотой извести в бункера-дозаторы.
С бункера-накопителя песка по нижнему транспортёру и далее по перекидному транспортёру и далее по наклонному транспортёру песок автоматически подаётся в бункер-дозатор песка.
С бункера-накопителя песка тонкомолотого по нижнему шнеку и далее по наклонному шнеку тонкомолотый песок автоматически подаётся в бункер-дозатор тонкомолотого песка.
С бункера-накопителя извести тонкомолотой по нижнему шнеку и далее по наклонному шнеку тонкомолотая известьавтоматически подаётся в бункер-дозатор тонкомолотой извести.
С Ёмкости воды по трубе водаавтоматически подаётся в ёмкость-дозатор воды.
Все бункера-дозаторы и ёмкость-дозатор расположены над планетарным бетоносмесителем.
5. Приготовление рабочей смеси(песок, тонкомолотый песок, вода и тонкомолотая известь).
С бункеров-дозаторов песок и тонкомолотый песок через дозаторы в нужной пропорции автоматически подаются в планетарный смеситель, где тщательно перемешиваются. Потом с ёмкости-дозатора воды, через дозатор в нужной пропорции автоматически подаётся водаи всё тщательно перемешивается. Датчик влажности автоматически контролирует подачу водыв нужной пропорции. Потом с бункера-дозатора через дозатор в нужной пропорции автоматически подаётся тонкомолотая известь(негашёная). И все компоненты тщательно перемешиваются в планетарном бетоносмесителе и далее эта приготовленная рабочая смесь автоматически по наклонному транспортёру и по верхнему раздаточному транспортёру, при помощи плужковых сбрасывателей подаётся в бункер-реактор.
6. Бункер-реактор. Приготовление силикатной смеси.
Поступившая в бункер-реактор рабочая смесь будет находиться там до 2 часов. Там будет происходить гидротация извести: присоединение молекул воды к молекулам извести, в результате чего получается гидратная известь. При гашении извести происходит выделение тепла и нагрев силикатной смеси до 90 градусов. И одновременно происходит усреднение(гомогенизация) силикатной смеси. Бункер-реактор является промежуточной ёмкостью для хранения и снабжения гиперпресса силикатной смесью.
7. Приготовление формовочной силикатной смеси.
С бункера-реактора по нижнему транспортёру силикатная смесь автоматически подаётся в планетарный бетоносмеситель, где дополнительно тщательно перемешивается и доувлажняется до влажности формовочной силикатной смеси необходимой для формования кирпича-сырца. Температура формовочной силикатной смеси 50 градусов. Датчик влажности автоматически регулирует подачу нужного количества воды. Всё тщательно перемешивается и формовочная силикатная смесь через люк подаётся в бункер Гиперпресса.
8. Формовка кирпича-сырца
С бункера формовочная силикатная смесь автоматически подаётся на гиперпресс, где происходит формование кирпича-сырца давлением = 275кг/кв.см. За один цикл формуется: 4шт. или 8шт. или 16шт..(на плашок), цельный или пустотелый кирпич-сырец или пазо-гребневые блоки. После прессования кирпич-сырец (или пазо-гребневые блоки) автоматически передвигаются на приёмный стол, откуда автомат-укладчик по 8шт. или по 16шт. за цикл автоматически переносит и укладывает кирпич-сырец на пустые тележки автоклавные в стопу по 512шт.(для автоклавов D=1620мм.) или по 1280шт. (для автоклавом D=2420мм.) Далее тележки автоматически доставляются к автоклавам.
9. Автоматическая Линии доставки:а) тележки автоклавной с кирпичом-сырцом к автоклаву
Тележка автоклавная с стопой 512шт. или с стопой 1280шт. .с кирпичом-сырцом по линии доставки, через поворотные круги автоматически доставляется и останавливается напротив нужного автоклава, у которого торцевые крышки открыты. Поворотный круг автоматически поворачивает тележку автоклавную на 90 градусов. Толкатель автоматически заталкивает тележку автоклавную с стопой 512шт. или с стопой 1280шт. кирпича-сырца. в автоклав. С противоположного конца автоклава тележка автоклавная с стопой 512шт. или с стопой 1280шт. изготовленного силикатного кирпича выталкивается на линию доставки тележки автоклавной с силикатным кирпичом на поворотный круг напротив укладчика стопы 512 шт. на деревянный поддон и к линии доставки пустой тележки автоклавной к гиперпрессу. И так цикл за циклом пока автоклав не будет заполнен полностью кирпичом-сырцом. Торцевые крышки автоклава закрываются.
10. Автоклавная обработка(автоклав проходной)
Основной технологический процесс образования силикатного кирпича происходит в автоклаве. Кварцевый песок в автоклаве образует поверхностный растворимый оксид кремния SIO2, который реагирует гидроокисью кальция и водой и образует гидросиликат кальция. Где при температуре 175 — 210 градусов и при давлении 10-16 Бар (Атм.) образования гидросиликата кальция и перекристаллизации их гидрат окиси кальция в результате химической реакции кирпич-сырец приобретает прочность силикатного кирпича марки: М:150-250. Время нахождения а автоклаве= (1,5 часа выдержка) + (6 часов при температуре 175-210 градусов и давлении 10-16 Бар(Атм)) + (1,5 часа остывание).
11. Автоматическая Линия доставки тележки автоклавной с силикатным кирпичом от автоклава к укладчику стопы 512шт. или стопы 1280шт. на деревянный поддон
Тележка автоклавная с стопой 512шт. или с стопой 1280шт. силикатного кирпича выкатившаяся из автоклава на поворотный круг, автоматически делает поворот на 90 градусов на поворотном кругу и далее автоматически передвигается кареткой с толкателями на поворотный круг напротив укладчика стопы.
12. Укладчик-автомат стопы 512шт. силикатного кирпича с тележки автоклавной на деревянный поддон
От автоклава тележка автоклавная с стопой 512шт. силикатного кирпича автоматически передвигается и останавливается на поворотном кругу напротив укладчика стопы. Укладчик стопы автоматически сжимает стопу 512шт. силикатного кирпича и переносит её на деревянный поддон, который установлен на цепном транспортёре на линии доставки на холодный склад, а пустая тележка автоклавная передвигается к укладчику-сырца.
13. Автоматическая Линия доставки пустой тележки автоклавной от укладчика стопы 512шт. к укладчику-сырца.
Когда укладчик стопы перенёс стопу 512шт. с силикатным кирпичём на деревянный поддон, пустая тележка автоклавная на поворотном кругу делает поворот на 90 градусов и автоматически передвигается кареткой с толкателями к укладчику-сырца. И весь цикл повторяется вновь.
14. Упаковщик-автомат стопы 512шт. в полиэтиленновую плёнку
Деревянный поддон с стопой 512шт. силикатного кирпича по цепному транспортёру автоматически передвигается к упаковщику. где деревянный поддон с стопой 512шт. на поворотном кругу вращается и упаковывается в полиэтиленновую плёнку.
15. Линия отправки стопы 512шт. упакованной в полиэтиленновую плёнку на холодный склад
После упаковки стопы 512шт. силикатного кирпича в полиэтиленновую плёнку на деревянном поддоне установленному на цепном транспортёре автоматически передвигается за стены здания для складирования на холодном складе при помощи автокара.
Пульт управления электронный для управления всеми механизмами и гидрораспределителями с электромагнитным управлением. Вся технологическая линия работает автоматически.
Виды изделий:
|
Как было отмечено, известь используется также при производстве автоклавных (силикатных) материалов и изделий. ![]() Автоклав — аппарат, закрывающийся герметически, предназначенный для обработки изделий насыщенным водяным паром под давлением выше атмосферного (рис. А.49). Промышленные горизонтальные автоклавы изготавливаются из листовой стали и имеют форму цилиндра диаметром 2,0-2,2 м, длиной 17-24 м. Автоклав закрывается крышками либо с одной стороны (тупиковый), либо с двух сторон (проходной) и рассчитан на рабочее давление 8-16 атм. По окончании загрузки автоклава крышки герметически закрываются и начинается гидротермальная обработка путем подачи водяного пара от котельной. Процесс автоклавной обработки можно подразделить на три периода (рис. 5.9). В течение первого периода производят подъем давления насыщенного водяного пара от атмосферного до заданного. Продолжительность периода 1-4 ч, иногда его подразделяют на два этапа: 1. Подъем температуры с начала пуска пара в автоклав до установления температуры 100 °C; 2. Повышение температуры от 100 °C до максимальной. ![]() Первый период характеризуется значительным перепадом температур на поверхности и в центре изделия, иногда достигающим 30-50 °C. Поэтому температуру и давление в этот период следует повышать медленно, быстрое повышение может привести к разрушению изделий под действием термических напряжений. Второй период называется изотермической выдержкой, в это время в автоклаве поддерживаются требуемые температура и давление водяного пара. Продолжительность второго периода до 9 ч. В течение третьего периода давление водяного пара в автоклаве постепенно снижается от требуемого до атмосферного (продолжительность 1-5 ч). Третий период, так же как и первый, иногда разделяют на два этапа: от начала выпуска пара до температуры 100 °C и от 100 °C до 18-20 °C. В этот период также возможно разрушение изделий за счет интенсивного парообразования в порах при быстром снижении давления и возникающих при этом термических напряжений. Перечисленные периоды автоклавной обработки оказывают существенное влияние на фазовый состав и структуру как связки, так и искусственного камня в целом. ![]() Режим подбирают так, чтобы получить изделия с требуемыми строительно-техническими свойствами при минимальных затратах. Важными технико-экономическими показателями автоклавной технологии являются степень заполнения автоклава изделиями и продолжительность обработки. Продолжительность автоклавной обработки в заводских условиях составляет от 10 до 16 ч при давлении 8 атм (0,8 МПа) и температуре 174 °C. Автоклавная обработка сырьевых смесей, состоящих из кварцевого песка и извести, изменяет характер процессов твердения и является основной стадией производства силикатных (автоклавных) материалов. При гидротермальной обработке известь взаимодействует с SiO2 кварца с образованием низкоосновных гидросиликатов кальция переменного состава: хСаО * ySiО2 * zh3О. Основность образующихся гидросиликатов (CaО/SiО2) изменяется в пределах от 0,8 до 1,5 и более. Целью автоклавной (гидротермальной) обработки является синтез гидросиликатов, которые являются связующим веществом (связывают зерна кварцевого песка и образуют искусственный камень высокой прочности). Технические свойства силикатных изделий определяются основностью и микроструктурой образующихся гидросиликатов кальция. Последние, в свою очередь, изменяются в зависимости от состава сырьевой смеси, дисперсности компонентов и режима автоклавной обработки. Автоклавная технология позволяет получать изделия полной заводской готовности за 10-15 ч. Автоклавная обработка широко применяется при производстве следующих видов строительных изделий: силикатного кирпича; изделий из плотных силикатных бетонов — панелей внутренних несущих стен, перекрытий и покрытий; изделий из ячеистых бетонов — крупноразмерных панелей, блоков, а также теплоизоляционных материалов. |
История ООО КЗССМ
Далеко не каждое предприятие в Казани может гордиться столь весомой и насыщенной событиями биографией. В ноябре 1930 года на северной окраине города заработал силикатный завод «Имени 1 Мая» — одно из первых предприятий стройиндустрии Татарстана. Его проектная мощность составляла 30 млн. штук силикатного кирпича в год, основные производственные операции тогда выполнялись вручную. В 1931 году завод выпустил 10 млн. штук кирпича.
За восемь десятков прошедших лет завод кардинально расширил ассортимент выпускаемой продукции, открыл новые цеха и разросся территориально. С 2003 года завод начал производство цветного силикатного кирпича, в 2005 году построен новый цех по производству блоков из ячеистого бетона, с 2008 по 2015 год произведена замена более половины прессового оборудования на новые – импортные, которые позволили получать изделия с улучшенными физико-техническими характеристиками и идеальной геометрией. В 2015году в состав ООО «КЗССМ» в качестве третьего производства вошел завод ЖБК, где за восемь месяцев 2015 года проведена глубокая модернизация технологии и оборудования производства железобетонных изделий: полностью заменено оборудование бетоносмесительного участка на новое импортное, установлено и введено в эксплуатацию оборудование по автоматизированной раздаче бетона по участкам формовочного цеха и смонтирована линия безопалубочного формования по производству пустотных плит перекрытия. В настоящее время продолжаются работы по реализации крупной инвестиционной программы на первом производстве завода.
Качество и оптимальные цены выпускаемой продукции, ее постоянно растущий ассортимент позволяют ООО «КЗССМ» занимать ключевые позиции на рынке строительных материалов Республики Татарстан.
История силикатных изделийКирпич — один из традиционных строительных материалов. Силикатный кирпич — искусственный безобжиговый стеновой материал, основу которого составляют известь (6-11%), песок (90-95%) и вода. Смесь данных компонентов прессуется, затем в процессе автоклавирования под действием пара высокого давления и температуры приобретает твердость и прочность. Через некоторое время материал готов к использованию на стройплощадке.
Более сотни лет силикатная промышленность производит экологически безупречный строительный материал из естественного сырья, минеральный состав силикатного кирпича в точности соответствует опорному корсету естественно образовавшегося известняка. Из блоков известняка возведены знаменитые Египетские пирамиды, древние мастера-каменотесы выполнили свою работу ювелирно: в щель между блоками не вставишь и лезвия ножа.
Научно-технический прогресс, индустриализация, породили потребность найти новые, надежные, быстро производимые, дешевые строительные материалы.
Знаковым стало событие, произошедшее 5 октября 1880года. Именно тогда доктор Михаэлис получил в Берлине патент на изготовление силикатного кирпича с применением автоклавной обработки сырца. Технологический процесс формовки путем прессования с последующей автоклавной обработкой вот уже более ста лет составляет основу промышленного производства силикатных изделий.
Россия одна из первых стран в мире, где был запущен массовый выпуск силикатного кирпича. К 1901 г. в России было уже 9 заводов, которые выпускали 150 млн. шт. силикатного кирпича в год. К концу 20-х. началу 30-х г.г. XX столетия начинается промышленное производство из силикатного кирпича в России, именно в это время вводятся в строй основные производственные площадки по всей стране.
К концу XX — началу XXI века производители налаживают выпуск цветного силикатного кирпича. Окрашенный кирпич применяется для облицовочных работ, возводимые здания приобретают черты индивидуальности, города приобретают краски. Начинается выпуск облицовочного кирпича с колотой и рустированной поверхностью, имитацией сколов природного камня — еще один инструмент воплощения идей дизайнеров и архитекторов.
Налаживается производство крупно — и мелкоформатных блоков, nepегородочных межквартирных и межкомнатных изделий. Средства малой механизации в сочетании с применением крупноформатных изделий увеличивают скорость строительства.
Сегодня силикатные изделия – отличный экологически безупречный строительный материал, прочный, надежный долговечный и функциональный.
Силикатные материалы и изделия
Категория: Материалы для строительства
Силикатные материалы и изделия
Силикатные изделия представляют собой искусственный каменный материал, изготовленный из смеси извести, песка и воды, отформованный путем прессования под большим давлением и прошедший автоклавную обработку.
В строительстве широкое распространение получили силикатный кирпич; силикатный плотный бетон и изделия из него; ячеистые силикатные бетоны и изделия; силикатный бетон с пористыми заполнителями.
Силикатный кирпич прессуют из известково-песчаной смеси следующего состава (%): чистый кварцевый песок 92—94; воздушная известь 6—8 и вода 7—8. Подготовленную в смесителях известково-песчаную массу формуют на прессах под давлением 15—20 МПа и запаривают в автоклавах при давлении насыщенного пара 0,8 МПа и температуре примерно 175 °С.
При запаривании известь, песок и вода вступают в реакцию, в результате которой образуется гидросиликат кальция, цементирующий массу и придающий ей высокую прочность. Продолжительность цикла автоклавной обработки 10—14 ч, а всего процесса изготовления силикатного кирпича 16—18 ч, в то время как процесс изготовления обычного глиняного кирпича длится 5—6 сут.
Силикатный кирпич выпускается двух видов: одинарный размером 250 X 120 X 65 мм и модульный размером 250 X 120 X 88 мм. Объемная масса силикатного кирпича 1800—1900 кг/м3, морозостойкость не ниже Мрз 15, водопоглощение 8—16% по массе. По прочности при сжатии силикатный кирпич делится на пять марок : 75, 100, ’25, 150 и 200. По теплопроводности силикатный кирпич незначительно отличается от обычного- глиняного и вполне заменяет последний при кладке стен любых зданий, кроме стен, маледящнхея в условиях высокой влажности или подвергающихся воздействию высоких температур (печи, дымовые трубы). По цвету силикатный кирпич светло-серый, но может быть и цветным, окрашенным в массе введением в нее минеральных пигментов.
Изделия из плотного силикатного бетона. Мелкозернистый плотный силикатный бетон — бесцементный бетон автоклавного твердения на основе известково-кремнеземистых или известково-зольных вяжущих — получают по следующей технологической схеме: часть кварцевого песка (8—15%) смешивается с негашеной известью (6—10%) и подвергается тонкому помолу в шаровых мельницах, затем измельченное известково-песчаное вяжущее и обычный песок (75—85%) затворяют водой (7—8%), перемешивают в бетономешалках и затем смесь поступает на формовочный стенд. Отформованные изделия запаривают в автоклавах при температуре 175—190° С и давлении пара 0,8 и 1,2 МПа.
Изделия из плотного силикатного бетона имеют объемную массу 1800—2200 кг/м3, морозостойкость 25—50 циклов, прочность при сжатии 10—60 МПа.
Из плотного силикатного бетона изготовляют крупные полнотелые стеновые блоки, армированные плиты перекрытий, колонны, балки, фундаментные и цокольные блоки, конструкции лестниц и перегородок.
Силикатные блоки для наружных стен и стен во влажных помещениях должны иметь марку не ниже 250.
Изделия из ячеистого силикатного бетона. По способу образования пористой структуры ячеистые силикатные бетоны бывают пеносиликатные и газосиликатные.
Основным вяжущим для приготовления этих бетонов является молотая известь. В качестве кремнеземистых компонентов вяжущего и мелких заполнителей используют молотые пески, вулканический туф, пемзу, золу-унос, трепел, диатомит, трас, шлаки.
При изготовлении ячеистых силикатных изделий пластичную известково-песчаную массу смешивают с устойчивой пеной, прчго- товленной из препарата ГК, мыльного корня и др. , или с газооб- разователями — алюминиевой пудрой, а затем смесь заливают в формы и подвергают автоклавной обработке.
Объемная масса пеносиликатных изделий и газосиликатных изделий 300—1200 кг/м3, прочность при сжатии 1—20 МПа.
По назначению ячеистые силикатные изделия делятся на теплоизоляционные объемной массой до 500 кг/м3 и конструктивно-теплоизоляционные объемной массой более 500 кг/м3.
Теплоизоляционные ячеистые силикаты находят применение в качестве утеплителей, а из конструктивно-теплоизоляционных силикатов изготовляют наружные стеновые блоки и панели, а также комплексные плиты покрытий здания.
Изделия из силикатного бетона на пористых заполнителях. В качестве вяжущего силикатного бетона на пористых заполнителях используют тонкомолотые известково-кремнеземистые смеси, а крупными заполнителями служат керамзит, пемза, поризованные шлаки и другие пористые легкие природные и искусственные материалы в виде гравия и щебня. После автоклавной обработки такие бетоны приобретают прочность при сжатии от 3,5 до 20 МПа при объемной массе от 500 до 1800 кг/м3 и из них в основном изготовляют блоки и панели наружных стен жилых и общественных зданий.
Материалы для строительства — Силикатные материалы и изделия
Силикатный кирпич | АО Силикат
Технологическая линия по производству силикатного кирпича Описание технологического процесса производства силикатного кирпичаПесок, просеянный на струнном сите, автомобильным транспортом подается в цех и складируется в расходных бункерах.
Дробленая известь, полученная из известняка путем его обжига в шахтной печи, поступает на помол в шаровые мельницы СМ-1456А, а затем пневмотранспортом подается в расходные бункера извести нового цеха.
Песок и известь из расходных бункеров подаются в двухвальный смеситель для приготовления силикатной смеси, сюда же дозатором подается вода для увлажнения смеси.
Силикатная масса после двухвального смесителя распределяется по реакторам непрерывного действия для гашения.
Продолжительность нахождения смеси в реакторах должна обеспечивать полное гашение извести в смеси. Смесь по запросу от прессов из реакторов поступает в двухвальные смесители для домешивания и доувлажнения.
Готовая формовочная смесь подается на пресса для формования кирпича или камней. Сформованный кирпич-сырец снимается с прессов и укладывается штабелеукладчиком на пропарочную вагонетку.
Пропарочные вагонетки с сырцом транспортируются электропередаточным мостом в автоклавы проходного типа. Тринадцать из них работают при максимальном давлении 15 атм., а остальные два – при 12 атм.
Длительность автоклавной обработки зависит от величины избыточного давления пара (температуры) и вида продукции. После обработки вагонетки с кирпичом с помощью электропередаточного моста с лебедкой выгружаются из автоклава.
Далее готовый кирпич подается на участок пакетирования, где происходит разделение штабеля на два пакета с обвязкой их упаковочной лентой в горизонтальном и вертикальном направлениях, а также упаковкой стретч-пленкой.
Затем упакованный кирпич транспортируется на склад готовой продукции.
Отгрузка кирпича производится мостовыми кранами и вилочным погрузчиком.
Линия силикатного кирпича — Оборудование из Китая
Оборудование из Китая для производства силикатного кирпича отличается высокой производительностью, надежностью и достойным качеством. Обратитесь в нашу компания за предоставлением подробного технико-коммерческого предложения, с указанием технических параметров линии, вариантов размещения оборудования, цены и способов доставки оборудования.
Мы поставляем не только целые технологические линии по производству силикатного кирпича, но и предлагаем услуги по модернизации уже существующих силикатных заводов. осуществляем проектирование, шефмонтаж и обучение персонала.
Автоматизированная линия производства силикатного кирпича на базе гидравлического пресса модели KDQ1300 (сжимающая сила до 130000 кН) способна производить за один цикл 48/24 шт. условного кирпича с глухими отверстиями. Гидравлический пресс выполняет формование кирпичей со скоростью 3.5 удара/мин. Ежегодная производительность такой линии составляет 60 млн. единиц продукции.
Пресс модели KDQ1300 оснащен большими гидравлическими цилиндрами, которые формируют необходимый объем сжимающей силы. Шатун такого цилиндра выполняет удары глубиной до 680мм. Высота зажима пресса (вертикальное расстояние между рабочей поверхностью и дном гидравлического пресса) равна 1290 мм.
Широкий ассортимент гидравлических прессов насчитывает несколько современных моделей, в том числе гидравлический пресс для изготовления стандартного силикатного кирпича, кирпичей с глухими отверстиями, бетонных блоков с глухими отверстиями и блоков со сквозными отверстиями. Для изготовления различных форм и размеров кирпичей достаточно использования одного гидравлического пресса. Максимальные размеры готового изделия составляют 480×240×190 мм.
Автоматизированный кран-делитель использует специальные зажимы для того, чтобы отделять кирпичи друг от друга, переносить их на транспортные тележки для последующей перевозки в складское помещение. Данный тип оборудования имеет современный дизайн конструкции и состоит из рамы и подъемного крана (механизма подъема/опускания материала). Уникальная технология контроля скорости позволяет оборудования с высокой точностью и безопасностью выполнять транспортировку кирпичей.
Специальная система обеспечивает контроль всего процесса транспортировки кирпичей к автоклавам и возвращение форм к первоначальной рабочей зоне. Эта система практически не требует ручного управления, а значит, увеличивает производительность, снижает нагрузку операторов и коэффициент наличия субъективных ошибок.
Технологический процесс производства силикатного кирпича
Краткое описание технологического процесса силикатного завода из Китая
1. Приготовление сырья на силикатном заводе
Комовая известь загружается в приемный бункер, вибрационным питателем подается в щековую дробилку, где происходит дробление до размеров менее 25 мм. Вибропитателем дробленая известь направляется в накопитель шаровой мельницы. Пыль, выделяемая технологическим оборудованием улавливается циклонами с осевым вентилятором. После шаровой мельницы молотая известь ковшовым элеватором подается в расходный бункер молотой извести. С нижней части бункера тонкомолотая известь винтовым конвейером подается в бункер дозатор. После автоматического дозирования, материал подается на смеситель. Песок необходимой фракции подается в смеситель.
2. Приготовление силикатной смеси
Смесь, после перемешивания в смесителе подается на наклонный ленточный конвейер и распределяется в силоса-реактора. В силосах-реакторах происходит гашение извести, и обволакивание гашеной тонкодисперсной извести частицами песка. С помощью питателя, готовая с заданной температурой смесь направляется в планетарный смеситель для перемешивания и доувлажнения силикатной смеси до формовочной влажности (4-6%).
3. Формование силикатного кирпича на китайском прессе
Готовая для формования силикатная смесь, ленточным конвейером подается в приемный бункер пресса. Дозированное количество силикатной смеси по конвейерной ленте подается в пресс для формования кирпича-сырца. Формованный кирпич отбирается захватом автомата-укладчика и укладывается на автоклавные вагонетки. Подача порожних автоклавных вагонеток, позиционирование и отвод заполненных автоклавных вагонеток в зоне действия пресса производится автоматикой самого пресса. Пресс из Китая для производства силикатного кирпича отличается достойным качеством по привлекательной цене.
Технические параметры пресса
Модель | KDQ680 | KDQ1100Z | KDQ1300 |
Производительность в год | 30 млн. | 50 млн. | 60 млн. |
Максимальная сила прессовки, кН | 6800 | 11000 | 13000 |
Максимальная толкающая сила, кН | 1300 | 2000 | 2500 |
Максимальная глубина удара, мм | 540 | 580 | 680 |
Высота хода, мм | 1200 | 1450 | 1600 |
Количество обрабатываемых кирпичей за один цикл, шт | 24 | 32 | 48 |
Мощность, кВт | 75 | 90 | 90 |
youtube.com/embed/-FXFjS9-1Tg»/>
4. Автоклавная обработки силикатного кирпича.
Автоклавы из Китая для пропарки силикатного кирпича
В автоклав помещают автоклавные вагонетки с кирпичом-сырцом. Количество одновременно автоклавируемых вагонеток с кирпичом-сырцом зависит от диаметра и длины автоклава. Плавно в течение 2,5 часов давление пара плавно повышается 0.8+1,2 МПа, температура в автоклаве достигается +170+190°С. В течении 7 часов происходит происходит процесс автоклавной обработки. После этого, в течении 1.5 часов снижают давление в автоклаве. Общее время выдержки составляет около 12 ч. Автоклавные вагонетки с силикатным кирпичом перемещают на секцию упаковки. Готовую продукцию упаковывают. После очистки, порожние автоклавные вагонетки с помощью передаточной тележки возвращаются обратно в прессовое отделение.
Автоклав из Китая для силикатного завода характеризуется долгим сроком службы и простым обслуживанием.
Временной цикл
- Время смешивания: 4-6 минут
- Время созревания: 2.
5~3 часа
- Время вторичного смешивания: 4-5 минут
- Формование: 3-3.5 раз/ минуту
- Система автоклавного твердения
- До-после автоклавирования: 0,5 ч
- Вакуумирование: 0,5 ч (0~-0.05 мПа)
- Подъем давления: 1,5 ч (0.05~1.3 мПа)
- Выдержка давления: 6ч (1,3 мПа)
- Понижение давления: 1,5 ч (1.3~0 мПа)
- Итого: 10 ч
(PDF) Кирпичи из золы-уноса, автоклавированные паром на основе извести
4. Краткое изложение результатов и заключение
Свойства образцов зольной пыли-песчано-извести
(обозначенных как T23 и T24), полученных в оптимальных условиях
Результаты суммированы и сопоставлены со свойствами
полнотелого глиняного кирпича типа 1,8 / 100 в соответствии со Стандартом Турции
dard TS 705 в Таблице 4.
В этом исследовании были получены следующие результаты:
Кирпич из парового автоклавного твердения может производиться с использованием золы y
, производимой на электростанции Seyito
mer, песка и извести.
Отмечено положительное влияние добавки песка на прочность кирпича на сжатие
. Двадцать процентов
добавки песка было оценено как оптимальное.
Оптимальная добавка извести была определена как 12%.
Давление формования кирпича имеет большое положительное влияние на
механическую прочность кирпича. Однако формирование
давлений выше 20 МПа имеет неблагоприятный эффект.
Оптимальное давление в автоклаве и время отверждения были
, определенные как 1.5 МПа и 6 ч соответственно.
Прочность на сжатие кирпичей, изготовленных из кварцевого песка
, выше, чем у кирпичей, изготовленных из
из речного песка.
Объемный удельный вес кирпича с добавлением кварцевого песка
составляет 1,15 г / см
3
, тогда как удельный объемный вес кирпича с добавлением речного песка
составляет 1,27 г / см
3
. Таким образом, удельный объемный вес
кирпичей из плёнки намного ниже, чем у традиционных глиняных кирпичей
.
Водопоглощение золо-силикатного кирпича
колеблется от 30% до 40%.
Теплопроводность золо-силикатного кирпича
со значением 0,34–0,36 Вт м
1
K
1
намного ниже
, чем у традиционной глины. кирпичи.
Флаконово-силикатный кирпич, произведенный в данном исследовании
, кажется подходящим для использования в качестве строительного материала. Производство кирпича этого типа
, безусловно, внесет
в переработку летучей золы и, следовательно, минимизирует негативное воздействие свалок летучей золы на окружающую среду.На
, с другой стороны, сокращение использования глины для производства
обычных глиняных кирпичей поможет защитить окружающую среду
. Кроме того, будут сокращены вредные выбросы от
печей для обжига глиняного кирпича. Значительно малый объемный вес
и низкая теплопроводность
кирпичей из плоской золы уменьшат затраты на строительство и тепло-
Затраты на охлаждение / охлаждение зданий
Благодарность
Авторы выражают признательность O
¨ztu
¨re Holding A.С. / Измир
за поддержку.
Ссылки
[1] Аль-Вакил Э.И., Эль-Кораши С.А., Уоссеф Х.Н. Промотирующий эффект
зародышей фазы C – S – H на построение фазы гидрата силиката кальция. Cem
Concr Res 1999; 21: 173–80.
[2] Болл М.С., Кэрролл РА. Исследования гидротермальных реакций пылевидной золы UK
. Часть 1: реакции между измельченной топливной золой и гидроксидом кальция
. Adv Cem Res 1999; 11 (2): 53–61.
[3] Баоджу Л., Ёцзюнь Х, Шицюн З., Цзянь Л.Некоторые факторы, влияющие на раннюю прочность на сжатие
парового бетона с ультрамелкой золой.
Cem Concr Res 2001; 31: 1455–8.
[4] Баят О. Характеристика турецких пеплов. Топливо 1998; 77 (9–10):
1059–66.
[5] Baykal G, Do
¨ven AG. Утилизация летучей золы в процессе гранулирования;
теория, области применения и результаты исследований. Ресур Консерв Реси
2000; 30: 59–77.
[6] Гони С., Герреро А., Луксан депутат, Масиас А.Активация пуццолоновой реакции зольной пыли
в гидротермальных условиях. Cem Concr Res
2003; 33: 1399–405.
[7] Айер Р.С., Скотт Дж. А.. Электростанция y ash — обзор использования добавленной стоимости
за пределами строительной отрасли. Консерв
Реси 2001; 31: 217–28.
[8] Климеш Д.С., Рэй А. Влияние размера частиц кварца на образование гидрограната
во время автоклавирования при 180 ° C в CaO – Al
2
O
3
–SiO
2
–H
2
O
система.Cem Concr Res 1998; 28: 1309–16.
[9] Ma W, Brown PW. Гидротермальные реакции золы с Ca (OH) 2
и CaSO4 2h3O. Cem Concr Res 1997; 27: 1237–48.
[10] Пэн Г, Фэн Н, Чан SYN. Образование и прочность кристаллического гидрата силиката кальция
, полученного путем однократной обработки в автоклаве. Adv
Struct Eng 1999; 2 (3): 191–7.
[11] Пимракса К., Вильгельм М., Кохбергер М., Врусс В. 2001. Новый подход
к производству кирпича из 100% летучей золы,
Международный симпозиум по утилизации золы.Доступно по адресу: http: //
www. Fl yash.info/agenda.html.
Таблица 4
Свойства золо-силикатного кирпича, полученного в оптимальных условиях
Кварцевый песок (0,2 мм) Речной песок (1 мм) Полнотелый глиняный кирпич TS 705
Песок (%) 20 Тип кирпича: 1,8 / 100
Летучая зола (%) 68
Известь (%) 12
Влажность (%) 14 —
Давление формования (МПа) 20 —
Давление в автоклаве (МПа) 1,5 —
Время отверждения (ч ) 6 —
Объемный вес (г / см
3
) 1.14 1,27 1,8
Теплопроводность (Вт м
À1
K
À1
) 0,34 0,36 0,7
Прочность на сжатие (МПа) 10,25 7,8 мин. 7,8
Водопоглощение (%) 40,5 32,8 макс. 18
Т. Чичек, М. Танрыверди / Строительство и строительные материалы 21 (2007) 1295–1300 1299
Кирпичей Калси — Начало нового предприятия в мире масонства. | by Insight-The Evolving Perceptions
В кладке используются различные типы кирпичей на основе таких материалов, как глина, бетон, известь, летучая зола и т. д.В современном мире каждому нужно укрытие для выживания, поэтому существует альтернативный метод производства кирпичей из песка и извести. В этой статье представлены процесс производства, история и различные испытания силикатного кирпича кальция.
Свежий кирпич CalsiИстория
Процесс изготовления кирпича из песка был открыт и запатентован доктором Уильямом Михаэлисом в 1880 году. Это правда, что Peppel 2 распознает силикатный кирпич с помощью других процессов, и в литературе можно найти многочисленные утверждения относительно «силикатного кирпича», изготовленного в Нью-Джерси около 1860 года.На самом деле этот материал представлял собой строительный кирпич, состоящий из обычного известкового раствора, которому придана форма и который позволил затвердеть. Насколько можно узнать, ни один из этих ранних процессов не оказался коммерчески успешным. Все силикатные кирпичи, которые сейчас продаются в мире, производятся в соответствии с основными принципами, закрепленными в оригинальном патенте Михаэлиса. Он позволил своему патенту истечь без использования. Практически сразу последовало несколько доработок.
Введение
Кирпичи из силиката кальция подходят как для наружных, так и для внутренних стен.Они доступны в виде облицовочного кирпича или обыкновенного кирпича. Кирпичи из силиката кальция состоят из песка, извести с высоким содержанием кальция и воды, широко известной как силикатный кирпич. Эти кирпичи используются для различных целей в строительной отрасли, таких как декоративные работы в зданиях, кладочные работы и т. Д.
Силикатный кирпич широко используется в европейских странах, Австралии и странах Африки. В Индии эти кирпичи широко используются в штате Керала, и их использование быстро растет.
Партия переработанных кирпичей CalsiМатериалы, используемые для силикатных кирпичей
Песок и гашеная известь, эти два вида сырья приобрели коммерческое значение во всем мире при производстве кирпичей Calsi.
Перечисленные ниже материалы в основном используются для производства кирпичей Calsi.
и. Песок:
Песок является основным компонентом кирпичей из силиката кальция. Песок используется в двух пропорциях. Часть его вступает в реакцию с известью, образуя связующий материал из силиката кальция. В то время как остальные песчинки составляют совокупность, которая связана вместе и образует основную часть кирпича. В первой пропорции очень важно, чтобы песок был как можно более мелким.Хороший практический подход заключается в том, что около 15% песка должно проходить через сито 100 меш. Оставшиеся 85% песка предназначены для образования инертного наполнителя или основной массы кирпича. Кирпичи из силиката кальция содержат большое количество песка, то есть 88–92%. Это означает, что свойства этих кирпичей зависят от свойств используемого песка. Таким образом, используемый песок должен быть хорошо рассортирован и не должен содержать никаких примесей, таких как органические вещества, растворимые соли и т. Д. Может присутствовать мелкодисперсная глина, но только до 4%, которая уплотняет кирпич и обеспечивает более гладкую текстуру.Для большей прочности желательно иметь по возможности более крупное зерно.
ii. Известь:
Доля извести, используемая в кирпиче кальси, относительно очень мала, но, помимо этого, они имеют первостепенное значение. Содержание извести в силикатно-кальциевых кирпичах колеблется от 8 до 12%. Используемая известь должна быть хорошего качества с высоким содержанием кальция. Перед прессованием кирпичей известь должна быть идеально гидратирована. В противном случае он будет расширяться во время обработки паром и производить внутренние напряжения, которых достаточно часто, чтобы разрушить кирпич.Известь также должна быть достаточно едкой, чтобы легко смешиваться с песком.
iii. Вода:
В процессе производства должна использоваться чистая вода. Морская вода, вода, содержащая растворимые соли или органические вещества более 0,25%, не подходят.
iv. Пигмент:
Пигменты обычно используются для придания цвета кирпичам. Их смешали с песком и известью. Общий вес кирпича содержит от 0,2 до 3% количества пигмента.Различные пигменты, используемые для получения разных цветов, как указано в таблице ниже:
Процесс производства силикатного кирпича
- На первом этапе подходящие пропорции песка, извести и пигмента тщательно смешиваются с 3-5% воды. . Образуется паста формовочной плотности.
- Смесь формуют в кирпичи с помощью пресса с вращающимся столом, который использует механическое давление для прессования кирпичей. Давление прессования варьируется от 31.От 5 до 63 Н / мм2.
- На заключительном этапе кирпичи помещаются в автоклав. Автоклав представляет собой стальной цилиндр с герметичными концами. Автоклав имеет длину около 20 метров и диаметр 2 метра.
- После помещения кирпичей в эту закрытую камеру давление насыщенного пара сбрасывается, составляющее примерно 0,85–1,6 Н / мм2. Температура внутри камеры повышается, и начинается химическая реакция.
- Содержание кремнезема в песке и содержание кальция в извести вступают в реакцию с образованием кристаллического соединения, называемого гипосиликатом кальция.Этот процесс длится от 6 до 12 часов. Наконец, полученные кирпичи вывозят на рабочее место.
Испытания силикатного силиката кальция
i. Прочность на раздавливание:
Прочность на раздавливание кирпича измеряется нагрузкой, которую он может выдержать, когда он уложен на плоскую поверхность, и нагрузка равномерно распределяется по верхней и нижней части. Полученные результаты будут отличаться в зависимости от процедуры тестирования, которая может отличаться.Скорость приложения нагрузки может вызвать явное изменение измеренной прочности на раздавливание. Если нагрузка применяется резко, результаты могут быть выше, чем они должны быть. Немецкие спецификации для силикатного кирпича требуют прочности на раздавливание 140 кг / см2 (2000 фунтов на квадратный дюйм). Строительный кодекс, изданный Нью-Йорком в 1905 году, определяет, что средняя прочность на раздавливание для пяти кирпичей должна быть не менее 3000 фунтов на квадратный дюйм, ни один кирпич не падает ниже 2500 фунтов на квадратный дюйм.
ii.Поперечная прочность:
Поперечная прочность кирпича измеряется путем поддержки кирпича с обоих концов и приложения нагрузки посередине до разрыва. Он указывает на сопротивление, которое кирпич может оказать любой силе, пытающейся его согнуть. Вкратце, он состоит из установки кирпича на двух параллельных опорах на расстоянии 7 дюймов друг от друга. Нагрузка прикладывается тупым острием, которое прижимается к кирпичу на полпути между опорами и параллельно им. Кирпич испытан ровным.Очевидно, что нагрузка, необходимая для разрушения кирпича, будет зависеть от ширины и глубины, а также от расстояния между опорами. Поэтому разрывная нагрузка сообщается редко, поскольку для этого потребуется подробное описание испытания. Фактором, который включает в себя все эти переменные, является модуль разрыва (MOR). Это равно 1,5-кратной разрывной нагрузке, умноженной на расстояние между опорами и деленной на ширину кирпича, умноженную на квадрат его толщины.
Преимущества кальциево-силикатного кирпича
Кальциево-силикатный кирпич имеет много преимуществ при использовании в кладке:
- Для оштукатуривания требуется небольшое количество раствора.
- Эти кирпичи обладают низкой теплопроводностью.
- Эти кирпичи однородны по цвету и фактуре.
- Прочность на сжатие силикатного кирпича составляет около 10 Н / мм2. Таким образом, они хорошо подходят для многоэтажных домов.
- В случае силикатного кирпича проблема высолов не возникает.
- Силикатный кирпич обеспечивает больший комфорт и доступность для архитекторов, позволяющих достичь желаемых форм и дизайнов.
- Эти кирпичи имеют точную форму, размер с прямыми краями, а также жесткую и легкую плотность 250 кг / м3.
- Уменьшается воздействие солнечного тепла на открытые стены из силикатно-кальциевого кирпича.
- Цветные силикатные кирпичи не требуют отделки стен, поэтому их стоимость снижается.
- Эти кирпичи обладают высокой огнестойкостью и водоотталкивающими свойствами.
- Стены из силикатного силикатного кирпича устойчивы к внешнему шуму.
- Эти кирпичи имеют низкую усадку и низкую удельную теплоемкость, негорючие и неагрессивные свойства.
- Стоимость строительства снижается примерно на 40% от общей стоимости за счет следующих факторов:
a.Затраты силикатно-кальциевых продуктов очень меньше.
г. Требуется меньшее количество раствора.
г. Толщина стенки может быть уменьшена за счет высокой прочности на сжатие.
Недостатки кальциево-силикатного кирпича
В некоторых условиях кальциево-силикатный кирпич не подходит, и его недостатки следующие:
- При наличии большого количества глины глиняные кирпичи более экономичны, чем кальциево-силикатные кирпичи.
- Они не подходят для закладки фундамента, так как не могут обеспечить водонепроницаемость в течение длительного времени.
- Они не могут противостоять огню в течение более длительного периода времени, следовательно, они непригодны для строительных печей и т. Д.
- Стойкость к истиранию у этих кирпичей очень низкая, поэтому их нельзя использовать для тротуаров.
Статья Автор:
Мухаммад Датский
Экспериментальное исследование фундаментальных механических свойств автоклавного силикатного кирпича Masonr
[1] GB11945-1999 , кирпич силикатный автоклавный.Пекин: China Architecture and Building Press, 1999. На китайском языке.
[2] GBJ129-96, Основные механические свойства метода испытаний каменной кладки.Пекин: China Architecture and Building Press, 1996. На китайском языке.
[3] JGJ98-2000, Проектирование строительного раствора по порядку ведения заседания.Пекин: China Architecture and Building Press, 2000. На китайском языке.
[4] JGJ70-90, Основные методы испытаний строительных растворов.Пекин: Китайская архитектурно-строительная пресса, 1990. На китайском языке.
[5] ШИ Чу-Сянь. Теория и проектирование конструкции кладки [M].. Пекин: China Architecture and Building Press, 2003, 11. На китайском языке. На китайском.
[6] GB50003—2001, Правила проектирования каменной кладки.Пекин: China Architecture and Building Press, 2001. На китайском языке.
[7] Гуй-Цю Лю. Основные исследования механического поведения каменной кладки [D]: докторская диссертация Хунаньского университета, Хунань: Институт гражданского строительства Хунаньского университета, 2005, 4.На китайском.
[8] Чжун-Цзи Чжан, Вэй-Цзюнь Ян. Тестовое исследование оптимального сочетания прочности блока и раствора для кладки из автоклавного силикатного кирпича [J].Мир плитки, 2007, 3: 31-34. На китайском.
DOI: 10.4028 / www.scientific.net / amr.168-170.1299
автоклав силикатного кирпича делая машину автоклав песка
Машина для производства песчаной извести в автоклаве высокого давления
Машина для производства силикатного кирпича автоклавная ДА-06 (18 л)… 1000LPH SS304 высокоэффективный завод фильтра очистки воды Ro с УФ стерилизатором. … а также от стерилизатора песка ce rohs и того, является ли стерилизатор песком оборудованием для радиационной стерилизации оборудованием для стерилизации паром под давлением или оборудованием для стерилизации сухим жаром.
Уточнить ценуоборудование для производства кирпича для автоклавов — Продажа промышленных автоклавных котлов
Производитель машин AAC и газоблоков от donyue group. наша машина aac aac , машина для производства пеноблоков, машина для производства силикатного кирпича в автоклаве.Линия по производству автоклавного кирпича из строительных отходов. кирпичи из промышленных отходов технологии производства и другое вспомогательное оборудование для производства.
Уточнить ценумашина для производства силикатного кирпича в автоклаве
Машина для производства силикатных блоков в автоклаве под высоким давлением. Ручная машина для производства силикатного кирпича. особенности машины для производства силикатного кирпича. Наша машина — это машина для формования кирпичей без горения. когда он работает, машина производит кирпичи с помощью простого процесса.Между тем, конструкция машины полностью закрыта для предотвращения попадания пыли. поэтому машина имеет характеристику
Узнать ценуПростой в использовании автоклав для кирпича — Alibaba
Машина для производства силикатного кирпича в автоклаве Машина для производства пенобетона в автоклаве Машина для производства пенобетона в автоклаве. US $ 799.00- $ 999.00 / Комплект. 1 компл. (Мин. Заказ) Провинция Хэнань Город Гунъи Восточно-Китайская металлургическая фабрика по производству угольных шахт. CN 2 ГОДА. 96,9% ответов. Связаться с поставщиком.
Уточнить ценуaac машина для производства кирпича паровая стерилизация промышленная…
Автоклав AAC может быть очень большим сосудом высокого давления для паровой отверждения, поэтому автоклав является основным инструментом для производства пеноблоков и пенобетона. Наш высокопроизводительный горизонтальный цилиндрический автоклав AAC изготовлен из высококачественной стали, используемой для изготовления кирпича из паровой золы, силикатного кирпича, шлакового кирпича, ячеистого бетона Подробнее
Узнать ценуавтоклав для кирпича, автоклав для кирпича Поставщики и …
Цена блоковAac в Индии Автоклавный автоклав из бетонного кирпича Aac Aac для производства силикатного кирпича.800000,00 $ / Набор. Получите информацию об образце. 1 компл. (Минимальный заказ) CN Guangxi Hongfa Heavy Machinery Co., Ltd. 4 года. 4.9 (2) Связаться с поставщиком. Добавить в избранное.
Уточнить ценуавтоклав для кирпича, автоклав для кирпича Поставщики и …
Автоклав / автоклав для бетона для кирпича А-класса для автоклава для производства кирпича / блоков из летучей золы. Типы: трубчатый реактор, резервуарный реактор, реактор со слоем твердых частиц, башенный реактор, струйный реактор и другие нетипичные реакторы. 2). 5. Услуги по обучению: Мы также проводим необходимое обучение по эксплуатации и ежедневному техническому обслуживанию котлов для местных рабочих.1).
Уточнить ценуЧто такое автоклавный кирпич? — Quora
Автоклавные кирпичи — это кирпичи, отвержденные паром под давлением. Преимущество заключается в том, что кирпич затвердевает менее чем за 10 часов по сравнению с более чем 10 днями. Прочность на сжатие автоклавного кирпича у нас намного выше. Когда автоклавирование используется в сочетании с …
Узнать ценуКачественная известковая сера для промышленности — Alibaba
Китай Профессиональный дизайн большой паровой автоклавный станок для производства песчано-известкового кирпича. 8900 долларов.00- 78 000,00 долл. США / компл. 1.0 комплект (минимальный заказ) 12 лет CN. Поставщик. Связаться с поставщиком. 1/4. Шнековая подача дешевого оборудования для упаковки мешков серного порошка и цемента. Готов к отправке. 308,00 $ / шт. 1 шт. (Минимальный заказ) $ 1475,00 / шт. (Доставка) 1 год CN.
Уточнить ценумашина для производства кирпича в автоклаве, машина для производства кирпича в автоклаве …
Эта машина для производства силикатного кирпича в автоклаве QT6-15 подходит для производства высококачественного прочного кирпича. С изменением формы модели стало возможным изготовление пустотелого кирпича, кирпича с несколькими отверстиями, жаропрочного кирпича, кирпича для защиты откосов, кирпича для травяных насаждений и т. Д.5.Подробная информация о машине для производства пустотелых кирпичей QTY5-15: 6.Наш пустотелый кирпич …
Узнать ценуaac машина для производства кирпича паровая стерилизация промышленная …
Автоклав AAC может быть очень большим сосудом высокого давления для паровой отверждения, поэтому автоклав является основным инструментом для производства пеноблоков и пенобетона. Наш высокопроизводительный горизонтальный цилиндрический автоклав AAC изготовлен из высококачественной стали, используемой для изготовления кирпича из паровой золы, силикатного кирпича, шлакового кирпича, ячеистого бетона Подробнее
Узнать ценуАвтоклавирование — Машины для производства кирпича и блоков Titan
При производстве силикатного кирпича, блоков и других изделий обычно используются автоклавы длиной до 36 метров, с разными диаметрами (2, 2.4 м) и толстые стены (до 14-18 мм). Агрегаты автоклавов могут работать при давлении 8-16 атмосфер.
Уточнить ценуАвтоклавы — Brickwell
Автоклав — это большое паровое оборудование, которое может использоваться для пропаривания силикатного кирпича, золы-уноса, шлакового кирпича, воздушного бетонного блока, цементной сваи и других цементных изделий. Наша компания может производить все виды автоклавов в соответствии с требованиями пользователей, чтобы удовлетворить требования приложения.
Уточнить ценуАвтоклав для силикатного кирпича — Промышленный котел
22 августа 2018 г. Кирпич — Википедия. Первые кирпичи были высушенными, но процесс отверждения мог ускоряться за счет применения тепла и давления в автоклаве.Кальций-силикатный кирпич. Кирпичи из силиката кальция или силикатные кирпичи для кладки. Кирпичи из силиката кальция изготавливаются из песка и извести и известны как силикатные кирпичи.
Уточнить ценуВысокотехнологичная машина для производства блоков из силикатного кирпича для автоклава AAC
Высокотехнологичная машина для производства блоков из силикатного кирпича в автоклаве AAC. Кирпич из автоклавного газобетона (AAC) — это легкий, многоячеистый новый строительный материал; К особенностям относятся более низкая плотность, теплоизоляция, возможность, огнестойкость и звукоизоляция.
Уточнить ценупроизводители силикатного кирпича
Лайм. Продукты извести от производителей Китая и Тайваня поставщики Покупают известь, детали извести производителей извести Импорт Экспорт, Оптовая продажа, Поставщики, Завод по производству извести, машина для производства кирпича-уноса, машина для производства силикатного кирпича, машина для производства бетонных блоков в автоклаве, легкая машина для производства блоков aac, смешивание и литейная машина, электроника.
Уточнить цену Цена машины кирпича автоклава, кирпич 2021 автоклава…
Цена на машину для производства кирпича в автоклаве— Выберите высококачественную машину для производства кирпича в автоклаве 2021 года по лучшей цене от сертифицированных китайских производителей кирпичной машины, поставщиков автоклавов в Китае, оптовых торговцев и фабрики на Made-in-China
Получить ценуавтоклав для кирпича, автоклав для кирпича Поставщики и …
Автоклав / автоклав для бетона для кирпича А-класса для автоклава для производства кирпича / блоков из летучей золы. Типы: трубчатый реактор, резервуарный реактор, реактор со слоем твердых частиц, башенный реактор, струйный реактор и другие нетипичные реакторы.2). 5. Услуги по обучению: Мы также проводим необходимое обучение по эксплуатации и ежедневному техническому обслуживанию котлов для местных рабочих. 1).
Уточнить цену Поставщики производителей автоклавов для извести— made-in-china
Сохранение физического здоровья может помочь вам оставаться здоровым и эмоционально. Если вы правильно питаетесь и поддерживаете форму, ваше тело будет сильным и поможет вам справиться со стрессом.
Узнать ценуКитай открывающийся вверх автоклав AAC Песок извести …
Автоклав AAC, Машина для производства блоков AAC, производитель / поставщик автоклавов в Китае, предлагающая машина для автоклава AAC с восходящим отверстием Конвейер и так далее.
Уточнить ценуКитайская машина для производства песка AAC в автоклаве с машиной для производства кирпича …
Автоклав, Автоклав AAC, Производитель / поставщик автоклавного оборудования в Китае, предлагает автоклав для песка AAC с машиной для производства кирпича, Самая популярная крупномасштабная производственная мощность в Китае Поставщик автоматических бетонных блоков Qt10-15, лучший полностью автоматический полый и твердый бетонные блоки Машина для производства кирпича и машина для производства брусчатки и так далее.
Уточнить ценуавтоклав бетонные изделия блок машина блок машина
Цена на оборудование для газоблока автоклавного газобетонаAAC… Газоблочное оборудование Aac Block Machine Hf Автоклав. 5. Производственная линия AAC / Производственная линия по производству газобетона в автоклаве 1) Вес продукта должен соответствовать 600 кг / м3. 2) годовая мощность 300000м3. 3) заданная пропорция сырья: цемент 6,5% известь 23% летучая зола 68% гипс 3% порошок алюминиевой пасты 350 г / м3. 4) вода и
Узнать ценуПроизводители известково-песчаного кирпича Поставщики, Китай известковый песок …
производитель / поставщик силикатного кирпича, список заводов производителей силикатного кирпича в Китае, быстро найдите квалифицированных китайских производителей, поставщиков, фабрики, экспортеров оптовиков на сайте Made-in-China…. Автоклав AAC с высоким давлением пара Машина для производства песчано-известковых блоков AAC.
Уточнить ценуПроизводство силикатного кирпича — Система управления автоклавом …
В частности, на больших заводах по производству силикатного кирпича рекомендуется немедленно повторно использовать пар, образующийся во время сброса давления. Это можно использовать для оптимизации и снижения энергозатрат на процесс закалки. С системой управления автоклавом Masa он
Узнать ценуМашина для производства силикатного кирпича для автоклава / мелкий песок…
Найдите машину для производства силикатного кирпича в автоклаве / Мелкую машину для производства песка / завод по дроблению медной руды от китайского производителя, фабрики, завода и поставщика — Shanghai Minggong Heavy Equipment Co., Ltd. на ECVV
Узнать ценуАвтоклавирование — Машины для производства кирпича и блоков Titan
При производстве силикатного кирпича, блоков и других изделий обычно используются автоклавы длиной до 36 метров, с разным диаметром (2, 2,4 м) и толщиной стенок (до 14-18 мм).Агрегаты автоклавов могут работать при давлении 8-16 атмосфер.
Уточнить ценуМашина для производства силикатного кирпича в автоклаве в Циндао, Китай
Автоклавная машина для производства силикатного кирпича в Циндао, Китай … Передвижная или стационарная разделительная машина для AAC. Производительность: долгая жизнь и высокая эффективность. Бренд: Сунит. Сырье: Летучая зола \ Цемент \ Известь. Емкость: 30000-300000 куб.м в год. Качество: хорошее.
Уточнить ценуВысокотехнологичная машина для производства блоков из силикатного кирпича для автоклава AAC
Высокотехнологичная машина для производства блоков из силикатного кирпича в автоклаве AAC.Кирпич из автоклавного газобетона (AAC) — это легкий, многоячеистый новый строительный материал; К особенностям относятся более низкая плотность, теплоизоляция, возможность, огнестойкость и звукоизоляция.
Уточнить ценуПроизводство силикатного кирпича Masa Group
Гидравлический пресс для силикатного кирпича Masa HDP. Сердцем завода по производству силикатного кирпича, несомненно, является пресс Masa, например. тип HDP 800. Masa может предложить различные типы прессов для различных требований к производительности. В полностью автоматических гидравлических прессах силикатная смесь прессуется в кирпичи.
Уточнить ценуАвтоклав для силикатного кирпича — Промышленный котел
22 августа 2018 г. Кирпич — Википедия. Первые кирпичи были высушенными, но процесс отверждения мог ускоряться за счет применения тепла и давления в автоклаве. Кальций-силикатный кирпич. Кирпичи из силиката кальция или силикатные кирпичи для кладки. Кирпичи из силиката кальция изготавливаются из песка и извести и известны как силикатные кирпичи.
Уточнить ценуКитай Автоматическая линия по производству силикатного кирпича — Китай…
С помощью шарнирно-сочлененного робота, ременного шкива и автоматического крана-штабелера зеленый кирпич укладывается на тележку автоклава. 4. Автоматическая линия по производству силикатного кирпича. Отверждение и хранение. Тележка автоклава, на которой уложены зеленые кирпичи, будет отправлена в автоклав для отверждения с помощью перетягивающего устройства.
Уточнить ценупроизводители силикатного кирпича
Лайм. Продукты извести от производителей Китая и Тайваня поставщики Покупают известь, детали извести производителей извести Импорт Экспорт, Оптовая продажа, Поставщики, Завод по производству извести, машина для производства кирпича-уноса, машина для производства силикатного кирпича, машина для производства бетонных блоков в автоклаве, легкая машина для производства блоков aac, смешивание и литейная машина, электроника.
Уточнить ценуЗавод вулканизационных автоклавов, Купить хорошую цену Сварка …
Текстильный химический бетонный блок автоклава для пропаривания силикатно-известкового кирпича под высоким давлением. Химический промышленный бетонный сосуд под давлением автоклава AAC с насыщенным паром. Промышленный автоклав для бетона Ø 3,2 м / Завод блоков AAC для блока из газобетона. Автоклав для дерева. Пневматические промышленные автоклавы под давлением для дерева / кирпича / резины / пищевых продуктов, Φ1,65 м
Уточнить ценуВысокоточная машина для производства блоков AAC, силикатный кирпич AAC…
вверх открывая автоклав машины автоклава AAC / блока извести песка AAC / блока золы уноса AAC 1. Характер продукции: 1) Автоклав является ключевым оборудованием, которое широко применяется на фабрике строительных материалов для автоклавированного лечения различных видов строительных материалов.
Уточнить ценуКитайская линия по производству кирпича для автоклавов, линия по производству кирпича для автоклавов …
Китай производители линии автоклавного кирпича — выберите высококачественные продукты линии автоклавного кирпича 2021 по лучшей цене от сертифицированной китайской производственной линии, поставщиков машинной линии, оптовых торговцев и фабрики на Made-in-China
Получить ценуaac машина для производства кирпича паровая стерилизация промышленная…
Автоклав AAC может быть очень большим сосудом высокого давления для паровой отверждения, поэтому автоклав является основным инструментом для производства пеноблоков и пенобетона. Наш высокопроизводительный горизонтальный цилиндрический автоклав AAC изготовлен из высококачественной стали, используемой для изготовления кирпича из паровой золы, силикатного кирпича, шлакового кирпича, ячеистого бетона Подробнее
Узнать ценуКитайская линия по производству песчаной извести или летучей золы AAC 300000 м3 …
Машина для производства блоков, Оборудование для производства кирпича, Производитель / поставщик оборудования для производства бетонных блоков в Китае, предлагает линию по производству песчаной извести или летучей золы AAC 300000 м3 — 400000 м3, Машина для производства кирпичных бетонных блоков Полностью автоматический ленточный конвейер, Продажа машин для производства кирпича Полностью автоматический ленточный конвейер и так далее.
Уточнить цену Оборудование автоклава кирпича известки песка парадеревянное с автоматическим управлением, Φ2.85m
Паровое оборудование для автоклава из песчано-известкового кирпича с автоматическим управлением, Φ2.85m
Краткие сведения:
Среда: воздух
Рабочая температура: 150 ° C Тип
: Промышленные автоклавы
Применения: Дерево, кирпич, резина, Пищевая, стекольная промышленность
Описание:
Широко используется в автомобильной, аэрокосмической, оборонной промышленности, отделке зданий и т. Д.Он оборудован предохранительным клапаном, манометром, температурным элементом и так далее.
Автоклав для стекла — это разновидность ключевого оборудования, которое используется для глубокой обработки стекла. Обеспечение требований безопасности к многослойному стеклу с помощью процесса термообработки и давления.
Помимо механических и пневматических способов открывания двери, он также имеет блокировку безопасности. Внутри автоклава есть нагревательные элементы для нагрева и нагнетания, а также устройство охлаждения. Он будет автоматически контролировать и определять открытие и закрытие дверей, температуру, давление в автоклаве с помощью контроллера ПЛК, что является прецессией стеклянной заготовки.
Технические характеристики:
Позиции | Агрегат | Технические характеристики и параметры | |||||||||
FJK1.4-1.65 902D × FJK1.4-1.65 902D | FJK1.5-2.5 × 5D | FJK1.5-2.68 × 5D | FJK1.5-2.85 × 5D | ||||||||
Внутренний диаметр | 906 1.652 | 2,5 | 2,68 | 2,85 | |||||||
Эффективная длина | M 19 2 | 5 | 5 | ||||||||
Расчетное давление | МПа | 1.4 | 1,5 | 1,5 | 1,5 | 1,5 | |||||
Расчетная температура | ° C 19 | 150000150 | 150 | ||||||||
Рабочее давление | МПа | 1.3 | 1,4 | 1,4 | 1,4 | 1,4 | |||||
Рабочая температура | ° C | 150000° C 19 150000 | 150 | 150 | |||||||
Средний | воздух | воздух | воздух 02 воздух | воздух 906 Калибр | MM | 900 | 1000 | 1000 | 1000 | 1000 | |
Эффективный объем | M3 | 10 | 10 | 31 | |||||||
Вес брутто | T | 7 | 9 | 16 | 25 0003 0 M 6 × 2.5 × 3 7 × 2,8 × 3 7 × 3 × 3,5 7,8 × 3,2 × 3,8 9 × 3,5 × 5 |
9024
1. Деревообрабатывающая промышленность
2. Кирпичная промышленность
3. Резиновая промышленность
4. Пищевая промышленность
5. Стекольная промышленность
Конкурентное преимущество:
Автоклав — это разновидность крупномасштабного парового оборудования.Его можно использовать для пропаривания силикатного кирпича, кирпича из золы, шлакового кирпича, газобетонных блоков, цементных свай и других цементных изделий. Кроме того, он также широко применяется для глубокой обработки стекла, дерева, резины, теплоизоляционных материалов, медицины, высокопрочного гипса, калибровки в промышленности рыболовных сетей и т. Д. Мы можем изготовить автоклавы различных форм в соответствии с требованиями наших клиентов.
Эксперты В нашей компании используются преимущества зарубежных аналогичных продуктов, и улучшен расчет прочности путем анализа основных частей, работающих под давлением, и проведения всевозможных стресс-тестов.
Оборудование автоклава кирпича известняка пара деревянное с автоматическим управлением, Φ2.85m Изображений |
Экспериментальные исследования золопесочно-известковых кирпичей с добавлением гипса
Ключевые слова: уголь зола уноса, конструкционный кирпич, песок, гипс, микроструктура, свойства
Американский журнал материаловедения и технологий , 2013 1 (3),
С. 35-40.
DOI: 10.12691 / материалы-1-3-2
Поступило 14.08.2013 г .; Отредактировано 26 августа 2013 г .; Принята в печать 28 августа 2013 г.
Авторские права © 2013 Издательство «Наука и образование». Все права защищены.1. Введение
Пылевидная зола, широко известная как летучая зола, является полезным побочным продуктом тепловых электростанций, использующих пылевидный уголь в качестве топлива.Высокая температура горения угля превращает глинистые минералы, присутствующие в угольном порошке, в плавленые мелкие частицы, в основном содержащие силикат алюминия. Полученная таким образом летучая зола обладает как керамическими, так и пуццолановыми свойствами. Летучая зола — опасные отходы. Проблема с летучей золой заключается не только в том, что для ее удаления требуется большое количество земли, воды и энергии, ее мелкие частицы, если с ними не справиться должным образом, в силу своей невесомости, могут попасть в воздух. Известно, что при неправильной утилизации летучая зола загрязняет воздух и воду и вызывает респираторные проблемы при вдыхании.
Во всем мире около 20% летучей золы используется в приложениях, связанных с бетоном. В основном CaO – SiO 2 –H 2 O и CaO – Al 2 O 3 — SiO 2 –H 2 O-фазы способствуют упрочнению [1, 2] . Летучая зола также используется во многих различных областях, таких как краски, пластмассы и в сельском хозяйстве [3, 4, 5, 6, 7] . В Бангладеш ежегодно производится около 0,6 миллиона тонн летучей золы, и ее производство, вероятно, значительно возрастет, поскольку будущие электростанции в Бангладеш, вероятно, будут работать на угле.С другой стороны, использование летучей золы пока не пользуется популярностью. Сообщается, что небольшое количество импортной летучей золы используется при производстве цемента в Бангладеш. Жизнеспособным вариантом массового использования летучей золы могло бы стать производство конструкционного кирпича, содержащего летучую золу в качестве основного ингредиента. Производство обычных глиняных кирпичей предполагает потребление большого количества глины. Это истощает верхний слой почвы и вызывает деградацию сельскохозяйственных земель. Если можно будет производить кирпичи из летучей золы, не содержащие глины, это не только поможет сохранить верхний слой почвы, но и снизит экологические проблемы, вызванные сбросом летучей золы.
В этом исследовании была сделана попытка произвести легкие кирпичи для строительных конструкций с использованием летучей золы, образующейся на ТЭЦ Барапукурия.
2. Материалы и методы
Для изготовления кирпича использовались смеси летучей золы, песка и гашеной извести с гипсом в качестве связующего. Были оптимизированы такие параметры процесса, как состав смеси, давление, условия отверждения и т. Д. Наконец, были определены свойства кирпичей, произведенных в оптимальных условиях.
Летучая зола, использованная в этом исследовании, была собрана с Барапукурийской ТЭС. Остальные ингредиенты — гашеная известь, песок и гипс — были собраны на местном рынке. Основные ингредиенты летучей золы представлены в таблице 1.
Таблица 1. Химический состав летучей золы Барапукурийской ТЭЦ
Образцы кирпича были изготовлены в условиях, указанных в таблице 2. По крайней мере, пять кирпичей были изготовлены для каждого типа образца. Перед изготовлением кирпича каждый ингредиент сырья сушили в муфельной печи при 110 ℃ в течение 24 часов.Взвешивали необходимое количество каждого ингредиента, добавляли 14% влаги и тщательно перемешивали компоненты. Чтобы обеспечить одинаковый размер кирпичей, каждый раз для заполнения полости формы использовалась известная масса смеси. Размер отверстия полости формы составлял 6 х 3,5 см. Гидравлический пресс использовался для приложения давления в течение 15 секунд (Рисунок 1). Затем кирпичи (рис. 2) были извлечены и окончательно отверждены. Отверждение производилось на воздухе с использованием водного спрея, путем помещения кирпичей под влажную ткань и выдерживания кирпичей в воде.Кирпичи, сформированные под различным давлением, также подвергались отверждению в течение разных периодов времени в оптимальных условиях отверждения.
Рисунок 1 . Гидравлический пресс
Рисунок 2 . Кирпич зольный, силикатно-известково-гипсовый
2.1. Методы испытаний2.1.1. Прочность на сжатие
Прочность на сжатие определяли путем приложения нагрузки к образцу с использованием универсальной испытательной машины.Нагрузка была приложена к площади размером 6 мм х 3,5 мм [размер одной стороны всего кирпича].
2.1.2. Микроструктура
Образцы наблюдали под оптическим микроскопом (ОМ), а микрофотографии записывали с помощью цифровой камеры (OPTIKA Microscope B-600 MET) для исследования пористости. Подготовка образцов не производилась.
2.1.3. Свойство усадки
Размеры кирпичей были измерены сразу после изготовления кирпичей, а также после отверждения, чтобы определить усадку кирпичей.
2.1.4. Объемный вес единицы
После 7 дней отверждения кирпичи сушили при 110 ℃ в течение 24 часов, а затем давали остыть до комнатной температуры. Затем измеряли сухой вес D (г). После этого кирпичи погружали на 24 часа в воду при комнатной температуре и измеряли взвешенный вес S (г). Затем кирпичи были удалены, поверхностная вода была вытерта влажной тканью и в течение 5 минут после извлечения кирпичей из водяной бани был измерен насыщенный вес W (г).Удельный объемный вес B, г / см 3 = D / V, где рассчитан объем V, см 3 = (W — S).
2.1.5. Начальная скорость абсорбции (IRA)
После измерения сухой массы D (г), как упоминалось ранее, поверхность слоя кирпича (поверхность размером 6 мм X 3,5 мм) заставляли абсорбировать воду в течение 1 мин. Вода была полностью удалена с поверхности кирпича в течение 10 с после удаления от контакта с водой, а вес D ’(г) был определен в течение 2 минут.Затем рассчитывали начальную скорость абсорбции IRA,% = D ’- D [Обозначение C 67-00 ASTM].
2.1.6. Абсорбционная способность
ASTM Обозначение C 67-00 использовалось для измерения абсорбционной способности A,% = [(W — D) / D].
2.1.7. Кажущаяся пористость, открытые поры и непроницаемые поры
Обозначение ASTM C 67-00 использовалось для определения кажущейся пористости P,% = [(W — D) / V], объем открытых пор, см 3 = W — D и непроницаемый объем пор, см 3 = D — S.
2.1.8. Тест на выцветание
Этот тест проводился в соответствии с ASTM C67-08. Для этого испытания один кирпич был вертикально помещен в воду с одним погруженным концом, а другой кирпич хранился в условиях окружающей среды. Через 7 дней оба кирпича сушили в печи при 110 ℃ в течение 24 часов. Затем оба кирпича наблюдались с расстояния 10 футов под углом не менее 50 футов с нормальным зрением. Если наблюдается какое-либо различие из-за наличия солевых отложений, рейтинг отображается как «высохший».Если никакой разницы не наблюдается, рейтинг отображается как «не высвечен».
2.1.9. Тест на радиоактивность
Радиоактивность смеси оптимального состава была исследована Отделом физики здоровья Комиссии по атомной энергии Бангладеш.
2.1.10. Изменение процесса и времени отверждения
Было исследовано влияние четырех различных процессов отверждения, т. Е. На неподвижном воздухе, с разбрызгиванием воды два раза в день, выдерживанием образца под влажной тканью и погружением образца под воду в течение семи дней.Наконец, был изучен эффект длительного отверждения. Для получения оптимального состава и разного давления уплотнения один комплект кирпичей выдерживали на воздухе в течение пяти недель. Другой набор сушили на воздухе в течение одной недели, а затем в течение четырех недель под водой. Затем сравнили их прочность на сжатие. Различие в прочности на сжатие исследовали с помощью инфракрасной спектроскопии с преобразованием Фурье (FTIR).
3. Результаты и обсуждение
3.1. Влияние песка на прочность на сжатиеОбразцы T1 — T4 (таблица 2) были подготовлены для определения влияния количества песка на прочность на сжатие.Прочность на сжатие может быть увеличена с 113,46 кг / см 2 до 165,57 кг / см 2 за счет увеличения количества песка с 10 до 40% (Рисунок 3). Максимальная прочность была обнаружена для 40% песка — 50% летучей золы — 10% известкового кирпича с 2% гипса. Поскольку основной целью данного исследования было массовое использование летучей золы, оптимальное количество песка было принято равным 30%, что дало прочность на сжатие 155,20 кг / см 2 . Улучшение механической прочности с увеличением содержания песка в большей степени объясняется повышенным количеством свободного SiO 2 , который легче реагирует с известью, чем зола-унос [8] .
3.2. Определение оптимального содержания извести и летучей золыРезультаты испытаний на прочность при сжатии, проведенные на образцах Т5 — Т9, показали, что максимальная прочность может быть достигнута с 15% извести и 55% летучей золы (Рисунок 4). Предел прочности на сжатие, найденный для этой композиции, составил 181,75 кг / см 2 .
Рисунок 3 . Влияние добавки песка на прочность на сжатие
Рисунок 4 . Влияние добавки извести на прочность на сжатие
3.3. Оптимальное количество гипсовой добавкиИзменение прочности на сжатие образцов T10 — T13, содержащих различные количества гипса, показано на рисунке 5. Можно видеть, что прочность на сжатие увеличилась с 181,75 кг / см 2 для 2% гипса до 287,78 кг / см 2 для оптимального содержания гипса 14%.
3.4. Влияние давления формования кирпича на прочность на сжатиеИспытания на прочность на сжатие образцов Т14 — Т16 показали, что прочность на сжатие увеличивается с увеличением давления формования кирпича (рис. 6).Образец T16 показал максимальную прочность на сжатие 417,96 кг / см 2 для давления формования кирпича 3000 фунтов на квадратный дюйм.
Рисунок 5 . Влияние добавки гипса на прочность на сжатие
Рисунок 6 . Влияние давления формования кирпича на прочность на сжатие
3.5. МикроструктураОбразцы Т14, Т15 и Т16 представляют собой образцы с оптимальным составом и различными давлениями формования кирпича.Микроструктура и другие свойства, помимо прочности на сжатие этих образцов, были исследованы для оптимизации давления формования кирпича. На рис. 7 показано, что как индивидуальный размер пор, так и общая пористость уменьшались с увеличением давления формования кирпича. Этого следовало ожидать.
Рисунок 7 . Микроструктура кирпичей, формованных под давлением (а) 1000 фунтов на квадратный дюйм (б) 2000 фунтов на квадратный дюйм (в) 3000 фунтов на квадратный дюйм [Все увеличения 500X]
3.6. Свойство усадкиЗаметной усадки не произошло, как это было измерено для образцов T14, T15 и T16.
3,7. Удельный весС увеличением давления формования кирпича объемный вес кирпича увеличивался (рисунок 8). Но выше 2000 фунтов на квадратный дюйм изменение плотности было незначительным. Максимальная плотность 1,81 г / куб.см была обнаружена для кирпичей, сформированных под давлением 3000 фунтов на квадратный дюйм, что намного ниже плотности кирпича на основе обожженной глины.
3.8. Начальная скорость абсорбции (IRA)Начальная скорость абсорбции кирпичей, изготовленных под давлением 1000 фунтов на квадратный дюйм, превышает 30 г, поэтому согласно ASTM C 67-00 эти кирпичи следует смачивать перед укладкой (Рисунок 9).С увеличением давления формования кирпича IRA упало ниже 30 г / м2. Самый низкий IRA 14,84 г был обнаружен для давления 3000 фунтов на квадратный дюйм. Так что эти кирпичи не нужно смачивать перед кладкой.
3.9. Впитывающая способностьКак показано на Рисунке 9, впитывающая способность составляла 14,63% для давления формования кирпича 1000 фунтов на квадратный дюйм. С увеличением давления это значение упало до 11,58% для давления 3000 фунтов на квадратный дюйм. Изменение абсорбционной способности при давлении выше 2000 фунтов на квадратный дюйм было незначительным.
Рисунок 8 . Влияние давления формования кирпича на объемную массу блока
Рисунок 9 . Влияние давления формования кирпича на абсорбционную способность и IRA
3.10. Кажущаяся пористость, открытые поры и непроницаемые порыВлияние давления формования кирпича на кажущуюся пористость, открытые поры и объем закрытых пор показано на Рисунке 10. Видимая пористость уменьшалась с увеличением давления. Выше 2000 фунтов на квадратный дюйм изменение было незначительным.Объем открытых пор также следовал той же тенденции. Как бы то ни было, на объем непроницаемых пор не повлияло давление формования кирпича. Этот результат указывает на то, что большее уплотнение при том же давлении возможно, если закрытые поры могут быть уменьшены посредством контроля размера частиц.
Рисунок 10 . Влияние давления формования кирпича на кажущуюся пористость, открытые поры и объем непроницаемых пор
3.11. ВыцветаниеБыло обнаружено, что кирпичи оптимального состава «не выцветают».Как видно на Фигуре 11, на поверхности испытанного кирпича не было обнаружено соли.
Рисунок 11 . Испытание высолов оптимального состава кирпича
3.12. РадиоактивностьРадиоактивность цезия-137 была ниже предела обнаружения установки, т.е. ниже 1,54 Бк / кг. Так что эти кирпичи не представляют опасности как источник радиоактивности.
3.13. Эффект отвержденияОбразец Т17 отверждался на неподвижном воздухе. Образцы Т18, Т19 и Т20 обрабатывали водным спреем два раза в день, держа образец под влажной тканью и погружая образец под воду соответственно.Максимальная прочность на сжатие 442,96 кг / см 2 была найдена для образца T18 (рисунок 12).
Рисунок 12 . Влияние процесса отверждения на прочность на сжатие
3.14. Эффект периода отвержденияОдин комплект кирпичей выдерживали в течение семи дней на воздухе; один подход — пять недель на воздухе, другой — первые четыре недели в воде, а затем одна неделя на воздухе. Максимальная прочность 877,36 кг / см 2 была обнаружена для кирпичей, сформированных под давлением 3000 фунтов на квадратный дюйм и отвержденных в воде в течение четырех недель, а затем одной недели на воздухе.FTIR-анализ показал (рис. 14), что, когда кирпичи выдерживались в воде в течение четырех недель, а затем одна неделя на воздухе вместо пяти недель на воздухе, более прочная межмолекулярная связь ОН-О стала преобладающей над более слабой внутримолекулярной связью ОН.
Рисунок 13 . Влияние процесса отверждения на прочность на сжатие
Рисунок 14 . FTIR-анализ кирпичей, отвержденных при различных условиях отверждения
4.Выводы
Из этого исследования можно сделать следующие основные выводы:
• Оптимальным составом необожженных кирпичей из золы-уноса, силиката, извести и гипса было 55 процентов летучей золы, 30 процентов песка, 15 процентов извести и 14 процентов гипса, а оптимальное давление формования кирпича составляло 3000 фунтов на квадратный дюйм.
• Повышение давления формования кирпича показало увеличение прочности на сжатие и удельного объемного веса, а также снижение IRA, абсорбционной способности, кажущейся емкости и объема открытых пор. Было обнаружено, что объем непроницаемых пор практически не зависит от давления формования кирпича.
• Для оптимального состава и давления кирпич обладает следующими свойствами:
1 Без усадки.
2 Объемный вес устройства: 1,81 г / см 3 .
3 Начальная скорость абсорбции (IRA): 14,84 г. Так что эти кирпичи не нужно смачивать перед кладкой.
4 Поглощающая способность: 11,58%.
5 Видимая пористость: 20,99%.
6 Объем открытых пор: 9,23 см 3 .
7 Объем непроницаемых пор: 34,74 см 3 .
8 Для оптимального состава и давления кирпичи, отверждаемые под струей воды два раза в день, показали максимальную прочность на сжатие 442,96 г / см. 2 .
Наконец, кирпичи, сформированные под давлением 3000 фунтов на квадратный дюйм, показали максимальную прочность 877,36 кг / см. 2 при отверждении в воде в течение четырех недель с последующей неделей на воздухе, а прочность определялась степенью межмолекулярной связи ОН-О.
Даже несмотря на то, что потребуются дальнейшие исследования до того, как будет сделан окончательный комментарий, кирпичи из золы-уноса, силикона, известняка и гипса, произведенные в этом исследовании, кажутся подходящими для использования в качестве строительного материала.Производство этого типа кирпича (если это технически и коммерчески жизнеспособно), безусловно, будет способствовать переработке летучей золы и, следовательно, минимизировать негативное воздействие на окружающую среду.
Список литературы
[1] | Goni, S. Guerrero, A. Luxan, M.P. и Macias, A. 2003. Активация пуццолоновой реакции летучей золы в гидротермальных условиях, Cem Concr Res , Vol. 33, стр 1399-405. | ||
В статье | CrossRef | ||
[2] | Klimesch, D.С. и Рэй, А. 1998. Влияние размера частиц кварца на образование гидрограната во время автоклавирования при 180 ℃ в системе CaO – Al 2 O 3 –SiO 2 –H 2 O, Cem Concr Res , Vol. 28, с. 1309-16. | ||
В статье | |||
[3] | Байкал и Довен, A.G. 2000. Утилизация летучей золы в процессе гранулирования; теория, области применения и результаты исследований, Resour Conserv Recy, Vol.30, с. 59-77. | ||
В статье | CrossRef | ||
[4] | Iyer, R.S. и Скотт, Дж. 2001. Летучая зола электростанции — обзор использования добавленной стоимости вне ресурсов строительной индустрии, Conserv Recy , Vol. 31, стр. 217-28. | ||
В статье | CrossRef | ||
[5] | Pimraksa, K.Вильгельм, М. Кохбергер, М. и Врусс, В. 2001. Новый подход к производству кирпичей из 100% летучей золы, Международный симпозиум по утилизации золы , Доступно по адресу: http://www.flyash.info/ повестка дня.html. | ||
В статье | |||
[6] | Poon, CS Kou, SC и Lam, L. 2002. Использование переработанных заполнителей в формованных бетонных кирпичах и блоках, Constr Build Mater , Vol.С. 281-9. | ||
В статье | |||
[7] | Токтай М.С. и Этин Б. 1991. Механическая прочность и водопоглощающие свойства автоклавных кирпичей из золы-уноса, TMMOB, Публикация Палаты инженеров-строителей , Vol. 1. С. 385-394. | ||
В статье | |||
[8] | Cicek, T.и Танрыверди, М. 2007. Кирпичи из летучей золы, автоклавированные паром на основе извести, Construction and Building Materials, Vol. 21. С. 1295-1300. | ||
В артикуле | CrossRef | ||
Известковые кирпичи — AribuyBD
Подробная информация о силикатном кирпиче
Силикатный кирпич изготавливается из песка, извести и воды (без добавок). Путем сильного прессования смеси и последующей автоклавной обработки получается прочный белый строительный материал.Хорошая звукоизоляция, хорошее накопление тепла и влаги, а также отличная огнестойкость — вот основные параметры, по которым архитекторы назначают кирпичи из известкового песка для каждого строительного проекта.
Силикатный кирпич — это сборный строительный материал, который одновременно обеспечивает структуру, теплоизоляцию и звукоизоляцию. SLB получают путем смешивания извести, песка и воды в периодическом процессе, при котором известь должна своевременно реагировать с негашеной известью, чтобы развить некоторую раннюю прочность сырого материала перед поступлением в автоклав.Негашеная известь, обладающая особым химическим составом, реакционной способностью и тонкостью помола, является одним из ключевых элементов в процессе литья силикатных изделий. Известковые штукатурки и штукатурки имеют такой же коэффициент линейного расширения, что и силикатный кирпич, что позволяет избежать образования трещин на поверхности
Вы также можете ознакомиться с нашим кирпичом из золы-уноса
ДОСТАВКА
Обычно доставляет от 12 до 48 часов
ДОСТАВКА
Бесплатная доставка для всех заказов * (в зависимости от стоимости заказа)
ВАРИАНТЫ ПРОСТОЙ ОПЛАТЫ
- Чистые банковские операции и кредит / Дебет / bKash / Nagad
- Наложенный платеж
- Вексель до востребования / Чек / Денежный перевод
Изображения продуктов используются только для справки.Реальные продукты могут незначительно отличаться по внешнему виду и цвету из-за освещения во время фотосъемки или отображения на мониторе.