каким он бывает, как его делают и проверяют
В холодное время года стройматериалы с пористой структурой, в том числе бетон, подвергаются повышенным нагрузкам. Под воздействием отрицательных температур бетонный монолит пропитывается водой, которая проникает в поры и, становясь льдом, расширяется при замерзании. Длительное пребывание бетонных изделий на морозе, повторное оттаивание и замерзание существенно снижают эксплуатационные характеристики материала. Поэтому одним из ключевых технических характеристик бетона является класс его морозостойкости.
Морозостойкость — показатель, характеризующий способность бетона противостоять многократному замораживанию и размораживанию без потери прочности.
Эксперт о морозостойкости бетона
Классы морозостойкости бетона и сферы его применения
Класс (в просторечии марка) бетона по морозостойкости имеет буквенно-числовое обозначение. ГОСТ выделяет следующие классы морозоустойчивости по областям эксплуатации.
- Низкий (ниже F50). Под воздействием отрицательной температуры такой материал трескается и рассыпается. Возможности его применения значительно ограничены. В России этот бетон практически не используется.
- Умеренный (F50 – F100). Самая популярная марка бетона по морозостойкости. Изделия и фундаменты из него эксплуатируются во всех климатических зонах России, где четко выделяются четыре сезона.
- Повышенный (F150 – F300). Выдерживает экстремальные температурные перепады, полностью сохраняя первоначальные эксплуатационные характеристики. Находит применение в районах с вечной мерзлотой, в Сибири и на Крайнем Севере.
- Высокий (F300 – F500). Используется в особых случаях. Например, в зонах периодическими колебаниями уровня воды и многослойным промерзанием грунтов.
- Сверхвысокий (выше F500). Находит штучное, сугубо индивидуальное применение в ответственных конструкциях, возводимых на очень длительный срок.
Как определяется морозостойкость бетона?
Ключевой критерий при определении морозоустойчивости бетона — установление максимального количества циклов заморозки-разморозки, при которых сохраняются первоначальные характеристики материала, а растрескивания и шелушения не определяются.
Лабораторные испытания материала имеют своей целью подробно продемонстрировать его поведение в естественных условиях эксплуатации. Результаты испытаний подтверждают либо не подтверждают реакцию материала на влияние внешних факторов. Условия испытаний на морозостойкость бетона подробно расписаны в ГОСТ 10060-95.
Морозостойкость бетона — способность сохранять физико-механические свойства при многократном переменном замораживании и оттаивании.
Морозостойкость бетона характеризуют соответствующей маркой по морозостойкости F.
Марка бетона по морозостойкости F — установленное нормами минимальное число циклов замораживания и оттаивания образцов бетона, испытанных по базовым методам, при которых сохраняются первоначальные физико-механические свойства в нормируемых пределах.
Цикл испытания — совокупность одного периода замораживания и оттаивания образцов.
Основные образцы — образцы, предназначенные для замораживания и оттаивания (испытания).
Контрольные образцы — образцы, предназначенные для определения прочности бетона на сжатие перед началом испытания основных образцов.
Лабораторные и альтернативные способы определения морозостойкости бетона
Для лабораторного исследования берутся основные (подверженные многократному замораживанию – размораживанию) и контрольные (новые, абсолютной прочности) образцы бетонного монолита.
Контрольные образцы бетона перед испытанием на прочность, а основные образцы перед замораживанием насыщают водой/раствором соли температурой (18±2) °С.
Для насыщения образцы погружают в жидкость на 1/3 их высоты на 24 ч, затем уровень жидкости повышают до 2/3 высоты образца и выдерживают в таком состоянии еще 24 ч, после чего образцы полностью погружают в жидкость на 48 ч таким образом, чтобы уровень жидкости был выше верхней грани образцов не менее чем на 20 мм.
Образцы помещают в морозильную камеру. После этого образцы размораживаются, и оценивается их состояние.
Существуют способы определения морозостойкости бетона подручными средствами. Для оценки показателя исследуются:
- Внешний вид материала. Крупная зернистая структура, наличие трещин, пятнистости, шелушащихся и расслаивающихся зон — все это свидетельствует о низкой морозоустойчивости бетона.
- Уровень водопоглощения. Когда показатель находится в диапазоне 5 — 6%, можно говорить о плохой устойчивости к низким температурам.
Еще один экспресс-метод определения морозоустойчивости реализуется по следующей схеме. Образцы исследуемого монолита погружаются в серно-кислый натрий и выдерживаются в нем в течение 24 часов. По истечении этого времени они подвергаются четырехчасовой сушке при 100 ºС. Цикл вымачивания и высушивания пятикратно повторяется аналогичным образом. По завершении эксперимента материал исследуют на предмет наличия трещин, сколов и других поверхностных дефектов.
Как повысить морозостойкость бетона?
Известно несколько способом повышения морозостойкости бетона. В их основе лежит то, что устойчивость материала к воздействию низких температур определяется количеством и величиной пор, а также исходным качеством и составом цементной основы.
- Уменьшение макропористости. Самый простой и доступный способ повышения уровня морозоустойчивости. Использование спецдобавок и создание особых условий для быстрого отвердевания цементного раствора минимизирует потребность продукта в воде. Результатом этого становится уменьшение пористости.
- Уменьшение количества воды в исходном растворе. Чтобы уменьшить потребность начального раствора в воде, в него добавляются специальные заполнители.
- Поздняя заморозка. Если заморозить бетон в позднем возрасте, это сократит его пористость.
- Гидроизоляция. С помощью специальной обмазки, окраски или пропитки на поверхности монолита создается защитная пленка, препятствующая проникновению в него атмосферной влаги.
Как заливают бетон в мороз
Бетон применяется в холодное время года, если строительные работы запоздали или идут на территории с высокой насыщенностью грунта влагой. Чтобы заливка бетонной смеси была успешной, стройплощадку предварительно прогревают тепловой пушкой или термоэлектрическими матами. Последние выполняют сразу две функции — гидроизоляции и обогрева.
Чтобы обогреть площадку можно применить и стандартную термоизоляцию. Самый простой вариант — использовать двухстороннюю пленку, которая растягивается в 2-3 см от основания. На пленку накладывают изоляцию и устанавливаются теплогенератор. На отвердевание бетона зимой обычно уходит не менее 4 дней.
Добавление в раствор прогретых инертных материалов и противоморозных добавок при зимних работах обязательно. Оно позволяет уменьшить размер больших пор (изменить структуру за счет увеличения числа микропор) и максимально удалить воду из раствора.
Подробный рассказ о том, как заливается бетон в холодное время года
Вывод
Морозостойкость — одно из важнейших свойств бетона как основного строительного материала, характеризующее его способность долговременно противостоять колебаниям температур от сезона к сезону. В условиях умеренного, а тем более арктического климата, когда годовая температурная амплитуда достигает 80 и более градусов, использование морозостойкого бетона не имеет альтернативы. Однако универсальной марки бетона, подходящей для всех случаев, не существует. Морозостойкий бетон покупается индивидуально для каждого объекта с учетом его назначения и местных условий.
Морозостойкость бетона и цемента, все о бетоне – компания «Бетонснаб»
Морозостойкость – это свойство
бетона, насыщенного водой, выдерживать регулярные оттаивания и
замораживания, сохраняя целостность структуры и прочность. Под
маркой материала подразумевают определенное количество циклов
оттаивания-замораживания, которое выдерживают образцы
определенного размера без уменьшения прочности на сжатие и без
потери массы (для дорожного бетона).
Компания «Бетонснаб», реализующая качественные стройматериалы и
предоставляющая услуги по аренде насоса для бетона, предлагает
морозостойкие бетоны марки F500, F400, F150, F100, F300, F200,
F75 и F50.
Факторы морозостойкости бетона
Количество макропор.
Уменьшения
макропористотсти можно добиться изменением водоцементного
соотношения, введением специальных добавок, созданием особых
условий застывания, качественным уплотнением и замораживанием в
позднем возрасте.
Характер пористости.
Изменить пористость бетона
марки 200 или
любой другой можно, добавив в него воздухововлекающих добавок.
Материал должен иметь 4–6 % резервных пор, которые при обычном
уровне насыщения водой остаются пустыми, но заполняются при
замерзании.
Вид применяемого цемента.
Самыми морозостойкими
являются бетоны,
сделанные из портландцемента и добавок с 5%-м содержанием
минерала С3А. Лучше их бывают только бетоны на основе
глиноземистого цемента.
Если Вам необходим насос для бетона или Вы хотите приобрести
морозостойкий бетон марки 200, 300 или любой другой, звоните нам
по телефонам из раздела «Контакты».
Высокоглиноземистый цемент, или просто ВГЦ
Высокоглиноземистый цемент (ВГЦ) — это высокопрочное быстротвердеющее гидравлическое вяжущее вещество, состоящее в основном из моно- и диалюминатов кальция (CaO*Al ), получаемый путем тонкого измельчения сырьевых составляющих шихты, ее последующего обжига во вращающейся печи при температуре 1450 С и тонкого измельчения полученного клинкера на струйной мельнице.
Исходными сырьевыми составляющими шихты являются: карбонат кальция по ТУ 113-03-00203789-23-94 и гидроксид алюминия по ТУ 1711-045-00196368-95. ОАО «Волховский Алюминиевый Завод» выпускает ВГЦ по ГОСТ 969-91 двух марок ВГЦ-1 и ВГЦ-2.
Минералогический состав, содержание CaO Al — 35-45%, ВГЦ применяется ровно в безукоризненном облике, таково и в качестве компонента расширяющихся, напрягающих, быстротвердеющих, огнеупорных и других специальных вяжущих веществ в металлургической, огнеупорной, цементной и др. отраслях промышленности.
ВГЦ может быть использован в качестве носителя катализаторов при конверсии ненасыщенных углеводородов. В заключительные годы ВГЦ получил размашистое применение в черной и цветной металлургии в составе жаропрочных бетонов и сухих жаропрочных каш, используемых в печах сталелитейной и сталепрокатной промышленности, туннельных печах, коксовых печах, котлах, сталеразливочных ковшах. Применение эдаких бетонов и смесей позволяет благодаря длинным теплоизоляционным свойствам экономить топливно-энергетические ресурсы за счет снижения теплопотерь, а так же в виду тонкой химической стойкости позволяет исключить химическое взаимодействие футеровки с растопленным металлом.
Высокая механическая прочность этих материалов, изрядный срок службы удешевляют производство, а быстроходный комплект прочности в ранние сроки твердения сокращает пора ремонтов. Жаростойкие бетоны и сухие смеси в сравнении со штучным огнеупорным материалом обеспечивают ускорение темпов строительства, снижение физических и трудозатрат.
Глиноземистый цемент представляет собой быстродействующий гидравлический вяжущий материал, который получают путем тонкого измельчения обожженной до спекания или сплавления богатой глиноземом сырьевой смеси. В качестве исходных материалов для получения глиноземного цемента используют известняк, известь или породы, с высоким содержанием глинозема (Al2O3). Химический состав такого цемента включает Al2O3 (минимум 35%), CaO (минимум 36%), SiO2 (2 — 4%) и Fe2О3 (10 — 14%). Внешние параметры глиноземистого цемента — это тонкий порошок серо-зеленого, коричневого или черного цвета.
По прочности на сжатие глиноземистые цементы подразделяются на две группы: цемент марки ГЦ-40 и марки ГЦ-50. Различаются они следующими параметрами: к концу первых суток прочность цемента марки ГЦ-40 составляет 22,5 МПа, а марки ГЦ-50 — 27,4 МПа. В возрасте 3-х суток прочность ГЦ-40 — 40 МПа, ГЦ-50 — 50 МПа.
Начало схватывания глиноземистых цементов происходит в возрасте не менее 45 минут, а конец схватывания — не позднее 10 часов. Глиноземистый цемент хорошо твердеют во влажной среде. При добавлении такого цемента в бетон, последний становится водонепроницаемым (его используют при контакте сооружений с пресной или сульфатной водой) и морозостойким, устойчивым к коррозии, что гарантирует полную сохранность арматуры.
Так же бетон с добавлением глиноземистого цемента может использоваться и для строительства в зимнее время (до -10C°) без дополнительного подогрева, т. к. при твердении такой бетон выделяет большое количество тепла за короткий промежуток времени. Благодаря тому, что глиноземистый цемент является быстротвердеющим, уже через 15 — 18 часов прочность его такова, что позволяет вводить сооружения в эксплуатацию.
Поэтому, несмотря на свою высокую стоимость этот цемент незаменим при срочных ремонтных и аварийных работах.
Глиноземистый цемент является одним из самых огнестойких цементов (его огнестойкость выше, чем у портландцемента). Он не теряет своих основных характеристик даже при эксплуатации в температурном режиме до 1700C°. В смеси с огнеупорными наполнителями, такими как магнезит, хромитовая руда, шамот, глиноземистый цемент используют для получения гидравлически твердеющих огнеупорных растворов и бетонов.
В основном глиноземистый цемент используют в промышленном строительстве, которое сопряжено с высокими температурами (например, в нагревательных устройствах, работающих в температурном режиме до 1300C°), агрессивными водными или газовыми средами (сульфатные воды, хлориды, серные соли, окись углерода, метан и т. д.). Он необходим для бетонных работ в зимнее время и для изготовления расширяющихся и безусадочных цементов.
Для аварийного и ремонтного строительства промышленных зданий и мостов, а так же для аварийной заделки пробоин в судах морского флота. Глиноземистый цемент используют и как компонент растворов и клеёв в строительной химии. Этот цемент подходит и для горнодобывающей промышленности, для постройки шахт, строительства подземных сооружений, для быстрого устройства фундаментов под машины и т. д.
Не исключен вариант применения глиноземистого цемента в срочных домашних ремонтных работах, т. к. этот цемент обладает коротким временем связывания и быстрое приращение механической выдержки. Здесь его используют для стройки каминов, облицовке печей, ремонта дымоходов и труб вентиляций. Так же он идет на подготовку полов, подоконников и притолок.
Глиноземистый цемент фасуют в мешки по 50 кг и в контейнерах (МКР-1 и ОС).
Как замесить цементный раствор? 📝
Для приготовления цементных растворов используют очищенный песок, вяжущий компонент и воду. В некоторых случаях в состав строительного теста вводят пластификаторы и химические присадки. Они повышают удобоукладываемость и технические характеристики смеси.
Выбирая и подготавливая компоненты, строители соблюдают ряд требований:
- отсутствие примесей в составе затворителя, цемента и наполнителя;
- единая фракция песка;
- точный состав смеси и его весовое соотношение;
- температурный диапазон при изготовлении раствора – от +10 до +40 С;
- однородность замеса.
Наличие земли, глины, инородных тел в песке или цементе снижают качество и морозостойкость раствора. После застывания такая смесь легко крошится и плохо переносит циклы замерзания-размерзания. В связи с этим операторы тщательно подбирают вид и марку цемента, рассчитывают пропорции и проводят оценку качества компонентов.
Марочный цемент
Вяжущим компонентом строительных смесей является цемент. В его состав входят гипс, клинкер и наполнитель: белит, анит, магнезит, силикат натрия или алюминатная база. От типа наполнителя зависит сфера применения и допустимые условия эксплуатации цемента.
Вид цемента | Сфера применения | |
Рекомендуется | Не рекомендуется | |
Портландцемент | Кладочные растворы, штукатурные смеси, затирки, бетонные изделия, ЖБИ. | Конструкции специального назначения. |
Шлаковый портландцемент | Подземные и подводные ЖБ-конструкции, включая фундаменты, цокольные этажи, чаши бассейнов. | Морозостойкие бетоны, кладочные растворы для печей, а также ЖБИ, предназначенные для надземной эксплуатации. |
Пуццолановый портландцемент | Подземные и подводные ЖБИ. | Морозостойкие бетоны, а также конструкции, испытывающие попеременное увлажнение и высыхание. |
Алюминатный | Жаростойкие и быстротвердеющие бетоны, кладочные смеси для печей, строительные растворы для проведения аварийных работ. |
Массивные ЖБИ, несущие конструкции: стены, блоки, фундаменты, а также растворы, приготавливаемые при температуре выше +25С.![]() |
Высокоалюминатный | Жаростойкие бетоны, штукатурки и кладочные смеси. | _ |
Гипсовый алюминатный | Водонепроницаемые смеси, безусадочные растворы. | Растворы, приготавливаемые при температуре ниже +1С, а также растворы, эксплуатируемые при температуре выше +80 С. |
Белитовый или цветной | Архетиктурные штукатурки | Строительные работы, растворы специального назначения. |
Таблица №1 – Цементные растворы и сферы их применения.
В частном строительстве наиболее популярным является портландцемент. Он отлично подходит для заливки фундаментов, ЖБ-плит и конструкций, оштукатуривания стен и приготовления кладочных смесей.
Во время застывания раствора связывающий компонент «схватывается» и превращается в цементный камень, прочность которого зависит от марки раствора. О маркировке и классификации цементов см. ниже.
Очищенный песок
Песок является структурным наполнителем, который удешевляет стоимость раствора и формирует его каркас. Качественный наполнитель повышает пластичность и прочность смеси, корректирует ее усадку и предотвращает образование трещин в цементном полотне.
Песок подбирают с учетом технических требований к раствору:
- для штукатурных работ подходит речной очищенный песок;
- для кладки – кварцевый наполнитель мелкой фракции;
- для приготовления бетонных растворов – сухой, очищенный материал любой фракции.
При изготовлении штукатурных и отделочных смесей песок заменяют гипсом. Он имеет порошкообразную текстуру и хорошо ложиться на поверхности.
Вода с нейтральный ph
Ржавая и жесткая вода снижает морозостойкость и жаропрочность смеси. Соли металлов, проникая в раствор, разрушают кристаллики цементного камня и провоцируют растрескивание полотна. Для затворения цемента подходит только чистая вода с нейтральным pH.
В качественном затворителе не должно быть следующих признаков загрязнения:
- резкий химический/органический запах;
- осадок, хлопья, накипь;
- коричневый, землистый, серый оттенок;
- примеси земли, глины, других компонентов;
- наличие инородных тел – кореньев, листвы, строительного мусора.
Для приготовления цементного раствора подходит техническая вода из колонки, колодца, реки. При необходимости жидкость очищают с помощью самодельных или бытовых фильтров, а также химических препаратов для нейтрализации солей металлов.
Присадки и пластификаторы
Химические добавки выбирают с учетом климатических особенностей региона и сферы применения строительного теста. Цементные растворы, изготовленные для замешивания бетона, обогащают морозостойкими и влагоупорными присадками. Они увеличивают сроки эксплуатации и прочностные характеристики бетонного полотна.
В штукатурные и кладочные смеси обычно добавляют пластификаторы, влияющие на их удобоукладываемость. Наиболее популярными пластифицирующими добавками являются стиральный порошок, мыльные растворы и жидкость для мытья посуды. В промышленных масштабах используют репудин, гександиовую кислоту и различные эфиры.
Расчет пропорций
Готовые цементные растворы отличаются по степени плотности. Она выражается в марках (М) или классах (В) и определяется цифровым обозначением от 50 до 500. Наиболее популярными являются следующие виды смесей:
- М100 – кладочные растворы, предназначенные для кирпича, блоков и керамической плитки;
- М150 – материалы для оштукатуривания поверхностей.
- М200 – для стяжки полов, монтажа кровли, черновой штукатурки;
- М250-500 – для приготовления бетонных смесей.
От марки цемента и типа приготавливаемого раствора зависят его пропорции.
Кладочные смеси
Для приготовления кладочного раствора используют марочный цемент, песок и гашеную известь. Последний компонент нейтрализует углекислоту, которая образуется во время затвердевания цементного камня.
Пропорции смеси зависят от марки цемента: М400 или М500. Растворы, замешанные на М500, включают:
- 1 ведро цемента;
- 3 ведра песка;
- 0,2 ведра гашеной извести.
Водоцементное соотношение в данном случае составляет 1:1.
Растворы, приготовленные на цементе М400, включают:
- 1 ведро цемента;
- 2,5 ведра песка;
- 0,3 ведра извести.
Водоцементное соотношение также составляет 1:1.
Марка готового раствора варьируется от М150 до М200 и должна совпадать с маркой кирпича.
Штукатурное тесто
При оштукатуривании поверхностей строители используют составы для набрызга, грунтовки и отделки. В их состав также входят цемент М400, наполнитель и вода.
Подготовительный слой включает:
- 1 ведро цемента;
- 4 ведра песка;
- 1 ведро воды.
Грунтовочная паста замешивается в пропорциях:
- 1 ведро цемента;
- 2 ведра песка;
- 1 ведро воды.
Штукатурку готовят из цемента, воды и гипса:
- 1 ведро цемента;
- 2 ведра гипса;
- 1 ведро воды.
В гипсовые растворы добавляют 1/10 ведра гашеной извести для повышения прочности состава.
Стяжка пола
Для заливки напольных покрытий подходят цементно-песочные растворы с пропорциями 1:4 (цемент-М400). В жилых домах используют составы, приготовленные из 1 части портландцемента и 3 частей очищенного песка.
Пластификаторы и полипропиленовые волокна снижают пластическую усадку покрытий, предотвращают их деформацию и растрескивание. В связи с этим строители рекомендуют добавлять в 100 литров раствора около 50 мл средства для мытья посуды, либо специальные присадки.
Технология приготовления раствора
Существуют ручные и автоматизированные технологии приготовления цементного раствора. В первом случае оператор использует совковую лопату или строительный миксер, во втором – бетономешалку или промышленный автобетоносмеситель.
Качественная смесь отличается высокой пластичностью и однородной структурой. Во время ее приготовления оператор контролирует водоцементное соотношение, чистоту раствора и его однородность.
Для проведения ручного замеса строители используют совковые лопаты или строительные миксеры, для автоматизированного – бетономешалку. Оператор заранее подготавливает полиэтиленовую пленку, ведра для расходников и готового раствора, а также емкость для воды и корыто для замеса.
На подготовительном этапе песок пересыпают на полиэтилен, чтобы он не напитался влагой от земли. При выпадении осадков наполнитель закрывают пленкой, т.к. в сыром виде он ухудшает удобоукладываемость смеси. Воду и цемент доставляют на строительную площадку заранее.
Технология замеса включает несколько этапов.
- Воду заливают в корыто или автобетоносмеситель и туда же добавляют первое ведро цемента.
- Раствор вымешивают лопатой или миксером до полного растворения клинкера. Таким образом в смесь вводят весь объем цемента.
- В раствор добавляют песок до получения пастообразной консистенции.
Готовый материал переливают в ведра и используют по назначению.
Товарные растворы от компании ЕвроБетон
Комбинат строительных материалов EuroBeton предлагает своим клиентам готовые растворы на основе цемента М400 и М500.
Все материалы проходят производственный контроль качества и соответствуют требованиям ГОСТ. Изготовление и доставка товара осуществляется в день обработки заказа. Постоянным и оптовым клиентам предоставляются скидки.
Смотрите также
Хие бетоны и смеси на цементной основе | Продукция
Зимний бетон ТБ С 30
Специальный бетон для повторной заливки и других бетонных работ. Морозостойкий. Максимальный размер зерен 3 мм. Класс прочности C 25/30 (K 30). Объем готовой массы ок. 500 л / 1000 кг. Температура использования +5°C – -15°C.
Ознакомьтесь с продуктомЗимний бетон ТБ С 40
Специальный бетон для повторной заливки и других бетонных работ. Морозостойкий. Максимальный размер зерен 3 мм. Класс прочности C 30/37 (K 37). Объем готовой массы 11-12 л /25 кг. Температура использования +5°C…-15°C.
Ознакомьтесь с продуктомСухой бетон на цементной основе K 30
Специальный бетон для заливки класса прочности C 25/30 (K 30). Морозостойкий. Хорошая износостойкость и плотность. Максимальный размер зерен 3 мм. Объем готовой массы около 500 л / 1000 кг. По заказу также доступен размер зерен 10 мм (только для упаковки 1000 кг).
Ознакомьтесь с продуктомСухой бетон на цементной основе K 45
Специальный бетон для заливки класса прочности C 35/45 (K 45). Морозостойкий. Хорошая износостойкость и плотность. Максимальный размер зерен 3 мм. Объем готовой массы 11–12 л / 25 кг. По заказу также доступен размер зерен 10 мм (только для упаковки 1000 кг).
Сухой бетон S 100
Базовый бетон для широкого спектра бетонных заливок. Максимальный размер зерен 10 мм. Прочность на сжатие около 25 МПа. Объем готовой массы 12–13 л / 25 кг. Морозостойкий.
Ознакомьтесь с продуктомБетон для заделки JB 600/3
Высокопрочный бетон, разбухающий до твердения, предназначенный для заливки в стесненных условиях и для завершающей и заполняющей заливки. Основные объекты применения — монтажная заливка бетонных элементов и заливка швов, а также различные виды заливки при монтаже анкеров. Максимальный размер зерен 3 мм. Класс прочности C 50/60 (K 60). Соответствует требованиям SILKO. Объем готовой массы 11-12 л /25 кг. Соответствует требованиям класса R4.
Ознакомьтесь с продуктомБетон для заделки ЙБ 1000/3
Высококлассный бетон для сложной точечной заливки, например, для крепления и установки оборудования. Благодаря некоторому разбуханию перед схватыванием, бетон хорошо заполняет пустоты. Максимальный размер зерен 3 мм. Класс прочности C 60/75 (K 80). Объем готовой массы 11-12 л /25 кг. Соответствует требованиям SILKO. Соответствует требованиям класса R4.
Ознакомьтесь с продуктомЗимний бетон для заделки TJB
Специальный бетон, разбухающий до твердения, для завершающей заливки и мелких бетонных работ, а также различных видов заливки при монтаже анкеров. Максимальный размер зерен 3 мм. Класс прочности C40/50 (K 50). Объем готовой массы 11-12 л /25 кг. Температура использования +5°C – -15°C.
Быстро затвердевающий бетон ПБ
Специальный бетон с быстрым нарастанием прочности. Подходит, например, для заделки бетонных конструкций, заполнения пустот и заливки пола. Класс прочности C 30/37. Максимальный размер зерен 3 мм. Объем готовой массы 12-13 л /25 кг. По заказу также размер зерен 10 мм.
Ознакомьтесь с продуктомСИЛКО Корро SKC C35/45
Специальный бетон для требовательных объектов заливки, находящихся под воздействием мороза и солей. Максимальный размер зерен # 10 мм. Класс прочности C 35/45 (K 45). Соответствует требованиям SILKO.
Минимальная доставка 3 мешка.
Ознакомьтесь с продуктомСИЛКО Пикакорро SPC C35/45
Специальный быстрозатвердевающий раствор для требовательных объектов. Максимальный размер зерен # 3 мм. Класс прочности C 35/45 (K 45). Соответствует требованиям SILKO.
Минимальная доставка 3 мешка.
Ознакомьтесь с продуктомQuick Drill 45
Технология Fescon Quick Drill — это новая система для ускорения цементации (стабилизации) грунта при разведках месторождений. Система состоит из быстросхватывающегося цемента Ciment Fondu Lafarge и пакетов добавки Quick Drill 45, при помощи которой можно регулировать свойства цементной пасты.
Цемент в Новотроицке | ООО ТД «Агидель»
ООО ТД «Агидель» предлагает широкий ассортимент цемента различных марок, оптом и в розницу по доступным ценам в Оренбургской области.
В наличии всегда цемент производства ООО «ЮуГПК»( Новотроицкий цемент) в различной фасовке.
Цемент марки МКР (ЦЕМ I 42,5Н, ЦЕМ II/А-Ш 42,5Н, ЦЕМ II/В-Ш 42,5Н, ЦЕМ III/А 32,5Н) фасованный в мешках по 1 тонне.
Новотроицкий цемент россыпью (ЦЕМ I 52,5Н, ЦЕМ I 42,5Н, ЦЕМ II/А-Ш 42,5Н, ЦЕМ II/В-Ш 42,5Н, ЦЕМ III/А 32,5Н) с возможностью доставки автоцементовозами с электрическими и дизельными компрессорами.
- — Цемент Аккерман М400 (ЦЕМ III/А 32,5Н) в мешках на паллетах
- — Цемент Аккерман М500 (Цем II/B-К (Ш-И) 42,5Н) в мешках на паллетах, высокостойкий, морозостойкий, долговечный.
- — Цемент Аккерман М600 (ЦЕМ III/А 32,5Н) в мешках на паллетах инновационный, активированный, долговечный.
Наименование | Содержимое | Гост | Отгрузка |
---|---|---|---|
Цемент в Новотроицке ООО «ЮуГПК» |
Продукция завода-изготовителя г. Новотроицк |
||
Цемент в Новотроицке МКР (Мешки по 1 тн. |
ЦЕМ I 42,5Н |
31108-2016 |
|
Цемент в Новотроицке Россыпью |
ЦЕМ I 52,5Н |
31108-2016 |
|
Цемент в Новотроицке М400 (на паллетах) |
(ЦЕМ III/А 32,5Н) (универсальный, надежный, прочный) |
31108-2016
|
|
Цемент в Новотроицке М600 (на паллетах) |
(ЦЕМ I 52,5Н) (инновационный, активированный, долговечный) |
31108-2016
|
|
Цемент в Новотроицке М500 (на паллетах) |
Цем II/B-К (Ш-И) 42,5Н (высокостойкий, морозостойкий, долговечный) |
31108-2016
|
Морозостойкий бетон — цены в Москве и Московской области с доставкой
Цена указана без учета НДС и стоимости доставки.
Порядок работы
Оставляете заявку
Круглосуточно.
Всегда с вами,
днем и ночью.
Уточняем детали
и делаем
предложение
Любые консультации
по строительству
и материалам.
Согласовываем
сроки отгрузки
и способы оплаты
Низкая цена.
Любая форма
оплаты.
Изготавливаем
бетонную смесь
Все по ГОСТ.
Импортное
оборудование,
стабильное качество.
Доставляем
ваш заказ
Всегда в срок.
Без сюрпризов.
Морозостойкость бетона – это его качество оставаться монолитной структурой при многократных перепадах температур и повышенной влажности. Морозостойкий состав предназначается для строительства фундаментов и дорожного полотна, возведения гидротехнических сооружений, для упрочнения бетонных конструкций. ООО «Омега Бетон» осуществляет производство и продажу с последующей доставкой раствора, в том числе и морозостойкого, марка и класс которого подходит для целевого строительства. Регионы обслуживания – Москва и Московская область.
Как определить марку морозостойкого бетона
Степень морозостойкости бетонной смеси определяется в испытательной лаборатории и обозначается символом F, а также цифрами, указывающими количество циклов заморозки-разморозки бетона. Это такие обозначения, как F50, F75, F100, F150, F200, F300, F400, F500. Чтобы произвести правильный расчет смеси, эксплуатационные показатели всех марок морозостойкого бетона нужно узнавать из таблицы:
Морозостойкость |
Области применения марки бетона |
Низкая: менее F50 |
Быстрое растрескивание на открытом воздухе при резких перепадах температур и влажности. |
Средняя: F50-F150 |
Самая популярная марка, имеющая средние параметры прочности на сжатие при постоянном воздействии контрастных температур и повышенной влажности. Применяется повсеместно, например, Москва и регионы. |
Повышенная: F150-F300 |
Пользуется спросом в условиях севера. |
Высокая: F300-F500 |
Эксплуатация в особых условиях. |
Особо высокая: более F500 |
Эксплуатация в исключительных условиях. Прочность и долговечность регулируется добавками. |
- Марка бетона указывает на средние значения прочности в кг/см2.
- Класс бетона определяет показатель гарантированной прочности состава.
Способность раствора схватываться при отрицательных температурах обеспечивается не маркой бетона, а наличием присадок, что влияет на конечную стоимость. Чтобы смесь не теряла свои качества при перевозке, ООО «Омега Бетон» предлагает автопарк специализированной техники, в котором есть миксеры и АБС любого объема и мощности. Цена бетона за 1 м3 указана в прайс-листе на сайте производителя, где можно выбрать любой образец.
Требуемую прочность морозостойкого бетона можно рассчитать с использованием линейной зависимости:
R б = F(Ц/В+10Д),
где Ц — расход цемента, кг/м3, В — расход воды, л/м3, Д — объем воздуха в бетоне, %.
Рассчитайте необходимый объем бетона
БСГ и арматуры на ваш объект
ПМД (противоморозные добавки) для бетона
Расчет характеристик готового бетона, его марка и класс определяются лабораторными испытаниями, которые завод-производитель проводит постоянно. Так как компания работает с заказчиками в Москве и Московской области, то продажа смеси F50, F75, F100, F150 является самой востребованной. Быстрое изготовление, доставка и разгрузка при помощи спецтехники компании обеспечивают качество бетона производства ООО «Омега Бетон». Компания предоставляет в аренду специализированную технику, в том числе миксеры с объемом резервуара 6-10 м3.
Требуемая морозостойкость достигается применением спецдобавок. Стандартные добавки для повышения устойчивости к воздействию температур в широком диапазоне имеют следующие свойства:
- Вещества, повышающие плотность бетона за счет замедления схватываемости и скорости седиментации.
- Добавки-катализаторы воздушных пузырьков. Поры воздуха повышают термоизоляционные характеристики бетона и невосприимчивость к перепадам температур.
Добавки улучшают эксплуатационные характеристики бетона, повышают антикоррозийные свойства, определяют цвет бетона.
Изготовление морозостойкого бетона на производственных мощностях ООО «Омега Бетон» происходит с использованием качественных основных материалов и присадок. Очистка песка, щебня или гравия до требуемых фракций, промывание материала, правильный выбор марки цемента – все это не только обеспечивает высокий класс конечного продукта, но и увеличивает стоимость бетона несколько увеличивается. Поэтому ООО «Омега Бетон» предлагает купить бетон у завода-производителя. Цена заказа определяется специалистами отдела продаж, смесь отгружается в м3, для перевозки используется автомобиль-миксер. Выгружается товарный бетон на объекте при помощи собственных АБС компании.
Достоинства и недостатки
Отрицательные моменты:
- При минусовых температурах смесь схватывается при дополнительном подогреве, чтобы не допустить замерзание и кристаллизацию влаги. Без использования подогрева необходимо добавлять присадки, иначе бетон не будет достаточно прочным.
- Противоморозные добавки увеличивают время схватывания раствора и его стоимость.
Преимущества:
- Морозостойкий бетон можно применять в любых климатических поясах.
- Бетон не деформируется и не крошится.
- Увеличивает срок эксплуатации объекта.
- Водонепроницаемость и антикоррозийная защита.
Предложение от завода-производителя
ООО «Омега Бетон» предлагает купить товарный морозостойкий бетон собственного производства. Собственный автопарк миксеров и АБС сделает доставку надежной и обеспечит качество раствора. Есть возможность онлайн-заказа и обсуждения условий договора на месте. Мы всегда идем навстречу своим партнерам.
Сертификаты
«Омега бетон» — ваш надежный поставщик
Возврат к списку
Метод испытаний для оценки морозостойкости бетона на ватерлинии гидротехнических сооружений
ASTM C672 / C672M (2003) Стандартный метод испытаний устойчивости бетонных поверхностей к образованию накипи, подвергшихся воздействию химикатов для борьбы с обледенением. Американское общество испытаний и материалов, Нью-Йорк
Chatterji S (2003) Замораживание материалов на основе цемента с воздухововлекающими добавками и специфические действия воздухововлекающих агентов. Cem Concr Compos 25: 759–765
Статья Google Scholar
Fagerlund G (1972) Критические степени насыщения при замерзании пористых и хрупких материалов. Кандидат наук. диссертация, Лундский университет, Лунд, (на шведском языке)
Fagerlund G (1977) Международное совместное испытание метода критической степени насыщения для оценки устойчивости бетона к замерзанию / оттаиванию. Mater Struct 4: 231–253
Google Scholar
Fagerlund G (1997) Внутренняя морозостойкость — современное состояние.В: Материалы международного семинара RILEM по морозостойкости бетона, Эссен, стр. 321–338
Fridh K (2005) Внутренние морозостойкие повреждения бетона. Кандидат наук. диссертация, Лундский университет, Лунд
Heggestad R, Myran R (1967) Исследования 132 норвежских бетонных плотин. В: 9-й Международный конгресс ICOLD по большим плотинам, Стамбул, т. 3, pp 491–517
ICOLD (1996) Плотины и связанные с ними сооружения в холодном климате. Бюллетень ICOLD 105
Jacobsen S (1995) Образование накипи и растрескивание при испытании замораживания / оттаивания без герметизации портландцемента и бетонов на основе кварцевого дыма. Кандидат наук. диссертация, Норвежский технологический институт, Тронхейм
Johannesson B (2010) Изменение размеров и содержания льда в затвердевшем бетоне при различных температурах замерзания и оттаивания. Cem Concr Compos 32: 73–83
Статья Google Scholar
Кокубу М., Охаши К., Такеи С., Канаива А., Мурата С. (1967) Примеры разрушения поверхностей бетонных дамб в результате повреждения морозом.В: 9-й международный конгресс ICOLD по большим плотинам, Стамбул, т. 3, pp 31–51
Krus J (1996) Географически индуцированные циклы замораживания-оттаивания в шведских бетонных конструкциях. Отчет Королевского технологического института, Стокгольм
Lehtinen P (1979) Об износе бетона, наблюдаемом в плотинах и гидротехнических сооружениях в Финляндии. В: 13-й международный конгресс ICOLD по большим плотинам, Нью-Дели, т. 2, pp 83–90
Линдмарк С. (1998) Механизмы образования отложений солевого инея на материалах, связанных портландцементом: исследования и гипотезы. Кандидат наук. докторская, Лундский университет, Лунд
Литван Г.Г. (1976) Морозостойкость цемента в присутствии антиобледенителей. Cem Concr Res 6: 351–356
Статья Google Scholar
MacInnis C, Whiting JD (1979) Морозостойкость бетона, подвергнутого действию антиобледенительного агента. Cem Concr Res 9: 325–336
Статья Google Scholar
Penttala V (2006) Поверхностное и внутреннее разрушение бетона из-за солевых и незасоленных нагрузок замораживания-оттаивания.Cem Concr Res 36: 921–928
Статья Google Scholar
Пауэрс Т.С. (1945) Рабочая гипотеза для дальнейших исследований морозостойкости бетона. J Am Concr Inst 16: 245–272
Google Scholar
Powers TC (1949) Потребность в воздухе морозостойкого бетона. В: Proceedings of the Highway Research Board 29, Bull 33: 184–211
Powers TC (1954) Расстояние между пустотами как основа для производства воздухововлекающего бетона. J Am Concr Inst 25: 741–760
Google Scholar
Пауэрс ТК (1956) Морозостойкость бетона в раннем возрасте. В: Материалы симпозиума RILEM по зимнему бетонированию, Копенгаген, стр. 1–46. Перепечатано научно-исследовательскими лабораториями Портландцементной ассоциации, Бюллетень 71
Пауэрс Т.С., Браунъярд Т.Л. (1947) Исследования физических свойств затвердевшего портландцементного теста — Часть 8.Замерзание воды в затвердевшем портландцементном тесте. J Am Concr Inst 18: 933–969
Google Scholar
Пауэрс Т.С., Хельмут Р.А. (1953) Теория изменения объема затвердевшего портландцементного теста при замерзании. В: Proceedings of the road research board 32, Bull 46: 285–297
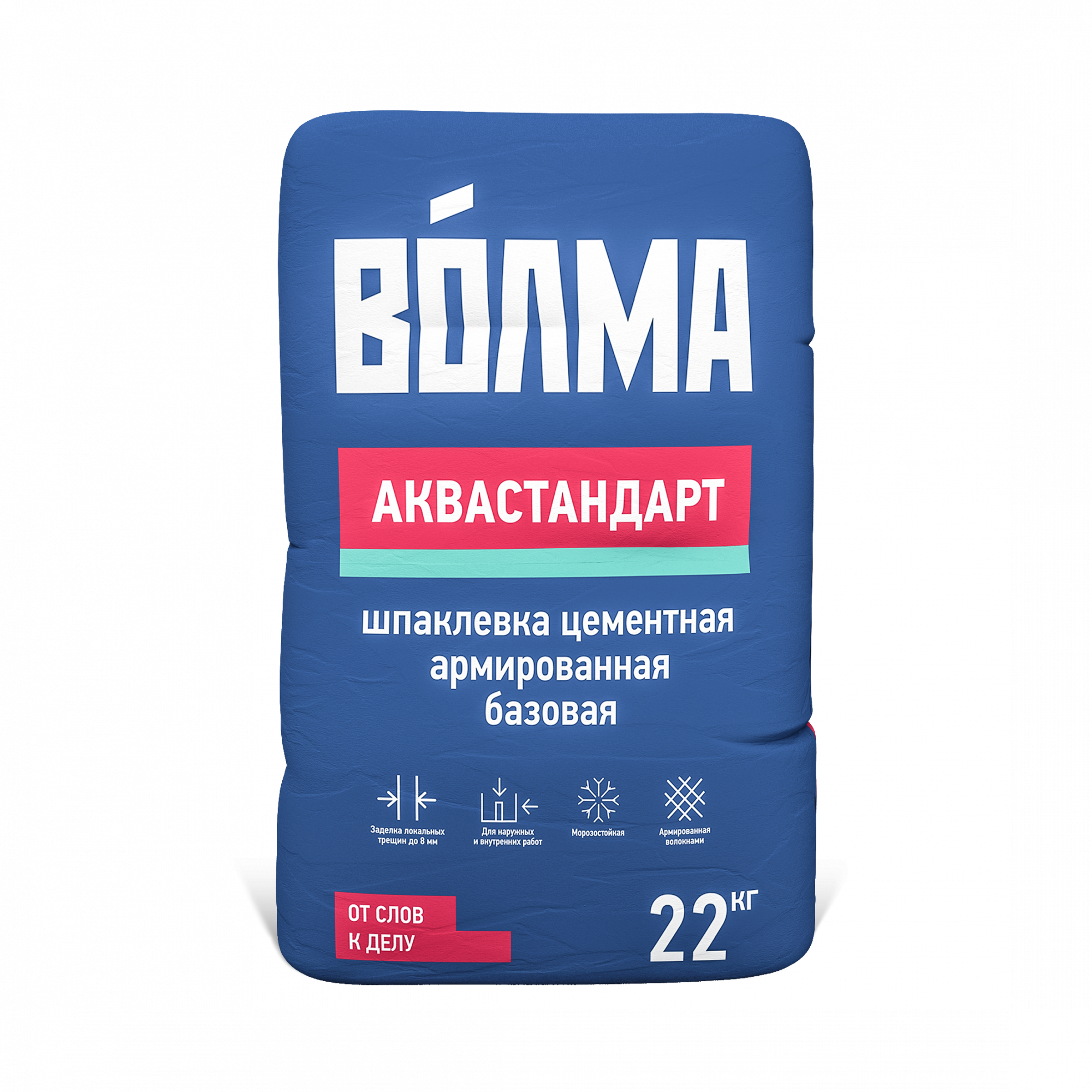
Setzer MJ (2002) Разработка модели микроледяной линзы. В кн .: Материалы 2-го международного семинара RILEM по морозостойкости бетона, Эссен, с. 133–145
Сетцер М.Дж., Фагерлунд Г., Янссен Д.Д. (1996) Тест CDF — метод испытаний на сопротивление замораживанию-оттаиванию бетона — тесты с раствором хлорида натрия (CDF). Mater Struct 29: 523–528
Статья Google Scholar
SS 13 72 44 (1995) Испытания бетона — затвердевший бетон — образование накипи при замерзании. Шведский институт стандартов
Валенца JJ, Scherer GW (2007) Обзор масштабирования солей: II. Механизмы. Cem Concr Res 37: 1022–1034
Статья Google Scholar
Валенца Дж. Дж., Шерер Г. В. (2007) Механизм образования солей на цементной поверхности. Mater Struct 40: 259–268
Статья Google Scholar
Исследование коррозионной / проницаемости / морозостойкости бетона экспериментальным и микроскопическим методами при различных соотношениях воды и связующего | Международный журнал бетонных конструкций и материалов
Влияние различных методов погружения бетона в агрессивную среду
Метод погружения является одним из наиболее важных факторов коррозии бетона.Различные методы погружения приводят к разным продуктам коррозии. Влияние на прочность на сжатие и изгиб бетона было проанализировано с использованием трех методов погружения: половинного замачивания, полного замачивания (типичный метод коррозии в реальных конструкциях, рис. 3) и сухой-влажной циркуляции.
Рис. 3Коррозионный процесс бетона.
Результаты испытаний на прочность приведены на рис. 4, и каждая полоса указывает определенный метод коррозии, чтобы было легче увидеть разницу в изменении прочности образцов бетона с различной степенью коррозии. Прочность на сжатие и изгиб бетона снизились при трех методах погружения с непрерывным увеличением времени коррозии. Коэффициенты устойчивости к коррозии при сжатии через 50 дней и 100 дней были в 0,99 раза и 0,85 раза выше, чем до коррозии при испытании на полное погружение, соответственно. Коэффициенты коррозионной стойкости и сопротивления сжатию через 50 дней и 100 дней были в 0,95 раза и 0,80 раза выше, чем до коррозии в испытании на половину погружения, соответственно.Коэффициенты устойчивости к коррозии при сжатии через 50 дней и 100 дней были в 0,88 раза и 0,69 раза выше, чем до коррозии при испытании на полное погружение, соответственно. Коэффициенты коррозионной стойкости и сопротивления изгибу через 50 и 100 дней были в 0,95 раза и 0,86 раза выше, чем до коррозии при испытании на полное погружение, соответственно. Коэффициенты коррозионной стойкости и сопротивления изгибу через 50 и 100 дней были в 0,88 раза и 0,70 раза выше, чем до коррозии в испытании на половину погружения, соответственно.Коэффициенты коррозионной стойкости и сопротивления изгибу через 50 дней и 100 дней были в 0,78 раза и 0,53 раза выше, чем до коррозии при испытании на полное погружение, соответственно. Результаты исследования показали, что коррозия при полном погружении была самой слабой, коррозия при половинном погружении — на втором месте, а коррозия при цикле «сухой-влажный» была самой сильной.
Влияние трех методов погружения на прочность бетона С20.
На рис. 5 показано, что коэффициент сопротивления коррозии сопротивления сжатию и коэффициент сопротивления коррозии сопротивления изгибу были выше через 50 дней по сравнению с таковыми до коррозии.Коррозионно-стойкие коэффициенты сопротивления сжатию при полном погружении, половинном погружении и циклах «сухой-влажный» за 50 дней были в 1,05, 1,04 и 0,91 раза выше, чем до коррозии, соответственно. Коэффициенты коррозионной стойкости и сопротивления изгибу при полном погружении, половинном погружении и циклах «сухой-влажный» были в 1,00, 0,95 и 0,87 раза выше, чем до коррозии, соответственно. Правило было таким же, как и на рис. 4: результаты исследований показали, что коррозия при полном погружении была самой слабой, коррозия при половинном погружении была второй, а коррозия при цикле «сухой-мокрый» была самой сильной.На рисунке 6 показано, что коэффициенты устойчивости к коррозии сопротивления сжатию и коэффициенты сопротивления коррозии сопротивления изгибу через 50 дней и 100 дней были больше по сравнению с коэффициентами до коррозии. Коэффициент коррозионной стойкости имеет тенденцию к увеличению с 50 до 100 дней. Последний был преобладающим в вышеуказанных условиях, а коэффициент сопротивления коррозии сопротивления сжатию и коэффициент сопротивления коррозии сопротивления изгибу были выше, чем у бетона C40.
Влияние трех методов коррозии на прочность бетона С30.
Рис. 6Влияние трех методов коррозии на прочность бетона С40.
На рисунке 7 показано, что коэффициент сопротивления коррозии сопротивления сжатию и коэффициент сопротивления коррозии сопротивления изгибу через 50 дней и 100 дней были больше по сравнению с таковыми до коррозии. Диапазон увеличения коэффициента сопротивления коррозии сопротивления сжатию и коэффициента сопротивления коррозии сопротивления изгибу для IH был больше, чем для IF, в процессе коррозии от 50 дней до 100 дней при трех условиях коррозии.Точно так же диапазон увеличения для IC был больше, чем для коэффициента коррозионной стойкости IH сопротивления сжатию и коэффициента коррозионной стойкости сопротивления изгибу. Это показывает, что бетон C50 имеет хорошую коррозионную стойкость.
Рис. 7Влияние трех методов коррозии на прочность бетона С50.
$$ {\ text {Na}} _ {2} {\ text {SO}} _ {4} {\ text {+ 10H}} _ {2} {\ text {O}} \ to {\ text { Na}} _ {2} {\ text {SO}} _ {4} \ cdot 1 0 {\ text {H}} _ {2} {\ text {O}} $$
(8)
$$ {\ text {Na}} _ {2} {\ text {SO}} _ {4} \ cdot 1 0 {\ text {H}} _ {2} {\ text {O}} + {\ текст {Ca}} _ {2} \ left ({\ text {OH}} \ right) _ {2} \ to {\ text {Ca}} _ {2} {\ text {SO}} _ {4} \ cdot 2 {\ text {H}} _ {2} {\ text {O + 2NaOH}} + 8 {\ text {H}} _ {2} {\ text {O}} $$
(9)
$$ {\ text {MgSO}} _ {4} + {\ text {Ca}} _ {2} \ left ({\ text {OH}} \ right) _ {2} + 2 {\ text {H }} _ {2} {\ text {O}} \ to {\ text {Ca}} _ {2} {\ text {SO}} _ {4} \ cdot 2 {\ text {H}} _ {2 } {\ text {O + Na (OH)}} {} _ {2} $$
(10)
$$ 3 {\ text {Ca}} _ {2} {\ text {SO}} _ {4} \ cdot 2 {\ text {H}} _ {2} {\ text {O + 4CaO}} \ cdot {\ text {Al}} _ {2} {\ text {O}} _ {3} \ cdot 1 2 {\ text {H}} _ {2} {\ text {O + 14H}} _ {2} {\ text {O}} \ to 3 {\ text {CaO}} \ cdot {\ text {Al}} _ {2} {\ text {O}} _ {3} \ cdot 3 {\ text {Ca} } _ {2} {\ text {SO}} _ {4} \ cdot 1 2 {\ text {H}} _ {2} {\ text {O + Ca}} _ {2} \ left ({\ text {OH}} \ right) _ {2} $$
(11)
Во время испытаний на сульфатостойкость образцов бетона сульфат-ионы проникают в образцы бетона, и сульфат стимулирует гидратацию вяжущих материалов, превращение безводного Na 2 SO 4 в Na 2 SO 4 · 10H 2 O увеличивает громкость примерно на 3. 1 раз, преобразование Na 2 SO 4 · 10H 2 O и MgSO 4 в Ca 2 SO 4 · 2H 2 O увеличивает объем примерно в 2 раза, и реакция AFt (эттрингит) увеличивает объем примерно в 1,2 раза. Также на ранней стадии реакции поры заполняются кристаллами соли, которые повышают прочность бетона. При продолжающейся кристаллизации давление кристаллизации приведет к неравномерному расширению бетона, поскольку увеличивающееся образование гидратированных продуктов, таких как эттрингит и гипс, заполняет поры.Наконец, бетон трескается, когда давление кристаллизации превышает предел прочности бетона. Следовательно, прочность бетона в конечном итоге снижается из-за одновременного действия физической и химической коррозии, вызванной процессом солеобразования.
Влияние разной прочности бетона в агрессивных средах
Прочность бетона — еще один очень важный фактор, влияющий на коррозию бетона. На рисунке 8 показаны прочность и коррозионная стойкость бетона различной прочности в агрессивной среде.
Рис. 8Влияние прочности бетона на коррозию.
Коррозионно-стойкий коэффициент сопротивления сжатию был меньше 1 через 50 дней и 100 дней для бетона C20 на рис. 8а, а коэффициенты сопротивления сжатию других классов прочности бетона были больше 1 через 50 дней и 100 дней. Коэффициенты коррозионной стойкости бетона на изгиб от C20 до C40 были меньше 1 через 50 и 100 дней, за исключением бетона C50 на рис.8а. Правила коррозии для бетона различной прочности на рис. 8b такие же, как на рис. 8а. Коррозионно-стойкий коэффициент сопротивления сжатию и коррозионно-стойкий коэффициент сопротивления изгибу были менее 1 через 50 дней и 100 дней для бетона C20 на рис. 8c. Коэффициент сопротивления коррозии сопротивления сжатию и коэффициент устойчивости к коррозии сопротивления изгибу были больше 1, когда бетон C30 подвергался коррозии в течение 50 дней, а коэффициент устойчивости к коррозии сопротивления сжатию и коэффициент устойчивости к коррозии сопротивления изгибу были меньше 1, когда время коррозии достигло 100 дней. Коэффициент сопротивления коррозии сопротивления сжатию и коэффициент устойчивости к коррозии сопротивления изгибу были больше 1, когда время коррозии бетона C40 и C50 составляло 50 дней и 100 дней.
Образцы бетона C20, C30, C40, C50 подвергались коррозии в сухом и влажном цикле в течение 50 дней отдельно, затем материалы для XRD-тестов были получены на 5 мм ниже поверхности этих образцов (рис. 9). Согласно рентгеноструктурному анализу, основными веществами в испытанных образцах бетона были C – S – H, AFt, Ca (OH) 2 , CaCO 3 и негидратированные частицы цемента.Кроме того, также наблюдаются CaSO 4 · 2H 2 O и Mg (OH) 2 . По мере снижения прочности бетона максимальные значения AFt, CaSO 4 и Mg (OH) 2 все увеличиваются. Согласно приведенному выше анализу, чем выше прочность бетона, тем выше его коррозионная стойкость. Из данных коэффициента прочностной коррозии видно, что антикоррозионные свойства бетона C40 и C50 были лучше, чем у бетона C20 и C30.Это говорит о том, что расчетная прочность бетона не должна быть ниже, чем у C40 в агрессивной среде.
Рис. 9Рентгенограммы различной прочности бетона в коррозионном растворе.
Морозостойкость бетона при различных соотношениях воды и связующего
Морозостойкость — очень важный показатель прочности бетона. Путем тестирования относительных динамических модулей упругости, потери массы и индекса замерзания-оттаивания был получен закон влияния прочности бетона при различных соотношениях воды и связующего.Результаты анализа представлены на рис. 10, 11 и 12.
Рис. 10Относительный динамический модуль упругости при циклах замораживания – оттаивания.
Рис. 11Потеря массы при замораживании – оттаивании.
Рис. 12 Показатели замораживания-оттаивания бетона различной прочности.
Из рис. 10 видно, что разрушение происходит в бетоне C20 после завершения 25 циклов замораживания – оттаивания, а относительный динамический модуль упругости составил всего 19,06, что очень мало.Бетон C30, бетон C40 и бетон C50 выдерживают до 300 циклов замораживания-оттаивания. По мере увеличения количества циклов замораживания-оттаивания относительный динамический модуль упругости бетона уменьшается. Относительный динамический модуль упругости бетона C40 был в 1,19 раза выше, чем у бетона C30 при 300 циклах замораживания-оттаивания. Относительный динамический модуль упругости бетона C50 был в 1,23 раза выше, чем у бетона C30 при 300 циклах замораживания-оттаивания. Относительный динамический модуль упругости бетона C50 составлял всего 1.В 3 раза больше, чем у бетона C40 при 300 циклах замораживания-оттаивания. Чем выше прочность бетона, тем больше его относительный динамический модуль упругости.
Рисунок 11 показывает, что потеря массы из-за разной прочности бетона была очень небольшой при циклах замораживания-оттаивания. Диапазон потери массы составлял от 0,1 до — 0,21, и правило изменения не было очевидным. Оценка сопротивления бетона замерзанию по потере массы не была очевидной по сравнению с относительным динамическим модулем упругости. Таким образом, относительный динамический модуль упругости рекомендуется для оценки морозостойкости бетона.
Видно, что при анализе класса прочности бетона и индекса морозостойкости на рис. 12 индекс промерзания-оттаивания составил всего 1,59%, а повреждение произошло после 25 циклов замораживания-оттаивания бетона С20. Показатели морозостойкости бетона C40 и бетона C50 были в 1,19 раза и 1,23 раза выше, чем у бетона C30 соответственно. Чем выше прочность бетона, тем выше индекс промерзания и оттаивания и лучше морозостойкость. Повышение прочности бетона — эффективный метод повышения морозостойкости бетона.Однако, когда бетон был в определенной степени улучшен, улучшение морозостойкости не было очевидным. Например, индекс сопротивления замораживанию-оттаиванию бетона C40 составил 93,07, а бетона C50 — 96,29. Показатели морозостойкости были очень близки. Поэтому рекомендуется выбирать подходящую марку прочности бетона, отвечающую требованиям морозостойкости и долговечности бетона.
Противопроницаемость бетона при различных соотношениях воды и связующего
Непроницаемость бетона — важный показатель, отражающий устойчивость бетона к проникновению внешних материалов.Электрический поток — это ток, проходящий через бетонный образец, который используется для оценки прочности антипроницаемости.
На рисунке 13 показано, что электрические потоки для бетона C30, бетона C40 и бетона C50 были в 0,89 раза, 0,67 раза и 0,53 раза больше, чем для бетона C20, соответственно. Электрический поток уменьшался по мере увеличения прочности бетона. Чем выше прочность бетона, тем лучше его водонепроницаемость.
Рис. 13Электрический поток разной прочности бетона.
Цементная плитка морозостойкая? — Часто задаваемые вопросы о цементной плитке — Цементная плитка
Мы слышим много мнений о том, является ли энкаустическая цементная плитка «морозостойкой». Там, где мы находимся, температура редко опускается намного ниже точки замерзания, здесь это сложно проверить. По этой причине мы решили использовать нашу морозильную камеру Maytag для тестирования. Предполагается, что внутренняя температура домашней морозильной камеры близка к нулю градусов по Фаренгейту.
Мы использовали квадратную часть тайла Surf «Agua», оставшуюся после работы с плиткой.Этот кусок плитки размером примерно 8 дюймов на 8 дюймов сначала вымачивали на несколько часов в воде, а затем запечатывали в пакет с застежкой-молнией и помещали в морозильную камеру. Когда его сняли и дали оттаять на открытом воздухе, видимых повреждений не было.
Затем мы взяли ту же плитку и погрузили половину в таз с водой, а верхнюю половину оставили вне воды. Это было помещено в морозильную камеру. Вода в это время замерзла. Ему дали оттаять на солнце, и никаких видимых повреждений не наблюдалось.
Мы повторяем это снова и снова, и каждый раз … Никаких изменений в плитке.
Основываясь на этом эксперименте, я бы не побоялся использовать нашу цементную плитку на открытом воздухе в той части страны, где бывает холодная погода, но VLT не дает никаких гарантий относительно замерзания. Я бы удостоверился, что плитка была установлена в твердый слой раствора (без туннельных потоков воздуха под плиткой), и что плитка была надежно залита раствором и запечатана.
Как и во многих других случаях, я думаю, что риск разрушения плитки на открытом воздухе связан с тем, что вода поднимется под плитку и расширится при замерзании.Это может привести к появлению трещин и подъему плитки.
На фото выше крупным планом показан край плитки, который мы неоднократно замораживали и оттаивали. Вы можете увидеть неповрежденный цветной слой износа на лицевой стороне плитки.
Мы продолжим тестировать нашу плитку и поставить тот же кусок, который этим летом неоднократно подвергался замораживанию / оттаиванию под палящим солнцем, и если мы когда-нибудь увидим какие-либо признаки ухудшения, мы сообщим об этом здесь.
— Ланди Уайлдер
Haws Круглый морозостойкий бетонный фонтан
Фонтаны для питья на круглых бетонных пьедесталах с вибро-литым армированием
Эти модели морозостойкие, антивандальные, круглые, из виброустойчивого железобетона.
питьевые фонтанчики на пьедестале, которые можно использовать круглый год, когда температура может опускаться ниже нуля.Модель
включает удлинитель капота для защиты полированной хромированной головки барботера и пневматическую кнопку
Система клапанов, устойчивая к замерзанию. Круглая конструкция пьедестала позволяет удобно размещать фонтан в различных помещениях.
локации, не занимая слишком много места.
Головка барботера, кнопка и фильтр для отходов отполированы, хромированы и защищены от вандализма. Легко использовать кнопка требует менее 5 фунтов.чтобы активировать, делая эти питьевые фонтанчики простыми для питья. Выбирайте из широкого ассортимента различных вариантов цвета цемента и отделки, чтобы подобрать эти питьевые фонтанчики к любой среде. Для более детального просмотра Для выбора цвета и отделки выберите вариант цвета, показанный ниже.
Клапаны морозостойкие
Модель 6518FR — это полностью спроектированная система с пневматическим приводом. с приводом от замораживания заглубляющий клапан установлен ниже линии замерзания, с обратным клапаном для слива воды из устройство, когда оно не используется, и для предотвращения перекрестного загрязнения обратным потоком.Подходящие товары
Модель 3060FR
Устаревший номер модели ‘3060FR’, ‘3060FR-CC’, ‘3060FR-CF’ и ‘3060FR-CCF’
Теперь требуются 3060FR, 3060FR-CC, 3060FR-CF или 3060FR-CCF и одна из клапанных систем (модель 6518FR), перечисленных ниже (продаются отдельно) для полного блока.
- Модель 3060FR — Фонтан на круглой подставке (морозостойкий).
- Модель 3060FR-CC — Цементный круглый пьедестал (устойчивый к замерзанию), изготовленный по индивидуальному заказу.
- Модель 3060FR-CF — Пьедестал круглой формы с нестандартной отделкой (морозостойкий) поилочный фонтанчик.
- Модель 3060FR-CCF — Круглый пьедестал нестандартного цвета и отделки (морозостойкий).
- Модель 6518FR — клапанная система (устойчивая к замерзанию), полностью сконструированный клапан с пневматическим управлением. Применяется для 2 барботеров.
Haws производит все фонтанчики для питья, которые не содержат свинца по всем известным определениям, включая
Стандарт ANSI / NSF 61, раздел 9,
Предложение 65 Калифорнии и
Федеральный закон о безопасной питьевой воде.
% PDF-1.6 % 1 0 obj > эндобдж 4 0 obj > эндобдж 2 0 obj > транслировать 2011-02-08T14: 11: 26 + 01: 002011-02-14T09: 59: 34 + 01: 002011-02-14T09: 59: 34 + 01: 00Adobe Acrobat 9.41 Подключаемый модуль захвата бумаги / pdfuuid: 810cf7a1-6c3d-4652-a165-c6e9f6df342euuid: 7842e6a6-3931-4c8f-b773-4d30139b0922 конечный поток эндобдж 3 0 obj > эндобдж 5 0 obj > / XObject> >> / Аннотации [51 0 R 52 0 R 53 0 R 54 0 R] / Родитель 3 0 R / MediaBox [0 0 595 842] >> эндобдж 6 0 obj > / Шрифт> / ProcSet [/ PDF / Text / ImageB] >> / Тип / Страница >> эндобдж 7 0 объект > / Шрифт> / ProcSet [/ PDF / Text / ImageB] >> / Тип / Страница >> эндобдж 8 0 объект > / Шрифт> / ProcSet [/ PDF / Text / ImageB] >> / Тип / Страница >> эндобдж 9 0 объект > / Шрифт> / ProcSet [/ PDF / Text / ImageB] >> / Тип / Страница >> эндобдж 10 0 obj > / Шрифт> / ProcSet [/ PDF / Text / ImageB] >> / Тип / Страница >> эндобдж 11 0 объект > / Шрифт> / ProcSet [/ PDF / Text / ImageB] >> / Тип / Страница >> эндобдж 12 0 объект > / Шрифт> / ProcSet [/ PDF / Text / ImageB] >> / Тип / Страница >> эндобдж 13 0 объект > / Шрифт> / ProcSet [/ PDF / Text / ImageB] >> / Тип / Страница >> эндобдж 14 0 объект > / Шрифт> / ProcSet [/ PDF / Text / ImageB] >> / Тип / Страница >> эндобдж 15 0 объект > / Шрифт> / ProcSet [/ PDF / Text / ImageB] >> / Тип / Страница >> эндобдж 16 0 объект > / Шрифт> / ProcSet [/ PDF / Text / ImageB] >> / Тип / Страница >> эндобдж 17 0 объект > / Шрифт> / ProcSet [/ PDF / Text / ImageB] >> / Тип / Страница >> эндобдж 18 0 объект > / Шрифт> / ProcSet [/ PDF / Text / ImageB] >> / Тип / Страница >> эндобдж 19 0 объект > / Шрифт> / ProcSet [/ PDF / Text / ImageB] >> / Тип / Страница >> эндобдж 20 0 объект > / Шрифт> / ProcSet [/ PDF / Text / ImageB] >> / Тип / Страница >> эндобдж 21 0 объект > / Шрифт> / ProcSet [/ PDF / Text / ImageB] >> / Тип / Страница >> эндобдж 22 0 объект > / Шрифт> / ProcSet [/ PDF / Text / ImageB] >> / Тип / Страница >> эндобдж 23 0 объект > / Шрифт> / ProcSet [/ PDF / Text / ImageB] >> / Тип / Страница >> эндобдж 24 0 объект > / Шрифт> / ProcSet [/ PDF / Text / ImageB] >> / Тип / Страница >> эндобдж 25 0 объект > / Шрифт> / ProcSet [/ PDF / Text / ImageB] >> / Тип / Страница >> эндобдж 26 0 объект > / Шрифт> / ProcSet [/ PDF / Text / ImageB] >> / Тип / Страница >> эндобдж 27 0 объект > / Шрифт> / ProcSet [/ PDF / Text / ImageB] >> / Тип / Страница >> эндобдж 28 0 объект > / Шрифт> / ProcSet [/ PDF / Text / ImageB] >> / Тип / Страница >> эндобдж 29 0 объект > / Шрифт> / ProcSet [/ PDF / Text / ImageB] >> / Тип / Страница >> эндобдж 30 0 объект > / Шрифт> / ProcSet [/ PDF / Text / ImageB] >> / Тип / Страница >> эндобдж 31 0 объект > / Шрифт> / ProcSet [/ PDF / Text / ImageB] >> / Тип / Страница >> эндобдж 32 0 объект > / Шрифт> / ProcSet [/ PDF / Text / ImageB] >> / Тип / Страница >> эндобдж 33 0 объект > / Шрифт> / ProcSet [/ PDF / Text / ImageB] >> / Тип / Страница >> эндобдж 34 0 объект > / Шрифт> / ProcSet [/ PDF / Text / ImageB] >> / Тип / Страница >> эндобдж 35 0 объект > / Шрифт> / ProcSet [/ PDF / Text / ImageB] >> / Тип / Страница >> эндобдж 36 0 объект > / Шрифт> / ProcSet [/ PDF / Text / ImageB] >> / Тип / Страница >> эндобдж 37 0 объект > / Шрифт> / ProcSet [/ PDF / Text / ImageB] >> / Тип / Страница >> эндобдж 38 0 объект > / Шрифт> / ProcSet [/ PDF / Text / ImageB] >> / Тип / Страница >> эндобдж 39 0 объект > / Шрифт> / ProcSet [/ PDF / Text / ImageB] >> / Тип / Страница >> эндобдж 40 0 объект > / Шрифт> / ProcSet [/ PDF / Text / ImageB] >> / Тип / Страница >> эндобдж 41 0 объект > / Шрифт> / ProcSet [/ PDF / Text / ImageB] >> / Тип / Страница >> эндобдж 42 0 объект > / Шрифт> / ProcSet [/ PDF / Text / ImageB] >> / Тип / Страница >> эндобдж 43 0 объект > / Шрифт> / ProcSet [/ PDF / Text / ImageB] >> / Тип / Страница >> эндобдж 44 0 объект > / Шрифт> / ProcSet [/ PDF / Text / ImageB] >> / Тип / Страница >> эндобдж 45 0 объект > / Шрифт> / ProcSet [/ PDF / Text / ImageB] >> / Тип / Страница >> эндобдж 46 0 объект > / Шрифт> / ProcSet [/ PDF / Text / ImageB] >> / Тип / Страница >> эндобдж 47 0 объект > транслировать xW [o6 &} h, Q [ʼn $ [i% $ ‘ڱ & ndC Y: m «; HFUXTU dШ ڠ v_e \ SC3! i] ҌѢ ڠډ Q , j * ojoxxYm9] / rub: of}; | # Gv0gS: {; \ dC0! U-5_: c \ xv ~~ 4WG4ZʜyZskvIU0? Qnʵe9) w # ӷ &] ⑀ȄK # ÈMF- # 1> ‘zVVkOQ «2D Ձ | @ ae;] 37 ^ `3Джм3 rCr0vX ܧ {ҀtA5X5fjQ / DE ڗ 3 YH
Морозостойкость бетонов, содержащих измельченный гранулированный доменный шлак
MATEC Web of Conferences 163 , 05001 (2018)Морозостойкость бетонов, содержащих измельченный гранулированный доменный шлак
Павел Луковски 1 * , Али Салих 2 и Джоанна Дж. Соколовская 1
1 Варшавский технологический университет, факультет гражданского строительства, ул. Armii Ludowej 16, Варшава 00-637, Польша
2 Roadstone Ltd., A CRH Group Company, Фортунестаун, Таллахт, Дублин 24, Ирландия
* Автор, ответственный за переписку: [email protected]
Аннотация
В статье рассматривается влияние добавки измельченного гранулированного доменного шлака (ГГШ) на морозостойкость бетона.GGBS — ценный модификатор бетона, обладающий скрытыми гидравлическими свойствами и особенно улучшающий химическую стойкость бетона. Однако характеристики бетонов с доменным шлаком при замораживании и оттаивании до сих пор полностью не объяснены и остаются предметом обсуждения. Авторы исследовали бетоны, содержащие различные количества GGBS и портландцемента CEM I, с различными значениями отношения воды к вяжущему, с использованием и без использования воздухововлекающей добавки.Результаты исследований показывают, что добавка доменного шлака вызывает некоторое ухудшение морозостойкости бетона. Степень этого ухудшения зависит от соотношения воды и вяжущего и аэрации бетона. Однако даже при наименее благоприятных условиях бетон с добавкой ГГБС соответствовал требованиям по морозостойкости после 200 циклов замораживания и оттаивания, приведенным в Стандарте PN-B-06265.
© Авторы, опубликовано EDP Sciences, 2018
Это статья в открытом доступе, распространяемая в соответствии с условиями лицензии Creative Commons Attribution License 4.0, что разрешает неограниченное использование, распространение и воспроизведение на любом носителе при условии правильного цитирования оригинальной работы. (http://creativecommons.org/licenses/by/4.0/).
Устойчивость к замораживанию-оттаиванию бетона с воздухововлекающими добавками
Одним из наиболее разрушительных воздействий на бетон является резкое изменение температуры (циклы замораживания-оттаивания). Типы разрушения бетонных конструкций в результате циклического замораживания-оттаивания в основном можно разделить на поверхностное образование отложений (характеризующееся потерей веса) и рост внутренних трещин (характеризующееся потерей динамического модуля упругости).В настоящем исследовании изучалась долговечность бетона, изготовленного с воздухововлекающим агентом, после 0, 100, 200, 300 и 400 циклов замораживания-оттаивания. Экспериментальные исследования образцов бетона с воздухововлекающими добавками C20, C25, C30, C40 и C50 были выполнены в соответствии с «Методикой испытаний на длительность и прочность на обычном бетоне» GB / T 50082-2009. Динамический модуль упругости и потеря веса образцов измеряли после различных циклов замораживания-оттаивания. Было проанализировано влияние циклов замораживания-оттаивания на относительный динамический модуль упругости и потерю веса.Результаты показали, что динамический модуль упругости и вес уменьшались по мере повторения циклов замораживания-оттаивания. Согласно результатам экспериментов, они показали, что воздухововлекающий бетон C30, C40 и C50 по-прежнему оставался прочным после 300 циклов замораживания-оттаивания.
1. Введение
Бетон считается одним из самых неоднородных и требовательных инженерных материалов, используемых человечеством. Прочность [1–5] бетона определяется как способность выдерживать разрушающее воздействие окружающей среды без ухудшения в течение определенного периода времени.Долговечность бетона включает в себя устойчивость к морозу, коррозии, проникновению, карбонизации, коррозии под напряжением, химическому воздействию и так далее.
Бетон может быть поврежден, если он подвергается циклам замораживания-оттаивания. Американский институт бетона (ACI) установил спецификации для защиты бетона, укладываемого в холодную погоду. ACI определил холодную погоду как период, когда более трех дней подряд средняя дневная температура воздуха ниже 40 F (Фаренгейта). Устойчивость бетона к замораживанию-оттаиванию имеет первостепенное значение в странах с отрицательными температурными условиями, таких как Арктическая зона, Россия, Северный Китай и Китай. Повреждение от замерзания, прогрессирующее разрушение, которое начинается с отслоения поверхности или накипи и заканчивается полным обрушением, является серьезной проблемой, когда бетон используется в более холодных регионах. Ухудшение продолжается по мере повторения циклов замораживания и оттаивания, и материал постепенно теряет свою жесткость и прочность. Вдобавок индуцируется возрастающее необратимое расширение. Так что повреждение от мороза — очень сложный процесс утомления. Повышение морозостойкости и продление срока службы бетона представляло собой серьезную научно-техническую проблему.
Hong-Qiang et al. [4] и Ли-кун [5] исследовали относительный динамический модуль упругости (RDME) и потерю веса простого бетона после различных циклов замораживания-оттаивания. Sun et al. [6] исследовали потерю динамического модуля упругости высокопрочного бетона под действием нагрузки и циклов замерзания-оттаивания. Захариева и др. [7] исследовали влияние циклов замораживания-оттаивания на потерю динамического модуля упругости повторно используемого заполнителя бетона. Влияние раствора хлорида натрия, циклического замораживания-оттаивания и внешней нагрузки на относительный динамический модуль упругости (RDME) и потерю веса бетона было экспериментально исследовано Sun et al.[8]. Cohen et al. [9] исследовали относительный динамический модуль упругости (RDME) и потерю веса безвоздушного высокопрочного бетона после циклов замораживания-оттаивания.
Воздухововлекающий агент [10–13] рекомендован почти для всех бетонов, в основном для повышения устойчивости к циклам замораживания-оттаивания при воздействии воды и химикатов для борьбы с обледенением в холодных регионах. Было задокументировано очень мало исследований по устойчивости бетона с воздухововлекающими добавками к замерзанию и оттаиванию. В данной статье представлены экспериментальные исследования относительного динамического модуля упругости и потери веса бетонов с воздухововлекающими добавками C20, C25, C30, C40 и C50 после 0, 100, 200, 300 и 400 циклов замораживания-оттаивания в соответствии с « Метод испытаний на долговечность и долговечность на обычном бетоне »GB / T50082-2009 [14]. И влияние циклов замораживания-оттаивания на относительный динамический модуль упругости и потерю веса бетона с воздухововлекающими добавками C20, C25, C30, C40 и C50 было проанализировано в соответствии с экспериментальными результатами.
2. Методики экспериментов
2.1. Материалы и пропорции смеси
В этом исследовании использовались местные материалы. Использовался китайский стандарт (GB175-99) [15] портландцемент 425 (который имеет стандартную прочность на сжатие 42,5 МПа в возрасте 28 дней).Использовался природный речной песок с модулем крупности 2,6. Крупный заполнитель представлял собой щебень диаметром от 5 до 20 мм. Пропорции смеси приведены в таблице 1. Смешивание начинали после помещения в смеситель всего крупного и мелкого заполнителей. Эти ингредиенты перемешивали в течение примерно 1 мин, а затем за 1 мин добавляли воду с воздухововлекающим агентом. Наконец, после добавления всей воды перемешивание продолжалось примерно 2 мин.
2.2. Испытательные образцы и программы испытанийБыли подготовлены бетонные призмы размером (для определения потери веса и динамического модуля упругости).Образцы были отлиты в стальных формах, уплотнены внешней вибрацией и извлечены из формы через 24 часа. Все образцы были обработаны в условиях 95% относительной влажности в течение 23 дней. После этого образцы были погружены в воду на 4 дня перед циклами замораживания-оттаивания. Затем, когда возраст образцов составил 28 дней, образцы бетона с воздухововлекающими добавками были помещены в аппарат замораживания-оттаивания. В этой статье использовался аппарат для испытания на замораживание-оттаивание [16], отвечающий требованиям «метода испытаний на долговечность и долговечность обычного бетона» GB / T 50082-2009.Циклы замораживания-оттаивания состояли из поочередного понижения температуры образцов с 6 ° C до 6 ° C и повышения ее от до 6 ° C, в то время как температура антифриза варьировалась от до, а затем нагревается до всех в течение 2,5 ~ 3 часов. Динамический модуль упругости и потеря веса каждого образца были измерены перед помещением образцов размером 30 мм в устройство замораживания-оттаивания. Один образец размером 50 мм помещался в резиновый контейнер. В котором стандартные бетонные призмы были окружены водой.Образцы удаляли для тестирования, когда они находились в размороженном состоянии с интервалами в 50 или 100 циклов. 3.Результаты и обсужденияПоверхность разрушения образцов бетона с воздухововлекающими добавками C30, подвергшихся 0, 200 и 400 циклов замораживания-оттаивания, показано на рисунках 1 (а), 1 (б) и 1 (с). Микротрещины возникли после воздействия циклов замораживания и оттаивания, а затем крупные агрегаты и часть цемента были разделены из-за действия циклов замораживания-оттаивания. Таким образом, отслоение поверхности или образование накипи были вызваны циклами замораживания-оттаивания, как показано на рисунках 1 (b) и 1 (c). 3.1. Относительный динамический модуль упругостиRDME для бетона с воздухововлекающими добавками C20, C25, C30, C40 и C50 после различных циклов замораживания-оттаивания приведен в таблице 2.
Относительный динамический модуль упругости определяется следующим образом: где — относительный динамический модуль упругости при циклах замораживания-оттаивания, выраженный в процентах, рассчитанный как среднее значение трех образцов; — динамический модуль упругости при циклах замораживания-оттаивания; — динамический модуль упругости перед циклами замораживания-оттаивания. После 300 циклов замораживания-оттаивания образцы бетона с воздухововлекающими добавками C30, C40 и C50 показали небольшую потерю RDME, в то время как образцы бетона с воздухововлекающими добавками C20 и C25 показали значительную потерю RDME, как показано на рисунке 2. Как видно из таблицы 2 и рисунка 2, для бетона с воздухововлекающими добавками C20, C25, C30, C40 и C50 RDME медленно снижался в течение первых 200 циклов замораживания-оттаивания; RDME воздухововлекающего бетона C20, C25, C30, C40 и C50 составлял 96,70, 90,75, 94,60, 99,05 и 97,50 процентов после 200 циклов замораживания-оттаивания. Sun et al. [8] и Захариева и др. [7] исследовали влияние циклов замораживания-оттаивания на RDME простого бетона.Ли-кун сделал вывод о том, что RDME снизился до 62 процентов после 100 циклов замораживания-оттаивания. Hong-Qiang et al. обнаружили, что RDME снизился до 64 процентов после 100 циклов замораживания-оттаивания. Динамический модуль упругости — это отношение напряжения к деформации, когда напряжение наименьшее при динамических нагрузках. Его можно измерить с помощью продольной или изгибной вибрации. Он отражает характеристики эластичности материала, аналогично начальному тангенциальному модулю упругости при статических нагрузках.Потеря динамического модуля упругости при циклах замораживания-оттаивания означает потерю эластичности. Следовательно, влияние циклов замораживания-оттаивания на RDME простого бетона выше, чем на RDME бетона с воздухововлекающими добавками. 3.2. Потеря веса Одним из видов разрушения бетонных конструкций в результате циклического замораживания-оттаивания является образование накипи на поверхности. Накипь на поверхности — это потеря клея и раствора с поверхности бетона в результате циклического замораживания-оттаивания или внутренней реакции заполнителя (например.грамм. щелочно-кремнеземная реакция в бетоне, смешанном со щелочно-реактивным заполнителем). В таблице 3 приведен вес бетона с воздухововлекающими добавками после различных циклов замораживания-оттаивания. Потеря веса бетона с воздухововлекающими добавками в зависимости от количества циклов замораживания-оттаивания показана на рисунке 3.Потеря веса определяется следующим образом: где — потеря веса при циклах замораживания-оттаивания, выраженная в процентах, рассчитанная как среднее значение трех образцов; — вес при циклах замораживания-оттаивания; — вес до циклов замораживания-оттаивания.
Из таблицы 3 и рисунка 3 видно, что влияние циклов замораживания-оттаивания на потерю веса бетона с воздухововлекающими добавками C20 и C25 больше, чем влияние на потерю веса C30, C40. и воздухововлекающий бетон C50. После 200 циклов замораживания-оттаивания потеря веса составила 0,70, 0,67 и 0,25 процента для бетона с воздухововлекающими добавками C30, C40 и C50, в то время как потеря веса составила 2,35 и 3,58 процента для бетона с воздухововлекающими добавками C20 и C25. Результаты испытаний показывают, что потеря веса бетона с воздухововлекающими добавками C30 составила 0.20 процентов по сравнению с 1,81 процентом для простого бетона после 100 циклов замораживания-оттаивания [4]. Для бетона с воздухововлекающими добавками C20, C25, C30, C40 и C50 максимальная потеря веса составила всего 4,38 процента после 300 циклов замораживания-оттаивания. В то время как Hong-Qiang et al. [4] обнаружили, что потеря веса простого бетона C30 снизилась до 3,74 процента после 125 циклов замораживания-оттаивания. Для простого бетона увеличение веса наблюдалось Хун-Цяном [4] и Ли-куном [5] в течение первых 25 циклов замораживания-оттаивания. Для бетона с воздухововлекающими добавками увеличения веса не наблюдалось. Потеря веса бетонных образцов вызвана отслоением поверхности или отслоением. Изменение веса во время циклов замораживания-оттаивания происходит из-за движения внутрь и наружу воды в образце, а также из-за отделения поверхности или образования окалины (образование накипи — это потеря пасты и раствора с поверхности бетона в результате циклического замораживания-оттаивания). Как только возникнет микротрещина, испорченные зоны, заполненные окружающей водой, вызовут изменение веса образца. Если масса поверхностного отрыва больше, чем вода, поглощенная образцами бетона, вес образцов бетона увеличится.Вес бетонных образцов будет уменьшаться, когда масса поверхностного отрыва меньше, чем вода, поглощенная бетонными образцами. В реальных бетонных конструкциях поверхность бетона заметно покрывается отложениями при воздействии противообледенительной соли и циклов замораживания-оттаивания, вызванных изменением климата. Скорость цикла в лабораторных условиях была намного выше, чем в естественной среде, из-за быстрого изменения температуры.Таким образом, разумно, что образование накипи, наблюдаемое во время испытаний, было более серьезным, а глубина накипи на конкретных образцах была более 1 мм. 3.3. Ультразвуковая скоростьМногие конструкции, такие как мосты, туннели, плотины, здания и другие, были построены из бетонного материала. В течение жизненного цикла этих конструкций может происходить разрушение из-за механических, термических или химических нагрузок. Это часто приводит к развитию пористости, микротрещин и трещин в материале.Знание состояния бетонной конструкции необходимо для предотвращения или устранения повреждений, поэтому неразрушающая характеристика является важным способом, и часто предлагается ультразвуковой метод. В этой работе скорость ультразвука в бетоне с воздухововлекающими добавками C30 была измерена ультразвуковым методом в соответствии с «Правилами испытаний бетона для строительства портов и водоворотов» JTJ 270-98 [17]. В Таблице 4 показан процент уменьшения скорости ультразвука в бетоне с воздухововлекающими добавками после различных циклов замораживания-оттаивания.Из таблицы 4 видно, что скорость ультразвука медленно уменьшалась в течение первых 200 циклов замораживания-оттаивания, и это дало только примерно 2,4% снижение по сравнению с начальным значением. Однако в последующих циклах замораживания-оттаивания наблюдается, что ухудшение обычно продолжается. А после 400 циклов замораживания-оттаивания он снизился примерно до 84,7 процента от исходного значения.
3.4. ОбсуждениеБетон представляет собой трехфазную композитную структуру в микроскопическом масштабе, цементную матрицу, заполнитель и межфазную переходную зону между ними. Микротрещины будут вызваны действием циклов замораживания и оттаивания; направление и распространение микрокосмических трещин являются стохастическими. Микрокосмические трещины разнообразны и расширяются по мере повторения циклов замораживания-оттаивания.Бетон с воздухововлекающими добавками содержит миллиарды микроскопических ячеек с воздухом, когда воздухововлекающие агенты использовались в бетоне. Они уменьшают внутреннее давление на бетон, создавая крошечные камеры для расширения воды при замерзании. Таким образом, сравнивая результаты испытаний в этой статье с выводом других авторов [4, 5], умерший процент для относительного динамического модуля упругости и потери веса воздухововлекающего бетона меньше, чем у простого бетона после того же циклы замораживания-оттаивания.Это означает, что снижение морозостойкости бетона с воздухововлекающими добавками происходит медленнее, чем у обычного бетона. Это потому, что смешанный воздухововлекающий агент в бетоне может эффективно их составлять и, таким образом, улучшать его устойчивость к замораживанию-оттаиванию. 4. Заключение Было исследовано влияние циклов замораживания-оттаивания на RDME и потерю веса бетона с воздухововлекающими добавками C20, C25, C30, C40 и C50. Основываясь на экспериментальной работе в этом исследовании и обсуждении экспериментальных результатов, результаты исследования можно резюмировать следующим образом: (а) RDME уменьшался по мере повторения циклов замораживания-оттаивания. |