Газосиликатные блоки | Березовский КСИ
Технология изготовления газосиликатных блоков
Приготовление ячеисто-бетонной смеси
Дозировку компонентов смеси: песчаного шлама, шлама из отходов от резки, калибровки массивов и промывки смесителя, дополнительной воды, цемента, известково-песчаного вяжущего или молотой извести, алюминиевой суспензии производят автоматически при помощи весов с точностью ± 1 %.
Приготовление газобетонной смеси производится в смесителе с числом оборотов 1400 мин-1 .
Дозировка компонентов в смеситель производится в следующем порядке: шлам-отходы, песчаный шлам, дополнительная вода, цемент, известково-песчаное вяжущее или молотая известь, водно-алюминиевая суспензия. Время загрузки компонентов смеси в смеситель с одновременным перемешиванием должно быть не более 3 мин.
Управление процессом дозирования и смесеприготовления осуществляется с центрального пульта. Система управления процессом дозирования и смесеприготовления с программной памятью (SIMATICS 7) работает автоматически и управляется от компьютеров. Заливка смеси из смесителя производится в форму, при помощи распределительной системы.. По окончании процесса формования или перерыва в работе более 0,5 ч мешалка промывается водой в количестве 150-200 кг и отходы от промывки подаются в расходную емкость и далее в мешалку для перемешивания отходов при удалении «горбушки» и калибровки массивов и затем в шламбассейн для возвратного шлама.
Формование ячеисто-бетонного массива
Ячеисто-бетонная смесь заливается в формы, затем при помощи трансбордера устанавливается на ударный стол. По мере вспучивания бетонной смеси включается площадка с применением ударных воздействий (высота падения и частота удара настраивается),которые используются для тиксотропного разжижения ячеисто-бетонной смеси во время её вспучивания.
Созревание ячеисто – бетонного массива
Созревание ячеисто-бетонного массива происходит в камерах отверждения при температуре воздуха не менее 20 оС до приобретения требуемой пластической прочности сырца 1,5-2,7 ед.
Разрезание ячеисто-бетонного массива
Форма с «созревшим » массивом трансбордером передаётся к крану для перестановки и комплектации и кантуется на 90º.
Замки формы открываются, и корпус формы отделяется от сырца массива, и последний остаётся на запарочном днище (борт-поддон), который устанавливается на тележку резательной машины. Пустой корпус формы транспортируется к устройству для обратной подачи запарочных днищ, очищается и соединяется с последним в единую форму.
Установленный краном на тележку ячеисто-бетонный массив-сырец подаётся под резательные машины. На станции боковой обрезки и профилировки струнами (стальная, высокопрочная проволока диаметром (0,8-1,0) мм осуществляется боковая вертикальная калибровка сырца, а также, при необходимости, специальными стальными ножами, нарезка профилей ( «паз-гребень»).
Затем массив подается на продольную пилу для горизонтальной продольной резки, где производится его разрезка по ширине изделия с шагом равным 5 мм. Ширина изделий варьируется от 50 до 500 мм.
После этого массив подается на установку поперечной резки. Разрезка осуществляется за счет опускающейся сверху вниз рамы со струнами, совершающими колебательные движения; осуществляется фрезерование ручных захватов; вакуумным устройством снимается верхний срезанный слой (горбушка).
Разрезанный массив манипулятором устанавливается на автоклавную тележку.
Все отходы от калибровки и разрезки ячеисто-бетонного массива собираются из под резательных машин и используются при приготовлении смеси.
Автоклавная обработка
Разрезанный массив на запарочном днище устанавливается на автоклавную тележку и передается на пути накопления, откуда подаются в тупиковый автоклав 2,9 х 39 м, где производится тепловлажностная обработка.
С целью интенсификации твердения и сокращения времени автоклавной обработки осуществляется отвод конденсата из автоклава, перепуск пара из автоклава в автоклав. Процесс автоклавной обработки ведется по заданной программе в автоматическом или ручном режиме по утвержденным графикам в зависимости от плотности и ширины изделий. В зоне накопления перед автоклавами должен быть обеспечен влажностно-тепловой режим.
Размеры стеновых блоков — Монолит Ресурс
Большинство строительных технологий предусматривают использование различных стеновых блоков при возведении зданий и сооружений, особенно при строительстве малоэтажных домов и нежилых помещений. Стеновые блоки производятся из материалов, имеющих прекрасно подходящие для кладки стен характеристики, при этом предусмотрен выпуск продукции разного размера. Разнообразие размеров изделий облегчает проектирование зданий, экономит время при кладке, а также облегчает работу строителям.
Закажите керамзитобетонные блоки на выгодных условиях, позвонив нам по телефонам:
8-910-077-44-33
или отправляйте заявку через форму на сайте.
Классификация в зависимости от материала
Стеновые блоки можно классифицировать по нескольким признакам. В первую очередь, их можно разделить на группы в зависимости от материала, из которого они изготовлены. В настоящее время для производства стеновых блоков используют следующие материалы:
- железобетон;
- пенобетон;
- керамзитобетон;
- газосиликатный бетон;
- пескоцемент;
- гипс;
- шлак;
- керамическая глина;
- арболит;
- пеносиликатный бетон.
1. Железобетонные блоки изготавливаются на основе тяжелого бетонного раствора и обладают большой массой. Укрепленные прочной металлической арматурой, блоки из железобетона давно применяются даже при возведении многоэтажных зданий. Долгие годы эксплуатации построек из такой продукции доказали их прочность и устойчивость к износу. Основными характеристиками железобетонных изделий являются их устойчивость к влажной среде и прекрасные звукоизоляционные свойства.
2. Для изготовления стеновых блоков из пенобетона в цементный раствор добавляется пена, имеющая специфический состав. Такие изделия используются для постройки малоэтажных жилых и офисных зданий, а также хозяйственных построек. Блоки из пенобетона применяются как для кладки стен, так и для их облицовки. Главные плюсы — высокие теплоизоляционные свойства, небольшой вес и доступная цена.
3. Керамзитобетон, использующийся для производства керамзитобетонных стеновых блоков, по своим свойствам близок к железобетону, но обладает более легким весом. Изделия из керамзитобетона можно использовать как при кладке несущих стен, так и для возведения второстепенных межкомнатных перегородок. Основными их достоинствами являются небольшая масса и хорошие звуко- и теплоизоляционные свойства.
4. В состав бетона, из которого изготавливают газосиликатные блоки, входят кварцевый песок, известь и различные отвердители и газообразователи. Такая продукция имеет ячеистую структуру благодаря газообразованию в процессе производства и отличается прекрасными огнеупорными и шумоизоляционными качествами. Как правило, газосиликатные блоки часто используются для строительства 1-2х-этажных жилых домов и нежилых помещений.
5. Пескоцементные стеновые блоки, как и железобетонные, изготавливаются из тяжелых бетонных смесей на основе песка и отличаются большим весом. Большая масса изделий из пескоцемента позволяет использовать их для кладки несущих конструкций при постройке малоэтажных зданий, хорошие прочностные показатели обеспечивают долговечность таких построек. Также пескоцементные блоки обладают хорошей морозостойкостью и огнеупорностью.
6. На основе гипса с различными специальными добавками производятся пазогребневые блоки. Так как гипс не является особопрочным материалом, такие изделия обычно применяются для постройки ненесущих стен и облицовки уже готовых помещений. К положительным свойствам пазогребневых блоков можно отнести хорошие шумо- и звукоизоляционные качества, небольшой вес, а также устойчивость к появлению коррозии.
7. Шлакоблоки изготавливают на основе шлакобетонного раствора из различных производственных отходов. Такой вид стеновых блоков не обладает особой прочностью и используется для кладки стен, которые не будут испытывать несущие нагрузки. К достоинствам таких стройматериалов относят их низкую стоимость, сравнительно небольшой вес и долговечность.
8. На основе красной глины с добавлением описок производят достаточно востребованные в настоящее время керамоблоки. Этот вид стеновых блоков обладает улучшенными теплоизоляционными свойствами и небольшим весом, а также прекрасной устойчивостью к действию огня. Дополнительно можно выделить их высокую экологичность и отсутствие токсических выделений.
9. Арболитовые блоки изготавливают на основе особого вида легкого бетона — арболита. Такие изделия по физическим свойствам близки к деревянным, так как в состав бетонной смеси для их производства входит преимущественно деревянная щепа, иногда ее содержание доходит до 90%. Оригинальным составом бетона объясняются отличные тепло- и звукоизоляционные качества этой продукции вкупе с хорошим воздухообменом.
10. Пеносиликатные блоки производятся из легкого бетона, состав которого похож на пенобетон, но вместо цемента используется кварцевый песок, также добавляются некоторые дополнительные составляющие. Такие изделия используют для кладки и облицовки стен в невысоких строениях, они широко востребованы по причине своей легкости и простоты кладки и дальнейшей обработки.
Классификация в зависимости от габаритов
Следующим признаком, по которому можно классифицировать стеновые блоки, являются их размеры. Блоки для кладки стен из разных материалов имеют отличающиеся друг от друга размеры, также, для удобства кладки, изделия из одного материала делают различной длины, ширины и высоты. Таким образом, их можно разделить на две большие группы:
- малоразмерные;
- крупногабаритные.
Обычно к крупноразмерным блокам относят изделия с габаритами от 600х300х200 и крупнее. Более мелкие блоки считаются малоразмерными.
Использование малоразмерных стеновых блоков
Стеновые блоки небольшого размера могут быть использованы для нескольких видов строительных работ.
1. Основным назначением, как и следует из названия строительного материала, является выгонка стен в малоэтажных строениях и кладка второстепенных перегородок. Стройматериалы небольшого размера обычно изготовлены из легких материалов, поэтому из них не строят несущие стены и конструкции. Легкие блоки просто не выдержат постоянной ощутимой нагрузки, и такая стена будет недолговечной.
2. Кроме малоэтажных зданий, небольшие стеновые блоки используются для обустройства перегородок в многоэтажных жилых или офисных помещениях. При кладке несущих стен многоэтажки из прочного железобетона, вполне допустимо использовать легкие малоразмерные блоки для кладки второстепенных перемычек, не имеющих значения для распределения общих нагрузок в строении.
3. Небольшой размер удобен для быстрой кладки стен, так как вес и габариты изделий позволяют достаточно легко управляться с ними одному работнику. Опыт использования стеновых блоков показал, что их кладка осуществляется в 4-6 раз быстрее, чем кладка аналогичной стены из кирпича. Использование таких материалов позволяет значительно увеличить темп строительных работ и ускорить сроки сдачи объекта заказчику.
4. Кроме кладки стен, малоразмерные блоки можно использовать для заполнения пустоты в несущих конструкциях многоэтажных строений, которые обустроены в виде каркаса из двух железобетонных плит с промежутком между ними. Уложенные в этот промежуток легкие небольшие блоки значительно улучшают тепло- и звукоизоляционные характеристики помещения.
5. Еще одним назначением некоторых видов блоков является облицовка уже готовых стен. Для облицовки строения со стороны улицы обычно используют специальную продукцию, имеющую наружный декоративный облицовочный слой. Сегодня выпускаются изделия с разным декором, и у владельцев возводящихся строений есть возможность подобрать устраивающий их дизайн дома.
Из чего делают малоразмерные блоки?
Малогабаритные стеновые блоки производят из легких бетонных смесей, на выходе получая изделия как с плотной, так и с ячеистой структурой.
К изделиям из легких видов бетона относятся блоки:
- шлакобетонные;
- керамзитобетонные;
- пемзосодержащие;
- с арболитом;
- из полистиролбетона.
Для производства ячеистобетонных изделий используют материалы следующих видов:
- пенобетон;
- газосиликатный бетон;
- газобетон;
- пенозолобетон;
- пеносиликат;
- газозолобетон.
Применение крупногабаритных стеновых блоков
Крупные блоки используют для выгонки несущих стен, которые при эксплуатации здания будут выдерживать значительные нагрузки. Такие стены должны иметь большую толщину и выкладываются из тяжелых крупногабаритных стройматериалов. Большой вес таких изделий не предполагает их ручную укладку, для работы со стеновыми блоками подобных габаритов необходимо использовать специальное оборудование для подъема и перемещения грузов.
Так как достаточно большая длина изделий не допускает разных вариантов их укладки, крупные стеновые блоки выпускаются разной формы. Так, можно выделить изделия:
- основные, прямоугольной формы;
- угловые, предназначенные для четкой геометрической выгонки углов здания;
- цокольные, для кладки укрепленного цоколя;
- перемычные, для обустройства перемычек внутри строящегося помещения.
Крупногабаритные стеновые блоки изготавливаются из тяжелых бетонных смесей, также при их производстве часто используется арматура для укрепления изделия и увеличения его долговечности. Производители сегодня используют следующие виды бетонных растворов для изготовления такой продукции:
- шлакобетон — достаточно прочный материал для кладки несущих стен, имеет хорошие теплоизоляционные качества;
- ячеистые виды бетонов — обычно газосиликат и пенобетон, используются для малоэтажного строительства, чаще всего — загородных коттеджей;
- газобетон — не очень подходящий материал для кладки стен в районах с повышенной влажностью, в остальном — удобен для проведения работ и имеет легкий вес;
- пенобетон — огнеупорность и экологичность материала являются его главными преимуществами и делают блоки из пенобетона широко востребованными при возведении малоэтажных домов;
- блоки из кирпичей — поставляются уже с заводов в готовом собранном виде и применяются для кладки несущих стен в зданиях различного назначения, в том числе многоэтажных;
- из дикого камня — изготавливаются в каменных карьерах и используются для кладки массивных несущих конструкций.
Кроме того, существуют разновидности многослойных стеновых блоков, состоящие из тяжелого бетонного слоя, утеплителя и наружного декоративного слоя.
Преимущества крупногабаритных блоков для кладки стен
Несмотря на более сложные технологии кладки и необходимость грузоподъемных механизмов, крупноблочное строительство имеет ряд несомненных преимуществ. К ним можно отнести следующие проявления:
- при строительстве многоэтажных сооружений, кладка из крупноразмерных блоков занимает гораздо меньше времени, чем кладка кирпичных стен с такими же несущими характеристиками;
- кроме экономии времени, возведение стен из таких стройматериалов существенно облегчает труд рабочих на стройке;
- при применении стеновых блоков значительно проще добиться строгих геометрических форм кладки, которые придают сооружению элегантный законченный вид;
- тепло- и звукоизоляционные свойства материалов отменяют необходимость в кладке отдельного утепляющего слоя, что значительно уменьшает стоимость строительства и сокращает его сроки;
- использование блоков, имеющих декоративный внешний слой, так же отменяют дополнительную специальную облицовку стен;
- блочное здание или сооружение имеет меньшую массу, чем аналогичное кирпичное строение, таким образом, нагрузка на фундамент и несущие конструкции снижается, что обеспечивает увеличение срока эксплуатации здания на несколько десятилетий.
Газосиликатный кирпич: состав и характеристики
Огромную популярность в качестве основного строительного материала набирает газосиликатный кирпич. Его технические характеристики и свойства позволяют строить эффективные здания, которые соответствуют всем современным меркам. Если говорить о соотношении цены и качества, то с уверенностью можно сказать, что газосиликатные блоки занимают одно из первых мест.
Материал уже проверен временем и успешно выполняет свои функции. Его применяют для строительства всех видов конструктивных элементов сооружений и построек любого назначения. Почему газосиликатные блоки стали такими популярными? Чем они отличаются от классических строительных материалов? В чем их особенность? Ответы на эти и многие другие вопросы вы найдете в статье.
Газосиликатные блоки – что это
Если говорить простым языком, то газосиликатный материал – это одна из разновидностей ячеистого бетона. Готовый материал получался пористым, но имел такие же характеристики, как у бетона. Отличием являлось то, что благодаря пористой структуре, блоки имели меньший вес. Материал получали путем добавления в бетонный раствор специальных добавок, образующих поры. В XIX веке раствор перемешивали с кровью быка или свиньи, чтобы получить данный эффект. Белок в крови, вступая в реакцию с другими компонентами, образовывал пену. Один из советских строителей, Брюшков М.Н., в 1930-х годах заметил, что растение мыльный корень, которое растет в Средней Азии, наделяет цемент новой особенностью. Когда растение добавляли в смесь, она начинала пениться, тем самым увеличиваясь в объеме. Когда раствор застывал, пористая структура сохранялась. Однако самую важную роль в изготовлении ячеистого бетона сыграл Альберт Эриксон, архитектор из Швеции, который разработал технологию получения материала, путем добавления химических газообразующих компонентов. Он и запатентовал свое изобретение. Но, из чего делают газосиликатные кирпичи сегодня?
Исходя из СН 277-80, газобетонный раствор должен состоять из следующих компонентов:
- портландцемент высокого качества, поученный согласно ГОСТ 10178-76, в составе которого есть силикат кальция, не меньше 50%, трехкальциевый алюминат, не больше 6%.
Добавлять трепел в состав нельзя;
- песок, с техническими требованиями согласно ГОСТ 8736-77, в котором глинистые и илистые включения не превышают 2%, а наличие кварца равно 85%;
- простая вода, соответствующая требованиям ГОСТ 23732-79;
- кальциевая известь-кипелка, соответствующая ГОСТ 9179-77, не меньше 3 сорта. Ее скорость гашения должна составлять 5–15 мин. и не больше 2% пережога. Оксид магния и оксид кальция в составе – не меньше 70%;
- алюминиевая пудра ПАП–1 или ПАП–2, используемая в качестве образователя газа;
- сульфанол С, поверхностно-активное вещество (ПАВ).
Как выглядит газосиликатный кирпич, вы можете посмотреть на фото ниже.
Именно из этих компонентов и производят газосиликатный кирпич. Примечательно, что готовые изделия из газосиликатной смеси можно разделить на 2 вида:
- Автоклавный.
- Неавтоклавный.
Они отличаются способом изготовления. Газосиликатные кирпичи из автоклава, благодаря особой обработке в нем, имеют повышенные показатели по усадке при высыхании (в 5 раз лучше) и прочности. Изготовление в автоклаве довольно технологичное и энергоемкое, поэтому их цена несколько выше. Сушка газосиликатного кирпича происходит при температуре 175 ˚C, под давлением в 0,8–1,2 МПа. Такую обработку могут позволить себе только большие предприятия.
Что касается неавтоклавного газосиликатного кирпича, то его изготовление обходится значительно дешевле, но немного с худшими показателями. Изготовленная смесь затвердевает в природных условиях, без внешнего влияния.
Размеры и вес газосиликатных кирпичей
Одним из преимуществ газосиликатных блоков, является их размер. Он значительно больше, чем у обычных кирпичей, благодаря чему возведение здания проходит на порядок выше (в 4 раза), при том, что количество швов и соединений максимально снижено. Это значительно сокращает трудозатраты. Да и расход раствора значительно уменьшается. Как известно, размер кирпичей определяется тремя величинами: длиной, шириной и толщиной. Стандартный размер стенового газосиликатного кирпича равен 600×200×300 мм. Существует также стеновой полублок, размер которого составляет 600×100×300 мм. Но, это далеко не все размеры. В зависимости от производителя, изготавливают блоки следующих размеров:
- 500×200×300 мм;
- 588×150×288 мм;
- 600×250×50 мм;
- 600×250×75 мм;
- 600×250×100 мм;
- 600×250×250 мм;
- 600×250×400 мм и т.д.
Вы можете найти любой размер, который потребуется для ваших работ. Имея эти данные, мы можем сравнить, сколько кирпичей в газосиликатном блоке. К примеру, возьмем стандартный кирпич размером 250×120×65 мм и стандартный газосиликатный блок, 600×200×300 мм. Объем такого кирпича составляет 0,00195 м3. Объем же силикатного блока равен 0,036 м3. Если разделить их, получается, что в 1 блоке 1,85 кирпичей. Примечательно то, что на 1 м3 кладки требуется 27,7 блоков, а кирпичей – 512 шт., что в 18 раз меньше. А что сказать о весе?
Понятно, что на вес будут влиять габариты и плотность материала. Чем они больше, тем выше вес. Стандартный газосиликатный блок имеет вес 21–29 кг, а зависимости от плотности. Вес – одно из преимуществ таких изделий. Если сравнивать с теми же кирпичами, то масса 1 м3 кирпичей равна: 512 шт. × 4 кг. (масса 1 кирпича) = 2048 кг. А в 1 м3 газосиликатного блока: 27,7 × 21 = 581,7 кг. Разница более чем очевидна. За счет габаритов и пористой структуры, общий вес блоков из газосиликата намного меньше.
Основные физико-механические характеристики газосиликатных кирпичей
Немаловажными факторами, которые отличают изделия, являются следующие показатели:
- Плотность.
- Теплопроводность.
- Морозостойкость.
Как упоминалось выше, от плотности напрямую зависит вес и свойства материала. В зависимости от этого, газосиликатные кирпичи делятся на маркировки:
- D700, самые плотные, используются для постройки конструкций с повышенной этажностью.
- D600–D500, средней плотности, используются для постройки малоэтажных домов и перегородок.
- D400 и ниже, теплоизоляционный материал, который используют для утепления контура несущей стены.
Обратите внимание! Чем выше плотность изделия, тем выше проводимость тепла.
Отличием газосиликатных блоков является и их теплопроводность. К примеру, готовые блоки марки D700 обладают показателем 0,18–0,20 Вт/м·°С (ниже чем у красного кирпича). Если говорить о марке D600–D500, то показатели еще ниже – 0,12–0,18 Вт/м·°С. Самая низкая теплопроводность у изделий марки D400, равная 0,08–0,10 Вт/м·°С.
Внимание! Теплопроводность дерева составляет 0,11–0,19 Вт/м·°С. Поэтому ячеистый бетон в этом плане превышает даже дерево. Это материал, который способен дышать. Учтите, что это касается полностью сухого материала. Если он мокрый, проводимость увеличивается.
Что касается морозостойкости, то она зависит от объема пор блоков. Стандартные блоки, изготовленные в естественных условиях, могут выдерживать 15–35 циклов замерзания и размораживания.
Но, некоторые производители, изготовляющие блоки в автоклаве заявляют, что их изделия имеют морозостойкость 50–100 циклов, что действительно поражает. Все же, отталкиваясь от информации в ГОСТ 25485-89, в среднем морозостойкость ячеистого бетона не выше 35 циклов.
Другие преимущества материала
Стоит отметить, что газосиликатный кирпич имеет и другие характеристики. Благодаря своему составу, он является экологически чистым материалом, который не вредит здоровью человека. Изделия из газобетона находятся на втором месте по экологичности, после дерева. Кроме того, автоклавные блоки не будут гнить из-за отсутствия среды обитания для микроорганизмов. Грызуны не будут его есть и заводиться внутри.
Высокая пожаробезопасность – еще одно преимущество ячеистых бетонов. Он не горит! Материал можно использовать для возведения преград для огня. В конструкции предел распространения огня составляет 0 см. А пористая структура газосиликата позволяет эффективно препятствовать проникновению шума. Если вам придется работать с этим материалом, вы сможете оценить еще одну тонкость – простота обработки. С ним легко работать, используя простые плотницкие инструменты. Как видите, газосиликатный кирпич не зря считается одним из лучших материалов, используемых для строительства!
Стеновые блоки в Перми
Ремонт, а особенно строительство являются одной из важнейших частей в жизни каждого из нас, ведь человеку присуще желание комфорта. Но как только начинается стройка, всегда стает ребром вопрос о сумме, которая непосредственно уйдет на ремонт. Желание немного сэкономить, неотъемлемо у каждого, особенно, если дело коснется столь ресурсоемкого дела, как переделка жилища. Но сегодня строительство всегда идет навстречу тем, экономным людям, производители выпускают множество материалов, применение которых станет гораздо результативнее, а вместе с тем и дешевле. Один из таких ярких примеров — стеновые блоки.Блоки стеновые являются строительным материалом, который используют для кладки стен с минимальным швом. Стеновые блоки с разной толщиной успешно использують для того, чтобы заполнить каркас в процессе монолитной железобетонной стройки.
Стеновые блоки в Перми, в основном, делают из легкого ячеистого бетона. Различают также две категории блоков — пенобетонные и газосиликатные.
Пенобетон является легким ячеистым бетоном, который получается как следствие естественного твердения раствора, цемента, песка, воды и специальной пены. По технологии производства, которую применяют для пенобетона, готовые изделия получаются в виде блоков (заливается пенобетон по блок-формам, а затем затвердевает естественным способом без дальнейшего вмешательства).

Газосиликат является ячеистым бетоном, который в свою очередь состоит из кварцевого песка, извести, цемента и воды. Такая смесь затем дополняется алюминиевой пудрой, которая станет газообразователем. Компоненты сначала смешиваются, а затем поступают в специальный автоклав, затем, при определенных условиях, они вспениваются и впоследствии затвердевают. Газосиликатные изделия производят только в рамках заводских условий, а затем поступают в руки заказчика как готовые и адаптированные к строительству блоки.
По большему счету, основные составляющие как пенобетона, так и газосиликата почти одинаковые. Их разница лишь в том, какой используется вспениватель, а также способ, который применяется для отвердевания.
Стеновые блоки, помимо всего вышесказанного, делают из керамзитобетона. В таких стеновых блоках родительским материалом станет керамзит, как главный вид заполнителя, а также вода и цемент. Спекшаяся оболочка, которая покрывает гранулу керамзита, придает ей колоссальную прочность!
Керамзитобетонные блоки характеризуются отличными теплоизоляционными свойствами. Стеновые блоки, как из керамзитобетона, так и из газосиликата, выделяются среди всех также и малым весом. Блоки также являются негорючими, даже не разрушающимися под всевозможными воздействиями высоких температур и кислот!
Стеновые блоки можно использовать в процессе строительства всевозможных сооружений. Стеновые блоки в Перми чаще всего используются при строительстве жилых домов. Использование стеновых блоков даст возможность снизить стоимость работ за счет того, что они будут выполнены в более короткие сроки, помимо этого процесс возведения стен потребует меньшего расхода бетона. При этом затраты труда очень покажутся вам очень малыми, в сравнении с работами с кирпичом.
Стеновые блоки позволяют создать эксклюзивный, индивидуальный, попросту неповторимый вид для любого здания. Это осуществляется благодаря широчайшему выбору цветовой гаммы, а также ассортименту всевозможных материалов для внешнего декора.
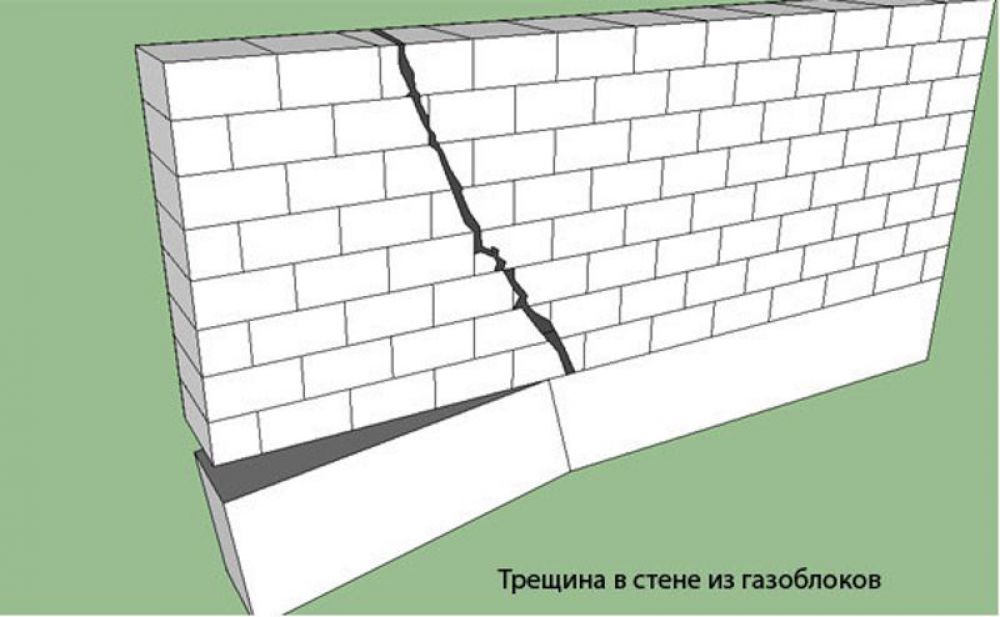
Стеновые блоки помимо всего прочего целым рядом свойств:
- Стеновые блоки являются прочным, долговечным материалом, который помимо всего обладает улучшенными показателями морозоустойчивости, огнеупорности и кислотостойкости.
- Также стеновые блоки способствуют увеличению полезной площади вашего помещения не только за счет общей толщины блоков без снижения характерного качества теплообмена, но и прочности более тонких конструкций. Именно поэтому в процессе той или иной стройки стеновые блоки в Перми с уверенностью вытесняют всевозможные другие материалы. Построенный из стеновых блоков дом, будет не только комфортным, теплым и качественным, но также позволит сэкономить в процессе его возведения.
- Более того стоимость самих блоков довольно таки выгодно отличается от прочих строительных материалов.
- Все свойства стеновых блоков способствуют созданию ощущения комфорта за счет обладания термостойкими эффектами, поэтому в помещении, которое построили из стеновых блоков, жильцам будет прохладно летом, зимой же будет тепло. Из этого выплывают меньшие затраты, которые уйдут на отопление вашего дома.
- Плюс ко всему прочему — сокращение общих затрат на доставку ваших стеновых блоков. Ведь благодаря их низкому весу (стеновые блоки, как известно. являются гораздо легче кирпич или прочий материал) объемы доставляемого материала станут больше.
Выделим все преимущества, которые так или иначе присущи стеновым блокам:
- Гарантия тепла и комфорта, превосходная морозоустойчивость и огнеупорность.
- Увеличение полезной площади.
- Стеновые блоки совсем не снижают качество свойств теплообмена в вашем помещении.
- Малые затраты труда на установку и доставку.
- Относительная дешевизна в сравнении с остальными строительными материалами.
Из всего вышесказанного стоит сделать простой вывод — строительство зданий с применением стеновых блоков в Перми позволит вам колоссально сэкономить ваши финансовые средства, получив при этом теплый, комфортный и уютный дом.

Стены из газосиликатных блоков — наружные, несущие, устройство, возведение, армирование
Газосиликатные блоки – это универсальный строительный материал. Их производят из молотого кварцевого песка, воды, известково-цементной смеси, содержащей негашеную известь, и алюминиевого порошка, выступающего в качестве газообразующей добавки. Готовые блоки имеют равномерную пористую структуру, их плотность зависит от соотношения составных компонентов.
Сфера их применения зависит от плотности. Газосиликатные блоки наименьшей плотности (350 кг/м3) используются для теплоизоляции. Для возведения наружных стен одноэтажных зданий – жилых помещений или хозяйственных построек, внутренних перегородок – достаточная плотность 400 кг/м3.
Несущие стены домов высотой до трех этажей возводят из блоков плотностью 500 кг/м3. Наибольшей прочностью обладает материал с удельным весом 700 кг/м3. Этого достаточно для строительства многоэтажных жилых и производственных помещений.
Основные преимущества этого строительного материала:
- небольшой вес;
- высокая степень прочности;
- тепло- и шумоизолирующие свойства, паропроницаемость и морозостойкость;
- крупный размер, точность форм и простота обработки существенно ускоряет процесс постройки, позволяет минимизировать толщину швов и снижает стоимость работ.
Возведение и устройство стен из газосиликатных блоков
Первое правило при устройстве стен из газосиликатных блоков упоминается во всех источниках: работы по укладке не проводятся в сырую дождливую погоду. Этот строительный материал очень гигроскопичен, и впитавшаяся влага при перепаде температур может привести к деформации кладки.
Укладка производится на монолитный ленточный фундамент на песчаной подушке глубиной 1,8 м или столбчатый фундамент с обвязкой монолитным железобетонным поясом. На фундамент укладывают слой гидроизоляции из рубероида, битумного полиматериала или раствора на основе сухих смесей. Это необходимо, для защиты нижнего ряда от поступающей в цоколь влаги.
Начинают кладку с выставления угловых (маячных) элементов, выравнивая их по горизонтали и вертикали. Еще раз замеряются диагонали будущей постройки, они должны быть одинаковыми. Между угловыми элементами натягивается шнур-уровень, по которому будут укладываться рядовые газоблоки. Если стена длинная, то можно в центре положить еще один блок, чтобы шнур не провисал.
Для кладки используется цементно-песчаный раствор (в соотношении 3:1) или сухие клеевые смеси. Перед укладкой грани блоков смачивают водой, во избежание быстрого высыхания нанесенного раствора. Клеевой раствор равномерно наносится на горизонтальную и вертикальную поверхность зубчатой кельмой или шпателем слоем 1-3 мм. Нужно следить, чтобы клеевой смесью была покрыта вся горизонтальная поверхность без зазоров. Первый ряд является своеобразным фундаментом будущей стены, и к его качеству следует отнестись с особой тщательностью. Его укладывают на цементно-песчаный раствор. Между угловыми газоблоками укладываются горизонтальные. Укоротить блок можно с помощью обычной или электрической пилы.
Перед укладкой последующих рядов еще раз проверяется горизонтальный и вертикальный уровень с помощью шнура, отвеса, уголка. Блоки второго и последующих рядов начинают укладывать от угла со смещением относительно нижнего элемента. Минимальная ширина смещения – 8 см (0,4 от высоты блока).
Наружные стены из газосиликатных блоков
В соответствии со строительными нормами минимальная толщина однородной наружной стены из газосиликатных блоков должна быть не менее 37,5 см при условии кладки с применением клеевых смесей и толщиной шва не более 5 мм. Для утепления применяется облицовка кирпичом или сайдингом. Если планируется оштукатуривание фасада, отделка плиткой или искусственным камнем, то ширина кладки из газобетона увеличивается до 50 см.
Несущие стены из газосиликатных блоков
Возведение несущих стен из газосиликатных блоков также начинается с угловых элементов. Внутренняя стена соединяется с внешней с помощью перевязочной кладки. Блоки для их устройства используются той же марки, что и для наружных, так как они должны будут выдерживать нагрузку от перекрытия.
Для внутренних перегородок, не выполняющих несущую функцию, подойдут блоки толщиной от 100 до 200 мм. Они соединяются с внешней стеной с помощью гибких связей или анкеров.
Армирование стен из газосиликатных блоков
Постройка из газосиликата постоянно подвергается деформирующим нагрузкам, которые возникают при осаждении почвы, перепадах температуры, неравномерности усадки. Это может привести к возникновению мелких трещин, ухудшающих внешний вид. Армирование стен из газосиликатных блоков воспринимает напряжение, возникающее при деформации, и предохраняет стены от растрескивания. Армирование не влияет на несущую способность кладки.
При возведении стен из газосиликатных блоков целесообразно проводить армирование каждые 3 ряда металлической сеткой малого сечения, а также зоны под оконными проемами, опоры перемычек и конструктивные элементы, подвергающиеся повышенной нагрузке.
При высоте этажей здания до 3 метров осуществляется связь между поперечными и продольными стенами:
- во внешних углах газобетон перевязывается сваренными из арматуры Г-образными элементами длиной не менее 30 см;
- в местах примыкания внутренних перегородок – арматурной сеткой толщиной 3-4 мм или Т-образными анкерами из полосовой стали толщиной 3-4 мм;
- в оконных и дверных проемах (сверху и снизу) газосиликат армируется с помощью 8-10 мм арматуры. По 2 прута длиной 50 см в каждую сторону.
Перед укладкой плит перекрытия на наружных стенах из газосиликатных блоков делается специальный армопояс, равномерно распределяющий нагрузку. Для этого можно положить два ряда керамического полнотелого кирпича или уложить специальные U-образные блоки, армировать их и залить бетонным раствором.
Многие из выполненных нами объектов построены именно из газосиликата, мы достаточно часто строим дома из газобетона. Наша компания «Проект» оказывает строительные услуги в Москве и Подмосковье. Опытные специалисты выполнят работы на самом высоком профессиональном уровне.
Бригада рабочих | Кладка газосиликатных блоков своими руками, плюсы и минусы
Свойства газосиликата.
Из газосиликатных блоков (ячеистого бетона) широко и повсеместно возводят малоэтажные здания, жилые и подсобные помещения, складские и промышленные сооружения. Газосиликат создан искусственно из смеси песка, цемента, извести и воды с добавлением алюминиевой пудры в качестве реагента для газообразования. Доля цемента в составе небольшая, основную вяжущую функцию выполняет известь.
Все компоненты газосиликатных блоков натуральные и не вредят здоровью людей. Процесс затвердения блоки проходят в специальной автоклаве при высокой температуре под давлением. Строго выдерживаются линейные размеры, расхождения в размерах блоков одной партии не больше 1 мм, поэтому для укладки газосиликатных блоков достаточно тонкого слоя раствора до 3 мм, что дает существенную экономию. Производят блоки различной плотности, которая определяет прочность материала.
Для утепления стен используют блоки D100-D200, внутренние перегородки возводят из блоков марки D300-D500, а несущие стены – из конструкционного газосиликата D1000-D1400. Продукция из газосиликата разнообразна, это не только блоки для выгонки стен, но также дугообразные и арочные, перемычки и перегородки, панели перекрытий.
Также привлекательность блоков из газосиликата заключается в его легкости, влагонепроницаемости, отменной звукоизоляции и огнеупорности, низкой теплопроводимости. Наружные стены из газосиликатных блоков не требуют отделки. К внутренним стенам из газосиликата можно применить любой из видов отделки.
Как возводить стены из газосиликатных блоков своими руками.
Инструменты для укладки блоков: мастерок с зубцами 4-5 мм для нанесения раствора или клеевой смеси, дрель-миксер насадкой, строительный уровень, резиновый молоток и пила «болгарка».
Блоки укладывают на готовый фундамент. Между фундаментом и первым рядом блоков по всему периметру будущих стен, следует проложить два слоя армированного рубероида в качестве гидроизолятора, затем слой раствора из цемента и песка (это обязательное условие). Со второго ряда можно использовать клеевую смесь. Чтобы вода, стекая по стенам, не попадала на швы между фундаментом и стеной, блоки укладывают так, чтобы стена выступала относительно цоколя и фундамента как минимум на 5 см.
Работа по укладке блоков начинается с разметки. Чтобы стены получились ровными, выбираем основные четыре угла дома и измеряем диагонали и натягиваем нити по углам.
Раствор замешивают густо, чтобы не плыл, на жидком растворе блоки проседают и их трудно выровнять. Раствор накладывают по краям блока в виде двух дорожек высотой примерно 5 см, плотно прижимают к месту укладки и выравнивают резиновым молоточком. Возведение стен начинают с углов, с укладки 4 опорных блоков, которые тщательно выравнивают по уровню в горизонтальной и вертикальной плоскости (строительный уровень для блоков не длиннее 80 см). Стену выравнивают по натянутой нити, а горизонтальность уровнем по диагоналям блока. После того, как блок выровняли по горизонтали, нанести 2-3 удара в торец, чтобы плотно прижать его к предыдущему блоку.
На стыке несущих стен и при укладке блоков со второго ряда выполняют «перевязку» (смещение блоков на 15-20 см).
Оконные и дверные проемы.
Оконный проем начинается на высоте 1 метра от основания пола, после стяжки и утеплителя высота уменьшиться до 80-85 см. Высота от верхнего края оконного проема до потолка примерно равна 35 см, это не обязательная, а больше эстетическая норма. Над оконными проемами укладывают железобетонные перемычки заводского производства.
На последний ряд блоков заливают железобетон, размер монолитного пояса 20х15 см. Можно в качестве теплоизолятора использовать сам газосиликатный блок, он же исполнит роль несъёмной опалубки. Такой пояс делают по всему периметру несущий стен под кровлю. Для внутренних стен монолитный пояс не делают.
Перегородки внутри дома выполняют из блоков 100-200 мм толщиною. Их перевязывают с несущими стенами, используя куски арматуры по 20-25 см, которые забивают в несущую стену до половины, а вторая половина заходит в стыковочный блок перегородки. Перегородки с потолочными перекрытиями соединяются строительной пеной. Излишки засохшей пены срезают ножом по уровню стены.
Есть ли достойная альтернатива газосиликату?
Как вариант — пеноблоки. Это на сегодня один из востребованных материалов при возведении стен из строительных блоков загородных домов. Их кладка должна обязательно осуществляться профессионалами. Только проффессиональные бриагады возводят стены и перегородки из пеноблоков, гарантируя при этом хорошую теплопроводность и влагостойкость материала. Цены на кладку пеноблоков примерно такие же как и на газосиликатные блоки
Газосиликатные блоки
ПОЧЕМУ ЦЕНА НА ГАЗОСИЛИКАТНЫЕ БЛОКИ ОСТАЕТСЯ НИЗКОЙ?Согласно расчетам, цена строительства дома из газосиликатных блоков в два раза ниже, чем из кирпича. Однако нужно учитывать некоторые свойства газосиликата. Дело в том, что плотность газосиликатных блоков должна быть высокой, чтобы получить необходимую прочность конструкции. Купить специальные блоки из газосиликата придется по цене выше, чем обычные. Еще нужно помнить, что нужно покупать больше газосиликатных блоков, чем будет использовано при возведении. Все дело в их характеристиках. К сожалению, этот материал хрупкий, поэтому его часть разрушается в процессе транспортировки и отгрузки. Но даже с учетом этих особенностей цена строительства дома из газосиликатных блоков будет ниже, чем при использовании кирпича в этих целях.
Люди, которые купили газосиликатные блоки и уже возвели из них дома, говорят, что для стен придется купить хорошую наружную обшивку, ввиду особенностей этого материала. Без обшивки просто не обойтись, так как влага может привести к потере внешнего вида готовой стены из газосиликата, к появлению неприятного запаха и постепенному разрушению. При выборе обшивки руководствуйтесь следующими требованиями:
- газосиликатные блоки подвержены воздействию воды, поэтому обшивка должна быть водонепроницаемой;
- обшивка должна «дышать»;
- между и обшивкой нужно оставить специальный зазор для вентиляции; газосиликатными блоками
- в процессе осадки дома обшивка не должна подвергаться деформации.
Вы можете купить штукатурку или пенопласт, но они не позволят вам добиться необходимых технических характеристик обшивки. Да, их цена значительно ниже, чем у аналогов, но вскоре вам придется делать ремонт фасада, что является весьма дорогостоящим процессом.
ПРЕИМУЩЕСТВА И НЕДОСТАТКИКаждый материал имеет свои особенности, что обуславливает специфику применения. Газосиликатные блоки – не исключение. Мы выделяем следующие преимущества этого материала.
- Цена на газосиликатные блоки ниже, чем на аналогичные строительные материалы.
- Вес газосиликата в пять раз меньше массы бетона. Поэтому трудоемкость работ и цена транспортировки снижаются.
- Прочность на сжатие позволяет возводить из газосиликатных блоков даже большие конструкции.
- Показатели теплоизоляции в три раза лучше, чем у кирпича.
- Блоки из газосиликата длительное время сохраняют тепло.
- Показатели звукоизоляции на порядок выше, чем у кирпича.
- Огнестойкость.
- Безопасность использования для здоровья человека. В процессе изготовления этого стройматериала используются только экологически чистые компоненты.
- «Дышащий» материал создает комфортную атмосферу внутри помещений.
- Геометрическая точность материала ускоряет монтаж.
Однако даже современные стройматериалы имеют недостатки. В отношении газосиликатных блоков выделяют следующие.
- Низкая прочность.
- Подверженность воздействию влаги и холода.
- Может дать осадку выше критических значений и дать трещину.
Несмотря на недостатки, плюсы покупки газосиликатных блоков делают этот материал популярным. Применение газосиликатных блоков – это подлинная экономия, безопасность, экологическая чистота и удобство возведения конструкций. Поэтому выбор газосиликатных блоков в качестве строительного материала оптимален для заказчика.
Прочность газосиликатных блоков. Что такое газосиликатные блоки, их характеристики, плюсы и минусы. Эксплуатационные параметры газосиликатных блоков
Практичность
Прочность
Устойчивое развитие
Стоимость
итоговая оценка
Эксплуатационные параметры газосиликатных блоков
Срок службы — номинал до 100 лет в нормальном климате и до 50 лет во влажном климате.При правильном уходе, наличии штукатурки и водостоков стандартные сроки вполне соответствуют настоящим.
Расход материалов — зависит от климатических условий. Рекомендуемая толщина стенок составляет от 400 мм в умеренном климате до 800 мм в северных регионах.
Класс прочности на сжатие — характеризует гарантированное давление, которое не приведет к разрушению. Блоки плотностью 600 кг / м3 имеют класс прочности от В1.5 до В3,5 (в 2-3 раза меньше, чем у кирпича). У теплоизоляционных конструкций с плотностью материала 300 кг / м3 класс прочности намного ниже — В0,75-В1,5.
Отметим, что снижение класса прочности газосиликатных блоков не означает реального снижения прочности конструкции. Для пористого материала масса всей кладки (как следствие оказываемое давление) в 2,5-3 раза ниже, чем у кирпичной конструкции.
Морозостойкость — численно показывает количество циклов оттаивания, которое может выдержать конкретный тип материала, не теряя более 15% своей прочности.В данном случае обозначение, которое выглядит как F50, означает, что гарантированное количество циклов равно 50.
Технические испытания проводятся в суровых условиях, значительно превышающих изменения окружающей среды. Блок погружают в воду до полного насыщения, а затем помещают в морозильную камеру. На самом деле таких суровых условий не бывает, поэтому основная функция параметра — сориентировать покупателя в более приемлемом варианте для конкретной климатической зоны.
Коэффициент теплопроводности — зависит от плотности и влажности материала.Так, самый легкий газосиликатный блок (300 кг / м3) имеет теплопроводность около 0,08 Вт / (м²С), а самый тяжелый (600 кг / м3) — почти в 2 раза больше. Увеличение влажности материала на 1% увеличивает теплопроводность на 4-5%.
В таблице приведены отличия блоков разных марок по теплопроводности, усадке, морозостойкости и паропроницаемости:
Газосиликатные блоки — хороший выбор для небольших домов, особенно в холодном климате.Для дачи или стен в квартире пористый материал также станет удобным и недорогим выходом из положения. При покупке следует внимательно проверять содержимое поддонов — недобросовестные продавцы могут продавать блоки с высоким процентом брака.
Газосиликатные блоки — это разновидность легкого ячеистого материала, имеющего достаточно широкую область применения в строительстве. Популярность изделий из ячеистого бетона данного типа обусловлена высокими техническими качествами и многочисленными положительными характеристиками.В чем преимущества и недостатки газосиликатных блоков, и каковы особенности их использования при строительстве домов?
Газосиликат считается улучшенным аналогом газобетона. В производственную технологию его изготовления входят следующие компоненты: высококачественный портландцемент
- , содержащий более 50 процентов неорганического соединения силиката кальция;
- вода;
- алюминиевый порошок в качестве вспенивателя;
- Известь гашеная, обогащенная на 70 процентов оксидами магния и кальция;
- песок кварцевый мелкий.
Смесь этих компонентов дает высококачественный пористый материал с хорошими техническими характеристиками:
- Оптимальная теплопроводность. Этот показатель зависит от качества материала и его плотности. Марка газосиликатных блоков Д700 соответствует теплопроводности 0,18 Вт / м ° С. Этот показатель немного выше многих значений для других строительных материалов, в том числе и железобетона.
- Морозостойкость. Газосиликатные блоки плотностью 600 кг / м³ способны выдержать более 50 циклов замораживания-оттаивания.У некоторых новых марок заявлен индекс морозостойкости до 100 циклов.
- Плотность материала. Эта величина варьируется в зависимости от типа газосиликата — от D400 до D700.
- Способность поглощать звуки. Шумоизоляционные свойства сотовых блоков равны коэффициенту 0,2 на звуковой частоте 1000 Гц.
Многие технические параметры газосиликата в несколько раз превышают характерные показатели кирпича. Для обеспечения оптимальной теплопроводности стены выкладываются толщиной 50 сантиметров.Для создания таких условий из кирпича требуется размер кладки 2 метра.
Качество и свойства газосиликата зависят от соотношения компонентов, используемых для его приготовления. Повысить прочность изделий можно за счет увеличения дозы цементной смеси, но при этом снизится пористость материала, что скажется на других его технических характеристиках.
Виды
Газосиликатные блоки делятся, в зависимости от степени прочности, на три основных типа:
- Конструкционные.Из такого материала возводятся постройки не выше трех этажей. Плотность блока — D700.
- Конструкционная и теплоизоляция. Газосиликат этого типа применяется для кладки несущих стен в зданиях не выше двух этажей, а также для возведения межкомнатных перегородок … Его плотность колеблется от D500 до D700.
- Теплоизоляция. Материал успешно применяется для снижения степени теплоотдачи стен. Его прочность невысока, а из-за высокой пористости плотность достигает всего D400.
Газосиликатные строительные блоки производятся двумя способами:
- Автоклав. Технология изготовления заключается в обработке материала под высоким давлением пара 9 бар и температурой 175 градусов. Такая пропарка блоков осуществляется в специальных промышленных автоклавах.
- Неавтоклавный. Приготовленная газосиликатная смесь естественным образом застывает более двух недель. При этом поддерживается необходимая температура воздуха.
Газосиликат, полученный автоклавированием, имеет самые высокие технические характеристики.Такие блоки обладают хорошими прочностными и усадочными характеристиками.
Размер и вес
Размер газосиликатного блока зависит от типа материала и его производителя. Наиболее распространены следующие размеры, выражаемые в миллиметрах:
- 600x100x300;
- 600x200x300;
- 500x200x300;
- 250x400x600;
- 250x250x600.
Газосиликат из-за своей ячеистой структуры является довольно легким материалом.Вес пористых изделий различается в зависимости от плотности материала и его типоразмеров:
- D400 — от 10 до 21 кг;
- D500-D600 — от 9 до 30 кг;
- D700 — от 10 до 40 кг.
Небольшая масса блоков и возможность выбора необходимого размера значительно облегчают процесс строительства.
Сфера применения газосиликатных блоков
В строительстве газосиликат успешно применяется для следующих целей:
- строительство зданий;
- теплоизоляция различных зданий;
- изоляция теплотехнических и строительных конструкций.
Количество ячеек на кубический метр в добываемых газосиликатных блоках разное. Следовательно, область применения материала напрямую зависит от плотности материала:
- 700 кг / м³. Наиболее эффективно такие блоки используются при строительстве многоэтажных домов. Строительство многоэтажек из газосиликата обходится намного дешевле, чем из железобетона или кирпича.
- 500 кг / м³. Материал используется для строительства малоэтажных домов — до трех этажей.
- 400 кг / м³. Этот газосиликат подходит для кладки одноэтажных домов. Чаще всего его используют для недорогих хозяйственных построек. Кроме того, материал успешно применяется для утепления стен.
- 300 кг / м³. Ячеистые блоки с низким показателем плотности предназначены для утепления несущих конструкций. Материал не способен выдерживать высокие механические нагрузки, поэтому не подходит для возведения стен.
Чем меньше плотность ячеистых блоков, тем выше их теплоизоляционные качества.В связи с этим конструкции из газосиликата с плотной структурой часто требуют дополнительного утепления. В качестве изоляционного материала используются плиты пенополистирола.
Достоинства и недостатки
Строительство домов из газосиликатных блоков вполне оправдано невысокой стоимостью материала и его многочисленными преимуществами:
- Блоки для строительства домов отличаются высокой прочностью. Для материала со средней плотностью 500 кг / м³ степень механического сжатия составляет 40 кг / см3.
- Небольшой вес газосиликатных изделий позволяет избежать дополнительных затрат на доставку и установку блоков. Ячеистый материал в пять раз легче обычного бетона.
- За счет хорошей теплоотдачи снижается расход тепла. Это свойство позволяет существенно сэкономить на отоплении здания.
- Высокая звукоизоляция. Благодаря наличию пор ячеистый материал защищает от проникновения шума в здание в десять раз лучше, чем кирпич.
- Хорошие экологические свойства. Блоки не содержат токсичных веществ и полностью безопасны в использовании. По многим экологическим показателям газосиликат приравнивается к древесине.
- Высокая паропроницаемость изделий позволяет создавать в помещении хорошие условия микроклимата.
- Негорючий материал предотвращает распространение огня в случае пожара.
- Точные пропорции размеров блоков позволяют выполнять кладку стен ровно.
- Доступная цена материала.При хороших технических показателях цена газосиликатных блоков относительно невысока.
Пористый материал наряду со многими достоинствами имеет ряд недостатков:
- Механическая прочность блоков несколько ниже, чем у железобетона и кирпича. Поэтому при вбивании гвоздей в стену или ввинчивании дюбелей поверхность легко осыпается. Блоки достаточно плохо удерживают тяжелые детали.
- Способность впитывать влагу. Газосиликат хорошо и быстро впитывает воду, которая проникает в поры, снижает прочность материала и приводит к его разрушению.При строительстве зданий из разных типов пористый бетон используется для защиты поверхностей от влаги. На стены рекомендуется наносить штукатурку в два слоя.
- Морозостойкость блоков зависит от плотности изделий. Марки газосиликатов ниже D 400 не выдерживают 50-летнего цикла.
- Материал склонен к усадке. Поэтому, особенно для блоков класса ниже D700, первые трещины могут появиться через пару лет после постройки здания.
При отделке стен из газосиликата в основном применяется гипсовая штукатурка. Он отлично скрывает все швы между блоками. Цементно-песчаные смеси не прилипают к пористой поверхности, а при понижении температуры воздуха образуются небольшие трещинки.
Популярность газосиликата растет с каждым годом. Ячеистые блоки обладают практически всеми качествами, необходимыми для эффективного строительства малоэтажных домов … Некоторые характеристики намного превосходят характеристики других материалов. С помощью легких газосиликатных блоков можно построить надежное здание с небольшими затратами в относительно короткие сроки.
Еще одним популярным материалом, занявшим значительную долю на рынке строительных материалов, является газосиликат. Готовые лепные блоки имеют много общего с искусственным камнем и обладают заметными преимуществами. По этой причине газосиликатные блоки приобрели такую широкую популярность при строительстве домов.
Где используются газосиликатные блоки?
Область применения газосиликата находится в следующих областях:
- теплоизоляция зданий,
- Строительство зданий и несущих стен,
- изоляция систем отопления.
Газосиликатные блоки по своим качествам имеют много общего с пенобетоном, но при этом превосходят их по механической прочности.
В зависимости от плотности материала. есть несколько областей применения:
- Плотность блоков от 300 до 400 кг / м3 сильно ограничивает их распространение, и такие блоки чаще используются в качестве утеплителя для стен. Их низкая плотность не позволяет использовать их в качестве основы для стен, так как они будут разрушаться при значительных механических нагрузках.Но в качестве утеплителя небольшая плотность играет роль, поскольку чем плотнее молекулы прилипают друг к другу, тем выше становится теплопроводность и тем легче холоду проникать в комнату. Следовательно, блоки с низкой теплопроводностью обеспечивают более эффективную теплоизоляцию, Блоки
- плотностью 400 кг / м3 нашли свое применение при строительстве одноэтажных зданий и рабочих помещений. За счет повышенной прочности блоков и их меньшего веса значительно снижаются затраты на устройство фундамента, Блоки
- плотностью 500 кг / м3 чаще используются при строительстве зданий высотой в несколько этажей.Как правило, высота здания не должна превышать трех этажей. Такие блоки в прямой зависимости от климата либо вообще не утепляются, либо требуют традиционных методов утепления.
- Самый лучший вариант для строительства многоэтажных домов — это использование блоков плотностью 700 кг / м3. Такой показатель позволяет возводить многоэтажные жилые и производственные дома. Благодаря более низкой стоимости возведенные стены из газосиликатных блоков заменяют традиционные кирпичные и железобетонные стены.
Чем выше плотность, тем хуже теплоизоляционные характеристики, поэтому в таких зданиях потребуется дополнительная изоляция. Чаще всего внешний обеспечивается с помощью плит пенопласта или пенополистирола. Этот материал имеет невысокую цену и при этом обеспечивает хорошую теплоизоляцию помещения в любое время года.
В последнее время значительно укрепились позиции газосиликата, как одного из самых востребованных материалов в строительстве.
Относительно небольшой вес готовых блоков существенно ускорит возведение здания. Например, газосиликатные блоки, размеры которых имеют типовые значения, по некоторым оценкам, снижают трудоемкость при установке до 10 раз по сравнению с кирпичными.
Стандартный блок плотностью 500 кг / м3 и весом 20 кг заменяет 30 кирпичей, общий вес которых составляет 120 кг. Таким образом, установка блоков на малоэтажные дома не требует специального оборудования, это снизит трудозатраты и время, затрачиваемое на возведение здания.По некоторым оценкам, экономия времени достигает 4-кратного снижения затрат.
Характеристики материала
Имеет смысл перечислить основные технические характеристики газосиликатных блоков:
- Удельная теплоемкость блоков, изготовленных автоклавированием, составляет 1 кДж / кг * ° С. Например, по железобетону аналогичный показатель находится на уровне 0,84, .
- плотность железобетона в 5 раз выше, но при этом коэффициент теплопроводности газосиликата всего 0.14 Вт / м * ° С, что примерно аналогично древесине сосны или ели. У железобетона значительно более высокий коэффициент, 2,04,
- звукопоглощающие характеристики материала на уровне коэффициента 0,2, при частоте звука 1000 Гц,
- цикличность морозостойкости для газосиликатных блоков с плотностью материала ниже 400 кг / м3 не нормируется, для блоков плотностью до 600 кг / м3 до 35 циклов. Блоки плотностью более 600 кг / м3 способны выдерживать 50 циклов замораживания-оттаивания, что соответствует 50 климатическим годам.
Если сравнивать газосиликатные блоки с кирпичом, то показатели не в пользу последнего. Так, необходимая толщина стены для обеспечения достаточной теплопроводности блоков составляет до 500 мм, тогда как для кирпича потребуется аналогичная кладка толщиной 2000 мм. Расход раствора для кладки материала составит 0,12 м3 для кирпича и 0,008 м3 для газосиликатных блоков на 1 м2 кладки.
Вес одного квадратного метра стен составит до 250 кг для газосиликатного материала и до двух тонн кирпича.Для этого потребуется соответствующая толщина фундамента под несущие стены строящегося дома. Для кирпичной кладки потребуется толщина фундамента не менее 2 метров, тогда как для газосиликатных блоков достаточно толщины всего 500 мм. Трудоемкость укладки блоков значительно ниже, что снизит трудозатраты.
Помимо прочего, газосиликатные блоки значительно экологичнее. Коэффициент этого материала составляет два балла, что приближает его к натуральному дереву.При этом показатель экологичности кирпича находится на уровне от 8 до 10 единиц.
Преимущества и недостатки газосиликатных блоков
Газосиликатные блоки, цена на которые значительно удешевит стоимость строительства дома, обладают следующим рядом неоспоримых преимуществ:
- Легкость готовых блоков. Газосиликатный блок весит в 5 раз меньше аналогичного бетонного блока. Это значительно снизит затраты на доставку и установку.
- Высокая механическая прочность на сжатие. Газосиликат с индексом D500, что означает его плотность 500 кг / м3, показывает показатель до 40 кг / см3.
- Показатель термического сопротивления в 8 раз выше, чем у тяжелого бетона. Благодаря пористой структуре он обеспечивает хорошие показатели теплоизоляции.
- Газосиликатные блоки обладают теплоаккумулирующими свойствами. Они способны передавать скопившееся тепло в помещение, что снизит затраты на отопление.
- За счет пористой структуры степень звукоизоляции в 10 раз выше, чем у кирпича.
- Материал не содержит токсинов и имеет хорошие экологические характеристики.
- Газосиликат отличается негорючестью и не распространяет горение. ОН выдерживает прямое воздействие пламени не менее трех часов, что практически полностью исключает ситуацию с распространением огня.
- Паропроницаемость блоков намного выше, чем у конкурентов.Считается, что материал способен хорошо «дышать», создавая при этом комфортный микроклимат в помещении.
Однако газосиликатные блоки в настоящее время не способны нанести сокрушительный удар всем конкурентам. У этого материала тоже есть существенные недостатки:
- Газосиликат имеет низкую механическую прочность. Когда в него ввинчивается дюбель, он начинает крошиться и крошиться и при этом не может обеспечить эффективное удержание. Грубо говоря, еще можно повесить часы или картину на стену из газосиликатных блоков.Но полка уже может разрушиться, так как крепеж может просто выскользнуть из стены.
- Блоки не обладают хорошей морозостойкостью. Несмотря на заявленный производителем цикл в 50 лет для марок с повышенной прочностью, достоверных сведений о долговечности блоков Д300 нет.
- Главный недостаток газосиликата — высокое влагопоглощение. Он проникает в конструкцию, постепенно разрушая ее, и материал теряет прочность.
- Из указанного недостатка вытекает следующее: скопление и впитывание влаги приводит к появлению грибка.В этом случае пористая структура служит хорошим условием для ее распространения.
- Материал способен значительно давать усадку, в результате чего в блоках часто появляются трещины. Более того, через два года трещины могут появиться на 20% уложенных блоков.
- Не рекомендуется применять цементно-песчаные штукатурки. Они могут просто упасть со стены. Гипсовая штукатурка, рекомендованная многими продавцами, также не является эффективным средством … При нанесении на стену из газосиликатных блоков она не способна скрыть швы между блоками, а при наступлении холодов на ней появляются заметные трещины.
.Это связано с перепадами температур и изменением плотности материала.
- Из-за высокого влагопоглощения штукатурка требует как минимум двух слоев. К тому же из-за сильной усадки штукатурка потрескается. На герметичность они не повлияют, но эстетическую составляющую сильно нарушат. Гипсовая смесь хорошо сцепляется с газосиликатными блоками и, несмотря на появление трещин, не отрывается.
Как изготавливают газосиликатные блоки
Газосиликатные блоки целесообразнее покупать у тех дилеров, которые представляют продукцию известных производителей.Современное качественное оборудование на производственных линиях позволяет обеспечить должный контроль качества производимых газосиликатных блоков, благодаря чему покупатель уверен в долговечности закупаемой продукции.
Сам производственный процесс разделен на несколько этапов, каждый из которых, что типично, полностью автоматизирован. Это исключает вмешательство человеческого фактора, от которого часто зависит качество продукции. Особенно по пятницам и понедельникам. Те, кто работал на производстве, поймут.
Известь, песок и гипс измельчаются, что является основой для производства блоков. Добавляя воду, песок измельчается до жидкой смеси. Его отправляют в миксер, в который добавляют цемент, гипс и известь. Далее компоненты замешиваются, и во время этого процесса к ним добавляется алюминиевая суспензия.
После того, как все компоненты были тщательно перемешаны друг с другом, смесь разливается в формы, которые перемещаются в зону созревания. При воздействии температуры 40 ° C в течение четырех часов материал набухает.При этом активно выделяется водород. Благодаря этому конечная масса приобретает необходимую пористую структуру.
С помощью токарного захвата и отрезного станка блоки разрезаются на требуемые размеры … В то же время автоматика контролирует точную и бездефектную резку изделий.
После этого блоки отправляются в автоклав для окончательной прочности. Этот процесс происходит в камере при температуре 180 ° C в течение 12 часов.В этом случае давление паров на газосиликат должно быть не менее 12 атмосфер. Благодаря этому режиму готовые блоки приобретают оптимальное значение конечной прочности.
Благодаря крану-разделителю и оборудованию для окончательного контроля качества блоки укладываются для их последующего естественного охлаждения. После этого на автоматической линии с блоков удаляются возможные загрязнения, блоки упаковываются и маркируются.
Примечательно то, что процесс производства безотходный, так как в момент резки, даже на стадии затвердевания, отходы сырого массива отправляются на повторную переработку, добавляя материал в другие блоки.
Поддоны с фасованными газосиликатными блоками получают собственный технический паспорт с подробными физическими свойствами и техническими характеристиками продукта, чтобы покупатель мог быть уверен в соответствии заявленным характеристикам.
Дальнейшая работа уже для дилеров и маркетологов, от которых будет зависеть успех продаж продукта.
Этот материал имеет значительные конкурентные преимущества и пользуется заслуженной популярностью на строительном рынке нашей страны.Отличается минимальным весом, что упрощает возведение стен, а также обеспечивает надежную теплоизоляцию интерьера, благодаря пористой структуре. К тому же газосиликатные блоки привлекают покупателей доступной ценой, которая выгодно отличается от кирпичных или деревянных.
Естественно, что этот строительный материал имеет свои особенности, а также специфику применения. Поэтому, несмотря на невысокую стоимость, использование газобетонных блоков не всегда целесообразно.Чтобы лучше разобраться в этих тонкостях, есть смысл подробно рассмотреть основные технические характеристики материала.
Состав газосиликатных блоков
Материал изготовлен по уникальной технологии. В частности, блоки получают вспениванием, что придает им ячеистую структуру. Для этого в формы с исходной смесью добавляется пенообразователь, которым обычно играет алюминиевый порошок. В результате сырье значительно увеличивается в объеме, и образуются пустоты.
Для приготовления исходной смеси обычно используют следующий состав:
Высококачественный цемент с содержанием силиката калия более 50% .
Песок, с 85% кварца.
Известь с содержанием оксидов магния и кальция более 70% и скоростью гашения до 15 минут.
Сульфанол С.
Стоит отметить, что включение цемента в смесь не является обязательным условием, а если используется, то в минимальных количествах.
Закалка блока завершается в автоклавных печах, где работают высокие давление и температурный режим.
Технические характеристики
Для газосиликатных блоков характерны следующие технические параметры:
Насыпной вес из 200 перед 700 шт. … Это показатель сухой плотности газобетона, на основании которого маркируются блоки.
Прочность на сжатие … Это значение варьируется в пределах B0.03-B20 , в зависимости от предполагаемого использования.
Показатели теплопроводности … Эти значения находятся в пределах 0,048-0,24 Вт / м, и напрямую зависят от плотности продукта.
Паронепроницаемость … Это соотношение составляет 0,30–0,15 мг / Па и также изменяется с увеличением плотности.
Усадка … Здесь оптимальные значения колеблются в пределах 0.5-0-7 , в зависимости от сырья и технологии изготовления.
Циклы замораживания … Это морозостойкость, обеспечивающая замораживание и оттаивание блоков без нарушения конструкции и прочностных показателей. По этим критериям газосиликатным блокам присвоена классификация от F15 до F100 .
Необходимо уточнить, что это не справочные показания, а средние значения, которые могут меняться в зависимости от технологии производства.
Размеры по ГОСТ
Конечно, производители выпускают газосиликатные блоки разных размеров. Однако большинство предприятий стараются следовать установленным нормам. ГОСТ за номером 31360 в редакции 2007 г. года. Здесь прописаны следующие размеры готовой продукции:
Важно понимать, что по ГОСТ допускаются отклонения значений длины и диагонали, которые относят готовые изделия к 1. -е или 2 -я категория.
Размеры стеновых блоков
ТД «Лиски-газосиликат» | ||||
Длина, мм | Ширина, мм | Высота, мм | Объем одного блока, м3 | |
Блоки обыкновенные | 600 | 200 | 250 | 0,03 |
600 | 250 | 250 | 0,038 | |
Блоки язычка | 600 | 200 | 250 | 0,03 |
600 | 300 | 250 | 0,045 | |
600 | 400 | 250 | 0,06 | |
600 | 500 | 250 | 0,075 | |
Блоки газосиликатные «YTONG» | ||||
Блоки обыкновенные | 625 | 200 | 250 | 0,031 |
625 | 250 | 250 | 0,039 | |
625 | 300 | 250 | 0,047 | |
625 | 375 | 250 | 0,058 | |
625 | 500 | 250 | 0,078 | |
Блоки язычка | 625 | 175 | 250 | 0,027 |
625 | 200 | 250 | 0,031 | |
625 | 250 | 250 | 0,039 | |
625 | 300 | 250 | 0,047 | |
625 | 375 | 250 | 0,058 | |
П-образные блоки | 500 | 200 | 250 | * |
500 | 250 | 250 | * | |
500 | 300 | 250 | * | |
500 | 375 | 250 | * |
Количество блоков на 1м3 кладки
Для этого необходимо перевести стороны блока в нужную единицу измерения и определить, сколько кубометров занимает один блок.
Наиболее распространенные на рынке продукты имеют следующие стандартные размеры: 600 * 200 * 300 … Переводим миллиметры в метры, и получаем 0,6 * 0,2 * 0,3 … Чтобы узнать объем одного блока, умножаем числа и получаем 0,036 м3 … Затем кубометр делим на полученную цифру.
Результат — число 27,7 , что после округления дает 28 газосиликатных блоков в кубометровой кладке.
Размеры перегородок
Вес материала
Конструкционная масса блока меняется в зависимости от плотности готового изделия.Судя по маркировке, можно выделить следующий вес:
Помимо плотности, основным фактором изменения веса считается общий размер готового блока.
Плюсы и минусы газобетона
Как и любой строительный материал, газосиликатные блоки имеют свои сильные и слабые стороны … К положительным характеристикам можно отнести следующие моменты:
Газосиликатный бетон относится к категории негорючих материалов и способен выдерживать воздействие открытого пламени до 5 часов , не изменяя формы и свойств.
Большие габаритные размеры обеспечивают быстрое возведение стеновых конструкций.
Блоки имеют относительно небольшой вес, что значительно упрощает рабочий процесс.
В производстве только натуральные материалы, поэтому газосиликатные блоки экологически чистые.
Пористая структура обеспечивает высокие показатели теплоизоляции помещения.
Материал прост в обработке, что позволяет возводить стены сложной геометрии.
К недостаткам можно отнести следующее:
Хорошо впитывают влагу, что сокращает срок эксплуатации.
Применение для приклеивания специальных клеев.
Обязательная внешняя отделка.
Следует отметить, что газосиликатные блоки требуют прочного основания. В большинстве случаев требуется армирующий пояс.
Газосиликат или газобетон?
Оба материала относятся к категории ячеистых бетонов, поэтому имеют практически идентичную структуру и свойства. Многие строители считают, что газосиликат и газобетон — это два названия одного и того же материала.Однако это заблуждение. При внешнем сходстве газобетон имеет ряд отличительных особенностей, что определяет их дальнейшее применение и технические характеристики.
В частности, при производстве газобетона допускается естественное твердение блока на открытом воздухе, для газосиликатного — автоклавные печи обязательно. Кроме того, для газобетонных блоков основным вяжущим является цемент, для силикатных аналогов — известь. Использование разных компонентов влияет на цвет готовых блоков.
Если говорить о конкретных характеристиках, можно заметить следующие отличия:
Газосиликатные блоки имеют равномерное распределение полых ячеек, что обеспечивает высокую прочность.
Вес газобетонных блоков намного больше, что требует армированного фундамента при строительстве.
По теплоизоляции газосиликатные блоки превосходят газобетонные.
Газобетон лучше впитывает влагу, что обеспечивает большее количество циклов замерзания.
Газосиликатные блоки имеют более согласованную геометрию, в результате можно упростить отделку стеновых конструкций.
По прочности материалы идентичны и могут служить более 50 лет .
Если ответить на вопрос: «Что лучше?» Газосиликатные блоки имеют гораздо больше технических преимуществ. Однако технология изготовления вынуждает увеличивать стоимость готовой продукции, поэтому газобетонные блоки дешевле.Поэтому желающие построить дом из качественного и современного материала выбирают газосиликат, желающие сэкономить на строительстве — предпочитают пенобетон.
При этом необходимо учитывать регион применения: в помещениях с повышенной влажностью воздуха срок службы газосиликатных блоков значительно сокращается.
Оштукатуривание стен из газосиликатных блоков
Штукатурка стен подразумевает соблюдение определенных правил и норм.В частности, внешняя отделка выполняется только после завершения внутренних работ . .. В противном случае на границе газосиликата и штукатурного слоя образуется слой конденсата, который вызовет трещины.
Если говорить о технологии работы, то можно выделить три основных этапа:
Нанесение грунтовочного слоя для улучшения адгезии.
Монтаж стеклопластиковой арматурной сетки.
Штукатурка.
Для отделочных работ лучше использовать силикатные смеси и силиконовые штукатурки, обладающие отличной эластичностью.Штукатурку нанести шпателем, прикоснувшись смесью к армирующей сетке. Минимальная толщина слоя 3 см , максимальная — 10 … Во втором случае штукатурка наносится в несколько слоев.
Клей для газосиликатных блоков
Структура материала предполагает использование специальных клеев для возведения стеновых конструкций. Стоит отметить, что специалисты рекомендуют приобретать клей и блоки в наборе, чтобы исключить конфликты материалов и обеспечить максимальное сцепление.При выборе клея нужно учитывать время застывания состава. Некоторые смеси схватываются на 15-20 минут , но это не показатель качества клея. Оптимальное время схватывания — 3-4 часа .
Если говорить о конкретных наименованиях, можно обратить внимание на следующие марки клея:
Win-160.
Юнис Униблок.
Следует отметить, что для летнего и зимнего строительства используются разные клеи.Во втором случае в смесь добавляют специальные добавки; на упаковке есть соответствующая отметка.
Расход клея на 1м3
Эта информация обычно предоставляется производителем и варьируется в пределах 1,5-1,7 кг … Необходимо уточнить, что приведенные значения актуальны только для горизонтальных поверхностей: для кубатуры расход клея составит заметно выше. Средние значения расхода клея на 1м3 кладки будут примерно 30 кг .
Обратите внимание, что это расчеты производителя и могут отличаться от фактических значений. Например, профессиональные строители утверждают, что на 1м3 кладки из газосиликатных блоков уходит не менее 40 кг … Это связано с тем, что пластичный состав заполняет все пустоты и изъяны в готовом блоке.
Рейтинг независимых производителей
Перед началом строительства важно выбрать производителя материала, который поставляет на рынок качественную продукцию.В российском регионе доверие потребителей заслужили следующие компании:
ЗАО «Кчелла-Аэроблок Центр» … Это немецкая компания, часть производственных мощностей которой находится в России. Продукция компании известна во всем мире своим немецким качеством. Любопытно, что XELLA работает по нескольким направлениям, три из которых направлены на добычу и последующую переработку сырья.
ЗАО «ЕвроАэроБетон» … Предприятие специализируется на производстве газосиликатных блоков с на 2008 год … Предприятие имеет собственные производственные линии, на которых применяется автоматизированный процесс, используется оборудование ведущих мировых брендов. Завод расположен в Ленинградской области, г. Сланцы.
ООО «ЛСР. Строительство-Урал » … Головной офис компании находится в Екатеринбурге, завод занимает лидирующие позиции на Урале. Предприятие имеет полувековую историю, использует автоматизированный производственный процесс, контролирует качество на всех этапах.
ЗАО «Липецкий силикатный завод» … История предприятия началась с 1938 года , это один из основных поставщиков центрального региона России. В 2012 году компания получила международный сертификат класса ISO 9001.2008 , что говорит о высоком качестве выпускаемой продукции.
ОАО «Костромской силикатный завод» … Одно из старейших предприятий страны, основанное в 1930 г. год.За годы существования был разработан специальный устав, позволяющий вывести качество продукции на принципиально новый уровень. Компания дорожит своей репутацией и не может похвастаться отрицательными отзывами потребителей.
Отметим, что это далеко не полный список надежных производителей газосиликатных блоков в российском регионе. Однако продукция этих брендов — лучшее соотношение цены и качества.
В современных строительных технологиях большое значение придается выбору материала для возведения того или иного типа здания.Газосиликатные блоки сегодня считаются одними из самых популярных строительных материалов, которые отличаются рядом преимуществ и используются довольно часто.
Их широкое распространение обусловлено оптимальным соотношением цены и качества — по большому счету, ни один другой строительный материал не может поддерживать это соотношение так выгодно.
Если посмотреть, то вряд ли газобетон относится к современным строительным материалам — он был разработан в конце 19 века. В начале прошлого века группа ученых даже запатентовала открытие нового чудо-материала, но его свойства были далеки от тех, которые отличают сегодняшние газовые силикаты.
В современном виде газосиликатный материал был получен в конце 20 века — это бетон с ячеистой структурой, твердение которого происходит в автоклаве. Этот метод был найден еще в 30-х годах, и с тех пор не претерпел существенных изменений. Улучшение характеристик произошло за счет внесения усовершенствований в технологию его производства.
Газобетон — одна из основ для производства газосиликатных блоков
Принцип изготовления
В качестве исходных ингредиентов для производства газобетона используются следующие вещества:
- песок; Цемент
- ;
- лайм;
- гипс;
- вода.
Для получения ячеистой структуры в состав добавляют порцию алюминиевой пудры, которая служит для образования пузырьков. После перемешивания массу выдерживают необходимое время, ожидая набухания, после чего разрезают на части и помещают в автоклав. Там масса затвердевает в среде пара — это энергосберегающая и экологически чистая технология. При производстве газобетона не выделяются вредные вещества, способные нанести значительный вред окружающей среде или здоровью человека.
Недвижимость
Характеристики, отличающие газосиликатные блоки, позволяют рассматривать их как строительный материал, хорошо подходящий для строительства зданий. Специалисты утверждают, что газобетон сочетает в себе лучшие качества камня и дерева — стены из него прочны и хорошо защищают от холода.
Пористая структура блоков гарантирует высокие показатели пожарной безопасности
Ячеистая структура объясняет небольшой коэффициент теплопроводности — он намного ниже, чем у кирпича.Поэтому постройки из газосиликатного материала не так требовательны к утеплению — в некоторых климатических зонах оно вообще не требуется.
Ниже мы приводим основные свойства газосиликата, благодаря которым он стал настолько популярным в строительной отрасли:
- малая масса при внушительных габаритах — это свойство позволяет значительно снизить затраты на установку. Кроме того, для погрузки, транспортировки и возведения стен не требуется кран — достаточно обычной лебедки.По этой причине скорость строительства также намного выше, чем при работе с кирпичом;
- хорошая обрабатываемость — газосиликатный блок можно без проблем распиливать, сверлить, фрезеровать обычным инструментом;
- высокая экологичность — специалисты утверждают, что этот показатель для газобетона сопоставим с деревянным. Материал не выделяет вредных веществ и не загрязняет окружающую среду, при этом, в отличие от дерева, не гниет и не стареет;
- технологичность — газосиликатные блоки изготовлены таким образом, что с ними удобно работать.Помимо небольшой массы, они отличаются удобной формой и технологичностью выемок, захватов, пазов и т. Д. Благодаря этому скорость работы с ними увеличивается в 4 раза по сравнению со строительством зданий из кирпича;
- низкая теплопроводность газосиликатных блоков — это связано с тем, что газобетон на 80 процентов состоит из воздуха.
В зданиях, построенных из этого материала, снижаются затраты на отопление, к тому же их можно утеплить на треть меньше;
В газосиликатном доме будет поддерживаться стабильный микроклимат в любое время года
- Морозостойкость — в конструкции есть специальные пустоты, куда при промерзании вытесняется влага.При соблюдении всех технических требований к изготовлению морозостойкость газобетона превышает двести циклов;
- Звукоизоляция — очень важный параметр, так как сегодня уровень шума на улицах достаточно высокий, а дома хочется отдохнуть в тишине. Газосиликат за счет пористой структуры хорошо сдерживает звук, выгодно в этом плане по сравнению с кирпичом;
- пожарная безопасность — минералы, используемые для производства газосиликата, не поддерживают горение.Газосиликатные блоки способны выдерживать воздействие огня в течение 3-7 часов, поэтому его используют для строительства дымоходов, лифтовых шахт, огнестойких стен и т. Д.
- высокопрочный — газосиликат выдерживает очень высокие сжимающие нагрузки, поэтому подходит для строительства зданий с несущими стенами до трех этажей или каркасно-монолитных зданий без каких-либо ограничений;
- негигроскопичность — пенобетон не впитывает воду, которая при попадании на него быстро сохнет, не оставляя следов.Это связано с тем, что пористая структура не задерживает влагу.
результаты Голосовать
Где бы вы предпочли жить: в частном доме или в квартире?
Вернуться на
Где бы вы предпочли жить: в частном доме или в квартире?
Вернуться на
Основным недостатком газосиликата является недостаточная прочность на изгиб, однако специфика его использования такова, что он практически исключает возможность изгибающих нагрузок, поэтому этот недостаток не играет большой роли.
Чем меньше воздуха в теле искусственного камня, тем выше его прочность и плотность
Марки газоблока
Плотность газосиликатных блоков — главный критерий, который учитывается при маркировке.
В зависимости от размеров строительный материал имеет разный набор характеристик, что определяет сферу его применения.
Ниже мы рассмотрим различные марки газосиликата и способы их применения в строительстве:
- D300 — наиболее подходящий строительный материал для возведения монолитных зданий.Плотность газосиликатных блоков этой марки составляет 300 кг / м 3 — хорошо подходит для возведения стен малоэтажных домов в один слой или для двухслойных монолитных домов с высокой степенью теплоизоляции;
- D400 — применяется для строительства двухэтажных домов и коттеджей, а также для теплоизоляции наружных несущих стен многоэтажных домов;
- D500 — это тип с наилучшим сочетанием теплоизоляционных и конструктивных характеристик.Он идентичен по плотности бревенчатым или деревянным балкам и применяется для возведения перегородок и внутренних стен зданий, проемов окон и дверей, а также оболочек армированных перемычек, стропил и ребер жесткости;
- D 600 — это газосиликатный блок с максимальной плотностью, которая составляет 600 кг / м 3, применяется там, где необходимо устройство прочных стен, подверженных высоким нагрузкам.
Ниже представлена таблица, иллюстрирующая другие параметры, по которым различают газосиликатные блоки разных марок.
В зависимости от плотности все газосиликатные блоки принято делить на конструкционные, конструкционные и теплоизоляционные и теплоизоляционные.
Точность размеров
Газосиликаты могут иметь отклонения в размерах. В зависимости от размера различают три категории точности этого материала:
- Первая категория предназначена для укладки блока насухо или на клей. Допускает погрешность размеров по высоте, длине и толщине до полутора миллиметров, прямоугольности и углам — до двух миллиметров, краям — до пяти миллиметров.
- Вторая категория предназначена для укладки на клей газосиликатных блоков.
В нем допускается погрешность основных размеров до двух миллиметров, прямоугольности — до 3 миллиметров, углов — до 2 миллиметров и кромок — до 5 миллиметров.
- На раствор ставят газоблоки третьей категории, у которых погрешность основных размеров не более 3 миллиметров, прямоугольности — менее 3 мм, углов — до 4 миллиметров, кромок — до 10 миллиметров.
Выбор газосиликата
При покупке газосиликатных блоков обычно оценивают три критерия, влияющие на решение:
- функциональные характеристики — плотность, морозостойкость, теплопроводность и др .;
- размер одного блока;
- объем одного блока; Стоимость
- .
Плиты из силиката кальция — Surani Interior
Силикат кальция — белый сыпучий порошок, полученный из известняка и диатомовой земли.Он имеет низкую насыпную плотность и высокое физическое водопоглощение. Он используется в дорогах, изоляции, кирпиче, черепице, поваренной соли и встречается в цементах, где он известен как белит (или в обозначении химика цемента C2S).
Мы вовлечены в предложение Блоков силиката кальция. Сырье для силикатного кирпича включает известь, смешанную с кварцем, измельченный кремний или измельченный кремнистый камень вместе с минеральными красителями.
Материалы смешивают и оставляют до полной гидратации извести, затем смесь прессуют в формы и выдерживают в автоклаве в течение двух или трех часов для ускорения химического твердения.
Готовые кирпичи получаются очень аккуратными и однородными. Кирпичи могут быть разных цветов, обычно белый, но могут быть и пастельные оттенки.
Картон из силиката кальция Основные области применения:
- Электростанции Котлы, паропроводы, выхлопные трубы газовых установок, турбины, мазутные трубопроводы и дымоходы.
Удобрения, переработка нефтеперерабатывающей и нефтехимической промышленности, установка крекинга газа, нагреватель, воздуховоды, бойлер, паропроводы и технологические трубопроводы.
- Сталелитейная промышленность Вал доменной печи, печь и вытяжная труба, ямы для выдержки, печи повторного нагрева и отжига, котел-утилизатор, кровельные и регенераторные щиты коксовых батарей и печи для обжига извести, воздуховоды горячего воздуха и дымовых газов.
- Устройство риформинга на основе губчатого железа, резервуар десуферизатора, каналы горячего воздуха и дымовых газов, а также система рекуперации отходящего тепла.
- Циклоны для подогрева цементной промышленности, предварительный нагреватель, воздуховод Klin Riser, колпак, колосниковый охладитель, канал третичного воздуха, дымоход
- Газовые каналы и Э.С.П.
- Сахарный котел, паровой и технологический трубопровод
Не можете найти то, что ищете? Звоните нам: + 91-22-25005757 / 5758 | 80800 33501/80805 80580
ORНажмите здесь, чтобы связаться с нами >>
Этот сайт использует файлы cookie для повышения производительности.Если ваш браузер не принимает файлы cookie, вы не можете просматривать этот сайт.
Настройка вашего браузера для приема файлов cookie
Существует множество причин, по которым cookie не может быть установлен правильно. Ниже приведены наиболее частые причины:
- В вашем браузере отключены файлы cookie. Вам необходимо сбросить настройки своего браузера, чтобы он принимал файлы cookie, или чтобы спросить, хотите ли вы принимать файлы cookie.
- Ваш браузер спрашивает вас, хотите ли вы принимать файлы cookie, и вы отказались.Чтобы принять файлы cookie с этого сайта, нажмите кнопку «Назад» и примите файлы cookie.
- Ваш браузер не поддерживает файлы cookie. Если вы подозреваете это, попробуйте другой браузер.
- Дата на вашем компьютере в прошлом. Если часы вашего компьютера показывают дату до 1 января 1970 г.,
браузер автоматически забудет файл cookie. Чтобы исправить это, установите правильное время и дату на своем компьютере.
- Вы установили приложение, которое отслеживает или блокирует установку файлов cookie.Вы должны отключить приложение при входе в систему или проконсультироваться с системным администратором.
Почему этому сайту требуются файлы cookie?
Этот сайт использует файлы cookie для повышения производительности, запоминая, что вы вошли в систему, когда переходите со страницы на страницу. Чтобы предоставить доступ без файлов cookie потребует, чтобы сайт создавал новый сеанс для каждой посещаемой страницы, что замедляет работу системы до неприемлемого уровня.
Что сохраняется в файле cookie?
Этот сайт не хранит ничего, кроме автоматически сгенерированного идентификатора сеанса в cookie; никакая другая информация не фиксируется.
Как правило, в файлах cookie может храниться только информация, которую вы предоставляете, или выбор, который вы делаете при посещении веб-сайта. Например, сайт не может определить ваше имя электронной почты, пока вы не введете его. Разрешение веб-сайту создавать файлы cookie не дает этому или любому другому сайту доступа к остальной части вашего компьютера, и только сайт, который создал файл cookie, может его прочитать.
Полезное использование диоксида углерода в производстве сборных железобетонных изделий (Технический отчет)
Шао, Исинь. Выгодное использование углекислого газа в производстве сборных железобетонных изделий . США: Н. П., 2014.
Интернет. DOI: 10,2172 / 1155035.
Шао, Исинь. Выгодное использование углекислого газа в производстве сборных железобетонных изделий . Соединенные Штаты. https://doi.org/10.2172/1155035
Шао, Исинь.
Чт.
«Полезное использование диоксида углерода в производстве сборных железобетонных изделий». Соединенные Штаты. https://doi.org/10.2172/1155035. https://www.osti.gov/servlets/purl/1155035.
@article {osti_1155035,
title = {Выгодное использование диоксида углерода в производстве сборного железобетона},
author = {Shao, Yixin},
abstractNote = {Изучена возможность использования углекислого газа в качестве сырья при производстве сборного железобетона.Двуокись углерода реагирует с соединениями кальция в бетоне, образуя твердые карбонаты кальция в связующей матрице. Два типичных сборных железобетона проверяются на их способность удерживать углекислый газ во время производства. Это бетонные блоки и фиброцементные панели. Эти два продукта в настоящее время производятся серийно и обрабатываются паром. Двуокись углерода может использоваться для замены пара в процессе отверждения для ускорения ранней прочности, повышения долговечности и снижения энергии и выбросов. Для реакции в течение 24-часового технологического окна теоретически максимально возможное поглощение углерода бетоном составляет 29% в расчете на массу цемента в продукте.Для достижения максимального поглощения разработан специальный процесс, повышающий эффективность реакции до 60-80% при 4-часовом отверждении диоксидом углерода и повышающий устойчивость к циклическому замораживанию-оттаиванию и воздействию сульфат-ионов. Процесс также оптимизирован для достижения проектной цели по утилизации углерода в размере 10 долларов США за тонну CO2. Используя самоконцентрирующуюся абсорбционную технологию, можно производить CO2 высокой чистоты по цене ниже 40 долларов за тонну. Благодаря недорогим технологиям улавливания и утилизации CO2 можно создать сеть для улавливания и утилизации углерода вблизи источников углерода.Если бы все блочные производители и производители панелей в Соединенных Штатах могли внедрить в свое производство углекислый газ вместо пара, использование углерода только на этих двух рынках могло бы потреблять более 2 Мт CO2 в год. Этот процесс сбора и использования может быть распространен на большее количество сборных железобетонных изделий и будет продолжаться в течение многих лет.},
doi = {10.2172 / 1155035},
url = {https://www.osti.gov/biblio/1155035},
journal = {},
number =,
объем =,
place = {United States},
год = {2014},
месяц = {6}
}
Огнеупор | промышленный материал | Британника
Огнеупорный материал , любой материал с необычно высокой температурой плавления, который сохраняет свои структурные свойства при очень высоких температурах.Огнеупоры, состоящие в основном из керамики, в больших количествах используются в металлургической, стекольной и керамической отраслях, где им придают различные формы, чтобы покрыть внутренности печей, обжиговых печей и других устройств, обрабатывающих материалы при высоких температурах.
В этой статье рассматриваются основные свойства керамических огнеупоров, а также основные огнеупорные материалы и их применение. В некоторых местах статьи упоминаются технологии обработки, используемые при производстве керамических огнеупоров; Более подробное описание этих процессов можно найти в статьях «Традиционная керамика» и «Современная керамика».Связь между свойствами керамических огнеупоров и их химическим составом и микроструктурой объясняется составом и свойствами керамики.
Недвижимость
Из-за высокой прочности, которую демонстрируют их первичные химические связи, многие керамические материалы обладают необычно хорошим сочетанием высокой температуры плавления и химической инертности. Это делает их полезными в качестве огнеупоров. (Слово «огнеупор» происходит от французского réfractaire, , что означает «тугоплавкий».) Свойство химической инертности имеет особое значение в металлургии и стекольном производстве, где печи подвергаются воздействию чрезвычайно агрессивных расплавленных материалов и газов. Помимо устойчивости к температуре и коррозии, огнеупоры должны обладать превосходной стойкостью к физическому износу и истиранию, а также к термическому удару. Термический шок возникает, когда объект быстро охлаждается от высокой температуры. Поверхностные слои сжимаются относительно внутренних слоев, что приводит к развитию растягивающего напряжения и распространению трещин. Керамику, несмотря на ее хорошо известную хрупкость, можно сделать стойкой к термическому удару, изменив ее микроструктуру во время обработки.Микроструктура керамических огнеупоров довольно грубая по сравнению с белыми изделиями, такими как фарфор, или даже с изделиями из структурной глины с менее мелкой текстурой, такими как кирпич. Размер зерен наполнителя может измеряться в миллиметрах, а не в микрометрах, характерных для белой керамики. Кроме того, большинство керамических огнеупорных изделий довольно пористые, с большим количеством воздушных пространств различного размера, включенных в материал. Наличие крупных зерен и пор может снизить несущую способность продукта, но также может притупить трещины и тем самым снизить подверженность термическому удару.Однако в случаях, когда огнеупор будет контактировать с агрессивными веществами (например, в стекловаренных печах), пористая структура нежелательна. Затем керамический материал может быть изготовлен с более высокой плотностью, включающей меньшее количество пор.
Состав и обработка
Состав и обработка керамических огнеупоров сильно различаются в зависимости от области применения и типа огнеупора. Большинство огнеупоров можно классифицировать по составу на глиняные и неглинистые.Кроме того, они могут быть классифицированы как кислотные (содержащие диоксид кремния [SiO 2 ] или диоксид циркония [ZrO 2 ]), основные (содержащие оксид алюминия [Al 2 O 3 ] или оксиды щелочноземельных металлов, такие как известь [CaO] или магнезия [MgO]). К огнеупорам на основе глины относятся шамотная, высокоглиноземистая и муллитовая керамика. Существует широкий ассортимент неглинистых огнеупоров, включая основные материалы, глинозем со сверхвысоким содержанием алюминия, кремнезем, карбид кремния и циркон. Большинство изделий из глины обрабатываются аналогично другим традиционным изделиям из керамики, например, изделиям из структурной глины; е.g., для формования изделий используются процессы твердого бурового раствора, такие как штамповка или экструзия, которые затем сушатся и пропускаются через длинные туннельные печи для обжига. Обжиг, как описано в статье традиционной керамики, вызывает частичное остекловывание или образование стекла, которое представляет собой процесс жидкого спекания, который связывает частицы вместе. С другой стороны, огнеупоры на неглиной основе склеиваются с использованием технологий, предназначенных для современных керамических материалов. Например, керамика из сверхвысокого оксида алюминия и циркония связывается посредством спекания в жидком или твердом состоянии, основные кирпичи связываются посредством химических реакций между компонентами, а карбид кремния связывается реакционным способом из кварцевого песка и кокса.Эти процессы описаны в статье «Современная керамика».
Огнеупоры на основе глины
В этом разделе описаны состав и свойства огнеупоров на основе глины. Большинство из них производится в виде предварительно отформованного кирпича. Большая часть остальной продукции представляет собой так называемые монолитные материалы, которые можно формировать и отверждать на месте. В эту категорию входят растворы для цементирования кирпича и смеси для набивки или торкретирования (распыление из пистолета под давлением) на место.Кроме того, легкая огнеупорная изоляция может быть изготовлена в виде древесноволокнистых плит, одеял и форм для вакуумного литья.
Рабочей лошадкой огнеупоров на глиняной основе являются так называемые шамотные материалы. Они сделаны из глин, содержащих алюмосиликатный минерал каолинит (Al 2 [Si 2 O 5 ] [OH] 4 ) плюс примеси, такие как щелочи и оксиды железа. Содержание глинозема колеблется от 25 до 45 процентов. В зависимости от содержания примесей и отношения глинозема к кремнезему шамоты классифицируются как легкие, средние, высокопроизводительные и сверхмощные, причем температура использования возрастает по мере увеличения содержания глинозема.Шамотные кирпичи или огнеупорные кирпичи демонстрируют относительно низкое расширение при нагревании и, следовательно, умеренно устойчивы к тепловому удару. Они довольно инертны в кислой среде, но довольно реактивны в основных средах. Кирпич шамотный используется для облицовки внутренних частей доменных печей, доменных печей и коксовых печей.
Высокоглинозем
Огнеупоры с высоким содержанием глинозема производятся из боксита, природного материала, содержащего гидроксид алюминия (Al [OH] 3 ) и каолинитовые глины.Это сырье обжигается с получением смеси синтетического оксида алюминия и муллита (алюмосиликатный минерал с химической формулой 3Al 2 O 3 · 2SiO 2 ). Огнеупоры с высоким содержанием глинозема по определению содержат от 50 до 87,5 процентов глинозема. Они намного прочнее шамотных огнеупоров при высоких температурах и в основных средах. Кроме того, они обладают лучшей стабильностью объема и стойкостью к истиранию. Кирпич высокоглиноземистый используется в доменных печах, доменных печах и ковшах для жидкой стали.
Муллит
Муллит представляет собой алюмосиликатное соединение с определенной формулой 3Al 2 O 3 · 2SiO 3 и содержанием оксида алюминия примерно 70 процентов. Он имеет температуру плавления 1850 ° C (3360 ° F). Для получения такого состава с бокситом смешивают различные глины. Твердеют муллитовые огнеупоры путем спекания в электрических печах при высоких температурах. Они являются наиболее устойчивыми из алюмосиликатных огнеупоров и обладают отличной стойкостью к высокотемпературным нагрузкам.Муллитовые кирпичи используются в доменных печах и в подоконниках стекловаренных печей.
Гонка за изобретением цемента
На протяжении всего жизненного цикла бетона — от известняка до цемента и бетона — Solidia производит до 70 процентов меньше выбросов по сравнению с портландцементом. Таким образом, если 1000 кг портландцемента высвободят 1000 кг более своего жизненного цикла, то цемент Solidia выпускает всего 300 килограммов. Это не ноль, но это шаг вперед для отрасли, которая добилась лишь незначительного прогресса.
Более того, бетон, произведенный с использованием цемента Solidia, превосходит строительные стандарты и требует менее 24 часов для отверждения по сравнению с неделями для отверждения портландцемента. Эти утверждения были подтверждены Министерством здравоохранения США. Energy, которая предоставила стартапу некоторое финансирование. Solidia также использовала уже существующие цементные заводы для производства 10 000 метрических тонн своей продукции, демонстрируя масштабируемость.
Во время экскурсии главный технолог компании Николас ДеКристофаро привел пример того, сколько углекислого газа удерживается цементом Solidia.Он положил бетонный кирпич (около 12 дюймов x 5 дюймов x 5 дюймов). на столе. «Этот блок, — сказал он, — уловил столько углекислого газа, сколько вы можете найти в воздухе во всей этой комнате». (Комната представляла собой офис среднего размера, 15 футов x 15 футов x 10 футов.)
УспехSolidia на данный момент вызвал большой интерес, и это помогло им собрать более 60 миллионов долларов. В совет директоров компании входят представители LafargeHolcim и HeidelbergCement, крупнейших в мире и четвертые по величине цементные компании соответственно; Кляйнер Перкинс Кауфилд Байерс, один из крупнейших инвесторов в мире; а также BASF и Air Liquide, два из крупнейших мировых поставщиков сыпучих химикатов.В октябре Солидия объявила о большом раунде финансирования от Oil and Gas Climate Initiative, группы некоторых из крупнейших нефтяных компаний мира, которые рассматривают развитие технологий как средство выживания в мире с ограниченным выбросом углерода.
Тем временем другие цементные стартапы находят собственные ниши. Канадский стартап CarbonCure имеет 50 бетонных заводов в Северной Америке, использующих его технологию. В отличие от Solidia, CarbonCure не изобретала заново цемент.Вместо, он обнаружил неэффективность процесса и заполнил пробел, ну, углекислым газом.
Когда цемент смешивается с водой и гравием для образования бетона, он начинает улавливать углекислый газ из воздуха с образованием карбоната кальция. Но реакция так и не доходит до завершения, потому что бетон твердеет до требований строителей. искать без того, чтобы весь цемент в смеси реагировал с улавливанием двуокиси углерода. CarbonCure работает с производителями бетона, которые используют обычный портландцемент.Вместо термического или парового отверждения CarbonCure создает камеры, в которых бетон блоки обработаны углекислым газом. В среде со 100-процентным содержанием углекислого газа вступает в реакцию гораздо больше цемента, чем в воздухе, где концентрация углекислого газа составляет всего 0,4 процента.
Полученный бетонный продукт имеет большую прочность на разрыв и твердость, чем продукт, полученный без отверждения углекислым газом. Чистый углекислый газ поступает от поставщиков, которые все чаще используют отходы химической промышленности. процессы, которые в противном случае выбросили бы его в атмосферу.Производители бетона могут окупить затраты на технологию CarbonCure, взимая со своих клиентов более высокую цену за то, что, по их мнению, является лучшим продуктом. в За 10 лет с момента основания компания собрала более 10 миллионов долларов. В прошлом году калифорнийский проект высокоскоростной железной дороги объявил, что будет использовать бетон CarbonCure на 30-мильном участке между Мадерой и Фресно.
Другой стартап, Calix, , базирующаяся в Австралии, разработала процесс, который сокращает время и энергию, необходимые для нагрева известняка.Более того, вместо того, чтобы бросать уголь в печь для обогрева, он использует природный газ, который производит менее половины выбросов углерода на единицу произведенной энергии.
Вот как это работает. В обычных печах известняк и уголь сжигаются в одной камере. Вместо этого Calix использует двухствольную конструкцию, в которой природный газ сжигается во внешнем бочке, а известняк заливается сверху вниз. во внутренний ствол. Поскольку тепло не находится в прямом контакте с известняком, реакция должна быть менее эффективной, чем в обычной печи.Но Calix решает эту проблему, предварительно измельчая известняк в мелкий порошок, что увеличивает площадь его поверхности и позволяет косвенному нагреву завершить ту же реакцию.
Углекислый газ, выделяющийся во внутренней камере в виде известняка, превращается в известь и затем может быть уловлен в виде чистого газа и либо храниться в канистрах для использования в таких стартапах, как CarbonCure, либо закопан под землей в истощенных нефти и газе. поля, где он может безопасно оставаться вдали от атмосферы Земли.
В целом, процесс значительно снижает выбросы при производстве цемента. Сотрудничая с HeidelbergCement, Calix выиграла грант Европейского Союза в размере 15 миллионов долларов в феврале на начало строительства завода в Италии, который может доказать технология работает коммерчески.
В меньшем масштабе, Carbicrete — это компания, основанная на исследованиях, проведенных в Университете Макгилла в Канаде. Компания полностью отказывается от цемента.Вместо этого он использует промышленный шлак, отходы производства металлов, в качестве связующее в бетоне. С химической точки зрения шлак представляет собой сложную смесь, содержащую множество силикатов и оксидов, подобных тем, которые содержатся в цементе. Как и другие стартапы, он отверждает бетон в присутствии углекислого газа, компания утверждает, что это бетон с отрицательными выбросами, характеристики которого лучше, чем у обычного бетона. Хотя в мире недостаточно шлака для производства всего необходимого нам бетона, компания может просто найдите нишевое приложение.В конце концов, в отличие от ограниченных запасов волластонита, который необходимо добывать, шлак доступен как отходы, за утилизацию которых часто платит металлургическая промышленность.
Строим лучший мир с помощью зеленого цемента | Наука
«Знаете, цемент везде», — говорит Николаос Власопулос, инженер-эколог Имперского колледжа в Лондоне, сидя в ярко освещенном конференц-зале колледжа в громадном семиэтажном здании, о котором идет речь.«Это все вокруг нас».
В прошлом году в мире было произведено 3,6 миллиарда тонн цемента — минеральной смеси, которая затвердевает в бетон при добавлении к воде, песку и другим материалам — и это количество может увеличиться на миллиард тонн к 2050 году. В глобальном масштабе это единственное вещество, которое люди используют больше чем бетон, по общему объему, составляет вода.
Власопулос говорит, что достоинства цементадавно очевидны: он недорогой, текучий и, что несколько необъяснимо, становится твердым, как камень.Но редко признают еще одну важную деталь: цемент грязный. Не грязный, потому что в нем не снимут одежду, хотя эта проблема преследовала строителей на протяжении веков. Ключевой ингредиент — известняк, в основном карбонат кальция, останки очищенных от панциря морских существ. Рецепт изготовления цемента требует нагревания известняка, для чего требуется ископаемое топливо. А при нагревании известняк выбрасывает углекислый газ в атмосферу, где он улавливает тепло, способствуя глобальному потеплению.На производство цемента приходится 5 процентов мировых выбросов углекислого газа, производимых человеком; в Соединенных Штатах только потребление ископаемого топлива (для транспорта, электричества, химического производства и других целей) и черная металлургия выделяют больше парниковых газов. А поскольку быстро развивающиеся страны, такие как Китай и Индия, используют цемент для строительства своего подъема, грязь от цемента становится одним из главных недостатков глобализации.
Если широкая общественность не замечает огромного вклада цемента в загрязнение воздуха, то 31-летний Власопулос уже давно об этом знает.Он вырос в Патрах, греческом порту. Его отец был инженером, а мать работала в банке, а летом Власопулос уезжал из колледжа Димокришн Панэпистимион Фракис, где он изучал экологическую инженерию, и вместе со своим дядей работал на цементном заводе. Это было случайно. Его работа заключалась в сборке оборудования для измерения уровня выбросов углекислого газа. Они были высокими; Обычно завод производит около тонны углекислого газа на каждую тонну цемента. Власопулос считал работу интересной, но не видел цемента в своем будущем.Это было скучно, было старым, грязным.
Затем один из его профессоров в Имперском колледже, где он работал над степенью магистра инженерных наук, получил финансирование на исследование нового типа цемента, производимого австралийской компанией. Профессор Кристофер Чизман убедил Власопулоса участвовать в проекте и получить степень доктора философии. «Это был шанс хорошо поработать», — сказал Власопулос в своей типично сдержанной манере.
Люди пытались построить лучший цемент практически с начала истории.Более 2000 лет назад римляне изобрели смесь извести, вулканического пепла и кусков камня, чтобы сформировать бетон, который использовался для создания гаваней, памятников и зданий — клей ранних городов, включая Пантеон и Колизей. В 1820-х годах в Лидсе, Англия, примерно в 200 милях от Имперского колледжа, каменщик по имени Джозеф Аспдин изобрел современный цемент. Аспдин разогрел смесь тонко измельченного известняка и глины на своей кухне. После того, как он добавил воды, смесь затвердела. Voilà — так родился строительный блок промышленной революции.Поскольку материал выглядел как популярный строительный камень с острова Портленд, Аспдин назвал свое изобретение портландцементом. Патент, выданный в 1824 году, был направлен на «усовершенствование способа производства искусственного камня».
Австралийские разработчики попробовали новый рецепт, смешивая портландцемент с оксидом магния. Они надеялись сократить выбросы углерода, потому что оксид магния может заменить часть известняка, а оксид магния не нужно нагревать при такой высокой температуре.Известняк должен быть нагрет до 2600 градусов по Фаренгейту, но оксид магния может быть приготовлен для цемента при 1300 градусах, температуре, которая может быть достигнута с биомассой и другими видами топлива, которые выделяют меньше углерода, сокращая потребление ископаемого топлива.
Но Власопулос быстро обнаружил, что смесь не снижает общих выбросов углекислого газа. В некоторых тестах выбросы почти удвоились, потому что сам оксид магния образуется путем нагревания карбонатов магния, процесса, при котором выделяется диоксид углерода.
«Я помню, как чувствовал себя очень разочарованным, потому что, когда вы видите, что проект, над которым вы работаете, на самом деле не такой, как вы думали, вы теряете мотивацию», — сказал он. «Но мы чувствовали, что это очень стоящий проект, стоящая идея, поэтому мы попытались найти другой способ решения проблемы».
В то время, когда Власопулос поднял этот вопрос, в 2004 году крупные цементные компании по всему миру искали новые способы сделать портландцемент более экологически чистым.Производители добавили побочные продукты из стали, такие как шлак; остатки угля, такие как летучая зола; и другие материалы, такие как оксид магния, для увеличения объема цементной смеси, требующие меньше портландцемента. Они экспериментировали с минеральными добавками, чтобы снизить температуру, необходимую для приготовления материалов.
Но сложно изменить продукт, химический состав которого недостаточно изучен. «На самом деле мы никогда не знали точного химического состава этого материала», — сказал Хэмлин Дженнингс, эксперт по химии цемента и глава Concrete Sustainability Hub Массачусетского технологического института, одной из нескольких академических инициатив по созданию «зеленого» цемента.«Я не думаю, что сегодня в мире существует какой-либо строительный материал, который изучен хуже, чем портландцемент».
Пока цементные компании возились с оригиналом, Власопулос пошел другим путем. «С портландцементом можно сделать так много, чтобы он стал лучше», — сказал он. «Что есть, то есть. Это материал, с которого вы начинаете. Мы должны были придумать что-то еще ». Власопулосу понравилась идея использовать оксид магния в качестве замены известняка для формирования цемента, но ему требовался другой материал, чтобы сделать его твердым.Смешивание оксида магния с водой не поможет — смесь станет густой. И ему нужно было найти источник оксида магния, который не выделял бы так много углекислого газа. Класс материала, на котором он остановился, — это силикаты магния, безуглеродные соединения, полученные из талька, серпентина, оливина или других минералов. Мировые запасы этих минералов составляют около 10 000 миллиардов тонн, что является важным фактором, потому что, если у кого-то закончится мука, выпечка пирогов будет невозможна.
Власопулос не очень-то хочет объяснять, как работает его экспериментальное соединение.Его секретный соус, пожалуй, очень прибыльный секрет. Было зарегистрировано несколько патентов. Он раскроет многое: несколько лет назад он начал смешивать оксид магния с другими химическими соединениями, которые он создал, и с водой. Смесь затвердела в маленький шарик. Он принес его в офис Чизмена. «Вы могли почувствовать тепло, исходящее от этого маленького мяча, — сказал Чизмен. «Что-то явно происходило». Горели химические реакции; высвобождалась энергия. Они не особо волновались. «Я имею в виду, что мы говорим здесь о цементе — это не совсем самый сексуальный материал в мире», — сказал Чизман.«Я не бегал по коридорам, катаясь на колесах, но это было интересно».
Химические вещества, которые Власопулос смешивает с оксидом магния и водой для затвердевания цемента, представляют собой карбонаты магния, которые он производит, добавляя диоксид углерода к другому сырью. Это означает, что в некоторых сценариях цемент не просто углеродно-нейтральный — он отрицательный. На каждую тонну произведенного цемента Власопулоса может быть поглощена одна десятая тонны углекислого газа.
В конце концов Власопулос с помощью Cheeseman основал компанию Novacem по разработке нового цемента.Фирма с более чем дюжиной сотрудников и партнерскими отношениями с некоторыми из крупнейших цементных компаний в мире расположена в бизнес-инкубаторе для начинающих высокотехнологичных компаний в Имперском колледже. В то время как некоторые другие компании на объекте являются стартапами в области наук о жизни, с микробиологическими лабораториями, полными машин для секвенирования генов и коллекциями пробирок, лаборатория Novacem представляет собой просторное предприятие, производящее громкие звуки, множество пыли и ведро за ведром с цементом. Это первый цементный завод в центре Лондона со времен римлян.
Рабочие в касках, защитных очках, масках и белых халатах работают на миниатюрной версии цементного завода, мало чем отличающейся от того, на котором Власопулос работал во время летних перерывов.
Несмотря на то, что Novacem все еще совершенствует свои процедуры, он вместе с еще пятью другими компаниями и университетскими центрами борется за создание более экологичного цемента. «Учитывая все внимание к выбросам углерода в наши дни, появилось много предпринимателей», — сказал Дженнингс из Массачусетского технологического института. «Они видят возможности.«В цементную промышленность с доходом 170 миллиардов долларов в год вливаются инвестиционные деньги.
У калифорнийской компании Calera, пожалуй, самый необычный подход: она использует углекислый газ, выбрасываемый электростанцией, и смешивает его с морской водой или рассолом для создания карбонатов, которые используются для производства цемента. Их можно добавлять в портландцемент, чтобы частично или полностью заменить известняк. Calera получил 50 миллионов долларов инвестиций от Винода Хосла, компьютерного инженера, который, возможно, является самым уважаемым и богатым инвестором Кремниевой долины в зеленые технологии.«Мы фактически делаем наш цемент из CO2», — сказал основатель компании Брент Констанц. «Мы берем CO2, который мог бы попасть в атмосферу, и превращаем его в цемент». Технология все еще находится в разработке: демонстрационный завод в Мосс-Лендинг, Калифорния, и партнерство с китайской группой по строительству завода рядом с угольной шахтой во Внутренней Монголии, где они планируют использовать выбросы углекислого газа для производства цемента.
Calix, австралийская компания, производит цемент с использованием перегретого пара, который модифицирует частицы цемента и делает их более чистыми и химически активными.В процессе также выделяется углекислый газ, что облегчает улавливание газа и предотвращение его попадания в атмосферу.
Технологический университет Луизианы, как Novacem и Calera, полностью отказывается от известняка; в нем используется паста под названием геополимер, состоящая из летучей золы, гидроксида натрия и гидроксида калия.
«Пыль со временем уляжется, и одна из этих идей сработает», — сказал Дженнингс.
Вначале одним из самых больших скептиков Novacem была крупнейшая частная строительная компания Великобритании Laing O’Rourke.Директор, отвечающий за наблюдение за перспективной университетской работой, Дирадж Бхардвадж узнал о продукте Novacem благодаря своим ученым связям. Он посмотрел на химию, подумал, что все проверил, и несколько лет назад поделился этой идеей с председателем, у которого было много сомнений. По его словам, цемент не может быть достаточно прочным для коммерческого использования. Нужен был известняк. Когда материал Novacem достигнет 40 мегапаскалей — абсолютного минимума прочности, необходимого для структурной стабильности, — тогда он мог бы заинтересоваться.
Семь дней спустя небольшой кусок цемента Novacem, помещенный в тиски, попал в эту точку. Двадцать восемь дней спустя он достиг 60 мегапаскалей. Затем Бхардвадж передал результаты председателю, который сказал: «Давайте сделаем это поработать». Лайнг О’Рурк теперь является крупным партнером Novacem. Сегодня, после долгих усилий, цемент приближается к 80 мегапаскалям. Бетон из цемента Novacem сопоставим по прочности с некоторым стандартным бетоном.
Среди других партнеров Novacem — Lafarge в Париже, крупнейший в мире производитель строительных материалов, и Rio Tinto, лондонская глобальная горнодобывающая компания, стремящаяся помочь Novacem в добыче силикатов магния.
«Цементная промышленность сейчас развивается финансово значимым и научно значимым образом», — сказал Дженнингс, имея в виду все различные экспериментальные подходы. «Мир меняется. Всем, включая все цементные компании, необходимо быть как можно более экологичным и немного лучше заботиться о мире ».
Jennings отказался одобрить какой-либо конкретный новый цемент. «Если Novacem работает, — сказал он, — это очень привлекательная идея.”
Бхардвадж более внимателен. Он сказал, что недавно пошел в свою команду инженеров. «Честно говоря, не будьте вежливы», — сказал он им. «Отложите в сторону любые вопросы об углероде. Как ты думаешь, это что-то вроде портландцемента? » Ответ удивил его: они сказали, что так лучше. Почему? Он был не только сильным, но и чисто-белым. Портландцемент слегка серый. «Вы можете добавить красок к этому цементу», — сказал Бхардвадж. «Представьте, что в вашем доме есть цементная стена любого цвета, которую вы хотите.”
Цемент имеет прекрасный оттенок белого, как отметил Власопулос, демонстрируя опытный образец цементного завода своей компании. Ссылаясь на соседние лаборатории биологических наук, он сказал: «Мы громче», добавив: «Они там лечат людей; мы лечим кое-что еще ». Неповоротливая машина перед ним, в данный момент простаивающая, имеет длинные трубы, которые гремят и лязгают, срабатывают сигнализация и миксеры, которые взбивают и выплевывают ведра творения Власопулоса.
Власопулос был в приподнятом настроении, потому что накануне сделал предложение своей девушке.(Она сказала «да».) В углу комнаты находилось то, что он называл «нашим музеем». На маленьком столике лежали первые куски цемента Novacem — они были похожи на детские кубики, только более пыльные. «Это было не очень хорошо», — сказал он, держа хрупкую на вид сколотую. «Теперь мы знаем, что делаем». Завод может производить около пяти тонн цемента в год. Компания также работает над еще одним объектом, который будет производить 200 тонн в год. Если все пойдет хорошо, компания намерена лицензировать свой рецепт производителям цемента по всему миру.
Главное препятствие, которое компании еще предстоит преодолеть, — это история. Портландцемент завод . Так было всегда, с того дня 1824 года на кухне Джозефа Аспдина. «Цемент существует очень давно, — сказал Бхардвадж. «Люди этому верят. Они могут осмотреть все постройки, сохранившиеся сотни лет назад. Таким образом, для Novacem подтверждение долговечности потребует времени. Им придется действовать медленно. Если мне нужно построить мост или здание из цемента Novacem, как мне убедить людей, что это нормально? Вот в чем проблема.Никто не хочет, чтобы мост рухнул ».
На вопрос, пойдет ли он по мосту, построенному из цемента Novacem, Бхардвадж ответил: «У меня с этим не будет проблем». Но этот мост еще не построен.
Майкл Розенвальд написал о нанотехнологиях и охотниках за гриппом для Смитсоновского института . Джон Риттер живет в Пенсильвании.
.